第三部分:金属连接成形工艺
第三章 金属罐的结构设计及成型工艺

金属包装容器结构设计与制造
(a)圆罐
(b)方形罐
图3—16罐身口部翻边尺寸
②锡焊罐制造工艺 ③电阻焊制罐工艺及主要设备
图3—17滚凸筋示意图
株洲工学院包印学院 吴若梅
金属包装容器结构设计与制造
图3-18电阻焊原理
图3一19苏德罗尼克焊机主电路原理
(a)罐身方向与轧制方向关系 (b)A处的放大图
图3-3罐盖或罐底的膨胀圈结构
(3)易开结构
①卷开结构 ②易开盖结构
图3-4圆边结构
株洲工学院包印学院 吴若梅
金属包装容器结构设计与制造 图3-5 固体包装易开盖罐
图3—7液体包装易开盖
图3-6新型固体包装易开盖罐
株洲工学院包印学院 吴若梅
金属包装容器结构设计与制造
3 三片罐罐身的制造工艺及设备 三片罐中,若按罐身制造工艺的不同可分为锡焊罐、粘接罐、卷
r1=α0=.310--15.01β=r525=00.1-1.0 r3=0.2-1.0
株洲工学院包印学院 吴若梅
金属包装容器结构设计与制造
内径153mm的罐盖和冲模结构尺寸
株洲工学院包印学院 吴若梅
金属包装容器结构设计与制造 罐盖板尺寸设计 5 成型工艺 两重卷边 T=1.75-2.00 W=3.30-3.60 B1 =2.10-2.20 B2=2.20-
2 罐型与规格: 罐号 15267 公称直径 153 内径153.4 外高 267
计算体积4823.73cm3
3 制造工艺 : 电阻焊
4 三片罐结构设计
(1)罐身:罐身接缝 环筋 翻边结构 罐身板尺寸设计
(2)罐盖和罐底
膨胀圈 :两个外凸筋与三级斜坡
园边 d=153.1 d1=153.5 d2=152.8 D1=164.3 D2=162.1 h2=3.3
第三章连接成形介绍
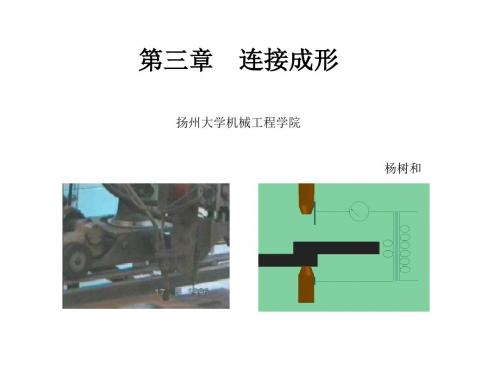
电弧产生的原理
一般情况下,气体是不导电的,要使两极间能够连 续地放电,必须使两极间的气体电离,连续不断地产 生带电粒子(电子、正负离子),同时,在两极间应 有足够的电压,带电粒子在电场的作用下向两极做定 向运动,即形成导电体并通过很大的电流,产生强烈 的电弧放电。 这也是产生电弧的条件。
焊接电弧所使用的电源称为弧焊电源。
酸性焊条:药皮熔渣中酸性氧化物(如SiO2、TiO2、Fe2O3)比碱
3.焊条的牌号与型号
(1)型号:国家标准中规定的焊条代号。
(2)牌号: 焊条牌号是焊条行业标准中规定的焊条代号。 其表示方法为:以大写拼音字母或汉字表示焊条的类别,后面跟三位数字,前两位表 示焊缝金属的性能,如强度、化学成分、工作温度等;第三位数字表示焊条药皮的类 型和焊接电源。
第三章 连接成形
第三章 连接成形
(三)改善焊接接头组织和性能的措施
(1)选材:尽量选择低碳且硫、磷含量低的钢材作为焊接结构材料。 (2)适当控制冷却速度:使热影响区尽量缩小。对于低碳钢,采用细焊丝
、小电流、高焊速,可提高接头韧度,减轻接头脆化;对于易淬硬钢,在
不出现硬脆马氏体的前提下适当提高冷却速度,可以细化晶粒,有利于改 善接头性能。
第三章 连接成形
扬州大学机械工程学院
杨树和
第三章 连接成形
一、基本内容
§3.1 §3.2 §3.3 §3.4 §3.5
电弧焊 其它连接方法 常用金属材料的焊接 焊接件的结构工艺性 胶接
二、重点 1、焊接接头及热影响区的组织与性能的变化;焊接应力与变形产生的原因、规 律和预防方法; 2、常用金属的焊接性能及其应采用的; 3、焊接结构设计的工艺性。 三、难点 1、接头组织形成的机理; 2、焊接应力、变形的客观规律及防止措施,焊接方法的选用 。
第三篇(塑性加工)

纤维组织的稳定性很高,不能用热处理或其它方法加以消 除,只有经过锻压使金属变形,才能改变其方向和形状。 合理利用纤维组织
应使零件在工作中所受的最大正应力方向与纤维方向重合;
最大切应力方向与纤维方向垂直; 并使纤维分布与零件的轮廓相符合,尽量不被切断。
§1-3
金属的可锻性
金属材料通过塑性加工获得优质零件的难易程度。 (经塑性加工而不断裂) 塑性
三拐曲轴的锻造过程
§2-1 锻造方法
自由锻特点
●
坯料表面变形自由;
● 设备及工具简单,锻件重量不受限制; ● ● ●
锻件的精度低; 生产率低,适用于单件小批生产; 是大型锻件的唯一锻造方法。
§2-1 锻造方法
模锻
使加热后的金属在模膛内
受压变形以获得所需锻件 的方法。 应用: 大批量生产中小锻件。 <150Kg,如曲轴、连 杆、齿轮。
在冷加工时,形变强化使金属塑性降低,进
一步加工困难,应安排中间退火工艺。 实质:塑性变形时位错运动受阻,使交叉滑移中位错运动范围缩小,因 此,金属性能随之改变。
一、金属材料产生加工硬化
金属材料 强度和硬 度提高, 塑性和韧 性下降。
有利:加工硬化可提高产品性能! 不利:进一步的塑性变形带来困难! 加热可消除硬化现象!
压力使金属成型为各种型材和锻件等。
a)自由锻 b)模锻 c)胎模锻 胎模锻:自由锻设备上,采用不与上、下砧相连接的活动模具 成形锻件的方法。是介于自由锻和模锻之间的锻造工艺方法。 2)冲压 利用冲模将金 属板料切离或变形 为各种冲压件。
3)轧制 使金属坯料通过两个旋转轧辊之间的间隙而产生塑性变形的 加工方法。 用于生产各种型材、管材、板材等。
模锻
模锻是利用锻模使坯 料变形而获得锻件的 锻造方法。
汽车高强度钢材技术的发展
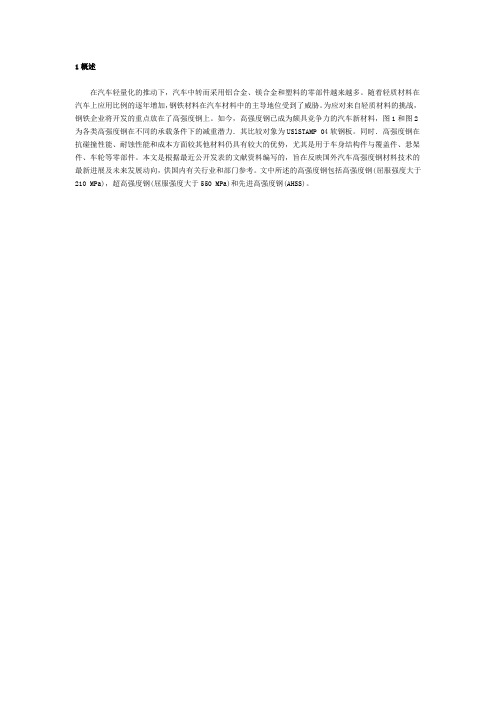
1概述在汽车轻量化的推动下,汽车中转而采用铝合金、镁合金和塑料的零部件越来越多。
随着轻质材料在汽车上应用比例的逐年增加,钢铁材料在汽车材料中的主导地位受到了威胁。
为应对来自轻质材料的挑战,钢铁企业将开发的重点放在了高强度钢上。
如今,高强度钢已成为颇具竞争力的汽车新材料,图1和图2为各类高强度钢在不同的承载条件下的减重潜力.其比较对象为USlSTAMP 04软钢板。
同时.高强度钢在抗碰撞性能、耐蚀性能和成本方面较其他材料仍具有较大的优势,尤其是用于车身结构件与覆盖件、悬架件、车轮等零部件。
本文是根据最近公开发表的文献资料编写的,旨在反映国外汽车高强度钢材料技术的最新进展及未来发展动向,供国内有关行业和部门参考。
文中所述的高强度钢包括高强度钢(屈服强度大于210 MPa),超高强度钢(屈服强度大于550 MPa)和先进高强度钢(AHSS)。
2主要技术进展超轻车身(ULSAB)、超轻覆盖件(ULSAC)、超轻悬架系统(ULSAS)和新概念超轻车身(ULSAB-AVC)等项目的成功实施,验证了高强度钢在减轻汽车自重和改善车辆性能中的有效性。
为了将这些项目所取得的技术成果转化为现实的生产力,近期的高强度钢技术研究,主要集中在支撑技术(Enabling Technologies)上。
2.1若干高强度钢的开发当前正处于新一代高强度钢开发的前夜。
从冶金学的角度看,近几年高强度钢材料的开发,大多只是对原有钢种牌号的补充或性能改善,厚度进一步减薄,材料本身并未取得突破性进展。
开发的难点是要针对不同的零件,力求在产品的强度、塑性和成本之间取得平衡。
SFGHITEN、NANOHITEN、ERW和HISTORY是日本JFE公司最近开发出的几种高强度钢。
其中SFGHITEN为含Nb系列高强度IF钢板,主要应用对象是汽车车身外板,研究用钢的化学成分见表1。
SFGHITEN利用析出的Nb(C,N)微粒和细化晶粒得到强化,其独特之处在于晶界附近存在所谓“无沉淀区”,它降低了材料的屈服强度。
机械制造工艺学电子教案
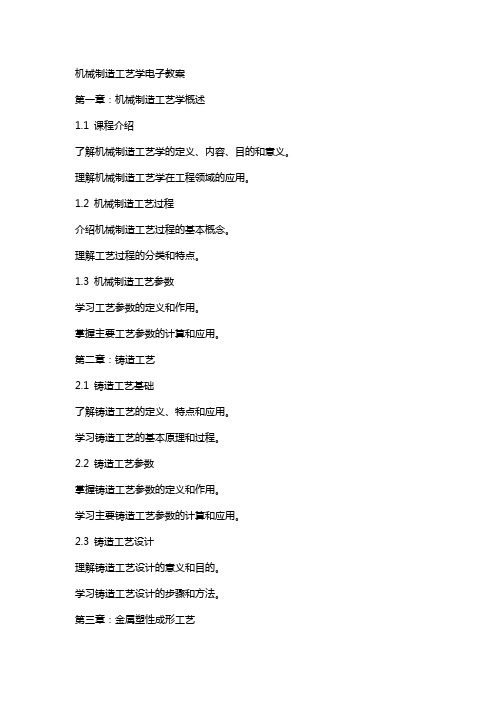
机械制造工艺学电子教案第一章:机械制造工艺学概述1.1 课程介绍了解机械制造工艺学的定义、内容、目的和意义。
理解机械制造工艺学在工程领域的应用。
1.2 机械制造工艺过程介绍机械制造工艺过程的基本概念。
理解工艺过程的分类和特点。
1.3 机械制造工艺参数学习工艺参数的定义和作用。
掌握主要工艺参数的计算和应用。
第二章:铸造工艺2.1 铸造工艺基础了解铸造工艺的定义、特点和应用。
学习铸造工艺的基本原理和过程。
2.2 铸造工艺参数掌握铸造工艺参数的定义和作用。
学习主要铸造工艺参数的计算和应用。
2.3 铸造工艺设计理解铸造工艺设计的意义和目的。
学习铸造工艺设计的步骤和方法。
第三章:金属塑性成形工艺3.1 金属塑性成形工艺基础了解金属塑性成形工艺的定义、特点和应用。
学习金属塑性成形工艺的基本原理和过程。
3.2 金属塑性成形工艺参数掌握金属塑性成形工艺参数的定义和作用。
学习主要金属塑性成形工艺参数的计算和应用。
3.3 金属塑性成形工艺设计理解金属塑性成形工艺设计的意义和目的。
学习金属塑性成形工艺设计的步骤和方法。
第四章:焊接工艺4.1 焊接工艺基础了解焊接工艺的定义、特点和应用。
学习焊接工艺的基本原理和过程。
4.2 焊接工艺参数掌握焊接工艺参数的定义和作用。
学习主要焊接工艺参数的计算和应用。
4.3 焊接工艺设计理解焊接工艺设计的意义和目的。
学习焊接工艺设计的步骤和方法。
第五章:机械加工工艺5.1 机械加工工艺基础了解机械加工工艺的定义、特点和应用。
学习机械加工工艺的基本原理和过程。
5.2 机械加工工艺参数掌握机械加工工艺参数的定义和作用。
学习主要机械加工工艺参数的计算和应用。
5.3 机械加工工艺设计理解机械加工工艺设计的意义和目的。
学习机械加工工艺设计的步骤和方法。
第六章:机械装配工艺6.1 机械装配工艺基础了解机械装配工艺的定义、特点和应用。
学习机械装配工艺的基本原理和过程。
6.2 装配工艺参数掌握装配工艺参数的定义和作用。
5第三篇焊接成形工艺
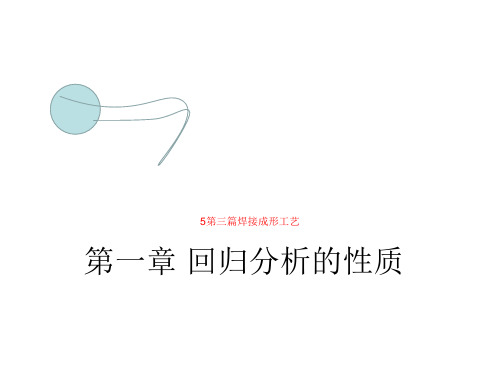
J422 ——牌号(焊接行业中焊条代号)
药皮类型、电流种类、 1-5酸性、6、7碱性 抗拉强度 420MPa 结构钢焊条。
注意:
• 焊条型号是国家标准中的焊条代号;焊条牌号是焊 接行业的焊条代号,注意型号和牌号的对应关系。
• 按熔渣性质,焊条可分为两类: ➢ 酸性焊条:药皮熔渣中的酸性氧化物较多,适于各
5第三篇焊接成形工艺
第一章 回归分析的性质
焊接成型
• 焊接的实质 通过加热或加压等手段,使分离的两 部分金属借助于金属间原子的粘结与扩散作用, 使分离的金属材料牢固地连接起来,成为不可拆 卸的连接方式。
• 焊接特点 • 1)能化大为小,拼小为大:把大型复杂的机器零
部件,分解为简单的小零部件来准备毛坯,然后 再用焊接的方法把它们连接起来,这样可简化锻 造或锻压工艺,还可以解决铸锻能力的不足。
小,变形较小,焊缝致密无渣壳,成形美观。 • ③ 适用性广—可以焊接几乎所有的金属,特
别适于焊接易氧化材料。 • ④明弧可见,操作方便,可以全位置焊接。
•氩弧焊与熔渣保护焊相比的缺点
• ① 氩气成本高,设备比较复杂。 • ② 只能在室内进行焊接—以防保护气体被
破坏。 • 氩弧焊主要用于焊接铝、镁、钛及其合金,
• ④ 焊前预热,可减小温差,减少焊接应力 较为效。
• ⑤ 采用小能量焊接方法,或焊后立即捶击。 • ⑥ 需较彻底地消除焊接应力时,焊后去应
力退火。
• ⑦ 采用水压试验或振动法消除焊接应力。
(七)焊接变形
• 焊接变形:由焊接应力引起的变形。 • 变形种类: • 收缩变形 角变形 弯曲变形 扭曲变形 波浪变形
• 3)熔化金属与空气接触,产生氧化物,使钢中合金元素 C、Si、Mn烧蚀,氮、氢在高温下溶解于液态金属,产生 氮化物增加焊缝脆性,氢的溶入会引起氢脆化—空气在高 温电弧作用下分解出原子状态的氧、氮、氢。
金属成形产业链

金属成形产业链全文共四篇示例,供读者参考第一篇示例:金属成形产业链是指利用金属材料进行各种成形加工的产业链。
包括金属开采、金属加工、金属制造等环节。
金属成形产业链在现代工业中扮演着重要的角色,广泛应用于汽车、航空航天、电子等领域。
金属成形产业链的第一环节是金属开采。
金属开采是指从矿石中提取金属的过程,通常包括勘探、采矿、矿石处理等步骤。
金属开采是金属成形产业链的基础环节,直接影响着后续加工和制造的质量和成本。
第二环节是金属加工。
金属加工是指将金属材料进行各种成形加工的过程,通常包括锻造、压力加工、切削、焊接等工艺。
金属加工是将金属材料加工成各种零部件和组件的重要环节,是金属成形产业链的核心环节。
第三环节是金属制造。
金属制造是指利用金属材料制造各种成品产品的过程,包括汽车、飞机、电子产品等。
金属制造是金属成形产业链的最终环节,直接决定着金属产品的质量和性能。
金属成形产业链的发展受到多方面因素的影响。
技术水平是推动金属成形产业链发展的重要因素。
随着科技的不断进步,金属成形技术也在不断更新换代,生产效率和产品质量得到了显著提升。
市场需求也是影响金属成形产业链发展的关键因素。
随着人们生活水平的提高和产业结构的调整,金属产品的需求也在不断增加,促进了金属成形产业链的发展。
政策环境和产业政策也对金属成形产业链的发展起着重要作用。
政府出台的各种产业政策和法规,可以引导和规范金属成形产业链的发展方向,促进产业升级和转型。
金属成形产业链在中国的发展具有广阔的市场前景和发展空间。
通过不断加大技术创新和产品升级力度,金属成形产业链可以实现产业升级和转型,提高国内金属制造产业的整体竞争力。
随着中国汽车、航空航天、电子等行业的快速发展,金属成形产品的需求也在不断增加,为金属成形产业链的发展带来了机遇和挑战。
第二篇示例:金属成形产业链是现代制造业中一个非常重要的部分,涵盖了众多产业环节,包括原材料采购、加工制造、销售分销等多个环节。
金属材料的成型工艺

5
20231/7./17爆炸焊
爆炸焊是以炸药为能源进行金属间焊接的方法。这种焊接是 利用炸药的爆轰,使被焊金属面发生高速倾斜碰撞,在接触面上造 成一薄层金属的塑性变形,在此十分短暂的冶金过程中形成冶金结 合。
爆炸焊的特点是: 1)能将任意相同的、特别是不同的金属材料迅速牢固地焊接起来。 2)工艺十分简单,容易掌握。 3)不需要厂房、不需要大型设备和大量投资。 4)不仅可以进行点焊和线焊,而且可以进行面焊-爆炸复合,从 而获得大面积的复合板、复合管和复合管棒等。 5)能源为低焊速的混合炸药,它们价廉、易得、安全和使用方便。
4
锻造基础知识
锻202造1/7/是17 对金属坯料(不含板材)施加外力,使其产生塑性变形、改变尺
寸、形状及改善性能,用以制造机械零件、工件、工具或毛坯的成形加 工方法。
根据在不同的温度区域进行的锻造,针对锻件质量和锻 造工艺要求的不同,可分为冷锻、温锻、热锻三个成型温 度区域。一般地讲,在有再结晶的温度区域的锻造叫热锻, 不加热在室温下的锻造叫冷锻。
的工件,形状和尺寸精度高,表面光洁,加工工序少, 便于自动化生产。当加工工件大、厚,材料强度高、 塑性低时,都采用热锻压。
(4)等温锻压 工件在整个成形过程中温度保持
不变。等温锻压是为了充分利用某些金属在某一温度 下所具有的高塑性,或为了获得特定的组织和性能, 所需费用较高,仅用于特殊的锻压工艺,如超塑成形。
7
4.冲压 2021/7/17
冲压:金属板料在冲压模之间受压产生分离或产生塑
性变形的加工方法。
按加工温度分类:热冲压和冷冲压。前者适合变 形抗力高,塑性较差的板料加工;后者在室温 下进行,是薄板常用的冲压方法。
8
•冲压基础知识
金属材料成型_3.6超塑性成型

5)超塑性无模拉拔成形
利用超塑性材料在超塑性状态下对温度的敏感性,只在被加工 的棒料或管材外部加设感应加热圈,并在棒料或管材的两端施加载 荷,当感应圈移动时,就会形成横截面周期变化,甚至非周期变化 的棒形零件,或者是变壁厚的管形零件。
TWO
2
超塑性成型工艺特点
1)金属塑性大为提高,过去认为只能采用铸造成形而不能锻造成形 的镍基合金,也可进行超塑性模锻成形,因而扩大了可锻金属的种类。
图3-36 飞机上采用的部分SPF、SPF/DB构件
FOUR
4
超塑性成型重点企业
Luxfer 的集团公司 Superform USA 及其附属公司 Superform Aluminium 是全球最大的铝、镁和钛超塑成型零件供 应商,主要为航空航天、汽车、卡车、铁路、医疗系统和建筑行 业提供零件。Airstair 是一种内置于小型飞机门内的四级楼梯,需 要制造有23 个焊接部件的铝组件。但 Superform USA 使用 PA M - S TA M P 对 该 组 件 进 行 了 整 体 设 计 , 实 现 了 更 轻 量 、 刚 性 和 低成本的解决方案。
图3-35 径向辅助压力拉深原理示意
4)超塑性挤压成形
将毛坯直接放入模具内一起加热到最佳的超塑性温度,保持恒 温,以恒定的慢速加载、保压,在封闭的模具中进行压缩成形的工 艺。它是利用超塑性合金在变形中的极低变形抗力进行挤压成形, 故所使用的模具简单,寿命高,对变形程度大的零件,可一次成形, 省去了中间退火程序,工序得到简化。它可成形零件和模具。
近年来,我国新机研制及改进机型中,前缘襟翼、鸭翼、整体壁板和 腹鳍等大尺寸钛合金构件采用SPF/DB技术。针对型号对金属防热结构的 需求,航天材料及工艺研究所开展了钛合金波纹板SPF 技术研究,成功 制备出TC4 钛合金防热瓦等热结构部件。
材料成形技术基础答案_第2版_施江澜_赵占西主编-推荐下载
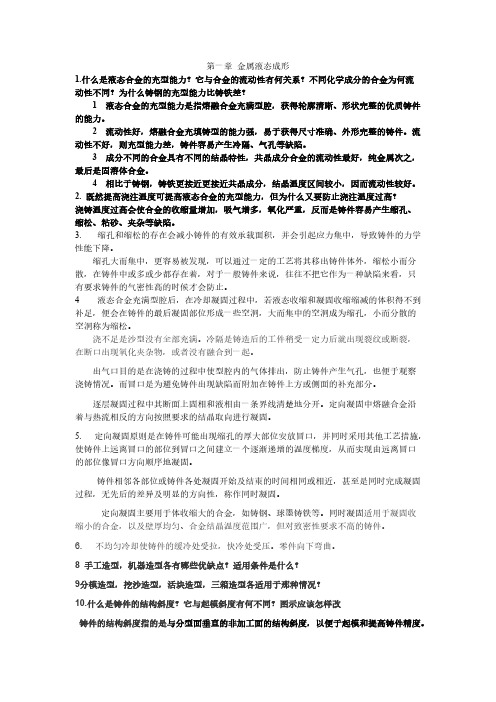
第一章金属液态成形1.什么是液态合金的充型能力?它与合金的流动性有何关系?不同化学成分的合金为何流动性不同?为什么铸钢的充型能力比铸铁差?1 液态合金的充型能力是指熔融合金充满型腔,获得轮廓清晰、形状完整的优质铸件的能力。
2 流动性好,熔融合金充填铸型的能力强,易于获得尺寸准确、外形完整的铸件。
流动性不好,则充型能力差,铸件容易产生冷隔、气孔等缺陷。
3 成分不同的合金具有不同的结晶特性,共晶成分合金的流动性最好,纯金属次之,最后是固溶体合金。
4 相比于铸钢,铸铁更接近更接近共晶成分,结晶温度区间较小,因而流动性较好。
2. 既然提高浇注温度可提高液态合金的充型能力,但为什么又要防止浇注温度过高?浇铸温度过高会使合金的收缩量增加,吸气增多,氧化严重,反而是铸件容易产生缩孔、缩松、粘砂、夹杂等缺陷。
3. 缩孔和缩松的存在会减小铸件的有效承载面积,并会引起应力集中,导致铸件的力学性能下降。
缩孔大而集中,更容易被发现,可以通过一定的工艺将其移出铸件体外,缩松小而分散,在铸件中或多或少都存在着,对于一般铸件来说,往往不把它作为一种缺陷来看,只有要求铸件的气密性高的时候才会防止。
4 液态合金充满型腔后,在冷却凝固过程中,若液态收缩和凝固收缩缩减的体积得不到补足,便会在铸件的最后凝固部位形成一些空洞,大而集中的空洞成为缩孔,小而分散的空洞称为缩松。
浇不足是沙型没有全部充满。
冷隔是铸造后的工件稍受一定力后就出现裂纹或断裂,在断口出现氧化夹杂物,或者没有融合到一起。
出气口目的是在浇铸的过程中使型腔内的气体排出,防止铸件产生气孔,也便于观察浇铸情况。
而冒口是为避免铸件出现缺陷而附加在铸件上方或侧面的补充部分。
逐层凝固过程中其断面上固相和液相由一条界线清楚地分开。
定向凝固中熔融合金沿着与热流相反的方向按照要求的结晶取向进行凝固。
5. 定向凝固原则是在铸件可能出现缩孔的厚大部位安放冒口,并同时采用其他工艺措施,使铸件上远离冒口的部位到冒口之间建立一个逐渐递增的温度梯度,从而实现由远离冒口的部位像冒口方向顺序地凝固。
第三章金属的铸造成形工艺砂型铸造-造型方法
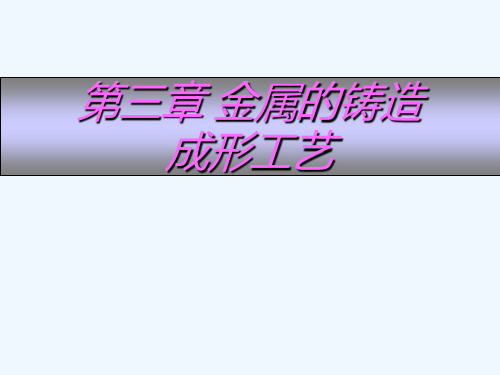
造型方法的选择
微震紧实:
微震紧实是在加 压坚实型砂的同时, 砂箱和模板作高频率、 小振幅震动。此方法 生产率较高、紧实度 均匀、噪声小。广泛 用于成批生产中、小 型铸件。
气动微震压实造型
造型方法的选择
抛砂紧实:
抛砂紧实是利用 离心力抛出型砂,使 型砂在惯性力下完成 填砂和坚实。该方法 生产率高,能量消耗 少、噪声低、型砂坚 实度均匀、适用性广。 主要适用于单件、小 批、成批、大量生产 中、大型铸件或大型 芯。
造型方法的选择 活块造型:活块造型是在制模时将铸件上的妨碍 起模的小凸台,肋条等这些部分作成活动的 (即活块)。起模时,先起出主体模样,然后 再从侧面取出活块。其造型费时,工人技术水 平要求高。主要用于单件、小批生产带有突出 部分、难以起模的铸件。
造型方法的选择
脱箱造型: 脱箱造型主要采用活动砂箱来造型, 在铸型合型后,将砂箱脱出,重新用于造 型。 一个砂箱可制出许多铸型。金属浇注 时为防止错型,需用型砂将铸型周围填紧, 也可在铸型上套箱。常用于生产小铸件, 因砂箱无箱带,故砂箱一般小于400mm。
造型方法的选择 地坑造型:地坑造型是利用车间地面砂床作为铸 型的下箱。大铸件需在砂床下面铺以焦炭,埋 上出气管,以便浇注时引气。 地坑造型仅用或不用上箱 即可造型,因而减少了造 砂箱的费用和时间,但造 型费工、生产率低,要求 工人技术水平高。适用于 砂箱不足,或生产要求不 高的中、大型铸件,如砂 箱、压铁、炉栅、芯骨等
型芯的制作
造型方法的选择
机器造型
机器造型是指用机器全部完成或至少完成 紧砂操作的造型工序。机器造型铸件尺寸精确、 表面质量好、加工余量小,但需要专用设备, 投资较大,适合大批量生产。 常用的机器造型方法有:压实式、震实 式、抛砂式、射压式等。
金属塑性成形原理及工艺
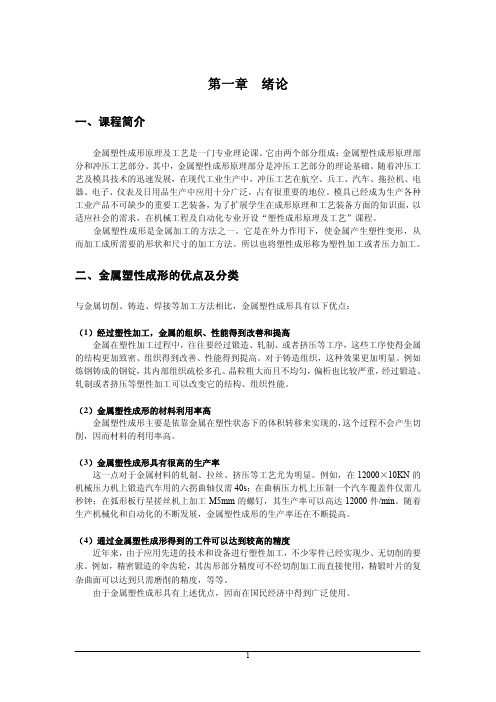
2
4.锻造
锻造的示意图如图 4 所示。 锻造可以分为自由锻造和模锻。自由锻造一般是在锤锻或者水压机上,利用简单的工具 将金属锭或者块料锤成所需要形状和尺寸的加工方法。 自由锻造不需要专用模具, 因而锻件 的尺寸精度低、生产效率不高。模锻是在模锻锤或者热模锻压力机上利用模具来成形的。金 属的成形受到模具的控制,因而其锻件的外形和尺寸精度高,生产效率高,适用于大批量生 产,模锻又可以分为开式模锻和闭式模锻。
4
变形问题和轴对程问题; (5)屈服准则:屈雷斯加屈服准则、密席斯屈服准则、屈服准则的几何表达、平面问 题和轴对程问题中屈服准则的简化; (6)本构方程:弹性应力应变关系、塑性变形时应力应变关系的特点、塑性变形的增 量理论、塑性变形的全量理论;
六、课程要求
金属塑性加工原理的任务是研究塑性成形中共同的规律性问题, 就是在阐述应力、 应变 理论以及屈服准则等塑性理论的基础上, 研究塑性加工中有关力学问题的各种解法, 分析变 形体内的应力和应变分布,确定变形力和变形功,为选择设备和模具设计提供依据。所以, 要求大家: (1) 掌握金属塑性变形的金属学基础, 具体的说就是金属的结构和金属塑性变形机理。 (2)了解影响金属塑性和塑性成形的主要因素。 (3)掌握塑性变形的力学基础:包括应力分析、应变分析、屈服准则和应力应变关系。 (4)掌握塑性成形力学问题的各种解法以及其在具体工艺中的应用。
图4
5.冲压
冲压又可以分为拉深、弯曲、剪切等等。其示意图见图 5。 拉深等成形工序是在曲柄压力机上或者油压机上用凸模把板料拉进凹模中成形, 用以生 产各种薄壁空心零件。 弯曲是坯料在弯矩的作用下成形,如板料在模具中的弯曲成形、板带材的折弯成形、钢 材的矫直等等。 剪切是指坯料在剪切力作用下进行剪切变形,如板料在模具中的冲孔、落料、切边、板 材和钢材的剪切等等。
第3章 金属材料的塑性成形——压力加工
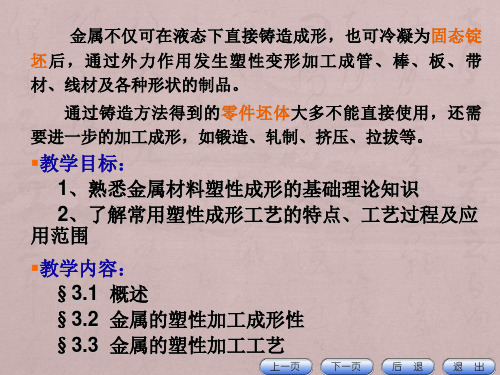
其优劣主要取决于金属本身和变形时的外部条件。
影响可锻性的因素
(1) 金属的成分:纯金属好于合金,fcc好于bcc好 于hcp,低碳钢优于高碳钢,低碳低合金钢优于 高碳高合金钢;有害杂质元素一般使可锻性变坏
(2) 金属的组织:单相组织好于多相组织;铸态下 的柱状组织、粗晶粒组织、晶界上存在偏析或有 共晶莱氏体组织使可锻性变差
2、研究与开发塑性加工过程的计算机模拟技术与模具 CAD/CAE/CAM技术等。
3、研究与开发柔性成形技术、增量成形技术、净成形技 术、近净成形技术、复合成形技术等。
4、研究与开发使环境净化的加工技术,如低噪音、小/ 无震动、节省能源、资源或再利用的加工技术。
§3.2 金属的塑性加工成形性
金属的塑性加工成形性/可锻性(Forgeability) : 用来衡量金属在外力作用下发生塑性变形而不易 产生裂纹的能力,是金属重要的工艺性能之一;
(3) 加工条件 1) 变形温度:一般变形温度的升高,可提高金 属的可锻性;但注意过热、过烧问题
不同合金系8种典型金属的可锻性
Ⅰ—纯金属及单相合金(铅合金、 钼合金、镁合金);Ⅱ—纯金属及 单相合金(晶粒长大敏感者)(铍、镁 合金、钨合含、钛合金);Ⅲ—具 有不溶解组分的合金(高硫钢,含 硒不锈钢);Ⅳ—具有可溶组分的 合金(含氧化物的钼合金,含可溶 性碳化物和氮化物的不锈钢); Ⅴ—加热时形成有塑性第2相的合 金(高铬不锈钢);Ⅵ—加热时形成 低熔点第2相的合金(含硫的铁、含 锌的镁合金);Ⅶ—冷却时形成有 塑性第2相的合金(碳钢和低合金钢 、-钛合金和钛合金);Ⅷ—冷 却时形成脆性第2相的合金(高温合
可显著减小总变形力,用小设备加工大零件。
材料成型技术基础第2版课后习题答案
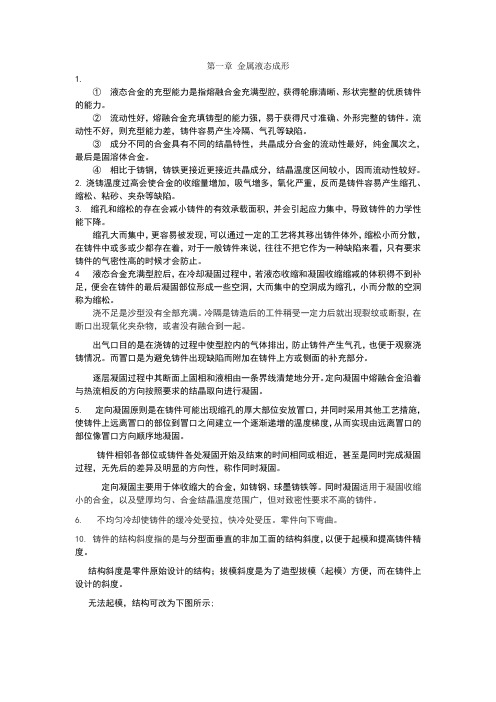
第一章金属液态成形1.①液态合金的充型能力是指熔融合金充满型腔,获得轮廓清晰、形状完整的优质铸件的能力。
②流动性好,熔融合金充填铸型的能力强,易于获得尺寸准确、外形完整的铸件。
流动性不好,则充型能力差,铸件容易产生冷隔、气孔等缺陷。
③成分不同的合金具有不同的结晶特性,共晶成分合金的流动性最好,纯金属次之,最后是固溶体合金。
④相比于铸钢,铸铁更接近更接近共晶成分,结晶温度区间较小,因而流动性较好。
2.浇铸温度过高会使合金的收缩量增加,吸气增多,氧化严重,反而是铸件容易产生缩孔、缩松、粘砂、夹杂等缺陷。
3.缩孔和缩松的存在会减小铸件的有效承载面积,并会引起应力集中,导致铸件的力学性能下降。
缩孔大而集中,更容易被发现,可以通过一定的工艺将其移出铸件体外,缩松小而分散,在铸件中或多或少都存在着,对于一般铸件来说,往往不把它作为一种缺陷来看,只有要求铸件的气密性高的时候才会防止。
4 液态合金充满型腔后,在冷却凝固过程中,若液态收缩和凝固收缩缩减的体积得不到补足,便会在铸件的最后凝固部位形成一些空洞,大而集中的空洞成为缩孔,小而分散的空洞称为缩松。
浇不足是沙型没有全部充满。
冷隔是铸造后的工件稍受一定力后就出现裂纹或断裂,在断口出现氧化夹杂物,或者没有融合到一起。
出气口目的是在浇铸的过程中使型腔内的气体排出,防止铸件产生气孔,也便于观察浇铸情况。
而冒口是为避免铸件出现缺陷而附加在铸件上方或侧面的补充部分。
逐层凝固过程中其断面上固相和液相由一条界线清楚地分开。
定向凝固中熔融合金沿着与热流相反的方向按照要求的结晶取向进行凝固。
5.定向凝固原则是在铸件可能出现缩孔的厚大部位安放冒口,并同时采用其他工艺措施,使铸件上远离冒口的部位到冒口之间建立一个逐渐递增的温度梯度,从而实现由远离冒口的部位像冒口方向顺序地凝固。
铸件相邻各部位或铸件各处凝固开始及结束的时间相同或相近,甚至是同时完成凝固过程,无先后的差异及明显的方向性,称作同时凝固。
金属连接成形

4
材料热加工基础
金属的连接成形
5
材料热加工基础
金属的连接成形
二、连接成形的特点
与切削加工、压力加工、铸造、热处理一起构 成了现代金属加工技术。在汽车、船舶、飞机、航 天、石油化工、桥梁、建筑、交通、电力电子等部 门得到广泛的应用。
6
材料热加工基础
金属的连接成形
与铆接比有如下特点: 1、连接性能好。焊接接头的力学性能、耐高 低温、高压性能和导电性、耐腐蚀性、耐磨性、 密封性等均可达到与母材性能一致。 例,120万kW核电站锅炉,外径6400mm,壁 厚 200mm ,高 13000mm ,耐压 17.5MPa 。使用温 度350℃,接缝不能泄漏。应用焊接方法可制造出 了满足上述要求的结构。 2 、与铆接相比,结构重量 轻,节约材料,制造周期短,成 本低。简化工艺,能以小拼大, 被喻为神奇的“钢铁裁缝”。
辽宁工程技术大学 材料科学与工程学院
材料热加工基础
第三篇
金属的连接成形
材料加工工程系 刘少平制作
材料热加工基础
金属的连接成形
第三篇 金属的连接成形
目 录
第一章 金属连接成形原理及途径 第二章 连接成形的主要工艺 第三章 常用金属材料的焊接
2
材料热加工基础
金属的连接成形
第一章
连接成形原理及途径
3
材料热加工基础
13
材料热加工基础
金属的连接成形
焊接方法的分类
1 2 3 4 1-焊缝区 2-熔合区 3-热影响区 4-母材
熔化焊
焊接方法
压力焊
钎
焊
手工电弧焊 气焊 氩弧焊 电弧焊 气体保护焊 CO2焊 电渣焊 埋弧焊 电子束焊 激光焊 点 焊 电阻焊 缝 焊 摩擦焊 对 焊 扩散焊 高频焊 烙铁钎焊 火焰钎焊 炉中钎焊
我国在金属材料及热加工领域取得的杰出成果、先进工艺与技术
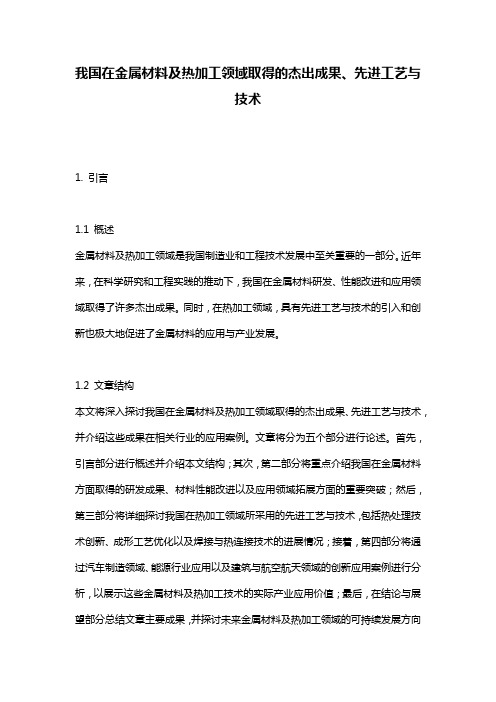
我国在金属材料及热加工领域取得的杰出成果、先进工艺与技术1. 引言1.1 概述金属材料及热加工领域是我国制造业和工程技术发展中至关重要的一部分。
近年来,在科学研究和工程实践的推动下,我国在金属材料研发、性能改进和应用领域取得了许多杰出成果。
同时,在热加工领域,具有先进工艺与技术的引入和创新也极大地促进了金属材料的应用与产业发展。
1.2 文章结构本文将深入探讨我国在金属材料及热加工领域取得的杰出成果、先进工艺与技术,并介绍这些成果在相关行业的应用案例。
文章将分为五个部分进行论述。
首先,引言部分进行概述并介绍本文结构;其次,第二部分将重点介绍我国在金属材料方面取得的研发成果、材料性能改进以及应用领域拓展方面的重要突破;然后,第三部分将详细探讨我国在热加工领域所采用的先进工艺与技术,包括热处理技术创新、成形工艺优化以及焊接与热连接技术的进展情况;接着,第四部分将通过汽车制造领域、能源行业应用以及建筑与航空航天领域的创新应用案例进行分析,以展示这些金属材料及热加工技术的实际产业应用价值;最后,在结论与展望部分总结文章主要成果,并探讨未来金属材料及热加工领域的可持续发展方向和前景展望。
1.3 目的本文旨在全面介绍我国在金属材料及热加工领域取得的杰出成果、先进工艺与技术,突出其重要性和实际应用价值。
通过深入剖析相关成果和案例,我们可以更好地了解我国在这一领域的科学研究和产业发展水平,并为未来的进一步创新提供有益启示。
同时,该文旨在促进学者、科研机构和产业界之间的信息交流与合作,以推动我国金属材料及热加工领域的快速发展,不断提升其在国际舞台上的竞争力。
2. 金属材料的杰出成果:2.1 研发成果:我国在金属材料领域取得了许多重要的研发成果。
首先,我们在金属合金的研究与开发方面取得了巨大进展。
通过合金的优化设计和制备工艺的改进,我们成功地提高了许多金属合金的力学性能、耐腐蚀性能和热稳定性。
例如,在航空航天领域,我们开发出一系列新型镍基和钛基高温合金,用于制造高压涡轮叶片和燃气涡轮引擎等关键部件,使飞机的性能得到显著提升。
材料加工工艺第三章 焊接技术

材料工艺基础(焊接技术)
4
3.2.2 熔化焊接
(1) 氧-乙炔火焰焊(气焊)
可用于焊接大部分黑色金 属和有色金属工件,具有 设备简单,操作灵活,成 本低等优点,应用广泛。
特点:飞溅少,电弧稳定, 焊缝成形美观;焊丝熔敷速 度快,生产率高;调整焊剂 成分,可焊接多种材料;抗 气孔能力较强。但药芯焊丝 制造较困难,且容易变潮, 使用前应烘烤。
焊接材料:碳钢、低合金钢、不锈钢等
材料工艺基础(焊接技术)
14
(5) 电渣焊
电渣焊是利用电流通过熔渣所产生的电阻热作为热源进行 焊接的一种熔焊方法。
① 焊接温度低 ② 可焊接各种金属及合金 ③ 可焊接厚度差别很大的焊件
单件生产率低 焊前对焊件表面的加工清理和装配精度要求十分严格
在航空工业中,用扩散焊制成的钛制品可以代替多种制品、 火箭发动机喷嘴耐热合金与陶瓷的焊接。 机械制造工业中,将硬质合金刀片镶嵌到重型刀具上等。
材料工艺基础(焊接技术)
材料工艺基础(焊接技术)
29
滚焊视频
材料工艺基础(焊接技术)
30
(3) 对焊
利用焊件端面的电阻热,使断面达到热塑性状态,施加顶 压力实现焊接。可分为电阻对焊和闪光对焊。
材料工艺基础(焊接技术)
31
(4) 摩擦焊
利用焊件接触端面 相互摩擦产生的热 量,使端面达到热 塑性状态,然后迅 速施加顶锻力,实 现焊接的一种固相 压焊方法。
材料工艺基础(焊接技术)
- 1、下载文档前请自行甄别文档内容的完整性,平台不提供额外的编辑、内容补充、找答案等附加服务。
- 2、"仅部分预览"的文档,不可在线预览部分如存在完整性等问题,可反馈申请退款(可完整预览的文档不适用该条件!)。
- 3、如文档侵犯您的权益,请联系客服反馈,我们会尽快为您处理(人工客服工作时间:9:00-18:30)。
《材料加工工程》试题库第三部分:金属连接成形工艺一、判断题:(请判断下列概念或说法是否正确,对的在题后括号内打“√”,错的打“×”)1、弧压反馈式埋弧焊机调节电流实际是调节电源外特性曲线(√)2、电阻焊工艺的焊接性比熔焊工艺的焊接性差。
(×)3、电弧焊机的输出端绝对不能短路,否则会烧坏焊机。
(×)4、细丝CO2焊应该采用等速送丝调节系统。
(√)5、负载持续率是负载工作时间与整个周期之比值的百分数。
(×)6、面向腐蚀介质的奥氏体不锈钢焊缝,必须最先施焊。
(×)7、低氢焊条应采用直流电源。
(√)8、多层焊工艺对防止焊缝出现冷裂纹是有益处的。
(√)9、TIG焊是熔化极气体保护焊的英文缩写。
(×)10、转移型等离子弧,电极接电源正极,焊件接电源负极。
(×)11、粗丝埋弧焊应采用变速送丝调节系统。
(√)12、钨极氩弧焊焊接铝合金时宜采用交流电源。
(√)二、单项选择题:(从下列各题备选答案中选出一个正确答案,将其代号填写在相应的横线上。
)1、焊接电弧是一种气体放电现象,其维持放电电压为V左右。
(A )A 10B 20C 30D 402、电弧能有效地把电能转化为。
(D )A.热能B.光能C.机械能D.以上全部3、焊条药皮中含有钾、钠、钙等时,会使电弧。
(A )A.稳定性提高B.稳定性降低C.温度提高D.温度降低4、电弧三个区域的电流密度分布关系是:(B)A 阳极最高,阴极次之,弧柱最低B阴极最高,阳极次之,弧柱最低C 弧柱最高,阴极次之,阳极最低D弧柱最高,阳极次之,阴极最低5、被焊接的两种材料可以为。
(D )A同类金属或非金属材料B同类或不同类金属材料C金属与非金属 D 以上全部6、铝合金MIG焊当弧长为2~8 mm时,其熔滴过渡为过渡。
(C)A 射流过渡B射滴过渡C亚射流过渡D短路过渡7、电弧三个区域的温度分布关系是:(C)A 阳极最高,弧柱居中,阴极最低B阴极最高,弧柱居中,阳极最低;C 弧柱较高,两极较低;D各区温度相等。
8、焊缝成形系数φ表示为。
(C)A H/aB H/BC B/HD a/H9、电阻焊产生电阻热的外部条件是。
(A )A 焊接区要通以强大的焊接电流B 焊接区要施以强大的电极压力C 焊接区要长时间地接触和摩擦D 焊接区要通以惰性保护气体10、在稳定状态下弧焊电源输出电压与电流的关系曲线称为曲线。
(C)A 电弧静特性B 电源动特性C 电源静特性D 电弧动特性11、电弧焊时,焊接电流、电弧电压是分别影响焊缝的主要因素。
(A )A 熔深、熔宽B熔宽、熔深 C 熔深、余高D熔宽、余高12、细丝熔化极电弧焊应采用调节系统。
(C)A 焊接电流反馈B电弧电压反馈C等速送丝D以上任一种三、改错题:(每小题只有一处错误,在错误的文字部分下面划横线,并改正。
)1、焊接电弧是气体自持放电中电压最高、电流最大的区段。
“电压最高”改为“电压最低”2、熔化极气体保护电弧焊的电弧两极应采用直流正接法。
“正接法”改为“反接法”3、熔化极气体保护焊通常采用陡降外特性的电源。
“陡降”改为“平、缓”4、TIG 是埋弧焊的英文缩写“埋弧焊”改为“钨极氩弧焊”5、直流反接法时,焊条应接电源负极。
“电源负极”改为“电源正极”6、重要结构的焊缝,焊后应保留适当的余高“保留适当的余高”改为“除去余高或磨成凹形”四、:简答题1、简述熔化极自动电弧焊两种调节方式的调节原理及适用范围。
答:1)熔化极等速送丝电弧自身调节系统(1)调节原理依统靠电弧自身内反馈具有的自身调节作用,达到补偿干扰,稳定焊接工艺参数的目的。
(2)工艺应用范围a)较细焊丝(直径小于或等于4毫米)埋弧焊、缓降外特性电源。
b)细焊丝(直径小于或等于1.6毫米)气体保护焊、平外特性电源。
2)电弧电压反馈调节系统(1)调节原理采用闭环自动调节控制,是一种变速送丝调节系统。
(2)工艺应用范围多用于粗焊丝(直径大于或等于4毫米)埋弧焊、配用下降特性焊接电源。
2、简述熔化极气体保护电弧焊短路和射流两种过渡的工艺条件、特点及其适用范围。
答:1)短路过渡工艺条件:细焊丝、小电流、低电压。
工艺特点:熔滴细小、过渡频率高、焊缝成形美观。
应用范围:薄板、全位置二氧化碳气体保护焊。
2)射流过渡工艺条件:氩气或富氩气保护、临界电流以上、长弧。
工艺特点:熔滴更细小、过渡频率更高、轴向过渡、过程稳定、焊缝熔深大;应用范围:应用广泛,中、厚板合金钢、不锈钢MIG焊,铝及其合金MIG焊。
3、简述金属工艺焊接性和使用焊接性及其主要影响因素。
答:1)工艺焊接性:是指在一定的工艺条件(包括焊接方法、焊接材料、焊接工艺参数和结构型式等)下焊接时,产生焊接缺陷的倾向性和严重性;2)使用焊接性:是指焊接接头或整体结构是否满足技术条件所规定的各种使用性能的要求;3)影响因素:a)材料因素:材料本身的化学成分、组织状态和力学性能等对其焊接性起着决定性的作用;b)工艺因素:包括所采用的焊接方法和焊接工艺规程;c)结构因素:焊接接头的结构设计直接影响到它的刚度、拘束应力的大小和方向;d)使用条件。
4、简述焊接电弧静特性曲线特征及其对应的电弧焊方法。
答:1)特征:电弧电压与焊接电流呈U型曲线。
2)对应焊接方法:下降段,一般没有对应的实用焊接方法;水平段,对应焊条电弧焊,埋弧焊,钨极氩弧焊等;上升段,对熔化极气体保护电弧焊。
五、综合分析题:1、某厂应用CO2气体保护颗粒过渡工艺焊接厚板构件,焊丝直径1.6mm,所取焊接电流400安培、电弧电压24伏、小档直流电感、直流正接法,结果熔滴过渡不稳,飞溅严重且焊缝出现大量气孔。
试分析形成原因。
答:1)电弧电压取值过低,不能形成稳定的细滴过渡,应将电弧电压提高到34~35伏;2)直流电感不应取小档,细滴过渡可以去掉直流电感:3)采用直流正接法错误,会造成严重的飞溅甚至气孔。
应采用直流反接法。
2、试论铝、镁及其合金(δ>3mm)采用TIG焊工艺时采用交流电源的原因、可能出现的问题以及对焊机的功能要求。
答1)采用交流电源的原因(1)交流电源负半周,工件发射电子,可以清除工件表面的氧化膜(阴极雾化作用);(2)交流电源正半周,钨棒发射电子,电弧稳定;同时钨极产热低,可使其烧损少(冷却作用)。
2)可能出现的问题(1)交流电源频繁过零,即稳定电弧问题;(2)交流电源的整流作用产生直流分量,即消除直流分量问题。
3)对焊机的功能要求(1)应具有高频或脉冲引弧、稳弧功能;(2)能消除直流分量(或方波交流电源)3、试论交流TIG焊工艺时直流分量产生的原因、危害以及其对焊机的功能要求。
答:1)直流分量产生的原因(1)交流电源负半周,工件发射电子,电流较小;(2)交流电源正半周,钨棒发射电子,电流较大;(3)电源正、负半周电流波形不对称,产生直流分量2)直流分量危害(1)削弱阴极雾化(清理)作用,不利于清除工件表面氧化膜;(2)使焊机工作条件变坏降低效率和功率因数;(3)影响电弧及焊接过程的稳定性。
3)对焊机的功能要求(1)应具有高频或脉冲引弧、稳弧功能;(2)能消除直流分量(或方波交流电源)。
4、某厂用熔化极气体保护焊工艺,纯氩气保护焊接合金钢,结果出现电弧不稳,焊缝成形不规则等缺陷。
试分析其原因并提出解决方案。
答:缺陷原因有:1)熔池的粘度大,浸润铺展性差,气孔、咬边倾向大;2)阴极斑点稳定性差,焊缝几何尺寸均匀性差;3)焊缝形状系数较小,“指状”熔深倾向大等。
解决办法:(4分)混合一定比例的氧化性气体便可克服纯Ar保护的上述不足,并同时保留了纯Ar 保护的优点,如Ar+CO2、Ar+CO2+O2、Ar+O2等5、某工程师采用直流TIG焊机焊接板厚为10 毫米的铝合金构件,正极性接法时焊件表面熔化不好、成形极差,反极性接法则电极烧损严重、电弧极不稳定。
试分析其原因,找出解决的办法。
答:1)原因:(1)铝及铝合金表面氧化膜应利用阴极雾化(清理)作用去除;(2)直流反接,有阴极雾化(清理)作用,但采用较大电流时,钨极烧损严重,造成电弧不稳;(3)直流正接,钨极发射电子、电弧稳且钨极烧损小,但无阴极雾化(清理)作用,无法清除表面氧化膜,焊缝成形极差。
2)解决办法:(1)可用普通交流电源代替直流焊接电源;(2)可用交流方波电源代替直流焊接电源。
6、试论低合金钢结构的强化机理、焊接性问题及主要工艺措施。
答:1)低合金钢结构的强化机理(1)热轧钢(σs=294~343Mpa)含碳量在0.2%以下,含合金元素总量不超过3%,含Mn量不超过1.8%,含Si量不超过0.6%。
加入Si、Mn不仅可固溶强化铁素体,还可使铁—碳相图的共析点向低碳方向移动,从而增加珠光体的相对量,以提高钢的强度。
(2)正火钢(σs>390Mpa),除固溶强化外,必须通过沉淀强化进一步提高钢的强度。
因此在热轧钢的基础上再加入某些沉淀强化的合金元素,如V、Nb、Ti、Mo等。
2)低合金钢结构的焊接性问题(1)热影响区脆化(热输入不当、高温时间长、冷却速度快等)(2)冷裂纹(热轧钢的淬硬倾向最小,强度级别高的正火钢冷裂纹敏感性增大。
)(3)热裂纹(一般倾向较小,厚壁根部、边缘焊道,可能出现)3)主要工艺措施(1)预热;(2)控制热输入;(3)后热及焊后热处理。
7、试论四种保护气体Ar、CO2、Ar+O2(1%~5%)、Ar+CO2(20%)的特点及应用答:1)氩气(Ar)特性:(1)单原子惰性气体,高温不分解、不放热、不与金属化学反应,也不溶于金属。
(2)其比重比空气大,比热容和导热系数比空气小,(3)保护性能和稳弧性能良好。
用途:(1)纯Ar保护主要用于有色金属及其合金、活性金属及其合金、高温合金的焊接。
(2)熔化极气体保护焊、惰性气体保护焊、等离子弧焊等。
2)二氧化碳(CO2)特性:(1)多原子气体,高温吸热分解为一氧化碳和氧,对电弧有较强的冷却作用;(2)CO2气体比重大,高温分解体积增大,因而具有较好的隔离保护效果;(3)CO2具氧化性,但目前采用的焊丝(如H08Mn2SiA等)和药芯焊丝,已经解决氧化性等问题,能保证焊缝的冶金质量,用途:(1)适用于低碳钢和低合金结构钢(2)熔化极气体保护焊。
3)Ar+O2(1%~5%)(5分)特性:(1)具有一定的氧化性,可克服纯Ar保护时,电弧阴极斑点漂移、液态金属粘度及表面张力较大,造成焊缝熔深及成形不规则、产生气孔及焊缝咬边等问题。
(2)可以改善熔滴过渡形态,细化熔滴;同时还可降低液态金属粘度及表面张力,改善焊缝成形。
用途:(1)用于不锈钢、高合金钢的焊接;(2)钢的射流过渡或脉冲过渡气体保护焊。
4)Ar+CO2(20%)特性:(1)有较好地熔深和焊缝成形,(2)增大电弧热功率、降低焊接成本用途:(1)低碳钢、低合金结构钢焊接;(2)可用于射流、脉冲或短路形式的气体保护焊。