2015年-2016年工伤事故分析报告
工伤事故分析报告
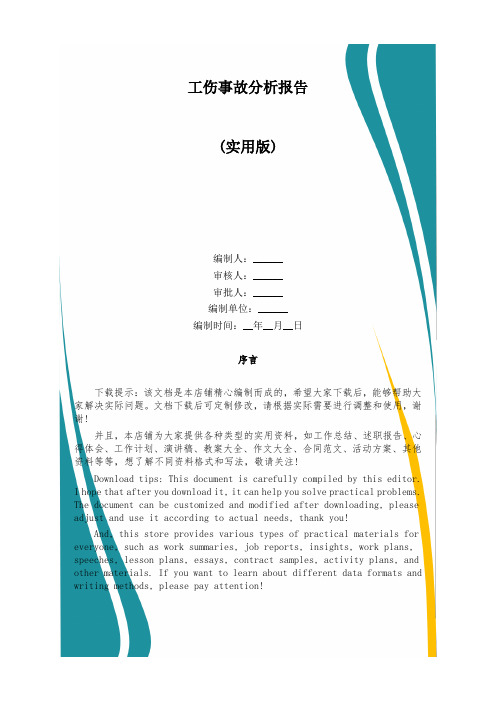
工伤事故分析报告(实用版)编制人:______审核人:______审批人:______编制单位:______编制时间:__年__月__日序言下载提示:该文档是本店铺精心编制而成的,希望大家下载后,能够帮助大家解决实际问题。
文档下载后可定制修改,请根据实际需要进行调整和使用,谢谢!并且,本店铺为大家提供各种类型的实用资料,如工作总结、述职报告、心得体会、工作计划、演讲稿、教案大全、作文大全、合同范文、活动方案、其他资料等等,想了解不同资料格式和写法,敬请关注!Download tips: This document is carefully compiled by this editor.I hope that after you download it, it can help you solve practical problems. The document can be customized and modified after downloading, please adjust and use it according to actual needs, thank you!And, this store provides various types of practical materials for everyone, such as work summaries, job reports, insights, work plans, speeches, lesson plans, essays, contract samples, activity plans, and other materials. If you want to learn about different data formats and writing methods, please pay attention!工伤事故分析报告工伤事故分析报告(通用3篇)工伤事故分析报告篇1关于煤机公司申某X意外事故的调查调查时间:X年X月X日星期X18:10调查人员:发展中心:王、郑、刘X公司安全部:刘X调查内容:XX车间工伤事故事故发生时间:事故发生地点:当事人:郭某、申某、牛某负责人:车间主任——申某安全部负责人——刘X事故处理:事故发生当天早上5:30左右,事故发生后相关负责人等第一时间将伤者送往东胜中心医院接受治疗。
工伤事故分析报告 (4)

工伤事故分析报告1. 引言工伤事故是指在工作过程中,由于人身意外事故导致工人受伤或丧失劳动能力的事件。
工伤事故对劳动者和企业都带来了极大的损失,因此分析工伤事故的原因和趋势对于预防事故的发生具有重要意义。
本报告将对工伤事故进行分析,并提出相应的预防措施。
2. 数据收集与分析为了深入了解工伤事故的情况,我们收集了过去一年内发生的工伤事故的相关数据。
以下是对这些数据的分析结果。
2.1 事故类型分析通过对事故类型的分类统计,我们得出了如下结果:•机械伤害:占总事故数的40%•坠落伤害:占总事故数的30%•电击伤害:占总事故数的20%•化学伤害:占总事故数的10%可以看出,机械伤害和坠落伤害是发生频率最高的两类工伤事故。
2.2 事故发生地点分析根据事故发生地点的统计结果,我们得出了以下结论:•车间事故:占总事故数的50%•建筑工地事故:占总事故数的30%•办公室事故:占总事故数的20%事故最容易发生的地点是车间,其次是建筑工地,办公室事故相对较少。
2.3 事故造成的伤害程度分析根据伤害程度的统计数据,我们得出了以下结论:•轻伤:占总事故数的50%•重伤:占总事故数的30%•死亡:占总事故数的20%大部分事故造成的是轻伤,但也有一定数量的重伤和死亡事故发生。
3. 原因分析为了找出工伤事故发生的原因,我们对每个事故案例进行了详细的调查和分析。
以下是我们总结出的主要原因:•机械维护不当•安全设施缺失•工人培训不足•操作不规范•管理不到位这些原因在多起事故中都有出现,说明了事故发生的根本原因是管理和操作方面的问题。
4. 预防措施为了避免工伤事故的发生,我们提出了以下预防措施:•加强机械设备的维护保养,确保设备运行正常;•安全设施的完善,包括安全护栏、防护板等;•加强对工人的培训,使其熟悉相关操作规程;•制定并执行严格的操作规范;•强化管理措施,建立健全的安全管理体系。
通过采取以上措施,我们可以有效降低工伤事故的发生概率,并保障劳动者的安全和生命健康。
工伤事故报告范文
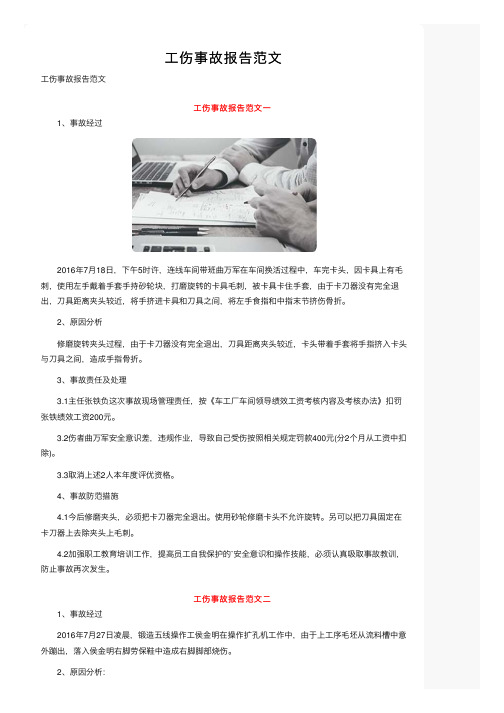
⼯伤事故报告范⽂⼯伤事故报告范⽂ ⼯伤事故报告范⽂⼀、事故经过 1 2、原因分析 修磨旋转夹头过程,由于卡⼑器没有完全退出,⼑具距离夹头较近,卡头带着⼿套将⼿指挤⼊卡头与⼑具之间,造成⼿指⾻折。
3、事故责任及处理 3.1主任张铁负这次事故现场管理责任,按《车⼯⼚车间领导绩效⼯资考核内容及考核办法》扣罚张铁绩效⼯资200元。
3.2伤者曲万军安全意识差,违规作业,导致⾃⼰受伤按照相关规定罚款400元(分2个⽉从⼯资中扣除)。
3.3取消上述2⼈本年度评优资格。
4、事故防范措施 4.1今后修磨夹头,必须把卡⼑器完全退出。
使⽤砂轮修磨卡头不允许旋转。
另可以把⼑具固定在卡⼑器上去除夹头上⽑刺。
4.2加强职⼯教育培训⼯作,提⾼员⼯⾃我保护的`安全意识和操作技能,必须认真吸取事故教训,防⽌事故再次发⽣。
⼯伤事故报告范⽂⼆ 1、事故经过 2016年7⽉27⽇凌晨,锻造五线操作⼯侯⾦明在操作扩孔机⼯作中,由于上⼯序⽑坯从流料槽中意外蹦出,落⼊侯⾦明右脚劳保鞋中造成右脚脚部烧伤。
2、原因分析: 设备存在安全隐患,没有被及时处理,流料槽挡铁过低,上⼯序⽑坯意外从流料槽中蹦出;同时事故⼈员劳保鞋⽆鞋带处于敞开状态,不正确穿戴劳保⽤品,造成热⽑坯掉⼊鞋内,造成脚部灼伤。
3、事故责任及处理 3.1⼚长助理韩⼩五、线长翟战芳负这次事故现场管理责任,按《锻造⼚安全⽂明⽣产考核办法》扣罚韩⼩五、翟占芳绩效⼯资200元。
3.2伤者侯⾦明安全意识差,导致⾃⼰受伤按照相关规定罚款300元。
3.3取消上述3⼈本年度评优资格。
4、事故防范措施 4.1检查各⽣产线流料槽挡铁⾼度,不合格进⾏更换。
4.2加强职⼯教育培训⼯作,提⾼员⼯⾃我保护的安全意识。
正确穿戴好劳保⽤品,每天各线线长班前会对员⼯劳保穿戴进⾏检查。
阅读延伸》》⼯伤事故申报流程 ⼀、当事⼈发⽣⼯伤后,需24⼩时内在⼈⼒资源部进⾏备案,并附⼯伤发⽣情况说明(时间,地点,经过,就医情况,是否有⼈垫付医疗费⽤等信息); ⼆、⼈⼒资源部接到备案后,48⼩时内(节假⽇顺延)向⼯伤部门提交“⼯伤事故登记表”,进⾏备案; 三、当事⼈在发⽣⼯伤后⼀个⽉内,向⼈⼒资源部提交如下相关材料: 1、当事⼈⾝份证复印件; 2、医院病历复印件; 3、夜班排班表(仅上夜班⼈员提交); 4、交通事故认定书、民事赔偿调解书(附各项赔偿明细)上下班路线图、上下班时间表/排班表(仅发⽣交通事故⼈员提交); 四、⼈⼒资源部将相关材料提交⼯伤认定部门,等待社保局⼯伤科审核; 五、⼯伤认定部门通知⼈⼒资源部审核结果,⼈⼒资源部通知当事⼈提交报销医疗费⽤所需如下材料: 1、⼯伤医疗费⽤清单; 2、药费原始凭证、病历; 3、住院、治疗费⽤(总费⽤清单); 4、出院⼩结; 5、内置钢板、钢钉需医院提供的内置材料条形码(仅有此项治疗的当事⼈提交); 六、⼈⼒资源部将材料提交⼯伤部门进⾏费⽤报销审核,等待审核结果; 七、查询费⽤报销审核结果,将报销费⽤通过财务部转⼊当事⼈银⾏账户。
工伤事故分析报告
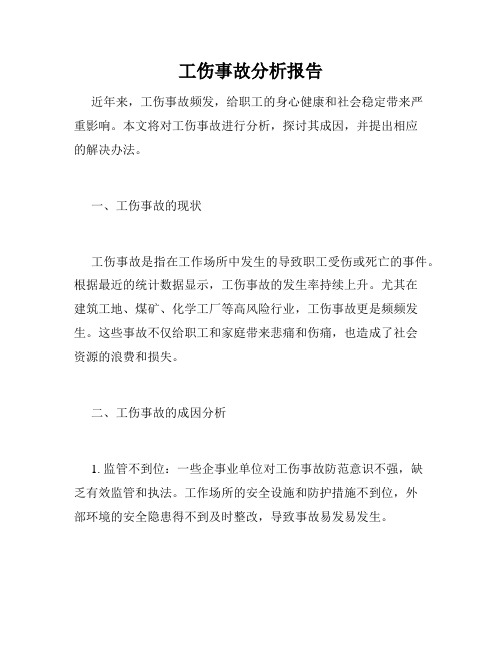
工伤事故分析报告近年来,工伤事故频发,给职工的身心健康和社会稳定带来严重影响。
本文将对工伤事故进行分析,探讨其成因,并提出相应的解决办法。
一、工伤事故的现状工伤事故是指在工作场所中发生的导致职工受伤或死亡的事件。
根据最近的统计数据显示,工伤事故的发生率持续上升。
尤其在建筑工地、煤矿、化学工厂等高风险行业,工伤事故更是频频发生。
这些事故不仅给职工和家庭带来悲痛和伤痛,也造成了社会资源的浪费和损失。
二、工伤事故的成因分析1. 监管不到位:一些企事业单位对工伤事故防范意识不强,缺乏有效监管和执法。
工作场所的安全设施和防护措施不到位,外部环境的安全隐患得不到及时整改,导致事故易发易发生。
2. 职工意识不强:一些职工自身安全意识不足,对于工作中的潜在危险缺乏足够的预防意识。
在工作中违章操作、使用不符合标准的工具设备等行为屡见不鲜,从而增加了工伤事故发生的可能性。
3. 经营利益压力:在以经济利益为导向的公司中,为了追求更高的利润,一些企业会忽视安全生产问题。
他们可能不安排充足的培训、不提供足够的安全设备,进而给职工带来安全隐患。
4. 技术条件滞后:在一些产业中,技术条件过于陈旧,设备维护保养不到位,存在着潜在的安全隐患。
特别是在高风险行业,技术条件滞后可能导致设备故障频发,从而引发工伤事故。
三、工伤事故的解决办法1. 加强监管体系:政府部门应加大对企事业单位的监管力度,确保相关安全法规的落实。
同时,也要建立联合执法机制,加大对违法企业的惩罚力度,形成强有力的监管体系。
2. 提高职工安全意识:企业应加强职工的安全培训和教育,提高职工的安全防范意识。
可以通过定期安全培训、安全知识宣传、事故案例分享等方式,让职工了解工作中的安全风险和如何避免事故的发生。
3. 增加经济补偿:政府应建立健全的工伤保险制度,提高工伤赔偿金标准,为工伤职工提供更有力的保护。
此外,企业也应建立自己的工伤补偿机制,提高职工的安全保障意识。
4. 加强技术创新:在高风险行业中,企业应加大科技研发投入,提升技术条件和设备质量。
年度工伤分析报告模板

年度工伤分析报告模板年度工伤分析报告一、工伤情况概述本年度,共发生XX起工伤事故,造成XX人死亡,XX人重伤,XX人轻伤。
工伤事故整体呈现下降趋势,但仍然存在一定的安全隐患。
二、工伤原因分析1. 人为原因:人为操作不合规范、操作不当、违反工作纪律等是工伤事故的主要原因。
对此,应对员工进行持续的安全教育和培训,强化工作纪律意识,提高员工的安全操作技能。
2. 设备原因:设备故障、维护不当、老化等因素也是工伤事故的重要原因。
对于老化的设备,应及时更换或修理,加强日常维护工作,确保设备的正常运行。
3. 环境原因:工作环境不良,包括通风不好、照明不足、地面湿滑等,也容易引发工伤事故。
对于这些环境问题,应及时进行整改,并制定相关的安全规范,确保员工的工作环境安全。
三、工伤部位分析1. 身体部位:头部、上肢和下肢是工伤事故中最容易受伤的部位。
这些部位的伤害往往会对员工的工作和生活造成较大的影响。
在具体工作中,应加强对这些部位的防护,提高员工的安全防护意识。
2. 内脏部位:内脏器官的损伤也是工伤事故中的重要伤害类型,如头部和胸部的撞击伤、内脏挤压伤等。
对于从事高风险职业的员工,应加强相关防护措施,减少内脏损伤的发生。
四、工伤年龄分析年轻员工是工伤事故的高发群体,其中18-29岁的员工占比最高。
主要原因是缺乏安全意识和工作经验。
针对这一情况,应加强对于年轻员工的安全教育,提高他们的安全防护意识和工作技能。
五、工伤性质分析1. 机械伤:机械设备的操作和维护是造成机械伤事故的主要原因。
要加强对机械设备的安全检查,提高员工的机器操作技能。
2. 高处坠落伤:工人在高空作业时没有正确使用安全带或护栏,或者作业平台没有进行足够的安全保护,容易发生高处坠落事故。
应建立高空作业的具体规范和操作程序,确保员工的安全作业。
六、工伤预防措施1. 加强安全教育培训,提高员工的安全意识和操作技能。
2. 定期检查设备并进行维护,确保设备的正常运行。
工伤事故分析报告5篇

工伤事故分析报告工伤事故分析报告5篇随着个人的文明素养不断提升,报告与我们愈发关系密切,我们在写报告的时候要注意语言要准确、简洁。
写起报告来就毫无头绪?下面是小编精心整理的工伤事故分析报告,欢迎阅读与收藏。
工伤事故分析报告有限公司是牛仔服饰生产知名、核心企业之一,公司成立于20xx年9月,位于中国举世闻名的经济发达地区——长三角地区、江苏省服装名镇——程桥,占地面积达50亩,建设面积8500㎡。
现拥有各类进口、国产设备1600多台,员工人数300多人,其中专业管理人员26人。
自20xx年生产外贸订单以来,目前公司拥有固定资产20xx万元,配有空调服装流水线车间5900㎡。
总公司具备完整的产品研发、生产、洗水和后整理等配套作业能力,并能独立完成酵洗、漂洗、石洗、碧纹洗、套染喷砂、手擦、立体猫须等多种复杂洗水、染色加工工艺,年产量达400万件以上。
公司技术打样中心配有加拿大PAD服装CAD打版排料软件,主要生产牛仔服装、茄克、风衣、晴棉防寒服、童装等十多个系列的服装,年生产能力150万件,产品远销美国、欧洲、日本、韩国和香港等十多个国家和地区,其中80%外销美国,公司与世界服装零售商BeBeJcpenneyPerry EllsKohl′s等建立了良好的合作关系。
公司通过ISO9001质量体系认证,严格执行各项质量标准,贯彻“高标准、零缺陷”的管理要求,并遵循“最快捷、最有效、最彻底”的处理原则,做到客户与工厂的“零距离” 、产品质量“零缺陷” 、企业内外“零抱怨”,也是企业近年来提出的新要求新标准。
随着六合区社会保险的不断推进完善,所显现出的问题更多。
工伤问题涉及面广,社会影响巨大,一旦发生工伤事故,不但用工单位正常的经营生产会受到影响,而且更为重要的是对工伤职工本人及其家庭带来严重后果,造成经济上、精神上的巨大损失。
鉴于工伤问题的严重性,我们特对20xx年的工伤事故情况进行分析,来预防工伤事故的发生,维护工伤者的权益,促进生产经营单位的良好发展。
工伤事故分析报告

工伤事故分析报告工伤事故分析报告根据本公司工伤事故的实际情况,结合相关数据和分析结果,我们为大家报告以下工伤事故的分析结果。
首先,本次工伤事故发生在本公司生产车间。
具体情况为一名员工在操作机器时不慎手指被夹伤,进一步造成严重的手指骨折。
经过调查分析,我们得出以下结论。
首先,事故发生的原因主要是操作员工没有正确按照操作规程进行操作。
在事故发生时,员工没有戴好劳保手套,并且操作过程中没有注意到机器的运行状态。
这种疏忽大大增加了发生事故的概率。
其次,事故的发生也与机器设备本身的安全性有一定的关系。
通过对机器设备的检查发现,这台机器在设计时没有考虑到操作的便捷性以及安全性。
在操作过程中,机器的活动部分没有足够的防护措施,容易造成操作人员的伤害。
另外,我们还发现公司对员工的安全培训存在一定的不足。
操作员在上岗前没有接受足够的培训和教育,缺乏对安全操作的意识和技能。
这种状况直接导致了此次工伤事故的发生。
以此为基础,我们提出以下对策和建议:首先,公司应加强对员工的安全教育和培训,特别是对操作员的培训。
培训内容应包括操作规程的正确实施、戴劳保用品和注意机器运行状态等相关知识和技能。
同时,公司应优化机器设备的安全性能,加强与设备生产厂商的沟通,要求对机器进行改进,增加相关防护措施,减少操作员的伤害风险。
此外,公司还应建立一套完善的安全监控机制,包括加强对设备的定期维护和检查,以及进行安全巡视等措施,确保设备的正常运行和操作员的安全。
最后,公司应制定严格的安全制度和操作规程,并加强对其执行的监督。
同时还应建立健全的事故报告和处理机制,遇到事故时及时采取有效的应对措施,确保事故不再发生或尽可能减少其损失。
通过对本次工伤事故的分析和解决方案的提出,我们相信可以有效地预防类似的事故的发生,保障员工的安全和健康,促进公司的持续发展。
工伤事故分析报告

工伤事故分析报告根据最新数据显示,工伤事故在全球范围内仍然十分普遍,给企业、员工及整个社会带来了巨大的负面影响。
因此,对工伤事故进行全面的分析是非常有必要的。
本文将从事故原因、影响及预防措施等方面对工伤事故进行分析报告。
首先,工伤事故的原因是多方面的。
一方面,人为原因是工伤事故的主要原因之一。
这包括员工的操作不当、安全意识淡漠、违规操作等等。
另一方面,设备设施的缺陷也是工伤事故的重要诱因。
例如,设备老化、维护不及时、设备故障等都可能导致事故的发生。
此外,管理不善也是工伤事故的一个重要原因,例如缺乏完善的安全管理制度、培训不足等。
其次,工伤事故给企业、员工及整个社会带来了巨大的影响。
对企业而言,工伤事故不仅会造成生产中断、设备损失等直接经济损失,更重要的是会损害企业形象和声誉,影响企业的可持续发展。
对员工而言,工伤事故可能导致伤残、失业甚至生命危险,给个人和家庭带来沉重的负担。
对社会而言,工伤事故会增加医疗资源的压力,引发社会不安定因素,降低生活质量和幸福指数。
最后,为了预防工伤事故的发生,需要采取一系列的措施。
首先,建立健全的安全管理制度是必不可少的。
企业应该制定详细的安全规程,明确责任分工,建立安全督导机制,确保每个环节都得到有效监督和控制。
同时,加强员工培训也非常重要。
通过培训能够提高员工的安全意识,掌握正确的操作方法,提高应对突发事件的能力。
此外,加强设备设施的维护和检修,确保其正常运行,避免因设备故障导致的事故发生。
此外,加强监督检查和隐患排查,及时发现问题并采取措施进行整改。
综上所述,工伤事故分析报告总结了工伤事故的原因、影响及预防措施。
通过汲取事故教训,加强企业内部安全管理和员工培训,采取有效的安全措施,可以降低工伤事故的发生率,保障员工的安全和生命健康,推动企业和社会的可持续发展。
工伤事故分析报告范文
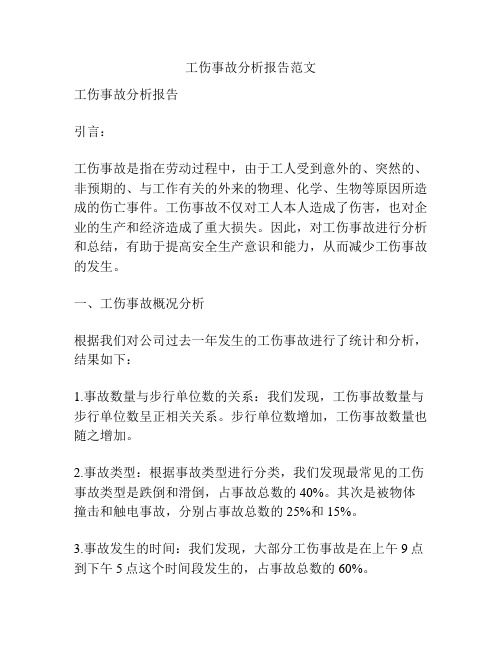
工伤事故分析报告范文工伤事故分析报告引言:工伤事故是指在劳动过程中,由于工人受到意外的、突然的、非预期的、与工作有关的外来的物理、化学、生物等原因所造成的伤亡事件。
工伤事故不仅对工人本人造成了伤害,也对企业的生产和经济造成了重大损失。
因此,对工伤事故进行分析和总结,有助于提高安全生产意识和能力,从而减少工伤事故的发生。
一、工伤事故概况分析根据我们对公司过去一年发生的工伤事故进行了统计和分析,结果如下:1.事故数量与步行单位数的关系:我们发现,工伤事故数量与步行单位数呈正相关关系。
步行单位数增加,工伤事故数量也随之增加。
2.事故类型:根据事故类型进行分类,我们发现最常见的工伤事故类型是跌倒和滑倒,占事故总数的40%。
其次是被物体撞击和触电事故,分别占事故总数的25%和15%。
3.事故发生的时间:我们发现,大部分工伤事故是在上午9点到下午5点这个时间段发生的,占事故总数的60%。
4.事故人员性别和年龄分布:根据受伤员工的性别和年龄进行统计,我们发现男性员工比女性员工更容易发生工伤事故,占工伤总数的70%。
另外,在年龄方面,25岁以下的员工发生工伤事故的概率较高,占工伤总数的50%。
二、工伤事故发生原因分析经过对工伤事故的调查和统计,我们总结出以下几个主要原因:1.缺乏安全意识:部分员工对安全意识的重要性认识不足,对工作中存在的安全隐患忽视或忽略,导致工伤事故的发生。
2.工作强度过大:部分员工的工作强度过大,长时间工作导致疲劳,从而增加了工伤事故发生的概率。
3.管理不到位:公司在安全管理方面存在一定的不足,未能及时发现和解决潜在的安全隐患,导致工伤事故的发生。
4.技能不足:部分员工技术水平不够,不具备相应的安全操作技能,容易发生工伤事故。
三、工伤事故预防对策根据以上的工伤事故分析,我们针对不同的原因提出以下预防对策:1.加强安全教育:通过组织安全教育培训,提高员工的安全意识和安全操作技能,从根本上预防工伤事故的发生。
工伤事故分析报告
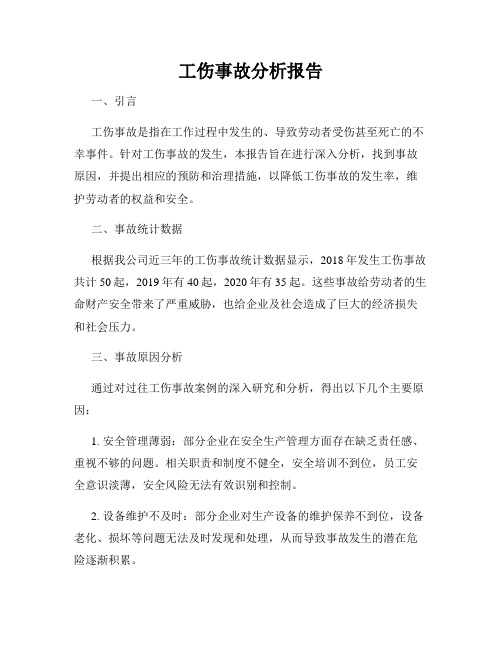
工伤事故分析报告一、引言工伤事故是指在工作过程中发生的、导致劳动者受伤甚至死亡的不幸事件。
针对工伤事故的发生,本报告旨在进行深入分析,找到事故原因,并提出相应的预防和治理措施,以降低工伤事故的发生率,维护劳动者的权益和安全。
二、事故统计数据根据我公司近三年的工伤事故统计数据显示,2018年发生工伤事故共计50起,2019年有40起,2020年有35起。
这些事故给劳动者的生命财产安全带来了严重威胁,也给企业及社会造成了巨大的经济损失和社会压力。
三、事故原因分析通过对过往工伤事故案例的深入研究和分析,得出以下几个主要原因:1. 安全管理薄弱:部分企业在安全生产管理方面存在缺乏责任感、重视不够的问题。
相关职责和制度不健全,安全培训不到位,员工安全意识淡薄,安全风险无法有效识别和控制。
2. 设备维护不及时:部分企业对生产设备的维护保养不到位,设备老化、损坏等问题无法及时发现和处理,从而导致事故发生的潜在危险逐渐积累。
3. 作业规程不规范:一些企业在作业规程制定方面存在不足,工人操作不规范,防护措施不到位,从而容易发生安全事故。
4. 监督执法不严格:相关监管部门在工伤事故的预防和治理方面缺乏有效监督和严格执法,导致企业对安全生产的重视程度不高。
四、预防和治理措施为了降低工伤事故的发生率,提高劳动者的安全保障和企业的经济效益,我们提出以下预防和治理措施:1. 健全安全生产管理体系:建立和完善相关的安全管理体系,明确相关职责和制度,加强对员工的安全培训,提高员工的安全意识。
2. 加强设备维护保养:定期对生产设备进行检查和维护,确保设备安全可靠,预防潜在的事故隐患。
3. 规范作业流程和防护要求:制定规范的作业规程和防护要求,加强对员工的规范操作培训,确保作业过程安全可控。
4. 强化监督执法:相关监管部门要加大对企业的监督执法力度,严肃查处违法违规行为,提高企业对安全生产的重视性。
五、结论与展望通过对工伤事故的分析和预防措施的提出,相信能够有效减少工伤事故的发生,降低劳动者的伤亡风险,促进企业的可持续发展。
我院工伤事故原因分析及预防措施
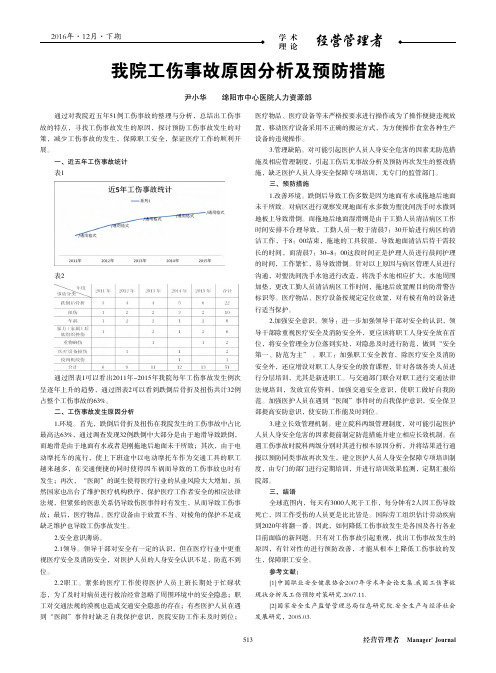
通过图表1可以看出2011年-2015年我院每年工伤事故发生例次 呈逐年上升的趋势,通过图表2可以看到跌倒后骨折及扭伤共计32例 占整个工伤事故的63%。
二、工伤事故发生原因分析 1.环境。首先,跌倒后骨折及扭伤在我院发生的工伤事故中占比 最高达63%,通过调查发现32例跌倒中大部分是由于地滑导致跌倒, 而地滑是由于地面有水或者是刚拖地后地面未干所致;其次,由于电 动摩托车的流行,使上下班途中以电动摩托车作为交通工具的职工 越来越多,在交通便捷的同时使得因车祸而导致的工伤事故也时有 发生;再次,“医闹”的诞生使得医疗行业的从业风险大大增加,虽 然国家也出台了维护医疗机构秩序,保护医疗工作者安全的相应法律 法规,但紧张的医患关系仍导致伤医事件时有发生,从而导致工伤事 故;最后,医疗物品、医疗设备由于放置不当、对棱角的保护不足或 缺乏维护也导致工伤事故发生。 2.安全意识薄弱。 2.1领导。领导干部对安全有一定的认识,但在医疗行业中更重 视医疗安全及消防安全,对医护人员的人身安全认识不足,防范不到 位。 2.2职工。紧张的医疗工作使得医护人员上班长期处于忙碌状 态,为了及时对病员进行救治经常忽略了周围环境中的安全隐患;职 工对交通法规的漠视也造成交通安全隐患的存在;有些医护人员在遇 到“医闹”事件时缺乏自我保护意识,医院安防工作未及时到位;
513
经营管理者 Manager' Journal
三、预防措施 1.改善环境。跌倒后导致工伤多数是因为地面有水或拖地后地面 未干所致。对病区进行观察发现地面有水多数为盥洗间洗手时水撒到 地板上导致滑倒。而拖地后地面湿滑则是由于工勤人员清洁病区工作 时间安排不合理导致,工勤人员一般于清晨7:30开始进行病区的清 洁工作,于8:00结束,拖地的工具较湿,导致地面清洁后待干需较 长的时间,而清晨7:30-8:00这段时间正是护理人员进行晨间护理 的时间,工作繁忙,易导致滑倒。针对以上原因与病区管理人员进行 沟通,对盥洗间洗手水池进行改造,将洗手水池相应扩大,水池周围 加垫,更改工勤人员清洁病区工作时间,拖地后放置醒目的防滑警告 标识等。医疗物品、医疗设备按规定定位放置,对有棱有角的设备进 行适当保护。 2.加强安全意识。领导:进一步加强领导干部对安全的认识,领 导干部除重视医疗安全及消防安全外,更应该将职工人身安全放在首 位,将安全管理全方位落到实处,对隐患及时进行防范,做到“安全 第一、防范为主” 。职工:加强职工安全教育,除医疗安全及消防 安全外,还应增设对职工人身安全的教育课程,针对各级各类人员进 行分层培训,尤其是新进职工。与交通部门联合对职工进行交通法律 法规培训,发放宣传资料,加强交通安全意识,使职工做好自我防 范。加强医护人员在遇到“医闹”事件时的自我保护意识,安全保卫 部提高安防意识,使安防工作能及时到位。 3.建立长效管理机制。建立院科两级管理制度,对可能引起医护 人员人身安全危害的因素提前制定防范措施并建立相应长效机制。在 遇工伤事故时院科两级分别对其进行根本原因分析,并将结果进行通 报以预防同类事故再次发生,建立医护人员人身安全保障专项培训制 度,由专门的部门进行定期培训,并进行培训效果监测,定期汇报给 院部。 三、结语 全球范围内,每天有3000人死于工作,每分钟有2人因工伤导致 死亡,因工作受伤的人员更是比比皆是。国际劳工组织估计劳动疾病 到2020年将翻一番。因此,如何降低工伤事故发生是各国及各行各业 目前面临的新问题。只有对工伤事故引起重视,找出工伤事故发生的 原因,有针对性的进行预防改善,才能从根本上降低工伤事故的发 生,保障职工安全。 参考文献: [1]中国职业安全健康协会2007年学术年会论文集.我国工伤事故 现状分析及工伤预防对策研究.2007.11. [2]国家安全生产监督管理总局信息研究院.安全生产与经济社会 发展研究,2005.03.
工伤事故分析报告

工伤事故分析报告工伤事故是指在工作中突发的不幸,意外或伤害事件,这些事件会给员工的身体和心理健康带来危害, 甚至会危及员工的生命安全。
近年来,中国本着人民安全第一的原则,加强了工伤保险制度,建立了完整的社会救济体系,同时各个企业也都在积极开展工伤事故的分析,从而来探究事故的原因,进一步完善企业的安全管理制度。
本文将对工伤事故分析报告的意义、分析方法及实施效果进行探讨,以期在工作场所保障员工安全方面提供一定的参考值和指导。
一、意义工伤事故分析报告的意义在于分析事故发生的原因,并作出科学合理可行的决策和措施,以推动工作场所安全生产的持续改进。
具体来说,它的主要作用如下:1. 发现安全管理方面存在的问题分析报告能够揭示一些常规的和潜在的问题,如员工教育培训、劳动保护、设备安全、安全文化建设等方面的缺陷。
在发现问题后,企业可以有针对性的进行整改,避免同类问题重演。
2. 推进行动作的改进分析报告可以为企业提供有力的改进意见,为管理者制定相关安全计划提供科学合理的指导,提高管理者意识,对相关制度的制定起到优胜劣汰的作用,让工作场所更加安全。
3. 避免类似事件反复发生对于一个工伤事故,要想取得有价值的分析结果,必须把教训总结起来,从而保障员工的安全,减少同类事故的发生。
安全管理工作是一个长期不断反复的过程,如果异类事件屡次发生,将极大地增加企业工作环境的不稳定性,分析报告能帮助企业对治理进行更加科学的规划和实施。
4. 推动整个行业的安全管理一个企业所发生的工伤事故往往会影响到整个行业,通过分析报告的发布,可以将其他同行业企业当做其他业态进行对比,推动行业整体安全水平的提高,使大众在选择工作时更具有判断力。
二、分析方法分析工伤事故的方法有多种,其中比较有效的有鱼骨图法、因果分析法、树状图法等。
以下是分别阐述它们的分析原理和不同之处:1. 鱼骨图法鱼骨图法是一种辅助思考的工具,它通过对事故所涉及的不同环节展开分析,最终以图形化的方式形成“鱼骨图(也称为“鱼骨图”)”。
工伤事故深思报告范文
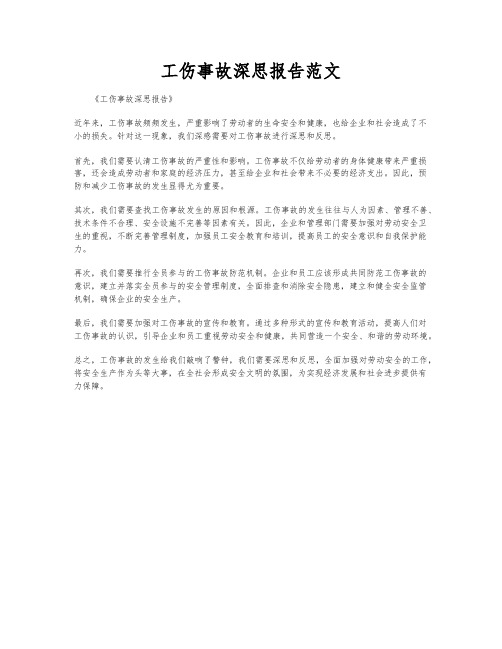
工伤事故深思报告范文
《工伤事故深思报告》
近年来,工伤事故频频发生,严重影响了劳动者的生命安全和健康,也给企业和社会造成了不小的损失。
针对这一现象,我们深感需要对工伤事故进行深思和反思。
首先,我们需要认清工伤事故的严重性和影响。
工伤事故不仅给劳动者的身体健康带来严重损害,还会造成劳动者和家庭的经济压力,甚至给企业和社会带来不必要的经济支出。
因此,预防和减少工伤事故的发生显得尤为重要。
其次,我们需要查找工伤事故发生的原因和根源。
工伤事故的发生往往与人为因素、管理不善、技术条件不合理、安全设施不完善等因素有关。
因此,企业和管理部门需要加强对劳动安全卫生的重视,不断完善管理制度,加强员工安全教育和培训,提高员工的安全意识和自我保护能力。
再次,我们需要推行全员参与的工伤事故防范机制。
企业和员工应该形成共同防范工伤事故的意识,建立并落实全员参与的安全管理制度,全面排查和消除安全隐患,建立和健全安全监管机制,确保企业的安全生产。
最后,我们需要加强对工伤事故的宣传和教育。
通过多种形式的宣传和教育活动,提高人们对工伤事故的认识,引导企业和员工重视劳动安全和健康,共同营造一个安全、和谐的劳动环境。
总之,工伤事故的发生给我们敲响了警钟,我们需要深思和反思,全面加强对劳动安全的工作,将安全生产作为头等大事,在全社会形成安全文明的氛围,为实现经济发展和社会进步提供有力保障。
工伤事故报告(1)

7.所有车间生产人员必须按要求穿戴劳保防护用品。
二 原因分析
J
1.为什么会压到手指? 实习生安全意识淡薄,缺乏识别岗位安全风险隐患的。 2.为什么识别安全隐患能力淡薄? 新进员工入职后未做安全培训,上岗前也未做岗位技能与设备安全操 作等相关培训 3.为什么没有及时培训? 由于生产任务紧张,该班组老员工全部被安排到夜班生产,实习大学 生则由班长带领进行白班生产,操作前班长仅进行了口头方面的安全培训, 但是没有考虑到安全光栅在手动状态下失效的因素。 4.为什么安全光栅在手动状态下失效? 该设备在手动状态下,安全光栅模块与设备动作模块脱节,只有在自 动状态下才能起到保护作用,而发生事故时左侧油缸属于手动状态,导致 安全光栅失效。
2.新进员工岗前培训考核:
设备安全操作指导-----生产制造部 岗位质量培训------生产制造部/质量部 岗位技能培训------生产制造部 3.转岗员工: 按照4M变更要求进行登记培训-----生产制造部 4.设备科定期对车间所有设备进行机/电等安全部位的巡检。
5.不定期对员工进行岗位安全操作抽查,以确保每位员工对岗位操作的 安全点熟知并遵守。
2016年3月12日上午10:30左右,武汉汽 车学院实习生田家平在机加车间 F10后桥 压衬套岗位进行作业时,设备油温过高, 停机后在未启动油压的前提下装配衬套, 按启动按钮时机器未动作,怀疑是衬套安 装不到位,在没有按紧急开关下私自伸左 手检查衬套安装位置,然后看到液压开关 未开,就用右手打开,机器启动时,左手 未及时拿开,导致左手食指和中指被压伤 发生安全事故,压伤的严重程度见图。
J
宁 波 建 新 底 盘 系 统 有 限 公 司 Ningbo Jianxin Chassis System Co., Ltd
工伤事故分析报告

工伤事故分析报告
近年来,随着工业化和城市化的快速发展,工伤事故已成为威
胁职工身体健康和生命安全的重要问题。
针对这一问题,我着手
进行了一份工伤事故分析报告。
首先,我们看到的是,工伤事故往往集中发生在建筑工地、工
厂和矿山等重工业场所。
这些场所常常存在重物运输、高处作业、机械操作等高危环节,一旦操作不当便可能导致严重事故。
其次,我们分析了事故的原因。
一般来说,事故的发生可以归
纳为三个方面:一是操作人员过度疲劳或不熟悉操作流程;二是
安全设备保养不善或缺少安全设备;三是管理不当,监管不严格。
这些问题导致职工的生命和安全遭到威胁。
当然,针对工伤事故应该采取措施。
在预防方面,企业应该加
强操作人员的培训和指导,提高职工的安全意识,加强安全设备
的维护和保养。
同时,企业的管理也应该更加严格,加大对职工
的安全培训,严格落实安全作业制度,加强设备的检查和维护。
在事故发生后,需要及时进行救援,做好应急处理工作。
同时,企业也要负起事故的责任,积极处理受伤职工的问题,并尽一切
可能避免再次发生类似的事故。
总之,工伤事故的发生不只是企业问题,更是社会问题。
在短
时间内,我们能做的是采取切实可行的措施,预防和减少工伤事
故发生的可能性。
在长期,我们应该加强对安全管理方面的研究
和探讨,为提升职工身体健康和生命安全保驾护航。
公司工伤年度分析报告

公司工伤年度分析报告公司工伤年度分析报告随着工业化进程的加速推进,公司工伤现象也逐渐增多。
为了更好地了解和控制工伤问题,我们对公司去年的工伤情况进行了详细的年度分析。
一、工伤总体情况在过去的一年里,我们公司共发生工伤事故50起,其中轻伤40起,重伤6起,死亡4起。
与上一年度相比,工伤事故总数有所增加,特别是死亡事故的发生率有较大程度的上升。
二、工伤原因分析根据对每起工伤事故的调查和分析,我们总结出以下几个主要的工伤原因:1. 安全管理不到位。
部分员工对安全意识的培养不足,存在随意操作、违规操作的情况。
同时,公司的安全管理制度也存在不完善之处,对于员工的安全教育和培训工作还需进一步加强。
2. 设备老化或故障。
有些工作场所的设备存在存在老化、损坏等问题,对员工的安全构成了一定的威胁。
加之维修保养工作不及时,导致设备故障的风险进一步增加。
3. 劳动强度过大。
在一些工作环境中,工人们承受着较大的体力和精神压力,劳动强度过大容易导致工伤事故的发生。
三、防范措施建议为了减少工伤事故的发生,我们提出以下防范措施建议:1. 加强员工安全培训。
通过定期开展培训,提高员工的安全意识和操作技能,使其能够正确使用设备和遵守安全规章制度。
2. 完善安全管理制度。
加强对各个环节的安全管理,明确责任和权限,并建立健全应急机制,及时处置紧急情况。
3. 配备充足的安全设备。
提供合适的个人防护装备,确保员工在工作中的安全。
4. 定期维护和检修设备。
加强对设备的维护保养工作,定期进行检修,确保设备的安全运行。
5. 减轻劳动强度。
合理安排工作任务和工作时间,适当休息和调整员工的体力和精神状态,降低因劳累引起的工伤事故的发生。
通过以上的措施,相信公司的工伤问题会得到一定的改善和控制。
同时,我们也应该认识到预防工伤是一个持续不断的工作,需要全体员工的共同努力和积极配合。
只有通过不断地总结经验教训,及时调整和优化安全管理措施,才能确保员工的生命安全和身体健康。
工伤分析报告

工伤分析报告引言工伤是指在工作过程中,因工作原因导致身体受伤的情况。
工伤的发生对于劳动者和雇主都会带来一定的损失。
为了减少工伤的发生和提高工作环境安全性,需要进行详细的工伤分析。
本报告将对某公司在过去一年内发生的工伤进行分析,总结其原因和教训,为未来的工作安全提供参考。
数据收集和方法为了分析工伤的情况,我们收集了过去一年内发生的工伤报告,并分析了每一起工伤事故的原因、受伤部位、工种和工龄等相关信息。
同时,我们也参考了相关法律法规和行业标准,以确保对工伤情况的分析准确和全面。
工伤分析结果根据我们的分析,过去一年内共发生了50起工伤事故。
下面是我们对工伤情况的具体分析:工伤事故的原因我们对50起工伤事故进行了原因分析,发现以下几个主要原因:1.不当操作:30%的工伤事故是由于不当操作导致的。
这表明员工在操作机器、设备或工具时,缺乏必要的培训和指导,或者疏忽大意导致事故的发生。
2.不安全的工作环境:20%的工伤事故是由于工作环境不安全导致的。
例如,工作区域没有明确的安全标志和防护设备,缺乏紧急疏散通道等。
3.设备故障:15%的工伤事故是由于设备故障导致的。
这表明公司需要更加重视设备的维护和保养工作,以确保员工的工作安全。
4.人为因素:10%的工伤事故是由于员工的人为因素导致的,例如疲劳、缺乏专注等。
这表明公司需要加强员工的安全意识培训,提高员工对工作安全的重视。
工伤部位和严重程度我们对50起工伤事故的受伤部位和严重程度进行了统计。
以下是我们的分析结果:1.上肢受伤最多:34%的工伤事故中,受伤部位为上肢。
这表明在工作过程中,上肢的受伤风险相对较高。
2.严重程度较轻:大部分的工伤事故(70%)是属于轻度受伤,只有少数(10%)属于重度受伤。
这说明大部分的工伤事故虽然给员工带来了一定的伤害,但没有威胁到生命安全。
工种和工龄对工伤的影响我们还对不同工种和不同工龄员工的工伤情况进行了分析。
以下是我们的研究结果:1.工种的影响:我们发现,在某些工种中,工伤的风险更高。
- 1、下载文档前请自行甄别文档内容的完整性,平台不提供额外的编辑、内容补充、找答案等附加服务。
- 2、"仅部分预览"的文档,不可在线预览部分如存在完整性等问题,可反馈申请退款(可完整预览的文档不适用该条件!)。
- 3、如文档侵犯您的权益,请联系客服反馈,我们会尽快为您处理(人工客服工作时间:9:00-18:30)。
关于2015年至2016年工伤事故分析报告
一.工伤事故总体情况
2015年公司进行了组织架构调整、经营战略规划调整,同比生产能力比2014年没有很大的提高,为了扩大生产改善管理,2015年7月份导入精益生产管理,2016年进行人员精简整编,2016年11月起公司扩大生产规模,同年引进了少量成型半自动输送系统。
设备得到改善,但是工伤事故也频繁发生,小伤频繁发生,较大十级以上工伤事件也有发生,2016年在全体职工的共同努力改善下,工伤事故发生率得到了有效的控制。
数据报告分析具体如下:全厂现在职职工最高峰时700多人, 2015年工伤28起,总费用支出93232.47元,2016年截止11月工伤发生数6起,费用支出:36852.24元(其中包括2015年工伤未结案的二次理疗费用)。
二.工伤事故发生的部门、月份、受伤部位等情况
表1:2015年工伤事故部门分布发生比率
费用:
表2:2015年-2016年工伤事故发生月份统计表表3: 2015年-2016年工伤事故受伤部位统计表
三、工伤事故原因分析
根据我公司所发生的工伤事故,发生工伤事故的原因多种多样,受伤部位80%在手指部位,但综合起来不外乎是人的不安全因素,物的不安全状态,管理缺陷,员工安全意识不足等方面,具体体现如下:
1、人的因素
一、2015年/2016年发生的工伤,主要人为操作不当导致,作业现场操作方法没有形成标准化,员工未按规范操作等原因导致事故发生;
二、个别管理人员缺乏安全意识,对安全工作重视不足。
将工作重心放在了产品生产上,对日常安全生产工作重视度不够。
对员工安全知识的培训宣导、岗前操作教育培训没有做到位,存在应付检查现象。
三、员工技能素质不强,防范技能欠缺。
一是员工专业技能不强,对生产工艺、机械设备性能、劳动防护用品认识不够,员工为图省事,有的直接不用;加上技术不够娴熟,容易发生事故。
2、物的因素
一是小部分设备缺乏安全防护设施。
类似管件车间有小部分机械设备无防护,无警示牌是造成事故的一个重要方面。
部分受控气动设备没有做防呆装置,也是导致事故发生的部分原因。
3、管理因素
新员工上岗前缺少必要的技能和安全生产知识培训。
当前员工流动性很大,加上招工困难,公司一招到工人,不管熟练与否,只通过了行政部岗前安全基本知识培训,新手直接上岗,生产车间内并未及时做岗位安全培训,引发事故。
四、对策及措施
1.要加强安全生产培训,提高员工安全生产能力。
要求各部门及车间建立健全岗前培训制度,对新员工及换岗员工开展有关技能、安全防范以及紧急避险的岗前培训。
对在岗职工有针对性地分工种、分岗位进行全员培训,切实提高员工劳动技能和安全生产意识。
2.建立健全规章制度,强化作业现场管理。
公司要严格建立和完善科学合理的安全生产制度和操作规则,使员工有章可循。
同时要加大安全检查力度,将突击检查与全面检查相结合,要对公司的每一个生产环节进行定期巡查,发现问题立即进行整改,杜绝安全生产隐患。
同时加强对员工的日常管理,对违反、违规操作、操作失误的现象要予以批评教育,确保员工有章必循。
3.落实安全责任,建立绩效考核机制。
安全生产要层层落实责任,明确安全责任制度,对发生安全事故的,要追究是责任事故或非责任事故,直接落实本部门车间管理负责人的责任。
4.启动多能工技能看板,实现目视化管理,确实落实实施新员工上岗前的技能教育培训,减少不必要的意外伤害损失。
2017年“0”工伤事故目标。
奖励奖金《》?
行政部人力资源课
2016年11月17日
附件: 2015年-2016年工
伤事故分析报告.xlsx
工伤事故报告(进
行中)(2).xlsx。