烧结过程的理论基础
烧结生产知识

烧结生产知识一、铁矿石烧结知识(原料条件)1、天然矿粉与烧结1)天然矿粉包括富矿粉和贫矿粉,其中天然矿粉含铁量在45%以上的通常称为富矿粉,含铁量低于45%的通常称为贫矿粉。
45%这个界限随着冶炼技术的发展是会变化的。
2)铁矿粉烧结是重要的造块技术之一。
由于开采时产生大量的铁矿粉,特别是贫铁矿富选促进了铁精矿粉的生产发展,使铁矿粉烧结成为规模最大的造块作业。
烧结矿比天然矿石有许多优点,如含铁量高、气孔率大、易还原、有害杂质少、含碱性熔剂等。
2、铁矿石分类:按照铁矿物不同的存在形态,分为磁铁矿、赤铁矿、褐铁矿、菱铁矿四大类。
1)磁铁矿:磁铁矿化学式为Fe3O4,也可以视为Fe2O3与FeO的固溶体。
比密度为4.9--5.2t/m3,硬度为5.5--6.5,难还原和破碎,有金属光泽,具有磁性。
其理论含铁量为72.4%。
磁铁矿晶体为八面体,组织结构较致密坚硬,一般成块状和粒状,表面颜色由钢灰色到黑色,条痕均是黑色,俗称青矿。
2)赤铁矿:赤铁矿俗称“红矿”,化学式为Fe2O3,其矿物成份是不含结晶水的三氧化二铁,密度为4.8—5.3,硬度不一,结晶完整的赤铁矿硬度为5.5—6.0,理论含铁量70%。
赤铁矿由非常致密的结晶组织到很分散的粒状,结晶的赤铁矿外表颜色为钢灰色和铁黑色,其它为暗红色,但条痕均为暗红色。
3)褐铁矿:褐铁矿石(mFe2O3. nH2O)是一种含结晶水的Fe2O3,按结晶水含量不同,褐铁矿分为五种,其中以2Fe2O3. 3H2O形式存在的较多。
4)菱铁矿:菱铁矿石的化学式为FeCO3,理论含铁量为48.2%。
自然界中常见的是坚硬致密的菱铁矿,外表颜色为灰色和黄褐色,风化后变为深褐色,条痕为灰色或带黄色,由玻璃光泽。
菱铁矿的比重为3.8吨/米3,无磁性。
3、铁矿粉分类:1)精矿粉:也称选粉。
是天然矿石经过破碎、磨碎、选矿等加工处理,除去一部分脉石和杂质,使含铁量提高后的极细的矿粉叫精矿粉。
烧结理论基础知识考试题A卷

烧结理论基础知识考试题A卷(满分150分)姓名: 得分:一, 推断题(正确记“√”, 错误记“×”)每题2分, 共20分1, 若倒数第二个风箱的废气温度低于倒数第一个风箱的废气温度说明烧结“终点”滞后(√)。
2, 烧结的点火强度低, 可通过延长点火时间或加大煤气流量来提高(√)3, 当料层厚度及抽风量肯定时, 真空度愈高, 则料层透气性愈好。
(×)4, 煤气爆炸主要是由于空气和煤气形式爆炸的混合气体, 同时混合气体达到必要的温度(着火点)或遇上明火造成, 二者缺一不可(√)5, 氧化亚铁是低价铁, 还原性能好, 因此烧结矿中FeO越高, 还原性越好(×)6, 点火后料面呈清黑色, 并有金属光泽局部熔融为最好(×)7, 配料计算将返矿视为常数, 计算时不考虑返矿这是传统的配料计算方法。
(√)8, 当电子秤不准, 电子秤实际配比及微机给定配比不符, 生产上常将不准的电子秤的配比加大或缩小, 来保证电子秤下料量及微机给定的下料量相符, 这种方法临时应急是可行的(√)9, 磁铁矿的主要化合物是四氧化三铁Fe3O4。
(√)10, 赤铁矿的主要化合物是Fe2O3, 3H2O(×)1、二, 填空题。
每空1分, 共30分2、严格限制烧结三点温度, 即点火温度, (终点温度), (总管废气温度)4、在运行混合料抽风烧结的过程中, 沿整个料层高度将呈现出性质不同的五个带为(烧结矿带), (燃料燃烧带), (预热带), (干燥带), (过湿带)5、配料室五勤一准操操作内容是: (勤检查), (勤联系), (勤分析推断)(勤计算调整), (勤总结沟通), 一准为: (配料精确)6、返矿加水的目的是降低返矿的(温度), 稳定混合料水粉, 以利于造球。
7、网目数是指在(1英寸或2.54cm)筛网上的筛孔数, 这是英国泰勒标准筛的表示方法;8、烧结生产工艺流程大体可分为八个部分, 受料系统, 原料打算系统, (配料系统), (混合制粒系统), (烧结系统)抽风系统, (成品处理系统), 除尘系统9、烧结厂用燃料粒度一般标准是≤3mm的部分大于(80)%为合格。
粉末冶金原理-黄培云烧结这章思考题及答案详解

烧结这章思考题1.烧结理论研究的两个基本问题是什么?为什么说粉体表面自由能降低是烧结体系自由能降低的主要来源或部分?答:研究的两个基本问题:①烧结为什么会发生?也就是烧结驱动力或热力学的问题。
②烧结是怎样进行的?烧结的机构和动力学问题。
原因:首先体系自由能的降低包含表面自由能的降低和晶格畸变能的降低。
因为理论上,烧结后的低能位状态至多是对应单晶体的平衡缺陷浓度,而实际上烧结体总是具有更多热平衡缺陷的多晶体,因此烧结过程中晶格畸变能减少的绝对值,相对于表面能的降低仍然是次要的。
2.粉末等温烧结的三个阶段是怎样划分的?实际烧结过程还包括哪些现象?答:①粘结阶段:颗粒间接触再通过成核,结晶长大等形成烧结颈。
特点:颗粒内晶粒不发生变化,颗粒外形也基本未变,烧结体不收缩,密度增加极微,强度和导电性有明显增加(因颗粒结合面增大)②烧结颈长大阶段:烧结颈长大,颗粒间形成连续空隙网络。
晶粒长大使晶界扫过的地方空隙大量消失。
特点:烧结体收缩,密度和强度增加。
③闭孔隙球化和缩小阶段:闭孔量大增,孔隙球化并缩小。
特点:烧结体缓慢收缩(但主要靠小孔消失和孔隙数量的减少来实现),持续时间可以很长,仍会残留少量隔离小孔隙。
还有可能出现的现象:①粉末表面气体或水分的蒸发。
②氧化物的还原的离解。
③颗粒内应力的消除。
④金属的回复和再结晶以及聚晶长大等。
3.用机械力表示烧结驱动力的表达式是怎样?式中的负号代表什么含义?简述空位扩散驱动力公式推导的基本思路和原理。
答:①机械力表示的烧结驱动力表达式:。
(参考书上模型):作用在烧结颈上的应力。
:表面张力。
:曲率半径。
式中负号表示作用在曲颈面上的应力是张力,方向朝颈外。
②空位扩散驱动力公式推导思路:2ov v c c kT热力学本质:在烧结颈上产生的张应力减小了烧结球内空位生成能。
(意味空位在张力作用下更容易生成。
)具体推导公式见书。
过剩空位浓度:由于空位生成能的减小,烧结颈处比烧结体内更容易生成大量空位,由此产生了空位浓度差,即过剩空位浓度(梯度)v c 。
烧结机工作原理

烧结机工作原理引言概述:烧结机是一种用于冶金和材料加工的设备,广泛应用于钢铁、有色金属和陶瓷等行业。
它通过将粉末材料加热至高温并施加压力,使粉末颗粒结合成坚固的块状物体。
本文将详细介绍烧结机的工作原理。
一、加热系统1.1 加热元件:烧结机通常采用电加热元件,如电阻丝或者电加热器。
这些元件通过电流通入产生热量,将工作室内的温度提升至所需的烧结温度。
1.2 温度控制:烧结过程中,温度控制是非常重要的。
烧结机通常配备温度传感器和控制系统,以监测和维持工作室内的温度在一个稳定的范围内。
1.3 加热方式:烧结机可以采用不同的加热方式,包括辐射加热、对流加热和传导加热。
具体选择哪种加热方式取决于烧结材料的性质和加热效果的要求。
二、压力系统2.1 压力源:烧结机通常配备一个压力源,如液压系统或者气动系统。
这些系统通过施加压力,使粉末颗粒在加热的同时密切结合。
2.2 压力控制:烧结过程中,压力的控制也非常重要。
烧结机通常配备压力传感器和控制系统,以监测和调节施加在粉末颗粒上的压力。
2.3 压力传递:烧结机通过压力传递装置,将压力从压力源传递到工作室内的烧结模具上。
这些传递装置通常包括液压缸、气动缸或者机械传动装置。
三、烧结模具3.1 模具设计:烧结模具是用于容纳和成型粉末颗粒的关键部件。
模具的设计应考虑到烧结材料的形状和尺寸要求,以及烧结过程中的温度和压力条件。
3.2 模具材料:烧结模具通常采用高温合金钢或者陶瓷材料制成,以确保其在高温和高压环境下的稳定性和耐磨性。
3.3 模具创造:烧结模具的创造通常采用数控加工技术,以确保模具的精度和表面质量。
同时,还需要进行热处理和表面处理,以提高模具的使用寿命和耐磨性。
四、烧结过程4.1 烧结温度:烧结温度是烧结过程中的一个重要参数,它决定了粉末颗粒的烧结程度和物理性质。
不同的烧结材料和应用领域有不同的烧结温度要求。
4.2 烧结时间:烧结时间是指粉末颗粒在高温和高压环境下保持一定时间,以使颗粒之间的结合更加坚固。
烧结工艺理论知识(全面)

第一章烧结生产概述§1-1 烧结生产在冶金工业中的地位一、简述烧结工艺的产生和发展烧结方法在冶金生产中的应用,起初是为了处理矿山、冶金、化工厂的废气物(如富矿粉、高炉炉尘、扎钢皮、炉渣等)以便回收利用。
随着钢铁工业的快速发展,矿石的开采量和矿粉的生成量亦大大增加。
据统计,每生产1t生铁需1.7~1.9t铁矿石,若是贫矿,需要的铁矿石则更多。
另外,由于长期的开采和消耗,能直接用来冶炼的富矿愈来愈少,人们不得不大量开采贫矿(含铁25%~30%)。
但贫矿直接入炉冶炼是很不经济的,所以必须经过选矿处理。
选矿后的精矿粉,在含铁品位上是提高了,但其粒度不符合高炉冶炼要求。
因此,对开采出来的粉矿(0~8mm)和精矿粉都必须经过造块后方可用于冶炼。
我国铁矿资源丰富,但贫矿较多,约占80%以上,因此,冶炼前大都需经破碎、筛分、选矿和造块等处理过程。
烧结生产的历史已有一个多世纪。
它起源于资本主义发展较早的英国、瑞典和德国。
大约在1870年前后,这些国家就开始使用烧结锅。
我国在1949年以前,鞍山虽建有10台烧结机,总面积330m2,但工艺设备落后,生产能力很低,最高年产量仅几十万吨。
我国铁矿石烧结领域取得的成就,概括起来包括以下几个方面:(1)烧结工艺:自1978年马钢冷烧技术攻关成功后,一批重点企业和地方骨干企业基本完成了热烧改冷烧工艺。
部分企业建成原料混匀料场,并投入使用,绝大多数钢铁企业实现了自动化配料、混合机强化制粒、偏析布料、冷却筛分、整粒及铺底料技术。
(2)新工艺、新技术开发和应用:如高碱度烧结矿技术、小球烧结技术、低温烧结技术、低硅烧结技术等,在钢铁企业得到推广应用,并取得了显著的效益。
(3)设备大型化和自动化:20世纪50年代,我国最大烧结机75m2,60年代130 m2,80年代265m2,90年代宝钢二、三期和武钢等450m2烧结机相继投产,这些都是我国自行设计、自行制造,并实现自动化生产的。
小球烧结技术---小球烧结法的理论基础

立志当早,存高远小球烧结技术---小球烧结法的理论基础小球烧结法就是将烧结混合料制成小球,以提高烧结料层的透气性,实现厚料层及低温烧结的方法。
小球烧结法一般要求混合料中粒度不小于3mm 的小球占混合料总量的75%以上。
该方法所制得烧结矿胶结相主要以针状和柱状铁酸钙为主,烧结矿强度高、还原性好、粉末少、块度大。
早在20 世纪60 年代,我国就进行了小球烧结法的研究,鞍钢开发了适合红矿烧结的双球烧结工艺,但因工艺难度较大,一直未能实现工业化生产。
80 年代,日本成功地开发了部分小球烧结法,于1987 年在福山4 号烧结机上投产,各项主要烧结技术指标都明显优于普通烧结法。
在国内外研究的基础上,钢铁研究总院开发成功了小球烧结新工艺,然后和有关单位合作,于1994~1996 年,小球烧结法在泰山钢铁公司烧结厂和首钢矿山公司烧结厂进行工业化生产获得成功,结束了我国小球烧结工艺只停留在试验研究阶段的历史,这是我国几代烧结工作者努力奋斗的结果。
目前,小球烧结法已在我国钢铁企业得到广泛推广和应用,取得了显著的经济效益。
小球烧结法可以大幅度地提高烧结矿产量,改善烧结矿质量,降低烧结燃料消耗,其理论根据分析如下:烧结机的产量可用下式计算:Q=60KRBHV (1) 式中Q———产量,t/h; K———成品率,%;R———混合料松散密度,t/m3;B———烧结机宽度,m;H———料层高度,m;V———烧结机机速,m/min。
式1 中H 用垂直烧结速度表示时,则:C=H/t 因:C=H/(L/V) 则:CL=HV (2) 式中C———垂直烧结速度,m/min; t———烧结时间,min,t=L/V;K———烧结机长度,m。
将式2代入式1:Q=60KRBCL (3) 在式3 中,烧结机的宽度B 和长度L 为不变量,成品率K、烧结料松散密度R 和垂直烧结速度C 为变量。
可见,采取措施提高成品率K、混合料松散密度R 和垂直烧结速度C 是烧结机增产的关键,现对这。
烧结过程的基本理论
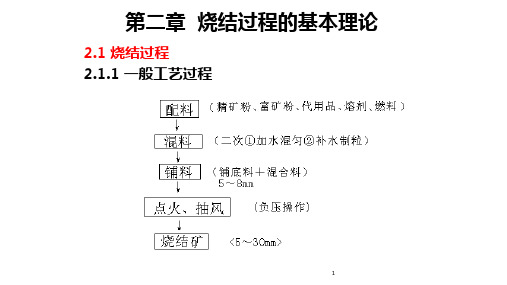
高温区厚度计算(即燃烧带大小的计算)可采用C.T.布拉塔可 夫及B.U.杜卡什提出的新方法,其计算公式如下(烧结料内 燃料与惰性料组成并两者不发生化学反应):
24
上式表明:燃烧带的宽度是由燃料粒度直径、 气流速度、原始气体中氧的浓度、料层透气性及 系数b来决定的。
计算结果与实验室测定结果很接近,但由于计 算式的假定条件与实际生产条件有差别,计算结 果与实际的误差值不超过30%~40%。
11
2.2 燃料的燃烧与热交换
• 烧结过程中,固体燃料燃烧所获得的高温和CO气体,为液相 生成和一切物理化学反应的进行,提供了所必需的热量和气 氛条件。
2.2.1 燃烧反应的一般规律 • 所谓燃烧反应就是在着火温度下,燃料中的可燃成分被激烈
氧化的过程,并放出大量热量。 • 烧结生产所用的固体燃料焦粉和无烟煤燃烧的一般原理如下:
因此,烧结过程可在较短时间内完成,当料层小于 300 mm时,烧结时间一般为12~16 min。
19
二、高温区的温度水平和厚度
注意区分烧结料层与烧结矿层
20
二、高温区的温度水平和厚度 理解出发点:在烧结过程中,燃烧层从原料表面逐渐向原料内部移动
高温区温度水平对烧结矿的影响: ✓ 高温区温度↑→生成液相多→烧结矿的强度↑; ✓ 温度过高→出现过熔现象,烧结料层的透气性↓( ? ),气流阻力↑,
21
图2-3是烧结料层高温区热平衡示意图,从中我们可以看 出下列平衡关系。
22
影响高温区温度水平及厚度的因素:
(1)配碳量:配C量↑→QT↑→燃烧层的温度水平↑,厚度↑ (2)燃料的粒度:粒度↓→比表面积↑→与空气接触条件↑→燃烧速度
↑→温度水平高、厚度小 (3)固体燃料的燃烧性能:
粉末冶金原理第七章

7.2
烧结过程的热力学基础
7.2.1 烧结的基本过程 7.2.2 烧结的热力学问题 7.2.3 烧结驱动力的计算
7.2
烧结过程的热力学基础
图7-1
烧结球之间形成烧结颈的扫描 电子显微照片
7.2.1 烧结的基本过程
(1)黏结阶段 烧结初期,颗粒间的原始接触点或面转变成 晶体结合,即通过成核、结晶长大等原子过程形成烧结颈。 (2)烧结颈长大阶段 原子向颗粒结合面大量迁移,使烧结 颈扩大,颗粒间的距离缩小,形成连续的孔隙网络;同时由 于晶粒长大,晶界越过孔隙移动,而被晶界扫过的地方,孔 隙大量消失。 (3)闭孔隙球化和缩小阶段 当烧结体密度达到90%以后, 多数孔隙被完全分隔,闭孔数量增加,孔隙形状趋近球形并 不断缩小。
7.2.1 烧结的基本过程
图7-2 球形颗粒的烧结模型 a)烧结前颗粒的原始接触 b)烧结早期的烧结颈长大 c)、d)烧结后期的孔隙球 化
7.2.2 烧结的热力学问题
1)由于颗粒结合面(烧结颈)的增大和颗粒表面的平直化,粉 末体的总比表面积和总表面自由能减小。 2)烧结体内孔隙总体积和总表面积减小。 3)粉末颗粒内晶格畸变逐渐消除。
7.2.3 烧结驱动力的计算
图7-3
烧结颈模型
7.2.3 烧结驱动力的计算
图7-4
两球模型
7.2.3 烧结驱动力的计算
图7-6 颈部直径为X的两球形 颗粒的烧结剖视图
7.2.3 烧结驱动力的计算
图7-7
不同温度下烧结时间对烧结颈大小、表面积减小率、 收缩率和致密化的影响
7.3
烧结理论与物质迁移
图7-38 烧结过程接触面和孔隙形状、尺寸的变化模型
7.3.5 烧结末期
图7-26 烧结时间与孔隙率、孔径、晶粒之间的关系。
无机材料科学基础《烧结》知识点

(1)常压烧结:又称无压烧结。
属于在大气压条件下坯体自由烧结的过程。
在无外加动力下材料开始烧结,温度一般达到材料的熔点0.5-0.8即可。
在此温度下固相烧结能引起足够原子扩散,液相烧结可促使液相形成或由化学反应产生液相促进扩散和粘滞流动的发生。
常压烧结中准确制定烧成曲线至关重要。
合适的升温制度方能保证制品减少开裂与结构缺陷现象,提高成品率。
(2)热压烧结与热等静压烧结:热压烧结指在烧成过程中施加一定的压力(在10~40MPa),促使材料加速流动、重排与致密化。
采用热压烧结方法一般比常压烧结温度低100ºC左右,主要根据不同制品及有无液相生成而异。
热压烧结采用预成型或将粉料直接装在模内,工艺方法较简单。
该烧结法制品密度高,理论密度可达99%,制品性能优良。
不过此烧结法不易生产形状复杂制品,烧结生产规模较小,成本高。
作为陶瓷烧结手段,利用来自于表面能的表面应力而达到致密化的常压烧结法虽是一般常用的方法,但是,不依赖于表面应力,而在高温下借助于外压的方法,也是可以采用的。
这就是称为热压法的烧结方法。
广义来说,在加压下进行烧结的方法包括所有这类方法,超高压烧结和热等静压(HIP)烧结也属于这类方法。
不过,一般都作为在高温下施加单轴压力进行烧结的方法来理解。
其基本结构示于图1。
首先,制备粉体试料,置于模型中,在规定温度下加热、加压,获得烧结体。
由于下述原因而采用这种方法:(1)烧结温度降低;(2)烧结速度提高;(3)使难烧结物质达到致密化。
因为能够在颗粒成长或重新结晶不大可能进行的温度范围达到致密化,所以,可获得由微小晶粒构成的高强度、高密度烧结体。
图2所示,是热压对陶瓷致密化影响效果之一例。
将热压作为制造制品的手段而加以利用的实例有:氧化铝、铁氧体、碳化硼、氮化硼等工程陶瓷。
连续热压烧结生产效率高,但设备与模具费用较高,又不利于过高过厚制品的烧制。
热等静压烧结可克服上述弊缺,适合形状复杂制品生产。
烧结过程的理论基础

烧结过程的理论基础烧结就是将矿粉、熔剂和燃料,按一定比例进行配加,均匀的混合,借助燃料燃烧产生的高温,部分原料熔化或软化,发生一系列物理、化学反应,并形成一定量的液相,在冷却时相互粘结成块的过程。
一、烧结过程的基本原理近代烧结生产是一种抽风烧结过程,将矿粉、燃料、熔剂等配以适量的水分,铺在烧结机的炉篦上,点火后用一定负压抽风,使烧结过程自上而下进行。
通过大量的实验对正在烧结过程的台车进行断面分析,发现沿料层高度由上向下有五个带,分别为烧结矿带、燃烧带、预热带、干燥带和过湿带。
当前国内外广泛采用带式抽风烧结,代表性的生产工艺流程如图3—1所示。
1、烧结五带的特征(1)烧结矿带在点燃后的烧结料中燃料燃烧放出大量热量的作用下,混合料熔融成液相,随着高负压抽风作用和燃烧层的下移,导致冷空气从烧结矿带通过,物料温度逐渐降低,熔融的液相被冷却凝固成网孔状的固体,这就是烧结矿带。
此带主要反应是液相凝结、矿物析晶、预热空气,此带表层强度较差,一般是返矿的主要来源。
(2)燃烧带该带温度可达1350~1600度,此处混合料软化、熔融及液相生成,发生异常复杂的物理化学变化。
该层厚度为15~50mm 。
此高炉灰轧钢皮 (10~0mm ) 碎焦无烟煤 (25~0mm ) 石灰石白云石 (80~0mm ) 精矿富矿粉 (10~0mm )空气排出废气(热烧结矿)冷烧结矿图3—1 烧结生产一般工艺流程图带对烧结产量及质量影响很大。
该带过宽会影响料层透气性,导致产量低。
该带过窄,烧结温度低,液相量不足,烧结矿粘结不好,导致烧结矿强度低。
燃烧带宽窄主要受物料特性、燃料粒度及抽风量的影响。
(3)预热带该带主要使下部料层加热到燃料的着火温度。
一般温度为400~800度。
该带主要反应是烧结料中的结晶水及部分碳酸盐、硫酸盐分解,磁铁矿进行还原以及组分间的固相反应等。
(4)干燥带烧结料的热废气从预热带进入下层,迅速将烧结料加热到100℃以上,因此该带主要是水分的激烈蒸发。
第一章 硫化矿焙烧与烧结

黑龙江某矿 51.34 0.88 32.53 11.48 0.12 0.02 0.04 0.02 0.50 85
在火法炼Sb时,首先使Sb2S3矿石或精矿中的锑全部氧化挥 发为适合于用碳还原的Sb2O3 (俗称锑氧),然后把收尘设备中收 集到的锑氧用碳还原得到金属锑。
用相同的氧化挥发焙烧处理HgS矿石生产金属汞更简单,焙 烧过程将HgS分解氧化为金属汞和SO2,汞蒸气随炉气逸出,在 冷凝系统内冷凝成液态金属汞。
硫化锌精矿的粒度细小,95%以上小于 40μm。堆密度为1.7~2g/cm3。在选用精矿 氧化焙烧脱硫设备时,应当充分利用精矿粒 度小、比表面大、活性高以及硫化物本身也 是一种“燃料”的特点。
实用文档
1.3.2 锌精矿流态化焙烧的生产实践
硫化精矿的流态化焙烧是强化的冶金过程,氧化反应剧烈进 行并放出大量热,可以维持炉内锌精矿焙烧的正常温度 900~1100 ℃。由于精矿粒子被气流强烈搅动而在炉内不停地翻 动,整个炉内各部分的物理化学反应是比较均一的,从而可以保 持炉内各部的温度很均匀,温差只有10℃左右。而且可以设置活 动的冷却水管,当温度上升时,随时将其插入流态化床以调节温 度。所以采用流态化焙烧可以严格控制焙烧温度。
1.2.1 ZnS氧化的热力学 硫化锌精矿焙烧过程实质上是硫化物的氧化过程,参与
焙烧反应的主要元素是Zn、S和O,当处理含铁较高的精矿时, Fe也是参与反应的主要元素,即讨论的主要问题是Zn-S-O系 与Zn-Fe-S-O系的热力学性质。 1)硫化锌氧化生成氧化锌
烧结过程的理论基础
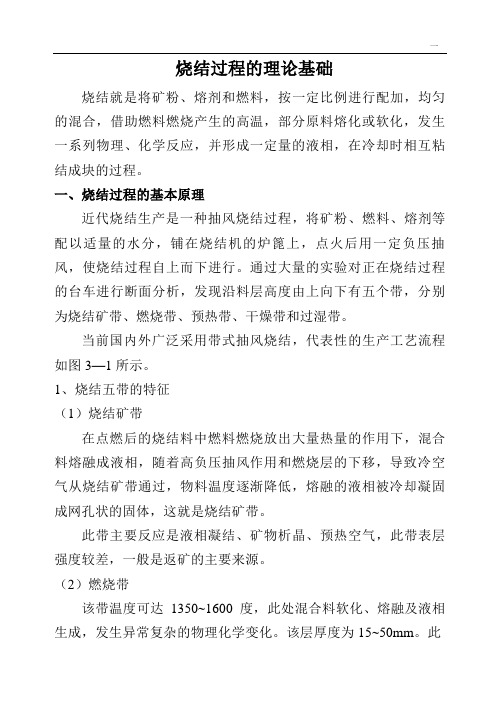
烧结过程的理论基础烧结就是将矿粉、熔剂和燃料,按一定比例进行配加,均匀的混合,借助燃料燃烧产生的高温,部分原料熔化或软化,发生一系列物理、化学反应,并形成一定量的液相,在冷却时相互粘结成块的过程。
一、烧结过程的基本原理近代烧结生产是一种抽风烧结过程,将矿粉、燃料、熔剂等配以适量的水分,铺在烧结机的炉篦上,点火后用一定负压抽风,使烧结过程自上而下进行。
通过大量的实验对正在烧结过程的台车进行断面分析,发现沿料层高度由上向下有五个带,分别为烧结矿带、燃烧带、预热带、干燥带和过湿带。
当前国内外广泛采用带式抽风烧结,代表性的生产工艺流程如图3—1所示。
1、烧结五带的特征(1)烧结矿带在点燃后的烧结料中燃料燃烧放出大量热量的作用下,混合料熔融成液相,随着高负压抽风作用和燃烧层的下移,导致冷空气从烧结矿带通过,物料温度逐渐降低,熔融的液相被冷却凝固成网孔状的固体,这就是烧结矿带。
此带主要反应是液相凝结、矿物析晶、预热空气,此带表层强度较差,一般是返矿的主要来源。
(2)燃烧带该带温度可达1350~1600度,此处混合料软化、熔融及液相生成,发生异常复杂的物理化学变化。
该层厚度为15~50mm。
此图3—1 烧结生产一般工艺流程图高炉灰轧钢皮 (10~0mm ) 碎焦无烟煤 (25~0mm ) 石灰石白云石 (80~0mm ) 精矿富矿粉 (10~0mm )带对烧结产量及质量影响很大。
该带过宽会影响料层透气性,导致产量低。
该带过窄,烧结温度低,液相量不足,烧结矿粘结不好,导致烧结矿强度低。
燃烧带宽窄主要受物料特性、燃料粒度及抽风量的影响。
(3)预热带该带主要使下部料层加热到燃料的着火温度。
一般温度为400~800度。
该带主要反应是烧结料中的结晶水及部分碳酸盐、硫酸盐分解,磁铁矿进行还原以及组分间的固相反应等。
(4)干燥带烧结料的热废气从预热带进入下层,迅速将烧结料加热到100℃以上,因此该带主要是水分的激烈蒸发。
(5)过湿带从烧结料点火开始,物料中的水分就开始转移到气流中去。
粉末冶金原理-烧结解析

按烧结过程有无液相出现
固相烧结:
单元系固相烧结:单相(纯金属、化合物、固溶体)粉末 的烧结:烧结过程无化学反应、无新相形成、无物质聚集 状态的改变。 多元系固相烧结:
烧结的机构和动力学问题
§3-2 烧结过程的热力学基础
一、烧结的基本过程
原始接触 孔隙球化
烧结颈长大
粉末等温烧结过程的三个阶段
等温烧结过程按时间大致可分为三个界限不十分明显的阶段: 1.粘结阶段 烧结初期,颗粒间的原始接触点或面转变成晶体结合,
烧结过程的驱动力
烧结热力学,即解决Why的问题
物质迁移方式Leabharlann 烧结动力学—烧结机构,即解决How的问题, 即物质迁移方式和迁移速度
上述理论在典型烧结体系中的应用
研究方法:
烧结几何学 烧结物理学
烧结化学
计算机模拟
烧结模型:两球模型、球-板模型
物质迁移机构:扩散、流动
组元间的反应(溶解、形成化合物) 及与气氛间的反应
但可能高于次要组分的熔点: WC-Co合金, W-Cu-Ni合金
(二) 烧结的重要性
1)粉末冶金生产中不可缺少的基本工序之一
(磁粉芯和粘结磁性材料例外)
烧 结 的
2)对PM制品的性能有决定的影响(烧结废品很难补救, 如铁基部件的脱渗碳和严重的烧结变形)
重 要 性
3)烧结消耗是构成粉末冶金产品成本的重要组成部分 (设备、高温、长时间、保护气氛)。
借助于建立物理、几何或化学模型, 进行烧结过程的计算机模拟(蒙特-卡 洛模拟)
烧结过程的理论基础

烧结过程的理论基础烧结是一种通过高温和压力将细粉状材料压制成成型体的加工方法。
在烧结过程中,粉末颗粒之间发生了部分熔融、扩散、结合和收缩现象,最终形成了密实的、具有一定机械强度和结构稳定性的成型体。
烧结过程的理论基础主要涉及燃烧理论、传热理论、材料科学等方面的知识。
1.燃烧理论烧结过程中常用的燃烧方式包括气相燃烧、固相燃烧和液相燃烧。
在燃烧过程中,燃料与氧化剂反应产生高温高能的燃烧产物,为烧结提供了必要的热能。
燃烧产物的温度越高,烧结过程中的热传递效果越好,有利于颗粒间的结合和收缩。
2.传热理论热传递是烧结过程中的一个重要环节。
热传递可以通过传导、对流和辐射等方式进行。
传导是指热量通过颗粒之间或颗粒内部的分子振动和传递,对于高温下的烧结过程尤为重要。
对流是指在气体或液体中,通过流体的对流传导热量,对于烧结中的气体流动和温度分布具有重要影响。
辐射是指物体表面的热能以电磁波的形式辐射出去,对于高温烧结具有显著效果。
3.材料科学烧结过程中,粉末颗粒之间的结合主要是通过扩散和熔融发生的。
扩散是指原子或分子在固体中由高浓度区向低浓度区传递的过程,是粉末颗粒烧结过程中结合的主要方式。
熔融是指粉末颗粒在高温下部分熔化,形成液相,通过液相的黏结作用形成连续的成型体。
材料科学中的物理化学性质、晶体学、材料力学等知识对于理解和控制烧结过程中的结合机制和力学性能具有重要意义。
总之,烧结过程的理论基础涉及燃烧理论、传热理论和材料科学等多个方面的知识。
这些理论和原理的深入研究和应用,可以帮助理解烧结过程中颗粒的结合机制、热传递现象以及成型体的力学性能,为烧结工艺和材料应用提供理论指导。
烧结的常识

烧结工艺的原理
• 烧结过程的理论基础是用物理化学(热力学、动 力学)的基本原理研究烧结过程中固体燃料的燃 烧、水分的蒸发与冷凝、含铁原料及熔剂的分解、 氧化及还原规律。 • 用传热学的基本原理来研究烧结过程热量传 输规律、料层中温度分布规律及蓄热现象; • 用流体力学的基本原理研究烧结过程气体运 动规律、分析料层的透气性及对工艺参数影响; • 用物理化学及结晶矿物学研究烧结过程的固 相反应、液相生成与冷凝、烧结矿成矿机理及结 构特性。
• 烧结对熔剂的质量要求总的要求是:有效成分高,酸性物质和S、P 等有害杂质少,粒度和水分合适。 • 碱性熔剂:含有CaO和MgO等碱性物质的熔剂。 • 种类: 石灰石:CaCO3 • 生石灰:CaO • 消石灰:Ca(OH)2 • 白云石:[Ca.Mg(CO3)2] • 菱镁石:MgCO3 • 轻烧白云石和菱镁石酸性熔剂:含有效成分SiO 2、 高的熔 剂 • 橄榄石:(Mg.Fe)2.SiO2 • 蛇纹石:3MgO.2SiO 2.2H2O • 石英: SiO2
烧结的发展史
• 1897年T· Hunting Ton申请了硫化铅矿培烧专利,采用烧 结锅用于生产。 • 1905年E· Savelsberg首次将烧结锅用于铁矿粉烧结。 J· • 1909年S· Penbach首次出现连续式烧结机用于铅矿石。 • 1911年D· Lloyd首次出现抽风连续带式烧结机用于铁矿 L· 粉烧结,这种D-L型烧结机也是百年后现代烧结的雏形。 • 我国建国初期,仅有首钢烧结锅,本钢烧结盘以及 鞍钢的50m2带式烧结机。 • 1952年从前苏联引进面积最大的75m2烧结机。 • 80年代宝钢引进日本450m2烧结机。 • 90年代我国已能自行设计和制造大型烧结机。
大型烧结机的特点
材料科学基础14章烧结

者之差可以由下式描述:
3 C Co RT
式中:ΔC为颗粒内部与表面的空位差;γ为表面能;δ3空 位体积;ρ曲率半径;Co为平表面的空位浓度。 这一浓度差导致内部质点向表面扩散,推动质点迁移,可
以加速烧结。
五.烧结过程的动力学描述方法
a.坯体收缩率或颈部变化:dv/dt,ΔV/V, 颈部半径x/原始粒径r; b.气孔率和吸水率: dPc/dt; c.体积密度与理论密度之比θ:θ=烧结体 体积密度/真密度,dθ/dt。
§14– 2 固态烧结
固态烧结完全是固体颗粒之间的高温固结过程,没有 液相参与。固态烧结的主要传质方式有:蒸发一凝聚、扩散
传质和塑性流变。
一.蒸发-凝聚传质(推动力为蒸气压差Δ P) 1.传质条件:a.粉体在高温下有较 大的蒸气压;b.凸凹面压差大ΔP↑ (要求颗粒小) ;c.有足够高的温度。 2.传质机理:由于颗粒表面(凸面 蒸气压比颈部(凹面)蒸气压高, 故质点从表面蒸发通过气相传递凝聚到颈部,而使颈部逐 渐被填充。这种传质过程仅仅在高温下蒸气压较大的系统 内进行,如氧化铅、氧化铍和氧化铁的烧结。
3.液相烧结模型
a.金格尔(Kingery)液相烧结模型:在液相量较 少时,溶解-沉淀传质过程发生在晶粒接触界面 处溶解,通过液相传递扩散到球型晶粒自由表面 上沉积。 b. LSW模型:当坯体内有大量液相而且晶粒大 小不等时,由于晶粒间曲率差导致使小晶粒溶解, 通过液相传质到大晶粒上沉积。
液相烧结根据液相量及液相性质可分为两类 情况:a.固-液不润湿,液相数量为0.01mol%-0.5mol%,烧结模型为双球型,传质方式以扩散 为主;b.固-液润湿,液相数量多,传质方式为溶 解-沉淀。
6 2 r 5t 5
材料科学基础2-第三章-烧结过程
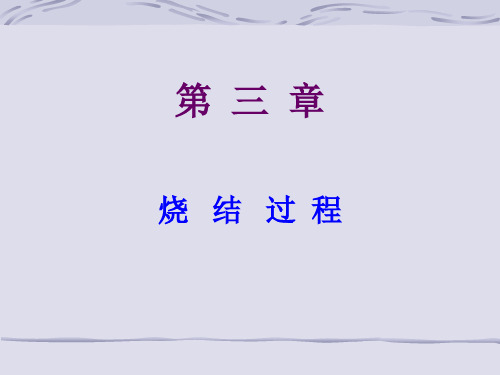
通常可将烧结过程分成几步:
a.烧结前颗粒堆积:颗粒间彼此以点接触,有的相 互分开,有较多的空隙。
ab. T,t,产生颗粒间键合和重排,粒子相互 靠拢,a中的大孔隙逐渐消失,气孔总体积迅速减少, 但颗粒间仍以点接触为主,总表面积没有缩小
bc.有明显的传质过程,由点接触逐渐扩大为面接 触,粒界增加,固-气表面积相应减少,但空隙仍连 通。
➢无液相参与的烧结,即只在单纯固相颗粒之间进 行的烧结称为固相烧结
➢有部分液相参与的烧结称为液相烧结 ➢通过蒸发-凝聚机理进行传质的烧结称为气相烧结
3. 根据烧结体系的组元多少分类: ➢烧结可分为单组元系统烧结、二组元系统烧结和多 组元系统烧结。单组元系统烧结在烧结理论的研究中 非常有用。而实际的粉末材料烧结大都是二组元系统 或多组元系统的烧结。
❖在烧结过程中,坯体内部发生一系列物理变化过程:
(i)颗粒间首先在接触部分开始相互作用,颗粒接触 界面逐渐扩大并形成晶界(有效粘结,Bonding)
(ii)同时气孔形状逐渐发生变化、由连通气孔变成孤 立气孔并伴随体积的缩小,气孔率逐渐减少
(iii)发生数个晶粒相互结合,产生再结晶和晶粒长 大等现象
第三章
烧 结 过程
❖一种或多种固体(金属、氧化物、氮化物、 粘土等)粉末经压制成为坯体,坯体中含有大 量气孔,颗粒之间的接触面积较小,强度较低。
❖烧结---将坯体加热到一定温度后,坯体中颗 粒开始相互作用,气孔逐渐收缩,气孔率逐渐 减少,颗粒接触界面逐渐扩大为晶界,最后数 个晶粒相互结合,产生再结晶和晶粒长大,坯 体在低于熔点温度下变成致密,坚硬的烧结体
烧结过程有两个共性的基本特征:一是需要高温加热,第二是 烧结的目的是为了使粉体致密,产生相当强的机械强度
烧结理论基础备

1、烧结原理概述烧结是目前国内外钢铁企业最广泛采用的铁原产造块方法。
现在各烧结厂使用的烧结机几乎都是下部抽风的带式烧结机。
据此,烧结过程可以概括为:将烧结混合料配以适量的水分,经混匀及制粒后铺到烧结机的台车上,烧结料表面点火,在下部风箱强制抽风作用下,料层内燃烧自上而下燃烧并放热,混合料在高温作用下发生一系列物理、化学变化,最终固结成烧结矿。
对烧结过程的解剖研究,抽风烧结过程有明显的分层性。
一般自上而下分为五层:烧结矿带、燃烧带、预热干燥带、水分冷凝带及原始料带。
烧结点火后,五带依次出现,随时间的推移,各层向下移动,最后各层又依次消失,最后剩下的全部是烧结矿层。
烧结矿带又称成矿带,在烧结矿层中,空气被预热,烧结矿被冷却,表面和裂缝处出现氧化现象。
在同燃烧层接近处所生成的液相温度降低冷凝并结晶,使烧结料固结,形成烧结矿。
在燃烧带内,燃料被上部加热的空气氧化燃烧,放出热量,使烧结料加热,温度升高(一般可达1100~1500℃)。
从燃料开始着火(焦粉着火温度一般为700℃)到燃烧完毕需要一定时间,燃烧带有一定厚度(15~80mm)。
在燃烧带内进行着软熔、还原、氧化以及石灰石和硫化物分解等反应。
此带对烧结过程产量及质量影响很大。
该带过宽则料层透气性差,导致产量低,过窄则烧结温度低,液相量不足,烧结矿粘结不好,强度低。
该带的宽窄受燃烧粒度、抽风量等因素影响。
在干燥预热层中发生水分蒸发,并从燃烧带出来的高温废气中吸收热量,使燃料加热到着火温度。
此层内还会出现固相反应、氧化还原反应以及结晶水分解等。
此带特点是热交换迅速,由于热交换剧烈,废气温度很快从1000℃下降到60~70℃。
水分冷凝带又称过湿带,因上层下来的废气中含有大量水汽,由于废气温度降低到与之相应的露点以下,水汽重新凝结于混合中,产生过湿现象。
水分冷凝破坏已造好的混合料小球,使料层透气性变差。
原始料带处于料层最下部。
在此带中物料的物理、化学性质基本不变。
- 1、下载文档前请自行甄别文档内容的完整性,平台不提供额外的编辑、内容补充、找答案等附加服务。
- 2、"仅部分预览"的文档,不可在线预览部分如存在完整性等问题,可反馈申请退款(可完整预览的文档不适用该条件!)。
- 3、如文档侵犯您的权益,请联系客服反馈,我们会尽快为您处理(人工客服工作时间:9:00-18:30)。
烧结过程的Байду номын сангаас论基础
烧结就是将矿粉、熔剂和燃料,按一定比例进行配加,均匀的混合,借助燃料燃烧产生的高温,部分原料熔化或软化,发生一系列物理、化学反应,并形成一定量的液相,在冷却时相互粘结成块的过程。
一、烧结过程的基本原理
近代烧结生产是一种抽风烧结过程,将矿粉、燃料、熔剂等配以适量的水分,铺在烧结机的炉篦上,点火后用一定负压抽风,使烧结过程自上而下进行。通过大量的实验对正在烧结过程的台车进行断面分析,发现沿料层高度由上向下有五个带,分别为烧结矿带、燃烧带、预热带、干燥带和过湿带。
该带严重影响了烧结料的透气性,破坏已造好混合料小球,最好的解决办法就是预热混合料。
图3—2烧结过程各层反应示意图
2、烧结过程分层原因
带式烧结机有明显的分层性,如图3—2所示。抽风烧结过程的这种分层性,是烧结过程自上而下进行的特点所决定的。烧结料中的燃料点燃之后,随抽入的空气继续燃烧,于是料层的表面形成了燃烧层,当这一层的燃料燃烧完毕后,下部料层中的燃料继续燃烧,于是燃烧层向下移动,而其上部形成了烧结矿层。燃烧层产生的高温废气进入燃烧层以下的料层之后,很快将热量传递给烧结料,使料温急剧上升。随着温度的升高,到100℃以上,首先出现混合料中的水分蒸发,达到300~400℃,水分蒸发完毕,继续升高到800℃,混合料中的燃料着火。这样,燃烧层下部形成了100~400℃之间以水分蒸发为主的干燥层和400~800℃之间的预热层。实际上,干燥层和预热层之间没有明显的界限,因此,也有统称为干燥—预热层的。高温废气将热量传递给混合料使之干燥和预热之后,进入干燥层以下的料层,当温度下降到水蒸气的露点(大约60℃)以下时,在干燥层中蒸发进入废气的水分在这里重新凝结,形成了过湿层。随着烧结过程的进行,燃烧层、预热层和干燥层逐渐下移,烧结矿层逐渐扩大,湿料层逐渐减小,最后全部烧结料变为烧结矿层。
燃烧层是烧结料层中温度最高的区域,因此也称高温区。高温区温度水平和厚度对烧结过程的影响非常显著。
首先,高温区移动速度,即垂直燃烧速度,是决定烧结矿产量的主要因素。产量同垂直烧结速度成正比关系,而垂直烧结速度和风速成0.77~1.05次方的关系。因此,增加风速即可提高垂直烧结速度,提高产量。但垂直烧结速度也不能过快,过快会引起烧结矿强度下降,成品率低。混合料的热容量大,导热性好,粒度小,以及吸热反应发展,都能增加混合料从废气中吸热的能力,从而使烧结速度减小,降低烧结矿产量。而适当增加混合料的水分和溶剂用量时,由于改善了烧结料层的透气性,有利于提高烧结速度。
3、烧结料层中发生的物理化学变化及其对烧结生产的影响
烧结矿层在料层的最上部,抽入的空气首先要穿过烧结矿层,而烧结矿层中已无燃料的燃烧,所以被抽入的空气所冷却,发生熔融矿物的结晶和新相的形成过程,并将自身的热量传递给空气,使空气温度升高(称为自动蓄热作用)。由于气流作用和来不及逸出的气泡及冷却时的体积收缩,熔融物冷却后成为多孔状块矿,使料层透气性增加,负压降低。在与空气接触的烧结矿表面层,还可能发生低价氧化物的再氧化反应。
燃烧层主要是固体燃料的燃烧,引起料层温度的升高和液相的生成。燃烧层的温度高达1350~1600℃,超过了烧结料的软化和熔化温度,为产生一定数量的液相使烧结料粘结成块创造了条件。此外,燃烧层内还发生碳酸盐和硫酸盐的分解,磁铁矿的氧化、赤铁矿的热分解以及在固体燃料颗粒的周围高价氧化物的还原等反应。由于燃烧层内存在大量液相粘结物,气体通过料层的阻力增加,透气性变坏,不利于提高产量,因此,生产中要求燃烧层的厚度不要太大,一般在15~50mm之间。
当前国内外广泛采用带式抽风烧结,代表性的生产工艺流程如图3—1所示。
1、烧结五带的特征
(1)烧结矿带
在点燃后的烧结料中燃料燃烧放出大量热量的作用下,混合料熔融成液相,随着高负压抽风作用和燃烧层的下移,导致冷空气从烧结矿带通过,物料温度逐渐降低,熔融的液相被冷却凝固成网孔状的固体,这就是烧结矿带。
此带主要反应是液相凝结、矿物析晶、预热空气,此带表层强度较差,一般是返矿的主要来源。
在过湿层中,由于重新凝结的水分充塞于烧结料颗粒之间,使气流通过的阻力增加,同时,由于水分过多,超过混合料的原始水分,严重时使物料成泥泞状,严重降低料层透气性,大大降低烧结速度。粒度愈细和吸水性差的物料,这种现象愈明显。
燃烧层对烧结的影响:
燃烧层是烧结生产过程中最重要的部分,这里主要对此层对烧结生产的影响做详细的叙述。
(3)预热带
该带主要使下部料层加热到燃料的着火温度。一般温度为400~800度。
该带主要反应是烧结料中的结晶水及部分碳酸盐、硫酸盐分解,磁铁矿进行还原以及组分间的固相反应等。
(4)干燥带
烧结料的热废气从预热带进入下层,迅速将烧结料加热到100℃以上,因此该带主要是水分的激烈蒸发。
(5)过湿带
从烧结料点火开始,物料中的水分就开始转移到气流中去。含有水蒸气的废气经过料层冷却后,废气被冷却到露点温度,致使其中水蒸气冷凝,这部分烧结料中的水分含量超过了物料的原始水分,出现了过湿现象,这一区域成为过湿带。
(2)燃烧带
该带温度可达1350~1600度,此处混合料软化、熔融及液相生成,发生异常复杂的物理化学变化。该层厚度为15~50mm。此
(-)(+)3~0mm
水
水、蒸汽
煤气与空气
空气
烟道灰
烟尘
返矿
排出废气
(热烧结矿)冷烧结矿
图3—1烧结生产一般工艺流程图
带对烧结产量及质量影响很大。该带过宽会影响料层透气性,导致产量低。该带过窄,烧结温度低,液相量不足,烧结矿粘结不好,导致烧结矿强度低。燃烧带宽窄主要受物料特性、燃料粒度及抽风量的影响。