铜合金重力铸造教程(第二部分)
铜水龙头重力铸造设计手册
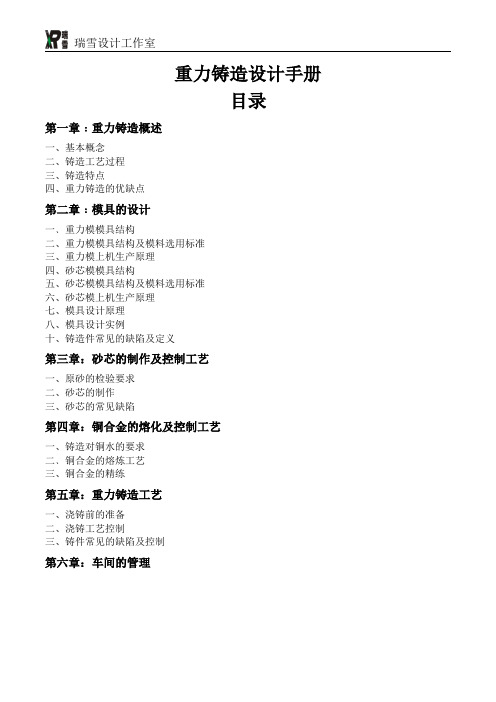
4.2.3具有良好的溃散性,便于产品的整理。
5 铸造工艺流程﹕
重力铸造工艺流程见图 1-3 所示(以公司现实际生产状况为例),从流程图
可以看出,铸造铜水的熔炼过程,实际上是一方面对铜锭的消耗,同时又对毛边、
浇道、以及报废铜产品回收利用以及加入微量元素对铜水成份进行调整的过程。
瑞雪设计工作室
铸 造 工 艺 流 程 图(图 1-3)
第三章:砂芯的制作及控制工艺
一、原砂的检验要求 二、砂芯的制作 三、砂芯的常见缺陷
第四章:铜合金的熔化及控制工艺
一、铸造对铜水的要求 二﹑铜合金的熔炼工艺 三、铜合金的精练
第五章:重力铸造工艺
一、浇铸前的准备 二、浇铸工艺控制 三、铸件常见的缺陷及控制
第六章:车间的管理
瑞雪设计工作室
第一章:重力铸造概述
第一节 模具设计的要求 模具设计是重力浇铸过程中的一个十分关键问题,合理的模具设计,科学的 操作工艺及严格控制的熔融金属成分,是重力铸造的品质保证,下面我们就目前 公司重力模设计的经验及模具设计的标准进行简单的介绍: 1 重力模对材料的要求: 1.1 具有耐高温性能,即高温下不熔化﹑不变形; 1.2 具有一定的热稳定性,即高温下不氧化﹑不腐蚀﹑不生长﹑不与铸造合金
提高铸件的力学性能; 3.1.3 金属模具尺寸准确、表面光洁,从而提高了铸件的尺寸精度及表面质量,
也便于加工定位及减少抛光余量; 3.1.4 节省了场地,可以提高铸造车间单位面积上铸件产量; 3.1.5 易实现机械化、自动化,提高生产效率,减轻劳动强度; 3.1.6 减少了混砂、制型等工艺,所以一定程度上减少了噪音、刺激性气体、粉
RQ=∆X/λ ➁。
其中∆X 为物体厚度,λ为物体导热系数。所以在铸件壁厚、间隙、重力模
铜合金重力铸造教程(第二部分)
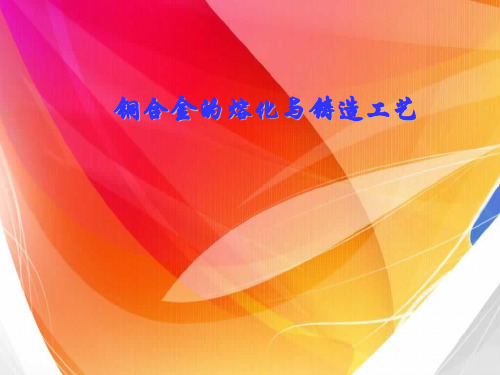
③沸腾除气法:沸腾除气是在工频有芯感 应电炉熔炼高锌黄铜时常用的一种特殊除气方 法。如熔化黄铜时锌的蒸发就可以将溶解在合 金液体中的气体去除。由于熔化温度较高超过 锌的沸点(907℃),因此在熔炼后期会出现 喷火现象,即锌的沸腾,这样有利于气体的排 除。
• (2)除渣精炼 ①静置澄清法:静置澄清过程一般是让熔 体在精炼温度下,保持一段时间使氧化及熔渣 上浮或下沉而除去。 ②浮选除渣法:浮选除渣是利用熔剂或惰 性气体与氧化物产生的某种物理化学作用,即 吸附或部分溶解作用,造成浮渣而将氧化物除 去。 ③熔剂除渣法:在熔体中加入熔剂,通过 对氧化物的吸附、溶解、化合造渣,将渣除去, 熔剂的造渣能力越强,除渣精炼的效果越好。
• 5.4.铜合金的配比
根据铁模尺寸大小要求合金配料总量为1200g
(1)黄铜(H68) 纯铜:1200g×68%=816g 锌: 1200g×32%=384g (需考虑烧损量 1.5~2%)
(2)铝青铜(QAl10) 纯铜: 1200g×90%=1080g 铝: 1200g×10%=120g
重铸基础知识
1,调整模具,清理砂筒 2,调整气压 3,漏气处贴胶 4,对准射砂口
1,增加固化时间 2,提高固化温度 3,严格按照参数混砂 1,减少固化时间 2,降低固化温度 1,仔细刮砂芯 2,射砂道小心掰掉或用锯条锯掉
夹生
焦酥
1,固化时间过长 2,固化温度过高 1,刮砂芯不仔细 2,连接射砂道敲掉后型砂表面有凹坑
4.影响铸模铸锭质量的主要因素
• (1)浇铸温度:浇铸温度过高或过低都是不 利的,因为采用较高的浇铸温度,势必就要使 炉内熔体的温度作相应的提高,这将引起铜合 金在熔化和保温过程中大量的吸气,同时也会 增加烧损,在浇铸时会使氧化加剧。此外,过 高的浇铸温度也会对铸模的寿命产生不利影响, 尤其是平模浇铸时模底板更容易遭到破坏。当 浇铸温度偏低时,熔体流动性变差,不利于气 体和夹渣上浮,也易使铸锭产生冷隔缺陷。因 此,必需根据合金的性质,结合具体的工艺熔炼时金属的损耗和氧化
铜合金溶铸工艺操作流程
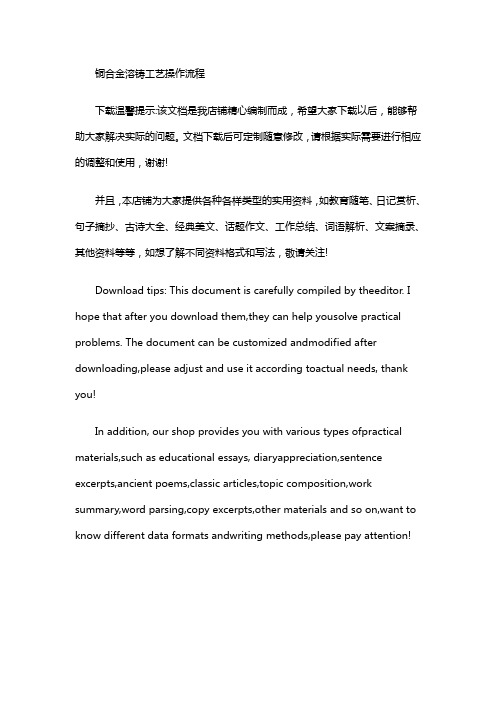
铜合金溶铸工艺操作流程下载温馨提示:该文档是我店铺精心编制而成,希望大家下载以后,能够帮助大家解决实际的问题。
文档下载后可定制随意修改,请根据实际需要进行相应的调整和使用,谢谢!并且,本店铺为大家提供各种各样类型的实用资料,如教育随笔、日记赏析、句子摘抄、古诗大全、经典美文、话题作文、工作总结、词语解析、文案摘录、其他资料等等,如想了解不同资料格式和写法,敬请关注!Download tips: This document is carefully compiled by theeditor. I hope that after you download them,they can help yousolve practical problems. The document can be customized andmodified after downloading,please adjust and use it according toactual needs, thank you!In addition, our shop provides you with various types ofpractical materials,such as educational essays, diaryappreciation,sentence excerpts,ancient poems,classic articles,topic composition,work summary,word parsing,copy excerpts,other materials and so on,want to know different data formats andwriting methods,please pay attention!铜合金溶铸工艺是一种生产铜合金铸件的常用方法,下面是该工艺的操作流程:1. 原材料准备- 铜合金原料:根据需要生产的铜合金种类,提前准备好相应的原料,如铜、锡、铅、锌等。
铜合金铸件铸造工艺设计手册

铜合金铸件铸造工艺设计手册
一、浇注系统设计
1.铜合金阻流面积的计算公式
F阻=
√G 0.161K√h
说明:本式只适用于干型、侧注,其他浇注类型要乘以转换系数,见表1。
式中: G-铸件浇注重量(kg)
K-速度系数由表2选定
h-压力头高度由浇口杯表面至内浇道中心线距离(cm),见表3 表1转换系数
表3 h值的选定
顶注式中注式底注式
在设计开放式浇注系统时,压力头还要加上h1,按表4决定。
1
2.铜合金浇道各部分截面面积比例
铜合金浇道各部分截面面积比例见表5。
表5铜合金浇道各部分截面面积比例
3.各种浇道的具体结构尺寸。
3.1横浇道、直浇道尺寸见表6
表6横浇道、直浇道尺寸
h=0.8a
h=(1~1.2)a
注:a.断面积单位cm,其余mm.
b. 要求撇渣效果大时采用h大的横浇道。
3.2内浇道尺寸见表7
表7内浇道断面尺寸
注:断面积单位cm,其余单位mm。
一、冒口尺寸的确定
热节圆法计算冒口尺寸,见表8
表8热节圆法计算冒口尺寸圆柱型铸件
长方形铸件
易割冒口
轮和套类
H为切割冒口用的留量
二、锡青铜铸件的机械加工余量
锡青铜铸件的机械加工余量(手工造型)见表9。
表9锡青铜铸件的机械加工余量(手工造型)(单位:mm)。
简易重力铸造机操作规程

简易重力铸造机操作规程简易重力铸造机操作规程一、操作前的准备工作:操作人员应熟悉重力铸造机的结构、性能和使用方法,了解操作规程和安全操作要求。
在操作前,应对机器进行必要的检查和维护,确保其正常运行。
1. 对机器的外观进行检查,保证机器没有明显的外部损坏。
2. 检查电源线是否完好,插头是否接触良好。
3. 检查冷却系统和水源是否正常,确保流量稳定。
4. 检查燃气系统是否正常,确保燃气泄漏情况。
5. 清洁工作台和操作区域,保持干净整洁。
二、操作步骤:1. 打开电源开关,确认主电源指示灯亮起。
2. 打开冷却水开关,确认冷却水顺畅。
3. 打开燃气阀门,确认燃气是否供应正常。
4. 装模就位:根据需要,选择合适的模具并将其安装到模具台上。
确保模具和模具台之间的接触紧密,防止出现渗漏的情况。
5. 加热:按照所需的温度要求,设置加热控制器的温度。
等待加热控制器显示温度达到设定温度。
6. 准备熔炼材料:根据使用要求,准备好需要熔炼的铸造材料,并放入预熔炉中。
7. 熔炼:将预熔炉中的铸造材料转移到铸造炉中,并启动铸造炉的加热系统,等待铸造炉内的铸造材料完全熔化。
8. 出气:打开出气阀门,排除铸造炉内的气体,确保铸造过程中不会受到气泡的影响。
9. 倒模:当铸造材料完全熔化并排除气泡后,打开模具台上的浇口,倒入铸造材料,保持连续倒注直至浇注完毕。
10. 冷却:在铸造完成后,等待铸件自然冷却至合适温度,可以打开模具台上的浇口,取出铸件。
11. 关闭燃气阀门,断开电源和冷却水源,清理操作区域。
三、安全操作注意事项:1. 操作人员必须熟悉机器的工作原理和操作规程,严禁未经培训人员操作机器。
2. 操作人员应佩戴安全防护设备,如安全帽、防护眼镜、防护手套等。
3. 在加热过程中,操作人员应远离加热区域,以防止烫伤。
4. 在铸造过程中,操作人员应小心操作,防止溅洒或烫伤。
5. 操作人员应随时关注机器运行状态,如发现异常情况应立即停机并报修。
重力铸造
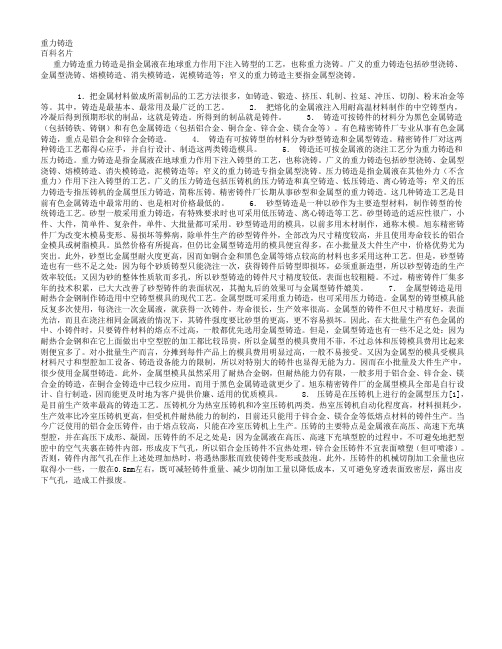
重力铸造百科名片重力铸造重力铸造是指金属液在地球重力作用下注入铸型的工艺,也称重力浇铸。
广义的重力铸造包括砂型浇铸、金属型浇铸、熔模铸造、消失模铸造,泥模铸造等;窄义的重力铸造主要指金属型浇铸。
1.把金属材料做成所需制品的工艺方法很多,如铸造、锻造、挤压、轧制、拉延、冲压、切削、粉末冶金等等。
其中,铸造是最基本、最常用及最广泛的工艺。
2.把熔化的金属液注入用耐高温材料制作的中空铸型内,冷凝后得到预期形状的制品,这就是铸造。
所得到的制品就是铸件。
3.铸造可按铸件的材料分为黑色金属铸造(包括铸铁、铸钢)和有色金属铸造(包括铝合金、铜合金、锌合金、镁合金等)。
有色精密铸件厂专业从事有色金属铸造,重点是铝合金和锌合金铸造。
4.铸造有可按铸型的材料分为砂型铸造和金属型铸造。
精密铸件厂对这两种铸造工艺都得心应手,并自行设计、制造这两类铸造模具。
5.铸造还可按金属液的浇注工艺分为重力铸造和压力铸造。
重力铸造是指金属液在地球重力作用下注入铸型的工艺,也称浇铸。
广义的重力铸造包括砂型浇铸、金属型浇铸、熔模铸造、消失模铸造,泥模铸造等;窄义的重力铸造专指金属型浇铸。
压力铸造是指金属液在其他外力(不含重力)作用下注入铸型的工艺。
广义的压力铸造包括压铸机的压力铸造和真空铸造、低压铸造、离心铸造等;窄义的压力铸造专指压铸机的金属型压力铸造,简称压铸。
精密铸件厂长期从事砂型和金属型的重力铸造。
这几种铸造工艺是目前有色金属铸造中最常用的、也是相对价格最低的。
6.砂型铸造是一种以砂作为主要造型材料,制作铸型的传统铸造工艺。
砂型一般采用重力铸造,有特殊要求时也可采用低压铸造、离心铸造等工艺。
砂型铸造的适应性很广,小件、大件,简单件、复杂件,单件、大批量都可采用。
砂型铸造用的模具,以前多用木材制作,通称木模。
旭东精密铸件厂为改变木模易变形、易损坏等弊病,除单件生产的砂型铸件外,全部改为尺寸精度较高,并且使用寿命较长的铝合金模具或树脂模具。
金 属 模 重 力 铸 造 法

金属模重力铸造法CRA VITY DIE CASTING PROCESS1.1概要靠重力往金属模里浇铸熔汤的铸造方法,通常称为金属模重力铸造法(GRA VITY DIE CASTING PROCESS)。
同样,用砂型的重力铸造法也是普遍的,但用的是砂型,而金属模重力铸造法所用的模具是金属的,可以反复使用,很方便。
因此,作为一种利用熔汤温度较低的轻合金来铸造,这比砂型铸造更普遍。
利用使熔汤急速冷却的方法,可以获得组织致密的高品质铸件。
但,由于采用的是金属模具,其铸造方案、排气对策、涂型方法及模具温度的调整等方面与砂型铸造法有很大差异。
表1.1表示了金属模具铸造法与砂型铸造法比较,其优点和缺点。
1.2铸造方案1.2.1铸造方案的基本型铸造方案必须这样设计:注汤时,通常汤口要注满,不能产生熔汤的乱流,熔汤流动要静,并迅速地注入模具型腔。
为此,注汤口要设计成容易注汤的宽大形式,汤口若开在下下方,其断面积要小,并设计有斜度,使熔汤流动不乱,进入模具型腔的熔汤能调速。
图1.1列出了铸造方案的基本型。
实际的方案设计要符合基本行的要求,选择和合并基本型,对汤道、汤口位置、数量、大小、形状等都需要充分考虑后在决定。
(1)A方案此方案称为下注方案、底注方案或顶上方案,熔汤是从铸件底部注入。
此方案的汤口断面设计成锥形,这样,空气不容易卷入,流速能调整。
但是,由于熔汤由一处流入,模具的汤口附近和型芯的温度上升,容易产生缩孔。
(2)B方案此方案称为垂直坝方案、仿垂直坝等,为了防止A方案的缺陷,把垂直坝在铸件侧面扩大。
随着熔汤向模具内充填,由于熔汤是从高位置流入,可以在冒口附近,将温度高的熔汤补充进去。
(3)C方案此方案与B方案相同,称为垂直坝、仿垂直坝等。
此方案是熔汤由底部流入,依次凝固,在流入铸件型腔前,其流速可以做到很缓慢。
此例如图1.1所示。
熔汤一旦流入断面积较大的顶汤部分,其流速将变得缓慢,此过程生成的氧化物大部分在顶汤部分,铸件的质量较好。
(完整版)第二节常用的铸造方法

第二节常用的铸造方法(五)离心铸造离心铸造是将金属液浇入绕水平、倾斜或立轴旋转的铸型,在离心力的作用下凝固的铸造方法。
铸件的轴线与旋转铸型的轴线重合。
铸型可用金属型、砂型、陶瓷型、熔模壳型等。
1.离心铸造机离心铸造机是离心铸造所用的设备,按其旋转轴空间位置的不同分为立式、卧式二种。
立式离心铸造机的铸型是绕垂直轴旋转(图2-2-41a),由于金属液的重力作用,铸件的内表面呈抛物线形,故铸件不易过高,它主要用于铸造高度小于直径的环类、套类及成形铸件。
卧式离心铸造机的铸型是绕水平轴旋转(图2-2-41b),铸件的壁厚较均匀,主要用长度大于直径的管类、套类铸件。
图2-2-41 离心铸造示意图图 2-2-9 离心铸造2.离心铸造的特点和应用与其它铸造方法相比,离心铸造的优点是:(1)优点1)铸件组织致密,无缩孔、缩松、气孔、夹渣等缺陷,力学性能好。
2)铸造圆形中空铸件时,不用型芯和浇注系统,简化了工艺过程,降低了金属消耗。
3)提高了金属液的充型能力,改善了充型条件,可用于浇注流动性较差的合金及薄壁铸件。
4)可生产双金属铸件,如钢套内镶铜轴承等,其结合面牢固、耐磨,又可节约贵重金属材料。
5)离心铸造适应性较广,铸造合金的种类几乎不受限制。
既合适于铸造中空件,又可以铸造成形铸件。
中空铸件的内径通常为8~3000mm;铸件长度可达8000mm;质量可由几克至十几吨。
但离心铸造不宜生产易偏析的合金(如铅青铜等),铸件内表面较粗糙,尺寸不易控制。
(2)应用离心铸造主要用于生产各种管、套、环类铸件,如铸铁管、铜套、滑动轴承、缸套、双金属钢背铜套等铸件,也可用于生产齿轮、叶轮、涡轮等成形铸件。
(六)熔模铸造熔模铸造是指在易熔(如蜡料)制成的模样上包覆若干层耐火涂料,待其干燥硬化后熔出模样而制成型壳,型壳经高温培烧后即可浇注的铸造方法。
熔模铸造是精密铸造方法之一。
1.熔模铸造的工艺过程熔模铸造的工艺过程如动画2-2-7所示。
铜合金铸造工艺操作流程及要点—

金属型重力铸造铜合金工艺流程及操作要点1、工艺流程图2、操作要点表1 熔炼工艺技术条件卡片合金种类 出炉温度 脱氧剂 覆盖剂 精炼剂 加料与融化操作顺序 锡白铜1220~1250℃铜—磷木炭冰晶石铜+镍+木炭→融化→磷铜除氧→锡→除气→磷铜除氧→钛→测温→精炼、搅拌、捞渣→浇铸 铝白铜 1220~1250℃ 木炭 冰晶石铜+镍+铁+木炭→融化→中间合金→融化→少量铜→铝→除气→测温→精炼、搅拌、捞渣→浇铸表2 熔炼流程中的操作要点炉料配制 炉料熔炼原料准备 精炼、除气、扒渣 浇铸 上涂料浇铸前模具预热模具预热合模装冒口冷却开模,取出铸件保温冒口准备前期必要工具,用品准步骤要点工具与用品准备⑴提前准备好热电偶、钟罩、扒渣工具、搅拌工具、铁锤、铁钳等必要工具和精炼剂、覆盖剂、涂料等用品。
⑵钟罩、扒渣工具、搅拌工具需要在使用前上好涂料并烤干。
⑶锡白铜使用的工具用涂料为氧化锆,铝白铜使用的工具涂料为氧化锌。
炉料配制与加料原则⑴按照烧损量原则计算好各个组元成分含量,每次配12Kg料,得两个锭。
⑵炉料称量时至少需要两个人确认称量准确无误。
⑶向坩埚内加铜、镍的原则:少量铜(下)→全部镍(中)→剩余铜(上)。
⑷加入易烧损的元素(TI、Al等)要用钟罩按进金属液体内。
⑸炉料添加前应充分预热除水分。
模具预热与上涂料⑴上涂料前模具预热到150℃左右,上完涂料后在浇铸前模具预热到350℃左右。
⑵锡白铜使用的模具涂料为4%石墨+96%机油,铝白铜使用的模具涂料为氧化锌。
坩埚使用原则⑴冷坩埚使用前将坩埚在200℃下充分预热。
⑵不能用硼砂作为覆盖剂⑶浇铸完成后,应迅速清理坩埚内残留的金属、渣等残留物。
炉子使用及功率调节原则⑴开炉子前,检查炉子水、电、气是否正常。
⑵加热功率设置原则:10Kw→材料变暗红→20Kw→材料通红→最大功率。
浇铸⑴模具合模后,先在模具的一个模筒上部放置保温冒口,待金属液浇满模具后,迅速在另一个模筒上部放置好冒口。
铜及铜合金铸造工艺流程

铜及铜合金铸造工艺流程
(总3页)
本页仅作为文档封面,使用时可以删除
This document is for reference only-rar21year.March
铜合金铸件铸造工艺流程
一、原材料准备
首先进行原材料化学成分分析,对检验合格的原材料予以采用,对检验不合格的原材料予以退回。
然后按原材料配比计算结构称重各种原料。
二、熔炼
按一定加料顺序和比例把原材料加入炉中。
如先将
88%铜加入炉内,加温成液态后再将10%的锌和1%的铅加入炉内搅拌均匀使炉内温度一致,30分钟后达到1200度熔化后用铜清渣剂进行初步清渣。
三、浇铸前化验
初步清渣后,取样检测,结果与产品标准在0.5%范围内,然后根据客户要求添加所需元素。
四、离心浇铸
将铜水注入离心浇铸机,离心机转速控制在1000转
/min,温度控制在1100-1200摄氏度,10分钟后降温到500-600摄氏度,往浇注机注入脱模剂,待冷却后
取出成品。
五、车床加工、镗孔、喷砂
将浇铸成型的铸件按客户要求上车床加工后镗孔,喷砂,制成成品,包装完成。
六、检验入库
铸件由检验员检验合格,填写产品名称、标号、生产日期、件数以及使用前注意事项的标签(标签所填写的内容对照标准要求,项目可以多列但不能少列)然后由工人转入成品库摆放整齐,由库管员核对无误后入库。
黄铜重力铸造方法
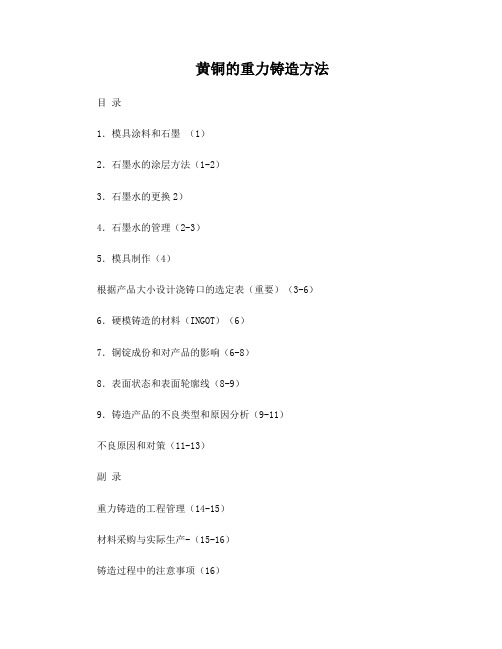
黄铜的重力铸造方法目录1.模具涂料和石墨(1)2.石墨水的涂层方法(1-2)3.石墨水的更换2)4.石墨水的管理(2-3)5.模具制作(4)根据产品大小设计浇铸口的选定表(重要)(3-6)6.硬模铸造的材料(INGOT)(6)7.铜锭成份和对产品的影响(6-8)8.表面状态和表面轮廓线(8-9)9.铸造产品的不良类型和原因分析(9-11)不良原因和对策(11-13)副录重力铸造的工程管理(14-15)材料采购与实际生产-(15-16)铸造过程中的注意事项(16)重点整理(16-17)模具设计时的注意事项(17-19)砂芯制作(19-22)砂芯用砂子的比较试验()(22-24)砂芯试验报告(24)砂芯生产标准及砂子检验标准24)样品制作时的注意事项(24-26)劝告事项(26-27)重力铸造的基础知识1. 模具涂料和石墨1)在铜合金的铸造过程中,每浇注一次,模具表面要涂上一次涂料。
同时也要冷却模具温度。
在实际工作中,通常是把模具浸泡在涂料槽(石墨水槽),以此解决上述要求。
石墨的作用:石墨是耐热物质,将高温铜水与模具隔开,保护、延长模具寿命;石墨粉很细,可增加铜水流动性,使产品易于浇铸。
经验说明,要生产表面细腻的良好铸造产品,其涂料凝聚力强、硬度要好。
在这儿推荐使用易取且易与水混合的尘土状石墨粉(Graphite)。
推荐使用青岛石墨股份有限公司生产的石墨:铸造土状石墨,粒度235目,含碳量:80%为了防止在连续工作中石墨水的温度上升与石墨粉沉淀于水槽底部,通常采用电动搅拌机或吹气搅拌机。
电动搅拌机可以防止石墨粉的沉淀,但其冷却效率不高。
还是利用吹气方式为好。
石墨水槽设计:石墨水槽的高度不低于浇铸工作台,防止沙芯掉入,其底部越尖,吹气冷却的效果越好。
参考:1) 石墨水浓度因产品大小的不同其要求也有所差别。
一般采用粒度为220~250Mesh(目)的石墨粉,浓度为20%~30%。
2) 经过浸泡在石墨水槽冷却过的模具温度控制在100℃~180℃为好。
《铜合金铸件铸造技术》课程学习指南

课程导学一、课程概述:《铜合金铸件铸造技术》课程主要培养铜合金石膏型铸造、离心铸造、熔模铸造各岗位上的一线作业人员和管理人员,是高职材料成型与控制技术专业(铸造方向)开设的一门重要的专业核心课程。
本课程是在“校企合作”的办学模式下,以“工学结合”人才培养模式为指导,与企业深度合作,开发的基于工作过程系统化课程体系中的一门课程。
通过本课程及相关专业课程的学习,确保每位学生能够获得铸造工、熔炼工职业资格证书,学生能够掌握铜合金铸件石膏型铸造、离心铸造、熔模铸造技术的主要工艺方法与职业技能。
二、主要内容、课标要求、重点、难点及关键通过以上学习内容的学习和能力的培养,达到下列素质目标:熟悉铸造专业职业领域国家及行业相关标准,掌握铸造专业及岗位核心技术,具有较强的实践动手能力;能正确面对困难、压力和挫折,具有积极进取、乐观向上和健康平和的心态。
遵纪守法,具有良好的诚信品质、敬业精神、责任意识、竞争意识、创新意识。
能根据专业领域的需要,运用多种媒介、多种方式采集、提炼、加工、整理信息。
掌握专业所需的计算方法,计算来的数据,并对专业问题进行分析、预测和评价。
具有良好的心态和换位思考的宽广胸怀,尊重他人,诚以待人,能够敏锐发现共同的话题和兴趣,运用巧妙的方式和对方沟通。
牢固树立团队利益高于个人利益的观点,尊重并理解他人的观点与处境,能评价和约束自己的行为,能综合地运用各种交流和沟通的方法进行合作。
具有发现问题,提出问题并运用所学的综合知识去努力思考、积极探索,并且创造性地解决问题的能力。
综合素质能力:具有良好的社会责任感、团队协作精神、良好的职业道德。
三、课程教学资源1.产品图纸、工艺技术文件及相关标准。
2.课程标准、课时授课计划、教学方案、教学食品等。
3.参考教材、教师讲义、工程手册、工艺案例、专业文章。
4.专业教学资源库,课程网站。
四、学法指导在本课程的学习过程中,要类比三种特种铸造工艺和砂型铸造之间的区别和联系,不但有利于认识不同特种铸造方法的特点和应用环境,而且还可以从整体上掌握不同的铸造方法的区别和联系。
铜合金熔炼与铸锭2[新版]
![铜合金熔炼与铸锭2[新版]](https://img.taocdn.com/s3/m/65646852c950ad02de80d4d8d15abe23482f038c.png)
铜合金熔炼与铸锭要得到合格的铜合金制品,必须先制得合格的铜、铜合金液。
故此,铜合金的熔炼和铸造是获得优质铜合金制品和材料的关键工效之一。
铜合金铸造成锭坯的常见缺陷,如力学性能不合格、气孔、氧化夹杂、偏析等。
主要原因之一是熔炼工艺控制不当造成。
所以,对铜合金液的质量有如下的要求。
①必须严格控制铜合金的化学成份,要符合国家标准规定的指标。
②铜合金液要纯净,不得含有气体和氧化物。
③铜合金液不得过烧,不得有偏析。
要获得合格的合金液,除了严格控制熔炼工艺外,首要的是要有合格的原材料。
在熔炼铜合金是所用的原材料有新金属、回炉料和中间合金。
1.1铜合金熔炼时的金属损耗和配料1、我司黄铜用料:电铜、锌锭、光亮丝、纯漆线、Q料、拉伸料、普通角料(回料)、四类搭用料。
2、我司磷铜用料:镀白磷、镀锡紫铜、普磷、普紫铜。
3、熔炼时的金属损耗金属熔炼损耗通常是指熔炼过程中,金属的挥发、氧化烧损、与炉衬作用的消耗等全部损耗的总和。
1)金属的挥发在熔炼过程中,金属的挥发是难以避免的,尤其是一些易挥发的元素有所回因挥发损失过大致使控制成份发生困难;故在熔炼工艺上应视其情况采取相应的措施。
2)氧化烧损熔融金属中合金元素的氧化烧损,与合金元素对氧的亲合力及含量有关,凡与氧的亲合力比基体金属大、表面活性强的金属,必然易烧损。
4、降低熔炼损耗的途径①用熔池面积小的炉子熔炼。
②制定合理的工艺操作规程。
易氧化、挥发的合金元素应制成中间合金在最后加入,或在溶剂覆盖下溶化。
③碎屑散料应打包。
④选用适宜的覆盖剂覆盖。
⑤正确选用溶剂,同时采取高温扒渣或捞渣,降低渣中金属损耗。
5 配料原则与配料计算1)配料原则①确定合金各组元的配料比及易耗组元的补偿量。
②在保证合金的主要成份及杂质含量合乎国家标准的前提下,尽可能少用新金属,以扩大低品位原料及回料的使用量。
③在保证合金质量的前提下,对合金中贵金属尽可能按标准的下限含量配料。
④为保证某些制品的特殊要求,在国家标准范围内科适当调整某些元素的含量,及制度生产中实际控制的内部标准。
《铜合金铸件铸造技术》教学大纲

《铜合金铸件铸造技术》教学大纲一、课程基本信息课程基本信息见表1。
表1 《铜合金铸件铸造技术》课程基本信息二、课程性质与任务1.课程性质《铜合金铸件铸造技术》课程是材料成型与控制技术专业进行岗位能力培养的一门专业综合学习领域核心课程,本课程针对人才需求组织教学内容,按照工作过程设计教学环节,为岗位需求提供职业能力,为培养高素质技能型专门人才提供保障。
2.课程任务《铜合金铸件铸造技术》课程的主要任务是学习石膏型铸造、离心铸造、熔模铸造生产铜合金铸件的工艺技术,使学生掌握石膏型铸造、离心铸造、熔模铸造、坩埚炉熔炼、感应电炉熔炼工艺过程及生产技术,并能编制并实施铜合金铸件生产工艺规程。
通过本课程的学习,学生应具备严谨、安全、创新、质量意识等方面的素质。
三、课程目标1.知识目标(编号Ai)A1铜合金基础知识。
A2铜合金铸造方法选择A3石膏型铸造技术。
A4离心铸造技术。
A5石蜡-硬脂酸模料、水玻璃型壳等熔模铸造技术。
A6中温模料、硅溶胶型壳等熔模铸造工艺设计及铸造技术。
A7电阻坩埚炉熔炼工艺。
A8中频感应炉熔炼铜合金铸件工艺及浇注技术要点。
A9震动落砂、切割、打磨、抛丸等铸件清理方法。
A10铸件质量检验。
2.能力目标(编号Bi)B1能够完成铜合金铸件的石膏型铸造、离心铸造、熔模铸造工艺方法的合理选择。
B2能够通过小组协作完成铜合金铸件石膏型铸件工艺方法的编制、生产过程的准备、设备的选择、熔炼、浇注等工艺过程。
B3能够通过小组协作完成铜合金铸件离心铸造工艺的编制、设备的选择及使用、熔炼、浇注、清理等工艺过程。
B4能够通过小组协作完成铜合金铸件熔模铸造工艺的编制、模料的选择、熔模的压制、组焊、型壳的制造、焙烧、熔炼、浇注等工艺过程。
B5具备一定的敬业精神、责任意识、竞争意识、创新意识。
B6熟悉区域内行业企业生产力现状,熟悉专业职业领域国家及行业相关标准,认知专业领域及工作范围和工作职责。
B7掌握材料成型专业及岗位核心技术,具有较强的实践动手能力,具备从事企业铜合金铸件生产岗位工作的能力。
北京科技大学铸造合金及制备工艺4.2-铸造青铜

材料科学与工程学院 材料成形与控制工程系 毛卫民
4.2 铸造铜合金及制备工艺
4.2.1 概述 纯铜的基本性质:纯铜的颜色为紫红,故 又称其为红铜、紫铜;熔点为1083℃; 20℃时的比重为8.96g/cm3;纯铜的导电性 良好,仅次于纯银;纯铜的导热性良好; 纯铜的塑性极好。 当纯铜中混入少量的其它金属时,将会严 重地降低其导电性和导热性,如下图所 示。
铸造铜合金的两大特点 具有良好的耐蚀性:尤其对大气、淡水、海 水等介质,铸造铜合金具有良好的耐蚀性,因 此铸造铜合金大量用于造船和化学工业,如管 配件、阀门、泵体、船用螺旋桨(如下图所示) 等。
船用铸造青铜螺旋桨铸件
具有良好的导热性和耐磨性,铸造铜合 金常用于制作机器中承受重载荷和高速旋 转轴的滑动轴承、轴套,也用来制作齿 轮、电器零件,如下图所示。
ZQSn10-1(P) 化学成分(wt%):Sn9∼11, P0.6∼1.2; 力学性能:在金属型铸造条件下, σb220∼250MPa,σs140∼200MPa,δ3%, HB80∼120(ZQSn10-2的硬度HB75∼90); 该青铜的硬度高、耐磨性好,用于铸造高 载荷和高速滑动下工作的衬套、蜗轮等零 件,但该青铜的切削加工性能较差; ZQSn10-1的铸态组织如下图所示。
α固溶体枝晶
灰色的α+δ 共析体
ZQSn10-1(P)的铸态组织
4.2.2.3 铸造无锡青铜 铸造锡青铜虽然耐蚀性高,摩擦系数小、 耐磨性高,但强度低,结晶间隔大,因而 铸造性能差,铸件的气密性低,而且铸造 锡青铜的价格高,所以发展了铸造无锡青 铜,如铸造铝青铜、铸造铅青铜、铸造铍 青铜 、铸造硅青铜、铸造锰青铜、铸造铬 青铜、铸造锑青铜等。 下面就主要叙述铸造铝青铜、铸造铅青 铜、铸造铍青铜的相图、组织和性能。
- 1、下载文档前请自行甄别文档内容的完整性,平台不提供额外的编辑、内容补充、找答案等附加服务。
- 2、"仅部分预览"的文档,不可在线预览部分如存在完整性等问题,可反馈申请退款(可完整预览的文档不适用该条件!)。
- 3、如文档侵犯您的权益,请联系客服反馈,我们会尽快为您处理(人工客服工作时间:9:00-18:30)。
1,砂芯模的检查(包括磨具行腔,定位销是否磨损, 加热板是否紧固等) 2,气压调整 3,清理分型面异 物 4,检查抽芯是否安装良好
1,调整模具,清理砂筒 2,调整气压 3,漏气处贴胶 4,对准射砂口
1,增加固化时间 2,提高固化温度 3,严格按照参数混砂
1,砂芯无强度,易断芯 2,易掉砂,易砂眼
1,减少固化时间 2,降低固温度
利的,因为采用较高的浇铸温度,势必就要使 炉内熔体的温度作相应的提高,这将引起铜合 金在熔化和保温过程中大量的吸气,同时也会 增加烧损,在浇铸时会使氧化加剧。此外,过 高的浇铸温度也会对铸模的寿命产生不利影响, 尤其是平模浇铸时模底板更容易遭到破坏。当 浇铸温度偏低时,熔体流动性变差,不利于气 体和夹渣上浮,也易使铸锭产生冷隔缺陷。因 此,必需根据合金的性质,结合具体的工艺条 件,制定适当的浇铸温度范围。
• (3)合金熔化时放出大量热量的金属,不应单独加入 到熔液中,而应与预先留下的基体冷料同时加入。如 熔炼铝青铜时,将铝加入到铜液中时会发生放热反应, 使铜液剧烈地过热,因此熔炼时应先加三分之二的铜, 熔化后再加铝,并同时加入剩余的三分之一的铜,这 样加铝所发出的热量为后加入的铜所利用,可以避免 合金熔体过热。
树
➢呋喃II型:苯酚,甲醛,糠醇(含氮低,淡蓝色)
脂
➢ZHR—I型:尿醛,酚醛,糠醇(中氮树脂,深绿色)
*砂芯的发气量主要是因为树脂中尿素受热分解,产生NH3与H2
固化剂:常温呈碱性,中和树脂酸性,减缓树脂反应们延长混好砂的存放时间 添加剂:增加粘合强度 涂料:填补凹坑
制芯篇——制芯工艺1
一,砂芯配比
• 5.3. 操作要点 ①锌能很好地气和脱氧,加入少量Cu-P中间合 金的目的是改善合金熔体的流动性。 ②为了减少熔炼损耗,要在低温加锌。 ③铝青铜中铝为强氧化元素,在熔炼过程中极 易氧化,生成高熔点Al2O3,形成悬浮渣液, 极不易除去,加入冰晶石熔剂除去Al2O3的效 果好。 ④冰晶石熔剂的加入量为炉料量的0.1~0.3%, 分两次加入。 ⑤浇铸时要掌握好浇铸温度和浇铸速度,确保 铸锭质量。
1,密封处缺料漏水 2,影响出水量(缺陷在水道处), 3妨 碍加工(缺陷在阀芯,水嘴等需加 工出) 4,增加成本(消耗铜)
➢挂件砂:50kg砂+180ml固化剂+800ml树脂+30ml添加剂 ➢龙头砂:50kg砂+170ml固化剂+700ml树脂+30ml添加剂
二,混砂工艺 砂+固化剂
树脂
添加剂
1-2分钟
2-3分钟
1分钟
➢要求混沙机转速120~150转/分,太低的转速不易搅拌均匀,太高的 转速沙芯易发热,树脂易板结,流动性不好。混砂时,原砂温度不 应超过35度 ➢混好的树脂砂在存放过程中流动性将逐渐下降,所以混好的砂应 在一小时内用完,混砂时,要根据车间生产需要,不宜多混。特别
➢3,圆砂流动性好,紧密度好,但高温易膨胀
注 意 事
➢1,原砂应充分干燥,因为砂中的水分加热后 会 破坏树脂膜,影响粘结强度
➢2,砂温不宜过低(15-30度),过低降低树脂粘
项 度,不宜混匀
➢3,砂温不宜过高,加速反应,存放性差
制芯篇——造型材料3
➢呋喃I 型:尿素,甲醛,糠醇(含氮高,一般为无色,或淡黄色)
*所有合成树脂为酸性物质,请带好劳保用品进行操作
制芯篇——砂芯不良及原因分析
主要缺陷
形成原因
错模,胀模 疏松,孔洞,吹不满
夹生
1.模具变形 2.定位销磨损,合膜模不良 3.磨具磨损变形 4.分模面有杂物 4.抽芯抽出不良,使型芯裂开
1,排气不良 2,射砂气压过大或过小 3,合模不严 4,模具漏气 5,射砂口堵住,或未对准
②浮选除渣法:浮选除渣是利用熔剂或惰 性气体与氧化物产生的某种物理化学作用,即 吸附或部分溶解作用,造成浮渣而将氧化物除 去。
③熔剂除渣法:在熔体中加入熔剂,通过 对氧化物的吸附、溶解、化合造渣,将渣除去, 熔剂的造渣能力越强,除渣精炼的效果越好。
4.影响铸模铸锭质量的主要因素 • (1)浇铸温度:浇铸温度过高或过低都是不
• (2)浇铸时间:不同牌号的铜合金都有最适 宜的铸造温度,高于或低于这个温度将直接影 响铸锭的质量。对于铸模铸锭方式来说,铸造 温度的控制与浇铸时间密切相关,因为浇铸时 间越长,先后浇铸的金属熔体的温度差越大。 对于铸造温度范围较窄的合金来说,浇铸时间 越长,浇铸温度也就越难控制。
• (3)浇铸速度:浇铸速度通常以锭模内金属 熔体每秒钟上升的毫米数来表示。浇铸速度的 选择原则是:①在保证铸锭产品质量的前提下, 适当提高浇铸速度;②对于某一确定的合金, 若合金化程度低,结晶温度范围小,导热性好, 可适当提高浇铸速度;③若锭模的冷却速度大, 铸锭直径较小,浇铸速度可适当提高。
• 5.4.铜合金的配比
根据铁模尺寸大小要求合金配料总量为1200g (1)黄铜(H68) 纯铜:1200g×68%=816g
锌: 1200g×32%=384g (需考虑烧损量 1.5~2%)
(2)铝青铜(QAl10) 纯铜: 1200g×90%=1080g
铝: 1200g×10%=120g
重铸基础知识
③沸腾除气法:沸腾除气是在工频有芯感
应电炉熔炼高锌黄铜时常用的一种特殊除气方 法。如熔化黄铜时锌的蒸发就可以将溶解在合 金液体中的气体去除。由于熔化温度较高超过 锌的沸点(907℃),因此在熔炼后期会出现 喷火现象,即锌的沸腾,这样有利于气体的排 除。
• (2)除渣精炼
①静置澄清法:静置澄清过程一般是让熔 体在精炼温度下,保持一段时间使氧化及熔渣 上浮或下沉而除去。
3. 除气精炼
• (1)气体的去除 熔炼铜合金的除气方法常用的有:气体除气法、 熔剂除气法、沸腾除气法。 ①气体除气法:采用惰性气体,它与金属液 不发生作用,不溶解在金属液内,也不与溶解 在金属液内的气体作用,如氮气、氩气。惰性 气体除气,就是将氮气(N2)用钢管通入到金 属液的底部,放出很多气泡,气泡上升时,能 将溶解在金属液中的气体带出来。这是因为当 氮气泡在金属液中上升时,溶解在金属液中的 氢气就会向氮气气泡中扩散,因此随氮气泡的 上升而带走。
• (4)两种金属熔点相差较大时,应先加入易熔金属, 形成熔液时,再加入难熔金属,利用难熔金属的溶解 作用,逐渐溶解于熔液中。如熔化含铜80%,含镍20% 的白铜时,先将铜熔化,并加热至1300℃左右,再将 镍加入(镍块要小些,容易熔化)液体中,逐渐熔化。 这样缩短熔炼时间,又保证合金成分。
• (5)能够减少熔液大量吸收气体的合金元素,应先入 炉熔化。
5.熔化工艺
• 5.1. 黄铜熔炼工艺 熔料准备→预热坩埚至发红→加铜和木炭→ 升温至1200℃熔化→加锌(分批加入到熔体 中)→搅拌→加中间合金(Cu-8P)→搅拌 →静置→出炉→扒渣→浇铸
• 5.2. 铝青铜熔炼工艺 熔料准备→预热坩埚至发红→先加2/3电解铜 →加熔剂(冰晶石)→升温至1200℃熔化→ 加纯铝→熔化后再加1/3电解铜→加熔剂→熔 化→搅拌→静置→出炉→扒渣→浇铸
➢ 2、模具应调整到无错模,间隙不能大于0.05mm。 ➢ 3、下砂不能过多,需标准,否则射砂斗的密封圈要破损。 ➢ 4、 固化时间不宜过短。(应在模具内硬化70-80%、但烤砂芯时间短在外面慢慢硬化)也不是
固化时间长,强度就上升,时间太长反而强度会下降 ➢ 5、刚制成的砂芯并未完全硬化,修刮毛边和合模线时要小心,并修刮干净,装箱后要保证砂
什么是重力铸造?
用铁、铜或其它金属型材料作铸型,在重力 作用下,将熔融的金属注入铸型而获得铸 件的工艺方法称之为重力铸造。
重力铸造工艺流程
混砂
制芯
熔炼
浇注
开模取件
整模落砂
铸件检验
铸件洗砂
切浇道
重铸基本工序
制
浇
整
芯
铸
理
➢ 重铸基本可分为制芯,浇铸,整理三大块
➢ 每一道工序都必须严格的按照工艺参数执行
其他(断裂,顶针伸入)
1,顶针速度不一,或顶针长度不一 2,顶针板未水平推进 3,型砂不宜脱模,所以顶针伸入
影响
解决方案
1,铸件壁厚不匀 2,型芯不易放入磨具 3,断芯 4,产品加工余量不足
1,影响出水量(缺陷在水道处), 2妨 碍加工(缺陷在阀芯,水嘴等需加 工出) 3,增加成本(消耗铜)
1,砂芯无强度,易断芯 2,砂芯内水分未烤干
铜合金的熔化与铸造工艺
1. 装料原则及熔化顺序
• (1)炉料最多的金属应首先入炉进行熔化。 炉料较多的金属先熔化,形成金属熔池后再逐 渐地加入其它金属元素,这样可以减少金属元 素的熔损。
• (2)易氧化、易挥发的合金元素应最后入炉 熔化。如熔炼黄铜时要先加铜,铜熔化后再加 锌,因为铜的熔点是1083℃,而锌的熔点是 417℃,锌的沸点是907℃,熔炼时若先加锌就 会造成锌的大量挥发烧损,而熔炼时先加铜, 铜熔化后再加锌,锌在铜液中迅速溶解,当合 金液达到浇铸温度时,即可出炉浇铸,因此可 以减少锌的熔炼烧损。
1,固化时间短 2,固化温度过低 3,砂芯配比不良,或混砂不良
焦酥
1,固化时间过长 2,固化温度过高
清理不良(毛刺未刮干 净,表面凹坑)
1,刮砂芯不仔细 2,连接射砂道敲掉后型砂表面有凹坑
强度低 变形
1,夹生 2,存放时间过长 3,混好的砂放置时间长,天热变质 4,配比不良
1,型砂放置不正确 2,型砂中铁丝冷却后变形
➢ 工艺参数若需优化,需在工程师确认下做相应更改,并作 好详细记录
制芯篇——造型材料1
原砂
造
粘连剂
型
材
料
辅助材料
1、硅砂 2、石灰石砂 3、特种砂
1、粘土 2、水泥 3、水玻璃 4、有机水溶性粘结剂 5、油类粘结剂 6、合成树脂粘结剂 7、其它铸造用粘结剂