钎焊温度对CMSX-4单晶高温合金接头组织与性能的影响
焊接工艺对焊接接头性能的影响

焊接工艺对焊接接头性能的影响焊接工艺在现代制造业中扮演着重要的角色,它对于焊接接头的质量和性能有着直接的影响。
正确选择和控制焊接工艺对于确保焊接接头的稳定性和可靠性至关重要。
本文将探讨焊接工艺对焊接接头性能的影响,旨在帮助读者更好地理解焊接工艺与焊接接头性能之间的关系。
1.影响力和需求1.1 焊接工艺的选择焊接工艺的选择需要考虑焊接接头的要求以及焊接材料的特点。
例如,在高温条件下,TIG焊接工艺可能更适合。
而在焊接薄板时,激光焊接工艺可能是更好的选择。
因此,选择合适的焊接工艺可以确保焊接接头的性能符合需求。
1.2 焊接接头的应力分布焊接工艺对焊接接头的应力分布有直接的影响。
如果焊接工艺不当,可能导致焊接接头的应力集中在某个区域,从而降低焊接接头的强度和耐久性。
因此,正确选择和控制焊接工艺可以帮助分散应力,提高焊接接头的强度和韧性。
2.焊接工艺的参数选择2.1 焊接电流和电压焊接电流和电压是影响焊接接头性能的重要参数。
电流的大小决定焊接接头的强度,而电压的调节则可以影响焊接接头的均匀性。
过小的电流可能导致焊接接头强度不够,过大的电流则会使焊接接头发生烧穿等缺陷。
因此,在具体应用中要根据焊接接头的要求选择合适的电流和电压。
2.2 焊接速度焊接速度是控制焊接接头性能的关键参数之一。
速度过快会导致焊接接头的强度降低,质量下降。
过慢则可能导致过热区域扩大,产生焊接缺陷。
因此,确定合适的焊接速度对于确保焊接接头质量至关重要。
3.3.1 构型和形状焊接工艺直接影响焊接接头的构型和形状。
不同的焊接工艺可能导致不同的接头形状和尺寸,从而进一步影响焊接接头的性能。
例如,激光焊接工艺可以实现深度焊接,适用于有特殊要求的接头。
3.2 组织和晶粒生长焊接工艺会对焊接接头的组织和晶粒生长产生直接影响。
不同的工艺参数可能导致晶粒尺寸和组织的变化,从而影响接头的力学性能和耐腐蚀性能。
因此,合理选择和控制焊接工艺对于控制焊接接头组织和晶粒生长至关重要。
CMSX-4单晶高温合金TLP接头组织与性能

CMSX-4单晶高温合金TLP接头组织与性能王瑶;唐新华;崔海超【摘要】采用含Si的BNi-5非晶箔片作为中间层合金对CMSX-4镍基单晶合金棒在放电等离子体烧结炉中进行TLP连接,采用SEM观测了TLP接头在不组织形貌特征,借助于EDS分析了TLP接头界面处的物相组成及其对接头力学性能的影响.采用常温和高温拉伸试验验证了不同焊接工艺条件对TLP接头性能的影响.结果表明,在1 200℃/5 kN/20 min工艺参数下可得到满意的TLP接头,此时组织分布较为均匀,常温抗拉强度达到了母材的95%,760℃高温抗拉强度达到母材的99%.【期刊名称】《焊接》【年(卷),期】2018(000)003【总页数】6页(P24-29)【关键词】瞬间液相扩散焊;CMSX4;镍基单晶高温合金;接头组织;力学性能【作者】王瑶;唐新华;崔海超【作者单位】上海交通大学材料科学与工程学院上海市激光制造与材料表面改性重点实验室,上海200240;高新船舶与深海开发装备协同创新中心,上海200240;上海交通大学材料科学与工程学院上海市激光制造与材料表面改性重点实验室,上海200240;高新船舶与深海开发装备协同创新中心,上海200240;上海交通大学材料科学与工程学院上海市激光制造与材料表面改性重点实验室,上海200240;高新船舶与深海开发装备协同创新中心,上海200240【正文语种】中文【中图分类】TG4540 前言镍基高温合金具有优良的高温性能,近年来广泛用于商业航空燃气喷气发动机涡轮叶片中[1]。
CMSX-4是第二代镍基单晶高温合金,是在第一代CMSX系列单晶的基础上大幅度添加了难熔元素Re,显微组织主要由γ′相和γ相组成。
由于发动机涡轮叶片具有复杂的型腔结构,单凭铸造技术难以实现整体制造,需采用连接技术。
绝大多数高温合金用熔焊的方法连接极易产生熔焊裂纹[2]。
例如,用钨极氩弧焊连接CMSX-4单晶,焊接接头会出现凝固裂纹[3]。
钎焊质量的影响因素
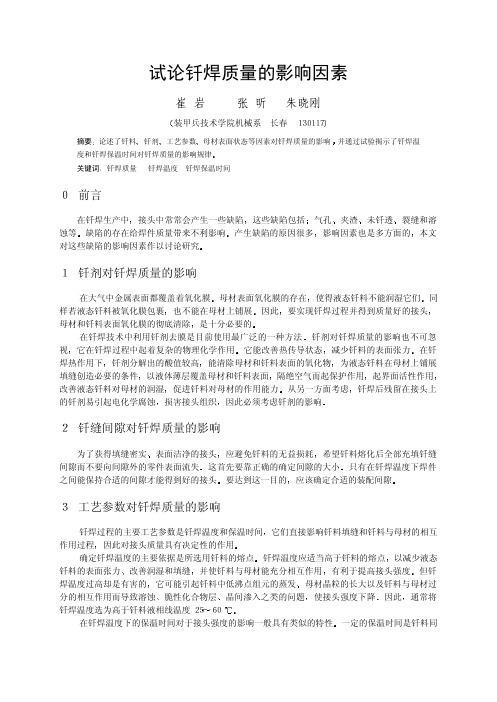
试论钎焊质量的影响因素崔岩张昕朱晓刚摘要钎剂母材表面状态等因素对钎焊质量的影响钎焊质量钎焊温度钎焊保温时间0 前言 在钎焊生产中这些缺陷包括夹渣裂缝和溶蚀等产生缺陷的原因很多本文对这些缺陷的影响因素作以讨论研究母材表面氧化膜的存在同样若液态钎料被氧化膜包裹因此母材和钎料表面氧化膜的彻底清除 在钎焊技术中利用钎剂去膜是目前使用最广泛的一种方法它在钎焊过程中起着复杂的物理化学作用减少钎料的表面张力钎剂分解出的酸值较高为液态钎料在母材上铺展填缝创造必要的条件隔绝空气而起保护作用改善液态钎料对母材的润湿从另一方面考虑损害接头组织 2 钎缝间隙对钎焊质量的影响 为了获得填缝密实应避免钎料的无益损耗这首先要靠正确的确定间隙的大小要达到这一目的 3 工艺参数对钎焊质量的影响 钎焊过程的主要工艺参数是钎焊温度和保温时间因此对接头质量具有决定性的作用钎焊温度应适当高于钎料的熔点改善润湿和填缝有利于提高接头强度它可能引起钎料中低沸点组元的蒸发脆性化合物层使接头强度下降通常将钎焊温度选为高于钎料液相线温度25一定的保温时间是钎料同母材相互扩散但过长的保温时间同样会导致某些过程的过分发展而走向反面首先要考虑钎料与母材相互作用的特性生成脆性相应尽量缩短保温时间如果通过二者的相互作用能消除钎缝中的脆性相或低熔组织时保温时间也与焊件大小和钎缝间隙值有关为了保证钎料同母材必要的相互作用 为了系统地研究钎焊工艺参数对接头力学性能的影响规律用相同的钎剂NH3Cl 3²â¶¨Æä¼ôÇÐÇ¿¶È220 Òò´ËÑ¡ÔñÇ¥º¸Î¶ÈΪ230范围内在一定的钎焊温度下接头的剪切强度的基本变化趋势是当达到某一最高值后钎焊温度超过310 ½ÓÍ·µÄ¼ôÇÐÇ¿¶È³öÏÖ´ó·ù¶ÈµÄ½µµÍÔÚÇ¥º¸Î¶ÈΪ270 钎焊保温时间为30 s的最佳工艺参数匹配下 4 结论 本文论述了钎料工艺参数等因素分别对钎焊质量的影响试验证明参考文献1 王守业等,第八次全国焊接会议论文集1997134 2 沈宁福等,.凝固理论进展与快速凝固 1996684 3 胡晓萍,银基钎料中杂质元素的影响及机理研究19987崔岩1971年生讲师 联系人长春市花园路1号 机械工程系 联系电话4847097 。
热暴露下预应变对CMSX-4单晶高温合金的显微组织演变的影响

热暴露下预应变对CMSX-4单晶高温合金的显微组织演变的影响B. G. CHOI;C. Y. JO;H. U. HONG;I. S. KIM;S. M. SEO;H. M. KIM【摘要】在室温下,对经完全热处理的第二代单晶高温合金CMSX-4实施压缩和拉伸预应变.压缩和拉伸预应变在单晶CMSX-4中产生了剪切带.单晶CMSX-4在950℃下热暴露10h,沿剪切带产生了γ'粒子择优粗化.剪切带上的γ'粒子逐渐侵入γ通道.最后,γ通道沿着剪切带消失.TCP状粒子伴随着γ通道的消失而出现.然而,热暴露10 h的普通单晶CMSX-4没有产生TCP沉淀,也没有γ'粒子择优粗化.热暴露100 h的预应变CMSX-4沿剪切带产生了γ'粒子和TCP相粒子择优粗化,基体中也有γ'粒子粗化.【期刊名称】《中国有色金属学报(英文版)》【年(卷),期】2011(000)006【总页数】6页(P1291-1296)【关键词】预应变;显微组织演变;高温合金;CMSX-4【作者】B. G. CHOI;C. Y. JO;H. U. HONG;I. S. KIM;S. M. SEO;H. M. KIM【作者单位】High Temperature Materials Group, Korea Institute of Materials Science, 797 Changwondaero, Changwon 641-010, Korea;High Temperature Materials Group, Korea Institute of Materials Science, 797 Changwondaero, Changwon 641-010, Korea;High Temperature Materials Group, Korea Institute of Materials Science, 797 Changwondaero,Changwon 641-010, Korea;High Temperature Materials Group, Korea Institute of Materials Science, 797 Changwondaero, Changwon 641-010, Korea;High Temperature Materials Group, Korea Institute of Materials Science, 797 Changwondaero, Changwon 641-010, Korea;High Temperature Materials Group, Korea Institute of Materials Science, 797 Changwondaero, Changwon 641-010, Korea【正文语种】中文With the rapid development of automobile industry,advanced manufacturing technologies make automobile production to develop tothe direction of high-quality,high efficiency, low consumption and cleanness.The application of magnesium alloy in automobiles can play an important role in reducing the emission and conserving the energy resources.At present, one of the urgent problems to be resolved in the applications of magnesium alloy is to improve its strength to enable to apply to structural parts with requirement of high strength.However, magnesium alloy products are mainly castings, among which more than 90% are die castings,while magnesium alloy forgings with high-performanceare rarely applied[1-3].The main reason is because magnesium alloy is difficult to be forged due to its low plasticity.The high-cost production limits the application and development of high-performance magnesium alloy forgings to some extent.One of the differences between magnesium alloy and other materials such as aluminum alloy lies in the fact that magnesium cannot be forged toomany times,because the strength will decrease with the time increasing of heating and forging, especially when the heating temperature before forging is high and the time of reserving is long.Therefore, the time of forging for magnesium alloy in the process of forging compression should be controlled as short as possible[4].Extrusion perform closed molding forming process is a new near/net-shape technology developed based on the principles of plastic forming of magnesium alloy.On this basis, this work concerns the evolution of microstructure and texture of magnesium alloy during close net-shape pressing of extruded perform AZ61 magnesium alloy by using the technology of EBSD.The alloy used in the present study was AZ61 Mg alloy with the chemical composition listed in Table1.The alloy was supplied in the form of semi-continuouscast ingot with geometry of d 112 mm×250 mm.The ingot was homogenized at 385 ˚C for 12 h, and then extruded by the XJ-800T horizontal extruder for the profiles, with the parameters of temperature 385 ˚C,holding time 4 h, extrusion ratio 32 and extrusion speed 13-17 mm/s.The samples with a gauge geometry of 99.6 mm×9.0 mm for pressing were sectioned from the profiles by wire electric discharge machine, then were heated to the temperature of 400 ˚C in an electric resistance furnace for 12 min.As the self-made die was preheated to the same temperature, the pressing process can be carried out on 200 t forging machine.The pressing direction is perpendicular to the section at the speed of 5-17 mm/s with deformation rates of 10%, 30%,50%, 60%, respectively.The pressed samples were then air cooled and trimmed.Theschematic diagram of the processes is shown in Fig.1.The metallographic specimens of as-cast and heat treated states were sectioned from the billet at R/2 of its central line.They were firstly ground by abrasive papers,mechanically polished and chemically etched for 5-30 s using the solution of picric acid (3 g)+acetic acid (20 mL)+C2H5OH(50 mL) H2O (20 mL).The microstructure was observed by optical microscopy (OM).The specimens as-extruded and as-die pressed with different rates were sectioned as shown in Fig.2, then ground and electropolished for EBSD test in the material testing centre at Chongqing University.The microstructures of as-cast and solution treated at 400 ˚C AZ61 are represented in Figs.3(a) and (b)respectively.The as-cast AZ61 is character ized by α-Mg and intermetallic network phase β-Mg17Al12 distributed along the grain boundaries, which is produced by divorced eutectic phase.Such microstructure is typical in as-cast Mg-Al series, marked by image analysis as secondary dendrite arm with spacing of 35 µm.In Fig.3(b) uniform single phase is presented due to β-phase remelting into α-Mg after solution treatment at 400 ˚C for 12 h, and its average grain size are 110 µm.The microstructures of as-extruded AZ61 and as-die pressed with different rates are shown in Fig.4.It can be seen from Fig.4(a) that significant dynamic recrystallization(DRX) takes place during extrusion process, and coarse grain is replaced by finer equiaxed grain with average size of 3.5 µm.When the as-extruded sample is pressed in the die at 400 ˚C with deformation rate 10%, the average size of finer equiaxed grain tends to increase to 6µm.DRX is almost completed as the deformation rateincreases, and the recrystallized grains are distributed parallel to the pressing direction and rotated along the boundaries.When the deformation rate is within 30%,the average grain size is 2-3 µm, whereas the rate reaches 50%-60%, the grain size is decreased to 1-2.5µm, and the recrystallized grains of AZ61 magnesium alloy are elongated or crushed and present on “S”streamlines, as shown in Fig.5.At a certain deformation temperature and small deformation degree, distrotional energy of metal material is relatively small even without enough recrystallization energy, so the grain size of alloy does not change obviously, while the deformation rates arrive at a certain value (2%-10%)[5], the grain size tends to increase with small deformation rate (10%) under 400˚C.The average recrystallized grain size can be expressed byd=K(G/N)1/4, where G is the linear velocity of growth, N is the nucleation rate, K is the proportional factor.The recrystallized grain size is determined by the ratio of G/N.The ratio of G/N is relatively small with small deformation rate, so the deformation rate of AZ61 alloy is 10%, which grows up apparently.With increasing deformation rate, distrotional energy of metal material raises too, G and N increase at the same time, but the increment rate of N is greater than the increment rate of G, which resultsin the rate of G/N reduce and grain size is refined, while deformation rate reaches up to 50%-60%, the increment rate of N and increment rate of G are basically analogous and the recrystallized grain size of alloys basically tends to be stable.Texture and grain orientation of AZ61 magnesium alloy during as-extruded and as-die pressing of extruded preformed with different rates are illustrated in Figs.6(a)-(b).Grain boundary sliding has little influence on grain orientation, and texture formation is caused by intracrystalline plastic slip.Generally, the deformation during hot processing is also caused by texture, and various types of texture represent different deformation mechanisms[6].Studies[7-11] have shown that a strong basal texture (0001) is formed as a result of basal slip and pyramidal twinning in magnesium alloys during rolling.Fig.6(a) is characterized by initial texture formed in extruded preforming, and the initial orientation is at basal texture {0001}<100> located in the centre of pole figure (Y0), while the basal texture is symmetrical and parallel to extrusion direction (ED), whereas minute quantity of grains is along prismatic plane (10)parallel to ED, and the maximum texture intensity is 15.37 and the peak value of misorientation of grain is 28˚-38˚.Texture and grain or ientation vary significantly with deformation rate increment, whereas texture intensity decreases.It can be seen from Figs.6(b)-(c) that basal texture {0001}<10> of initial orientation deviates from Y0 with a certain angle, and texture intensity is 5.48, 6.84, 9.62, 9.30 respectively.Themaximum texture intensity can be obtained when deformation rate of pressing reaches up to 50%, and further deformation leads to texture intensity decrease.The deformation texture mechanism of magnesium alloys is caused by grain rotation under external stress,and differs as stress changes.In the extrusion process, the state of plane stress is tensile in extrusiondirection(ED) and compressed in normal direction (ND), and the initial basal texture{0001}<100> is parallel to ED, as shown in Fig.7(a).Initial deformation for specimens in hot pressing process of AZ61 is similar to uniaxial compression, and only transverse deformation takes place, whereas longitudinal size remains the same.Further deformation leads to metallic flow in transverse direction under three-dimensional compressive stress. Because width/height ratio is 4, deformation instability occurred in initial pressing, and the shear stress incurs irregular metallic flow, which is illustrated in Ⅱ and Ⅲ zones in Fig.5.Meanwhile, the shear stress also leads to grain rotation along boundaries with certain angles, and basal texture and grain orientation are easily perceived with increasing deformation.The strong basal fiber texture formed during extrusion gives rise to weak basal texture intensity at the beginning of pressing process, so the basal slip and pyramidal twinning cannot effort under normal compressive stress. Therefore, further deformation can be easily conducted, which, in contrast,leads to fiber texture[12]intensified.Simultaneously, the basal preferential orientation deviates from extrusion direction and aligns with the main pressing and deformation direction under three-dimensional compressive stress, as shown inFig.7(b).1) The average size of as-extruded grain is 3.5 µm,while the grain afterhot-pressing is significantly refined.And the average size of grains is 6 µm which tends to increase with small deformation.As deformation rate is 30%, the average size of grains is 2-3 µm, whereas the def ormation rate reachesup to 50%-60%, the size is decreased to 1-2.5 µm and tends to be stable, but grain refined are not obvious.2) The profiles of extruded preforming is dominantly on basal texture {0001}<10>, and the basal plane is parallel to extrusion direction (ED).As deformation continues, the inner shear stress gives rise to grain rotation along boundaries with certain angles and initial basal texture and grain orientation vary remarkably,though the texture intensity is weaker than that as-extruded.The basal preferential orientation deviates from extrusion direction and aligns with the pressing direction.【相关文献】[1] KANG H T, OSTROM T.Mechanical behavior of cast and forged magnesium alloys and their microstructures [J].Materials Science and Engineering A, 2008, 49(1/2): 52-56.[2] GUAN S K, WU L H, WANG P.Hot forgeability and die-forging forming of semi-continuous casting AZ70 Mg-alloy [J].Materials Science and Engineering A, 2009, 499(1/2): 187-191.[3] WU Li-hong, GUAN Shao-kang, WANG Li-guo, LIU Jun.Wrought magnesium alloys and several key factors affecting the forging forming [J].Forging Technology.2006, 31(4): 7-10.(in Chinese)[4] LONG Si-yuan, CAO Feng-hong, LIAO Hui-min.A compound forming method of magnesium 200810069225.7[P].2008-01-10.[5] CUI Zhong-qi.Metallurgy and heat treatment [M].2006: 1.[6] YANG Ping, REN Xue-ping, ZHAO Zu-de.Microstructures and textures in hot deformed and annealed AZ31 magnesium alloy [J].Transactions of Materials and Heat Treatment, 2003, 12(4): 12-17.(in Chinese)[7] MYAGCHILOV S, DAWSON P R.Evolution of texture in aggregates of crystals exhibiting both slip and twinning [J].Modelling and Simulation in Materials Science and Engineering,1999, 7: 975-1004.[8] WAGNER L, HILPERT M, WENDT J.On methods for improving the fatigue performance of the wrought magnesium alloys AZ31 and AZ80 [J].Materials Science Forum, 2003,419/422: 93-102.[9] KALIDINDI S R.Modeling anisotropic strain hardening and deformation textures in low stacking fault energy materials [J].International Journal of Plasticity, 2001, 17: 837-860. [10] CHRISTIANJ W, MAHAJAN S.Deformation twinning [J].Progress in Materials Science, 1995, 39: 1-157.[11] POSS R.Sheet metal production of magnesium [J].Materials Science Forum, 2003, 419/422: 327-336.[12] VALLE J A, PRADO M T, RUANO O A.Texture evolution during large strain hot rolling of the AZ61 Mg alloy [J].Materials Science and Engineering A, 2003, 355: 68-78.。
焊接过程中的热循环对材料性能的影响

焊接过程中的热循环对材料性能的影响在现代制造业中,焊接是一种广泛应用的连接工艺。
然而,在焊接过程中,材料会经历复杂的热循环,这对材料的性能产生了显著的影响。
了解这些影响对于确保焊接结构的质量和可靠性至关重要。
焊接过程中的热循环是指在焊接时,焊件上某一点的温度随着时间的变化而经历的升温、高温停留和降温的过程。
这种热循环具有快速加热和冷却的特点,与传统的热处理过程有很大的不同。
热循环对材料的微观组织产生了直接的影响。
在加热阶段,材料内部的晶粒会发生长大。
当温度升高到相变温度以上时,还会发生相变,如奥氏体化。
在高温停留阶段,相变过程会进一步发展,并且可能导致合金元素的扩散和重新分布。
而在快速冷却阶段,新的相变产物形成,可能会产生马氏体、贝氏体等硬脆相。
对于金属材料来说,热循环会改变其力学性能。
一般而言,焊接热影响区(HAZ)的硬度会比母材高。
这是因为快速冷却导致了硬脆相的形成,使得材料的脆性增加。
同时,热循环还可能导致材料的强度和韧性发生变化。
在某些情况下,焊接接头的强度可能高于母材,但韧性却下降,这增加了焊接结构在使用过程中发生脆性断裂的风险。
热循环对材料的耐腐蚀性也有影响。
焊接过程中产生的微观组织变化和残余应力可能会破坏材料表面的钝化膜,使得材料更容易受到腐蚀介质的侵蚀。
特别是在一些恶劣的环境中,如海洋环境或化学工业环境,焊接接头的腐蚀问题更为突出。
此外,热循环还会引起焊接残余应力的产生。
残余应力是在焊接过程中由于不均匀的加热和冷却而在焊件内部残留的应力。
这些残余应力可能会导致焊件的变形、开裂,甚至影响其疲劳寿命。
在一些大型焊接结构中,如桥梁、压力容器等,残余应力的控制是至关重要的。
为了减轻焊接热循环对材料性能的不利影响,可以采取一些措施。
例如,选择合适的焊接工艺和参数,如控制焊接电流、电压、焊接速度等,以优化热循环曲线。
此外,焊前预热和焊后热处理也是常用的方法。
预热可以降低焊接时的冷却速度,减少硬脆相的形成;焊后热处理则可以消除残余应力,改善微观组织和性能。
影响焊接接头组织与性能的因素分析
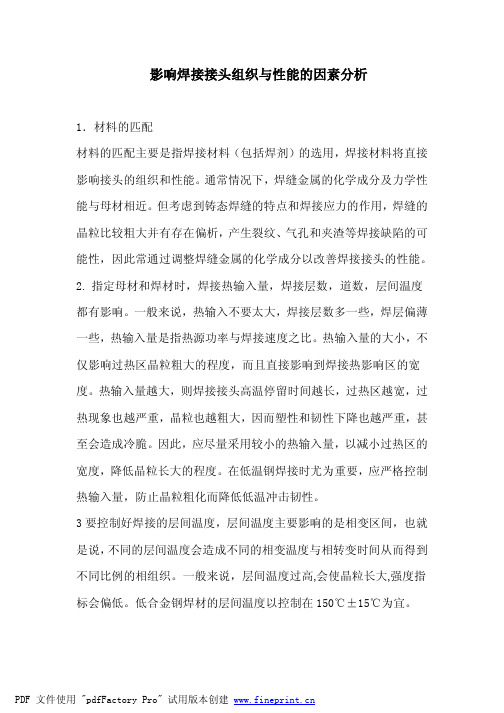
影响焊接接头组织与性能的因素分析1.材料的匹配材料的匹配主要是指焊接材料(包括焊剂)的选用,焊接材料将直接影响接头的组织和性能。
通常情况下,焊缝金属的化学成分及力学性能与母材相近。
但考虑到铸态焊缝的特点和焊接应力的作用,焊缝的晶粒比较粗大并有存在偏析,产生裂纹、气孔和夹渣等焊接缺陷的可能性,因此常通过调整焊缝金属的化学成分以改善焊接接头的性能。
2. 指定母材和焊材时,焊接热输入量,焊接层数,道数,层间温度都有影响。
一般来说,热输入不要太大,焊接层数多一些,焊层偏薄一些,热输入量是指热源功率与焊接速度之比。
热输入量的大小,不仅影响过热区晶粒粗大的程度,而且直接影响到焊接热影响区的宽度。
热输入量越大,则焊接接头高温停留时间越长,过热区越宽,过热现象也越严重,晶粒也越粗大,因而塑性和韧性下降也越严重,甚至会造成冷脆。
因此,应尽量采用较小的热输入量,以减小过热区的宽度,降低晶粒长大的程度。
在低温钢焊接时尤为重要,应严格控制热输入量,防止晶粒粗化而降低低温冲击韧性。
3要控制好焊接的层间温度,层间温度主要影响的是相变区间,也就是说,不同的层间温度会造成不同的相变温度与相转变时间从而得到不同比例的相组织。
一般来说,层间温度过高,会使晶粒长大,强度指标会偏低。
低合金钢焊材的层间温度以控制在150℃±15℃为宜。
4另外每一焊道间一定要清理干净,见金属光泽。
如果是不锈钢,还应注意冷却速率,注意t-800/500区间不能停留太久。
5.熔合比熔合比是指在焊缝金属中局部熔化的母材所占的比例。
熔合比对焊缝性能的影响与焊接材料和母材的化学成分有关。
当焊接材料与母材的化学成分基本相近且熔池保护良好时,熔合比对焊缝的熔合区的性能没有明显的影响。
当焊接材料与母材的化学成分不同时,如碳、合金元素和硫、磷等杂质元素的含量不同,那么,在焊缝中紧邻熔合区的部位化学成分变化比较大,变化的幅度与焊接材料同母材间化学成分的差异及熔合比有关。
cmsx-4单晶高温合金在不同温度下的低周疲劳行为

cmsx-4单晶高温合金在不同温度下的低周疲劳行为CMSX-4是一种单晶高温合金,具有优异的高温力学性能。
在高温下,它具有很高的强度和良好的抗氧化性能,能够承受高温高应力的作用。
然而,在长时间的高温作用下,CMSX-4会出现低周疲劳现象,降低了其使用寿命。
因此,在工程实践中,了解CMSX-4的低周疲劳行为十分重要。
低周疲劳是指在应力循环次数较少的情况下,由于材料内部微观组织的破坏而造成的失效。
通常,低周疲劳的应力循环次数小于10^4次。
这种失效机制通常发生在高温下,包括高温松弛、晶间裂纹扩展、位错滑移、局部塑性变形等。
CMSX-4在高温下的低周疲劳行为主要受以下因素的影响:1.温度:温度是影响低周疲劳行为的重要因素之一。
通常情况下,随着温度的升高,材料的强度和韧性都会降低,低周疲劳寿命也会减少。
当温度接近材料的熔点时,材料的疲劳寿命会急剧降低。
2.应力幅值:应力幅度是另一个影响低周疲劳行为的重要因素。
随着应力幅度的增加,材料的疲劳寿命会急剧下降。
当应力幅度超过临界值时,材料会发生塑性变形和裂纹扩展,导致失效。
3.微观组织:微观组织是影响低周疲劳行为的重要因素之一。
CMSX-4采用高温下的单晶铸造工艺制造,具有优异的晶体结构和均匀的结构性能。
这种组织结构有效地防止了裂纹的形成和扩展。
4.环境:环境条件也会对CMSX-4的低周疲劳行为产生影响。
在氧化性环境下,材料的抗氧化性能会受到影响,导致材料的疲劳寿命减少。
综上所述,了解CMSX-4的低周疲劳行为对于保证材料在高温高应力环境下的长期可靠性具有重要意义。
在实际应用中,可以通过优化温度、应力幅度和微观组织等因素来提高CMSX-4的低周疲劳寿命,保证其可靠性和安全性。
镁钢TIG熔钎焊夹层及焊后热处理对接头组织与性能的影响
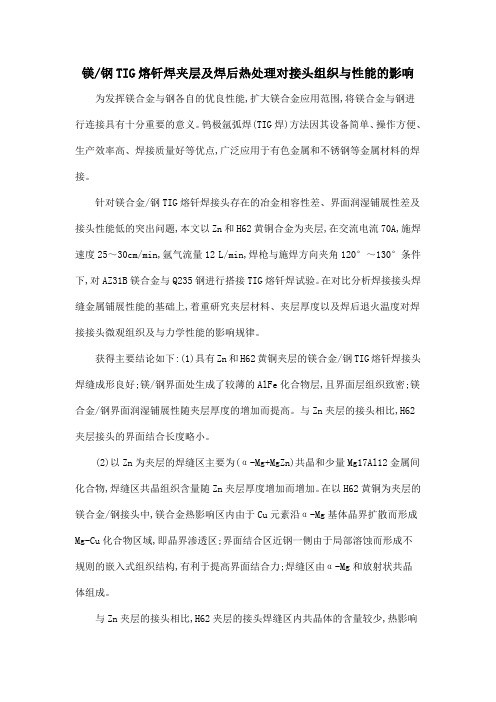
镁/钢TIG熔钎焊夹层及焊后热处理对接头组织与性能的影响为发挥镁合金与钢各自的优良性能,扩大镁合金应用范围,将镁合金与钢进行连接具有十分重要的意义。
钨极氩弧焊(TIG焊)方法因其设备简单、操作方便、生产效率高、焊接质量好等优点,广泛应用于有色金属和不锈钢等金属材料的焊接。
针对镁合金/钢TIG熔钎焊接头存在的冶金相容性差、界面润湿铺展性差及接头性能低的突出问题,本文以Zn和H62黄铜合金为夹层,在交流电流70A,施焊速度25~30cm/min,氩气流量12 L/min,焊枪与施焊方向夹角120°~130°条件下,对AZ31B镁合金与Q235钢进行搭接TIG熔钎焊试验。
在对比分析焊接接头焊缝金属铺展性能的基础上,着重研究夹层材料、夹层厚度以及焊后退火温度对焊接接头微观组织及与力学性能的影响规律。
获得主要结论如下:(1)具有Zn和H62黄铜夹层的镁合金/钢TIG熔钎焊接头焊缝成形良好;镁/钢界面处生成了较薄的AlFe化合物层,且界面层组织致密;镁合金/钢界面润湿铺展性随夹层厚度的增加而提高。
与Zn夹层的接头相比,H62夹层接头的界面结合长度略小。
(2)以Zn为夹层的焊缝区主要为(α-Mg+MgZn)共晶和少量Mg17Al12金属间化合物,焊缝区共晶组织含量随Zn夹层厚度增加而增加。
在以H62黄铜为夹层的镁合金/钢接头中,镁合金热影响区内由于Cu元素沿α-Mg基体晶界扩散而形成Mg-Cu化合物区域,即晶界渗透区;界面结合区近钢一侧由于局部溶蚀而形成不规则的嵌入式组织结构,有利于提高界面结合力;焊缝区由α-Mg和放射状共晶体组成。
与Zn夹层的接头相比,H62夹层的接头焊缝区内共晶体的含量较少,热影响区的α-Mg晶粒细小;随H62夹层厚度增加,镁合金母材的晶界渗透区宽度增大。
(3)具有Zn和H62黄铜夹层的镁合金/钢TIG熔钎焊接头焊缝区的显微硬度均高于母材,且随夹层厚度增加,硬度升高愈烈。
焊接热循环对焊接接头组织与性能的影响分析

焊接热循环对焊接接头组织与性能的影响分析焊接是一种常见的金属连接方法,通过加热和冷却来使金属材料相互结合。
焊接热循环是指焊接过程中金属材料所经历的加热和冷却的循环过程。
这个循环过程对焊接接头的组织和性能有着重要的影响。
首先,焊接热循环会对焊接接头的组织结构产生影响。
焊接过程中,焊接接头会经历高温和低温的循环,这会导致金属材料的晶粒尺寸发生变化。
在高温下,晶粒会长大,而在低温下则会细化。
这种晶粒尺寸的变化会影响焊接接头的力学性能。
晶粒细化可以提高焊接接头的强度和韧性,而晶粒粗化则会降低其力学性能。
因此,焊接热循环对焊接接头的晶粒尺寸有着直接的影响。
其次,焊接热循环还会对焊接接头的残余应力产生影响。
焊接过程中,金属材料会经历热胀冷缩的过程,从而产生残余应力。
这些残余应力可能会导致焊接接头产生变形、裂纹等缺陷。
焊接热循环的循环次数和温度变化幅度都会对残余应力产生影响。
循环次数越多、温度变化幅度越大,残余应力就越大。
因此,在焊接过程中需要合理控制焊接热循环,以减小残余应力对焊接接头的影响。
此外,焊接热循环还会对焊接接头的晶体结构产生影响。
焊接过程中,金属材料的晶体结构可能会发生相变。
相变会改变金属材料的晶体结构和性质,从而影响焊接接头的性能。
例如,某些金属在焊接过程中可能发生固溶体析出现象,导致焊接接头的硬度发生变化。
此外,相变还可能导致焊接接头的晶体结构发生变化,从而影响其力学性能。
因此,在焊接过程中需要考虑焊接热循环对晶体结构的影响,以保证焊接接头的性能。
最后,焊接热循环还会对焊接接头的耐腐蚀性能产生影响。
焊接过程中,金属材料会经历高温和低温的循环,这可能会导致焊接接头的耐腐蚀性能发生变化。
例如,某些金属在高温下容易发生氧化反应,从而降低其耐腐蚀性能。
此外,焊接热循环还可能导致焊接接头的组织结构发生变化,从而影响其耐腐蚀性能。
因此,在焊接过程中需要注意焊接热循环对焊接接头的耐腐蚀性能的影响。
综上所述,焊接热循环对焊接接头的组织和性能有着重要的影响。
焊接工艺对合金材料性能的影响研究
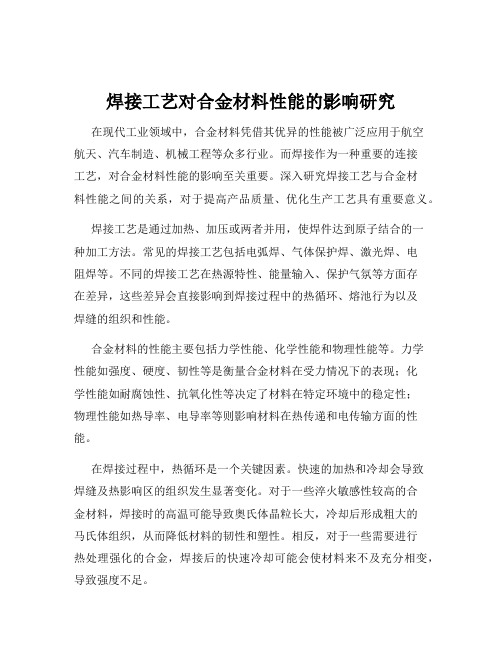
焊接工艺对合金材料性能的影响研究在现代工业领域中,合金材料凭借其优异的性能被广泛应用于航空航天、汽车制造、机械工程等众多行业。
而焊接作为一种重要的连接工艺,对合金材料性能的影响至关重要。
深入研究焊接工艺与合金材料性能之间的关系,对于提高产品质量、优化生产工艺具有重要意义。
焊接工艺是通过加热、加压或两者并用,使焊件达到原子结合的一种加工方法。
常见的焊接工艺包括电弧焊、气体保护焊、激光焊、电阻焊等。
不同的焊接工艺在热源特性、能量输入、保护气氛等方面存在差异,这些差异会直接影响到焊接过程中的热循环、熔池行为以及焊缝的组织和性能。
合金材料的性能主要包括力学性能、化学性能和物理性能等。
力学性能如强度、硬度、韧性等是衡量合金材料在受力情况下的表现;化学性能如耐腐蚀性、抗氧化性等决定了材料在特定环境中的稳定性;物理性能如热导率、电导率等则影响材料在热传递和电传输方面的性能。
在焊接过程中,热循环是一个关键因素。
快速的加热和冷却会导致焊缝及热影响区的组织发生显著变化。
对于一些淬火敏感性较高的合金材料,焊接时的高温可能导致奥氏体晶粒长大,冷却后形成粗大的马氏体组织,从而降低材料的韧性和塑性。
相反,对于一些需要进行热处理强化的合金,焊接后的快速冷却可能会使材料来不及充分相变,导致强度不足。
焊缝的化学成分也是影响合金材料性能的重要因素。
在焊接过程中,由于母材和填充材料的混合、元素的烧损以及气体的侵入等,焊缝的化学成分可能会与母材有所不同。
例如,在不锈钢的焊接中,如果焊缝中的铬含量降低,会削弱其耐腐蚀性。
此外,焊接过程中产生的气孔、夹渣等缺陷也会降低焊缝的力学性能和化学性能。
焊接工艺参数如焊接电流、电压、焊接速度、焊接角度等对合金材料性能有着显著的影响。
焊接电流和电压决定了焊接热源的能量输入,从而影响焊缝的熔深、熔宽和热影响区的大小。
焊接速度过快可能导致焊缝未熔合、气孔等缺陷;焊接速度过慢则会使热影响区过大,降低材料性能。
焊接工艺对微合金钢焊接接头组织性能的影响

焊接工艺对微合金钢焊接接头组织性能的影响
焊接工艺是指在焊接过程中所采用的操作方法、设备、参数和焊接材料等综合技术措施。
微合金钢是一种添加微量合金元素的中碳钢,具有良好的焊接性能和优异的力学性能。
焊接工艺对微合金钢焊接接头的组织性能具有重要的影响。
焊接工艺对接头的热影响区(HAZ)和焊缝金属(WZ)的晶粒尺寸和晶粒形貌有影响。
合理选择焊接工艺可以控制热输入量和焊接速度,从而控制HAZ的尺寸和形貌。
过高的焊
接热输入会导致HAZ区域过大和晶粒变大,使材料的韧性和抗冷裂性能下降。
通过选择适
当的焊接工艺参数,可以得到较小的HAZ区域和细小的晶粒,提高接头的韧性和抗冷裂性能。
焊接工艺对接头的相组成和相形貌有影响。
焊接过程中,由于瞬态热循环的作用,会
导致接头区域的相变,影响接头的组织性能。
焊接工艺参数的选择会导致相的种类和含量
的变化,进而影响接头的力学性能和腐蚀性能。
通过合理选择焊接工艺参数,可以得到较
少的硬质相形成,提高接头的韧性和耐蚀性。
焊接工艺对微合金钢焊接接头的组织性能具有重要的影响。
合理选择焊接工艺参数可
以控制HAZ的尺寸和晶粒形貌,调控相的组成和形貌,减小焊接残余应力和变形,从而提
高接头的韧性、抗冷裂性能、耐蚀性和外观质量。
在实际应用中,需要根据具体情况选择
合适的焊接工艺,以保证微合金钢焊接接头的性能要求。
焊接工艺对接头微观组织与性能的影响分析

焊接工艺对接头微观组织与性能的影响分析引言:焊接是一种常见的金属连接方法,广泛应用于工业生产中。
然而,焊接工艺的选择和控制对接头的微观组织和性能具有重要影响。
本文将分析焊接工艺对接头微观组织和性能的影响,并探讨如何优化焊接工艺以提高接头质量。
一、焊接工艺对接头组织的影响1. 熔化区组织:焊接过程中,熔化区是焊接接头的关键部位。
焊接工艺的选择和控制会直接影响熔化区的组织。
例如,焊接电流和焊接速度的调节会影响熔化区的晶粒尺寸和形态。
较高的焊接电流和较快的焊接速度会导致较大的熔化区晶粒,降低接头的强度和韧性。
2. 热影响区组织:焊接过程中,除了熔化区外,热影响区也是焊接接头的重要部分。
焊接工艺的热输入和冷却速度会对热影响区的组织产生影响。
较高的热输入和较慢的冷却速度会导致热影响区的晶粒长大和相变,使接头的硬度增加,降低了韧性。
3. 金属间化合物形成:在某些焊接过程中,焊接材料和基材之间会发生金属间化合物的形成。
焊接工艺的选择和控制会影响金属间化合物的形成和分布。
适当的焊接工艺可以促进金属间化合物的均匀分布,提高接头的强度和耐腐蚀性。
二、焊接工艺对接头性能的影响1. 强度:焊接工艺的选择和控制对接头的强度具有重要影响。
适当的焊接工艺可以获得较高的焊缝强度,提高接头的承载能力。
而错误的焊接工艺选择和控制会导致焊缝强度降低,影响接头的使用寿命。
2. 韧性:焊接工艺的选择和控制也会对接头的韧性产生影响。
适当的焊接工艺可以获得较好的韧性,使接头在受到冲击或振动时能够具有一定的变形和吸能能力。
而错误的焊接工艺选择和控制会导致接头的脆性增加,容易发生断裂。
3. 耐腐蚀性:焊接工艺的选择和控制还会对接头的耐腐蚀性产生影响。
适当的焊接工艺可以避免焊接缺陷和金属间化合物的不均匀分布,提高接头的耐腐蚀性。
而错误的焊接工艺选择和控制会导致接头的腐蚀敏感区域增加,降低了接头的耐腐蚀性能。
三、优化焊接工艺以提高接头质量1. 选择合适的焊接方法:不同的焊接方法适用于不同的材料和应用场景。
高温真空钎焊炉中焊接接头的增强技术与结构优化方法
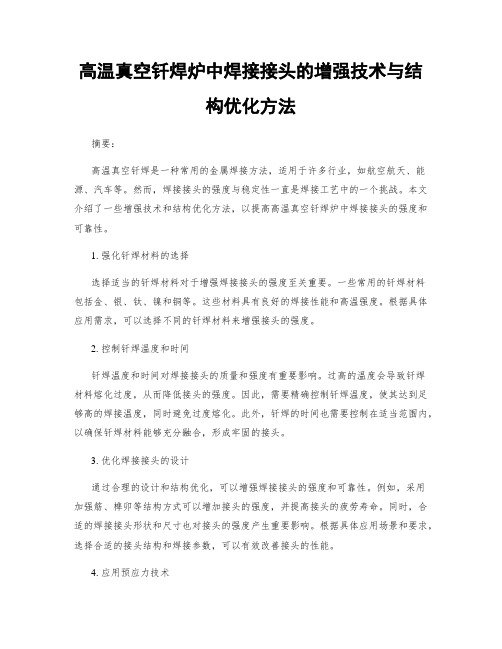
高温真空钎焊炉中焊接接头的增强技术与结构优化方法摘要:高温真空钎焊是一种常用的金属焊接方法,适用于许多行业,如航空航天、能源、汽车等。
然而,焊接接头的强度与稳定性一直是焊接工艺中的一个挑战。
本文介绍了一些增强技术和结构优化方法,以提高高温真空钎焊炉中焊接接头的强度和可靠性。
1. 强化钎焊材料的选择选择适当的钎焊材料对于增强焊接接头的强度至关重要。
一些常用的钎焊材料包括金、银、钛、镍和铜等。
这些材料具有良好的焊接性能和高温强度。
根据具体应用需求,可以选择不同的钎焊材料来增强接头的强度。
2. 控制钎焊温度和时间钎焊温度和时间对焊接接头的质量和强度有重要影响。
过高的温度会导致钎焊材料熔化过度,从而降低接头的强度。
因此,需要精确控制钎焊温度,使其达到足够高的焊接温度,同时避免过度熔化。
此外,钎焊的时间也需要控制在适当范围内,以确保钎焊材料能够充分融合,形成牢固的接头。
3. 优化焊接接头的设计通过合理的设计和结构优化,可以增强焊接接头的强度和可靠性。
例如,采用加强筋、榫卯等结构方式可以增加接头的强度,并提高接头的疲劳寿命。
同时,合适的焊接接头形状和尺寸也对接头的强度产生重要影响。
根据具体应用场景和要求,选择合适的接头结构和焊接参数,可以有效改善接头的性能。
4. 应用预应力技术预应力技术是一种常用的增强焊接接头强度的方法。
通过在接头中引入预应力,可以使接头在负载作用下保持内部张力状态,提高其承载能力和抗疲劳性能。
预应力技术对于大型结构和长期使用的接头尤为重要,在设计和制造中应充分考虑并应用预应力技术。
5. 优化焊接工艺参数焊接工艺参数的优化对焊接接头的性能改善至关重要。
通过调整焊接电流、压力和速度等参数,可以控制焊接过程中的热输入和冷却速度,从而影响接头的组织和性能。
优化焊接工艺参数可以提高接头的强度、韧性和抗疲劳性能。
结论:高温真空钎焊炉中焊接接头的增强技术和结构优化方法对于提高接头的强度和可靠性至关重要。
焊接工艺对接头性能的影响分析

焊接工艺对接头性能的影响分析在现代制造业中,焊接作为一种重要的连接技术,广泛应用于汽车、航空航天、船舶、建筑等众多领域。
焊接接头的性能直接关系到整个结构的质量和可靠性。
不同的焊接工艺会对接头的性能产生显著的影响,深入了解这些影响对于优化焊接工艺、提高焊接质量具有重要意义。
焊接工艺的种类繁多,常见的有电弧焊、气体保护焊、电阻焊、激光焊等。
每种焊接工艺都有其独特的特点和适用范围。
电弧焊是一种传统且广泛应用的焊接方法。
在电弧焊中,通过电弧产生的高温使焊件局部熔化,形成焊缝。
这种焊接工艺操作相对简单,成本较低,但焊接过程中的热输入较大,容易导致接头区域的热影响区变宽,从而影响接头的力学性能。
热影响区的组织和性能可能会发生变化,例如晶粒长大、硬度降低等。
此外,电弧焊的焊缝中可能会存在气孔、夹渣等缺陷,影响接头的密封性和强度。
气体保护焊则是在电弧周围通过气体形成保护氛围,防止焊缝金属被氧化和污染。
常见的气体有氩气、二氧化碳等。
相比电弧焊,气体保护焊的焊接质量较高,焊缝成形美观,缺陷较少。
由于热输入相对较小,热影响区也相对较窄,对接头性能的不利影响较小。
然而,气体保护焊的设备成本较高,对操作技术要求也较高。
电阻焊是利用电流通过焊件时产生的电阻热进行焊接的方法。
这种焊接工艺效率高,适合大批量生产,但焊接接头的厚度通常有限,且焊接后的接头表面可能会有压痕。
激光焊是一种先进的焊接技术,具有高能量密度、高精度、热影响区小等优点。
由于激光束的聚焦性好,能够实现微小焊缝的精确焊接,对焊件的热影响极小,因此接头的性能往往较为优异。
但激光焊设备昂贵,成本较高,限制了其在一些领域的广泛应用。
焊接工艺参数也是影响接头性能的重要因素。
焊接电流、电压、焊接速度、焊接角度等参数的选择直接关系到焊缝的形状、尺寸、组织和性能。
焊接电流过大时,会导致焊缝熔深增加,但同时也会使热影响区扩大,接头的残余应力增大,可能会引起变形和裂纹等问题。
焊接电流过小,则焊缝熔深不足,容易出现未焊透等缺陷。
温度对混合焊接工艺稳定性的影响分析
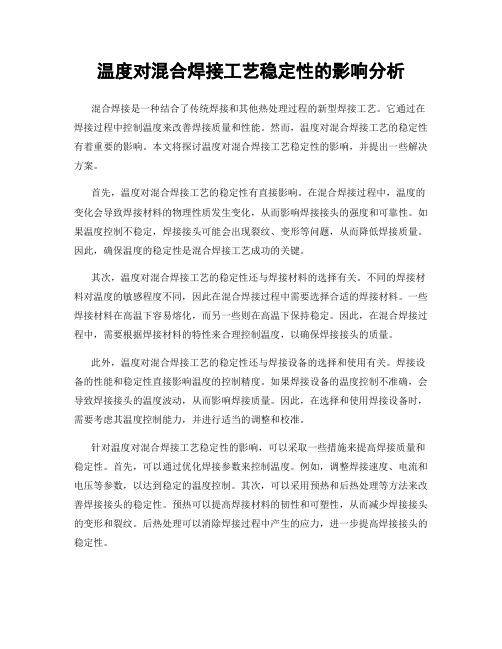
温度对混合焊接工艺稳定性的影响分析混合焊接是一种结合了传统焊接和其他热处理过程的新型焊接工艺。
它通过在焊接过程中控制温度来改善焊接质量和性能。
然而,温度对混合焊接工艺的稳定性有着重要的影响。
本文将探讨温度对混合焊接工艺稳定性的影响,并提出一些解决方案。
首先,温度对混合焊接工艺的稳定性有直接影响。
在混合焊接过程中,温度的变化会导致焊接材料的物理性质发生变化,从而影响焊接接头的强度和可靠性。
如果温度控制不稳定,焊接接头可能会出现裂纹、变形等问题,从而降低焊接质量。
因此,确保温度的稳定性是混合焊接工艺成功的关键。
其次,温度对混合焊接工艺的稳定性还与焊接材料的选择有关。
不同的焊接材料对温度的敏感程度不同,因此在混合焊接过程中需要选择合适的焊接材料。
一些焊接材料在高温下容易熔化,而另一些则在高温下保持稳定。
因此,在混合焊接过程中,需要根据焊接材料的特性来合理控制温度,以确保焊接接头的质量。
此外,温度对混合焊接工艺的稳定性还与焊接设备的选择和使用有关。
焊接设备的性能和稳定性直接影响温度的控制精度。
如果焊接设备的温度控制不准确,会导致焊接接头的温度波动,从而影响焊接质量。
因此,在选择和使用焊接设备时,需要考虑其温度控制能力,并进行适当的调整和校准。
针对温度对混合焊接工艺稳定性的影响,可以采取一些措施来提高焊接质量和稳定性。
首先,可以通过优化焊接参数来控制温度。
例如,调整焊接速度、电流和电压等参数,以达到稳定的温度控制。
其次,可以采用预热和后热处理等方法来改善焊接接头的稳定性。
预热可以提高焊接材料的韧性和可塑性,从而减少焊接接头的变形和裂纹。
后热处理可以消除焊接过程中产生的应力,进一步提高焊接接头的稳定性。
综上所述,温度对混合焊接工艺的稳定性具有重要影响。
通过控制温度、选择合适的焊接材料和使用稳定的焊接设备,可以提高混合焊接工艺的稳定性和焊接质量。
此外,采取预热和后热处理等措施也可以进一步提高焊接接头的稳定性。
钎焊的温度

钎焊的温度【原创版】目录一、钎焊的概述二、钎焊的温度范围三、钎焊温度的影响因素四、钎焊温度的控制方法五、结论正文一、钎焊的概述钎焊是一种常见的金属连接方法,它是通过加热使钎料熔化,填充在待连接的金属零件之间,然后冷却凝固,从而使金属零件连接在一起的过程。
钎焊具有连接强度高、接头变形小、加工方便等优点,因此在各种金属制品的制造中得到了广泛应用。
二、钎焊的温度范围钎焊的温度范围是指在进行钎焊过程中,所需要加热到的最低温度和最高温度之间的范围。
这个范围的大小,直接影响到钎焊的效果和质量。
钎焊温度过低,钎料无法熔化,无法起到连接作用;钎焊温度过高,会导致钎料烧损,连接强度下降,甚至可能出现焊点脱落的情况。
三、钎焊温度的影响因素钎焊温度的影响因素主要有以下几个:1.钎料的种类:不同的钎料,其熔点不同,所需的钎焊温度也就不同。
2.金属零件的材料:不同的金属材料,其导热系数、比热容等热传导性能不同,对钎焊温度的要求也就不同。
3.焊接厚度:焊接厚度越大,需要的钎焊温度就越高。
4.钎焊设备:不同的钎焊设备,其加热方式和加热效率不同,对钎焊温度的要求也会有所不同。
四、钎焊温度的控制方法要保证钎焊的质量,关键在于控制好钎焊温度。
以下是一些常见的钎焊温度控制方法:1.选择合适的钎料:根据待连接的金属零件的材料和性能要求,选择熔点适中、润湿性好、填充性能好的钎料。
2.设定合适的加热温度:根据钎料的熔点和金属零件的热传导性能,设定合适的加热温度,确保钎料能够在适当的时间内熔化。
3.控制加热速度:加热速度过快,容易导致钎焊温度过高,烧损钎料;加热速度过慢,容易导致钎焊温度不足,钎料无法熔化。
因此,需要根据实际情况,控制好加热速度。
4.实时监测温度:采用温度计等设备,实时监测钎焊过程中的温度变化,以便及时调整加热参数,保证钎焊质量。
高温真空钎焊炉中焊接接头的变形与应力分析
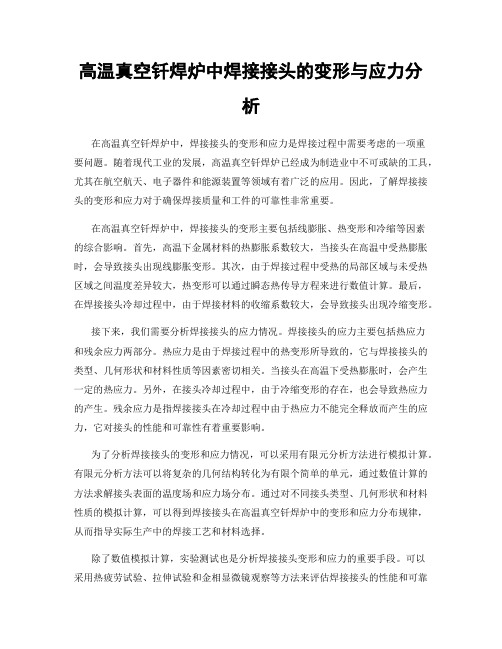
高温真空钎焊炉中焊接接头的变形与应力分析在高温真空钎焊炉中,焊接接头的变形和应力是焊接过程中需要考虑的一项重要问题。
随着现代工业的发展,高温真空钎焊炉已经成为制造业中不可或缺的工具,尤其在航空航天、电子器件和能源装置等领域有着广泛的应用。
因此,了解焊接接头的变形和应力对于确保焊接质量和工件的可靠性非常重要。
在高温真空钎焊炉中,焊接接头的变形主要包括线膨胀、热变形和冷缩等因素的综合影响。
首先,高温下金属材料的热膨胀系数较大,当接头在高温中受热膨胀时,会导致接头出现线膨胀变形。
其次,由于焊接过程中受热的局部区域与未受热区域之间温度差异较大,热变形可以通过瞬态热传导方程来进行数值计算。
最后,在焊接接头冷却过程中,由于焊接材料的收缩系数较大,会导致接头出现冷缩变形。
接下来,我们需要分析焊接接头的应力情况。
焊接接头的应力主要包括热应力和残余应力两部分。
热应力是由于焊接过程中的热变形所导致的,它与焊接接头的类型、几何形状和材料性质等因素密切相关。
当接头在高温下受热膨胀时,会产生一定的热应力。
另外,在接头冷却过程中,由于冷缩变形的存在,也会导致热应力的产生。
残余应力是指焊接接头在冷却过程中由于热应力不能完全释放而产生的应力,它对接头的性能和可靠性有着重要影响。
为了分析焊接接头的变形和应力情况,可以采用有限元分析方法进行模拟计算。
有限元分析方法可以将复杂的几何结构转化为有限个简单的单元,通过数值计算的方法求解接头表面的温度场和应力场分布。
通过对不同接头类型、几何形状和材料性质的模拟计算,可以得到焊接接头在高温真空钎焊炉中的变形和应力分布规律,从而指导实际生产中的焊接工艺和材料选择。
除了数值模拟计算,实验测试也是分析焊接接头变形和应力的重要手段。
可以采用热疲劳试验、拉伸试验和金相显微镜观察等方法来评估焊接接头的性能和可靠性。
通过对焊接接头进行负荷测试和断口分析,可以全面了解接头在不同工况下的力学行为和疲劳寿命。
综上所述,高温真空钎焊炉中焊接接头的变形与应力分析是确保焊接质量和工件可靠性的重要步骤。
2007哈工大—温度对Ti_Ni钎焊C_SiC与Nb接头组织及性能的影响
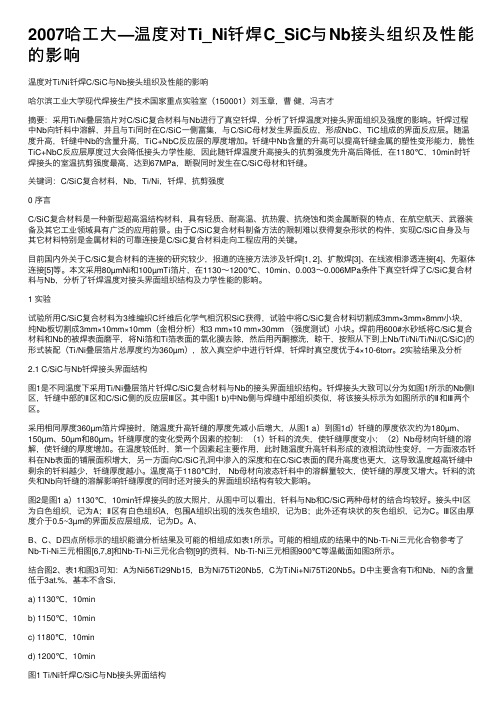
2007哈⼯⼤—温度对Ti_Ni钎焊C_SiC与Nb接头组织及性能的影响温度对Ti/Ni钎焊C/SiC与Nb接头组织及性能的影响哈尔滨⼯业⼤学现代焊接⽣产技术国家重点实验室(150001)刘⽟章,曹健,冯吉才摘要:采⽤Ti/Ni叠层箔⽚对C/SiC复合材料与Nb进⾏了真空钎焊,分析了钎焊温度对接头界⾯组织及强度的影响。
钎焊过程中Nb向钎料中溶解,并且与Ti同时在C/SiC⼀侧富集,与C/SiC母材发⽣界⾯反应,形成NbC、TiC组成的界⾯反应层。
随温度升⾼,钎缝中Nb的含量升⾼,TiC+NbC反应层的厚度增加。
钎缝中Nb含量的升⾼可以提⾼钎缝⾦属的塑性变形能⼒,脆性TiC+NbC反应层厚度过⼤会降低接头⼒学性能,因此随钎焊温度升⾼接头的抗剪强度先升⾼后降低,在1180℃,10min时钎焊接头的室温抗剪强度最⾼,达到67MPa,断裂同时发⽣在C/SiC母材和钎缝。
关键词:C/SiC复合材料,Nb,Ti/Ni,钎焊,抗剪强度0 序⾔C/SiC复合材料是⼀种新型超⾼温结构材料,具有轻质、耐⾼温、抗热震、抗烧蚀和类⾦属断裂的特点,在航空航天、武器装备及其它⼯业领域具有⼴泛的应⽤前景。
由于C/SiC复合材料制备⽅法的限制难以获得复杂形状的构件,实现C/SiC⾃⾝及与其它材料特别是⾦属材料的可靠连接是C/SiC复合材料⾛向⼯程应⽤的关键。
⽬前国内外关于C/SiC复合材料的连接的研究较少,报道的连接⽅法涉及钎焊[1, 2]、扩散焊[3]、在线液相渗透连接[4]、先驱体连接[5]等。
本⽂采⽤80µmNi和100µmTi箔⽚,在1130~1200℃、10min、0.003~0.006MPa条件下真空钎焊了C/SiC复合材料与Nb,分析了钎焊温度对接头界⾯组织结构及⼒学性能的影响。
1 实验试验所⽤C/SiC复合材料为3维编织C纤维后化学⽓相沉积SiC获得,试验中将C/SiC复合材料切割成3mm×3mm×8mm⼩块,纯Nb板切割成3mm×10mm×10mm(⾦相分析)和3 mm×10 mm×30mm (强度测试)⼩块。
- 1、下载文档前请自行甄别文档内容的完整性,平台不提供额外的编辑、内容补充、找答案等附加服务。
- 2、"仅部分预览"的文档,不可在线预览部分如存在完整性等问题,可反馈申请退款(可完整预览的文档不适用该条件!)。
- 3、如文档侵犯您的权益,请联系客服反馈,我们会尽快为您处理(人工客服工作时间:9:00-18:30)。
钎焊温度对CMSX-4单晶高温合金接头组织与性能的影响侯星宇;孙元【摘要】采用一种镍基合金钎料钎焊CMSX-4单晶高温合金, 利用扫描电镜、电子探针等分析手段研究接头的微观组织与相组成, 并利用高温持久试验机测试接头的高温持久性能, 讨论不同钎焊工艺条件下, 接头的组织与性能变化规律及接头的断裂机制.研究发现, 随着钎焊温度的提高, 焊缝中低熔点化合物相减少, 小尺寸凝固缺陷消失, 白色硼化物比例先升高后降低, γ'沉淀相增多, 接头的高温组织稳定性增加.当钎焊温度不低于1 290℃时, CMSX-4单晶高温合金接头在980℃/100 Mpa 条件下的持久寿命可达到400 h.观察接头的断口形貌发现, 断裂均发生在焊缝处, 断裂模式为以脆性断裂为主的混合断裂.%The single crystal superalloy CMSX-4 was brazed with a Ni-based filler alloy, the microstructure and the phase composition were studied by scanning electron microscopy ( SEM), electron probe microanalysis ( EPMA) . The stress rupture property of joint was tested by high temperature stress rupture property testing machine. The result shows that the fracture mechanism and stress rupture property at high temperature of joint transformed with the different brazing temperature. With the increase of brazing temperature, the low melting point eutectic phase and the solidification defect with small size disappears, the proportion of white boron compounds increases firstly and then decreases. Besides, the amount of the precipitated phase and the high temperature structure stability of joint increase. When the brazing temperature is not lower than1 290 ℃, the rupture life of CMSX-4 superalloy under the condition of 980 ℃/100 MPa reac hes up to 400 h.The fracture morphology of joints shows that all the fractures occurred at the weld seam. The fracture mode of joint is the mixed fracture characterized by brittle fracture.【期刊名称】《焊接》【年(卷),期】2019(000)001【总页数】6页(P40-44,后插3)【关键词】单晶高温合金;钎焊;持久性能;镍基合金钎料【作者】侯星宇;孙元【作者单位】中国科学院金属研究所,沈阳 110016;沈阳科金新材料有限公司,沈阳110016;中国科学院金属研究所,沈阳 110016【正文语种】中文【中图分类】TG4540 前言CMSX-4单晶高温合金是国外某公司研制的第二代含铼镍基单晶高温合金,其综合性能优异,现已广泛应用于该国的先进航空发动机中,未来在国内的民用航空发动机上具有广阔的应用前景。
通过开展CMSX-4单晶高温合金连接技术研究,不但可以实现复杂零部件的高性能连接,还可对存在铸造缺陷或服役后的叶片进行修复,有效提高航空发动机可靠性和使用寿命,具有重大应用价值。
分析CMSX-4单晶合金的特性发现,由于该合金含有较高的Al,Ti,W,Ta,Re 等沉淀强化及固溶强化元素,其焊接性较差。
常用的氩弧焊、激光焊、电子束焊接、等离子弧焊等熔焊方法对此类合金进行焊接较易产生裂纹,且由于熔焊过程中母材局部熔化,因而对零件的装配和母材的组织性能均会产生较大影响[1-6]。
真空钎焊技术形状适应性和工艺稳定性较好,钎焊过程中母材不熔化,其焊接热过程对母材组织影响小,工件受热均匀,变形量小,是单晶高温合金最常用的连接方法[7-11]。
目前,国内对于承受应力较大的区域通常采用(Transient Liquid Phase,TLP)连接方法 [12-16]。
但TLP连接的保温时间较长、成本较高,且焊接热过程对母材组织影响较大,并需要严格控制焊缝间隙,对零件的配合精度和母材晶体取向均提出较高要求,工艺适用性不佳[17-18]。
因此有必要探寻一种钎焊时间较短、接头性能优良的钎焊连接方法,文中即对此开展研究。
该研究针对CMSX-4合金的成分特点,研制了一种镍基钎料,用于钎焊CMSX-4单晶高温合金,通过对比不同钎焊温度下接头的显微组织,研究钎焊温度对接头高温持久性能的影响,分析接头的断裂机制,优化钎焊工艺,从而获得具有优异高温力学性能的接头。
1 试验材料及工艺研究中使用的母材为CMSX-4单晶高温合金试棒,试棒的取向为(001)方向,试棒的尺寸为φ13 mm×210 mm,其主要成分见表1。
利用线切割机沿垂直于母材CMSX-4单晶棒(001)方向切割成待焊样品,样品尺寸为φ13 mm×35 mm。
文中所用钎料为中国科学院金属研究所自主研制的镍基钎料JSSNi60,粉末的粒径不大于74 μm,其化学成分见表1。
将准备好的钎料与粘结剂混合、调匀,然后放置于母材样品的待焊表面,再利用储能点焊机将CMSX-4母材之间的焊缝间隙控制为200 μm,并将适量钎料置于焊接面周围。
将装配好的样品放入真空钎焊炉中,以10 ℃/min的速率将待焊试样加热至500 ℃,保温20 min,使粘结剂充分挥发,再以10 ℃/min的速率加热至1 070 ℃,保温20 min,使母材与钎料各区域温度均匀一致,随后以20 ℃/min的速率升温至钎焊温度1 230~1 310 ℃,并保温30 min,焊后快速冷却至200 ℃以下。
在钎焊过程中,炉内真空度不低于5.0×10-2 Pa。
利用扫描电子显微镜(Scanning Electron Microscope, SEM)观察接头的显微组织,并采用电子探针(Electron Probe Microanalysis, EPMA)对接头的元素分布和各相成分进行分析,推测焊缝的相组成。
持久性能测试在悬臂式持久试验机上进行,测试CMSX-4单晶高温合金钎焊接头在980 ℃/100 MPa条件下的持久寿命。
表1 CMSX-4单晶高温合金与JSSNi60镍基钎料的成分(质量分数,%)2 试验结果2.1 钎焊温度对接头显微组织的影响图1为采用JSSNi60镍基钎料分别在1 230 ℃,1 250 ℃,1 270 ℃,1 290 ℃和1 310 ℃保温30 min条件下钎焊CMSX-4单晶高温合金的显微组织。
结合前期研究结果分析[10,18-19],接头内主要相组成为高熔点的白色硼化物相(图1中位置2)、保温阶段形成的初生γ-Ni固溶体(图1中位置5)、弥散分布于γ-Ni中的γ′增强相(图1中位置4)以及钎料凝固阶段依次形成的灰色块状低熔点化合物相(图1中位置6)和深色块状低熔点化合物相(图1中位置1)。
分析对比各钎焊温度的接头组织发现,该钎料能在1 230~1 310 ℃的温度范围内对CMSX-4母材进行有效地钎焊连接,并且随着钎焊温度的增加,焊缝中低熔点化合物相含量减少,白色硼化物比例先升高后降低,小尺寸凝固缺陷消失(图1中位置3),γ′相含量增加。
如图1a所示,在1 230 ℃/30 min条件下焊接时,接头中出现大量不规则形状的灰色块状相、白色骨架状和块状相、γ′增强相以及少量深色块状相和小尺寸凝固缺陷。
利用EPMA对接头进行成分分析可知,其中界面区域成分(原子分数)为2.37%Si,1.23%Ti,66.89%Ni,11.59%Cr,11.23%Co,6.69%Al,应为钎焊保温阶段形成的初生γ-Ni相及弥散分布其中的γ′相[10]。
保温时,钎料中的B,Si元素向界面处的母材扩散,界面区成分发生变化,使液相钎料以母材为形核基底进行等温凝固,形成连续镍基固溶体,并在降温时从中析出γ′相[11]。
焊缝中的白色相为高钨的M3B2型硼化物,其成分(原子分数)为35.4%B,5.2%Si,17.1%Ni,18.1%W,5.3%Cr,6.3%Nb,7.5%Co,5.1%Mo。
借助Thermo-calc软件计算及作者前期研究结果[10]可知,在钎焊保温时,液相钎料中存在未熔化的M3B2型硼化物相,它们在降温过程中继续从液相中析出,并随着液相钎料中W,Mo等元素含量的降低,后析出的化合物成分也随之发生变化,成为了灰色的富Co,Ni,Nb,Si元素的硼化物[20-22],其成分(原子分数)为12.4%B,9.8%Si,32.6%Ni,5.9%W,8.2%Cr,9.3%Nb,14.5%Co,5.2%Mo,2.1%Re。
随着炉温继续下降以及接头成分的改变,钎料中的Si元素在焊缝中溶解度下降,形成了少量深色(Ni, Nb, Co)3Si型块状硅化物相[11,21-23],其成分(原子分数)为1.4%B,22.8%Si,54.8%Ni,0.7%Ti,12.3%Nb,6.5%Co,1.5%Cr。
由于钎焊温度较低,在焊缝中形成的低熔点化合物相将对接头力学性能产生不利影响。
图1 不同钎焊温度下的CMSX-4单晶高温合金接头微观组织当钎焊温度升高到1 250 ℃后,接头组织如图1b所示。
由于钎焊温度的升高,保温时处于熔融状态的钎料中所含固相硼化物的比例减少,使液相中W,Mo等难熔元素含量相对提高,且较高的温度使接头中的B元素更快地扩散至母材中,以至于在保温结束后的降温过程中,富W,Mo元素的液态钎料开始非平衡凝固,白色硼化物相增多,灰色硼化物相明显减少,γ′相尺寸减小,深色硅化物相和小尺寸缺陷消失。