模具制造工艺试卷1及答案
模具工理论试卷

- 1 -模具制造工(高级) 模拟试卷(一)姓名________________一.判断题(下列判断正确的请打勾,错误的打叉。
每题 2 分,共 30 分) 1. 采 用级 进 模 连 续 冲 压 时 , 落 料 和 切 断 工 序 一 般 安 排 在 最 后 工 位 。
( x )2. 步 距 精 度 要 求 高 的 级 进 模 应 以 侧 刃 、 挡 块 作 为 定 距 零 件 。
( v )3. 精冲模具的工作部分由凸模、凹模、凸凹模、卸料板和顶出器等组成。
( v )4. 选 择 工 艺 基 准 时 要 尽 量 遵 循 基 准 重 合 原 则 。
( v )5. 半导体电流是电子电流和空穴电流的合成。
( v )6. 设计注塑模导柱和导套时, 导柱长度的确定必须保证在合模过程中型芯即将进 入型腔或对合时,导柱应首先进入导套。
( v )7. 从进料口注入的熔融料,由于型腔表面散热而黏度下降, 使流动性改善, 因此 流到末端时其熔接强度提高。
( x )8. 注塑模具中水道通路的大小和布局结构及加热、 冷却方式对注塑模温度调节系 统的正常工作状态没有直接的影响。
( x )9. 正 火 冷 却 速 度 比 退 火 快 , 转 变 温 度 低 些 , 从 而 获 得 的 组 织 更 细 小。
( v )10. 电火花加工可以避免电极损耗的问题。
( x ) 11. 生产上模具失效一般是指模具的零件损坏后无法修复再使用。
( x ) 12. 拉深模的主要失效形式以磨粒磨损为主,伴有黏附磨损。
( v ) 13. 平面图形中的尺寸可分为定形尺寸和定位尺寸。
( ) ( v )14. 绘制单个圆柱齿轮时分度圆可以不画。
(v )15. 三坐标测量仪测量误差分布满足正态分布。
( v )二.填充题(请将正确的答案填在横线空白处。
每空 2 分,共 30 分) 1.在推件板上安装_弹顶____的目的是防止冲件吸附在_凸模__上。
模具制造工艺考试题库

一、单选题(本大题共15小题,每题1分,共15分。
)请将答案填写在题干后旳括号内。
1、下列工件最适合成型磨削加工旳是 C 。
A、凹模;B、型腔;C、凹模镶块;D、紫铜电极。
2、在不同生产类型下,同一产品旳工艺过程是 C 。
A、相似旳;B、相似旳;C、不同旳;3、下列有关数控机床坐标系说法对旳旳是 A 。
A、工件坐标系旳方向和机床坐标系旳方向一致;B、工件坐标系和机床坐标系都是操作者设定旳;C、机床坐标系旳原点就是工件编程旳原点。
4、要提高电火花加工旳工件表面质量,应考虑: B 。
A、使脉冲宽度增大;B、使电流峰值减小;C、增大放电间隙。
5、铰孔重要用于加工 C 。
A、大尺寸孔;B、盲孔和深孔;C、中小尺寸未淬硬旳孔;D、中小尺寸已淬硬旳孔。
6、对有色金属零件旳外园表面加工,当精度规定为IT6,Ra=0.4μm时,它旳终了加工措施应当采用 A 。
A、精车;B、精磨;C、粗磨;D、研磨。
7、下列A C 可超声波切割加工。
A、陶瓷B、紫铜C、玻璃D、塑料8、下列A B C D可制作模具电铸成形旳原模(母模)。
A、塑料B、石膏C、金属材料D、环氧树脂9、对塑料模浇口套旳装配,下列说法对旳旳有:B C。
A、浇口套与定模板采用间隙配合B、浇口套旳压入端不允许有导入斜度C、常将浇口套旳压入端加工成小圆角D、在浇口套旳导入斜度加工时不需留有修磨余量10、分散装配旳特点是:AA、适合成批生产B、生产效率低C、装配周期长D、装配工人少11、工序集中到极限时,把零件加工到图样规定旳规定旳工序应当是 A 。
A、一种;B、二个;C、多种。
12、在机械加工工艺规程中旳安装是指 D 。
A、刀具在机床上旳装夹过程;B、工件更换机床时所发生旳装卸工作;C、工件在机床上装卸所完毕旳工艺过程;D、工件在机床上旳定位和夹紧过程。
13、零件机械加工顺序旳安排,一般应遵循 A 旳原则。
A、先加工基准表面,后加工其他表面;B、先加工次要表面,后加工重要表面;C、先加工孔和型腔,后加工平面。
《模具制造工艺编制》试题库及答案

试题库一、填空题1. 模具加工工艺规程一般包括模具_____________________ 、___________________ 、和_____________ 、工件的检验方法、切削用量和时间定额等。
2. 模具零件常用的毛坯主要有__________ 、 __________ 、 ______ 和半成品件四种。
3. 工序可分为_____ 、_____ 、______ 和走刀(行程)。
4. 安装方法可以归纳为___________ 、 ___________和采用夹具安装法等。
5. 工件在加工之前,使同一批工件在机床或夹具上占据某一正确位置的过程称为______ ,然后将其固定使其在加工过程保持位置不变的操作称为_________ 。
6. 定位精基准的选择有以下原则:为保证工件加工表面获得较高的加工精度应遵守基准______________ 原则;为保证各表面间都能获得较高的位置精度,多数工序所选择的精定位基准,应遵守基准___________ 原则。
其次还可以根据工件的加工要求可按互为基准和自为基准选择精定位基准。
7. 一个或一组工人,在一个___________ 对同一个或同时对几个工件所连续完成的那部分______________ 称为工序。
8. 零件加工后的实际几何参数(尺寸、形状和位置)与理想几何参数的符合程度称为_____________ ,而它们之间的____________ 称为加工误差。
9. 研磨导柱常出现的缺陷是___________________________________ 。
10. 模座的加工主要是______ 和_________ 的加工。
为了使加工方便和容易保证加工要求,在个工艺阶段应先加工_________ ,后加工__________ 。
11. 确定加工余量的方法有_______ 法、 _________法和__________ 法,其中在模具生产中被广泛采用是__________ 法。
专科模具制造工艺》_试卷_答案

专科《模具制造工艺》一、(共75题,共150分)1. 以下选项中()不是万能夹具上工件的装夹方法。
(2分)A.用螺钉固紧工件B.用铣床的通用夹具C.用精密平口钳装夹D.用磁力平台装夹.标准答案:B2. 模具制造的特点下列选项中不正确的是()。
(2分)A.制造质量要求高B.形状复杂C.材料硬度高D.批量生产.标准答案:D3. 数控机床的标准坐标系是以()来确定的。
(2分)A.混合坐标B.绝对坐标系C.相对坐标系D.右手直角笛卡尔坐标系.标准答案:D4. 成型磨削时,零件()。
(2分)A.只能是圆柱面B.形状不能是曲面C.不能带凸肩D.能带凸肩.标准答案:C5. 闭环控制系统一般不用于()数控机床上。
(2分)A.经济型B.中、高档C.精密D.工业级.标准答案:A6. 轴类零件在一台车床上车端面、外圆和切断。
此时工序为()。
(2分)A.一个B.两个C.三个D.四个.标准答案:A7. 精铣的尺寸精度可达(),表面粗糙度为()。
(2分)A.B.C.D..标准答案:D8. 下列不属于平面加工方法的是()。
(2分)A.刨削B.磨削C.铣削D.铰削.标准答案:D9. 坐标磨床有三个主要的运动,说法错误的是()。
(2分)A.砂轮的转动(自转)B.上下往复运动C.主轴的行星回转(公转)D.水平往复运动.标准答案:D10. 根据型腔模电火花加工的特点,对电极材料的要求是()。
(2分)A.易于加工制造成形B.电极损耗大C.加工速度慢D.价格较贵.标准答案:A11. 某导柱的材料为40钢,外圆表面要达到IT6级精度,Ra0.8μm,则加工方案可选()。
(2分)A.粗车—半精车—粗磨-精磨B.粗车—半精车—精车C. .标12 A. .标13 A. B. C.D. .标14 A. C. .标15 A. C. .标16(A. C. .标17 A. .标18具A. .标19 A. .标20 A. C. .标21 A. .标22 A. C.23. 电解加工与被加工材料的()无关,故可加工任何金属材料。
模具工试题及答案
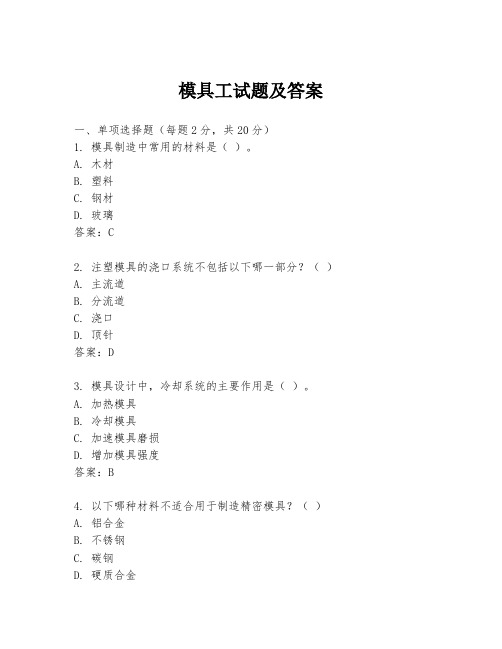
模具工试题及答案一、单项选择题(每题2分,共20分)1. 模具制造中常用的材料是()。
A. 木材B. 塑料C. 钢材D. 玻璃答案:C2. 注塑模具的浇口系统不包括以下哪一部分?()A. 主流道B. 分流道C. 浇口D. 顶针答案:D3. 模具设计中,冷却系统的主要作用是()。
A. 加热模具B. 冷却模具C. 加速模具磨损D. 增加模具强度答案:B4. 以下哪种材料不适合用于制造精密模具?()A. 铝合金B. 不锈钢C. 碳钢D. 硬质合金答案:C5. 在模具制造过程中,用于确定模具尺寸的工艺是()。
A. 切割B. 焊接C. 测量D. 抛光答案:C6. 模具的寿命通常取决于()。
A. 材料硬度B. 使用频率C. 维护保养D. 所有以上因素答案:D7. 在模具设计中,凹模和凸模的配合关系是()。
A. 凸模嵌入凹模B. 凹模嵌入凸模C. 凸模和凹模相互独立D. 凸模和凹模完全重合答案:A8. 模具的热处理工艺主要用于改善材料的()。
A. 韧性B. 硬度C. 耐腐蚀性D. 抗拉强度答案:B9. 下列哪种加工方法不适用于模具制造?()A. 数控铣削B. 线切割C. 激光切割D. 手工雕刻答案:D10. 模具的表面处理通常包括()。
A. 抛光B. 喷砂C. 电镀D. 所有以上方法答案:D二、多项选择题(每题3分,共15分)1. 模具制造中常用的材料包括()。
A. 铝合金B. 不锈钢C. 塑料D. 碳钢E. 硬质合金答案:ABDE2. 注塑模具的组成部分包括()。
A. 浇口系统B. 冷却系统C. 顶针系统D. 模具框架E. 模具底座答案:ABCD3. 模具设计中,影响模具寿命的因素包括()。
A. 材料硬度B. 使用频率C. 维护保养D. 模具设计E. 模具制造工艺答案:ABCDE4. 模具的表面处理方法包括()。
A. 抛光B. 喷砂C. 电镀D. 阳极氧化E. 热处理答案:ABCD5. 模具制造过程中可能使用的加工方法包括()。
模具制造技术试卷及答案6套
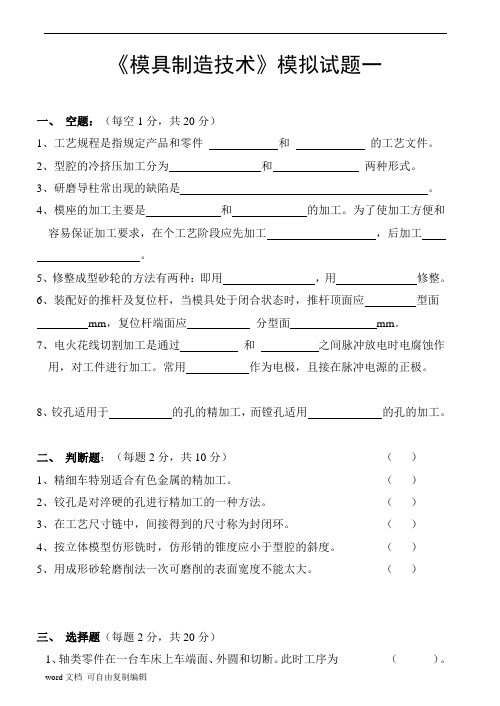
《模具制造技术》模拟试题一一、空题:(每空1分,共20分)1、工艺规程是指规定产品和零件和的工艺文件。
2、型腔的冷挤压加工分为和两种形式。
3、研磨导柱常出现的缺陷是。
4、模座的加工主要是和的加工。
为了使加工方便和容易保证加工要求,在个工艺阶段应先加工,后加工。
5、修整成型砂轮的方法有两种:即用,用修整。
6、装配好的推杆及复位杆,当模具处于闭合状态时,推杆顶面应型面mm,复位杆端面应分型面mm。
7、电火花线切割加工是通过和之间脉冲放电时电腐蚀作用,对工件进行加工。
常用作为电极,且接在脉冲电源的正极。
8、铰孔适用于的孔的精加工,而镗孔适用的孔的加工。
二、判断题:(每题2分,共10分)()1、精细车特别适合有色金属的精加工。
()2、铰孔是对淬硬的孔进行精加工的一种方法。
()3、在工艺尺寸链中,间接得到的尺寸称为封闭环。
()4、按立体模型仿形铣时,仿形销的锥度应小于型腔的斜度。
()5、用成形砂轮磨削法一次可磨削的表面宽度不能太大。
()三、选择题(每题2分,共20分)1、轴类零件在一台车床上车端面、外圆和切断。
此时工序为()。
A一个B两个C三个D四个2、下列不属于型腔加工方法的是()。
A电火花成形B线切割C普通铣削D数控铣削3 、下列不属于平面加工方法的是()A刨削B磨削C铣削D铰削4、某导柱的材料为40钢,外圆表面要达到IT6级精度,Ra.8um则加工方案可选()A粗车—半精车—粗磨—精磨B粗车—半精车—精车C粗车—半精车—粗磨5、简要说明零件加工所经过的工艺路线的卡片是()A机械加工工艺过程卡 B 机械加工工艺卡C机械加工工序卡6、铰孔主要用于加工()A 大尺寸孔B 盲孔、深孔C 中小尺寸未淬硬孔D中小尺寸已淬硬孔7、但电极平动法的特点是()A只需工作台平动 B 只需一个电极 C 较轻易加工高精度的型腔D 可加工具有清角、清棱的型腔8、关于ISO代码中G00的功能说法正确的是()A是直线插补指令B 是快速移动且加工指令C是快速移动但不加工指令9、对于非圆型孔的凹模加工,正确的加工方法是:()A 可以用铣削加工铸件型孔B 可以用铣削作半精加工C 可用成型磨削作精加工10、对于非圆凸模加工,不正确的加工方法是:()A可用刨削作粗加工B淬火后,可用精刨作精加工C 可用成型磨削作精加工四、简答题(共20分)1、拉深模试模时出现制件起皱的缺陷,找出其产生的原因以及调整方法。
模具制造技术试卷及答案6套
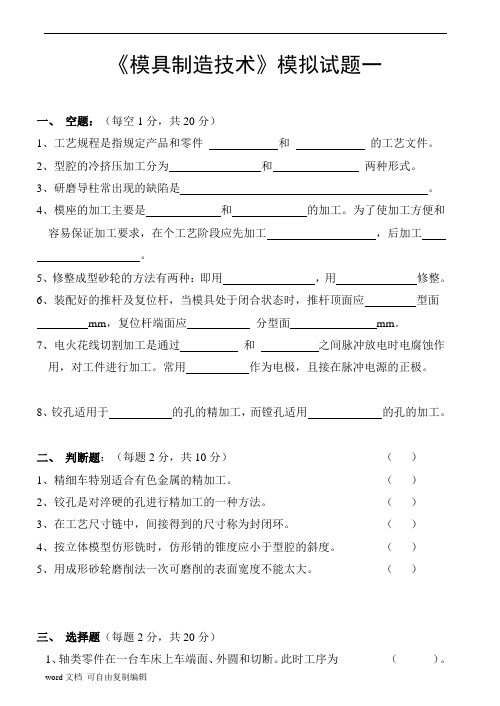
《模具制造技术》模拟试题一一、空题:(每空1分,共20分)1、工艺规程是指规定产品和零件和的工艺文件。
2、型腔的冷挤压加工分为和两种形式。
3、研磨导柱常出现的缺陷是。
4、模座的加工主要是和的加工。
为了使加工方便和容易保证加工要求,在个工艺阶段应先加工,后加工。
5、修整成型砂轮的方法有两种:即用,用修整。
6、装配好的推杆及复位杆,当模具处于闭合状态时,推杆顶面应型面mm,复位杆端面应分型面mm。
7、电火花线切割加工是通过和之间脉冲放电时电腐蚀作用,对工件进行加工。
常用作为电极,且接在脉冲电源的正极。
8、铰孔适用于的孔的精加工,而镗孔适用的孔的加工。
二、判断题:(每题2分,共10分)()1、精细车特别适合有色金属的精加工。
()2、铰孔是对淬硬的孔进行精加工的一种方法。
()3、在工艺尺寸链中,间接得到的尺寸称为封闭环。
()4、按立体模型仿形铣时,仿形销的锥度应小于型腔的斜度。
()5、用成形砂轮磨削法一次可磨削的表面宽度不能太大。
()三、选择题(每题2分,共20分)1、轴类零件在一台车床上车端面、外圆和切断。
此时工序为()。
A一个B两个C三个D四个2、下列不属于型腔加工方法的是()。
A电火花成形B线切割C普通铣削D数控铣削3 、下列不属于平面加工方法的是()A刨削B磨削C铣削D铰削4、某导柱的材料为40钢,外圆表面要达到IT6级精度,Ra.8um则加工方案可选()A粗车—半精车—粗磨—精磨B粗车—半精车—精车C粗车—半精车—粗磨5、简要说明零件加工所经过的工艺路线的卡片是()A机械加工工艺过程卡 B 机械加工工艺卡C机械加工工序卡6、铰孔主要用于加工()A 大尺寸孔B 盲孔、深孔C 中小尺寸未淬硬孔D中小尺寸已淬硬孔7、但电极平动法的特点是()A只需工作台平动 B 只需一个电极 C 较轻易加工高精度的型腔D 可加工具有清角、清棱的型腔8、关于ISO代码中G00的功能说法正确的是()A是直线插补指令B 是快速移动且加工指令C是快速移动但不加工指令9、对于非圆型孔的凹模加工,正确的加工方法是:()A 可以用铣削加工铸件型孔B 可以用铣削作半精加工C 可用成型磨削作精加工10、对于非圆凸模加工,不正确的加工方法是:()A可用刨削作粗加工B淬火后,可用精刨作精加工C 可用成型磨削作精加工四、简答题(共20分)1、拉深模试模时出现制件起皱的缺陷,找出其产生的原因以及调整方法。
模具制造工艺试题及答案资料

模具制造工艺试题及答案一、填空I、典型的刀具磨损过程分为初期磨损、正常磨损和急剧磨损阶段。
2 •精加工基准的选择原则应遵循如下原则:统一基准、基准重合、互为基准和自为基准等原则。
3•在切削加工中,用于描述切削机理的指标是切削层及切削层参数,切削层参数包括切削层公称厚度hD 、切削层公称宽度bD 和切削面积,其中切削面积=hD X bD 。
4 •积屑瘤很不稳定,时生时灭,在_________________ 粗加工_________ 时产生积屑瘤有一定好处,在 _______ 精加工 _________ 时必须避免积屑瘤的产生。
5、工件加工顺序安排的原则是先粗后精、先主后次穿插进行、先基面后其它、先面后孔。
6 基本时间和辅助时间的总和,称为作业时间 _____________ 。
7、切削用量三要素是指—切削速度 _ 、背吃刀量和_ 进给量—。
8、根据力的三要素,工件夹紧力的确定就是确定夹紧力的大小、一方向__________ 和作用点。
9、刀具的正常磨损有前刀面磨损、后刀面磨损和前后刀面同时磨损 ____ 。
10工件经一次装夹后所完成的那一部分工艺内容称为安装。
II、工件通常采用的三种定位方法是直接找正法、划线找正法和夹具定位的方法。
12、主偏角是指过主切削刃上选定点,在基面内测量的主切削刃和假定进给方向的夹角。
13、砂轮的的特性由磨粒、结合剂、粒度、硬度、组织五方面要素决定。
14、所谓基准就是工件上用来确定其它点线面的位置的那些点、线___、面,一般用中心线、对称线或平面来做基准。
15•切削运动包括主运动和进给运动两种,其中主运动运动是切削运动中速度最高,消耗功率最大的运动。
16•最常用的刀具切削部分的材料是高速钢、硬质合金,其中硬度高的是硬质合金,制造工艺性好的是高速钢。
17•工件定位时被限制的自由度少于六个,但能满足工件加工技术要求的定位形式称为不完全定位。
18.工件以一面两孔定位时,常采用一个支承板,一个圆柱销和一个 _削边销作为定位元件限制工件的自由度,该定位方式共限制了工件的 6个自由度,其中削边销限制了工件一个自由度。
《模具制造工艺》期末试卷及答案

XX技师学院________学年第二学期《模具制造工艺》课程期末考试试卷专业模具年级 __ 考试形式:闭卷,所需时间 90 分钟2分)1、工艺过程是指改变生产对象的形状,尺寸、相对位置和性质等,使之成为成品、半成品的生产过程。
2、修整成型砂轮的方法有两种:用挤压轮修整成形砂轮、用金刚石修整成型砂轮。
3、修整成形砂轮的夹具有修整砂轮角度的夹具和修整砂轮圆弧的夹具。
4、正弦分中夹具适用于磨削同一中心的凸圆弧,对于凹圆弧磨削,则需要用成形砂轮配合进行。
5、线切割加工中常用的电极丝有钼丝、铜丝、钨丝。
其中钼丝应用最广泛。
6、生产中常用的装配方法有互换法、分组法、修配法、调整法。
7、在冷冲模装配过程中,导柱、导套与模座,凸模与凸模固定板等零件的连结可采用压入法固定、低熔点合金固定、环氧树脂粘结和无机粘结剂粘结等技术。
8、塑料模导柱、导套装配后,应保证动模板在启模和合模时都能灵活滑动,无阻滞现象,长导柱装配,应在定模板上的导套装配完成后,以导套导向将导柱压入动模板内。
9、凸模常用的固定方法是压入法。
它包括铆接和台肩固定两种形式。
10、塑料模导柱、导套分别安装在塑料模的动模和定模部分上,是模具合模和启模的导向装置。
2 分)将答案填在试题前面的括号内轴类零件在一台车床上车端面、车外圆和切断,此时工序应为 A 。
A.一个B.二个 C.三个 D.四个()2、关于机械加工工艺过程中的工步、工序、安装之间关系说法 A 是正确的。
A.一道工序可以划分为几次安装,一次安装又可划分为几个工步B.一次安装可以划分为几道工序,一道工序又可划分为几个工步C一道工序只有两次安装,一次安装可以划分为几个工步D.一道工序可以划分为几个工步,每个工步有两次安装()3、测量零件已加工表面的尺寸和位置所使用的基准为 B 。
A.定位基准B.测量基准C.装配基准D.工艺基准()4、在机械加工工艺过程中,首先要加工精基准面,这是为了B 。
A.消除工件中的残余变形应力,减少工件变形误差B.使以后各道工序加工有精确的定位基准C.避免主要的加工表面产生加工硬化D.有利于减小以后各工序加工表面的表面租糙度E.有利于精基准面本身的表面精度的提高()5、某导柱材料为40钢,外圆面要达IT6级精度,Ra达0.8μm,则加工方案可选 A 。
模具制造工艺试题及答案

一、填空1、典型的刀具磨损过程分为初期磨损、正常磨损与急剧磨损阶段。
2.精加工基准的选择原则应遵循如下原则: 统一基准、基准重合、互为基准与自为基准等原则。
3.在切削加工中,用于描述切削机理的指标就是切削层及切削层参数,切削层参数包括切削层公称厚度 hD 、切削层公称宽度bD 与切削面积,其中切削面积=hD× bD。
4.积屑瘤很不稳定,时生时灭,在粗加工时产生积屑瘤有一定好处,在精加工时必须避免积屑瘤的产生。
5、工件加工顺序安排的原则就是先粗后精、先主后次穿插进行、先基面后其它、先面后孔。
6、基本时间与辅助时间的总与,称为作业时间。
7、切削用量三要素就是指__ 切削速度 _、___背吃刀量与_ 进给量 __。
8、根据力的三要素,工件夹紧力的确定就就是确定夹紧力的大小、_方向_ ______与作用点。
9、刀具的正常磨损有前刀面磨损、后刀面磨损与前后刀面同时磨损。
10工件经一次装夹后所完成的那一部分工艺内容称为安装。
11、工件通常采用的三种定位方法就是直接找正法、划线找正法与夹具定位的方法。
12、主偏角就是指过主切削刃上选定点,在基面内测量的_ 主切削刃与假定进给方向的夹角。
13、砂轮的的特性由磨粒、结合剂、粒度、硬度、组织五方面要素决定。
14、所谓基准就就是工件上用来确定其它点线面的位置的那些__点___、__线___、____面__,一般用中心线、对称线或平面来做基准。
15.切削运动包括主运动与进给运动两种,其中主运动运动就是切削运动中速度最高,消耗功率最大的运动。
16.最常用的刀具切削部分的材料就是高速钢、硬质合金,其中硬度高的就是硬质合金 ,制造工艺性好的就是高速钢。
17.工件定位时被限制的自由度少于六个,但能满足工件加工技术要求的定位形式称为不完全定位。
18、工件以一面两孔定位时,常采用一个支承板 ,一个圆柱销与一个削边销作为定位元件限制工件的自由度,该定位方式共限制了工件的 6 个自由度,其中削边销限制了工件一个自由度。
模具设计与制造技术考试题与答案
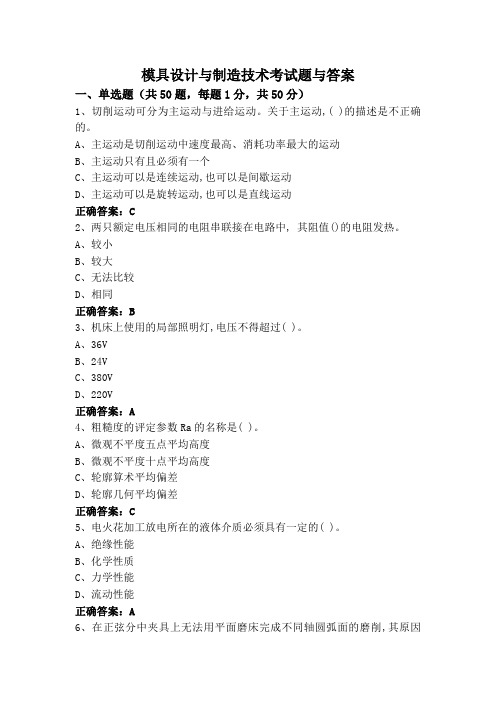
模具设计与制造技术考试题与答案一、单选题(共50题,每题1分,共50分)1、切削运动可分为主运动与进给运动。
关于主运动,( )的描述是不正确的。
A、主运动是切削运动中速度最高、消耗功率最大的运动B、主运动只有且必须有一个C、主运动可以是连续运动,也可以是间歇运动D、主运动可以是旋转运动,也可以是直线运动正确答案:C2、两只额定电压相同的电阻串联接在电路中, 其阻值()的电阻发热。
A、较小B、较大C、无法比较D、相同正确答案:B3、机床上使用的局部照明灯,电压不得超过( )。
A、36VB、24VC、380VD、220V正确答案:A4、粗糙度的评定参数Ra的名称是( )。
A、微观不平度五点平均高度B、微观不平度十点平均高度C、轮廓算术平均偏差D、轮廓几何平均偏差正确答案:C5、电火花加工放电所在的液体介质必须具有一定的( )。
A、绝缘性能B、化学性质C、力学性能D、流动性能正确答案:A6、在正弦分中夹具上无法用平面磨床完成不同轴圆弧面的磨削,其原因A、分度盘精度低B、量块高度不合适C、没有安装正弦圆柱的空间D、两顶尖装夹工件正确答案:C7、带传动中两轮直径不变,若将主动轮转速增大一倍,则传动比( )。
A、增大两倍B、增大一倍C、减小一倍D、不变正确答案:D8、职业道德行为的最大特点是( )。
A、普遍性和广泛性B、时代性和创造性C、自觉性和习惯性D、实践性和实用性正确答案:C9、对于熔体粘度高、玻璃化温度高、冷却速率快的塑料制品应采用( )注射。
A、低压B、快速C、慢速D、答案B、C正确答案:B10、工程中常见回转体中,三面投影均为一个圆的是( )。
A、球B、圆柱C、圆锥D、圆环正确答案:A11、属位置公差项目的符号是( )。
A、─B、〓D、○正确答案:C12、以下选项中属于转动副的是( )。
A、燕尾滑板B、丝杠与螺母C、铰链连接D、滑块与导轨正确答案:C13、下列关于创新的论述,正确的是( )。
A、创新与继承根本对立B、创新不需要引进国外新技术C、创新就是独立自主D、创新是民族进步的灵魂正确答案:D14、已加工表面和待加工表面之间的垂直距离称为( )。
模具制造工艺学试卷及答案

一、判断题:正确的打符号√,错误的打符号×。
〔每题2分,共20分〕1、零件构造的工艺性好就是指零件的构造形状在满足使用要求的前提下,按现有的生产条件能用较经济的方法加工出来〔√〕2、外表粗糙、精度低的毛坯粗基准的选择:一般情况下,同一尺寸方向上的粗糙基准只能使用二次〔×〕3、工步是在加工外表、加工工具都不变的情况下,连续完成的那一局部工序。
〔√〕4、在加工过程中直接保证的尺寸等称为封闭环。
〔×〕5、采用正弦精细平口钳或正弦磁力台夹具只能磨削平面或斜面〔×〕6、光整加工是最后决定零件形状和尺寸精度的加工工艺方法。
〔×〕7、周磨加工精度较高,适用于精磨。
〔√〕8、铰孔是对中小直径未淬硬孔进展半精加工和精加工。
〔√〕9、成形磨削中,凸模必须设计为镶拼构造。
〔×〕10、电火花成型加工适宜加工低刚度工件及微细加工。
〔√〕二、选择题:〔每题2分,共20分〕1、在不同的生产类型下,同一产品的工艺过程是〔 C 〕A、一样的;B、相似的;C、不同的。
2、以下不属于平面加工方法的是〔 D 〕A、刨削B、磨削C、铣削D、铰削。
3、对有色金属零件的外圆外表加工,当精度要求为IT6,时,它的终了加工方法应该采用〔 A 〕A、精车;B、精磨;C、粗磨;D、研磨。
4、选择精基准的原则中讲到的"基准重合〞是指〔A〕A、选择设计基准作为精基准B、以粗基准作为精基准C、在多数工序中采用同一组精基准定位D、选择加工外表本身作为精基准5、以下适合线切割加工的对象是〔 C 〕A、阶梯孔、阶梯轴;B、型腔;C、成型刀、样板;D、非导电材料。
7、电火花加工凹模型孔是利用〔 C 〕之间脉冲放电产生电腐蚀现象的原理而进展的。
A.工作液与工件;B.工作液与工具电极;C.工件与工具电极。
8、用坐标镗床加工孔系,其外表粗糙度可达〔 B 〕A、;B、;C、。
9、模具电火花穿孔加工常用的电极构造形式有〔 A 〕。
模具制造工艺学习题集答案(谭海林)

第1章模具制造工艺规程的基础知识一、填空题1.生产类型是指企业(或车间、工段、班组、工作地)生产专业化的分类,包括单件生产、批量生产、大量生产三种类型。
(1-1)2.工艺规程是指规定产品和零件制造工艺过程和操作方法的工艺文件。
(1-1)3.在制订零件的机械加工工艺规程时,必须保证质量、生产率、经济性三个方面的基本要求。
(1-1)4.制订工艺规程的最基本原始资料是零件图。
(1-1)5.工艺过程是指改变生产对象的形状,尺寸、相对位置和性质等,使之成为成品、半成品的生产过程(1-1)6.工序是指一个或一组工人,在一个固定的工作地点(如机床或钳工台等),对同一个或同时对几个工件进行加工所连续完成的那部分工艺过程。
(1-1)7.划分工序的依据是工作地(设备)、加工对象是否变动、加工是否连续完成。
(1-1)8.工序是机械加工工艺过程的基本组成部分。
(1-1)9.安装是工件在机床上正确地定位和夹紧。
(1-1)10.工位是指工件在一次装夹后,工件与夹具或设备的可动部分一起,相对刀具或设备的固定部分所占据的每一个位置。
(1-1)11.铰孔适用于中小尺寸的孔的精加工,而镗孔适用大尺寸的孔的加工。
(1-2)12.铰孔、拉孔适用于直径较小的孔的精加工,淬硬的孔只能用磨削进行加工。
13.模具制造中,通常按照零件结构和工艺过程的相似性,将各种零件大致分为轴类零件、套类零件、盘环类零件、板类零件以及腔类零件等。
(1-2)14.模具零件常用的毛坯主要有锻件、铸件、半成品件、焊接件、各种型材及板料等(1-2)15.铸件毛坯适用于形状复杂的零件,锻件毛坯适用于强度要求较高,而形状比较简单的零件。
(1-2)16.对阶梯式圆凸模,如果各台阶直径相差不大,可直接采用棒料作毛坯,使毛坯准备工作简化(1-2)17.大型凸缘式模柄零件,宜采用锻件作毛坯,以节省材料和减少机械加工的工作量。
(1-2)18.在加工时,为了保证工件相对于机床和刀具之间的正确位置(即将工件定位)所使用的基准称为定位基准。
模具设计与制造试题一及答案
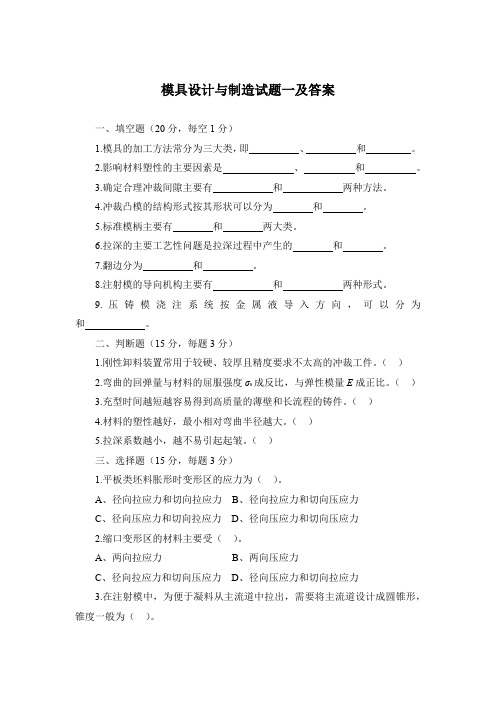
模具设计与制造试题一及答案一、填空题(20分,每空1分)1.模具的加工方法常分为三大类,即、和。
2.影响材料塑性的主要因素是、和。
3.确定合理冲裁间隙主要有和两种方法。
4.冲裁凸模的结构形式按其形状可以分为和。
5.标准模柄主要有和两大类。
6.拉深的主要工艺性问题是拉深过程中产生的和。
7.翻边分为和。
8.注射模的导向机构主要有和两种形式。
9.压铸模浇注系统按金属液导入方向,可以分为和。
二、判断题(15分,每题3分)1.刚性卸料装置常用于较硬、较厚且精度要求不太高的冲裁工件。
()2.弯曲的回弹量与材料的屈服强度σs成反比,与弹性模量E成正比。
()3.充型时间越短越容易得到高质量的薄壁和长流程的铸件。
()4.材料的塑性越好,最小相对弯曲半径越大。
()5.拉深系数越小,越不易引起起皱。
()三、选择题(15分,每题3分)1.平板类坯料胀形时变形区的应力为()。
A、径向拉应力和切向拉应力B、径向拉应力和切向压应力C、径向压应力和切向拉应力D、径向压应力和切向压应力2.缩口变形区的材料主要受()。
A、两向拉应力B、两向压应力C、径向拉应力和切向压应力D、径向压应力和切向拉应力3.在注射模中,为便于凝料从主流道中拉出,需要将主流道设计成圆锥形,锥度一般为()。
A、2°~6°B、6°~10°C、10°~16°D、16°~20°4.在注射成形的每个周期中,将塑件及浇注系统凝料从模具中脱出的机构称为()。
A、导向机构B、顶件机构C、抽芯机构D、推出机构5.压铸过程中,金属熔体从冲头向前快速运动,高速通过内浇口直至充满型腔,此时熔体流动速度称为()。
A、冲头速度B、充型速度C、冲头空压射速度D、熔体速度四、简答题(50分)1.模具设计的基本条件是什么?模具设计的关键技术是什么?(5分)2.模具制造过程一般包括哪几个阶段?(5分)3.什么是排样?排样的分类是什么?(5分)4.影响最小相对弯曲半径的因素主要有哪些?(5分)5.在注射模具中,选用热塑性塑料时,主要考虑哪些工艺特性?(5分)6.注射模浇注系统的设计原则是什么?(5分)7.冲裁过程分为哪三个阶段,每个阶段各有什么特征?(10分)8.压铸模中分型面的选择要点有哪些?(10分)试题一答案一、填空题(20分,每空1分)1.铸造加工、切削加工、特种加工2.材料的化学成分、金相组织、力学性能3.理论确定法、经验确定法4.直通式、台阶式5.刚性、浮动6.起皱、拉裂7.内缘翻边、外缘翻边8.导柱导向、锥面定位9.切向浇口、径向浇口二、判断题(15分,每题3分)1.√2.×3.√4.×5.×三、选择题(15分,每题3分)1.A2. B3.A4.D5.B四、简答题(50分)1.模具设计的基本条件是什么?模具设计的关键技术是什么?(5分)答:模具设计有两个基本条件,即工件的材料、性能、规格和成型设备的种类、性能、规格。
模具制造工试题和答案
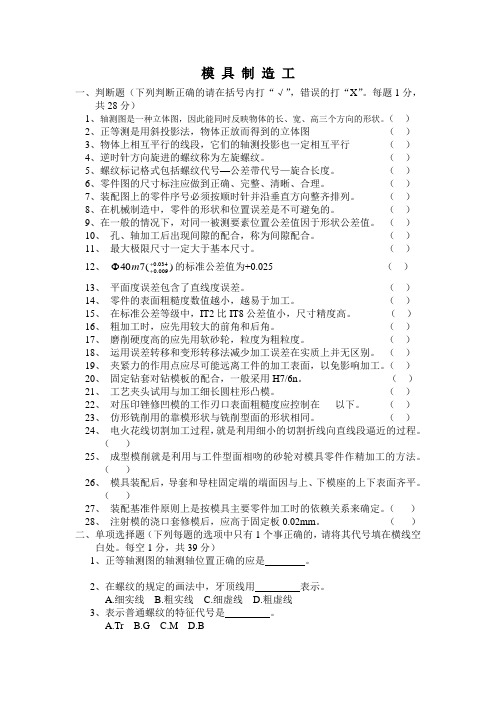
模 具 制 造 工一、判断题(下列判断正确的请在括号内打“√”,错误的打“X ”。
每题1分,共28分)1、轴测图是一种立体图,因此能同时反映物体的长、宽、高三个方向的形状。
( )2、正等测是用斜投影法,物体正放而得到的立体图 ( )3、物体上相互平行的线段,它们的轴测投影也一定相互平行 ( )4、逆时针方向旋进的螺纹称为左旋螺纹。
( )5、螺纹标记格式包括螺纹代号—公差带代号—旋合长度。
( )6、零件图的尺寸标注应做到正确、完整、清晰、合理。
( )7、装配图上的零件序号必须按顺时针并沿垂直方向整齐排列。
( )8、在机械制造中,零件的形状和位置误差是不可避免的。
( )9、在一般的情况下,对同一被测要素位置公差值因于形状公差值。
( )10、 孔、轴加工后出现间隙的配合,称为间隙配合。
( )11、 最大极限尺寸一定大于基本尺寸。
( )12、 )(740034.0009.0++Φm 的标准公差值为+0.025 ( )13、 平面度误差包含了直线度误差。
( )14、 零件的表面粗糙度数值越小,越易于加工。
( )15、 在标准公差等级中,IT2比IT8公差值小,尺寸精度高。
( )16、 粗加工时,应先用较大的前角和后角。
( )17、 磨削硬度高的应先用软砂轮,粒度为粗粒度。
( )18、 运用误差转移和变形转移法减少加工误差在实质上并无区别。
( )19、 夹紧力的作用点应尽可能远离工件的加工表面,以免影响加工。
( )20、 固定钻套对钻模板的配合,一般采用H7/6n 。
( )21、 工艺夹头试用与加工细长圆柱形凸模。
( )22、 对压印锉修凹模的工作刃口表面粗糙度应控制在 以下。
( )23、 仿形铣削用的靠模形状与铣削型面的形状相同。
( )24、 电火花线切割加工过程,就是利用细小的切割折线向直线段逼近的过程。
( )25、 成型模削就是利用与工件型面相吻的砂轮对模具零件作精加工的方法。
模具制造技术试题(带部分答案)

模具制造技术试题一、填空题:(每空1分,共25分)1、研磨导柱常出现的缺陷是“喇叭口”(孔的尺寸两端大中间小)。
2、模座的加工主要是平面和孔的加工。
为了使加工方便和容易保证加工要求,在个工艺阶段应先加工平面,后加工3、装配好的推杆及复位杆,当模具处于闭合状态时,推杆顶面应高出型面0.05-0.10 mm,复位杆端面应低于分型面0.02-0.05 mm。
4、电火花线切割加工是通过工具电极和工件电极之间脉冲放电时电腐蚀作用,对工件进行加工。
常用钼丝作为电极,且接在脉冲电源的_____极。
5、万能夹具是成形磨床的主要部件,也可在平面磨床或万能工具磨床上使用。
由十字滑块、回转部分、分度部分和工件的装夹部分组成。
6模具装配方法有_____、和________三种.7、成形磨削按加工原理可分为成形砂轮磨削法与夹具成形磨削法两大类。
9、成形磨削的方法有、、和。
二选择题(共10分)1、集中装配的特点是。
A、从零件装配成部件或产品的全过程均在固定地点。
B、由几组(或多个)工人来完成。
C、对工人技术水平要求高。
D、装配周期短。
2、对于型腔的机械加工,正确的方法有。
A、在仿形铣床上加工B、可在立式铣床上加工C、可在圆弧铣床上加工3 、下列不属于平面加工方法的是( D )A刨削B磨削C铣削D铰削4、轴类零件在一台车床上车端面、外圆和切断。
此时工序为( A )A一个B两个C三个D四个5 塑料模具试模时模具的调整内容不包含的是A开模距离B顶出距离C型腔修整D锁模力三、名词解释1工序2 照相腐蚀加工3压印锉修4 组成环5 电规准6单电极平动法四编程题(10分)编制如图所示凸模线切割程序,采用3B代码,切割起点为O,引入段长度OA=5mm,加工顺序O→A→B→C→D→A→O,不考虑半径补偿.五问答题1导柱加工中为什么要研磨中心孔?2什么是修配装配法?(5分)3冲模工作零件装配时,间隙调整的方法有哪些?(5分)4万能夹具的十字滑块和分度盘各起什么作用?5、什么是精基准?试述选择精基准的原则。
- 1、下载文档前请自行甄别文档内容的完整性,平台不提供额外的编辑、内容补充、找答案等附加服务。
- 2、"仅部分预览"的文档,不可在线预览部分如存在完整性等问题,可反馈申请退款(可完整预览的文档不适用该条件!)。
- 3、如文档侵犯您的权益,请联系客服反馈,我们会尽快为您处理(人工客服工作时间:9:00-18:30)。
北华航天工业学院2013—2014学年第二学期
模具制造工艺A试卷评分标准及参考答案
一、填空(共10分,每空1分)
1. 若采用成型磨加工凸模时,若其加工有几个回转中心的工件所采用的夹具为万能夹具。
2. 高速铣削的可加工硬度高达 HRC55-65 的零件。
3. 成型磨削是将零件的轮廓线分解成若干直线与圆弧然后按照一定的顺序逐段磨削,使之达到图
纸的技术要求。
4. 电火花成型加工中粗加工采用负极性加工,电火花线切割的精加工采用正极性加工。
5. 在快速成型过程中,需将CAD实体模型进行表面网格化处理,生成 stl 文件。
6. 超声波加工适于加工的材料有:宝石、玻璃等
7. 电解加工时,母模与电源负极连接。
二、问答题(共60分,每小题10分)
1. 请从模具零件表面层应力状态角度分析采用磨削、电火花成型、高速铣削三种工艺的差别。
磨削表面应力较大,主要为拉应力
电火花由于切削力较小,但存在高温现象,所以有一定的拉应力,但较小。
高速铣削切削力较小,但应力状态主要为压应力
2. 请简述电火花成型加工的工艺范围及其特点。
结构上适合型腔及深沟槽的加工,精度高,效率低,需制造电极,故生产周期长。
3. 请简述熔融沉积制造法快速成型工件的全过程。
构造三维模型—三维模型近似处理—成型方向选择—分层切片处理—选择适当的工艺进行分层叠加
成型三维产品—工件剥离—进行后强化或表面处理。
4.请简述电火花成型加工的原理。
一定的正负极距离,电压作用下形成放电通道,电场作用下,电子和离子撞击工件表面,剧烈的撞击及快速的汽化爆炸作用,完成加工
5. 请比较在固定凸模时采用压入法或铆接法的利弊.
压入法制造困难,但精度高。
铆接法正好相反
6.对于形状复杂、凸模数量又多的小间隙冲裁模,如何控制凸模与凹模间的间隙?
可采用镀铜法透光法涂层法腐蚀法,保证镀层、涂层或腐蚀量与间隙一致
三、综合题(共30分)
1. 如图所示,请编写其加工工艺规程。
(本题12分)
1、备料:将毛坯锻成平行六面体。
尺寸165mm×
165mm×25mm
2、热处理:退火
3、铣平面:铣各平面,厚度留磨削余量0.6mm,
侧面留磨削余量0.4mm
4、磨平面:磨上下平面,留磨削余量0.3~0.4mm磨
相邻两侧面保证垂直
5、钳工划线:划出对称中心线,固定孔及销孔线
6、钳工:加工固定孔及销孔及穿丝孔
7、检验
8、热处理:按热处理工艺保58~62HRC
9、磨平面:磨上下面及其基准面达要求
10、线切割:切割挡料销孔及型孔,留研磨余量0.01mm
11、研磨:研型孔达规定技术要求
12、检验
2.请按下图制定斜导柱抽芯机构的装配工艺(本题7分)
⑴型芯装入型芯固定板成为型芯组件。
⑵安装导块按设计要求在固定板上调整滑块和导
块的位置,待位置确定后,用夹板将其夹紧,钻导块安装
孔和动模板上的螺孔,安装导块。
⑶安装定模板锁楔保证锁楔斜面与斜滑块斜面有
70%以上的接触面。
(如侧芯不是整体的,在侧芯位置垫上
相当于制件壁厚的铁片或铝片)
⑷闭模,检查间隙x 值是否合格。
(通过修磨或更
换滑块尾部垫片保证x 值)
⑸镗导柱孔将定模板、滑块和型芯组一起用夹板夹紧,在卧式镗床上镗斜导柱孔。
⑹松开模具,安装斜导柱。
⑺修整滑块上的导柱孔口为圆环状(即倒角)
⑻调整导块,使其与滑块松紧合适。
然后钻销孔,压入销钉。
⑼镶侧型芯。
3. 如图所示,请采用3B代码制定线切割程序,切割起点为右端直线下端点。
(本题4分)
B 0 B35000 B 35000 Gx L2
B 10200 B0 B 10200 Gx L3
B 0 B35000 B 35000 Gx L4
B 10200 B 0 B 10200 Gx L3
4.请按下图制定模具装配工艺(本题7分)
1-下模 2-卸料螺钉 3-导柱
4-固定板 5-橡胶 6-导料销
7-落料凹模 8-推件块 9-固定板
10-导套 11-垫板 12、20-销钉
13-上模板 14-模柄 15-打杆
16、21-螺钉 17-冲孔凸模
18-凸凹模 19-卸料板
22-挡料销
(一)组件装配
模具总装配前,将主要零件如模架、模柄、凸模等进行组装。
1)将压入式模柄14装配于上模座13内,并磨平端面。
2)将凸模17装入凸模固定板9内,成为凸模组件。
3)将凸凹模18装入凸凹模固定板4内,成为凸凹模组件。
4)将导柱、导套压入上、下模板,成为模架。
导柱、导套之间滑动要平稳,无阻滞现象,并且上、下模板之间应平行。
(二)确定装配基准件
落料冲孔复合模应以凸凹模为基准件,首先确定凸凹模在模架中的位置。
1)安装凸凹模组件,加工下模座漏料孔确定凸凹模组件在下模座上的位置,然后用平行夹板将凸凹模组件和下模座夹紧,在下模座上画出漏料孔线。
2)加工漏料孔下模座漏料孔尺寸应比凸凹模漏料孔尺寸单边大0.5~1mm。
3)安装凸凹模组件将凸凹模组件在下模座重新找正定位,并用平行夹板夹紧。
钻铰销孔、螺孔,安装定位销20和螺钉21。
(三)安装上模部分
1)检查上模各个零件尺寸是否能满足装配技术条件要求。
如推板8顶出端面应突出落料凹模端面等。
打料系统各零件尺寸是否合适,动作是否灵活等。
2)安装上模,调整冲裁间隙将上模系统各零件分别装于上模座13和模柄14孔内,用平行夹板将落料凹模7、凸模组件、垫板12和上模座14轻轻夹紧,然后调整凸模组件和凸凹模4及冲孔凹模的冲裁间隙,以及调整落料凹模和凸凹模及落料凸模的冲裁间隙。
可采用垫片法调整,并用纸片进行试冲、调整,直至各冲裁间隙均匀。
再用平行夹板将上模各板夹紧。
3)钻铰上模销孔和螺孔上模部分用平行夹板夹紧,在钻床上以凹模8上的销孔和螺钉孔作为引钻孔,钻铰销孔和螺钉孔。
然后安装定位销12和螺钉16。
(四)安装弹压卸料部分
1)安装弹压卸料板将弹压卸料板套在凸凹模上,弹压卸料板和凸凹模组件端面垫上平行垫铁,保证弹压卸料板端面与凸凹模上平面的装配位置尺寸,用平行夹板将弹压卸料板和下模夹紧。
然后在钻床上同钻卸料孔。
最后将下模各板上的卸料螺钉孔加工到规定尺寸。
2)安装卸料橡皮和定位销在凸凹模组件上和弹压卸料板上分别安装卸料橡皮5和定位销22,拧紧卸料螺钉2。
(五)检验
按冲模技术条件进行装配检查。
(六)试冲按生产条件试冲,合格后入库。