甲醇生产
甲醇生产原理

甲醇生产原理
甲醇是一种常见的有机化合物,其化学式为CH3OH。
甲醇的生产原理主要基于合成气的反应,合成气是一种由一氧化碳和氢气组成的气体混合物。
以下是甲醇的生产原理:
1. 合成气制备:首先,通过煤炭、天然气等碳源进行气化或重整反应,产生含有一氧化碳和氢气的合成气。
合成气可根据不同的反应条件和催化剂组合进行生产。
2. 反应器选择:将合成气送入甲醇合成反应器中。
常用的反应器有低温反应器和高温反应器。
低温反应器可通过合成气的洗涤和压缩降低温度,利于甲醇的选择性生成。
高温反应器则有利于反应速率的提高。
3. 反应催化:甲醇合成反应通常在催化剂的存在下进行。
常用的催化剂有金属氧化物,如铜-锌-铝催化剂。
催化剂可以提高甲醇生成的速率和选择性。
4. 反应条件:甲醇的合成受到反应温度、压力和催化剂活性等条件的影响。
通常在中等压力(10-100大气压)和适当的温度(200-300摄氏度)下进行反应。
5. 分离提纯:在反应后,甲醇与未反应的气体、杂质物质等要进行分离和提纯。
常用的方法包括蒸汽混合、蒸馏、吸附等工艺。
通过上述原理,合成气中的一氧化碳和氢气可实现有效转化为
甲醇。
甲醇是一种重要的工业原料,在化工、能源、医药和农业等领域有着广泛的应用。
甲醇生产原理的研究和改进,有助于提高甲醇的生产效率和质量。
甲醇生产

授课内容:•甲醇生产方法•合成气生产方法•合成气生产甲醇原理知识目标:•了解常见甲醇生产方法•了解合成气生产方法•掌握合成气生产甲醇原理能力目标:•分析和判断各种甲醇生产方法的优缺点•分析和判断合成气制甲醇反应产物中产品的分布特点思考与练习:•常见生产甲醇方法有哪些?•合成气生产方法有哪些?•影响合成气生产甲醇的主要因素有哪些?甲醇是饱和醇中最简单的一元醇,最早是由木材和木质素干馏制得,俗名又称“木醇”或“木精”。
甲醇(CH3OH在通常状态下为无色、略带乙醇香味的挥发性液体。
甲醇与水互溶,在汽油中也有很大的溶解度,熔点175.6K,常压沸点337.8K。
甲醇毒性很大,饮入5〜8ml可使人失明,30ml能致人死亡。
甲醇蒸气与空气能形成爆炸性混合物,爆炸极限为6.0%〜36.5%。
甲醇是仅次于三烯和三苯的重要基础有机化工原料,尤其近年来在有些以达国家中,甲醇以清洁燃料的身份登上了环境保护的殿堂,更使其身份倍增。
因此,发达国家中甲醇产量仅次于乙烯、丙烯、苯,居第四位。
甲醇广泛用于有机合成、染料、合成纤维、合成橡胶、涂料和国防等工业。
甲醇大量用于生产甲醛和对苯二甲酸二甲酯。
以甲醇为原料经羰基化反应直接合成醋酸已经工业化。
近年来,随着技术的发展的能源结构的改变,甲醇又开辟了许多新的用途,是合成人工蛋白的重要原料,蛋白转化率高,发酵速度快,价格便宜,所得人工合成蛋白是很好的畜禽饲料。
以甲醇为原料生产烯烃和汽油已实现工业化。
因此,甲醇的生产具有十分重要的意义。
第一节生产方法早期用木材或木质素干馏法制甲醇的方法,在工业上已经被淘汰。
现在,凡含有碳素的固体、液体和气体均可转化为碳的化合物,再以人工合成法制取甲醇。
目前,可以制取甲醇的方法有以下几种。
一、氯甲烷水解法氯甲烷的水解反应如下:CH 3Cl + H 2O NaOH CH3OH +HCl但是,即使与碱溶液共沸至140C,其水解速度仍很慢。
在300〜350C,在碱石灰作用下氯甲烷可以定量地转变为甲醇和二甲醚,反应式如下:2CH3Cl + Ca (OH)2 CaCl2 +2CH3OHCH3Cl + CH 3OH CH3OCH3 + HClCH3OCH3 + H 2O 2CH3OH在350C,于流动系统中进行这一过程时,所得到的甲醇产率为67% 二甲醚为33%氯甲烷的转化率达98%。
甲醇生产工艺流程图
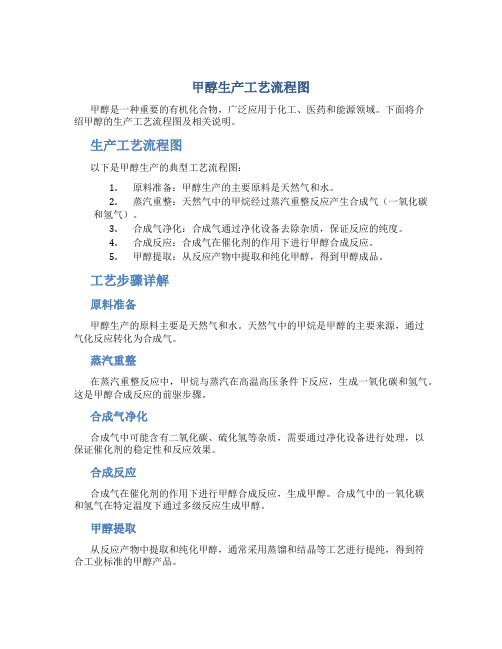
甲醇生产工艺流程图甲醇是一种重要的有机化合物,广泛应用于化工、医药和能源领域。
下面将介绍甲醇的生产工艺流程图及相关说明。
生产工艺流程图以下是甲醇生产的典型工艺流程图:1.原料准备:甲醇生产的主要原料是天然气和水。
2.蒸汽重整:天然气中的甲烷经过蒸汽重整反应产生合成气(一氧化碳和氢气)。
3.合成气净化:合成气通过净化设备去除杂质,保证反应的纯度。
4.合成反应:合成气在催化剂的作用下进行甲醇合成反应。
5.甲醇提取:从反应产物中提取和纯化甲醇,得到甲醇成品。
工艺步骤详解原料准备甲醇生产的原料主要是天然气和水。
天然气中的甲烷是甲醇的主要来源,通过气化反应转化为合成气。
蒸汽重整在蒸汽重整反应中,甲烷与蒸汽在高温高压条件下反应,生成一氧化碳和氢气。
这是甲醇合成反应的前驱步骤。
合成气净化合成气中可能含有二氧化碳、硫化氢等杂质,需要通过净化设备进行处理,以保证催化剂的稳定性和反应效果。
合成反应合成气在催化剂的作用下进行甲醇合成反应,生成甲醇。
合成气中的一氧化碳和氢气在特定温度下通过多级反应生成甲醇。
甲醇提取从反应产物中提取和纯化甲醇,通常采用蒸馏和结晶等工艺进行提纯,得到符合工业标准的甲醇产品。
结论甲醇生产工艺是一个复杂的过程,需要经过多个步骤的精心设计和操作才能获得高质量的产品。
通过合理控制反应条件、提高催化剂的活性和选择合适的分离工艺,可以提高甲醇生产效率和产品质量,满足不同需求。
以上是关于甲醇生产工艺流程图的介绍,希望能给您带来一些帮助和启发。
甲醇工艺流程介绍

甲醇工艺流程介绍甲醇是一种重要的有机化工产品,广泛应用于化工、医药、农药、塑料、合成纤维等领域。
甲醇的生产工艺主要有四种,包括合成气法、天然气重整法、甲烷水蒸气重整法和木质素液化法。
本文将详细介绍甲醇的生产工艺流程。
一、合成气法合成气法是最常用的甲醇生产工艺,其主要原料是天然气或煤炭。
该工艺流程包括气化、合成气净化、气体转化、甲醇合成和甲醇精制等环节。
首先,将天然气或煤炭进行气化,生成合成气。
气化反应需要高温高压环境下进行,主要反应为C+H2O=CO+H2、气化产物中含有一定量的一氧化碳和氢气。
接下来,对合成气进行净化。
合成气中的杂质如硫化物、氨、氯化物等需要被去除,以保证后续反应的顺利进行。
净化工艺主要包括酸性气体的吸收、氢气和一氧化碳的选择性吸附等。
然后,将净化后的合成气进行转化。
转化主要是通过催化剂的作用,将一氧化碳和二氧化碳转化为甲醇。
转化反应的主要反应为CO+2H2=CH3OH。
该反应需要适宜的温度和压力条件,并且需要选择合适的催化剂。
最后,将合成气中生成的甲醇进行精制。
精制工艺主要包括蒸馏、吸附和冷凝等过程,以去除甲醇中的杂质,得到高纯度的甲醇产品。
二、天然气重整法天然气重整法是一种以天然气为原料生产甲醇的工艺。
该工艺流程包括重整、甲醇合成和甲醇精制等环节。
首先,将天然气进行重整反应,生成合成气。
重整反应主要是将天然气中的甲烷和水蒸气在催化剂的作用下进行反应,生成氢气和一氧化碳。
重整反应的主要反应为CH4+H2O=CO+3H2接下来,将重整反应生成的合成气进行甲醇合成。
甲醇合成反应的条件和催化剂与合成气法相似。
最后,对甲醇进行精制,得到高纯度的甲醇产品。
三、甲烷水蒸气重整法甲烷水蒸气重整法是一种以天然气为原料生产甲醇的工艺。
该工艺流程包括甲烷水蒸气重整、甲醇合成和甲醇精制等环节。
首先,将甲烷进行水蒸气重整反应,生成合成气。
重整反应的主要反应为CH4+H2O=CO+3H2接下来,将重整反应生成的合成气进行甲醇合成。
甲醇生产工艺与操作

甲醇生产工艺与操作甲醇(CH3OH)是一种无色、难燃的液体,是重要的工业原料和溶剂。
甲醇的生产工艺主要有合成气法、天然气法和余热法等。
下面简要介绍甲醇的生产工艺和操作。
1. 合成气法合成气法是目前甲醇生产中最常用的方法。
该方法是通过将天然气或煤转化为合成气(一氧化碳和氢气的混合物),再通过催化剂的作用,将合成气转化为甲醇。
合成气法的主要步骤包括气化、净化、合成、分离和净化等。
2. 天然气法天然气法是利用天然气作为原料生产甲醇的方法。
该方法在气化步骤中,直接利用天然气进行气化,生成合成气,然后经过合成、分离和净化等步骤得到甲醇。
天然气法相对于合成气法,减少了气化步骤,简化了工艺流程。
3. 余热法余热法是利用工业生产中产生的余热来生产甲醇的方法。
该方法在循环床和余热再利用等工艺条件下,通过将废气进行循环利用,使得废气中的有机物充分利用,生成合成气,再经过催化剂的作用转化为甲醇。
甲醇的生产操作包括原料准备、反应、分离、回收和净化等步骤。
1. 原料准备在甲醇生产过程中,对于不同的工艺,相应的原料也不同。
合成气法中,主要原料包括天然气和煤。
天然气法中,主要原料为天然气。
余热法则是利用工业生产中的余热进行甲醇生产。
2. 反应甲醇的合成反应主要通过催化剂的作用进行。
合成气与催化剂在适当的温度和压力条件下进行反应,生成甲醇。
3. 分离在反应后,需要对产物进行分离。
主要的分离操作包括冷凝分离和蒸馏分离。
通过降温,将甲醇从反应气体中分离出来。
4. 回收回收操作主要是对分离得到的甲醇进行回收利用。
通过蒸馏、过滤和再结晶等操作,将甲醇进行纯化。
5. 净化甲醇的净化操作主要是去除杂质。
通过吸附剂或催化剂的作用,去除甲醇中的杂质,提高甲醇的纯度。
总的来说,甲醇的生产工艺主要有合成气法、天然气法和余热法等方法,生产操作包括原料准备、反应、分离、回收和净化等步骤。
这些工艺和操作对于甲醇的生产具有重要意义,能够确保甲醇的质量和产量。
甲醇生产方法

甲醇生产方法
甲醇的生产方法主要有以下几种:
1. 合成气法:通过对一氧化碳(CO)和氢气(H2)的合成反应制取甲醇。
这种方法是目前主要的工业生产方法,可以通过催化剂催化反应进行,产量较大。
2. 木质素法:将木质纤维素或纤维素材料进行碱蒸煮,得到的溶液经过酸化后析出木糖,在经过酵母发酵转化为乙醇,再通过蒸馏、脱水等步骤转化为甲醇。
这种方法适用于利用农林废弃物等资源进行甲醇生产。
3. 甲酸法:将甲酸和水蒸汽在高温下催化反应生成甲醇。
这种方法需要较高的反应温度和压力,产量较低。
4. 二氧化碳还原法:利用光合作用或化学氧化的方式获取二氧化碳,并通过还原反应将二氧化碳转化为甲醇。
这种方法是一种环保、可持续的甲醇生产方法,但目前在工业应用上还不够成熟。
需要注意的是,甲醇的生产方法还涉及催化剂的选择、反应条件的控制等多个因素,不同的方法适用于不同的生产规模和场景。
甲醇的生产方法

甲醇的生产方法甲醇是一种广泛应用于工业和化学领域的重要有机化合物,也是一种重要的燃料。
它的生产方法有多种,其中最主要的是从天然气或煤炭中生产。
本文将介绍甲醇的生产方法,包括传统的天然气和煤炭生产法、新型的生物质生产法以及未来可能的人工光合作用生产法等。
一、天然气和煤炭生产法天然气和煤炭生产法是目前最主要的甲醇生产方法。
这种方法主要是利用天然气或煤炭中的一氧化碳和氢气来生产甲醇。
具体的生产流程如下:1、气体净化:将天然气或煤炭中的杂质去除,以保证后续反应的纯度和效率。
2、蒸汽重整:将天然气或煤炭中的甲烷转化为一氧化碳和氢气。
3、合成气净化:将蒸汽重整产生的合成气中的杂质去除,以保证后续反应的纯度和效率。
4、合成反应:将合成气中的一氧化碳和氢气在催化剂的作用下进行反应,生成甲醇。
5、甲醇提纯:将反应产生的混合物中的甲醇和水分离,提纯甲醇。
这种方法的优点是生产成本低,产量大,且可以利用天然气和煤炭等资源。
但是,这种生产方法的缺点也很明显,主要是产生大量的二氧化碳等有害气体,对环境造成污染。
二、生物质生产法生物质生产法是一种新型的甲醇生产方法。
这种方法主要是利用生物质中的碳水化合物,通过生物发酵或化学转化来生产甲醇。
具体的生产流程如下:1、生物质预处理:对生物质进行物理或化学处理,以提取出其中的碳水化合物。
2、生物发酵或化学转化:将生物质中的碳水化合物在微生物或化学催化剂的作用下进行发酵或转化,生成甲醇。
3、甲醇提纯:将反应产生的混合物中的甲醇和水分离,提纯甲醇。
这种方法的优点是可以利用生物质等可再生资源,避免对环境造成污染。
但是,这种方法的缺点也很明显,主要是生产成本高,产量低,且生产过程中需要消耗大量的水和能源。
三、人工光合作用生产法人工光合作用生产法是一种未来可能的甲醇生产方法。
这种方法主要是利用人工合成的光合作用体系,将二氧化碳和水在光合作用体系的作用下进行反应,生成甲醇。
具体的生产流程如下:1、人工光合作用体系的制备:合成一种人工光合作用体系,包括光催化剂、电子传递体系和光反应中心等。
甲醇制作方法是什么-
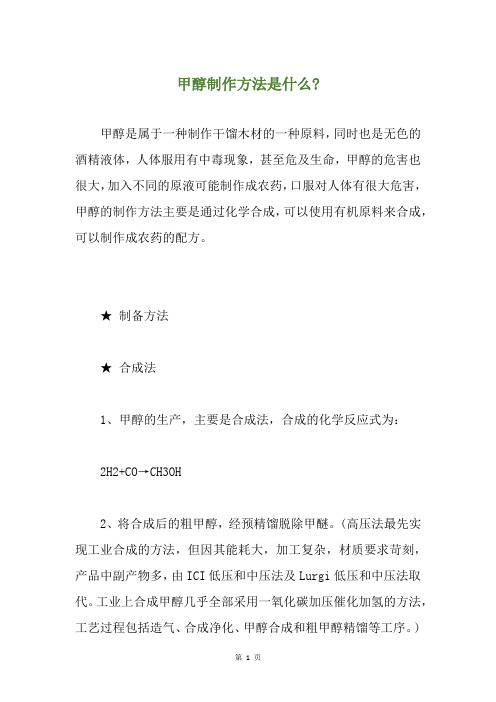
甲醇制作方法是什么?甲醇是属于一种制作干馏木材的一种原料,同时也是无色的酒精液体,人体服用有中毒现象,甚至危及生命,甲醇的危害也很大,加入不同的原液可能制作成农药,口服对人体有很大危害,甲醇的制作方法主要是通过化学合成,可以使用有机原料来合成,可以制作成农药的配方。
★制备方法★合成法1、甲醇的生产,主要是合成法,合成的化学反应式为:2H2+CO→CH3OH2、将合成后的粗甲醇,经预精馏脱除甲醚。
(高压法最先实现工业合成的方法,但因其能耗大,加工复杂,材质要求苛刻,产品中副产物多,由ICI低压和中压法及Lurgi低压和中压法取代。
工业上合成甲醇几乎全部采用一氧化碳加压催化加氢的方法,工艺过程包括造气、合成净化、甲醇合成和粗甲醇精馏等工序。
)3、将粗甲醇净化,净化过程包括精馏和化学处理。
化学处理主要用碱破坏在精馏过程中难以分离的杂质,并调节pH值;精馏主要是脱除易挥发组分如二甲醚,以及难挥发的乙醇、高碳醇和水。
粗馏后的纯度一般都可达到98%以上。
4、将工业甲醇用精馏的方法将含水量降到0.01%以下。
再用次碘酸钠处理,可除去其中的丙酮。
经精馏得纯品甲醇。
5、BV-Ⅲ级甲醇的制备主要采用精馏工艺。
以工业甲醇为原料,经精馏、超净过滤、超净分装,得高纯甲醇产品。
一般均以工业甲醇为原料,经常压蒸馏除去水分,控制塔顶64~65℃,过滤除去不溶物即可。
★干馏法最早是用木材干馏法生产甲醇,故甲醇也叫木醇。
自然游离状态的甲醇非常的少,故这种方法既浪费木材,产品又含有丙酮等杂质,并且很难除去。
因为这种方法不能满足需要,1924年以后,人们开始逐渐停止使用这个方法。
★应用领域基本有机原料之一,用于制造氯甲烷、甲胺和硫酸二甲酯等多种有机产品。
也是农药(杀虫剂、杀螨剂)、医药(磺胺类、合霉素等)的原料,合成对苯二甲酸二甲酯、甲基丙烯酸甲酯和丙烯酸甲酯的原料之一。
甲醇的主要应用领域是生产甲醛,甲醛可用来生产胶粘剂,主要用于木材加工业,其次是用作模塑料、涂料、纺织物及纸张等的处理剂。
甲醇生产方法

甲醇生产方法甲醇是一种重要的化工原料和能源源,广泛应用于化工、医药、农药、塑料、合成纤维、染料等领域。
甲醇的生产方法有多种,下面将介绍其中的几种主要方法。
一、合成气法合成气法是目前甲醇生产的主要方法之一。
该方法利用合成气(一氧化碳和氢气的混合气体)作为原料,经过一系列催化反应得到甲醇。
合成气的产生可以采用煤气化、重油气化、天然气重整等方法。
合成气法甲醇生产过程主要分为三步:合成气制备、甲醇合成和甲醇精制。
首先,通过合成气制备装置将原料气体进行净化、调配,合成合适的合成气。
然后,将合成气经过催化剂床层进行合成反应,生成含有甲醇的合成气体。
最后,通过甲醇精制装置对合成气体进行精制,去除杂质和水分,得到高纯度的甲醇产品。
二、生物法生物法是一种利用微生物催化合成甲醇的方法。
该方法主要利用甲醇菌在适宜的条件下,通过代谢产生甲醇。
生物法甲醇生产的原料主要是可再生资源,如木材、农作物秸秆等。
生物法甲醇生产过程主要包括底物制备、发酵和甲醇提取。
首先,将底物进行预处理,将其转化为可供微生物利用的底物。
然后,将底物与甲醇菌一起进行发酵,通过微生物的代谢作用,底物转化为甲醇。
最后,通过提取工艺将甲醇从发酵液中提取出来,得到纯净的甲醇产品。
三、气相催化法气相催化法是一种利用催化剂在气相条件下进行反应合成甲醇的方法。
该方法主要利用氢气和二氧化碳作为原料,经过一系列催化反应生成甲醇。
气相催化法甲醇生产过程主要包括原料准备、反应器催化和甲醇分离。
首先,将原料气体进行净化和调配,得到合适的原料气体。
然后,将原料气体经过催化剂床层进行催化反应,生成含有甲醇的气体。
最后,通过分离工艺将甲醇与其他气体分离,得到高纯度的甲醇产品。
以上是几种常见的甲醇生产方法,每种方法都有其适用的场合和优劣势。
随着技术的进步和工艺的改进,甲醇的生产方法也在不断发展和完善,以提高生产效率和降低成本,更好地满足市场需求。
希望通过不断的研究和创新,能够实现甲醇生产的可持续发展。
甲醇生产方法

1、甲醇氧化制甲醛甲醇在高温、浮石银、催化剂或其它固体催化剂存在下直接氧化制甲醛。
目前,国内外40%以上的甲醇用于制甲醛,进而合成树脂、塑料及其他化工原料。
聚甲醛是性能优良的工程塑料,其用途十分广泛。
甲醛还用来制取丁二醇、乌洛托品等近一百种下游产品。
2、甲醇氨化制甲胺将甲醇与氨按一定比例混合,在370~420℃、5.0~20.0MPa压力下,以活性氧化铝为催化剂进行合成,制得一甲胺、二甲胺、三甲胺的混合物,再经精馏可得一、二或三甲胺产品。
一、二、三甲胺用于农药、医药、染料方面或用作有机原料中间体。
3、甲醇羰基化制醋酸由甲醇和一氧化碳在低压下羰基合成制醋酸,其总量占世界醋酸生产能力的50%以上。
4、甲醇酯化可生产各种酯类化合物。
5、甲醇与氯气、氢气混合催化反应生成一、二、三氯甲烷,直至四氯化碳。
一氯甲烷可用作有机硅化合物和含氟树脂的原料,又是重要的甲基化剂,用于生产甲基纤纤维素、季胺化学品等。
二氯甲烷用于去漆剂、气雾剂、医药原料及硅片生产。
三氯甲烷可生产HCFC-22作制冷剂,或进一步加工生产四氟乙烯等产品,可用作有机溶剂、萃取剂,还可用作染料和药物的中间体等。
四氯甲烷可用行生产F-11、F-12等。
6、甲醇在金属硅铝催化剂或ZSM-5型分子筛存在下,脱水可制得二甲醚。
7、甲醇脱氢制甲酸甲酯。
甲酸甲酯是有机合成原料,可用于制甲酰胺、二甲基甲酰胺等。
甲酰胺是医药、香料、染料的原料,还可用作纸张处理剂,纤维工业的柔软剂,有机合成的极性溶剂等。
二甲基甲酰胺是重要的有机化工原料和优良的溶剂,可用作气体吸收剂、农药、聚氯酯合成革以及聚丙烯腈抽丝和丁二烯抽提等领域。
8、甲酸制甲基叔丁基醚(MTBE)。
MTBE具有较好的调和特性,从环保和发动机操作两方面考虑,均被认为是汽油最好的改良剂,MTBE被列入世界上50种基本化工产品之一,每吨MTBE约需消耗0.4吨甲醇,因此可望成为今后甲醇消费的大市场。
9、甲醇用作燃料。
甲醇的生产方法

甲醇的生产方法
甲醇,又称甲醇醇、甲酒精,是一种无色、易燃、有刺激性气味的液体。
甲醇
是一种重要的有机化工原料,广泛用于制造甲醛、甲酸、甲苯、二甲醚等化工产品,同时也可用于制造溶剂、染料、涂料、塑料、医药、农药等。
甲醇的生产方法主要包括合成气法、天然气重整法、煤气化法和生物法。
其中,合成气法是目前主要的甲醇生产方法之一。
合成气法是通过气相催化剂在一定温度和压力下,将一定比例的一氧化碳和氢气转化成甲醇。
该方法具有原料来源广泛、生产成本低、产品纯度高等优点,因此得到了广泛应用。
天然气重整法是利用天然气作为原料,通过重整反应制备合成气,再将合成气
转化成甲醇。
这种方法具有原料资源丰富、能耗低、产品纯度高等优点,是目前甲醇生产的重要方法之一。
煤气化法是利用煤炭作为原料,通过煤气化反应制备合成气,再将合成气转化
成甲醇。
这种方法可以有效利用煤炭资源,但由于煤气化过程复杂,生产成本较高,因此在甲醇生产中的应用相对较少。
生物法是利用生物质作为原料,通过生物转化反应制备合成气,再将合成气转
化成甲醇。
这种方法具有原料来源可持续、对环境友好等优点,是一种具有潜力的甲醇生产方法。
总的来说,甲醇的生产方法多种多样,各有优劣。
在选择生产方法时,需要综
合考虑原料资源、能源消耗、生产成本、产品纯度等因素,以及对环境的影响。
随着科技的不断进步和创新,相信未来会有更多高效、低成本、环保的甲醇生产方法出现,为甲醇工业的发展带来新的机遇和挑战。
《化工生产技术》项目6 甲醇的生产

20世纪60年代中期由英国ICI公司开
发成功了铜基催化剂,根据加入助剂的
不同可分为Cu-Zn- Cr系列和Cu-Zn- Al系 列。铜基催化剂活性高、性能好,而且活 性可调(铜含量增加,催化活性提高), 适宜的反应温度为220~270℃,但铜基催 化剂对硫极为敏感,遇硫易中毒失活,且 热稳定性较差。
甲烷部分氧化 法生产甲醇, 原料便宜,工 艺流程简单, 但因生产技术 比较复杂,副 反应多,产品 分离困难,原 料利用率低, 工业上尚未广 泛应用。
由一氧化碳和 氢合成甲醇, 称为合成气法。 根据所使用的 催化剂、反应 温度和反应压 力不同,合成 气法又可分为 高压法、中压 法和低压法, 现在的大型甲 醇装置均采用 中、低压法。
反应中放出的热量必须及时移除,否则易使 催化剂温升过高,使催化剂发生熔结现象而使 催化活性下降。
铜基催化剂的热稳定性较差,控制反应温度 尤为重要。
4.2反应压力的确定
一氧化碳加氢合成甲醇的主反应是体 积缩小的反应,增加压力,有利于向正反 应方向进行。在铜基催化剂作用下,反应 压力与甲醇生成量的关系如图6-5所示。
图片6-1罐装甲醇
图片6-2煤制甲醇资源综合
国内甲醇生产企业主 要分布在具有资源优势的 西部地区,内蒙古、山东、 宁夏、陕西等地产能占比 较大,而消费市场主要集 中在东部沿海地区。
01 甲醇工业现状及发展趋势
图6-3甲醇储罐利用项目现场
国外甲醇生产能力主要分布在北美、 中南美、中东、亚洲、东欧、西欧、大洋 洲及非洲等地,美洲是世界上最大的甲醇 生产地,约占世界总生产能力的40%。
04 工艺条件的确定
一氧化碳加氢合成甲醇是放热反应,温度不同,热效应也不同。温度 越高,反应的热效应也越大。
制甲醇工艺流程

制甲醇工艺流程甲醇,化学式CH3OH,是一种重要的有机化合物,也是一种重要的工业原料。
甲醇工艺流程是指甲醇的生产过程,通常包括原料准备、合成、精馏和提纯等步骤。
下面将详细介绍甲醇工艺流程的各个环节。
1. 原料准备甲醇的主要原料是天然气、煤、木质纤维等。
天然气是最常用的原料,其主要成分是甲烷,可以通过催化气化制备合成气。
合成气中含有一定比例的一氧化碳和氢气,是甲醇合成的重要原料。
在原料准备阶段,需要对原料进行处理,去除杂质和调整成分比例,以满足甲醇合成的要求。
2. 合成甲醇的合成是通过一系列化学反应实现的。
通常采用的是低温低压合成法,即在一定的温度和压力条件下,将合成气经过催化剂催化反应生成甲醇。
常用的催化剂有氧化锌、铬、铜等金属氧化物。
合成反应是一个复杂的多步反应过程,需要严格控制反应条件和催化剂的选择,以提高甲醇的产率和纯度。
3. 精馏合成反应产生的甲醇与未反应的气体和液体混合物需要进行分离和提纯。
这一过程通常采用精馏法,即根据不同物质的沸点差异,通过升温使其分离。
在精馏过程中,需要控制温度和压力,以保证甲醇的纯度和产率。
4. 提纯精馏得到的甲醇仍然可能含有少量杂质,需要进行进一步的提纯。
常用的方法包括结晶法、萃取法和蒸馏法等。
通过这些方法,可以去除甲醇中的水、酸、碱等杂质,提高甲醇的纯度和质量。
以上就是甲醇工艺流程的主要环节。
通过原料准备、合成、精馏和提纯等步骤,可以实现甲醇的高效生产。
甲醇作为重要的工业原料,在化工、医药、农业等领域有着广泛的应用,其生产工艺的优化和改进对于提高甲醇的产率和质量具有重要意义。
希望本文对甲醇工艺流程有所帮助。
甲醇的制备方法

甲醇的制备方法
标题:甲醇的制备方法
一、引言
甲醇,化学式为CH3OH,是一种无色透明液体,有特殊气味,具有极强的挥发性。
甲醇在化工、制药、燃料等领域有着广泛的应用。
本文将介绍几种常见的甲醇制备方法。
二、甲醇的工业生产方法
1. 二氧化碳加氢法:这是一种以天然气或煤炭为原料,通过蒸汽重整得到氢气和一氧化碳,然后用氢气和一氧化碳合成甲醇的方法。
此法的优点是原料来源广泛,成本较低。
2. 煤炭间接液化法:这种方法是以煤炭为原料,先将其转化为合成气(一氧化碳和氢气),然后再通过催化剂的作用合成甲醇。
这种方法的优点是可以充分利用我国丰富的煤炭资源。
三、实验室制备甲醇的方法
1. 氧化锌催化还原法:利用甲醛与锌粉反应生成甲醇。
具体步骤如下:首先将甲醛溶液加入到含有氧化锌催化剂的反应器中,然后加热至沸腾,反应一段时间后冷却,再经过蒸馏和干燥,即可得到甲醇。
2. 醇酸酯水解法:利用乙酸甲酯与水在硫酸催化下进行水解反应,生成甲醇和乙酸。
该方法操作简单,但需要处理产生的副产物乙酸。
四、结论
甲醇作为一种重要的化工原料,其制备方法多种多样。
不同的制备方法有不同的优缺点,选择哪种方法主要取决于原料来源、设备条件以及产品纯度等要求。
随着科技的进步,相信未来会有更多高效、环保的甲醇制备方法被开发出来。
甲醇的生产方法

甲醇的生产方法甲醇是一种重要的有机化工原料,也是一种重要的能源化工产品。
它的生产方法主要有合成气法、煤焦油法、天然气法等。
其中,合成气法是目前主要的生产方法之一。
合成气法是指利用天然气、煤、石油等为原料,经过气化、合成气制备、甲醇合成等一系列工艺过程,最终生产甲醇的方法。
具体步骤如下:首先,原料气化。
将天然气、煤或石油等原料在气化炉中进行气化反应,生成合成气。
合成气主要由一氧化碳和氢气组成,是后续生产甲醇的重要原料。
其次,合成气制备。
将合成气经过一系列净化和转化反应,去除杂质,提高一氧化碳和氢气的纯度,为后续的甲醇合成提供优质的原料。
然后,甲醇合成。
将经过制备的合成气经过催化剂的作用,在高温高压条件下进行甲醇合成反应,生成甲醇产品。
甲醇合成反应是整个生产过程中的关键步骤,催化剂的选择和反应条件的控制对甲醇的产率和质量都有重要影响。
最后,甲醇的精制和提纯。
经过合成反应生成的甲醇产品中还会含有少量的杂质和水,需要经过精制和提纯过程,去除杂质和水分,得到纯净的甲醇产品。
总的来说,合成气法是一种成熟、稳定的甲醇生产方法,具有原料来源广泛、工艺流程简单、产品质量稳定等优点。
随着工艺技术的不断进步,合成气法生产甲醇的效率和能耗都在不断提高,为甲醇的生产提供了可靠的技术支持。
除了合成气法,煤焦油法和天然气法也是甲醇生产的重要方法。
煤焦油法是利用煤焦油为原料,通过气化、合成气制备和甲醇合成等工艺过程生产甲醇。
天然气法则是直接利用天然气为原料,经过催化转化反应合成甲醇。
这两种方法各有其适用的原料来源和工艺特点,为甲醇的生产提供了多样化的选择。
综上所述,甲醇的生产方法主要包括合成气法、煤焦油法和天然气法。
这些方法各有其适用的场合和优缺点,可根据实际情况选择合适的生产方法,以满足市场需求和经济效益的要求。
随着技术的不断进步,相信甲醇生产技术将会不断提高,为甲醇产品的质量和产量带来更大的提升。
生产甲醇的几种流程图

生产甲醇的几种流程图(一)甲醇的生产流程图(二)高压法合成甲醇工艺流程1-合成塔;2-水冷凝器;3-甲醇分离器;4-循环压缩机;5-铁油分离器;6-粗甲醇中间槽(三)低压法生产甲醇的原理流程图1加热炉2转化炉 3废热锅炉 4加热器 5脱硫器 6 、24、21、17、12为水冷器7气液分离器 8合成气三段离心式压缩机 9循环气压缩机10甲醇合成塔 11、15 热交换器 13甲醇分离器 14 粗甲醇中间槽16脱轻组分塔 18分离塔 19、22 再沸器20甲醇精馏塔 23 CO2吸收塔(四)甲醇生产高压法、中压法、低压法三种方法及区别高压工艺流程一般指的是使用锌铬催化剂,在300—400℃,30MPa高温高压下合成甲醇的过程。
自从1923年第一次用这种方法合成甲醇成功后,差不多有50年的时间,世界上合成甲醇生产都沿用这种方法,仅在设计上有某些细节不同,例如甲醇合成塔内移热的方法有冷管型连续换热式和冷激型多段换热式两大类;反应气体流动的方式有轴向和径向或者二者兼有的混合型式;有副产蒸汽和不副产蒸汽的流程等。
近几年来,我国开发了25-27MPa压力下在铜基催化剂上合成甲醇的技术,出口气体中甲醇含量4%左右,反应温度230-290℃。
ICl低压甲醇法为英国ICl公司在1966年研究成功的甲醇生产方法。
从而打破了甲醇合成的高压法的垄断,这是甲醇生产工艺上的一次重大变革,它采用51-1型铜基催化剂,合成压力5MPa。
ICl法所用的合成塔为热壁多段冷激式,结构简单,每段催化剂层上部装有菱形冷激气分配器,使冷激气均匀地进入催化剂层,用以调节塔内温度。
低压法合成塔的型式还有联邦德国Lurgi公司的管束型副产蒸汽合成塔及美国电动研究所的三相甲醇合成系统。
70年代,我国轻工部四川维尼纶厂从法国Speichim公司引进了一套以乙炔尾气为原料日产300吨低压甲醇装置(英国ICI专利技术)。
80年代,齐鲁石化公司第二化肥厂引进了联邦德国Lurge公司的低压甲醇合成装置。
甲醇生产工艺流程图

合成气为原料生产甲醇主要分为三种方式: 1 高压法
2 中压法
3 低压法
甲醇的生产方法介绍
1、高压法 用一氧化碳与氢在高温(340~420℃)
高压(30.0~50.0MPa)下用锌-铬氧化物作催化剂 合成甲醇。
2、低压法
一氧化碳与氢气为原料在低压(5.0MPa)和 275℃左右的温度下,采用铜基催化剂合成甲醇。低 压法成功的关键是采用了铜基催化剂,铜基催化剂 比锌-铬催化剂活性好得多,是甲醇合成反应能在较 低的压力和温度下进行。
甲醇合成反应器是甲醇生产的核心设备,从操作、结构
材料、及维修等方面考虑,甲醇反应器的基本要求如下:
1
、在操作上,要求催化剂床层的温度易控制,调
节灵活,合成反应的转化率高,催化剂的生产强度大,能以
较高能位回收反应热,床层中气体分布均匀,压降低。
2
、在结构上,要求简单紧凑,高压空间利用率高,
触媒装卸方便。
1 、温度高会影响催化剂的使用寿命。在温度高 的情况下,铜基催化剂晶格发生变化,催化剂 活性表面逐渐减少。如果温度超过280℃,催化 剂活性很快丧失。
2 、温度高会影响产品质量。反应温度高,在CO 加H2的反应中,副反应生产量增加,使 粗甲 醇中杂质增加,不但影响产品质量,而且增加 了H2的单耗。
选用合成压力一般为
4~6Mp。操作压力还受
400
350℃
催化剂活性、负荷高低、
空速大小、冷3 4 5 6 7 8 9 10 11 12
P/MPa
3、催化剂
在低压法甲醇合成工业中,催化剂的使用是至关重 要的。
铜基催化剂改进了甲醇合成塔结构,使得反应温度 能够严格控制,从而延长了铜基催化剂的使用寿命。 铜基催化剂的活性与铜含量有关
甲醇的制备

甲醇的制备
甲醇的制备如下:
1、甲醇的生产,主要是合成法,尚有少量从木材干馏作为副产回收。
合成的化学反应式为:2H2+CO→CH3OH。
2、将合成后的粗甲醇,经预精馏脱除甲醚。
(高压法最先实现工业合成的方法,但因其能耗大,加工复杂,材质要求苛刻,产品中副产物多,由ICI低压和中压法及Lurgi低压和中压法取代。
工业上合成甲醇几乎全部采用一氧化碳加压催化加氢的方法,工艺过程包括造气、合成净化、甲醇合成和粗甲醇精馏等工序。
)
3、将粗甲醇净化,净化过程包括精馏和化学处理。
化学处理主要用碱破坏在精馏过程中难以分离的杂质,并调节pH 值;精馏主要是脱除易挥发组分如二甲醚,以及难挥发的乙醇、高碳醇和水。
粗馏后的纯度一般都可达到98%以上。
4、将工业甲醇用精馏的方法将含水量降到0.01%以下。
再用次碘酸钠处理,可除去其中的丙酮。
经精馏得纯品甲醇。
5、BV-Ⅲ级甲醇的制备主要采用精馏工艺。
以工业甲醇为原料,经精馏、超净过滤、超净分装,得高纯甲醇产品。
一般均以工业甲醇为原料,经常压蒸馏除去水分,控制塔顶64~65℃,过滤除去不溶物即可。
- 1、下载文档前请自行甄别文档内容的完整性,平台不提供额外的编辑、内容补充、找答案等附加服务。
- 2、"仅部分预览"的文档,不可在线预览部分如存在完整性等问题,可反馈申请退款(可完整预览的文档不适用该条件!)。
- 3、如文档侵犯您的权益,请联系客服反馈,我们会尽快为您处理(人工客服工作时间:9:00-18:30)。
一、填空题
1.甲醇合成包括以下几个工序:原料气的制备、原料气的净化、压缩、甲醇合成和粗甲醇精馏。
2..原料气的净化包括两方面内容,一是脱除对甲醇合成催化剂有毒害作用的硫的化合物。
二是调节原料气的组成。
3.甲醇生产的原料大致有煤、石油、天然气和含H2、CO的工业废气等。
4.固体燃料制甲醇原料气中,①水分<5%②挥发分<6%③灰分<15%④硫含量<1%
5.电除尘分离气体中的悬浮物灰尘包括三个基本过程,即悬浮灰尘的荷电;电荷灰尘在电场中回收;除去收尘电极上的积灰。
6.气体脱硫的方法分为两类,一类是干法脱硫,一类是湿法脱硫。
7.甲醇原料气中的硫主要有硫化氢、硫氧化碳、二硫化碳、硫醇、硫醚、环状硫化物等。
8.一氧化碳变换催化剂主要包括中温变换催化剂、低温变换催化剂和宽温耐硫变换催化剂三种。
9.按吸附质与吸附剂之间引力场的性质,吸附可分为化学吸附和物理吸附。
10.工业上合成甲醇的流程分两类,一类是高压合成流程,使用锌铬催化剂,操作压力25—30MPa,操作温度330—390℃;另一类是低中压合成流程,使用铜系催化剂,操作压力5—15MPa,操作温度235—285℃.
11.工业用甲醇合成催化剂主要有锌铬催化剂和铜基催化剂两类。
12.甲醇合成主要设备有甲醇合成塔、水冷凝器、甲醇分离器、滤油器、循环压缩机、粗甲醇贮槽。
13.热钾碱法操作条件中,增加碳酸钾浓度,可提高溶液吸收CO2的能力,减少溶液循环与提高气体净化度。
14.甲醇可在银催化剂上,在600—650℃下进行气相氧化,或脱氢生成甲醛。
CH3OH+1/2O2=HCHO+H2O;CH3OH-H2→HCHO。
二、解答题
1.甲醇合成工艺条件?答:(1)反应温度:甲醇合成的反应均为放热反应,温度升高使反应速率加快,但平衡常数的数值将会降低。
其次,反应温度还与所选催化剂的活性温度有关,一般zn-cr催化剂的活性温度为320-400℃,铜基催化剂的活性温度为200-290℃。
另外,甲醇合成反应速率越高,则副反应增多。
(2)压力:从热力学分析,甲醇合成是体积缩小的反应,因此增加压力对平衡有利,可提高甲醇平衡产率。
在高压下,因气体体积缩小了,甲醇合成反应速率也会因此加快。
但是过高的压力会对设备制造、工艺管理及操作都带来困难,不仅增加了建设投资,而且增加了生产中的能耗。
对于合成甲醇的反应,目前工业上使用三种压力,即高压法、中压法、低压法。
最初采用锌铬催化剂,压力一般控制在25-30MPa。
目前普遍使用的铜基催化剂,操作压力可降至5MPa。
后来还发展了压力为10-15MPa的中压合成法,也采用铜基催化剂。
(3)气体组成:甲醇原料气的主要组成是CO、CO2与H2,生产中合理的氢碳比应比化学计量比略高些,实际上控制的略高于2,一般控制在
2.05-2.15,即通常保持略高的氢含量。
另外,甲醇原料气中还含有少量的CH4或N2等其他气体组分,对甲醇合成反应不利,所以要定期进行排放。
(4)空速:空速是指气体与催化剂接触时间的长短。
如果采用较低的空速,催化剂的生产强度较低。
如果采用较高的空速,催化剂的生产强度虽可以提高,但增大了预热所需传热面积,出塔热能利用降低,增大了动力消耗。
另外,空速增加到一定程度后,催化床温度将不能维持。
在甲醇合成生产中,空速一般控制在10000-30000h-1之间。
2.甲醇合成工艺流程?答:新鲜气由压缩机压缩到所需要的合成压力与从循环机来的循环气混合后分为两股,一股为主线进入热交换器,将混合气预热到催化剂活性温度,进入合成塔;另一股副线不经过热交换器而直接进入合成塔以调节进入催化层的温度。
经过反应后的高温气体进入热交换器与冷原料气换热后,进一步在水冷却器中冷却,然后在分离器中分离出液态粗甲醇,送精馏工序提纯制备精甲醇。
为控制循环气中惰性气的含量,分离出甲醇和水后的气体需小部分放空,大部分进循环机增压后返回系统,重新利用未反应的气体。
3.联醇生产的特点、工艺要求及工艺流程?答:(1)与合成氨联合生产甲醇通称为联醇,在铜洗工段前,设置甲醇合成塔,用合成氨原料气中的CO、CO2、及H2合成甲醇。
操作压力10-13MPa,采用铜基催化剂,催化剂床层温度240-280℃,合成塔一般采用自热式合成塔。
主要特点:①充分利用现有合成氨生产装置,
只需增添甲醇合成与精馏两套设备就可以生产甲醇,所以投资省、上马快。
②在合成氨厂设置联醇生产,不仅可以使变换工段CO指标放宽,变换的蒸汽消耗降低,而且可以使铜铣工段进口CO含量降低,铜洗负荷减轻,从而使合成氨厂的变换、压缩和铜洗工段能耗降低。
(2)联醇生产的特殊要求:①联醇工艺与合成氨生产串联,但为了提高催化剂的利用效率,经合成分离后的一部分气体可去铜洗进行精制,除去残存的CO、CO2后作为合成氨的原料气体使用,而另一部分气体则用循环机进行循环,继续合成甲醇。
②由于联醇工艺与合成氨生产串联,因此生产能力是以合成氨产量与甲醇产量之和,即所谓“总氨”产量来表示。
在“总氨”生产能力不变的情况下,甲醇生产能力用醇氨比来表示,醇氨比可以在一定范围内调整。
③联醇生产作为合成氨流程中的一个环节,甲醇生产会影响合成氨及整个系统的生产,在甲醇生产不正常或事故状态下,要维持合成氨的生产等。
(3)联醇生产工艺流程:由变换送来经过净化的变换气,其中含有约28%左右的CO2,为了减少氢气的消耗与提高粗甲醇的质量,变换气经压缩机加压到2MPa进入水洗塔,用水吸收CO2,使CO2降低到1.5%-3.0%.然后回压缩机进一步加压到13MPa左右,经水冷器和油分离器除去其中的油和水后,与甲醇循环机出口的循环气混合,进循环机滤油器进一步分离油水后,进入活性炭过滤器,除去气体中夹带的少量润滑油、铁锈及其他杂质,出来的是比较纯净的甲醇合成原料气,经甲醇合成塔之主、副线进入甲醇合成塔。
出塔气体进入水冷凝器,使合成的气态甲醇、二甲醚、高级醇、烷烃与水冷凝或溶解为液体,然后在分离器中把液体分离出来。
被分离出来的液体粗甲醇减压后到粗甲醇中间贮槽,以剩余压力送往精馏工段。
经分离后的一部分气体,由循环机加压后,循环回合成塔继续合成甲醇;另一部分气体经醇后气分离器,进一步除去气体中少量甲醇,进铜洗塔、碱洗塔进行精制,使精制后气体中(CO+CO2)<25cm3/m3,再回压缩机,加压到32MPa,送氨合成系统。
醇后气分离器分离下来的少量稀甲醇,减压后去粗甲醇中间贮槽。
4.工业生产上普遍采用的双塔流程中有两台精馏塔:预精馏塔和主精馏塔。
(1)①预精馏塔的主要作用是:第一,脱除粗甲醇中的二甲醚;第二,加水萃取,脱除与甲醇沸点相近的轻馏分;第三,除去其他轻组合有机杂质。
通过预精馏后,二甲醚和大部分轻组分基本脱除干净。
②预精馏塔组成:根据实际生产经验,为达到预精馏目的,预精馏塔至少需50块塔板,塔径为1—2m,板间距为300—500mm,总高度约20—30m。
入料口一般有2—4个。
(2)①主精馏塔的作用是:第一,将甲醇组分和水及重组分分离,得到产品精甲醇;第二,将水分离出来,并尽量降低其有机杂质的含量,排出系统;第三,分离出重组合—杂醇油;第四,采出乙醇,制取低乙醇含量的精甲醇。
②主精馏塔组成:根据生产实际经验,需要75—85层塔板,塔径一般为1.6—3m,板间距为300—600mm,塔总高度约为35—45m。
入料口设3—5个,精甲醇采出口有4个,重组分采出口设4—5个。
5. 甲醇生产中脱碳的原因及干法脱碳的原理?答:(1)以重油和煤、焦为原料制得的甲醇粗原料气中,二氧化碳是过剩的,合成甲醇时氢碳比太低,对合成反应极为不利,因此,这部分二氧化碳必须从系统中脱除,同时利用各种脱碳方法还可去除气体中的硫化氢。
(2)干法脱碳(原理)是利用空隙率极大的固体吸附剂在高压、低温条件下,选择性吸收气体中的某种或某几种气体,再将所吸附的气体在减压或升温条件下,解吸出来的脱碳方法。
常见的方法有变压吸附和变温吸附。
6.(1)一氧化碳变换的基本原理为CO+H2O=CO2+H2;(2)有机硫转化为无机硫:甲醇合成原料气必须将气体中总含硫量控制在0.2cm3/m3以下。
只有采用低温甲醇洗才能在变换前脱除有机硫。
设置变换工序,除噻吩外,其他有机硫化物均可在铁基变换催化剂上转化为H2S,便于后工序脱除。
如果变换工序采用的是耐硫催化剂,就不需设两次脱硫,即变换前无需脱硫,全部硫化物在变换后可一次脱除。
7.制备甲醇原料气,应合理控制二氧化碳与一氧化碳的比例?答:二氧化碳在原料气中的最佳含量,应根据甲醇合成所用的催化剂量与甲醇合成操作温度相应调整。
在使用锌—铬催化剂的高压合成装置中,原料气含二氧化碳4﹪—5﹪时,催化剂的使用寿命与生产能力不受影响,合成设备操作稳定而且可以自热,但是粗甲醇含水量为14%—16%。
因此,对于锌—铬催化剂上甲醇合成的反应,原料气中二氧化碳低于5%为宜。
在采用铜基催化剂时,原料气中二氧化碳可适当增加,可使塔内总放热量减少,以保护铜基催化剂温度均匀、稳定,不致过热,延长催化剂使用寿命。