高Al2O3炉渣对高炉生产的影响1
高Al2O3炉渣对高炉生产的影响

高Al2O3炉渣对高炉生产的影响随着我国钢铁产业的迅速发展,对炼铁原料的需求日益扩大,进口矿粉已占相当数量。
目前国内进口的矿粉主要是澳矿与印矿,这两种矿粉中Al2O3含量普遍偏高。
山东泰山钢铁集团(简称泰钢)高炉炉渣中Al2O3含量平均在18.2%左右,最高时可达到22%。
炉渣Al2O3含量高时炉渣的流动性和稳定性都将变差,易引起炉墙粘结与炉缸堆积,破坏高炉冶炼的正常进程,给高炉操作带来一系列的问题。
如不制定科学的操作方针与方法,将引起炉况不顺,影响产量与质量。
因此,Al2O3含量高的炉渣严重制约了高炉的正常生产。
2 Al2O3含量对炉渣性能的影响Al2O3属于中性,但在高炉冶炼中可认为是酸性物质,其熔点是2050℃,在高炉冶炼中与SiO2混合后仍产生高熔点(1545℃)的物质,使渣铁流动性差,分离困难。
当加入碱性物质如CaO或MgO后,尽管CaO的熔点是2570℃,MgO熔点是2800℃,但与SiO2和 Al2O3结合后生成低熔点(低于1400℃)的物质,在高炉内熔化,形成流动性良好的炉渣,使渣铁分离,保证高炉正常生产。
2.1 Al2O3小于15%时能够改善炉渣的稳定性当Al2O3含量在5%~20%、MgO含量小于20%时,在CaO/SiO2约为1.0的区域里熔化温度较低;当Al2O3含量低时,随着碱度的增加,炉渣熔化温度增加较快;当Al2O3含量大于10%后,随碱度增加,熔化温度增高减缓,熔化温度区域扩大,炉渣粘度随碱度变化也减缓,炉渣稳定性增加。
可以认为Al2O3的存在削弱了CaO/SiO2变化的影响。
2.2 高Al2O3炉渣对高炉冶炼的不利影响Al2O3小于15%时能够改善炉渣的稳定性,有利于高炉操作,但炉渣中Al2O3含量一般在15%~18%,原因是高Al2O3炉渣难以熔化,并且粘度增大,流动性变差,会产生以下负面影响:(1)高Al2O3炉渣的初渣堵塞炉料间的空隙,使料柱透气性变差,增加煤气通过时的阻力。
马钢10#高炉高Al2O3炉渣冶炼实践
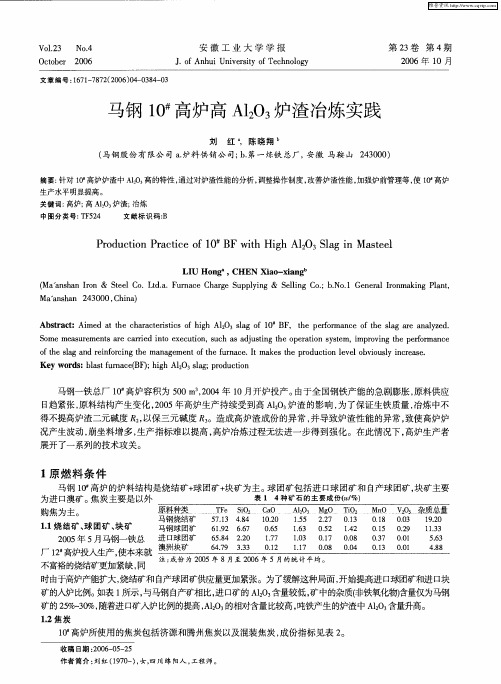
Ma nh n 4 0 0 C ia ' sa 2 3 0 , hn ) a
Ab t a t sr c :Ai d a h h r c e it s o i h A1 lg o 0 me tt e c a a trsi f h g 2 sa f 1 BF t e p ro ma c f t e sa r n l z d c 03 , h e f r n e o h lg a e a ay e .
摘要: 针对 1 0 高炉炉渣 中 A 高 的特性 , l 通过对炉渣性能 的分析 , 调整操作制度 , 改善炉渣性能 , 加强炉前管理等 , 1 高炉 使 生产水平 明显提高 。
关键词: 高炉; A:, 高 1 炉渣; O 冶炼
中 图分 类号 : F 2 T54 文 献标 识 码 : B
o e sa n e n o c n h n g me t ft e f r a e I ma e h r d c in l v lo v o sy i c e s . f h lg a d r i f r i g t e ma a e n u n c . t k s t e p o u t e e b i u l n r a e t o h o
P o u t n P a t e o 0 F wi g 2 l g i se l r d ci r c i f1 #B t Hih A1 S a n Ma te o c h O3
LI Hon .CHEN a -x ang U g Xi o i
( ' sa rn& Se l o Lda F raeC ag u pyn Ma nh nI a o t . t. un c h re S p lig& S ln o; . o1G nrl rn a igPa t eC . e igC . bN . e ea I m kn ln, l o
济钢高炉高Al2O3炉渣渣系优化试验研究

济钢 高炉 高 AI 炉渣渣 系优化试 验研究 2 O3
李 学付 , 贻 留, 方 杨金 福 , 马继 波 , 杨雄 文
( 济钢集团有限公司 , 山东 济南 20 0 ) 511 摘 要: 以济钢现场高炉 渣样为基 准 , 正交 设计方法 , 采用 设计 了2 组试验方案 , 5 研究 了w A , 1%~ 3 ( 1 ) 5 2 %的高炉炉渣 0 为
区 间 ( 图 3 、 ) 炉 渣 熔化 性 温 度影 响 不 大 。在 见 ab对 图 3 , A ,2 .%、 O 1 . c中 当 1 = 09 Mg = 32 O %为熔 化 性温 度
最低 。此时 , 降低 M O, 渣 的熔化性 温度将 升 g 炉
2 l 2 2 2 3 2 4
此, 必须采取合理的措施 , 降低高 A:, l 对炉渣黏度 O 的影 响 。研 究炉 渣 中铝 、 二元 碱度 对炉 渣黏 度和 熔
化性 温度 的影响 , 提出济钢 高炉合理 的渣 系组 成 。
1 1 1 1 l 3 50 9 0 .0 8 . 1 1 1 1 13 2 5 9 1 . 5 9 . 2 9 11 1 3 25 0 .5 9 . 2 1 12 140 . 0 0 .0 30 2 l 1 1 13 3 0 O 1 .0 9 . 21 1 1 1 13 0 0 3 .0 6 . 2l 1 1 1 l3 3 5 4 .5 9 .
1 1 11 138 . 7 O .5 14 1 1 1 2 1 3 9. 7 1 -O 8 3 1 9 1 1 l37 . 8 .O 28 1 1 1 1 l38 . 8 O .5 41
试验 号 A B c
1 4 1 5 1 6 1 7 l 8 l 9 2 O
2 1 l2 1 3 7 3 3 3 _0 9 . 2 l 1 1 13 5 0 3 2 .0 8 . 2 l 12 l3 90 l 2 .O 8 . 2 1 12 l3 80 2 4 -0 9 .
三安高炉高A12O3炉渣冶炼实践
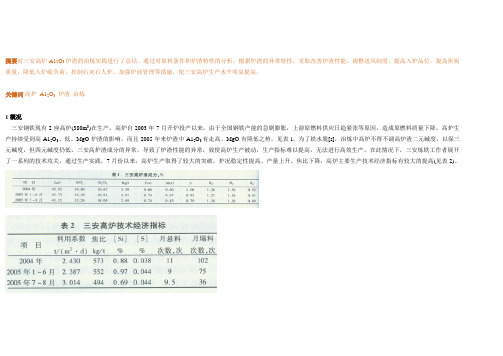
摘要对三安高炉A12O3炉渣的冶炼实践进行了总结。
通过对原料条件和炉渣特性的分析,根据炉渣的异常特性,采取改善炉渣性能,调整送风制度,提高入炉品位,提高焦炭质量,降低入炉硫负荷,控制石灰石人炉,加强炉前管理等措施,使三安高炉生产水平明显提高。
关键词高炉 A12O3炉渣冶炼1概况三安钢铁现有2座高炉(380m3)在生产。
高炉自2003年7月开炉投产以来,由于全国钢铁产能的急剧膨胀,上游原燃料供应日趋紧张等原因,造成原燃料质量下降,高炉生产持续受到高A12O3、低。
MgO炉渣的影响,而且2005年来炉渣中A12O3有走高、MgO有降低之势,见表l。
为了铁水脱[s],冶炼中高炉不得不调高炉渣二元碱度,以保三元碱度,但四元碱度仍低。
三安高炉渣成分的异常,导致了炉渣性能的异常,致使高炉生产被动,生产指标难以提高,无法进行高效生产。
在此情况下,三安炼铁工作者展开了一系列的技术攻关,通过生产实践,7月份以来,高炉生产取得了较大的突破,炉况稳定性提高、产量上升、焦比下降,高炉主要生产技术经济指标有较大的提高(见表2)。
2原料条件三安钢铁高炉无法进行高效冶炼的主要原因是人炉原料的化学成分变化较大。
2.1 烧结矿表3为三安高炉入炉烧结矿化学成分。
从表:可以看出,烧结矿中的A12O3含量有逐渐升高之势而MgO含量则在逐渐下行。
2.2球团矿、块矿三安高炉从一开始,坚持使用100%熟料作业,采用80%~85%烧结矿配加15%~20%球团矿的炉料结构,但进入2004年下半年,由于球团矿供量紧、价格高,为了降低成本,开始使用生矿配料。
表4为三安高炉所用的球团矿、生矿成分。
2.3焦炭表5为三安高炉所用的焦炭成分指标。
焦炭指标向好的方向发展。
3炉渣特性分析高炉渣成分以CaO、SiO2、Al2O3为主,但MgO在渣中又起到独特的作用,故以CaO一SiO2一Al2O3一MgO四元相图来讨论炉渣的有关特性。
三安高炉渣CaO偏上限,Al2O3严重高出上限,MgO偏下限,R2严重高出上限。
高炉高铝渣问题的探索与解决
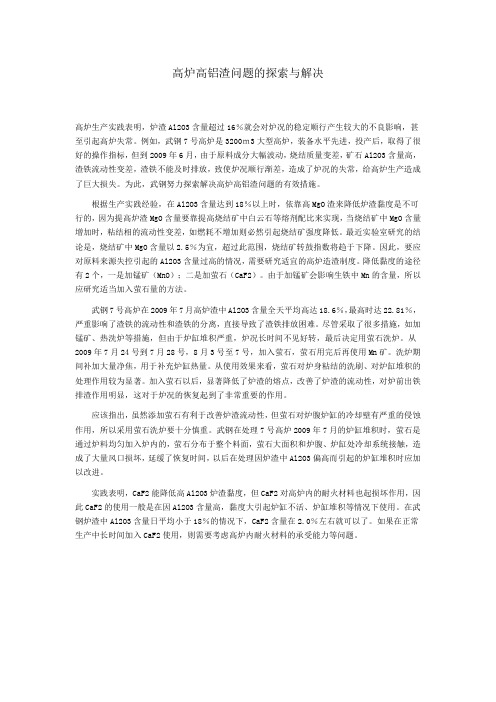
高炉高铝渣问题的探索与解决高炉生产实践表明,炉渣Al2O3含量超过16%就会对炉况的稳定顺行产生较大的不良影响,甚至引起高炉失常。
例如,武钢7号高炉是3200m3大型高炉,装备水平先进,投产后,取得了很好的操作指标,但到2009年6月,由于原料成分大幅波动,烧结质量变差,矿石Al2O3含量高,渣铁流动性变差,渣铁不能及时排放,致使炉况顺行渐差,造成了炉况的失常,给高炉生产造成了巨大损失。
为此,武钢努力探索解决高炉高铝渣问题的有效措施。
根据生产实践经验,在Al2O3含量达到18%以上时,依靠高MgO渣来降低炉渣黏度是不可行的,因为提高炉渣MgO含量要靠提高烧结矿中白云石等熔剂配比来实现,当烧结矿中MgO含量增加时,粘结相的流动性变差,如燃耗不增加则必然引起烧结矿强度降低。
最近实验室研究的结论是,烧结矿中MgO含量以2.5%为宜,超过此范围,烧结矿转鼓指数将趋于下降。
因此,要应对原料来源失控引起的Al2O3含量过高的情况,需要研究适宜的高炉造渣制度。
降低黏度的途径有2个,一是加锰矿(MnO);二是加萤石(CaF2)。
由于加锰矿会影响生铁中Mn的含量,所以应研究适当加入萤石量的方法。
武钢7号高炉在2009年7月高炉渣中Al2O3含量全天平均高达18.6%,最高时达22.81%,严重影响了渣铁的流动性和渣铁的分离,直接导致了渣铁排放困难。
尽管采取了很多措施,如加锰矿、热洗炉等措施,但由于炉缸堆积严重,炉况长时间不见好转,最后决定用萤石洗炉。
从2009年7月24号到7月28号,8月3号至7号,加入萤石,萤石用完后再使用Mn矿。
洗炉期间补加大量净焦,用于补充炉缸热量。
从使用效果来看,萤石对炉身粘结的洗刷、对炉缸堆积的处理作用较为显著。
加入萤石以后,显著降低了炉渣的熔点,改善了炉渣的流动性,对炉前出铁排渣作用明显,这对于炉况的恢复起到了非常重要的作用。
应该指出,虽然添加萤石有利于改善炉渣流动性,但萤石对炉腹炉缸的冷却壁有严重的侵蚀作用,所以采用萤石洗炉要十分慎重。
FeO和Al_2O_3质量分数对高炉初渣粘度的影响
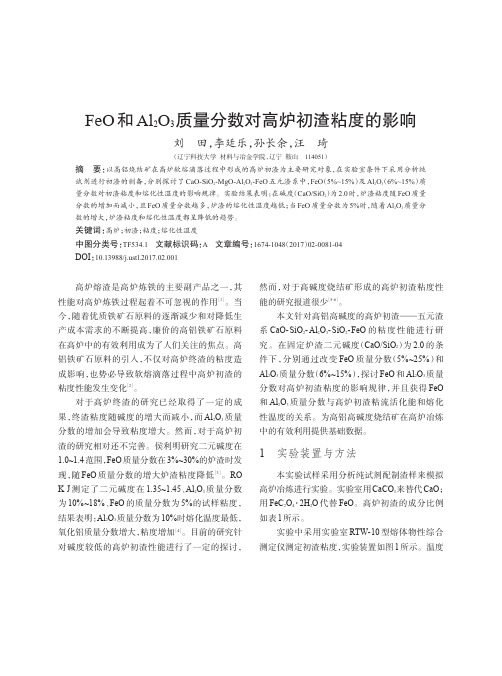
增至 15%,活化能变化不大,炉渣中简单的 Fe2+和 O2-离子的比例增大,流体阻力降低,粘度减小。另 外,炉渣活化能随 Al2O3 质量分数的增大而减小, 与图 3 的粘度曲线有很好的一致性;Al2O3 表现为 酸性,提供了炉渣简单的[AlO6]5-八面体结构,从而 降低炉渣粘度。
表 2 各成分炉渣的活化能 Tab.2 Activation energy of slag with different composition
图 2 三种 w( FeO)的炉渣粘度与温度的关系 Fig.2 Influence of FeO content on tviscosity of slag
图 3 为 FeO 质量分数为 5%、二元碱度为 2.0、 Al2O3的质量分数分别为 6%、9%、12%、15%的初渣 粘度-温度图。随 Al2O3的质量分数增大,粘度呈现 减小趋势。Al2O3 在炉渣中存在两性:一方面,破坏 了部分硅酸根离子所形成的网络结构[8];另一方 面 ,生 成 一 些 相 对 简 单 的[AlO6]5- 八 面 体 结 构[9]。 对于高炉终渣来说,由于碱度较低,随着 Al2O3 质 量 分 数 的 增 加 ,炉 渣 粘 度 也 随 之 增 大 ,流 动 性 变 差。但是,在本研究中,初渣碱度为 2.0,可以认为 Al2O3 在初渣中主要以简单的[AlO6]5-八面体结构 存在,间接地降低了初渣的碱度,使初渣中由于高 碱度而引起的固相组分比例降低,进而降低了初 渣的粘度。
较低,其质量分数的增大直接导致炉渣粘度和结 晶温度的降低;另外,FeO 在 Si-O 网络结构中提供 自由移动的 Fe2+和 O2-,而 Fe2+和 O2-与 Si-O 网络结 构相比较小,使炉渣粘度降低[7]。
烧结矿质量及其对高炉冶炼主要操作指标的影响

高炉主要操作指标
利用系数
燃料比
1.228
813
1.998
559.4
2.412
535.0
2.153
496.7
2.28
478.0
0.788
793.2
0.463
878.0
1.519
556.9
1.719
547.6
2.147
538.0
0.472
986
1.234
610
2.04
601
2.20
550
近几年有不少钢铁企业采用低品位、大渣量的做法,主观愿望想降低成本,实际适得其反,造
2 烧结矿质量的内涵和价值
烧结矿的质量由化学成分、物理性能和冶金性能三部分组成,它们三者间的关系是:化学成分是基 础,物理性能是保证,冶金性能是关键。
2.1 烧结矿的主要化学成分及其价值
烧结矿的主要化学成分包括品位和SiO2、碱度、MgO、Al2O3和FeO,还有S、P、Ka2O、ZnO和Cl等有 害元素。 2.1.1 含铁品位对烧结矿质量的价值
900℃还原/% 80.75 80.10 77.12 85.51 81.56 79.12
烧结生产之所以要配MgO是为了满足高炉炼铁炉渣流动性、脱硫和脱碱(K2O+Na2O)的需 求。
2.1.6 FeO含量对烧结矿质量的价值 FeO含量也是烧结矿的一个重要内容,FeO含量的高低直接影响烧结矿的强度、粒度和冶金
烧结配矿优化及高炉生产应对实践

M etallurgical smelting冶金冶炼烧结配矿优化及高炉生产应对实践张利波摘要:近些年,高炉炼铁一直是冶炼生铁过程中应用的最重要的技术,居于主导地位。
最近几年,全球的学者即使研究出许多高炉炼铁技术,不过在制作成本的经济性方面,依旧不能和以往的高炉制造技术进行比较。
国内,因为历史条件与制造成本的干预,非高炉炼铁技术的发展速度较慢,超过百分之九十五的生铁依旧借助高炉进行制作。
高炉生产期间,入炉原料重点是烧结矿、球团矿和块矿,而且烧结矿的比例高于百分之八十。
所以,烧结矿的品质高低在高炉生产过程中占据着主导作用,提升烧结矿品质对于缩减制作成本、保证高炉良好的运行具备着较高的作用。
关键词:烧结配矿优化;高炉生产;应对实践对策现如今使用的矿粉、矿石以及含铁工业物料等,使得烧结原料逐渐繁杂,如何通过原料的优化搭配实现品质最优、成本最优是钢铁生产重点关注的问题。
烧结矿是高炉的主要“口粮”,其质量的好坏直接影响高炉生产稳定和各项经济技术指标的完成。
为了确保烧结矿质量稳定,工作人员运用智能化手段,提升烧结配料精度,改善烧结矿质量,为高炉高效生产筑牢保障。
1 研究背景1.1 铁矿粉市场行情在我国环保政策高效实施的环境下,钢铁公司开始限制产量,铁矿石的需求数目逐渐下降。
不过在2017年~2018年鉴因为钢铁利润空间的变化,个别产能被释放,导致铁矿石的需求数目逐渐提升。
身为铁矿石的出产地澳大利亚与巴西境内铁矿石的出产量也随之增加,不过市场依然处于供需不平衡的状态,导致铁矿石的流通价格较高。
并且,因为持续的挖掘与应用优质资源,导致地球上的优质铁矿石数量逐步的减少,铁矿石供需框架的调节会是后期国际上需要一起面临与开展的工作。
我国铁矿石的存储数量位于世界前列,大约为整体存储量的百分之十二,整体的应用潜力较高。
由于铁矿的开采、加工工艺的提升,铁矿资源的整体应用会呈现出良好的经济性。
1.2 烧结配矿结构优化的理论基础低品矿粉为减少烧结资金投入最为重要的方式,不过品味下降可能导致非铁元素的高效提升,造成烧结矿品质降低,为后续高炉生产留下隐藏的危害,科学的应用铁矿粉高温特性展开烧结配矿,能够提升烧结配矿的效果。
对高炉操作的分析

对高炉操作的分析高炉操作是一项生产实践与理论性很强的工艺流程。
本文介绍了高炉冶炼对原燃料(精料)的要求和高炉冶炼的四大基本操作制度(装料制度、送风制度、热制度、造渣制度)以及冷却制度的内容与选择;也介绍了高炉的炉前操作对高炉冶炼的影响,高炉操作的出铁口维护等内容;同时,还阐述了高炉冶炼的强化冶炼技术操作如高炉的高压操作,富氧喷煤操作(富氧操作、喷煤粉操作、富氧喷煤操作),高风温操作(风温对高炉的影响和风温降焦比等)等操作细节。
本文介绍的内容对高炉冶炼都很重要,望与高炉的实际情况结合,减少高炉操作失误,从而使高炉冶炼取得更好的经济技术指标。
中国是世界炼铁大国,2007年产铁4.894亿吨,占世界49.5%,有力地支撑我国钢铁工业的健康发展。
进入21世纪以来,我国钢铁工业高速发展,新建了大批大、中现代化高炉。
在当前国内外市场经济竞争更加激烈的情况下,各企业都面临如何进一步降低生产成本的问题。
在高炉炼铁过程中,如何操作,改善操作,保持炉况稳定进行,降低消耗,提高经济效益是高炉工作者的一项重要任务。
在遵循高炉冶炼基本规则的基础上,根据冶炼条件的变化,及时准确地采取调节措施。
一.高炉炼铁以精料为基础高炉炼铁应当认真贯彻精料方针,这是高炉炼铁的基础.,精料技术水平对高炉炼铁技术指标的影响率在70%,高炉操作为10%,企业现代化管理为10%,设备运行状态为5%,外界因素(动力,原燃料供应,上下工序生产状态等)为5%.。
高炉炼铁生产条件水平决定了生产指标好坏。
因此可见精料的重要性。
1. 精料方针的内容:·高入炉料含铁品位要高(这是精料技术的核心),入炉矿含铁品位提高1%,炼铁燃料比降低1.5%,产量提高2.5%,渣量减少30kg/t,允许多喷煤15 kg/t。
原燃料转鼓强度要高。
大高炉对原燃料的质量要求是高于中小高炉。
如宝钢要求焦炭M40为大于88%,M10为小于6.5%,CRI小于26%,CSR大于66%。
高炉炼铁试题库

高炉炼铁试题库一、填空题1.高炉生产的主要原料是、、和熔剂。
答案:铁矿石及其代用品;锰矿石;燃料2.焦碳的高温反应性,反应后强度英文缩写分别为、、其国家标准值应该是、(百分比)。
答案:CRI、CSR、≤35%、≥55%3.矿石中的Pb是一种有害杂质,其含量一般不得超过。
答案:0.1%4.每吨生铁消耗的含Fe矿石中,每增加1%SiO2,将使吨铁渣量增加。
答案:35-40kg5.焦炭中的硫多以、和的形态存在,其中以形态存在的占全部硫量的67%-75%。
答案:硫化物、硫酸盐;有机硫;有机硫6.矿石的冶金性能包括、性能、还原膨胀性能、荷重还原软化性能和熔滴性能。
答案:还原性、低温还原粉化7.炼铁的还原剂主要有三种,即、和。
答案:碳、一氧化碳、氢8.高炉内CO不能全部转变成CO2的原因是因为铁氧化物的需要过量的CO与生成物平衡。
答案:间接还原9.高炉内碱金属的危害根源在于它们的。
答案:循环和富集10.选择风机时,确定风机出口压力应考虑风机系统阻力、和等因素。
答案:料柱透气性;炉顶压力11.停炉方法有和两种方法。
答案:物料填充;空料线打水12.高炉的热效率高达,只要正确掌握其规律,可进一步降低燃料消耗。
答案:75%-80%13.要使炉况稳定顺行,操作上必须做到三稳定,即、、。
答案:炉温、碱度、料批14. 造渣制度应根据和确定。
答案:原燃料条件;生铁品种15. 风口前每千克碳素燃烧在不富氧,干风的条件下,所需风量为。
答案:4.44m3/kg16. 开炉料的装入方法有、、。
答案:炉缸填柴法、填焦法、半填柴法17. 影响高炉寿命的因素有筑炉材质、、操作制度和措施。
答案:冷却设备和冷却制度、护炉与补炉18. 铁矿石还原速度的快慢,主要取决于和的特性。
答案:煤气流;矿石19. 选择冷却壁结构型式,要以为基础,以防止为目的,以防止(冷却壁破损)为措施,以作为根本的原则。
答案:热负荷;内衬侵蚀和脱落;高炉长寿20. 一般风温每提高100℃,使理论燃烧温度升高,喷吹煤粉每增加10kg/t,理论燃烧温度降低。
高炉炉缸堆积的原因及处理方法

高炉炉缸堆积的原因及处理方法2016-10-12王筱留,祁成林冶金之家通常,炉温波动较大、煤气流分布不太正常时,采用一般调节手段,在短期内就可以纠正,转为正常。
但是国内多座高炉因长期失常,处理困难.造成重大损失:这种现象出现在长期休风或封炉复风后的较长一段时间,由于钢铁企业调度不当,使高炉较长时间的慢风操作后,再转入正常生产时出现炉况失常,造成炉缸不活、堆积、本文详细分析了高炉炉缸堆积的原因,介绍了炉缸堆积的处理方法。
1 炉缸堆积的征状1)出铁前后风量和风压变化,出铁前风量减少、风压升高,出铁后风量增加、风压下降,形成周期性波动;2)炉渣变粘,有时带铁,即渣铁分离不好,这在高铝低镁渣表现突出;3)煤气流分布呈现边缘过度发展,中心打不开;4)风口工作不均匀,时有升降和未充分加热的黑焦降落到风口;5)炉缸工作不均匀而且顺行差。
上述征状操作者是知道的,但是在生产中不是明显地同时出现,尤其是仪表检测手段不齐全的高炉更易被忽视。
最终表现为炉缸不活,炉子不接受风量,产量较低。
这是炉缸堆积的初期征兆,需要认真寻找原因,对症处理。
2 炉缸堆积的主要原因原燃料质量问题1)焦炭质量变差是炉缸堆积的重要原因实践表明,焦炭质量对高炉炉缸影响很大,而且是造成炉缸失常的重要原因。
从焦炭在炉内劣化的过程看,在块状带还未发生,碳熔损反应前重要的是 M10,而在熔损反应发生区则是 CRI 和 CSR,而对炉缸工作来说是 CSR,它决定着软熔带焦窗的透气性,滴落带焦塔(死料柱)的透气性和透液性,因为 M10、M40、CRI 和 CSR 决定着高炉内各部位的空隙度ξC,空隙度的变化将影响煤气流的流向。
目前高炉炉缸不活、堆积大多是由焦炭质量变差造成的,我国焦炭质量与高炉炼铁的要求有一定差距。
2)捣固焦质量问题目前,正在推广、大量销售给高炉生产用的捣固焦质量应该引起大家注意。
焦炭是煤在隔绝空气下干馏而成的,其质量与配煤、煤在高温下产生胶质的数量、炼焦过程工艺参数等诸多因素有关。
炉渣中Al2O3含量升高的影响及处理措施

炉渣中Al2O3含量升高的影响及处理措施通过对2005年1号高炉各项生产指标观察,明显地看出进入秋季高炉生产的黄金季节,产量水平却在下滑,经过对2005年9月份首秦1号高炉生产情况分析,得出渣中Al2O3升高是造成产量下滑的一项重要原因,给高炉顺行带来严重影响。
为此而成立精料小组,采取组织跟踪取样检验和统计分析的方法,通过调节烧结矿配料结构,以改善炉渣性能,从而有效控制了原燃料成分波动带来的不利影响,同时高炉做出调整,保证了高炉生产顺行,使各项技术指标维持在先进水平。
标签:高炉;Al2O3;炉渣;精料1、概况:首秦1号高炉于2004年6月6日建成投产。
设计有效容积为1200m3,18个风口2个出铁口。
采用俄罗斯卡鲁金顶燃式热风炉,煤气空气双预热,无料钟炉顶,全软水密闭循环冷却,喷涂内衬,高炉煤气连续自动分析,炉顶成像监测和炉喉十字测温煤气监测系统,螺旋排渣技术等一系列国内外新技术。
特别是高炉煤气回收系统采用全干式低压脉冲布袋除尘新工艺,是国内首次在1200m3级的高炉应用并取得成功,在热风炉全烧高炉煤气条件下,风温可达1250℃,风量最高3250m3/min,利用系数2.25,使用寿命15年,使用原料为资产烧结矿加秘鲁球团矿和澳大利亚块矿。
投产初期受单一生产线影响,每一环节都会产生瓶颈效应,使高炉生产受到限制,进入2005年以后,每月生产都超过设计利用系数,进入2005年夏季,在节能降耗方面尤为突出,6月份入炉焦比已达301Kg/t,然而到了秋季高炉的黄金生产时期产量却一度下滑。
2005年1号高炉各项经济技术指标统计如下表,经分析发现高炉渣中Al2O3含量一段时间突然升高,炉渣粘度升高,流动性变差,已经对高炉顺行带来影响。
因此如何将高炉渣中的Al2O3含量控制在合理范围内,在炉渣中Al2O3含量较高情况下,各项经济技术指标仍达先进水平,是首秦炼铁系统的重点攻关课题。
从表中显示7月到10月产量下降,焦比升高,萤石用量9月对多。
高炉矿渣质量系数
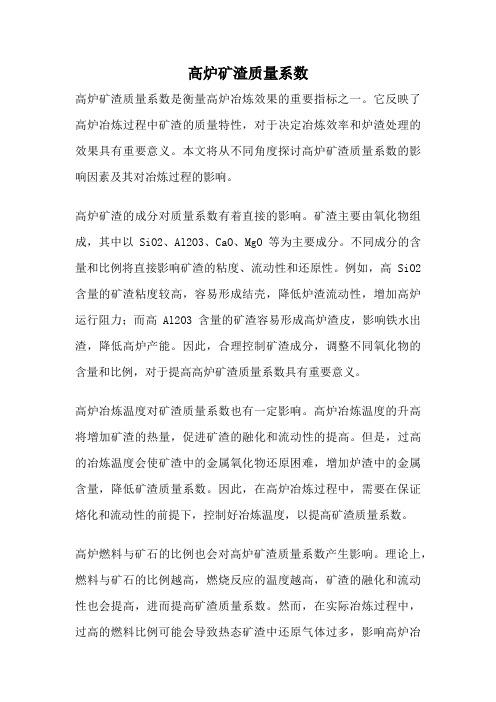
高炉矿渣质量系数高炉矿渣质量系数是衡量高炉冶炼效果的重要指标之一。
它反映了高炉冶炼过程中矿渣的质量特性,对于决定冶炼效率和炉渣处理的效果具有重要意义。
本文将从不同角度探讨高炉矿渣质量系数的影响因素及其对冶炼过程的影响。
高炉矿渣的成分对质量系数有着直接的影响。
矿渣主要由氧化物组成,其中以SiO2、Al2O3、CaO、MgO等为主要成分。
不同成分的含量和比例将直接影响矿渣的粘度、流动性和还原性。
例如,高SiO2含量的矿渣粘度较高,容易形成结壳,降低炉渣流动性,增加高炉运行阻力;而高Al2O3含量的矿渣容易形成高炉渣皮,影响铁水出渣,降低高炉产能。
因此,合理控制矿渣成分,调整不同氧化物的含量和比例,对于提高高炉矿渣质量系数具有重要意义。
高炉冶炼温度对矿渣质量系数也有一定影响。
高炉冶炼温度的升高将增加矿渣的热量,促进矿渣的融化和流动性的提高。
但是,过高的冶炼温度会使矿渣中的金属氧化物还原困难,增加炉渣中的金属含量,降低矿渣质量系数。
因此,在高炉冶炼过程中,需要在保证熔化和流动性的前提下,控制好冶炼温度,以提高矿渣质量系数。
高炉燃料与矿石的比例也会对高炉矿渣质量系数产生影响。
理论上,燃料与矿石的比例越高,燃烧反应的温度越高,矿渣的融化和流动性也会提高,进而提高矿渣质量系数。
然而,在实际冶炼过程中,过高的燃料比例可能会导致热态矿渣中还原气体过多,影响高炉冶炼的稳定性和安全性。
因此,需要在燃料与矿石的比例上做出合理的调整,以达到最佳的高炉矿渣质量系数。
高炉操作参数的调整也是影响高炉矿渣质量系数的重要因素之一。
高炉操作参数包括风温、风速、料层厚度、矿石粒度等。
风温和风速的调整可以改变高炉内的气流分布和温度分布,进而影响矿渣的融化和流动性。
料层厚度的调整可以影响高炉内气固两相的接触程度,进而影响矿渣的还原性和流动性。
矿石粒度的调整可以改变高炉内固体颗粒的堆积密度和渗透性,进而影响矿渣的渗透性和流动性。
因此,合理调整高炉操作参数,对于提高矿渣质量系数具有重要意义。
《高炉炼铁技术》项目8任务8.3造渣过程及对冶炼过程的影响
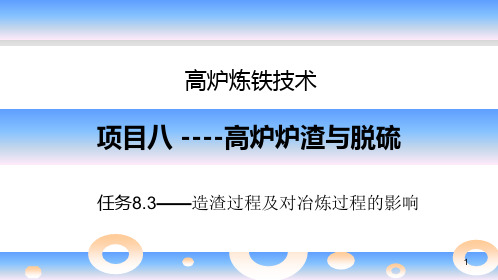
三、我国几种特殊炉渣的冶炼问题
我国土地辽阔,铁矿石资源特点各异,而且复合矿又多,除 高TiO渣和高CaF2渣外,还有一些特殊炉渣。 1.高Al203渣 一般炉渣中含Al20310%~15%,较合适。但有些Al203高 的矿石,或高焦比,高灰分的生产高炉,容易造成Al203超 过20%~25%,它的炉渣特点是难熔而且粘度大。可采用 增大碱性氧化物浓度的办法来降低粘度,但由于它本身熔点 也高,故不可过多使用。
3)初渣生成。矿石从软化到熔融滴落就形成了初渣。
4
3.中间渣的变化 形成的初渣在滴落下降过程中,随着温度升高,化学成分和 物理性质将不断发生变化;FeO不断被还原减少,流动性随 温度升高而增加。实际上,中间渣就是在风口水平以上,软 熔带以下,正在滴落过程中的炉腹渣。中间渣能否顺利落下, 取决于原料成分和炉温的•。稳定。矿石成分不稳定,往往造成 炉温和中渣成分的激烈波动,导致粘度的剧变,使高炉不顺。 使用热态强度高的焦炭,保证气流正常分布是中渣顺利滴落 的基本条件。
8
2.高MgO渣 炉渣中MgO>15%时容易造成熔点升高,它与高Al203 渣相反,这时应控制CaO/SiO2值不可过大。MgO=15 %~20%时,CaO/SiO2=0.9为宜MgO=25%时, CaO/SiO2=0.8为宜。
3.高Al203,高Mg0渣 此种炉渣更难冶炼,难熔、粘度大,应控制渣中 Al203+MgO≤40%,而且CaO/SiO2<1.0。
9
4.高K20,高Na20渣 钾(K)钠(Na)的化合物主要以各种硅酸盐或碳酸盐的形态进 入高炉,随炉料下降到高温区后,被碳还原为金属钾与钠, 由于其汽化温度低(钾766℃,钠890℃)还原后立即变成蒸 气进入煤气流中,气态的金属钾、钠在上升过程中与其他 物质反应形成氰化物、硅酸盐、碳酸盐及少量硫酸盐钾钠 化合物,并且分别以固态或液态沉积在炉料的表面与孔隙 中,或被软熔炉料所吸收形成初渣。
高炉炼铁 氧化铝和氧化镁含量对炉渣的影响
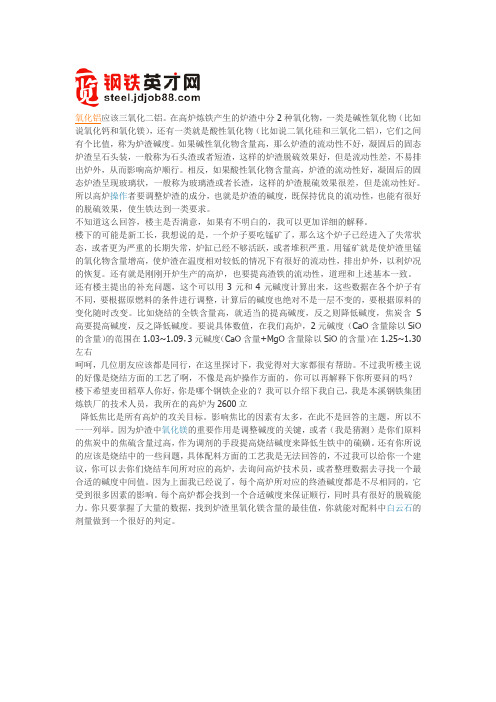
氧化铝应该三氧化二铝。
在高炉炼铁产生的炉渣中分2种氧化物,一类是碱性氧化物(比如说氧化钙和氧化镁),还有一类就是酸性氧化物(比如说二氧化硅和三氧化二铝),它们之间有个比值,称为炉渣碱度。
如果碱性氧化物含量高,那么炉渣的流动性不好,凝固后的固态炉渣呈石头装,一般称为石头渣或者短渣,这样的炉渣脱硫效果好,但是流动性差,不易排出炉外,从而影响高炉顺行。
相反,如果酸性氧化物含量高,炉渣的流动性好,凝固后的固态炉渣呈现玻璃状,一般称为玻璃渣或者长渣,这样的炉渣脱硫效果很差,但是流动性好。
所以高炉操作者要调整炉渣的成分,也就是炉渣的碱度,既保持优良的流动性,也能有很好的脱硫效果,使生铁达到一类要求。
不知道这么回答,楼主是否满意,如果有不明白的,我可以更加详细的解释。
楼下的可能是新工长,我想说的是,一个炉子要吃锰矿了,那么这个炉子已经进入了失常状态,或者更为严重的长期失常,炉缸已经不够活跃,或者堆积严重。
用锰矿就是使炉渣里锰的氧化物含量增高,使炉渣在温度相对较低的情况下有很好的流动性,排出炉外,以利炉况的恢复。
还有就是刚刚开炉生产的高炉,也要提高渣铁的流动性,道理和上述基本一致。
还有楼主提出的补充问题,这个可以用3元和4元碱度计算出来,这些数据在各个炉子有不同,要根据原燃料的条件进行调整,计算后的碱度也绝对不是一层不变的,要根据原料的变化随时改变。
比如烧结的全铁含量高,就适当的提高碱度,反之则降低碱度,焦炭含S 高要提高碱度,反之降低碱度。
要说具体数值,在我们高炉,2元碱度(CaO含量除以SiO 的含量)的范围在1.03~1.09,3元碱度(CaO含量+MgO含量除以SiO的含量)在1.25~1.30左右呵呵,几位朋友应该都是同行,在这里探讨下,我觉得对大家都很有帮助。
不过我听楼主说的好像是烧结方面的工艺了啊,不像是高炉操作方面的,你可以再解释下你所要问的吗?楼下希望麦田稻草人你好,你是哪个钢铁企业的?我可以介绍下我自己,我是本溪钢铁集团炼铁厂的技术人员,我所在的高炉为2600立降低焦比是所有高炉的攻关目标。
高铝对高炉炼铁的影响及优化
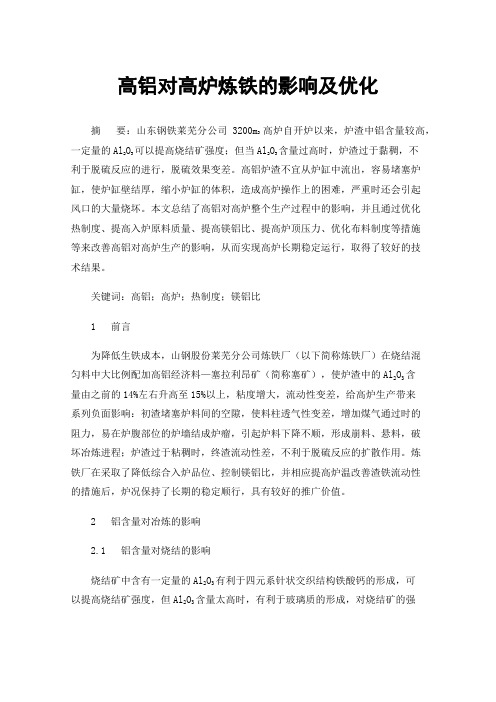
高铝对高炉炼铁的影响及优化摘要:山东钢铁莱芜分公司3200m3高炉自开炉以来,炉渣中铝含量较高,一定量的Al2O3可以提高烧结矿强度;但当Al2O3含量过高时,炉渣过于黏稠,不利于脱硫反应的进行,脱硫效果变差。
高铝炉渣不宜从炉缸中流出,容易堵塞炉缸,使炉缸壁结厚,缩小炉缸的体积,造成高炉操作上的困难,严重时还会引起风口的大量烧坏。
本文总结了高铝对高炉整个生产过程中的影响,并且通过优化热制度、提高入炉原料质量、提高镁铝比、提高炉顶压力、优化布料制度等措施等来改善高铝对高炉生产的影响,从而实现高炉长期稳定运行,取得了较好的技术结果。
关键词:高铝;高炉;热制度;镁铝比1 前言为降低生铁成本,山钢股份莱芜分公司炼铁厂(以下简称炼铁厂)在烧结混匀料中大比例配加高铝经济料—塞拉利昂矿(简称塞矿),使炉渣中的Al2O3含量由之前的14%左右升高至15%以上,粘度增大,流动性变差,给高炉生产带来系列负面影响:初渣堵塞炉料间的空隙,使料柱透气性变差,增加煤气通过时的阻力,易在炉腹部位的炉墙结成炉瘤,引起炉料下降不顺,形成崩料、悬料,破坏冶炼进程;炉渣过于粘稠时,终渣流动性差,不利于脱硫反应的扩散作用。
炼铁厂在采取了降低综合入炉品位、控制镁铝比,并相应提高炉温改善渣铁流动性的措施后,炉况保持了长期的稳定顺行,具有较好的推广价值。
2 铝含量对冶炼的影响2.1 铝含量对烧结的影响烧结矿中含有一定量的Al2O3有利于四元系针状交织结构铁酸钙的形成,可以提高烧结矿强度,但Al2O3含量太高时,有利于玻璃质的形成,对烧结矿的强度和低温还原粉化性能不利[1]。
实践证明,当烧结矿中铝含量>2.5%,对烧结矿强度和低温还原粉化性能影响较大。
2.2 铝含量对高炉生产的影响Al2O3在炉渣中有一定的脱硫效果,但弱于CaO和MgO。
对高炉生产的影响具体表现为:在炉内,压差升高,上部容易悬料,炉缸容易粘结堆积;在炉外,主沟内渣铁不易分离,渣中带铁,渣沟内炉渣流动性很差,容易结壳。
高炉炼铁中炉渣成分对钢铁质量的影响
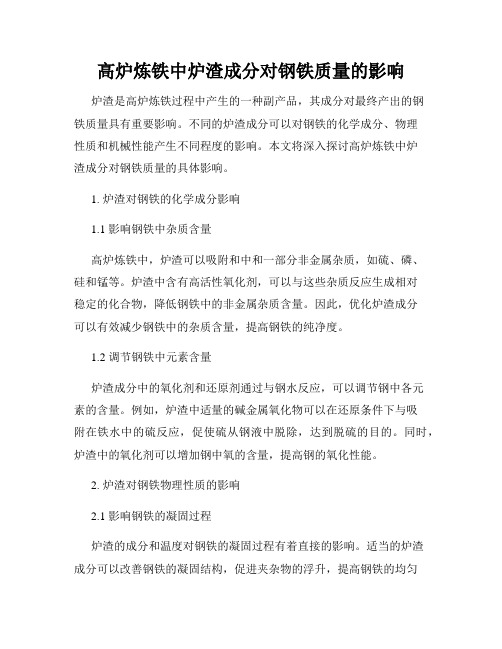
高炉炼铁中炉渣成分对钢铁质量的影响炉渣是高炉炼铁过程中产生的一种副产品,其成分对最终产出的钢铁质量具有重要影响。
不同的炉渣成分可以对钢铁的化学成分、物理性质和机械性能产生不同程度的影响。
本文将深入探讨高炉炼铁中炉渣成分对钢铁质量的具体影响。
1. 炉渣对钢铁的化学成分影响1.1 影响钢铁中杂质含量高炉炼铁中,炉渣可以吸附和中和一部分非金属杂质,如硫、磷、硅和锰等。
炉渣中含有高活性氧化剂,可以与这些杂质反应生成相对稳定的化合物,降低钢铁中的非金属杂质含量。
因此,优化炉渣成分可以有效减少钢铁中的杂质含量,提高钢铁的纯净度。
1.2 调节钢铁中元素含量炉渣成分中的氧化剂和还原剂通过与钢水反应,可以调节钢中各元素的含量。
例如,炉渣中适量的碱金属氧化物可以在还原条件下与吸附在铁水中的硫反应,促使硫从钢液中脱除,达到脱硫的目的。
同时,炉渣中的氧化剂可以增加钢中氧的含量,提高钢的氧化性能。
2. 炉渣对钢铁物理性质的影响2.1 影响钢铁的凝固过程炉渣的成分和温度对钢铁的凝固过程有着直接的影响。
适当的炉渣成分可以改善钢铁的凝固结构,促进夹杂物的浮升,提高钢铁的均匀性和性能。
同时,通过调节炉渣温度,可以控制钢铁的冷却速率,对钢的初晶组织和晶粒尺寸产生影响,进而影响钢铁的宏观力学性能。
2.2 影响钢铁的热传导性能炉渣成分中的氧化物对钢铁的热传导性能有一定的影响。
例如,适量添加的碱金属氧化物可以提高炼钢渣的热导率,加快钢铁的冷却速度,改变钢的晶化过程,从而影响钢铁的组织和性能。
3. 炉渣对钢铁机械性能的影响3.1 影响钢铁的强度和塑性高炉炼铁过程中炉渣的成分直接影响钢铁的强度和塑性。
合适的炉渣成分可以调节钢铁的晶格形貌,改善钢的晶界结构,提高钢材的强度。
同时,炉渣的成分也能影响钢铁的晶界塑性,合理选择炉渣成分可以提高钢材的塑性,使其具有更好的韧性和延展性。
3.2 影响钢铁的耐蚀性能高炉炼铁过程中炉渣的成分对钢铁的耐蚀性能有一定影响。
炼铁原理解析高炉内燃烧反应与炉渣生成的热力学分析
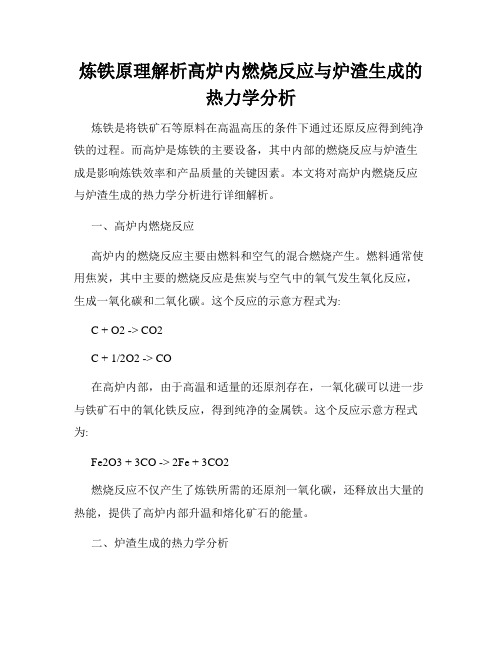
炼铁原理解析高炉内燃烧反应与炉渣生成的热力学分析炼铁是将铁矿石等原料在高温高压的条件下通过还原反应得到纯净铁的过程。
而高炉是炼铁的主要设备,其中内部的燃烧反应与炉渣生成是影响炼铁效率和产品质量的关键因素。
本文将对高炉内燃烧反应与炉渣生成的热力学分析进行详细解析。
一、高炉内燃烧反应高炉内的燃烧反应主要由燃料和空气的混合燃烧产生。
燃料通常使用焦炭,其中主要的燃烧反应是焦炭与空气中的氧气发生氧化反应,生成一氧化碳和二氧化碳。
这个反应的示意方程式为:C + O2 -> CO2C + 1/2O2 -> CO在高炉内部,由于高温和适量的还原剂存在,一氧化碳可以进一步与铁矿石中的氧化铁反应,得到纯净的金属铁。
这个反应示意方程式为:Fe2O3 + 3CO -> 2Fe + 3CO2燃烧反应不仅产生了炼铁所需的还原剂一氧化碳,还释放出大量的热能,提供了高炉内部升温和熔化矿石的能量。
二、炉渣生成的热力学分析在高炉内,炼铁过程中不可避免地产生大量的炉渣。
炉渣是由矿石中的非金属物质和燃料中的灰份等杂质在高温下熔化形成的。
炉渣的主要成分是氧化物和硅酸盐。
其中,炉渣中的主要氧化物包括SiO2、FeO、Al2O3等。
它们的生成需要满足化学反应的热力学条件,例如以下反应:SiO2 + 2C -> Si + 2CO2FeO + SiO2 -> Fe2SiO4这些反应在高温下进行,其产物成为固态的炉渣。
此外,炉渣中还含有一部分未完全熔化的矿石残渣和炭质杂质等。
炉渣的生成与燃烧反应有密切的关系,在高炉内有利于保护炉衬和促进燃料的燃烧。
炉渣对于炼铁过程具有重要作用。
首先,它能与金属铁形成液滴状,并与气体相分离,保护金属铁免受气体的侵蚀。
其次,炉渣中的某些成分能吸附铁矿石和冶金还原产物中的杂质,促进冶金反应的进行。
此外,炉渣还能降低金属铁的熔点,有利于金属铁的收集和流动。
因此,合理控制炉渣的生成和组成对于炼铁工艺的顺利进行和炼铁产品质量的提高至关重要。
- 1、下载文档前请自行甄别文档内容的完整性,平台不提供额外的编辑、内容补充、找答案等附加服务。
- 2、"仅部分预览"的文档,不可在线预览部分如存在完整性等问题,可反馈申请退款(可完整预览的文档不适用该条件!)。
- 3、如文档侵犯您的权益,请联系客服反馈,我们会尽快为您处理(人工客服工作时间:9:00-18:30)。
高Al2O3炉渣对高炉生产的影响
黄溆
摘要:高炉炉渣中Al2O3含量偏高易造成炉渣粘度增高,流动性变差,引起炉墙粘结与炉缸堆积,直接影响高炉炉况。
对此应制定科学的操作方法与操作方针,适当提高炉温水平,降低炉渣碱度,使炉渣保持良好的流动性与稳定性,下部调剂应提高鼓风动能,进一步活跃炉缸,同时要加强入炉原料管理,减少入炉粉末,采用强度和高温冶金性能好的焦炭,才能保证炉况顺行,取得良好的冶炼指标。
关键词:高炉;Al2O3;流动性;碱度;炉温
1 引言
云南天高镍业有限公司高炉炉渣中Al2O3含量平均在17%左右,最高时可达到21%。
炉渣Al2O3含量高时炉渣的流动性和稳定性都将变差,易引起炉墙粘结与炉缸堆积,破坏高炉冶炼的正常进程,给高炉操作带来一系列的问题。
引起炉况不顺,影响产量与质量。
因此,Al2O3含量高的炉渣严重制约了高炉的正常生产。
2Al2O3含量对炉渣性能的影响
Al2O3属于中性,但在高炉冶炼中可认为是酸性物质,其熔点是2050℃,在高炉冶炼中与SiO2混合后仍产生高熔点(1545℃)的物质,使渣铁流动性差,分离困难。
当加入碱性物质如CaO或MgO后,尽管CaO的熔点是2570℃,MgO 熔点是2800℃,但与SiO2和Al2O3结合后生成低熔点(低于1400℃)的物质,在高炉内熔化,形成流动性良好的炉渣,使渣铁分离,保证高炉正常生产。
2.1 Al2O3小于15%时能够改善炉渣的稳定性
当Al2O3含量在5%~20%、MgO含量小于20%时,在CaO/SiO2约为1.0的区域里熔化温度较低;当Al2O3含量低时,随着碱度的增加,炉渣熔化温度增加较快;当Al2O3含量大于10%后,随碱度增加,熔化温度增高减缓,熔化温度区
域扩大,炉渣粘度随碱度变化也减缓,炉渣稳定性增加。
可以认为Al2O3的存在削弱了CaO/SiO2变化的影响。
2.2 高Al2O3炉渣对高炉冶炼的不利影响
Al2O3小于15%时能够改善炉渣的稳定性,有利于高炉操作,但炉渣中Al2O3含量一般在15%~18%,原因是高Al2O3炉渣难以熔化,并且粘度增大,流动性变差,会产生以下负面影响:
(1)高Al2O3炉渣的初渣堵塞炉料间的空隙,使料柱透气性变差,增加煤气通过时的阻力。
同时,该炉渣在高炉内易在炉腹部位的炉墙结成炉瘤,引起炉料下降不顺,形成崩料、悬料,破坏冶炼进程。
(2)由于高Al2O3炉渣过于粘稠,其终渣流动性差,不利于脱硫反应的扩散作用,脱硫效果变差。
一般当Al2O3大于18%时,炉渣的脱硫能力大大降低。
(3)高Al2O3炉渣终渣流动性差,容易堵塞炉缸,不宜从炉缸中流出,使炉缸壁结厚,缩小炉缸的体积,造成高炉操作上的困难。
严重时还会引起风口和渣口的大量烧坏。
(4)高炉炉渣中Al2O3含量在10%~15%时,有利于提高炉渣的稳定性,但当Al2O3含量继续升高时,炉渣的稳定性变差。
炉温不足,其流动性急剧变差,不仅顺行不好,有时放渣出铁也会困难。
因此当炉温不足时,极易引起炉缸炉温不足的渣铁堆积。
3 对策
高炉炉渣中Al2O3含量高时,其流动性和稳定性变差,将严重制约高炉的正常冶炼,影响高炉顺行和产量的提高。
但目前高炉炼铁原料供应紧张,短时间内无法得到根本的改善。
因此,只有改善高炉操作,分析原燃料的各项性能对高炉的影响,综合探讨各种冶炼制度的适应性,制定合理科学的操作方针,使炉况稳定顺行,才能取得最佳的冶炼指标。
3.1 适当降低炉渣碱度,提高炉温水平
高炉炉渣中Al2O3含量在15%~18%时,炉渣的熔化温度明显上升,粘度增大,流动性变差,此时,若盲目降低炉温水平,追求低硅冶炼,极易造成炉缸堆积。
当炉渣二元碱度CaO/SiO2约为1.0时,炉渣的流动性是最好的。
炉渣的碱
度降低不利于脱硫,为此应适当将炉温提高,使炉渣具有充足的物理热,满足炉渣的脱硫能力。
这是高Al2O3炉渣冶炼实现高炉稳定顺行重要的手段。
韶关钢铁集团公司根据其炉渣中Al2O3含量高的情况,实行中硅中硫操作,适当降低炉渣碱度至0.95~1.03,保证了炉渣具有良好的物理和化学性能,同时适当控制生铁中含硅在0.70%~0.90%,以保证炉渣物理热和脱硫能力,取得了较为理想的冶炼指标。
3.2 适当提高鼓风动能,改善炉缸的工作状态
下部调剂应保证合理的鼓风动能,使炉缸充分活跃,消除死区,减小高Al2O3炉渣因流动性变差引起炉缸堆积的可能性。
天高镍业323m3高炉因渣中Al2O3含量高炉况不稳,从开炉开始一直使用Φ100mm的风口小套,努力提高风温水平,天高镍业323m3高炉月平均风温水平目前已达到1120℃。
高风温能使炉缸热量充沛,因此在操作中应保证高风温利用水平。
3.3 提高入炉品位,降低渣量
渣量的高低直接影响高炉软熔带的透气和透液性。
渣量低时高炉的透气性得到改善,即使高炉的炉渣粘度较高,对料柱透气和透液性的影响也较小。
3.4 适当提高渣中MgO的含量
MgO高时会降低炉渣的粘度,改善炉渣的流动性,同时能提高炉渣的脱硫能力。
当高炉炉渣中Al2O3含量高时,MgO的作用显得格外重要。
一般渣中Al2O3含量大于15%时,将MgO的含量提至11%左右,炉渣的物理和化学性能会得到改善。
3.5 提高入炉焦炭的强度和高温冶金性能
焦炭是高炉内最重要的透气和透液物。
随着冶炼强度的日益增强,高炉内软熔带焦层的作用越来越明显,是保持高炉内部透气性的关键。
同时,在高炉的炉腹下部,焦炭粉化是造成高炉炉内下部透气性和透液性恶化的根源。
因此,必须提高焦炭的强度和高温冶金性能。
焦炭在块状带以后要经历碳的熔损反应及越来越高的热作用,焦炭的表面结构遭到破坏,M40与M10等指标已失去作用,入炉焦炭在高炉下部具有好的反应强度(CSR)与低的反应性(CRI)是关键。
入炉焦炭质量的改善在一定程度上减缓了炉渣中Al2O3含量高对高炉下部透气性的负面影响。
3.6 加强入炉原燃料管理,减少入炉粉末量
制定合理的筛分制度,严格落实,保证烧结矿、焦炭、生矿的筛分质量。
一是严格入炉料的槽位管理,严格控制小于5mm的低槽位现象;二是严格控制筛分速度;三是严格落实清筛网制度。
4 结论
高炉炉渣中Al2O3含量高时,炉渣的流动性与稳定性都降低,脱硫能力下降,使高炉的透气性变差,易引起炉况不顺,且极易引起炉墙结厚与炉缸堆积等炉况失常现象。
针对这种在短时间内无法根本改善原料的现状,只有制定科学、合理的操作制度,才能减小高Al2O3炉渣对高炉冶炼带来的不利影响,使高炉稳定顺行,取得优良的冶炼指标。