常用普通螺纹钻、攻切削参数
常用切削参数表

超过机床最大转速。)(安全距离3mm。)
常用切削参数表
切削刀具/切削类型 粗铣 盘铣刀 精铣 立铣刀 铰刀 粗镗刀(2刃) 粗镗刀(2刃) 精镗刀(1刃) 麻花钻 合金钻头 可转位钻头 扩孔钻 普通丝锥 合金丝锥 螺纹铣刀 粗镗刀 麻花钻 铣 铰 粗镗 半精镗 精镗 切削速度(m/min) 100-120 150-180 80—100 3—8 100-120 120-140 160-180 30 80 80 30 20 4 70-90 160 30 每齿进给(mm/齿) 0.2 0.1 0.2 0.1 0.2 0.15 0.1 0.15 0.15 0.2 0.15 螺距P(mm/r) 螺距P(mm/r) 0.15 0.15 0.15
钻
扩 攻丝 铣螺纹 倒角
切削条件:无内冷,一般材料(如钢、铸离3mm。)
削参数表
备注 总加工长度=加工长度+1个刀具直径+20mm 齿数按实际刀具 注意:退刀时间(齿数按实际刀具) 2齿 2齿 1齿 2齿(注意:加工长度计算考虑刀尖3mm、出孔口3mm) 2齿 1齿 2齿 注意:退刀时间(1齿) 注意:退刀时间(1齿) 齿数按实际刀具 1齿 直径比螺纹孔大6-8mm左右(2齿)
数控车床螺纹切削循环指令编程
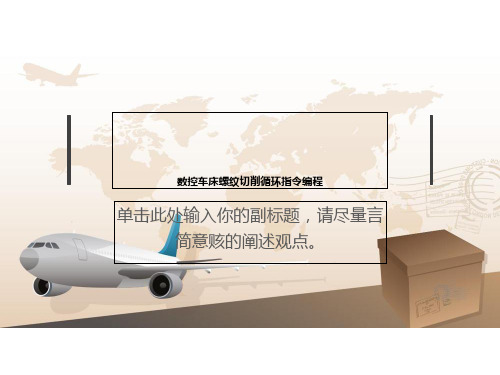
M 20—5g 6g— S
旋合长度代号 顶径公差带代号
中径公差带代号
公称直径
普通螺纹代号
4.螺纹标记含义(2)
(2)内螺纹标记 内螺纹标记如图所示。
M20×1.5—6H—S— LH
螺纹旋向 螺纹短旋合长度 中径和顶径公差带代号 螺距(指细牙) 公称直径 普通螺纹代号
4.螺纹标记含义(3)
(3)关于螺纹标记的几点说明: 1)对于粗牙螺纹螺距,可以省略标注其螺距项, 而细牙螺纹则必须标注; 2)对于多线螺纹,采用“公称直径×Ph导程P螺距 ”方式标注,或者在后面增加括号用英文进行说明 ,如两线为“two starts”,三线为“three starts”;
4.螺纹车刀的安装与找正(2)
4.螺纹车刀的安装与找正(3)
为了保证装刀要求,在装夹外螺纹车刀时 常采用角度样板找正螺纹刀尖角度,如图 所示,将样板靠在工件直径最大的素线上, 以此为基准调整刀具角度。
4.螺纹车刀的安装与找正(4)
4.螺纹车刀的安装与找正(5)
5.螺纹车削刀具切入与 切出行程的确定(1)
4.螺纹标记含义(4)
(3)关于螺纹标记的几点说明: 3)对于左旋螺纹,应在旋合长度之后标注 “LH”代号,右旋螺纹不需要标注; 4)对于螺纹旋合长度,分为三组,即短旋合长 度(S)、中等旋合长度(N)和长旋合长度( L),一般采用中等旋合长度。
二、螺纹加工工艺设计
1.螺纹加工走刀路线设计(1)
数控车床螺纹切削循环指令编程
单击此处输入你的副标题,请尽量言 简意赅的阐述观点。
项目11 数控车床螺纹切 削循环指令编程
一、螺纹基础知识
1.常见螺纹类型(1)
(1)按照用途分类 螺纹按用途不同可 分为联接螺纹和传动螺纹。
钻孔攻丝标准规格表
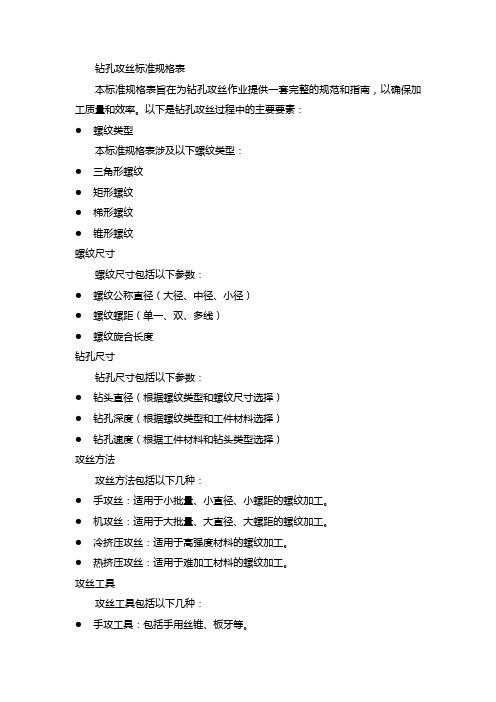
钻孔攻丝标准规格表本标准规格表旨在为钻孔攻丝作业提供一套完整的规范和指南,以确保加工质量和效率。
以下是钻孔攻丝过程中的主要要素:●螺纹类型本标准规格表涉及以下螺纹类型:●三角形螺纹●矩形螺纹●梯形螺纹●锥形螺纹螺纹尺寸螺纹尺寸包括以下参数:●螺纹公称直径(大径、中径、小径)●螺纹螺距(单一、双、多线)●螺纹旋合长度钻孔尺寸钻孔尺寸包括以下参数:●钻头直径(根据螺纹类型和螺纹尺寸选择)●钻孔深度(根据螺纹类型和工件材料选择)●钻孔速度(根据工件材料和钻头类型选择)攻丝方法攻丝方法包括以下几种:●手攻丝:适用于小批量、小直径、小螺距的螺纹加工。
●机攻丝:适用于大批量、大直径、大螺距的螺纹加工。
●冷挤压攻丝:适用于高强度材料的螺纹加工。
●热挤压攻丝:适用于难加工材料的螺纹加工。
攻丝工具攻丝工具包括以下几种:●手攻工具:包括手用丝锥、板牙等。
●机攻工具:包括机用丝锥、板牙等。
●辅助工具:包括冷却液、润滑剂等。
表面处理表面处理包括以下几种:●镀层处理:如镀铬、镀锌等,以提高耐腐蚀性和美观度。
●抛光处理:如机械抛光、化学抛光等,以提高表面光滑度和美观度。
●其他处理:如喷涂、电泳等,以满足特殊需求。
螺纹精度根据实际需求和标准,螺纹精度可分为不同的等级。
常见的螺纹精度等级有:4H、6H、8H等。
在选择螺纹精度等级时,需考虑使用要求、工件材料、加工工艺等因素。
一般来说,高精度等级的螺纹适用于关键部位和高强度连接,而低精度等级的螺纹则适用于一般连接。
具体选择应根据实际需求确定。
8. 其他参数其他参数包括以下内容: (1)材料硬度:钻孔攻丝前应了解材料的硬度范围,以便选择合适的钻头和丝锥。
一般来说,软材料易加工,而硬材料则需选用高硬度钻头和丝锥。
(2)工件装夹:工件的装夹方式应确保稳定可靠,以便在钻孔攻丝过程中避免工件移动或偏移。
(3)冷却与润滑:钻孔攻丝过程中应使用冷却液和润滑剂,以降低切削温度,减少切削阻力,提高加工质量和效率。
常用刀具的切削参数

常用刀具的切削参数1.钻头:钻头是一种旋转式刀具,通常用于在硬材料上钻孔。
切削速度是指钻头每分钟旋转圈数,一般以转/分钟(RPM)为单位。
切削速度的选择将受到材料类型和钻头直径的影响。
对于大型孔径和脆性材料,较低的切削速度可能更合适。
进给量是指每转刀具在轴向(沿钻孔方向)上移动的距离。
进给量的选择将受到钻头直径和材料类型的影响。
较大直径的钻头可能需要较大的进给量。
切削深度是指钻头在一次进给中的轴向深度。
如果切削深度太大,可能会导致钻头断裂或切削不洁净。
切削深度的选择还将受到材料类型和钻头直径的影响。
2.铣刀:铣刀是一种回转和前进运动刀具,常用于平面加工、开槽和切割。
切削速度是指铣刀每分钟旋转圈数,同样以转/分钟(RPM)为单位。
切削速度的选择将受到材料类型、铣刀材料和刀具直径的影响。
进给量是指铣刀在工件表面上移动的距离。
较大的进给量将导致更高的切削速度,但也可能影响切削表面的质量。
切削深度是指铣刀在一次运动中与工件表面的最大距离。
切削深度的选择将受到材料类型和铣刀直径的影响。
3.车刀:车刀是一种在工件上进行旋转切削的刀具,常用于车削和车削加工。
切削速度是指车刀每分钟旋转圈数,仍然以转/分钟(RPM)为单位。
切削速度的选择将受到材料类型、车刀材料和刀具直径的影响。
进给量是指车刀在工件上移动的距离。
较大的进给量可以提高生产效率,但也可能影响切削表面的质量。
切削深度是指车刀与工件表面的最大距离。
切削深度的选择将受到材料类型和车刀直径的影响。
4.锯片:锯片是一种用于切割材料的刀具,常用于金属、木材和塑料加工。
切削速度是指锯片每分钟旋转圈数,仍然以转/分钟(RPM)为单位。
切削速度的选择将受到材料类型、锯片材料和刀具直径的影响。
进给量是指锯片在工件上移动的距离。
较大的进给量可以提高切割速度,但也可能导致切割表面质量的下降。
切削深度是指锯片与工件表面的最大距离。
切削深度的选择通常由锯片的直径和材料类型确定。
M8螺纹孔
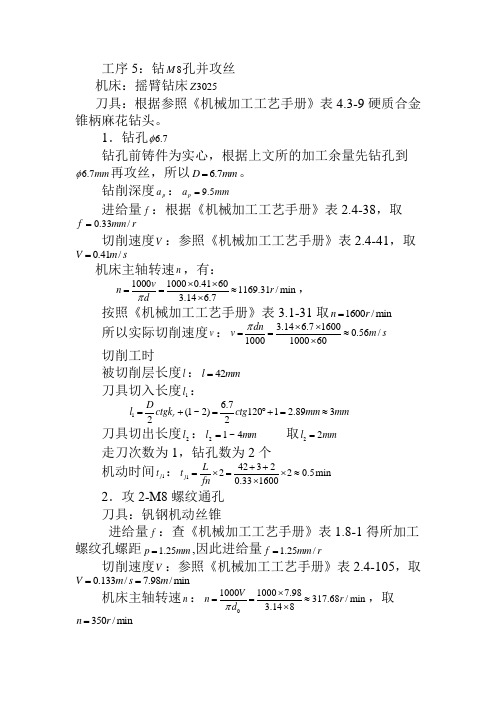
工序5:钻8M 孔并攻丝 机床:摇臂钻床3025Z刀具:根据参照《机械加工工艺手册》表4.3-9硬质合金锥柄麻花钻头。
1.钻孔 6.7φ钻孔前铸件为实心,根据上文所的加工余量先钻孔到6.7mm φ再攻丝,所以 6.7D mm =。
钻削深度p a :9.5p a mm =进给量f :根据《机械加工工艺手册》表2.4-38,取r mm f /33.0=切削速度V :参照《机械加工工艺手册》表2.4-41,取0.41/V m s =机床主轴转速n ,有:100010000.41601169.31/min 3.14 6.7v n r dπ⨯⨯==≈⨯,按照《机械加工工艺手册》表3.1-31取1600/min n r = 所以实际切削速度v : 3.14 6.716000.56/1000100060dn v m s π⨯⨯==≈⨯切削工时被切削层长度l :42l mm = 刀具切入长度1l :1 6.7(1~2)1201 2.89322r D l ctgk ctg mm mm =+=︒+=≈刀具切出长度2l :mm l 4~12= 取22l mm =走刀次数为1,钻孔数为2个机动时间1j t :14232220.5min 0.331600j L t fn++=⨯=⨯≈⨯2.攻2-M8螺纹通孔 刀具:钒钢机动丝锥进给量f :查《机械加工工艺手册》表1.8-1得所加工螺纹孔螺距 1.25p mm =,因此进给量 1.25/f mm r =切削速度V :参照《机械加工工艺手册》表2.4-105,取0.133/7.98/min V m s m ==机床主轴转速n :0100010007.98317.68/min 3.148V n r d π⨯==≈⨯,取350/min n r =丝锥回转转速n 回:取350/min n r =回实际切削速度V ':0 3.1483500.15/1000100060d n V m s π⨯⨯'==≈⨯被切削层长度l :9.5l mm =刀具切入长度1l :1(1~3)3 1.25 3.75l f mm ==⨯= 刀具切出长度2l :22~33 1.25 3.75l f mm ==⨯=(),加工数为2 机动时间2j t :121229.5 3.75 3.759.5 3.75 3.75220.13min 1.5350 1.5350j l l l l l l t fn fn ++++++++=+⨯=+⨯≈⨯⨯回()() 本工序机动时间j t :120.50.130.63min j j j t t t =+=+=。
孔加工的切削参数表格(精)
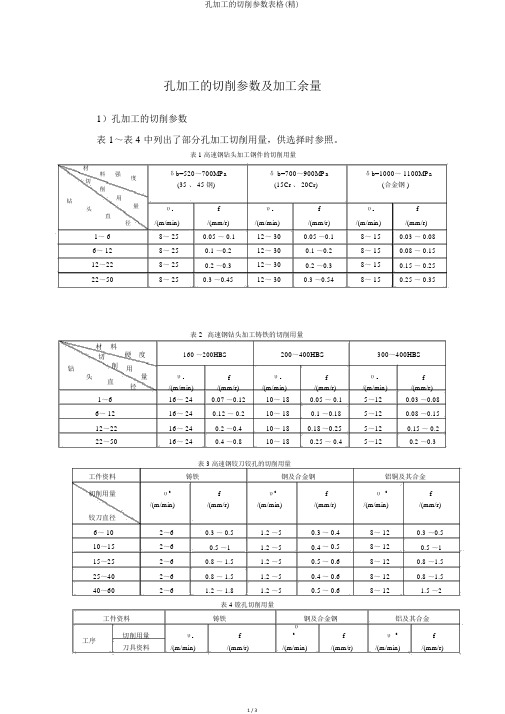
孔加工的切削参数及加工余量1)孔加工的切削参数表 1~表 4 中列出了部分孔加工切削用量,供选择时参照。
表 1 高速钢钻头加工钢件的切削用量材料强δb=520~700MPa δ b=700~900MPa δb=1000~ 1100MPa 切度(35 、 45 钢) (15Cr 、 20Cr) (合金钢 )削钻用量 f f f头υc υ c υc 直径/(m/min) /(mm/r) /(m/min) /(mm/r) /(m/min) /(mm/r) 1~ 6 8~ 25 0.05 ~ 0.1 12~ 30 0.05 ~0.1 8~ 15 0.03 ~ 0.08 6~ 12 8~ 25 0.1 ~0.2 12~ 30 0.1 ~0.2 8~ 15 0.08 ~ 0.15 12~22 8~ 25 0.2 ~0.3 12~ 30 0.2 ~0.3 8~ 15 0.15 ~ 0.25 22~50 8~ 25 0.3 ~0.45 12~ 30 0.3 ~0.54 8~ 15 0.25 ~ 0.35表 2 高速钢钻头加工铸铁的切削用量材料硬度160 ~200HBS 200~400HBS 300~400HBS 切钻削用量υ c f υ c f υ c f 头直径/(m/min) /(mm/r) /(m/min) /(mm/r) /(m/min) /(mm/r) 1~6 16~ 24 0.07 ~0.12 10~ 18 0.05 ~ 0.1 5~12 0.03 ~0.08 6~ 12 16~ 24 0.12 ~ 0.2 10~ 18 0.1 ~0.18 5~12 0.08 ~0.15 12~22 16~ 24 0.2 ~0.4 10~ 18 0.18 ~0.25 5~12 0.15 ~ 0.2 22~50 16~ 24 0.4 ~0.8 10~ 18 0.25 ~ 0.4 5~12 0.2 ~0.3表 3 高速钢铰刀铰孔的切削用量工件资料铸铁钢及合金钢铝铜及其合金切削用量υc f υc f υ c f /(m/min) /(mm/r) /(m/min) /(mm/r) /(m/min) /(mm/r) 铰刀直径6~ 10 2~6 0.3 ~ 0.5 1.2 ~5 0.3 ~ 0.4 8~ 12 0.3 ~0.5 10~15 2~6 0.5 ~1 1.2 ~5 0.4 ~ 0.5 8~ 12 0.5 ~1 15~25 2~6 0.8 ~ 1.5 1.2 ~5 0.5 ~ 0.6 8~ 12 0.8 ~1.5 25~40 2~6 0.8 ~ 1.5 1.2 ~5 0.4 ~ 0.6 8~ 12 0.8 ~1.5 40~60 2~6 1.2 ~ 1.8 1.2 ~5 0.5 ~ 0.6 8~ 12 1.5 ~2表 4 镗孔切削用量工件资料铸铁钢及合金钢铝及其合金工序切削用量υc fυc f υ c f刀具资料/(m/min) /(mm/r) /(m/min) /(mm/r) /(m/min) /(mm/r)高速钢20~2515~300.35 ~0.7100~ 150 0.5 ~ 1.5粗加工35~50 0.4 ~0.45100~ 250 合金 50~70高速钢20~35 15~50 0.15 ~0.45100~ 2000.2 ~ 0.5半精加工50~70 0.15 ~ 0.45 合金 95~135高速钢70~90D1 级<0.08 0.02 ~0.15150~ 4000.06 ~ 0.1精加工100~135合金D 级 0.12 ~0.152)孔加工的加工余量表 5 中列出在实体资料上的孔加工方式及加工余量,供选择时参照。
攻螺纹的计算公式

攻螺纹的计算公式攻螺纹是机械加工中常见的一项操作,要想把这活儿干漂亮,咱们得搞清楚相关的计算公式。
先说攻螺纹前底孔直径的计算。
这就好比盖房子打地基,地基不稳,房子就容易出问题。
底孔直径要是算错了,螺纹加工也准得掉链子。
对于普通螺纹,底孔直径的计算公式是:D 钻 = D - P 。
这里的“D 钻”指的是底孔直径,“D”是螺纹大径,“P”呢,就是螺距。
比如说,咱要攻一个 M10 粗牙螺纹,螺距是 1.5mm。
那底孔直径就是 10 - 1.5 = 8.5mm 。
我记得有一次在车间实习的时候,我旁边的小李就因为底孔直径算错了,闹出了笑话。
那天师傅布置了个任务,让我们各自加工几个螺纹零件。
小李风风火火地就开始干,结果他把底孔直径算小了,攻螺纹的时候那丝锥死活进不去,急得他满头大汗。
师傅过来一看,哭笑不得,让他重新算重新做。
打那以后,小李每次算底孔直径都格外认真,再也不敢马虎了。
再来说说攻螺纹时切削速度的计算。
切削速度要是不合适,螺纹表面的质量可就没法保证啦。
切削速度的计算公式是:v = πdn / 1000 。
这里的“v”是切削速度,“d”是螺纹直径,“n”是主轴转速。
举个例子,假如螺纹直径是 10mm,主轴转速是 500 转/分钟,那切削速度就是 3.14×10×500÷1000 = 15.7m/min 。
给大家分享个我自己的经历。
有一回参加技能比赛,在攻螺纹这个环节,我一开始没太注意切削速度,结果加工出来的螺纹表面很粗糙。
这可把我给急坏了,赶紧调整参数重新加工,好在最后完成得还不错,有惊无险啊!还有攻螺纹时扭矩的计算,这也很关键。
扭矩要是太大,丝锥容易折断;扭矩太小,又攻不进去。
扭矩的计算公式是:M = 0.15×D×P×K 。
其中“M”是扭矩,“D”是螺纹大径,“P”是螺距,“K”是修正系数。
比如说,螺纹大径是 12mm,螺距是 1.75mm,修正系数取 1.1,那扭矩就是0.15×12×1.75×1.1 ≈ 3.47 N·m 。
丝锥和钻头的参数对照表

丝锥和钻头的参数对照表
丝锥和钻头是机械加工中经常用到的工具,它们在加工金属材料时具有重要的作用。
丝锥是一种用于加工螺纹的切削工具,而钻头则是一种用于加工孔洞的切削工具。
下面是丝锥和钻头的参数对照表:
一、丝锥参数对照表:
1. 规格型号:表示丝锥的大小规格,常用的规格有M3、M4、M5等。
2. 材质:表示丝锥的制作材料,常见的材质有高速钢、合金钢等。
3. 刃型:表示丝锥的刃口形状,常见的有直齿、螺旋齿等。
4. 镀层:表示丝锥表面的镀层,常见的有涂层、电镀等。
5. 使用环境:表示丝锥可适用的加工环境,例如钢铁、铝合金等。
二、钻头参数对照表:
1. 直径:表示钻头的直径大小,常用的直径有0.5mm、1.0mm、1.5mm 等。
2. 材质:表示钻头的制作材料,常见的材质有高速钢、硬质合金等。
3. 刃型:表示钻头刃口的形状,常见的有中心钻、镐头钻等。
4. 镀层:表示钻头表面的镀层,常见的有钛金属、电镀等。
5. 使用环境:表示钻头可适用的加工环境,例如木材、金属等。
丝锥和钻头在具体使用时需要根据实际情况进行选择,如要加工螺纹则需要选择丝锥,要加工孔洞则需要选择钻头。
此外,对于丝锥和钻头的刀具保养与维护也需要特别注意,如及时清洗、防止生锈等,以保证其使用寿命和效果。
各类数控刀具转速进给切削量吃刀量参数

各类数控刀具转速进给切削量吃刀量参数数控刀具的转速、进给和切削量是刀具切削加工的重要参数,对加工质量、效率和刀具寿命等方面均有影响。
下面将介绍不同类型的数控刀具的转速、进给和切削量。
1. 铣削参数:数控铣削是常见的数控加工方法之一,常用的铣削刀具包括立铣刀、面铣刀和无心线焊接铣刀等。
铣削刀具的转速范围较大,一般在500-8000转/分之间。
对于高硬度材料的加工,转速一般较低,对于切削困难的材料,可以适当降低转速。
进给量受到刀具直径和材料硬度的影响,通常在0.1-1mm/齿之间。
切削深度也受到切削稳定性的限制,一般在刀具直径的1/2左右。
2. 钻削参数:数控钻削是通过旋转的钻削刀具对工件进行钻孔加工。
钻削刀具的转速一般较高,取决于刀具材料、刃数和切削物材料等因素,通常在200-8000转/分之间。
进给量一般为0.05-0.5mm/转,可以根据材料硬度和孔径大小进行调整。
吃刀量一般为刀具直径的1/4-1/23. 镗削参数:数控镗削是通过旋转的镗刀对孔加工进行切削的一种方法。
镗削刀具的转速较低,一般在100-1000转/分之间。
进给量和切削速度的关系较大,进给量一般为0.1-1mm/转,可以根据材料硬度和切削稳定性进行调整。
镗刀一般为刀具直径的1/4-1/24.螺纹加工参数:螺纹加工是通过数控车削或数控铣削进行的。
螺纹加工的刀具转速一般较低,取决于螺纹规格和材料硬度等因素。
进给量一般为螺距的1/2-2倍之间。
切削深度一般为刀具螺纹高度的1/2左右。
总的来说,数控刀具的转速、进给和切削量等参数需要根据具体的加工要求和材料性质进行调整。
在实际生产中,需要根据材料硬度、刀具材料、切削稳定性和切削效率等因素进行综合考虑,以获得最佳的加工效果。
普通螺纹 标准

普通螺纹标准普通螺纹是一种常用的螺纹连接方式,广泛应用于机械、汽车、航空航天等行业。
它的设计与制造要求都有一定的标准,下面就来介绍一些与普通螺纹相关的参考内容。
1. 螺纹设计与标准:普通螺纹的设计与标准有很多,其中包括国内标准和国际标准。
国内标准主要有GB/T 1167-1996《普通螺纹》、GB/T 3678-2006《普通螺纹零件技术要求》等。
国际标准有ISO 724-1978《一般用途精密螺纹标准》、ISO 965-1-2013《Metric screw threads—Principles and basic data—Part 1: Metric screw threads》等。
2. 螺纹参数规定:普通螺纹的参数规定主要包括螺距、螺纹直径、牙型角等。
螺距是单位长度内螺纹的回转数,它与螺纹直径有关。
螺纹直径是指螺纹外径或内径,它与牙型角一起决定了螺纹的牙高、牙宽等尺寸。
3. 螺纹制造工艺:普通螺纹的制造工艺一般包括车削、攻丝、滚牙等。
车削是最常用的制造螺纹的方法,它适用于较大直径的螺纹。
攻丝是用切削刀具直接在工件上切削出螺纹,适用于小直径螺纹。
滚牙是使用滚牙刀具在预先加工好的螺纹孔中滚制螺纹,适用于高精度螺纹。
4. 螺纹连接的紧固原理:普通螺纹的连接原理是利用螺纹的摩擦力将螺纹连接的零件固定在一起。
当两个螺纹连接的零件旋转时,螺纹的摩擦力可以防止它们的相对运动,使之保持紧固状态。
同时,螺纹连接也可以通过加装垫圈等配件来实现密封功能。
5. 螺纹连接的验收:普通螺纹连接的验收主要包括两个方面:尺寸验收和功能验收。
尺寸验收主要是检查螺纹的外径、内径、螺距等参数是否满足设计要求;功能验收主要是检查螺纹的装拆是否灵活、螺纹间的摩擦力是否适当等。
总之,普通螺纹是一种常用的螺纹连接方式,它的设计与制造有一定的标准要求,如螺纹设计与标准、螺纹参数规定、螺纹制造工艺、螺纹连接的紧固原理和螺纹连接的验收等。
丝锥和钻头的参数对照表
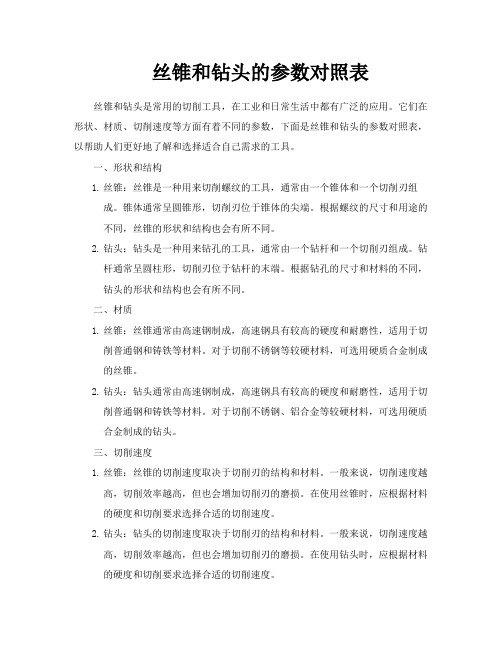
丝锥和钻头的参数对照表丝锥和钻头是常用的切削工具,在工业和日常生活中都有广泛的应用。
它们在形状、材质、切削速度等方面有着不同的参数,下面是丝锥和钻头的参数对照表,以帮助人们更好地了解和选择适合自己需求的工具。
一、形状和结构1.丝锥:丝锥是一种用来切削螺纹的工具,通常由一个锥体和一个切削刃组成。
锥体通常呈圆锥形,切削刃位于锥体的尖端。
根据螺纹的尺寸和用途的不同,丝锥的形状和结构也会有所不同。
2.钻头:钻头是一种用来钻孔的工具,通常由一个钻杆和一个切削刃组成。
钻杆通常呈圆柱形,切削刃位于钻杆的末端。
根据钻孔的尺寸和材料的不同,钻头的形状和结构也会有所不同。
二、材质1.丝锥:丝锥通常由高速钢制成,高速钢具有较高的硬度和耐磨性,适用于切削普通钢和铸铁等材料。
对于切削不锈钢等较硬材料,可选用硬质合金制成的丝锥。
2.钻头:钻头通常由高速钢制成,高速钢具有较高的硬度和耐磨性,适用于切削普通钢和铸铁等材料。
对于切削不锈钢、铝合金等较硬材料,可选用硬质合金制成的钻头。
三、切削速度1.丝锥:丝锥的切削速度取决于切削刃的结构和材料。
一般来说,切削速度越高,切削效率越高,但也会增加切削刃的磨损。
在使用丝锥时,应根据材料的硬度和切削要求选择合适的切削速度。
2.钻头:钻头的切削速度取决于切削刃的结构和材料。
一般来说,切削速度越高,切削效率越高,但也会增加切削刃的磨损。
在使用钻头时,应根据材料的硬度和切削要求选择合适的切削速度。
四、使用方法1.丝锥:使用丝锥时,需要先在工件上打孔,然后将丝锥插入孔中,通过旋转丝锥切削出螺纹。
切削过程中要保持适当的切削速度和切削力,避免过度用力或转速过快导致切削刃损坏。
2.钻头:使用钻头时,需要先在工件上打孔,然后将钻头插入孔中,通过旋转钻头切削出孔。
切削过程中要保持适当的切削速度和切削力,避免过度用力或转速过快导致切削刃损坏。
常用普通螺纹钻、攻切削参数
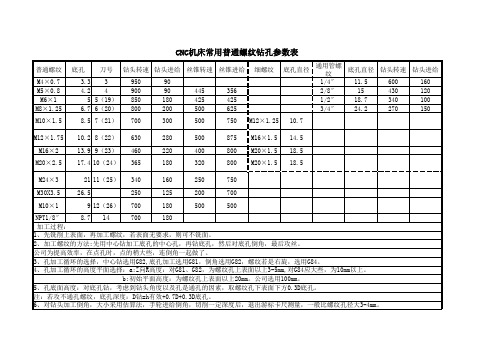
6、对钻头加工倒角,大小采用估算法,手轮进给倒角,切削一定深度后,退出游标卡尺测量,一般比螺纹孔径大3-4mm。
7、对丝锥:因为孔加工刀具对刀时是以钻尖或丝锥端中心为刀位点,攻螺纹时,由于丝锥切削部分有锥角,端部不能切出完整的牙型, 丝锥钻入深度应大于螺纹有效深度。一般可取:H丝=h有效+0.7D。D为螺纹大径。 8、中心钻应短,有良好的刚度。
通用管螺 纹
1/4″ 2/8″ 1/2″ 3/4″
底孔直径
11.5 15
18.7 24.2
钻头转速
600 430 340 270
钻头进给
160 120 100 150
8.5 7(21) 700
37
M12×1.75 10.2 8(22) 630
280
500
875 M16×1.5 14.5
180
500
500
NPT1/8″
8.7 14
700
180
加工过程:
1、先铣削上表面,再加工螺纹,若表面无要求,则可不铣面。
2、加工螺纹的方法:先用中心钻加工底孔的中心孔,再钻底孔,然后对底孔倒角,最后攻丝。
公司为提高效率,在点孔时,点的稍大些,连倒角一起做了。
3、孔加工循环的选择,中心钻选用G82,底孔加工选用G81,倒角选用G82,螺纹若是右旋,选用G84。
M16×2
13.9 9(23) 460
220
400
800 M20×1.5 18.5
M20×2.5 17.4 10(24) 365
180
320
800 M20×1.5 18.5
M24×3
21 11(25) 340
160
250
750
常用螺纹丝锥攻牙切削参数
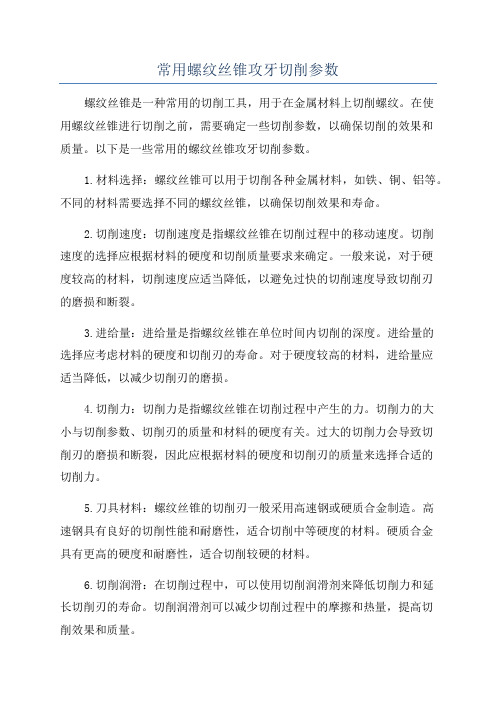
常用螺纹丝锥攻牙切削参数螺纹丝锥是一种常用的切削工具,用于在金属材料上切削螺纹。
在使用螺纹丝锥进行切削之前,需要确定一些切削参数,以确保切削的效果和质量。
以下是一些常用的螺纹丝锥攻牙切削参数。
1.材料选择:螺纹丝锥可以用于切削各种金属材料,如铁、铜、铝等。
不同的材料需要选择不同的螺纹丝锥,以确保切削效果和寿命。
2.切削速度:切削速度是指螺纹丝锥在切削过程中的移动速度。
切削速度的选择应根据材料的硬度和切削质量要求来确定。
一般来说,对于硬度较高的材料,切削速度应适当降低,以避免过快的切削速度导致切削刃的磨损和断裂。
3.进给量:进给量是指螺纹丝锥在单位时间内切削的深度。
进给量的选择应考虑材料的硬度和切削刃的寿命。
对于硬度较高的材料,进给量应适当降低,以减少切削刃的磨损。
4.切削力:切削力是指螺纹丝锥在切削过程中产生的力。
切削力的大小与切削参数、切削刃的质量和材料的硬度有关。
过大的切削力会导致切削刃的磨损和断裂,因此应根据材料的硬度和切削刃的质量来选择合适的切削力。
5.刀具材料:螺纹丝锥的切削刃一般采用高速钢或硬质合金制造。
高速钢具有良好的切削性能和耐磨性,适合切削中等硬度的材料。
硬质合金具有更高的硬度和耐磨性,适合切削较硬的材料。
6.切削润滑:在切削过程中,可以使用切削润滑剂来降低切削力和延长切削刃的寿命。
切削润滑剂可以减少切削过程中的摩擦和热量,提高切削效果和质量。
7.切削表面处理:切削过程中产生的切削屑可能会对切削表面造成损坏。
为了获得更好的切削表面质量,可以采用适当的切削参数和切削润滑剂,并及时清除切削屑。
总之,螺纹丝锥的切削参数应根据材料的硬度、切削质量要求和切削刃的寿命来确定。
通过合理选择切削速度、进给量、刀具材料和切削润滑等参数,可以获得高质量的螺纹切削效果。
常用机械加工工艺参数表

第 1 页,共 4 页
2946821407.xlsx
用硬质合金精镗孔(铸铁)的切削用量
加工直径
切削用量
(毫米)
V(米/分)
So(毫米/转)
0~999
70~90
0.12~0.15
主偏角 30 45 60 75 90
PxPy 修正系数
KPx2
KPz2 r
0.63 1 1.14 1.2 1.28 1.05 1 0.96 0.94 1.12
KPz3 0.95 0.98 1 1
用硬质合金半精镗孔(钢)的切削用量
加工直径
切削用量
(毫米)
V(米/分)
So(毫米/转)
0~999
90~135
0.15~0.45
主偏角 30 45 60 75 90
PxPy 修正系数
KPx2
KPz2 r
0.63 1 1.14 1.2 1.28 1.05 1 0.96 0.94 1.12
<30 30~130
>130
精镗孔常用工序间余量 在直径上的工序间余量 (毫米) 0.2~0.25 0.25~0.40
0.35~0.5
攻螺纹(钢件)切削速度V(米/分)
加工螺纹直
螺距 t (毫米)
径(毫米) 0.5 0.75 1 1.25 1.5 2 3
3~6
67 8
8~10
7 8 9 9 10
12~16 8 9 10 10 11 11
用硬质合金铰刀铰孔(铸铁)的切削用量
加工直径
切削用量
(毫米) V(米/分)
So(毫米/转)
6~10
8~10
0.30~0.50
10~15
常用螺纹的主要参数
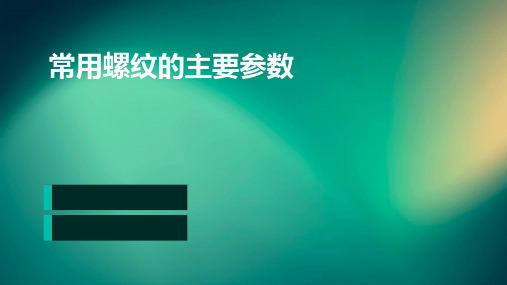
塑料的优点是重量轻、绝缘性 好、防水性能优良,缺点是强 度较低、容易变形。
06 螺纹加工工艺
车削加工
适用范围
车削加工适用于加工内外螺纹,尤其适用于长螺纹的加工。
优点
车削加工的螺纹精度高,表面粗糙度低,且加工范围广,能够满足 多种规格和长度的螺纹加工需求。
工艺流程
车削加工的工艺流程包括工件夹持、刀具安装、切削进给、螺纹车 削等步骤。
连接
连接强度
螺纹的连接强度取决于其几何参数, 如螺距、牙型角和螺纹深度等。这些 参数决定了螺纹的机械性能,从而影 响其连接强度。
耐久性
在长期负载下,螺纹连接可能会松动 。为了提高耐久性,可以采用预紧或 防松措施,如使用垫片或弹簧圈。
传动
效率
螺纹传动效率取决于其几何参数和润 滑条件。为了提高效率,可以选择合 适的润滑剂,并优化螺纹参数以减少 摩擦。
矩形螺纹
矩形螺纹主要用于传递运动和动力,如机床进给箱、测量仪器等。其牙型为矩形, 牙顶角为90°,传动效率高,但牙根较浅,强度较低。
矩形螺纹的螺距和牙型高度较大,因此其传动平稳、准确,但加工较困难,一般 需要用丝锥或板牙加工。
梯形螺纹
梯形螺纹主要用于传递运动和动力,如车床、铣床等机床的进 给系统。其牙型为等腰梯形,牙顶角为30°或37°,牙根较深, 强度较高。
优点
攻丝加工的螺纹精度较高,且切削效率较高,能够 满足一定范围内的螺纹加工需求。
工艺流程
攻丝加工的工艺流程包括工件夹持、钻孔、攻丝等 步骤。
THANKS FOR WATCHING
感谢您的观看
05 螺纹材料
碳钢
碳钢是一种常用的螺 纹材料,具有较高的 强度和耐磨性。
碳钢的优点是成本低、 强度高,缺点是容易 生锈和腐蚀。
切削攻牙计算公式

切削攻牙计算公式切削攻牙是一种常见的机械加工工艺,用于制造各种齿轮、螺纹等零部件。
在进行切削攻牙时,需要对切削参数进行计算,以确保工件能够达到设计要求的尺寸和精度。
切削攻牙计算公式是进行这些计算的基础,下面将介绍一些常用的切削攻牙计算公式及其应用。
1. 切削速度计算公式。
切削速度是切削过程中刀具表面单位时间内通过的距离,通常用m/min或ft/min来表示。
切削速度的计算公式为:Vc = π D n / 1000。
其中,Vc为切削速度,D为刀具直径(mm),n为主轴转速(r/min)。
这个公式可以帮助我们根据刀具直径和主轴转速来计算切削速度,从而选择合适的切削速度以确保刀具和工件的加工效果。
2. 进给速度计算公式。
进给速度是工件在切削过程中沿着切削方向移动的速度,通常用mm/r或in/r 来表示。
进给速度的计算公式为:f = fz z n。
其中,f为进给速度,fz为每齿进给量(mm/z),z为刀具齿数,n为主轴转速(r/min)。
这个公式可以帮助我们根据每齿进给量、刀具齿数和主轴转速来计算进给速度,从而控制工件的加工速度和质量。
3. 切削力计算公式。
切削力是切削过程中刀具对工件施加的力,通常用N或lbf来表示。
切削力的计算公式为:Fc = k ap ae f。
其中,Fc为切削力,k为切削力系数,ap为切削深度(mm),ae为切削宽度(mm),f为进给速度(mm/r)。
这个公式可以帮助我们根据切削深度、切削宽度和进给速度来计算切削力,从而选择合适的刀具和加工参数以确保加工效果。
4. 切削功率计算公式。
切削功率是切削过程中刀具所消耗的功率,通常用kW或hp来表示。
切削功率的计算公式为:Pc = Fc Vc / 1000。
其中,Pc为切削功率,Fc为切削力(N),Vc为切削速度(m/min)。
这个公式可以帮助我们根据切削力和切削速度来计算切削功率,从而选择合适的主轴功率和切削参数以确保加工效果。
以上介绍了切削攻牙计算公式的一些常见应用,这些公式是进行切削参数计算的基础,能够帮助我们选择合适的切削速度、进给速度、切削力和切削功率,以确保工件能够达到设计要求的尺寸和精度。
m12x1.75螺纹标准
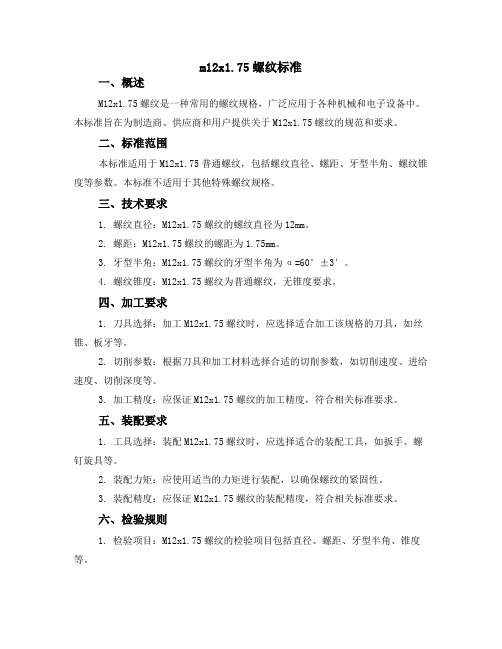
m12x1.75螺纹标准一、概述M12x1.75螺纹是一种常用的螺纹规格,广泛应用于各种机械和电子设备中。
本标准旨在为制造商、供应商和用户提供关于M12x1.75螺纹的规范和要求。
二、标准范围本标准适用于M12x1.75普通螺纹,包括螺纹直径、螺距、牙型半角、螺纹锥度等参数。
本标准不适用于其他特殊螺纹规格。
三、技术要求1. 螺纹直径:M12x1.75螺纹的螺纹直径为12mm。
2. 螺距:M12x1.75螺纹的螺距为1.75mm。
3. 牙型半角:M12x1.75螺纹的牙型半角为α=60°±3′。
4. 螺纹锥度:M12x1.75螺纹为普通螺纹,无锥度要求。
四、加工要求1. 刀具选择:加工M12x1.75螺纹时,应选择适合加工该规格的刀具,如丝锥、板牙等。
2. 切削参数:根据刀具和加工材料选择合适的切削参数,如切削速度、进给速度、切削深度等。
3. 加工精度:应保证M12x1.75螺纹的加工精度,符合相关标准要求。
五、装配要求1. 工具选择:装配M12x1.75螺纹时,应选择适合的装配工具,如扳手、螺钉旋具等。
2. 装配力矩:应使用适当的力矩进行装配,以确保螺纹的紧固性。
3. 装配精度:应保证M12x1.75螺纹的装配精度,符合相关标准要求。
六、检验规则1. 检验项目:M12x1.75螺纹的检验项目包括直径、螺距、牙型半角、锥度等。
2. 检验方法:根据相关标准采用测量工具进行测量,确保各项参数符合要求。
3. 检验周期:定期进行螺纹的检验和维修,确保其正常工作。
4. 合格标准:螺纹的各项参数应符合相关标准要求,否则视为不合格。
七、附加说明本标准未涉及到的其他内容,应根据实际情况进行说明和补充。
如有疑问,请联系相关机构或人员。
螺纹加工细则

螺纹加工细则
M2以下由钳工攻牙 M2-M3(不包括)金属材料采用挤压丝锥攻牙;非金属材料采用切削丝锥 M3-M10采用切削丝锥,通孔用直槽先端丝锥, 盲孔用螺旋丝锥。 M10(不包括)以上及底孔﹥∮10直管螺纹采用螺纹铣削加工,(注意牙刀底部到牙尖的距离) 对于铸造不锈钢、POM 材料、大底板、不采用cnc攻牙。 符合CNC加工普通螺纹深度要求, 不增加CNC装夹次数上尽可能安排CNC攻牙 不锈钢303、304等材料采用普通碳钢切削参数的50% 螺丝最深加工到≤3倍公称直径;3.5D以上极限深度,须定制非标刀具(暂不转CNC加工)。
CNC加工普通螺纹有效深度要求
螺纹规格 M 3 4 5 6 8 10 12 牙距 0.5 0.7 0.8 1 1.25 1.5 1.75 旋合牙数 (10个牙) 5 7 8 10 12.5 15 17.5 底孔深度 7 9.8 11.2 14 17.5 21 24.5
底孔深度以4P+旋合牙数+钻尖计算,约等于2.5~3倍公称直径; 最深加工到≤3D;3.5D以上极限深度,须定制非标刀具 所有螺旋丝锥须加深2P(导向)
- 1、下载文档前请自行甄别文档内容的完整性,平台不提供额外的编辑、内容补充、找答案等附加服务。
- 2、"仅部分预览"的文档,不可在线预览部分如存在完整性等问题,可反馈申请退款(可完整预览的文档不适用该条件!)。
- 3、如文档侵犯您的权益,请联系客服反馈,我们会尽快为您处理(人工客服工作时间:9:00-18:30)。
M16×2
13.9 9(23) 460
220
400
800 M20×1.5 18.5
M20×2.5 17.4 10(24) 365
180
320
800 M20×1.5 18.5
M24×3
21 11(25) 340
160
250
750
M30X3.5
26.5
250
125
200
700
M10×1
9 12(26) 700
4、孔加工循环的高度平面选择:a:Z向R高度:对G81、G82,为螺纹孔上表面以上3-5mm,对G84应大些,为10mm以上。
b:初始平面高度:为螺纹孔上表面以上20mm。公司选用100mm。
5、孔底面高度:对底孔钻,考虑到钻头角度以及孔是通孔的因素,取螺纹孔下表面下方0.3D底孔。
注:若攻不通孔螺纹,底孔深度:D钻=h有效+0.7D+0.3D底孔。
425
425
1/2″
18.7
340
100
M8×1.25
6.7 6(20) 800
200
500
625
3/4″
24.2
270
150
M10×1.5
8.5 7(21) 700
300
500
750 M12×1.25 10.7
M12×1.75 10.2 8(22) 630
280
500
875 M16×1.5 14.5
6、对钻头加工倒角,大小采用估算法,手轮进给倒角,切削一定深度后,退出游标卡尺测量,一般比螺纹孔径大3-4mm。
7、对丝锥:因为孔加工刀具对刀时是以钻尖或丝锥端中心为刀位点,攻螺纹时,由于丝锥切削部分有锥角,端部不能切出完整的牙型,
丝锥钻入深度应大于螺纹有效深度。一般可取:H丝=h有效+0.7D。D为螺纹大径。
CNC机床常用普通螺纹钻孔参数表
普通螺纹 底孔
刀号
钻头转速 钻头进给 丝锥转速 丝锥进给
细螺纹
底孔直径
通用管螺 纹
底孔直径
钻头转速
钻头进给
M4×0.7
3.3 3
950
90
1/4″
11.5
600
160
M5×0.8
4.2 4
900
90
445
356
2/8″
15
430
120
M6×1
5 5(19) 850
180
8、中心钻应短,有良好的刚度。
180
500
500
NPT1/8″
8.7 14
7பைடு நூலகம்0
180
加工过程:
1、先铣削上表面,再加工螺纹,若表面无要求,则可不铣面。
2、加工螺纹的方法:先用中心钻加工底孔的中心孔,再钻底孔,然后对底孔倒角,最后攻丝。
公司为提高效率,在点孔时,点的稍大些,连倒角一起做了。
3、孔加工循环的选择,中心钻选用G82,底孔加工选用G81,倒角选用G82,螺纹若是右旋,选用G84。