8D介绍
8D报告介绍
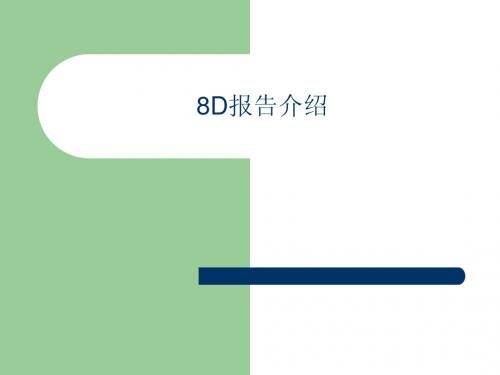
五、对8D工作方法的评价
1.优点 发现真正肇因的有效方法,并能够采取针对性措施 消除真正肇因,执行永久性矫正措施.能够帮助探索 允许问题逃逸的控制系统.逃逸点的研究有助于提高 控制系统在问题再次出现时的监测能力.预防机制的 研究有助于帮助系统将问题控制在初级阶段. 2.缺点 3.8D培训废时,且本身具有难度.除了对8D问题解决 流程进行培训外,还需要数据挖掘的培训,以及对 所需用到的分析工具(如帕累托图、鱼骨图和流程 图,等等)进行培训.
8D报告介绍
一、8D简述
8D报告又称团队导向问题解决方法、8D问题 求解法,是福特公司处理问题的一种方法,亦 适用于制程能力指数低于其应有值时有关问题 解决,它提出了一套符合逻辑的解决问题的方 法,同时对于统计制程管制与实际的品质提升 架起了一座桥梁。 8D(8Disciplines)问题解决8步法 8D原名叫做8Disciplins,意思是8个人人皆知解 决问题的固定步骤.
二、问题解决8步法
Disciplines5.选定及确认长期改善行动效果:拟订改善计划、 列出可能解决方案、选定与执行长期对策、验证改善措施, 清除D4发生的真正原因,通常以一个步骤一个步骤的方式说 明长期改善对策,可以用专案计划甘特图,并说明品质手法 的应用. Disciplines6.改善问题并确认最终效果:执行D5后的结果与成 效验证. Disciplines7.预防再发生及标准化:确保D4问题不会再次发生 的后续行动方案,如人员教育训练、改善案例分享、作业标 准化、产出BKM、执行FCN、分享知识和经验等. Disciplines8. 恭喜小组及规划未来方向:若上述步骤完成后 问题已改善,肯定改善小组的努力,并规划未来改善方向.
8D方法介绍及应用-8D方法介绍及应用

五、8D步骤—D3临时对策
问题发生了,在原因没有找到之前,已经发出去 的产品、库存产品、正在生产的产品都可能会存在 同样隐患,不能仅仅是检查库存产品就可以了。
需要考虑的问题:
1.防止继续产生不 良品(减少不良品产 生)。
2.减小产生的不良和 后续可能产生不良对 客户的影响。
临时纠正措施应包括:
- 避免用户因产品无法使用导致停产(快速补货或100% 检验) - 对客户处及公司库存产品的质量验证或跟踪处理 - 在永久纠正措施未验证有效之前,对在制品的临时措 施(如:增加检验频次等)
计划和执行选取的防止再发生对策。
需要考虑的问题:
1.确定并执行预 防再发对策, 并应注意持续 实施监控,以 确定根因已经 消除。
2.待步入生产阶 段,应即监视 纠正措施长期 效果,必要时 采行补救措施。
3.验证 预防再发 对策有效 后,可以 停止临时 措施。
五、8D步骤-D7效果确认及标准化
为防止同一问题及类似问题再次发生。应 将相关对策形成书面文件(管理制度、程序 文件、作业指导书、表单、技术文件等)。
HOW MUCH
什么程度 问题发生的程度、量
问题描述举例:
住友总部采购2月5日反馈我司批次号131123的 02295HT产品2月2日在宫崎工厂压延中1400米处发生捻 制不良,捻制不良持续了5米,捻制不良的图片见附图。 该产品编号21-025,生产日期1月1日,该轮产品已被 剔除,该批其余产品未再出现该现象。问题样品已隔 离并待贵司取回。
口
破 损
15
数
10
69.56 52.17
86.93
100 % 75 50
5
25
0
0
A BC DE F GH
8D工作方法

找到造成问题的主要原因后,即开始拟出对策的方法。对策的
方法也许有好几种,例如修理或更新磨具。试试对可能的选择列
出其优缺点,要花多少钱?多少人力?能持续多久?再对可能的 方法作一最佳的选择,并且确认这样的对策方法不会产生其他副
பைடு நூலகம்
D6.执行及验证永久对策
当永久对策准备妥当,则可开始执行及停止暂时对策 。并且对永久对策作一验证,例如观察不良率由
目录 8D的定义 8D流程介绍 8D格式的填写和要求 8D常见的问题及处理方法 如何评审8D的纠正预防措施有效
1.8D的定义
1.概述
8D最早是美国福特公司使用的经典质量问题分析手法。 二战期间,美国政府率先采用一种类似8D的流程——“ 军事标准1520”,又称之为“不合格品的修正行动及部 署系统”。 1987年,福特汽车公司首次用书面记录下8D 法,在其一份课程手册中这一方法被命名为“团队导向 的问题解决法”(Team Oriented Problem Solving) 。
2.8D流程介绍
D1.建立解决问题的小组
若问题无法独立解决,通知你认为有关的人员组成团
队。团队的成员必须有能力执行,例如调整机器或懂得 改变制程条件,或能指挥作筛选等。
D2.描述问题
向团队说明何时、何地、发生了什么事、严重程度、 目前状态、如何紧急处理、以及展示照片和收集到的证
据。想象你是FBI的办案人员,将证物、细节描述越清楚
较。列出您所知道的所有生产条件(即鱼骨图),逐一 观察,看看是否有些条件走样,还是最近有些什么异动 ?换了夹具吗?换了作业员?换了供应商?换了运输商 ?修过电源供应器?流程改过?或比较良品与不良品的
检查结果,看看哪个数据有很大的差异?尺寸?重量?
8D具体是指什么

8D具体是指什么8D具体是指八个D,是一种问题解决方法和工具,用于团队解决问题和改进流程。
它是一种结构化的方法,涉及八个步骤,即问题定义、团队组织、问题纠正、根本原因分析、解决方案、实施、效果验证和预防措施。
下面将详细介绍这八个步骤。
第一步,问题定义(D1):在这一步中,团队需要明确目标并确保大家对问题的定义有一致的理解。
团队成员可以使用一些工具,如鱼骨图或五个为什么方法来帮助确定问题的根本原因。
这一步骤的目的是确保问题得到准确定义,以便后续步骤能够有针对性地解决问题。
第二步,团队组织(D2):在这一步中,团队需要明确成员角色和责任,并分配合适的人来解决问题。
团队成员应该具备较强的问题解决能力,能够有效地协同合作。
团队的组织结构和规模取决于具体的问题和公司的需求。
第三步,问题纠正(D3):在这一步中,团队需要识别问题的临时解决方案并实施,以便尽快控制问题的规模和影响。
这些纠正措施有助于防止问题继续恶化,并为下一步的根本原因分析提供基础。
第四步,根本原因分析(D4):在这一步中,团队需要识别问题的根本原因,而不仅仅是表面上的原因。
团队可以使用一些常见的工具,如5W1H分析、鱼骨图或五个为什么方法来进行根本原因分析。
这一步骤的目标是真正理解问题的本质,以便能够制定有效的解决方案。
第五步,解决方案(D5):在这一步中,团队需要制定解决问题的具体方案。
这些解决方案应该是根据根本原因分析得出的结论,并且需要经过多次讨论和评估,确保其可行性和有效性。
解决方案可以包括一些改进措施、培训计划或流程调整等。
第六步,实施(D6):在这一步中,团队需要将制定的解决方案付诸实施,并确保实施过程中的顺利进行。
这需要团队成员的密切协作和有效的沟通,以便解决问题并实现目标。
实施解决方案可能需要一定的时间和资源,因此团队需要做好计划和准备。
第七步,效果验证(D7):在这一步中,团队需要评估已实施解决方案的效果,并与预期的目标进行比较。
8D报告思维模式

a.接受客户的投诉,捕捉投诉信息,同步获取有关异常的内部信息(在制在库品)和外部反馈信息(客户端异常图片丶不良样品寄回);
b.不要分析了一半,再去同客户确认这,确认那.谁都烦,还耽误事.
3.收到投诉于2H内正式回复客户收到信息;并于24H内回复客户D0-D3;1-3-5原则:1天内出D1-D3围堵,3天出初步分析D4,5天内出正式8D;
b.讲不出什么,一问三不知;讨论开始后,问批次,要查一下!问不良率及数量,再问一下!问哪几个客户丶哪些地区有投诉,要再确认一下!就只听说产品坏了,那具体哪里坏了,不太清楚!那这会还怎么讨论下去?(D0没做好)
3.品质人员要学会依事实为依据(样品丶图片,描述10分钟不如一张图片实在),用数据说话(讲半天的好与坏,不如一组数据实在),让利益推动改善(如果不强势,也只能用这招了)。
1.一个界定良好的问题,已经将问题解决了一半;
大方向不能错,小问题可探讨;如果大家忙活了半天,因为问题描述错误或者方向都错了,又要重新来,大家弄死你的心都有了.走夜路背后都凉飕飕的.
2.大家都很忙,讲重点,简明扼要。我说话声音大,所以大多数都是我先讲.为这事我可没少吼人,因为,我遇到......
a.讲了半天,大家不知道你在讲什么?(需要5W2H,实在不行事先写在白板上,连口水都省了.)
8D教学
8D是一种思维方式,问题改善的方法,
只要大家在处理问题时慢慢形成这种思维模式就好了(现在公司出现品质问题,连生产组长都知道问下在制在库在途品和改善措施,"我们用完库存还有没有?厂商那边还有没有?改完模后面不会再有了吧?研发要是不改我们这批就不克服了".)
一.8D介绍:
8D &PDCA 介绍

No
Root
Cause
临时/長期矯正措施
负责 Owner Due Date 验证方法 单位
5.1
Short term(临时对策)
(在长期对策实施前的临时
对策)
Long term(长期对策) (最终的矫正措施)
预计目标
Sample
No
Root Cause
Action Item
1 發現B15 Robot上ARM定 撕除ARM tape 位用之tape鬆脫 改貼高粘度鋁膠帶
2021/4/7
慢性損失(Common case) 極限值 時間
IVO Confidential
▪ 革新的問題 ▪ 為了降至極限值, 革新 的對策是必要的
6 Sigma way
10
8D的基本理念
Basic Concept
Focus on 产品 Product
Step 1:Describe the Issue (問題描述)
2021/4/7
Prepared by 彭义 Date:09-3-18
IVO Confidential
2
8D的由来及常用文本格式
1.8D 的全名叫做 8 Disciplines,它是一种处理问题的工具。 2.8D=PDCA + Analysis + team work 3.原先由Ford 公司提出,之後已成为QS9000/ ISO TS16949、福特公司的特殊要求。
CF侧ARC异常
O
定(CF-
ARC unload以呼气相确
(11/20sheet)
ARC)
认
* O 主要因, △ 疑似要因, X 非要因
IVO Confidential
8D方法介绍

二、8D的9个步骤详细说明
D4:定义和验证根本原因和问题逃出点 ➢ 目的:使用问题解决过程和工作表来识别问题的根本原因;
识别问题逃出点(流出不良的原因);验证根本原因和问题逃出点。 ➢ 关键要点:评估识别可能原因每一个原因;验证确认真正的原因;检
关键要点: 选择预防措施验证有效性决策
组织、人员、设备、环境、材料、文件重新确定
工具: 评估/检查清单、
二、8D的9个步骤详细说明
D8:小组祝贺
➢ 目的: 承认小组的集体努力,对小组工作进行总结并祝贺。 关注的问题被解决,确认,核实,,被权威人士审核签名
通过并存盘. ➢ 关键要点: 有选择的保留重要文档 流览小组工作,将心得形成文件 了解小组对解决问题的集体力量, 及对解决问题作出的贡献 必要的物质、精神奖励。
YN
备注/ 結果
5.最终分析 临时对策后的OK部品发交时间和数量
备注:
5 最终分析
时间
真 考正虑事 的原项:因:制造上/不良流出上/DFL未识别上的原因分析
人,机,料,法
3.初期分析 3. 供应商内部流出原因(或汽车厂家处未识别出)的初步分析
附件1:
经过表 (示例)
项目名:***********************************
****年**月
****年**月
1 2 3 4 5 6 7 8 9 10 11 12 13 14 15 16 17 18 19 20 21 22 23 24 25 26 27 28 29 30 1 2 3 4 5 6 7 8 9 10 11 12 13 14 15 16 17 18
全面质量管理-8D介绍之D0-D3

团队的成功
• 方向清晰 • 时间足够 • 提供所需的培训 • 技术及信息的资源充足 • 范围适当 • 有坚强的领导者
二、8D步骤—D2问题描述
问题描述是指要解决的问题,即有什么缺陷。
问题描述的标准: 一个有效的问题描述是 具体的 它明确地解释了有什么不对,并从类似的问题中找出不足; 可观察的 它描述了问题的可见迹象; 可测量的 它描述了“多少”或“多少频度”,以定量的术语指明了问题的范围; 可控制的 一个可控制的问题是一个可以在6到12个月内解决的问题。如果 一个问题太大,它应被分解成几个更小的可控制的问题。
?按需要调整团队成员?小组成员的人数控制在4到10个之间?选择具有相应技能知识资源权力等的人作为团队成员?各类成员之间职责任务合理搭配二8d步骤d1建立小组团队的力量?承诺?打破藩篱?扩展知识和经验?高昂的士气?开放而诚实的沟通团队的失败
全面质量管理— 8D介绍之一
质量故事 8D简介 D0-D3介绍 结束语
一、质量故事
预防大于治疗—质量重在预防
有位客人到某人家里作客,看见主人家的灶上烟囱是直的,旁边又有很多木材,客人告诉主人说:“烟囱要改曲,木材须移 去,否则将来可能会有火灾。”主人听了没有做任何表示。
不久主人家里果然失火,四周的邻居赶紧跑来救火,最后火被扑灭了,于是主人烹羊宰牛,宴请四邻。以酬谢他们救火的功劳, 但是并没有请当初建议他将木材移走,烟囱改曲的人。
必要时,开发上述的临时措施也需要一定的理由证明是有效的,可另起一页, 以使客户放心!!!
结束语
一件没有预料的事情可能引起故障,一个长久被忽视的问题可能导致一次危 机。
——明茨伯格(加拿大管理学家)
• 快速圆满解决问题,提高顾客满意度,取得更多订单!
8D工作方法简单介绍.PPT

D7:预防再发生
目的:
修改现有的管理系统、操作系统、 工作惯例、设计与规程以防止这一问题 与所有类似问题重复发生。
D7:预防再发生
关键要点:
•选择预防措施 •验证有效性 •决策 •组织、人员、设备、环境、材料、文件重新 确定
D8:小组祝贺
目的:
承认小组的集体努力,对小组工 作进行总结并祝贺。
D8:小组祝贺
“什么东西出了什么问题”
方法:质量风险评定,FMEA分析
D2:问题说明
关键要点:
•收集和组织所有有关数据以说明问题 •问题说明是所描述问题的特别有用的数据的总结 •审核现有数据,识别问题、确定范围 •细分问题,将复杂问题细分为单个问题 •问题定义,找到和顾客所确认问题一致的说明,“什么东西 出了什么问题”,而原因又未知 •风险等级
D3:实施并验证临时措施
目的:
保证在永久纠正措施实施前,将问 题与内外部顾客隔离。
(原为唯一可选步骤,但发展至今 都需采用)
方法:FMEA、DOE、PPM
D3:实施并验证临时措施
关键要点:
•评价紧急响应措施 •找出和选择最佳“临时抑制措施” •决策 •实施,并作好记录 •验证(DOE、PPM分析、控制图等)
•小组长或成员因工作调动,不能履行职责,又未 及时变更。
•问题说明—停留在故障表现上,没有用工程师的语言 ,造成许多问题只是治标不治本。
•临时措施—没有采取临时措施,保证问题与顾客隔离 。
•根本原因—没有对所有可能原因进行测试以确定根本 原因,而多是凭经验。
•永久措施—选择措施前,没有进行成本、效果等方面 的评价,以利于决策。措施确定后无计划或预防措施 保证。
•必要的验证手段—在根本原因或永久措施的验证阶段 ,缺少必要的试验或验证手段。
8D 介绍

必要时,考慮選擇 方案所涉及的風險
选择最佳方案
四、8D內容的要求 (6)
6. Prevent Action
提出杜绝问题发生的根本对策, 制定一个实施永久措施的计划,确定过程控 制方法并纳入文件,以确保根本原因的消除。在生产中应用该措施时应监 督其长期效果。以使該缺失不再具有發生的可能性。 关键要点: 重新审视小组成员 执行永久纠正措施,废除临时措施 利用故障的可测量性确认故障已经排除 控制计划、工艺文件修改 >FMEA 是否已經review過﹐如果需要更新是否更新過. >Control plan是否已經review過﹐如果需要更新是否更新過. >制程規格是否已經review過﹐如果需要更新是否更新過. >增加檢驗不能算作改善措施﹐并且不要加入到預防改善行動中. >稽核不要加入到預防改善行動中.
恭賀小組成員
對所有積極參與的小組成員 進行適當的承認
對小組的效益進行溝通
8、恭贺小組
四、8D內容的要求 (1)
1. CA Team Members: 列出小組成員,他們的職務﹐及小組的主導者. •D1:小组成立 目的: 成立一个小组,小组成员具备工艺/产品的知识,有配给的时间并授予了权限,同时应具有所要求的能 解决问题和实施纠正措施的技术素质。小组必须有一个指导和小组长。 关键要点: 成员资格,具备工艺、产品的知识 目标 分工 程序
執行永久對策
• 执行永久性的纠正措施,应注意持续实施控制,以确保 根本原因已经消除.并应监视纠正措施的长期效果;必 要时采取补救措施。 • 当验证永久对策有效后,即可以停止临时措施。
针对选定的糾正措施
修正衡量指标以及 对现行的质量控制 模式進行工程变更
利用數據 (如SPC或推移圖) 來進行確認
8D手法介绍

5 Why 范例: 为何停机
问1:为什么机器停了? 问2:为什么机器会超载? 问3:为什么轴承会润滑不 足? 问4: 为什么润滑幫浦会 失灵? 问5: 为什么润滑幫浦的 轮轴会耗损? 答1:因为机器超载, 保险 丝烧断了 答2: 因为轴承的润滑不 足 答3: 因为润滑幫浦失灵 了 答4: 因为幫浦的轮轴耗 损了 答5: 因为杂质跑到里面 去了
Page 15 of 80
5 Why 范例: 为何停机
问1:为什么机器停了? 问2:为什么机器会超载? 问3:为什么轴承会润滑不 足? 答1:因为机器超载, 保险 丝烧断了 答2: 因为轴承的润滑不 足 答3: 因为润滑幫浦失灵 了
Pagபைடு நூலகம் 16 of 80
5 Why 范例: 为何停机
Page 18 of 80
5 Why 的分布层次
现象
为什么机器停了? 现在
为什么机器会超载?
wh y
看得到的, 可感觉 , 可测量
问题 一次因 (近因)
wh
紧急处理
wh 真因 y
治标对策 (暂时)
为什么轴承会润滑不足?
为什么润滑幫浦会失灵?
wh y
过去
真因y
改善行动 防呆设计
真因
为什么润滑幫浦的 轮轴会耗损?
P D
(-)
列出问题点
Page 30 of 80
PDCA 与CA-PDCA实施步骤
PDCA
活动计划的制作
2. 课题明确化 3. 方策拟定 4. 最适策追究 5. 最适策实施 6. 效果确认 1.主题选定 适用 何种 QC STORY 的判定
CA-PDCA
活动计划的制作
2. 现況把握 3. 要因分析 4. 对策拟定 5. 对策实施
什么是8d报告

什么是8d报告8D报告是一种质量管理工具,用于解决问题、改进过程和防止问题再次发生。
它有助于组织识别并解决根本原因,以及实施正确的纠正和预防措施。
下面将详细介绍8D报告的步骤和其在质量管理中的应用。
1. D1:形成问题解决小组 - 团队的组建是开始解决问题的第一步。
这个小组应该由不同部门的成员组成,以确保问题得到全面的分析和解决。
2. D2:描述问题 - 在这一步骤中,小组需要准确地描述问题的性质和影响。
问题描述应该尽可能详细,并提供相关数据和证据来支持问题的存在。
3. D3:立即采取临时措施 - 为了防止问题进一步扩大,小组需要立即采取临时措施。
这些临时措施是为了解决当下问题并保证继续运营。
4. D4:确定根本原因 - 在这一步骤中,小组需要通过分析、问责和检查来确定问题的根本原因。
这需要深入了解问题并找到导致问题的核心因素。
5. D5:制定纠正措施 - 一旦根本原因确定,小组需要制定纠正措施。
这些措施应该能够解决根本原因,并预防类似问题再次发生。
6. D6:实施纠正措施 - 在这一步骤中,纠正措施需要被实施并监测其有效性。
团队应该制定一份实施计划,并确保纠正措施得到执行。
7. D7:验证纠正措施的有效性 - 在实施了纠正措施后,小组需要验证这些措施的有效性。
这可以通过各种方式,如数据分析、产品测试等。
8. D8:预防措施的部署 - 一旦纠正措施验证有效,小组需要部署预防措施,以防止类似问题再次发生。
这些预防措施可以包括流程改进、员工培训等。
8D报告在质量管理中起到了重要的作用。
通过遵循这八个步骤,组织能够更好地解决问题,改善过程,并避免类似问题的重复出现。
此外,8D报告也促进了团队合作和跨部门的交流,因为小组成员来自不同的部门,他们能够提供不同的观点和经验,帮助解决问题。
总之,8D报告是解决问题和改进过程的一种系统性方法。
通过其明确的步骤和严谨的执行,组织能够建立一个高效的质量管理系统,从而提高产品和服务的质量,满足客户的需求,并提高组织的竞争力。
标准版8D报告教材
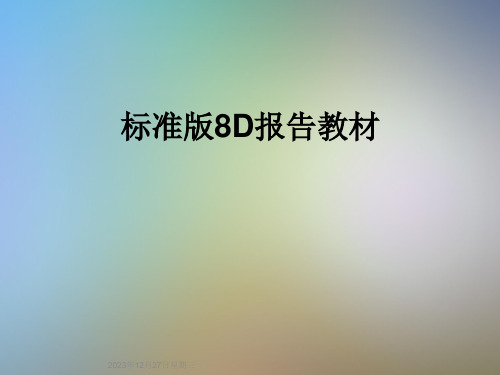
•
-1.推移圖
-2.管制圖
• 。以統計方法驗証效果的顯著與不顯著
• 。收集數據驗證改善措施的成效。(建議一至 二個月期間的資料收集)
•二. 8D工作方法的介绍
•D7:预防再发生
•目的: • 修改现有的管理系统、操作系统、
工作惯例、设计与规程以防止这一问题 与所有类似问题重复发生。
•二. 8D工作方法的介绍
被探测出但未被探测出的点
•
必要问题:
• 是否有鱼骨图分析? 是否 有是/不是分析?
• 是否确定了可接受的根本原因?
• 过程的根本原因是否被认可?
• 根本原因是否得到验证?
• “五个为什么”方法是否应用?
• 逃逸点是否确定?
• 现行控制系统是否有能力探测被确定的问题?
魚骨圖
•MAN(因1)
•因2 •ENVIRONMENT
MANY)的方法才能落實執行 • ∞執行過程中要確認效果相同的問題不再出現 •
•二. 8D工作方法的介绍
D4:原因分析及證實
• ∞以魚骨圖為架構,用腦力激盪的方式找出可能的原因 (POTENTIAL ROOT CAUSES)
• ∞以5WHYS深入追蹤直到分析出真正的原因(问题根源), 並追查出為何目前的系統無法顯驗出此異常
潤滑不足?
失靈了
• 。問4:為什麼潤滑泵 • 。答4:因為泵浦的輪
浦會失靈?
軸耗損了
• 。問5:為什麼潤滑泵 • 。答5:因為雜質跑到
浦的輪軸會耗損?
裡面去了
•二. 8D工作方法的介绍
•D4:原因分析及證實
•针对D2问题描述来测试每一个可能的原因,分析根本原因,
•
验证根本原因
•
品质部培训8D课程PPT培训课件

总结词:预防措施
详细描述:在汽车行业中,8D方法不仅解决问题,还 注重预防类似问题的再次发生,通过根本原因分析和改 善措施来降低质量风险。
案例二:电子行业中的8D应用
在此添加您的文本17字
总结词:高效解决问题
在此添加您的文本16字
培训者或回答者总结 并重申关键点。
参与者提问,培训者 或指定的回答者回答 问题。
注意事项
确保问题与主题相关,避免偏离主题。
尊重每个参与者的观点,避免争论或 攻击性语言。
THANKS FOR WATCHING
感谢您的观看
和精准度。
05 Q&A环节
总结
01
确保所有参与者都有机会提问和 回答问题,以促进交流和互动。
02
鼓励开放和诚实的对话,以便更 好地理解问题和解决方案。
目的
提供机会让参与者提问和分享他们的 观点和经验。
帮助解答参与者在培训过程中可能产 生的疑问。
步骤
培训者宣布Q&A环 节开始,并解释规则 和流程。
预防再发生
对问题进行总结和归纳,完善预 防措施,防止类似问题的再次发 生。
02 8D课程详解
成立问题解决小组
总结词
成立一个跨部门的问题解决小组,成 员包括问题领域的专家和具有解决问 题能力的人员。
详细描述
针对出现的问题,从各个部门抽调人 员,组成一个结构合理、专业性强、 经验丰富的问题解决小组,确保问题 得到全面、专业的分析和解决。
详细描述
根据问题解决的各个阶段,撰写详细的8D 报告,记录问题的现象、分析、解决过程和 效果评估等,为今后的工作提供经验和参考。
8D报告的评价标准

华阳通用电子有限公司.8D 报告的评价标准整理: SQA-Springsun 日期:2012年2月13日8D(Eight Disciplines of Problem Solving)是福特公司解决问题的8条基本准则。
是福特公司在20世纪90年代早期引进的技术方法来解决工厂和供应商的问题。
8D是解决问题的一种工具,通常是客户所抱怨的问题要求公司分析,并提出永久解决及改善的方法。
8D是由一个准备步骤和8个步骤组成。
这些步骤用来客观地确定、定义和解决问题,并防止相似问题的再次发生。
解决问题的8个步骤:问题发生成立8D 小组问题描述实施并验证临时性纠正措施确定和验证问题的根本原因选择和验证永久性纠正措施实施和确认永久性纠正措施防止问题再次发生/系统预防性建议表彰小组和个人的贡献D0D1(10分)D2(10分)D3(15分)D4(15分)D5(15分)D6(15分)D7(15分)D8 (5分)8D目标:解决问题,保证品质积累解决问题的经验。
8D准则:针对出现的问题,找出问题产生的根本原因,提出短期、中期、长期的对策,并采取相应的行动,彻底解决问题,杜绝或尽量减少问题重复出现。
8D好处:z可以通过建立小组训练内部合作能力z推进有效的问题解决和预防技术z改进整个质量和生产率z防止相同或类似问题的再发生z提高顾客满意度有效实施8D的质量工具:z控制计划(PC)z潜在失效模式及后果分析(FMEA)z生产件批准程序(PPAP)z统计过程控制(SPC)z试验计划(DOE)8D说明:1)选定了目标,一定要找出其根本原因,针对产生问题的原因,制订短期对策、中期对策、长期对策。
短期对策:是指生产现场怎么办?中期对策:是指即将要生产的怎么办?长期对策:是指如何将问题解决在发生之前?2)必须采取行动,有对策,执行是关键。
有了对策,必须是不折不扣地执行。
3)持之以恒,必须要坚持行动,解决问题必须要达到彻底清楚的目的。
绝不能因为解决了一半而导致问题周而复始,不时复出发生。
- 1、下载文档前请自行甄别文档内容的完整性,平台不提供额外的编辑、内容补充、找答案等附加服务。
- 2、"仅部分预览"的文档,不可在线预览部分如存在完整性等问题,可反馈申请退款(可完整预览的文档不适用该条件!)。
- 3、如文档侵犯您的权益,请联系客服反馈,我们会尽快为您处理(人工客服工作时间:9:00-18:30)。
经过连续五次不停地问“为什么”,才找到问题的真正原因和解决的方法,
在油泵轴上安装过滤器。
追问到此,最终的原因就算找到了,给油泵装上过泸器,再换上保险丝,机器就正常运行了,如果
不进行一番追问的话,也许简单的换上一根保险丝,机器照样立即转动,但是用不了多久,机器 就会停下来,因为最终原因没找到.
18
D5提出长期改善对策
直因 對策
1.請人資部根據各職位市場薪資定義各職位各 級標準薪資水平. 2.請人資部參照各職位各級標準薪資水平,制 訂內部晉升調薪制度. 1. 根 據 各 職 位 的 工 作 特 點 建 立 人 力 儲 備 制 度 2. 建 立 真 正 有 效 的 代 理 人 機 制 .
擔當者
原因分析分为两步: 1.找出影响的因素. 2.采用5个为什么找出真实的原因
12
过程介绍—D4原因分析
一.找出影响的因素
H.S导热膏接触不到芯片,经分析可能有以下原因:
1.导热膏厚度偏薄:说明偏薄为何会造成H.S导热膏接触不到芯片
2.H.S底部平面度不良:说明平面度不良为何…… 3.芯片平面度不良:说明平面度不良为何…… 针对以上可能原因一一验证: 1.测量库存品导热膏厚度验证….
17
D5提出长期改善对策
提出的长期对策一般注意以下问题: 1.长期对策应着眼于原因分析中真实原因进行,即长期对策应与原因 分析一一对应,一个原因分析对应一条改善对策. 2.长期对策一般允许有提高…..,加强…….,教育训练等字眼,此为无 效对策. 3.改善对策应不限于某一点,某一个机种,某一个供货商,某一个客户, 而是全面的改善,才能杜绝再发生类似问题,称为以点带面,否则 会呈现”野火烧不尽,春风吹又生”的现象.
组员为各部门骨干人员,应对问题的分析,解决有相当的能力,一般是工程师 和主管级. 在进行8D分析过程中,可以根据问题的发展变更或增加组员 根据问题的性质,选取具有恰当的技能、知识、资历、权威等的人员,一般 制造.如是客诉质量问题,制造.QC.业务,生管人员为8D小组常态参加人员
a.涉及到产品设计方面,RD人员须参加 b.涉及到作业方法,PE及IE须参加 c.涉及到原物料的,IQC,SQE,采购须参加
8
D3-提出并实施短期对策
短期对策又称临时对策,应急对策,首要目标是满足客人的要求,以不影响客人生产和 出货为原则,包括提出短期对策及实施两个阶段. 在拟定短期对策前,须先确认以下信息: 1.不良率:如不良率太高,则不选择重工,可选择重新生产等方式 2.不良现象:问题点是否清楚,如不清楚,则不能轻易决定处理方式. 3.质量标准是否有争议:如标准有争议,可先厘清质量标准,如暂不能与客人达成一致, 先以客人标准来作业. 4.客人生产进度:客人何时上线生产,需要多少数量,来决定安排重工的时间,人数以 及是否可以拉回重工. 5.重工方式:需要确认重工方法,是否需要治具,SOP等 6.厂内生产进度:结合客人的生产需要,评估换货是否可行. 短期对策须在很短的时间提出并执行,一般在客人提出问题,8H内提出并实施,如客 人特急件,则按客人要求配合.
7
D2 成立8D小组
• 小组配合事项: 1) Leader: 统筹8D过程的运作,掌控实施进度 组织和协调小组成员关系. 2) 各成员 8D分析改善方法的进行. 范本: 1.问题点描述: 苏州名硕10/9发现10/8进料的DCV-00154-N2-GP H.S有尺寸偏大现象,要求 10-+/-0.1mm,实际有偏大现象,为10.2~10.3mm,抽检100pcs,有20pcs不 良,不良率20% 2.经查此款H.S为供货商生产(IQC,SQE,采购),且与检验方法有关(DQE),所以 小组成员应包括: Leader:QA,组员:生管,业务/业助,组装线(制造),IQC,SQE,采购,DQE,QC
6
D2 成立8D小组
• 8D小组成员的组成: a) b) 由Leader及组员组成,将人数限制在4-10人. Leader一般品保主管担任, 对产品生产,特性及质量标准较为熟悉 要求具备较强的系统观念,熟练运用QC新旧手法及SPC,FMEA等工具
c)
具备较强的组织,协调,沟通及文字表达能力
11
过程介绍—D4原因分析
• • • • • 原因分析是8D过程中的核心步骤,这一步会直接影响到长期对策,如 果原因分析思路不够正确,后面的长期对策也会失效. 从5W1E人,机,料,法,环,测量原因分析. 一个问题,往往需要从多个角度,多方面分析,所以在分析问题时,先 列出可能造成的原因. 在列出可能的原因后,再利用实验逐一验证,找出真正的原因. 分析原因多采用因果图,柏拉图等方式进行
○
各崗位無人力 儲備
C B D
能力不足
新人上崗前教育訓 練不足
新人教育訓練時間 偏少 教育訓練內容不完 善
◎ ○
15
○ E
公司體制變革,流 程未相應做修改
案例分析
不良现象: 客户投诉DCV-00114-M1-GP(来料号:250017471-GP)无螺纹
原因分析: 1,包装线对铆钉的全检不彻底,导致无牙纹之不良品铆于散 热器本体上. 2,来料铆钉有无牙纹之不良.特采上线全检时产线没有完全 执行全检动作.
預計完成 日期 10月1日
調薪制度不完善
人資部
各崗位無人力儲備
人 資 部 &各 單位主管
10月1日
未建立各崗位招聘考 評規範
1.根據各職位所需技能要求,制訂書面考卷,建 立資料庫 人 資 部 &各 2.制訂各職位實際操作考核辦法 單位主管 3.根據各職位各級別分別制訂招聘新人面試權 限 制 訂 各 崗 位 新 人 上 崗 前 教 育 訓 練 制 度 ,全 脫 產 進行教育訓練,如間接人員需在產線學習1個 月,經考核合格再至用人部門上崗 1.導入新流程,及時變更作業規範. 2.各單位在修改文件或制訂新文件,需召開相 關單位討論,達成共識,再正式發行. 3.ISO整合各個流程是否連貫,再檢討細部權責 分工. 人 資 部 &各 單位主管
失误原因
原因归类
所占比例
忘记
对过程/作业不熟悉 缺乏工作经验 故意失误 疏忽行动迟缓 缺乏适当的作业指导
人
人 人 人 人 人 方法
77.8%
11.1%
突发事件
设备
11.1%
从上表可以看出,在导致失误的原因中,人占了绝大部分77.8%
20
D5提出长期改善对策
1.传统的失误防止出发点 人为失误所占的比重很大,长期以来,各公司采取防止失误的主要措施是”培训与惩罚”,即对 作业者进行大量培训,管理人员每每劝导作业者工作要更加认真和努力,确实通过培训, 可以避免相当一部分人为失误,比如由对过程/作业不熟悉,缺乏工作经验,但由于人为疏 忽,忘记等所造成的失误却很防止,惩罚与教育相结合的方式并不怎么成功. 2.防呆法: 防呆思路 削除 替代 简化 目标 削除可能的失误 用更可靠的过程代替目 前的过程以降低失误 使作业更容易完成 方法 产品及工艺上的设计具有防呆功能 运用机器/治具/模具/自动化生产 技术 评价 最好 较好
3
8D过程概述
• 8D:解决问题的8个步骤/ 8Disciplines of Problem Solving;
D1 描述问题
D2 成立8D 小组
D3 提出并实施短期对策
D4 原因分析
D8 改善效果总结 /表彰
D7 标准化
D6 实施和验证长期 改善对策
D5 提出长期改善对策
4
用8D的时机
一般是客人(包括外部客户,内部客户)或组织内反馈 出的质量异常信息或其他异常信息,均可采用8D的 方法进行改善,已采用8D方法的窗体有: 1.CAR-----外部客户投诉时 2.SCAR-----供货商来料异常时 3.矫正措施单---厂内违反流程作业时 4.品质异常单----厂内制程品质异常时 5.内部稽核不符合项报告单-----内部稽核不符合事项 改善 6.A3 Report ---项目改善
10
D3-提出并实施短期对策
范本: 1.问题点描述: 苏州名硕10/9发现10/8进料的DCV-00154-N2-GP H.S有尺寸偏大现象,要求 10-+/-0.1mm,实际有偏大现象,为10.2~10.3mm,抽检100pcs,有20pcs不 良,不良率20% 2.小组成员: Leader:QA,组员:生管,业务/业助,组装线(制造),IQC,SQE,采购,DQE,QC. 3.短期对策: 1) 客人端1Kpcs库存,我司10/8派人重工,10/9完成,共重出200pcs不良品. 2) 厂内成品2K,10/9重工完成,共重工100pcs不良品 3) 厂内在制无库存 4) 厂内H.S原物料无库存 5) 途中及仓库无库存 6) 供货商无库存
16
连问五次为什么?(5W分析法) —— 一种根本系统解决问题的办法
丰田汽车公司前副社长大野耐一曾举了一个例子来找出停机的真正原因
有一次,大野耐一在生产线上的机器总是停转,虽然修过多次但仍不见
好转。于是,大野耐一与工人进行了以下的问答:
问“为什么机器停了?”答“因为超过了负荷,保险丝就断了。” 问“为什么超负荷呢?”答“因为轴承的润滑不够。” 问“为什么润滑不够?”答“因为润滑泵吸不上油来。” 问“为什么吸不上油来?”答“因为油泵轴磨损、松动了。” 问“为什么磨损了呢?”再答“因为没有安装过滤器,混进了铁屑等杂质。”
8D方法与技巧
1
8D方法培训的主要内容
• • • • • • 8D课程的目标 8D 过程概述 8D 使用时机 8D过程介绍 8D案例分析 8D实际演练
2
8D课程的目标
• 完成本课程后,参加本课程的人员能够:
描述8D过程的每一个步骤。 作为8D成员有效地参加到工作中去。 8D帮助解决重复发生的问题,能独立使用8D方法, 主导8D分析过程的进行,较好的完成8D Report. 能够对问题进行深入的分析,找到真因,并予以彻底 解决.