塑性变形对材料组织与性能的影响
塑性变形对组织和性能的影响

④ 引起磁性变化
⑤ 化学活性↑ 溶解性↑ 耐蚀性 ↓
The End
思考: 塑性变形会对组织 和性能产生什么影响
I live in a small world.
3.变形织构 原来紊乱的位向出现了有序化,具有严格的 位向性。这个过程叫做“择优取向”。 具有择优取向的晶体组织称为 “变形织构”。
思考: 塑性变形会对组织 和性能产生什么影响
I live in a small world.
思考: 塑性变形会对组织 和性能产生什么影响
I live in a small world.
2.亚结构 随ε↑,ρ↑,位错缠结→形成胞状组织 →亚结构,使一个晶粒分割成许多位向差 很小的亚晶粒。 1
亚晶界 = 位错墙
ε↑,胞的数量↑,晶块的尺寸↓, 位向差 ↑
2
思考: 塑性变形会对组织 和性能产生什么影响
思考: 塑性变形会对组织 和性能产生什么影响
I live in a small world.
பைடு நூலகம்
亚结构细化,位错密度增加,产生加工硬化
Q:什么是加工硬化
A:随着塑性变形程度的增加,金属的强度硬度增加,而塑性、韧性 下降,产生所谓“加工硬化”现象
Q:加工硬化产生的原因
A:随着塑性变形的进行,位错运动和互相交割,产生塞积群、割阶、 固定位错、缠结网等,阻碍了位错进一步运动,即提高了进一步变 形的抵抗力
金属或合金经塑性变形过程中, 为什么要进行中间退火处理??
思考: 塑性变形会对组织 和性能产生什么影响
I live in a small world.
2、亚结构细化,位错密度增加,产生加工硬化
Q:加工硬化现象的优点?
A:它是工业上用于提高金属强度、硬度和耐磨性的重要 手段之一,特别是对那些不能以特处理方法强化的纯金 属和某些合金尤为重要!
塑性变形对金属组织和性能的影响
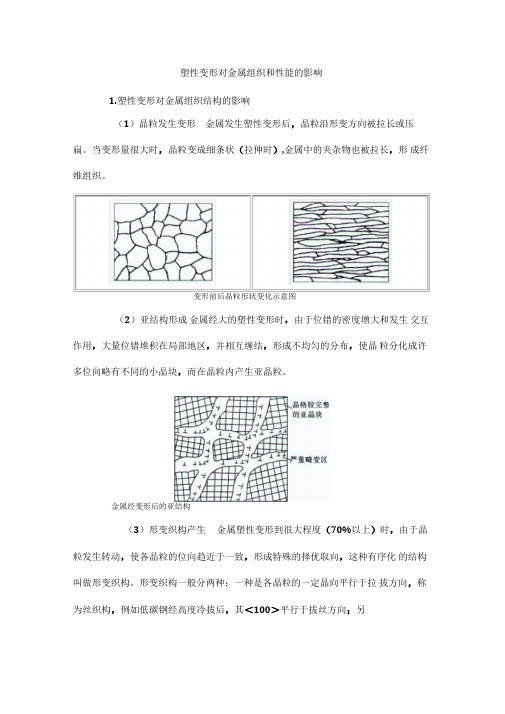
塑性变形对金属组织和性能的影响1.塑性变形对金属组织结构的影响(1)晶粒发生变形金属发生塑性变形后,晶粒沿形变方向被拉长或压扁。
当变形量很大时,晶粒变成细条状(拉伸时),金属中的夹杂物也被拉长,形成纤维组织。
变形前后晶粒形状变化示意图(2)亚结构形成金属经大的塑性变形时,由于位错的密度增大和发生交互作用,大量位错堆积在局部地区,并相互缠结,形成不均匀的分布,使晶粒分化成许多位向略有不同的小晶块,而在晶粒内产生亚晶粒。
金属经变形后的亚结构(3)形变织构产生金属塑性变形到很大程度(70%以上)时,由于晶粒发生转动,使各晶粒的位向趋近于一致,形成特殊的择优取向,这种有序化的结构叫做形变织构。
形变织构一般分两种:一种是各晶粒的一定晶向平行于拉拔方向,称为丝织构,例如低碳钢经高度冷拔后,其<100>平行于拔丝方向;另一种是各晶粒的一定晶面和晶向平行于轧制方向,称为板织构,低碳钢的板织构为{001}<110>。
(购只构形变织构示意图2.塑性变形对金属性能的影响(1)形变强化金属发生塑性变形,随变形度的增大,金属的强度和硬度显著提高,塑性和韧性明显下降。
这种现象称为加工硬化,也叫形变强化。
产生加工硬化的原因是:金属发生塑性变形时,位错密度增加,位错间的交互作用增强,相互缠结,造成位错运动阻力的增大,引起塑性变形抗力提高。
另一方面由于晶粒破碎细化,使强度得以提高。
在生产中可通过冷轧、冷拔提高钢板或钢丝的强度。
(2)产生各向异性由于纤维组织和形变织构的形成,使金属的性能产生各向异性。
如沿纤维方向的强度和塑性明显高于垂直方向的。
用有织构的板材冲制筒形零件时,即由于在不同方向上塑性差别很大,零件的边缘出现“制耳”。
在某些情况下,织构的各向异性也有好处。
制造变压器铁芯的硅钢片,因沿[100]方向最易磁化,采用这种织构可使铁损大大减小,因而变压器的效率大大提高。
因形变织构造成深冲制品的制耳示意图(3)物理、化学性能变化塑性变形可影响金属的物理、化学性能。
塑性变形对金属组织和性能的影响

塑性变形对金属组织和性能的影响1. 塑性变形对金属组织结构的影响(1)晶粒发生变形金属发生塑性变形后,晶粒沿形变方向被拉长或压扁。
当变形量很大时, 晶粒变成细条状(拉伸时), 金属中的夹杂物也被拉长, 形成纤维组织。
变形前后晶粒形状变化示意图(2)亚结构形成金属经大的塑性变形时, 由于位错的密度增大和发生交互作用, 大量位错堆积在局部地区, 并相互缠结, 形成不均匀的分布, 使晶粒分化成许多位向略有不同的小晶块, 而在晶粒内产生亚晶粒。
金属经变形后的亚结构(3)形变织构产生金属塑性变形到很大程度(70%以上)时, 由于晶粒发生转动, 使各晶粒的位向趋近于一致, 形成特殊的择优取向, 这种有序化的结构叫做形变织构。
形变织构一般分两种:一种是各晶粒的一定晶向平行于拉拔方向, 称为丝织构, 例如低碳钢经高度冷拔后, 其<100>平行于拔丝方向; 另一种是各晶粒的一定晶面和晶向平行于轧制方向, 称为板织构, 低碳钢的板织构为{001}<110>。
形变织构示意图2. 塑性变形对金属性能的影响(1)形变强化金属发生塑性变形, 随变形度的增大, 金属的强度和硬度显著提高, 塑性和韧性明显下降。
这种现象称为加工硬化, 也叫形变强化。
产生加工硬化的原因是:金属发生塑性变形时, 位错密度增加, 位错间的交互作用增强, 相互缠结, 造成位错运动阻力的增大, 引起塑性变形抗力提高。
另一方面由于晶粒破碎细化, 使强度得以提高。
在生产中可通过冷轧、冷拔提高钢板或钢丝的强度。
(2)产生各向异性由于纤维组织和形变织构的形成, 使金属的性能产生各向异性。
如沿纤维方向的强度和塑性明显高于垂直方向的。
用有织构的板材冲制筒形零件时, 即由于在不同方向上塑性差别很大, 零件的边缘出现“制耳”。
在某些情况下, 织构的各向异性也有好处。
制造变压器铁芯的硅钢片, 因沿[100]方向最易磁化, 采用这种织构可使铁损大大减小, 因而变压器的效率大大提高。
《金属材料与热处理》第三章金属的塑性变形对组织性能
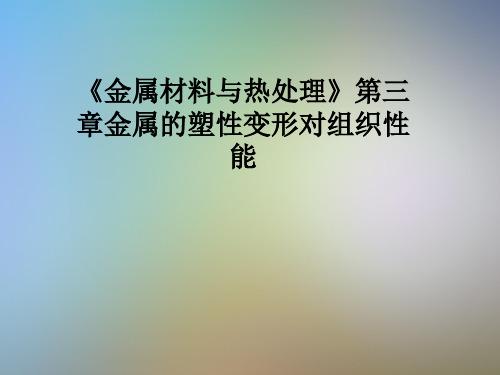
重冷塑性变形的金属,经1小时加热后能完全再结晶的 最低温度来表示。
最低再结晶温度:
T再=0.4T熔点 式中温度单位为绝对温度(K)。
8
学习情境三:金属的塑性变形对组织性能的影响 3.2
(3)再结晶温度影响因素:
1)变形程度 ➢2)金金属属再纯结度晶前:塑纯性度变越形高的, 最相低对再变结形晶量温称度为也预就先越变低形 度➢。3)预;加先热变速形度越大, 金属的晶体缺陷就越多, 组织越不 稳➢➢杂再定质结, 最和晶低合是再金一结元扩晶素散温(过度高程也熔, 需就点一越元定低素时;)间阻才碍能原完子成扩;散和晶 ➢界➢当提迁预高移先加, 可变热显形速著度度提达会高一使最定再低大结再小晶结后在晶,较最温高低度温再;度结下晶发温生度;趋于某 一➢高原稳纯始定度晶值铝粒。(越99粗.9大9,9再%结)最晶低温再度结越晶高温。度为80 ℃; ➢工业纯铝(99.0%)最低再结晶温度提高到290 ℃。
3
学习情境三:金属的塑性变形对组织性能的影响 3.2
3、热加工晶粒大小控制措施
(1).控制较低的加工终了温度 (2).控制较大的变形程度 (3).控制较快的冷却速度
0
学习情境三:金属的塑性变形对组织性能的影响 3.2
3、产生残余内应力 ➢定义:外力去除后,金属内部残留下来的应力。
产生原因:金属发生塑性变形时,内部变形不均匀, 位错、空位等晶体缺陷增多,会产生残余内应力。
➢1)宏观内应力 ➢2)微观残余应力 ➢3)晶格畸变应力
1
学习情境三:金属的塑性变形对组织性能的影响 3.2
3
学习情境三:金属的塑性变形对组织性能的影响 3.1
第一节 金属的塑性变形
塑性变形对金属组织性能的影响

塑性变形对金属组织性能的影响塑性变形是指金属在外力作用发生不可恢复的变形。
因为金属在变形过程中承受很大的外力,所以金属的组织和性能一定会发生变化。
由于金属发生塑性变形时的温度不同,所以金属塑性变形可以根据变形温度分为冷变形,温变形,热变形。
在不同的温度下,金属发生塑性变形时其组织和性能会发生不同的变化。
1.冷塑性变形对金属组织和性能的影响金属发生塑性变形时其变形机制主要有位错的滑移,孪生,扭折,高温下还有晶界滑动和扩散蠕变等方式。
在这些变形方式下,金属的组织会在晶粒形状尺寸,亚结构等方面产生变化,还会产生变形织构等。
在位错的运动过程中,位错之间,位错与溶质原子,间隙原子,空位之间,位错与第二相质点之间都会发生相互作用,引起位错数量,分布的变化。
从微观角度来看,这就是金属组织结构在塑性变形过程中发生的主要变化。
随着金属变形的进行及程度的增加,金属内部的位错密度开始增加,这是因为位错在运动到各种阻碍处如晶界,第二相质点等会受到阻碍,位错就会不断塞积和增值,直到可以使得相邻晶粒内的位错发动才能继续运动。
同时位错运动时所消耗的能量中会有一小部分没有转换成热能散发出去,反而会以弹性畸变能的形式存储在金属内部,使金属内部的点阵缺陷增加。
金属冷塑性变形后还会造成金属内部的亚结构发生细化,如原来在铸态金属中的亚结构直径约为0.01cm,经冷塑性变形后,亚结构的直径将细化至0.001-0.00001cm。
同样金属晶体在塑性变形过程中,随着变形程度的增大,各个晶粒的滑移面和滑移方向会逐渐向外力方向转动。
当变形量很大时,各晶粒的取向会大致趋向于一致,从而破坏了多晶体中各晶粒取向的无序性,也称为晶粒的择优取向,变形金属中这种组织状态则称为变形织构。
在塑性变形过程中随着金属内部组织的变化,金属的机械性能将产生明显的变化。
随着变形程度的增大,金属的硬度,强度显著升高,而塑性韧性则显著下降,这一变化称为加工硬化。
加工硬化认为是与位错的运动和交互作用有关。
塑性变形对材料组织和性能的影响

0.9 μm
Adapted from Fig. 4.6, Callister 6e. (Fig. 4.6 is courtesy of M.R. Plichta, Michigan Technological University.)
17
二、冷变形金属的加工硬化
定义: 金属屈服后,欲使之继续变形必须增加应力的 现象。表现为强度显著提高、塑性明显下降。 发生加工硬化时应力-应变经验关系式:
材料的变形与再结晶
2. 多晶体的加工硬化 (1)加工硬化率明显高于单晶体,无第一阶段。 (2)加工硬化率高。 要使处于硬取向的滑移系启动,必须增大外力; 塑性变形过程中各晶粒内部运动位错的强烈交互 作用使位错塞积严重,晶界处应力集中,硬化曲 线很陡,加工硬化率高。
材料的变形与再结晶
三、形变织构 在外加应力的作用下,各晶粒发生转动, 结果使每个晶粒的某个取向都转动到力轴 方向上来,形成择优取向。具有择优取向 的组织称为织构。
材料的变形与再结晶
DIlloy after cold working: • Dislocations entangle with one another during cold work. • Dislocation motion becomes more difficult.
机制: 位错缠结,主次滑移系间交互作用强烈,形成位 错胞。多个滑移系统被激活,位错运动障碍增 大,使位错运动的自由程缩短,变形进行困难。
材料的变形与再结晶
(3)第三阶段
θ 抛物线硬化阶段, 值呈减小趋势。滑移 线变成滑移带,且滑移带发生碎化。螺位错 发生交滑移,使塞积位错得以松弛,加工硬 化程度减弱。
材料的变形与再结晶
金属塑性变形对组织和性能的影响

金属塑性变形对组织和性能的影响(一)变形程度的影响塑性变形程度的大小对金属组织和性能有较大的影响。
变形程度过小,不能起到细化晶粒提高金属力学性能的目的;变形程度过大,不仅不会使力学性能再增高,还会出现纤维组织,增加金属的各向异性,当超过金属允许的变形极限时,将会出现开裂等缺陷。
对不同的塑性成形加工工艺,可用不同的参数表示其变形程度。
锻造比Y锻:锻造加工工艺中,用锻造比Y锻来表示变形程度的大小。
拔长:Y锻=SO/S (S0 S分别表示拔长前后金属坯料的横截面积);镦粗:Y锻=HO/H(H0 H分别表示镦粗前后金属坯料的高度)。
碳素结构钢的锻造比在2~3 范围选取,合金结构钢的锻造比在3~4 范围选取,高合金工具钢(例如高速钢)组织中有大块碳化物,需要较大锻造比(Y 锻=5~12),采用交叉锻,才能使钢中的碳化物分散细化。
以钢材为坯料锻造时,因材料轧制时组织和力学性能已经得到改善,锻造比一般取1.1~1.3 即可。
表示变形程度的技术参数:相对弯曲半径(r/t )、拉深系数(m)、翻边系数(k)等。
挤压成形时则用挤压断面缩减率( & p)等参数表示变形程度。
(二)纤维组织的利用纤维组织:在金属铸锭组织中的不溶于金属基体的夹杂物(如FeS等),随金属晶粒的变形方向被拉长或压扁呈纤维状。
当金属再结晶时,被压碎的晶粒恢复为等轴细晶粒,而夹杂物无再结晶能力,仍然以纤维状保留下来,形成纤维组织。
纤维组织形成后,不能用热处理方法消除,只能通过锻造方法使金属在不同方向变形,才能改变纤维的方向和分布。
纤维组织的存在对金属的力学性能,特别是冲击韧度有一定影响,在设计和制造零件时,应注意以下两点:(1)零件工作时的正应力方向与纤维方向应一致,切应力方向与纤维方向垂直。
(2)纤维的分布与零件的外形轮廓应相符合,而不被切断。
例如,锻造齿轮毛坯,应对棒料镦粗加工,使其纤维呈放射状,有利于齿轮的受力;曲轴毛坯的锻造,应采用拔长后弯曲工序,使纤维组织沿曲轴轮廓分布,这样曲轴工作时不易断裂(三)冷变形与热变形通常将塑性变形分为冷变形和热变形。
冷塑性变形对金属组织和性能的影响

冷塑性变形对金属组织和性能的影响
图1-12 面心立方晶格金属形变织构示意图
织构的形成使多晶体金属出现各向异性,在冲压复杂形 状零件(如汽车覆盖件等)时,产生不均匀塑性变形则可能导致 工件报废。但是,也可利用织构现象来提高硅钢板的某一方向 的磁导率。
冷塑性变形对金属组织和性能的影响
二、 冷塑性变形对金属性能的影响 1. 产生加工硬化
金属材料随着冷塑性变形程度的增大,强度 和硬度逐渐升高,塑性和韧性逐渐降低的现象称 为加工硬化或冷作硬化,这也是冷塑性变形后的 金属在力学性能方面最为突出的变化。
冷塑性变形对金属组织和性能的影响
显然,加工硬化是金属内部组织结构发生变化的宏观表 现。经冷变形后,晶界总面积增大,位错密度也增大,位错 线间的距离减小,彼此干扰作用明显增强,使得能够产生滑 移变形的潜在部位减少,从而导致滑移阻力增加,塑性变形 能力降低。再则,金属冷变形后,原来的晶粒破碎了,形成 许多亚结构,在亚晶粒边界上聚集着大量位错,产生严重的 晶格畸变,也对滑移过程产生巨大阻碍。所有这些都使金属 变形抗力升高,塑性和韧性降低。图1-13是ωC=0.3%碳钢冷 轧后力学性能的变化。
冷塑性变形对金属组织和性能的影响
图1-14 制耳现象
但是织构现象在有些方面是 可以利用的。例如,生产变压器 硅钢片时,其晶格为体心立方, 沿[100]晶向最易磁化,如采 用具有织构取向的硅钢片制作铁 芯,使其[100]晶向平行于磁 场方向,则其磁导率显著增大, 从而提高变压器效率金属组织和性能的影响
图1-13 ωC=0.3%碳钢冷轧后力学性能的变化
冷塑性变形对金属组织和性能的影响
加工硬化使金属强化是以牺牲金属的塑性、韧性为 代价的,而且在冷变形加工过程中随着加工硬化现象的 产生要不断增加机械功率,故对设备和工具的强度提出 了较高要求,随着材料塑韧性的下降,也可能发生脆性 破坏。此外,加工硬化也使冷轧、冷拔、冲压等成形工 艺增加能耗,为恢复塑性继续进行冷变形往往要进行中 间退火,这就使生产周期延长,成本增加。
塑性变形再结晶对组织性能的影响

塑性变形再结晶对组织性能的影响试验一塑性变形再结晶对Q235钢组织性能的影响一引言1、塑性变形对金属组织与性能的影响金属经塑性变形后,不仅形状和尺寸上发生变化,其组织和性能也发生变化。
随着塑性变形量的增大,金属材料的由原始的等轴晶组织向纤维状组织转变,即晶粒将沿变形方向逐渐伸长,变形度越大,则伸长也越显著;当变形度很大时,其组织呈纤维状。
组织影响性能,由于变形产生了大量的位错和孪晶,对金属起到了强化作用,金属的强度和硬度有所提高,塑性下降,即产生了所谓的“加工硬化”现象。
另外,随着变形程度的加剧,原来位向不同的各个晶粒会逐渐取得近于一致的位向,而形成了形变织构,使金属材料的性能呈现出明显的各向异性。
2、塑性变形后再结晶对组织性能的影响塑性变形金属加热温度到再结晶温度时,原子活动能力增大,金属的显微组织发生明显的变化,由破碎拉长或压扁的晶粒变为均匀细小的等轴晶粒。
由于加热温度低于相变温度,故没有发生相变,只是一个新晶粒形核和长大的过程,即再结晶。
再结晶消除了冷加工纤维组织、加工硬化和残余应力,使金属又重新恢复到冷塑性变形前的状态,纤维组织消失,取而代之的是均匀细小的等轴晶粒。
再结晶温度与金属本性、杂质含量、冷变形程度、保温时间、材料的原始晶粒度等有关。
再结晶所产生的晶粒大小在很大程度上取决于冷变形程度的大小。
工业生产中则常以经过大变形量(约70%以上度的变形金属经1h 保温,能完成再结晶(﹥95%转变量)的最低温度,定为该金属的再结晶温度。
实验证明,金属的熔点愈高,在其他条件相同时,其再结晶温度也愈高。
金属的再结晶温度(T再) 与其熔点(T熔) 间的关系,大致可用下式表示:T 再=0.4 T熔其中,T 再、T 熔按绝对温度计算,以铜为例,纯铜的熔点是1083℃,系数取0.40时,计算如下:T 再=0.40T熔=0.40×(1083+273)K=542.4K=269.4℃金属的纯度越高,再结晶温度就越低,再结晶过程也就越快。
材料科学基础-第6章塑性变形1

7
7
6.1.1 单晶体的塑性变形
晶体塑性的好坏,不仅取决于滑移系的多少,还与滑 移面上原子的密排程度和滑移方向的数目等因素有关。 例如体心立方金属α-Fe,与面心立方金属的滑移系 同样多,都为12个。但它的滑移方向没有面心立方金
属多,同时滑移面间距离较小,原子间结合力较大, 必须在较大的应力作用下才能开始滑移,所以它的塑 性要比铝、铜等面心立方金属差。
图6-6 拉伸时晶体发生转动的示意图
14
14
6.1.1 单晶体的塑性变形
5.多系滑移与交滑移 多滑移:若有多组滑移系相对于外力轴的方向相同, 分切应力同时达到临界值,滑移一开始就可以在两个 或多个滑移系同时进行。 交滑移:在晶体中,还会发生两个或两个以上滑移面 沿着同一个滑移方向同时或交替进行滑移的现象。
4
4
图6-2 滑移带形成示意图
5
5
2.滑移系 金属中的滑移是沿着一定的晶面和一定的晶向进行的, 这些晶面称为滑移面,晶向称为滑移方向。
表6-1
三种常见金属晶体结构的滑移系
6
6
6.1.1 单晶体的塑性变形
滑移面通常是晶体中原子排列最密的晶面,而滑移方 向则是原子排列最密的晶向。这是因为密排面之间的 距离最大,面与面之间的结合力较小,滑移的阻力小, 故易滑动。而沿密排方向原子密度大,原子每次需要 移动的间距小,阻力也小。 一个滑移面和该面上的一个滑移方向组成一个滑移系。 每个滑移系表示晶体进行滑移时可能采取的一个空间 取向。 晶体中的滑移系越多,滑移过程中可能采取的空间取 向便越多,滑移越容易进行,故这种晶体的塑性便越 好。密排六方晶体由于滑移系数目太少,故塑性较差。
11
11
图6-4 镁单晶拉伸的屈服应力与晶体取向的关系
金属塑性变形对组织和性能的影响

金属塑性变形对组织和性能的影响多晶体金属经塑性变形后,除了在晶粒内出现滑移带和孪晶等组织特征外,还具有以下组织结构的变化:①形成纤维组织,塑性变形后,晶粒沿变形方向逐渐伸长,变形量越大,晶粒伸长的程度也越大。
当变形量很大时,晶粒呈现出一片如纤维状的条纹,称为纤维组织.当金属中有杂质存在时,杂质也沿变形方向拉长为细带状(塑性杂质)或粉碎成链状(脆性杂质).②形变亚结构的形成及细化.●形变亚结构的形成机理:在切应力作用下,位错源所产生的大量位错沿滑移面运动时,将遇到各种阻碍位错运动的障碍物,如晶界、亚晶界、第二相颗粒及割阶等,造成位错缠结.这样,金属中便出现了由高密度的缠结位错分隔开的位错密度较低的区域,即形变亚结构。
●亚结构的细化,形变亚结构的边界是严重晶格畸变区,堆积大量位错,而内部的晶格则相对完整,仅有稀疏的位错网络,这种亚结构也称为胞状亚结构或形变胞.(内部完整,外部包满位错)③产生变形织构,与单晶体一样,多晶体在塑性变形时也伴随着晶体的转动过程,故当变形量很大时,多晶体中原为任意取向的各个晶粒会逐渐调整其取向而趋于一致,这种现象称为晶粒的择优取向,这种由于金属塑性变形使晶粒具有择优取向的组织叫做形变织构。
同种材料随着加工方式的不同,可能出现不同类型的织构:●丝织构:在拉拔时形成,其特征是各晶粒的某一晶向与拉拔方向平行或接近平行。
●板织构:在轧制时形成,其特征是各晶粒的某一晶面与平行于轧制平面,而某一晶向平行于轧制方向。
性能特点:显示出各向异性。
塑性变形对金属性能的影响金属产生加工硬化(也称形变强化)在塑性变形过程中,随着金属内部组织的变化,金属的力学性能也将产生明显的变化,即随着变形程度的增加,金属的强度、硬度增加,而塑性、韧性下降,这一现象即为加工硬化或形变硬化。
加工硬化的原因:与位错的交互作用有关。
随着塑性变形的进行,位错密度不断增大,位错运动时的相互交割加剧,产生固定割阶、位错缠结等障碍,使位错运动的阻力增大.引起形变抗力的增加,金属的强度提高.加工硬化的是强化金属材料的方法之一。
第二章 塑性变形--第二节 塑性变形对组织和性能的影响

8
三、织构现象的产生
( 1 )形变织构:多晶体材料由塑性变形导致的 各晶粒呈择优取向的组织。变形量达到70-90%时 产生。 (2)类型 丝织构:某一晶向趋 于与拔丝方向平行。(拉 拔时形成) 板织构:某晶面趋于 平行于轧制面,某晶向趋 于平行于主变形方向。 (轧制时形成)
9
形变织构对性能的影响 力学性能:深冲板材变形易产生制耳。(各向异性) 物理性能:硅钢片{100}[100]织构可减少铁损。
6
加工硬化的利弊 (1)利 强化金属的重要途径(如铝、铜、不锈 钢); 材料加工成型的保证(如冷拔钢丝); 提高材料使用安全性。 (2)弊 变形阻力提高,动力消耗增大.
7
塑性变形对材料物理、化学性能的影响 导电率、导磁率下降,比重、热导率下降; 结构缺陷增多,扩散加快; 化学活性提高,腐蚀加快。
Ⅰ 残余应力易引起变形、开裂,如黄铜弹壳的腐蚀开裂体的加工硬化效应比单晶体强。晶粒越细,硬化效应越 强。
5
总结
1.固溶体的加工硬化:主要通过柯氏气团对位错 的钉扎作用。 2.单晶体的加工硬化:主要通过位错间的相互纠 缠作用。 3.多晶体的加工硬化:除了位错间的相互纠缠作 用外,还有晶界对位错运动的阻碍作用。多晶体 的加工硬化效应比单晶体的加工硬化效应强。
三个阶段组成: I阶段——易滑移阶 段; Ⅱ阶段——线性硬化 阶段; Ⅲ阶段——抛物线型 硬化阶段
3
位错的交割 晶体中位错线的方位各式 各样,不同滑移面上运动的位 错在运动中相遇就有可能发生 位错互相切割现象,称之为位 错的交割. 位错的交割的结果在原来 是直的位错线上形成一段一个 或几个原子间距大小的折线 (割阶),使原来的位错线变 长,能量增加,因此交割过程 对位错运动具有阻碍作用,使 变形过程中产生应变硬化。
材料科学基础_材料的塑形变形

第三节
• • • • •
滑移的位错理论分析
滑移的实质是位错的运动 位错的增殖 位错的交割 位错的塞积 加工硬化
滑移的实质是位错的运动
大量的理论研究证明,滑移原来是由于滑移面上 的位错运动而造成的。图示例子表示一刃型位错在切 应力的作用下在滑移面上的运动过程,通过一根位错 从滑移面的一侧运动到另一侧便造成一个原子间距的 滑移。
滑移的实质是位错的运动
位错的滑移面就是晶体的滑移面,柏氏矢量的 方向就是晶体的滑移方向。为了使位错的能量较低, 在结构容许的条件下,尽量减小柏氏矢量,所以原子 的密排方向就成为了位错的柏氏矢量的方向。
位错的增殖
塑性变形的过程中,尽管位错移出晶体产 生滑移台阶,但位错的数量(位错密度)却在不 断的增加,这是因为在外应力作用下发生塑性 变形时位错会发生增殖。
3. 应变:物体形状尺寸所发生的相对改变。物体内部 某处的线段在变形后长度的改变值同线段原长之比 值称为“线应变”;物体内两互相垂直的平面在变 形后夹角的改变值称为“剪应变”或“角应变”; 变形后物体内任一微小单元体体积的改变同原单位 体积之比值称为“体积应变”。
变形过程
低碳钢的拉伸曲线如 图所示。 在应力低于弹性极限 σ e时,材料发生的 变形为弹性变形;应 力在σ e到σ b之间将 发生的变形为均匀塑 性变形;在σ b之后 将发生颈缩;在K点 发生断裂。
塑性变形过程--颈缩
1. 颈缩:试样将开始发生不均匀的塑性变形, 产生了颈缩,即塑性变形集中在一局部区域 进行。 2. 特点:颈缩发生后,宏观表现为外力在下降, 工程应力在减小,但颈缩区的材料承受的真 实应力依然在上升。
3. 极限强度:材料开始发生颈缩时对应的工程 应力σ b ,这时试样出现失稳,颈缩真实应 力依然在上升,但能承受的总外力在下降。
塑性变形对材料性能的影响研究

塑性变形对材料性能的影响研究引言:材料工程的发展离不开对材料性能的深入研究和了解。
其中,塑性变形是一个重要的研究方向。
塑性变形是材料受到外力作用后,在不断应力增大的情况下发生的形变现象。
本文将探讨塑性变形对材料性能的影响,并分析其机制和应用前景。
一、塑性变形与材料力学性能材料的塑性变形是由于结晶体内部的原子移动和位错滑移所引起的。
位错是材料内部的微观缺陷,可以看作是构成晶体的原子排列的错位。
塑性变形对材料的力学性能有着显著的影响。
首先,塑性变形能够提高材料的延展性和塑性,使其具有更好的韧性和可塑性。
相比于脆性材料,经过塑性变形的材料在受力时能更好地承受应力,并且具有更好的抗断裂性能。
其次,塑性变形还可以改善材料的力学强度。
塑性变形过程中,原子滑移受到应力的作用,位错在晶体内移动,从而引起材料内部晶粒的重新排列。
这样,材料中的晶粒得到细化,晶界的面积增加,从而有效地提高材料的强度。
此外,塑性变形还可以消除材料中的一些缺陷和内部应力,提高材料的耐腐蚀性能和疲劳寿命。
综上所述,塑性变形对材料的力学性能有着积极的影响。
二、塑性变形与材料电子性能材料的电子性能是指在电子的传导和非传导过程中,材料所表现出的特性。
而塑性变形对材料的电子性能同样有着重要的影响。
塑性变形使材料内部发生变形和位错产生,从而改变了材料的晶体结构和电子分布。
对于金属材料来说,塑性变形会导致电子云的重新分布以及电子与原子排列之间的相互作用发生变化。
这些变化会影响金属的导电性、电阻率和磁性等电子性能。
一些研究表明,在塑性变形后,金属材料的电导率会有所改善,从而提高其导电性能。
此外,塑性变形还可以增加材料表面的电子密度,并增强电子在材料内部的传输。
这些变化不仅对金属材料的电子性能有着积极的影响,也为材料在电子器件方面的应用提供了新的可能性。
三、塑性变形与材料化学性能除了对材料的力学性能和电子性能有影响外,塑性变形也可以对材料的化学性能产生一定的影响。
材料科学基础试题一二及参考答案
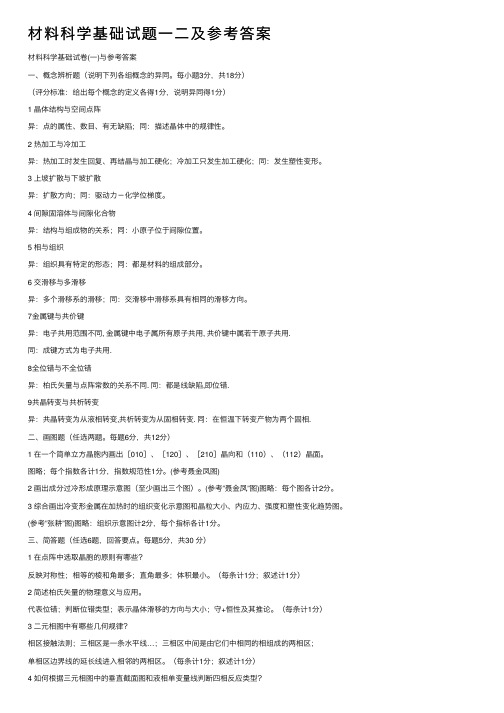
材料科学基础试题⼀⼆及参考答案材料科学基础试卷(⼀)与参考答案⼀、概念辨析题(说明下列各组概念的异同。
每⼩题3分,共18分)(评分标准:给出每个概念的定义各得1分,说明异同得1分)1 晶体结构与空间点阵异:点的属性、数⽬、有⽆缺陷;同:描述晶体中的规律性。
2 热加⼯与冷加⼯异:热加⼯时发⽣回复、再结晶与加⼯硬化;冷加⼯只发⽣加⼯硬化;同:发⽣塑性变形。
3 上坡扩散与下坡扩散异:扩散⽅向;同:驱动⼒-化学位梯度。
4 间隙固溶体与间隙化合物异:结构与组成物的关系;同:⼩原⼦位于间隙位置。
5 相与组织异:组织具有特定的形态;同:都是材料的组成部分。
6 交滑移与多滑移异:多个滑移系的滑移;同:交滑移中滑移系具有相同的滑移⽅向。
7⾦属键与共价键异:电⼦共⽤范围不同, ⾦属键中电⼦属所有原⼦共⽤, 共价键中属若⼲原⼦共⽤.同:成键⽅式为电⼦共⽤.8全位错与不全位错异:柏⽒⽮量与点阵常数的关系不同. 同:都是线缺陷,即位错.9共晶转变与共析转变异:共晶转变为从液相转变,共析转变为从固相转变. 同:在恒温下转变产物为两个固相.⼆、画图题(任选两题。
每题6分,共12分)1 在⼀个简单⽴⽅晶胞内画出[010]、[120]、[210]晶向和(110)、(112)晶⾯。
图略;每个指数各计1分,指数规范性1分。
(参考聂⾦凤图)2 画出成分过冷形成原理⽰意图(⾄少画出三个图)。
(参考”聂⾦凤”图)图略:每个图各计2分。
3 综合画出冷变形⾦属在加热时的组织变化⽰意图和晶粒⼤⼩、内应⼒、强度和塑性变化趋势图。
(参考”张耕”图)图略:组织⽰意图计2分,每个指标各计1分。
三、简答题(任选6题,回答要点。
每题5分,共30 分)1 在点阵中选取晶胞的原则有哪些?反映对称性;相等的棱和⾓最多;直⾓最多;体积最⼩。
(每条计1分;叙述计1分)2 简述柏⽒⽮量的物理意义与应⽤。
代表位错;判断位错类型;表⽰晶体滑移的⽅向与⼤⼩;守+恒性及其推论。
塑性变形行为对材料力学的影响

塑性变形行为对材料力学的影响塑性变形是指在材料受到外力作用下,保持形变的能力,而不会恢复到原始形状。
它是材料力学中的重要现象,对材料性能和力学行为有着深远的影响。
本文将探讨塑性变形行为对材料力学的影响,并分析其对材料强度、韧性、疲劳寿命和变形机制的影响。
首先,塑性变形对材料强度的影响是显著的。
在材料受到外力作用时,塑性变形能够增加其抗拉、抗压和抗弯强度。
塑性变形使材料内部的晶体结构发生重新排列和畸变,形成了更多的位错和晶界,这些缺陷可以阻碍传递应力,提高材料的强度。
例如,在金属材料中,塑性变形能够使晶粒细化,提高材料的屈服强度和抗拉强度。
其次,塑性变形对材料韧性的影响也是重要的。
韧性是材料抵抗断裂和破坏的能力,也是衡量材料耐用性的重要指标。
塑性变形可以使材料在受到外力作用时产生大量的塑性变形能量吸收,从而提高材料的韧性。
塑性变形减缓了应力集中和裂纹扩展的速度,增加了材料的断裂韧性。
同时,塑性变形还可以通过分散和吸收裂纹能量来提高材料的断裂韧性。
此外,塑性变形还对材料的疲劳寿命产生了影响。
疲劳寿命是材料在循环载荷下发生断裂或失效的程度。
塑性变形会导致材料内部形成许多微观缺陷和位错,这些缺陷和位错会催化和加速疲劳裂纹的产生和扩展。
因此,在疲劳加载下,塑性变形可能导致材料疲劳寿命的缩短。
研究表明,在低应力幅值下,材料的疲劳寿命受到塑性变形的支配,而在高应力幅值下,疲劳寿命受到裂纹扩展的支配。
最后,塑性变形行为对材料的变形机制也有着重要的影响。
根据材料的力学行为可以分为弹性和塑性变形两种。
弹性变形是可逆的,当外力去除时,材料会恢复到原始形状,而塑性变形是不可逆的,材料无法完全恢复到原始形状。
塑性变形机制涉及材料内部位错的移动和重排、晶粒滑移、孪晶和晶间滑移等过程。
这些变形机制的存在和相互作用直接影响材料的变形行为和性能。
综上所述,塑性变形行为对材料力学有着重要的影响。
塑性变形可以提高材料的强度和韧性,但也可能缩短材料的疲劳寿命。
金属塑性变形对组织和性能的影响

金属塑性变形对组织和性能的影响(一)变形程度的影响塑性变形程度的大小对金属组织和性能有较大的影响。
变形程度过小,不能起到细化晶粒提高金属力学性能的目的;变形程度过大,不仅不会使力学性能再增高,还会出现纤维组织,增加金属的各向异性,当超过金属允许的变形极限时,将会出现开裂等缺陷。
对不同的塑性成形加工工艺,可用不同的参数表示其变形程度。
锻造比Y锻:锻造加工工艺中,用锻造比Y锻来表示变形程度的大小。
拔长:Y锻=S0/S(S0、S分别表示拔长前后金属坯料的横截面积);镦粗:Y锻=H0/H(H0、H分别表示镦粗前后金属坯料的高度)。
碳素结构钢的锻造比在2~3范围选取,合金结构钢的锻造比在3~4范围选取,高合金工具钢(例如高速钢)组织中有大块碳化物,需要较大锻造比(Y锻=5~12),采用交叉锻,才能使钢中的碳化物分散细化。
以钢材为坯料锻造时,因材料轧制时组织和力学性能已经得到改善,锻造比一般取1.1~1.3即可。
表示变形程度的技术参数:相对弯曲半径(r/t)、拉深系数(m)、翻边系数(k)等。
挤压成形时则用挤压断面缩减率(εp)等参数表示变形程度。
(二)纤维组织的利用纤维组织:在金属铸锭组织中的不溶于金属基体的夹杂物(如FeS等),随金属晶粒的变形方向被拉长或压扁呈纤维状。
当金属再结晶时,被压碎的晶粒恢复为等轴细晶粒,而夹杂物无再结晶能力,仍然以纤维状保留下来,形成纤维组织。
纤维组织形成后,不能用热处理方法消除,只能通过锻造方法使金属在不同方向变形,才能改变纤维的方向和分布。
纤维组织的存在对金属的力学性能,特别是冲击韧度有一定影响,在设计和制造零件时,应注意以下两点:(1)零件工作时的正应力方向与纤维方向应一致,切应力方向与纤维方向垂直。
(2)纤维的分布与零件的外形轮廓应相符合,而不被切断。
例如,锻造齿轮毛坯,应对棒料镦粗加工,使其纤维呈放射状,有利于齿轮的受力;曲轴毛坯的锻造,应采用拔长后弯曲工序,使纤维组织沿曲轴轮廓分布,这样曲轴工作时不易断裂(三)冷变形与热变形通常将塑性变形分为冷变形和热变形。
- 1、下载文档前请自行甄别文档内容的完整性,平台不提供额外的编辑、内容补充、找答案等附加服务。
- 2、"仅部分预览"的文档,不可在线预览部分如存在完整性等问题,可反馈申请退款(可完整预览的文档不适用该条件!)。
- 3、如文档侵犯您的权益,请联系客服反馈,我们会尽快为您处理(人工客服工作时间:9:00-18:30)。
变形量很大时,晶粒拉长,出现纤维组织
等轴晶
沿变形方向 晶粒拉长
2 亚结构的变化
• 金属晶体在塑性变形的同时,位错密度迅速提高 。 • 经塑性变形后,多数金属晶体中的位错分布不均匀,当形变 量较小时,形成位错缠结结构。 • 当变形量继续增加时,大量位错发生聚集,使晶粒分化成许 多位向略有不同的小晶块, 产生亚晶粒,即形成胞状亚结构。
• 第II阶段,滑移在几组相交的滑移面中发生,由于运动位错之间 的交互作用,形成不利于滑移的结构状态,在相交滑移面上形 成割阶扭折、固定为错,位错运动变得非常困难,故该阶段称
为线性硬化阶段。加工硬化现象显著。
第III阶段,在应力进一步增高的
条件下,已产生的滑移障碍将逐 渐被克服,并通过交滑移的方式 继续进行变形。由于该段曲线呈 抛物线变化,故称为抛物线型硬 化阶段。
不过加工硬化现象也存在不利之处,由于金属在
加工过程中塑性抗力不断增加,造成塑性变形困难。
另外由于加工硬化使金属变脆,因而在以
便继续变形加工而不致裂开。
用位错理论分析纯金属与合金在冷变形加工时,在产
生加工硬化机理上有何区别。
• 答:纯金属单晶体产生加工硬化的机理主要是:
• 问题:强化金属材料的方法有哪些?并指出其异同点。
• 加工硬化、固溶强化、弥散强化、沉淀强化、细晶强化。
• 共同点也就是金属强化的实质,在于塑性变形时增加了
位错运动的阻力。 • 不同点:(1)加工硬化:位错塞积、林位错阻力和形成 割阶阻碍位错运动(2)细晶强化:增加了晶界,增加了 位错塞积的范围(3)固溶强化:溶质原子沿位错聚集并 钉扎位错(4)第二相强化:分散的强化相颗粒迫使位错 切过或绕过强化相颗粒而额外做功,都是分散相强化的
一般来说,高层错能晶体易形成胞状亚结构。而低层错能晶 体形成这种结构的倾向较小。 这是由于对层错能高的金属而言,在变形过程中,位错不 易分解,在遇到阻碍时,可以通过交滑移继续运动,直到与 其它位错相遇缠结,从而形成位错聚集区域(胞壁)和少位 错区域(胞内)。
层错能低的金属由于其位错易分解,形成扩展位错,不易
在体心立方纯金属铌中,微量的间隙原子(C、N、0等),
由于会发生与位错的交互作用而产生屈服现象,从而使曲
线第一阶段几乎消失。
密排六方纯金属镁由于只沿
一组相平行的滑移面作单系
滑移,位错的交截作用很弱, 故第1阶段曲线很长,以至几 乎第II阶段还没充分发展时试 样就已经断裂了。
多晶体的塑性变形由于晶界的阻碍作用和晶粒之间的协 调配合作用,各晶粒不可能以单一滑移系动作,而必然有多 组滑移系同时作用,因此多晶体的应力——应变曲线不会出
• (1)当外力在滑移面及滑移方向上的分切应力达到临界分 切应力时位错源开动,位错增殖使位错密度增加。 • (2)在发生多系滑移后,在两个相交滑移面上运动的位错 必然会互相交割,形成割阶、扭结,使其运动阻力增大。 • (3)位错之间发生反应,形成固定位错,造成位错塞积, 使位错运动阻力进一步增大。
• 对纯金属多晶体,其加工硬化机理比单晶体多出了晶界
交滑移,其运动性差,因而通常只形成分布较均匀的复杂网
络结构。
3 性能的变化
• (1)加工硬化(形变强化) • 金属发生塑性变形, 随变形度增大, 金属的强度和硬度显 著升高, 塑性和韧性明显下降。这种现象称为加工硬化。
强度指标增加、塑
性指标下降。
冷轧对铜及钢性能 的影响
金属的加工硬化特性可以从其应力-应变曲线上反映出 来。图是单晶体的应力-应变曲线,单晶体的塑性变形可划 分为三个阶段描述: 第I阶段,当切应力达到晶体的 临界分切应力值时,滑移首先从 一个滑移系中开始,由于位错运 动所受的阻碍很小,因此该阶段 称为易滑移阶段。此阶段加工硬 化率低。
• 而各种晶体由于其结构类型、取向、杂质含量以及试验温度
等因素的影响,实际曲线有所改变 。 • 具有低层错能的铜显示了典型的应力-应变曲线持征;而具 有高层错能的铝,则由于其位错不易扩展,容易交滑移,故 应力-应变曲线的第III阶段开始较早,第II阶段极短 。 晶体中的杂质可使应力—应 变曲线的硬化系数有所增大, 曲线第I阶段将随杂质含量的 增加而缩短,甚至消失。
造成的位错塞积作用,阻碍了位错的运动。
• 对于合金,若是单相固溶体,其加工硬化机理比纯金属
多晶体又多出了固溶强化作用,即溶质原子与位错的弹 性相互作用形成柯氏气团,化学相互作用形成铃木气团, 阻碍位错的运动。 • 若是多相合金,其加工硬化机理比固溶体合金又多出来 沉淀强化、弥散强化机制,强化机理分别是位错的绕过 机制和切过机制,使位错运动阻力更进一步增大。
• 冷变形过程中形成亚结构是许多金属(例如铜、铁、钼、 钨、钽、铌等)普遍存在的现象。 • 一般认为亚结构对金属的加工硬化起重要作用,由于各 晶块的方位不同,其边界又为大量位错缠结,对晶内的 进一步滑移起阻碍作用。因此,亚结构可提高金属和合 金的强度。 • 利用亚晶来强化金属材料是措施之一。
研究表明,胞状亚结构的形成与否与材料的层错能有关,
位错机制。
(2)其它性能变化
经塑性变形后的金属,由于点阵畸变、位错与 空位等晶体缺陷的增加,其物理性能和化学性能也 会发生一定的变化。如电阻率增加,电阻温度系数 降低,磁导率、热导率下降。此外,由于原子活动
现单晶体曲线的第1阶段,而且其硬化曲线更陡。
• 塑性变形过程中位错密度的不断增加极其所产生的钉扎作用
是导致加工硬化的决定性因素。 • 加工硬化现象作为变形金属的一种强化方式,有其实际应用 意义,如许多不能通过热处理强化的金属材料,可以利用冷 变形加工同时实现成形与强化的目的。 • 例如对于工业上广泛应用的铜导线,由于要求导电性好,不 允许加合金元素,加工硬化是提高强度的唯一方法。
塑性变形对材料组织与性能的影响
晶体发生塑性变形后,不仅其外形发生了变化,其内部组 织以及各种性能也都发生了变化。
(1)显微组织的变化
经塑性变形后,金属材料的显微组织发生了明显的改变, 各晶粒中除了出现大量的滑移带、孪晶带以外,其晶粒形状 也会发生变化,随着变形量的逐步增加,原来的等轴晶粒逐 渐沿变形方向被拉长,当变形量很大时,晶粒已变成纤维状。