中间轴齿轮机加工工艺及夹具设计
齿轮类零件加工工艺分析及夹具方案
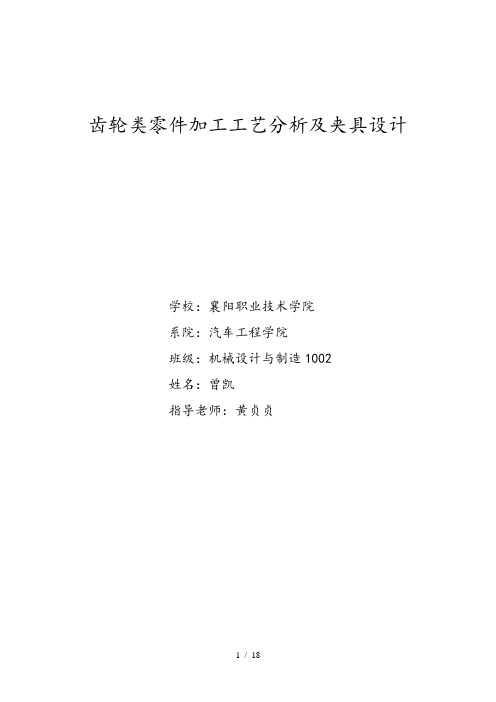
齿轮类零件加工工艺分析及夹具设计学校:襄阳职业技术学院系院:汽车工程学院班级:机械设计与制造1002姓名:曾凯指导老师:黄贞贞目录摘要 (4)第一章齿轮类零件加工工艺规程编制概述 (5)1.1工艺编制的总体步骤 (5)第二章对齿轮类零件的加工工艺编制及分析 (6)2.1分析齿轮类零件的技术要求 (6)2.2明确毛坯尺寸 (8)2.3拟定工艺路线 (8)2.4设计工序内容 (10)2.5填写工艺文件 (10)第三章对齿轮类零件加工工艺进行合理性分析 (11)第四章夹具设计的要求 (11)4.1 了解夹具设计的总体要求 (11)第五章夹具设计的特点 (12)5.1确定夹具的类型 (12)5.2钻模的主要类型 (12)第六章工件夹紧计算及选择 (13)6.1工件的夹紧 (13)6.2 夹紧力的选择 (13)6.3夹紧力的计算及精度分析 (14)第七章夹具的结构分析及设计 (16)7.1夹具的夹紧和定位 (16)7.2夹具的导向 (17)第八章夹具的总体分析 (17)第九章致谢 (18)摘要齿轮类零件是典型零件之一,它在机械主要用于传动,齿轮类零件主要有齿轮.齿轮轴,涡轮涡杆,在机械领域运用很广泛。
按传动形式分圆柱类齿轮、锥齿轮、齿条等。
按齿形状分:齿轮、齿、字齿等。
按制作方法分:铸造齿轮、烧结齿轮、轧制齿轮等。
我以齿轮加工工艺编制分析齿轮的加工要求,在生产实际中阐述齿轮的工艺过程,及工艺的合理性。
夹具在机械加工中有举足轻重的作用,好的夹具才是保障零件加工的方法。
我从夹具的分析、设计、计算、使用方面概述夹具的用途。
按专业化程度可分为通用夹具、专用夹具、可调夹具、组合夹具、成组夹具、标准夹具、随行夹具、组合机床夹具等。
我这次设计的是盖板式钻夹具。
这是一种专用夹具,专为一工件的一道工序而设计的夹具。
关键词:齿轮、夹具、工艺、设计1.1工艺编制的总体步骤1.分析零件的结构和技术要求(1)分析图样资料①加工工艺表面的尺寸精度和形状精度②各加工表面之间以及加工表面和不加工表面之间的位置精度③加工表面的粗糙度及表面的其他要求④热处理及其他要求(2)零件的结构工艺分析。
齿轮类零件加工工艺分析及夹具设计毕业设计论文
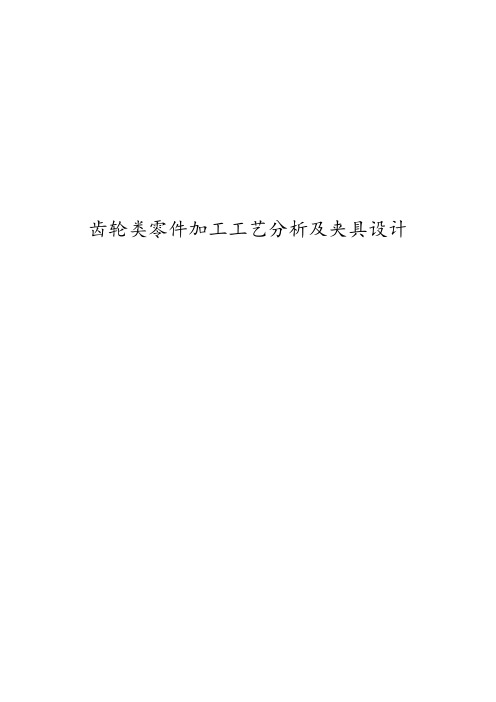
齿轮类零件加工工艺分析及夹具设计毕业设计(论文)原创性声明和使用授权说明原创性声明本人郑重承诺:所呈交的毕业设计(论文),是我个人在指导教师的指导下进行的研究工作及取得的成果。
尽我所知,除文中特别加以标注和致谢的地方外,不包含其他人或组织已经发表或公布过的研究成果,也不包含我为获得及其它教育机构的学位或学历而使用过的材料。
对本研究提供过帮助和做出过贡献的个人或集体,均已在文中作了明确的说明并表示了谢意。
作者签名:日期:指导教师签名:日期:使用授权说明本人完全了解大学关于收集、保存、使用毕业设计(论文)的规定,即:按照学校要求提交毕业设计(论文)的印刷本和电子版本;学校有权保存毕业设计(论文)的印刷本和电子版,并提供目录检索与阅览服务;学校可以采用影印、缩印、数字化或其它复制手段保存论文;在不以赢利为目的前提下,学校可以公布论文的部分或全部内容。
作者签名:日期:学位论文原创性声明本人郑重声明:所呈交的论文是本人在导师的指导下独立进行研究所取得的研究成果。
除了文中特别加以标注引用的内容外,本论文不包含任何其他个人或集体已经发表或撰写的成果作品。
对本文的研究做出重要贡献的个人和集体,均已在文中以明确方式标明。
本人完全意识到本声明的法律后果由本人承担。
作者签名:日期:年月日学位论文版权使用授权书本学位论文作者完全了解学校有关保留、使用学位论文的规定,同意学校保留并向国家有关部门或机构送交论文的复印件和电子版,允许论文被查阅和借阅。
本人授权大学可以将本学位论文的全部或部分内容编入有关数据库进行检索,可以采用影印、缩印或扫描等复制手段保存和汇编本学位论文。
涉密论文按学校规定处理。
作者签名:日期:年月日导师签名:日期:年月日注意事项1.设计(论文)的内容包括:1)封面(按教务处制定的标准封面格式制作)2)原创性声明3)中文摘要(300字左右)、关键词4)外文摘要、关键词5)目次页(附件不统一编入)6)论文主体部分:引言(或绪论)、正文、结论7)参考文献8)致谢9)附录(对论文支持必要时)2.论文字数要求:理工类设计(论文)正文字数不少于1万字(不包括图纸、程序清单等),文科类论文正文字数不少于1.2万字。
齿轮齿条零件机械加工工艺规程及专用夹具设计
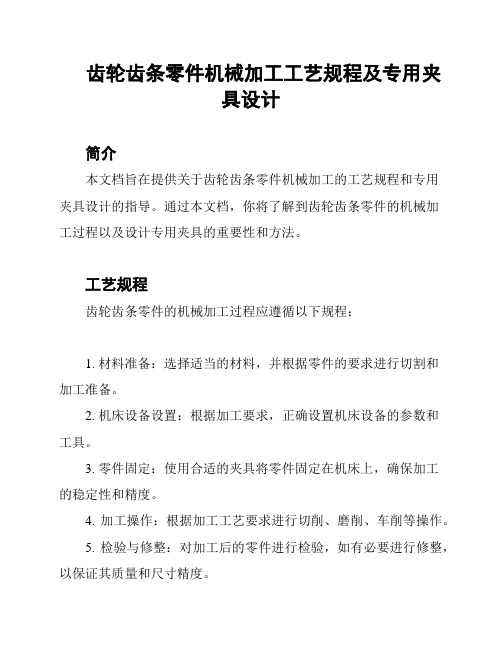
齿轮齿条零件机械加工工艺规程及专用夹具设计简介本文档旨在提供关于齿轮齿条零件机械加工的工艺规程和专用夹具设计的指导。
通过本文档,你将了解到齿轮齿条零件的机械加工过程以及设计专用夹具的重要性和方法。
工艺规程齿轮齿条零件的机械加工过程应遵循以下规程:1. 材料准备:选择适当的材料,并根据零件的要求进行切割和加工准备。
2. 机床设备设置:根据加工要求,正确设置机床设备的参数和工具。
3. 零件固定:使用合适的夹具将零件固定在机床上,确保加工的稳定性和精度。
4. 加工操作:根据加工工艺要求进行切削、磨削、车削等操作。
5. 检验与修整:对加工后的零件进行检验,如有必要进行修整,以保证其质量和尺寸精度。
6. 表面处理:根据需要,对零件进行表面处理,如镀铬、镀锌等。
专用夹具设计设计合适的专用夹具是确保齿轮齿条零件机械加工过程的关键。
下面是一些设计专用夹具的重要原则和方法:1. 夹具类型选择:根据零件的形状和加工要求,选择合适的夹具类型,如平面夹具、圆形夹具等。
2. 夹具定位:确保夹具能够准确地定位零件,以保证加工的精度和一致性。
3. 夹具固定:夹具的固定方式应牢固可靠,能够承受加工过程中的力和振动。
4. 夹具材料选择:选择适当的夹具材料,具有足够的强度和耐磨性,同时尽量避免对零件表面的损伤。
5. 夹具调试与测试:在使用之前,对夹具进行调试和测试,确保夹具的性能和可靠性。
总结本文档介绍了齿轮齿条零件机械加工的工艺规程和专用夹具设计的重要性。
通过遵循正确的工艺规程和合理设计专用夹具,可以提高加工效率和质量,确保零件的尺寸精度和稳定性。
齿轮夹具和齿轮加工工艺

VS
智能化技术还可以用于夹具的设计和 制造过程中,通过计算机辅助设计和 仿真技术,可以快速设计和优化夹具 系统,减少试制时间和成本。同时, 通过智能化检测技术,可以实现齿轮 加工质量的实时监控和反馈控制,进 一步提高加工精度和质量稳定性。
环境友好型加工方法的探索
随着环境保护意识的提高,齿轮加工行业也开始关注环境友好型加工方法的研究和应用。通过采用环保材料、优化加工工艺 和减少废弃物排放等措施,可以降低齿轮加工过程中的环境污染。
夹具的设计原则
01
保证工件定位准确、稳 定可靠,防止产生振动 和位移。
02
尽量减小切削力对工件 的影响,提高工件的加 工精度和表面质量。
03
方便夹具的安装、调整 和使用,提高生产效率 和降低成本。
04
夹具的结构应尽量简单、 紧凑、轻便,便于制造、 装配、维修和更换易损 件。
夹具的使用和维护
01
02
轮的加工精度和效率。
在汽车齿轮加工中,常用的夹具包括三 爪卡盘、四爪卡盘、数控机床夹具等。 这些夹具能够快速、准确地定位和夹紧 工件,减少加工误差,提高生产效率。
夹具的设计和使用需要充分考虑工件的 形状、尺寸、加工精度等要求,以及加 工设备的性能和加工环境的影响。合理 的夹具设计能够显著提高齿轮的加工质
磨齿加工中常用的夹具包括磨轮夹具、工件夹具等。这些 夹具通常采用高精度轴承、导轨和气动控制等技术,以确 保稳定的安装和精确的定位,从而获得高质量的磨齿效果 。
夹具在铣齿加工中的使用
铣齿加工是一种用于加工特殊形状和特殊用途齿轮的方法。在铣齿加工中,夹具 的作用是固定毛坯和引导铣刀进行切削。
铣齿加工中常用的夹具包括分度头、夹板、定位块等。这些夹具的设计需要考虑 到不同类型和尺寸的毛坯以及不同形状和尺寸的铣刀,以确保精确的定位和稳定 的切削过程。
齿轮轴零件的机械加工工艺规程及专用夹具设计

摘要本文是对齿轮轴零件加工应用及加工的工艺性分析,主要包括对零件图的分析、毛坯的选择、零件的装夹、工艺路线的制订、刀具的选择、切削用量的确定、加工工艺文件的填写。
选择正确的加工方法,设计合理的加工工艺过程。
此外还对支架零件的两道工序的加工设计了专用夹具.机床夹具的种类很多,其中,使用范围最广的通用夹具,规格尺寸多已标准化,并且有专业的工厂进行生产。
而广泛用于批量生产,专为齿轮轴工件加工工序服务的专用夹具,则需要各制造厂根据工件加工工艺自行设计制造。
本论文夹具设计的主要内容是设计专用夹具。
关键词齿轮轴,加工工艺,专用夹具,设计IAbstractThis paper is the analysis of the gear shaft parts processing technology application and processing, including the parts diagram analysis, the choice of blank, parts of the fixture, the formulation of the process route, tool selection, cutting, processing documents. Choose the correct processing methods, design the reasonable process. In addition, processing of two processes to support part of the design of special fixture.Many kinds of the machine tools fixture, the fixture, the most widely used, the size has been standardized, and there is a professional factory production. But widely uses in the volume production, specially the special fixture for gear shaft workpiece machining processes and services, to the factory according to the workpiece machining process to design and manufacture. The main content of this thesis is to design fixture design fixture.Keywords gear shaft, machining process, fixture, designI目录引言 (3)1 绪论 (4)1.1 机械加工工艺概述 (4)1.2机械加工工艺流程 (4)1.3夹具概述 (5)1.4机床夹具的功能 (5)1.5机床夹具的发展趋势 (6)1.5.1机床夹具的现状 (6)1.5.2 现代机床夹具的发展方向 (6)2工艺规程设计 (8)2.1 零件的分析 (8)2.1.1 零件的作用 (8)2.1.2 零件的工艺分析 (8)2.2 工艺规程设计 (9)2.2.1 确定毛坯的制造形式 (9)2.2.2 基面的选择 (9)2.2.3 制定工艺路线 (10)2.2.4 机械加工余量,工序尺寸及毛坯尺寸的确定 (13)2.2.5 确定切削用量 (13)3 基本工时 (27)I4 铣16槽夹具设计 (31)4.1研究原始质料 (35)4.2定位基准的选择 (35)4.3 切削力及夹紧分析计算 (35)4.4 误差分析与计算 (37)4.5 定向键与对刀装置设计 (38)4.6 夹具设计及操作的简要说明 (40)结论 (41)致谢 (42)参考文献 (43)II引言机械制造技术基础毕业设计是在学完了机械制造技术基础后的教学环节,它一方面要求学生通过设计能获得综合运用过去所学过的全部课程进行工艺及结构设计的基本能力,另外,也为以后做好毕业设计进行一次综合训练和准备。
齿轮轴机械加工工艺及夹具设计

齿轮轴机械加工工艺及夹具设计背景知识(一)齿轮轴的作用齿轮轴零件的主要作用是支撑回转零件、实现回转运动并传递转矩和动力。
齿轮轴零件是将齿轮部分和轴做成一体无需键配合的一种常见机械零件。
齿轮轴具备传动效率高、结构紧凑和使用寿命长等一系列优点,是通用机械特别是工程机械传动中的重要零件之一。
齿轮轴的工作能力一般取决于轴的强度和刚度,转速高时还取决于轴的振动稳定性。
(二)机械制造工艺相关知识A.基本概念(1)生产过程是指从原材料到产品出厂的全部劳动过程。
(2)机械加工工艺过程是机械产品生产过程的一部分,是对零件采用机械加工的方法直接改变毛坯的形状、尺寸、和表面质量等,使之成为合格零件的过程。
(3)工序一个(或一组)工人在一个工作地对一个(或同时对几个)工件连续完成的那一部分工艺过程。
(4)安装如果在一个工序中需要对工件进行几次装夹,则每次装夹下完成的那一部分内容称为一个安装。
(5)工位在工件的一次装夹后,工件(或装配单元)与夹具或设备的可动部分一起相对刀具或设备的固定部分所占据的每一个位置称为工位。
(6)工步在加工表面(或装配时的连接表面)和加工(或装配)工具不变的情况下,所连续完成的那一部分工序称为工步。
(7)走刀切削刀具在加工表面上切削一次所完成的工步内容,称为一次走刀。
(8)生产纲领是在计划期内生产的产品产量和进度计划。
(9)生产类型是指企业(或车间、工段、班组、工作地)生产专业化的程度分类。
一般分为单件生产、成批生产和大批量生产三种类型。
B.机械加工工艺规程(1)机械加工工艺规程有:机械加工工艺过程卡片、机械加工工序卡片、标准零件或典型零件工艺过程卡片、单轴自动车床调整卡片、多轴自动车床调整卡片、机械加工工序操作指导卡片、检验卡片等。
(2)制定工艺规程的基本要求是:在保证产品质量的前提下,能尽量提高生产率和降低成本,并充分利用现有生产条件,保证工人具有良好而安全的劳动条件。
(3)制定工艺规程的步骤:①收集和熟悉制定工艺规程的有关资料图样,进行零件的结构工艺性分析;②确定毛坯的类型及制造方法;③选择定位基准;④拟定工艺路线;⑤确定各工序的工序余量、工序尺寸及其公差;⑥确定各工序的设备、刀具、夹具、量具和辅助工具;⑦确定各工序的切削用量及时间定额;⑧确定主要工序的技术要求及检验方法;⑨进行技术经济分析;⑩编制工艺文件。
齿轮夹具和齿轮加工工艺

3、选择合适的刀具,根据齿轮精度要求,选择精度合适的刀具。 4、调整机床 必要时对机床有关部位进行调整,如导轨、轴承间隙等。使其
牌良好的工件状态。
5、正确安装工件 工件安装时各接触表面不能沾有铁屑,杂物和油污等。并 防止工件装夹歪斜。
常用插齿夹具结构如图所示:
工作尺寸小于40时。心轴 采用整体结构。大于40时 采用镶套结构。心轴工作尺寸
的选取与滚齿夹具相同。与工
作台连接处锥度为1:10。外 径及锥面径向跳动不大于
0.005。表面粗糙度不大于
0.4。心轴必须经过淬硬处理和磨削,螺纹部位不淬硬。 垫圈两平面要平整,两端面平行度误差不大于0.005。
加工的影响和碰伤表面。
(5)合理安排热处理工序 在机械加工以前进行退火、正火处理,在粗 加工后进行调质或时效处理。对于要求渗碳淬火或高频淬火的。
(6)确定各工序的具体内容 包括选择机床、夹具、刀具和量具,确定 工序余量工序尺寸,确定切削余量时间定额等。
3、齿轮加工工艺实例
现介绍一双联齿轮的工艺过程,其尺寸及技术要求如 图6-4所示。
第二节 齿轮加工工艺基本知识
一个零件往往需要经过几种机床加工,齿轮 加工也是这样。如加工轴齿轮,需要经过车削、 铣削、磨削、齿形加工、钳加工等工序。而这些 加工工序是彼此联系的,因此加工时必须全面考 虑,具体分析零件的特点及技术要求,根据产品 的质量、生产批量、经济性,以及设备条件等情 况选择适当的加工方法,定制出经济的、先进的、 合理的工艺过程。
6、注意刀具行程位置 如插齿加工多联齿轮中小齿轮时,要认真调整刀具行 程位置。
齿轮轴的加工工艺流程及夹具设计

齿轮轴的加工工艺流程及夹具设计下载提示:该文档是本店铺精心编制而成的,希望大家下载后,能够帮助大家解决实际问题。
文档下载后可定制修改,请根据实际需要进行调整和使用,谢谢!本店铺为大家提供各种类型的实用资料,如教育随笔、日记赏析、句子摘抄、古诗大全、经典美文、话题作文、工作总结、词语解析、文案摘录、其他资料等等,想了解不同资料格式和写法,敬请关注!Download tips: This document is carefully compiled by this editor. I hope that after you download it, it can help you solve practical problems. The document can be customized and modified after downloading, please adjust and use it according to actual needs, thank you! In addition, this shop provides you with various types of practical materials, such as educational essays, diary appreciation, sentence excerpts, ancient poems, classic articles, topic composition, work summary, word parsing, copy excerpts, other materials and so on, want to know different data formats and writing methods, please pay attention!1. 引言齿轮轴是机械传动系统中的重要部件,其加工工艺及夹具设计对于产品质量和生产效率具有重要意义。
齿轮类零件加工工艺分析与夹具设计论文

毕业设计论文齿轮类零件加工工艺分析与夹具设计目录摘要4第一章齿轮类零件加工工艺规程编制概述51.1工艺编制的总体步骤5第二章对齿轮类零件的加工工艺编制与分析62.1分析齿轮类零件的技术要求62.2明确毛坯尺寸82.3拟定工艺路线82.4设计工序容102.5填写工艺文件10第三章对齿轮类零件加工工艺进行合理性分析11第四章夹具设计的要求114.1 了解夹具设计的总体要求11第五章夹具设计的特点125.1确定夹具的类型125.2钻模的主要类型12第六章工件夹紧计算与选择136.1工件的夹紧136.2 夹紧力的选择136.3夹紧力的计算与精度分析14 第七章夹具的结构分析与设计167.1夹具的夹紧和定位167.2夹具的导向17第八章夹具的总体分析17第九章致18摘要齿轮类零件是典型零件之一,它在机械主要用于传动,齿轮类零件主要有齿轮.齿轮轴,涡轮涡杆,在机械领域运用很广泛。
按传动形式分圆柱类齿轮、锥齿轮、齿条等。
按齿形状分:齿轮、齿、字齿等。
按制作方法分:铸造齿轮、烧结齿轮、轧制齿轮等。
我以齿轮加工工艺编制分析齿轮的加工要求,在生产实际中阐述齿轮的工艺过程,与工艺的合理性。
夹具在机械加工中有举足轻重的作用,好的夹具才是保障零件加工的方法。
我从夹具的分析、设计、计算、使用方面概述夹具的用途。
按专业化程度可分为通用夹具、专用夹具、可调夹具、组合夹具、成组夹具、标准夹具、随行夹具、组合机床夹具等。
我这次设计的是盖板式钻夹具。
这是一种专用夹具,专为一工件的一道工序而设计的夹具。
关键词:齿轮、夹具、工艺、设计1.1工艺编制的总体步骤1.分析零件的结构和技术要求(1)分析图样资料①加工工艺表面的尺寸精度和形状精度②各加工表面之间以与加工表面和不加工表面之间的位置精度③加工表面的粗糙度与表面的其他要求④热处理与其他要求(2)零件的结构工艺分析。
零件的结构工艺是指所设计的零件在满足性能的要求下,制造的经济性和可行性,包括整个工艺过程,有毛坯制作、切削加工、装配与维修等工艺。
轴齿轮的机械加工工艺和工装设计设计

轴齿轮的机械加工工艺和工装设计设计轴齿轮的机械加工工艺和工装设计是确保齿轮的精度和性能的关键环节。
下面将详细介绍轴齿轮的机械加工工艺和工装设计的设计过程。
一、轴齿轮的机械加工工艺1.粗加工阶段在粗加工阶段,主要任务是切削掉多余的材料,使齿轮的基本形状和尺寸得以形成。
这个阶段通常采用铣削或车削的方法,根据设计要求和材料特性选择合适的刀具和切削参数。
2.半精加工阶段半精加工阶段是进一步细化齿轮的形状和尺寸,去除粗加工后留下的毛刺和加工痕迹。
这个阶段仍然采用铣削或车削的方法,但使用的刀具更加精细,切削参数也经过优化。
3.精加工阶段在精加工阶段,目标是提高齿轮的精度和质量。
这个阶段通常采用磨削的方法,使用磨床和精细的砂轮来达到高精度的表面粗糙度和平行度。
4.齿轮热处理阶段齿轮热处理是将齿轮加热到一定温度,然后进行淬火、回火等操作,以提高材料的硬度和耐磨性。
这个阶段对齿轮的性能和质量有重要影响,需要选择合适的热处理工艺并进行严格控制。
二、轴齿轮的工装设计1.夹具设计夹具是用于固定工件的工具,确保工件在加工过程中保持稳定。
针对轴齿轮的加工,需要设计专门的夹具来固定齿轮毛坯,确保齿轮在加工过程中不会发生移动或振动。
夹具设计需要考虑夹具的刚度、精度和可靠性等因素。
2.刀具设计刀具是用于切削材料的工具,其质量和性能对加工精度和效率有重要影响。
针对轴齿轮的加工,需要设计合适的刀具来满足切削要求。
刀具设计需要考虑刀具的材料、几何形状和切削参数等因素。
3.量具设计量具是用于测量工件尺寸和形状的工具。
为了确保轴齿轮的加工精度和质量,需要设计合适的量具来进行测量。
量具设计需要考虑量具的精度、测量范围和使用方便性等因素。
三、设计优化及改进建议1.优化加工工艺流程通过对现有加工工艺流程进行分析,可以发现存在的问题和瓶颈。
为了提高生产效率和降低成本,可以对加工工艺流程进行优化,例如减少加工工序、采用更高效的切削参数等。
2.引入先进的加工设备和工艺技术随着科技的不断进步,出现了许多先进的加工设备和工艺技术,可以显著提高加工效率和精度。
齿轮零件机械加工工艺规程及夹具设计

齿轮零件机械加工工艺规程及夹具设计一、引言齿轮作为机械传动中常见的零件,其在机械系统中的作用不可替代。
作为机械制造行业的一部分,齿轮加工工艺一直是制造企业关注的重点之一。
齿轮加工的质量直接影响到机械系统的性能和使用寿命。
本文主要介绍齿轮零件的机械加工工艺规程及夹具的设计,旨在提高机械加工制造企业的齿轮工艺水平,提高加工效率和质量。
二、齿轮零件机械加工工艺规程2.1、数控加工流程传统齿轮的加工方式主要是使用车床和铣床,依靠技术工人的经验和技术水平加工出质量较高的齿轮。
随着数控技术的发展,数控机床的应用逐渐普及。
数控机床具有高精度、高效率、高重复性等优点,能够满足齿轮加工的需求。
流程如下:(1)编写机床程序。
根据齿轮的尺寸、牙数等参数编写机床程序。
(2)安装夹具。
根据机床程序要求,将齿轮安装在夹具上,保证齿轮的位置和姿态。
(3)调整刀具。
根据齿轮的尺寸和形状,调整刀具的参数,使其能够精确的加工出齿轮的轮廓。
(4)加工制造。
启动机床程序,机床按照编写的程序进行自动加工。
2.2、装夹准确度齿轮的装夹是齿轮加工的基础,装夹准确度直接影响齿轮加工的精度和质量。
齿轮的装夹主要分为以下几种方式:(1)间隙装夹。
又称“二点定心法”,即通过安装工制造的误差对元件进行局部加紧或释紧,使得元件产生相对位移,进而实现定位目的。
(2)单点定位装夹。
在固定件上加工出一道槽,满足被加工零件的定位要求。
利用这道槽来和加工零件进行定位。
(3)面定位装夹。
利用平面的互相接触来实现装夹定位。
(4)对心装夹。
利用装夹机构使加工夹具中心轴线和被加工齿轮的中心轴对齐。
2.3、刀具选择齿轮的加工需利用专门的刀具来完成,通常采用带有切削刃的齿轮铣刀或齿轮加工刀片,刀具的选择应根据加工材料、齿轮的牙数和齿形以及齿轮加工的精度要求等一系列因素进行选择。
在使用刀具进行齿轮加工时,需要根据加工参数等一系列因素进行合理的切削力选择,以保证加工质量和刀具的寿命。
中间轴齿轮的加工工艺及及夹具设计
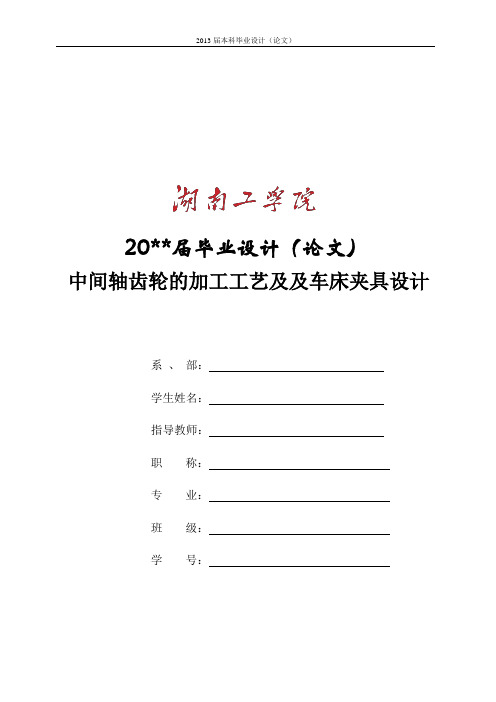
20**届毕业设计(论文)中间轴齿轮的加工工艺及及车床夹具设计系、部:学生姓名:指导教师:职称:专业:班级:学号:20**年5月20** 届毕业设计(论文)课题任务书系:机械工程系专业:机械制造与自动化摘要本次设计内容涉及了机械制造工艺及机床夹具设计、金属切削机床、公差配合与测量等多方面的知识。
中间轴齿轮的加工工艺规程及其车床的夹具设计是包括零件加工的工艺设计、工序设计以及专用夹具的设计三部分。
在工艺设计中要首先对零件进行分析,了解零件的工艺再设计出毛坯的结构,并选择好零件的加工基准,设计出零件的工艺路线;接着对零件各个工步的工序进行尺寸计算,关键是决定出各个工序的工艺装备及切削用量;然后进行专用夹具的设计,选择设计出夹具的各个组成部件,如定位元件、夹紧元件、引导元件、夹具体与机床的连接部件以及其它部件;计算出夹具定位时产生的定位误差,分析夹具结构的合理性与不足之处,并在以后设计中注意改进。
关键词:工艺;工序;切削用量;夹紧;定位;误差AbstractThis design content has involved the machine manufacture craft and the engine bed jig design, the metal-cutting machine tool, the common difference coordination and the survey and so on the various knowledge.The reduction gear box body components technological process and its the processing hole jig design is includes the components processing the technological design, the working procedure design as well as the unit clamp design three parts. Must first carry on the analysis in the technological design to the components, understood the components the craft redesigns the semi finished materials the structure, and chooses the good components the processing datum, designs the components the craft route; After that is carrying on the size computation to a components each labor step of working procedure, the key is decides each working procedure the craft equipment and the cutting specifications; Then carries on the unit clamp the design, the choice designs the jig each composition part, like locates the part, clamps the part, guides the part, to clamp concrete and the engine bed connection part as well as other parts; Position error which calculates the jig locates when produces, analyzes the jig structure the rationality and the deficiency, and will design in later pays attention to the improvement.Keywords: The craft;the working procedure;the cutting specifications;clamp;the localization;the error目录1.设计任务 (4)2.零件图分析 (5)2.1、零件的功用 (5)2.2、零件功用分析 (5)3.确定毛坯 (6)3.1、确定毛坯制造方法 (6)3.2、确定总余量 (6)3.3、绘制毛坯图 (7)4.制定零件工艺规程 (8)4.1、选择表面加工方法 (8)4.2、选择定位基准 (12)4.3、拟定零件加工工艺路线 (12)4.4、选择各工序所用机床、夹具、刀具、量具和辅具 (13)4.5、填写工艺过程卡片 (16)4.6、机械加工工序设计 (17)4.7、机械加工工序设计(续) (21)5.夹具设计 (30)5.1、功能分析与夹具总体结构设计 (30)5.2、夹具设计计算 (30)5.3、夹具制造与操作说明 (32)6.小结 (33)参考文献 (34)致谢 (35)1、设计任务设计"中间轴齿轮"零件(图1)机械加工工艺规程及某一重要工序的夹具。
齿轮加工工艺及夹具设计

精心整理一、设计题目(附图)齿类零件机械加工工艺规程制订及第_____工序工艺装备设计二、设计条件:1、零件图2、生产批量:中批量生产(4000件)三、设计内容:㈠零件图分析:1、零件图工艺性分析(结构工艺性及条件分析);2、绘制零件图。
㈡毛坯选择㈢机械加工工艺路线确定:1、加工方案分析及确定2、基准的选择3、绘制加工工艺流程图13、基准1一、12(1内孔:¢30.5的内孔Ra1.6表面粗糙度是Ra1.6上述表面的加工难度不大,工艺性良好。
(2)位置精度分析该零件位置精度较高,工艺性良好。
二、毛坯确定1、毛坯类型确定零件结构简单,工作载荷不大,且为中批生产,查表取锻件。
2、毛坯结构、尺寸和精度确定简化零件结构细节,由于零件为中批生产,故毛坯精度取普通级,CT9级。
由表查得工件顶、侧面余量为2m.。
根据这些数据,绘出毛坯——零件合图。
如图所示:三、工艺路线拟订1、主要表面加工方案确定¢40Ra1.6粗车(IT11,Ra12.5)——半精车(IT9,Ra6.3)——精车(IT7,Ra1.6)¢30.5孔Ra1.6粗车(IT11,Ra12.5)——半精车(IT9,Ra6.3)——精车(IT7,Ra1.6)2、加工阶段划分四、工序尺寸计算4.切削速度计算:因为yvxvpm faTCvv=查表Cv=8.1x v=0y v=0.55 m=0.125Zv=0.25所以v=3.78m/min机床主轴转速n=76r/min然后选用机床具有的与计算转速接近的额定的转速作为实际转速5.机床主电机的功率核算粗加工阶段要切除的余量大,加工时需要较大的切削功率,所以,还要对机床的功率进行核算轴向力计算FFFF oy Z F f C d K =查表得420F C = 1.0F Z =0.8Fy=1FK=计算的F=1704N扭矩计算:MMMM Oy Z M fC d K =0.206M C =2MZ=0.8Fy=1MK=计算的M=44N.m 功率计算0.3530M oM Vkw P d ∙== 已知:Z525机床主电机功率2.2kw ,可以肯定,完全可以满足加工要求。
- 1、下载文档前请自行甄别文档内容的完整性,平台不提供额外的编辑、内容补充、找答案等附加服务。
- 2、"仅部分预览"的文档,不可在线预览部分如存在完整性等问题,可反馈申请退款(可完整预览的文档不适用该条件!)。
- 3、如文档侵犯您的权益,请联系客服反馈,我们会尽快为您处理(人工客服工作时间:9:00-18:30)。
1 零件的工艺分析及生产类型的确定1. 1 零件的作用题目所给定的是设计宽度为40mm的中间轴齿轮“零件”,其功用是传递动力和改变输出轴运动方向。
1.2 零件的工艺分析及零件的生产类型本零件为回转体零件,其最主要加工面是φ62H7孔和齿面,但基准孔φ62H7要求内孔表面粗糙度Ra值为0.8,且两者有较高的同轴度要求其公差为φ0.04,是加工工艺需要重点考虑的问题。
其次两轮毂端面由于装配要求,对φ62H7孔有端面跳动要求其公差为φ0.05。
最后,两齿圈端面在滚齿时要作为定位基准使用,故对φ62H7孔也有端面跳动要求。
依据题目知:年产50000件,达到了批量生产的水平。
2 选择毛坯,确定毛坯尺寸,设计毛坯图2.1 选择毛坯该零件材料为20Cr钢。
本零件的主要功用是传递动力,其工作时需承受较大的冲击载荷,要求有较高的强度和韧性,故毛坯应选择锻件,以使金属纤维尽量不被切断保证零件工作可靠。
又由于年产量为50000件,达到了批量生产的水平,且零件形状较简单,尺寸也不大,故应采用模锻。
这从提高生产率、保证加工精度上考虑,也是应该的。
2.2 确定毛坯的总余量查机械制造技术基础课程设计指导书由表2-7查得a=6,b=5,c=9。
确定垂直方向上总余量为2×0.5a=2×0.5×6=6mm。
水平方向上总余量为2×0.5b=2×0.5×5=5mm。
内孔总余量为2×0.5c=2×0.5×9=9mm。
2.3 确定毛坯尺寸上面得出加工总余量适用于机械加工粗糙度R a≥1.6μm,除φ62H7孔为R a=0.8μm以外,其余各加工表面为R a≥1.6μm,因此这些表面的毛坯尺寸只需要将零件的尺寸加上总余量即可,外圆尺寸为:130+6=136mm;锻造内孔尺寸:62-9=53mm;两个端面间间距为:40+5=45mm:齿宽方向尺寸为:20+5=25mm;3. 制定零件工艺规程3.1 选择定位基准1)粗基准选择重要考虑装夹方便、可靠,选一大端面和外圆作为定位粗基准。
2)精基准选择齿轮的设计基准是φ62H7孔,根据基准重合原则,并同时考虑统一精基准原则,选φ62H7孔作为主要定位精基准。
考虑定位稳定可靠,选一大端面作为第二定位精基准。
在磨孔工序中,为保证齿面与孔的同轴度,选齿面作为定位基准。
在加工环槽工序中,为装夹方便,选外圆表面作为定位基准。
3.2 选择表面加工方法1)φ62H7孔:①生产批量较大,应采用高效加工方法;②零件热处理会引起较大变形,为保证φ62H7孔的精度及齿面对φ62H7孔的同轴度,热处理后需对该孔再进行加工。
故确定热加工前采用扩孔和拉孔的加工方法,热后采用磨孔方法。
2)齿面根据精度要求,并考虑生产批量较大,故采用滚齿-剃齿的加工方法。
3)大小端面采用粗车-半精车-精车加工方法。
4)环槽采用车削方法。
3.3零件加工工艺路线1)扩孔(立式钻床,气动三爪卡盘);2)粗车外圆,粗车一端大、小端面,一端内孔倒角(普通车床,气动可胀心轴);3)半精车外圆,粗车另一端大、小端面,另一端内孔倒角(普通车床,气动可胀心轴);4)拉孔(卧式拉床,拉孔夹具);5)精车外圆,精车一端大、小端面,一端外圆倒角(普通车床,气动可胀心轴);6)精车另一端大、小端面,另一端外圆倒角(普通车床,气动可胀心轴);7)车槽(普通车床,气动三爪卡盘);8)滚齿(滚齿机,滚齿夹具);9)一端齿圈倒角(倒角机,倒角夹具);10)另一端齿圈倒角(倒角机,倒角夹具);11)检验;12)热处理;(淬火+低温回火)13)磨孔(内圆磨床,节圆卡盘);14)最终检验。
该工序采用分散原则,各工序工作相对简单考虑到该零件生产批量较大,工序分散可简化调整工作,易于保证加工质量,且采用气动夹具,可提高加工效率。
4 工序设计4.1 加工余量及工序尺寸的确定(1)外圆加工由零件加工工艺路线得外圆加工由粗车外圆—半精车外圆—精车外圆三道工序。
查文献[1]表3.2-2和查文献[2] 表 5-29 得粗车外圆加工精度为IT11~IT13,取IT12级精度,半精车外圆的加工精度为IT8~IT10,取IT9级精度,精车外圆的加工精度为IT7~IT8,取IT7级精度。
工序名称 工序余量 经济精度 工序尺寸粗车 3.5 h12 φ132.504.0-半精车 1.8 h9 φ130.701.0-精车 0.7 h7 φ130015.0-(2)端面的加工由零件加工工艺路线得端面加工由粗车端面—半精车端面—精车端面三道工序。
查文献[1]表 3.2-21和查文献[2]表5-29 得粗车端面加工精度为 IT11~IT13,取IT12级精度,半精车外圆的加工精度为IT8~IT10,取IT9级精度,精车外圆的加工精度为IT7~IT8,满足零件图要求。
① 大端面各工序尺寸为:工序名称 工序余量 经济精度 工序尺寸粗车 3.4 H12 41.63.00+半精车 1.0 H9 40.6074.00+精车 0.6 40±0.5② 小端面各工序尺寸为:工序名称 工序余量 经济精度 工序尺寸粗车 3 H112 22021.00+半精车 1.2 H9 20.8052.00+精车 0.8 20±0.2(3)内孔加工根据零件加工工艺路线得内孔加工由扩孔—拉孔—磨孔三道工序。
查文献[2] 表5-44 得磨孔加工余量0.5mm 。
查文献[1]表3.2-12得拉孔加工余量为1mm 。
根据内孔总余量9mm ,得出扩孔加工余量9+1+0.5=10.5mm 。
查文献[2]表5-29 得粗扩经济精度为IT12~IT13 取IT12,精拉经济精度为IT7~IT9,取IT7,查文献[1] 表4.1-9 得磨孔精度为IT7,满足零件图要求。
工序名称 工序余量 经济精度 工序尺寸扩孔 9 H12 φ60.53.00+拉孔 1 H8 φ61.5046.00+磨孔 0.5 φ62009.0021.0+-4.2齿形加工根据齿面粗糙度以及精度等级,选择滚齿与滚齿加工方法,查文献[2]表5-18 得滚齿加工精度为IT8,剃齿加工精度为IT7。
加工时先进行滚齿,然后在进行剃齿,保证各个尺寸要求。
2.4.1 切削用量的确定1)外圆φ130的加工本工序采用粗车—半精车—精车的加工方法,选用硬质合金外圆车刀左偏刀,刀片材料YT15,K r =90°和弯头车刀K r =45°精车用弯头刀K r =45°、刀尖圆弧半径0.5mm ,刀杆尺寸16×25。
查文献[4] 表3-13 得粗车外圆的进给量f=0.71mm/r 。
查文献[4] 表3-14 得半精车外圆进给量f=0.36mm/r 。
查文献[4] 表3-15 得精车外圆进给量f=0.23mm/r 。
查文献[4] 表3-19 取粗车切削速度V=1.5m/s ,半精车切削速度V=2m/s ,精车切削速度V=2.5m/s 。
根据加工余量可得粗车被吃刀量p a =2.25mm,半精车被吃刀量p a =0.9mm ,精车被吃刀量p a =0.35mm 。
粗车主轴转速:d v n π100060⨯==min /32.216132.514.35.1100060r =⨯⨯⨯. 查文献[4]附表5-56得CA6140主轴转速n=200r/min.则实际切削速度:s m dn v /39.11000602005.13214.3601000=⨯⨯⨯=⨯=π. 半精车主轴转速:d v n π100060⨯==min /40.2927.13014.32100060r =⨯⨯⨯. 查文献[4]附表5-56得CA6140主轴转速n=320r/min.则实际切削速度:s m dn v /19.21000603207.13014.3601000=⨯⨯⨯=⨯=π. 精车主轴转速:d v n π100060⨯==min /47.36713014.35.2100060r =⨯⨯⨯ 查文献[4] 附表5-56 得CA6140主轴转速n=400r/min.则实际切削速度:s m dn v /72.210006040013014.3601000=⨯⨯⨯=⨯=π 工时计算:粗车: mm k a l r p2)32(tan 1=-+= mm l 32= mm l 43=m i n 24.020071.043225321=⨯+++=+++==i fn l l l l i fn L T J 半精车: mm k a l r p2)32(tan 1=-+= mm l 32= mm l 43=m i n 30.032036.043225321=⨯+++=+++==i fn l l l l i fn L T J 精车: mm k a l r p35.2)32(tan 1=-+= mm l 32= mm l 43=min 37.04000.234335.225321=⨯+++=+++==i fn l l l l i fn L T J 2)端面的加工本工序也采用粗车—半精车—精车的加工方法,大小端面采用硬质合金左偏刀K r =90°和弯头车刀K r =45°① 大端面的加工根据加工余量可知,粗车被吃刀量p a =2.2mm,半精车被吃刀量p a =0.5mm 。
精车被吃刀量p a =0.3mm查文献[4] 表3-13 得粗车端面进给量f=0.73mm/r.查表3-14 半精车端面进给量f=0.30mm/r. 查表3-15 精车端面进给量f=0.20mm/r.初取端面粗车切削速度V=1.6m/s,半精车切削速度V=2.2m/s. 精车切削速度V=2.8m/s粗车主轴转速:d v n π100060⨯==min /64.4077514.36.1100060r =⨯⨯⨯. 查文献[4] 附表5-56 得机床主轴转速n=400r/min 。
则实际切削速度:s m dn v /57.11000604007514.3601000=⨯⨯⨯=⨯=π. 半精车主轴转速:d v n π100060⨯==min /51.5607514.32.2100060r =⨯⨯⨯. 查文献[4] 附表5-56 得机床主轴转速n=560r/min 。
则实际切削速度:s m dnv /2.21000605607514.3601000=⨯⨯⨯=⨯=π. 精车主轴转速:dv n π100060⨯==min /38.7137514.38.2100060r =⨯⨯⨯. 查文献[4] 附表5-56 得机床主轴转速n=760r/min 。
则实际切削速度:s m dn v /00.31000607607514.3601000=⨯⨯⨯=⨯=π. 工时计算:粗车: mm k a l r p 2)32(tan 1=-+=mm l 32= mm l 43= mm l l l d d L 25.1643225.607523211=+++-=+++-= m i n 05.0140073.025.16=⨯⨯==i fn L T j 半精车: mm k a l r p2)32(tan 1=-+= mm l 32= mm l 43=mm l l l d d L 75.1543225.617523211=+++-=+++-= min 09.015603.075.15=⨯⨯==i fn L T j 精车: mm k a l r p 3.2)32(tan 1=-+=mm l 32= mm l 43= mm l l l d d L 8.15433.22627523211=+++-=+++-= min 1.017602.08.15=⨯⨯==i fn L T j ② 小端面的加工根据加工余量可知,粗车被吃刀量p a =1.3mm,半精车被吃刀量p a =1.2mm ,精车被吃刀量p a =0.8mm.查文献[4]表3-13 得粗车端面进给量f=0.94mm/r.查文献[4]表3-14 半精车端面进给量f=0.35mm/r. 查文献[4]表3-15 精车端面进给量f=0.24mm/r.初取端面粗车切削速度V=1.5m/s,半精车切削速度V=2.0m/s. 精车切削速度V=2.5m/s.粗车主轴转速:dv n π100060⨯==min /50.22013014.35.1100060r =⨯⨯⨯. 查文献[4] 附表4-3-1 得机床主轴转速n=200r/min 。