黄金矿山生产工艺
黄金冶炼工艺流程

黄金冶炼工艺流程我国黄金资源储量丰富,分布较广,黄金冶炼方法很多。
其中包括常规的冶炼方法和新技术。
冶炼方法、工艺的改进,促进了我国黄金工业的发展。
目前我国黄金产量居世界第五位,成为产金大国之一。
黄金的冶炼过程一般为:预处理、浸取、回收、精炼。
1.黄金冶炼工艺方法分类1.1矿石的预处理方法分为:焙烧法、化学氧化法、微生物氧化法、其他预处理方法。
1.2浸取方法浸取分为物理方法、化学方法两大类。
其中,物理方法又分为混汞法、浮选法、重选法。
化学方法分为氰化法(又分:氰化助浸工艺、堆浸工艺)与非氰化法(又分:硫脲法、硫代硫酸盐法、多硫化物法、氯化法、石硫合剂法、硫氰酸盐法、溴化法、碘化法、其他无氰提金法)。
1.3溶解金的回收方法分为:锌置换沉淀法、炭吸附法、离子交换法、其它回收方法。
1.4精炼方法主要有全湿法,它包括电解法、王水法、液氯法、氯化法、还原法火法、湿法一火法联合法。
2.矿石的预处理随着金矿的大规模开采,易浸的金矿资源日渐枯竭,难处理金矿将成为今后黄金工业的主要资源。
在我国已探明的黄金储量中,有30%为难处理金矿。
因此,难处理金矿的预处理方法成为当前黄金工业提金的关键问题。
难处理金矿,通常又称为难浸金矿或顽固金矿,它是指即使经过细磨也不能用常规的氰化法有效地浸出大部分金的矿石。
因此,通常所说的难处理金矿是对氰化法而言的。
2.1焙烧法焙烧是将砷、锑硫化物分解,使金粒暴露出来,使含碳物质失去活性。
它是处理难浸金矿最经典的方法之一。
焙烧法的优点是工艺简单,操作简便,适用性强,缺点是环境污染严重。
含金砷黄铁矿一黄铁矿矿石中加石灰石焙烧,可控制砷和硫的污染;加碱焙烧可以有效固定S、As等有毒物质。
美国发明的在富氧气氛中氧化焙烧并添加铁化合物使砷等杂质进入非挥发性砷酸盐中,国内研发的用回转窑焙烧脱砷法,哈萨克斯坦研发的用真空脱砷法以及硫化挥发法,微波照射预处理法,俄罗斯研发的球团法等都能有效处理含砷难浸金矿石。
黄金生产工艺流程

黄金生产工艺流程一、黄金的开采黄金的开采是指从地下或水中提取黄金矿石的过程。
通常,这个过程包括以下几个步骤:1. 地质勘探:通过地质调查、地球物理勘探等手段,确定有潜在的黄金矿床存在的区域。
2. 矿床评估:对发现的潜在矿床进行详细评估,确定其规模、品位等信息。
3. 岩土工程:进行工程勘察和设计,确定采矿方案、选址等。
4. 开挖:使用爆破、机械开挖等方法将矿石从地下或水中取出。
5. 运输:将采出的矿石运往选矿厂进行后续处理。
二、黄金的选冶黄金选冶是指对采集到的原始黄金进行加工和提纯,以获得高纯度和高品质的黄金。
通常,这个过程包括以下几个步骤:1. 破碎:将原始黄金通过粗碎机等设备进行粉碎。
2. 磨细:使用球磨机等设备将粉碎后的原始黄金进一步磨细。
3. 浮选:使用浮选机等设备将黄金与其他杂质分离。
4. 氰化提取:将黄金矿石放入氰化物溶液中,使其中的黄金溶解并通过吸附剂等进行回收。
5. 精炼:对提取出的黄金进行电解、火法等方法进行精炼,以获得高纯度的黄金。
三、黄金的铸造黄金铸造是指将精炼后的黄金进行加工和成型。
通常,这个过程包括以下几个步骤:1. 铸模:根据需要制作出相应形状的铸模。
2. 熔化:将精炼后的黄金放入高温熔炉中进行熔化。
3. 浇注:将熔化后的黄金倒入铸模中进行浇注。
4. 冷却:等待浇注后的黄金冷却成型。
5. 打磨和抛光:对成型后的黄金进行打磨和抛光,以获得更好的表面光泽和质感。
四、总结以上就是完整的黄金生产工艺流程。
从开采到选冶再到铸造,每个环节都需要精密的设备和专业的技术支持。
黄金生产工艺的完善和提高,不仅有助于提高黄金的品质和产量,也有助于保护环境和促进可持续发展。
金矿工艺流程
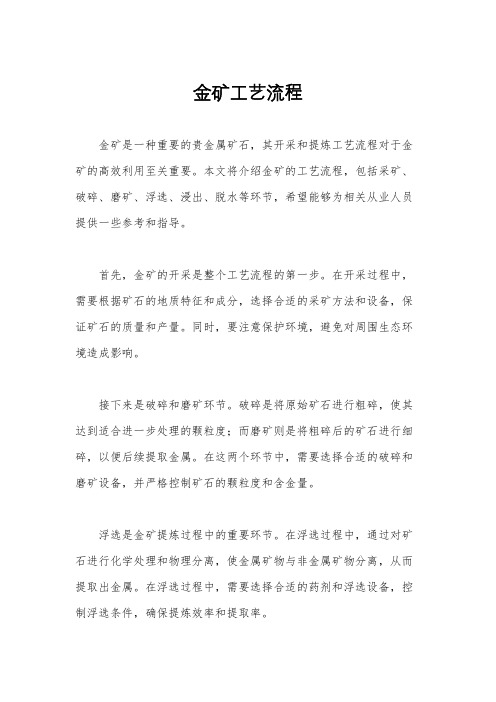
金矿工艺流程金矿是一种重要的贵金属矿石,其开采和提炼工艺流程对于金矿的高效利用至关重要。
本文将介绍金矿的工艺流程,包括采矿、破碎、磨矿、浮选、浸出、脱水等环节,希望能够为相关从业人员提供一些参考和指导。
首先,金矿的开采是整个工艺流程的第一步。
在开采过程中,需要根据矿石的地质特征和成分,选择合适的采矿方法和设备,保证矿石的质量和产量。
同时,要注意保护环境,避免对周围生态环境造成影响。
接下来是破碎和磨矿环节。
破碎是将原始矿石进行粗碎,使其达到适合进一步处理的颗粒度;而磨矿则是将粗碎后的矿石进行细碎,以便后续提取金属。
在这两个环节中,需要选择合适的破碎和磨矿设备,并严格控制矿石的颗粒度和含金量。
浮选是金矿提炼过程中的重要环节。
在浮选过程中,通过对矿石进行化学处理和物理分离,使金属矿物与非金属矿物分离,从而提取出金属。
在浮选过程中,需要选择合适的药剂和浮选设备,控制浮选条件,确保提炼效率和提取率。
浸出是金矿提炼的关键环节之一。
在浸出过程中,通过化学反应将金属从矿石中提取出来,得到金属的浸出液。
在浸出过程中,需要选择合适的浸出剂和浸出设备,控制浸出条件,确保金属的高效提取。
最后是脱水环节。
在脱水过程中,将浸出液中的金属进行分离和提纯,得到最终的金属产品。
在脱水过程中,需要选择合适的脱水设备,控制脱水条件,确保金属产品的质量和纯度。
总的来说,金矿工艺流程涉及到采矿、破碎、磨矿、浮选、浸出、脱水等多个环节,每个环节都有其特定的工艺要求和操作技巧。
只有严格按照工艺流程进行操作,并结合实际情况进行调整和优化,才能够实现金矿的高效提炼和利用。
希望本文所介绍的金矿工艺流程能够为相关从业人员提供一些参考和指导,推动金矿行业的发展和进步。
金矿选矿工艺流程

金矿选矿工艺流程一、前言金矿选矿工艺流程是指将金矿中的金属元素分离出来的过程。
随着科技的不断进步,金矿选矿工艺也在不断改进和完善。
本文将介绍目前较为常见的金矿选矿工艺流程。
二、原理金矿中常见的金属元素有金、银、铜等,这些元素通常以硫化物或氧化物的形式存在于矿物中。
因此,选矿工艺流程需要通过化学反应或物理作用将这些元素从矿物中分离出来。
三、流程1. 破碎首先需要将原料经过粗碎和细碎处理,使其达到适合进一步处理的颗粒度。
通常采用锤式粉碎机和球磨机进行处理。
2. 磨浸经过初步粉碎后,需要对原料进行湿法细粉处理,使其成为可浸出状态。
这个过程称为“磨浸”。
3. 浮选经过初步浸出后,需要对溶液进行浮选处理,将其中含有黄铁矾等杂质去除,并提高黄金含量。
该过程通常采用气浮法和泡沫浮选法。
4. 氧化经过浮选处理后,需要将黄金还原为金属状态。
这个过程称为“氧化”。
通常采用碱性或酸性氧化。
5. 吸附经过氧化处理后,需要通过吸附剂将金属元素吸附到固定相上。
通常采用活性炭进行吸附。
6. 脱附经过吸附处理后,需要脱除吸附剂上的金属元素。
这个过程称为“脱附”。
通常采用碱性或酸性脱附。
7. 再生经过脱附处理后,需要对吸附剂进行再生处理,以便重复使用。
该过程通常采用高温热解或酸洗法进行再生。
四、总结以上就是金矿选矿工艺流程的详细介绍。
不同的金矿选矿工艺流程在具体实施时可能会有所不同,但总体流程基本相同。
在实施过程中需要注意安全问题,并根据具体情况进行调整和优化。
黄金冶炼工艺流程

黄金冶炼工艺流程黄金冶炼是将金矿石中的金元素提取出来,经过一系列的工艺流程,最终得到纯金产品。
下面将为您介绍黄金冶炼的工艺流程。
一、矿石破碎和磨碎黄金矿石往往以岩石的形式存在,需要将其破碎成较小的颗粒大小。
通常采用的方法是先进行粗破,将矿石破碎成较大的块状物;然后通过细破,将块状物再次破碎成更小的颗粒。
接着,将破碎后的矿石进行磨碎,使其细化成细砂。
二、矿石浸出矿石浸出是冶炼过程中最为关键的一步。
通常采用氰液浸出法,即将砂浆状的矿石与含氰溶液混合,使其中的金元素与氰化剂发生反应,生成金氰化物溶液。
这个过程一般分为两个阶段:粗浸和细浸。
粗浸是指将砂浆状的矿石与氰化剂在浸出槽中进行反应,使金元素与氰化剂充分接触,生成金氰化物溶液;细浸则是将粗浸所得的溶液经过连续分离、过滤等工序,去除杂质,得到较纯的金氰化物溶液。
三、金氰化物溶液处理所得的金氰化物溶液需要进行一系列的处理才能得到纯金。
处理过程通常有以下几个步骤:1. 吸附:通过将金氰化物溶液与颗粒状活性碳接触,使金离子被活性碳吸附上去,形成金负载活性碳。
2. 脱附:通过加热或用酸洗等方法,使活性碳上的金离子脱附下来,得到金负载活性碳的金负载脱附溶液。
3. 锌粉还原:将金负载脱附溶液与锌粉混合,通过锌粉的还原作用,将金离子还原为金属金,同时锌粉会被氧化成氧化锌。
4. 溶液净化:还原后的溶液中可能含有一些杂质,需要通过滤液、沉淀等方法将杂质去除。
四、金的析出和精炼通过还原得到的金溶液中的金属金,需要经过析出和精炼过程,最终得到纯金。
1. 析出:将还原得到的金溶液与一定浓度的硫酸等混合,使其中的金反应生成不溶于溶液中的金盐沉淀,然后经过过滤、洗涤等步骤,得到金盐的沉淀。
2. 精炼:将金盐沉淀通过高温加热,使其化为液态金属金,然后通过吹气、注氧等方法去除其中的杂质。
最后,通过冷却凝固,得到纯金。
五、纯金产品制备通过精炼得到的纯金通常是以块状或片状存在的,需要进行加工制备成不同形态的金制品。
金矿选矿工艺

金矿的选矿工艺的调查1.重选1)跳汰选金2)摇床选金3)溜槽选金4)螺旋选矿机选金5)圆锥选矿机选金2.混汞选法1)内混汞法2)外混汞法3.氰化法1)离子交换树脂法2)锌丝置换法3)搅拌氰化法4)渗滤氰化法5)堆浸氰化法6)锌粉置换法7)炭浆法4.浮选法1.重选重选法是根据矿物相对密度(通常称比重)的差异来分选矿物的。
密度不同的矿物粒子在运动的介质中(水、空气与重液)受到流体动力和各种机械力的作用,造成适宜的松散分层和分离条件,从而使不同密度的矿粒得到分离。
常用的重选设备图为:不同的重选方法只是上图的最后一步的方法(螺旋机选矿法见方法四)不同而已。
重选是选金最古老、最普遍的方法之一。
在砂金矿中,金通常是呈单体自然金形态存在,粒度一般大于16吨/米3,与脉石密度差大,因此重选是选别砂金矿最主要、最有效、最经济的方法。
但在脉金,重选是很少单独使用,不作为联合提金流程的一部分,一般是在磨矿与分级回路中,采用跳汰机和螺旋溜槽与摇床配合,提前回收一解理的粗粒单体金,以利于其后的浮选和氢化作业,并可获得合格的金精矿。
这种方法在小型金矿和地方群采矿才用得较普遍,如内蒙的金厂沟梁、大水清等金矿。
重选选金的主要设备是各种形式的溜槽、跳汰机和摇床。
除常规重选设备外,根据我国金矿的生产特点,在消化、吸收国外先进设备基础上,我国研制了皮带溜槽、罗斯溜槽、圆形跳汰机、砂金离心洗选机组等新型重选设备,在黄金生产中以取得良好效果。
如山东沂南金矿金场选矿厂在磨矿分级回路设置软覆面(毛毯)溜槽,金的回收率可达70%。
软覆面溜槽还用来处理浮选和混汞尾矿,以提高金的回收率。
混汞法按其生产方式可分为内混汞和外混汞。
在砂金矿山普遍用混汞法分离金与重砂矿物;而在脉金矿山,混汞通常作为联合流程的一部分与浮选、重选、氰化等配和,主要用来捕收粗粒单体金。
1)跳汰选金法跳汰选金法是以跳汰机为选金设备的选金过程。
跳汰机是常用重选设备,类型很多。
目前我国选金厂多采用典瓦尔型隔膜跳汰机,见下图。
金矿堆浸工艺流程

金矿堆浸工艺流程金矿堆浸工艺是一种将含金矿石堆积在露天堆浸场中进行黄金浸出的方法。
该工艺流程包括选矿、堆浸、溶液处理和黄金提取等四个主要环节。
首先是选矿。
在金矿堆浸工艺中,通常是将从矿山开采得到的含金矿石进行选矿处理。
选矿过程主要是通过对矿石进行破碎、磨矿、筛分等步骤,将矿石粒度控制在较合适的范围内,以提高堆浸效果。
接下来是堆浸。
将经过选矿处理的含金矿石堆积在露天堆浸场中,形成一个或多个堆浸堆。
为了提高黄金的浸出率,通常会使用一定浸出剂添加到堆浸堆中。
常用的浸出剂有氰化钠、氧化钠等。
浸出剂通过与含金矿石中的黄金反应,将黄金溶解为金氰离子,并逐渐浸出。
然后是溶液处理。
浸出液中的金氰离子溶液通过管道排出,进入溶液处理设备。
溶液处理包括一系列的步骤,主要是对溶液进行纯化、过滤、析出等处理,去除杂质和沉淀物,使金氰离子溶液更加纯净。
最后是黄金提取。
经过溶液处理的金氰离子溶液进一步进行浓缩和提取操作,使其金浓度增加,以便于后续的黄金提取。
黄金提取方法有多种,其中常用的是吸附法和电解法。
吸附法主要是利用活性炭等吸附剂将金氰离子吸附到表面,形成含金炭;电解法则是将金氰离子溶液通过电解设备进行电解,使金离子还原为固态金属。
金矿堆浸工艺流程的特点是工艺简单、投资成本低、适用于开发低品位、大规模金矿石资源。
但是,堆浸工艺也存在一些问题,如对环境的影响较大、周期较长、浸出率低等。
因此,在实际应用中要根据矿石性质和生产要求进行合理选择和优化。
总的来说,金矿堆浸工艺流程是一种常用的金矿提取方法,通过选矿、堆浸、溶液处理和黄金提取等环节,可以将含金矿石中的黄金有效浸出和提取,实现金矿资源的利用。
金矿提炼技术简介
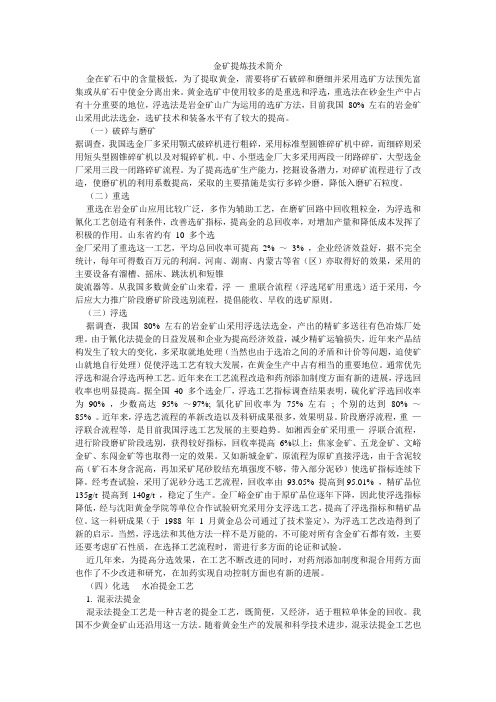
金矿提炼技术简介金在矿石中的含量极低,为了提取黄金,需要将矿石破碎和磨细并采用选矿方法预先富集或从矿石中使金分离出来。
黄金选矿中使用较多的是重选和浮选,重选法在砂金生产中占有十分重要的地位,浮选法是岩金矿山广为运用的选矿方法,目前我国80% 左右的岩金矿山采用此法选金,选矿技术和装备水平有了较大的提高。
(一)破碎与磨矿据调查,我国选金厂多采用颚式破碎机进行粗碎,采用标准型圆锥碎矿机中碎,而细碎则采用短头型圆锥碎矿机以及对辊碎矿机。
中、小型选金厂大多采用两段一闭路碎矿,大型选金厂采用三段一闭路碎矿流程。
为了提高选矿生产能力,挖掘设备潜力,对碎矿流程进行了改造,使磨矿机的利用系数提高,采取的主要措施是实行多碎少磨,降低入磨矿石粒度。
(二)重选重选在岩金矿山应用比较广泛,多作为辅助工艺,在磨矿回路中回收粗粒金,为浮选和氰化工艺创造有利条件,改善选矿指标,提高金的总回收率,对增加产量和降低成本发挥了积极的作用。
山东省约有10 多个选金厂采用了重选这一工艺,平均总回收率可提高2% ~3% ,企业经济效益好,据不完全统计,每年可得数百万元的利润。
河南、湖南、内蒙古等省(区)亦取得好的效果,采用的主要设备有溜槽、摇床、跳汰机和短锥旋流器等。
从我国多数黄金矿山来看,浮—重联合流程(浮选尾矿用重选)适于采用,今后应大力推广阶段磨矿阶段选别流程,提倡能收、早收的选矿原则。
(三)浮选据调查,我国80% 左右的岩金矿山采用浮选法选金,产出的精矿多送往有色冶炼厂处理。
由于氰化法提金的日益发展和企业为提高经济效益,减少精矿运输损失,近年来产品结构发生了较大的变化,多采取就地处理(当然也由于选冶之间的矛盾和计价等问题,迫使矿山就地自行处理)促使浮选工艺有较大发展,在黄金生产中占有相当的重要地位。
通常优先浮选和混合浮选两种工艺。
近年来在工艺流程改造和药剂添加制度方面有新的进展,浮选回收率也明显提高。
据全国40 多个选金厂,浮选工艺指标调查结果表明,硫化矿浮选回收率为90% ,少数高达95% ~97%; 氧化矿回收率为75% 左右; 个别的达到80% ~85% 。
金矿工艺流程
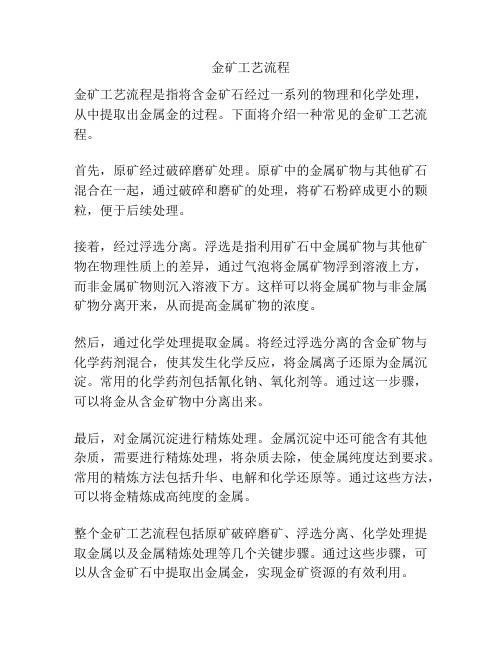
金矿工艺流程金矿工艺流程是指将含金矿石经过一系列的物理和化学处理,从中提取出金属金的过程。
下面将介绍一种常见的金矿工艺流程。
首先,原矿经过破碎磨矿处理。
原矿中的金属矿物与其他矿石混合在一起,通过破碎和磨矿的处理,将矿石粉碎成更小的颗粒,便于后续处理。
接着,经过浮选分离。
浮选是指利用矿石中金属矿物与其他矿物在物理性质上的差异,通过气泡将金属矿物浮到溶液上方,而非金属矿物则沉入溶液下方。
这样可以将金属矿物与非金属矿物分离开来,从而提高金属矿物的浓度。
然后,通过化学处理提取金属。
将经过浮选分离的含金矿物与化学药剂混合,使其发生化学反应,将金属离子还原为金属沉淀。
常用的化学药剂包括氰化钠、氧化剂等。
通过这一步骤,可以将金从含金矿物中分离出来。
最后,对金属沉淀进行精炼处理。
金属沉淀中还可能含有其他杂质,需要进行精炼处理,将杂质去除,使金属纯度达到要求。
常用的精炼方法包括升华、电解和化学还原等。
通过这些方法,可以将金精炼成高纯度的金属。
整个金矿工艺流程包括原矿破碎磨矿、浮选分离、化学处理提取金属以及金属精炼处理等几个关键步骤。
通过这些步骤,可以从含金矿石中提取出金属金,实现金矿资源的有效利用。
金矿工艺流程的优化可以提高金属回收率和纯度。
例如,在破碎磨矿阶段,选择合适的破碎设备和磨矿设备,可以更好地破碎和磨碎矿石,提高浮选效果。
在浮选分离阶段,选择适当的浮选药剂和气泡生成装置,可以提高金属矿物的浮选率和分离效果。
在化学处理阶段,优化药剂配比和反应条件,可以提高金的提取率。
在金属精炼处理阶段,选择适当的精炼方法和设备,可以降低杂质含量,提高金属纯度。
总之,金矿工艺流程是将含金矿石经过一系列的物理和化学处理,从中提取金属金的过程。
通过优化工艺流程和设备选择,可以提高金属回收率和纯度,实现金矿资源的有效利用。
金矿选矿工艺流程

金矿选矿工艺流程
《金矿选矿工艺流程》
金矿选矿是金矿石中金属金从原矿石中经浮选选矿、焙烧或氰化提取工艺过程中的化学、物理、和机械分离过程,是金矿加工的重要环节之一。
金矿选矿工艺流程的设计与实施直接影响了金矿的提取率和质量。
在金矿选矿工艺中,通常需要经过破碎、磨矿、浮选、干燥、熔炼等多个工序。
首先是破碎工艺,将原矿石经过初级破碎,减小矿石的粒径,方便后续的磨矿工序。
接下来是磨矿工艺,将初级破碎后的矿石进一步细化,达到合适的颗粒度,以便于进行浮选分离。
然后是浮选工艺,通过将金矿石与浮选剂混合搅拌,利用其与矿石表面的特殊性质分离出金属金,达到提取金的目的。
在浮选后通常需要对浮选泡沫进行处理,将其中的金属金分离出来。
最后是干燥和熔炼工艺,将金属金从浮选浆液中提取出来,进行熔炼得到纯金。
金矿选矿工艺流程的设计和改进一直是金矿加工领域的研究重点,不断提高提取率和纯度,减少环境污染和能源消耗。
随着科学技术的不断发展,金矿选矿工艺流程也在不断创新和完善,以满足金矿的高效加工需求。
总的来说,金矿选矿工艺流程是一个复杂的系统工程,需要化学、物理、机械等多个领域的知识和技术与工艺相结合,以达到高效提取和精炼金属金的目的。
通过不断地改进和创新,金
矿选矿工艺流程将会更加高效、环保、节能,为金矿加工业的发展做出贡献。
黄金生产工艺流程

黄金生产工艺流程一. 引言在全球范围内,黄金一直以来都是一种备受珍视的贵金属,具有很高的经济价值和文化价值。
黄金的生产工艺流程是指通过一系列的工艺步骤将黄金从矿石中提取出来,并进行精炼和加工,最终得到高纯度和高质量的黄金产品。
本文将详细介绍黄金的生产工艺流程。
二. 黄金矿石开采黄金矿石是指含有一定量的黄金的矿石,它们通常分布在地壳的深处,因此需要开采探测。
黄金矿石的开采通常包括以下几个步骤:2.1 矿区勘探和选址首先,需要对潜在的黄金矿区进行勘探和选址工作。
通过使用地质勘探技术,例如地质雷达、重力勘探和电磁探测等,来确定可能存在黄金矿石的地下位置和规模。
2.2 井下开采和露天采矿根据地质勘探结果,选择合适的开采方法,包括井下开采和露天采矿。
井下开采主要是通过挖掘和爆破的方式将矿石从地下开采出来;露天采矿则是通过开挖矿坑和运输设备将矿石从地表开采出来。
2.3 矿石选矿经过开采后,需要对矿石进行选矿处理,即将黄金矿石与其他无用矿石分离。
这通常通过物理和化学方法实现,例如重力分选、浮选和磁选等。
三. 黄金提取和分离经过矿石选矿后,接下来是黄金的提取和分离过程。
主要包括以下几个步骤:3.1 破碎和磨矿将选矿后的黄金矿石先进行破碎和磨矿处理,以便更好地释放出黄金颗粒。
这通常通过使用破碎机、磨矿机和球磨机等设备来实现。
3.2 提金浸出经过破碎和磨矿处理后,将矿石与一定溶液接触,常用的溶液为氰化物溶液。
黄金会与氰化物结合形成金氰化物,在溶液中溶解。
这一步骤被称为提金浸出,是黄金提取的关键步骤。
3.3 固液分离和固金提取经过提金浸出后,需要对固液混合物进行固液分离,将溶液与固体分离开来,通常采用过滤或离心等方法。
然后将得到的含有黄金的溶液进行固金提取,将金氰化物还原为金属黄金。
3.4 精炼在固金提取过程中得到的黄金含有杂质,需要进行精炼以提高纯度。
有多种精炼方法可选择,包括湿法精炼和火法精炼等。
湿法精炼通常采用电解法,将黄金溶解在电解质中,然后用电流沉积出纯金属黄金。
金矿生产工艺流程
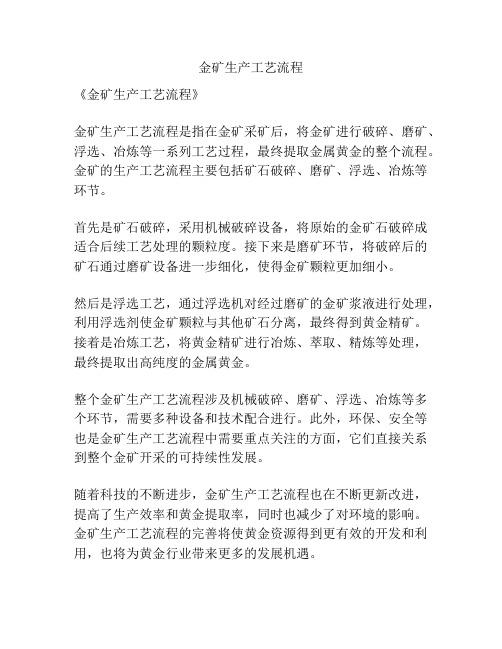
金矿生产工艺流程
《金矿生产工艺流程》
金矿生产工艺流程是指在金矿采矿后,将金矿进行破碎、磨矿、浮选、冶炼等一系列工艺过程,最终提取金属黄金的整个流程。
金矿的生产工艺流程主要包括矿石破碎、磨矿、浮选、冶炼等环节。
首先是矿石破碎,采用机械破碎设备,将原始的金矿石破碎成适合后续工艺处理的颗粒度。
接下来是磨矿环节,将破碎后的矿石通过磨矿设备进一步细化,使得金矿颗粒更加细小。
然后是浮选工艺,通过浮选机对经过磨矿的金矿浆液进行处理,利用浮选剂使金矿颗粒与其他矿石分离,最终得到黄金精矿。
接着是冶炼工艺,将黄金精矿进行冶炼、萃取、精炼等处理,最终提取出高纯度的金属黄金。
整个金矿生产工艺流程涉及机械破碎、磨矿、浮选、冶炼等多个环节,需要多种设备和技术配合进行。
此外,环保、安全等也是金矿生产工艺流程中需要重点关注的方面,它们直接关系到整个金矿开采的可持续性发展。
随着科技的不断进步,金矿生产工艺流程也在不断更新改进,提高了生产效率和黄金提取率,同时也减少了对环境的影响。
金矿生产工艺流程的完善将使黄金资源得到更有效的开发和利用,也将为黄金行业带来更多的发展机遇。
金矿提取工艺流程

金矿提取工艺流程金矿提取工艺流程主要包括破碎、磨矿、浸出、吸附和电积等环节。
首先是破碎环节。
金矿石一般较硬,需要经过破碎工艺将其变为可处理的小颗粒。
常见的破碎设备有颚式破碎机和圆锥破碎机。
破碎后的矿石颗粒一般在几毫米至几厘米之间。
接下来是磨矿环节。
磨矿是将颗粒状的矿石细化,使金矿石与提取剂更充分地接触。
磨矿设备主要有球磨机和浮选机。
球磨机通过旋转的钢球和矿石的摩擦碰撞将矿石细化。
浮选机则通过气泡将金矿石中的金粒和提取剂一起上升到液面,从而实现分离。
接下来是浸出环节。
浸出是利用金矿石与提取剂之间的化学反应,将金颗粒与其他杂质分离。
常见的提取剂有氰化物、硫化物和氧化剂。
氰化物溶液在一定温度和压力下与金矿石反应,形成氰化金离子,浸出金颗粒。
然后是吸附环节。
吸附是利用活性炭等材料将金离子吸附到其表面。
吸附设备一般是液固分离设备,如吸附柱或吸附槽。
吸附剂和金离子在一定条件下接触,金离子会优先吸附在吸附剂表面。
最后是电积环节。
电积是让吸附剂上的金离子通过电解还原成固态金属。
通常使用电解槽进行电积,电积槽中的电积液由含有金离子的溶液组成。
在电流的作用下,金离子在电积剂表面上电还原成金属。
工艺流程中还包括中间处理环节,如浸矿渣的处理和废水的处理。
浸矿渣处理可以通过干燥、焙烧或浸出再处理等方式,回收其中的金属。
废水处理主要是对含有金离子的废水进行处理,以达到环保要求。
总而言之,金矿提取工艺流程是一个复杂的过程,需要经过破碎、磨矿、浸出、吸附和电积等环节。
这些环节相互配合,最终实现金矿石与提取剂的化学反应,将金颗粒从矿石中提取出来。
同时,还需要进行中间处理环节,以将浸矿渣和废水有效处理。
这个流程要求很高的设备和技术,以确保金矿提取的效率和质量。
金矿生产工艺流程

金矿生产工艺流程金矿生产工艺流程是指将金矿从矿石中提取出金属金的一系列工艺步骤。
下面就简单介绍一下金矿生产工艺流程的主要步骤和流程。
首先,整个金矿生产工艺流程可以分为四个主要的环节:采矿、选矿、冶炼和提纯。
采矿是完成金矿从地下开采到地上的过程。
开采方式有露天开采和地下开采两种。
露天开采是指通过挖掘机和炮矿机等设备将金矿露天开采出来,适用于矿床比较大且矿体比较近地表的情况。
地下开采则是通过矿井进入地下进行采矿,在地下开采过程中需要进行支护和排水工程等。
采矿完成后,将矿石送到选矿厂进行选矿处理。
选矿是将矿石中的有价金属和无价杂质进行分离的过程。
首先,将原矿石进行粉碎、磨矿和浮选等步骤,将金矿和其他矿物分离。
浮选是指通过泡沫浮选剂使金矿颗粒在泡沫中上浮,将其与其他矿物分离。
选矿过程中还会使用各种化学药剂帮助分离有价金属和无价杂质。
通过选矿工艺,可以将金矿的品位提高到一定的程度。
接下来是冶炼过程,将经过选矿处理的金矿转化为金属金。
冶炼通常采用高温熔炼的方法。
首先将金矿石进行破碎并与焦炭混合,然后将混合料放入炉子中进行高温熔炼。
在炉内,金矿石中的金属金会与焦炭发生反应,生成金属金并与其他金属物质分离。
随后,通过物理和化学处理,将金属金从其他杂质中进一步分离出来。
最后是提纯过程,将冶炼得到的金属金进行进一步的提纯和精炼。
一般而言,提纯过程会采用水力选矿、重选和电解等方法。
水力选矿是利用水力力场将金属金与其他金属分离,重选是利用重力分离的原理将金属金与其他杂质分离。
通过这些方法,可以将金属金的纯度进一步提高。
综上所述,金矿生产工艺流程是一个将金矿从地下开采到最终提炼出金属金的复杂过程。
这个过程包括采矿、选矿、冶炼和提纯等多个环节。
通过不同的工艺方法,可以最大限度地提高金矿的品位和纯度,实现高效的金矿生产。
金矿生产工艺流程

金矿生产工艺流程金矿生产工艺流程是指将含金矿石经过一系列的处理工艺,将金属金从矿石中提取出来的过程。
下面是金矿生产工艺流程的简要介绍:1. 矿石开采:金矿的开采通常通过露天或地下开采方式进行。
露天开采一般适用于较浅的金矿,而地下开采适用于深层金矿。
2. 破碎和磨矿:将矿石通过破碎机进行破碎,使得矿石颗粒变小。
随后,将破碎后的矿石送入球磨机或压磨机进行磨矿,进一步使矿石颗粒细化。
3. 砂浆制备:将磨矿后的矿石通过水和化学试剂混合,制备成砂浆。
砂浆中的金属金以颗粒的形式存在。
4. 浮选:利用浮选机将金属金与其他矿石进行分离。
浮选过程中,通过控制泡沫浮力、药剂和搅拌等参数,使得金属金颗粒浮于矿浆的表面,形成泡沫以便分离。
5. 浓缩:将浮选后的泡沫矿液进一步进行浓缩,去除其中的水分和杂质。
通常采用离心机、压滤机和浓缩器等设备进行操作。
6. 冶炼:将得到的含金浓缩物送入冶炼炉进行冶炼。
冶炼的目的是将金属金从浓缩物中进一步提取出来。
7. 精炼:将冶炼得到的金属金进行精细化处理,去除其中的其他杂质。
通过熔融、氧化、还原、电解等方法,可得到高纯度的金属金。
8. 深度处理:在精炼后,金属金的纯度还不够高。
因此需要进行一些深度处理操作,例如溶剂萃取、离子交换和电解沉积等,以进一步提高金属金的纯度。
9. 金属金制品生产:将经过深度处理的金属金用于制造各种金属金制品,如金饰品、金币、工艺品等。
总的来说,金矿生产工艺流程包括开采、破碎磨矿、砂浆制备、浮选、浓缩、冶炼、精炼、深度处理和金属金制品生产等步骤。
通过这些工艺流程,金矿中的金属金能够得以高效提取和利用。
金矿设备工艺流程

金矿设备工艺流程
《金矿设备工艺流程》
金矿设备工艺流程是将原始金矿石经过一系列的加工和提取过程,将金属金提取出来的一种工艺流程。
下面就来介绍一下金矿设备工艺流程的主要步骤。
第一步是原料破碎和筛分。
原始金矿石是被挖掘出来的块状矿石,需要经过破碎和筛分的过程,将大块的矿石破碎成小块,并且根据矿石的大小进行筛分,以便后续的处理。
第二步是磨矿。
磨矿是指将筛分后的矿石进行磨碎的过程,目的是将矿石中的金属金暴露出来,方便后续的提取。
通常采用的设备是磨矿机,通过旋转的钢球和矿石一起进行研磨,将金属金研磨出来。
第三步是浮选。
浮选是将矿石中的金属金进行提取的过程,采用的设备是浮选机。
在浮选机中,常用的是可溶性浮选剂,将矿石中的金属金吸附在气泡上,然后将气泡浮上水面,从而实现金属金的提取。
第四步是干燥和成品。
将浮选后的金属金进行干燥处理,以去除水分,并且进行成品加工,将金属金提炼成金条或金块。
以上就是金矿设备工艺流程的主要步骤,通过这些步骤,原始的金矿石可以得到金属金的提取和加工,成为市场上的金制品。
黄金 冶炼 方法

黄金冶炼方法黄金冶炼产品为成品金。
冶炼有粗炼和精炼之分。
精粗炼产品为合金(俗称合质金),我国黄金矿山就地产金多为合质金,直接交售给银行。
黄金富矿块和各种金精矿运往有色冶炼厂加工提炼成品金(俗称含量金)。
建国40年来,黄金冶炼和综合回收发展较快,冶炼技术和工艺装备水平不断提高,冶炼成本日益降低,促进了黄金生产的发展。
1.黄金矿山金的就地冶炼70年代以前,黄金生产处于初步发展阶段,除少数矿山开始采用氰化法提金工艺外,矿山就地产金主要是从砂矿重选所得的自然金和精矿的冶炼,以及混汞法提金工艺产出的汞膏为原料就地冶炼,就地产金量仅占总产量的30%,70%的金依靠有色冶炼厂回收。
1970年以后,黄金生产逐步发展,氰化法提金工艺日益广泛地应用,矿山就地产金量日渐增多,1985年矿山成品金的产量已占全国黄金产量的70%,选厂产出的精矿产品大部分就地氰化冶炼产出成品金。
矿山就地冶炼多数采用传统的坩埚法熔炼,因生产工艺和处理物料性质不同,所产合质金的含金量也不一样,直接交售银行因含金量不高或含银不计价等原因,有的矿山为提高质量和经济效益采取了化学法除杂再次熔炼或电解法进行金银分离精炼。
焦家金矿曾于1984年试验采用水冶新工艺,将氰化金泥经电氯化除去贱金属(用水溶液氯化法提金和氨浸法提银)获得含金品位99.9%成品金和含银99.9%的银锭,金泥中的铜、铅也同时回收(用湿法处理金泥有被推广的趋势)。
招远金矿成功地研制出一种Φ1.5×1.8m的转炉熔炼金泥,取代了过去的坩埚熔炼,降低了成本,改善了劳动条件。
这一方法在山东新城金矿等矿山普遍推广应用,效果较好。
招远冶炼厂是我国自行研究、设计和建设的第一家黄金冶炼厂,专门处理多金属硫化物金精矿,以提取黄金为主,同时回收银、铜、铅、硫等,是综合冶炼、化工为一体的新型企业。
招远冶炼厂的建成投产,为我国黄金生产冶炼工艺填补了一项技术空白,采用焙烧-酸浸-(盐浸)-氰化浸出联合工艺,解决了长期以来采、选、冶之间的生产矛盾,解决了金精矿长途外运损失(年损失率2%~3%),运输压力大和综合利用问题。
黄金冶炼厂工艺流程
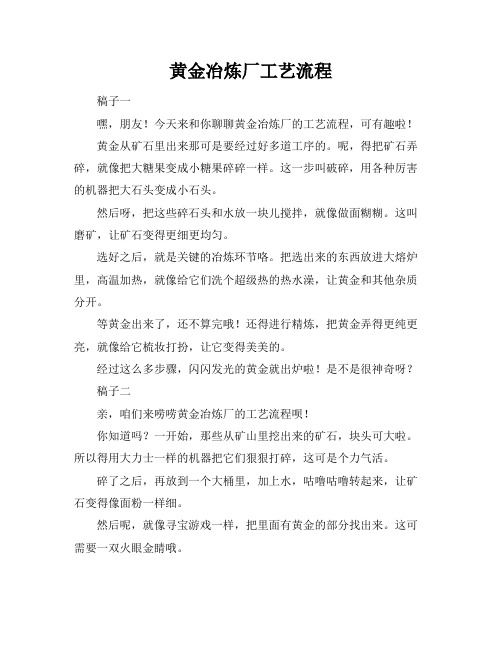
黄金冶炼厂工艺流程
稿子一
嘿,朋友!今天来和你聊聊黄金冶炼厂的工艺流程,可有趣啦!
黄金从矿石里出来那可是要经过好多道工序的。
呢,得把矿石弄碎,就像把大糖果变成小糖果碎碎一样。
这一步叫破碎,用各种厉害的机器把大石头变成小石头。
然后呀,把这些碎石头和水放一块儿搅拌,就像做面糊糊。
这叫磨矿,让矿石变得更细更均匀。
选好之后,就是关键的冶炼环节咯。
把选出来的东西放进大熔炉里,高温加热,就像给它们洗个超级热的热水澡,让黄金和其他杂质分开。
等黄金出来了,还不算完哦!还得进行精炼,把黄金弄得更纯更亮,就像给它梳妆打扮,让它变得美美的。
经过这么多步骤,闪闪发光的黄金就出炉啦!是不是很神奇呀?
稿子二
亲,咱们来唠唠黄金冶炼厂的工艺流程呗!
你知道吗?一开始,那些从矿山里挖出来的矿石,块头可大啦。
所以得用大力士一样的机器把它们狠狠打碎,这可是个力气活。
碎了之后,再放到一个大桶里,加上水,咕噜咕噜转起来,让矿石变得像面粉一样细。
然后呢,就像寻宝游戏一样,把里面有黄金的部分找出来。
这可需要一双火眼金睛哦。
找到了有黄金的,就把它们放进大火炉里烤一烤。
温度超级高,那些杂质就被赶跑啦,黄金就慢慢现身。
不过这时候的黄金还不够完美,还得再好好收拾收拾。
就像给小姑娘化妆,让它变得更加漂亮纯粹。
在整个过程中,工人们都可认真啦,每一步都小心翼翼,就怕黄金跑掉或者变丑。
经过这么多努力,哇塞,金灿灿的黄金就出现在我们眼前啦,是不是超级厉害?。
金生产工艺

金生产工艺
黄金生产工艺主要包括采矿、选矿、冶炼等环节。
1. 采矿:黄金采矿通常采用露天开采和地下开采两种方式。
露天开采适用于矿体浅薄、储量较大的矿床;地下开采适用于矿体深埋、储量较小的矿床。
采矿过程中,矿工使用各种工具和设备将含金矿石从地下挖掘出来。
2. 选矿:选矿是将含金矿石中的含金矿物与其他杂质分离的过程。
常用的选矿方法包括浮选、重选、磁选等。
选矿过程可以提高金矿石的品位,使其达到可冶炼的程度。
3. 冶炼:冶炼是将含金矿石中的金元素提取出来的过程。
常用的冶炼方法包括氰化法、浮选法、焙烧法等。
氰化法是目前最常用的冶炼方法,通过将含金矿石与氰化物溶液反应,使金离子溶解在溶液中,然后通过电解或其他方法将金离子还原成金属金。
4. 精炼:精炼是将冶炼得到的粗金进一步提纯的过程。
常用的精炼方法包括电解精炼、化学精炼等。
精炼过程可以提高金的纯度,使其达到市场要求的标准。
需要注意的是,黄金生产过程中需要严格遵守环保和安全规定,以减少对环境的影响和保障工人的安全。
同时,黄金生产企业也需要不断创新和改进生产工艺,提高生产效率和降低成本,以适应市场需求和可持续发展的要求。
- 1、下载文档前请自行甄别文档内容的完整性,平台不提供额外的编辑、内容补充、找答案等附加服务。
- 2、"仅部分预览"的文档,不可在线预览部分如存在完整性等问题,可反馈申请退款(可完整预览的文档不适用该条件!)。
- 3、如文档侵犯您的权益,请联系客服反馈,我们会尽快为您处理(人工客服工作时间:9:00-18:30)。
黄金矿山生产工艺
黄金矿山生产工艺主要包括以下几个过程:
1. 采矿
采矿是从地下或露天矿山中开采黄金矿石的过程。
露天采矿是指在地
表开采裸露的矿石,而地下采矿则需要在地下挖掘出矿石。
采矿的方
式有很多种,常用的方法包括硬岩采矿、软岩采矿和深部采矿等。
采
矿的主要工具有矿用车、钻机、打火机和矿井提升设备等。
2. 矿石破碎
采矿得到的矿石往往是较大的石块,需要经过破碎才能进一步处理。
矿石破碎主要有两个步骤:首先通过震荡筛将矿石分级;然后将矿石
放入破碎机中进行破碎。
破碎的目的是使矿石粉碎成较小的颗粒,便
于后续的选矿和冶炼。
3. 矿石选矿
矿石选矿是将矿石内的杂质物质、杂质金属等分离出来,使它们与黄
金分离。
一般而言,选矿的首要目的是使黄金尽可能地筛选出来,而
将精细石英和其他杂质物质舍弃掉。
选矿的方法有很多种,包括浮选、重力选矿、磁选和电选等。
选矿的主要设备有浮选机、重介质分选机、磁选机和振动筛等。
4. 冶炼
选矿后的矿石通过熔炼等技术处理成金属黄金。
冶炼过程中,先将矿
石加热成炉渣,然后将其冷却接触冶金剂(例如碳)使黄金分离出来,最后通过淬火、烘烤等方法提高黄金纯度。
黄金冶炼的工具包括熔炉、反应釜和高温烧结炉等。
5. 金条加工
经过冶炼,在黄金矿山的生产工艺中会得到黄金金属,但它还不完整。
黄金金属可能会被混入金属杂质、以及填料和其他掺杂物。
因此,黄
金需要经过精炼、铸造、表面加工等多个步骤,最终成为符合贵金属
标准的金条或其它产品。
以上就是黄金矿山生产工艺的五个主要过程。
这些过程涵盖了从采矿
到金条加工等多个阶段,并需要使用各种设备和技术才能成功完成。
在全球,黄金矿山生产工艺各不相同,但这些矿区通常都采用差不多
的基础流程。