关于齿轮表面强化技术分析详细版
高强度汽车齿轮表面强化技术的发展研究

车辆工程技术24车辆技术在汽车系统中,齿轮是动力系统的重要构成部分,承担着改变速度、传递扭矩等任务,通常满载荷运行,这就要求汽车齿轮具备良好的强度与应用寿命。
随着新能源汽车、现代汽车与其他机械工业的发展,其动力机构要求齿轮具有更高强度、更高效率、更高寿命,这些要求不仅需要优化齿轮设计,还需要开发齿轮新材料,研发新型的齿轮加工技术与强化技术。
而表面强化技术则是增强齿轮强度、延长齿轮应用寿命的关键,从抗齿轮弯曲疲劳、抗齿面接触疲劳两个表面强化技术入手,探索齿轮强化技术的发展与研究。
1 汽车齿轮材料技术与研究现状分析齿轮是汽车传动机构的重要部分,承担着改变速度、传递扭矩的重要作用,其经常处在连续高载荷的运行状态,齿轮不仅会进行滚动,还需要滑动,同时还承受着脉冲作用力,这些里力的综合作用会导致齿轮破损,影响齿轮的正常运行。
为保障汽车传动效率,要求汽车齿轮必须具备良好的强度与应用寿命。
综合分析来看,齿轮破坏的形式主要表现为四类,第一为磨损,第二是齿面胶合,第三是齿轮折断,第四则是点蚀。
分析发现,这些破坏多集中发生在齿轮的表面与齿根位置。
为此,采取一定的齿轮表面强化技术,有助于降低齿轮破坏,保证齿轮表面完整性。
通过采取齿轮表面强化技术,可以改变齿轮形态特征、组织结构、硬度、表面粗糙度,增强齿轮的弯曲疲劳抗力、接触疲劳抗力,提升齿轮强度,保证齿轮应用的综合效益。
随着汽车种类增加,应用用途的多样性要求越来越多,对齿轮的强度、使用寿命提出了更高的要求。
为此,需要做好齿轮表面强化技术的探究工作,同时做好齿轮材料研究,保证齿轮的应用质量。
2 汽车齿轮表面强化技术分析汽车齿轮表面强化技术主要包含两个部分,即抗齿轮弯曲疲劳表面强化技术与抗齿面接触疲劳表面强化技术,通过这些技术的研究与使用,可以有效改进齿轮性能,增强齿轮整体指标,有助于实现齿轮高质量、长期安全运行。
2.1 抗齿轮弯曲疲劳表面强化技术抗齿轮弯曲疲劳表面强化主要是通过齿轮喷丸强化的方式来实现,喷丸强化指的是应用一定的机械手段,对齿轮表面进行压缩、变形处理,从而在齿轮表面生成形变改性层,达到增强齿轮表面强度的目的。
硬化齿轮制造技术研究

硬化齿轮制造技术研究齿轮是传动机构中常用的一种零部件。
在很多机械传动中,齿轮的质量和性能起着至关重要的作用。
如何提高齿轮的耐磨性、抗疲劳性、噪音低等级以及准确度,一直是齿轮制造过程中的难点。
为了解决这些问题,许多制造技术不断地涌现出来。
其中,硬化齿轮制造技术就是一种重要的发展趋势。
一、硬化齿轮的特点硬化齿轮制造技术是一种将齿轮表面硬化的方法,通过提升齿轮表面的硬度,来提高齿轮的使用寿命和工作性能,同时减小了齿轮齿面的磨损和削减率,从而达到更好的使用效果。
硬化齿轮制造技术有很多的优点。
首先,硬化齿轮的硬度变高了,因此能够承受更大的负荷,抗疲劳性更好。
同时,硬化齿轮的表面光滑度也得到提高,摩擦和磨损都得到了很好的控制。
再者,硬化齿轮的噪音低等级也会有所提高,这对于一些噪音敏感的工业和机械设备来说尤为重要。
二、硬化齿轮的制造方法在制造硬化齿轮时,最主要的就是硬化过程。
硬化过程是借助高温、高压、高速等外力作用下,让齿轮表面经一定深度淬火而形成的。
在此过程中,要注意以下几点:1. 硬化时温度的控制。
普遍情况下硬化温度控制在800℃左右。
不过硬化温度也会根据不同材料的类型和厚度等因素不同而进行调整。
2. 硬化后的长期处理。
硬化后的齿轮需要再次回火。
在这个过程中,长时间的低温处理可以帮助保持齿轮表面硬度的同时,使得齿轮的耐腐蚀性变更好。
3. 清洁操作。
齿轮表面要保持清洁干净,无油无水,否则硬化效果会大打折扣。
三、规范化的生产流程硬化齿轮的生产流程比较复杂,需要细致认真的操作,遵循规范化、标准化的制造流程才能保证硬化齿轮的质量。
整个流程大致可以分为以下几个步骤:1. 理论分析。
在生产硬化齿轮之前,要先对涉及到的工业材料的性能进行详细的分析,并根据所选材料的特点设计方案。
2. 制造齿轮。
制造齿轮时,要根据设计要求进行制造,包括材料的选择、齿轮加工、刀具磨损情况等。
3. 检验工序。
检验工序是硬化齿轮制造中的重要工作,要对齿轮进行检查,保证无裂纹,无毛刺,无塌陷等缺点。
齿轮表面喷丸强化的工艺试验

1 齿 面 喷 丸 强 化 工 艺 简 述
喷 丸强化 工艺 是提 高齿轮 疲劳 强度 的方法 之一 。 通 过 喷丸 强 化能 提 高齿 面疲 劳 寿命 ,消 除机 加 工 刀
痕 产 生 的 内应力 , 改善 润 滑性 能 。 齿 面喷 丸强 化 是 以压 缩 空气 为 动力 ,选 用 细球
维普资讯
主持人 : 张禾/ 艺 ・ 料 工 材
齿 轮 表 面 喷 丸 强 化 的 工 艺 试 验
冯 琴 ( 西 宜春齿 轮 制 造有 限公 司) 江
摘要 : 喷丸强化工艺是提 高摩托车渗碳齿轮表面疲 劳强度的方法之一 , 喷丸工艺参数的合理
选择 很 重要 , 产 时应 防止 过度 喷 丸 , 选择 硬 而韧 的 丸料 。 生 要
时 间
m l n 4 8
丸 粒 硬 度 丸 粒速 度 表 面 硬 度
HRC 48 5 ~ 5 48 5 ~ 5 m, S 6 0 6 0 HRA 8l ~81 5 . 81 5 8 . ~ 2
国 内外 摩 托 车上 的渗 碳 齿 轮绝 大 多数 都 采用 齿 轮表
面喷 丸强 化 处理 。
b 热 处 理 工 艺 :齿 轮在 台 湾 三永 公 司生 产 的 .
S 8 54 续式 网带炉 中渗碳 处理 , Y.0 —连 淬碳 热处理 工艺 参 数 见表 l 。
表 1 渗碳 热处理炉 内区段 的工艺参数
件 内 , 据 裂纹 扩 展理 论 , 纹不 会 扩展 到 压应 力层 根 裂
C 喷 丸工 艺 : Q32 B型转 台式 抛 丸机 上进 . 在 55 行 喷 丸处 理 , 丸处 理 参 数见 表 2 喷 。
齿轮的激光相变强化处理
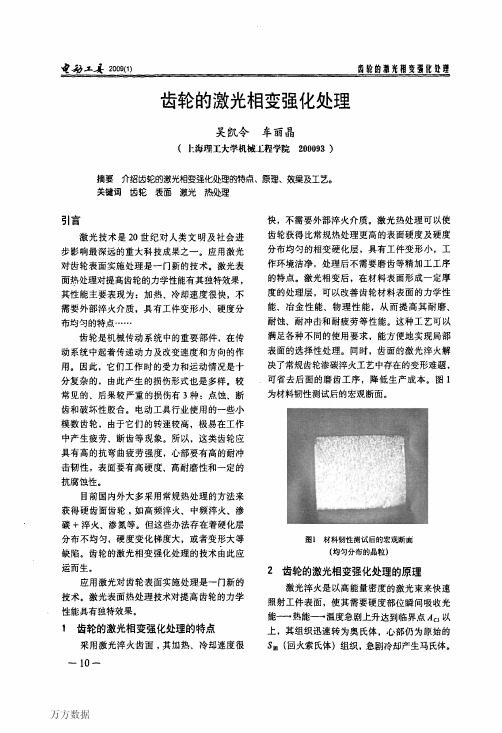
电彩工其2009(1)齿轮的激光朔变强化处理齿轮的激光相变强化处理吴凯令车丽晶(}:海理工大学机械工程学院200093)摘要介绍齿轮的激光相变强化处理的特点、原理、效果及工艺。
关键词齿轮表面激光热处理引言激光技术是20世纪对人类文明及社会进步影响最深远的重大科技成果之一。
应用激光对齿轮表面实施处理是一门新的技术。
激光表面热处理对提高齿轮的力学性能有其独特效果,其性能主要表现为:加热、冷却速度很快,不需要外部淬火介质,具有工件变形小、硬度分布均匀的特点……齿轮是机械传动系统中的重要部件,在传动系统中起者传递动力及改变速度和方向的作用。
因此,它们工作时的受力和运动情况是十分复杂的,由此产生的损伤形式也是多样。
较常见的、后果较严重的损伤有3种:点蚀、断齿和破坏性胶合。
电动工具行业使用的一些小模数齿轮,由于它们的转速较高,极易在工作中产生疲劳、断齿等现象。
所以,这类齿轮应具有高的抗弯曲疲劳强度,心部要有高的耐冲击韧性,表面要有高硬度、高耐磨性和一定的抗腐蚀性。
目前国内外大多采用常规热处理的方法来获得硬齿面齿轮,如高频淬火、中频淬火、渗碳+淬火、渗氮等。
但这些办法存在着硬化层分布不均匀,硬度变化梯度大,或者变形大等缺陷。
齿轮的激光相变强化处理的技术由此应运而生。
应用激光对齿轮表面实施处理是一门新的技术。
激光表面热处理技术对提高齿轮的力学性能具有独特效果。
1齿轮的激光相变强化处理的特点采用激光淬火齿面,其加热、冷却速度很一】0一快,不需要外部淬火介质。
激光热处理可以使齿轮获得比常规热处理更高的表面硬度及硬度分布均匀的相变硬化层,具有工件变形小,工作环境洁净,处理后不需要磨齿等精加工工序的特点。
激光相变后,在材料表面形成一定厚度的处理层,可以改善齿轮材料表面的力学性能、冶金性能、物理性能,从而提高其耐磨、耐蚀、耐冲击和耐疲劳等性能。
这种工艺可以满足各种不同的使用要求,能方便地实现局部表面的选择性处理。
同时,齿面的激光淬火解决了常规齿轮渗碳淬火工艺中存在的变形难题,可省去后面的磨齿工序,降低生产成本。
高强度汽车齿轮表面强化技术的研究现状和发展趋势_陈勇

1.1 国内外汽车齿轮材料及齿轮工艺参数 模数是齿轮重要的参数,选取汽车齿轮模数
通常要考虑强度、噪声、轻量化及加工工艺等因 素。表1为乘用车和商用车齿轮常用模数及直径工 艺参数范围。
汽车齿轮在传递扭矩和改变速度过程中,通 常处于高速、高载荷、交变冲击载荷等工作环境 中。汽车齿轮材料不仅需要良好的机械加工性能 和热处理渗碳淬火性能,还必须满足合理的成本 需求。为保证齿面和齿顶端淬火深度的稳定性, 通常选用碳质量分数为0.2%左右,单独或复合添 加Ni、Cr、Mn、Mo等合金元素的渗碳合金钢[6]。日 本、德国在汽车高强度齿轮低碳合金钢材料领域进 行了长期的研究开发,表2为常用汽车齿轮材料的 成分组成,目前国内外汽车齿轮用钢主要为 20CrMnTi(国内)、20MnCrS(德系)、20CrMoH(日 系),表中钢种A、B、C为高疲劳用钢[7]。
1.00–1.30
20MnCrS (German)
0.17–0.22 ≤ 0.4 1.1–1.4 ≤ 0.025 0.02–0.04
1–1.3
20CrMoH (Japan)
0.20
0.25
0.73 0.030 0.030
1.05 0.20
Steel A
众所周知根据研究实践表明提高齿轮的疲劳强度寿命极限既需要改善优化材料的合金成分渗碳碳氮共渗热处理技术还必须与齿轮的表面强化处理技术的研究开发结合起来即实现综合的齿轮表面完整性得到更佳的齿轮抗疲劳性能才能实现对高强度齿轮接触疲劳极限弯曲疲劳极限疲劳耐久寿命最佳摩擦因数的高性能要求45
第 30 卷 第 1 期 2017 年 2 月
收稿日期:2016-10-13;修回日期:2017-01-07 网络出版日期:2017-01-19 08:39;网络出版地址:/kcms/detail/11.3905.TG.20170119.0839.002.html 通讯作者:陈勇(1954—),男(汉),教授,博士;研究方向:汽车变速器开发与高强度齿轮技术;E-mail:chenyong1585811@ 引文格式:陈勇, 臧立彬, 巨东英, 等. 高强度汽车齿轮表面强化技术的研究现状和发展趋势[J]. 中国表面工程, 2017, 30(1): 1-15.
高强度汽车齿轮表面强化技术的研究现状和发展趋势

Internal Combustion Engine&Parts0引言齿轮是汽车机械中传递动力的一个重要零件,其使用寿命及其强度与机械装置的优劣性是关系非常密切的。
随着社会的发展和进步,科技的日新月异,各行各业的人们对汽车的性能有着不同的要求,其要求不断提高,因此对齿轮的要求也就更加严格。
近几年来,各大汽车公司对汽车齿轮的研发都非常重视。
尤其日本、美国、英国、德国等国家提出了非常严格的市场规范。
齿轮需要具备较高的强度和速度,以及耐久、寿命长等特点。
这对齿轮的设计和改进提出了新的研究方向,也为开发新的材料和技术带来了新的任务。
其中,齿轮的表面强化技术是最关键的核心技术,全面提升齿轮的高强度是必要且重要的,需要进一步展开分析和研究。
1汽车齿轮材料技术及研究现状汽车齿轮在传递扭矩和改变速度过程中,往往处于高载荷的工作环境下。
这就在很大程度上要求汽车齿轮材料要具备很好的性能。
汽车中的齿轮处于长期连续负荷的工作状态,齿轮在工作的状态下,既要滚动使用,又需要滑动使用。
在转动的同时,还会受到脉冲的作用。
齿轮存在四种破坏的形式,齿轮被折断会受到破坏,齿轮的点蚀与微观点蚀,齿轮的磨损也会使齿轮受到破坏,齿面的胶合也是一个重要因素。
总体来说,汽车齿轮有四类破坏形式:①齿面胶合;②宏观点蚀、微观点蚀;③磨损;④轮齿折断。
轮齿的表面是非常重要的,轮齿表面要保持完整的状态,也就是不受到任何损伤,这样强化后能够决定表面的状态。
轮齿的表面涂改也是需要重视的,需要综合考虑厚度和强度等因素。
随着科技的进步,汽车的种类越来越多,对齿轮的要求也就越来越高。
所以,也应重视齿轮的材料。
基础材料有较高的质量,才能保障齿轮的质量和使用。
对———————————————————————作者简介:李文军(1990-),男,河北沧州人,助理工程师,研究方向为机械设计制造及其自动化。
的空气制动管路安装时,将卡套预装工作作为其重要组成部分,在不同的方式使用下,要予以不同问题的分析。
齿轮齿面强化方法概述
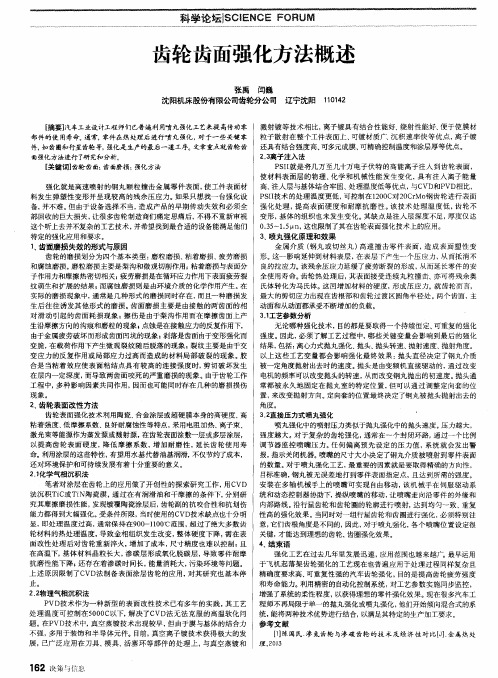
3 , 喷丸强化原理和效果
金 属介质 ( 钢丸 或 切丝丸 ) 高速 撞 击零 件表 面 , 造 成表 面塑 性 变
齿面磨损失效的形式与原因
特定 的强化应 用和 要求。
1
、
强化 就 是高速喷射 的钢 丸颗 粒撞击 金属 零 件表面 , 使 工件表 面材 高 、 注人层 与基 体结合 牢固、 处 理温度低等 优点 , 与c V D和P V D 相 比, P S I I 技术 的处理 温度 更低 , 可控制在 1 2 0 0 C 对2 0 C r Mo 钢 齿 轮进 行表 面 强 化处 理 , 提 高表 面硬 度 和耐 摩抗 磨 性 。 该 技术 处理 温 度低 , 齿 轮不
齿轮 的磨 损划分为 四个基 本 类型 : 磨粒 磨损、 粘 着磨损 、 疲劳磨 损 形 。 这一 影响延伸到材 料表层 , 在表 层下 产生一 个压 应力 , 从而抵消 不 和腐蚀磨 损。 磨 粒磨 损主要是梨 沟和微观切 削作用 ; 粘着磨 损与表 面分 良的拉应力。 该残余压 应力延缓了疲劳断 裂的形成, 从而延长零件 的安 子作用力和摩擦热密 切相关; 疲 劳磨 损是在循环应力作用下表面疲 劳裂 全使 用寿命。 齿 轮热 处理后 , 其表面接 受连 续丸粒 撞击、 亦可将 残余奥 纹萌生和扩展 的结果 ; 而腐 蚀磨 损则是 由环境 介质的化 学作用产 生。 在 氏体 转化为马 氏体 。 这 回增加 材料的硬 度 , 形成 压 应力。 就 齿轮而 言, 实际 的磨 损现象 中, 通常是几种 形式的磨 损同时存在 , 而且一种磨损 发 最 大的剪切应力出现在齿根部 和齿轮过 渡区圆角半径 处。 两个齿面 , 主 生后 往往诱 发其 他形式 的磨 损 齿面 磨损 主要是 由接触 的两齿 面的相 动面和从动面都承受不断增 加的负载。 对滑 动引起 的齿面 耗损 现象 ; 擦 伤 是 由于梨 沟作用而在 摩擦 齿面上 产 3 . 1 工艺参数 分析 生沿摩 擦方 向的沟痕 和磨粒的现象 ; 点蚀是在 接触应 力的反复作用下, 无论 哪种强化技 术, 目的都是要取得 一个持 续恒定 、 可重复 的强化 由于 金属疲劳破 坏而形成齿面 凹坑 的现象 ; 剥 落是齿面由于变 形强化而 强 度。 因此 , 必须 了解工 艺过程 中, 哪些关键 变量会 影响 到最后 的强化 变脆, 在 载荷作用下产生微 观裂纹 随后脱落 的现 象 ; 裂纹主要 是由于交 结果 , 包括 : 离心力式抛丸 强化 、 抛头、 抛头转速 、 抛射速度 、 抛射角度。 变应力 的反 复作 用或局 部应力 过高 而造成 的材料局 部破 裂 的现象 。 胶 以上这 些工艺变 量 都会 影响强化 最终 效果 : 抛头直径 决定了钢丸 介质 合 是 当粘 着效 应使 表面粘 结点具 有 较高 的连接 强度 时, 剪切破 坏发 生 被一定角度抛射 出去 时的速度 。 抛头 是由变 频机直 接驱动的 , 通过改变 在 层 内一定深 度, 而导致两 齿面 咬死 的严重磨 损的现象 。 由于齿 轮工作 电机 的频 率可以改变抛头 的转速 , 从而改变钢丸 抛出的初速度 。 抛头通 工程 中, 多种 影响 因素共同作用 , 因而也可 能同时存在 几种 的磨 损损 伤 常都 被永久 地 固定在 抛丸 室的特定位 置 , 但可 以通过调 整 定向套 的位 现象 。 置, 来改变抛射 方 向。 定向套的位置 最终决 定了钢丸被 抛头抛 射出去 的 2 齿 轮表 面 改性 方法 角度。
齿轮表面的喷丸强化技术
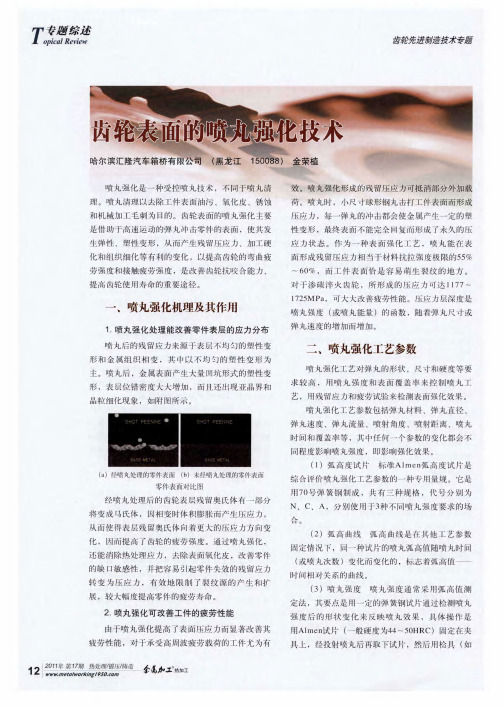
平均值
相对值
平 均值 38 . 5×l。 O
相对值 l0 O%
O7 .5×l。 10 0 0 %
间低 于 规 定 时 间时 ,可 以对 该 工 件再 进 行 一 次 补 充
强化
强化抛丸 ( ) 3 2 O 4 6 >5 6 O >l l 次 . ×l。 5 % 4 . ×l。 0 3%
3 提高 齿轮的疲劳 寿命 .
例3 :一 汽 采 用 强 化 喷 丸 工 艺 对 “ 放 ”牌 汽 解 车 变 速 器 一 挡齿 轮 进 行 疲 劳寿 命 试 验 ,显 著 提 高 了 齿 轮 的疲 劳 寿 命 ,如 表 1 示 。为 了提 高 “ 放 ” 所 解 牌 主 动 螺旋 齿 轮 的 疲 劳 寿命 采 用 大 圆弧 滚 刀切 齿 , 增 大 齿轮 圆角 可 以 使 主 动 螺 旋 齿 轮 的寿 命 由2 .3 08 万 次 提 高  ̄ 6 .4 次 ,如 果 再 采 用 强 化 喷 丸 ,可 1 95 万 1 以 使 其疲 劳 寿 命 提 高到 2 0 万 次 。 1. 9
A me N量 仪 )测量 弯 曲弧 的 高 度 。 l nI ] 喷 丸 强 度 的 另一 种 检 验 方 法 为 残 留应 力检 测 ,
速度达20r n 9 0/ ,弹 丸硬 度 为 5 HRC mi 7 。其 喷 丸试
验 结果 如 下 :
即对强化喷丸后的工件进行残留应 力的检测 ,具体
例4 齿轮 采 用 碳 氮 共 渗 后 喷 丸 强 化 ,提 高 了 : 接 触 疲 劳 强 度 。 如 S M4 0  ̄ 齿 轮 ,经 通 氨 气 等 C 2H 进 行 碳 氮 共 渗 , 随 着 含 氮 量 的 增 加 , △HV ( 硬 度 降 )提 高 ,即 抗 回火 性 能 提 高 , 回火 温 度 可 达 3 0 。解 决 了 汽车 用 自动 变 速 器AI 常 规 渗 碳 齿 0℃ T 轮 齿 面接 触 疲 劳 破坏 问题 。
表面强化技术改善机械零部件使用寿命的重要作用分析
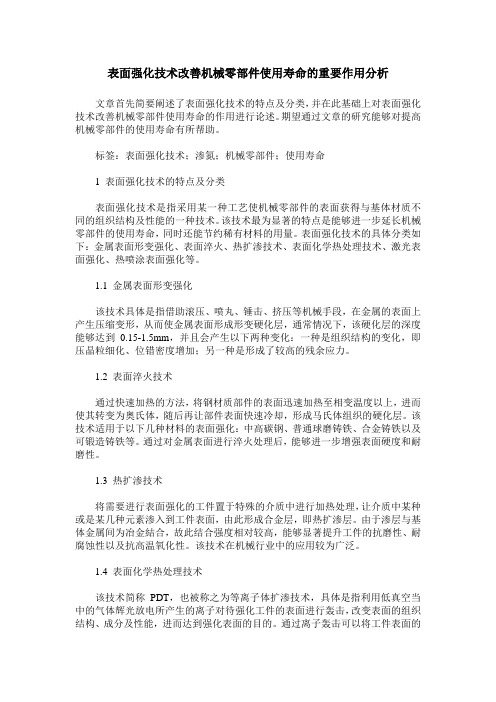
表面强化技术改善机械零部件使用寿命的重要作用分析文章首先简要阐述了表面强化技术的特点及分类,并在此基础上对表面强化技术改善机械零部件使用寿命的作用进行论述。
期望通过文章的研究能够对提高机械零部件的使用寿命有所帮助。
标签:表面强化技术;渗氮;机械零部件;使用寿命1 表面强化技术的特点及分类表面强化技术是指采用某一种工艺使机械零部件的表面获得与基体材质不同的组织结构及性能的一种技术。
该技术最为显著的特点是能够进一步延长机械零部件的使用寿命,同时还能节约稀有材料的用量。
表面强化技术的具体分类如下:金属表面形变强化、表面淬火、热扩渗技术、表面化学热处理技术、激光表面强化、热喷涂表面强化等。
1.1 金属表面形变强化该技术具体是指借助滚压、喷丸、锤击、挤压等机械手段,在金属的表面上产生压缩变形,从而使金属表面形成形变硬化层,通常情况下,该硬化层的深度能够达到0.15-1.5mm,并且会产生以下两种变化:一种是组织结构的变化,即压晶粒细化、位错密度增加;另一种是形成了较高的残余应力。
1.2 表面淬火技术通过快速加热的方法,将钢材质部件的表面迅速加热至相变温度以上,进而使其转变为奥氏体,随后再让部件表面快速冷却,形成马氏体组织的硬化层。
该技术适用于以下几种材料的表面强化:中高碳钢、普通球磨铸铁、合金铸铁以及可锻造铸铁等。
通过对金属表面进行淬火处理后,能够进一步增强表面硬度和耐磨性。
1.3 热扩渗技术将需要进行表面强化的工件置于特殊的介质中进行加热处理,让介质中某种或是某几种元素渗入到工件表面,由此形成合金层,即热扩渗层。
由于渗层与基体金属间为冶金結合,故此结合强度相对较高,能够显著提升工件的抗磨性、耐腐蚀性以及抗高温氧化性。
该技术在机械行业中的应用较为广泛。
1.4 表面化学热处理技术该技术简称PDT,也被称之为等离子体扩渗技术,具体是指利用低真空当中的气体辉光放电所产生的离子对待强化工件的表面进行轰击,改变表面的组织结构、成分及性能,进而达到强化表面的目的。
轮齿表面强化喷丸及应用

轮齿表面强化喷丸及应用
轮齿是机械中常见的传动部件,其表面强度决定了传动的可靠性和寿命。
为了增强轮齿表面的强度和耐磨性,常采用喷丸技术进行表面强化处理。
轮齿表面强化喷丸是通过喷射高速喷丸流体,将高速运动的颗粒冲击在轮齿表面上,产生压应力和塑性变形,进而提高其表面强度。
喷丸流体中常使用的颗粒材料包括钢球、圆锆砂等。
轮齿表面强化喷丸的应用主要体现在以下几个方面:
1. 提高轮齿的疲劳寿命:喷丸可以消除轮齿表面的应力集中,增加表面的压应力,有效提高轮齿的疲劳寿命,降低疲劳断裂的风险。
2. 增强轮齿的耐磨性:喷丸能够使轮齿表面形成一定的硬化层和压痕,提高轮齿的硬度和耐磨性,延长使用寿命。
3. 改善轮齿的齿面质量:通过喷丸可以去除轮齿表面的氧化物、油污和锈蚀物,使得轮齿表面更加平整和洁净,提高齿轮的精度和运行的平稳性。
4. 修复轮齿的缺陷:喷丸还可以修复轮齿表面的裂纹、腐蚀和磨损等缺陷,延长轮齿的使用寿命。
总之,轮齿表面强化喷丸可以有效提高轮齿的耐磨性、疲劳寿命和传动效率,提高机械传动系统的可靠性和寿命。
齿轮表面处理工艺

齿轮表面处理工艺
齿轮表面处理工艺是指通过对齿轮表面进行特定的加工、处理、涂覆、镀膜等工艺,以改善齿轮表面性能和使用寿命的一种技术方法。
齿轮表面处理工艺主要包括以下几种:
1. 硬化处理:齿轮表面硬化是指将齿轮表面加热至其临界温度以上,然后迅速冷却,使其表层硬度显著提高的一种表面处理方式。
硬化处理可以提高齿轮表面的耐磨性、疲劳寿命和承载能力。
2. 渗碳处理:齿轮表面渗碳是指在齿轮表面加热的同时,在其表面加入含有碳元素的气体或液体,使碳元素渗入齿轮表面,形成高碳化层,以提高齿轮表面的硬度、耐磨性和疲劳寿命。
3. 涂覆处理:齿轮表面涂覆是指在齿轮表面涂覆一层具有特定功能的涂层,如硅酸盐涂层、聚酰亚胺涂层、钼涂层等,以提高齿轮表面的耐磨性、防腐蚀性和摩擦特性。
4. 镀膜处理:齿轮表面镀膜是指在齿轮表面镀上一层金属或合金,如镀铬、镀镍、镀钨等,以提高齿轮表面的硬度、耐磨性和抗腐蚀性。
综上所述,齿轮表面处理工艺对于提高齿轮使用寿命和性能具有重要意义,不同的处理方式可根据具体应用场景和需求选择使用。
喷丸法使齿轮齿面得到强化的原理
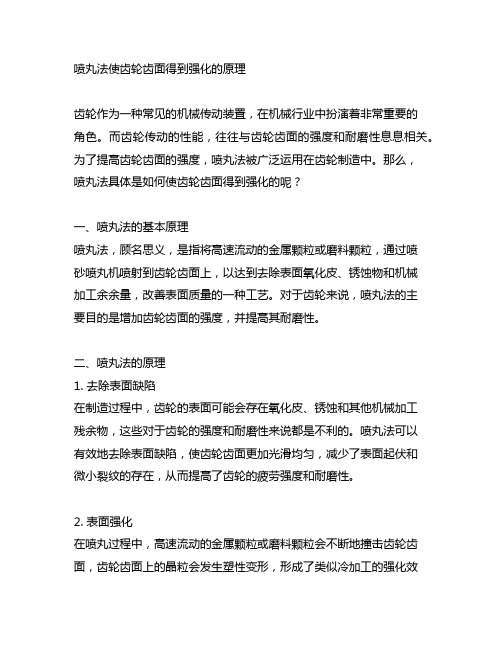
喷丸法使齿轮齿面得到强化的原理齿轮作为一种常见的机械传动装置,在机械行业中扮演着非常重要的角色。
而齿轮传动的性能,往往与齿轮齿面的强度和耐磨性息息相关。
为了提高齿轮齿面的强度,喷丸法被广泛运用在齿轮制造中。
那么,喷丸法具体是如何使齿轮齿面得到强化的呢?一、喷丸法的基本原理喷丸法,顾名思义,是指将高速流动的金属颗粒或磨料颗粒,通过喷砂喷丸机喷射到齿轮齿面上,以达到去除表面氧化皮、锈蚀物和机械加工余余量,改善表面质量的一种工艺。
对于齿轮来说,喷丸法的主要目的是增加齿轮齿面的强度,并提高其耐磨性。
二、喷丸法的原理1. 去除表面缺陷在制造过程中,齿轮的表面可能会存在氧化皮、锈蚀和其他机械加工残余物,这些对于齿轮的强度和耐磨性来说都是不利的。
喷丸法可以有效地去除表面缺陷,使齿轮齿面更加光滑均匀,减少了表面起伏和微小裂纹的存在,从而提高了齿轮的疲劳强度和耐磨性。
2. 表面强化在喷丸过程中,高速流动的金属颗粒或磨料颗粒会不断地撞击齿轮齿面,齿轮齿面上的晶粒会发生塑性变形,形成了类似冷加工的强化效应。
这种强化效应可以使齿轮齿面的硬度得到提高,从而增加了齿轮齿面的强度,延长了齿轮的使用寿命。
三、喷丸法的优势1. 高效性喷丸法是一种高效的表面处理工艺,能够在较短的时间内完成对齿轮齿面的处理,适用于批量生产。
2. 环保性相比于化学处理方法,喷丸法不需要使用大量的化学溶剂和腐蚀剂,减少了对环境的污染。
3. 经济性喷丸法在齿轮制造中的应用成本相对较低,且能够有效提高齿轮的使用性能,具有较高的性价比。
四、我的个人观点和理解喷丸法作为一种常见的表面处理工艺,对于齿轮齿面的强化具有非常重要的意义。
通过喷丸法的处理,不仅可以提高齿轮齿面的强度和耐磨性,延长其使用寿命,还可以改善齿轮的整体性能,提高传动效率。
在齿轮制造领域,喷丸法的应用前景十分广阔。
总结回顾:喷丸法通过去除表面缺陷、增强表面强度和改善表面质量,使得齿轮齿面得到了有效的强化,提高了其整体性能和耐久度。
齿轮表面硬化工艺

齿轮表面硬化工艺
齿轮是机械设备中常见的传动元件。
为了提高齿轮的使用寿命和
耐磨性,人们发明了齿轮表面硬化工艺。
下面将详细介绍该工艺的步骤。
第一步:准备工作
在进行齿轮表面硬化前,需要进行一些准备工作。
首先需要对齿
轮进行表面清洗,以确保齿轮表面不存在杂物和污渍。
然后需要对齿
轮表面进行研磨处理,以满足后续工艺的要求。
第二步:淬火处理
淬火是齿轮表面硬化的核心步骤。
在淬火前需要对齿轮进行预热
处理,以避免齿轮在淬火过程中出现变形或断裂。
预热温度要控制在500℃左右,时间要根据齿轮的材料和尺寸而定。
预热后,将齿轮放入
淬火介质中进行淬火处理。
淬火介质通常为油、水或盐酸等。
淬火过
程需要控制温度和时间,以确保齿轮表面硬度达到要求。
第三步:回火处理
淬火后的齿轮表面硬度很高,但同时也变得非常脆。
为了增加齿
轮的韧性和强度,需要进行回火处理。
回火温度一般在200~400℃之间,时间要根据齿轮的材料和硬度而定。
回火后,齿轮表面的硬度会下降,但韧性和强度会得到大幅提升。
第四步:清洗和检验
齿轮表面硬化过程结束后,还需要进行清洗和检验。
清洗可以将
残留的杂质和油污清除干净。
检验包括对齿轮表面硬度、硬化层深度、表面质量等方面进行检测,以确保齿轮的质量符合要求。
以上就是齿轮表面硬化工艺的步骤。
通过该工艺的处理,齿轮表
面的硬度、耐磨性和寿命都会得到大幅提升,从而为机械设备的长期
使用提供了保障。
表面强化技术PPT课件
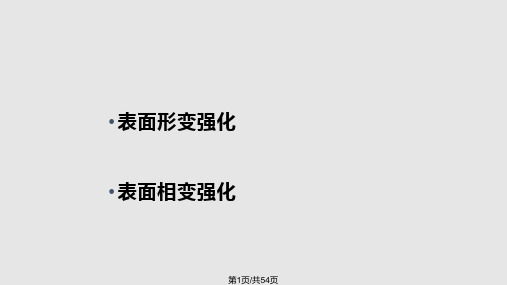
• 4.感应加热面淬火的应用
• (1)齿轮的表面淬火。齿轮一般用调质钢制 造,如45、40Cr钢经调质处理后进行表面淬 火,然后自回火得表面组织为隐晶回火M, 硬度54-58HRC,心部组织为回火S,硬度 20-25HRC。
•(2)机床导轨表面淬火。车床导轨由 HT320制造,原始组织为珠光体+细片状石 墨,导轨表面要求耐磨,因此用高频加热表 面 淬 火 , 获 得 马 氏第体38页+/共细54页片 状 石 墨 , 硬 度 提 高
• 表面形变强化 • 表面相变强化
第1页/共54页
• 原理 • 喷丸强化 • 表面滚压技术 • 孔挤压强化
第2页/共54页
一、原理
• 1.定义:是指在金属材料表面施加外力,使表面比较薄的一层发生塑性变形, 晶粒得到细化,从而提高零件表面疲劳强度和抗应力腐蚀能力的工艺手段。
• 2.机理: 加工硬化机理。即随变形量的增 加,金属强度硬度升高,塑性韧性下降。
(5)因为加热快,可以靠自冷淬火,工艺过程 简单,表面氧化倾向小。
• 2. 目的:使钢铁获得高的表面硬度和 压应力状态,从而提高其耐磨性和疲 劳强度。
• 特别适合承受弯曲、扭转、摩擦或冲 击的零件。
第28页/共54页
• 3、表面淬火用材料 • 含碳量为%%的中碳钢。 • 4、表面淬火后组织 • 表面:M回 • 心部:回火索氏体(调质处理)或铁素体+索氏体(正火)
为对飞机等重要大型结构件的表面进行表面无 损检测寻找疲劳裂纹和硬性损伤,首要的表面工 艺是退漆。传统的方法是使用化学剂剥离或用砂 轮手工打磨,这两种方法均存在不足之处。
塑料喷丸退漆是近年来发展起来的新工艺。其 原理为:颗粒状塑料在压缩空气的作用下.通过 喷管高速喷射到工件表面在塑料丸较锋利的棱角 切割和冲撞击打双重作用下使漆层表面发生割裂
齿轮激光淬火强化技术
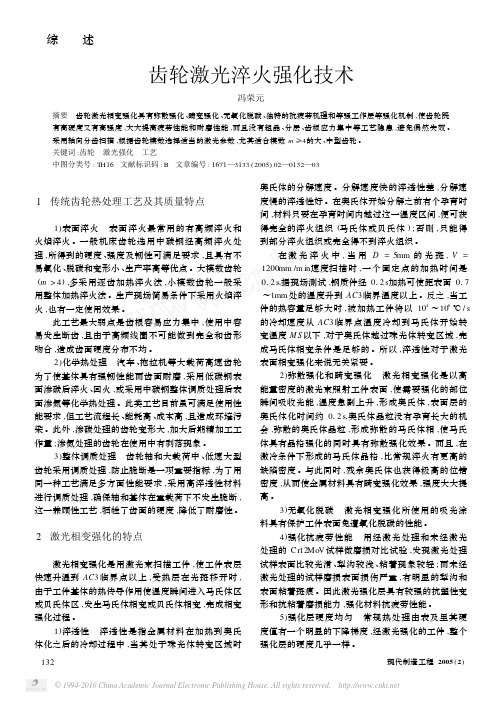
齿轮激光淬火强化技术冯荣元摘要 齿轮激光相变强化具有弥散强化、畸变强化、无氧化脱碳、独特的抗疲劳机理和等强工作层等强化机制,使齿轮既有高硬度又有高强度,大大提高疲劳性能和耐磨性能,而且没有粗晶、分层、齿根应力集中等工艺隐患,避免偶然失效。
采用轴向分齿扫描,根据齿轮模数选择适当的激光参数,尤其适合模数m≥4的大、中型齿轮。
关键词:齿轮 激光强化 工艺中图分类号:T H16 文献标识码:B 文章编号:1671—3133(2005)02—0132—031 传统齿轮热处理工艺及其质量特点1)表面淬火 表面淬火最常用的有高频淬火和火焰淬火。
一般机床齿轮选用中碳钢经高频淬火处理,所得到的硬度、强度及韧性可满足要求,且具有不易氧化、脱碳和变形小、生产率高等优点。
大模数齿轮(m>4),多采用逐齿加热淬火法,小模数齿轮一般采用整体加热淬火法。
生产现场简易条件下采用火焰淬火,也有一定使用效果。
此工艺最大弱点是齿根容易应力集中,使用中容易发生断齿,且由于高频线圈不可能做到完全和齿形吻合,造成齿面硬度分布不均。
2)化学热处理 汽车、拖拉机等大载荷高速齿轮为了使基体具有强韧性能而齿面耐磨,采用低碳钢表面渗碳后淬火、回火,或采用中碳钢整体调质处理后表面渗氮等化学热处理。
此类工艺目前虽可满足使用性能要求,但工艺流程长、能耗高、成本高,且造成环境污染。
此外,渗碳处理的齿轮变形大,加大后期精加工工作量;渗氮处理的齿轮在使用中有剥落现象。
3)整体调质处理 齿轮轴和大载荷中、低速大型齿轮采用调质处理,防止脆断是一项重要指标,为了用同一种工艺满足多方面性能要求,采用高淬透性材料进行调质处理,确保轴和基体在重载荷下不发生脆断,这一兼顾性工艺,牺牲了齿面的硬度,降低了耐磨性。
2 激光相变强化的特点激光相变强化是用激光束扫描工件,使工件表层快速升温到AC3临界点以上,受热层在光斑移开时,由于工件基体的热传导作用使温度瞬间进入马氏体区或贝氏体区,发生马氏体相变或贝氏体相变,完成相变强化过程。
- 1、下载文档前请自行甄别文档内容的完整性,平台不提供额外的编辑、内容补充、找答案等附加服务。
- 2、"仅部分预览"的文档,不可在线预览部分如存在完整性等问题,可反馈申请退款(可完整预览的文档不适用该条件!)。
- 3、如文档侵犯您的权益,请联系客服反馈,我们会尽快为您处理(人工客服工作时间:9:00-18:30)。
文件编号:GD/FS-1384
(解决方案范本系列)
关于齿轮表面强化技术分
析详细版
A Specific Measure To Solve A Certain Problem, The Process Includes Determining The Problem Object And Influence Scope, Analyzing The Problem, Cost Planning, And Finally Implementing.
编辑:_________________
单位:_________________
日期:_________________
关于齿轮表面强化技术分析详细版
提示语:本解决方案文件适合使用于对某一问题,或行业提出的一个解决问题的具体措施,过程包含确定问题对象和影响范围,分析问题,提出解决问题的办法和建议,成本规划和可行性分析,最后执行。
,文档所展示内容即为所得,可在下载完成后直接进行编辑。
在一系列机械传动系统中,齿轮发挥着十分关键的作用,是一类不可或缺的部件,所以,保证齿轮具有良好性能也便显得尤为重要了。
本文将基于齿轮表面强化技术展开相应的分析,包括传统技术、新技术以及复合技术等,以期为齿轮表面强化工作提供一些有益的参考。
齿轮表面强化概述
随着应用环境的日益复杂,人们对齿轮表面性能提出了更高要求,不仅要求其具有一定的硬度、耐磨性,还要求其具有理想的心部韧性以及抗腐蚀性等。
传统技术(渗碳等)开始难以满足实际需要,新的齿
轮表面强化技术(如激光加热表面淬火技术、喷丸技术、表面镀膜技术等)陆续出现,并得到了广泛应用。
齿轮表面强化技术
2.1.传统技术
以渗碳技术为例。
对于汽车用齿轮而言,其制作工艺相对简单,绝大部分以普通低碳钢、低碳合金钢这两种钢材为原材料,先经过渗碳淬火处理,再经过低温回火处理制作而成。
渗碳工艺通常在920-930℃这一温度条件下进行,能够在一个相对较短的时间内使得渗层达到既定深度。
接下来,先予以淬火处理,在经过低温回火处理,便能够在齿轮表面形成一层高碳马氏体,不仅强化了齿轮表面硬度,还提高了齿轮表面的耐磨性。
至于心部则为低碳马氏体,从而使其具有足够的韧性。
在齿轮表面强化处理中,渗
碳技术得到了广泛应用。
需要指出的是,渗碳技术具有一系列难以克服的缺点,如需要较高的处理温度,容易导致工件变形,无法获得较高的表面精度等,上述缺点的存在使得该技术的实际应用存在一定的制约。
当齿轮对自身表面硬度要求一般时,往往不采用该表面处理技术。
2.2.新技术
2.2.1.激光加热表面淬火技术
该技术诞生于上世纪七十年代,其代表性的应用为美国通用汽车公司采用这一技术对动力转向变速箱的内表面予以处理。
到上世纪八十年代中后期,激光加热表面淬火技术已经较为成熟,无论是理论发展,还是实际应用,均获得了空前发展。
所谓激光表面加热淬火技术指的是,将激光有效地聚集在一起,然后对相应的工件进行加热,使其表面组织在极短时间内
转变成奥氏体,自行冷却并最终在工件表面形成马氏体淬硬层。
对齿轮表面进行强化时,如果采用的是传统技术,那么在沿齿廓方向上通常无法形成呈均匀分布状态的硬化层,然而,采用激光加热表面淬火技术却能够很好地实现上述目的,除保证淬硬层呈均匀分布状态外,还能使其具有一个较高硬度。
2.2.2.喷丸技术
所谓喷丸技术指的是,利用相应的机械手段向工件表面施加一定的压力,使其受压变形,借助形变这种方式于工件表面生成硬化层(其深度范围通常为0.5-1.5mm)。
喷丸技术能够有效提高工件表面硬度以及强度,因而在金属表面改性加工中获得了广泛应用。
在科学技术的带动下,新的喷丸工艺不断涌现,主要包括:一、激光喷丸。
该技术能够实现对参数的有效控制,但存在残余应力偏大的缺憾;二、高
压水射流喷丸。
该技术有效解决了残余应力分布问题,因此,能够使得工件具有一个良好的周期抗疲劳强度;三、微粒冲击。
该技术借助微小弹丸的冲击以完成表面处理工作,能够大幅提高工件表面的实际硬度,与此同时,不会出现表面粗糙度过大的问题;
四、超声喷丸。
可对材料表面进行纳米化处理,还有助于氮化温度的有效降低。
喷丸技术不仅能够大幅强化工件的抗疲劳性能,还能够明显提升工件的抗腐蚀以及抗开裂能力,所以,在汽车齿轮表面强化方面得以广泛应用。
2.2.
3.表面镀膜技术
在生产技术不断提升的带动下,工业领域对薄膜所具有的性能提出了更高的要求,一方面要求膜、衬底之间具有良好的附着性,另一方面要求膜具有理想的硬度,同时还应具有厚度较深的特点。
为实现上述
要求,基于传统沉积技术的离子镀膜技术应运而生。
所谓离子镀膜技术指的是,在化学气相沉积领域有机引入低压气体放电技术,借助直流电场,或者是高频电场,又或者是微波场,给反应气体施加应的作用,使其发生辉光放电。
在那些具有低温性质的等离子体中,高能电子、反应气体这两种物质将会发生一系列非弹性碰撞,如此一来,导致反应气体分子发生电离或者激发效应,从而减少了化合物形态转化过程中所需要的能量,使得反应温度得以进一步降低,当温度降低时,便能够于工件表面形成理想的化合物涂层。
该技术的优势:一、镀膜操作时不需要过高温度,仅为500℃左右[3]
,如此一来,使得可用基材的选择范围得以大幅拓宽;二、形成的镀层不仅涂覆均匀,而且性能稳定,另外,技术支持工业化生产;三、对于离子体而
言,其渗、镀工艺能够同炉完成,从而有效简化了工艺,使得效率得以明显提高;四、其薄膜成分具有良好的可控性,因而便于梯度沉积的实现。
由于具有上述优点,该技术在那些对耐磨性有着较高要求的齿轮表面处理上得到了良好的应用。
2.3.复合强化技术
以传统技术和新技术的结合应用为例。
对工件予以“等离子渗氮+类金刚石膜”复合强化处理之后,无论在表面硬度方面,还是在膜/基结合强度方面,又或者是耐磨性能方面,均明显强于仅采用镀类金刚石膜的那一类工件。
氮化处理之后,将会于钢表面生成一定深度的硬化层,该硬化层为类金刚石膜提供了一个良好支撑体。
硬化层硬度的大幅增加,使得类金刚膜表面、钢基体之间存在一个明显的硬度梯度,如此一来,使得材料表面获得了更为优异的性能,如良
好的耐腐蚀性等。
类金刚膜能够有效强化工件表面的抗磨损性能。
这种复合强化技术能够对齿轮表面性能,尤其是耐磨性产生积极改善,所以,在齿轮表面强化方面具有理想的应用前景。
目前,在齿轮表面强化方面,复合强化技术具有十分明显的优越性,因而获得了人们的普遍认可。
越来越多的专家、学者开始致力于该领域的研究,相信不久的将来,复合强化技术将会在齿轮表面强化领域发挥出更大的作用。
可在这里输入个人/品牌名/地点
Personal / Brand Name / Location Can Be Entered Here。