废旧轮胎橡胶的裂解处理工艺
轮胎裂解工艺介绍

微负压热裂解处理废旧轮胎技术与设备“微负压热裂解”技术,把废旧轮胎处理产生四种产品:燃料油、ECO 炭黑、钢丝和可燃性气体。
公司年处理废旧轮胎的能力为10000 吨,可产生燃料油4500 吨,ECO 炭黑3500 吨,钢丝1000 吨和可燃性气体1000 吨。
除了很少量的气体排放外,没有其他的废物排放。
通过处理废旧轮胎所获得的ECO 炭黑,由于质量可靠,成本低,目前已经被国内10 多家轮胎生产企业用做轮胎的生产原料,这样就形成了废轮胎-ECO 炭黑-轮胎的产业链循环,而目前生产上绝大多数的炭黑是通过石油提炼出来的。
此外,废旧轮胎热裂解产生的燃料油如果再进行深加工,还可以进一步加工成汽油、柴油和沥青。
本项技术如果能够在全国得到大力推广,不单可以有效的处理废旧轮胎,消除污染,还可以从一定程度上缓解我国的能源危机。
技术与设备无剥离、微负压热裂解废旧轮胎处理技术解决了其他的热裂解技术处理废旧轮胎存在的问题,在以下几个关键技术和设备制造方面获得成功:1、采用无剥离技术在热裂解前不需要将橡胶与钢丝分离,从而降低了能耗,大幅度提高了经济效益。
2、采用微负压热裂解技术热裂解采用微负压工艺技术,确保在生产过程中气体不外溢,提高热裂解效率,从根本上消除了由于气体外溢而引起的不安全隐患。
3、采用无氧(或贫氧)热裂解技术热解炉采用先进、出料密封系统,改善了炉体的密封性能,使废轮胎胶粒处于无氧(或贫氧)状态下裂解。
这不仅减少了能源的损失,还使热解炉的安全生产有了保障。
4、采用了高效率的可燃性气体回收技术在生产过程中,橡胶经热裂解后,大部分变成液体油品,少量的可燃性气体循环作为热解炉的燃料使用。
从而保证了热解炉的热能供应,减少了废气排放,提高了经济效益和环境效益。
5、成套设备的标准化设计一套自动化、标准化设备包括两条热裂解生产线,年处理能力为1万吨(约120万条轿车轮胎)。
热裂解生产线由破碎系统、进料系统、热裂解处理系统、油品处理系统、尾气回收处理系统、水循环系统、炭黑处理系统以及湿法炭黑造粒包装系统等八大系统组成。
轮胎裂解技术

3工程分析3.1工艺原理简述本项目的核心工艺为废轮胎的热裂解处理工艺。
轮胎主要由橡胶(包括天然橡胶、合成橡胶)、炭黑及多种有机、无机助剂(包括增塑剂、防老剂、硫磺和氧化锌等)组成。
废轮胎的热裂解是指在无氧或缺氧工况及适当的温度下,橡胶中主链具有不饱和键的高分子断裂,产物主要是单体、二聚物和碎片,生成物再聚合为多种烯烧,从而脱出挥发性物质并形成固体炭的过程,其产物主要是燃料油、裂解气等可贮存性能源和炭黑、钢丝,各产物成分随热解方式、热解温度等变化而不同。
裂解方程式如下:(-CH2-CH2-) 11 —► n[C+H2+CH4+C2H6+C3H8+C4Hio+C5Hi2+- • -+C11H24+* * -C20H42+- * -](说明:C5H12〜C11H24为汽油饰分,C12H26-C20H42为柴油镉分,C20以上为重油)本项目轮胎热解温度为200〜450°C,热解炉采用炉外加热、微负压、贫氧热裂解工艺操作,炉体密闭,在生产过程中确保气体不外泄,提高热裂解效率,同时从根本上消除了生产过程中由于气体外泄而引起的不安全隐患和二次污染。
3.2生产工艺流程本项目主要原料为外购的干净废旧轮胎(每条己切成4〜5块),无需清洗、破碎、抽钢丝等预处理工序,直接经人工进料进入裂解炉内,进料工段约2小时,每台设备每天进料10J 裂解炉内是一个持续升温的环境,炉体内部在4小时内升温至200-300°C, 此时裂解气开始处于稳定生成状态,接下來的5〜8小时内温度缓慢爬升,当温度到达450°C 时,可认为轮胎裂解己基本完成。
裂解过程中产生大量烟气,其成分主要包含重油(液态)、轻油(气态)、裂解气和少量水蒸气等,烟气经管道流入分汽包。
在分汽包内,重油(约占废轮胎质量的2%)下沉至渣油罐,通过油泵储存在储油罐内;气态成分经管道进入循环水冷却系统。
在管道内冷却后的烟气分为液体和气体,其中气体为裂解气,液体为轻油和水的混合物。
轮胎裂解技术

3 工程分析3.1 工艺原理简述本项目的核心工艺为废轮胎的热裂解处理工艺。
轮胎主要由橡胶(包括天然橡胶、合成橡胶)、炭黑及多种有机、无机助剂(包括增塑剂、防老剂、硫磺和氧化锌等)组成。
废轮胎的热裂解是指在无氧或缺氧工况及适当的温度下,橡胶中主链具有不饱和键的高分子断裂,产物主要是单体、二聚物和碎片,生成物再聚合为多种烯烃,从而脱出挥发性物质并形成固体炭的过程,其产物主要是燃料油、裂解气等可贮存性能源和炭黑、钢丝,各产物成分随热解方式、热解温度等变化而不同。
裂解方程式如下:(-CH2-CH2-)n n[C+H2+CH4+C2H6+C3H8+C4H10+C5H12+…+C11H24+…C20H42+…] (说明:C5H12~C11H24为汽油馏分,C12H26~C20H42为柴油馏分,C20以上为重油)本项目轮胎热解温度为200~450℃,热解炉采用炉外加热、微负压、贫氧热裂解工艺操作,炉体密闭,在生产过程中确保气体不外泄,提高热裂解效率,同时从根本上消除了生产过程中由于气体外泄而引起的不安全隐患和二次污染。
3.2 生产工艺流程本项目主要原料为外购的干净废旧轮胎(每条已切成4~5块),无需清洗、破碎、抽钢丝等预处理工序,直接经人工进料进入裂解炉内,进料工段约2小时,每台设备每天进料10t。
裂解炉内是一个持续升温的环境,炉体内部在4小时内升温至200~300℃,此时裂解气开始处于稳定生成状态,接下来的5~8小时内温度缓慢爬升,当温度到达450℃时,可认为轮胎裂解已基本完成。
裂解过程中产生大量烟气,其成分主要包含重油(液态)、轻油(气态)、裂解气和少量水蒸气等,烟气经管道流入分汽包。
在分汽包内,重油(约占废轮胎质量的2%)下沉至渣油罐,通过油泵储存在储油罐内;气态成分经管道进入循环水冷却系统。
在管道内冷却后的烟气分为液体和气体,其中气体为裂解气,液体为轻油和水的混合物。
液体流入油水分离器,分离出的轻质油分经油泵进入油罐储存,少量含油废水经雾化后喷入裂解炉燃烧室作为燃料使用;裂解气经管道输送至裂解炉燃烧室作为燃料使用。
废旧轮胎橡胶的裂解处理工艺
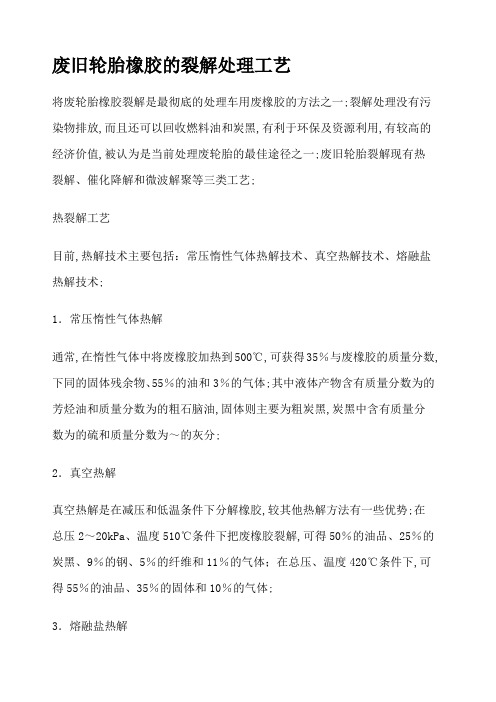
废旧轮胎橡胶的裂解处理工艺将废轮胎橡胶裂解是最彻底的处理车用废橡胶的方法之一;裂解处理没有污染物排放,而且还可以回收燃料油和炭黑,有利于环保及资源利用,有较高的经济价值,被认为是当前处理废轮胎的最佳途径之一;废旧轮胎裂解现有热裂解、催化降解和微波解聚等三类工艺;热裂解工艺目前,热解技术主要包括:常压惰性气体热解技术、真空热解技术、熔融盐热解技术;1.常压惰性气体热解通常,在惰性气体中将废橡胶加热到500℃,可获得35%与废橡胶的质量分数,下同的固体残余物、55%的油和3%的气体;其中液体产物含有质量分数为的芳烃油和质量分数为的粗石脑油,固体则主要为粗炭黑,炭黑中含有质量分数为的硫和质量分数为~的灰分;2.真空热解真空热解是在减压和低温条件下分解橡胶,较其他热解方法有一些优势;在总压2~20kPa、温度510℃条件下把废橡胶裂解,可得50%的油品、25%的炭黑、9%的钢、5%的纤维和11%的气体;在总压、温度420℃条件下,可得55%的油品、35%的固体和10%的气体;3.熔融盐热解将轮胎碎块浸入氯化锂/氯化钾的低共熔混合物中,加热至500℃,产生47%的油、45%的固体残余物和12%的气体;油中大约包括质量分数为的芳烃油、质量分数为的链烯烃和质量分数为的石脑油;残余物中有炭黑类似物以及轮胎中未发生变化的纤维和钢丝成分;气体为C1~C4的石脑油和链烯烃混合物;催化降解工艺采用路易斯酸熔融盐催化剂进行废轮胎橡胶降解的方法,反应迅速;催化剂以氯化锌、氯化锡和碘化锑效果最佳;当采用质量分数为的锌和钴盐作为催化剂,混入废橡胶料中,可以使液体油、气体产品中的总硫量至少降低40%,液体产品中的总氮量降低50%;为提高相对分子质量较小的C1~C4烯烃的回收率,可在废橡胶中加入碱金属或碱土金属碳酸盐,这种催化剂在转化时,对增大异丁烯质量分数效果尤其明显;微波解聚工艺废轮胎微波解聚的微波发生装置的频率为2450MHz,输入功率为1100W,输出功率为580W;将已被破碎成5~10kg的块状废轮胎盛入容器中,再将容器放入微波发生器内,导入氮气,施加微波后,废轮胎块从内部发热,数十秒内废橡胶急速分解,局部热分解产生的有机气体从橡胶发生龟裂处喷射出来;分解后,炭黑残留原处并形成局部堆积,由于炭黑吸收微波,在连续施加微波的情况下碳黑变得赤热,加剧有机成分的排出,数分钟内废轮胎橡胶就会变为以炭黑为主体的黑色粉末;生成气体由导出管导出,经过三个冷却收集器,将气体和液状物分离;解聚生成物中油、气占50%以上,碳占40%左右;废轮胎热裂解流程及产品用途通常废轮胎热裂解工厂的生产流程主要包括4个部分,包括原料预制系统、热裂解反应器系统、气-油回收分离系统、固体回收系统;。
废轮胎的热裂解处理工艺工程化分析

第46卷 第13期·46·作者简介:康永(1981-),男,研究生,工程师。
现从事复合材料研究工作。
收稿日期:2019-10-29(3)裂解气燃烧废气(G3)a.裂解气的性质轮胎在不同的裂解温度下产生的热解气成分不同,可以用一、二次反应理论来阐释:当热解温度较低时,废轮胎首先发生生成大分子脂肪烃类(主要为烯烃)的一次反应;热解温度较高或停留时间较长时,一次反应产物继续发生二次反应,二次反应有两个方向,一是生成小分子气态烃的裂化反应,另一种是生成芳香烃、大分子缩合焦状物质的芳香环化反应,甲烷和氢气为芳香环化反应的副产物。
热解温度在较低的450 ℃时,热解产物主要为一次反应产物,即氢气、甲烷、乙烷、乙烯等低分子烃类浓度较低,而丁烷、戊烷等大分子烃类浓度较高。
对轮胎回转窑450 ℃的裂解气成分分析,裂解气的主要组分如表9所示。
由表9可知,轮胎热解气主要为烃类,另外还有少量的CO 、NO 、CO 2和 H 2S 。
烃类组分主要为甲烷,NOX 主要以NO 的形式存在, H 2S 的含量较低,热解气可视为一种较清洁的燃料。
b.裂解气燃烧废气源强项目轮胎热裂解共产生裂解气3 000 t/a ,其中2 350 t/a 供给裂解炉燃烧室燃烧,剩余650 t/a 进废气燃烧室燃烧掉。
项目采用风机鼓风的方式促使裂解气完全燃烧,根据裂解气成分可知,燃烧产物的主要成分是 H 2O 、CO 2、NOx 、SO 2,除此之外,由于可能存在一定比例的裂解气无法完全燃烧,燃烧废气中还可能含有颗粒物、烃类、硫化氢等污染物。
上海绿人生废轮胎的热裂解处理工艺工程化分析康永(榆林市瀚霆化工技术开发有限公司, 陕西 榆林 718100)摘要:本文介绍了废轮胎热裂解工艺流程以及裂解原理,并按照项目预先设计的处理量计算了体系的物料平衡和热量平衡。
对项目运营期的主要污染因素进行了分析,提出了具体的防治措施。
关键词:工程化分析;工艺流程;裂解原理;物料平衡;热量平衡;污染因素中图分类号:TQ330.9文章编号:1009-797X(2020)15-0046-05文献标识码:B DOI:10.13520/ki.rpte.2020.15.011态经济科技有限公司在上海市奉贤区建立了废旧轮胎综合利用与资源化示范基地,目前该工厂运行情况良好。
轮胎炼油的原理

轮胎炼油的原理
轮胎炼油的原理主要基于热裂解技术,这是一种在无氧或缺氧条件下对废弃轮胎进行高温分解的过程。
具体步骤如下:
1.预处理阶段:废旧轮胎首先经过切割、破碎等预处理过程,以便减小体积并提高物料与反应介质的接触面积。
2.热裂解阶段:预处理后的轮胎碎片送入到密封的热裂解反应器中,在严格的控制下加热到300-600摄氏度(甚至更高),这个过程中不引入氧气或只维持极低的含氧量,以防止燃烧而是促使橡胶中的大分子化合物发生热裂解反应。
3.化学反应:在高温下,轮胎橡胶中的高分子链(主要是含有碳氢元素的长链结构)断裂成较小的分子,包括烃类(如汽油、柴油、重油等)、气体(如甲烷、乙烯、丙烯等)和固体残渣(主要是炭黑和钢丝)。
4.产物收集:
气体产物通过冷却系统冷凝后得到液态燃料油。
轻质气态烃可以直接作为能源使用或进一步提纯处理。
固体炭黑可以回收利用于橡胶制品、颜料等行业。
钢丝可通过磁选等方式分离出来,作为金属原料回收。
5.环保措施:该过程中需要配备环保设施,确保有害物质如硫化物、多环芳烃等得到有效处理和排放达标。
总之,轮胎炼油是将不可降解的废轮胎转化为有价值的能源和资源的一种方式,实现了废弃物的资源化利用,但同时由于可能产
生污染,必须严格遵守相关环保法规和技术标准进行操作。
废旧轮胎橡胶的裂解处理工艺
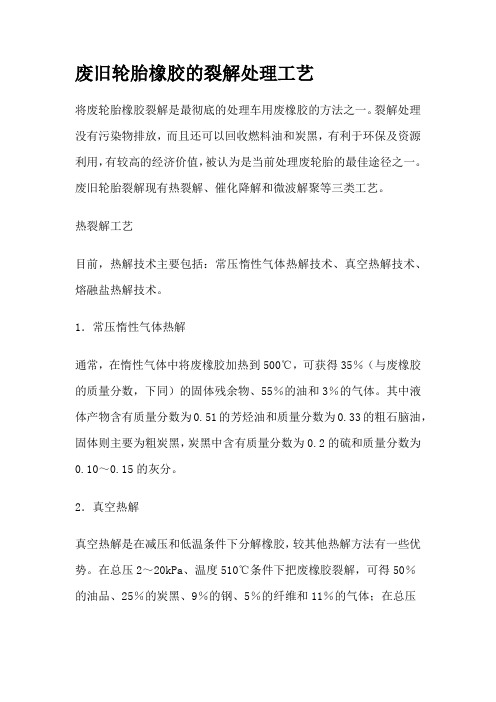
废旧轮胎橡胶的裂解处理工艺将废轮胎橡胶裂解是最彻底的处理车用废橡胶的方法之一。
裂解处理没有污染物排放,而且还可以回收燃料油和炭黑,有利于环保及资源利用,有较高的经济价值,被认为是当前处理废轮胎的最佳途径之一。
废旧轮胎裂解现有热裂解、催化降解和微波解聚等三类工艺。
热裂解工艺目前,热解技术主要包括:常压惰性气体热解技术、真空热解技术、熔融盐热解技术。
1.常压惰性气体热解通常,在惰性气体中将废橡胶加热到500℃,可获得35%(与废橡胶的质量分数,下同)的固体残余物、55%的油和3%的气体。
其中液体产物含有质量分数为0.51的芳烃油和质量分数为0.33的粗石脑油,固体则主要为粗炭黑,炭黑中含有质量分数为0.2的硫和质量分数为0.10~0.15的灰分。
2.真空热解真空热解是在减压和低温条件下分解橡胶,较其他热解方法有一些优势。
在总压2~20kPa、温度510℃条件下把废橡胶裂解,可得50%的油品、25%的炭黑、9%的钢、5%的纤维和11%的气体;在总压0.3kPa、温度420℃条件下,可得55%的油品、35%的固体和10%的气体。
3.熔融盐热解将轮胎碎块浸入氯化锂/氯化钾的低共熔混合物中,加热至500℃,产生47%的油、45%的固体残余物和12%的气体。
油中大约包括质量分数为0.21的芳烃油、质量分数为0.34的链烯烃和质量分数为0.45的石脑油。
残余物中有炭黑类似物以及轮胎中未发生变化的纤维和钢丝成分。
气体为C1~C4的石脑油和链烯烃混合物。
催化降解工艺采用路易斯酸熔融盐催化剂进行废轮胎橡胶降解的方法,反应迅速。
催化剂以氯化锌、氯化锡和碘化锑效果最佳。
当采用质量分数为0.01的锌和钴盐作为催化剂,混入废橡胶料中,可以使液体油、气体产品中的总硫量至少降低40%,液体产品中的总氮量降低50%。
为提高相对分子质量较小的C1~C4烯烃的回收率,可在废橡胶中加入碱金属或碱土金属碳酸盐,这种催化剂在转化时,对增大异丁烯质量分数效果尤其明显。
废旧轮胎热解与裂解方案

废旧轮胎热解与裂解方案废旧轮胎回收综合利用的管理策略是确保整个回收系统顺利运行和有效利用资源的重要保障。
管理策略包括政策法规制定、监管机制建立、市场机制引导、技术创新推广等方面。
还需要加强与相关产业和部门的合作,形成联合力量,共同推动废旧轮胎回收综合利用工作的开展。
废旧轮胎回收综合利用研究不仅对环境具有重要意义,还能够带来显著的经济效益。
废旧轮胎的回收和加工可以创造就业机会,促进产业链上下游的协同发展。
废旧轮胎的再利用也可以降低生产成本,提高资源利用效率,增加企业的竞争力。
废旧轮胎回收综合利用研究还能够推动相关技术的创新和发展,促进产业升级和转型,为社会经济的可持续发展做出贡献。
废旧轮胎是一种常见的废弃物,由于其体积庞大、不易降解以及存在环境污染的风险,对于废旧轮胎的回收综合利用具有重要的现实意义。
废旧轮胎回收综合利用研究的目的在于寻找有效的处理方法,最大限度地减少对环境的污染,并实现资源的可持续利用。
随着全球经济的快速发展和人口的增加,废旧轮胎问题日益突出。
传统的废旧轮胎处理方式主要是填埋和焚烧,但这些方式会导致严重的环境问题,如土壤和水源的污染,大气中有害物质的释放等。
因此,回收和综合利用废旧轮胎成为全球各国的共同关注点。
废旧轮胎回收综合利用可以减少废弃轮胎对环境的污染。
废旧轮胎中的橡胶、钢丝等材料在自然环境中难以降解,会导致土壤和水源的污染,危害生态系统的平衡。
通过回收综合利用,可以将废旧轮胎中的有害物质进行处理和转化,减少对环境的污染,保护生态环境的可持续发展。
本文内容信息来源于公开渠道,对文中内容的准确性、完整性、及时性或可靠性不作任何保证。
本文内容仅供参考与学习交流使用,不构成相关领域的建议和依据。
一、废旧轮胎回收综合利用发展方向(一)加强废旧轮胎回收体系建设废旧轮胎回收是解决环境污染和资源浪费的关键环节,因此需要加强废旧轮胎回收体系的建设。
首先,要完善回收网点的布局,增加回收站点的数量和覆盖范围,使废旧轮胎回收更加便捷。
轮胎裂解工艺技术
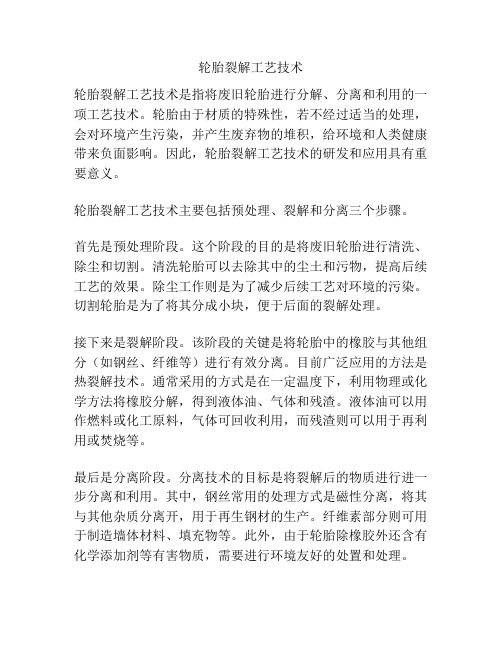
轮胎裂解工艺技术轮胎裂解工艺技术是指将废旧轮胎进行分解、分离和利用的一项工艺技术。
轮胎由于材质的特殊性,若不经过适当的处理,会对环境产生污染,并产生废弃物的堆积,给环境和人类健康带来负面影响。
因此,轮胎裂解工艺技术的研发和应用具有重要意义。
轮胎裂解工艺技术主要包括预处理、裂解和分离三个步骤。
首先是预处理阶段。
这个阶段的目的是将废旧轮胎进行清洗、除尘和切割。
清洗轮胎可以去除其中的尘土和污物,提高后续工艺的效果。
除尘工作则是为了减少后续工艺对环境的污染。
切割轮胎是为了将其分成小块,便于后面的裂解处理。
接下来是裂解阶段。
该阶段的关键是将轮胎中的橡胶与其他组分(如钢丝、纤维等)进行有效分离。
目前广泛应用的方法是热裂解技术。
通常采用的方式是在一定温度下,利用物理或化学方法将橡胶分解,得到液体油、气体和残渣。
液体油可以用作燃料或化工原料,气体可回收利用,而残渣则可以用于再利用或焚烧等。
最后是分离阶段。
分离技术的目标是将裂解后的物质进行进一步分离和利用。
其中,钢丝常用的处理方式是磁性分离,将其与其他杂质分离开,用于再生钢材的生产。
纤维素部分则可用于制造墙体材料、填充物等。
此外,由于轮胎除橡胶外还含有化学添加剂等有害物质,需要进行环境友好的处置和处理。
轮胎裂解工艺技术的发展,不仅可以实现对废旧轮胎的有效处理和资源利用,还可以减少环境污染,并为经济发展提供新的动力。
与传统的焚烧和填埋等处理方式相比,轮胎裂解工艺技术具有高效、无污染、资源化利用的特点。
在实际应用中,轮胎裂解工艺技术还存在一些挑战和问题,如产能规模、技术成本和废弃物的后续处理等方面。
因此,需要加大对轮胎裂解技术的研发投入,提高工艺技术的稳定性和经济性,完善相关政策和标准的制定,促进轮胎资源化利用的可持续发展。
总之,轮胎裂解工艺技术是一项重要的环保技术,具有重大的社会和经济价值。
通过合理的工艺流程,可以将废旧轮胎转化为再生资源,促进可持续发展,减少资源浪费和环境污染。
废旧轮胎处理工艺流程
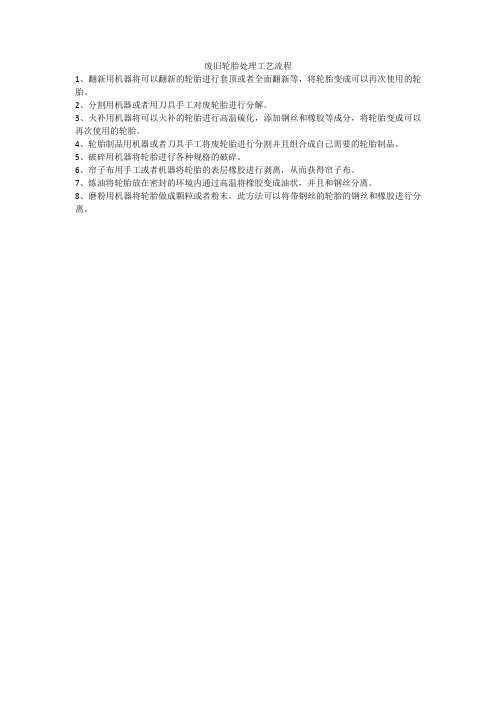
废旧轮胎处理工艺流程
1、翻新用机器将可以翻新的轮胎进行套顶或者全面翻新等,将轮胎变成可以再次使用的轮胎。
2、分割用机器或者用刀具手工对废轮胎进行分解。
3、火补用机器将可以火补的轮胎进行高温硫化,添加钢丝和橡胶等成分,将轮胎变成可以再次使用的轮胎。
4、轮胎制品用机器或者刀具手工将废轮胎进行分割并且组合成自己需要的轮胎制品。
5、破碎用机器将轮胎进行各种规格的破碎。
6、帘子布用手工或者机器将轮胎的表层橡胶进行剥离,从而获得帘子布。
7、炼油将轮胎放在密封的环境内通过高温将橡胶变成油状,并且和钢丝分离。
8、磨粉用机器将轮胎做成颗粒或者粉末,此方法可以将带钢丝的轮胎的钢丝和橡胶进行分离。
轮胎裂解设备工艺操作流程

轮胎裂解设备工艺操作流程轮胎裂解是指将废旧轮胎进行高温处理,将轮胎内部的橡胶材料分解成小分子油气和碳黑等物质的过程。
以下是轮胎裂解设备的工艺操作流程:1.主要设备准备首先需要准备好轮胎裂解设备,包括反应器、加热炉、冷却系统、凝析器、气体分离系统等。
确保各个设备正常运行和连接。
2.原料准备准备好待处理的废旧轮胎,并根据需要对轮胎进行预处理,例如剪断轮胎为适合入料的大小块状物。
3.裂解反应将预处理后的轮胎块装入反应器中,封闭反应器并将反应器加热至一定温度。
利用反应器内部的真空环境和高温,使轮胎内部的橡胶材料发生热解反应,生成油气和碳黑等产物。
4.油气分离经过一段时间的裂解反应后,反应器中的油气产物会通过凝析器进一步分离。
将凝析器与反应器连接,并设置一定的温度和压力,以使油气产物冷凝成液体和气体相,进而分离。
5.液体处理将凝析器中分离出的液体油产品进行处理。
首先将液体油进行脱气处理,去除部分气体。
然后,通过沉淀、过滤、脱色等过程,去除杂质和不纯物质,提炼出纯净的轮胎油。
6.气体处理经过凝析器的气体产物需要进行进一步处理和利用。
首先,将气体中的碳黑和其他固体颗粒物质进行过滤和分离。
然后,通过气体分离系统,将气体中的可利用物质(例如可燃气体)与废气等进行分离,以获得高价值的产物。
7.废渣处理轮胎裂解反应后,会产生一定量的固体废渣,包括未经裂解的固体材料和碳黑等。
这些废渣需要进行安全处理和处置,以减少环境污染。
通常可以采取填埋、焚烧或回收利用等方法进行废渣处理。
8.产品收集与贮存最后,根据需要,将通过轮胎裂解设备得到的纯净的轮胎油和其他产物进行收集和储存。
可以使用贮罐、容器等器材进行产品的暂存和储存。
以上所述是一般的轮胎裂解设备的工艺操作流程,具体操作流程可能因设备型号和生产工艺的不同而有所差异。
在进行轮胎裂解操作时,还应注意安全环保,确保设备的正常运行和产品的质量。
废旧轮胎裂解炼油工艺原理及设备简介

废旧轮胎是五大固废之一,其回收利用一直是循环经济不可或缺的重要领域。
废旧轮胎不具有生物降解性,大量积压对自然环境形成占用和巨大破坏,而且堆积也容易引起火灾,造成二次污染。
轮胎裂解是将废旧轮胎投放到高温常压裂解釜中,加入催化剂后对废轮胎加热进行催化裂解,从而产生轮胎油、炭黑、钢丝和不凝气,轮胎油主要用于燃料或者经过炼油厂提炼后获得汽油和柴油,目前市场上的轮胎油多数直接用作燃料使用。
废轮胎制备燃料油采用回转窑热解技术,废轮胎回转窑热解技术较其它工艺更为广泛,回转窑热解炉优势在于对废轮胎进料粒径破碎程度要求低, 而且热解炭性质十分均匀,不需要高负压,而是采用风机引起的微负压条件,生产稳定,设备投入小,收益快,是目前应用较为广泛的一种生产工艺。
废轮胎裂解炼油基本流程:将废轮胎放进裂解斧中,加热升温,脱水,然后升温,轮胎融化然后气化,经冷凝器冷凝,分离器分离,振荡过滤可获得液体轮胎油。
一、废轮胎裂解炼油详细介绍:1. 进料进料即将废轮胎投入到裂解斧中,此过程可以人工进料、平板输送机进料和液压进料机进料等方式,较新工艺工厂通常采用液压进料机进料,因其生产效率高,节省人力,不用冷却裂解釜缩短生产周期,同时环保等优点而被众多工厂广泛采用。
2.裂解气化废轮胎投入到裂解斧中,然后加热升温裂解斧,使裂解斧中的温度逐渐升至100℃,此过程中废轮中的水分及小分子物质会挥发,然后析出沉降至分离器中放出,随着水分及小分子物质逐渐挥发完全,裂解斧中的温度就会继续上升,达到140℃时,废轮胎开始融化成液态,打开转动,使得转炉转动,温度继续升高,已经融化的轮胎会随着温度的升高而逐渐气化,等裂解斧中的温度上升到260℃-280℃时,然后维持6-12h(根据气化情况而定),此时压力在1.2kg/㎡,直到完全气化,气化的气体会到冷凝器中冷凝。
3.燃烧油冷凝经裂解斧气化的气体,经过离心分离器去除灰尘等杂质,然后进入粗口经、直通式冷凝器中冷却,经冷凝器冷却获得的液体油进入毛油储罐,然后经油泵打入振动过滤机中过滤,进一步去除杂质,可获得成品油。
轮胎高温裂解工艺

轮胎高温裂解工艺一、引言轮胎高温裂解工艺是一种利用高温条件将废旧轮胎转化为能源和化工产品的环保技术。
本文将对轮胎高温裂解工艺进行详细介绍,包括工艺原理、工艺流程以及产品应用等方面。
二、工艺原理轮胎高温裂解工艺是利用高温条件下轮胎中的橡胶和其他有机物质发生热分解,生成可燃气体和液体油品的一种工艺。
在高温条件下,轮胎中的橡胶会发生热裂解,生成大量的气体和液体产物。
其中,气体主要为可燃气体,如甲烷、乙烷等,可用于发电或供热;液体产物主要为液体油品,如轻油、重油等,可用于化工原料或燃料。
三、工艺流程轮胎高温裂解工艺一般包括预处理、热裂解、气体分离和液体处理等步骤。
具体的工艺流程如下:1. 预处理:将废旧轮胎进行切割或破碎,并去除其中的金属和纤维材料,以减少后续工艺中的干扰和污染。
2. 热裂解:将经过预处理的轮胎送入热裂解反应器中,通过加热使其达到高温条件。
在高温下,轮胎中的橡胶和其他有机物质发生热分解,生成可燃气体和液体油品。
3. 气体分离:经过热裂解后,产生的气体和液体混合物进入气体分离装置。
在气体分离装置中,通过冷却和分离等操作,将可燃气体和非可燃气体进行分离。
其中,可燃气体可以作为能源供应,非可燃气体则可进行处理或回收利用。
4. 液体处理:经过气体分离后,液体油品进入液体处理装置。
在液体处理装置中,通过蒸馏、精制等工艺,将液体油品进行进一步处理和提纯,以得到符合要求的化工产品或燃料。
四、产品应用轮胎高温裂解工艺可以将废旧轮胎转化为可燃气体和液体油品,具有广泛的应用前景。
这些产品可以用于以下方面:1. 可燃气体应用:可燃气体可以作为发电厂、工业企业和居民生活供热等领域的能源供应。
利用可燃气体发电可以减少对化石燃料的依赖,降低温室气体排放。
2. 液体油品应用:液体油品可以作为化工原料或燃料供应。
例如,轻油可以用于石化行业的生产,重油可以作为燃料供应给工业锅炉或炼油厂。
3. 废物处理:轮胎高温裂解工艺可以有效处理废旧轮胎,减少其对环境造成的污染。
轮胎裂解工艺介绍

轮胎裂解工艺介绍轮胎裂解工艺是指将废弃轮胎进行再利用的一种技术,旨在从废旧轮胎中回收和再利用其原材料。
此工艺通过将轮胎中的橡胶物质进行裂解,可以得到多种有用的产物,包括碳黑、石油、燃料油等,从而实现轮胎的综合利用,减少废旧轮胎的环境污染。
1.初步处理:废旧轮胎需要进行初步处理,包括去除轮胎中的金属物质和纤维物质。
这些金属物质和纤维物质会对裂解过程和产物的纯度产生不利影响。
2.破碎:将废旧轮胎进行破碎处理,使轮胎颗粒变小。
破碎后的轮胎颗粒可以更好地进行后续的裂解处理。
3.轮胎裂解:将破碎后的轮胎颗粒进行高温裂解处理。
一般情况下,裂解温度在450-650摄氏度之间,这个温度范围可以有效地使橡胶物质进行裂解,并产生有用的产物。
4.产物分离:经过裂解处理后,产生的气体、液体和固体产物需要进行分离。
一般情况下,气体产物主要包括燃气和各种有机气体,液体产物主要包括燃料油和溶剂油,固体产物主要是碳黑和钢丝。
5.产物处理:裂解后得到的产物需要经过进一步处理,以提高其纯度和可利用性。
例如,燃料油可以进行脱硫、脱氮等处理,以减少对环境的负面影响。
碳黑可以进行磁选等处理,以去除其中的金属杂质。
6.再利用:经过裂解和处理后的产物可以用于再利用。
燃料油可以用作炼油、发电和加热燃料等。
碳黑可以用于橡胶制品、涂料和油墨等的生产。
钢丝可以用于废钢回收和焚烧等。
轮胎裂解工艺的优点是能够将废旧轮胎进行高效利用,减少资源浪费和环境污染。
通过该工艺,轮胎中的橡胶、金属和纤维等材料可以得到有效回收,减少资源的消耗。
此外,该工艺还能够减少废旧轮胎的垃圾处理量,降低对环境的负面影响。
然而,轮胎裂解工艺也存在一些挑战和问题。
首先,裂解过程需要消耗大量的能源,对环境产生一定的影响。
其次,裂解过程中产生的气体和废水需要进行处理,以减少对环境的污染。
此外,裂解产生的产物的纯度和质量也需要得到一定的提高,以提供更高价值的再利用。
总之,轮胎裂解工艺是一种有效的废旧轮胎处理技术,可以进行废旧轮胎的综合利用,减少资源浪费和环境污染。
废旧轮胎分解制油和炭黑装置的技术原理和优势

废旧轮胎分解制油和炭黑装置的技术原理和优势废旧轮胎是一种常见的废弃物,对环境造成了严重的污染和资源浪费。
为了有效利用废旧轮胎的资源价值,减少对环境的负面影响,废旧轮胎分解制油和炭黑装置被广泛应用。
本文将介绍这一装置的技术原理和优势。
1. 技术原理废旧轮胎分解制油和炭黑装置采用了热压脱胶和热热解两个主要工艺步骤。
(1)热压脱胶热压脱胶是利用高温和压力将废旧轮胎中的橡胶与钢丝分离的过程。
首先,将废旧轮胎切成小块,然后将这些轮胎碎片投入到脱胶机中。
脱胶机通过加热和压力,将橡胶与钢丝分离开来。
(2)热热解热热解是指将脱胶后的橡胶经过高温处理,使其发生热解反应,产生液体油气和固体炭黑。
这一步骤通常在真空下进行。
热热解过程中,高温会将橡胶分解成碳氢化合物,进而转化为油气。
2. 优势废旧轮胎分解制油和炭黑装置相比传统的废胎处理方法,具有以下几个明显的优势。
(1)资源回收利用废旧轮胎中的橡胶和钢丝可以得到有效的分离和回收。
通过热压脱胶和热热解工艺,废旧轮胎中的橡胶可以转化为油气,用于燃料和化工原料的生产;而废旧轮胎中的钢丝可以用于再生资源的加工和利用。
这种资源回收利用的方式不仅减少了废旧轮胎对环境的负面影响,还可以为其他工业产品和能源提供可再生的原料。
(2)环境友好废旧轮胎分解制油和炭黑装置的工艺过程基本无废水、无固废和低污染,减少了废旧轮胎对环境造成的负面影响。
尤其是通过热热解工艺,废旧轮胎中的橡胶可以转化为油气,取代传统石油燃料的使用,减少了对石油资源的依赖,同时减少了石油开采和燃烧对环境的污染。
(3)经济效益废旧轮胎分解制油和炭黑装置不仅可以实现资源回收利用,同时还能产生经济效益。
通过将废旧轮胎转化为油气和炭黑,可以为相关产业提供原料和能源,推动产业链上下游的协同发展。
此外,利用废旧轮胎的资源价值也可以创造就业机会,提升当地经济发展水平。
(4)节约能源废旧轮胎分解制油和炭黑装置实现了对废胎资源的综合利用。
废旧橡胶的催化裂解工艺
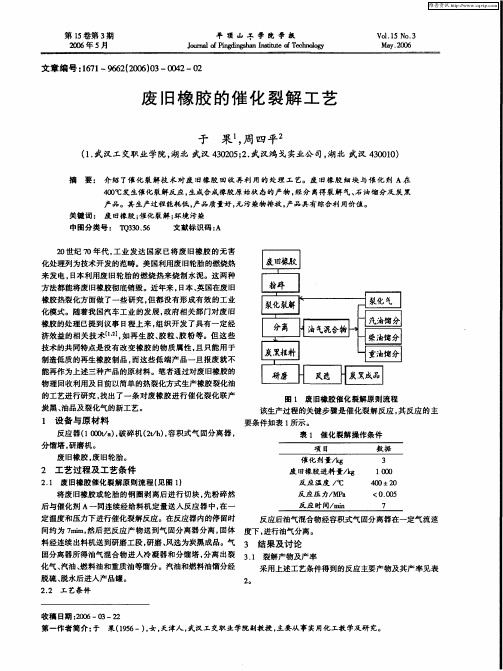
该生产过程 的关 键步骤是 催化裂 解反应 , 反应 的主 其 要条件如表 1 所示 。
表 1 催化裂解操作条件
项I l f 数 据
l 设 备与原 材料
反应器 ( 0 a , 10 O ) 破碎机 ( ) 容积式 气 固分 离器 , 2 , 分馏塔 , 研磨机 。 废 旧橡胶 , 旧轮胎 。 废
细粉 含 量/ %
54 8
2 1
——
空 气 甲烷
10 .3 3 .3 2 9
2 一反 丁 烯 2 一顺 丁 烯
维普资讯
第1 5卷第 3 期
于 果 等 : 旧橡胶 的催 化裂解 工艺 废
4 3
表 2 催 化 裂 解 反 应 产 物 及 其产 率
子 的二次结 构可按不 同的使用 目的和要求 先经机 械磨 细 ,
产溺 名称
摘 要 : 介绍 了催 化 裂 解技 术对 废 旧橡 胶 回收 再利 用的 处理 工 艺。废 旧橡 胶 细块 与 催 化 剂 A在 4 0C 生催化 裂解反应 , 0  ̄发 生成合 成橡胶 原始状 态的产 物 , 经分 离得 裂解 气、 油馏分及 炭 黑 石
产品。其生产过程能耗低 , 品质 量好 , 产 无污染物排放 , 产品具有综合利 用价值 。
技术的共 同特点是没 有改 变橡胶 的物质属性 , 只能用于 且
制造低质 的再生 橡胶 制品 , 而这 些低端产 品一旦报 废就不 能再作 为上 述三 种产品的原材料。笔者通过对废 旧橡胶 的 物理 回收利用及 目前 以简单的热裂化方式生产橡胶 裂化油 的工艺进行研究 , 出了一条对 废橡胶进 行催化 裂化联产 找 炭黑 、 油品及裂化气 的新工艺 。
废轮胎、废橡胶热裂解技术规范编制说明.DOC

废轮胎、废橡胶热裂解技术规范编制说明标准起草组二〇一六年九月废轮胎、废橡胶热裂解技术规范编制说明一、标准工作概况1.1 前言我国是世界轮胎生产和消费的第一大国,也是废轮胎产生大国。
目前我国橡胶消耗量约占世界橡胶消耗总量的 30%以上,连续多年居世界首位,其中 80%以上的天然橡胶和 30%以上的合成橡胶依赖进口。
据统计,2015 年我国废旧轮胎产生量约 3 亿条,重量合1000 万吨以上。
因此,提高废轮胎的综合利用水平,加快发展我国废轮胎循环利用,是缓解我国橡胶资源短缺的重要举措,也是发展橡胶工业循环经济的必然选择。
由于废轮胎具有很强的抗热、抗机械和抗降解性,数十年都不会自然消失,堆在地面占用大量耕地,且易滋生蚊虫、传染病菌,更容易引发火灾,产生有害气体,严重污染环境,被人们称为“黑色污染”源。
我国废轮胎资源综合利用的途径主要是:生产再生橡胶、橡胶粉和热裂解。
热裂解是废轮胎循环利用吃干榨尽的最终环节,目前国内尚处于民间自发组织阶段,还没有配套的规范和标准,民间自发形成的“土法炼油”,投资小,生产成本低,利润高,对环境造成了极大的污染、对资源造成了极大的浪费,成为了社会焦点问题,也引起了国务院领导的高度重视,总理、副总理曾批示:迅即采取措施予以禁止,不可让其蔓延和发展。
要抓紧制定废旧轮胎等废弃物资回收利用的法规和规章。
废轮胎橡胶土法炼油也严重冲击了正规热裂解技术和企业的正常经营,扰乱了热裂解行业的健康发展。
为落实国务院领导的批示精神,在行政立法和条例未出台之前,制定有效的技术立法--国家标准,对热裂解行业的发展进行积极的技术引导是十分必要的,制定和执行热裂解行业技术标准,才能规范我国轮胎橡胶循环再利用行业可持续的健康发展。
1.2 任务来源2006 年 10 月 26 日、10 月 27 日,国务院总理温家宝、主管付总理曾培炎对国务院特刊第 692 期《有媒体称不少地方废轮胎土法炼油问题突出》分别做出批示:请发改委会同环保总局在弄清情况的基础上迅即采取措施予以禁止,不可让其蔓延和发展。
- 1、下载文档前请自行甄别文档内容的完整性,平台不提供额外的编辑、内容补充、找答案等附加服务。
- 2、"仅部分预览"的文档,不可在线预览部分如存在完整性等问题,可反馈申请退款(可完整预览的文档不适用该条件!)。
- 3、如文档侵犯您的权益,请联系客服反馈,我们会尽快为您处理(人工客服工作时间:9:00-18:30)。
将废轮胎橡胶裂解是最彻底的处理车用废橡胶的方法之一。
裂解处理没有污染物排放,而且还可以回收燃料油和炭黑,有利于环保及资源利用,有较高的经济价值,被认为是当前处理废轮胎的最佳途径之一。
废旧轮胎裂解现有热裂解、催化降解和微波解聚等三类工艺。
热裂解工艺
目前,热解技术主要包括:常压惰性气体热解技术、真空热解技术、熔融盐热解技术。
1.常压惰性气体热解
通常,在惰性气体中将废橡胶加热到500C,可获得35%(与废橡胶的质量分数,下同)的固体残余物、55%的油和3%的气体。
其中液体产物含有质量分数为的芳烃油和质量分数为的粗石脑油,固体则主要为粗炭黑,炭黑中含有质量分数为的硫和质量分数为~的灰分。
2.真空热解
真空热解是在减压和低温条件下分解橡胶,较其他热解方法有一些优势。
在总压2〜20kPa温度510C条件下把废橡胶裂解,可得50% 的油品、25%的炭黑、9%的钢、5%的纤维和11%的气体;在总压、温度420C条件下,可得55%的油品、35%的固体和10%的气体。
3.熔融盐热解将轮胎碎块浸入氯化锂/氯化钾的低共熔混合物中,加热至500C, 产生47%的油、45%的固体残余物和12%的气体。
油中大约包括质量分数为的芳烃油、质量分数为的链烯烃和质量分数为的石脑油。
残余物中有炭黑类似物以及轮胎中未发生变化的纤维和钢丝成分。
气体为C1〜C4的石脑油和链烯烃混合物。
催化降解工艺
采用路易斯酸熔融盐催化剂进行废轮胎橡胶降解的方法,反应迅速。
催化剂以氯化锌、氯化锡和碘化锑效果最佳。
当采用质量分数为的锌和钴盐作为催化剂,混入废橡胶料中,可以使液体油、气体产品中的总硫量至少降低40%,液体产品中的总氮量降低50%。
为提高相对分子质量较小的C1〜C4烯烃的回收率,可在废橡胶中加入碱金属或碱土金属碳酸盐,这种催化剂在转化时,对增大异丁烯质量分数效果尤其明显。
微波解聚工艺
废轮胎微波解聚的微波发生装置的频率为2450MH,z 输入功率为
1100V y输出功率为580W将已被破碎成5〜10kg的块状废轮胎盛入容器中,再将容器放入微波发生器内,导入氮气,施加微波后,废轮胎块从内部发热,数十秒内废橡胶急速分解,局部热分解产生的有机气体从橡胶发生龟裂处喷射出来。
分解后,炭黑残留原处并形成局部堆积,由于炭黑吸收微波,在连续施加微波的情况下碳黑变得赤热,加剧有机成分的排出,数分钟内废轮胎橡胶就会变为以炭黑为主体的黑色粉末。
生成气体由导出管导出,经过三个冷却收集器,将气体和液状物分离。
解聚生成物中油、气占50%以上,碳占40%左右。
废轮胎热裂解流程及产品用途通常废轮胎热裂解工厂的生产流程主要包括 4 个部分,包括原料预制系统、热裂解反应器系统、气-油回收分离系统、固体回收系统。