粉末冶金烧结件表面问题及解决方案
粉末冶金烧结件表面问题及解决方案

因其它夹杂而产生的表面缺陷
Fe-Cu-C 系,Cu:Distaloy ACu
缺陷附近的金相分析
缺陷附近无聚合的迹象
从填料靴中发现的大尺寸杂质
因Ni催化作用而产生的表面崩裂
AHC100 + 1%Ni + 1%Zn-st
能谱分析:崩裂处的Ni含量较高
崩裂原因及解决方案
• 脱蜡过程不够完全,过早进入高温区 • Ni对CxHy裂解的催化作用 • Ni粉的聚合
不同润滑剂的尺寸分布
Metallube
90% below 50% below 10% below
(um )
115,60 48,25 7,46
Kenolube
90% below 50% below 10% below
(u m)
59,95 21,76 0,20
H-wax
90% below 50% below 10% below
cps Fe
6
4
Cu
Fe
Ni
Cu
2
Ni
Mn
Cr O
Al Mg Si
S S
0
cps 0
2
4
S
3
Cu
2
Ni Cu
Fe
Ni
1
Mn Cr O
Si Al Mg
S
0
0
2
Mn Fe
Cr Cr Mn
Ni
Cu
Ni
Cu
4
6
8
10
Energy (keV)
Fe
Mn
Mn Fe Cu
Cr Cr
Ni
Cu Ni
4
6
8
10
粉末冶金烧结件密度不均应对措施_概述说明以及解释
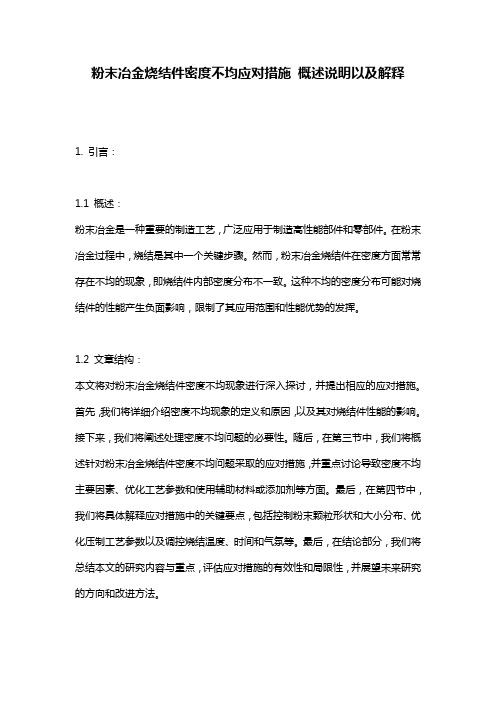
粉末冶金烧结件密度不均应对措施概述说明以及解释1. 引言:1.1 概述:粉末冶金是一种重要的制造工艺,广泛应用于制造高性能部件和零部件。
在粉末冶金过程中,烧结是其中一个关键步骤。
然而,粉末冶金烧结件在密度方面常常存在不均的现象,即烧结件内部密度分布不一致。
这种不均的密度分布可能对烧结件的性能产生负面影响,限制了其应用范围和性能优势的发挥。
1.2 文章结构:本文将对粉末冶金烧结件密度不均现象进行深入探讨,并提出相应的应对措施。
首先,我们将详细介绍密度不均现象的定义和原因,以及其对烧结件性能的影响。
接下来,我们将阐述处理密度不均问题的必要性。
随后,在第三节中,我们将概述针对粉末冶金烧结件密度不均问题采取的应对措施,并重点讨论导致密度不均主要因素、优化工艺参数和使用辅助材料或添加剂等方面。
最后,在第四节中,我们将具体解释应对措施中的关键要点,包括控制粉末颗粒形状和大小分布、优化压制工艺参数以及调控烧结温度、时间和气氛等。
最后,在结论部分,我们将总结本文的研究内容与重点,评估应对措施的有效性和局限性,并展望未来研究的方向和改进方法。
1.3 目的:本文旨在提供一个综合而系统的概述,确立针对粉末冶金烧结件密度不均现象的应对措施,并解释这些措施中所涉及的关键要点。
通过深入了解密度不均现象产生原因和影响机理,我们可以更好地认识到处理该问题的必要性。
同时,我们希望通过阐明应对措施所涵盖的技术方法和策略,为粉末冶金领域从业人员提供一些实用而可行的指导,以改善烧结件密度不均问题,并推动该领域技术发展和应用创新。
2. 粉末冶金烧结件密度不均现象:2.1 密度不均的定义和原因粉末冶金烧结件密度不均是指在制备过程中,烧结件中不同部位的密度存在差异。
这种差异可以表现为局部区域密度较高或较低,或者整体的密度分布不均匀。
导致粉末冶金烧结件密度不均的主要原因有以下几点:1) 粉末颗粒形状和大小的差异:粉末颗粒的形状和大小对于绿体成型和烧结过程中颗粒堆积的紧密程度有重要影响。
放置粉末冶金件生锈的方法

放置粉末冶金件生锈的方法
粉末冶金件是一种常见的工程材料,通常由金属粉末通过压制和烧结工艺制成。
由于粉末冶金件通常是由金属制成,因此它们容易受到氧气和水的影响而产生生锈。
为了防止粉末冶金件生锈,可以采取以下方法:
1. 表面处理,可以通过镀层或涂层的方式来保护粉末冶金件的表面,例如镀锌、镀镍、喷涂防腐漆等。
这些表面处理可以有效地阻止氧气和水接触到金属表面,从而减少生锈的可能性。
2. 使用不锈钢粉末,在制备粉末冶金件时,可以选择不锈钢粉末作为原料,因为不锈钢具有抗氧化和耐腐蚀的特性,能够有效地延缓生锈的速度。
3. 控制环境,尽量避免粉末冶金件长时间暴露在潮湿、高温或者酸碱环境中,这些环境会加速金属的生锈速度。
保持干燥和通风的环境有助于减少生锈的可能性。
4. 定期维护,定期对粉末冶金件进行清洁和保养,及时清除表面的污垢和水渍,使用防锈剂进行保护,可以延长其使用寿命并减
少生锈的风险。
5. 合理设计,在工程设计中考虑到粉末冶金件的使用环境和条件,合理选择材料和表面处理方式,可以从根本上减少生锈问题的发生。
综上所述,通过表面处理、材料选择、环境控制、定期维护和合理设计等多种方法,可以有效地防止粉末冶金件的生锈问题,延长其使用寿命。
希望以上回答能够满足你的需求,如果还有其他问题,欢迎继续提问。
粉末冶金零件毛刺产生原因及去除技术

粉末冶金零件毛刺产生原因及去除技术粉末冶金是绿色制造技术,具有高质量、高效率、低成本的特点,已广泛应用于机械、电子、自动化和航空航天等领域。
随着工业化和自动化水平的提高,对机械零件的制造精度要求越来越高,使用条件要求越来越苛刻,毛刺逐渐引起高度重视,去除毛刺成为零件加工过程中的关键工序。
1毛刺产生原因毛刺的产生与零件的设计和制造方法有很大关系。
粉末冶金是以金属粉末(或金属粉末与非金属粉末的混合)作为原料,经过成形和烧结制造金属材料、复合材料及各种类型制品的工艺过程。
粉末零件压制模具的设计、安装粉坯成形过程,将直接影响到粉末冶金零件的表面质量。
1、模具结构粉末冶金模具一般包括4部分,例如用于制作压溃强度试样的成形模具,即由上模冲、下模冲、芯棒、阴模组成,如图1所示。
2、毛刺产生的原因(1)模具的间隙粉末冶金技术是一种金属粉末模压成形技术,模具的阴模与模冲、模冲与芯棒之间的相对滑动必然存在配合间隙,当金属粉末或精整烧结坯件在模具中受到压力而成形时,会产生流动或塑性变形。
成型件在模具配合间隙处,产生的填充效应,是造成毛刺的根本原因。
当间隙在0.008mm左右时,零件的直线、棱角部分会出现毛刺;当模具间隙达0.002mm 时,就易出现锐边毛刺。
粉末冶金件的毛刺会随着间隙的变化而变化,而模具的间隙还依赖于加工表面粗糙度的变化,如图2所示,当Ra值从0.2增加到0.8,间隙从0.002mm增加0.008mm。
这类毛刺均匀分布在零件周围,零件表面粗糙度好。
(2)模具的精度粉末压制多采用容量装粉法,模具表面与粉末直接接触,细小的粉末颗粒,易进入模具间隙中,形成多体摩擦。
在生产实践中,模冲与阴模、模冲与芯棒之间的间隙是动态变化的,粉末颗粒就会随着模具间隙的变化而变形,从而产生加工硬化,增加了粉末颗粒的硬度和耐磨性。
虽然模具具有较高的硬度和耐磨性,但模具间的粉末颗粒在加工硬化以后,当模具间隙进一步缩小时,模具的表面就会留下细微划痕。
粉末冶金铁基零件的烧结-硬化处理

粉末冶金铁基零件的烧结-硬化处理作者:刘宁凯来源:《城市建设理论研究》2014年第22期摘要:铁基粉末冶金零件用烧结-硬化处理,能得到和常规的热处理相同的显微组织与力学性能,从而可取消传统的将零件用间歇式加热炉重新加热奥氏体化-油淬火等作业,不但节能,而且可减低生产费用。
关键词:粉末冶金铁基零件;烧结硬化;淬透性中图分类号:TF文献标识码: A一、粉末冶金铁基零件的烧结以及热处理工艺(一)烧结工艺烧结实际是将压述在低于主要组分恪点的温度下进行的热处理。
目的是使粉末颗粒问从机械喃合转变为原子之间的晶界结合。
压还内部是粉末颗粒表面问机械压力下接触,而原子与原子之间结合的材料,需要通过烧结,使压还达到冶金结合的材料,使粉末冶金材料达到所需要的力学性能和物化性能。
图1烧结过程示意图如图1所示,图1(a)是烧结前压述中粉末的接触状态,这种结合只是机械结合,粉末颗粒的界面仍然可区分可分离开。
图1 (b)中粉末颗粒接触点的结合状态发生了改变,颗粒界面为晶界面所取代。
随着烧结的进行,结合面增加,直至颗粒界面完全转变为晶界面,最后成为图1(C)所示的状态,颗粒之间的孔隙由不规则的形状转变为球形的孔隙。
粉末烧结是系统自由能降低的过程,换句话说,压还的内能高于烧结体的内能,其主要体现在:(1)粉末颗粒的表面能。
粉末压还具有很大的表面自由能,这种表面能随粉末颗粒的细化而增加。
压还烧结后,颗粒表面消失,将会释放出较大的表面能,这也成为烧结的驱动能。
(2)粉末颗粒内部的畸变能。
在混合和压制过程中粉末颗粒会发生变形而产生畸变,蕴藏着丰富的能量,这些能量液是烧结的驱动能。
由此可见,压还从热力学上来说是处于非常不稳定的状态。
当内能高到一定的程度会发生自动烧结,但在一般情况下,体系的内能不足以驱动烧结进行,所以需要加热到某一温度才能进行烧结。
(二)热处理与其他金属材料一样,我们同样可以通过热处理的方法改善粉末冶金材料力学性能。
应用在粉末冶金材料中的热处理方法有:退火、正火、萍火、回火以及渗碳、渗氮等。
粉末冶金机械行业痛点与解决措施

粉末冶金机械行业痛点与解决措施粉末冶金机械行业是以金属粉末为原料,通过粉末冶金技术加工制造各类零件和产品的行业。
该行业在制造高精度、复杂形状和耐磨、耐腐蚀的零部件方面具有独特优势。
然而,该行业也面临着一些痛点和挑战。
本文将就粉末冶金机械行业的痛点进行分析,并提出相应的解决措施。
一、粉末冶金机械行业痛点1.技术研发能力相对薄弱:目前,粉末冶金机械行业在技术研发方面相对滞后,缺乏核心技术的创新能力。
这使得企业难以在同行业中脱颖而出,无法满足市场对高质量、高效率的需求。
2.原材料成本高昂:粉末冶金机械行业的原材料主要是金属粉末。
由于原材料价格的波动以及供给不稳定,企业的原材料成本居高不下,使得产品的成本压力增大。
3.前工序制备不足:粉末冶金制品的成型前工序对成品质量至关重要。
然而,目前该行业在前工序的制备方面存在许多不足,如脱模困难、不易操作等问题,制约了粉末冶金机械行业的发展。
4.加工精度不高:粉末冶金制造的产品通常需要经过多次加工和处理才能达到所需精度。
然而,目前行业内对于高精度制造的要求相对较高,对加工精度的要求也相对较高。
5.环保要求和能源消耗:粉末冶金制造过程中会产生大量的废气、废水和废渣,严重污染环境。
另外,粉末冶金制造过程中能源消耗也较大,对能源的消耗也提出了更高的要求。
二、解决措施1.加强技术创新和研发能力:粉末冶金机械行业需要加大技术创新的力度,培养和引进专业技术人才,加强与高校和研究机构的合作,提升企业的技术研发能力。
通过持续创新和技术突破,提高企业的核心竞争力。
2.寻找替代原料和降低成本:企业可以寻找替代原料,如开发新型合金和金属粉末,以降低成本。
此外,企业还可以通过优化供应链和生产流程,降低运营成本,提高企业的经济效益。
3.加强前工序的制备技术:企业可以加大对前工序制备技术的研发和投入,提高前工序制备的质量和效率,以提高产品的一致性和成型效果。
同时,培养技术操作人员,提高操作技能,使生产过程更加稳定和可控。
粉末冶金常见问题解决方案
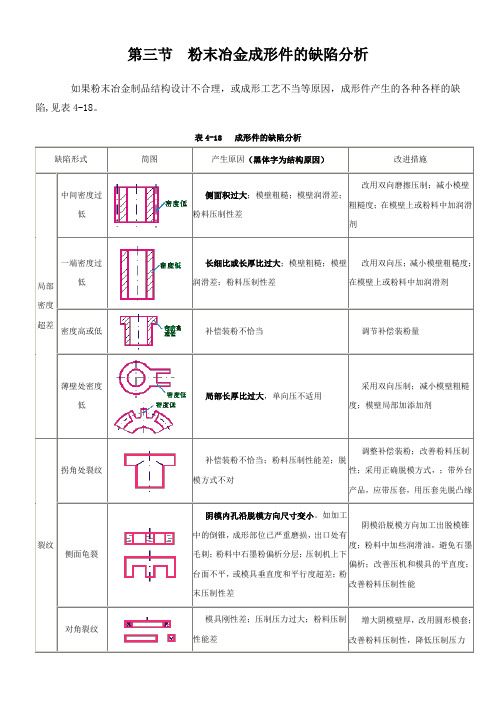
第三节粉末冶金成形件的缺陷分析如果粉末冶金制品结构设计不合理,或成形工艺不当等原因,成形件产生的各种各样的缺陷,见表4-18。
表4-18 成形件的缺陷分析缺陷形式简图产生原因(黑体字为结构原因)改进措施局部密度超差中间密度过低侧面积过大;模壁粗糙;模壁润滑差;粉料压制性差改用双向磨擦压制;减小模壁粗糙度;在模壁上或粉料中加润滑剂一端密度过低长细比或长厚比过大;模壁粗糙;模壁润滑差;粉料压制性差改用双向压;减小模壁粗糙度;在模壁上或粉料中加润滑剂密度高或低补偿装粉不恰当调节补偿装粉量薄壁处密度低局部长厚比过大,单向压不适用采用双向压制;减小模壁粗糙度;模壁局部加添加剂裂纹拐角处裂纹补偿装粉不恰当;粉料压制性能差;脱模方式不对调整补偿装粉;改善粉料压制性;采用正确脱模方式,;带外台产品,应带压套,用压套先脱凸缘侧面龟裂阴模内孔沿脱模方向尺寸变小。
如加工中的倒锥,成形部位已严重磨损,出口处有毛刺;粉料中石墨粉偏析分层;压制机上下台面不平,或模具垂直度和平行度超差;粉末压制性差阴模沿脱模方向加工出脱模锥度;粉料中加些润滑油,避免石墨偏析;改善压机和模具的平直度;改善粉料压制性能对角裂纹模具刚性差;压制压力过大;粉料压制性能差增大阴模壁厚,改用圆形模套;改善粉料压制性,降低压制压力(达相同密度)皱纹︵即轻度重皮︶内台拐角皱纹大孔芯棒过早压下,端台先已成形,薄壁套继续压制时,粉末流动冲破已成形部位,又重新成形,多次反复则出现皱纹加大大孔芯棒最终压下量,适当降低薄壁部位的密度;适当减小拐角处的圆角外球面皱纹压制过程中,已成形的球面,不断地被流动粉末冲破,又不断重新成形的结果适当降低压坯密度;采用松装比重较大的粉末;最终滚压消除;改用弹性模压制过压皱纹局部单位压力过大,已成形处表面被压碎,失去塑性,进一步压制时不能重新成形合理补偿装粉避免局部过压;改善粉末压制性能缺角掉边掉棱角密度不均,局部密度过低;脱模不当,如脱模时不平直,模具结构不合理,或脱模时有弹跳;存放搬动碰伤改进压制方式,避免局部密度过低;改善脱模条件;操作时细心侧面局部剥落镶拼阴模接缝处离缝;镶拼阴模接缝处倒台阶,压坯脱模时必然局部有剥落(即球径大于柱径,或球与柱不同心)拼模时应无缝;拼缝处只许有不影响脱模的台阶,(即图中球部直径可小一些,但不得大,且要求球与柱同心)表面划伤模腔表面粗糙度大,或硬度低;模壁产生模瘤;模腔表面局部被啃或划伤提高模壁的硬度、减小粗糙度;消除模瘤,加强润滑尺寸超差――模具磨损过大;工艺参数选择不合理采用硬质合金模;调整工艺参数不同心度超差――模具安装调中差;装粉不均;模具间隙过大;模冲导向段短调模对中要好;采用振动或吸入式装粉;合理选择间隙;增长模冲导向部分。
粉末色差不良的原因
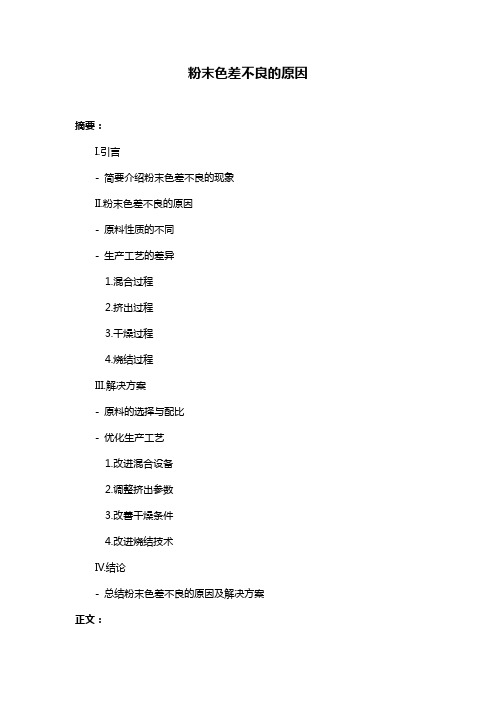
粉末色差不良的原因摘要:I.引言- 简要介绍粉末色差不良的现象II.粉末色差不良的原因- 原料性质的不同- 生产工艺的差异1.混合过程2.挤出过程3.干燥过程4.烧结过程III.解决方案- 原料的选择与配比- 优化生产工艺1.改进混合设备2.调整挤出参数3.改善干燥条件4.改进烧结技术IV.结论- 总结粉末色差不良的原因及解决方案正文:粉末色差不良是粉末冶金制品生产中常见的问题,它会影响产品的性能和外观。
为了提高产品质量,必须对粉末色差不良的原因进行深入分析,并提出有效的解决方案。
粉末色差不良的原因主要包括原料性质的不同和生产工艺的差异。
首先,原料性质的不同会导致粉末的颜色差异。
例如,不同矿区的铁精矿和氧化铝粉在颜色上会有所不同。
因此,在选择原料时,应尽量选择颜色相近的原料,并进行合理的配比,以保证粉末的颜色一致性。
其次,生产工艺的差异也是造成粉末色差不良的主要原因。
在生产过程中,混合、挤出、干燥和烧结等环节都会影响粉末的颜色。
为了解决这个问题,我们需要从以下几个方面进行改进:1.混合过程:优化混合设备,确保原料能够充分混合,以消除原料间的色差。
同时,应控制混合时间,避免过度混合导致粉末颜色的变化。
2.挤出过程:调整挤出参数,如压力、速度和挤出温度,以保证粉末的均匀性和良好的流动性。
此外,应定期检查挤出设备,确保设备运行稳定。
3.干燥过程:改善干燥条件,如温度、湿度和时间,以保证粉末的干燥程度。
同时,应避免粉末在干燥过程中受热不均,导致颜色差异。
4.烧结过程:改进烧结技术,如调整烧结温度、保温时间和冷却速率,以保证粉末的致密性和颜色的一致性。
总之,粉末色差不良的原因包括原料性质的不同和生产工艺的差异。
为了提高粉末冶金制品的质量,我们需要从原料选择和生产工艺两方面入手,寻找合适的解决方案。
铁基粉末冶金轴套表面粗糙的原因
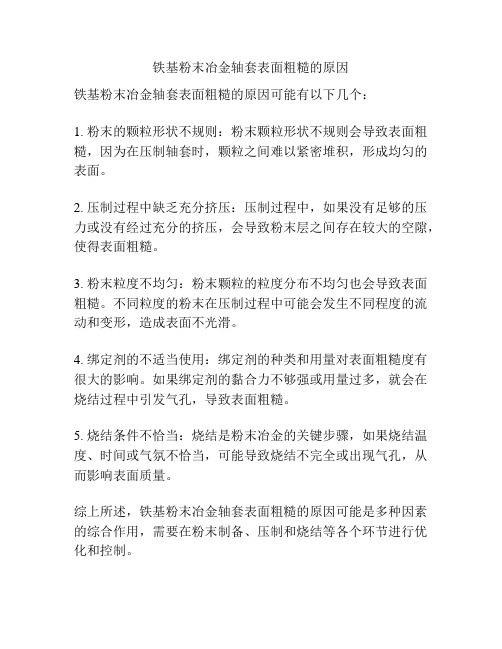
铁基粉末冶金轴套表面粗糙的原因
铁基粉末冶金轴套表面粗糙的原因可能有以下几个:
1. 粉末的颗粒形状不规则:粉末颗粒形状不规则会导致表面粗糙,因为在压制轴套时,颗粒之间难以紧密堆积,形成均匀的表面。
2. 压制过程中缺乏充分挤压:压制过程中,如果没有足够的压力或没有经过充分的挤压,会导致粉末层之间存在较大的空隙,使得表面粗糙。
3. 粉末粒度不均匀:粉末颗粒的粒度分布不均匀也会导致表面粗糙。
不同粒度的粉末在压制过程中可能会发生不同程度的流动和变形,造成表面不光滑。
4. 绑定剂的不适当使用:绑定剂的种类和用量对表面粗糙度有很大的影响。
如果绑定剂的黏合力不够强或用量过多,就会在烧结过程中引发气孔,导致表面粗糙。
5. 烧结条件不恰当:烧结是粉末冶金的关键步骤,如果烧结温度、时间或气氛不恰当,可能导致烧结不完全或出现气孔,从而影响表面质量。
综上所述,铁基粉末冶金轴套表面粗糙的原因可能是多种因素的综合作用,需要在粉末制备、压制和烧结等各个环节进行优化和控制。
粉末冶金零件毛刺的产生原因

粉末冶金零件毛刺的产生原因如今,我们看到的很多零件都是使用粉末冶金技术生产,粉末冶金具有高质量、高效率、低成本的特点背广泛运用。
但随着使用条件的要求越来越高,对产品的制造要求也越来越精细。
在粉末冶金零件生产过程中产生的毛刺也得到了重视,那么,粉末冶金零件毛刺的产生原因是什么?日东粉末冶金公司为大家解答下。
1.模具间隙粉末冶金技术是一种金属粉末模压成形技术,模具的阴模与模冲、模冲与芯棒之间的相对滑动必然存在配合间隙,当金属粉末或精整烧结坯件在模具中受到压力而成形时,会产生流动或塑性变形。
成型件在模具配合间隙处,产生的填充效应,是造成毛刺的根本原因。
日东粉末冶金齿轮2、模具的精度粉末压制主要采用体积装粉法。
模具表面与粉末直接接触。
细粉末颗粒容易进入模具间隙,形成多体摩擦。
在生产实践中,模具之间的粉末颗粒经过加工硬化后,模具间隙将进一步减小,模具表面将留下细小划痕。
随着磨损的加剧,模具表面粗糙度降低,从而增加了粉末与模具之间的摩擦。
脱模过程中容易出现毛刺,甚至无法形成毛刺。
此外,模具的精度或制造精度也会对产品的质量产生一定的影响。
毛刺的形式取决于模具的表面质量。
一般来说,零件表面粗糙,没有金属光泽。
粉末冶金铰链3.模具损坏粉末冶金零件常常有倒角,为了减少后续机械加工,节约成本,在设计模具的时候就把倒角加在模具上,这样模具上易出现薄边,甚至尖角,在这些地方易损坏。
由于模具形状复杂,制造成本高,所以往往在不影响产品最终质量的前提下,会出现飞边毛刺。
毛刺形状相对规则,存在于模具缺陷中。
4、模具安装与使用模具一般从下到上,从内到外安装,定位取决于模具本身的配合。
由于模具配合间隙的存在,无法保证模具安装调试时配合间隙的均匀分布。
间隙大的一侧易出现毛刺,间隙小的一侧易发生干摩擦,造成局部粘着磨损;其次,由于安装本身的缺陷,模具冲头在操作过程中受力不均匀。
在巨大压力的作用下,很容易产生微小的横向运动,导致一个方向上的间隙增大。
粉末冶金轴承生产过程中不良

第二部分:烧结不良
2-1.过烧不良
允收限度
2-2.炉斑不良
允收限度
第1页凡有过烧则不可凡炉斑则不可
1.调节和控制好炉内温度
2.调节和控制好网速,加强点检
3.加强点检确认
不良描述:产品表面有许多黑色
或黄色的小孔洞
识别方法:普通目视
1.炉内本体温度过高
2.网速过慢
3.烧结炉异常(如卡炉导致烧
结时间过长等)不良描述:产品上呈现一块块黑
色斑点
识别方法:普通目视
1.炉渣或低溶点的异物掉在
产品上,进入产品组织内,且有一定深度2.烧结铁盒内表面过脏,与产
品接触烧结后产生炉斑 1.定期清炉2.上料前确保铁盒干净不良写真及状态描述重点发生原因改善对策不良写真及状态描述重点发生原因改善对策。
铁基粉末冶金零件烧结过程氧化、脱碳的原因及解决办法

粉 末 冶金 铁 基 零 件 烧 结 过 程 的氧 化 和 脱 碳 常
常 同时存 在 , 在大 多数 情况 下 , 氧化 时常 伴有 不 同程
降低 了产 品 的强 度 , 污染 了铁 基 体 ; 然 , 量 增 也 显 过 加 石 墨 的副作用 也是 不容 忽视 的 。
本 文对 推 杆式 炉和 网带式 炉 烧结铁 基 零件 的过 程 作 了较 为深 入 的分 析 , 到 了产 生 上 述 现象 的根 找 本 原 因 , 化脱 碳现 象得 到 了较好 的解 决 。 氧
id. e The r s ls i ia e h tox da i n i ror p ro d ofsnt rng wa a e e u t nd c t d t a i to n p i e i r i e i s c us d by CO2 a nd H 2 a n l t rpe i d c u e hear l a ge i wa e o lng s t Renf r i hea r o nd i a e r o a s d by t i e ka n t rc o i e . i o cng t ipr o O s a i g t e e t la g i r a i he fow a e o r t c i e ga nd t o e to e ln o pr v n e ka e,nc e sng t l r t fp o e tv sa he c nt n fCO n i
DI NG u -a H a tng
( uin] xn T n se o L d L n y nF j n 3 4 0 , hn ) Fj a i i u g tn C . t o g a ui 6 0 2 C ia n a
2024年粉末冶金的烧结技术(三篇)

2024年粉末冶金的烧结技术⑴按原料组成不同分类。
可以将烧结分为单元系烧结、多元系固相烧结及多元系液相烧结。
单元系烧结是纯金属(如难熔金属和纯铁软磁材料)或化合物(Al2O3、B4C、BeO、MoSi2等)熔点以下的温度进行固相烧结。
多元系固相烧结是由两种或两种以上的组元构成的烧结体系,在其中低熔成分的熔点温度以下进行的固相烧结。
粉末烧结合金多属于这一类。
如Cu-Ni、Fe-Ni、Cu-Au、W-Mo、Ag-Au、Fe-Cu、W-Ni、Fe-C、Cu-C、Cu-W、Ag-W等。
多元系液相烧结以超过系统中低熔成分熔点的温度进行的烧结。
如W-Cu-Ni、W-Cu、WC-Co、TiC-Ni、Fe-Cu(Cu10%、Fe-Ni-Al、Cu-Pb、Cu-Sn、Fe-Cu(Cu10%)等⑵按进料方式不同分类。
分为为连续烧结和间歇烧结。
连续烧结烧结炉具有脱蜡、预烧、烧结、制冷各功能区段,烧结时烧结材料连续地或平稳、分段地完成各阶段的烧结。
连续烧结生产效率高,适用于大批量生产。
常用的进料方式有推杆式、辊道式和网带传送式等。
间歇烧结零件置于炉内静止不动,通过控温设备,对烧结炉进行需要的预热、加热及冷却循环操作,完成烧结材料的烧结过程。
间歇烧结可依据炉内烧结材料的性能确定合适的烧结制度,但生产效率低,适用于单件、小批量生产,常用的烧结炉有钟罩式炉、箱式炉等。
除上述分类方法外。
按烧结温度下是否有液相分为固相烧结和液相烧结;按烧结温度分为中温烧结和高温烧结(1100~1700℃),按烧结气氛的不同分为空气烧结,氢气保护烧结(如钼丝炉、不锈钢管和氢气炉等)和真空烧结。
另外还有超高压烧结、活化热压烧结等新的烧结技术。
2.影响粉末制品烧结质量的因素影响烧结体性能的因素很多,主要是粉末体的性状、成形条件和烧结的条件。
烧结条件的因素包括加热速度、烧结温度和时间、冷却速度、烧结气氛及烧结加压状况等。
⑴烧结温度和时间烧结温度的高低和时间的长短影响到烧结体的孔隙率、致密度、强度和硬度等。
铁基粉末冶金零件蒸汽处理中常见的质量问题及其解决措施
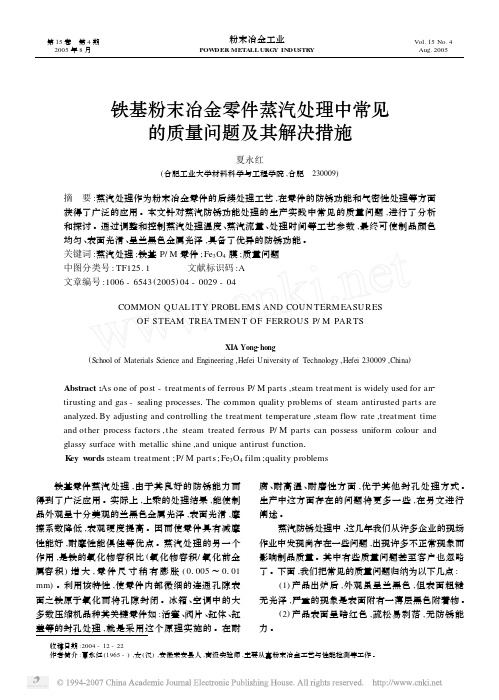
收稿日期:2004-12-22作者简介:夏永红(1965-),女(汉),安徽来安县人,高级实验师,主要从事粉末冶金工艺与性能检测等工作。
铁基粉末冶金零件蒸汽处理中常见的质量问题及其解决措施夏永红(合肥工业大学材料科学与工程学院,合肥 230009)摘 要:蒸汽处理作为粉末冶金零件的后续处理工艺,在零件的防锈功能和气密性处理等方面获得了广泛的应用。
本文针对蒸汽防锈功能处理的生产实践中常见的质量问题,进行了分析和探讨。
通过调整和控制蒸汽处理温度、蒸汽流量、处理时间等工艺参数,最终可使制品颜色均匀、表面光滑、呈兰黑色金属光泽,具备了优异的防锈功能。
关键词:蒸汽处理;铁基P/M 零件;Fe 3O 4膜;质量问题中图分类号:TF125.1 文献标识码:A 文章编号:1006-6543(2005)04-0029-04COMMON QUAL IT Y PROBL EMS AND COUN TERM EASU RESOF STEAM TREA TM EN T OF FERROUS P/M PAR TSXIA Yong 2hong(School of Materials Science and Engineering ,Hefei University of Technology ,Hefei 230009,China )Abstract :As one of post -treatments of ferrous P/M parts ,steam treatment is widely used for an 2tirusting and gas -sealing processes 1The common quality problems of steam antirusted parts are analyzed 1By adjusting and controlling the treatment temperature ,steam flow rate ,treatment time and other process factors ,the steam treated ferrous P/M parts can possess uniform colour and glassy surface with metallic shine ,and unique antirust function 1K ey w ords :steam treatment ;P/M parts ;Fe 3O 4film ;quality problems 铁基零件蒸汽处理,由于其良好的防锈能力而得到了广泛应用。
粉末冶金的工艺流程-粉末的烧结后处理
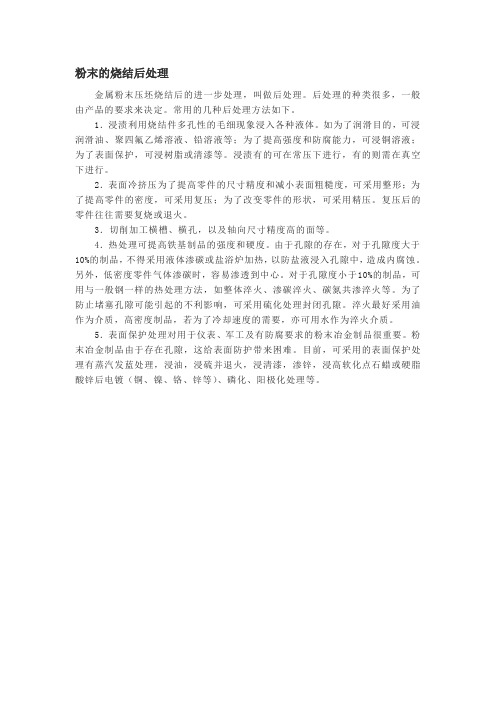
粉末的烧结后处理
金属粉末压坯烧结后的进一步处理,叫做后处理。
后处理的种类很多,一般由产品的要求来决定。
常用的几种后处理方法如下。
1.浸渍利用烧结件多孔性的毛细现象浸入各种液体。
如为了润滑目的,可浸润滑油、聚四氟乙烯溶液、铅溶液等;为了提高强度和防腐能力,可浸铜溶液;为了表面保护,可浸树脂或清漆等。
浸渍有的可在常压下进行,有的则需在真空下进行。
2.表面冷挤压为了提高零件的尺寸精度和减小表面粗糙度,可采用整形;为了提高零件的密度,可采用复压;为了改变零件的形状,可采用精压。
复压后的零件往往需要复烧或退火。
3.切削加工横槽、横孔,以及轴向尺寸精度高的面等。
4.热处理可提高铁基制品的强度和硬度。
由于孔隙的存在,对于孔隙度大于10%的制品,不得采用液体渗碳或盐浴炉加热,以防盐液浸入孔隙中,造成内腐蚀。
另外,低密度零件气体渗碳时,容易渗透到中心。
对于孔隙度小于10%的制品,可用与一般钢一样的热处理方法,如整体淬火、渗碳淬火、碳氮共渗淬火等。
为了防止堵塞孔隙可能引起的不利影响,可采用硫化处理封闭孔隙。
淬火最好采用油作为介质,高密度制品,若为了冷却速度的需要,亦可用水作为淬火介质。
5.表面保护处理对用于仪表、军工及有防腐要求的粉末冶金制品很重要。
粉末冶金制品由于存在孔隙,这给表面防护带来困难。
目前,可采用的表面保护处理有蒸汽发蓝处理,浸油,浸硫并退火,浸清漆,渗锌,浸高软化点石蜡或硬脂酸锌后电镀(铜、镍、铬、锌等)、磷化、阳极化处理等。
铝基粉末冶金件的制造难点及对策
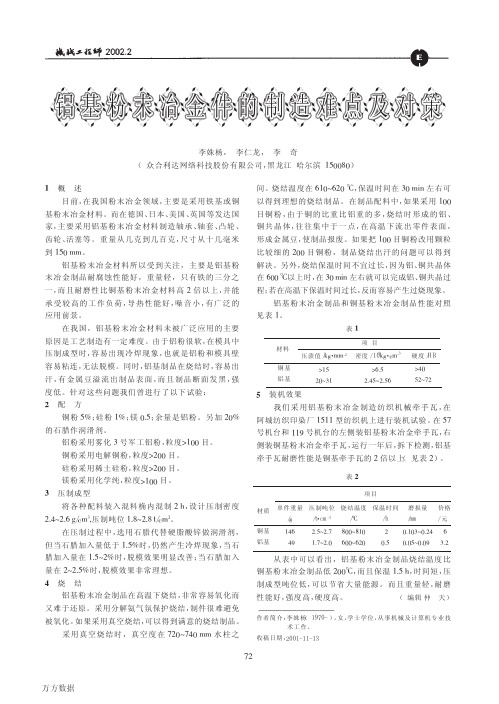
材料 压溃值 ! ・ 8. $$ 铜基 铝基
9%
目前, 在我国粉末冶金领域, 主要是采用铁基或铜 基粉末冶金材料。而在德国、 日本、 美国、 英国等发达国 家, 主要采用铝基粉末冶金材料制造轴承、 轴套、 凸轮、 齿轮、 活塞等。重量从几克到几百克, 尺寸从十几毫米 到 !"# $$。 铝基粉末冶金材料所以受到关注,主要是铝基粉 末冶金制品耐腐蚀性能好,重量轻,只有铁的三分之 并能 一, 而且耐磨性比铜基粉末冶金材料高 % 倍以上, 承受较高的工作负荷, 导热性能好, 噪音小, 有广泛的 应用前景。 在我国,铝基粉末冶金材料未被广泛应用的主要 原因是工艺制造有一定难度。由于铝粉很软, 在模具中 压制成型时, 容易出现冷焊现象, 也就是铝粉和模具壁 容易粘连, 无法脱模。同时, 铝基制品在烧结时, 容易出 汗, 有金属豆溢流出制品表面, 而且制品断面发黑, 强 度低。针对这些问题我们曾进行了以下试验:
! 4 1##,1!# -##,-%#
! . / % #’"
! -#’!#(,#’%+ #’#",#’#7
%’",%’3 !’3,%’#
从表中可以看出,铝基粉末冶金制品烧结温度比 铜基粉末冶金制品低 %##4, 而且保温 !’" *, 时间短, 压 制成型吨位低, 可以节省大量能源。而且重量轻, 耐磨 性能好, 强度高, 硬度高。
"
"
"
"
"
"
"
"
"
"
"
"
"
"
"
"
"
- 1、下载文档前请自行甄别文档内容的完整性,平台不提供额外的编辑、内容补充、找答案等附加服务。
- 2、"仅部分预览"的文档,不可在线预览部分如存在完整性等问题,可反馈申请退款(可完整预览的文档不适用该条件!)。
- 3、如文档侵犯您的权益,请联系客服反馈,我们会尽快为您处理(人工客服工作时间:9:00-18:30)。
断面
能谱分析:裂纹处存在大量杂质
cps
30
Fe
Fe Fe Mn
20 Mn
Cl
10
Mg Cu Si O Al Ca Na
Cl S S
Ca K K Ca Ti
C Cu
0
0
2
4
cps
Fe 25
S
20
15
Mn
10
C
Cl Ca
5
Cu Al O Na Si Ca Cu
Cl S
Ca K K
0
0
2
4
Mn
6
Fe Mn
• 加大气流量,加长脱蜡区(降低带速) • 降低烧结气氛中的 CO CO2比 • 填粉过程中防止Ni粉的聚合
因其它夹杂而产生的表面缺陷
Fe-Cu-C 系,Cu:Distaloy ACu
缺陷附近的金相分析
缺陷附近无聚合的迹象
从填料靴中发现的大尺寸杂质
因Ni催化作用而产生的表面崩裂
AHC100 + 1%Ni + 1%Zn-st
能谱分析:崩裂处的Ni含量较高
崩裂原因及解决方案
• 脱蜡过程不够完全,过早进入高温区 • Ni对CxHy裂解的催化作用 • Ni粉的聚合
一种表面斑痕 • 因较粗的Cu颗粒而产生的针孔 • 因Ni催化作用而产生的表面崩裂 • 因其它夹杂而产生的表面缺陷
Fe-P-C系烧结件的表面发泡问题
Counts
每个烧结舟中第一个部件发泡
Fe
Fe Fe
1000
500
P
C
Si
Cu
0
Counts 0
2
4
6
8
Fe
Fe FEenergy (keV)
1000
解决方案
• RBO • 将基体铁粉换成含纯度较高的铁粉(Mn
含量较低) • 用Amidwax代替Zn-stearate
因较粗的Cu颗粒而产生的针孔
Fe-Cu-C 系, Cu粉:100目
金相分析
孔洞尺寸100-150um
孔洞附近:微细珠光体+马氏体 Cu含量较高
解决方案:铜粉由100目换成200目
Fe3P, 1120C/30min
500 P
C
Si
C
8
Energy (keV)
解决方案
• 加大脱蜡区的气流量,以防止润滑剂在 部件表面的沉积,产生Fe-P-C液相
• 将一个无用的部件放在每个烧结舟的第 一个部件的位置
与压制过程相关的表面裂纹
中线处 裂纹
裂纹表面及断面:裂纹处密度低
表面
Cu Cu
8
10
Energy (keV)
Mn Fe
Cu Cu
6
8
10
Energy (keV)
正常处 裂纹处
芯棒局部表面的不充分退磁
对压制模具及冲模进行有效退磁
因石墨粉形成团粒而导致的表面缺陷
Distaloy AE+0.7C 1250C/20min
缺陷处从碳含量明显高于 正常处 解决方案:Starmix
粉末冶金烧结件的表面问题 及其解决方案
• 不同的表面问题 • 影响粉冶部件表面问题的有关因素 • 举例(解决方案)
不同的表面问题
• 针孔 • 孔洞 • 表面崩裂 • 发泡 • 斑痕 • 裂纹
影响粉冶部件表面问题的有关因素
• 原料粉末的纯度 (Al, Mn, SI, Ca, S, C, P, O) • 添加剂的颗粒的尺寸 (C, Cu, MnS, Fe3P, 润滑剂等) • 原料粉的合金化方式(普通,预合金,扩散型合金) • 润滑剂的选择 (H-wax, Zn-st, Knolube, Metalube) • 混粉方式 (Premix, Starmix) • 压制过程 (模具表面状况,粉尘,模具退磁) • 脱蜡时间及部件的填充率(崩裂,气泡,Ni催化反应) • 脱蜡时气流量的控制(残余润滑剂) • 炉腔内杂质的沉积 (Mn,S,P)
(u m)
33,92 7,60 1,37
Zn-Stearate
90% below 50% below 10% below
(u m)
16,15 3,49 0,08
举例
• Fe-P-C系烧结件的表面发泡问题 • 与压制过程相关的表面裂纹 • 因石墨粉形成团粒而导致的表面缺陷 • 在脱蜡过程中产生的表面斑痕 • 与润滑剂,铁粉内的杂质及脱蜡过程相关的另
在脱蜡过程中产生的表面斑痕
产生条件: •Metallub + MnS •液态 Metallub同 时存在于表面及 内部
解决方案 : •RBO •加大脱蜡区的 气流量
与润滑剂,铁粉内的杂质及脱蜡过程 相关的另一种表面斑痕
Fe-Cu-C系 雾化铁粉 + Zn-Stearate
能谱分析:斑痕处存在大量杂质(Mn, S等)
cps Fe
6
4
Cu
Fe
Ni
Cu
2
Ni
Mn
Cr O
Al Mg Si
S S
0
cps 0
2
4
S
3
Cu
2
Ni Cu
Fe
Ni
1
Mn Cr O
Si Al Mg
S
0
0
2
Mn Fe
Cr Cr Mn
Ni
Cu
Ni
Cu
4
6
8
10
Energy (keV)
Fe
Mn
Mn Fe Cu
Cr Cr
Ni
Cu Ni
4
6
8
10
Energy (keV)
不同润滑剂的尺寸分布
Metallube
90% below 50% below 10% below
(um )
115,60 48,25 7,46
Kenolube
90% below 50% below 10% below
(u m)
59,95 21,76 0,20
H-wax
90% below 50% below 10% below