基于PLC的变频器液位控制设计
基于PLC的液位控制系统设计
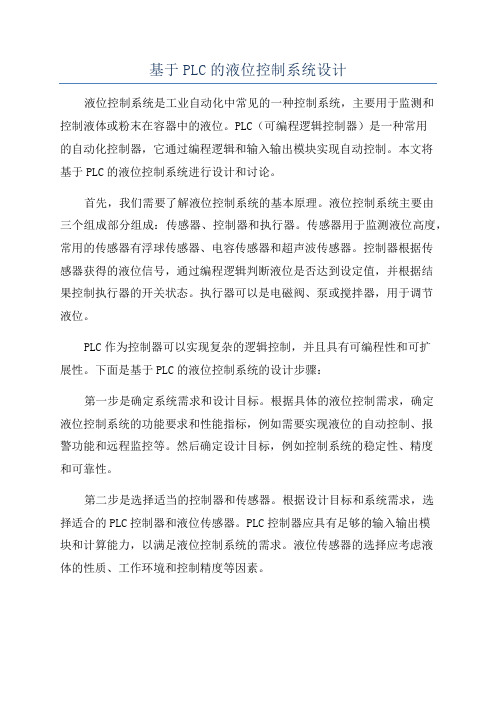
基于PLC的液位控制系统设计液位控制系统是工业自动化中常见的一种控制系统,主要用于监测和控制液体或粉末在容器中的液位。
PLC(可编程逻辑控制器)是一种常用的自动化控制器,它通过编程逻辑和输入输出模块实现自动控制。
本文将基于PLC的液位控制系统进行设计和讨论。
首先,我们需要了解液位控制系统的基本原理。
液位控制系统主要由三个组成部分组成:传感器、控制器和执行器。
传感器用于监测液位高度,常用的传感器有浮球传感器、电容传感器和超声波传感器。
控制器根据传感器获得的液位信号,通过编程逻辑判断液位是否达到设定值,并根据结果控制执行器的开关状态。
执行器可以是电磁阀、泵或搅拌器,用于调节液位。
PLC作为控制器可以实现复杂的逻辑控制,并且具有可编程性和可扩展性。
下面是基于PLC的液位控制系统的设计步骤:第一步是确定系统需求和设计目标。
根据具体的液位控制需求,确定液位控制系统的功能要求和性能指标,例如需要实现液位的自动控制、报警功能和远程监控等。
然后确定设计目标,例如控制系统的稳定性、精度和可靠性。
第二步是选择适当的控制器和传感器。
根据设计目标和系统需求,选择适合的PLC控制器和液位传感器。
PLC控制器应具有足够的输入输出模块和计算能力,以满足液位控制系统的需求。
液位传感器的选择应考虑液体的性质、工作环境和控制精度等因素。
第三步是进行系统硬件设计。
根据选定的PLC控制器和传感器,设计系统的硬件连接和布置。
将传感器与PLC控制器连接,确保信号的稳定传输。
同时,还需要考虑系统的电气安全和防护措施。
第四步是进行PLC编程。
根据设计需求和目标,编写逻辑控制程序。
程序应能够实现液位的监测、判断和控制,同时具备保护和报警功能。
编程语言通常使用ladder diagram(梯形图),也可以使用其他编程语言如指令列表和函数图。
第五步是进行系统调试和优化。
完成PLC编程后,进行系统调试和优化。
对系统进行全面的测试,确保液位的检测和控制功能正常运行。
基于PLC的液位控制系统毕业设计论文

基于PLC的液位控制系统毕业设计论文摘要:本文基于PLC(可编程逻辑控制器)技术,设计了一种液位控制系统,该系统能够实时监测液位,并根据设定值进行液位控制。
本文详细介绍了该系统的硬件设计、软件设计以及系统测试,并对系统的性能进行了评估和分析。
实验结果表明,该液位控制系统能够稳定可靠地实现对液位的控制。
关键词:PLC;液位控制;硬件设计;软件设计;系统测试1.引言液位控制是工业中常见的一种控制过程。
在各种工业领域,如化工、能源、水利等,在液位控制方面都有较高的需求。
随着自动化技术的不断发展,PLC技术成为液位控制的一个重要工具。
2.系统硬件设计在本系统硬件设计中,我们采用了PLC、液位传感器、电磁阀等关键元件。
PLC作为控制中心,接收传感器的信号,根据设定值来控制电磁阀的开启和关闭。
液位传感器负责实时监测液位的变化,并将信号传输给PLC。
电磁阀根据PLC的指令来控制液位的增减。
3.系统软件设计在本系统软件设计中,我们使用了PLC编程语言来实现液位控制的逻辑。
首先,我们定义了PLC的输入和输出信号,然后根据设定的逻辑进行编程。
具体来说,当液位高于设定值时,PLC会关闭电磁阀,减少液位的上升;当液位低于设定值时,PLC会打开电磁阀,增加液位的下降。
通过循环执行这些逻辑,系统可以实现对液位的控制。
4.系统测试为了验证系统的可行性和性能,我们进行了一系列的测试。
首先,我们针对液位控制器的输入输出进行了测试,确保其正常工作。
然后,我们使用液位泵和液位计进行了实际测试,记录了系统在不同液位变化条件下的性能。
实验结果表明,该液位控制系统具有良好的稳定性和可靠性。
5.结果和分析通过对实验数据的分析,我们得出了以下结论:该液位控制系统能够满足不同液位变化条件下的控制需求;系统响应速度较快,能够在短时间内完成液位的调整;系统具有良好的稳定性,能够稳定地维持设定的液位。
6.结论本文基于PLC技术设计了一种液位控制系统,并进行了详细的硬件设计、软件设计和系统测试。
基于PLC的变频器液位控制设计

结 构框 图 , 然后 在根据 工艺要 求 , 绘制 出各功 能单 元的详细功 能框 图。 4 3编 写程序 . 编写 程序就 是 根据设 计 出的 框 图逐 条地
编写控制 程序 , 这是整个 程序设计 工作的核心
部分 。 4 4 程 序测试和 调试 . 程序 测试和调试 不 同 , 软件测试 的 目的是 尽 可能 多地 发现软件 中的错误 , 软件调 试的任 务是 进一 步 诊 断和 改正 软 件 中的错 误 。 4 5 编 写程序说 明书 . 程序说 明书是对 程序的综 合说 明 , 是整个 程 序 设 计 工 作 的总 结 。 图 1 系统设计流 程 图。 是
维普资讯
2Q Q: Q!
Sc en a Tech ogY i ce nd nol Consu tng I i Her d al
工 业 技 术
基于 P C的变频器 液位控制设计 L
张 斌 ( 哈工ห้องสมุดไป่ตู้ 电子仪器 厂 )
摘 要: 随着 电力电子技术以及工业 自动控制技术的发展 , 得交流变频调 速系统在工业 电机 拖动领域得 到了广泛应用 。另外 , 使 由于 P C L 的功能 强大、容 易使 用、高可靠性 , 常常被用 来作为现场数据 的采集 和设 备的控制 。 本设计就是利 用变频 器和 PL C实现水 池水位的控
的选 用高性 能的 P C, 全能够 胜任 此功 能 。 L 完 系统 控制结构 如 图 l 示。 所 P C采集 传感 器 、监 控 电机及变 频器等 L 有关 的各类对象 的信息 。本 系统 中, 电机采 对 用一 台变 频 器来进 行频 率 的调节 控制 。采用 P C输 出 的模拟量 信号作 为变频 器的控 制端 L 输 入 信号 , 而 控制 电机 转 速大 小 , 从 并且 向 P LC反馈 自身 的工 作状 态信号 , 当发生 故障 时, 能够 向 P C 出报警信号 。由于变 频调速 L 发 是通 过改 变 电动机 定子 供 电频率 以改 变 同步 转速来 实现 的 , 故在调 速过 程 中从 高速到 低速 都可 以保 持 有 限的 转 差功 率 , 此具 有 高效 因 率 、宽范 围、高精 度的调速 性 能。
基于S7-1200PLC的水箱液位控制系统的设计

基于S7-1200PLC的水箱液位控制系统的设计重庆科技学院摘要水箱液位控制系统是一种用于监测、控制水箱液位的自动化设备。
它通过搭载传感器、控制器和执行机构等组件,实现对水箱液位的实时监控和自动控制。
通常,水箱液位控制系统由传感器,控制器,执行机构。
水箱液位控制系统的使用范围广泛,包括建筑物、工业生产、农业灌溉、城市给排水和环保等领域。
它具有结构简单、安装方便、实时性强等特点,该系统能够提高水资源的利用效率、减少用水浪费和防止水源的污染。
本文基于S7-1200 PLC实现水箱液位控制系统设计。
该系统由硬件和软件两部分组成,硬件包括PLC、人机界面触摸屏、传感器、执行器等;软件实现传感器数据处理、PID稳态控制、安全等功能;关键词:液位控制 PLC PID 传感器重庆科技学院本科生毕业设计 3水箱液位控制系统硬件设计1绪论在工业领域,几乎在各个行业都会或多或少的涉及到液位的检测等问题,然而液位变量具有延迟滞后性,参数不稳定,复杂多变等问题,因此,这就需要本文采取更为精确的控制器去实现液位变量的检测。
传统控制具有很多缺陷:比如精度低、速度慢、灵敏度低等。
一个稳定的液位系统,可以保证安全可靠的工业生产、高效的生产效率、充分合理的利用能源等,大大提高了工业生产的经济价值。
日益激烈的市场竞争,要求本文的控制技术必须更加先进,此前的控制技术已落伍,显然无法满足需求,这种对先进技术的需求加速了可编程逻辑控制器的问世。
引入PLC控制器后,能够使控制系统变得更集中、有效、及时。
2水箱液位控制总体方案设计2.1水箱液位控制系统实际应用特征水箱液位控制系统是一种广泛应用于水箱的自动化控制系统,常见于民用和工业领域。
实际应用中,水箱液位控制系统具有以下特征:①实时性强:系统能够实时检测水箱内的液位信息,并根据液位变化及时控制水泵的启停,保证水位稳定。
②可靠性高:系统通过各类安全措施确保水泵的正常启停,不会出现过量或不足的水位情况,避免因为水位变化带来的安全隐患。
基于PLC的液位控制系统研究毕业设计(论文)

毕业设计论文基于PLC的液位控制系统研究摘要本文设计了一种基于PLC的储罐液位控制系统。
它以一台S7-200系列的CPU224和一个模拟量扩展模块EM235进行液位检测和电动阀门开度调节。
系统主要实现的功能是恒液位PID控制和高低限报警。
本文的主要研究内容:控制系统方案的选择,系统硬件配置,PID算法介绍,系统建模及仿真和PLC编程实现。
本设计用PLC编程实现对储罐液位的控制,具有接线简单、编程容易,易于修改、维护方便等优点。
关键字:储罐;液位控制;仿真;PLCAbstractThis article is designed based on PLC, tank level control system. It takes a series s7-200 CPU224 and an analog quantities of EM235 expansion module to level detection and electric valve opening regulation.System main function is to achieve constant low level PID control and limiting alarm.The main contents of this paper: the choice of the control system plan, system hardware configuration, PID algorithm introduced, system modeling and simulation, and PLC programming. PLC programming with the design of the tank level control have the advantage of simple wiring, easy programming, easy to modify, easy maintenance and so on.Key word: tank ; level ;control ;simulation ;plc目录摘要 (I)ABSTRACT ........................................................... I I 1 绪论. (1)1.1盐酸储罐恒液位控制任务 (1)1.2本文研究的意义 (2)1.3本文研究的主要内容 (2)2 控制系统方案设计 (3)2.1储罐液位控制的发展及现状 (3)2.2系统功能分析 (3)2.3系统方案设计 (4)3 系统硬件配置 (5)3.1电动控制阀的选择 (5)3.1.1 控制阀的选择原则 (5)3.1.2 ZAJP 精小型电动单座调节阀性能和技术参数介绍 (10)3.2液位测量变送仪表的选择 (13)3.2.1 液位仪表的现状及发展趋势 (13)3.2.2 差压变送器的测量原理 (13)3.2.3 差压式液位变送器的选型原则 (14)3.2.4 DP系列LT型智能液位变送器产品介绍 (15)3.3PLC机型选择 (16)3.3.1 PLC历史及发展现状 (16)3.3.2 PLC机型的选择 (18)3.3.3 S7-200系列CPU224和EM235介绍 (20)4 PID算法原理及指令介绍 (21)4.1PID算法介绍 (22)4.2PID回路指令 (24)5 系统建模及仿真 (28)5.1系统建模 (28)5.2系统仿真 (30)5.2,1 MATLAB语言中Simulink交互式仿真环境简介 (30)5.2.2 系统仿真 (31)第6章系统编程实现 (33)6.1硬件设计 (33)6.1.1 绘制控制接线示意图 (33)6,1.2 I/O资源分配 (33)6.2软件设计 (34)6.2.1 STEP 7 Micro/Win V4.0 SP6编程软件介绍 (34)6.2.2 恒液位PID控制系统的PLC控制流程 (35)6.2.3 编写控制程序 (36)6.2.4 程序清单 (39)结束语 (40)参考文献 (41)致谢 (42)1 绪论1.1 盐酸储罐恒液位控制任务如图1.1所示为某化工厂稀盐酸储罐,该罐为钢衬聚四氟乙烯储罐,罐体高6米,容量为50立方米,重500千克。
基于PLC的液位控制系统设计

毕业设计开题报告1. PID 简述简述 过程控制通常是指石油、化工、冶金、轻工、纺织、制药、建材等工业生产过程中的自动控制程中的自动控制,它是自动化技术的一个极其重要的方面。
本次毕业设计是基于PLC 的液位控制系统的设计,它的控制对象是水箱的液位,是过程控制中经常遇到热工参数。
本人在这次设计中主要负责控制策略——PID 算法的确定,就在次将PID 算法作个简要的介绍。
算法作个简要的介绍。
在生产过程自动控制的发展历程中在生产过程自动控制的发展历程中,PID ,PID 控制是历史最久、生命力最强的基本控制方式。
它简单实用制方式。
它简单实用,,易于实现易于实现,,适用范围广适用范围广,,鲁棒性好鲁棒性好,,在现今的工业过程中获得了广泛的应用广泛的应用..据统计据统计,,目前工业控制器中约有90%90%仍是仍是PID 控制器。
PID 控制器的设计及其参数整定一直是控制领域所关注的问题。
其设计和整定方法得到国内外广泛研究, 著名的如Ziegler-Nichols 法、基于内模控制的方法及基于误差的积分的优化方法。
基于误差的积分准则由于能较好地反映闭环系统的性能以及易于计算的原因基于误差的积分准则由于能较好地反映闭环系统的性能以及易于计算的原因,,在PID 优化设计中被广泛采用。
(1)在工业生产过程控制中,模拟量的模拟量的 PID (比例、比例、积分、积分、微分)调节是常见的一种控制方式,这是由于这是由于PID 调节不需要求出控制系统的数学模型,至今为止,很难求出许多控制对象准确的数学模型,对于这一类系统,使用使用PID 控制可以取得比较令人满意的效果,同时同时PID 调节器又具有典型的结构,可以根据被控对象的具体情况,采用各种PID 的变种,有较强的灵活性和适用性。
在模拟量的控制中,经常用到经常用到PID 运算来执行来执行PID 回路的功能,PID 回路指令使这一任务的编程和实现变得非常容易。
如果一个果一个 PID 回路的输出回路的输出M ( t)是时间的函数,则可以看作是比例项、积分项和微分项三部分之和(2),即:,即:dt de K M edt K e K t M C tc C *+++*=⎰00)( 式中式中 e ——偏差;——偏差;T i ——积分常数;——积分常数;T d ——微分常数;——微分常数;K c ——放大倍数(比例系数)——放大倍数(比例系数)M 0——偏差为零时的控制值,有积分环节存在,此项也可不加——偏差为零时的控制值,有积分环节存在,此项也可不加以上各量都是连续量,第一项为比例项,最后一项为微分项,中间两项为积分项。
「基于PLC的液位控制系统设计1」

「基于PLC的液位控制系统设计1」液位控制系统是工业领域最常见的自动控制系统之一,它可以实现对液体的实时监控和自动控制。
本文将介绍基于可编程逻辑控制器(PLC)的液位控制系统的设计。
首先,我们需要了解液位控制系统的基本组成部分。
液位控制系统一般包括液位传感器、执行器(如泵或阀门)、PLC和人机界面。
液位传感器用于检测液体的高度,然后将信号传输到PLC。
PLC通过逻辑控制算法,根据液位传感器的信号来控制执行器的操作,从而达到对液位的控制。
人机界面用于操作人员与液位控制系统直接交互,如设置液位控制参数、显示液位信息等。
在设计液位控制系统时,首先需要确定液体的容器类型和液位的测量范围,选择适合的液位传感器。
常见的液位传感器包括浮球传感器、压阻式传感器和超声波传感器等。
然后,选择合适的执行器来控制液位,如泵或阀门。
根据液位控制的需求,确定PLC的规格和类型,如简单控制任务可以选择小型PLC,而复杂控制任务可能需要使用高性能PLC。
接下来,需要进行液位控制的逻辑设计。
液位控制系统的逻辑设计可以使用Ladder Diagram或Structured Text进行编程。
通过编程实现对液位的监测和控制。
例如,当液位低于一定值时,PLC通过控制执行器来注入液体,当液位高于一定值时,PLC通过控制执行器来排出液体。
在设计过程中,要考虑到液位变化的延迟和波动。
针对这个问题,可以使用滤波技术和控制算法来解决。
滤波技术可以减少传感器信号中的噪音和干扰,控制算法可以根据液位变化的速率来调整执行器的操作,从而使液位控制更加精确和稳定。
最后,测试和调试液位控制系统。
在测试中,需要验证液位传感器的准确性和PLC的控制性能。
通过对系统的模拟和实际运行进行测试,可以发现和解决潜在问题,确保液位控制系统的正常运行。
总结起来,基于PLC的液位控制系统设计需要考虑液位传感器的选择、执行器的选择、PLC的规格和类型、逻辑设计、滤波技术、控制算法以及测试和调试。
基于PLC与组态王的液位控制系统设计与实现

控制对其参数整定,并利用组态王软件构建组态环境进行调试 结果表明,采用 P I E ) 控制算法实现对液位的控制,系统运
行平稳 ,超调量为 1 1 %,调节时 间大概为 3 mi n ,能够基本 满足液位控制要求。
关键字:P L C;液位控制;组态;P I D控 制 中图分类号:T P 2 7 3 文献标识码 :A 文章编号:1 6 7 3 - 2 2 1 9( 2 0 1 3 )0 8 - 0 0 2 4 - 0 4
参数 ,阀门的进水量 Q1 为控制变量 。如果 QI = Q2时,系统处于平衡 状态 ,此时的液位为 给定值 h ,假定某一时刻 ,阀门 1
突然开大
,导致 Q 1 进 水量变大 ,平衡 被打破则会 引起
—
h 液位开始变化 。于是有 :
( 2 - 1 )
d A h ( △ Q l 一 △ Q 2 ) : — A
0 引 言
液位是过程控制系统中非常普遍 的被控对象 ,液位控制涉及工控领域广泛 ,同时液位控制具有非线性及滞后性等特点 ,
常规控制方法往往难以满足控制要求 ,因此液位控制系统 的可业 生产
控制环境下 , P L C的高可靠性及稳定性得到广泛应用 , 组态软件能够完成对现场数据 的采集、实时 曲 线 和历史曲线的 显示 、 在线修改控制参数及报表输 出等功能 而被 广泛应用。本文介绍 的液位控制系统结合 P L C技 术和组态 王软件实现液位控制 , 对控制过程进行实 时整定及在线监控 ,具有控 制灵 活方便 、显示直观及控制效果好等优点 。
调节阀选用气体打开式,如果液位大于给定,则 P L C输出信号减小使阀门开度减小 ,液位降低,反之则升高。系统 自动运
行调节使液位高度维持到工艺要求 范围内【 j J 。
基于PLC的液位控制
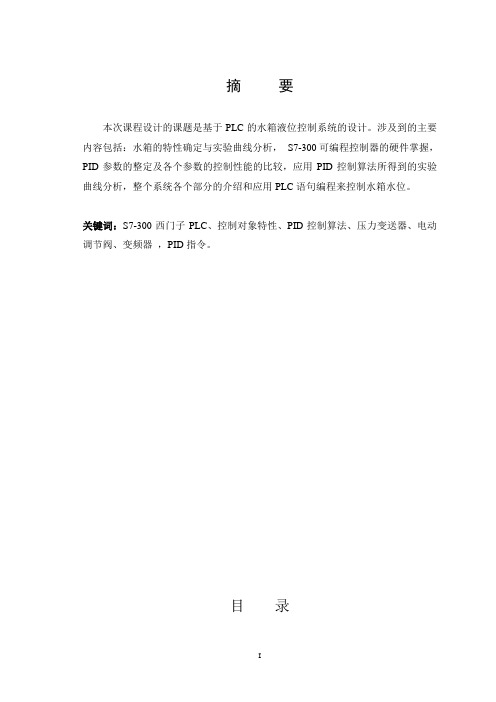
摘要本次课程设计的课题是基于PLC的水箱液位控制系统的设计。
涉及到的主要内容包括:水箱的特性确定与实验曲线分析,S7-300可编程控制器的硬件掌握,PID参数的整定及各个参数的控制性能的比较,应用PID控制算法所得到的实验曲线分析,整个系统各个部分的介绍和应用PLC语句编程来控制水箱水位。
关键词:S7-300西门子PLC、控制对象特性、PID控制算法、压力变送器、电动调节阀、变频器,PID指令。
目录摘要 (I)第1章引言 (1)1.1 实验目的 (1)1.2 实验原理 (1)1.3 设计方案的确定 (2)第2章系统硬件介绍 (2)2.1 西门子PLC控制系统简介 (2)2.3模拟量输入模块 (3)2.4模拟量输出模块 (3)2.5 电源模块 (4)第三章系统硬件控制设计 (5)3.1 系统设计 (5)3.2 硬件设计 (6)3.2.1 检测单元 (6)3.2.2 执行单元 (7)第四章软件设计 (8)4.1 FC105 介绍: (8)4.2 FC 106 介绍: (8)4.3 FB41 介绍 (9)4.4 软件控制流程图: (10)第五章程序实现 (10)5.1 step 7 软件编程: (10)5.2程序调试与结果 (15)5.3 过程中出现的问题与解决办法 (15)第6章实验心得与体会 (19)附录:程序清单 (20)参考文献 (24)第1章引言1.1 实验目的1熟悉可编程序控制器的工作原理、主要参数、硬件结构、模块特性、安装配置及指令系统、程序设计、调试方法。
2、熟悉S7-300模拟量模块的工作原理,掌握硬件安装接线的方法及软件的设置及编程。
3、掌握模拟量模/数、数/模转换的原理,输入输出编程方法及STEP7开发环境的使用。
4 掌握过程控制的中pid的调节方法,实现液位的自由控制。
1.2 实验原理本次实验采用PLC 控制,将液位控制在设定高度,根据上水箱液位信号输出给PLC ,PLC根据P I D 参数进行PID 运算,输出信号给变频器,然后由变频器控制水泵供水系统的进水流量,从而达到控制液位的恒定的目的。
基于PLC的液位控制系统设计设计

基于PLC的液位控制系统设计设计一、设计背景:液位控制系统是工业自动化领域中常见的一种工艺控制系统,用于控制容器内液体的液位。
液位控制系统在化工、冶金、电力、制药等行业中广泛应用,对于保证生产过程中液位的稳定和控制具有重要意义。
基于PLC的液位控制系统可以实现对液位的精确控制和自动化操作,提高生产效率和产品质量。
二、设计原理:三、系统组成:1.传感器:用于检测容器内液体的液位变化,并将液位信号转换为电信号,传输给PLC;2.信号处理模块:对传感器传输过来的信号进行调理和处理,将处理后的信号传输给PLC;3.PLC:作为控制核心,接收信号处理模块传输过来的信号,并根据事先设定的控制策略进行逻辑控制;4.执行机构:根据PLC控制信号对容器内液体进行加输或排泄操作,以控制液位的变化;5.人机界面:通过触摸屏或键盘等控制输入设备,实时监控和调整液位控制系统的参数,以及实施手动控制。
四、设计步骤:1.确定液位控制系统的控制目标和要求:根据具体的应用场景,确定液位的目标值、控制精度、稳定性要求等;2.选择合适的传感器:根据液体的性质和工业环境,选择适合的液位传感器,如浮子式液位传感器、压力式液位传感器等;3.确定信号处理模块:根据传感器输出的信号特点,确定合适的信号处理模块,对传感器信号进行调理和处理,以适应PLC输入信号的要求;4.PLC逻辑控制程序设计:根据液位控制系统的控制目标和要求,设计PLC的逻辑控制程序,包括液位目标设定、控制策略、输出控制信号等;5.确定执行机构:根据液体的加输或排泄要求,选择适当的执行机构,如电动阀门、气动阀门等;6.进行系统的连接和调试:将传感器、信号处理模块、PLC、执行机构按照设计要求进行连接,并进行系统的调试和测试,确保系统的功能正常;7.人机界面设计和实施:根据液位控制系统的需要,设计合适的人机界面,以实现参数设置、控制操作、故障诊断等功能。
五、优势与应用:1.精度高:PLC控制系统可以实现对液位的精确控制,提高控制精度和稳定性;2.自动化程度高:PLC可以根据设定的控制策略进行自动化控制操作,减少人工操作,提高生产效率;3.可靠性强:PLC控制系统具有较强的抗干扰能力,能够稳定运行,并且具有自动故障诊断功能,便于维护和排除故障;4.灵活性好:PLC控制系统可以根据实际需求进行灵活配置和调整,适应不同的液位控制要求。
基于PLC的触摸屏液位控制设计

74 | 电子制作 2018年8月制。
可由PLC 实现液体上料的自动化控制。
触摸屏具有实时监控、修改参数灵活、报警显示和易学易用等特点,与 PLC 控制结合,使得操作更加方便,运行可视化,大大降低了操作的风险。
本文以自动化的液体送料设计为载体,利用PLC 和 触摸屏技术,使得生产过程更加透明、安全和方便,减小劳动强度、提高生产效率,为实际生产和教育教学提供参考。
1 系统设计思路系统以触摸屏为上位机,PLC 为控制中心,以液位传感器作为液位测量装置,电磁阀作为控制对象。
液体存储器设置上限位和下限位,到达下限位时,系统发出警报,提示添加液体。
在触摸屏中操作模式有自动添加和手动添加两种,也可由实物开关开启上料过程,添加到上限位时,停止添加。
触摸屏能实时显示液体的高度,以实现可视化和实时监控。
控制系统结构图如图1所示。
图1 液位系统的控制图2 系统元器件选择与设置■2.1 控制器本系统的控制单元选用三菱FX3U—32MR,FX3U 系列三菱PLC 是第三代紧凑型微型可编程控制器,运算、存储、FX3U 系列PLC 不提供模拟量的输入端口,因此需要一个扩展模块做为液位传感器信号的处理器。
为了适用教学的多样性,选用特殊扩展模块FX3U-3A-ADP,它有两个输入端(电压信号输入、电流信号输入),一个输出端(模拟信号输出),最大分辨率为12位。
接受0~10V 直流电压输入信号和4~20mA 的直流电流输如信号。
通道的A/D 转换值被自动写入FX 3U 可编程控制器的特殊数据寄存器中,数据读写指令较为简单。
本设计用到的A/D 转换的关系图如图2所示。
图2 模拟量输入、数字量输出转换关系■2.3 液位传感器液位传感器是测量液体的高度的元器件,大多数液位传感器为压力传感器,经过压敏传感元件,把液体压力转换为电信号,再经过补偿、修正,转化成可测量的电信号(一般为4~20mA/0~5VDC)。
液位传感器分为二大类,接触式和非接触式。
基于PLC的液位控制系统毕业设计论文

基于PLC的液位控制系统毕业设计论文目录1. 内容概述 (2)1.1 研究背景 (3)1.2 研究目的 (4)1.3 研究意义 (4)1.4 国内外研究现状 (5)1.5 论文结构 (6)2. PLC控制系统基础 (7)3. 液位控制系统需求分析 (9)3.1 系统概述 (10)3.2 系统功能需求 (11)3.3 系统性能指标 (12)3.4 系统设计约束 (14)4. 液位控制系统硬件设计 (15)4.1 硬件组成及连接方式 (17)4.2 传感器选型及安装方式 (18)4.3 执行器选型及安装方式 (20)4.4 PLC选型及安装方式 (22)4.5 电气接线及调试 (24)5. 液位控制系统软件设计 (24)5.1 软件架构设计 (26)5.2 控制算法设计 (28)5.3 PLC程序编写 (29)5.4 仿真与调试 (31)6. 系统集成与测试 (33)6.1 系统集成方案设计 (34)6.2 系统测试与验证 (36)6.3 结果分析与讨论 (37)7. 结论与展望 (38)7.1 研究成果总结 (39)7.2 进一步研究方向建议 (40)1. 内容概述本毕业设计论文旨在深入研究和探讨基于可编程逻辑控制器(PLC)的液位控制系统设计与实现。
通过系统化的设计流程,结合理论分析与实际应用,全面阐述PLC在液位控制中的关键作用及其优化策略。
随着工业自动化技术的不断发展,液位控制作为工业生产过程中的重要环节,其精确性和稳定性对于保障产品质量和生产效率具有至关重要的作用。
PLC作为一种高效、可靠的工业控制设备,在液位控制领域得到了广泛应用。
本研究将围绕基于PLC的液位控制系统展开深入研究。
PLC具有强大的数据处理能力,能够实时监控液位变化,并根据预设的控制算法输出相应的控制信号。
PLC的可靠性高、抗干扰能力强,能够在恶劣的工业环境下稳定运行。
PLC还具有易于扩展和维护的特点,便于用户根据实际需求进行系统升级和改造。
安徽工程大学毕业答辩毕业论文基于plc和组态软件的液位控制系统设计

1. 概 述
目的与意义
液位控制由于其应用极其普遍,种类繁多, 其中不乏一些大型的复杂系统。它主要有以下 几个特点:1、时滞性很大,2、时变性,3、非 线性。 这几个特点,都严重影响PID控制的效果,在 实际生产中而随着生产线的更新及生产过程控 制要求的提高,要求液位控制系统有高的控制 精度,即准确稳定的液位,一般的得自动化控 制方式已不能满足工业生产控制的要求,为了 使系统具有直观准确的显示功能,我们采用 PLC和组态软件对液位进行控制。
PLC 外部设备连接
I0.0
I0.1
液位变 送器
S7-200 PLC CPU226
扩展AI模块 EM235
扩展AO模块 EM232
高液位 报警 I0.2
低液位 报警 I0.3
变频器 MM420
10
3. 系统硬软件设计
变量分配表
11
3. 系统硬软件设计
M C G S 组 态 用 户 界 面
12
4. 结 论
和
变
频
器
的 链 接 线 路
SB3
SB2
KA K1 A K2 A 3KA 4启
动
停止 SB1
手 动
KA
KA
KA HL
2
3
4
~220 V 24V
NL
1L
I0.0
Q0.
I0.1
Q0 0.
I0.2
Q1 0.
I0.3
Q2 0.
I0.4
23L
I0.5
Q0.
I0.6
Q4 0.
I0.7
Q5 0.
1L+
Q650.
I1.0
14
目录
基于PLC的变频器液位控制设计

Ci w e n生ea o£ ha e c ogsnP d nN T h li d us o : c r t
基于 P C的变频器液位控制设 计 L
张 斌 Biblioteka ( 尔滨 水 泵 厂 电 器厂 , 龙 江 哈 尔滨 10 0 ) 哈 黑 500
摘 要: 随着电力电子技 术 以及工业 自 动控制技 术的发展 , 使得 交流变频调速 系统在 工业 电机拖动领域得 到 了广泛应用。 另外 , 由于 P C的 L 功能强大、 易 用 、 容 使 高可靠性 , 常常被 用来作 为现场数 据的采集和设备的控制 。本设计就是利 用变频 器和 P C实现 水池 水位 的控制 。 L
关 键 词 :L 系统 ; 制 ; 计 P C; 控 设
前言: 变频 器技术是 一门综合性 的技术 , 它 备 的故障信 息能 够及 时反映 在远程 P C上 ; L 具 建立在控制技术 、 电子 电力技术 、 电子技术 和 有水位过高 、 报警和提示用户功能 ; 微 过低 计算机 技术 的基础 上 。它 与传统 的交 流拖动 系 2本设计控制结 构: 统 相 比,利用变频 器对交 流电动机进 行调速控 由于现场有一 台电机作 为被控对 象 ,可 以 制, 有许 多优点 , 节 电 、 易实现 对现 有 电动 使用单 台 P C进行 单个对象 的控制 ,只要适 当 如 容 L 机 的调速控制 、可以实现 大范 围内的高效连续 的选用 高性 能的 P C完全能够胜任 此功能 。系 L, 调速控制 、 实现速度 的精确控制 。容易实现 电动 统控 制结构如 图 1 所示 。 机 的正反 转切换 , 可以进行高额 度 的起停 运转 , PC L 采集 传感 器 、 监控电机及变频器等有关 可 以进行 电气制动 ,可以对 电动机进行 高速驱 的各类 对象 的信息 。本系统中 , 对电机采用一 台 动。 完善 的保护 功能: 变频器保 护功能很强 , 在运 变频 器来进行频率 的调节控制 。采用 P C输 出 L 行过程 中能随时检测 到各种故 障 ,并显示 故障 的模拟 量信 号作 为变频 器 的控制 端输入 信号 , 类别( 电网瞬 时电压 降低 , 网缺相 , 如 电 直流过 电 从 而控制 电机转速 大小 ,并且 向 P C反馈 自身 L 当发生故 障时 , 能够 向 P C发 L 压 , 率模 块过热 , 功 电机短路等 ) 立 即封 锁输 的工 作状态信号 , , 并 出电压 。这种 “ 自我保护” 的功能 , 不仅保护了变 出报 警信号 。由于变频 调速是 通过改变 电动机 频器 , 还保 护了电机不易损坏。 定子 供 电频率 以改变 同步转速来 实现 的,故 在 P C特点 : L 第一 , 可靠性 高 、 抗干扰 能力 强 , 调速 过程 中从 高速到低 速都可 以保持有 限的转 平均故障时 间为几 十万小时 。而且 P C采用 了 差 功率 , L 因此 具有 高效率 、 范 围 、 宽 高精 度 的调 许多硬件 和软 件抗干扰措 施 。第二 , 编程简 单 、 速性能 。 使用方便 目前 大多数 P C 用继电器控制形 式 L 采 3设备 的选 型 的梯形图编程方式 , 很容易被操作人员接受 。一 31P C及其扩展模块 的选型 : . L 些 P C还根据 具体问题设计 了如步进梯形指令 L 本 系统 有一 台电机 、 一个 液位传感 器 、 一个 等 , 一步简化了编程。第 三, 进 设计安装容 易 , 维 变频器 、 五个继 电器 , 共有 十八个 I / O点 , 它们构 护工作量少 。第 四 , 适用 于恶劣 的工 业环境 , 采 成被控对象 。 综合分析 各类 P C的特点 , L 最终选 用封装 的方式 , 合于各 种震 动 、 蚀 、 适 腐 有毒 气 L G公司的 K 1 0系列 P C。 一2 L 由于 K M— R 0集 7 D4 体等的应用场合 。第五 , 与外部设备 连接方便 , 成 2 输 入/ 输 出共 4 个 数字量 I 点 , 4 1 6 0 / 0 完全 采用统 一接线 方式 的可拆 装 的活动 端子 排 , 提 能满足控制要求 。 P C可连接 7 此 L 个扩展模块 , 供不 同的端子功 能适合 于多种 电气 规格。第六 , 最大 扩展 至 2 8 4 路数 字 量 I 点或 3 路模 拟 / 0 5 / O 2 K字节程序和数据存储空间 。 个 6 功能完善 、 通用性 强 、 体积小 、 能耗低 、 性能价格 量 I 点 。 6 比高。 独立的 3 k z 0 H 高速计数器 , 路独立 的 2 k z 2 0 H 高 本 系统 中,为了实现能 源的充分利 用和生 速脉冲输出 , 具有 PD控 制器 。 个 R 4 5 I 1 S 8 通讯/ 产 的需 要 , 需要对 电机进行转 速调节 , 考虑到 电 编程 口,具有 P I P 通讯协议 、 I MP 通讯协议和 自 机 的启 动 、 运行 、 调速 和制动的特性 , 采用 L G公 由方式通讯能力 。I / O端子排可很容易地整体拆 用于较高要求 的控制 系统 , 有更多的输入/ 具 司的 I5 P A变频器 , 统中 由 L S E — 系 G MA T R K系 卸。 列 P C完成数据 的采集和对变频器 、电机等设 输出点 , 强的模块扩 展能力 , 快 的运 行速度 L 更 更 备 的控制任务 。基 于 L G MAS E — L T R K P C的编 和功能更强的 内部集成特殊功能 。 程 软件, 采用 模块化 的程序 设计方 法 , 量采用 大 32变频器模块的选型 : . 代码重用 , 减少软件 的开发 和维护 。系统利用对 目前 , 市场上存在 各种各样 的变频器 , 本设 G公 司的 I 5 P A变频器 。I5 P A系列传动 P C软件 的设计 , L 实现变 频器 的参数设 置 、 故障 计采用 L 产 品最大 的优 点就是 在全功率 范围 内统一使 用 诊断和 电机 的启动和停止 。 1本设计 的控制要求 : 了相 同的控 制技术 ,例如启动 向导 ,自定 义编 系统 要求用户能 够的直观 了解现场设 备 的 程 , T D C控 制 , 通用备件 , 通用 的接 口技术 , 以及 调试和维护的通用软件工具 。内含启 T l作状 态及水位 的变化 ;要求 用户能够 远程控 用于选 型 、 令您 调试 易如 反掌 ; 自定义 编 程 : 制变频 器 的启动 和停止 ;用 户可 自行设 置水位 动引导 程序 , 犹如 P C令您发挥 自如 ; 积 L 体 的高低 , 以控制变频 器的起停 ; 变频器及其 他设 内置可编程模块 , 小 巧 : 滤波器 , 内置 斩波器及电抗器 、 性能卓越 。 4 系统的控制流程 : 41程 序设计 前准备工作 . 了解系统概 况 , 形成 整体概念 , 熟悉被控 对 象、 编制 出高质 量 的程 序 , 充分利 用手头 的硬 件
基于PLC的液位控制系统毕业设计论文

基于PLC的液位控制系统毕业设计论文随着工业自动化水平的不断提高,液位控制系统在工业领域中得到了
广泛的应用。
液位控制系统是通过感知到液体的高度来实现对液位的控制,常用于储罐、水塔等场所,以确保液位在安全范围内。
本篇毕业设计论文将基于PLC(可编程逻辑控制器)设计一个液位控
制系统。
PLC是一种专门用于工和生产过程中的自动化控制的计算机控制
系统。
本设计将通过PLC来实现对液位的检测和控制,并结合开关、传感
器和执行器等设备实现自动液位控制。
在设计过程中,首先需要对液位控制系统的硬件架构进行规划。
本设
计将使用PLC作为控制核心,并结合液位传感器、执行器和HMI(人机界面)等设备来完成整个系统。
同时,需要对传感器和执行器的选型进行讨论,并确定合适的设备参数。
其次,将进行软件编程工作。
通过PLC的编程软件,将液位传感器与PLC进行连接,并设置液位控制的逻辑程序。
根据液位高度的变化,PLC
将实时采集并处理液位信号,然后通过输出信号控制执行器,实现液位的
自动控制。
同时,将设计一个简单直观的人机界面,能够实时显示液位的
变化情况,方便操作和监控。
最后,需要进行液位控制系统的测试和验证。
通过模拟液位的变化情况,测试液位控制系统的响应速度和准确性。
根据测试结果,进行相应的
调整和改进,使其达到设计要求。
综上所述,本设计将通过PLC实现液位控制系统的设计和开发,并通
过对硬件和软件的完善,使其具备良好的稳定性、响应速度和准确性。
该
设计具有一定的实用价值,可在工业领域中得到广泛的应用。
基于PLC的液体混合控制系统设计
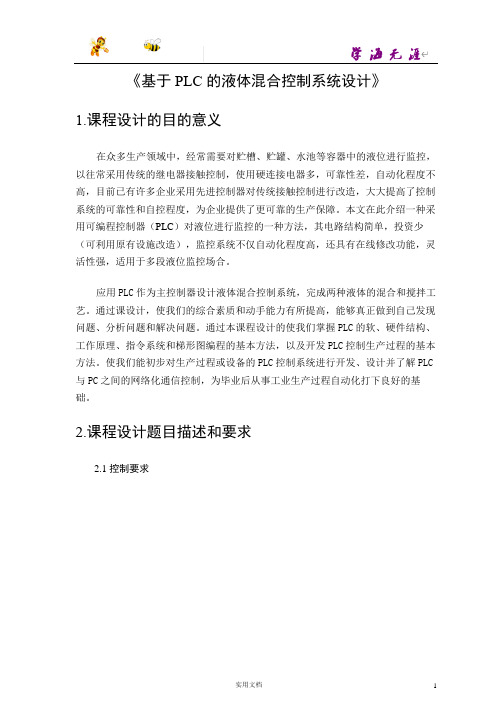
《基于PLC的液体混合控制系统设计》1.课程设计的目的意义在众多生产领域中,经常需要对贮槽、贮罐、水池等容器中的液位进行监控,以往常采用传统的继电器接触控制,使用硬连接电器多,可靠性差,自动化程度不高,目前已有许多企业采用先进控制器对传统接触控制进行改造,大大提高了控制系统的可靠性和自控程度,为企业提供了更可靠的生产保障。
本文在此介绍一种采用可编程控制器(PLC)对液位进行监控的一种方法,其电路结构简单,投资少(可利用原有设施改造),监控系统不仅自动化程度高,还具有在线修改功能,灵活性强,适用于多段液位监控场合。
应用PLC作为主控制器设计液体混合控制系统,完成两种液体的混合和搅拌工艺。
通过课设计,使我们的综合素质和动手能力有所提高,能够真正做到自己发现问题、分析问题和解决问题。
通过本课程设计的使我们掌握PLC的软、硬件结构、工作原理、指令系统和梯形图编程的基本方法,以及开发PLC控制生产过程的基本方法。
使我们能初步对生产过程或设备的PLC控制系统进行开发、设计并了解PLC 与PC之间的网络化通信控制,为毕业后从事工业生产过程自动化打下良好的基础。
2.课程设计题目描述和要求2.1控制要求按下起动按钮,电磁阀Y1闭合,开始注入液体A ,按L2表示液体到了L2的高度,停止注入液体A 。
同时电磁阀Y2闭合,注入液体B ,按L1表示液体到了L1的高度,停止注入液体B ,开启搅拌机M ,搅拌20s ,停止搅拌。
同时Y3为ON ,开始放出液体至液体高度为L3,再经10s 停止放出液体。
同时液体A 注入。
开始循环。
按停止按钮,所有操作都停止,须重新启动。
2.2 I/O 分配输入 输出起动按钮:I0.0 Y1:Q0.1停止按钮:I0.4 Y2:Q0.2L1按钮:I0.1 Y3:Q0.3L2按钮:I0.2 M :Q0.4L3按钮:I0.33、结构框图3.课程设计报告内容3.1 总体设计图3.1 结构框图3.2变频调速CPU224 MM440 EM235 电动机图 2.1 液体混合罐示意3.2.1变频调速的工作原理图改变供电电压的频率可以实现对交流电动机的速度控制,这就是变频调速。
基于PLC的变频器液位控制设计

基于PLC的变频器液位控制设计在工业控制领域中,液位控制是一个常见的任务。
液位控制的主要目标是维持容器中的液体的稳定液位。
在过去,这通常是通过使用传统的电气组件和传感器来实现的。
然而,近年来,随着PLC(可编程逻辑控制器)技术的发展以及变频器的普及,基于PLC的变频器液位控制设计变得越来越受欢迎。
本文将介绍基于PLC的变频器液位控制设计的步骤和原理。
步骤1:硬件配置要实现基于PLC的变频器液位控制设计,需要一个PLC控制器、一个变频器、一个电动阀门和一个液位传感器。
首先,将PLC控制器连接到计算机上,并使用PLC编程软件进行配置。
然后,将变频器连接到PLC控制器,并将电动阀门和液位传感器分别连接到变频器。
步骤2:软件编程使用PLC编程软件创建一个新的程序,并编写逻辑代码来控制液位。
在程序中,可以定义变量来存储液位传感器的数据,以及设置变频器的输出频率。
通过使用逻辑代码,可以实现液位控制的逻辑。
步骤3:传感器校准在操作之前,需要对液位传感器进行校准。
校准液位传感器是确保液位测量精确性的重要步骤。
可以使用已知液位的参考容器来进行校准,并使用PLC编程软件来调整传感器的输出。
步骤4:参数设置通过PLC编程软件,可以设置变频器的参数。
这些参数包括变频器的输出频率范围、启动和停止时间、加减速度等。
根据液位变化的速度和容器的大小,可以根据实际需求进行参数设置。
步骤5:控制逻辑通过PLC编程软件,可以编写逻辑代码来实现液位控制的功能。
根据液位传感器的数据和设定的控制逻辑,PLC可以控制变频器的输出频率来调整电动阀门的开闭程度,从而实现液位的控制。
原理基于PLC的变频器液位控制设计基于反馈控制原理。
液位传感器通过感知容器的液位,并将液位数据传输给PLC。
PLC根据液位传感器的数据和预设的控制算法来控制变频器的输出频率。
变频器会根据PLC发出的指令来调整电动阀门的开闭程度,从而实现液位的控制。
如果液位低于预设值,PLC将增加变频器的输出频率,使电动阀门打开。
- 1、下载文档前请自行甄别文档内容的完整性,平台不提供额外的编辑、内容补充、找答案等附加服务。
- 2、"仅部分预览"的文档,不可在线预览部分如存在完整性等问题,可反馈申请退款(可完整预览的文档不适用该条件!)。
- 3、如文档侵犯您的权益,请联系客服反馈,我们会尽快为您处理(人工客服工作时间:9:00-18:30)。
基于PLC的变频器液位控制设计
随着电力电子技术以及工业自动控制技术的发展,使得交流变频调速系
统在工业电机拖动领域得到了广泛应用。
另外,由于PLC的功能强大、容易使用、高可靠性,常常被用来作为现场数据的采集和设备的控制。
本设计就
是利用变频器和PLC实现水池水位的控制。
变频器技术是一门综合性的技术,它建立在控制技术、电子电力技术、微
电子技术和计算机技术的基础上。
它与传统的交流拖动系统相比,利用变频
器对交流电动机进行调速控制,有许多优点,如节电、容易实现对现有电动
机的调速控制、可以实现大范围内的高效连续调速控制、实现速度的精确控制。
容易实现电动机的正反转切换,可以进行高额度的起停运转,可以进行
电气制动,可以对电动机进行高速驱动。
完善的保护功能:变频器保护功能很强,在运行过程中能随时检测到各种故障,并显示故障类别(如电网瞬时电压降低,电网缺相,直流过电压,功率模块过热,电机短路等),并立即封锁输出电压。
这种“自我保护”的功能,不仅保护了变频器,还保护了电机不易损坏。
PLC特点:第一,可靠性高、抗干扰能力强,平均故障时间为几十万小时。
而且PLC采用了许多硬件和软件抗干扰措施。
第二,编程简单、使用方便目前大多数PLC采用继电器控制形式的梯形图编程方式,很容易被操作人员接受。
一些PLC还根据具体问题设计了如步进梯形指令等,进一步简化了编程。
第三,设计安装容易,维护工作量少。
第四,适用于恶劣的工业环境,采用
封装的方式,适合于各种震动、腐蚀、有毒气体等的应用场合。
第五,与外
部设备连接方便,采用统一接线方式的可拆装的活动端子排,提供不同的端
子功能适合于多种电气规格。
第六,功能完善、通用性强、体积小、能耗低、。