HAZET工具套件
沙特维克TH540规格书说明书

Technical Specification Spec number TH540-22 2012-11-16 Sandvik TH540Technical SpecificationSandvik Mining and Construction Reserves the right to change this specification without further notice.APPLICATIONSThe Sandvik TH540 is a high performance 40 tonne articulated underground dump truck for use in 5,0 x 5,0 meter haulage ways. Operator safety, health and comfort are enhanced by the enclosed, vibration isolation, ISO approved cabin. The TH540 is well suited for:• level or steep ramp production haulage in medium to large mines • mine development projects in medium to large mines • tunneling projects with restricted height• 3 pass loading with the Sandvik LH514 loaderCapacitiesPayload capacity 40 000 kg 88 200 lb Dump box22,0 m 3 28,8 yd³ Main dimensionsTotal length10 696mm 421 “ Maximum width 3 065 mm 121 “ Height2 896 mm 114 “ Height of the box2 876 mm113 “Dump Box Motion Times & MovementsDischarging time 14,0 secDumping angle61 º Speeds Forward & Reverse (Level / Loaded)1st gear 5,5 km/h 3,4 mph 2nd gear 7,2 km/h 4,5 mph 3rd gear 9,8 km/h 6,1 mph 4th gear 13,0 km/h 8,1 mph 5th gear 17,2 km/h 10,7 mph 6th gear 22,8 km/h 14,2 mph 7th gear31,1 km/h19,3 mph Reversing with 1st and 3rd gearSandvik Mining and Construction Reserves the right to change this specification without further notice.DIMENSIONS (SIDE VIEW)DIMENSIONS (TOP AND REAR VIEW)POWER TRAINEngineDiesel engine Volvo TAD1640VE (Tier 2) Output 405 kW (543 hp) @ 1 900 rpm Torque 2 761 Nm @ 1 200 rpmNumber of cylinders In-line 6Displacement 16,1 lCooling system Liquid cooledCombustion principle 4-stroke, direct injection, turbocharged, after cooledAir filtration Dry typeElectric system 24 VExhaust system Heat shield for exhaust manifold &turboAverage FuelConsumption49,0 l/h (at 50% load)Fuel Tank Capacity 700 l (185 gal)ConverterDana C9000 series With lock-upTransmissionDana 8000 series Power shift transmission withautomatic electric shift. Sevengears forward and two reverse. AxlesFront axle Kessler D106, oscillation ±13º Rear axle Kessler D106, fixedTiresTire size 29.5R25 E4**Brand and type subject to availabilityVEHICLE WEIGHTSOperating weightsTotal operating weight 34 700 kg76 400 lb Front axle25 900 kg57 000 lb Rear axle 8 800 kg19 400 lb Loaded weightsTotal loaded weight 74 700 kg164 600 lb Front axle 37 200 kg82 000 lb Rear axle 37 500 kg82 700 lb STANDARD OPERATORS COMPARTMENTISO certified ROPS/FOPS cabin with air conditioning Height 2 896 mm114”FRAMERear and front frame Welded steel box construction Central hinge Box constructed, adjustable lowerbearingSTEERING HYDRAULICSFully hydraulic, center articulated, power steering with two double acting cylinders. Closed centre system with a load sensing piston pump and pilot operated orbitral wheel steering.Turning RadiusTurning angle ±42,5 ° Inner 5 015 mm 197 ” Outer 9 132 mm 360 “ Main ComponentsHydraulic pump Variable displacement pistonpumpControl valve Pilot operatedCylinders 125 mm bore X 90 mm rodDUMP BOX HYDRAULICSFull hydraulic system, equipped with variable displacement piston pump. Oil flow to box hydraulic system from the steering hydraulics. Oil flow from the brake circuit pump is divided to the brake system and the oil cooler motor.Main ComponentsHydraulic pump Variable displacement pistonpumpControl valve Solenid operatedCylinders (2) 160 mm bore 110 mm rod Hydraulic oil tankcapacity225 l (60 gal)BRAKESService brakes are spring applied, hydraulically released, liquid cooled (LCB) multi-disc brakes on all wheels with two separate circuits for the front and rear axles. Service brakes also function as an emergency brake, when the emergency brake system is engaged.Main ComponentsPressure accumulator Piston type with chargingvalveBrake valve foot operated pedal, fullymodulatedBrake hydraulic tank 100 l (26,4 gal)Automatic BrakeActivationABASandvik Mining and Construction Reserves the right to change this specification without further notice.Sandvik Mining and Construction Reserves the right to change this specification without further notice. ELECTRICAL EQUIPMENTAlternator 2 x 28 V 140 A, Bosch Batteries 2 x 12V, 160 Ah Starter 24V Lights• Driving 4 x H365W, front & rear • Working 1 pc (H3 65 W) • Parking 4 pcs • Brake 2 pcs • Turn signals 4 pcsInstrumentation5,7 in LCD displaySAFETY AND ERGONOMICSROPS/FOPS certified operators compartment Low frequency suspension seat Adjustable armrests Seat beltLockable main switch Reverse alarm (CEN)External shutdown, 2 pcs in rear ABA brake systemSTANDARD MANUALSInstructions Manual- Operator’s Manual Hard copy, EU-languages - Maintenance Manual Hard copy, EU-languagesParts ManualHard copy, English Service and Repair ManualHard copy, English ToolMan CD (2 pcs)Electronic, in pdf. format, includes all the above manualsOTHER STANDARD EQUIPMENTAuxiliary Engine Brake - Volvo VEB (D16 only) Cyclone pre-filter for A/C device Fire extinguisher, 12 kg (CEN) Flashing beacon Reversing cameraWheel chocks and bracketsOPTIONAL EQUIPMENT Alternative Engines Alternative boxesMaterial density (t/m³) 2,2 2,0 1,7 Volume (m³) 18,0 20,0 24,0 Width(mm) 3 000 3 000 3 150Ejector box 20,0 m³, width 2 980 mmSandvik Mining and Construction Reserves the right to change this specification without further notice.GRADE PERFORMANCEEmptyPercent grade 0 5 10 15 201st gear (km/h) 5,5 5,4 5,4 5,4 5,4 2nd gear (km(h) 7,2 7,2 7,1 7,1 7,0 3rd gear (km/h) 9,8 9,7 9,7 9,6 9,5 4th gear (km/h) 13,0 12,8 12,7 12,5 12,4 5th gear (km/h) 17,2 16,9 16,6 16,4 14,46th gear (km/h) 22,8 22,3 21,8 19,47th gear (km/h) 31,130,126,1LoadedPercent grade0 5 10 15 201st gear (km/h) 5,5 5,4 5,3 5,3 5,2 2nd gear (km(h) 7,2 7,1 7,0 6,9 6,6 3rd gear (km/h) 9,8 9,6 9,4 8,8 5,0 4th gear (km/h) 12,9 12,6 11,8 9,2 5th gear (km/h) 17,1 16,5 12,46th gear (km/h) 22,6 20,37th gear (km/h) 30,6PRODUCTIVITY CURVEVolvo TAD1640VE Tier 2 and TAD1660 Tier 4iCalculated with 2% rolling resistance With lock-upTRACTIVE EFFORT CURVESandvik Mining and Construction Reserves the right to change this specification without further notice.。
黑德克·RT650旋转工具说明书

Copyright Black & Decker2RT650_UK.PM513-11-2000, 11:033RT650_UK.PM513-11-2000, 11:234ROTARY TOOL RT650CONGRATULATIONS!You have chosen a Black & Decker tool. Our aim is to provide quality tools at an affordable price.We hope that you will enjoy using this tool formany years.EC DECLARATION OF CONFORMITY RT650Black & Decker declares that these products conform to:98/37/EC, 89/336/EEC, 73/23/EEC,EN 50144, EN 55014, EN 60555Level of sound pressure, measured according to EN 50144:RT650L pA (sound pressure)dB(A)66.8L WA (acoustic power)dB(A)79.9Always wear ear protection if the sound pressure exceeds 85 dB(A).Hand/arm weighted vibration value according to EN 50144:RT6501.4 m/s2Colin Wills Director of Engineering BDCI, 4/F, 2 Dai Wang Street Tai Po Industrial EstateTai Po NT, Hong Kong INTENDED USEYour Black & Decker rotary tool RT650 has been designed for the following applications using the appropriate accessories:-Drilling in wood, metal and plastics-Cutting wood, metal and plastics-Engraving and shaping wood, metal,plastics and fibreglass-Polishing metal, glass and stone-Grinding metal, glass and ceramics-Sharpening metal-Sanding wood and fibreglass-Removing rust and corrosion from metalThis tool is intended for consumer use only.SAFETY INSTRUCTIONSWarning symbolsThe following symbols are used in this manual:Denotes risk of personal injury, loss of lifeor damage to the tool in case of non-observance of the instructions in thismanual.Denotes risk of electric shock.Read the manual prior to operation.Know your toolx Warning! When using mains-poweredtools, basic safety precautions, includingthe following, should always be followedto reduce the risk of fire, electric shock,personal injury and material damage.x Read all of this manual carefully beforeoperating the tool.x Before operating the tool, make surethat you know how to switch the tool off in an emergency.x Retain this manual for future reference.E N G L I SHRT650_UK.PM513-11-2000, 15:105General 1.Keep work area clean Cluttered areas and benches can cause accidents.2.Consider work area environment Do not expose the tool to rain. Do not use the tool in damp or wet conditions. Keep the work area well lit. Do not use the tool where there is a risk of causing fire or explosion, e.g. in the presence of flammable liquids and gases.3.Keep children away Do not allow children, visitors or animals to come near the work area or to touch the tool or mains cable.4.Dress properly Do not wear loose clothing or jewellery, as these can be caught in moving parts. Preferably wear rubber gloves and non-slip footwear when working outdoors. Wear protective hair covering to keep long hair out of the way.5.Personal protection Always use safety glasses. Use a face or dust mask whenever the operations may produce dust or flying particles. Wear ear protection whenever the sound level seems uncomfortable.6.Guard against electric shock Prevent body contact with earthed or grounded surfaces (e.g. pipes, radiators,cookers and refrigerators). Electric safety can be further improved by using a high-sensitivity (30 mA/30 mS) residual current device (RCD).7.Do not overreach Keep proper footing and balance at all times.8.Stay alert Watch what you are doing. Use common sense.Do not operate the tool when you are tired.9.Secure workpiece Use clamps or a vice to hold the workpiece.It is safer and it frees both hands to operate the tool.10.Connect dust extraction equipment If devices are provided for the connection of dust extraction and collection facilities, ensure that these are connected and properly used.11.Remove keys and adjusting wrenches Always check that keys and adjusting wrenches are removed from the tool before operating the tool.12.Extension cablesBefore use, inspect the extension cable andreplace if damaged. When using the tooloutdoors, only use extension cables intendedfor outdoor use.e appropriate toolThe intended use is described in this instruction manual. Do not force small tools or attachments to do the job of a heavy-duty tool. The tool will do the job better and safer at the rate for whichit was intended. Do not force the tool.Warning! The use of any accessory orattachment or performance of any operation with this tool other than those recommendedin this instruction manual may present a risk ofpersonal injury.14.Check for damaged partsBefore use, carefully check the tool and mains cable for damage. Check for misalignment and seizure of moving parts, breakage of parts,damage to guards and switches and any otherconditions that may affect its operation.Ensure that the tool will operate properly and perform its intended function. Do not use the tool if any part is damaged or defective.Do not use the tool if the switch does not turn iton and off. Have any damaged or defective parts repaired or replaced by an authorised repair agent. Never attempt any repairs yourself.15.Unplug the toolUnplug the tool when it is not in use, beforechanging any parts of the tool, accessories orattachments and before servicing.16.Avoid unintentional startingDo not carry the tool with a finger on theon/off switch. Be sure that the tool is switchedoff when plugging in.17.Do not abuse cordNever carry the tool by its cord or pull it to disconnect from the socket. Keep the cordaway from heat, oil and sharp edges.18.Store idle toolsWhen not in use, tools should be stored in a dry,locked up or high place, out of reach of children.19.Maintain tools with careKeep cutting tools sharp and clean for better and safer performance. Follow the instructions for maintenance and changing accessories.RT650_UK.PM513-11-2000, 11:036Keep handles and switches dry, clean and free from oil and grease.20.Repairs This tool complies with relevant safety requirements. Repairs should only be carriedout by qualified persons using original spare parts; otherwise this may result in considerable danger to the user.Additional safety instructions for rotary tools Wear safety glasses or goggles whenoperating this tool.x Only use Black & Decker accessoriesrecommended for this tool.x Never use any worn, cracked or damagedaccessories.x Hold the tool away from your face whenswitching on.x Keep your fingers away from rotating accessories.x Be careful not to accidentally hit any foreign objects in the workpiece.x Be aware that accessories may be hot shortly after use.x If an accessory jams, switch the tool off and unplug it before attempting to free the accessory.x Clamp the workpiece whenever possible,especially when using cutting discs.x Wear a dust mask whenever sanding.x Thoroughly remove all dust after sanding.x Take special care when sanding paint which is possibly lead based or when sanding some woods (e.g. MDF) and metal which may produce toxic dust:-Wear a dust mask specifically designed for protection against lead paint dust and fumes and ensure that persons within or entering the work area are also protected.-Do not let children or pregnant women enter the work area.-Do not eat, drink or smoke in the work area.-Dispose of dust particles and any otherdebris safely.ELECTRICAL SAFETYThe electric motor has been designed for onevoltage only. Always check that the power supplycorresponds to the voltage on the rating plate.This tool is double insulated in accordance with EN 50144; therefore no earth wire is required.Mains plug replacement (U.K. & Ireland only)x Should your mains plug need replacing and you are competent to do this, proceed as instructed below. If you are in doubt, contact an authorised repair agent or a qualified electrician.x Disconnect the plug from the supply and remove the fuse from the plug.x Cut off the plug and dispose of it safely; a plug with bared copper conductors is dangerous if engaged in a live socket outlet.x Only fit 13 Amperes BS1363A approved plugs fitted with the correctly rated fuse (1).x The cable wire colours, or a letter, will be marked at the connection points of most good quality plugs. Attach the wires to their respective points in the plug (see above).Brown is for Live (L) (2), blue is for Neutral (N) (4).x Before replacing the top cover of the mains plug ensure that the cable restraint (3)is holding the outer sheath of the cable firmly and that the leads are correctly fixed at the terminal screws.x If the plug has a fuse cover, make sure that the fuse cover is fitted. Do not use the plug if thefuse cover is missing or damaged.Never use a light socket.E N G L I SHRT650_UK.PM513-11-2000, 11:037Using an extension cable Always use an approved extension cable suitable for the power input of this tool (see technical data). Before use, inspect the extension cable forsigns of damage, wear and ageing. Replace the extension cable if damaged or defective.When using a cable reel, always unwind the cable completely. Use of an extension cable not suitable for the power input of the tool or which is damaged or defective may result in a risk of fireand electric shock.CARTON CONTENTS The carton contains:1Rotary tool 1Wrench 1Accessories and application guide 1Instruction manual x Carefully unpack all parts.x Please note that additional items may be found in the carton, depending on the letter suffix following the catalogue number of yourtool.OVERVIEW (fig. A)1.On/off switch 2.Spindle lock 3.Speed control knob 4.Collet 5.Collet nut6.Spindle7.Suspension hookASSEMBLY Before assembly, make sure that the tool is switched off and unplugged.Fitting and removing accessories (fig. B)x Make sure that the tool is switched off and unplugged.x Activate the spindle lock (2) by setting it to position B as shown.x Slacken the collet nut (5) by turningcounterclockwise.x Insert the shaft of the accessory into the collet as far as it will go.x Securely tighten the collet nut.x Release the spindle lock (2) by setting it toposition A as shown.x Make sure that the collet size matches the shaft diameter.x Never tighten the collet nut without an accessory in the collet.x Tighten and loosen the collet by hand if possible. If necessary, use the supplied wrench to loosen the collet. Do not useany tools that could mark the finish orbreak the collet.Replacing collets (fig. C)This tool is supplied with a 3.2 mm collet.Different sizes are available as an accessory toaccomodate a wide range of accessories. To fit thecorrect collet for the accessory to be used:x Make sure that the tool is switched off and unplugged.x Activate the spindle lock (2) by setting it to position B as shown.x Remove the collet nut (5) by turningcounterclockwise.x Pull the collet off the spindle (6).x Place the new collet into the spindle.x Loosely screw the collet nut onto the spindle.x Release the spindle lock (2) by setting it toposition A as shown.USELet the tool work at its own pace.Do not overload.x If you are not sure about the correctspeed setting, start with a low speedsetting and gradually increase it untilyou find the optimum setting.x Where indicated, never exceed the speed rating of an accessory. The wire brush accessory must not be used above speed setting 3 (15,000 min -1).Variable speed control (fig. D)The variable speed control allows you to adapt the speed of the tool to the application.RT650_UK.PM513-11-2000, 11:038x Set the control knob (3) to the desired setting.At setting 1 the tool will operate at low speed,8,000 min -1. At setting 6 the tool will operate at the maximum speed, 27,000 min -1.The table below suggests settings for different applications.Application Setting Drilling holes 4-5Cutting metal 5-6Engraving metal 4-5Removing rust 1-2Sharpening 3-5Polishing 1-2Sanding wood 5-6Removing paint 3-5Switching on and off (fig. E)x To switch the tool on, slide the on/off switch (1)forward (position I ).x To switch the tool off, slide the on/off switch to the rear (position 0).Hints for optimum use x Always hold the tool securely as shown in fig. F. For precision work, hold the tool near the front.x Do not exert too much pressure on the tool.x Consult your retailer for more information onavailable accessories.MAINTENANCE Your Black & Decker tool has been designed to operate over a long period of time with a minimum of maintenance. Continuous satisfactory operation depends upon proper tool care andregular cleaning.Before performing any maintenance,switch off and unplug the tool.x Regularly clean the ventilation slots in your tool using a soft brush or dry cloth.x Regularly clean the motor housing using a damp cloth. Do not use any abrasive orsolvent-based cleaner.PROTECTING THE ENVIRONMENT Should you find one day that your tool needs replacement, or if it is of no furtheruse to you, think of the protection of theenvironment. Black & Decker repair agents will accept old Black & Decker tools andensure that they are disposed of in anenvironmentally safe way.Technical dataRT650Voltage V AC 230Power input W 90No-load speed min -18,000 - 27,000Weight kg$GUARANTEE (UK, SOUTH AFRICA,AUSTRALIA AND NEW ZEALAND ONLY)Should your Black & Decker product become defective due to faulty materials or workmanship,within 24 months from the date of purchase,we guarantee to either replace all defective partsor -at our discretion- to replace the unit free ofcharge, provided that:x The product is returned to us or one of our authorised repair agents with proof of purchase.x The product has not been used for trade,professional or hire purposes.x The product has not been subjected to misuse or neglect.x The product has not sustained any damagethrough foreign objects, substances or accidents.x Repairs have not been attempted by anyone other than our service staff or authorised repair agents.This guarantee is offered as an extra benefit anddoes not affect your statutory rights.AFTER SALES SERVICE(UK, SOUTH AFRICA, AUSTRALIA ANDNEW ZEALAND ONLY)Black & Decker offers a nationwide network of authorised repair agents. The use of other than genuine Black & Decker parts and accessories may reduce the performance of the tool and cause personal injury and material damage.E N G L I SHRT650_UK.PM513-11-2000, 11:039The terms and conditions of the warranty could alsobe rendered void.OUR AFTER SALES SERVICE POLICY(UK, AUSTRALIA AND NEW ZEALAND ONLY)Full details on our after-sales service are available on the Internet at .Alternatively, contact our Service and Information Centre at the address towards the back of this manual.It is our aim that all Black & Decker customers should be totally satisfied with theirBlack & Decker product and our after sales service.If any help or advice is needed, please contact your local Black & Decker repair agent.If your product needs repair, please take or send it to an authorised repair agent, providing proof ofpurchase if claiming a guarantee repair.OTHER DIY TOOLSBlack & Decker has a full range of tools that make DIY jobs easy. If you would like further information on the following products, please contact our Service and Information Centre (see the address page towards the end of this manual) or your local Black & Decker retailer.DrillsCordless screwdriversCordless drills/screwdriversSandersJigsawsCircular sawsMitre sawsAngle grindersPlanersRoutersCorded and cordless multi-purpose tools Paint strippersWorkbenchesWe also have a wide range of accessories for the above tools.Not all products are available in all countries.RT650_UK.PM513-11-2000, 11:0310RT650_UK.PM513-11-2000, 11:0311RT650_UK.PM513-11-2000, 11:031213RT650_UK.PM513-11-2000, 11:03AustraliaD E WALT Industrial Power Tool Company Tel. 03 9895 92007 Clarice RoadFax 03 9899 7465Box Hill, Victoria 3128New ZealandBlack & DeckerTel. 09 579 760081 Hugo Johnson DriveFax 09 579 8200Penrose, Auckland, New Zealand South AfricaBlack & Decker South Africa (Pty) Ltd Tel. (011) 653-1400Physical address:Fax (011) 653-1499146 Lechwe Street Corporate parkRandjiesfontein, Midrand Postal address:Postnet Suite 107, Private Bag X65Halfway House 1685United KingdomBlack & Decker Tel. 01753 511234210 Bath RoadFax 01753 551155Slough, Berkshire SL1 3YDHelpline 01753 574277RT650_UK.PM513-11-2000, 15:0614RT650_UK.PM513-11-2000, 11:0315GUARANTEE CARDPlease complete this section immediately after the purchase of your tool and send it to Black & Decker in your country. If you live in Australia or New Zealand, please register by using the alternative guarantee card supplied.¡RT650_UK.PM513-11-2000, 15:0616。
GEDORE 3 4英寸水槽扳手套件说明书

p e "p e ! "UD 32 EAJUEGO DE LLAVES DE VASO 3/4"14 piezas› C on llaves de vaso hexagonales o perfil UD, forjadas y revenidas, uso manual › C on accesorios de acero al vanadio GEDORE 31CrV3› J uego U-2 con carraca reversible con moleta, dentado fino › J uego Z-94 con carraca de cuadradillo pasante › E n caja de metal de color GEDORE azul › D imensiones: 525 x 203 x 73 mmCarracaVasosAccessorios 0Código №! 3293 Z-943 D 32 15/16 1.1/16 1.1/8 1.1/4 1.5/16 1.3/8 1.1/2 1.5/8 1.7/8 2"+ 3287' 3290-8 -1611,36280500 D 32 EAZ" 3293 U-23 D 32 15/16 1.1/16 1.1/8 1.1/4 1.5/16 1.3/8 1.1/2 1.5/8 1.7/8 2"+ 3287' 3290-8 -1611,36280690 D 32 EAU-2D 32 EMAU-2JUEGO DE LLAVES DE VASO 3/4"25 piezas› C on llaves de vaso perfil UD, forjadas y revenidas, uso manual › C on accesorios de acero al vanadio GEDORE 31CrV3 › C on carraca reversible con moleta, dentado fino › E n caja de metal de color GEDORE azul › D imensiones: 660 x 230 x 80 mmCarracaVasosAccessorios 0Código №" 3293 U-23 D 32 22 24 27 30 32 36 41 46 503 D 32 7/8 15/16 1" 1.1/16 1.1/8 1.1/4 1.5/16 1.3/8 1.1/2 1.11/16 1.7/8 2"+ 3287' 3290-8 -1618,26281310 D 32 EMAU-2... ¡A TU MEDIDA!¡Individual – preciso – hecho a medida – flexible – simplemente perfecto!› E mpezando por dimensiones personalizadas, tratamiento de superficies especiales (color y/o acabado), pasando por módulos de herramientas hechos a medida, hasta productos electrónicos con programaciones especiales o el establecimiento de intervalos de mantenimiento individuales (servicios en general, servicios de calibración ) y mucho más.› N OSOTROS desarrollamos herramientas especiales, herramientas personalizadasy/o piezas de forja de calidad para USTED . › N os ocupamos de sus problemas. › ¡Contacte con nosotros!VASOS Y ACCESORIOS›A cero al vanadio GEDORE 31CrV3, cromadoP UPUU 32LLAVE DE VASO 3/4"hexagonal›E jecución según DIN 3124, ISO 2725-1›C on cuadradillo de accionamiento interior según DIN 3120 - D 20, ISO 1174,con seguro de pasador›U so manual, moleteado en cruz›A cero al vanadio GEDORE 31CrV3, cromado* fuera de norma!L d1d2t0Código№18*51,528,336,019,00,219626988032 1819*51,529,636,019,00,225627011032 192151,532,036,019,00,228626996032 212251,533,336,019,00,232627038032 222451,535,838,019,50,267627046032 242754,539,636,024,00,271627054032 2729*54,542,036,023,50,281627062032 293057,543,338,026,00,331627070032 303257,545,838,027,00,345627089032 3233*57,547,040,026,50,392627003032 333457,548,340,026,50,404627941032 34!L d1d2t0Código№3659,550,840,028,00,448627097032 3638*59,553,340,528,00,476627100032 384162,557,144,030,50,593627119032 414665,563,344,032,50,700627127032 465068,568,348,034,50,848627135032 505568,574,653,033,01,008627143032 556068,580,853,033,01,143627151032 60D 32 (MM)LLAVE DE VASO 3/4"perfil UD›E jecución según DIN 3124, ISO 2725-1›C on cuadradillo de accionamiento interior según DIN 3120 - D 20, ISO 1174,con seguro de pasador›U so manual, moleteado en cruz›A cero al vanadio GEDORE 31CrV3, cromado* fuera de norma!L d1d2t0Código№19*51,529,636,019,00,2216272160 D 32 192151,532,036,019,00,2236289800 D 32 212251,533,336,019,00,2276272240 D 32 222451,535,838,019,50,2576272320 D 32 242754,539,636,024,00,2556272400 D 32 2729*54,542,036,023,50,2726272590 D 32 293057,543,338,026,00,3196272670 D 32 303257,545,838,027,00,3326272750 D 32 3233*57,547,040,026,50,3586277040 D 32 333659,550,840,028,00,4186272830 D 32 36!L d1d2t0Código№38*59,553,340,528,00,4416272910 D 32 384162,557,144,030,50,5586273050 D 32 414665,563,344,032,50,6416273130 D 32 465068,568,348,034,50,8006273210 D 32 505568,574,653,033,00,9616273480 D 32 556068,580,853,033,01,0526273560 D 32 60 VASOS Y ACCESORIOSITX 32 T80U3290-83290-163296MANGO ARTICULADO 3/4"› E jecución según DIN 3122, ISO 3315› P ara llaves de vaso de uso manual con cuadradillo de accionamiento segúnDIN 3120, ISO 1174, con seguro de pasador › A cero al vanadio GEDORE 31CrV3, cromadoa "a y 0Código №3/4205471,965627925032963287MANGO CORREDIZO 3/4"› E jecución según DIN 3122, ISO 3315› P ara llaves de vaso de uso manual con cuadradillo de accionamiento segúnDIN 3120, ISO 1174, con seguro de pasador › A cero al vanadio GEDORE 31CrV3, cromadoa "a y 0Código №3/4205001,161627836032873290ALARGADERA 3/4"› E jecución según DIN 3123, ISO 3316› P ara llaves de vaso de uso manual con cuadradillo de accionamiento segúnDIN 3120, ISO 1174, con seguro de pasador › A cero al vanadio GEDORE 31CrV3, cromadoa "a y 0Código №3/4202000,57462784403290-8a "a y 0Código №3/4204001,07962785203290-16VASOS Y ACCESORIOSDVV-40ZRS 3353/4“1/2“20 mm 12,5 mm 3295 ARTICULACIÓN UNIVERSAL 3/4" › E jecución según DIN 3123, ISO 3316› P ara llaves de vaso de uso manual con cuadradillo deaccionamiento según DIN 3120, ISO 1174, con seguro de pasador › A cero al vanadio GEDORE 31CrV3, cromadoa "a Q "Q y 0Código№3/4203/4201080,580627917032953219PIEZA REDUCTORA 3/4" - 1/2"› E jecución según DIN 3123, ISO 3316› P ara llaves de vaso de uso manual con cuadradillo de accionamiento segúnDIN 3120, ISO 1174, con seguro de pasador › A cero al vanadio GEDORE 31CrV3, cromadoQ "Q a "a y 0Código№3/4201/212,5560,16862780103219。
海斯特器盒Hyster H40-60XT系列技术指南说明书

H40-60XT SERIESTECHNICAL GUIDE15151011372235C38E7XWDT HEAD CLEARANCESEE CHART 182019H40-50XT 44.4 (1129)H60XT 45.2 (1149)17b 2116Circled dimensions correspond to the line numbers on the tabulated chart inside the Technical Guide. Dimensions are in inches (mm).DIMENSIONS151011372235C 38E 7XWDTHEAD CLEARANCESEE CHART182019H40-50XT 44.4 (1129)H60XT 45.2 (1149)17a17b2116TRUCKMODEL C D E TW X in (mm)percentpercentin (mm)in (mm)in (mm)H40XT 17.1 (434)7053 6.6 (168)13.7 (349)27.6 (702)H50XT 19.5 (495)5553 6.6 (168)13.7 (349)27.6 (702)H60XT20.4 (518)58587.4 (168)14.5 (369)28.4 (722)HEAD CLEARANCESeat TypeStandard OHG*Optional OHG*Non-Suspension 46.9 (1192)43.0 (1092)36.9 (939)Full-Suspension46.9 (1192)N/AN/A* Seat in depressed position* This model may be equipped with an optional load weight system with an auxiliary display. The system must be calibrated for best results. The mast must be vertical and the forks at 350mm (14”). If these procedures are met the weight indicated on the display will be +/- 8%.CERTIFICATION: Hyster lift trucks meet the design and construction requirements of B56.1-1969, per OSHA Section 1910.178(a)(2), and also comply with the B56.1 revision in effect at time of manufacture. Certification of compliance with the applicable ANSI standards appears on the lift truck.Performance specifications / ratings are for truck equipped as described under Standard Equipment in this Technical Guide. Performance specifications are affected by the condition of the vehicle and how it is equipped, as well as by the nature and condition of the operating area. Specifications are subject to change and the proposed application should be discussed with your authorized Hyster Company Dealer.Limited by traction. For further information on this dimension, please contact your local Hyster ® dealer.G E N E R A L1Manufacturer Name Hyster Company 2Model H40XT*H50XT*H60XT*EnginePSI 2.4L 3Rated Capacitylb (kg)4000 (1814)5000 (2268)6000 (2722)4Load Center, Distance in (mm)24 (610)5Power Type - LPG, Dual Fuel LPGDual FuelLPG Dual FuelLPGDual Fuel6Operator Type Sit-Down Rider7Step Heightin (mm)16.3 (415)17.1 (435)8Tire Type - Cushion, Solid, Pneumatic Pneumatic 9Wheels, Number - Front/ Rear 2x/2D I ME N S I O N S 10Lift Height, Top of Fork (TOF)in (mm)129 (3292)126 (3209)11Lift Heights, Standard Limited Free Lift (LFL) w/LBR (TOF)in (mm) 5 (140)Lift Heights, Optional Full Free Lift (FFL) with LBR (TOF)in (mm)58 (1490)12Standard Carriage Widthin (mm)42 (1067)13Forks, Thickness x Width x Length in (mm) 1.6 X 3.9 X 42 (40 X 100 X 1067)15Mast Tilt Angles, Forward/Backward degrees 6/616Length To Face of Forksin (mm)99.5 (2528)101.9 (2589)106.3 (2701)17a Overall Width, Standard Tread in (mm)45.7 (1162)46.9 (1191)17b Overall Width, Wide Treadin (mm)52 (1322)52.2 (1326)18Height, Standard Mast - Loweredin (mm)86 (2170)89 (2245)19Height, Standard Mast - Extended with LBRin (mm)147 (3715)175 (4330)Height, Standard Mast - Extended without LBR in (mm)154 (3904)154 (3905)20Height, Standard Overhead Guardin (mm)87.7 (2228)88.6 (2250)Height, Optional Overhead Guard in (mm)83.8 (2128)84.6 (2150)21Turning Radius, Minimum Outside (OTR)in (mm)85.7 (2178)88 (2236)91.5 (2324)22Length, Center of Wheel to Face of Forksin (mm)18.5 (471)19 (483)23Aisle Width, Right Angle Stack (Add Length of Load) in (mm)104.3 (2649)106.6 (2707)110.3 (2802)24Equal Aisle, 90-Degree Intersecting Aisle in (mm)79.9 (2030)80.9 (2056)83 (2108)P E R F O R M A N C E25Travel Speed, Powershift Transmission RL/NL mph (km/h)11.4/11.6 (18.4/18.6)12.3/12.4 (19.8/20)26Lift Speed, Standard 2-Stage LFL RL/NLft/min (m/s)128/134 (0.65/0.68)112/118 (0.57/0.60)Lift Speed, Optional 3-Stage FFL RL/NLft/min (m/s)120/126 (0.61/0.64)106/112 (0.54/0.57)27Lowering Speed, Standard 2-Stage LFL RL/NLft/min (m/s)114/98 (0.58/0.50)Lowering Speed, Optional 3-Stage FFL RL/NL ft/min (m/s)114/98 (0.58/0.50)28Maximum drawbar pull RL/NLlb (kg)4947/2282 (2244/1035)4916/2217 (2230/1006)4438/2534 (2013/1149)Drawbar Pull, Standard Transmission @ 1 mph RL/NL lb (kg)4186/2282 (1899/1035)4154/2217 (1884/1006)3792/2534 (1720/1149)29Gradeability, Standard Transmission @ 1 mph RL/NL Percent 35.9/31.530.2/27.623.5/27.6W T .31Weight, Standard Truck (2-Stg. LFL 84/127) NLlb (kg)8170 (3705)8910 (4040)10300 (4671)Weight, Standard Truck (2-Stg. LFL 84/127) RL lb (kg)12170 (5520)13910 (6308)16300 (7392)32Axle Loading, Static Front/Rear NLlb (kg)3855/4311 (1748/1955)3695/5210 (1676/2363)4207/6089 (1908/2761)Axle Loading, Static Front/Rear RL lb (kg)10518/1648 (4770/747)12024/1881 (5453/853)14064/2232 (6378/1012)T I R E S & W H E E L S33Tire Size, Front 7.00 x 12 - 1228 x 9 - 1534Tire Size, Rear 6.00 x 9 6.50 x 1035Wheelbasein (mm) 63.9 (1623)66.9 (1700)37Ground Clearance, Lowest Point NL (w/RL subtract-6mm)in (mm) 3.3 (84) 4.1 (104)38Ground Clearance, Center of Wheelbase NL in (mm)7.5 (190)8.3 (210)39Service Brake - Method of Control/Operation Foot/Hydraulic 40Parking Brake - Method of Control/Operation Hand/Mechanical P O W E R T R A I N41Battery TypeMaintenance Free42Volts/Cold Cranking Amps v/cca 12/47543Engine, Manufacturer/Model PSI 2.4L44Permanent Output @ Rated RPM hp (kw)62 (46) @ 2700 RPM 45Torque @ Rated RPMft/lbs (kg/m)124 (17.1) @ 1600 RPM46Number of Cylinders/Displacement No/cc (ci)4/2351 (143)47Transmission Type, StandardElectronic PowershiftStandard Speeds, Forward - Reverse 1-149Hydraulic Tank Capacity (Drain and Refill)gal (liter)11.1 (42)50Fuel Tank Capacity (LPG & Duel Fuel Powered Units Only)gal (liter)18.2 (69)51Auxiliary Hydraulic Pressure Relief for AttachmentsPSI (Mpa)2550 (17.6)SPECIFICATIONSMAST SPECIFICATIONSH40-50XT MAST SPECIFICATIONSMaximum Fork Height (TOF) †OverallLoweredHeightOverall Extended Height Free-Lift (TOF)Approximate Total Weight ofStandard Equipped Truck* w/ Load Backrest w/o Load Backrest w/ Load Backrest w/o Load Backrest H40XT H50XTin (mm)in (mm)in (mm)in (mm)in (mm)in (mm)lbs (kg)lbs (kg) 2-STAGE LIMITED FREE-LIFT (LFL) VISTA™PLUS MAST129 (3290)86 (2170)178 (4515)154 (3904) 5 (140) 5 (140)7990 (3624)8720 (3955) 3-STAGE FULL FREE-LIFT (FFL) VISTA™PLUS MAST171 (4350)78 (1970)220 (5570)195 (4935)29 (750)54 (1390)8270 (3751)9000 (4082) 189 (4800)84 (2120)237 (6020)213 (5385)35 (900)60 (1540)8340 (3783)9080 (4119) 194 (4950)86 (2170)243 (6170)218 (5535)37 (950)62 (1590)8370 (3797)9110 (4132) 200 (5100)90 (2270)249 (6320)224 (5685)41 (1050)66 (1690)8410 (3815)9150 (4150) 218 (5550)96 (2420)267 (6770)242 (6135)47 (1200)72 (1840)8500 (3856)9240 (4191)†Lift heights over 171.5” (4356 mm) max. fork height are considered highlifts and require reduced capacity and restricted back tilt.* Total approximate weights listed include mast, standard carriage, load backrest extension, pneumatic tires and 70 lbs. LP tank and tank bracket.RL = Rated Load NL = No LoadH60XT MAST SPECIFICATIONSMaximum Fork Height (TOF) †OverallLoweredHeightOverall Extended Height Free-Lift (TOF)Approximate Total Weight ofStandard Equipped Truck* w/ Load Backrest w/o Load Backrest w/ Load Backrest w/o Load Backrest H60XTin (mm)in (mm)in (mm)in (mm)in (mm)in (mm)lbs (kg) 2-STAGE LIMITED FREE-LIFT (LFL) VISTA™PLUS MAST126 (3209)89 (2245)175 (4430)154 (3905) 5 (150) 5 (150)10050 (4559) 3-STAGE FULL FREE-LIFT (FFL) VISTA™PLUS MAST181 (4615)87 (2195)230 (5840)208 (5260)37 (965)63 (1600)10410 (4722) 187 (4768)91 (2295)236 (5990)213 (5410)41 (1065)65 (1655)10460 (4745) 211 (5368)101 (2545)260 (6590)237 (6010)51 (1315)75 (1905)10590 (4804) 228 (5815)107 (2695)278 (7040)256 (6495)57 (1465)80 (2055)10770 (4885)†Lift heights over 171.5” (4356 mm) max. fork height are considered highlifts and require reduced capacity and restricted back tilt.* Total approximate weights listed include mast, standard carriage, load backrest extension, pneumatic tires and 70 lbs. LP tank and tank bracket.RL = Rated Load NL = No LoadPSI 2.4L LPG engineElectronic powershift transmissionMonotrol® pedal directional control2-stage LFL VISTA TM PLUS mast42" wide hook-type carriage with 48" tall load backrest 42" forks6° forward / 6° back tilt3-function hydraulic control valveIntegrated dashboard displayHydrostatic power steeringNon-suspension vinyl seat with non-cinch seat belt Electronic hornKeyswitch startAdjustable steer columnPSI 2.4L dual fuel engineColumn-mounted directional shift leverHigh air intake with pre-cleanerAccumulatorKeyless start (with auxiliary key switch)Front and rear halogen or LED work lightsAnti-clog plus radiatorFire extinguisherLoad weight displaySwing-out LPG tank bracketTouchPoint mini-lever hydraulic controlsReturn-to-set-tilt (cowl mounted mechanical levers only) Rear drive handle with horn button10° forward / 6° back tiltClamping hydraulic control with detent4-function hydraulic control valve84" overhead guardOperator cab kit with heater12-volt power supplyBelly screenFrame mounted external tie downs Rubber floor matHigh air intakeIntegral tie downsOperator restraint systemAluminum core, anti-clog radiatorSingle pedal inch brakeHyster Stability System (HSS®)Cowl-mounted mechanical hydraulic control levers Fixed LPG tank bracket88" overhead guardUL classification LPCounterweight exhaust1 year / 2,000 hour full truck warranty3 years / 6,000 hour powertrain warrantySTANDARD EQUIPMENTOPTIONAL EQUIPMENTFull suspension seat – vinyl or clothRed, high-visibility, non-cinch seat beltGlass or polycarbonate overhead guard rain topIntegral sideshifterIntegral sideshifting fork positionerDual inch brake pedalsDual side view mirrorsAudible alarm – reverse activatedVisible alarm – amber strobeVisible alarm – blue spot lightVarious light packagesOverhead exhaustPneumatic shaped solid tiresNon-marking pneumatic shaped solid tiresWide treadTilt cylinder bootsTraction speed limiterTelemetry (3 levels)L1: Wireless monitoring (cellular or WiFi)L2: Wireless access (for use with operator swipe cards)L3: Wireless verification (facilitates operator checklistfunctionality)FEATURES AND OPTIONSHyster Company P .O. Box 7006Greenville, North Carolina 27835-7006Part No. H40-60XT/TG 2/2018 Litho in U.S.A.Trucks may be shown with optional equipment. © 2018 Hyster Company. All rights reserved.Hyster, , and STRONG PARTNERS. TOUGH TRUCKS. and MONOTROL are registered trademarks in the United States and certain other jurisdictions. Hyster products are subject to change without notice.Visit us online at or call us at 1-800-HYSTER-1.。
奥迪Q7服务救援车工具指导手册
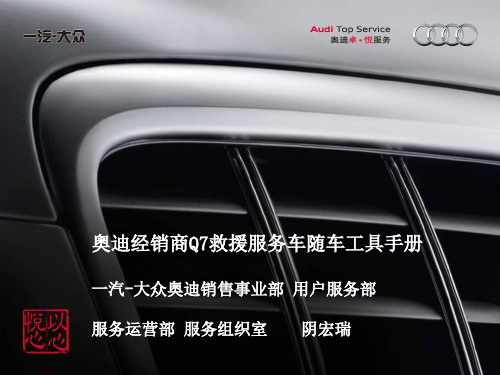
18
救援工具-----------工具柜第二层抽屉
1. 名称:带点烟器接头的照明灯 2. 品牌:Halogen 3. 数量:1件
19
救援工具-----------工具柜第二层抽屉
7. 2116Lg-T30
8. 2116Lg-T40
1. 名称:TOXE型内六角扳手组套 2. 品牌:Hazet
3. 数量:8件
10
救援工具-----------工具柜第一层抽屉
► 配置型号 ► 配置型号
1. 880-6
2. 880-7 3. 880-8 4. 880-9 5. 880-10 1. 名称:3/8″方六角套筒 2. 品牌:Hazet 3. 数量:17件 6. 880-11 7. 880-12 8. 880-13 9. 880-14
7. 450 N-18×19
8. 450 N-21×22 1. 名称:双开口扳手组件 2. 品牌:Hazet 3. 数量:10件 9. 450 N-24×26 10. 450 N-27×32
4
救援工具-----------工具柜第一层抽屉
► 配置型号 1. 630-6×7 2. 630-8×9 3. 630-10×11 4. 630-12×13 5. 630-14×15
6. 630-16×17
7. 630-18×19 8. 630-21×22 1. 名称:双环型扳手组件 2. 品牌:Hazet 9. 630-24×27 10. 630-30×32
3. 数量:10件
5
救援工具-----------工具柜第一层抽屉
► 配置型号 1. 2156
2. 746-1
3. 730-3
11. 火花塞套筒组件(2件)
12. 可逆棘轮组件(5件) 13. 一字改锥组件(4件) 14. 十字改锥组件(2件)
黑鹰自动车辆工具系列产品说明书

This is the safety alert symbol. It is used to alert you to potential personal injury hazards.Obey all safety messages that follow this symbol to avoid possible injury or death.ModelCapacity BH212812 Ton BH2208 20 Ton BH230830 TonAir Actuated Bottle JacksOperating Instructions & Parts ManualSFA Companies10939 N. Pomona Ave. Kansas City, MO 64153******************************SAFETY and GENERAL INFORMATIONSave these instructions. For your safety, read, understand, and follow the information provided with and on this jack before using. The owner and operator of this equipment shall have an understanding of this jack and safe operating procedures before attempting to use. The owner and operator shall be aware that use and repair of this product may require special skills and knowledge. Instructions and safety information shall be conveyed in the operator's native language before use of this jack is authorized. If any doubt exists as to the safe and proper use of this jack, remove from service immediately.Inspect before each use. Do not use if broken, bent, cracked or damaged parts are noted. Any jack that appears damaged in any way, or operates abnormally shall be removed from service immediately. If the jack has been or suspected to have been subjected to a shock load (a load dropped suddenly, unexpectedly upon it), immediately discontinue use until jack has been checked by a factory authorized service center (contact distributor or manufacturer for list of authorized service centers). It is recommended that an annual inspection be done by qualified personnel. Labels and Operator's Manuals are available from manufacturer.PRODUCT DESCRIPTIONBlackhawk Automotive Air Actuated Bottle Jacks are designed to lift, not support, rated capacity loads consisting of one end of a vehicle. Immediately after lifting, the load must be supported by a pair of appropriately rated jack ***************************************************************************************** air pressure is required to raise rated capacity load.Never use hydraulic jack as a stand alone device. After lifting, immediately support the lifted loadwith a pair of appropriately rated jack stands. Never place any portion of your body under a load when lifting or lowering the load.PREPARATIONBefore Use1. Verify that the product and application are compatible, if in doubt call Customer Support (816) 891-6390.2. Before using this product, read the operator's manual completely and familiarize yourself thoroughly with theproduct, its components and recognize the hazards associated with its use.3. Assemble handle, ensure spring clips align with slots.4. To familiarize yourself with basic operation, use the notched end of provided handle to engage and turn the releasevalve:a. Clockwise until firm resistance is felt to further turning. This is the ‘CLOSED’ release valve position used toraise the ram plunger.b. Counter-clockwise, but no more than 1 turn from the closed position. This is the ‘OPEN’ release valveposition used to lower the ram plunger.5. With ram fully retracted, locate and remove the oil filler plug/screw. Insert the handle into the handle sleeve, thenpump 6 to 8 strokes. Ensure the oil level is just below the oil filler hole. Reinstall the oil filler plug/screw.6. Pour a teaspoon of good quality, air tool lubricant into the air supply inlet of the lift control valve. Connect to airsupply and squeeze lift control valve for 3 seconds to evenly distribute lubricant.7. This product is equipped with the popular 1/4" NPT air coupler. When installing a different air coupler of yourchoice, ensure that thread tape or compound is used when servicing connections. To ensure dependable, trouble free operation an inline air dryer and oiler is recommended.8. Check that the pump operates smoothly and that the extension screw will thread up/down easily before puttinginto service. Replace worn or damaged parts and assemblies with Blackhawk Automotive authorized replacement parts only.Bleeding / Venting Trapped AirWith the release valve in the OPEN position (4b above) and with ram plunger fully lowered, locate and remove the oil filler plug/screw. Insert the handle into the handle sleeve; then pump 6 to 8 full strokes. This will help release any pressurized air which may be trapped within the reservoir. Oil level should be even with the bottom of the oil filler hole. Reinstall the oil filler plug/screw.Be sure all tools and personnel are clear before lowering load. Only attachments and/or adapters supplied by the manufacturer shall be used. Lift only on areas of the vehicle as specified by the vehicle manufacturer.OPERATIONRaising the Ram Plunger1. Assemble handle, ensure that spring clips align with slots.2. Place vehicle in the park, with emergency brake on and wheel securely chocked to prevent inadvertent vehicle movement.3. Locate and close release valve by turning handle clockwise until firm resistance is felt to further thread engagement.4. Verify lift point, center jack saddle under lift point.5. Squeeze the lift control valve or insert handle into handle sleeve and pump to contact lift point. To lift, continue pumping until load reaches desired height. DO NOT OPERATE BY AIR AND BY HAND PUMPING AT THE SAME TIME.6. Immediately transfer the lifted load to a pair of appropriately rated jack stands.Use only handle provided by jack manufacturer.The handle provided with this jack will safely engage the release valve and operate the handle sleeve. If handle is worn, operates abnormally, or will not positively engage the release valve, STOP , discontinue use of the jack until a factory replacement handle can be acquired.Make certain that all personnel are clear of Control the rate of descent of the load at all times . The more you open the release valve, the faster the load descends.1. Raise load high enough to clear the jack stands, then carefully remove jack stands (always used in pairs).2. Slowly turn the handle counter-clockwise, but no more than 1 turn. If the load fails to lower:a. Use another jack to raise the vehicle high enough to reinstall jack stands.b. Remove the affected jack and then the stands.c. Lower the load by turning the release valve counter-clockwise, but no more than 1 turn.3. After removing jack from under the load, push ram and handle sleeve down to reduce exposure to rust and contamination.MAINTENANCEImportant : Use only good grade hydraulic jack oil. Avoid mixing different types of fluid and NEVER use brake fluid, turbine oil, transmission fluid, motor oil or glycerin. Improper fluid can cause premature failure of the jack and the potential for sudden and immediate loss of load. We recommend Mobil DTE 13M or equivalent.Adding oil1. With ram plunger fully lowered and pump piston fully depressed, set jack in its upright, level position. Remove oil filler screw.2. Fill with oil until just below the rim of the oil filler screw hole. Reinstall the oil filler plug/screw. Changing oilFor best performance and longest life, replace the complete fluid supply at least once per year.1. With ram plunger fully lowered and pump piston fully depressed, remove the oil filler plug/screw.2. Lay the jack on its side and drain the fluid into a suitable container.Note: Dispose of hydraulic oil in accordance with local regulations.3. Fill with oil until just below the rim of the oil filler hole. Reinstall the oil filler plug/screw.Lubrication1. A periodic coating of light lubricating oil to pivot points will help to prevent rust and assure that pump assemblies move freely.2. Air pump should be internally lubricated before each use. Use good quality air tool lubricant. If no inline oiler is used, pour a teaspoon of air tool oil into the air control valve inlet. Operate the jack with air pressure to fully distribute the oil inside the air motor.CleaningPeriodically check the pump piston and ram for signs of rust/corrosion. Clean as needed and wipe with oily cloth.Note: Never use sandpaper or abrasive material on these surfaces!StorageWhen not in use, store the jack with pump piston and ram plunger fully retracted and air supply disconnected.TROUBLESHOOTINGSymptomPossible CausesCorrective ActionJack will not lift load• Release valve not tightly closed • Overload condition• Air pressure inadequate • Ensure release valve tightly closed • Remedy overload condition • Ensure adequate air pressure Jack will lift, but not maintain pressure• Release valve not tightly closed • Overload condition• Hydraulic unit malfunction • Ensure release valve tightly closed • Remedy overload condition• Contact Blackhawk Tech. Service Jack will not lower after unloading• Reservoir overfilled • Ensure load is removed, then drain fluid to proper levelPoor lift performance• Fluid level low• Air trapped in system• Ensure proper fluid level• With ram fully retracted, remove oil filler plug/screw to let pressurized air escape, then reinstall oil filler plug/screwWill not lift to full extension • Fluid level low• Ensure proper fluid levelSFA Companies10939 N. Pomona Ave. Kansas City, MO 64153816-891-6390******************************ONE YEAR LIMITED WARRANTYFor a period of one (1) year from date of purchase, SFA Companies will repair or replace, at its option, without charge, any of its products which fails due to a defect in material or workmanship under normal usage. This limited warranty is a consumer's exclusive remedy.Performance of any obligation under this warranty may be obtained by returning the warranted product, freight prepaid, to SFA Companies Warranty Service Department, 10939 N. Pomona Ave., Kansas City, MO 64153. Except where such limitations and exclusions are specifically prohibited by applicable law, (1) THE CONSUMER'S SOLE AND EXCLUSIVE REMEDY SHALL BE THE REPAIR OR REPLACEMENT OF DEFECTIVE PRODUCTS AS DESCRIBED ABOVE. (2) SFA Companies SHALL NOT BE LIABLE FOR ANY CONSEQUENTIAL OR INCIDENTAL DAMAGE OR LOSS WHATSOEVER. (3) ANY IMPLIED WARRANTIES, INCLUDING WITHOUT LIMITATION THE IMPLIED WARRANTIES OF MERCHANTABILITY AND FITNESS FOR A PARTICULAR PURPOSE, SHALL BE LIMITED TO ONE YEAR, OTHERWISE THE REPAIR, REPLACEMENT OR REFUND AS PROVIDED UNDER THIS EXPRESS LIMITED WARRANTY IS THE EXCLUSIVE REMEDY OF THE CONSUMER, AND IS PROVIDED IN LIEU OF ALL OTHER WARRANTIES, EXPRESS OR IMPLIED. (4) ANY MODIFICATION, ALTERATION, ABUSE, UNAUTHORIZED SERVICE OR ORNAMENTAL DESIGN VOIDS THIS WARRANTY AND IS NOT COVERED BY THIS WARRANTY .Some states do not allow limitations on how long an implied warranty lasts, so the above limitation may not apply to you. Some states do not allow the exclusion or limitation of incidental or consequential damages, so the above limitation or exclusion may not apply to you. This warranty gives you specific legal rights, and you may also have other rights, which vary from state to state.REPLACEMENT PARTS(refer to page 6 thru 8)Not all components of the jack are replacement items, but are illustrated as a convenient reference of location and position in the assembly sequence. When ordering parts, give Model number, serial number and parts description. Call or write for current pricing: SFA Companies, 10939 N. Pomona Ave. Kansas City, MO 64153, U.S.A. Tel:(816)891-6390Fax:(816)891-6599E-Mail:******************************Replacement Parts Illustration for Model BH2128 & BH2208Figure 3 - Model BH2128 & BH2208 Replacement Parts IllustrationItem DescriptionQty.3a Filler Plug (for BH2128 only)15Seal1a Dust Wiper 1b O-ring 1c O-ring1d Ram Bearing 1eBack-up Ring1Replacement Parts List for Models BH2128 & BH2208Item Description Qty.f U-cup 1g O-ring 2h Packing 1i Oil Seal 1j O-ring1k Ram Bearing (for BH2208)1lO-ring (for BH2208)1(*) Seal Kit Contents:Item Part# for BH2128Part# for BH2208Description Qty.1A120-10004-000A190-10002-000Cylinder Fastener 12A120-10003-000A190-10001-000Guide Ring 13a 5905-00100-200N/AFiller Plug 13b N/AG62S-03301-000Filler Screw 14A120-10002-000Special Washer 255905-00054-000Seal16BT10-24001-000Release Valve 175308-00095-000Gasket 28A27010-0001Air Motor 19A27010-0002Air Inlet Swivel 110A20060-0005Hose Assy.111A20060-0006Air Hose 112A20060-0007Lift Control Valve 113B020-15002-000Washer 114B080-15001-000Pump Cylinder 115A120-15101-000Pump Piston 1165115-08033-000Bolt 1175405-07024-000Pin118A120-13000-000Handle Socket 1195405-02018-000Snap Pin 120B10N-21000-000Handle Assembly121A27010-0011Air Coupler, Female 1/4 NPT 122A20060-0016Air Coupler, Male 1/4 NPT 123A27010-0008Piston, Air Motor 1245206-00008-001Nut1*A1206S-046A1906S-047Seal Kit (includes #4a, 6 & a~l)--A27010-0000Seal Kit, Air Motor --BH2128-L0BH2208-L0Label 1-BH2128-M1Manual1Figure 4 - Model BH2308 Replacement Parts IllustrationItem Part# for BH2308Description Qty.1B300-10003-000Saddle 125308-00380-000Spring 13B300-15000-000Reservoir 14G62S-03301-000Filler Screw 15B120-10003-000Filter 265905-00054-000Seal17BT02-17100-000Release Valve 18G100-44000-000Hyd. Cartridge 19A27010-0001Air Motor110A27010-0002Air Inlet Swivel 111A20060-0005Hose Assy.112A20060-0006Air Hose113A20060-0007Lift Control Valve 114B300-14002-000Washer115B300-14001-000Pump Cylinder 116B300-14101-000Pump Piston 117G150-04500-000Hyd. Cartridge 1185405-08030-000Pin219B300-13000-000Handle Socket 1205405-02018-000Snap Pin221B300-17000-000Handle Assembly 122A27010-0011Air Coupler, Female 123A20060-0016Air Coupler, Male 124A270-01100-0000Piston, Air Motor 1*B3000S-034Seal Kit--A27010-0000Seal Kit, Air Motor --BH2308-L0Label 1-BH2128-M1Manual1Replacement Parts Illustration and Parts List for Model BH2308Item Description Qty.2Spring 16Seal 1a O-ring 1b O-ring 1c Packing1d Back-up Ring 1e U-cup1f Back-up Ring 1g O-ring 1h Seal 1i U-cup1j Back-up Ring 1k Back-up Ring 1lO-ring1(*) Seal Kit Contents:1a23456789101113121415161718192021bcd ef gh l k ij242223。
海斯特(Hyster)4轮驱动型电筒搬运机产品技术指南说明书

J40XNLPRODUCT BROCHURECircled dimensions correspond to the line numbers on the tabulated chart inside the technical guide. Dimensions are in inches (millimeters).2Circled dimensions correspond to the line numbers on the tabulated chart inside the technical guide.Dimensions are in inches (millimeters).3The table below is a helpful guide to visualize the truck run time with different batteries in different applications. (Chart is a guide only and not a replacement for a site survey and full power study.)Heavy – High throughput, typically runs full capacity, runs either attachments or has high liftsMedium – High throughput, runs near capacity without attachments or high liftsLight – lower throughput, runs less than rated capacity without attachments or high liftsNote: Run time is from 100% to Lift-Lock Out. Charge time is from Lift-Lock Out to 100%.45CERTIFICATION: Hyster lift trucks meet the design and construction requirements of B56.1-1969, per OSHA Section 1910.178(a)(2), and also comply with the B56.1 revision in effectat time of manufacture. Certification of compliance with the applicable ANSI standards appears on the lift truck. Performance specifications are for a truck equipped as described under Standard Equipment on this Technical Guide. Performance specifications are affected by the condition of the vehicle and how it is equipped, as well as by the nature, condition of the operating area, proper service and maintenance of the vehicle. If these specifications are critical, the proposed application should be discussed with your dealer.NL = no load, RL = rated load。
“阿贝原则”的启示
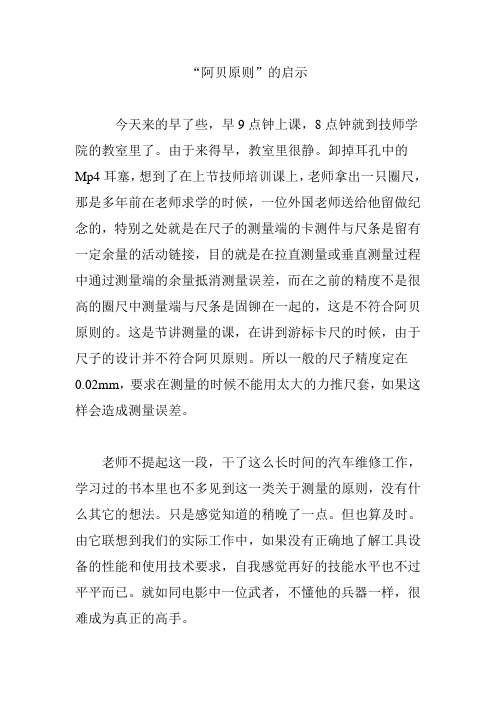
“阿贝原则”的启示今天来的早了些,早9点钟上课,8点钟就到技师学院的教室里了。
由于来得早,教室里很静。
卸掉耳孔中的Mp4耳塞,想到了在上节技师培训课上,老师拿出一只圈尺,那是多年前在老师求学的时候,一位外国老师送给他留做纪念的,特别之处就是在尺子的测量端的卡测件与尺条是留有一定余量的活动链接,目的就是在拉直测量或垂直测量过程中通过测量端的余量抵消测量误差,而在之前的精度不是很高的圈尺中测量端与尺条是固铆在一起的,这是不符合阿贝原则的。
这是节讲测量的课,在讲到游标卡尺的时候,由于尺子的设计并不符合阿贝原则。
所以一般的尺子精度定在0.02mm,要求在测量的时候不能用太大的力推尺套,如果这样会造成测量误差。
老师不提起这一段,干了这么长时间的汽车维修工作,学习过的书本里也不多见到这一类关于测量的原则,没有什么其它的想法。
只是感觉知道的稍晚了一点。
但也算及时。
由它联想到我们的实际工作中,如果没有正确地了解工具设备的性能和使用技术要求,自我感觉再好的技能水平也不过平平而已。
就如同电影中一位武者,不懂他的兵器一样,很难成为真正的高手。
在进行长度测量时需要计量器具的测量头或量臂移动,如游标卡尺、千分尺,其活动部件移动方向的正确性通常靠导轨保证。
导轨的制造与安装误差(如直线度误差及配合处的间隙)会造成移动方向的偏斜。
为了减小这种方向偏斜对测量结果的影响,1890年德国人艾恩斯特?阿贝(Ernst Abbe)提出了指导性原则:在长度测量中,应将标准长度量(标准线)安放在被测长度量(被测线)的延长线上,这就是阿贝原理。
也就是说,量具或仪器的标准量系统和被测尺寸应成串联形式。
若为并联排列,则该计量器具的设计,或者说其测量方法原理不符合阿贝原则。
游标卡尺便是这样,会因此产生较大的误差,可称阿贝误差。
千分尺的结构,若忽略读数装置的直径,也符合阿贝测长原则。
一、长度测量的几项基本原则1最小变形原则长度测量中引起被测件和测量器具的变形,主要是由于热变形和弹性变形(接触变形和自重引起的变形)。
一汽大众新迈腾救援服务车随车工具手册资料重点
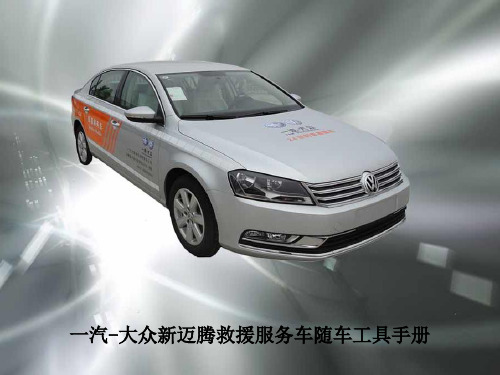
1.名称:米子型螺丝刀 2.品牌:Hazet 3.数量:3件 配置型号:H803-T20、
803-T25、 803-T30
1.名称:组挫10 2.品牌:Hazet 3.数量:1件 配置型号:E9102
迈腾救援车-----------救援工具
► 工具柜三号抽屉 1.名称:机修辅助工具 2.品牌:SATA 3.数量:5件
救援工具-----------工具柜一号抽屉
1.名称:3/8六角套筒、转换接头、万 向活接
2.品牌:Hazet 3.数量:19件
► 套筒配置型号 1. JTC33206 2. JTC33207 3. JTC33208 4. JTC33209 5. JTC33210 6. JTC33211 7. JTC33212 8. JTC33213 9. JTC33214 10.JTC33215 11.JTC33216 12.JTC33217 13.JTC33218 14.JTC33219 15.JTC33220 16.JTC33221 17.JTC33222
4、安装两个上箱体并对应孔位固定好, 但不安装抽屉。
救援工具-----------工具柜四号抽屉
1.名称:钳工锤子 2.品牌:Hazet 3.数量:2件
► 配置型号 1.300g——角扳手、切断钳 2.品牌:Hazet 3.数量:3件
► 配置型号 1. H428-10 2. H428-13 3. H1802-22
棘轮扳手3/8 H8816P
电路测试笔 JTC1612
加长杆 H8821-3
迈腾救援车-----------救援工具 ► 工具柜二号抽屉
1.名称:机修手动工具 2.品牌:Hazet 3.数量:22件
► 配置 1. 组锉10(1件) 2. 双头开口扳手组合(8件) 3. 螺丝刀组合(10件) 4. 米子型螺丝刀(3件)
A6L-保养手册

保养工作执行说明各保养项目的顺序是通过试验确定的,也是经过优化的。
因此,为了避免工作不必要的中断,必须遵守该顺序。
工作描述的顺序与最经常进行的保养方式- 常规保养的工作步骤相符。
如果在检查服务范围内确定有故障,并需要采取维修措施,则应通知客户。
空气滤清器:清洁空气滤清器壳并更新滤芯–旋出螺栓-1-,并向上取出空气导管。
–将导线-2- 从固定支架中脱开。
–松开空气导管-3- 的软管卡圈和插头连接(曲轴箱的排气孔,空气质量传感器)。
–用螺丝刀打开夹子-1-,并拉出空气导管。
–脱开并打开空气滤清器盖-2-,然后将它取出。
–旋下十字螺栓-3- 并更换滤芯。
–装配以倒序进行。
提示在用压缩空气吹洗空气滤清器外壳时,应注意以下问题:为避免发动机的功能故障,应用一块干净的抹布或蓝色无纺布盖住重要空气传输部件,如空气质量流量计、进气管等。
注意废弃物处理规定!燃油滤清器:在柴油发动机中进行更新–取下固定夹-5-。
–将调节阀-6- 连同其上连接的燃油管路一同拆下。
–将燃油管从软管接头-3- 和 -4- 处拔出。
–松开支架上的防松卡箍-1- 并将滤清器从支架上取下。
–用干净的柴油加注新的滤清器。
由此可以更快地起动发动机。
–将过滤器装入固定支架中,并以10 Nm 拧紧卡箍-1-–在安装调节阀时注意滤清器壳体中的O 形环。
–装入已连接燃油管路的调节阀。
–装上固定夹-5-。
–将燃油软管推入软管接头-3- 和 -4- 并用软管卡箍固定软管。
–起动发动机,目检燃油装置的密封性。
发动机机油:排放机油,更新机油滤清器6 缸汽油发动机 BBJ– 拆下隔音垫。
→ 章– 松开机油滤清器 -箭头- 及固定带(例如Hazet 2171-1)。
– 拆下机油滤清器。
提示注意废弃物处理规定! 留意有关机油滤清器的安装说明。
– 打开放油螺栓,将发动机油抽出。
– 清洁发动机上的机油滤清器密封面。
– 给橡胶密封条上少量的油。
– 旋入新的滤清器并拧紧。
警告!在更换了机油滤清器芯之后,应检查从机油 冷却装置出来的软管 -箭头- 与相邻的部件 之间是否畅通,并根据需要修正机油冷却装 置的位置。
工程师要知道的工具

工程师要知道的工具螺丝刀中文名称:螺丝刀英文名称:screw-driver定义:拧紧或旋松头部带一字或十字槽螺钉的工具。
根据规格标准,顺时针方向旋转为嵌紧;逆时针方向旋转则为松出。
一字螺丝可以应用于十字螺丝。
但十字螺丝拥有较强的抗变形能力。
u从其结构形状来说,通常有以下几种:1、直形。
这是最常见的一种。
头部型号有一字,十字,米字,T型(梅花型),H型(六角),等2、L形。
多见于六角螺丝刀,利用其较长的杆来增大力矩,从而更省力。
3、T形。
汽修行业应用较多。
u一字和十字螺丝刀为何共存为了给螺钉施加不大的扭距,人们想到了在螺钉头上开一条槽,用对应的一字形螺丝刀就能方便的拧紧和松开螺钉了。
随着科学技术的飞速发展,螺钉的应用越来越广泛,螺钉和一字螺丝刀的不足也呈现出来了。
首先是螺钉头的一字槽一旦受到破坏,螺钉就无法拧出。
一字槽的长度越长,也越容易在被拧的过程中遭到破坏。
为了能缩短槽口的长度,提高槽口抵抗破坏的能力,又能传递同样大小的扭力,人们想到用十字槽,可以承受同样的扭力,但一个槽口的长度却短了一半,抵抗破坏的能力却大大的加强了。
螺丝刀原本是一字形的,不能用于十字槽的螺钉,只有另外生产一种十字螺丝刀和十字槽螺钉相对应。
这样就有两种螺丝刀了。
为什么现在有两种螺丝刀呢?这是因为十字螺丝刀也就是这二十年的事情,而一字槽口的螺钉是从有机器以来就用着的。
不可能把老机器上的螺钉都换掉。
十字螺丝刀又不能用在一字槽口上,再说一字槽口的螺钉还在生产应用,所以要保留一字螺丝刀。
这样,新机器大多是用十字槽口螺钉,老的也还在使用,就有了同时使用两种螺丝刀的情况了。
u历史十字螺丝和十字螺丝刀是由亨利飞利浦(Henry Phillips)在上个世纪三十年代发明的。
首先使用在汽车的装配线上。
所以十字螺丝和十字螺丝刀也被称为飞利浦螺丝和飞利浦螺丝刀。
u螺丝刀规格1、一字螺丝刀的型号表示为刀头宽度*刀杆。
例如2×75mm,则表示刀头宽度为2mm,杆长为75mm(非全长)。
PreservCyt Solution套件使用指南说明书
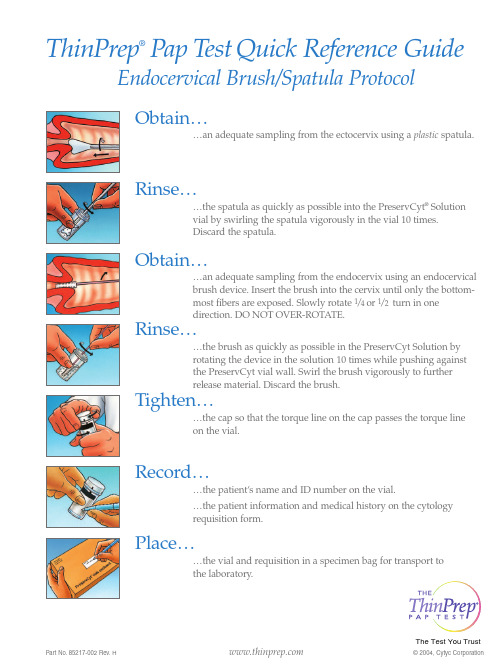
Obtain……an adequate sampling from the ectocervix using a plastic spatula.Rinse……the spatula as quickly as possible into the PreservCyt®Solutionvial by swirling the spatula vigorously in the vial 10 times.Discard the spatula.Obtain……an adequate sampling from the endocervix using an endocervicalbrush device. Insert the brush into the cervix until only the bottom-most fibers are exposed. Slowly rotate 1/4 or 1/2turn in onedirection. DO NOT OVER-ROTATE.Rinse……the brush as quickly as possible in the PreservCyt Solution byrotating the device in the solution 10 times while pushing againstthe PreservCyt vial wall. Swirl the brush vigorously to furtherrelease material. Discard the brush.Tighten……the cap so that the torque line on the cap passes the torque lineon the vial.Record……the patient’s name and ID number on the vial.…the patient information and medical history on the cytologyrequisition form.Place……the vial and requisition in a specimen bag for transport tothe laboratory.Endocervical Brush/Spatula ProtocolPart No.85217-002 Rev. HThe Test You TrustObtain……an adequate sampling from the cervix using a broom-like device. Insert the central bristles of the broom into the endo-cervical canal deep enough to allow the shorter bristles to fully contact the ectocervix. Push gently , and rotate the broom in a clockwise direction five times.Rinse……the broom as quickly as possible into the PreservCyt ®Solution vial by pushing the broom into the bottom of the vial 10 times, forcing the bristles apart. As a final step, swirl the broom vigorously to further release material. Discard the collection device.Tighten……the cap so that the torque line on the cap passes the torque line on the vial.Record……the patient’s name and ID number on the vial.…the patient information and medical history on the cytology requisition form.Place……the vial and requisition in a specimen bag for transport to the laboratory .Broom-Like Device Protocol。
HAZET 数显扳手说明书
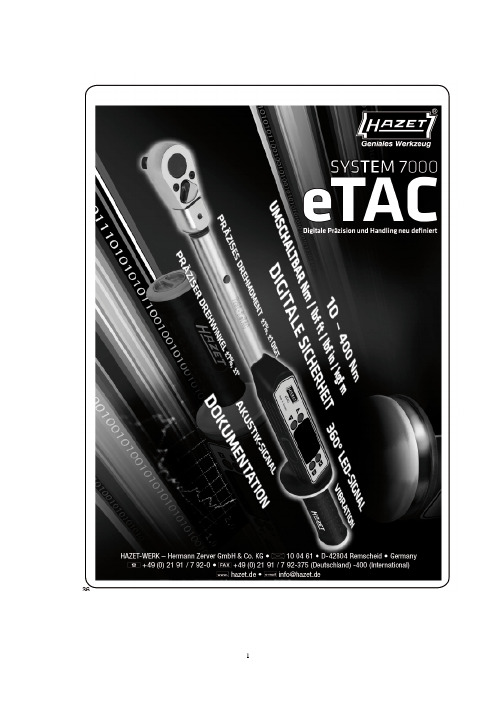
注意!长期不适用的扳手在储存时应把电池取出。
4
设计和功能 1,技术参数和工具配件
扳手类型:基本版(Basic Version) 和高级版(TOP Version)
技术参数
HAZET 型号 量程 Nm 测量单位 测量精度 力矩精度范围 转角测量量程 转角测量精度 转角精度范围 接口尺寸 棘轮头 有效长度mm 有/无棘轮头扳手长 度(mm) 有/无棘轮头扳手重 量(kg) 存储器容量 可设置参数 UBS 接口 语言 保护率 电池 9X12 10-100
第二级信号—绿光+中频率震动+蜂鸣:提示所加的力矩已经达到目标值范围以内,在 这个区域内应立即停止拧紧动作。较低的目标值和偏差很快就会超过。 第三级信号—红光+高频率震动+蜂鸣:提示所加力矩已经超出设定的目标值力矩值范 围。 第四级信号—红光持续+高频震动持续+蜂鸣持续:提示所加的力矩已经高于目标值的 最大值,旋转立即停止,否则会损坏扳手。 在完成一个操作之后, 如果再没有力矩施加到扳手, 则轮换显示在这次拧紧的最大力矩 值和 OK/NOK 信息。 在“Torque track”模式下,显示当前的扭矩值,没有目标值和偏差值,在此模式下,在 允许的最大的扭矩值到达后,只有第四级的信号起作用,在没有力矩继续施加的时候, 这个拧紧过程的最大的扭矩值被显示。
高级型扳手菜单结构图
10
高级型菜单结构图
1th 模式 2th 力矩 转角 扭矩 跟踪 峰值 转角 扭矩力矩值 000.0 单位 Nm, Ibf.ft Ibf.inKg.m 有效长度 有效长度 000.0mm 信号 预警值 00.0% 显示器 亮 暗 延时 延时 00.0 分钟 存储器 显示数值 删除数值 删除全部 存储器 显示 存储器 显示 删除全部 参数 参数 1 到 参数 10 工作流 工作流 1 到 工作流 10 日期/时 间 版本 日.月.年 时.分.秒 显示软件版 本 序号 校验 日期 释放号 语言 德语 英文 密码 旧 0000 阻止菜单 进入 计算机连 接 ….. 阻止 新 0000 密码 0000 不激活 激活 不激活 激活 力矩 转角 A1, 1PA1,2p力矩,转 角编程 蜂鸣关 蜂鸣开 震动关 震动开 目标值 000.0 转角 000° 右向 左向 右向 左向 精度 ±00.0% 精度 ±00.0° 力矩检查 转角检查 No Yes No Yes 扭矩力矩 000.0 低力矩值 000.0 低转角 00.0° 高力矩值 000.0
海德漢TNC 640使用手冊说明书
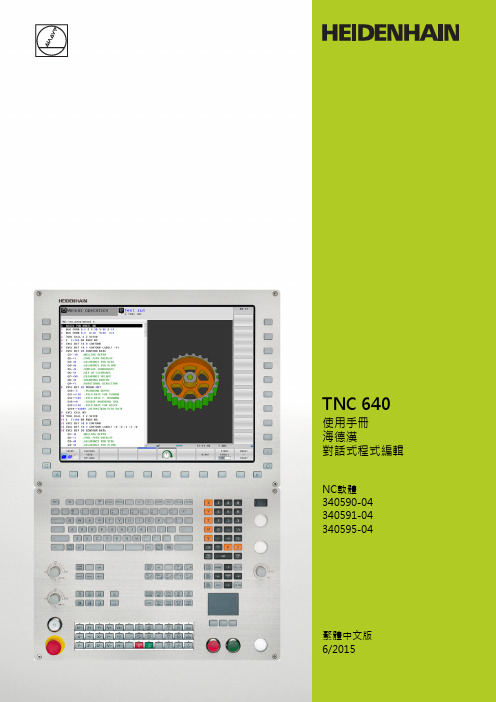
TNC的控制器TNC的控制器視覺顯示單元上的按鍵按鍵功能選擇分割畫面配置在加工模式與程式編輯模式之間切換顯示用於選擇螢幕上功能的軟鍵在軟鍵列之間切換文字數字鍵盤按鍵功能檔案名稱,註解DIN/ISO 程式編輯機械操作模式按鍵功能手動操作電子手輪使用手動資料輸入定位程式執行,單一單節程式執行,完整序列程式編輯模式按鍵功能程式編輯程式模擬程式/檔案管理,TNC功能按鍵功能選擇或刪除程式與檔案,外部資料傳輸定義程式呼叫,選擇工件原點及加工點表格選擇MOD功能顯示NC錯誤訊息的說明文字,呼叫TNCguide顯示所有目前錯誤訊息顯示計算器導覽鍵按鍵功能移動反白直接進入單節、循環程式及參數功能進給率與主軸轉速的電位計進給速率主軸轉速循環程式、子程式及程式段落重複按鍵功能定義接觸式探針循環程式定義與呼叫循環程式對於子程式編輯及程式段落重複進行輸入及呼叫標籤在程式內輸入程式停止符號刀具功能按鍵功能在程式內定義刀具資料呼叫刀具資料程式編輯路徑移動按鍵功能接近/離開輪廓FK 自由輪廓程式編輯直線極座標的圓心/極點利用圓心做圓弧加工具有半徑的圓含切線連接的圓弧切角/角落圓角特殊功能按鍵功能顯示特殊功能選擇格式內下一個標籤上/下一個對話方塊或按鈕輸入並編輯座標軸與數字按鍵功能. . .選擇座標軸或在程式當中輸入. . .數字小數點/倒反代數符號使用極座標輸入/增量值Q參數程式編輯/Q參數狀態儲存來自計算機的實際位置或數值NO ENT忽略對話問題,刪除字元確認輸入與重新對話總結單節,並離開輸入清除數字輸入或TNC錯誤訊息停止對話、刪除程式段落TNC的控制器基本原則有關本手冊有關本手冊本手冊內使用的符號說明如下。
要進行任何變更,或發現任何錯誤?我們持續努力改善我們的文件, 請將您的問題傳送至下列電子郵件位址: *************************。
TNC機型、軟體與特性TNC機型、軟體與特性此手冊說明由TNC搭配以下NC之軟體編號所包含的功能及特性。
ENVI去云补丁HazeTool使用说明

ENVI去云补丁HazeTool使用说明Haze Tool User Guide使用方式 (2)云层厚度检测 (2)HOT13 (2)操作步骤 (3)HOT123 (4)操作步骤 (4)案例 (5)云层厚度完善 (8)Haze perfection TM (9)操作步骤 (9)Haze perfection QB (11) Maskandinterpolation (12)案例 (13)Thresholdandinterpolation (13)fill_sink (14)flatten_peak (15)操作步骤 (15)云层去除 (17)Dark Substract (17)操作步骤 (20)Hist match (22)操作步骤 (22)Cloud Point (22)操作步骤 (23)案例 (28)鸣谢 (29)引文 (29)使用方式该模块是在ENVI4.4中二次开发而成。
使用时只需将文件置于***\ITT\IDL64\products\envi44\save_add文件夹内,然后运行ENVI,Basic Tool菜单中会出现一个Haze tool按钮。
绝对不要修改文件名,否则无效。
Haze tool主要由三部分组成:云层厚度检测(haze detection),云层厚度完善(haze perfection),云层去除(haze removal)。
这三部分前后连贯,每一步的结果都会影响到最终的除云效果,而且在参数的选择上主观性较大,这也是这个模块的缺点即不够自动化。
有问题联系作者请加QQ:27126797或者e-mail联系:****************除云案例请见作者博客:云层厚度检测一副影像中往往云层厚薄不一,因此不同厚度云覆盖下的地表需要恢复的强度不一;当然,完全遮挡地面的厚云不在考虑范围内。
在该模块中云层厚度检测有两个指数:HOT13和HOT123。
两者都是相对厚度检测,而不是绝对的光学厚度检测,HOT123是作者在HOT13的基础上的改进。
拜伐特汽车配件说明书

SCREAMIN’ EAGLE® PERFORMANCE
7" Daymaker® Projector LED Headlamp - Chrome
67700433
Screamin' Eagle Pro Street Tuner
41000008C
$299.95
LED Bullet Turn Signal Insert Kit - Front, Amber
91697-06A
®
61300505
Windshield Trim - Chrome
61300310
TOURING | FLHX | BLACK DENIM
DESCRIPTION ACCESSORIES FOR STYLE
PART NO.
DESCRIPTION ACCESSORIES FOR STYLE
ACCESSORIES FOR STYLE
FRONT END
Front End Kit - Chrome
45800037
Front Wheel Spacers - Chrome, ABS
41371-08
STREET GLIDE Slotted Stem Profile Custom Mirrors
Slipstream Vent Trim - Chrome
64900552A
65100085 65900012 65900015
$449.95
$109.95 $8.24 $8.25
Switch Housing Kit - Chrome
71500185
Chrome Clutch and Brake Master Cylinder Reservoir Kit
哈斯(Haas)和其他品牌的纹理工具详细产品介绍说明书

LAT HE TO OL INGFor H AAS and O ther B randsL1Extensive Product OfferingOver 25,000 Quality Products Including:Drills, Taps, Endmills, Threadmills, Reamers, Carbide Bars, Burs, Key Cutters, Dovetail Cutters, Chamfer Mills, Edge Breakers, Engraving Tools, Coolants, Cutting Oils, Toolholders, Live Tools & Tool Blocks for Lathes.Ease of Doing BusinessOur website and product catalogs have been designed to give our users the best experience possible. Find what you need fast and get technical informa-tion that will help you increase tool life and decrease cycle times. Personal technical support is always available to help you select the best tools for your application.American Made ValueAll RedLine products are 100% Made in the USA. We strive to offer quality products with outstanding value, and excellent deliveries at fair prices.Shop with ConfidenceWe value your business and will continue to do our best to meet your needs. If you are not completely satisfied with our service or purchase we will do our best to make it right.Why Buy RedLine Tools?Catalog IntroductionOur RedLine Lathe Tooling Catalog is your comprehensive guide to product selection for Live Tools, Tool Blocks & accessories for Lathes.Tooling for Haas 12 & 24 station bolt-on tool turrets and hybrid turrets can be found by Haas machine model starting on page 14.Live tools and toolholder blocks for machines equipped with BMT65 turrets can be found on pages 6-11. BMT65 Live Tools and Toolholder blocks work with Haas and select machines equipped with a BMT65 turret.To increase the productivity of your turning center, consider our tool blocks equipped with KM50 or Polygon Shank Couplings which allows you to change over or replace tools quickly and efficiently.Our live tools equiped with VariaConnect allow you to change tools in less than 20 seconds. These tools can be found on page 7.Compatible machine brands with BMT65 turrets include:Please check manufacturer drawings and refer to the diagrams below to verify fit on yourspecific machine turret.Doosan Daewoo Emag Emco Hwacheon Hyundai-WIA LEADWELLSamsung (SMEC)Victor WIA (KIA)BMT65 Live ToolsBMT65 Turret ToolingFits Haas & Other Brand LathesBMT65 Toolholder BlocksAxial & Radial with ER32 Spindle...........................6Axial & Radial with VariaConnect Spindle............7 VariaConnect Collet Chucks .............................7 VariaConnect Shrink Fit Holders .. (7)VariaConnect FaceMill Holders (7)VariaConnect Accessories (7)Standard Toolholder Blocks (8)Half-Index Toolholder Blocks (9)Quick Change Tool Blocks with Kennametal KM50 Connection..........10Quick Change T ool Blocks with Size 4 Polygon Shank Coupling. (11)Haas BMT65 Turret Technical Info (43)VDI40 Live ToolsTooling for Haas12 Station Bolt-On Tool Turrets and 12 & 24 Station Hybrid TurretsToolholder AccessoriesBolt-On Tools By Machine ModelReduction Sleeves .......................................................45-47 ER Collet Extensions & Hardware....................................48 Tap Holders - Straight Shank ...........................................49 ER Collets - Rego-Fix ................................................50-66 Tap Collets - BILZ ..................................................................67 ER Small Tool Adapters for Milling and Boring.........68-69 ER Small Tool Adapters for Sawing.............................70-71Axial with ER32 Spindle..................12Radial with ER32 Spindle................13Hardware (44)DS-30..........................................14-15 DS-30SS.....................................16-17 DS-30SS Y ...................................18-19 DS-30Y .......................................20-21 ST-20.........................................22-23 ST-20SS....................................24-25 ST-20SS Y ........................................26 ST-20Y .............................................27 ST-25...............................................28 ST-25Y .............................................29 ST-30.........................................30-31 ST-30SS....................................32-33 ST-30SS Y ..................................34-35 ST-30Y .......................................36-37 ST-35........................................38-39 ST-35Y .......................................40-41Haas Turrets T echnical Info......42-43Hardware (44)AxialBMT65 Axial Live Tool*Part Number Coupling Nut ColletRHAB65A32BMT65Internal ER32Radial BMT65 Radial Live Tool* • 800.791.7542Coolant Option: External CoolantCoolant Option: External CoolantVariaConnect Adapters & AccessoriesD1D2Part #28MM 64MM RVCER1634MM 64MM RVCER2042MM 64MM RVCER2550MM 64MM RVCER3263MM64MMRVCER40Part #CouplingL2Max RPMDrive RatioRHAB65AVCBMT6547MM6,0001:1BMT65 Axial Live Tool*Part #CouplingL3Max RPM Drive RatioRHRB65AVCBMT6588.13MM6,0001:1BMT65 Radial Live Tool*AxialRadialInternal Coolant/External Coolant** • 800.791.7542Half-Index**MM 95MM95MMPSC Size 4PSC Size 4Radial Live Tools*Coupling Nut ColletShort External ER32Medium External ER32Long External ER32 Radial Live Tools*Drum ToteExtensive Product OfferingVa ri ab le In de x & H el ixEn dm il ls at G en er al Pu rp os e Pr ic es!E n d m i l l sperformed by courteous, knowledgeable,See pages 6-7 & 12-13 for complete details.Coolant Option: Internal Coolant*T e c h n i c a l I n f o r m a t i o nHaas Turrets-Tech InfoDescriptionST-20(Y)ST-30(Y)ST-20SS(Y)DS-30(Y)ST-30SS(Y) DS-30SS(Y)SL-40ST-40ABOT TURRETOD DIAMETER (FLATS)16.16” (410mm)16.16” (410mm)———22.27” (566mm)A1VB12/24 TURRETOD DIAMETER (FLATS)18.95” (481mm)18.95” (481mm)21.45” (545mm)18.95” (481mm)21.20” (538mm)22.27” (566mm)A2VDI TURRETOD TURRET DIAMETER19.00” (483mm)19.00” (483mm)———23.75” (603mm)B VB12/24 TURRETVDI40 POCKET CIRCLE15.63” (397mm)15.63” (397mm)18.25” (464mm)15.63” (397mm)18.25” (464mm)20.00” (508mm)B1*VDI TURRETVDI40 POCKET CIRCLE15.63” (397mm)15.63” (397mm)—15.63” (397mm)—20.00” (508mm)C VB12/24 TURRETVDI40 POCKET SPACING7.81” (198mm)7.81” (198mm) 4.69” (119mm)7.81” (198mm)4.69” (119mm)10.00” (254mm)C1*VDI TURRETVDI40 POCKET SPACING4.04” (103mm) 4.04” (103mm)———5.17” (131mm)D BOT TURRETFROM FLATS TC CLEARANCE6.90” (175mm)8.00” (203mm)———9.00” (229mm)D1VB12/24 TURRETFROM FLATS TC CLEARANCE5.50” (140mm)6.85” (174mm) 4.50” (114mm) 6.85” (174mm) 5.85” (149mm)9.00” (229mm)D1VB12/24 TURRETFROM VDI40 CENTER TC CLEARANCE7.00” (178mm)8.35” (212mm) 6.00” (152mm)8.35” (212mm)7.35” (187mm)10.00” (254mm)D2VDI TURRETFROM VDI40 CENTER TC CLEARANCE7.00” (178mm)8.35” (212mm)———10.00” (254mm)E BOT TURRETBOLT-ON TOOL MAX REAR STICKOUT4.00” (102mm) 4.00” (102mm)———4.37” (111mm)E VB12/24 TURRETBOLT-ON TOOL MAX REAR STICKOUT4.00” (102mm) 4.00” (102mm) 4.00” (102mm) 4.00” (102mm) 4.00” (102mm) 4.37” (111mm)E VDI TURRETVDI40 POCKET MAX TOOL REAR STICK-OUT0.40” (10.2mm)0.40” (10.2mm)0.40” (10.2mm)0.40” (10.2mm)0.40” (10.2mm).40” (10.2 mm)F **REC. MAX TOOL STICKOUT FROM FACE OF TURRET AT FULL Z TRAVEL5.00” (127mm) 5.00” (127mm)5.00” (127mm)5.00” (127mm)6.00” (152mm)***G BOT TURRETID TOOL POCKET DIAMETER18.66” (474mm)————25.42” (646mm)H VB12/24 TURRETID TOOL POCKET DIAMETER21.45” (545mm)21.45” (545mm)23.20” (589mm)21.45” (545mm)23.20” (589mm)25.42” (646mm)I BOT TURRETID TOOL POCKET SPACING4.80” (122mm)————6.60” (168mm)JVB12/24 TURRETID TOOL POCKET SPACING10.72” (272mm)10.72” (272mm)6.00” (152mm)10.72” (272mm)6.00” (152mm)12.76” (324mm)*ST-10 VDI POCKETS ARE STAGGERED **EXCEEDING THIS STICKOUT MAY RESULT IN COLLISION WITH THE FRONT BULKHEAD***A 25” (635 mm) DEEP POCKET IN THE ST-40 AND ST-40L PROVIDES CLEARANCE FOR BORING BARS AND LONG TOOLS.D2A2B1C1DGIAD1CBH JA1D1A1JHBCEF(BOT TOOL POCKETS ONLY )D2C1B1C1Max Tool Stick OutBOT TurretVDI TurretST-10 VDI TurretVB Hybrid 12 StationVB24 Hybrid 24 Station(All SS Models)The 12 Station base mount tooling turret accepts base mount tools and live tools. and perimeter stations for ID tools.Bolt-On Wedge ClampL1Screw3/4" OD Reduction Sleeves (Inch)ER Straight Shank Collet ExtensionsPart #RSSER11660ER Replacement NosepiecesSeries Diameter Part #.6301.259Straight Shank Rigid Tap HoldersShank øCollet Size B*C.75Bilz #1 3.92 1.50RSSTHR01392.75Bilz #2 4.70 1.88RSSTHR02470 * The “B” dimension is the assembled length including standard tap colletA6.0Straight Shank Tension & Compression Tap HoldersShank øCollet Size B*C1.00Bilz #12.50 1.501.25Bilz #2 3.25 1.88* The “B” dimension is the assembled length including standard tap collet。
漫威迪克斯机械工具说明书

Mounting Surface
For illustration purposes hose reel is not shown attached to base. Do not remove hose reel from base.
Base Step 3
INSTALLING HOSE After reel is secured in position, attach air hose coming from compressor. Wrap threads of male connector on incoming air hose with thread-sealing tape (included) or apply thread sealant and connect to air inlet valve on side of hose reel. Connect other end of incoming air hose to air compressor. Apply thread-sealing tape to threads on hose before attaching air tools.
18. Hose Clamp 19. Bolt 20. Nut 21. Bolt (4) 22. Washer (4) 23. Nut (4) 24. Air Outlet (To Hose) 25. Nut (4) 26. Axle 27. Locking Cam 28. Retaining Ring 29. Tension Spring 30. Bolt (4) 31. Washer (4) 32. Nut (4) 33. Retaining Ring 34. Bolt (4)
• Brass connectors on hose and reel
Harbor Freight Tools 电动扳手说明书

1. Study, understand, and follow all instructionsbefore operating this device.2. Do not exceed rated capacity.3. Use only on hard, level surfaces.4. Lifting device only. Immediately after lifting,support the vehicle with appropriate means.5. Do not move or dolly the vehicle while on the jack.6. Failure to heed these markings may result inpersonal injury and/or property damage.7. Lift only areas of the vehicle as specifiedby the vehicle manufacturer.8. No alterations shall be made to this product.9. Never work on, under or around a loadsupported only by this device.10. Do not adjust safety valve.11. Wear ANSI-approved safety goggles andheavy-duty work gloves during use.12. Keep clear of load while lifting and lowering. 13. Lower load slowly.14. Apply parking brake and chock tiresbefore lifting vehicle.15. Lift vehicle only at manufacturerrecommended locations.16. Inspect before every use; do not use if parts areloose or damaged, or if leaking hydraulic fluid.17. Do not use for aircraft purposes.18. Do not use any objects (such as blocks of wood) inbetween Saddle Pad or Saddle and lifting point.Objects placed on the Saddle will reducethe stability of the Jack, and could allow thevehicle to slip off the Saddle and fall.19. The warnings, precautions, and instructionsdiscussed in this manual cannot cover allpossible conditions and situations that may occur.The operator must understand that common senseand caution are factors, which cannot be built intothis product, but must be supplied by the operator. 20. The Handle socket may be held down by a clip undertension. Wear ANSI-approved safety goggles before freeing Handle socket. Remove clip carefully.21. People with pacemakers should consult theirphysician(s) before use. Electromagnetic fields inclose proximity to heart pacemaker could causepacemaker interference or pacemaker failure.SAVE THESE INSTRUCTIONS.IMPORTANT! Before first use:Check hydraulic oil level and fill to 1/4″ below the Fill Plug hole as needed as stated on page 6. Thoroughly test the Jack for proper operation. If it does not work properly, bleed air from its hydraulic system as stated on page 6.The Daytona [DJ3000] 3 Ton Professional Super Duty Jack was engineered for automotive professionals. The Model [DJ3000] features Advanced Rapid Pump® technology for fast lift times and exceptionally long life. Long-Life AdvancedRapid Pump® HydraulicsThe hydraulic power unit is designed to provide over 5000 lift cycles with minimal wear.An Integrated Magnetic Filtration (IMF) System prevents contaminantsfrom damaging pump pistons andother high pressure components.Precision-engineered high performance seals along with a sealed non-vented reservoir ensure longer fluid life with no leaks.Rapid Pump technology delivers twice the lift force with each stroke to lift heavy loads in half the time of conventional hydraulic systems. The pistons are continuously force-loaded to keep the pump handle in ready position during use. Load limiters with a bypass valve protect the pump if an overweight load is attempted. Low-Profile/High Lift SaddleThe Low Profile design gives you aminimum height of just 3.75″ for working with low-clearance vehicles. The extended liftarm provides High Lift for a maximum height of 23.125″ for plenty of working space when properly supported. The big 5″ x 5″ saddle supports lift points solidly without dangerof slipping. The saddle can be removed to install lifting accessories (sold separately.) Super Duty Strength and Durability The Daytona Super Duty Professional Jack chassis is constructed from all-weldedsteel plate with I-beam reinforcementfor extraordinary strength and reliability. Contoured steel wheels and casters roll smoothly with less surface area contact for exceptional mobility. Fully lubricated with dual bearings and easy access grease fittings.Effortless OperationGet easy leverage and positioning with the extra long foam-protected lift handle. All moving components are factory lubed for smooth action with easily serviceable grease fittings in thelift mechanism. A locking spring mechanism keeps the handle in place during use.The Rapid Pump® system gives youeasy-twist universal joint hydraulic releasefor precise, controlled lowering.Feature Summary:• Integrated Magnetic Filtration (IMF) System extends pump life byeliminating contaminants• Rapid Pump® technology to reachworking height with the fewest strokes• Low Profile with a lowered height of3.75″ for low clearance vehicles• High Lift for a maximum height of 23.125″• Super Duty all-welded steelI-beam construction• Contoured lift arm for amplerocker panel side clearance• Pumps and ram pistons withlong-life precision milled premium seals• Big 5″ x 5″ saddle with rubber cushioned pad and option for accessories• Easy access grease fittings in lift arm pivot, handle socket and front wheels• All-steel contoured wheels for easy mobility • Knurled long-reach lift handle locks in place, foam guard to protect vehicle finish • Powder coated finish for durabilitySaddle Pad SaddleHandleFoamBumperHandleSocketHandleReleaseContoured Lift ArmRead the ENTIRE IMPORTANT SAFETY INFORMATION section at the beginning of thismanual including all text under subheadings therein before set up or use of this product. Removing Shipping ClipCAUTION! The Handle socket may be held down by a clip under tension. Wear ANSI-approved safety goggles before freeing Handle socket. Remove clip carefully.A wire clip holds the Handle Socket in position during shipment. This helps prevents shipping damage. To remove it:1. Press down on the Handle Socket torelieve tension on the wire clip.2. Disconnect the wire clip legs from the bar.3. Slowly raise the Handle Socketuntil tension is released.4. Remove the wire clip.Attaching the Handle1. Slide the Upper Handle into the Lower Handle.Line the Button on the Lower Handle up with the hole in the Upper Handle until it clicks into place.2. Pull on the Handle Release and insert the groovedend of the Handle into the Handle Socket.3. Let go of the Handle Release. Gently pull upon the Handle to make sure that it is secure.Bleeding Trapped Air1. With the Jack fully lowered, remove the Fill Plug ontop of the Cylinder. Check that the oil level inside the Cylinder is at the top of the Piston. See Figure B.2. Insert the Handle into the Handle Socketto operate the Release Valve.3. Turn the Handle counterclockwise to open the valve.4. Pump the Handle up and down quickly10-15 times to force air from the system.5. Replace the Fill Plug.Figure A: Hydraulic UnitAdding OilNOTICE: To prevent damage and premature wear, use only 22 viscosity, non-detergent hydraulic jack oil.1. With the Jack fully lowered, remove theFill Plug on top of the Cylinder.2. Add non-detergent 22 weight hydraulic jack oilinto the Fill Plug hole slowly until the oil level just reaches the top of the Piston inside the Cylinder.3.Replace the Fill Plug.Figure B: Fill LevelRead the ENTIRE IMPORTANT SAFETY INFORMATION section at the beginning of thismanual including all text under subheadings therein before set up or use of this product. LiftingPark vehicle on a flat, level, solid, surface safely away from oncoming traffic. Turn off the vehicle’s engine. Place the vehicle’s transmission in “PARK” (if automatic) or in its lowest gear (if manual).Set the vehicle’s emergency brake. Then, chock the wheels that are not being lifted.1. Turn the Handle counterclockwise to lower the Jack.Once the Jack is fully lowered, turn theHandle firmly clockwise to close it.2. Carefully position the Saddle of the Jack under thevehicle manufacturer’s recommended lifting point.(See vehicle manufacturer’s owner’s manualfor location of frame lifting point.)3. Pump the Handle until the top of the Jack’s Saddlehas nearly reached the vehicle lifting point. Positionthe Saddle directly under the vehicle’s lifting point. 4. To lift the vehicle, pump the Handle ofthe Jack. Use smooth, full strokes.5. Once the vehicle is raised, slide a jack stand ofappropriate capacity (not included) under a properlifting point referred to in the vehicle owner’smanual. Always use two jack stands, position themat the same point on each side of the vehicle.WARNING! The rated capacity of jack stands is per pair, not the individual capacities combined unless specifically noted on the product by the jack stand manufacturer. Do not exceed rated jack stand capacity. Ensure that the vehicle support points are fully seatedin the saddle of both jack stands. Use a matched pairof jack stands per vehicle to support one end only. Failure to do so may result in the load suddenly falling, which may cause personal injury and/or property damage.6. Center the vehicle’s lifting point(s) on the saddle ofthe jack stand(s). Set the jack stand(s) to the same height according to the manufacturer’s instructions,making sure that they lock securely into position.7. Slowly turn the Handle counterclockwise to lowerthe vehicle onto the saddle(s) of the jack stand(s).Then, turn the Handle firmly clockwise to close it.Lowering1. Carefully remove all tools, parts, etc.from under the vehicle.2. Position the Saddle under the lifting point.Turn the Handle firmly clockwise and raise load high enough to clear the jack stands,then carefully remove jack stands.3. Slowly turn the Handle counterclockwise(never more than 1/2 full turn) to lowerthe vehicle onto the ground.4. Lower the Jack completely. Then, store in asafe, dry location out of reach of children.5. To prevent accidents, turn off the tool anddisconnect its power supply after use. Clean, then store the tool indoors out of children’s reach.Procedures not specifically explained in this manual mustbe performed only by a qualified technician.TO PREVENT SERIOUS INJURY FROM TOOL FAILURE: Do not use damaged equipment. If abnormal noise or vibration occurs, have the problem corrected before further use.1. BEFORE EACH USE, inspect the generalcondition of the tool. Check for:• leaking hydraulic fluid,• loose hardware or parts,• misalignment or binding of moving parts,• cracked, bent or broken parts, and• any other condition that mayaffect its safe operation.Thoroughly investigate and correct the causes for all issues that are found. Do not use Jack until all issues are understood and properly corrected.ALSO, BEFORE EACH USE, thoroughly testthe Jack for proper operation prior to actual use.If the Jack’s motion seems spongy or theSaddle does not lift completely, followBleeding instructions on page 6.2. AFTER USE, wipe dry with a clean cloth. Then,store the Jack in a safe, dry location out of reachof children and other non-authorized people. NOTICE: Storing the Jack in a humid area orexposing it to corrosive vapor voids the warranty.3. Weekly - Jack Lubrication:a. Lubricate according to the below steps usingonly general purpose lithium grease.b.Inject grease into each of the 5 grease fittings.Figure C: Grease Fitting Locationc.Lubricate the linkages and pivot points lightly.Figure D: Additional Lubrication Points Note: Improper or inadequatelubrication voids the warranty.4. Change the hydraulic oil at leastonce every three years:a. With the Jack fully lowered, remove theFill Plug on the top of the Cylinder.b. Tip the Jack to allow the old hydraulic oilto drain out of the Housing completely,and dispose of the old hydraulic oil inaccordance with local regulations.c. Turn the Jack upright. Add non-detergent22 weight hydraulic jack oil into the Fill Plughole slowly until the oil level just reachesthe top of the Piston inside the Cylinder.d. Replace the Fill Plug.e. Follow instructions forBleeding Trapped Air on page 6.Figure E: Fill LevelTO PREVENT SERIOUS INJURY:Use caution when troubleshooting a malfunctioning jack. Stay well clear of the supported load. Completely resolve all problems before use. If the solutions presented in the Troubleshooting guide do not solve the problem, have a qualified technician inspect and repair the jack before use.After the jack is repaired: Test it carefully without a load by raising and lowering it fully,checking for proper operation, BEFORE RETURNING THE JACK TO OPERATION.DO NOT USE A DAMAGED OR MALFUNCTIONING JACK!Visit our website at: Emailourtechnicalsupportat:********************************Part Description Qty. 1Saddle Pad1 2Saddle Screw1 3Saddle1 4Lift Arm1 5Retaining Ring 162 6Front Wheel2 7Front Wheel Washer2 8Lock Nut M162 9Grease Fitting5 10Jack Frame1 11Support Bar Bolt2 12Retaining Ring 302 13Nut M164 14Screw M5X124 15Washer 164 16Washer 124 17Screw M12X224 18Rear Caster Assembly2 19Screw M8X204 20Washer 84 21Left Handle Socket Bolt1 22Washer 181Part Description Qty. 23Retaining Ring 252 24Return Spring2 25Hydraulic Pump Unit1 26Lower Handle 1 27Foam Bumper1 28Handle Lock Clip1 29Upper Handle1 30U-Joint1 31Handle Release1 32Roller Pin1 33Roller1 34Retaining Ring 141 35Handle Socket1 36Split Pin 4X551 37Hydraulic Pump Block1 38Lower Tie Rod1 39Upper Tie Rod1 40Retaining Ring 181 41Right Handle Socket Bolt1 42Cover Plate1 43Support Bar2 44Fill Plug1PLEASE READ THE FOLLOWING CAREFULLYTHE MANUFACTURER AND/OR DISTRIBUTOR HAS PROVIDED THE PARTS LIST AND ASSEMBLY DIAGRAM IN THIS MANUAL AS A REFERENCE TOOL ONLY. NEITHER THE MANUFACTURER OR DISTRIBUTOR MAKES ANY REPRESENTATION OR WARRANTY OF ANY KIND TO THE BUYER THAT HE OR SHE IS QUALIFIED TO MAKE ANY REPAIRS TO THE PRODUCT, OR THAT HE OR SHE IS QUALIFIED TO REPLACE ANY PARTS OF THE PRODUCT. IN FACT, THE MANUFACTURER AND/OR DISTRIBUTOR EXPRESSLY STATES THAT ALL REPAIRS AND PARTS REPLACEMENTS SHOULD BE UNDERTAKEN BY CERTIFIED AND LICENSED TECHNICIANS, AND NOT BY THE BUYER. THE BUYER ASSUMES ALL RISK AND LIABILITY ARISING OUT OF HIS OR HER REPAIRS TO THE ORIGINAL PRODUCT OR REPLACEMENT PARTS THERETO, OR ARISING OUT OF HIS OR HER INSTALLATION OF REPLACEMENT PARTS THERETO.Record Product’s Serial Number Here: Note: If product has no serial number, record month and year of purchase instead.Note: Some parts are listed and shown for illustration purposes only, and are not available individually as replacement parts.135 6918212425303540272983136442322628743424141213151617141920223938373433321011Page 11For technical questions, please call 1-888-866-5797.Item 63183Harbor Freight Tools Co. makes every effort to assure that its products meet high quality and durability standards, and warrants to the original purchaser that this product is free from defects in materials and workmanship for the period of 3 years from the date of purchase. This warranty does not apply to damage due directly or indirectly,to misuse, abuse, negligence or accidents, repairs or alterations outside our facilities, criminal activity, improper installation, normal wear and tear, or to lack of maintenance. We shall in no event be liable for death, injuriesto persons or property, or for incidental, contingent, special or consequential damages arising from the use ofour product. Some states do not allow the exclusion or limitation of incidental or consequential damages, so the above limitation of exclusion may not apply to you. THIS WARRANTY IS EXPRESSLY IN LIEU OF ALL OTHER WARRANTIES, EXPRESS OR IMPLIED, INCLUDING THE WARRANTIES OF MERCHANTABILITY AND FITNESS. This warranty gives you specific legal rights and you may also have other rights which vary from state to state.3491 Mission Oaks Blvd. • PO Box 6009 • Camarillo, CA 93011 • 1-888-866-5797。
- 1、下载文档前请自行甄别文档内容的完整性,平台不提供额外的编辑、内容补充、找答案等附加服务。
- 2、"仅部分预览"的文档,不可在线预览部分如存在完整性等问题,可反馈申请退款(可完整预览的文档不适用该条件!)。
- 3、如文档侵犯您的权益,请联系客服反馈,我们会尽快为您处理(人工客服工作时间:9:00-18:30)。
汽车测电笔
刮刀 圆柱冲
卷尺
圆锥冲
钳工凿
油管扳手
转接头
6.3mm套筒螺丝批
可弯式螺帽螺丝批
接长杆
柔性磁性捡拾器
三爪取物器 组合/两用扳手组
12.5mm套 筒及组件
6.3mm套筒及组件
6.3mm穿透式棘轮扳手
6.3mm棘轮扳手 10mm棘轮扳手
10mm转向棘轮扳手
12.5mm棘轮扳手
T型 滑杆
万向 接头
转向 接杆 万向 套筒
双开口扳手组
组合/两用 扳手组
双梅花扳手组
斜口钳 钢丝钳 尖嘴钳
卡簧钳
大力钳
水泵钳
安装锤 钳工锤
钢丝刷
1
螺丝刀 组件
2
套筒组 件-1
3
套筒组 件-2
4
扳手 组件
5
钳子 组件
6
锤 /冲 / 尺
7
其他
内六角扳手组
一字、十字 螺丝批组
花形螺丝批组
花形扳手组件
6.3mm系列 旋具头
12.5mm系列 E形套筒
10mm套筒 及组件
加长中孔花形 内六角扳手
10mm系列 E形套筒பைடு நூலகம்
6.3mm系列E 形套筒
12.5mm系列花 形旋具套筒