注射模具
注射模结构及分类
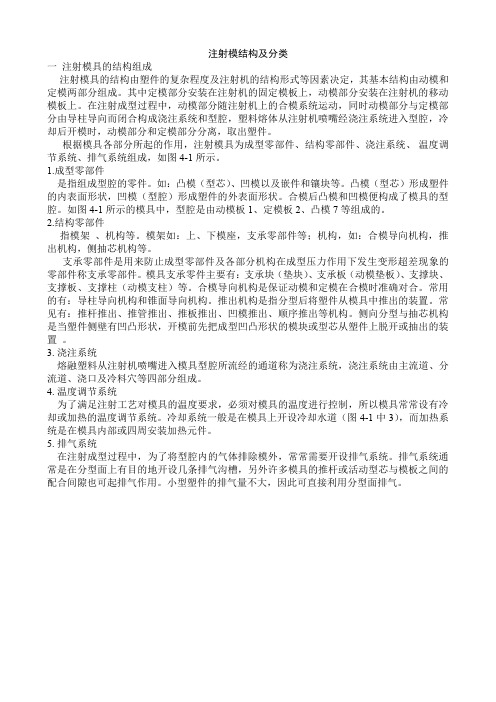
注射模结构及分类一注射模具的结构组成注射模具的结构由塑件的复杂程度及注射机的结构形式等因素决定,其基本结构由动模和定模两部分组成。
其中定模部分安装在注射机的固定模板上,动模部分安装在注射机的移动模板上。
在注射成型过程中,动模部分随注射机上的合模系统运动,同时动模部分与定模部分由导柱导向而闭合构成浇注系统和型腔,塑料熔体从注射机喷嘴经浇注系统进入型腔,冷却后开模时,动模部分和定模部分分离,取出塑件。
根据模具各部分所起的作用,注射模具为成型零部件、结构零部件、浇注系统、温度调节系统、排气系统组成,如图4-1所示。
1.成型零部件是指组成型腔的零件。
如:凸模(型芯)、凹模以及嵌件和镶块等。
凸模(型芯)形成塑件的内表面形状,凹模(型腔)形成塑件的外表面形状。
合模后凸模和凹模便构成了模具的型腔。
如图4-1所示的模具中,型腔是由动模板1、定模板2、凸模7等组成的。
2.结构零部件指模架、机构等。
模架如:上、下模座,支承零部件等;机构,如:合模导向机构,推出机构,侧抽芯机构等。
支承零部件是用来防止成型零部件及各部分机构在成型压力作用下发生变形超差现象的零部件称支承零部件。
模具支承零件主要有:支承块(垫块)、支承板(动模垫板)、支撑块、支撑板、支撑柱(动模支柱)等。
合模导向机构是保证动模和定模在合模时准确对合。
常用的有:导柱导向机构和锥面导向机构。
推出机构是指分型后将塑件从模具中推出的装置。
常见有:推杆推出、推管推出、推板推出、凹模推出、顺序推出等机构。
侧向分型与抽芯机构是当塑件侧壁有凹凸形状,开模前先把成型凹凸形状的模块或型芯从塑件上脱开或抽出的装置。
3. 浇注系统熔融塑料从注射机喷嘴进入模具型腔所流经的通道称为浇注系统,浇注系统由主流道、分流道、浇口及冷料穴等四部分组成。
4. 温度调节系统为了满足注射工艺对模具的温度要求,必须对模具的温度进行控制,所以模具常常设有冷却或加热的温度调节系统。
冷却系统一般是在模具上开设冷却水道(图4-1中3),而加热系统是在模具内部或四周安装加热元件。
注射模设计步骤及实例

注射模设计步骤及实例注射模是用于制作注射器、针筒等医疗设备的模具。
模具的制作是一个复杂而精细的过程,需要经历多个步骤。
下面将详细介绍注射模的设计步骤及实例。
1.确定需求:在开始设计之前,首先需要与客户充分沟通,了解客户的需求和要求,包括产品的形状、尺寸、材料等。
同时还需要了解注射模的使用环境和功能要求,以确保设计出符合实际需要的模具。
2.绘制初步草图:在了解客户需求的基础上,设计师将根据实际情况绘制初步草图。
这个过程需要考虑到模具的整体结构、零件的尺寸和形状等。
设计师可以使用CAD等软件进行绘图,以便对模具的设计进行更好的规划和控制。
3.模具分析:在绘制初步草图之后,设计师需要进行模具分析。
这个过程包括识别和解决可能出现的问题,比如材料选择、产品的易变形部位等。
同时,还需要对模具进行结构分析,确保模具的稳定性和可靠性。
4.详细设计:在完成模具分析之后,设计师将开始进行详细设计。
这个过程需要考虑到模具的每个零件的制造和组装过程。
设计师需要了解材料的特性,选择合适的工艺和加工方法,并进行每个零件的细节设计。
5.制造模具:在完成详细设计之后,设计师需要将设计图纸交给模具制造厂家进行加工和制造。
制造过程需要使用各种加工设备,比如车床、铣床等,对模具的零件进行加工。
在制造过程中,需要进行严格的质量控制,确保每个零件的精度和质量。
6.装配和调试:在完成模具的制造之后,需要对模具进行装配和调试,以保证模具的正常运行。
这个过程包括将各个零件按照设计要求进行组装,并对模具进行调整和测试。
在调试过程中,需要确保模具的各个部分和功能都正常运作。
7.试模和样品确认:在完成装配和调试之后,需要进行试模和样品确认。
试模是指将模具放入注射机进行注射,获得产品样品,并对产品进行检验。
样品确认是指客户对样品进行验收,并根据需要提出修改要求。
8.修改和改进:根据客户的反馈和需求,设计师需要对模具进行修改和改进。
这个过程包括根据样品确认的结果,对模具的设计进行修改,以提高模具的性能和使用效果。
第三章 塑料注射模具设计-1

3、具有侧向抽芯时的最大开模行程校核
Hc
H1
H2
第四节
浇注系统设计
1)将来自注射机喷嘴的塑料熔体均匀而
平稳地输送到型腔,同时使型腔内的气 体能及时顺利排出。输送流体
作用
2)在塑料熔体填充及疑固的过程中,将 注射压力有效地传递到型腔的各个部位, 以获得形状完整、内外在质量优良的塑 料制件。传递压力
分类
普通流道浇注系统
无流道浇注系统
主流道 组成 分流道 浇口 冷料穴
浇注系统的 设计原则
布局
尽可能采用平衡式布置 型腔布置和浇口开设部位尽 可能对称,防偏产生溢料 尽可能紧凑,减小模具尺寸
热量及压力损失要小:浇注系统的流程尽可能短,尺寸尽可能大。减少折弯、提 高光洁度; 浇注系统应按型腔布局设计,尽量与模具中心线对齐; 制品投影面较大时,应避免在模具单面开设浇口,否则会造成注射时受力不均;
(3)塑化能力
注塑机的塑化能力是影响模腔数目的另一个重要因素。将射出机 的塑化能力(P)除以每分钟估计的射出次数 (X)和塑件重量 (W), 即可计算出模腔数目。 模腔数目 = P / ( X × W) 模腔数目 = (K*M*T/3600- m浇)/ mi
M是注塑机的公称塑化量(g/h);T是注射成型周期(s)
课本中的模具
(5)组合活动镶块 & & &
四、其他模具 (1)定模设有推出机构的模具;
(2)弹簧分型拉杆定距式双分 型面模具;¥ (3)带自动脱螺纹机构的模具; 螺纹脱模机构动画.swf
定模设有推出机构
(4)带双向推出机构的模具;
(5)其它
带自动卸螺纹机构
马达固定板 感应开关 水路接头 垃圾钉 滑块镶针 滑块镶针 波 滑 珠 块 未 未 未
塑料注射模具知识点总结

概述塑料注射模具是用于制造塑料制品的一种装置,由模具基板、模具芯、注射系统、冷却系统、脱模系统等部分组成。
塑料注射模具制造是一项相对复杂的工艺,需要对材料、工艺、设计、加工等方面具有深入的了解和掌握。
本文将从材料、设计、加工、维护等方面综合介绍塑料注射模具的知识点。
一、塑料注射模具的材料1.1 模具基板材料模具基板是塑料注射模具的主要承载部分,需要具有高强度、耐磨损、耐腐蚀等特性。
常见的模具基板材料有P20、718、2738等。
P20材料具有良好的硬度和耐磨损性能,适合制作中小型模具;718材料具有高强度和硬度,适合制作大型模具;2738材料具有高镍合金特性,适合制作高精度模具。
1.2 模具芯材料模具芯是用于塑料制品内部结构的部分,需要具有高硬度、高精度、耐磨损等特性。
常见的模具芯材料有SKD61、S136等。
SKD61材料具有良好的热稳定性和硬度,适合制作高品质的模具芯;S136材料具有良好的耐腐蚀性和耐磨损性,适合制作高精度的模具芯。
1.3 注射系统材料注射系统是用于将熔融塑料材料注入模具腔内的部分,需要具有耐高温、耐腐蚀、高流动性等特性。
常见的注射系统材料有H13、H13W等。
H13材料具有良好的耐热性和抗氧化性,适合制作注射系统组件;H13W材料具有更高的硬度和耐磨损性,适合制作高性能的注射系统组件。
1.4 冷却系统材料冷却系统是用于控制模具温度的部分,需要具有良好的传热性能、耐腐蚀、高耐压等特性。
常见的冷却系统材料有铜合金、铝合金、不锈钢等。
铜合金具有良好的导热性和抗腐蚀性,适合制作冷却系统管道;铝合金具有较轻的重量和较高的导热性,适合制作冷却系统散热器;不锈钢具有较高的耐腐蚀性和耐压性,适合制作高性能的冷却系统组件。
1.5 脱模系统材料脱模系统是用于将成型塑料制品从模具中脱离的部分,需要具有良好的脱模性能、耐磨损、易维护等特性。
常见的脱模系统材料有冷作钢、硬质合金等。
冷作钢具有良好的硬度和耐磨损性,适合制作脱模系统零部件;硬质合金具有更高的硬度和耐磨损性,适合制作高性能的脱模系统零部件。
模具毕业设计103注射模的结构设计

模具毕业设计103注射模的结构设计注射模具是工业制造过程中使用最广泛的一种模具,其设计结构直接影响到注射产品的质量和生产效率。
本文将详细介绍注射模具的结构设计,包括模具的结构要求、主要零件设计和结构优化。
一、模具的结构要求1.注射模具的结构要具有良好的刚性和稳定性,以确保模具在注射过程中不发生变形和振动,影响产品的精度和表面质量。
2.注射模具的结构要便于装卸、维修和保养,以提高模具的使用寿命和工作效率。
3.注射模具的结构要尽可能简单,以降低模具的制造成本和维修成本。
二、注射模具的主要零件设计1.模具基座:模具基座是支撑模具的主要部件,其结构要具有足够的刚性和稳定性。
为了方便模具的安装和调整,模具基座通常采用箱式结构,并设置有调整螺栓。
2.模板:模板是注射模具的主要部件,其上安装有注射模具的零件和导向机构。
模板的结构要求平整度高、刚性好,并配有合适的冷却系统,以确保注射过程中的热平衡。
3.滑块和导柱:滑块和导柱是注射模具中重要的导向和定位部件。
滑块通常用于实现中空或复杂形状的注射产品,其结构要求刚性好、耐磨损,并具有良好的导向性能。
导柱负责注射模具的下模板与上模板的定位,其结构要求尺寸精确、表面光洁,并配有合适的润滑系统。
4.模芯和模腔:模芯和模腔是注射模具成型部件的关键零部件,直接决定了注射产品的形状和尺寸。
模芯和模腔的设计要考虑到材料的选用、热处理和表面处理等因素,以提高模具的耐用性和工作精度。
三、注射模具的结构优化为了进一步提高注射模具的生产效率和产品质量,可以采取以下措施进行结构优化:1.采用优质材料:选择适当的模具材料,具有良好的强度和耐磨性,以提高模具的使用寿命和工作精度。
2.优化冷却系统:合理设置注射模具的冷却系统,以提高注射过程中的热平衡,减少产品变形和缩水现象。
3.降低模具重量:通过优化模具结构和采用轻量化材料,来减轻模具的重量,降低模具的惯性和振动,提高注射产品的精度和表面质量。
第一节模具分类及与注射机的关系课件

2024/10/3
16
塑料注射成型模具
开模行程校核
对带螺纹的制品,如果要通过开模的动力和行程来旋出 螺纹型芯或螺纹型环,则应考虑全部脱出螺纹所需的开 模行程Hs 是否大于H1+H2 ,如果Hs >H1+H2 ,则以Hs为准。 设计模具时还要考虑注射机的顶出方式、顶杆中心距和 最大顶出距离,常见的顶出方式有:
另外还有转盘式注射机、旋转式注射机、热固性塑料 注射机、双色注射机等。
2024/10/3
20
结束
2024/10/3
21
储料——合模——注射——保压——补塑
(冷却——————)——开模——脱模
2024/10/3
(储料 ———)
22
2024/10/3
螺杆式注射机工作原理
23
2024/10/3
柱塞式注射机工作原理
第二章塑料注射成型模具
2024/10/3
1
第一节 模具分类及与注射机的关系
重点、难点
• 重点:
• 注射模具典型结构及类型 • 模具与注射机相关校核
• 难点:
• 模具与注射机相关校核
2024/10/3
2
注射模具典型结构
塑料注射成型模具
注射模具皆有动模和定模两部分,动模和定模闭合形成 型腔和浇注系统。开模时,动模移动离开定模露出型腔 中的塑料制品,然后注射机顶出系统推动模具顶出系统 顶出制品。
(机械锁模)
S>=Hm +H1+H2+5~10 (mm) (液压锁模)
2024/10/3
39
三板式模具开模行程校核
3
注射模具的工作原理
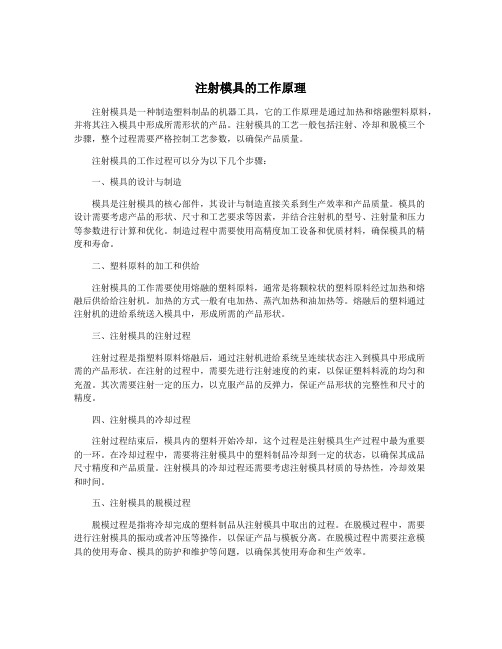
注射模具的工作原理注射模具是一种制造塑料制品的机器工具,它的工作原理是通过加热和熔融塑料原料,并将其注入模具中形成所需形状的产品。
注射模具的工艺一般包括注射、冷却和脱模三个步骤,整个过程需要严格控制工艺参数,以确保产品质量。
注射模具的工作过程可以分为以下几个步骤:一、模具的设计与制造模具是注射模具的核心部件,其设计与制造直接关系到生产效率和产品质量。
模具的设计需要考虑产品的形状、尺寸和工艺要求等因素,并结合注射机的型号、注射量和压力等参数进行计算和优化。
制造过程中需要使用高精度加工设备和优质材料,确保模具的精度和寿命。
二、塑料原料的加工和供给注射模具的工作需要使用熔融的塑料原料,通常是将颗粒状的塑料原料经过加热和熔融后供给给注射机。
加热的方式一般有电加热、蒸汽加热和油加热等。
熔融后的塑料通过注射机的进给系统送入模具中,形成所需的产品形状。
三、注射模具的注射过程注射过程是指塑料原料熔融后,通过注射机进给系统呈连续状态注入到模具中形成所需的产品形状。
在注射的过程中,需要先进行注射速度的约束,以保证塑料料流的均匀和充盈。
其次需要注射一定的压力,以克服产品的反弹力,保证产品形状的完整性和尺寸的精度。
四、注射模具的冷却过程注射过程结束后,模具内的塑料开始冷却,这个过程是注射模具生产过程中最为重要的一环。
在冷却过程中,需要将注射模具中的塑料制品冷却到一定的状态,以确保其成品尺寸精度和产品质量。
注射模具的冷却过程还需要考虑注射模具材质的导热性,冷却效果和时间。
五、注射模具的脱模过程脱模过程是指将冷却完成的塑料制品从注射模具中取出的过程。
在脱模过程中,需要进行注射模具的振动或者冲压等操作,以保证产品与模板分离。
在脱模过程中需要注意模具的使用寿命、模具的防护和维护等问题,以确保其使用寿命和生产效率。
注射模具是一项非常重要的生产技术,它涉及到材料科学、加工技术和机械设备的多个领域。
注射模具生产工艺需要由严格的工艺控制和操作规范,从而确保产品精度、质量和生产效率。
注射模分类

注射模分类1.单分型面注射模具(2 PLATE MOLD)单分型面注射模具又称为两板式模具,它是注射模具中最简单而又最常用的一类。
型腔的一部分(型芯)在动模板上,另一部分(凹模)在定模板上。
主流道设在定模一侧,分流道设在分型面上。
塑料成熔融状态后,通过啤机的喷嘴在高温、高压、高速下,经过浇注系统进入型腔。
保压一段时间,经过一段时间的冷却,使制品硬化到一定程度后,在啤机作用下使后模向后退,模具在P L1处开一段距离。
并且由于动模上拉料杆的拉料作用以及制品因收缩包紧在后模仁上,制品连同流道一起留在动模一侧。
接着啤机的顶杆通过K.O孔,推动顶针板,带动顶针等,顶出制品。
合模时在啤机的作用下使模具合拢。
顶针板由回针复位,带动顶针等回复原位。
(通过3D 图更详细的讲解模具结构及开模动作)。
2. 三板模或细水口模(3 PLATE MOLD, PIN-POINT GATE MOLD)有两个分型面将模具分成三部分,比两板模增加了浇口板,适用于制品的四周不准有浇口痕迹、成品表面针点进胶、进胶点偏心的场合,这种模具采用点浇口,所以叫细水口模。
开模时,在啤机作用下动模向后退,A、B板由于胶钉作用不开模,又由于唧嘴扣住流道,面板与水口推板固定不动。
故首先在P L1处开模,使分流道与制品分开。
经过B行程之后,行程螺丝带动水推板,使面板与水口推板在P L2开模,主流道脱离唧嘴。
再经过行程A之后,在限位螺丝1、2的作用下A板不能再跟B板远动。
PL3开模。
注意事项:设计时要保证以下关系:1:B>S1+S2+20; 2: L>A+B+C+20; 3: A>S1;B—限位螺丝(1)的行程;A—限位螺丝(2)的行程;S1—主流道的长度;S2—分流道的长度;C—上下模相插高度;3.热流道模(HOT RUNNER MANIFOLD)借助加热装置使浇注系统中的塑料不会凝固,也不会随制品脱模,所以又称无流道模。
优点:1)无废料2)可降低注射压力,可以采用多腔模;3)可缩短成型周期4)提高制品的质品。
注射模具的基本结构与分类

三、带活动镶件的注射模
1-定模板 2-导柱 3活动镶件 4-型芯 5动模板 6-动模垫板 7-垫板 8-弹簧 9-推 杆 10-推杆固定板 11-推板 12-动模座板
四、带有侧向抽芯的注射模
1-楔紧块 2-斜导柱 3-侧型芯滑块 4-型 芯 5-型芯固定板 6动模垫板 7-垫块 8动模座板 9-推板 10-推杆固定板 11推杆 12-拉料杆 13导柱 14-动模板 15浇口套 16-定模座板 17定位圈
四、自动脱螺纹的注射模
1-螺纹型芯 2-模脚 3动模垫板 4-定距螺钉 5-动模板 6-衬套 7定 模板 8-注射机开合模 丝杠
工作原理:
塑件带有内螺纹或外螺纹须自动脱模时,在 模具中需要设置可以旋转的螺纹型芯或者型环。 通过注射机的往复运动或旋转运动,或者设置专 门的驱动(如电动机或液压马达等)和传动机构, 带动螺纹型芯者型环转动,使塑件脱出。 开模时,A-A面先分开,同时,螺纹型芯1在 随着注射机开合模丝杆8的后退中自动旋转,此时, 螺纹塑件由于定模板7的止转作用并不移动,仍留 在型腔内。当A-A面分开一段距离,即螺纹型芯1 在塑件内还有最后一牙时,定距螺钉4拉动动模板 5,使模具沿B-B打开,此时,塑件随型芯一道离 开定模型腔,然后从B-B分型面两侧的空间取出。
六、推出机构设在定模一侧的注射模
1-动模座板 2-垫板 3-定模垫板 4-成型 镶件 5、7-螺钉 6动 模板 8-脱模板 9-拉 板 10-定模板 11-定 模座板 12型芯 13导 柱
工作原理:
为便于注射机锁模系统的顶出装置工作,模 具开模后,塑件一般留在动模一侧,模具脱模机 构也设置在动模一侧。有时由于塑件的特殊要求 或者形状的限制,开模后塑件可能留在定模一侧, 这时就需要在定模一侧设置脱模机构。定模一侧 的脱模机构一般是采用拉板、拉杆或者链条与动 模相连。。 开模后,塑件紧包在凸模11 上,塑件留在了 定模一侧,当动模左移一定距离,拉板8 通过定 距螺钉6 带动推件板7 将塑件从凸模中脱出。
注射模基本结构
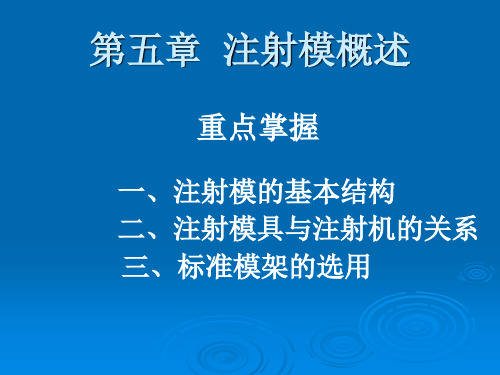
3.带有活动镶件的注射模具
塑件的外形结构复杂,无法 通过简单的分型从模具内取出塑 件,这时可在模具中设置活动镶 件和活动的侧向型芯或半块(哈 夫块)。 结构:图5—3。开模时活动 部件不能简单地沿开模方向与制 件分离,而是在脱模时将它们连 同制品一起移出模外,然后用手 工或简单工具将它们与塑件分开。 当将这些活动镶件嵌入模具时还 应可靠地定位。这类模具的生产 效率不高,常用于小批量或试生 产。
p=kpo (5—3) 式中 po——注射压力,MPa; k——压力损耗系数,随塑料品种、注射机形式、 喷嘴阻力、流道阻力等因素变化,可在0.2~0.4的范围 内选取。
型腔压力另几种确定方法: ①经验估计,成型中、小型塑料制品时型腔压力p取 20~40 MPa。对于流动性差、形状复杂、精度要求高的制 品,成型时需要较高的型腔压力。常用塑料推荐选用的型 腔压力见表5—l,因制件形状和精度不同时常选用的型腔 压力见表5—2。 ②利用注射流动和保压模拟软件来预测成型时所需的 锁模力,由于模拟过程中综合考虑了多种因素的影响,故 可靠性比以上的估算方法要好得多。
7.侧抽芯机构 有些带有侧凹或侧孔的塑件,被推出前须先进行侧向 分型,抽出侧向型芯后方能顺利脱模,此时需要在模具中 设置侧抽芯机构。 8.标准模架
为了减少繁重的模具设计与制造工作量,注射模大多 采用了标准模架结构,图5—l中的定位圈l、定模座板3、 定模板4、动模板5、动模垫板6、动模底座7、推出固定板 8、推板9、推杆11、导柱12等都属于标准模架中的零部件, 它们都可以从有关厂家订购。
V nVn V j m nmn m j
(5-1)
式中V(m)——一个成型周期内所需注射的塑料容积或质量, cm3 (g); n——型腔数目; Vn(mn)——单个塑件的容积或质量,cm3或g; Vj(mj)——浇注系统凝料的容量或质量,cm3或g。
注射模具的类型

6 ➢ 又称直角式注射模。该类模具在成型时进
料方向与开模方向垂直。
图3.47所示为一般的直角式注射模。
图3.47 直角式注射模
1 定模座板 2 浇道镶块 3 定模板 4 凹模 5 导柱 6 推件板
7 动模板 8 凸模 9 限位螺钉 10 推板 11 推杆 12 垫块
13 支承板
7. 自动卸螺纹的注射模具
图3.45 1 定模板 2 导柱 3 活动镶件 4 型芯 5 动模板 6 支承板7 模脚 8 弹簧 9 推杆 10 推杆固定板 11 推板
5
图3.46 定模部分带有推出
1 模脚 2 支承板 3 成型镶块 4 拉板紧固螺钉 5 动模板 6 7 推件板 8 拉板 9 定模板 10 定模座板 11 型芯 12 导柱
16 加热器孔17 定模座板
18 绝热层19 浇口套20 定位圈21 注射机喷嘴
塑料成型工艺与模具设计
分型,此时,塑件随着型芯一道离开定模
型腔,然后从B分型面两侧的空间取出。
图3.49 几种脱模机构
8 ➢包括热流道和绝热流道注射模 如图3.50所示为一热流道注射模。
图3.50
1 动模座板2,13 垫块3 推板 4 推杆固定板5 推杆
6 支承板7
8 动模板9 型芯10 导柱11 定模板
12 凹模14 喷嘴15
图3.48 自动卸螺纹的直角式注射模 1 螺纹型芯 2 垫块 3 支承板 4 5 动模板 6 衬套 7 定模板 8 注射机开合模丝杠
图3.49为自动卸螺纹的直角式注射模。 开模时,A分型面先分开,同时螺纹型芯随 着注射机开合模丝杠8的后退而自动旋转, 此时,螺纹塑件由于定模板7的止转而并不 移动,仍然留在模腔内。当A分型面分开一 段距离,螺纹型芯1在塑件内还有最后一牙 时,定距螺钉4拉动动模板5,使B分型面
项目七注射模具模架的选用

模架的成本和环保要求也是需要考虑的重要因素。在选用模架时,应选择具有成本效益 和环保要求的材料和结构形式。例如,可选择可回收利用的材料或可降解的材料来降低
对环境的影响。同时,还需要考虑模架的维护和保养成本,以确保长期的经济效益。
PART 04
注射模具模架的未来发展
REPORTING
WENKU DESIGN
注射模具模架是注射成型工艺中的重 要组成部分,其质量和性能直接影响 着注射成型的效率和产品质量。
注射模具模架的分类
根据模架的结构形式,可分为二板模架和三板模架。二板模 架结构简单,制造成本较低,适用于简单的制品;三板模架 则适用于结构较复杂的制品。
根据模架的材料,可分为铸铁模架、铝合金模架和钢材模架 。铸铁模架具有较高的强度和耐磨性,但重量较大;铝合金 模架轻便,易于搬运,但强度较低;钢材模架则具有较好的 综合性能。
实例三:包装容器注射模具模架的选用
总结词
考虑容器结构和材料
详细描述
包装容器的结构和材料对模架的选用有一定的影响。例如,对于纸盒包装容器,需要考虑纸盒的结构和强度要求; 对于塑料包装容器,需要考虑塑料的流动性和收缩率等特性。在选用模架时,应根据容器的结构和材料特性选择 合适的材料和结构形式。
实例三:包装容器注射模具模架的选用
项目七注射模具模架 的选用
https://
REPORTING
• 注射模具模架的概述 • 注射模具模架的选用原则 • 注射模具模架的选用实例 • 注射模具模架的未来发展
目录
PART 01
注射模具模架的概述
REPORTING
WENKU DESIGN
注射模具模架的定义
注射模具模架是用于固定和支撑注射 模具的关键部件,它由模座、定模板 和动模板等组成,用于承受注射机的 压力并将模具与注射机连接起来。
41注塑模具的结构形式

1、单分型面注射模 2、多分型面注射模 3、带有活动镶块的注射模 4、侧向分型抽芯的注射模 5、带有嵌件的注射模 6、自动卸螺纹的注射模 7、定模设置推出机构的注射模 8、带定距分型拉紧机构的注射模 9、无流道注射模
4-1 注射模具的结构形式
三、注射模零件分类 1、成型零件 直接与塑料接触,决定塑件形状与精度的零件,模具 的主要部分,如凹模、凸模、型芯等 2、结构零件 不与塑件接触,在模具中起定位、导向、安装、装配 等作用。
4-1 注射模具的结构形式
注射模主要由成型零件、浇注系统、分型与抽芯机构
、导向零件、推出机构、冷却和加热及排气系统等部 分组成。
• 五.结构零件 • 模具的结构零件,主要固定成形零件,使其组成一体的零件。主要包括定
模固定板、动模固定板、垫板及定模套、动模套等。 • 1.定模固定板 固定连接定模部分和安装在注射机上用的板,也是嵌镶浇
座之间有异物,而影响推板回不到最低位置,使塑件难以卸下。
4-1 注射模具的结构形式
注射模主要由成型零件、浇注系统、分型与抽芯机构
、导向零件、推出机构、冷却和加热及排气系统等部 分组成。
• 四.冷却及加热机构 • 冷却及加热机构主要包括冷水嘴、水管通道、加热板等。
主要是为了调节模具的温度,以保证塑件的质量。
• 一.成形零件 • 成形零件安包括定模型腔、动模型腔和型芯等零件。在注塑时,这类
零件直接接触塑料,以成形制品,其精度要求较高,是注射模的核心 零件 • 1.定模型腔 • 定模型腔又称凹模,主要成形塑件的外部形状。 • 2.动模型腔 • 动模型腔又称凸模,主要成形塑件的内部形状。 • 3.型芯 • 型芯一般固定在动模上,主要成形型孔及特殊形状的凹、凸;类塑件。
注射模的工作原理
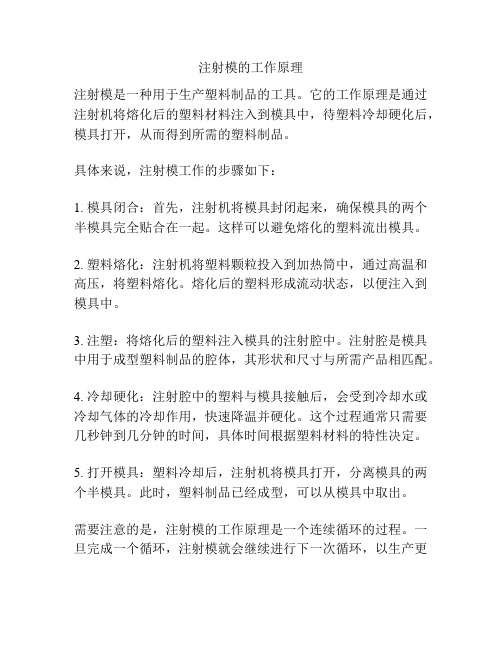
注射模的工作原理
注射模是一种用于生产塑料制品的工具。
它的工作原理是通过注射机将熔化后的塑料材料注入到模具中,待塑料冷却硬化后,模具打开,从而得到所需的塑料制品。
具体来说,注射模工作的步骤如下:
1. 模具闭合:首先,注射机将模具封闭起来,确保模具的两个半模具完全贴合在一起。
这样可以避免熔化的塑料流出模具。
2. 塑料熔化:注射机将塑料颗粒投入到加热筒中,通过高温和高压,将塑料熔化。
熔化后的塑料形成流动状态,以便注入到模具中。
3. 注塑:将熔化后的塑料注入模具的注射腔中。
注射腔是模具中用于成型塑料制品的腔体,其形状和尺寸与所需产品相匹配。
4. 冷却硬化:注射腔中的塑料与模具接触后,会受到冷却水或冷却气体的冷却作用,快速降温并硬化。
这个过程通常只需要几秒钟到几分钟的时间,具体时间根据塑料材料的特性决定。
5. 打开模具:塑料冷却后,注射机将模具打开,分离模具的两个半模具。
此时,塑料制品已经成型,可以从模具中取出。
需要注意的是,注射模的工作原理是一个连续循环的过程。
一旦完成一个循环,注射模就会继续进行下一次循环,以生产更
多的塑料制品。
这种工作原理使得注射模成为了一种高效、快速生产塑料制品的工具。
注射模具工作原理

注射模具工作原理
注射模具是工业生产中常用的一种模具。
其工作原理是:在注塑机中加热并熔化塑料颗粒,然后将高压熔体通过注塑机的喷嘴从注射模具的进气口进入模具腔中,填充模具腔内的空间,然后在高压下让熔体冷却,并保持一定的时间,以确保注塑件形成。
然后将注塑件从模具中推出并进行后续的加工处理。
注射模具的结构包括模芯和模具两部分。
模芯和模具通过注塑机控制系统实现注射过程。
模具内有一些流道和进气口,这些都是为了让熔体顺利地填充到模具内部。
模具的材质一般采用工具钢,以便能够承受高压熔体的压力和高温环境的侵蚀。
注射模具在工业生产中常用于制造塑料制品,如塑料容器、零件等。
- 1、下载文档前请自行甄别文档内容的完整性,平台不提供额外的编辑、内容补充、找答案等附加服务。
- 2、"仅部分预览"的文档,不可在线预览部分如存在完整性等问题,可反馈申请退款(可完整预览的文档不适用该条件!)。
- 3、如文档侵犯您的权益,请联系客服反馈,我们会尽快为您处理(人工客服工作时间:9:00-18:30)。
湖南工业大学课程设计资料袋机械工程学院学院(系、部)2012~2013 学年第 1 学期课程名称注塑成型工艺及模具设计指导教师陈吉平职称教授学生姓名薛开勇专业班级学号题目大口桶盖塑料成型加工及模具成绩起止日期2012 年12 月02 日至2012 年12 月25 日目录清单《塑料成型模具设计》课程设计设计说明书大口桶盖注塑成型工艺与模具设计起止日期:2012 年12 月03 日至2012 年12 月25 日学生姓名班级学号成绩指导教师(签字)机械工程学院- 1 -2012年12 月22 日目录课程设计任务书 1 大口桶盖附图2第1章塑料成型工艺性分析3 1.1塑件分析 3 1.2性能分析 31.2.1成型性能 31.2.2使用性能31.2.3主要性能指标4 1.3注射工艺参数4第2章分型面位置的分析和确定4 2.1分型面的选择原则4 2.2分型面选择方案5第3章塑件型腔数目及排列方式的确定5 3.1型腔数目的确定5 3.2型腔的排列方式5第4章注射机的选择和有关工艺参数的校核6 4.1所需注射量的计算64.1.1塑件质量和体积64.1.2浇注系统凝料体积64.1.3所需总注射量6 4.2塑件和流道凝料在分型面上的投影面积及所需锁模力的计算 6 4.3注射机型号的选择7 4.4有关工艺参数的校核74.4.1按注射机的额定注射量校核型腔数量74.4.2注射量的校核74.4.3塑件在分型面上的投影面积与锁模力的校核84.4.4注射压力的校核84.4.5 安装部分的尺寸校核8 第5章浇注系统的形式选择和截面尺寸的计算105.1主流道的设计10 5.2冷料穴的设计11 5.3浇口设计115.3.1浇口类型及位置的方案选择115.3.2浇口的结构尺寸- 15 -第6章成型零件的设计及力学计算- 15 -6.1成型零件的结构设计12 6.2成型零件工作尺寸计算- 16 -6.3成型零件的强度及支撑板厚度计算- 18 -6.3.1成型壁厚- 18 -- 2 -6.3.2型腔底板厚度- 18 -6.4成型零件的钢材的选用- 19 -第7章模架的确定和标准件的选用- 19 -第8章导向机构的设计- 20 -第9章脱模机构的设计- 20 -9.1脱模机构的设计原则- 20 -9.2塑件的脱模机构- 20 -9.3复位机构及其他机构- 21 -第10章温度调节系统的设计- 21 -10.1加热系统- 21 -10.2冷却系统- 21 -10.2.1冷却介质- 21 -10.2.2冷却系统的简单计算与核验- 21 -第11章排气槽的设计19第12章模具总体结构20第13章设计总结错误!未定义书签。
第14章参考文献错误!未定义书签。
- 3 -湖南工业大学课程设计任务书2011-2012学年第1学期机械工程学院(系、部) 专业材料成型班级材料094班课程名称:塑料成型加工与模具设计题目:大口桶盖注塑成型工艺及模具设计完成期限:自2011年12月12日至2011年12月25日共2周指导教师(签字):________________ 年月日- 4 -- 5 -教研室主任(签字):________________ 年 月 日 大口桶盖附图大桶盖二维图大桶盖三维图技术要求:1、塑件材料为PP(聚丙烯);2、塑件外表要求光滑;3、脱模斜度30′-1°;4、中批量生产;5、未注圆角R1-R2。
第1章塑料成型工艺性分析1.1 塑件分析如图1.1所示,塑件为大口桶盖,塑件材料为PP(聚丙烯),中批量生产。
由图可知,主要尺寸组成:塑件主体是厚度为2.5mm的薄壳体,圆柱侧面均匀分布着12跟R3.5的防滑圆柱,其他圆角为R1-R2,结构简单,便于加工成型。
图1-1 塑件工艺图1.2 性能分析1.2.1 成型性能该塑件材料选用PP(聚丙烯),聚丙烯是由丙烯聚合而制得的一种热塑性树脂,吸湿性小,易发生融体破裂,长期与热金属接触易分解;流动性好,但收缩范围及收缩值大,易发生缩孔、凹痕、变形;冷却速度快,浇注系统及冷却系统应缓慢散热,并注意控制成型温度;料温低温高压时容易取向,模具温度低于50度时,塑件不光滑,易产生熔接不良,流痕,90度以上易发生翘曲变形;塑料壁厚须均匀,避免缺胶,尖角,以防应力集中。
1.2.2 使用性能聚丙烯(PP)是热塑性塑料,耐腐蚀性和聚乙烯相似,且较优。
除浓硝酸、发烟硫酸、氯磺酸等强氧化性酸外,能耐大多数的有机和无机酸、碱、盐,也适于- 6 -在室外大气中暴露(加入2%炭黑的品种)。
对应力腐蚀破裂的抗蚀性良好,但能被某些强有机溶剂破坏。
聚丙烯比重小,强度高于聚乙烯,常温下耐冲击性能良好,0℃以下则变差。
耐温高性,在低于应力下可长期使用于110~120℃,因此,广用于聚乙烯和聚氟乙烯不适用的较高温度的环境。
加工成型方法和一般热塑性塑料相同,可制成管、槽、排烟道、实验室设备等,也可作这热喷或流化涂层。
1.2.3 主要性能指标1.3 注射工艺参数第2章分型面位置的分析和确定2.1分型面的选择原则分型面的选择是否合理对于塑件质量、模具制造与使用性能均有很大影响,它决定了模具的结构类型,是模具设计工作中的重要环节。
模具设计时应根据塑件的结构形状、尺寸精度、浇注系统形式、推出形式、排气方式及制造工艺等多种因素,全面考虑,合理选择。
选择分型面的总原则是保证塑件质量,且便于塑件脱模和简化模具结构,具体映遵循以下原则:- 7 -- 8 -1)分型面的选择应便于塑件脱模和简化模具结构,选择分型面应尽量使塑件开模时留在动模;2)分型面应尽可能选择在不影响外观的部位,并使其产生的溢料边易于消除和修整;3)分型面的选择应保证塑件尺寸精度;4)分型面选择应有利于排气;5)分型面选择应便于模具零件的加工;6)分型面选择应考虑注射机的规格。
7)分型面选择尽可能满足制件的使用要求。
9)分型面选择要有利于保证制品的外观质量。
2.2分型面选择方案由塑件形状及加工要求,可以采用如下图两种分型面方案:方案Ⅰ方案Ⅱ图2-1 分型面方案Ⅰ方案Ⅰ中分型面与开模方向平行,置于最大截面处,塑件包紧在动模型芯上。
利用推出机构易于推出,开模行程合理,模具结构简单,制造方便,塑件成型精度高,能够满足要求;案Ⅱ与方案Ⅰ很类似,但是方案Ⅰ多了一块型腔底板,加大了模具的制造复杂性和成本,所以方案Ⅰ不如方案Ⅱ好。
综上所述,分型面采用方案Ⅱ。
第3章 塑件型腔数目及排列方式的确定3.1型腔数目的确定为了使模具与注射机相匹配以提高生产率和经济性,并保证塑件精度,模具- 9 - 设计时应合理确定型腔数目。
模具型腔数目可选择一模一腔或者一模两腔。
由于该塑件尺寸较大,结构不是很复杂,精度要求较高,再结合经济性,可以确定采用一模一腔的结构。
3.2 型腔的排列方式由于采用的是一模一腔式结构,故排列结构是单一的。
点浇口适用于壳类、盒类塑件,故选用点浇口,模具结构为三板式直浇道推杆推出形式。
第4章 注射机的选择和有关工艺参数的校核注射模是安装在注射机上使用的工艺装备,因此设计注射模是应该详细了解现有注射机的技术规格才能设计出符合要求的模具。
注射机规格的确定主要是依据塑件的大小及型腔的数目和排列方式,在确定模具结构形式及初步估算外形尺寸的前提下,设计人员应对模具所需的注射量,锁模力,注射压力,拉杆间距,最大和最小模具厚度,推出形式,推出位置,开模距离等进行计算。
4.1所需注射量的计算4.1.1塑件质量和体积根据体积公式∑⨯=H S V ,初步算得结果如下:塑件体积:315.102cm V ≈塑件密度:1.04~1.06g/cm 3 ,取3.05g/cm 1=ρ塑件质量: g cm g m V m 28.93/91.0c 5.1023311=⨯==ρ4.1.2浇注系统凝料体积流道凝料的质量(包括浇口)2m 可按塑件质量的0.6倍计算,由于该模具采用一模一腔,所以浇注系统凝料质量为:g m 99.556.0g 28.936.0m 12=⨯=⨯=体积为:33125.616.05.1026.0cm cm V V =⨯=⨯=4.1.3所需总体注射量该模具一次注射所需塑料质量和体积分别为:g m m m m 25.149g 28.936.16.1121=⨯==+=333211645.615.1020cm cm cm V V V =+≈+=4.2塑件和流道凝料在分型面上的投影面积及所需锁模力的计算流道凝料(包括浇口)在分型面上的投影面积为2A ,在模具设计前是个未知数,根据单型腔模的设计分析,塑件在分型面上的投影面积为1A ,2A 是1A 的0.2-0.5倍,因此可用0.351A 来进行计算,故1212135.135.0A A A A A A =+=+=221.207711538635.1mm mm A =⨯=型腔压力:MPa MPa P K P 5.28953.00=⨯=⨯=型式中:K ——压力损耗系数,可在4.0~2.0的范围内选取,此时取0.3; 0P ——为注射压力,为70—120MPa ,取95MPa ;则 KN P A F m 0.592=⨯=4.3注射机型号的选定由上述数据查参考文献【1】附录6选注射机型号为XS-ZY-250,基本参数如下:4.4 有关工艺参数的校核 4.4.1按注射机的额定注射量校核型腔数量222115386414014014.34/mm mm mm d A =⨯⨯==π由参考文献【1】中5-2式可知,n jg V V V n -≤8.0式中:g V —注射机额定注射量 ,3cm ;j V —浇注系统凝料量,3cm ;n V —单个塑件的体积,3cm ;易算得,1≤35.15.10250.61-2508.0333=⨯cm cm cm ,符合条件。
4.4.2注射量的校核模具设计时,必须使得在一个注射成型周期内所需要注射的塑料熔体的容量或质量在注射机额定注射量的80%以内,取最大值为80%,则n j g nV V 80%V +≤式中:g V —注射机允许的最大注射量,3cm ;j V —浇注系统所需塑件的体积,3cm ;n V —单个塑件的体积,3cm 。
则:(102.53cm +61.53cm =1643cm )≤(80%×2503cm =2003cm )故满足要求。
4.4.3塑件在分型面上的投影面积与锁模力的校核计算投影面积与锁模力远小于所选注射机的投影面积和锁模力,故满足要求。
4.4.4注射压力的校核所选注射机额定注射压力为130MPa ,该塑件的注射压力为70-120MPa ,由于选用的是螺杆式注射机,其注射压力的传递比柱塞式要好,PP 的流动性能好,故注射压力选用95MPa ,注射应满足0max kP P ≥式中: max P —注射机额定注射压力;0P —注射成型时所用的注射压力;K —安全系数,常取4.1~25.1=K ,取1.3。