时效与冷处理对热处理变形的影响
热处理常见缺陷分析与对策-学习总结
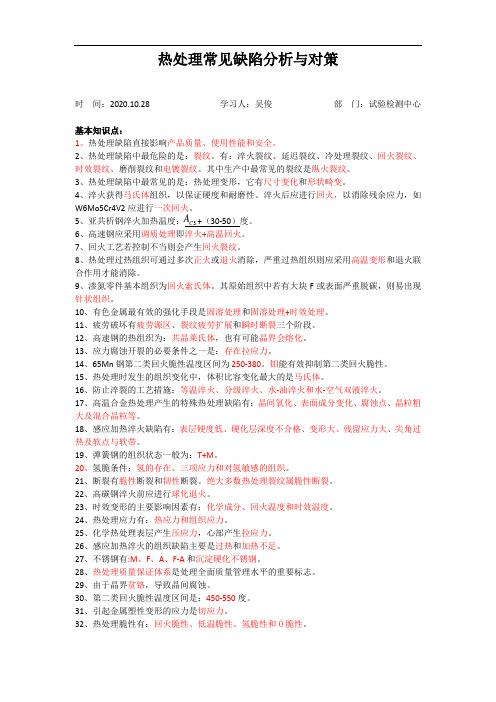
热处理常见缺陷分析与对策时 间:2020.10.28 学习人:吴俊 部 门:试验检测中心基本知识点:1、热处理缺陷直接影响产品质量、使用性能和安全。
2、热处理缺陷中最危险的是:裂纹。
有:淬火裂纹、延迟裂纹、冷处理裂纹、回火裂纹、时效裂纹、磨削裂纹和电镀裂纹。
其中生产中最常见的裂纹是纵火裂纹。
3、热处理缺陷中最常见的是:热处理变形,它有尺寸变化和形状畸变。
4、淬火获得马氏体组织,以保证硬度和耐磨性。
淬火后应进行回火,以消除残余应力,如W6Mo5Cr4V2应进行一次回火。
5、亚共析钢淬火加热温度: +(30-50)度。
6、高速钢应采用调质处理即淬火+高温回火。
7、回火工艺若控制不当则会产生回火裂纹。
8、热处理过热组织可通过多次正火或退火消除,严重过热组织则应采用高温变形和退火联合作用才能消除。
9、渗氮零件基本组织为回火索氏体。
其原始组织中若有大块F 或表面严重脱碳,则易出现针状组织。
10、有色金属最有效的强化手段是固溶处理和固溶处理+时效处理。
11、疲劳破坏有疲劳源区、裂纹疲劳扩展和瞬时断裂三个阶段。
12、高速钢的热组织为:共晶莱氏体,也有可能晶界会熔化。
13、应力腐蚀开裂的必要条件之一是:存在拉应力。
14、65Mn 钢第二类回火脆性温度区间为250-380。
钼能有效抑制第二类回火脆性。
15、热处理时发生的组织变化中,体积比容变化最大的是马氏体。
16、防止淬裂的工艺措施:等温淬火、分级淬火、水-油淬火和水-空气双液淬火。
17、高温合金热处理产生的特殊热处理缺陷有:晶间氧化、表面成分变化、腐蚀点、晶粒粗大及混合晶粒等。
18、感应加热淬火缺陷有:表层硬度低、硬化层深度不合格、变形大、残留应力大、尖角过热及软点与软带。
19、弹簧钢的组织状态一般为:T+M 。
20、氢脆条件:氢的存在、三项应力和对氢敏感的组织。
21、断裂有脆性断裂和韧性断裂。
绝大多数热处理裂纹属脆性断裂。
22、高碳钢淬火前应进行球化退火。
23、时效变形的主要影响因素有:化学成分、回火温度和时效温度。
《金属热处理缺陷分析及案例》完整版

第三章 热处理变形
一、产生原因:热处理应力引起。 二、对质量影响最大:淬火变形。 三、类别:尺寸变化和形状畸变。 四、影响因素: 1、成分(Mn、Cr、Si、Ni、Mo、B等 降低Ms点,减小淬火变形)。 工业上应用:微变形钢(含较多的Si、 W、V等合金元素)。
2、组织和应力状态:
(二)、热处理缺陷分析方法:
1、热处理缺陷的影响:直接影响产品质量、 使用性能和安全,所以准确分析和判断十分 重要。 2、分析方法:断口分析(裂源位置、扩展方 向、断裂性质和方式)、化学分析(材料成分、 沉积物、氧化物)、金相分析(晶粒、组织、 晶界)、力学性能试验(硬度、拉伸、冲出、 疲劳断裂韧度)、验证试验(原工艺和改进工 艺对比)、综合分析(得出缺陷产生的几种主 要原因,提出改进措施)。
第二章、热处理裂纹:
(一)、产生原因:内应力作用下发 生,最终断裂。条件是内应力>脆 断强度。 (二)、断裂类别: 1、裂纹按扩展程度:(失稳)可发 展裂纹、阻断裂纹(不断裂)。 2、断裂:脆性断裂和韧性断裂。多 数为脆性断裂(断口灰亮色)
(三)、加热不当形成的裂纹:
升温速度过快(多出现于灰铸铁、 合金铸铁、高锰钢、高合金钢铸 件)、表面增碳或脱碳[合金钢、低 碳马氏体钢20SiMn2MoV,高锰钢 (Mn13)]、过热或过烧(高速钢、不 锈钢)、氢致裂纹(条件:足够氢、 对氢敏感的金相组织和三向应力。 措施:脱氢、低温回火、自然时效、 低氢淬火)
2、按照危害程度分类:
(1)、第一类热处理缺陷: 最危险缺陷如裂纹,其中最 主要是淬火裂纹,其次加热 裂纹、延迟裂纹、冷处理裂 纹、回火裂纹、时效裂纹、 磨削裂纹和电镀裂纹等。
(2)、第二类热处理缺陷:
材料热处理变形的因素与控制

材料热处理变形的因素与控制摘要:随着金属材料加工与热处理技术的有机融合,不断对材料内部结构进行优化,有效提升材料性能。
,以保证在实际生产中热处理过程的有效应用,对中国的金属行业提升生产能力、提高产品质量的同时,在一定程度上推动相关企业的快速健康的发展。
因此,本文着重解决在对金属材料热加工中影响变形的原因,以及解决办法,以此来提高在金属材料加工当中的难题。
关键词:材料、热处理、变形、因素与控制一、影响金属材料热处理变形的因素1 时效、冷处理冷处理会导致残余奥氏体转变为马氏体,由于金属材料体积变大;低温回火和时效会使金属材料变形两种效应,这是由马氏体的分解造成的,硬质金属材料小;另一种是应力松弛的影响,造成金属材料的变形。
2 原始组织、应力状态①原材料的微观结构会影响金属材料的变形,如碳化物数量、合金元素的形态和偏析、以及纤维的锻造方向。
调理治疗通常是有效的,可以有效降低金属材料的绝对水平变形,淬火变形更多规则和进一步控制目的的变形金属材料。
②化学热处理的主要目的是提高金属材料的表面性能,如提高金属材料表面的氧化性,提高金属表面的耐磨性等。
二、影响材料热处理变形的因素1 温度对热处理造成变形的因素有很多,主要温度为主要影响因素,温度高低、保温时间等都会直接影响热应力以及组织应力形成以及产生的影响,另外,随着温度升高,金属塑形会逐渐增大,导致高温蠕变趋势更加明显,在淬火环节,加热温度主要对金属材料翘曲变形产生影响,对体积变形中所引发的尺寸变化并无明显影响。
因此,需要获得热处理参数的性能指标,同时,要想降低变形,需要对热处理的问温度进行严格测量与控制。
2 结构尺寸对于高碳钢轴类零件以及长轴类零件,在淬透后是马氏体组织,其主要组织应力形变,因此,其体积会有所增大,长度以及直径会有所增强。
合金钢轴类零件有着良好的淬透性,材料变形主要是由热应力以及组织应力共同作用产生,尺寸较小工件的长度与直径均会有所增大,而大尺寸工件的直径会缩小,长度会增大。
热处理对于钢铁材料性能的影响

热处理对于钢铁材料性能的影响热处理是一项重要的工艺,用于改变钢铁材料的性能。
通过控制材料的加热、保温和冷却过程,可以显著改善钢铁材料的力学性能、组织结构和耐腐蚀能力。
本文将深入探讨热处理对于钢铁材料性能的影响。
一、冷处理冷处理是热处理的一种重要方式,其主要目的是通过快速冷却来提高钢铁材料的硬度和强度。
当钢铁材料经过热处理后,快速冷却可以产生细小的晶粒,从而提高材料的硬度。
此外,冷处理还可以减少材料的残余应力,提高材料的耐磨性和疲劳寿命。
二、淬火处理淬火是一种将钢铁材料加热至适宜温度后迅速冷却的热处理方法。
淬火可以使钢铁材料的晶格结构发生变化,从而显著提高材料的硬度和强度。
通过控制淬火工艺参数,如冷却速率、冷却介质等,可以获得不同的硬度和强度。
然而,过快的冷却速率可能导致材料内部产生应力过大,从而引起开裂和变形。
三、回火处理回火是一种将冷处理的材料重新加热至适宜温度后保温一段时间,然后缓慢冷却的热处理方法。
回火可以减轻材料的内部应力,增加其韧性和塑性,降低脆性。
通过合理控制回火温度和时间,可以在硬度和韧性之间取得平衡,使材料具有较好的综合性能。
四、渗碳处理渗碳是一种将含碳气体或液体浸渍到钢铁材料表面,并进行高温处理的方法。
渗碳可以在材料表面形成高碳含量的渗层,从而提高材料的硬度和耐磨性。
此外,渗碳还可以改善材料的耐蚀性能和疲劳寿命。
常用的渗碳方法包括气体渗碳、液体渗碳和离子渗碳等。
五、固溶处理固溶处理是一种通过加热钢铁材料至固溶温度后快速冷却的热处理方法。
固溶处理可以使材料内部的溶质(如碳、氮等)扩散均匀,从而改善材料的强度和塑性。
此外,固溶处理还可以提高钢铁材料的冷加工性能,增加其可塑性。
综上所述,热处理对于钢铁材料性能具有显著的影响。
通过冷处理、淬火处理、回火处理、渗碳处理和固溶处理等方法,可以改善钢铁材料的硬度、强度、耐磨性、耐蚀性和韧性等性能。
因此,在钢铁制造和应用过程中,合理运用热处理技术可以有效提高钢铁材料的综合性能,满足不同工程和应用的需求。
金属材料热处理变形及开裂问题的解决措施
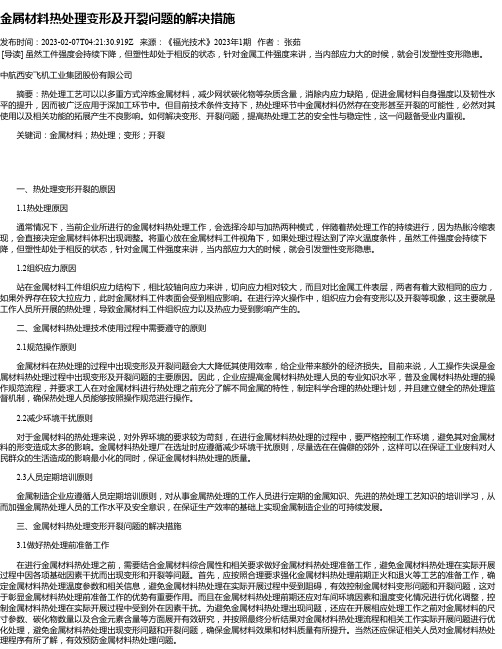
金属材料热处理变形及开裂问题的解决措施发布时间:2023-02-07T04:21:30.919Z 来源:《福光技术》2023年1期作者:张茹[导读] 虽然工件强度会持续下降,但塑性却处于相反的状态,针对金属工件强度来讲,当内部应力大的时候,就会引发塑性变形隐患。
中航西安飞机工业集团股份有限公司摘要:热处理工艺可以以多重方式淬炼金属材料,减少网状碳化物等杂质含量,消除内应力缺陷,促进金属材料自身强度以及韧性水平的提升,因而被广泛应用于深加工环节中。
但目前技术条件支持下,热处理环节中金属材料仍然存在变形甚至开裂的可能性,必然对其使用以及相关功能的拓展产生不良影响。
如何解决变形、开裂问题,提高热处理工艺的安全性与稳定性,这一问题备受业内重视。
关键词:金属材料;热处理;变形;开裂一、热处理变形开裂的原因1.1热处理原因通常情况下,当前企业所进行的金属材料热处理工作,会选择冷却与加热两种模式,伴随着热处理工作的持续进行,因为热胀冷缩表现,会直接决定金属材料体积出现调整。
将重心放在金属材料工件视角下,如果处理过程达到了淬火温度条件,虽然工件强度会持续下降,但塑性却处于相反的状态,针对金属工件强度来讲,当内部应力大的时候,就会引发塑性变形隐患。
1.2组织应力原因站在金属材料工件组织应力结构下,相比较轴向应力来讲,切向应力相对较大,而且对比金属工件表层,两者有着大致相同的应力,如果外界存在较大拉应力,此时金属材料工件表面会受到相应影响。
在进行淬火操作中,组织应力会有变形以及开裂等现象,这主要就是工作人员所开展的热处理,导致金属材料工件组织应力以及热应力受到影响产生的。
二、金属材料热处理技术使用过程中需要遵守的原则2.1规范操作原则金属材料在热处理的过程中出现变形及开裂问题会大大降低其使用效率,给企业带来额外的经济损失。
目前来说,人工操作失误是金属材料热处理过程中出现变形及开裂问题的主要原因。
因此,企业应提高金属材料热处理人员的专业知识水平,普及金属材料热处理的操作规范流程,并要求工人在对金属材料进行热处理之前充分了解不同金属的特性,制定科学合理的热处理计划,并且建立健全的热处理监督机制,确保热处理人员能够按照操作规范进行操作。
钢件热处理变形的原因总结

钢件热处理变形的原因总结
引起热处理变形的因素颇多,总括起来,基本上有三点:
1、固态相变时,各相质量体积的变化必然引起体积的变化,造成零件的胀与缩的尺寸变化;
2、热应力,包括急热热应力和急冷热应力,当它们超过零件在该温度下所具有的屈服极限时,将使零件产生塑性变形,造成零件的形状变化,即歪扭,或称为畸变;
3、组织应力也会引起形状的改变,即畸变。
一般说,淬火工件的变形总是由于以上的两种或三种因素综合作用的结果,但究竟哪一个因素对变形的影响较大,则需要具体情况作具体的分析。
总的来说,体积变化是由相变时比容的改变而引起的。
马氏体的质量体积比钢的其他组成相的质量体积要大,热处理时钢由其他组成相转化为马氏体时,必然引起体积的增加。
而奥氏体的质量体积要比钢的其他组织质量体积要小,在热处理时由其他组成相转变为奥氏体时,则引起体积的减小。
关于形状的变化,歪扭或称为畸变,主要是由于内应力或者外加应力作用的结果。
在加热、冷却过程中,因工件各个部位的温度有差别,相变在时间上有先后,有时发生的组织转变也不一致,而造成内应力。
这种内应力一旦超过了该温度下材料的屈服极限,就产生塑性变形,引起形状的改变。
此外工件内的冷加工残余应力在加热过程中的松弛,以及由于加热时受到较大的外加应力也会引起形状的变化。
在热处理时可能引起体积变化和形状变化的原因见下表。
表中“体积变化原因” 一栏未列入钢因热胀冷缩现象而产生的体积变化,钢由淬火加热温度到零下温度进行冷处理,均随温度的变化而有相应的体积变化,因热胀冷缩而引起的体积变化不均匀乃是热应力产生的原因,而且对变形有相当的影响。
热处理可能引起体积变化和形状变化的原因。
回火、调质、时效与冷处理工艺
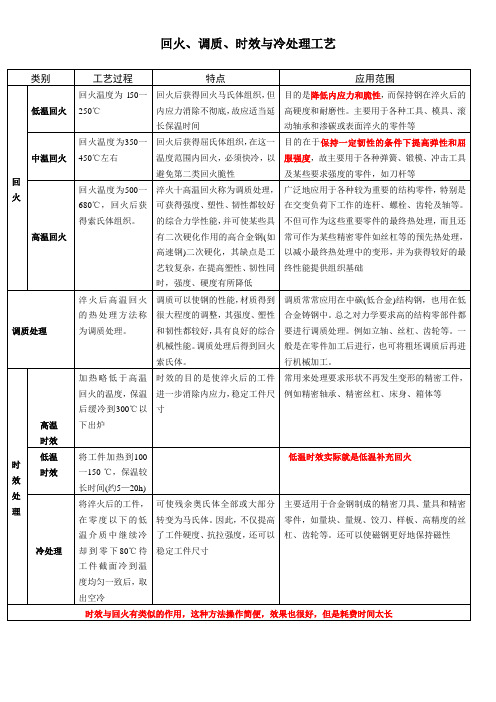
回火、调质、时效与冷处理工艺类别工艺过程特点应用范围回火低温回火回火温度为l50一250℃回火后获得回火马氏体组织,但内应力消除不彻底,故应适当延长保温时间目的是降低内应力和脆性,而保持钢在淬火后的高硬度和耐磨性。
主要用于各种工具、模具、滚动轴承和渗碳或表面淬火的零件等中温回火回火温度为350一450℃左右回火后获得屈氏体组织,在这一温度范围内回火,必须快冷,以避免第二类回火脆性目的在于保持一定韧性的条件下提高弹性和屈服强度,故主要用于各种弹簧、锻模、冲击工具及某些要求强度的零件,如刀杆等高温回火回火温度为500一680℃,回火后获得索氏体组织。
淬火十高温回火称为调质处理,可获得强度、塑性、韧性都较好的综合力学性能,并可使某些具有二次硬化作用的高合金钢(如高速钢)二次硬化,其缺点是工艺较复杂,在提高塑性、韧性同时,强度、硬度有所降低广泛地应用于各种较为重要的结构零件,特别是在交变负荷下工作的连杆、螺栓、齿轮及轴等。
不但可作为这些重要零件的最终热处理,而且还常可作为某些精密零件如丝杠等的预先热处理,以减小最终热处理中的变形,并为获得较好的最终性能提供组织基础调质处理淬火后高温回火的热处理方法称为调质处理。
调质可以使钢的性能,材质得到很大程度的调整,其强度、塑性和韧性都较好,具有良好的综合机械性能。
调质处理后得到回火索氏体。
调质常常应用在中碳(低合金)结构钢,也用在低合金铸钢中。
总之对力学要求高的结构零部件都要进行调质处理。
例如立轴、丝杠、齿轮等。
一般是在零件加工后进行,也可将粗坯调质后再进行机械加工。
时效处理高温时效加热略低于高温回火的温度,保温后缓冷到300℃以下出炉时效的目的是使淬火后的工件进一步消除内应力,稳定工件尺寸常用来处理要求形状不再发生变形的精密工件,例如精密轴承、精密丝杠、床身、箱体等低温时效将工件加热到100一150 ℃,保温较长时间(约5—20h)低温时效实际就是低温补充回火冷处理将淬火后的工件,在零度以下的低温介质中继续冷却到零下80℃待工件截面冷到温度均匀一致后,取出空冷可使残余奥氏体全部或大部分转变为马氏体。
回火、调质、时效与冷处理工艺
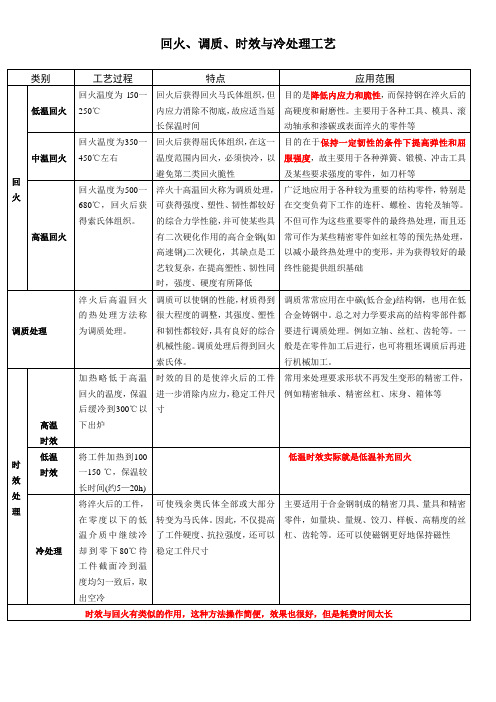
回火、调质、时效与冷处理工艺类别工艺过程特点应用范围回火低温回火回火温度为l50一250℃回火后获得回火马氏体组织,但内应力消除不彻底,故应适当延长保温时间目的是降低内应力和脆性,而保持钢在淬火后的高硬度和耐磨性。
主要用于各种工具、模具、滚动轴承和渗碳或表面淬火的零件等中温回火回火温度为350一450℃左右回火后获得屈氏体组织,在这一温度范围内回火,必须快冷,以避免第二类回火脆性目的在于保持一定韧性的条件下提高弹性和屈服强度,故主要用于各种弹簧、锻模、冲击工具及某些要求强度的零件,如刀杆等高温回火回火温度为500一680℃,回火后获得索氏体组织。
淬火十高温回火称为调质处理,可获得强度、塑性、韧性都较好的综合力学性能,并可使某些具有二次硬化作用的高合金钢(如高速钢)二次硬化,其缺点是工艺较复杂,在提高塑性、韧性同时,强度、硬度有所降低广泛地应用于各种较为重要的结构零件,特别是在交变负荷下工作的连杆、螺栓、齿轮及轴等。
不但可作为这些重要零件的最终热处理,而且还常可作为某些精密零件如丝杠等的预先热处理,以减小最终热处理中的变形,并为获得较好的最终性能提供组织基础调质处理淬火后高温回火的热处理方法称为调质处理。
调质可以使钢的性能,材质得到很大程度的调整,其强度、塑性和韧性都较好,具有良好的综合机械性能。
调质处理后得到回火索氏体。
调质常常应用在中碳(低合金)结构钢,也用在低合金铸钢中。
总之对力学要求高的结构零部件都要进行调质处理。
例如立轴、丝杠、齿轮等。
一般是在零件加工后进行,也可将粗坯调质后再进行机械加工。
时效处理高温时效加热略低于高温回火的温度,保温后缓冷到300℃以下出炉时效的目的是使淬火后的工件进一步消除内应力,稳定工件尺寸常用来处理要求形状不再发生变形的精密工件,例如精密轴承、精密丝杠、床身、箱体等低温时效将工件加热到100一150 ℃,保温较长时间(约5—20h)低温时效实际就是低温补充回火冷处理将淬火后的工件,在零度以下的低温介质中继续冷却到零下80℃待工件截面冷到温度均匀一致后,取出空冷可使残余奥氏体全部或大部分转变为马氏体。
浅谈常见热处理的缺陷及其影响
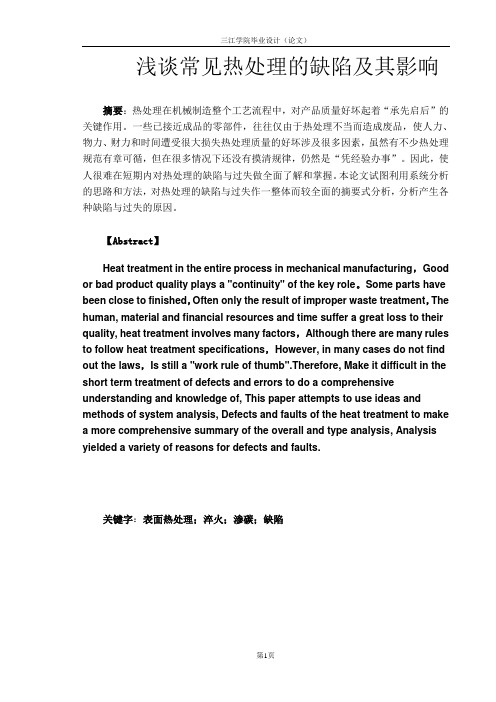
浅谈常见热处理的缺陷及其影响摘要:热处理在机械制造整个工艺流程中,对产品质量好坏起着“承先启后”的关键作用。
一些已接近成品的零部件,往往仅由于热处理不当而造成废品,使人力、物力、财力和时间遭受很大损失热处理质量的好坏涉及很多因素,虽然有不少热处理规范有章可循,但在很多情况下还没有摸清规律,仍然是“凭经验办事”。
因此,使人很难在短期内对热处理的缺陷与过失做全面了解和掌握。
本论文试图利用系统分析的思路和方法,对热处理的缺陷与过失作一整体而较全面的摘要式分析,分析产生各种缺陷与过失的原因。
【Abstract】Heat treatment in the entire process in mechanical manufacturing,Good or bad product quality plays a "continuity" of the key role。
Some parts have been close to finished,Often only the result of improper waste treatment,The human, material and financial resources and time suffer a great loss to their quality, heat treatment involves many factors,Although there are many rules to follow heat treatment specifications,However, in many cases do not find out the laws,Is still a "work rule of thumb".Therefore, Make it difficult in the short term treatment of defects and errors to do a comprehensive understanding and knowledge of, This paper attempts to use ideas and methods of system analysis, Defects and faults of the heat treatment to make a more comprehensive summary of the overall and type analysis, Analysis yielded a variety of reasons for defects and faults.关键字:表面热处理;淬火;渗碳;缺陷目录第1章热处理的缺陷概述 (3)1.1 热处理功能和产生缺陷的原因 (3)1.2 常见几种热处理缺陷 (3)第2章热处理常见缺陷 (5)2.1 过热和过烧 (5)2.2 氧化和脱碳 (5)2.3 变形和开裂 (5)2.3.1 淬火冷却应力 (5)2.3.2 淬火冷却变形 (6)2.3.3 淬火冷却开裂 (6)2.3.4 减少变形、防止开裂措施 (6)第3章典型热处理缺陷分析 (9)3.1 分析裂纹原因及改进措施 (9)3.2 后轴轮断裂原因及改进措施 (9)3.3渗碳件断裂原因及改进措施 (10)第4章总结 (12)参考资料 (13)谢辞 (14)第1章热处理缺陷的概括1.1 热处理功能和产生缺陷的原因热处理可以改善钢的加工工艺性能,改善其热处理可以改善钢的加工工艺性能,改善其使用性能,显著地提高锯的力学性锈,并延长其使使用性能,显著地提高锯的力学性锈,并延长其使用寿命。
浅析金属材料热处理变形问题及开裂问题的解决措施

– 115 –《装备维修技术》2020年第2期(总第176期)doi:10.16648/ki.1005-2917.2020.02.100浅析金属材料热处理变形问题及开裂问题的解决措施陈越伟(南京大驰科技有限公司,江苏 南京 210000)摘要: 工业生产蓬勃发展,带动各行业领域对金属材料需求量的逐步提升,机械设备制造中对其的应用也日益广泛。
热处理工艺技术可实现对金属材料的深加工,在提高材料综合性能方面意义重大,但受多方因素的影响,热处理环节中还存在变形、开裂的可能性,需要予以重视。
文章分析金属材料热处理变形、开裂的影响因素,遵循科学、实用、可操作的基本原则,提出解决变形以及开裂问题的关键措施,仅供参考。
关键词: 金属材料;热处理;变形;开裂热处理工艺可以以多重方式淬炼金属材料,减少网状碳化物等杂质含量,消除内应力缺陷,促进金属材料自身强度以及韧性水平的提升,因而被广泛应用于深加工环节中。
但目前技术条件支持下,热处理环节中金属材料仍然存在变形甚至开裂的可能性,必然对其使用以及相关功能的拓展产生不良影响。
如何解决变形、开裂问题,提高热处理工艺的安全性与稳定性,这一问题备受业内重视。
1. 金属材料热处理变形、开裂影响因素第一是冷处理工艺与时效。
金属材料前期冷处理过程当中有残留奥氏体→马氏体的转化反应,会在一定程度上增加金属材料体积。
同时,受到低温回火工艺及其时效的影响,一方面可能因应力松弛机制导致金属材料产生畸变,另一方面可能因马氏体转化分解以及大量碳化物分解析出导致金属材料体积下降。
第二是原始组织与应力状态。
原始组织对金属材料体积及其完整性的影响集中表现在热处理淬火环节前,主要通过碳化物数量、锻造所致纤维方向、以及合金元素偏析这几种机制实现。
通常可以依赖于调质处理的方式降低金属材料变形量绝对值,使淬火工艺所致材料变形更加规律,以达到合理控制变形的效果。
在此基础之上,化学热处理对改善材料表层性能有重要意义,但受到处理层深度局限的因素影响,为尽可能发挥渗透层作用,在化学热处理基础之上仅可进行磨削加工,进而导致变形矫正的难度增加,控制效果有所折扣[1]。
热处理答案(1)-1-副本

一、名词解释:1热强性:在室温下,钢的力学性能与加载时间无关,但在高温下钢的强度及变形量不但与时间有关,而且与温度有关,这就是耐热钢所谓的热强性。
2形变热处理:是将塑性变形同热处理有机结合在一起,获得形变强化和相变强化综合效果的工艺方法。
3热硬性:热硬性是指钢在较高温度下,仍能保持较高硬度的性能。
4等温淬火:工件淬火加热后,若长期保持在下贝氏体转变区的温度,使之完成奥氏体的等温转变,获得下贝氏体组织,这种淬火称为等温淬火。
5热疲劳:金属材料由于温度梯度循环引起的热应力循环(或热应变循环),而产生的疲劳破坏现象,称为热疲劳。
6渗氮:是在一定温度下一定介质中使氮原子渗入工件表层的化学热处理工艺。
7淬透性:淬透性是使钢强化的基本手段之一,将钢淬火成马氏体,随后回火以提高韧性是使钢获得高综合机械性能的传统方法。
8回火脆性:是指淬火钢回火后出现韧性下降的现象。
9二次硬化:二次硬化:某些铁碳合金(如高速钢)须经多次回火后,才进一步提高其硬度。
10回火稳定性:淬火钢在回火时,抵抗强度、硬度下降的能力称为回火稳定性。
11球化退火:是使钢中碳化物球化而进行的退火,得到在铁素体基体上均匀分布的球状或颗粒状碳化物的组织。
12化学热处理:是利用化学反应、有时兼用物理方法改变钢件表层化学成分及组织结构,以便得到比均质材料更好的技术经济效益的金属热处理工艺。
13淬硬性:指钢在淬火时硬化能力,用淬成马氏体可能得到的最高硬度表示。
14水韧处理:将钢加热至奥氏体区温度(1050-1100℃,视钢中碳化物的细小或粗大而定)并保温一段时间(每25mm壁厚保温1h),使铸态组织中的碳化物基本上都固溶到奥氏体中,然后在水中进行淬火,从而得到单一的奥氏体组织。
.15分级淬火:将钢加热至奥氏体区温度(1050-1100℃,视钢中碳化物的细小或粗大而定)并保温一段时间(每25mm壁厚保温1h),使铸态组织中的碳化物基本上都固溶到奥氏体中,然后在水中进行淬火,从而得到单一的奥氏体组织。
热处理对铸造铝合金材料的导热性能和导电性能的影响
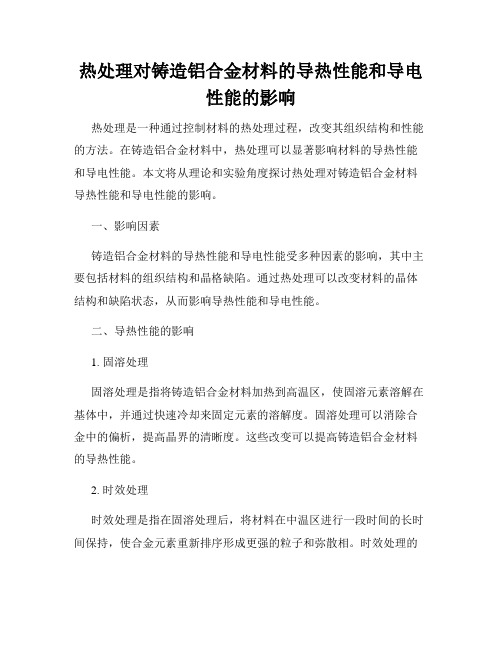
热处理对铸造铝合金材料的导热性能和导电性能的影响热处理是一种通过控制材料的热处理过程,改变其组织结构和性能的方法。
在铸造铝合金材料中,热处理可以显著影响材料的导热性能和导电性能。
本文将从理论和实验角度探讨热处理对铸造铝合金材料导热性能和导电性能的影响。
一、影响因素铸造铝合金材料的导热性能和导电性能受多种因素的影响,其中主要包括材料的组织结构和晶格缺陷。
通过热处理可以改变材料的晶体结构和缺陷状态,从而影响导热性能和导电性能。
二、导热性能的影响1. 固溶处理固溶处理是指将铸造铝合金材料加热到高温区,使固溶元素溶解在基体中,并通过快速冷却来固定元素的溶解度。
固溶处理可以消除合金中的偏析,提高晶界的清晰度。
这些改变可以提高铸造铝合金材料的导热性能。
2. 时效处理时效处理是指在固溶处理后,将材料在中温区进行一段时间的长时间保持,使合金元素重新排序形成更强的粒子和弥散相。
时效处理的主要目的是提高材料的抗变形和抗疲劳性能,同时也会对导热性能产生一定影响。
3. 冷处理冷处理是指将材料在室温下冷却到较低温度,通过相变来改变材料的结构和性能。
在冷处理过程中,晶界会发生位错滑移,从而导致晶格缺陷增多。
这些晶格缺陷会散射导热的电子和声子,从而影响导热性能。
三、导电性能的影响1. 固溶处理与导热性能类似,固溶处理可以提高铸造铝合金材料的导电性能。
这是因为固溶处理可以消除合金中的偏析和析出相,从而提高材料的晶格结构的完整性,减少晶间位错的发生,提高电子的迁移率。
2. 时效处理时效处理对铝合金材料的导电性能影响相对较小。
时效处理主要是通过合金元素的重新排序和粒子的析出来提高材料的强度和硬度,但对导电性能的改善程度有限。
3. 冷处理冷处理会增加晶格缺陷的数量,从而提高晶界的阻抗,影响电子的传输。
因此,冷处理对铝合金材料的导电性能有一定的负面影响。
四、结论热处理可以显著影响铸造铝合金材料的导热性能和导电性能。
固溶处理能够提高导热性能和导电性能,同时时效处理对导热性能和导电性能的影响相对较小。
时效处理——精选推荐
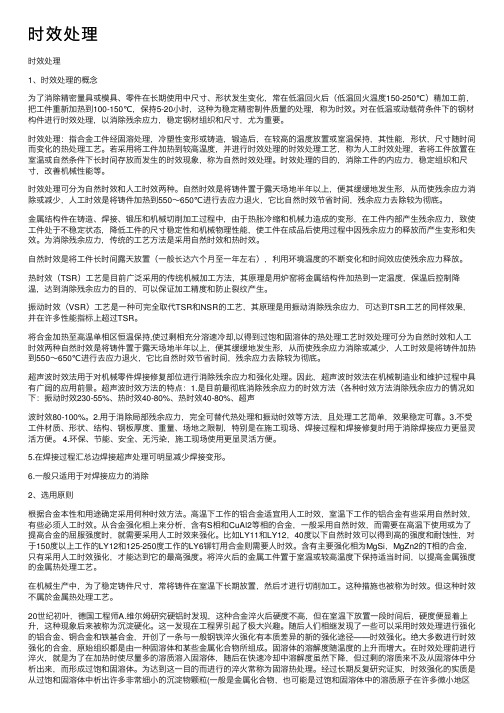
时效处理时效处理1、时效处理的概念为了消除精密量具或模具、零件在长期使⽤中尺⼨、形状发⽣变化,常在低温回⽕后(低温回⽕温度150-250℃)精加⼯前,把⼯件重新加热到100-150℃,保持5-20⼩时,这种为稳定精密制件质量的处理,称为时效。
对在低温或动载荷条件下的钢材构件进⾏时效处理,以消除残余应⼒,稳定钢材组织和尺⼨,尤为重要。
时效处理:指合⾦⼯件经固溶处理,冷塑性变形或铸造,锻造后,在较⾼的温度放置或室温保持,其性能,形状,尺⼨随时间⽽变化的热处理⼯艺。
若采⽤将⼯件加热到较⾼温度,并进⾏时效处理的时效处理⼯艺,称为⼈⼯时效处理,若将⼯件放置在室温或⾃然条件下长时间存放⽽发⽣的时效现象,称为⾃然时效处理。
时效处理的⽬的,消除⼯件的内应⼒,稳定组织和尺⼨,改善机械性能等。
时效处理可分为⾃然时效和⼈⼯时效两种。
⾃然时效是将铸件置于露天场地半年以上,便其缓缓地发⽣形,从⽽使残余应⼒消除或减少,⼈⼯时效是将铸件加热到550~650℃进⾏去应⼒退⽕,它⽐⾃然时效节省时间,残余应⼒去除较为彻底。
⾦属结构件在铸造、焊接、锻压和机械切削加⼯过程中,由于热胀冷缩和机械⼒造成的变形,在⼯件内部产⽣残余应⼒,致使⼯件处于不稳定状态,降低⼯件的尺⼨稳定性和机械物理性能,使⼯件在成品后使⽤过程中因残余应⼒的释放⽽产⽣变形和失效。
为消除残余应⼒,传统的⼯艺⽅法是采⽤⾃然时效和热时效。
⾃然时效是将⼯件长时间露天放置(⼀般长达六个⽉⾄⼀年左右),利⽤环境温度的不断变化和时间效应使残余应⼒释放。
热时效(TSR)⼯艺是⽬前⼴泛采⽤的传统机械加⼯⽅法,其原理是⽤炉窑将⾦属结构件加热到⼀定温度,保温后控制降温,达到消除残余应⼒的⽬的,可以保证加⼯精度和防⽌裂纹产⽣。
振动时效(VSR)⼯艺是⼀种可完全取代TSR和NSR的⼯艺,其原理是⽤振动消除残余应⼒,可达到TSR⼯艺的同样效果,并在许多性能指标上超过TSR。
将合⾦加热⾄⾼温单相区恒温保持,使过剩相充分溶速冷却,以得到过饱和固溶体的热处理⼯艺时效处理可分为⾃然时效和⼈⼯时效两种⾃然时效是将铸件置于露天场地半年以上,便其缓缓地发⽣形,从⽽使残余应⼒消除或减少,⼈⼯时效是将铸件加热到550~650℃进⾏去应⼒退⽕,它⽐⾃然时效节省时间,残余应⼒去除较为彻底。
时效与冷处理对热处理变形的影响
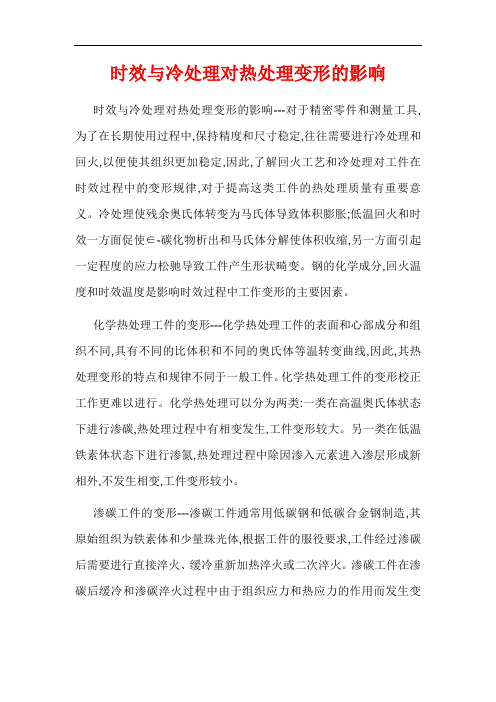
时效与冷处理对热处理变形的影响时效与冷处理对热处理变形的影响---对于精密零件和测量工具,为了在长期使用过程中,保持精度和尺寸稳定,往往需要进行冷处理和回火,以便使其组织更加稳定,因此,了解回火工艺和冷处理对工件在时效过程中的变形规律,对于提高这类工件的热处理质量有重要意义。
冷处理使残余奥氏体转变为马氏体导致体积膨胀;低温回火和时效一方面促使∈-碳化物析出和马氏体分解使体积收缩,另一方面引起一定程度的应力松驰导致工件产生形状畸变。
钢的化学成分,回火温度和时效温度是影响时效过程中工作变形的主要因素。
化学热处理工件的变形---化学热处理工件的表面和心部成分和组织不同,具有不同的比体积和不同的奥氏体等温转变曲线,因此,其热处理变形的特点和规律不同于一般工件。
化学热处理工件的变形校正工作更难以进行。
化学热处理可以分为两类:一类在高温奥氏体状态下进行渗碳,热处理过程中有相变发生,工件变形较大。
另一类在低温铁素体状态下进行渗氮,热处理过程中除因渗入元素进入渗层形成新相外,不发生相变,工件变形较小。
渗碳工件的变形---渗碳工件通常用低碳钢和低碳合金钢制造,其原始组织为铁素体和少量珠光体,根据工件的服役要求,工件经过渗碳后需要进行直接淬火、缓冷重新加热淬火或二次淬火。
渗碳工件在渗碳后缓冷和渗碳淬火过程中由于组织应力和热应力的作用而发生变形,其变形的大小和变形规律取决于渗碳钢的化学成分、渗碳层深度、工件的几何形状和尺寸以及渗碳和渗碳后的热处理工艺参数等因素。
工件按其长度、宽度、高度(厚度)的相对尺寸可以分为细长件、平面件和立方体件。
细长件的长度远大于其横截面尺寸,平面件的长度和宽度远大于其高度(厚度),立方体三个方向的尺寸相差不大。
最大热处理内应力一般总是产生在最大尺寸方向上。
若将该方向称为主导应力方向,则低碳钢和低碳合金钢制造的工件,渗碳后缓冷或空冷心部形成铁素体和珠光体时,一般沿主导应力方向表现为收缩变形,收缩变形率约为0.08-0.14%。
热处理变形原因与变形控制技术措施论文
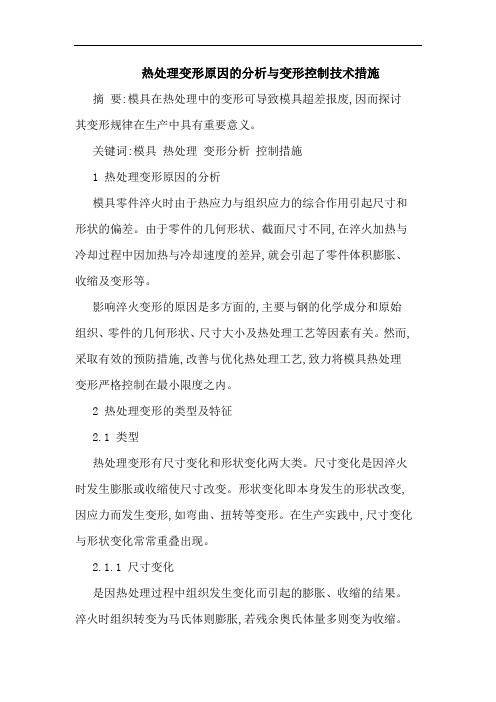
热处理变形原因的分析与变形控制技术措施摘要:模具在热处理中的变形可导致模具超差报废,因而探讨其变形规律在生产中具有重要意义。
关键词:模具热处理变形分析控制措施1 热处理变形原因的分析模具零件淬火时由于热应力与组织应力的综合作用引起尺寸和形状的偏差。
由于零件的几何形状、截面尺寸不同,在淬火加热与冷却过程中因加热与冷却速度的差异,就会引起了零件体积膨胀、收缩及变形等。
影响淬火变形的原因是多方面的,主要与钢的化学成分和原始组织、零件的几何形状、尺寸大小及热处理工艺等因素有关。
然而,采取有效的预防措施,改善与优化热处理工艺,致力将模具热处理变形严格控制在最小限度之内。
2 热处理变形的类型及特征2.1 类型热处理变形有尺寸变化和形状变化两大类。
尺寸变化是因淬火时发生膨胀或收缩使尺寸改变。
形状变化即本身发生的形状改变,因应力而发生变形,如弯曲、扭转等变形。
在生产实践中,尺寸变化与形状变化常常重叠出现。
2.1.1 尺寸变化是因热处理过程中组织发生变化而引起的膨胀、收缩的结果。
淬火时组织转变为马氏体则膨胀,若残余奥氏体量多则变为收缩。
冷处理时因残余奥氏体转变成马氏体又引起膨胀。
马氏体引起的体积膨胀随钢中碳含量增加而变大;其尺寸变化量亦随着增大。
淬火钢回火时马氏体发生分解,而引起收缩;收缩量随马氏体中c%的增多而增大,但若以淬火前的状态为基准,淬火回火后尺寸变化的总合,其结果仍是膨胀。
2.1.2 形状变化是因淬火钢内部的应力及加于外部的力量而引起的。
内部应力是因温度分布不均或因组织转变而引起的。
而外部的力主要是因自重而导致“下垂”。
加热温度越高、保温时间越长,这种因本身重量而引起的“下垂”变形更易发生。
工件加热时,因机械加工或常温加工所产生的残余应力,将发生形状变化。
即使是均匀加热,因钢的屈服点随温度上升而降低之故,此时只要有少许应力存在即发生变形。
因残余应力于外部周围较强。
当温度上升自外部进行时,变形于外部周围特别显著。
金属热处理的方法

调质热处理指的是金属热处理的方法。
将金属在固态范围内通过一定方式的加热、保温和冷却处理程序,使金属的性能和显微组织获得改善或改变,这种工艺方法称为热处理。
根据热处理的目的不同,有不同的热处理方法,主要可分为下述几种:(1)退火(代号Th):在退火热处理炉内,将金属按一定的升温速度加热到临界温度以上300~500℃左右,其显微组织将发生相变或部分相变,例如钢被加热到此温度时,珠光体将转变为奥氏体。
然后保温一段时间,再缓慢冷却(一般为随炉冷却)至室温出炉,这整个过程称为退火处理。
退火的目的是清除热加工时产生的内应力,使金属的显微组织均匀化(得到近似平衡的组织),改善机械性能(例如降低硬度,提高塑性、韧性和强度等),改善切削加工性能等等。
视退火处理工艺的不同,可分为普通退火、双重退火、扩散退火、等温退火、球化退火、再结晶退火、光亮退火、完全退火、不完全退火等多种退火工艺方式。
(2)正火(代号Z):在热处理炉内,将金属按一定的升温速度加热到临界温度以上200~600℃左右,使显微组织全部变成均匀的奥氏体(例如钢在此温度时,铁素体完全转变为奥氏体,或者二次渗碳体完全溶解于奥氏体),保温一段时间,然后置于空气中自然冷却(包括吹风冷却和堆放自然冷却,或者单件在无风空气中自然冷却等多种方法),这整个过程称为正火处理。
正火是退火的一种特殊形式,由于其冷却速度比退火快,能得到较细的晶粒和均匀的组织,使金属的强度和硬度有所提高,具有较好的综合机械性能。
(3)淬火(代号C):在热处理炉内,将金属按一定的升温速度加热到临界温度以上300~500℃左右,使显微组织全部转变成均匀的奥氏体,保温一段时间,然后快速冷却(冷却介质包括水、油、盐水、碱水等等),获得马氏体组织,可显着提高金属的强度、硬度和耐磨性等等。
淬火时的快速冷却导致的急剧组织转变会产生较大的内应力,并使脆性增大,因此必须随后及时进行回火处理或时效处理,以获得高强度与高韧性相配合的性能,一般较少仅仅采用淬火处理的工艺。
金属材料热处理变形的影响因素和策略研究
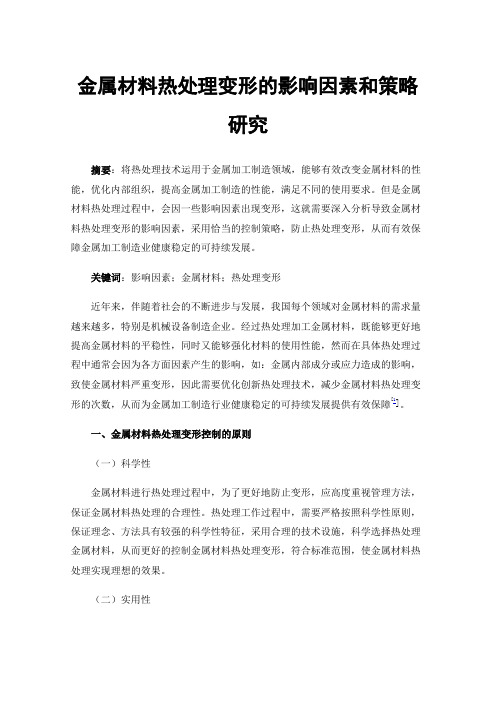
金属材料热处理变形的影响因素和策略研究摘要:将热处理技术运用于金属加工制造领域,能够有效改变金属材料的性能,优化内部组织,提高金属加工制造的性能,满足不同的使用要求。
但是金属材料热处理过程中,会因一些影响因素出现变形,这就需要深入分析导致金属材料热处理变形的影响因素,采用恰当的控制策略,防止热处理变形,从而有效保障金属加工制造业健康稳定的可持续发展。
关键词:影响因素;金属材料;热处理变形近年来,伴随着社会的不断进步与发展,我国每个领域对金属材料的需求量越来越多,特别是机械设备制造企业。
经过热处理加工金属材料,既能够更好地提高金属材料的平稳性,同时又能够强化材料的使用性能,然而在具体热处理过程中通常会因为各方面因素产生的影响,如:金属内部成分或应力造成的影响,致使金属材料严重变形,因此需要优化创新热处理技术,减少金属材料热处理变形的次数,从而为金属加工制造行业健康稳定的可持续发展提供有效保障[1]。
一、金属材料热处理变形控制的原则(一)科学性金属材料进行热处理过程中,为了更好地防止变形,应高度重视管理方法,保证金属材料热处理的合理性。
热处理工作过程中,需要严格按照科学性原则,保证理念、方法具有较强的科学性特征,采用合理的技术设施,科学选择热处理金属材料,从而更好的控制金属材料热处理变形,符合标准范围,使金属材料热处理实现理想的效果。
(二)实用性金属材料不是一种用之不竭的资源,这就需要按照实用性的基本原则使用金属材料,尽量防止金属材料出现浪费的情况。
金属材料热处理过程中,需要有效控制金属材料的变形,实现资源的最大化分配,减少资源,爱护环境,推动社会的长远发展。
另外,按照实用性原则,合理使用金属材料,加强对金属材料质量的控制,全面提升金属材料的使用率。
(三)易操作金属材料进行热处理过程中还需要科学选择操作场地条件,使变形控制精细化和科学化处理的严格要求得到满足。
与此同时,还需要提升变形控制方案的容错率,更好的控制环境因素带来的不良影响。
风电产品主要零部件加工变形的原因及应对方法

风电产品主要零部件加工变形的原因及应对方法发布时间:2023-04-21T03:11:47.272Z 来源:《当代电力文化》2023年第1期作者:马赛[导读] 随着国家对风电的支持,我国风力发电市场快速发展,风力发电技术也不断改善,风电生产商对于产品的质量要求也越来越高。
马赛润阳能源技术有限公司 300000摘要:随着国家对风电的支持,我国风力发电市场快速发展,风力发电技术也不断改善,风电生产商对于产品的质量要求也越来越高。
风电的主要零部件转子、定子、主轴、底座、塔筒等都是铸造而成,这些零部件的共同特征是壁厚相对薄,体积大,加工过程容易变形。
在加工过程中,工件变形一直是难以解决的问题。
工件变形成为机械加工行业工艺设计人员重要的研究课题之一。
本文针对风电主要零部件转子、定子、主轴、底座、塔筒等在加工过程中变形、变形的原因以及应对措施进行分析并加以阐述。
关键词:零部件;工件;风电;变形引言在实际的工业生产加工中,机械零件和设备生产是非常重要的环节,能够对加工工艺的精度产生关键性影响。
由于加工工艺对零件加工精度的影响会受到很多因素的制约,所以不同的加工工艺会对不同的零件加工精度产生不同的影响。
为了提升加工精度,提升机械加工的整体水平,需要不断对机械加工工艺进行探索和创新。
加工精度是指工件加工后的实际几何参数(尺寸、形状和位置)与设计几何参数的符合程度。
为了提升机械零件的可操作性,必须加强对精度的要求,降低或避免各种因素对加工产生的影响。
因此,在实践中要想有效地解决机械加工工艺对零件加工精度的影响,就必须对各种影响因素进行深入分析和探讨。
1机械加工工艺技术概述机械加工工艺技术是指利用传统的机械加工方法进行机械制造,并在制造中结合机械产品尺寸、形状及性质等方面设计的图纸和相关生产技术,形成完整的机械产品的零部件加工。
机械加工工艺技术水平决定了机械加工产品的质量,所以需要机械产业技术人员做好全面的加工工作,减少加工误差的出现,降低机械产业的成本。
2cr13热处理变形

2cr13热处理变形
2Cr13是一种不锈钢材料,通常在制造机械零件和刀具等领域使用。
对于2Cr13的热处理变形,以下是一些常见的方法:
1. 固溶处理:将2Cr13加热到1050℃-1100℃的温度范围,保持一段时间,然后快速冷却。
这样可以使材料中的碳化物完全溶解,提高材料的塑性和韧性。
2. 固溶时效处理:在固溶处理后,将2Cr13再加热到750℃-800℃的温度范围,保持一段时间,然后进行适当的冷却。
这样可以增加材料的硬度和强度。
3. 冷处理:将已经固溶处理和时效处理的2Cr13材料进行冷却处理,可以进一步提高材料的硬度和强度。
需要注意的是,热处理过程中的温度、保温时间和冷却速率等参数需要按照具体材料的要求进行控制,以确保所达到的性能和变形效果满足设计要求。
具体的热处理工艺应根据2Cr13的具体材质和使用要求决定,并在专业人员的指导下进行操作。
- 1、下载文档前请自行甄别文档内容的完整性,平台不提供额外的编辑、内容补充、找答案等附加服务。
- 2、"仅部分预览"的文档,不可在线预览部分如存在完整性等问题,可反馈申请退款(可完整预览的文档不适用该条件!)。
- 3、如文档侵犯您的权益,请联系客服反馈,我们会尽快为您处理(人工客服工作时间:9:00-18:30)。
时效与冷处理对热处理变形的影响---对于精密零件和测量工具,为了在长期使用过程中,保持精度和尺寸稳定,往往需要进行冷处理和回火,以便使其组织更加稳定,因此,了解回火工艺和冷处理对工件在时效过程中的变形规律,对于提高这类工件的热处理质量有重要意义。
冷处理使残余奥氏体转变为马氏体导致体积膨胀;低温回火和时效一方面促使∈-碳化物析出和马氏体分解使体积收缩,另一方面引起一定程度的应力松驰导致工件产生形状畸变。
钢的化学成分,回火温度和时效温度是影响时效过程中工作变形的主要因素。
化学热处理工件的变形---化学热处理工件的表面和心部成分和组织不同,具有不同的比体积和不同的奥氏体等温转变曲线,因此,其热处理变形的特点和规律不同于一般工件。
化学热处理工件的变形校正工作更难以进行。
化学热处理可以分为两类:一类在高温奥氏体状态下进行渗碳,热处理过程中有相变发生,工件变形较大。
另一类在低温铁素体状态下进行渗氮,热处理过程中除因渗入元素进入渗层形成新相外,不发生相变,工件变形较小。
渗碳工件的变形---渗碳工件通常用低碳钢和低碳合金钢制造,其原始组织为铁素体和少量珠光体,根据工件的服役要求,工件经过渗碳后需要进行直接淬火、缓冷重新加热淬火或二次淬火。
渗碳工件在渗碳后缓冷和渗碳淬火过程中由于组织应力和热应力的作用而发生变形,其变形的大小和变形规律取决于渗碳钢的化学成分、渗碳层深度、工件的几何形状和尺寸以及渗碳和渗碳后的热处理工艺参数等因素。
工件按其长度、宽度、高度(厚度)的相对尺寸可以分为细长件、平面件和立方体件。
细长件的长度远大于其横截面尺寸,平面件的长度和宽度远大于其高度(厚度),立方体三个方向的尺寸相差不大。
最大热处理内应力一般总是产生在最大尺寸方向上。
若将该方向称为主导应力方向,则低碳钢和低碳合金钢制造的工件,渗碳后缓冷或空冷心部形成铁素体和珠光体时,一般沿主导应力方向表现为收缩变形,收缩变形率约为0.08-0.14%。
钢的合金元素含量增加、工件的截面尺寸减小时,变形率也随之减小,甚至出现胀大变形。
截面厚度差别较大形状不对称的细长杆件,渗碳空冷后易产生弯曲变形。
弯曲变形的方向取决于材料。
低碳钢渗碳工件冷却快的薄截面一侧多为凹面;而12CrN3A、18CrMnTi等合金元素较高的低碳合金钢渗碳工件,冷却快的薄截面一侧往往为凸面。
低碳钢和低碳合金钢制造的工件经过920-940C温度下渗碳后,渗碳层碳的质量分数增加至0.6-1.0%,渗碳层的高碳奥在体在空冷或缓冷时要过冷至Ar1以下(600C左右)才开始向珠光体转变,而心部的低碳奥氏体在900C左右即开始析出铁素体,剩余的奥氏体过冷至Ar1温度以下也发生共析分解转变为珠光体。
从渗碳温度过冷至Ar1温度,共析成分的渗碳层未发生相变,高碳奥氏体只随着温度的降低而发生热收缩,与此同时,心部低碳奥氏体却因铁素体的析出比体积增大而发生膨胀,结果心部受压缩应力,渗碳层则受拉伸应力。
由于心部发生γ->α转变时,相变应力的作用使其屈服强度降低,导致心部发生压缩变形。
低碳合金钢强度较高,相同条件下心部的压缩塑性变形量较小。
形状不对称的渗碳工件空冷时,冷却快的一侧奥氏体线长度收缩量大于冷却慢的一侧,因而产生弯曲应力,当弯曲应力大于冷即慢的一侧的屈服强度时,则工件向冷却快的一侧弯曲。
对于合金元素含量较高的低碳合金钢,渗碳后表层具有高碳合金钢的成分,空冷时冷却快的一侧发生相变,形成硬度较高、组织比体积较大的新相,而另一侧因冷即较慢形成的新相硬度较低,故出现相反的弯曲变形。
渗碳工件的淬火变形规律可以用相同的方法分折。
渗碳件的淬火温度通常为800-820C,淬火时渗碳层的高碳奥氏体从渗火温度冷却至Ms点温度区间内将发生明显的热收缩;而同时心部低碳奥氏体转变为铁素体和珠光体、低碳贝氏体或低碳马氏体。
不论转变为何种组织,心部都因组织比体积的增大而发生体积膨胀,结果在渗碳层与心部产生较大的内应力。
一般来说,未淬透的情况下,由于心部的相变产物为屈服强度较低的铁素体和珠光体,因而心部在渗碳层热收缩压应力作用下,沿主导应力方向产生收缩变形;当心部的相变产物为强度较高的低碳贝氏体和低碳马氏体对,表层高碳奥氏体则在心部胀应力作用下产生塑性变形,结果主导应力方向而胀大。
随着渗碳钢碳含量和合金元素含量的增加,渗碳件淬火后心部硬度升高,主导应力方向胀大倾向增大。
当心部硬度为28-32HRC时,渗碳工件的淬火变形很小。
随着心部硬度的升高,胀大变形倾向增大。
很明显,提高渗碳件的淬透性等凡导致渗碳工件心部硬度升高的因素,都会增大渗碳工件沿主导应力方向的胀大倾向。
渗氮工件的变形---渗氮能够有效地提高工件表面的硬度和抗疲劳性,并能在一定程度上改善其耐蚀性。
渗氮温度较低,约为510-560C,钢铁材料在渗氮过程中,基本金属不发生相变,因此,渗氮工件变形较小。
渗氮一般是热处理的最后一道工序,工件在渗氮之后,除了高精度的工件还要进行研磨加工外,一般不再进行其他机械加工,因此,渗氮被广泛用来处理要求硬度高而变形小的精密零件。
尽管如此,渗氮工件仍会产生变形。
由于氮原子的渗入,使渗氮层的比体积增大,因此,渗氮工件最常见的变形是工件表面产生膨胀,由于表面渗氮层的胀大受到心部的阻碍,表层受到压应力,心部受拉应力作用。
内应力的大小受零件截面大小、渗氮钢的屈服强度、渗氮层氮浓度及渗氮层深度等因素的影响。
当工件截面尺寸较小,截面形状不对称、炉温和渗氮不均匀时,渗氮工件也会产生尺寸变化或弯曲与翘曲变形等形状畸变。
轴类零件经过渗氮后其变形规律是外径胀大,长度伸长。
径向胀大量通常随工件直径的增大而增艾,但最大胀大量不超过0.055mm。
长度伸长量一般大于径向胀大量,其绝对值随轴的长度增大而增大,但不随轴的长度变化而成比例的变化。
渗氮的套类工件的变形取决于壁厚,壁厚薄时,内外径都趋向于胀大,随着壁厚的增大,胀大量减小,壁厚足够大时,内径有缩小的趋势。
一般情况下,当工件的有效截面尺寸大于50mm时,渗氮处理的主要变形方式是表面膨胀。
但随着工件横截面积的减小,当渗氮层的截面积与心部截面积之比大于0.05小于0.7时,除了表面膨胀外,还必须考虑内应力引起的变形,沿工件主导应力方向的变形量可以用经验公式近似予以估算: ΔL=η(Ν/Κ)%ΔL----主导应力方向长度的增加; η----系数,取决于材料和渗氮工件横截面的形状;Ν------渗氮层的横截面积; Κ----心部的横截面积。
常用渗氮钢的η值工件横截面形状38CrMoALA 40CrNiMo圆形0.3 0.15方形0.4 0.2五>热处理变形的校正热处理变形的校正---工件的热处理变形可以在一定程度上加以控制和减小,但是不能够完全避免。
机械校正法---采用机械或局部加热的方法使变形工件产生局部微量塑性变形,同时伴随着残余内应力的释放和重新分布达到校正变形的目的。
常用的机械校正法有冷压校正、淬火冷却至室温前的热压校正、加压回火校正、使用氧-乙炔火焰或高频对变形工件进行局部加热的”热点”校正、锤击校正等。
机械校正的零件在使用、放置过程中或进行精加工时,由于残余应力的衰减和释放可能部分地恢复原来的变形和产生新的变形。
因此,对于承受高负荷的工件和精密零件,最好不要进行机械校正。
必须进行机械校正时,校正达到的塑性应变应该超过热处理变形的塑性应变,但校正塑性变形量必须控制在很小的范围内,一般应大于弹性极限应变的10倍,小于条件强度极限的十分之一。
校正要尽可能在淬火后应即进行,校正后应进行消除残余应力处理。
热处理变形工件的校正,要求操作者具有熟练的技术并很费工时,因此,校正自动化是热处理工作者的一项重要任务。
热处理校正法---对于因热处理胀大或收缩变形而尺寸超差的工件,可以重新使用适当的热处理方法对其变形进行校正。
常用的热处理校正法有在Ac1温度下加热急冷法对胀大变形的工件进行收缩处理---工件不发生组织比体积变化的相变,因此,不会产生组织应力,只产生因心部和表面热收缩量不同而形成的热应力。
急冷时工件表面急剧收缩对温度较高塑性较好的心部施以压应力,使工件沿主导应力方向产生塑性收缩变形,这是热处理收缩处理的机理。
钢的化学成分不同,其热传导和热膨胀系数不同,在Ac1温度下加热后,钢的塑性和屈服强度也不相同,靠热应力所能达到的塑性收缩变形效果不尽相同,一般碳素钢和低合金钢的收缩效果比较明显,高碳高合金钢的收缩效果则比较差。
收缩处理的加热温度应根据Ac1选择,应保证在水中激冷时不淬硬为原则,对奥氏体稳定性差的碳钢可采用稍高于Ac1的温度,以利用相变温度区的相变超塑性达到最大的收缩效果。
各类钢的加热温度是;碳素钢Ac1—20⌒Ac1+20C 低合金钢Ac1—20⌒Ac1+10C低碳高合金钢(1Cr13 、2Cr13 、18Cr2Ni4W A等) Ac1—30⌒Ac1+10C奥氏体型耐热耐蚀钢850—1000C加热时间应保证工件充分热透,冷却以食盐水激冷为最好。
Ac1温度下加热急冷收缩处理法,可以收缩处理各种不同形状的工件,如环形工件的内孔和外圆,扁方工件的孔、孔距尺寸及外形尺寸,轴类工件的长度以及某些需要局部尺寸收缩的工件等。
淬火胀大法对收缩变形的工件进行胀大处理---主要适用于形状简单的工件。
其原理是利用淬火时工件表层发生马氏体相变时比体积增大,对尚未发生马氏体相变或未淬透的心部施以拉应力,通过心部拉伸塑性变形达到工件沿主导应力方向胀大的目的。
对于低中碳钢和低中碳合金结构钢制造的工件,使用常规淬火加热温度的上限加热水淬时,在工件淬透或半淬透的情况下,可使主导应力方向胀大0.20—0.50%。
形状简单的工件可以左或稍高于Ac1温度下加热正火后,重复淬火1—2次。
CrMn、9CrSi、GCr15、CrWMn等过共析合金工具钢件,在原来未淬透的情况下,可按常规热处理规范的上限加热温度加热,并尽可能淬透或获得较深淬硬层,可使工件沿主导应力方向胀大0.15—0.20%。
淬火后应经240-280C回火,这类钢的淬火胀大变形主要靠淬火时马氏体相变的比体积增大,故胀大变形量有限,并有淬裂的危险。