NBR橡胶的配方设计精选文档
NBR特性配方
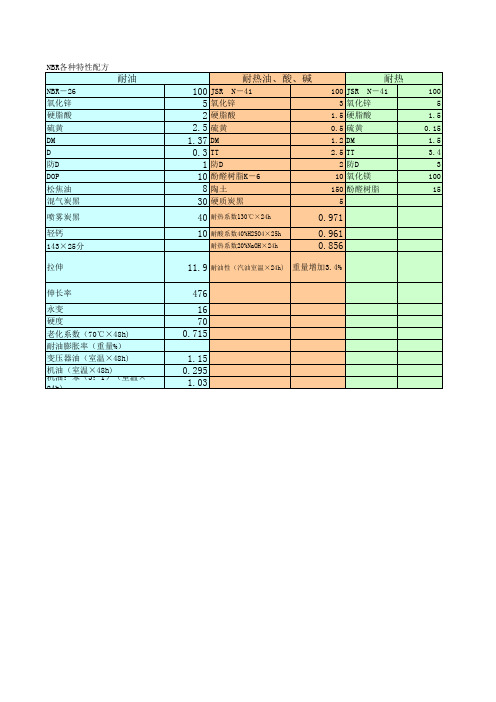
55 液体古马龙
伸长率
240 DOP
15 DOP
5 DOP
永变
0 防A
1.5 醋酸氯乙烯树脂
40 白炭黑
硬度
58 155℃×15分
硫化油膏
老化后100℃× 144h
拉伸
16.6 拉伸
19.6 拉伸
拉伸
13.5 伸长率
540 伸长率
605 伸长率
伸长率
365 弹回率%
49 硬度
74 硬度
脆性温度
—70℃未断 硬度
10 耐酸系数40%H2SO4×25h
耐热系数20%NaOH×24h
0.961 0.856
11.9 耐油性(汽油室温×24h) 重量增加3.4%
476
16 70 0.715
1.15 0.295 1.03
100 5
1.5 0.15
1.5 3.4
3 100
15
耐寒
低压缩变形
耐磨耐屈挠
低硬度
NBR-18
5 氧化锌 2 硬脂酸 2.5 硫黄 1.37 DM 0.3 TT 1 防D 10 酚醛树脂K-6 8 陶土 30 硬质炭黑
耐热
100 JSR N-41 3 氧化锌
1.5 硬脂酸 0.5 硫黄 1.2 DM 2.5 TT
2 防D 10 氧化镁 150 酚醛树脂
5
40 耐热系数130℃×24h
0.971
—45℃耐寒系数
0.83
压缩形变100 ℃×70h %
60 永变 12 磨耗cm3/1.61km
在ATSM3号 20 油中重量变
化%
0.1553
低硬度
高硬度
100 Chemigum N-6 5 氧化锌 1Βιβλιοθήκη 硬脂酸2.5 硫黄 1 DM
橡胶配方设计整理
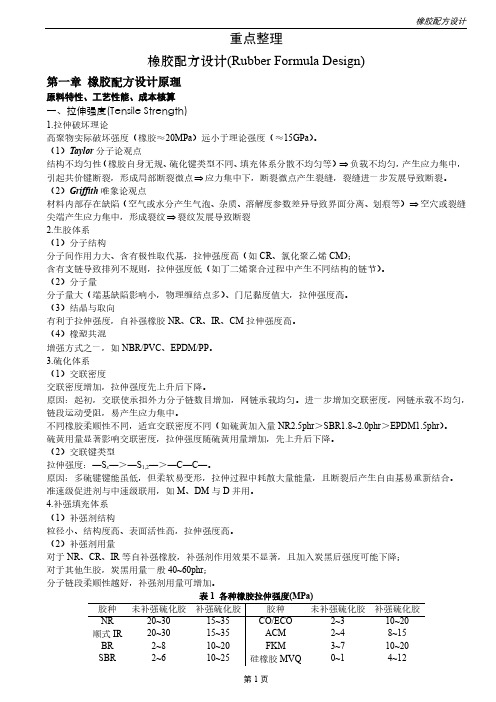
重点整理橡胶配方设计(Rubber Formula Design)第一章橡胶配方设计原理原料特性、工艺性能、成本核算一、拉伸强度(Tensile Strength)1.拉伸破坏理论高聚物实际破坏强度(橡胶≈20MPa)远小于理论强度(≈15GPa)。
(1)Taylor分子论观点结构不均匀性(橡胶自身无规、硫化键类型不同、填充体系分散不均匀等)⇒负载不均匀,产生应力集中,引起共价键断裂,形成局部断裂微点⇒应力集中下,断裂微点产生裂缝,裂缝进一步发展导致断裂。
(2)Griffith唯象论观点材料内部存在缺陷(空气或水分产生气泡、杂质、溶解度参数差异导致界面分离、划痕等)⇒空穴或裂缝尖端产生应力集中,形成裂纹⇒裂纹发展导致断裂2.生胶体系(1)分子结构分子间作用力大、含有极性取代基,拉伸强度高(如CR、氯化聚乙烯CM);含有支链导致排列不规则,拉伸强度低(如丁二烯聚合过程中产生不同结构的链节)。
(2)分子量分子量大(端基缺陷影响小,物理缠结点多)、门尼黏度值大,拉伸强度高。
(3)结晶与取向有利于拉伸强度,自补强橡胶NR、CR、IR、CM拉伸强度高。
(4)橡塑共混增强方式之一,如NBR/PVC、EPDM/PP。
3.硫化体系(1)交联密度交联密度增加,拉伸强度先上升后下降。
原因:起初,交联使承担外力分子链数目增加,网链承载均匀。
进一步增加交联密度,网链承载不均匀,链段运动受阻,易产生应力集中。
不同橡胶柔顺性不同,适宜交联密度不同(如硫黄加入量NR2.5phr>SBR1.8~2.0phr>EPDM1.5phr)。
硫黄用量显著影响交联密度,拉伸强度随硫黄用量增加,先上升后下降。
(2)交联键类型拉伸强度:—S x—>—S1,2—>—C—C—。
原因:多硫键键能虽低,但柔软易变形,拉伸过程中耗散大量能量,且断裂后产生自由基易重新结合。
准速级促进剂与中速级联用,如M、DM与D并用。
4.补强填充体系(1)补强剂结构粒径小、结构度高、表面活性高,拉伸强度高。
丁晴橡胶配方设计

TT 固化后呈半凝固态,对许多基材的粘附性和密封 性能良好,具有极优的抗冷热交变性能; 可通过改变温 度来控制凝胶时间,便于生产线操作; 固化过程中无副 产物产生,无收缩,无内应力;具有优异的电气绝缘性 能和耐高低温性能(-60℃~260℃); 凝胶受外力开裂后 可以自动愈合,同样起到防水、防潮的作用,不影响使 用效果; 具有优良的耐水、耐臭氧、耐电弧、耐气候老 化、收缩率小、防震、硫化后长期使用; 不需要任何底 涂处理就可以对绝大多数材料形成良好的粘接防D 2
最佳的配方
一个好的配方应该是充分发挥本厂生产设备的最佳能力, 同时它是型材良好的质量和最佳的经济效益的三结合。
具体配方设计
丁晴橡胶配方及其作用 JSR N-41 100 氧化锌 氧化锌在橡胶中起促进助剂的作用,提高硫化效 率,使用量约为2~5%。 硬脂酸 硬脂酸在橡胶应用中归属于硫化活性剂,又称助促进 剂!它的作用是加入橡胶中参与硫化反映过程,提高促进剂的活 性,是促进剂进一步充分发挥其最大的促进作用!在生产合成橡 胶过程中需加硬脂酸作乳化剂,在制造泡沫橡胶时,硬脂酸可作 起泡剂,硬脂酸还可用作橡胶制品的脱模剂。 一般胶料中硬脂酸于氧化锌合用!除了与氧化锌合用作为活 性剂以外,在胶料中也同时起到软化剂的作用,能使炭黑在胶料 中分散均匀!
其中材料作用 DM 起到增塑剂或延迟剂的作用。可产生平坦和中 速流化,硫化温度较高,有显著的后效性,不会早期硫 化,操作安全,易分散,不污染,硫化胶耐老化。本品 单独使用硫化速度慢,通常都与秋兰姆、二硫代氨基甲 酸盐、醛胺类、胍类促进剂并用,是G型氯丁胶的优良 抗焦烧剂。主要用于制造轮胎、胶管、胶鞋、胶布等般 工业品。在氯丁胶中还可以起到增塑剂或延迟剂的作用。
(一)对制品性能要求的了解
橡胶配方大全范文

橡胶配方大全范文1.天然橡胶配方:-天然橡胶:100份-硫磺:2份-罗塞林:5份-碳黑:50份-橡胶软化剂:5份-稳定剂:1份2.丁苯橡胶配方:-丁苯橡胶:100份-碳黑:40份-硫磺:2份-弹性体:5份-稳定剂:1份-硬质填料:10份3.丁羟橡胶配方:-丁羟橡胶:100份-碳黑:40份-硫磺:2份-粘度调节剂:5份-稳定剂:1份4.乙酸乙烯橡胶配方:-乙酸乙烯橡胶:100份-碳黑:50份-硫磺:2份-塑化剂:5份-硬质填料:10份-稳定剂:1份5.氯丁橡胶配方:-氯丁橡胶:100份-碳黑:40份-硫磺:2份-塑化剂:5份-稳定剂:1份-硬质填料:10份6.氟橡胶配方:-氟橡胶:100份-硫磺:2份-塑化剂:5份-硬质填料:10份-稳定剂:1份以上是几种常见的橡胶配方,其中的各种原料按比例混合,然后进行橡胶化反应。
这些配方可以根据具体的应用要求进行调整和改善,以满足不同领域对橡胶材料性能的需求。
在混合橡胶配方时需要注意以下几点:1.原料的质量:保证配方中的各种原料质量良好,以确保橡胶制品的性能。
2.混合均匀:混合原料时需要确保均匀混合,以避免出现局部性能差异。
3.适当调整配方:根据具体应用要求,可以适当调整配方中各种原料的比例,以获得更优异的性能。
4.工艺条件控制:橡胶化反应需要在一定的工艺条件下进行,如温度、时间等,需要严格控制这些条件,以保证反应的成功。
通过合理的配方设计和优化,可以制备出满足不同应用领域需求的橡胶制品,提供更好的性能和可靠性。
以上仅是几种常见的橡胶配方,实际应用中还需根据具体的要求进行细化和改进。
希望以上内容能对您有所帮助。
橡胶配方资料大全(doc 25页)

合计161 100.00 100.00 80.5 天然橡胶(NR)基础配方原材料名称NBC标准试样编号质量份原材料名称NBC标准试样编号质量份NR 氧化锌硬脂酸—37037210052防老剂PBN促进剂DM硫磺377373371112.5注:硫化时间为140℃×10min,20min,40min,80min。
NBS为美国国家标准局编写丁苯橡胶(SBR)基础配方原材料名称NBC标准试样编号非充油SBR配方充油SBR配方充油量25phr充油量37.5phr充油量50phr充油量62.5phr充油量75phr非充油SBR 充油SBR氧化锌硬脂酸硫磺炉法炭黑促进剂NS ——370372371378384100—311.75501—1253.751.252.1962.501.25—137.54.121.382.4268.751.38—1504.51.52.63751.5—162.54.881.632.8581.251.63—1755.251.753.0687.51.75Phr指每百质量份橡胶的分量数注:硫化时间为145℃×25min,35min,50min 氯丁橡胶(CR)基础配方原材料名称NBC标准试样编号纯胶配方半补强炉黑(SRF)配方CR(W型) 氧化镁硬脂酸SRF氧化锌—37637238237010040.5—510041295促进剂NA-22 防老剂D —3770.3520.52注:硫化时间为150℃×15min,30min,60min 丁基橡胶(IIR)基础配方原材料名称NBC标准试样编号纯胶配方槽黑配方高耐磨炭黑(HAF)配方IIR氧化锌硫磺硬脂酸促进剂DM 促进剂TMTD 槽发炭黑HAF —37037137237337437537810052——1——1005230.5150—10031.751—1—50注:硫化时间为150℃×20min,40min,80min;150℃×25min,50min,100min丁腈橡胶(NBR)基础配方原材料名称NBC标准试样编号瓦斯炭黑配方NBR氧化锌硬脂酸硫磺促进剂DM 瓦斯炭黑—370372371373382100511.5140注:硫化时间为150℃×10min,20min,80min顺丁橡胶(BR)基础配方原材料名称NBC标准试样编号HAF配方BR氧化锌硫磺硬脂酸促进剂NS —37037137238410031.520.9HAF ASTM型103油378—6015注:硫化时间为145℃×25min,35min,50min异戊橡胶(IR)基础配方原材料名称NBC标准试样编号HAF配方IR氧化锌硫磺硬脂酸促进剂NSHAF —37037137238437810052.2520.735注:硫化时间为15℃×20min,30min,40min,60min。
橡胶配方设计第二章

支链导致排列不规则 (4) 结晶与取向对Tensile的影响
如NR 、CR、IR自补强(应力诱导结晶 (5) 橡塑共混 NBR/PVC EPDM/PP
PPT文档演模板
橡胶配方设计第二章
PPT文档演模板
橡胶配方设计第二章
2、补强填充体系与耐磨性
(1)粒径小,活性大,结构度高,比表面积大, 耐磨性好
(2)用量 NR和SBR中 50~60phr CB BR中 60~70phr CB
资料介绍:不良路面,轮胎胶料中加入15phr 白炭黑,可提高耐磨性。
1) 减少胎面花纹掉块(相当于提高耐老化性) 2) 应用硅烷偶联剂及其他表面活性剂改性
PPT文档演模板
橡胶配方设计第二章
3、硫化体系
(1)交联类型 一般情况考虑,C-SX-C>C-S-C>C-C 具体到轮胎:生成单硫键可提高轮胎在光滑路面 上的耐磨性。 油封:采用过氧化物交联形成C-C键好。 (2)交联密度:交互作用
粒径小的CB交联密度小好 粒径大的CB交联密度大好
PPT文档演模板
密度(g/cm3) 硬度(邵A)
PPT文档演模板
1.115 1.095 1.103 1.067 1.115 1.164 1.192
72 76 78 81 72 77 83
橡胶配方设计第二章
经验公式
•配合剂种类
硬度变化
ISAF
+用量 ×3/5
SAF、气相法白炭黑 +用量 ×3/5
FEF、HAF、EPC +用量 ×1/2
•
PPT文档演模板
•硫化胶实际强度为20MPa左右
橡胶配方设计第三章
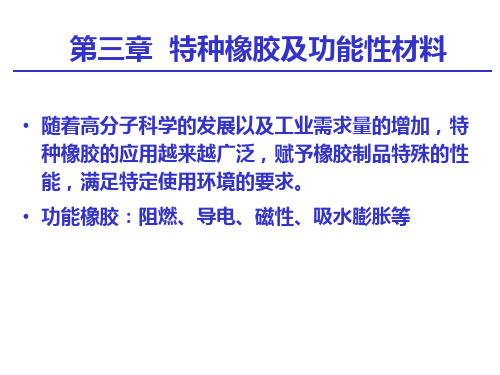
Heat Resistance oC
H 250 G 225
FPM FMVQ
MVQ
F 200 E 175 D 150 C 125 B 100 A 70
ACM
44%ACN HNBR
80%VA 34%ACN
40%VA EVM
CO/ECO 48%ACN
NBR
PU
CM/CSM 18%ACN
CR
SBR
EPDM IIR
BR NR
10 20 30 40 60 80 100 120 140 No
Classification of Elastomers according to Maximum Volume Change(%) in ASTM Oil 3#
(二)配合体系:
NBR 100
(1)硫化体系尽可能提高交联密度。
加大交联密度,提高定伸应力 CR CSM 用金属氧化物交联,PbO代替MgO IIR 采用树脂或醌肟效果好
各种橡胶耐H2SO4性能
编号
橡胶 H2SO4体积分数(%) 时间(d)
变化
1
FKM-23
2
EPDM
3
IIR
4
NBR
5
SBR
6
CR
7
CSM
8
EPDM
9
EPDM
10
IIR
发烟 发烟(62) 发烟(62) 发烟(62) 发烟(62) 发烟(62)
癸二酸酯和邻苯二甲酸酯凝固点低的软化剂降低tg四填料少用或不用选用软质或球形填料各种增塑剂对nbr耐寒性的影响增塑剂脆性温度t增塑剂脆性温度t空白邻苯二甲酸二辛酯邻苯二甲酸二丁酯邻苯二甲酸丁基月桂酯邻苯二甲酸丁基苄酯磷酸三苯甲酯2953753754237295磷酸三苯酯己二酸二辛酯液体古马隆30434474936527525与指定温度下的形变值之比来表示耐寒系数k为
丁腈橡胶密封件配方
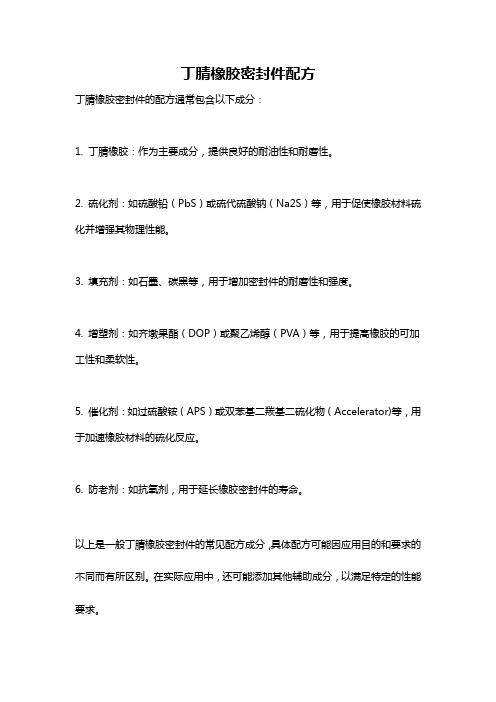
丁腈橡胶密封件配方
丁腈橡胶密封件的配方通常包含以下成分:
1. 丁腈橡胶:作为主要成分,提供良好的耐油性和耐磨性。
2. 硫化剂:如硫酸铅(PbS)或硫代硫酸钠(Na2S)等,用于促使橡胶材料硫化并增强其物理性能。
3. 填充剂:如石墨、碳黑等,用于增加密封件的耐磨性和强度。
4. 增塑剂:如齐墩果酯(DOP)或聚乙烯醇(PVA)等,用于提高橡胶的可加工性和柔软性。
5. 催化剂:如过硫酸铵(APS)或双苯基二羰基二硫化物(Accelerator)等,用于加速橡胶材料的硫化反应。
6. 防老剂:如抗氧剂,用于延长橡胶密封件的寿命。
以上是一般丁腈橡胶密封件的常见配方成分,具体配方可能因应用目的和要求的不同而有所区别。
在实际应用中,还可能添加其他辅助成分,以满足特定的性能要求。
抗静电丁腈橡胶配方
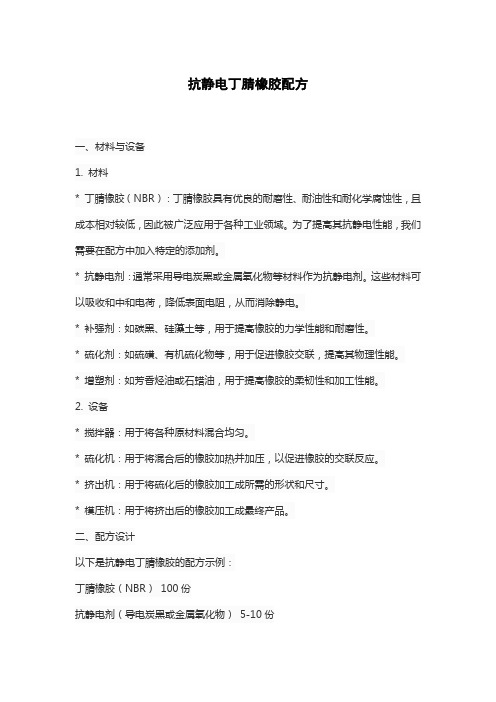
抗静电丁腈橡胶配方一、材料与设备1. 材料* 丁腈橡胶(NBR):丁腈橡胶具有优良的耐磨性、耐油性和耐化学腐蚀性,且成本相对较低,因此被广泛应用于各种工业领域。
为了提高其抗静电性能,我们需要在配方中加入特定的添加剂。
* 抗静电剂:通常采用导电炭黑或金属氧化物等材料作为抗静电剂。
这些材料可以吸收和中和电荷,降低表面电阻,从而消除静电。
* 补强剂:如碳黑、硅藻土等,用于提高橡胶的力学性能和耐磨性。
* 硫化剂:如硫磺、有机硫化物等,用于促进橡胶交联,提高其物理性能。
* 增塑剂:如芳香烃油或石蜡油,用于提高橡胶的柔韧性和加工性能。
2. 设备* 搅拌器:用于将各种原材料混合均匀。
* 硫化机:用于将混合后的橡胶加热并加压,以促进橡胶的交联反应。
* 挤出机:用于将硫化后的橡胶加工成所需的形状和尺寸。
* 模压机:用于将挤出后的橡胶加工成最终产品。
二、配方设计以下是抗静电丁腈橡胶的配方示例:丁腈橡胶(NBR)100份抗静电剂(导电炭黑或金属氧化物)5-10份补强剂(碳黑或硅藻土)30-50份硫化剂(硫磺或有机硫化物)2-5份增塑剂(芳香烃油或石蜡油)10-20份三、制备过程1. 将丁腈橡胶和各种添加剂按照上述配方比例准备齐全。
2. 使用搅拌器将所有原材料混合均匀,确保无颗粒状物质。
3. 将混合后的橡胶放入硫化机中加热并加压,以促进橡胶的交联反应。
4. 将硫化后的橡胶使用挤出机加工成所需的形状和尺寸。
5. 最后使用模压机将挤出后的橡胶加工成最终产品。
四、性能测试与优化1. 使用表面电阻测试仪测试产品的表面电阻,确认其是否达到预期的抗静电性能。
2. 根据测试结果对配方进行调整,如增加抗静电剂的用量或更换不同的抗静电剂,以达到最佳的抗静电效果。
3. 对优化后的配方进行重复制备和性能测试,以确保产品的性能稳定且符合预期要求。
丁腈橡胶配方技术

的污染 性 , 为污染 、 分 微污染 和无 污染 型胶种 。
( )所 用 第 三 单 体 及 其 种 类 5 三 单 体 的 NB 品 种 R 市 售 品 有
使用 二 乙烯基 苯 、 甲基 丙 烯酸 、 烯酸 作 为第 丙 ( )聚合 物状态 6 ( )井 用 聚台 物 7 一般 为块 状 ( 包 ) 也 胶 , 有 与 氯 乙烯并 用释 为
NB 的耐 热 性 比天然 橡胶 、 R 丁苯 橡胶 等
通 用橡胶 和氯 丁橡胶 好 。图 4为与 特种 橡胶
相 比对于 温度 和油 的使 用 范围 。 但是 , 一使 这
用范 围因 硫化体 系 和丙 烯腈 含量 的不 同而有
差异 。
使 用 时 间的 关 系 ( 6 , 图 ) 以作 为 评 价 橡 胶 密
田6 B N R尊 睦压鲭永久壹形保持 5 的 0 使 用噩崖与使用寿命的关 系
l一 婚 畦膏 糠 腔 ・一 丁 睛 椽 眭 , _丙 2 3 氯 丁椽 胶 |- 氯 鞋 橡胶 一 4
田 7 不 同丙 螺腑含量 N R的耐油性 与 B
耐 寒 性 的 美 系
冲击臆 性温度试 验 、 低温 屈挠试 验 、 低温压 缩 试 验 、 R 试 验 等 , 根 据 需 要 选 择符 合 实 T— 可
方 面 分类 : ( )丙 烯 腈 含 量 1 市 售 NB 的 丙 烯 腈 R
定 伸 应 力一 拉 伸 强 度一
硬 一
太 太
耐 磨 耗 性一
永久变形一 耐 性一
好
太 好
耐热性一 与 极性 聚 合 蛔 姻 相 蒋 性一
^一 日
好 太
含 量 约 在 1 ~ 5 的 范 围 。 5 0
橡胶配方设计综合实验
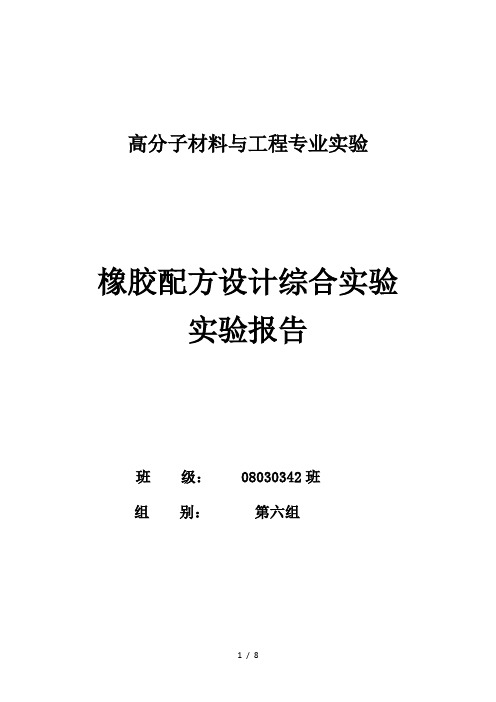
高分子材料与工程专业实验橡胶配方设计综合实验实验报告班级: 08030342班组别:第六组橡胶配方设计综合实验一、实验目的1、加深对丁腈橡胶的配方、各组分的作用原理及加工方法的认识。
2、进一步领会橡胶的塑炼、混炼的意义和原理。
3、进一步了解橡胶的硫化模压成型的基本方法,掌握塑炼混炼、压制硫化设备的操作方法及安全措施。
4、掌握炭黑的含量对橡胶力学性能的影响规律。
5、掌握数据处理和分析的方法。
二、实验原理丁腈橡胶制品的生产,首先有一个配料的问题,即在丁腈橡胶(生胶)中加入一定量的硫化剂、补强剂、增塑剂、防老剂等其他助剂,使之形成多组分体系。
本实验固定其他组分的含量,改变炭黑的用量,研究炭黑的含量对橡胶力学性能的影响。
在一定的温度下,首先塑炼丁腈橡胶,再将配好的实验原理进行混炼使各种助剂实现良好的分散,通过辊压成片,剪成一定形状的胶料,放入试样模具中,经过硫化成型成为所需的试样。
通过不同规格的裁刀,冲裁成性能测试的样品。
然后测试橡胶的拉伸强度、撕裂强度和硬度。
找出炭黑含量对橡胶力学性能的影响规律。
三、实验所用原料及仪器、设备1、实验用的原材料及参考配方2(1)开放式炼塑机(SK-160B)辊筒工作直径=160mm,辊筒工作长度=320mm,前辊转速=24.0r.p.m,后辊转速=17.8r.p.m,最大辊间距=4.5mm,最小压片厚度=0.2mm。
一次加料量=100~200g,辊筒最高加热温度≤200℃(2)平板硫化机(XKLB-25D)额定表压=145kg/cm²,油缸活塞直径D=160mm,电热板面积=360*360mm,模板最大加热温度≤200℃。
(3)密炼机混炼设备(HL-200型)(4)橡胶硬度计(5)万能拉伸测试仪四、实验工艺条件的预定1、材料配方的确定一五2、塑炼工艺条件的确定塑炼温度: 80℃。
塑炼时间:5min3、混炼工艺条件的确定加料顺序:固体软化剂(石蜡、硬脂酸)、小药(促进剂、活化剂、防老剂)、补强剂(炭黑、碳酸钙)液体软化剂。
nbr密封圈材料成分

NBR密封圈的材料是丁腈橡胶(NBR)和三元乙丙橡胶(EPDM)的混合物,具体成分包括丁二烯、丙烯腈和三元乙丙橡胶。
丁腈橡胶是由丁二烯聚合而成的单组分、无溶剂型橡胶,它与一般硫磺硫化体系不相适应,需要用活性较大的氧化锌、氧化镁作硫化辅助材料,硫化胶性能较硬,具有优良的耐油性和耐热性,适用于制作耐油橡胶制品如密封件(油封)、导轨密封件(轴封)和耐高、低温材料等。
三元乙丙橡胶是由乙烯、丙烯经乳液聚合而成的无侧链的单组分或双组分胶料,能在120℃下长期使用,在150℃下短期或间歇使用,并且具有优良的耐臭氧性、耐热性、耐候性、耐酸碱、耐寒性,但抗冲击性较差。
为了提高三元乙丙橡胶的性能和加工性能,通常需要添加各种配合剂,如硫磺、促进剂、防老剂等,以提高其耐热性、耐候性、弹性和抗冲击性等。
当这两种材料按照一定比例混合制备成NBR密封圈时,可充分发挥各自的优点,制成的密封件具有优良的密封性能和机械性能。
这种材料制成的密封件可用于各种环境中起到密封作用,防止液体、气体或蒸气的泄漏,也可用于减震和吸收噪音。
需要注意的是,NBR密封圈的材料成分可能会因生产厂家不同而有所差异,具体成分需要参考相关资料或咨询厂家。
丁腈橡胶配方技术(三)

丁腈橡胶配方技术(三)
三.NBR的耐热性
NBR 的耐热性比天然橡胶、丁苯橡胶等通用橡胶和氯丁橡胶好。
图4 为与特种橡胶相比对于温度和油的使用范围。
但是, 这一使用范围因硫化体系和丙烯腈含量的不同而有差异。
图4NBR 及特种橡胶对于温度和油的使用范围评价橡胶耐热性的指标有多种。
例如, 将橡胶试样的伸长率变化率保持在50%状态下, 通过加速老化试验得出使用温度与耐用时间的关系(图5)。
以此作为胶管等橡胶制品选材的标准。
又如, 将橡胶试样的压缩永久变形保持在50%的状态下, 测出使用温度与使用时间的关系(图6) , 以作为评价橡胶密封垫、“O”形圈等密封制品耐热性的指标。
图5NBR和特种橡胶的伸长率变化率保持50%的使用温度与耐热时间ACM-丙烯酸酯橡胶;CMS-氯磺化聚乙烯;CHC-氯醚橡胶;CR-氯丁橡胶
图6NBR等橡胶压缩永久变形保持50%的使用温度与使用寿命的关系1-丙烯酸酯橡胶;2-丁腈橡胶;3-氯丁橡胶;4-氯醚橡胶。
丁腈配方参考汇总
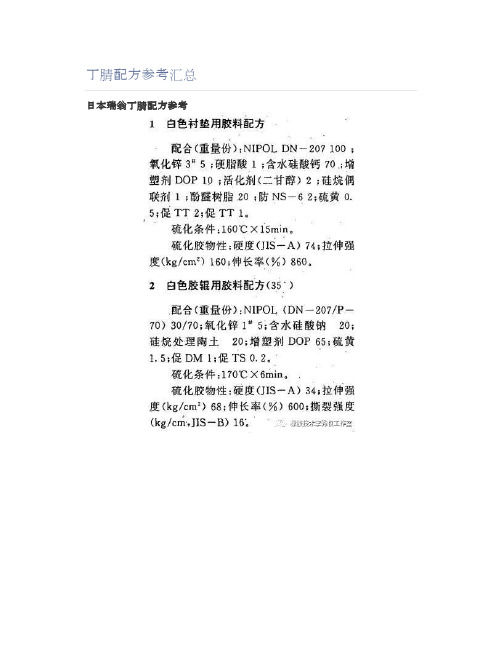
丁腈配方参考汇总日本瑞翁丁腈配方参考
以下配方仅供参考,通过实验室小配合检测基本达到使用要求,撕边容易,流动性好,不疵豁!
丁腈橡胶1502 50
丁腈橡胶2907 35
丁苯橡胶1502 15
氧化锌 4.5
硬脂酸 1.2
硫化剂DTDM 1.2
硫磺S 0.4
促进剂TRA 0.7
促进剂DM 1.3
白炭黑 25
橡胶补强剂(硅类填充剂) 15
轻质碳酸钙 20
酯类增塑剂 6
树脂 1.3
聚乙二醇 1.4
硅烷偶联剂 0.4
防老剂MB和L 2
内脱模剂 2
钛白粉和颜料若干
硫化温度:
180摄氏度*150s
硬度:72
强度:14.5
伸长:489%
压变:28
骨架油封是油封的典型代表,一般说的油封即指的是骨架油封。
油封的作用一般就是将传动部件中需要润滑的部件与出力部件隔离,不至于让润滑油渗漏。
骨架就如同混凝土构件里面的钢筋,起到加强的作用,并使油封能保持形状及张力。
按结构形式可分单唇骨架油封和双唇骨架油封。
双唇骨架油封的副唇起防尘作用,防止外界的灰尘,杂质等进入机器内部。
按骨架型式可分为内包骨架油封,外露骨架油封和装配式油封。
按工作条件可分为旋转骨架油封和往返式骨架油封。
用于汽油发动机曲轴,柴油发动机曲轴,变速箱,差速器,减震器,发动机,车桥等部位。
1
2
3
4
5
6
7
8
9
10
11
12
13
14
15
丁腈橡胶参考配方
成分投料比。
NBR 密封件配方设计

NBR 密封件配方设计一:常用橡胶用途及性能:特性:1、ACN ↑耐油性好,非极性或弱极性矿物油,植物油,液体燃料和有较高的稳定性。
2、耐热性优于NR SBR CR 可在120℃下长期使用。
3、属半导体材料。
4、耐油与压缩永久变形平衡,耐油性与电性能平衡。
5、丙烯晴含量对NBR 分类:➢极高丙烯腈含量Extreme High ACN >43%➢高丙烯腈含量High ACN 36%~42%➢中高丙烯腈含量Mid-High ACN 31%~35%➢中丙烯腈含量Middle ACN 25%~30%➢低丙烯腈含量Low ACN <24%总结:ACN% 越高,耐油性愈好耐热性改善,但TG差,ACN% 越低,低温性好,但耐油偏差。
且ML会升高,压缩永久变形好。
一般ACN% 在29%可过F17.过F19须用1965生胶。
二:共聚物组成(ACN含量)对NBR的影响三:硫化体系一般NBR 配方采用半有效硫化体系,例如:TT/CZ 1.5/1.5PHR, 这种硫化体系,具有耐热性较好的效果,SUL/TS 压缩变形和焦烧最优。
DM (CZ)拉伸强度好,用载硫剂可获得优良的压缩永久变形,镉镁硫化耐热150℃,过氧化物也可耐150℃高温。
且压缩永久变形最小,但撕裂差,活性用ZNO-A/ST-ACD5/1 使用,耐水配方用Pb3O4, 这时可不用ZNO-A, 但焦烧时间短。
四:防护体系:RD 耐热性最优MB/ZMTI耐热性优NBC抗臭氧效果好龟裂防护蜡,抗臭氧性佳AW抗臭氧性很佳总结:污染性比非污染性防护效果强,耐油配方,可选用难抽出防老剂。
或适当提高用量五:补强填充体系:1、N550 是快压出炉黑,一般2PHR提高一度,N774是半补强炉黑,一般3PHR提高一度,N990是中粒子热裂法炭黑,一般是4PHR提高一度压缩永久变形:N990>N550>N7742、一般配方里:N774 40PHR /N990 30PHR 油30PHR其硬度在50 度左右。
丁腈硫化配方范文
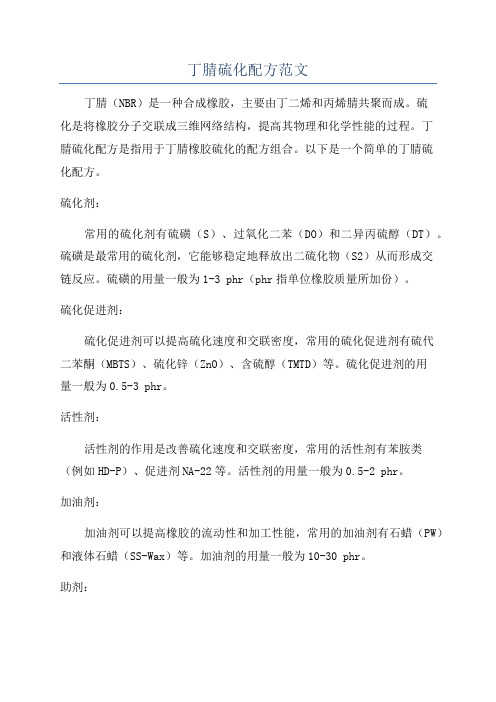
丁腈硫化配方范文丁腈(NBR)是一种合成橡胶,主要由丁二烯和丙烯腈共聚而成。
硫化是将橡胶分子交联成三维网络结构,提高其物理和化学性能的过程。
丁腈硫化配方是指用于丁腈橡胶硫化的配方组合。
以下是一个简单的丁腈硫化配方。
硫化剂:常用的硫化剂有硫磺(S)、过氧化二苯(DO)和二异丙硫醇(DT)。
硫磺是最常用的硫化剂,它能够稳定地释放出二硫化物(S2)从而形成交链反应。
硫磺的用量一般为1-3 phr(phr指单位橡胶质量所加份)。
硫化促进剂:硫化促进剂可以提高硫化速度和交联密度,常用的硫化促进剂有硫代二苯酮(MBTS)、硫化锌(ZnO)、含硫醇(TMTD)等。
硫化促进剂的用量一般为0.5-3 phr。
活性剂:活性剂的作用是改善硫化速度和交联密度,常用的活性剂有苯胺类(例如HD-P)、促进剂NA-22等。
活性剂的用量一般为0.5-2 phr。
加油剂:加油剂可以提高橡胶的流动性和加工性能,常用的加油剂有石蜡(PW)和液体石蜡(SS-Wax)等。
加油剂的用量一般为10-30 phr。
助剂:助剂主要包括抗氧剂、防老剂等,用于提高橡胶的耐热性和耐老化性能。
常用的助剂有有机羟基物(例如TMQ)、石墨烯等。
助剂的用量一般为1-5 phr。
填料:填料主要用于改变橡胶的力学性能和降低成本。
常用的填料有碳黑、石灰石粉等。
填料的用量一般为20-60 phr。
其他添加剂:根据需要,还可以添加其他的添加剂,如增塑剂、增韧剂、抗静电剂等。
以上只是一个简单的丁腈硫化配方,实际的配方会根据具体应用和要求进行调整。
在实际生产中,还需要考虑原料的品质、加工方法和工艺条件等因素。
配方的优化对于提高橡胶产品的性能和质量有着重要的作用。
- 1、下载文档前请自行甄别文档内容的完整性,平台不提供额外的编辑、内容补充、找答案等附加服务。
- 2、"仅部分预览"的文档,不可在线预览部分如存在完整性等问题,可反馈申请退款(可完整预览的文档不适用该条件!)。
- 3、如文档侵犯您的权益,请联系客服反馈,我们会尽快为您处理(人工客服工作时间:9:00-18:30)。
N B R橡胶的配方设计
精选文档
TTMS system office room 【TTMS16H-TTMS2A-TTMS8Q8-
NBR密封件配方设计
一、常用橡胶用途及性能:
1051 丙烯晴含量 41% ML75 SG 稍污染型1052 丙烯晴含量 33% ML50 SG 非污染型1053 丙烯晴含量 29% ML60 SG 非污染型1052M30丙烯晴含量33% ML30 SG 非污染型DN223丙烯晴含量 33%ML 35 SG非污染型丙烯晴含量 50% ML75 SG
非污染型
1965 丙烯晴含量 19% ML65 SG 非污染型DN401丙烯晴含量 18% ML78 SG 非污染型1043丙烯晴含量 29%ML 80 SG稍污染型
N230SL丙烯晴含量 35% ML42 SG 非污染型N260S丙烯晴含量 15% ML62 SG 非污染型
1052M40丙烯晴含量 33% ML40 SG 非污染型
特性:
1、ACN↑耐油性好,非极性或弱极性矿物油,植物油,液体燃料和有较高的稳定性。
2、耐热性优于NR SBR CR 可在120℃下长期使用。
3、属半导体材半料。
4、耐油与压缩永久变形平衡,耐油性与电性能平衡。
5、丙烯晴含量对NBR分类:
ACN% 43%以上极高ACN%NBR
36-42%以上高
31-35% 中高
25-30 中
24%以下低
总结:
ACN%越高,耐油性愈好耐热性改善,但TG差,ACN%越低,低温性好,但耐油偏差。
且ML会升高,压缩永久变形好。
一般ACN%在29%可过F17.过F19 须用1965或DN401生胶。
二、共聚物组成(ACN含量)对NBR的影响.项目ACN含量特点
密度低→→→高大
加工性(流动性)低→→→高良好
硫化速度低→→→高快
定伸应力、拉伸强度低→→→高大
硬度低→→→高大
耐磨性低→→→高良好
永久变形低→→→高大
耐油性低→→→
高良好
耐化学药品性低→→→高良好
耐热性低→→→高良好
和极性聚合物的相容低→→→高大
弹性低→→→高小
耐寒性低→→→高差
透气性低→→→高差
和增塑剂操作油的相容低→→→高差
三、硫化体系
一般NBR配方采用半有效硫化体系,例如:TT/CZ
,这种硫化体系,具有耐热性较好的效果,SUL/TS压缩歪和焦烧最优。
SUL/DM (CZ)拉伸强度好,用载硫剂可获得优良的压缩永久变形,镉镁硫化耐热150℃,过氧化物也可耐150℃高温。
且压缩永久变形最小,但撕裂差,活性用ZNO-A/ST-ACD5/1使用,耐水配方用Pb3O4,这时可不用ZNO-A,但焦烧时间短。
四、防护体系:
6C 耐屈挠龟裂。
OD?耐热性好,
RD 耐热性最优
MB/ZMTI?耐热性优
NBC 抗臭氧效果好
SUNGUARD?龟裂防护蜡,抗臭氧性佳。
AW?抗臭氧性很佳
总结:
污染性比非污染性防护效果强,耐油配方,可选用难抽出防老剂。
或适当提高用量
五、补强填充体系:
1、N550是快压出炉黑,一般2PHR提高一度,N774是半补强炉黑,一般3PHR 提高一度,N990是中粒子热裂法炭黑,一般是4PHR提高一度,
压缩永久变形:N990>N550>N774
2、一般配方里:N774 40PHR /N990 30PHR 油30PHR
其硬度在50度左右。
N550 40PHR/N7440 40PHR 油为15PHR 其硬度在70度左右,
N550 80PHR/N990 40 PHR 油为10PHR
其硬度在80度左右。
其中:在配合剂中其余份量不变的情况下,其抗张是N550>N774>N990.
3、白色填料,白烟补强效果最好,另#321,CLAY, CACO3具有一定的补强效果:321#活性大,补强效果好,但白色填料会吸附促进剂而延迟硫化,必须加入三乙醇胺,一般PEG4000S 2PHR即可,白色填料白烟增加,胶料硬度变硬。
ML升高,给加工带来困难。
六、加工助剂
一般用的酯类如:DOPDOS DOA,耐寒性好,其顺序如下,好DOS>DOA>DOP差,要求非抽性,用高分子增塑剂:如
聚酯类和非干性醇酸树脂等。