金属、高分子、陶瓷材料加工成型方法
材料成型技术基础

材料成型技术基础材料成型技术是一种将材料加工成所需形状和尺寸的制造方法。
它包括热成型、挤压、压缩成型、注塑成型、吹塑成型和复合成型等多种技术。
下面将对材料成型技术的基础知识进行介绍。
首先是热成型技术。
热成型是利用高温将材料加热到一定温度后,通过压力使其成型的一种方法。
常见的热成型方法有热压成型、热拉伸成型和热吹塑成型。
热成型技术可用于金属材料、塑料、橡胶等。
其次是挤压技术。
挤压是指通过将高温的材料推入压模中,利用模具的形状来使材料成型的一种方法。
挤压技术广泛应用于铝合金、铜合金、塑料等材料的生产。
再次是压缩成型技术。
压缩成型是指将粉末或颗粒材料装入压模中,然后通过压力使其成型。
常用的压缩成型方法有冲压、压铸、注射等。
压缩成型技术适用于金属、陶瓷等材料的制造。
注塑成型技术是指通过将熔融的塑料注入模具中,经过冷却凝固后取出成型的方法。
注塑成型技术广泛应用于塑料制品的生产,如塑料盒、塑料管等。
吹塑成型技术是将加热的塑料吹入空气或气体的膨胀中,通过气流的作用使塑料成型。
吹塑成型技术常用于制造塑料瓶、塑料容器等。
最后是复合成型技术。
复合成型是指将多种材料通过压合、热熔等方法使其粘结在一起的一种方法。
常见的复合成型方法有层压、模压和注射等。
复合成型技术可用于制造复合材料、夹层玻璃等产品。
总之,材料成型技术是一种将材料加工成所需形状和尺寸的制造方法。
不同的成型技术适用于不同的材料和产品,对于提高生产效率和产品质量具有重要意义。
了解和掌握这些基础知识对于进行材料成型工作是至关重要的。
高分子材料加工技术

高分子材料加工技术成型是将高分子材料通过热塑性或热固性工艺加工成特定形状的过程。
常见的成型方法包括挤出、注塑、吹塑、压延、镀膜等。
其中,挤出是一种通过将高分子材料加热至熔融状态,然后通过模具挤压出所需形状的工艺。
注塑是将高分子材料加热至熔融状态后注入到模具中,并通过压力使其充满模具内部形状的工艺。
吹塑是通过将高分子材料挤出成管状,并在一定压力下通过气流吹成制品的工艺。
压延是将高分子材料加热至玻态转变温度以上,然后通过压力在辊间压制成片状的工艺。
镀膜是在高分子材料的表面上涂覆一层金属或其他材料,以提高其耐磨性、导热性等性能的工艺。
改性是指通过添加填料、添加剂等方法改变高分子材料的性能。
填料可以增加高分子材料的强度、刚度和耐磨性等性能,常见的填料有玻璃纤维、碳纤维、硅胶等。
添加剂可以改变高分子材料的增塑性、耐候性、阻燃性等性能,常见的添加剂有防老化剂、增塑剂、阻燃剂等。
加工是将成型或改性后的高分子材料进行切割、钻孔、搪孔等工艺,以满足特定产品的要求。
常见的加工方法包括机械加工、热切割、激光切割等。
机械加工是通过机械设备如铣床、车床等进行切削、钻孔等操作,常用于加工较大尺寸的高分子制品。
热切割是通过将高分子材料加热至一定温度后进行切割的工艺,常用于加工薄膜、板材等较薄的制品。
激光切割是通过激光束的热作用将高分子材料切割,具有切割精度高、速度快等优点,常用于加工高精度的产品。
高分子材料加工技术的应用广泛,可以生产各种形式的产品,如管材、片材、薄膜、零件等。
然而,高分子材料加工过程中可能会产生一些问题,如热应力、挤出泡孔、缩水等。
为了解决这些问题,需要优化工艺参数,改善原材料的质量和稳定性。
总之,高分子材料加工技术是一门复杂而重要的技术,不仅可以满足各个领域的需求,还可以推动材料科学的发展。
随着科技的不断进步,高分子材料加工技术也将不断创新和发展,为社会的进步和发展做出更大的贡献。
金属材料的成型工艺

金属材料的成型工艺金属材料的成型工艺是指通过物理或化学方法将金属材料加工成所需形状的工艺过程。
成型工艺广泛应用于各个领域,如汽车、航空、船舶、建筑、制造业等。
它可以改变金属材料的形状、尺寸、性能和组织结构,使其适应不同的使用需求。
锻造是将金属材料加热至一定温度后,施加力并改变形状的工艺。
锻造可分为自由锻造、模锻和精锻。
自由锻造是直接对金属进行锻造,适用于简单形状的零部件。
模锻是使用模具对金属进行锤击或压制,适用于复杂形状和高精度要求的零部件。
精锻是在高温下对金属进行精密锻造,适用于高精度要求的零部件。
冲压是通过金属板材的拉伸、弯曲、切割和成形等工艺来制作零部件。
冲压工艺具有高效、节约材料、适用于大批量生产等优点,广泛应用于汽车制造、家电制造等领域。
铸造是通过将金属材料熔化后倒入模具中,使其凝固成型的工艺。
铸造可分为压力铸造和重力铸造。
压力铸造包括压铸、低压铸造和真空压力铸造。
压铸是将熔融金属注入压铸机模腔中,通过高压填充,并快速凝固成型。
低压铸造是将熔融金属通过压力填充式注射系统注入模具中,然后通过压力使其充满整个模腔,并凝固成型。
真空压力铸造是在真空环境中进行压铸,以提高铸件的质量和密度。
重力铸造是靠铸造机中的重力将熔融金属倒入模具中,凝固成型。
焊接是通过加热材料至熔化状态,通过外界压力和/或其他形式的能量传递,使金属材料连接起来的工艺。
常用的焊接方法包括电弧焊、气体保护焊、激光焊接等。
焊接工艺广泛应用于电子、汽车、船舶、航空航天等领域。
拉伸成型是将金属材料通过拉伸、挤压或者弯曲等方法成型的工艺。
拉伸成型可以提高材料的强度、硬度和耐磨性。
常见的拉伸成型工艺包括拉伸成型、锻造成型和爆炸成型等。
热成型是通过加热金属材料至塑性状态,然后在模具中进行变形的工艺。
热成型可以提高材料的塑性,使其更容易成形,并改变金属材料的结构和性能。
常用的热成型方法包括热压成型、热挤压、热拉伸等。
挤压成型是通过将金属材料放置在模具中,然后施加压力,使其通过模孔挤压成型的工艺。
高分子材料的加工与制备方法

高分子材料的加工与制备方法在现代科技的快速发展和应用推广下,高分子材料的加工和制备方法愈加重要和广泛应用。
高分子材料是一类由大量重复单体结构构成的大分子化合物。
而加工和制备高分子材料的方法则是指将这些物质转化为特定形状和性质的工艺过程。
本文将介绍几种常见的高分子材料加工和制备方法。
首先,传统的高分子材料加工方法之一是热塑性材料的注塑成型。
这种方法主要适用于聚合物材料,特点是可以生产出各种形状的制品,如塑料盖子、桶、板材等。
其具体工艺流程为:首先将高分子材料切割成颗粒状,然后将颗粒状的材料放入注塑机的料斗中,通过加热和挤出等过程,将材料熔融后注入模具中。
待冷却凝固后,即得到所需要的成品。
注塑成型方法的优点是生产效率高、成本相对较低,可以大规模生产。
而缺点是材料的形状和尺寸受模具限制。
此外,高分子材料的制备方法还包括热固性材料的热压成型。
这种方法主要适用于含有交联结构的高分子材料,如环氧树脂、酚醛树脂等。
它的工艺流程为:首先将高分子物质与硬化剂混合,形成粘稠的糊状物。
然后将糊状物放入模具中,施加热压力,使材料在高温下发生交联反应,从而形成固体。
热压成型的优点是可以制备出高耐热、高强度的制品,适用于需要高温环境下使用的产品。
然而,热压成型过程中对模具的要求较高,且成本较高。
此外,溶液共混是一种常见的高分子材料的制备方法。
这种方法适用于将两种或多种相溶的高分子材料混合在一起,从而得到新的复合材料。
具体步骤为:将两种高分子材料溶解在相同或相似的溶剂中,通过搅拌和混合等过程,使两种材料均匀分散在溶液中。
然后将溶液蒸发或使用其他方法将溶剂去除,得到固态的混合材料。
溶液共混的优点是制备过程简单、成本较低,可以获得新材料的独特性能。
而缺点则是混合后的材料性能难以控制,容易出现相分离现象。
最后,高分子材料还可以通过纺丝方法制备纤维。
纺丝方法主要适用于聚合物材料,如聚酯纤维、聚酰胺纤维等。
具体工艺流程为:首先将高分子材料加热熔化至黏度适宜的状态,形成糊状物。
四大高分子材料加工方法
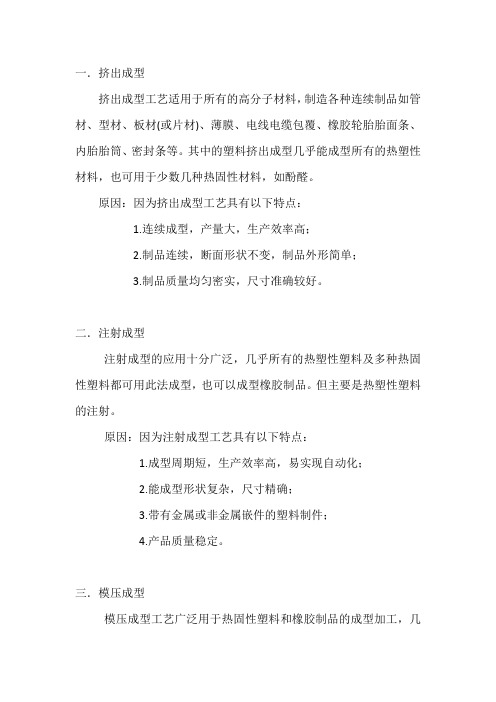
一.挤出成型挤出成型工艺适用于所有的高分子材料,制造各种连续制品如管材、型材、板材(或片材)、薄膜、电线电缆包覆、橡胶轮胎胎面条、内胎胎筒、密封条等。
其中的塑料挤出成型几乎能成型所有的热塑性材料,也可用于少数几种热固性材料,如酚醛。
原因:因为挤出成型工艺具有以下特点:1.连续成型,产量大,生产效率高;2.制品连续,断面形状不变,制品外形简单;3.制品质量均匀密实,尺寸准确较好。
二.注射成型注射成型的应用十分广泛,几乎所有的热塑性塑料及多种热固性塑料都可用此法成型,也可以成型橡胶制品。
但主要是热塑性塑料的注射。
原因:因为注射成型工艺具有以下特点:1.成型周期短,生产效率高,易实现自动化;2.能成型形状复杂,尺寸精确;3.带有金属或非金属嵌件的塑料制件;4.产品质量稳定。
三.模压成型模压成型工艺广泛用于热固性塑料和橡胶制品的成型加工,几乎所用的高分子材料都可用此方法来成型制品。
目前主要用于:热固性塑料的成型;橡胶制品的成型;复合材料的成型。
原因:因为模压成型工艺具有以下特点:1.与挤出和注射等成型工艺相比,模压成型工艺所需设备结构简单、制造精度不髙、制造费用低,所以投资少、见效快,为发展多品种、小批量的生产提供了有利条件;2.在模压成型过程中,由于塑料的流动距离很短,受填料的定向影响小,所以塑件的尺寸变动小,不易变形,尺寸稳定性好,机械性能稳定;3.相同吨位的压机可以成型较大平面的制品;4.模压成型工艺成熟,生产过程易于控制;5.模压成型中没有浇注系统,原材料浪费相对较少。
对于不能重复利用的热固性材料来讲,节约原料尤为重要;6.模压成型基本上适合于加工各种塑料,尤其像氨基树脂、环氧树脂和聚酰亚胺等材料,用注射成型既困难又会影响制品外观质量;对于用石棉或玻璃纤维等增强的塑料,在注射和挤出成型中,纤维易在浇口部分断裂,使制品的机械强度特别是冲击强度降低,失去增强的意义;聚酯团状和片状模塑料若采用注射成型,则需特殊的强迫加料装置,导致设备费用昂贵。
塑性加工原理
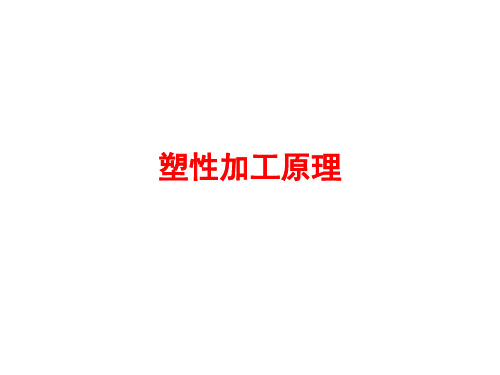
3D model of extrusions
Axis symmetrical finite element model of extrusion
拉拔:
将金属坯料拉过拉拔模模孔,而使金属拔长、其断面与模孔相 同的加工方法。主要用于生产各种细线材、薄壁管和一些特殊 截面形状的型材。
自由锻造:
将加热后的金属坯料置于上下砧铁间受冲击力或压力而变形的 加工方法。 模型锻造(模锻): 将加热后的金属坯料置于具有一定形状的锻模模膛内受冲击力 或压力而变形的加工方法。
根据金属流动方向与挤压凸模运动方向的关系,挤压可分为四种 方式:
(1)正挤压---金属流动方向与凸模运动方向相同. (2)反挤压---金属流动方向与凸模运动方向相反. (3)复合挤压---坯料一部分金属流动方向与凸模运动方向相同, 另一部分 则相反. (4)径向挤压---金属流动方向与凸模运动方向成90℃.
(3)温挤压---介于冷挤压和热挤压之间的挤压方法.温挤压时将金属 加热到适当温度(100~800℃)进行挤压.温挤压比冷挤压的变形抗 力小,较容易变形.
挤压成形的工艺特点:
(1)挤压时金属坯料处于三向压应力状态下变形,因此可提高金属坯 料的塑性,有利于扩大金属材料的塑性加工范围.
(2)可挤压出各种形状复杂,深孔,薄壁和异型截面的零件,且零件尺寸 精度高,表面质量好,尤其是冷挤压成形.
1、金属塑性成型特点 • 组织、性能好 • 材料利用率高 • 尺寸精度高 • 生产效率高
2、金属塑性成型的分类
1)块料成型 (1)一次加工
•轧制 •挤压 •拉拔 (2)二次加工 •自由锻 •模锻
2)板料成型
•冲裁 •弯曲 •拉延
3、课程目的和任务
1)阐明金属塑性变形的物理基础:从微观上研究塑性变形机理 及变形条件对金属塑性的影响,以便使工件在塑性成型时获得 最佳塑性状态、最高的变形效率和力学性能。
精选陶瓷的生产工艺原理与加工技术

浆料的性能要求:稳定性要好,在长时间加热而不搅拌的条件下不分 层与沉淀;可铸性要好,浆料铸满模腔并保持要求形状的能力;收缩率 要小,蜡浆由熔化的液体状态冷却凝固成固态时,会有体积收缩。
热压铸的工作原理:将配制成的料浆蜡板放置在热压铸机筒内,加热 至一定的温度熔化,在压缩空气的驱动下(或手动),将筒内的料浆通 过吸铸口压入模腔,根据产品的形状和大小保持一定的时间后,去掉压 力,料浆在模腔中冷却成型,然后脱模,取出坯体,有的还可进行加工 处理,或车削,或打孔等。 高温排蜡:坯体在烧成之前,先要经排蜡处理,否则由于石蜡在高温熔 化、流失、挥发、燃烧,坯体将失去粘结而解体。
300-800
氧化铝
400000
1500
碳化钛
390000
3000
金刚石
1171000
6000-10000
陶瓷的硬度为1000-5000HV
C、强度:陶瓷的强度不高,因为其晶界上存在有晶粒间的局部分离 或空隙,如空位、气孔、析出物,晶界上原子间键被拉长,键强度 被削弱,同时相同的电荷离子的靠近产生斥力,可能造成裂纹,所 以,消除晶界上不良作用,是提高陶瓷强度的基本途径。
陶瓷材料一般可分为普通陶瓷、特殊陶瓷与金属陶瓷三类 1、普通陶瓷:以天然硅酸盐矿物(粘土、长石、石英)经粉碎、压 制成型 、烧结而成的制品,如日用陶瓷、建筑陶瓷、电绝缘陶瓷等。 2、特殊陶瓷:采用高纯度的人工合成材料烧结而成,具有特殊力学、 物理、化学性能的陶瓷。如高温陶瓷、磁性陶瓷、压电陶瓷等。
3、金属陶瓷:用粉末冶金的方法制成,是金属与陶瓷组成的非均匀 复合材料制品。如金属陶瓷硬质合金等。
材料成型技术基础

材料成型技术基础材料成型技术基础材料成型技术是现代工业的核心技术之一,是将材料加工成所需形状、结构和性能的过程。
材料成型技术分为传统成型技术和先进成型技术两种。
前者包括热加工、冷加工、焊接等,后者则包括快速成型、激光加工、注塑成型等。
无论是哪种成型技术,都需要掌握材料成型技术基础知识才能熟练地操作和完成任务。
1.材料成型技术原理材料成型技术在原理上是通过施加压力,改变材料外观和性质。
采用不同的成型方法和工艺流程,可获得所需的形态和性能。
例如,金属冷加工依靠的是材料的塑性变形,而激光切割则是利用激光的高能量和热量来割断材料。
因此,不同成型技术的原理不同,工艺流程也不同。
2.材料成型技术分类材料成型技术主要可以分为常规材料成型技术和高级材料成型技术两类。
常规材料成型技术包括热加工、冷加工、铸造、焊接、切削等。
这些技术在工业生产中应用广泛,可以制造出各种形态的零部件和产品。
高级材料成型技术是在常规成型技术基础上,运用现代科技和工程技术发展起来的成型技术。
例如,金属材料的选择性激光烧结技术(SLS)、三维打印技术、激光切割技术和注塑成型技术等。
这些技术通常被用于制造高性能、高单价、高品质的工业产品。
3.常规材料成型技术热加工热加工技术是利用高温对材料进行塑性变形的加工方式。
通过热处理,可以使金属变得更加容易软化和延展。
热加工适合于制造大量的同样尺寸和形状的零件,例如轴、齿轮等机械元件。
冷加工冷加工技术是不需要高温处理的制造加工方法。
冷加工一般用于金属加工,由于没有热变形,冷加工一般具有更好的精度和表面光洁度。
冷加工应用广泛,例如冷拔、冷轧、冷环等。
铸造铸造是利用熔化的金属,将其注入模具中成型制品的加工方法。
铸造可以生产出各种不同尺寸和形状的零件,应用范围广泛,例如钢铁、铝合金、铜、铜合金等材料。
焊接焊接是将两个物体连接在一起的加工方式。
焊接广泛应用在车辆工业、建筑工业、航空航天工业等领域,例如电弧焊、气体保护焊、激光焊等技术。
材料工程复习思考题部分答案

《材料工程基础》复习思考题第一章绪论1、材料科学与材料工程研究的对象有何异同?答:材料科学侧重于发现和揭示组成与结构,性能,使用效能,合成与加工等四要素之间的关系,提出新概念,新理论。
而材料工程指研究材料在制备过程中的工艺和工程技术问题,侧重于寻求新手段实现新材料的设计思想并使之投入使用,两者相辅相成。
6、进行材料设计时应考虑哪些因素?答:.材料设计的最终目标是根据最终需求,设计出合理成分,制订最佳生产流程,而后生产出符合要求的材料。
材料设计十分复杂,如模型的建立往往是基于平衡态,而实际材料多处于非平衡态,如凝固过程的偏析和相变等。
材料的力学性质往往对结构十分敏感,因此,结构的任何细小变化,性能都会发生明显变化。
相图也是材料设计不可或缺的组成部分。
7、在材料选择和应用时,应考虑哪些因素?答:一,材料的规格要符合使用的需求:选择材料最基本的考虑,就在满足产品的特性及要求,例如:抗拉强度、切削性、耐蚀性等;二,材料的价格要合理;三,材料的品质要一致。
8、简述金属、陶瓷和高分子材料的主要加工方法。
答:金属:铸造(砂型铸造、特种铸造、熔模铸造、金属型铸造、压力铸造、低压铸造、离心铸造、连续铸造、消失模铸造)、塑性加工(锻造、板料冲压、轧制和挤压、拉拨)、热处理、焊接(熔化焊、压力焊、钎焊);橡胶:塑炼、混炼、压延、压出、硫化五部分;高分子:挤制成型、干压成型、热压铸成型、注浆成型、轧膜成型、等静压成型、热压成型和流延成型。
10、如何区分传统材料与先进材料?答:传统材料指已经成熟且已经在工业批量生产的材料,如水泥、钢铁,这些材料量大、产值高、涉及面广,是很多支柱产业的基础。
先进材料是正在发展,具有优异性能和应用前景的一类材料。
二者没有明显界限,传统材料采用新技术,提高技术含量、性能,大幅增加附加值成为先进材料;先进材料长期生产应用后成为传统材料,传统材料是发展先进材料和高技术基础,先进材料推到传统材料进一步发展。
高分子材料加工技术--压制成型

1.2工艺过程
高分子材料成型加工
高分子材料成型加工
2.片状模塑料模压成型
(Sheet Molding Compound. SMC)
2.1 配比:
不饱和聚酯 约20~30%
增稠剂
约 5%
无机填料 40~50%
引发剂
2~3%
脱模剂
0.5~1%
短切玻璃纤维或毡片 适量
2.2 工艺过程
高分子材料成型加工
高分子材料成型加工
三. 模型硫化工艺及硫化条件
工艺过程
混炼胶和橡胶半成品→ 计量→ 加料→ 闭 模→排气 →保压(硫化)→ 脱模→ 制品
这一过程基本上与热固性塑料的模压成型 相同,硫化工艺条件是硫化压力、硫化温 度和硫化时间。
高分子材料成型加工
1.硫化压力 大多数的橡胶制品的硫化是在一定压力下 进行的 一般模压制品的硫化压力为2~4 MPa 胶料流动性差,制品形状复杂,制品表面 花纹细致,结构复杂,厚制品,硫化温度 高,则硫化压力高一些。 太高的硫化压力会加速橡胶分子链的热降 解
高分子材料成型加工
一. 热固性模塑料的成型工艺性能:
1.流动性:热固性模塑料的流动性是指其在受热和受 压情况下充满整个模具型腔的能力。 影响流动性的因素:
压模塑料的性能和组成(分子量、颗粒形状、小分 子物质)
模具与成型条件(光洁度、流道形状、预热)
流动性要适中:
太大:溢出模外,塑料在型腔内填塞不紧,或树脂 与填料分头聚集。
高分子材料成型加工
根据实践经验,在选择模压成型的工艺条 件时,可以从模压压力、温度和时间三者 中先固定一个条件,如按经验选定成型压 力,然后再变化成型的温度和时间,从实 验中找出合理的条件来。
材料制备技术范文

材料制备技术范文材料制备技术是指通过一系列的工艺和方法,将原材料转化为所需的最终产品。
在材料制备技术中,常见的材料包括金属、陶瓷、复合材料、高分子材料等。
随着科学技术的不断进步,材料制备技术也在不断发展,从而满足了各种领域对材料性能和功能的不同需求。
在本文中,将会介绍几种主要的材料制备技术。
首先,金属材料的制备技术是最常见和重要的。
熔炼是一种常用的金属材料制备技术,通过将金属原料加热熔化,然后再冷却成型,最终得到所需形状的金属材料。
另外,还有一种常用的金属材料制备技术是粉末冶金。
在粉末冶金中,金属原料首先被粉碎成粉末,然后通过加压和热处理,使粉末颗粒之间发生冶金结合,最终形成金属制品。
其次,陶瓷材料的制备技术也是非常重要的。
烧结是一种常见的陶瓷材料制备技术,通过将陶瓷粉末加热到接近其熔点的温度,使粉末颗粒之间发生结合,最终形成致密的陶瓷材料。
此外,还有一种常用的陶瓷材料制备技术是溶胶-凝胶法。
在溶胶-凝胶法中,先将金属盐或有机金属化合物溶解在溶剂中,形成胶体溶液,然后通过凝胶化和热处理,使溶胶形成致密的陶瓷材料。
另外,复合材料的制备技术是近年来发展较快的领域。
复合材料是由两种或更多种不同类型的材料组合而成,通过充分利用各种材料的特性,从而获得更优越的性能。
常见的复合材料制备技术包括层压法、注塑法和纤维增强陶瓷基复合材料制备技术。
层压法是将预浸料(通常是纤维增强材料)与树脂层间层叠,然后通过热压或热固化等方法,使其结合成型。
注塑法是将熔融的塑料注入到具有空隙的模具中,然后使其冷却凝固,最终得到所需形状的复合材料制品。
纤维增强陶瓷基复合材料制备技术是将陶瓷基体与纤维增强材料结合,以提高材料的强度和韧性。
最后,高分子材料的制备技术也是很重要的一部分。
高分子材料制备技术主要包括聚合法、共混法和交联法。
聚合法是通过引发剂诱导单体分子之间的共价键结合,从而形成高分子链的方法。
共混法是将两种或多种高分子材料溶化在一起,通过混合和加工工艺,使其形成共存和相容的混合物。
陶瓷制备方法

陶瓷制备方法一、概述陶瓷是一种非金属材料,具有多种优良的物理和化学性质,如高温稳定性、耐腐蚀性、硬度高等。
陶瓷材料在日常生活和工业生产中有广泛应用,例如制作陶瓷器皿、建筑材料、电子元器件等。
本文将介绍几种常见的陶瓷制备方法。
二、干法制备方法1. 烧结法烧结法是将陶瓷原材料粉末在高温下进行烧结,使其颗粒间相互结合形成固体块材料。
该方法可分为普通烧结法和压电烧结法两种。
普通烧结法是将粉末制成坯体,然后在高温下烧结。
而压电烧结法是将陶瓷粉末与有机高分子混合后,压制成形,再在高温下进行烧结。
该方法具有成本低、制备周期短等优点,但制备出来的陶瓷材料致密度较低,有一定的气孔。
2. 真空压制法真空压制法是一种将陶瓷原材料粉末加热到熔点后,在真空环境下进行压缩成型的方法。
该方法制备出来的陶瓷材料致密度高、强度大,但成本较高。
3. 溶胶-凝胶法溶胶-凝胶法是将金属化合物或有机酸与其他化合物混合后,在加热和干燥后形成凝胶,然后再进行烧结。
该方法制备的陶瓷材料致密度高、粒度小,具有高温稳定性、耐腐蚀性等优点。
1. 凝胶注模法凝胶注模法是将陶瓷粉末与有机化合物混合后形成凝胶,然后放入注模机内注模,再进行热处理得到陶瓷制品。
该方法制备的陶瓷制品精度高、致密度好,表面光滑。
2. 喷雾干燥法喷雾干燥法是将含有陶瓷材料的溶液通过高压喷雾器雾化成微小颗粒,然后在气流中进行干燥得到陶瓷粉末。
该方法制备出来的陶瓷粉末粒度小、均匀,但成本较高。
3. 溶液浸渍法溶液浸渍法是将陶瓷原材料粉末加入到化学制剂的溶液中,使其渐渐凝结成凝胶,然后进行烧结制品。
该方法操作简单,成本低,但制备的陶瓷制品致密度不够。
坩埚法是一种古老的陶瓷制备方法,用于制作瓷器和陶器。
制作方法是将陶瓷原材料经过处理后,按一定比例混合后磨成均匀的陶瓷泥,放入坩埚内,在高温下进行烧制得到制品。
该方法适用于制作小型陶瓷制品。
2. 电化学制备法电化学制备法是一种利用电化学反应制备陶瓷材料的方法。
材料加工成型方法

材料加工成型方法概述:材料加工成型方法是指通过对材料进行一系列的加工和变形,使其达到预期的形状和尺寸的过程。
它是制造业中不可或缺的环节,涉及到多种材料和工艺,对产品质量和生产效率有着重要影响。
本文将介绍几种常见的材料加工成型方法。
一、铸造铸造是将熔融状态的金属或合金倒入预先制作好的铸型中,经过冷却凝固后得到所需形状的方法。
铸造是最早的材料加工成型方法之一,广泛应用于铁、钢、铝、铜等金属材料的生产中。
铸造具有成本低、生产效率高等优点,但也存在着缺陷和瑕疵的风险。
二、锻造锻造是通过对金属材料施加压力,使其在固态条件下发生塑性变形,从而得到所需形状的方法。
锻造分为冷锻和热锻两种形式,适用于各种金属材料的加工。
锻造具有改善材料内部结构、提高材料性能的作用,常用于制造高强度、高耐磨性的零件和工具。
三、挤压挤压是将金属材料通过压力使其通过模具孔口形成所需截面形状的方法。
挤压适用于各种金属材料,尤其适用于制造长条状或复杂截面的零件。
挤压具有高生产效率、材料利用率高等优点,广泛应用于建筑、汽车、航空等行业。
四、冲压冲压是利用冲压机将金属板材进行一系列的压制、拉伸、弯曲等变形,最终得到所需形状的方法。
冲压适用于各种金属材料的加工,常用于制造薄壁零件、复杂形状的零件。
冲压具有生产效率高、成本低等优点,被广泛应用于电子、家电、汽车等行业。
五、加工中心加工中心是一种集铣削、钻孔、镗削等多种加工功能于一体的机床,可以对材料进行高精度、复杂形状的加工。
加工中心适用于各种金属和非金属材料的加工,常用于制造模具、工装夹具等高精度零件。
加工中心具有高精度、高效率的特点,能够提高产品质量和生产效率。
六、3D打印3D打印是一种将数字模型直接转化为实体模型的制造技术,可以通过层层堆叠材料来构建所需形状的物体。
3D打印适用于各种材料,包括金属、塑料、陶瓷等。
3D打印具有制造复杂结构、个性化产品的优势,被广泛应用于医疗、航空航天、艺术设计等领域。
材料加工成型方法
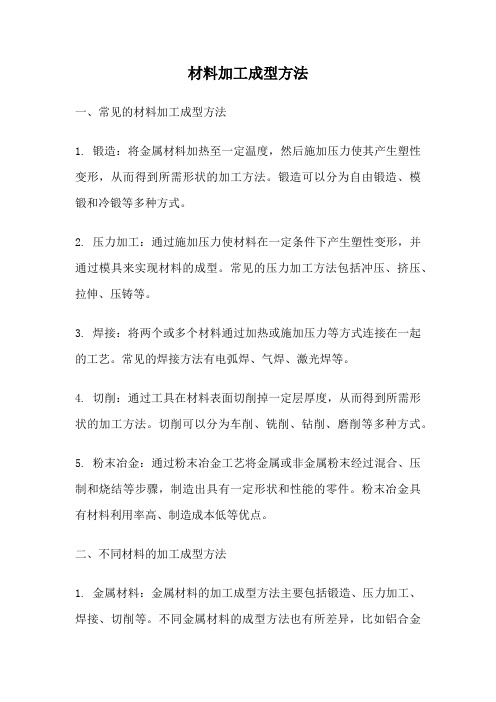
材料加工成型方法一、常见的材料加工成型方法1. 锻造:将金属材料加热至一定温度,然后施加压力使其产生塑性变形,从而得到所需形状的加工方法。
锻造可以分为自由锻造、模锻和冷锻等多种方式。
2. 压力加工:通过施加压力使材料在一定条件下产生塑性变形,并通过模具来实现材料的成型。
常见的压力加工方法包括冲压、挤压、拉伸、压铸等。
3. 焊接:将两个或多个材料通过加热或施加压力等方式连接在一起的工艺。
常见的焊接方法有电弧焊、气焊、激光焊等。
4. 切削:通过工具在材料表面切削掉一定层厚度,从而得到所需形状的加工方法。
切削可以分为车削、铣削、钻削、磨削等多种方式。
5. 粉末冶金:通过粉末冶金工艺将金属或非金属粉末经过混合、压制和烧结等步骤,制造出具有一定形状和性能的零件。
粉末冶金具有材料利用率高、制造成本低等优点。
二、不同材料的加工成型方法1. 金属材料:金属材料的加工成型方法主要包括锻造、压力加工、焊接、切削等。
不同金属材料的成型方法也有所差异,比如铝合金常用挤压、铸造等方法,而高温合金则常用粉末冶金和熔模铸造等方法。
2. 塑料材料:塑料材料的加工成型方法主要包括挤出、注塑、吹塑等。
挤出是将熔融的塑料通过模具挤出成型,注塑是将熔融的塑料注入模具中形成所需形状,吹塑是通过气压将塑料吹气膨胀成型。
3. 复合材料:复合材料通常由两种或多种不同性质的材料组合而成,因此其加工成型方法也较为多样。
常见的复合材料加工成型方法有层压、注塑、挤出等。
1. 材料的性质:不同材料具有不同的物理、化学性质,因此在选择加工成型方法时需要考虑材料的可塑性、熔点、硬度等因素。
2. 成型件的形状复杂程度:对于形状复杂的零件,通常需要采用多道工序的加工成型方法,如锻造、切削、焊接等的组合使用。
3. 生产效率和成本:不同的加工成型方法在生产效率和成本方面也有所差异,需要根据具体情况选择适合的方法,以提高生产效率并控制成本。
四、材料加工成型方法的发展趋势1. 自动化和智能化:随着科技的进步,材料加工成型方法也朝着自动化和智能化方向发展。
粉末压制及烧结方法
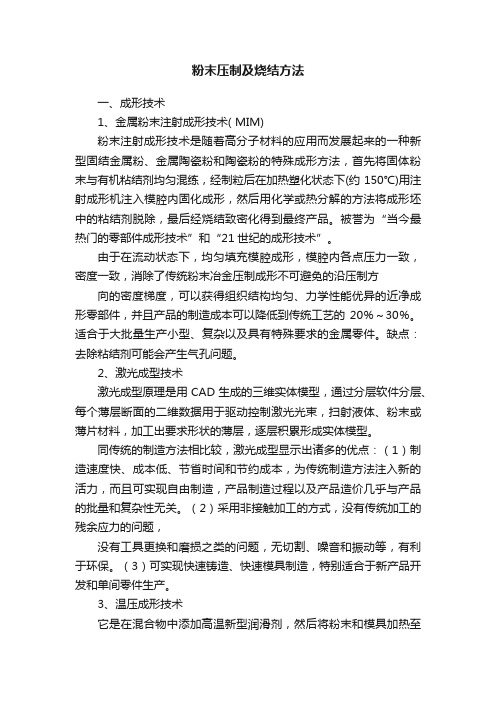
粉末压制及烧结方法一、成形技术1、金属粉末注射成形技术( MIM)粉末注射成形技术是随着高分子材料的应用而发展起来的一种新型固结金属粉、金属陶瓷粉和陶瓷粉的特殊成形方法,首先将固体粉末与有机粘结剂均匀混练,经制粒后在加热塑化状态下(约150℃)用注射成形机注入模腔内固化成形,然后用化学或热分解的方法将成形坯中的粘结剂脱除,最后经烧结致密化得到最终产品。
被誉为“当今最热门的零部件成形技术”和“21世纪的成形技术”。
由于在流动状态下,均匀填充模腔成形,模腔内各点压力一致,密度一致,消除了传统粉末冶金压制成形不可避免的沿压制方向的密度梯度,可以获得组织结构均匀、力学性能优异的近净成形零部件,并且产品的制造成本可以降低到传统工艺的20%~30%。
适合于大批量生产小型、复杂以及具有特殊要求的金属零件。
缺点:去除粘结剂可能会产生气孔问题。
2、激光成型技术激光成型原理是用CAD生成的三维实体模型,通过分层软件分层、每个薄层断面的二维数据用于驱动控制激光光束,扫射液体、粉末或薄片材料,加工出要求形状的薄层,逐层积累形成实体模型。
同传统的制造方法相比较,激光成型显示出诸多的优点:(1)制造速度快、成本低、节省时间和节约成本,为传统制造方法注入新的活力,而且可实现自由制造,产品制造过程以及产品造价几乎与产品的批量和复杂性无关。
(2)采用非接触加工的方式,没有传统加工的残余应力的问题,没有工具更换和磨损之类的问题,无切割、噪音和振动等,有利于环保。
(3)可实现快速铸造、快速模具制造,特别适合于新产品开发和单间零件生产。
3、温压成形技术它是在混合物中添加高温新型润滑剂,然后将粉末和模具加热至150℃左右进行刚性模压制,最后采用传统的烧结工艺进行烧结的技术,是普通模压技术的发展与延伸。
该技术主要有以下几个方面的特点:能以较低的成本制造出高性能的铁基等粉末冶金零部件;提高零部件生坯密度;产品具有高强度;便于制造形状复杂以及要求精密的零部件;密度均匀等该技术目前主要用于生产铁基合金零件,同时人们正在研究用这种技术制备铜基合金、钛合金等其它材料零件。
金属(陶瓷)粉末注射成型技术(MIM).
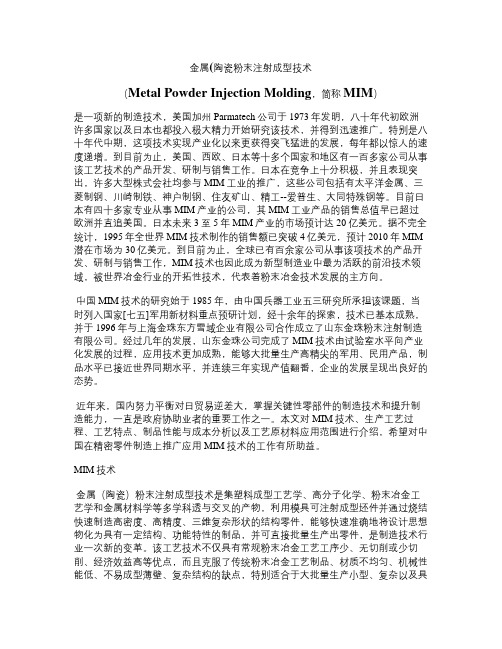
金属(陶瓷粉末注射成型技术(Metal Powder Injection Molding,简称MIM)是一项新的制造技术,美国加州Parmatech公司于1973年发明,八十年代初欧洲许多国家以及日本也都投入极大精力开始研究该技术,并得到迅速推广。
特别是八十年代中期,这项技术实现产业化以来更获得突飞猛进的发展,每年都以惊人的速度递增。
到目前为止,美国、西欧、日本等十多个国家和地区有一百多家公司从事该工艺技术的产品开发、研制与销售工作。
日本在竞争上十分积极,并且表现突出,许多大型株式会社均参与MIM工业的推广,这些公司包括有太平洋金属、三菱制钢、川崎制铁、神户制钢、住友矿山、精工--爱普生、大同特殊钢等。
目前日本有四十多家专业从事MIM产业的公司,其MIM工业产品的销售总值早已超过欧洲并直追美国。
日本未来3至5年MIM产业的市场预计达20亿美元。
据不完全统计,1995年全世界MIM技术制作的销售额已突破4亿美元,预计2010年MIM 潜在市场为30亿美元。
到目前为止,全球已有百余家公司从事该项技术的产品开发、研制与销售工作,MIM技术也因此成为新型制造业中最为活跃的前沿技术领域,被世界冶金行业的开拓性技术,代表着粉末冶金技术发展的主方向。
中国MIM技术的研究始于1985年,由中国兵器工业五三研究所承担该课题,当时列入国家[七五]军用新材料重点预研计划,经十余年的探索,技术已基本成熟,并于1996年与上海金珠东方雪域企业有限公司合作成立了山东金珠粉末注射制造有限公司。
经过几年的发展,山东金珠公司完成了MIM技术由试验室水平向产业化发展的过程,应用技术更加成熟,能够大批量生产高精尖的军用、民用产品,制品水平已接近世界同期水平,并连续三年实现产值翻番,企业的发展呈现出良好的态势。
近年来,国内努力平衡对日贸易逆差大,掌握关键性零部件的制造技术和提升制造能力,一直是政府协助业者的重要工作之一。
本文对MIM技术、生产工艺过程、工艺特点、制品性能与成本分析以及工艺原材料应用范围进行介绍,希望对中国在精密零件制造上推广应用MIM技术的工作有所助益。
四种常见的胶结类型
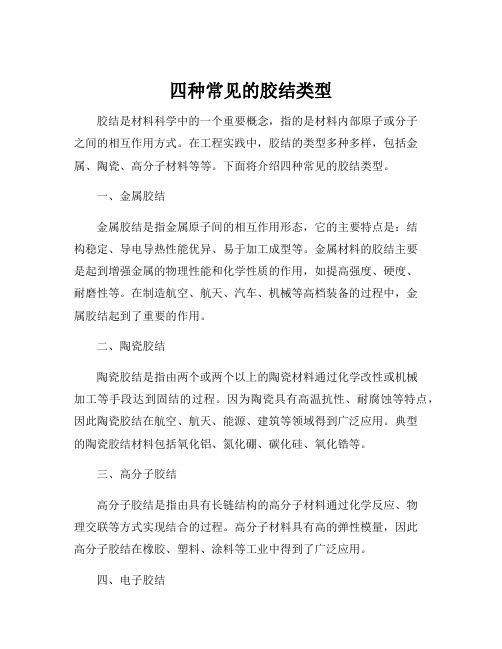
四种常见的胶结类型
胶结是材料科学中的一个重要概念,指的是材料内部原子或分子
之间的相互作用方式。
在工程实践中,胶结的类型多种多样,包括金属、陶瓷、高分子材料等等。
下面将介绍四种常见的胶结类型。
一、金属胶结
金属胶结是指金属原子间的相互作用形态,它的主要特点是:结
构稳定、导电导热性能优异、易于加工成型等。
金属材料的胶结主要
是起到增强金属的物理性能和化学性质的作用,如提高强度、硬度、
耐磨性等。
在制造航空、航天、汽车、机械等高档装备的过程中,金
属胶结起到了重要的作用。
二、陶瓷胶结
陶瓷胶结是指由两个或两个以上的陶瓷材料通过化学改性或机械
加工等手段达到固结的过程。
因为陶瓷具有高温抗性、耐腐蚀等特点,因此陶瓷胶结在航空、航天、能源、建筑等领域得到广泛应用。
典型
的陶瓷胶结材料包括氧化铝、氮化硼、碳化硅、氧化锆等。
三、高分子胶结
高分子胶结是指由具有长链结构的高分子材料通过化学反应、物
理交联等方式实现结合的过程。
高分子材料具有高的弹性模量,因此
高分子胶结在橡胶、塑料、涂料等工业中得到了广泛应用。
四、电子胶结
电子胶结是指通过电子云的共享或转移实现的材料结合。
例如,半导体材料的胶结就是一种电子胶结方式。
半导体材料具有良好的导电性能和独特的光电特性,因此在电子器件、显示屏、太阳能电池等领域得到了广泛应用。
综上所述,不同类型的胶结都有各自的特点和优势。
在实际应用中,需要根据需要进行选择,以达到最佳的效果。
- 1、下载文档前请自行甄别文档内容的完整性,平台不提供额外的编辑、内容补充、找答案等附加服务。
- 2、"仅部分预览"的文档,不可在线预览部分如存在完整性等问题,可反馈申请退款(可完整预览的文档不适用该条件!)。
- 3、如文档侵犯您的权益,请联系客服反馈,我们会尽快为您处理(人工客服工作时间:9:00-18:30)。
金属材料、高分子材料、陶瓷材料的成型制备方法金属材料加工成型方法金属材料成型工艺有以下几种一、金属液态成型也叫铸造。
它是将熔融的金属液体浇注到与零件形状相对应的铸造模型腔中,待冷却后得到实体毛坯或零件的工艺过程。
铸造加工的特点:1.适应性强2.成本低廉3.铸造组织存在一定缺陷4.工艺过程较难控制铸造方法分为砂型铸造、特殊铸造I、砂型铸造:用型砂做铸型的铸造方法,使用率90%砂型铸件的结构设计应注意1、力求外形简单,轮廓平直,只需一个分型面2、力求铸件的内腔铸造时,型芯数目最少,方便装配、清理、排气3、起模方向应设计结构斜度4、铸件应有合理的壁厚5、力求铸件壁厚均匀,防止局部积聚变形,造成裂纹、缩孔、缩松等缺陷6、尽量避免铸件中有过大的水平面,防止由于横截面突然增大,导致金属液面上升缓慢,致使型腔顶部受到长时间烘烤,造成夹砂缺陷、产生气孔等;将平面改为倾斜面II、特种铸造特种铸造:砂型铸造以外的其他铸造方法,包括熔模铸造、金属型铸造、压力铸造、低压铸造、离心铸造、陶瓷型铸造等。
①熔模铸造(失蜡铸造):在蜡模表面包以造型材料,待其硬化,将其中的蜡模熔去,从而获得无分型面的铸型的铸造方法。
基本过程:蜡模制造→结壳→脱蜡→造型→焙烧→浇铸→落砂清理熔模铸造(失蜡铸造)的特点a、铸件的精度高且表面光洁。
b、适用于各种铸造合金铸件,尤其是高熔点及难切削的合金的铸造。
c、熔模铸件的形状可以比较复杂,最小孔径0.5mm,壁厚0.3mm。
d、铸件的重量不宜太大,一般<=25kg,最大80kg左右。
e、工艺过程复杂,不易控制,使用和消耗的材料较贵,适用于形状复杂、精度较高或难以机加工的小型零件,如发动机叶片和叶轮等。
②金属型铸造:金属型铸造又称硬模铸造,它是将液体金属浇入金属铸型,以获得铸件的一种铸造方法。
铸型是用金属制成,可以反复使用多次(几百次到几千次)。
金属性铸造的优缺点可以“一型多铸”,铸件的力学性能提高,金属型铸件的冷却速度较快、组织比较致密铸件精度较高,可以少加工或不加工。
但是,成本高、周期长;铸造透气性差、无退让性,易产生冷隔、浇不足、裂纹等缺陷;铸件熔点不宜太高,重量也不宜太大。
主要用于:大批量的有色金属铸件,如内燃机的铝活塞、气缸体、缸盖、油泵壳体等。
③压力铸造:压力铸造(简称压铸)的实质是在高压作用下,使液态或半液态金属以较高的速度充填压铸型(压铸模具)型腔,并在压力下成型和凝固而获得铸件的方法。
压铸特点:高压和高速充填压铸型是压铸的两大特点。
它常用的压射比压是从几千至几万kPa,甚至高达2×105kPa。
充填速度约在10~50m/s,有些时候甚至可达100m /s以上。
充填时间很短,一般在0.01~0.2s范围内。
压铸优点:铸件表面质量高,可铸出复杂形状薄壁件或镶嵌件,生产率高。
主要适合于有色金属合金,如锌合金、铝合金、镁合金。
④低压铸造:介于重力铸造和压力铸造之间的一种方法,所用压力为2-7N/cm2。
主要用于生产质量高的铝镁合金铸件。
⑤离心铸造:将液态合金浇入高速旋转(250-1500r/min)的铸型中,使金属液在离心力作用下充填铸型并结晶。
主要用于生产圆筒形铸件。
二、塑性成形工艺塑性成形工艺:利用外力使坯料产生塑性变形,获得所需尺寸,形状和性能的产品(毛坯或零件)成型方法。
加工基本方式:轧制、挤压、拉拨、锻造(自由锻和模锻)和板料冲压。
轧制、挤压、拉拨用于金属型材、板材、管材和线材板料冲压和锻造用于毛胚和零件。
加工的特点:是一种重要的塑性成型方法,要求金属具有良好的塑性优点:金属塑性变形后,能压合铸坯的内部缺陷,提高金属机械性能保证强度和韧性,节省金属材料和加工工时间。
缺点:只适用于塑性金属材料,不能加工脆性材料如铸铁、青铜,不能加工形状太复杂的零件比如具有复杂外形和内腔的零件。
A、轧制:将金属靠摩擦力的作用,连续通过轧机上两个相对回转轧辊之间的空隙,进行压延变形成为型材(如圆钢、方钢、工字钢等)的加工方法。
B、挤压:将金属坯料置于一封闭的挤压模内,用强大的挤压力将金属从模孔中挤出成型,从而获得符合模孔截面的坯料或零件的加工方法。
C、锻造加工:对金属坯料(不含板材)施加外力,使其产生塑性变形、改变尺寸、形状及改善性能,用以制造机械零件、工件、工具或毛坯的成形加工方法。
可锻造的固体坯料可以是铁碳合金、铝合金、铜合金等。
锻造分为两种:①自由锻②模锻①自由锻: 利用冲击力或压力,使金属在上下之砧间塑性变形而获得所需尺寸、形状以及内部质量锻件的一种加工方法。
基本工序:镦粗、拔长、冲孔、弯曲、切割、扭转和错移辅助工序:方便基本工序而进行的修整工序:校正等②模锻:使金属坯料在模膛内受压而产生塑性变形,获得所需尺寸、形状以及内部质量锻件的加工方法称为模锻。
模锻优点:效率高、易操作、尺寸精确,质量好、减小切削工作量磨具昂贵、灵活性差、生产准备周期长、质量要小。
D、冲压加工成型:它是利用冲模使板材产生分离或变形的加工方法。
通板料冲压特点:(1)可冲压出形状复杂的零件,废料较少。
(2)产品具有足够高的精度和较低的表面粗糙度,互换性能好。
(3)能获得质量轻,材料消耗少,强度和刚度较高的零件。
(4)冲压操作简单,工艺过程便于机械化和自动化,成品率很高,故零件成本低。
常在冷态下进行,又叫冷冲压。
三、连接形式连接形式有以下几类:焊接、胶接、机械连接I、焊接:通过加热、加压,或两者共同作用(用或不用填充材料)使两部分分离的金属形体形成原子结合的一种永久性连接方法。
熔焊:电弧焊、气焊、电子束焊、激光焊压焊:电阻焊(点焊、缝焊、对焊)钎焊:锡焊、铜焊、银焊一般情况,低碳钢的焊接性能较好,焊接过程中不出现裂纹、气孔、夹渣等,焊后接头强度与母材相近,高碳钢,铸铁等较差。
在灯饰,金属家具等产品的加工过程中,都会用到。
1)熔焊:将工件需要焊接的部位加热至熔化状态,一般须填充金属并形成共同的熔池,待冷却凝固后,使分离工件连接成整体。
特点:是金属的熔化与结晶,类似于小型铸造过程,焊接时填充金属的目的是使焊接接头符合标准尺寸、外形,渗入有益元素以加强强度,熔焊的能量可以是电能、化学能和机械能。
2)压焊:在压力(或同时加热)作用下,被焊的分离金属结合面处产生塑性变形(有的伴随有熔化结晶过程)而使金属连接成整体。
特点:常见的如电阻焊(点焊、缝焊、对焊)。
1.金属待焊部位发生塑性变形,挤碎或挤掉结合面的氧化物及其他杂质 2.纯净的金属紧密接触,形成原子间的引力而牢固结合。
3.加热的目的:增加原子的动能,以提高塑性和降低顶锻力。
3)钎焊:熔点低于被焊金属的钎料熔化后,填充到被焊金属结合面的空隙之中,钎料凝固而将两部分金属连接成整体。
常见有:锡焊、铜焊、银焊。
特点:被焊金属不熔化,钎料熔化,依靠熔化的钎料对被焊金属的润湿性(浸润与附着能力)和毛细作用与被焊金属形成结合,从而将分离的金属连接。
II、胶接:胶接是将两种或两种以上的零件(构件)用胶粘剂连接起来的一种工艺方法,所构成的不可拆连接称为胶连接。
胶接工艺主要包括接头设计、表面处理、配胶和涂胶、固化和质量检测。
胶接优点:①能够将不同的金属或金属与非金属粘接在一起。
②可以粘接一些不易焊接的异形、复杂、微小和极薄零件。
③粘接接头处应力分布比较均匀,粘接胶层具有缓和冲击,消减振动的作用,使接头处疲劳强度得以提高。
④粘接胶层密封性能好,粘接剂可以将两种不同金属隔开,能防止电化学腐蚀。
⑤粘接重量轻,外表光整。
胶接的缺点是:①胶接剂对温度变化比较敏感。
②耐老化、耐酸、碱等性能较差。
③粘接接头的检查,特别是无损检验困难。
III、机械连接:螺栓与螺母连接,双头螺柱连接,螺钉连接,销连接,铆钉连接,压扩、卷边咬缝等机械方法连接将两个金属器件连接起来的方法。
塑料的加工成型方法一、塑料的加工成型塑料的成型分为一次成型和二次成型两类塑料的一次成型方法有:挤出成型、注射成型、压制成型、压延成型、其他成型方法(铸塑成型、模压烧结成型、传递成型、泡沫塑料的成型)。
二次成型有:中空吹塑成型、热成型、拉幅薄膜的成型。
⑴、挤出成型:挤出成型在塑料加工中又称为挤塑,在非橡胶挤出机加工中利用液压机压力于模具本身的挤出称压出。
是指物料通过挤出机料筒和螺杆间的作用,边受热塑化,边被螺杆向前推送,连续通过机头而制成各种截面制品或半制品的一种加工方法。
挤出成型原理:料自料斗进入料筒,在螺杆旋转作用下,通过料筒内壁和螺杆表面摩擦剪切作用向前输送到加料段,在此松散固体向前输送同时被压实;在压缩段,螺槽深度变浅,进一步压实,同时在料筒外加热和螺杆与料筒内壁摩擦剪切作用,料温升高开始熔融,压缩段结束;均化段使物料均匀,定温、定量、定压挤出熔体,到机头后成型,经定型得到制品。
1、挤出方法按塑化方式:干法挤出与湿法挤出按加压方式:连续挤出与间歇挤出2、特点生产连续、效率高、操作简单、应用范围广⑵、注射成型:是指有一定形状的模型,通过压力将融溶状态的胶体注入摸腔而成型。
工艺原理是:将固态的塑胶按照一定的熔点融化,通过注射机器的压力,用一定的速度注入模具内,模具通过水道冷却将塑胶固化而得到与设计模腔一样的产品。
主要用于热塑性塑料的成型,也可用于热固性塑料的成型。
工艺流程:1、成型前的准备;2、注射过程;3、制品的后处理。
1、成型前的准备为了使注射成型顺利进行和保证制品质量,生产前需要进行原料预处理、清洗机筒、预热嵌件和选择脱模剂等一系列准备工作。
2、注射过程注射过程一般包括:加料——塑化——注射——冷却——脱模。
加料:由于注射成型是一个间歇过程,因而需定量(定容)加料,以保证操作稳定,塑料塑化均匀,最终获得高质量的塑件。
塑化:成型物料在注射机机筒内经过加热,压实以及混合等作用,由松散的粉状或粒状固态转变成连续的均化熔体之过程。
注射:柱塞或螺杆从机筒内的计量位置开始,通过注射油缸和活塞施加高压,将塑化好的塑料熔体经过机筒前端的喷嘴和模具中的浇注系统快速送入封闭模腔的过程。
注射又可细分为流动充模、保压补缩、倒流三个阶段。
冷却:当浇注系统的塑料以及冻结后,继续保压已不再需要,因此可退回柱塞或螺杆,卸除料筒内的塑料熔体的压力,并加入新料,同时在模具内通入冷却水、油或空气等冷却介质,对模具进行进一步的冷却,这一阶段称为浇口冻结后的冷却。
实际上冷却过程从塑料熔体注入型腔起就开始了,它包括从充模、保压到脱模前的这一段时间。
脱模:塑件冷却到一定的温度即可开模,在推出机构的作用下将塑件推出模外。
3、制品的后处理1、退火:消除残余应力;2、调湿:使塑件颜色、性能及尺寸得以稳定。
⑶、压延成型:压延成型是将熔融塑化的热塑性塑料通过两个以上的平行异向旋转辊筒间隙,使溶体受到辊筒挤压延展、拉伸而成为具有一定规格尺寸和符合质量要求的连续片状制品,最后经自然冷却成型的方法。