软件定义PLC——工业互联网时代控制系统的技术变革
PLC的工业控制系统的设计与实现
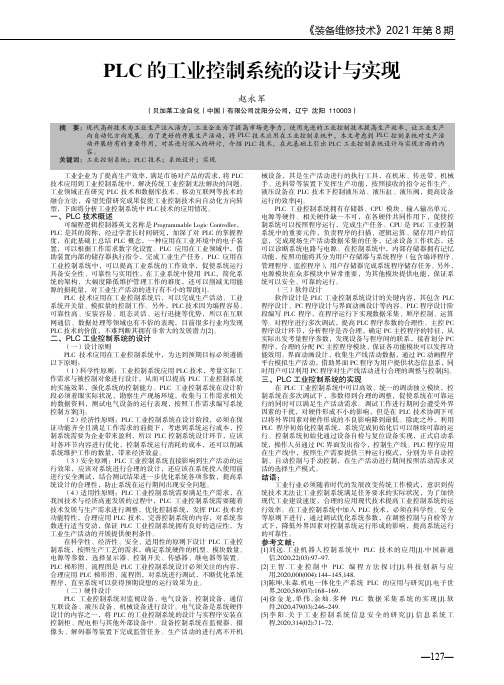
《装备维修技术》2021年第8期—127—PLC 的工业控制系统的设计与实现赵永军(贝加莱工业自化(中国)有限公司沈阳分公司,辽宁 沈阳 110003)工业企业为了提高生产效率,满足市场对产品的需求,将PLC 技术应用到工业控制系统中,解决传统工业控制无法解决的问题。
工业领域正在研究PLC 技术和数据库技术、移动互联网等技术的融合方法,希望凭借研究成果促使工业控制技术向自动化方向转型,下面将分析工业控制系统中PLC 技术的应用情况。
一、PLC 技术概述可编程逻辑控制器英文名称是Programmable Logic Controller,PLC 是其的简称,经过学者长时间研究,加深了对PLC 的掌握程度,在此基础上总结PLC 概念,一种应用在工业环境中的电子装置,可以根据工作需求数字化设置。
PLC 应用在工业领域中,借助装置内部的储存器执行指令,完成工业生产任务。
PLC 应用在工业控制系统中,可以提高工业系统的工作效率,促使系统运行具备安全性、可靠性与实用性,在工业系统中使用PLC,简化系统的架构,大幅度降低维护管理工作的难度,还可以削减无用能源的损耗量,对工业生产活动的进行有不小的帮助[1]。
PLC 技术应用在工业控制系统后,可以完成生产活动、工业系统开关量、模拟量的控制工作。
另外,PLC 技术因为编程容易、可靠性高、安装容易、组态灵活、运行迅捷等优势,所以在互联网通信、数据处理等领域也有不俗的表现,目前很多行业均发现PLC 技术的价值,不难判断其拥有非常大的发展潜力[2]。
二、PLC 工业控制系统的设计(一)设计原则 PLC 技术应用在工业控制系统中,为达到预期目标必须遵循以下原则: (1)科学性原则:工业控制系统应用PLC 技术,考量实际工作需求与被控制对象进行设计,从而可以提高PLC 工业控制系统的实施效果,强化系统的控制能力。
PLC 工业控制系统在设计阶段必须着眼实际状况,勘察生产现场环境,收集与工作需求相关的数据资料,测试电气设备的运行表现,按照工作需求编写系统控制方案[3]。
工控系统发展历程简述

工控系统发展历程简述工控系统是指用于监视和控制工业过程的计算机系统,它将传感器、执行器、控制器和网络等设备连接起来,实现对工业生产过程的自动化控制。
工控系统的发展历程可以追溯到20世纪40年代的自动化控制。
20世纪40年代至60年代,随着计算机技术的发展和应用,工业自动化开始兴起。
这一时期主要是以逻辑控制器(PLC)为核心的控制系统,PLC能够根据预设的逻辑程序对生产过程进行控制。
此时的工控系统主要以硬连线为主,控制器和执行器的连接直接通过硬电缆完成。
进入70年代,随着微电子技术的进步,计算机成为工业自动化领域中的关键设备。
工控系统开始使用分散式控制器(DCS)和远程输入输出(RIO)模块,实现了控制器和执行器之间的远程通信和数据交互。
此时的工控系统开始实现了分层架构,可以对多个工艺过程进行集中控制。
80年代至90年代,工控系统得到了进一步的发展。
随着计算机网络的普及和应用,工控系统开始采用以太网作为通信手段,实现了工控网络的建立。
这一时期,工控系统实现了更高级的控制策略,如模糊控制和遗传算法等,提升了控制系统的性能和精度。
进入21世纪,工控系统开始朝着更加智能化、数字化和网络化发展。
工业互联网的概念提出,工控系统开始采用云计算、大数据和物联网等新技术,实现工业设备的远程监控和管理。
此时的工控系统不仅能够实时采集和处理传感器数据,还可以通过云平台进行数据分析和优化控制。
随着工业自动化的发展和应用,工控系统在各个行业的应用越来越广泛。
例如,工控系统在汽车制造业中实现了自动化生产线的建立和运营;在能源领域,工控系统实现了电力、石油和天然气等资源的有效利用和控制;在化工行业,工控系统实现了化工生产的安全和高效。
总的来说,工控系统在过去几十年中经历了从硬连线控制到分散控制再到网络控制的发展过程。
随着计算机技术、网络技术和传感器技术的不断进步,工控系统将会越来越智能化、数字化和网络化,为工业生产带来更高效、安全和可持续的发展。
IPC和PLC概述
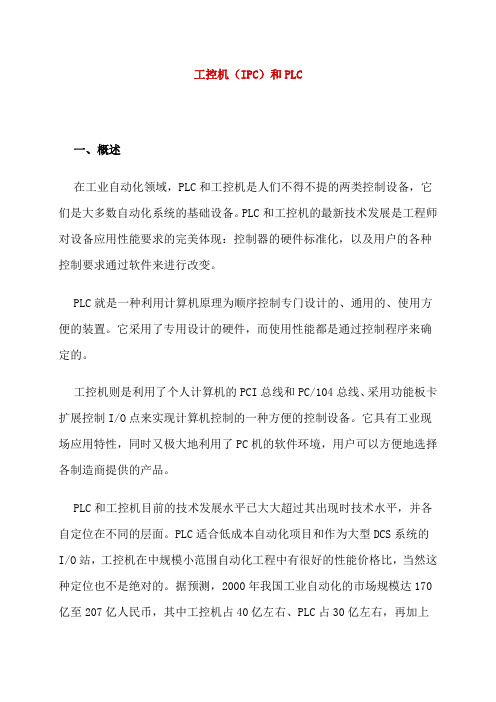
工控机(IPC)和PLC一、概述在工业自动化领域,PLC和工控机是人们不得不提的两类控制设备,它们是大多数自动化系统的基础设备。
PLC和工控机的最新技术发展是工程师对设备应用性能要求的完美体现:控制器的硬件标准化,以及用户的各种控制要求通过软件来进行改变。
PLC就是一种利用计算机原理为顺序控制专门设计的、通用的、使用方便的装置。
它采用了专用设计的硬件,而使用性能都是通过控制程序来确定的。
工控机则是利用了个人计算机的PCI总线和PC/104总线、采用功能板卡扩展控制I/O点来实现计算机控制的一种方便的控制设备。
它具有工业现场应用特性,同时又极大地利用了PC机的软件环境,用户可以方便地选择各制造商提供的产品。
PLC和工控机目前的技术发展水平已大大超过其出现时技术水平,并各自定位在不同的层面。
PLC适合低成本自动化项目和作为大型DCS系统的I/O站,工控机在中规模小范围自动化工程中有很好的性能价格比,当然这种定位也不是绝对的。
据预测,2000年我国工业自动化的市场规模达170亿至207亿人民币,其中工控机占40亿左右、PLC占30亿左右,再加上DCS系统、FCS系统和NCC系统(占60亿)中使用的PLC和工控机,可以看出其在工业自动化领域中举足轻重的作用。
这两类控制设备在各领域的自动化中扮演了不可缺少的角色。
图1给出了某自来水厂工业控制系统的典型结构图,其中采用了PLC作为I/O控制站、工控机作为监控机。
图1 工业控制系统的典型结构图目前,PLC的主流厂商有A-B、Siemens和Modicon等。
工控机的主流厂商有上海康泰克、北京康拓和研华、艾讯等。
PLC和工控机在其技术发展的历程中,为了适合工业现场应用的需要和用户二次开发的需要,都积极地发展高可靠性、网络化和高性能的用户开发软件方面的技术性能。
以下将重点介绍PLC和工控机在硬件、软件和网络方面技术应用现状和发展趋势。
二、PLC和工控机的硬件技术现状和发展PLC和工控机的最终用户为冶金、采矿、水泥、石油、化工、电力、机械制造、汽车、装卸、造纸、纺织、环保等行业,其主要的用途为:1、顺序控制顺序控制是应用最广泛的领域,它包括单机控制、多机群控制、自动生产线控制,如注塑机、印刷机械、订书机械、切纸机械、组合机床、磨床、装配机械、包装生产、电镀流水线和电梯控制等。
PLC
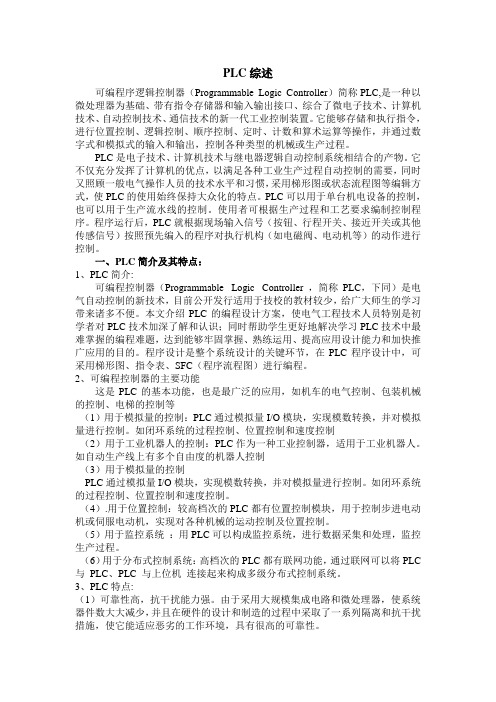
PLC综述可编程序逻辑控制器(Programmable Logic Controller)简称PLC,是一种以微处理器为基础、带有指令存储器和输入输出接口、综合了微电子技术、计算机技术、自动控制技术、通信技术的新一代工业控制装置。
它能够存储和执行指令,进行位置控制、逻辑控制、顺序控制、定时、计数和算术运算等操作,并通过数字式和模拟式的输入和输出,控制各种类型的机械或生产过程。
PLC是电子技术、计算机技术与继电器逻辑自动控制系统相结合的产物。
它不仅充分发挥了计算机的优点,以满足各种工业生产过程自动控制的需要,同时又照顾一般电气操作人员的技术水平和习惯,采用梯形图或状态流程图等编辑方式,使PLC的使用始终保持大众化的特点。
PLC可以用于单台机电设备的控制,也可以用于生产流水线的控制。
使用者可根据生产过程和工艺要求编制控制程序。
程序运行后,PLC就根据现场输入信号(按钮、行程开关、接近开关或其他传感信号)按照预先编入的程序对执行机构(如电磁阀、电动机等)的动作进行控制。
一、PLC简介及其特点:1、PLC简介:可编程控制器(Programmable Logic Controller ,简称PLC,下同)是电气自动控制的新技术,目前公开发行适用于技校的教材较少,给广大师生的学习带来诸多不便。
本文介绍PLC的编程设计方案,使电气工程技术人员特别是初学者对PLC技术加深了解和认识;同时帮助学生更好地解决学习PLC技术中最难掌握的编程难题,达到能够牢固掌握、熟练运用、提高应用设计能力和加快推广应用的目的。
程序设计是整个系统设计的关键环节,在PLC程序设计中,可采用梯形图、指令表、SFC(程序流程图)进行编程。
2、可编程控制器的主要功能这是PLC的基本功能,也是最广泛的应用,如机车的电气控制、包装机械的控制、电梯的控制等(1)用于模拟量的控制:PLC通过模拟量I/O模块,实现模数转换,并对模拟量进行控制。
如闭环系统的过程控制、位置控制和速度控制(2)用于工业机器人的控制:PLC作为一种工业控制器,适用于工业机器人。
(完整)工业控制系统的历史沿革及发展方向
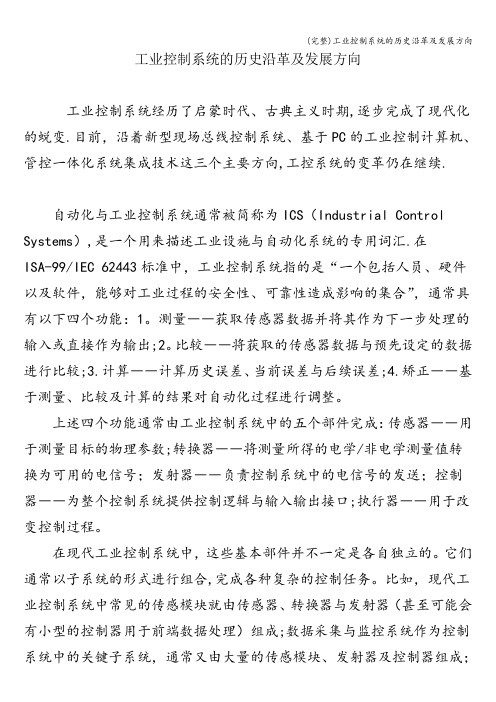
工业控制系统的历史沿革及发展方向工业控制系统经历了启蒙时代、古典主义时期,逐步完成了现代化的蜕变.目前,沿着新型现场总线控制系统、基于PC的工业控制计算机、管控一体化系统集成技术这三个主要方向,工控系统的变革仍在继续.自动化与工业控制系统通常被简称为ICS(Industrial Control Systems),是一个用来描述工业设施与自动化系统的专用词汇.在ISA-99/IEC 62443标准中,工业控制系统指的是“一个包括人员、硬件以及软件,能够对工业过程的安全性、可靠性造成影响的集合”,通常具有以下四个功能:1。
测量――获取传感器数据并将其作为下一步处理的输入或直接作为输出;2。
比较――将获取的传感器数据与预先设定的数据进行比较;3.计算――计算历史误差、当前误差与后续误差;4.矫正――基于测量、比较及计算的结果对自动化过程进行调整。
上述四个功能通常由工业控制系统中的五个部件完成:传感器――用于测量目标的物理参数;转换器――将测量所得的电学/非电学测量值转换为可用的电信号;发射器――负责控制系统中的电信号的发送;控制器――为整个控制系统提供控制逻辑与输入输出接口;执行器――用于改变控制过程。
在现代工业控制系统中,这些基本部件并不一定是各自独立的。
它们通常以子系统的形式进行组合,完成各种复杂的控制任务。
比如,现代工业控制系统中常见的传感模块就由传感器、转换器与发射器(甚至可能会有小型的控制器用于前端数据处理)组成;数据采集与监控系统作为控制系统中的关键子系统,通常又由大量的传感模块、发射器及控制器组成;而可编程逻辑控制器,通常集成了发射器与控制器,用于具体工业过程的控制.现代工业控制系统就是由各种传感器、控制器、执行器以及各种具有具体功能的子系统构成的具有复杂结构的控制网络。
就像罗马并不是一天建成的,现代工业控制系统也经历了启蒙时代、古典主义时期才完成现代化的蜕变。
历经三个重要历史时期启蒙时代:1935年之前工业控制系统作为工厂流程的一部分出现在世人面前大约是在十八世纪中期,但事实上,古代的希腊人与阿拉伯人就已经开始在诸如水钟、油灯这样的装置中使用浮动阀门进行自动控制了.世界上第一台有记载的自动控制设备是公元前二百五十年左右埃及人所使用的水钟.这台水钟以水作为动力进行计时与矫正,将世界最准确计时工具的头衔保持了将近两千年,直到摆钟被发明。
PLC发展历史

PLC发展历史PLC,即可编程逻辑控制器(Programmable Logic Controller),是一种专门用于工业自动化控制的电子设备。
它通过编程来实现自动化控制,广泛应用于工厂、机械设备、交通系统等领域。
下面将详细介绍PLC的发展历史。
1. 早期自动化控制系统在20世纪60年代之前,工厂和机械设备的控制主要依靠电气继电器和电路来完成。
这种控制方式存在着路线复杂、维护难点、可靠性低等问题,无法满足快速变化的生产需求。
2. 第一代PLC的浮现20世纪60年代末,PLC问世,标志着自动化控制进入了一个新的时代。
第一代PLC由德国西门子公司研发,它采用了数字电子技术和微处理器,通过编程来实现控制功能。
与传统的继电器控制相比,PLC具有编程灵便、可靠性高、易于维护等优势。
3. PLC的发展与应用扩展随着技术的不断进步,PLC在20世纪70年代得到了广泛的应用。
PLC的功能不断增强,支持更复杂的控制逻辑和更多的输入输出点。
同时,PLC的体积也不断减小,成本逐渐降低,使得更多的企业和行业能够采用PLC进行自动化控制。
4. PLC的网络化与开放性20世纪80年代,PLC开始向网络化和开放性发展。
PLC可以通过通信接口与其他设备进行数据交换,实现了分布式控制和远程监控。
此外,PLC的编程环境也得到了改善,采用了更友好的图形化编程界面,使得工程师能够更方便地进行编程和调试。
5. PLC的智能化与集成化21世纪初,PLC进一步智能化和集成化。
PLC开始支持更多的通信协议和网络标准,能够与其他自动化设备实现无缝对接。
此外,PLC还具备了更强大的计算和处理能力,能够处理更复杂的控制算法和任务。
6. PLC的未来发展趋势随着工业4.0和物联网的兴起,PLC的发展前景非常广阔。
未来,PLC将更加注重与云计算、大数据、人工智能等先进技术的结合,实现更智能、更高效的自动化控制。
同时,PLC还将进一步提升在安全性、可靠性和可维护性等方面的性能,以满足不断变化的工业需求。
PLC发展历史
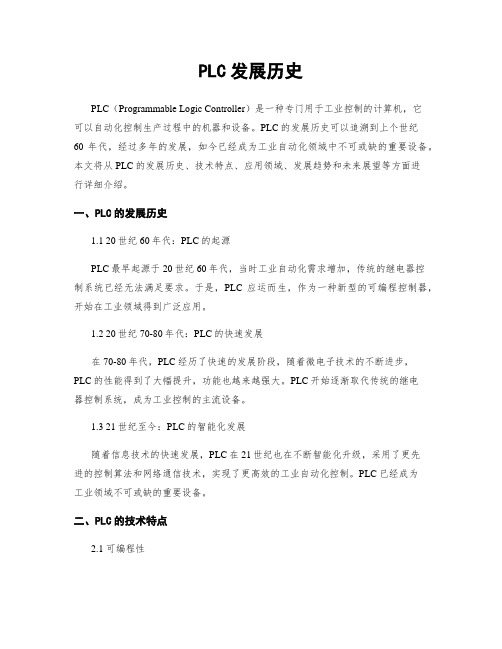
PLC发展历史PLC(Programmable Logic Controller)是一种专门用于工业控制的计算机,它可以自动化控制生产过程中的机器和设备。
PLC的发展历史可以追溯到上个世纪60年代,经过多年的发展,如今已经成为工业自动化领域中不可或缺的重要设备。
本文将从PLC的发展历史、技术特点、应用领域、发展趋势和未来展望等方面进行详细介绍。
一、PLC的发展历史1.1 20世纪60年代:PLC的起源PLC最早起源于20世纪60年代,当时工业自动化需求增加,传统的继电器控制系统已经无法满足要求。
于是,PLC应运而生,作为一种新型的可编程控制器,开始在工业领域得到广泛应用。
1.2 20世纪70-80年代:PLC的快速发展在70-80年代,PLC经历了快速的发展阶段,随着微电子技术的不断进步,PLC的性能得到了大幅提升,功能也越来越强大。
PLC开始逐渐取代传统的继电器控制系统,成为工业控制的主流设备。
1.3 21世纪至今:PLC的智能化发展随着信息技术的快速发展,PLC在21世纪也在不断智能化升级,采用了更先进的控制算法和网络通信技术,实现了更高效的工业自动化控制。
PLC已经成为工业领域不可或缺的重要设备。
二、PLC的技术特点2.1 可编程性PLC具有很强的可编程性,用户可以通过编程软件对PLC进行程序设计和逻辑控制,实现各种复杂的控制功能。
PLC的可编程性使得工业控制更加灵活和高效。
2.2 实时性PLC具有很高的实时性,能够实时监测和响应生产过程中的各种信号和事件,保证工业生产的稳定性和可靠性。
实时性是PLC在工业控制中的重要特点之一。
2.3 可靠性PLC具有很高的可靠性,采用了工业级的硬件和软件设计,能够在恶劣环境下稳定运行,保证工业生产的连续性和安全性。
可靠性是PLC在工业控制中的重要优势之一。
三、PLC的应用领域3.1 制造业在制造业领域,PLC被广泛应用于各种生产线和机械设备的控制,如汽车制造、电子制造、食品加工等领域,实现了生产过程的自动化和智能化。
可编程控制器的发展趋势PLC的发展趋势
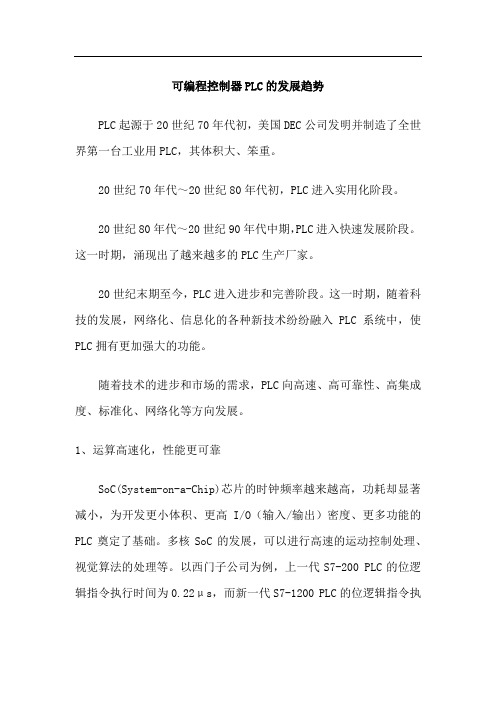
可编程控制器PLC的发展趋势PLC起源于20世纪70年代初,美国DEC公司发明并制造了全世界第一台工业用PLC,其体积大、笨重。
20世纪70年代~20世纪80年代初,PLC进入实用化阶段。
20世纪80年代~20世纪90年代中期,PLC进入快速发展阶段。
这一时期,涌现出了越来越多的PLC生产厂家。
20世纪末期至今,PLC进入进步和完善阶段。
这一时期,随着科技的发展,网络化、信息化的各种新技术纷纷融入PLC系统中,使PLC拥有更加强大的功能。
随着技术的进步和市场的需求,PLC向高速、高可靠性、高集成度、标准化、网络化等方向发展。
1、运算高速化,性能更可靠SoC(System-on-a-Chip)芯片的时钟频率越来越高,功耗却显著减小,为开发更小体积、更高I/O(输入/输出)密度、更多功能的PLC奠定了基础。
多核SoC的发展,可以进行高速的运动控制处理、视觉算法的处理等。
以西门子公司为例,上一代S7-200 PLC的位逻辑指令执行时间为0.22μs,而新一代S7-1200 PLC的位逻辑指令执行时间仅为0.1μs。
有些PLC甚至可以达到ns级别。
不少PLC生产厂家采用了多CPU(中央处理器)并行处理方式。
当前,PLC的抗干扰能力和可靠性已经非常完善,但随着应用环境越来越复杂,用户对PLC的抗干扰能力也提出了更高的要求。
统计表明,在所有故障中,CPU和I/O口故障仅占两成,其余都为外部故障,其中传感器故障为45%、执行器故障为30%、接线故障为5%。
另外,许多厂商的PLC都提供故障诊断功能,大大提高了系统的故障自诊断和处理能力。
2、高度集成化、模块化、小型化现在的PLC产品体积更小、功耗更低、功能更强。
近几年,很多PLC生产厂家推出了超小型PLC,用于单机自动控制或组建分布式控制系统。
例如西门子公司的LOGO!系列PLC,将CPU、I/O模块、操作显示单元集成到一起。
此外,很多原先需要扩展的功能如PROFINET 也被集成到CPU模块上,使系统成本大大降低。
plc在工业自动化控制领域中的应用及发展

plc在工业自动化控制领域中的应用及发展一、引言随着工业自动化的发展,PLC(可编程逻辑控制器)已经成为工业自动化控制领域中不可或缺的一部分。
本文将从PLC的定义、应用领域、发展历程、技术特点等方面进行详细介绍。
二、PLC的定义PLC是一种数字式,以工业现场为中心的控制器。
它通过数字计算机技术,对各种生产设备进行控制和监测,实现生产过程中的自动化控制。
三、PLC的应用领域1. 工厂自动化:在工厂生产线中,PLC可以对各种设备进行控制和监测,实现生产过程中的自动化控制。
2. 机床自动化:在机床加工过程中,PLC可以实现对各种设备进行精确的控制和监测。
3. 汽车生产线:在汽车生产线上,PLC可以对各种机器人进行精确的控制和监测。
4. 化工行业:在化工行业中,PLC可以对各种反应釜等设备进行精确的控制和监测。
5. 石油行业:在石油行业中,PLC可以对各种设备进行控制和监测,实现油田的自动化控制。
四、PLC的发展历程20世纪60年代,PLC开始在工业自动化领域中应用。
当时,PLC主要用于控制和监测生产线上的各种设备。
20世纪70年代,PLC开始普及,并逐渐取代了传统的继电器控制系统。
此时,PLC已经具有了更高的可靠性和精确性。
20世纪80年代,PLC开始大规模应用于各种工业自动化领域。
同时,PLC也得到了更加完善的技术支持。
21世纪初期,随着数字技术的不断发展和进步,PLC得到了更加广泛的应用。
五、PLC的技术特点1. 可编程性:PLC可以根据不同的控制需求进行编程,实现不同的控制功能。
2. 稳定性:由于采用数字电路技术,PLC具有更高的稳定性和可靠性。
3. 精确性:PLC可以对各种设备进行精确的控制和监测。
4. 扩展性:PLC可以通过扩展模块来扩展其功能。
5. 易维护性:PLC的故障排除和维护比传统的继电器控制系统更加容易。
6. 可编程性:PLC可以根据不同的控制需求进行编程,实现不同的控制功能。
六、PLC未来的发展趋势1. 智能化:未来,PLC将会变得更加智能化,可以通过人工智能等技术来实现更加高级的控制功能。
软plc的概念

软plc的概念软PLC (软件可编程逻辑控制器) 是一种基于软件的逻辑控制器,它能够在计算机上运行,并用软件模拟硬件PLC的功能。
软PLC通常与工业自动化系统和控制系统一起使用,用于监控和控制工业过程中的各种设备和机器。
软PLC的概念和发展软PLC的概念最早出现在20世纪80年代,当时计算机技术的发展使得人们开始尝试利用计算机进行自动化控制。
与硬PLC相比,软PLC具有更高的灵活性和可扩展性,因为它是基于软件的,可以在计算机上运行,而不是依赖于硬件设备。
软PLC的发展经历了几个重要的阶段。
最早期的软PLC是通过编写专门的控制程序,并在计算机上运行来实现的。
这种方法使用通用计算机来模拟PLC的硬件功能,但是由于计算机系统的软硬件差异,不适用于实时控制和高速数据处理。
然后,在20世纪90年代,随着计算机技术的进一步发展,一些厂商开始开发专门的软PLC软件,用于模拟PLC的各种功能。
这些软件通常具有实时控制和高速数据处理的能力,并且能够与外部设备进行实时通信。
近年来,随着嵌入式系统和物联网技术的进一步发展,软PLC的功能和应用领域也在不断扩展。
现代软PLC通常具有用于处理高速输入输出信号的专用硬件接口,以及用于与其他设备和系统进行通信的网络接口。
此外,软PLC还可以集成到云端平台上,实现远程监控和控制。
软PLC的特点和优势软PLC相较于硬PLC有一些明显的特点和优势:1. 灵活性和可扩展性:由于软PLC是基于软件的,其功能可以根据需要进行定制和扩展。
用户可以通过编写定制的控制程序来满足不同的应用需求。
此外,软PLC还可以方便地与其他软件系统和设备进行集成,实现更复杂的控制和监控功能。
2. 易于编程和调试:与硬PLC相比,软PLC通常提供更友好和直观的编程接口,使得编写和调试控制程序更加容易。
软PLC通常使用类似于传统编程语言的结构化文本语言或图形化编程工具,如函数块图(FBD)或梯形图(LD),使得工程师可以更快捷地开发和修改控制逻辑。
工业控制系统的技术发展和趋势

工业控制系统的技术发展和趋势工业控制系统是一个为工业生产自动化服务的重要技术领域,它的发展历程始于上世纪50年代,并在不断地演化和创新中得到不断地提升和完善。
随着科技和物联网技术的发展,工业控制系统也在不断地进化,变得更加智能化和灵活化。
本文将从技术发展和趋势方面谈谈工业控制系统的发展历程和未来趋势。
一、工业控制系统的发展历程1. 传统PLC控制传统的工控系统由工控计算机和PLC组成,工控计算机主要负责人机界面,数据采集、联机控制和数据处理等任务,而PLC负责现场控制操作。
PLC控制作为现代工业控制领域最早的编程化控制系统之一,具有建设周期短、维护方便、可靠性高等优势,成为了现代工业控制领域最主流的应用之一。
但是,PLC控制在大型或复杂的工业控制系统中,灵活性不足,很难实现分布式计算和复杂算法实现。
2. DCS随后,随着工业控制领域的不断发展和智能化趋势,DCS(分布式控制系统)等控制策略应运而生。
DCS控制针对大型复杂工业系统,其主要优点在于强大的控制能力、多点测量、多点操作,其相对于PLC控制而言为一种灵活高效的分布式控制方法,而且DCS可以方便的实现大规模的集群控制,是工业控制系统的发展之一。
3. PC控制现代工业控制系统中,随着工控技术的不断进步和计算机性能的不断提高,基于PC控制的技术应运而生。
它基于通用计算机平台,摆脱了传统的特殊硬件和编程方式,使得整个系统的开发成本大大降低,同时也提高了整个系统的可定制性和可升级性。
4. 大数据大数据技术的发展给现代工业控制系统带来了重要影响。
在控制系统中,消息传递和大数据分析应用价值非常高,可以利用大数据技术来分析工业控制中的各种问题,包括控制精度、稳定性、系统故障等,有效提高工业生产的效率和质量。
二、工业控制系统的未来趋势1. 智能化化、网络化、集成化现代工业控制要实现智能化,那么工业控制系统就需要更加智能。
随着制造业的深入开展,自动化成为未来产业中一项不可或缺的技术,未来工业控制系统将向网络化、智能化、集成化的方向发展,将很多机器和设备的信息通过物联网或其他技术进行互联,以实现更加丰富、精准、可靠的处理和控制,以达到更好的结果。
PLC控制系统概述
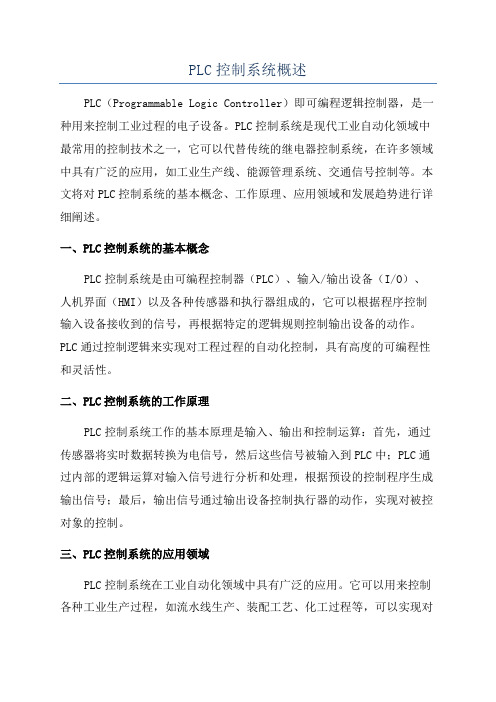
PLC控制系统概述PLC(Programmable Logic Controller)即可编程逻辑控制器,是一种用来控制工业过程的电子设备。
PLC控制系统是现代工业自动化领域中最常用的控制技术之一,它可以代替传统的继电器控制系统,在许多领域中具有广泛的应用,如工业生产线、能源管理系统、交通信号控制等。
本文将对PLC控制系统的基本概念、工作原理、应用领域和发展趋势进行详细阐述。
一、PLC控制系统的基本概念PLC控制系统是由可编程控制器(PLC)、输入/输出设备(I/O)、人机界面(HMI)以及各种传感器和执行器组成的,它可以根据程序控制输入设备接收到的信号,再根据特定的逻辑规则控制输出设备的动作。
PLC通过控制逻辑来实现对工程过程的自动化控制,具有高度的可编程性和灵活性。
二、PLC控制系统的工作原理PLC控制系统工作的基本原理是输入、输出和控制运算:首先,通过传感器将实时数据转换为电信号,然后这些信号被输入到PLC中;PLC通过内部的逻辑运算对输入信号进行分析和处理,根据预设的控制程序生成输出信号;最后,输出信号通过输出设备控制执行器的动作,实现对被控对象的控制。
三、PLC控制系统的应用领域PLC控制系统在工业自动化领域中具有广泛的应用。
它可以用来控制各种工业生产过程,如流水线生产、装配工艺、化工过程等,可以实现对工业设备的自动化控制。
此外,PLC控制系统还用于能源管理系统、交通信号控制、建筑物自动化等领域。
四、PLC控制系统的发展趋势随着科技的不断发展,PLC控制系统也在不断演进。
一方面,PLC的性能逐渐提升,从最初的16位到现在的32位和64位,处理能力和存储容量大大增加,可以处理更复杂的控制任务;另一方面,PLC逐渐融入各种网络通信技术,如以太网、无线通信等,实现与其他系统的互联互通;此外,PLC控制系统的人机界面也在不断改进,从最初的LED数码显示器到现在的触摸屏、工控机等,提高了操作和监控的便利性。
软件定义控制与流程工业互联网解决方案

超融合、微内核、高实时、高可靠、全自主
SaaS:工业 APP
工业大数据
人工智能
云平台 IaaS/PaaS
第三方 工业互联 网平台
第三方 工业互联 网平台
运行环境0
运行环境1
运行环境2
MaVIE W
KySCADA
PLC/DCS运行时
安 全
Window s
Linux
IEC61131
机
制
非实时系统
实时系统
摄像头 远程IO 机器人
电表
AUTBUS
热表
传感器
工业控制基础 • MaVIEW
软件
操作系统
• Intewell 工业互联 网操作系统
互联互通
• AUTBUS芯片 • TSN • 5G • 交换芯片/PHY芯片
软件定义控制方案获首届中国工业互联网大赛一等奖
2019年12月,工信部指导1009个作品参加角逐,东土科技“软件定义工业控制”工业互联网解决方案获 得最高荣誉一等奖,阐述了基于软件定义控制的工业服务器跨行业应用的能力,辅以芯片、总线、操作系 统、控制逻辑、工业应用全部自主可控,展现了东土科技工业底层技术突破的创新力量
微内核架构,可验证性高、可靠性高,可以进行 形式化验证特别适合安全关键系统
实时性性能优异 可靠性经久验证,高可靠余度设计业界领先 工信部电子五所扫描关键模块源码自主率100%,
Level 2: 操作层 SCADA/DCS/MES/SIS
Level1: 控制层 PLC/DCS/HMI/IPC
Level 0: 现场层 现场仪表/传感器/ 电机/变频器
工业各个行业控制软件 制造执行系统 全景可视化管理 资产健康管理
基于PLC的工业控制系统的设计与实现

基于PLC的工业控制系统的设计与实现一、本文概述在当前工业化生产日益智能化、自动化的背景下,设计与实现一套基于可编程逻辑控制器(PLC)的工业控制系统具有重要的实践意义和理论价值。
本文旨在全面探讨基于PLC的工业控制系统的设计原理、关键技术及其实际应用过程。
研究工作首先从梳理PLC的基本原理和功能特性入手,深入剖析其在控制领域中的核心地位,以及如何适应不同工业环境下的复杂控制需求。
本文系统地阐述了工业控制系统的设计思路,涵盖了系统架构设计、硬件选型配置、软件编程策略以及网络通信技术等方面。
在设计阶段,我们将详细介绍如何结合生产工艺流程,利用PLC的模块化和灵活性优势构建可靠且高效的控制方案。
在实现环节,将进一步探讨如何通过梯形图、结构文本等编程语言实现控制逻辑,并采用先进的故障诊断与安全防护措施确保系统的稳定运行。
全文将以具体的实际案例为依托,展示基于PLC的工业控制系统从设计规划到实施调试的全过程,旨在为相关领域的工程技术人员提供一套完整的、具有指导意义的设计方法和实践经验。
同时,通过对现有技术的总结和展望,本文还将对PLC在工业0及智能制造背景下的发展趋势和挑战进行探讨,以期推动我国工业自动化水平的不断提二、技术概述在进入基于PLC的工业控制系统的设计与实现之前,首先需要了解一些关键技术。
PLC,即可编程逻辑控制器,是一种广泛应用于工业控制系统中的数字化运算控制器。
它采用一类可编程的存储器,用于存储指令,执行逻辑运算,顺序控制,定时、计数和算术操作等面向用户的指令。
本节将重点概述PLC技术、工业控制系统设计的基本原则以及实现这些系统时常用的技术。
可靠性高:PLC采用了一系列的硬件和软件抗干扰措施,能在恶劣环境下稳定运行。
灵活性强:通过改变编程,PLC能适应不同的控制要求,具有良好的灵活性和扩展性。
需求导向:系统设计应以实际工业需求为出发点,确保系统功能满足生产需求。
经济高效:在满足功能需求的前提下,尽可能降低成本,提高系统效率。
PLC在工业控制中的应用
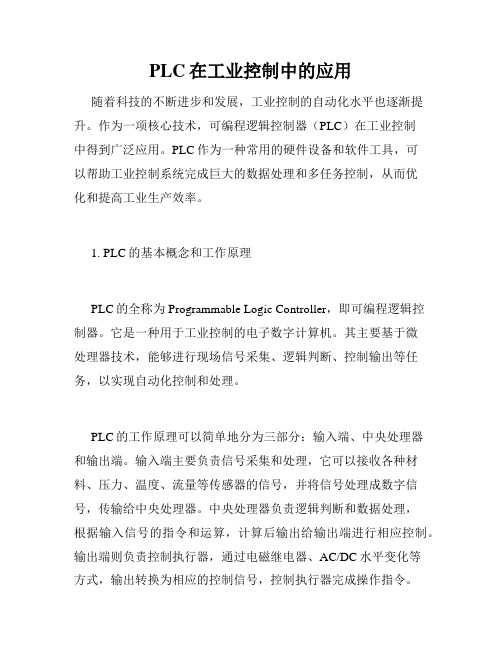
PLC在工业控制中的应用随着科技的不断进步和发展,工业控制的自动化水平也逐渐提升。
作为一项核心技术,可编程逻辑控制器(PLC)在工业控制中得到广泛应用。
PLC作为一种常用的硬件设备和软件工具,可以帮助工业控制系统完成巨大的数据处理和多任务控制,从而优化和提高工业生产效率。
1. PLC的基本概念和工作原理PLC的全称为Programmable Logic Controller,即可编程逻辑控制器。
它是一种用于工业控制的电子数字计算机。
其主要基于微处理器技术,能够进行现场信号采集、逻辑判断、控制输出等任务,以实现自动化控制和处理。
PLC的工作原理可以简单地分为三部分:输入端、中央处理器和输出端。
输入端主要负责信号采集和处理,它可以接收各种材料、压力、温度、流量等传感器的信号,并将信号处理成数字信号,传输给中央处理器。
中央处理器负责逻辑判断和数据处理,根据输入信号的指令和运算,计算后输出给输出端进行相应控制。
输出端则负责控制执行器,通过电磁继电器、AC/DC水平变化等方式,输出转换为相应的控制信号,控制执行器完成操作指令。
2. PLC的优点和特点PLC在工业控制中的应用具有很多优点和特点,其最主要的特点在于可编程性和实时控制性。
可编程性:PLC系统可以根据实际需要进行编程,设计出适合不同需求的程序,以满足不同的运行环境和需求。
该特点使得PLC在不同的工业控制环境下得到广泛应用,并可以适应复杂和多变的控制要求。
实时性:PLC的数据处理速度和控制反应速度非常快,可以实现实时控制和数据处理。
在自动化控制系统中,这种实时性可以实现协调各个执行单元之间的配合,提高系统的稳定性和可靠性。
其他优点和特点还包括:PLC系统具有稳定性高、可靠性强、维护管理方便、易于修改和升级等等,这些特点在公司的生产系统和设备故障排除中都有重要的作用。
3. PLC在工业控制中广泛应用于各种自动化系统,其具体应用包括以下几个方面:(1) 生产线自动化生产线自动化是PLC最常见的应用场景。
PLC的定义和概念

PLC的定义和概念PLC(Programmable Logic Controller)又称为可编程逻辑控制器,是一种数字电子仪器,具有自主控制和程序控制的功能。
PLC广泛应用于工业生产中,被称为工业控制的“心脏”,在自动化生产线、工业机器人、制造业以及航空航天等领域中发挥着越来越重要的作用。
PLC的历史可以追溯到20世纪60年代,当时受到美国汽车工业的需求影响,工程师发明了PLC以满足对自动化控制的需求。
PLC最初的任务是对汽车生产线进行控制,通过预先设定的程序来控制生产线上的机械和电器设备的运行,从而提高生产效率。
现在,PLC已经成为自动化生产和物流系统中的重要组件,它是一个数字控制器,可以根据特定的程序控制输入和输出,执行各种控制任务,包括监测、诊断、数据采集、故障排除等。
PLC的一个重要特点是它具有可编程性,通过编写程序,操作人员可以改变PLC的功能,使其适合不同的操作环境,满足不同的需求。
PLC的结构通常由以下部分组成:输入/输出(I/O)模块、中央处理器(CPU)、电源模块、存储器、通讯模块以及各种辅助模块。
I/O模块是PLC的输入和输出接口,它们接收现场(field)设备的输入信号(如温度、压力等)和送出控制信号(如打开或关闭阀门)。
CPU是PLC的中央处理器,负责执行各种控制算法和运行编写的程序。
存储器用于存储程序和数据,通讯模块用于在不同的PLC之间进行通讯,以实现更复杂的控制任务。
在PLC的辅助模块中,还包括安全模块、定时器、计数器、模拟模块以及触摸屏等。
除了上述基本部件以外,PLC还包括各种编程语言,如梯形图(Ladder Diagram)、函数图(Function Block Diagram)、指令列表(Instruction List)、结构化文本(Structured Text)以及序列图(Sequential Function Chart),这些语言用于编写PLC程序。
PLC的意义及工作原理

PLC的意义及工作原理1、PLC即可编程控制器(Programmable logic Controller,是指以计算机技术为基础的新型工业控制装置。
在1987年国际电工委员会(International Electrical Committee)颁布的PLC标准草案中对PLC做了如下定义:“PLC是一种专门为在工业环境下应用而设计的数字运算操作的电子装置。
它采用可以编制程序的存储器,用来在其内部存储执行逻辑运算、顺序运算、计时、计数和算术运算等操作的指令,并能通过数字式或模拟式的输入和输出,控制各种类型的机械或生产过程。
PLC 及其有关的外围设备都应该按易于与工业控制系统形成一个整体,易于扩展其功能的原则而设计。
”PLC的特点2.1可靠性高,抗干扰能力强高可靠性是电气控制设备的关键性能。
PLC由于采用现代大规模集成电路技术,采用严格的生产工艺制造,内部电路采取了先进的抗干扰技术,具有很高的可靠性。
例如三菱公司生产的F系列PLC平均无故障时间高达30万小时。
一些使用冗余CPU的PLC的平均无故障工作时间则更长。
从PLC的机外电路来说,使用PLC构成控制系统,和同等规模的继电接触器系统相比,电气接线及开关接点已减少到数百甚至数千分之一,故障也就大大降低。
此外,PLC带有硬件故障自我检测功能,出现故障时可及时发出警报信息。
在应用软件中,应用者还可以编入外围器件的故障自诊断程序,使系统中除PLC以外的电路及设备也获得故障自诊断保护。
这样,整个系统具有极高的可靠性也就不奇怪了。
2.2配套齐全,功能完善,适用性强PLC发展到今天,已经形成了大、中、小各种规模的系列化产品。
可以用于各种规模的工业控制场合。
除了逻辑处理功能以外,现代PLC 大多具有完善的数据运算能力,可用于各种数字控制领域。
近年来PLC的功能单元大量涌现,使PLC渗透到了位置控制、温度控制、CNC等各种工业控制中。
加上PLC通信能力的增强及人机界面技术的发展,使用PLC组成各种控制系统变得非常容易。
基于PLC工业控制系统关键技术分析
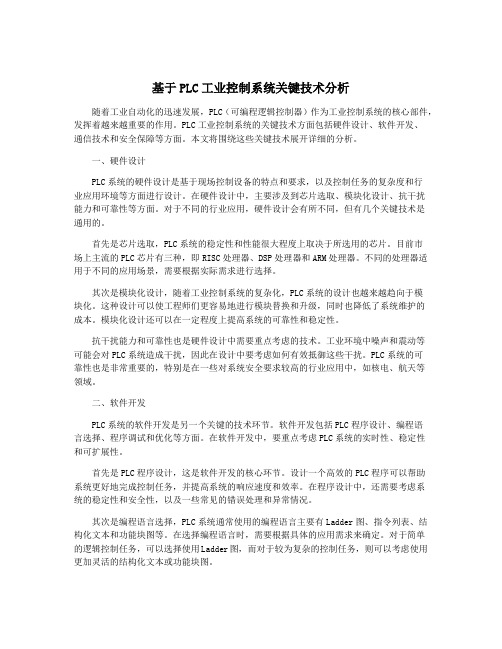
基于PLC工业控制系统关键技术分析随着工业自动化的迅速发展,PLC(可编程逻辑控制器)作为工业控制系统的核心部件,发挥着越来越重要的作用。
PLC工业控制系统的关键技术方面包括硬件设计、软件开发、通信技术和安全保障等方面。
本文将围绕这些关键技术展开详细的分析。
一、硬件设计PLC系统的硬件设计是基于现场控制设备的特点和要求,以及控制任务的复杂度和行业应用环境等方面进行设计。
在硬件设计中,主要涉及到芯片选取、模块化设计、抗干扰能力和可靠性等方面。
对于不同的行业应用,硬件设计会有所不同,但有几个关键技术是通用的。
首先是芯片选取,PLC系统的稳定性和性能很大程度上取决于所选用的芯片。
目前市场上主流的PLC芯片有三种,即RISC处理器、DSP处理器和ARM处理器。
不同的处理器适用于不同的应用场景,需要根据实际需求进行选择。
其次是模块化设计,随着工业控制系统的复杂化,PLC系统的设计也越来越趋向于模块化。
这种设计可以使工程师们更容易地进行模块替换和升级,同时也降低了系统维护的成本。
模块化设计还可以在一定程度上提高系统的可靠性和稳定性。
抗干扰能力和可靠性也是硬件设计中需要重点考虑的技术。
工业环境中噪声和震动等可能会对PLC系统造成干扰,因此在设计中要考虑如何有效抵御这些干扰。
PLC系统的可靠性也是非常重要的,特别是在一些对系统安全要求较高的行业应用中,如核电、航天等领域。
二、软件开发PLC系统的软件开发是另一个关键的技术环节。
软件开发包括PLC程序设计、编程语言选择、程序调试和优化等方面。
在软件开发中,要重点考虑PLC系统的实时性、稳定性和可扩展性。
首先是PLC程序设计,这是软件开发的核心环节。
设计一个高效的PLC程序可以帮助系统更好地完成控制任务,并提高系统的响应速度和效率。
在程序设计中,还需要考虑系统的稳定性和安全性,以及一些常见的错误处理和异常情况。
其次是编程语言选择,PLC系统通常使用的编程语言主要有Ladder图、指令列表、结构化文本和功能块图等。
什么是软PLC
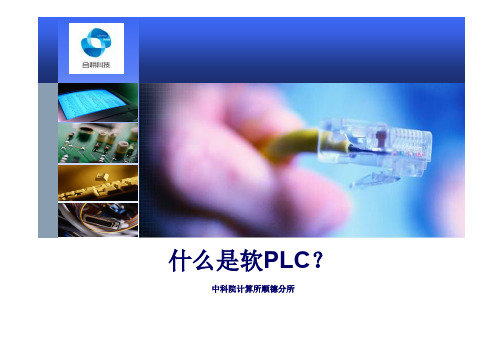
更方便, 更开放
应用特点
有特色
提高速度, 降低成本
①体现了IPC,PLC和DOC先进 技术的集成。可充分利用PC平 台上的硬件和软件资源,使控制 系统更具特色; ②系统更开放,应用更方便。 软件PLC通过自己开发工具提供 的OPC功能和Active控件,既可 连接Office软件,也可连接用 VB,VC开发的软件; ③基于PC+现场总线+分布式 IO的控制系统简化了复杂控制系 统的体系结构,提高了通信效率 和速度,降低了投资成本。
软PLC的技术是基于IEC61131-3标准的,因此在掌握标准语言后开发就比较容易。
LOGO
中科院计算所顺德分所
/hg1875381147 /kingsoftwps/
合耕科技教育学院 合耕教育
技术形成背景
20世纪90年代后期,人们逐渐认识到,传统PLC(本文简称硬PLC)自 身存在着这样那样的缺点:难以构建开放的硬件体系结构;工作人员必须经 过较长时间的专业培训才能掌握某一种产品的编程方法。其特征是:在保留 PLC功能的前提下,采用面向现场总线网络的体系结构,采用开放的通信接 口,如以太网、高速串口等;采用各种相关的国际工业标准和一系列的事实 上的标准;全部用软件来实现传统PLC的功能。
近年来,随着工业控制领域IEC61131-3 标准的制定和实施,一项新的控 制技术——软件PLC 迅速发展。所谓软件PLC,即以通用操作系统和 PC为 软硬件平台,用软件实现传统硬件PLC 的控制功能。或者说,将PLC 的控制 功能封装在软件内,运行于PC环境中。这样的控制系统提供了PLC 的相同 功能,却具备了PC机的各种优点。软件PLC 系统是由开发系统和运行系统 两部分组成,软件PLC 开发系统实际上就是带有编辑、调试和编译的PLC编 程器,其中编译部分是的硬件体系结构不再封闭,用户可以自己选择合适的硬件组成满足要求的 软PLC。
IT和OT融合之下,PLC控制器将如何发展?

IT和OT融合之下,PLC控制器将如何发展?今天我将从一个用户的地角度,来看待现在自动化行业PLC的未来在哪里。
作为一个从业自动化十几年的老司机来说。
不得不说现在的自动化行业已经是“百家争鸣,花开千朵”的情况了。
为什么这么说呢?就在中国迈向制造强国提出来中国制造2025愿景之下,就在德国倡导的工业4.0发起之际,就在美国举起工业互联网大旗之时。
所有的自动化的厂商和行业资深人士全部提出来,一个共同的目标,就是IT和OT融合,IT就是信息技术,OT 就是运营技术(自动化技术)。
这些雨后春笋般的先进的技术理念,超前的解决方案,犹如梨花带雨般毫无顾忌的滋润着国人的对自动化和信息化融合那饥渴的求知欲望。
我希望自动化用户们,理性对待这个知识膨胀的时代。
冷静的坐下来思考一下,你到底需要什么?而自动化产品又能给你什么?切入正题,我们今天就来看一下,做为用户你真正需要的是什么PLC?PLC的功能不想在这里做重复定义,大家基本上每天都在跟它直接和间接打着交道,可以说PLC已经成为自动化行业的代名词之一。
IT和OT在融合的道理上,我给大家提几个思考点,无关乎哪个厂商的产品。
1、PLC的高可靠性。
大家试想一下,PLC近10年在干什么?一直在扩展功能。
而在稳定性上大不如以前。
估计很多厂家人的开始准备手里的板砖了。
不知道有多少人还记得西家的S5,罗家的PLC5,施家的984,那个时代的产品,稳定性极高,现在的产品经常有要求加G3防腐等,在那个时代,什么保护都没有但就是不出故障,一款PLC5在满是碳粉的铝车间运行15年,备件都没有换过,就是不敢拔下来吹扫检修。
那这里是为什么呢?其实那个时代的电路板还不是高度集成,PLC的设计人员需要对电路板和元器件做参数设计和选型,在那个时代这些设计人员都是电路发烧级别,所以当时的PLC的可靠性和稳定性极高,当然价格也是不菲。
但操作的人性化可以说极差,碍于那个时代操作系统的发展背景。
但现在的PLC的可靠性呢?由于高度集成的芯片的出现,现在PLC的电路板很简单了,你打开看一下除了芯片和简单的外围电路没了。
- 1、下载文档前请自行甄别文档内容的完整性,平台不提供额外的编辑、内容补充、找答案等附加服务。
- 2、"仅部分预览"的文档,不可在线预览部分如存在完整性等问题,可反馈申请退款(可完整预览的文档不适用该条件!)。
- 3、如文档侵犯您的权益,请联系客服反馈,我们会尽快为您处理(人工客服工作时间:9:00-18:30)。
软件定义PLC——工业互联网时代控制系统的技术变革“随着云计算,机器学习和大数据等IT技术和工业控制领域OT技术的不断融合,工业互联网和智能制造已经成为未来工业生产的大势所趋。
工业互联网和智能制造赋予了未来制造更大的灵活性,小批量、多品种和可定制这些生产方式也逐渐成为了可能,这也要求现代生产制造的核心技术——工业自动化控制系统更加灵活有扩展性。
”为此,一种基于软件定义的PLC控制系统开始受到业界的关注和重视,甚至被誉为“工业互联网时代的新一代控制系统”。
那么,这是什么样的一种控制系统呢?为何更加适合工业互联网的要求呢?目前的最新进展是什么呢?近日,CONTROL ENGINEERING China采访了国内软件定义控制领导厂商东土科技的常务副总经理刘生富先生,就软件定义的PLC 控制系统做了一个深入的了解。
▎刘生富,东土科技常务副总经理工业互联网亟需更加灵活的控制系统市场竞争的加剧和技术的进步使得现在产品更新换代频繁,产品的生命周期越来越短。
制造业的生产模式随之发生巨大变化,工业互联网和智能制造成为解决从大规模“刚性制造”转向小批量“柔性制造”的必然选择。
工业互联网使得生产数据可以进行规模化集中存储,实现以前不可能实现的大数据,并利用云平台前所未有的计算能力对大数据进行分析,挖掘和优化生产效率。
智能制造使得现场设备、机器和工厂变得“更智能”,能够通过工业网络采集到各类现场数据。
但是在刘生富看来,现在无论是工业互联网还是智能制造,均未对工业控制系统的“大脑”PLC/DCS做出任何更进一步的技术变革,控制的核心PLC不能够灵活扩展,无疑将大大减弱工业控制系统灵活性和可扩展性,从而不能满足工业互联网条件下需要短时间内重新配置生产资源的需求。
同时,随着智能化需求的日益增长,以传统PLC/DCS为代表的第三代控制系统已经不能满足工业智能化的需求。
一方面,现在的控制系统不仅要处理传统的温度、压力、流量和液位等四大传感信号,而且还要能够处理视觉、语音等以前没有的信号,要支持5G等无线通信,这些对于传统的PLC是无法做到的。
另一方面,传统的PLC厂家各自都有自己的通信协议,不开放、不可扩展、不可兼容,这对于未来按需生产的智能制造是不相适应的。
而基于软件定义的PLC具有与生俱来的灵活性,能够利用虚拟化技术通过软件设置即可实现控制能力的扩展,这正是未来制造最需要的控制系统。
软件定义PLC改变工业互联网系统架构传统的工业控制系统通常被称为五层金字塔模型,从现场传感层到PLC/DCS控制层,再到上面的数据采集和监控SCADA层,生产执行MES层和企业管理ERP层。
随着工业互联网的应用,MES和ERP开始互联融合和云化。
目前的工业互联网平台以兼容传统架构的方式运行,通过实时或者历史数据库或者专门的数据采集网关进行现场数据的采集,然后上传到平台上进行数据处理、展示,以及利用工业App做数据应用,进行预测和优化生产过程。
但要实现真正意义上工业互联网所构建的蓝图,这样的架构并不能满足要求。
在工业生产过程中,最终的控制过程还需要PLC来进行控制,MES、ERP或者工业APP不仅需要从PLC直接采集数据,而且还需要PLC能够直接执行来自MES、ERP或者工业APP的指令,根据指令优化和调整PLC 控制程序,实现工业生产的效率提升,同时也避免繁琐的人工调试过程。
而现有的工业互联网平台还无法做到直达PLC的互操作,因此只有采用软件定义的PLC才能够与工业互联网平台直接相通,比如实现PLC轻松连接至互联网,将APP和分析结果嵌入机器和云,实现智能化和自我感知,无需更换PLC硬件即可改变和升级PLC,通过API和生态系统扩大工业互联网平台应用。
“软件定义PLC更强调的是一种体系,一种实现思想。
”刘生富补充说道,“工业互联网的新一代控制系统的最终目的,就是实现ERP、MES、工业APP直接驱动控制系统来实现大数据驱动的精确控制。
”软件定义PLC的优势前所未有软件定义其实并不是一个新词,从早先的“软件定义网络”,到后来的“软件定义一切”,其实软件定义已经走过了概念论证阶段,在IT领域已经一个成熟的技术。
当然在工业领域,由于可靠性和实时性要求都很高,所以软件定义并没有得到很多应用。
“东土倡导的软件定义PLC,是基于虚拟化技术,将传统专用的PLC功能解耦,利用软件定义网络的实现思路,通过应用程序来实现PLC逻辑控制的功能。
”刘生富解释道,“软件定义PLC的核心是硬件资源虚拟化和管理功能可编程。
”由于软件定义PLC实现了硬件和软件的分离,可以通过软件来配置硬件资源,所以有着传统PLC所不具备的优势。
首先,软件定义PLC通常没有硬件依赖性,很容易迁移和重用软件,用户可以灵活地选择不同的供应商,也允许用户更换或添加组件而不影响系统的其他部分,轻松实现可扩展性和系统模块化。
这在传统PLC控制中并不那么容易,或者根本不可能实现。
其次,软件定义PLC由于采用最新的处理器,CPU的性能要比PLC 要强很多,同时一个CPU可以虚拟出多个PLC,同时控制更多的设备。
而且软件定义PLC可以处理语音、视觉及未来5G等新的数据,甚至在PLC上直接运行各类行业算法、工业APP,这样在很多场合可省去工控机、服务器,这些在传统PLC上是很难实现的。
最后,刘生富强调,软件定义PLC还有一个有点是可以用高级语言编程。
传统PLC通常用梯形图、结构化文本等编程,需要专业的自动化工程师去做,而且用这些语言去编写现在的很多算法十分费劲,而用C或者C++这些高级语言就能十分容易。
软件定义PLC的实现——NEWPRE工业服务器尽管软件定义控制的技术已经成熟,目前国内外也有不少厂商和机构几年前也开始了研究,但是东土科技已经在2019年4月德国汉诺威展上率先发布软件定义控制的工业服务器NEWPRE。
▎汉诺威展DEMO:利用软件定义将Intel i7处理器的4个物理核虚拟出20个实时核,同时集成自动化控制、运动控制、机器视觉等功能。
“这款NEWPRE工业服务器就是一款软件定义PLC的代表作,它基于开放的x86虚拟化架构,在Intel最新的i7处理器上通过高实时虚拟化技术,可以虚拟出最多20个软件定义的实时系统以替代PLC控制器。
”刘生富用一套在汉诺威展出的实景DEMO解释道,用NEWPRE不但可以做逻辑控制,而且可以轻松集成各种工业APP,例如可视化、协同制造、 机器视觉和工业大数据分析引擎等行业应用软件,真正实现OT和IT技术的融合,满足工业互联网和智能制造的需求。
刘生富表示,虽然这样的系统看上去和PC-BASE类似,但其实也有着本质不同。
首先PC-BASE不会采用虚拟化技术,处理器的每个物理核对应一个PLC应用,而NEWPRE可以虚拟出更多的虚拟核来做PLC控制。
更为重要的是,PC-BASE通常都是基于Windows或者 Linux桌面操作和操作系统,桌面系统和操作系统为同一系统,而NEWPRE不仅安装运行了东土自主开发的实时操作系统Intewell,同时也可以运行Windows或者 Linux系统,两个系统同时隔离运行,在桌面系统发生宕机时并不会影响实时系统的正常运行。
▎NewPre3100系列工业服务器目前,在实时性方面,NEWPRE支持最小50us的循环时间。
在编程方面,集成了东土自己的工业控制编程平台MaVIEW,可以用拖拽式图形化编程,也可以支持IEC61131-3,用C++、MatLab/Simulink 等编程。
同时,内置多种协议的协议转换,支持MQTT或OPC-UA到云的连接。
“NEWPRE可以说是集边缘计算、过程控制、运动控制和机器视觉于一身,是工业互联网时代新一代控制系统,因此也获得了2019年首届工业互联网大赛一等奖。
”刘生富总结道。
应用众多软件定义PLC威力初显自从NEWPRE在去年4月发布以来,目前已经在众多领域得到应用,显示出了软件定义PLC的初步威力。
据刘生富介绍,在虚拟多核带来的优势方面,一个典型的应用是,在一条电子芯片生产上,一台NEWPRE虚拟出了13个PLC完成13个工位的自动控制,至今已经运行近一年,没有出现任何问题。
另一个比较典型的应用是,东土帮助Fanuc公司改进了机器人教学系统。
在使用NEWPRE之前,一台机器人通常要给三个学生使用,得给每个学生配一个工控机来运行学生的仿真模型,还需要一个PLC接受工控机下发的指令来控制机器人,相当于一台机器人得配三套系统。
而现在只要一个NEWPRE,就安装了三套桌面系统和一套实时系统,桌面系统支持模拟仿真,实时系统控制机器人的运动,这样就省去了系统的复杂性和成本。
在集成机器视觉优势方面,NEWPRE也已经得到应用。
目前东土和合作伙伴正在联合开发新的无人行车控制系统。
以前无人行车通常采用摄像机采集信息给工控机进行路径规划算法计算,然后通过PLC和变频器控制行车的走向。
现在用NEWPRE之后,可以省去工控机和PLC,不但节省了硬件成本,而且还大大简化了控制系统的架构。
“近一年来,我们NEWPRE还在燃气站站控、油库储油罐液位控制和工程车无人驾驶控制等方面都已经得到应用,可以说软件定义PLC的一些优势在实际应用中都超出了我们的预计。
”当然,在刘生富看来,这些应用只是初露锋芒,“目前,我们也在和东北大学流程工业综合自动化国家重点实验室合作,开发更多的行业算法库来促进软件定义PLC的应用,也希望有更多的行业有合作伙伴加入,一起开发行业应用。
”正如工业互联网还在早期发展阶段一样,软件定义PLC目前显然也还处在逐渐成熟阶段。
尽管目前传统PLC还属于绝对的主导地位,而且也在朝着更多适应工业互联网需求的方向在发展,但无疑软件定义PLC开创了传统PLC不一样的通向未来之路,也许在工业互联网时代真正到来那一天,也正是软件定义PLC大放异彩的那一天。