宝钢股份特钢事业部40T产线板带炼钢过程控制计算机系统
宝钢线材控冷过程计算机优化控制系统(案例介绍)
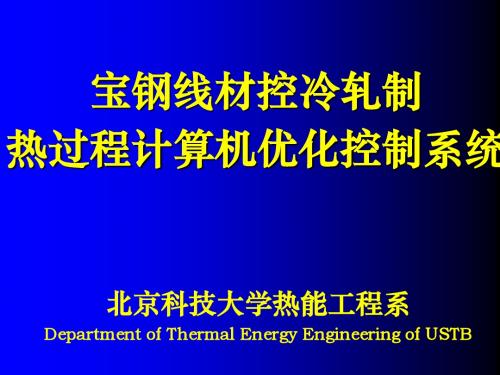
图4-4b 出炉目标温度为1100的轧线温度仿真
18 Back
不同成材规格仿真
左图为分析不同线材成 材规格对轧线温度所进 行的仿真计算,线材成 材规格为25mm。该图与 图4-4a比较可知:不同 成材规格对轧线温度影 响较大,这是由于不同 的成材规格有着不同的 轧制工艺过程。
图4-5a 线材成材规格为14mm的轧线温度仿真
Z L / 2时, r
t ha1 (t r1 t a ) r
10 Back
(5)水箱冷却热过程数学模型
t 1 t (r s ) t r r r
导热微分方程 初始条件
s Cs
0时,t (r ) t0 (r )
r 0时, t 0 r
2号检测点 4号检测点
减定径机 2号水箱
3号检测点
精轧机组
BACK 4
宝钢线材分厂计算机硬件配臵简图
5
三、控冷轧制热过程数学模型
数学模型的确定 输送过程传热数学模型 料坯轧制过程传热数学模型
水箱冷却热过程数学模型
BACK 6
(1) 数学模型的确定
针对轧机布置情况和数学模型的计算工作量,在保证数学模型 计算精度的前提下,尽可能地提高运算速度,对料坯在前两架轧 机轧制时采用方型断面的二维数学模型,在以后的轧制过程中采 用无限长圆柱的一维数学模型加以描述。两种模型的转换关系见 下图所示。
y 0时,
0时,t ( x, y) t0 ( x, y)
t h12 (t s 2 ta ) x
t 0 x
x w / 2时,
y h时,
t h13 (t s 3 t a ) y
t h11 (t s1 t a ) y
宝钢高炉过程计算机系统现场数据采集与处理方法
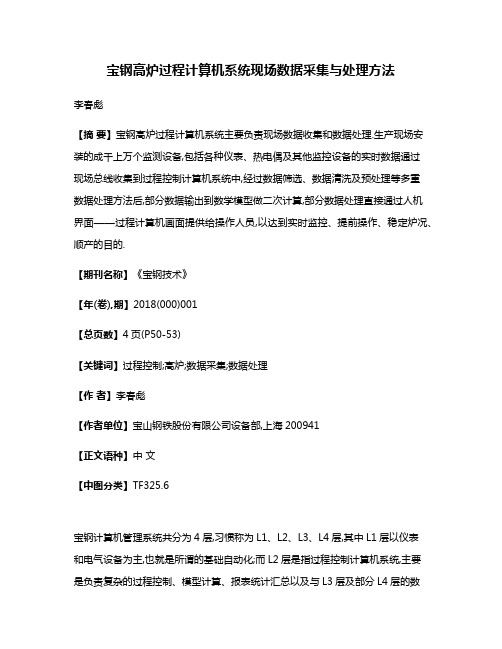
宝钢高炉过程计算机系统现场数据采集与处理方法李春彪【摘要】宝钢高炉过程计算机系统主要负责现场数据收集和数据处理.生产现场安装的成千上万个监测设备,包括各种仪表、热电偶及其他监控设备的实时数据通过现场总线收集到过程控制计算机系统中,经过数据筛选、数据清洗及预处理等多重数据处理方法后,部分数据输出到数学模型做二次计算,部分数据处理直接通过人机界面——过程计算机画面提供给操作人员,以达到实时监控、提前操作、稳定炉况、顺产的目的.【期刊名称】《宝钢技术》【年(卷),期】2018(000)001【总页数】4页(P50-53)【关键词】过程控制;高炉;数据采集;数据处理【作者】李春彪【作者单位】宝山钢铁股份有限公司设备部,上海200941【正文语种】中文【中图分类】TF325.6宝钢计算机管理系统共分为4层,习惯称为L1、L2、L3、L4层,其中L1层以仪表和电气设备为主,也就是所谓的基础自动化;而L2层是指过程控制计算机系统,主要是负责复杂的过程控制、模型计算、报表统计汇总以及与L3层及部分L4层的数据通信;L3层主要包含区域管理机系统,功能上接收L2层生产管理信息,经过整理汇总后将实绩上传至L4 层;L4 层可以通常理解为整体产销系统,包括生产合同、物料信息、库存、生产计划等整个生产销售流程。
早期,宝钢曾经出现过L1~L5层,其中L5层又称为企业战略层,通过L4 层的数据分析、整合后,数据发送L5层,提供给企业战略研发。
现在,随着数据存储设备和数据处理速度的大幅提升,L5层的概念已经逐渐淡化。
高炉过程控制计算机系统属于L2层级,主要功能包括:对L1层级数据的采集通讯、与L3层数据通讯、与焦化等其他L2层数据通讯,上料数据处理系统、本体数据处理系统、设备数据处理系统、热风炉数据处理系统、出铁数据处理系统、报表数据处理系统等,还有很重要的是人机界面部分,将采集来的数据经过处理、计算后呈现给用户,为用户进行生产操作时提供数据支撑。
宝钢电炉圆(方)坯连铸计算机系统运行实践

宝钢电炉圆(方)坯连铸计算机系统运行实践在钢铁工业的广阔天地里,计算机系统如同一位智慧的指挥官,它以精确无误的指令和决策,引领着生产线上的每一道工序。
特别是在宝钢电炉圆(方)坯连铸的生产线上,计算机系统的运行实践更是展现出了其卓越的性能和不可或缺的作用。
首先,我们不妨将这个计算机系统比作一位严谨的科学家。
它通过精确的数据收集和分析,确保了连铸过程中的每一个环节都能达到最优状态。
正如科学家在实验室中反复试验以求得最佳结果一样,这个系统也在不断地调整参数,以确保钢水的纯净度和连铸坯的质量。
它的存在,就像是给生产线装上了一双慧眼,能够洞察到每一个微小的变化,并及时作出反应。
其次,这个计算机系统还像一位经验丰富的指挥家。
在复杂的连铸过程中,它协调着各个环节的工作,确保生产的节奏稳定而有序。
就像指挥家在指挥一场交响乐时需要精准地控制每个乐手的演奏一样,这个系统也需要精确地控制每个设备的运行状态,以确保整个生产过程的和谐与统一。
然而,尽管这个计算机系统有着如此卓越的性能,但我们也不能忽视其中存在的问题和挑战。
比如,系统的维护和升级就是一个需要长期投入的问题。
随着技术的不断进步和生产线需求的不断变化,如何保持系统的先进性和适应性是一个需要深思的问题。
此外,系统的安全稳定运行也是至关重要的。
一旦出现故障或中断,可能会对整个生产线造成严重影响。
因此,我们需要对这个计算机系统进行全面的评价和思考。
一方面,我们要肯定其在提高生产效率、保证产品质量方面的重要作用;另一方面,我们也要对可能出现的问题保持警惕,并采取有效的措施来预防和解决这些问题。
只有这样,我们才能确保这个系统能够持续地为宝钢电炉圆(方)坯连铸生产线提供强大的支持。
总的来说,宝钢电炉圆(方)坯连铸计算机系统的运行实践是一个充满挑战和机遇的过程。
在这个过程中,我们需要不断地学习和探索,以便更好地利用这个系统的优势,同时克服其不足。
我相信,在宝钢人的共同努力下,这个系统一定能够发挥出更大的潜力,为宝钢的发展贡献更多的力量。
宝钢的生产管理系统介绍

宝钢的生产管理系统介绍宝钢是中国最大的钢铁企业之一,拥有完整的生产链条和世界一流的生产管理系统。
宝钢的生产管理系统是通过信息技术与自动化技术相结合,实现对生产过程的监控和管理的一种先进的生产管理体系。
下面将介绍宝钢的生产管理系统的特点和功能。
首先,宝钢的生产管理系统采用了先进的信息技术,包括物联网、云计算、大数据分析等。
通过在生产环节中引入传感器和数据采集设备,将各个环节的关键数据实时传输到系统中。
同时,通过云计算和大数据分析技术,对所收集到的大量数据进行处理和分析,实现对生产过程的实时监控和分析。
这样,宝钢的管理人员可以随时了解到生产过程的情况,及时做出决策和调整,提高生产效率和产品质量。
其次,宝钢的生产管理系统具有集成化的特点。
基于企业内部的ERP系统,将生产计划、物料管理、设备管理、质量管理等各个环节进行集成,并与供应商和客户的系统进行连接。
这样一来,可以实现从订单到生产计划再到生产执行,再到产品出库和配送的全过程管理,从而提高了生产的灵活性和效率。
此外,宝钢的生产管理系统还具有高度自动化的特点。
通过引入自动化设备和智能机器人,实现生产过程的自动化控制和操作。
例如,在宝钢的钢铁生产过程中,采用了先进的连铸技术和轧制技术,实现了从原料到成品的全自动生产过程。
而且,系统中还具备智能检测和报警功能,及时发现和处理生产过程中的异常情况,保障产品质量和生产安全。
最后,宝钢的生产管理系统还具备强大的数据分析和决策支持功能。
通过对生产过程中所收集到的数据进行分析和挖掘,可以发现生产过程中的潜在问题和改进空间,从而进行优化和调整。
同时,系统还配备了决策支持功能,提供了一系列的报表和指标,帮助管理人员进行决策和评估。
总的来说,宝钢的生产管理系统是一个先进、集成化、自动化的管理体系。
通过引入先进的信息技术、自动化设备和智能机器人,实现对生产过程的实时监控和管理。
同时,系统还具备数据分析和决策支持功能,帮助企业管理人员进行决策和优化。
宝钢股份公司的ERP系统建设

宝钢股份公司的ERP系统建设摘要介绍了宝钢股份公司建设冶金ERP系统的功能以及系统投运后取得的效果。
关键词 ERP系统冶金管理宝钢股份有限公司(以下简称宝钢)是我国现代化水平最高、规模最大的特大型钢铁联合企业,始建于1978年,经过一、二、三期的不断建设与发展,现今已成为一个年产超过1100万t钢的特大型现代化钢铁联合企业,主要产品包括:冷、热轧各类薄板、高速线材、无缝钢管等。
自建厂以来,遵循邓小平同志掌握新技术,要善于学习、更要善于创新的题词精神,大力推进现代化管理,始终坚持计算机系统的建设与工程建设同步原则。
目前已经基本上实现了企业管理的信息化,建成了宝钢自己的冶金ERP系统,构造了快速、有效的业务流程,设计了扁平、精干的流程型组织和协同、高效的经营运作模式,取得在成本、质量、服务、反应速度和技术创新等关键绩效上的突破性进步。
1.宝钢冶金ERP系统的主要功能1)销售管理子系统,包括:销售资源管理、用户合同管理、用户管理、货款管理、销售帐务管理等。
2)生产管理子系统,包括:合同处理、合同归并、合同计划、材料转用充当、材料申请、合同跟踪、产品准发、各区域作业计划、产能计划、方管坯存货管理、板坯存货管理、热轧存货管理、冷轧存货管理等。
3)质量管理子系统,包括:冶金规范管理、产品规范管理、质量判定、质量统计分析、检化验记录管理、质保书管理等。
4)产品运输管理子系统,包括:产成品存货管理、成品仓库发货管理、出厂计划管理、出厂环境管理、出厂资源平衡管理、洽运管理、发货调度管理、结算凭证管理、车船籍及费率管理等。
5)财务管理子系统,包括:产副品帐务管理、成本会计管理、厂务会计管理、普通会计管理、年度成本预算和报支系统等。
6)设备及维修综合管理子系统,包括:基准管理、点检管理、工事管理、备件管理、材料管理、固定资产管理、合同管理、维修成本管理、评价分析、图像管理等10个子系统。
7)信息作业管理子系统,主要用于上述各应用系统的管理,包括:用户授权、功能上线检查、通信管理、报表管理等功能模块,支撑系统的安全管理及作业的规范化管理。
计算机过程控制系统在炼钢厂的应用
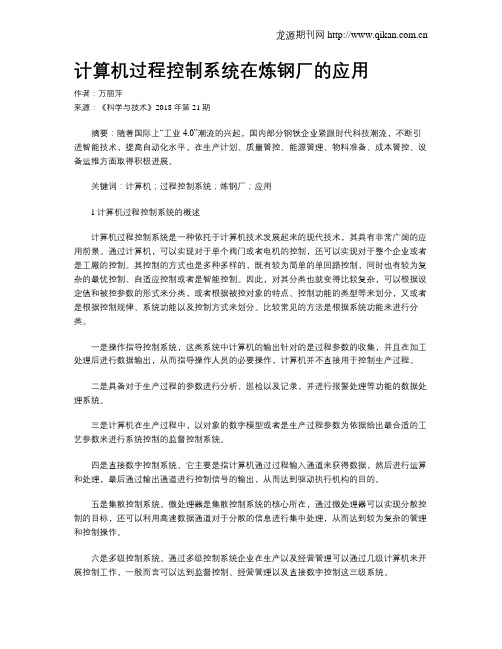
计算机过程控制系统在炼钢厂的应用作者:万丽萍来源:《科学与技术》2018年第21期摘要:随着国际上“工业4.0”潮流的兴起,国内部分钢铁企业紧跟时代科技潮流,不断引进智能技术,提高自动化水平,在生产计划、质量管控、能源管理、物料准备、成本管控、设备运维方面取得积极进展。
关键词:计算机;过程控制系统;炼钢厂;应用1计算机过程控制系统的概述计算机过程控制系统是一种依托于计算机技术发展起来的现代技术,其具有非常广阔的应用前景。
通过计算机,可以实现对于单个阀门或者电机的控制,还可以实现对于整个企业或者是工廠的控制。
其控制的方式也是多种多样的,既有较为简单的单回路控制,同时也有较为复杂的最优控制、自适应控制或者是智能控制。
因此,对其分类也就变得比较复杂,可以根据设定值和被控参数的形式来分类,或者根据被控对象的特点、控制功能的类型等来划分,又或者是根据控制规律、系统功能以及控制方式来划分。
比较常见的方法是根据系统功能来进行分类。
一是操作指导控制系统,这类系统中计算机的输出针对的是过程参数的收集,并且在加工处理后进行数据输出,从而指导操作人员的必要操作,计算机并不直接用于控制生产过程。
二是具备对于生产过程的参数进行分析、巡检以及记录,并进行报警处理等功能的数据处理系统。
三是计算机在生产过程中,以对象的数字模型或者是生产过程参数为依据给出最合适的工艺参数来进行系统控制的监督控制系统。
四是直接数字控制系统。
它主要是指计算机通过过程输入通道来获得数据,然后进行运算和处理,最后通过输出通道进行控制信号的输出,从而达到驱动执行机构的目的。
五是集散控制系统。
微处理器是集散控制系统的核心所在,通过微处理器可以实现分散控制的目标,还可以利用高速数据通道对于分散的信息进行集中处理,从而达到较为复杂的管理和控制操作。
六是多级控制系统。
通过多级控制系统企业在生产以及经营管理可以通过几级计算机来开展控制工作,一般而言可以达到监督控制、经营管理以及直接数字控制这三级系统。
计算机过程控制系统在炼钢厂的应用研究
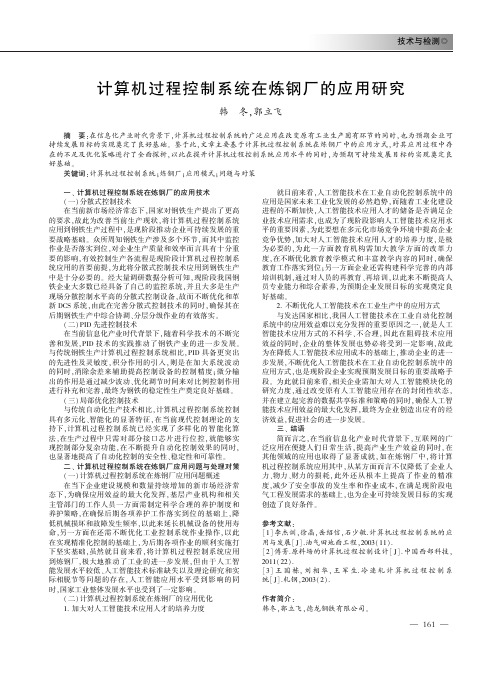
技术与检测Һ㊀计算机过程控制系统在炼钢厂的应用研究韩㊀冬,郭立飞摘㊀要:在信息化产业时代背景下,计算机过程控制系统的广泛应用在改变原有工业生产固有环节的同时,也为预期企业可持续发展目标的实现奠定了良好基础㊂鉴于此,文章主要基于计算机过程控制系统在炼钢厂中的应用方式,对其应用过程中存在的不足及优化策略进行了全面探析,以此在提升计算机过程控制系统应用水平的同时,为预期可持续发展目标的实现奠定良好基础㊂关键词:计算机过程控制系统;炼钢厂;应用模式;问题与对策一㊁计算机过程控制系统在炼钢厂的应用技术(一)分散式控制技术在当前新市场经济常态下,国家对钢铁生产提出了更高的要求,故此为改善当前生产现状,将计算机过程控制系统应用到钢铁生产过程中,是现阶段推动企业可持续发展的重要战略基础㊂众所周知钢铁生产涉及多个环节,而其中监控作业是否落实到位,对企业生产质量和效率而言具有十分重要的影响,有效控制生产各流程是现阶段计算机过程控制系统应用的首要前提,为此将分散式控制技术应用到钢铁生产中是十分必要的㊂经大量调研数据分析可知,现阶段我国钢铁企业大多数已经具备了自己的监控系统,并且大多是生产现场分散控制水平高的分散式控制设备,故而不断优化和革新DCS系统,由此在完善分散式控制技术的同时,确保其在后期钢铁生产中综合协调㊁分层分级作业的有效落实㊂(二)PID先进控制技术在当前信息化产业时代背景下,随着科学技术的不断完善和发展,PID技术的实践推动了钢铁产业的进一步发展㊂与传统钢铁生产计算机过程控制系统相比,PID具备更突出的先进性及灵敏度,积分作用的引入,则是在加大系统波动的同时,消除余差来辅助提高控制设备的控制精度;微分输出的作用是通过减少波动㊁优化调节时间来对比例控制作用进行补充和完善,最终为钢铁的稳定性生产奠定良好基础㊂(三)局部优化控制技术与传统自动化生产技术相比,计算机过程控制系统控制具有多元化㊁智能化的显著特征,在当前现代控制理论的支持下,计算机过程控制系统已经实现了多样化的智能化算法,在生产过程中只需对部分接口芯片进行位控,就能够实现控制部分复杂功能,在不断提升自动化控制效果的同时,也显著地提高了自动化控制的安全性㊁稳定性和可靠性㊂二㊁计算机过程控制系统在炼钢厂应用问题与处理对策(一)计算机过程控制系统在炼钢厂应用问题概述在当下企业建设规模和数量持续增加的新市场经济常态下,为确保应用效益的最大化发挥,基层产业机构和相关主管部门的工作人员一方面需制定科学合理的养护制度和养护策略,在确保后期各项养护工作落实到位的基础上,降低机械损坏和故障发生频率,以此来延长机械设备的使用寿命,另一方面在还需不断优化工业控制系统作业操作,以此在实现精准化控制的基础上,为后期各项作业的顺利实施打下坚实基础,虽然就目前来看,将计算机过程控制系统应用到炼钢厂,极大地推动了工业的进一步发展,但由于人工智能发展水平较低㊁人工智能技术标准缺失以及理论研究和实际相脱节等问题的存在,人工智能应用水平受到影响的同时,国家工业整体发展水平也受到了一定影响㊂(二)计算机过程控制系统在炼钢厂的应用优化1.加大对人工智能技术应用人才的培养力度就目前来看,人工智能技术在工业自动化控制系统中的应用是国家未来工业化发展的必然趋势,而随着工业化建设进程的不断加快,人工智能技术应用人才的储备是否满足企业技术应用需求,也成为了现阶段影响人工智能技术应用水平的重要因素,为此要想在多元化市场竞争环境中提高企业竞争优势,加大对人工智能技术应用人才的培养力度,是极为必要的,为此一方面教育机构需加大教学方面的改革力度,在不断优化教育教学模式和丰富教学内容的同时,确保教育工作落实到位;另一方面企业还需构建科学完善的内部培训机制,通过对人员的再教育㊁再培训,以此来不断提高人员专业能力和综合素养,为预期企业发展目标的实现奠定良好基础㊂2.不断优化人工智能技术在工业生产中的应用方式与发达国家相比,我国人工智能技术在工业自动化控制系统中的应用效益难以充分发挥的重要原因之一,就是人工智能技术应用方式的不科学㊁不合理,因此在阻碍技术应用效益的同时,企业的整体发展也势必将受到一定影响,故此为在降低人工智能技术应用成本的基础上,推动企业的进一步发展,不断优化人工智能技术在工业自动化控制系统中的应用方式,也是现阶段企业实现预期发展目标的重要战略手段㊂为此就目前来看,相关企业需加大对人工智能模块化的研究力度,通过改变原有人工智能应用存在的封闭性状态,并在建立起完善的数据共享标准和策略的同时,确保人工智能技术应用效益的最大化发挥,最终为企业创造出应有的经济效益,促进社会的进一步发展㊂三㊁结语简而言之,在当前信息化产业时代背景下,互联网的广泛应用在便捷人们日常生活,提高产业生产效益的同时,在其他领域的应用也取得了显著成就,如在炼钢厂中,将计算机过程控制系统应用其中,从某方面而言不仅降低了企业人力㊁物力㊁财力的损耗,此外还从根本上提高了作业的精准度,减少了安全事故的发生率和作业成本,在满足现阶段电气工程发展需求的基础上,也为企业可持续发展目标的实现创造了良好条件㊂参考文献:[1]李杰训,徐晶,岳绍信,石少敏.计算机过程控制系统的应用与发展[J].油气田地面工程,2003(11).[2]傅菁.原料场的计算机过程控制设计[J].中国西部科技,2011(22).[3]王国栋,刘相华,王军生.冷连轧计算机过程控制系统[J].轧钢,2003(2).作者简介:韩冬,郭立飞,德龙钢铁有限公司㊂161。
热轧计算机管理与控制系统下

第34卷 第2期2010年3月冶金自动化Metallurgical I ndustry Aut om ati onVol .34 No .2M arch 2010综述与评论热轧计算机管理与控制系统(下)王文瑞1,杨建中2,唐清荣2(1.宝山钢铁股份有限公司,上海200431;2.宝山钢铁股份有限公司不锈钢事业部)中图分类号:T G33419;TP271 文献标志码:B 文章编号:100027059(2010)022*******C o m puter m anagem en t and con tr ol system i n hot r olli n g(B)WANG W en 2rui 1,Y ANG Jian 2zhong 2,T ANG Qing 2r ong2(11B aoshan Iron &St ee l Co 1,Ltd 1,Shanghai 200431,China;21Sta i n l e ss Steel D ivisi on,Baoshan Iron &Stee l Co 1,Ltd .)313 板坯库对一体化计划执行的支持连铸产出的板坯是炼钢终计划执行完毕的结果,这些板坯入库后作为进一步编制热轧初计划和终计划的对象材料。
所以板坯的入库、堆垛、倒垛以及上料等仍以一体化计划为核心进行管理,其中堆垛的好坏直接影响到上料的作业效率。
31311 板坯入库和堆放策略从连铸直接入库的板坯信息中,凡在计划内的板坯均包含热轧预计划号(以下称轧制计划号)。
入库板坯包括:DHCR 吊销坯、HCR 坯、从连铸辊道直送的CCR 坯、从连铸台车运来的冷坯、外来坯以及各种情况的返回坯等。
板坯实物与板坯信息经核对确认后进行统一管理。
板坯堆放策略如下(以碳钢为例,不锈钢同理):(1)同一轧制计划号的板坯顺序堆放在同一垛位上;(2)相同R F 码的板坯堆在同一堆垛上;(3)在没有相同轧制计划号和R F 码时,按板坯属性(包括:出钢记号、规格尺寸等)堆放。
4钢铁生产自动化和计算机系统

转炉静态、动态控制 连铸连轧、热装热送
珠江钢厂、邯钢的薄板坯连铸连轧生产线 大连钢厂的全连续棒线材轧机 抚顺钢厂的模具扁钢轧机
生产过程的热态连接和冷态连接,连续化为实 施全过程自动控制创造了条件
专家系统由Offline Online发展
8
计算机控制与生产过程的自动化
4.1 钢铁生产自动化和计算机应用概述
数学模型的开发
80~90年代
从机理模型、经验模型、管理模型发展到专家 系统 管理型:如能源优化自动化管理系统
节能系统: 综合循环系统,如高炉炉顶煤气发电
能源自动化系统:钢厂排放物监测,机电系统
4 钢铁生产过程 自动化和计算机系统
在20世纪钢铁传统工艺流程主 要工序的技术进步中,有相当突出 的一部分是信息技术。在未来发展 中,谁能充分地利用信息技术,取 得提高劳动生产率的优势,谁就是 成功者。 生产过程的自动化是建立在生 产连续化的基础之上的。
2
4.1 钢铁生产自动化和计算机应用概述
能源管理系统:煤气管理,能源预测和调配控制 能源审计: 工程设计、经济性、优化操作
4
4.1 钢铁生产自动化和计算机应用概述
人工智能的应用
人工智能和人工智能与数学模型相结合
模糊控制 不确定性过程控制
专家系统 将多个专家的知识集合起来 应用于: 生产过程控制和预测,如高炉专家系统 设备故障诊断,如轧钢设备故障诊断
人工神经网络 推理过程强化,模拟人脑功能 如:高炉炉热预报,转炉造渣、终点控制
5
4.1 钢铁生产自动化和计算机应用概述
宝钢电炉圆(方)坯连铸计算机系统运行实践

宝钢电炉圆(方)坯连铸计算机系统运行实践
宝钢电炉圆(方)坯连铸计算机系统是一套高度自动化的控制系统,
它在钢铁生产过程中扮演着至关重要的角色。
该系统通过精确控制连
铸机的各个参数,确保了生产效率和产品质量的最大化。
在宝钢的电炉圆(方)坯连铸生产线上,计算机系统负责监控和调节
整个连铸过程。
系统的主要功能包括:
1. 温度控制:系统能够实时监测钢水的温度,并根据需要调节加热设备,以确保钢水在连铸过程中保持最佳温度。
2. 速度调节:连铸速度是影响产品质量的关键因素之一。
计算机系统
通过精确控制拉速,确保铸坯的内部结构均匀,避免裂纹和缺陷的产生。
3. 结晶器液位控制:系统能够自动调节结晶器内的液位,以适应不同
的生产条件和铸坯规格。
4. 二次冷却控制:计算机系统根据铸坯的冷却需求,自动调节冷却水
的流量和分布,以实现最佳的冷却效果。
5. 质量检测:系统配备有在线检测设备,能够实时监测铸坯的尺寸和
表面质量,及时发现并处理生产过程中的问题。
6. 数据记录与分析:计算机系统能够记录生产过程中的所有关键数据,并进行分析,以便优化生产流程和提高产品质量。
7. 故障诊断与报警:系统具备故障诊断功能,能够及时发现设备异常,
并发出报警,减少生产中断的风险。
8. 人机交互界面:友好的人机交互界面使得操作人员能够直观地监控生产过程,并进行必要的手动干预。
宝钢电炉圆(方)坯连铸计算机系统的运行实践表明,通过采用先进的自动化技术,可以显著提高生产效率,降低生产成本,同时确保产品质量的稳定性和一致性。
随着技术的不断进步和优化,该系统在未来的生产中将发挥更大的作用。
宝钢股份特钢事业部40T产线板带炼钢过程计算机应用控制功能设计
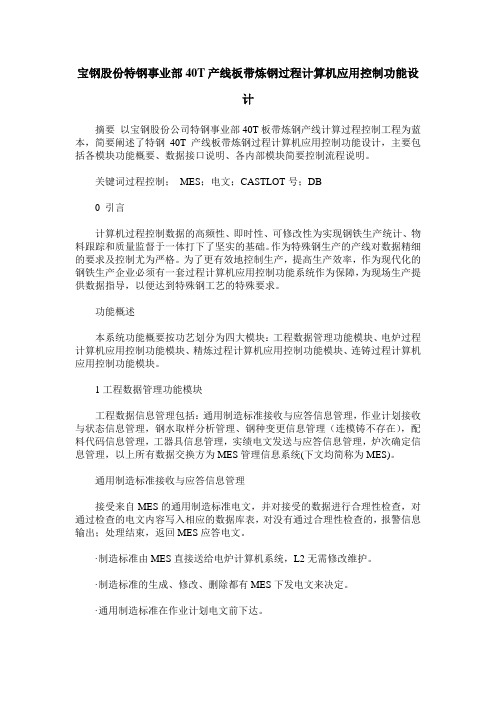
宝钢股份特钢事业部40T产线板带炼钢过程计算机应用控制功能设计摘要以宝钢股份公司特钢事业部40T板带炼钢产线计算过程控制工程为蓝本,简要阐述了特钢40T产线板带炼钢过程计算机应用控制功能设计,主要包括各模块功能概要、数据接口说明、各内部模块简要控制流程说明。
关键词过程控制;MES;电文;CASTLOT号;DB0 引言计算机过程控制数据的高频性、即时性、可修改性为实现钢铁生产统计、物料跟踪和质量监督于一体打下了坚实的基础。
作为特殊钢生产的产线对数据精细的要求及控制尤为严格。
为了更有效地控制生产,提高生产效率,作为现代化的钢铁生产企业必须有一套过程计算机应用控制功能系统作为保障,为现场生产提供数据指导,以便达到特殊钢工艺的特殊要求。
功能概述本系统功能概要按功艺划分为四大模块:工程数据管理功能模块、电炉过程计算机应用控制功能模块、精炼过程计算机应用控制功能模块、连铸过程计算机应用控制功能模块。
1工程数据管理功能模块工程数据信息管理包括:通用制造标准接收与应答信息管理,作业计划接收与状态信息管理,钢水取样分析管理、钢种变更信息管理(连模铸不存在),配料代码信息管理,工器具信息管理,实绩电文发送与应答信息管理,炉次确定信息管理,以上所有数据交换方为MES管理信息系统(下文均简称为MES)。
通用制造标准接收与应答信息管理接受来自MES的通用制造标准电文,并对接受的数据进行合理性检查,对通过检查的电文内容写入相应的数据库表,对没有通过合理性检查的,报警信息输出;处理结束,返回MES应答电文。
·制造标准由MES直接送给电炉计算机系统,L2无需修改维护。
·制造标准的生成、修改、删除都有MES下发电文来决定。
·通用制造标准在作业计划电文前下达。
·作业计划接收与状态信息管理·接受来自MES的作业计划电文,并对接受的数据进行合理性检查,对通过检查的电文内容写入相应的数据库表,对没有通过合理性检查的,报警信息输出;处理结束,返回MES应答电文。
宝钢高炉过程计算机系统现场数据采集与处理方法

李春彪%宝钢高炉过程计算机系统现场数据采集与处理方法
<%= >"(!&#RS;?8<<?;P=S;5% :53<=TUSP3?8% V3=3?;558?=% V3=3RS;?8<<4PY
%%宝钢计算机管理系统共分为 + 层$习惯称为 b#&b!&b*&b+ 层$其中 b# 层以仪表和电气设备为 主$也就是所谓的基础自动化%而 b! 层是指过程控 制计算机系统$主要是负责复杂的过程控制&模型 计算&报表统计汇总以及与 b* 层及部分 b+ 层的数 据通信%b* 层主要包含区域管理机系统$功能上接 收 b! 层生产管理信息$经过整理汇总后将实绩上 传至 b+ 层%b+ 层可以通常理解为整体产销系统$
/#
分$将采集来的数据经过处理&计算后呈现给用 户$为用户进行生产操作时提供数据支撑'
?@数据采集
宝钢高炉过程控制计算机系统的数据都是由 b! 过程计算机系统向 b# 基础自动化层主动采 集$宝钢高炉控制系统 b# 大部分采用的是日本的 恒河基础自动化设备$b#&b! 之间通过 GCH的方 式进行通信$其中又分为两大类采集方式#一类为 定周期数据采集$即 b! 以定周期模式向 b# 采集 数据$周期间隔可以由系统管理员设定$宝钢高炉 过程控制计算机系统中常用的包含 #&/&#"&*"&
热轧过程控制计算机系统的开发与集成
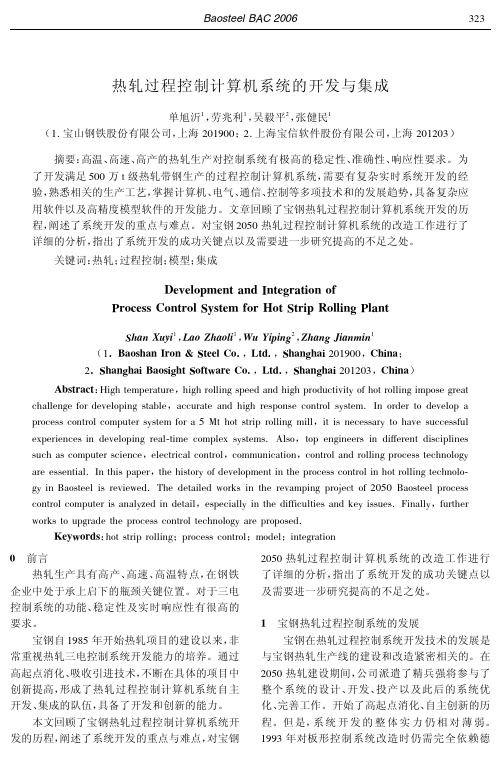
&"&
热轧过程控制计算机系统的开发与成
单旭沂! , 劳兆利! , 吴毅平" , 张健民! ( !# 宝山钢铁股份有限公司, 上海 "$!%$$ ; "# 上海宝信软件股份有限公司, 上海 "$!"$& ) ’ ’ 摘要: 高温、 高速、 高产的热轧生产对控制系统有极高的稳定性、 准确性、 响应性要求。为 了开发满足 ($$ 万 ) 级热轧带钢生产的过程控制计算机系统, 需要有复杂实时系统开发的经 验, 熟悉相关的生产工艺, 掌握计算机、 电气、 通信、 控制等多项技术和的发展趋势, 具备复杂应 用软件以及高精度模型软件的开发能力。文章回顾了宝钢热轧过程控制计算机系统开发的历 程, 阐述了系统开发的重点与难点。对宝钢 "$($ 热轧过程控制计算机系统的改造工作进行了 详细的分析, 指出了系统开发的成功关键点以及需要进一步研究提高的不足之处。 ’ ’ 关键词: 热轧; 过程控制; 模型; 集成
图 !" 功能关系示意图 ! # !" 应用功能开发 根据热轧生产流程, 需要考虑加热炉、 粗轧、 精轧、 板形、 层流冷却及卷取机等设备的设定与控 制。围绕生产过程的物流、 信息流及控制流展开 应用功能的开发, 具体内容包括材料跟踪、 数据通 信、 数据管理、 数据收集、 设定计算、 画面、 报表等。 这些是完成热轧过程控制所必备的基本功能, 是 确保热轧物流、 信息流畅通、 准确, 生产高度自动 化的前提条件。 ! # #" 热轧模型 为了获得高精度的产品, 就必须对热轧过程 进行精确的控制。因此, 建立高精度的过程控制 模型, 实现对板坯的加热、 宽度、 厚度、 板形、 轧制 过程中的温度、 卷取温度等进行预报、 设定以及周 期控制是整个过程控制系统的核心。 从抽象角度分析, 热轧控制系统的模型可分 : 物理模型、 控制模型以及自适应模 三大类 ( 图 $) 型。 #" 宝钢 !%&% 热轧轧线过程控制计算机系统改造 在热 轧 三 电 系 统 改 造 总 体 框 架 下, 实施对 $’(’ 热轧轧线过程控制计算机系统的改造。 # # ’" 系统设计 为了实施对复杂的热轧控制系统的分步改 造, 各子系统功能原则上维持不变, 只进行局部优 化。在对过程控制计算机系统改造时, 取消了原 前置处理机系统, 将其功能合理的分配到基础自 动化以及过程控制计算机系统中, 使整个控制系 统层次清晰、 功能分担更趋合理。 &# !# !" 主机系统 主机系统采用 )* 的 +,*)+ 服务器 -./’ 。 利用正在改造的板形控制计算机, 添置一些必要 的软硬件, 将现有精轧控制机的功能移植进去, 并 称其为精轧控制机。另外, 新置 & 台小型机, 其中 $ 台分别替换现有的粗轧控制机和层流冷却控制 机, 另 ! 台作为粗轧、 精轧和层流冷却控制机的备 用机。这 / 台主机均为多 0*1 系统, 除了本身带 有内置硬盘外, 还共享一套外置的磁盘阵列, 组成 一个互为热备的集群体系结构。 &# !# $" 存储系统 新系 统 在 数 据 存 储 上 实 现 了 基 于 .+2 的 3+45 磁盘技术, 最大程度保证了系统数据的完 整性和安全性。根据生产数据的特点和使用目 图 $" 热轧模型分类 的, 在数据管理上分别采用了数据库和文件系统,
计算机技术在钢铁板带生产中的应用
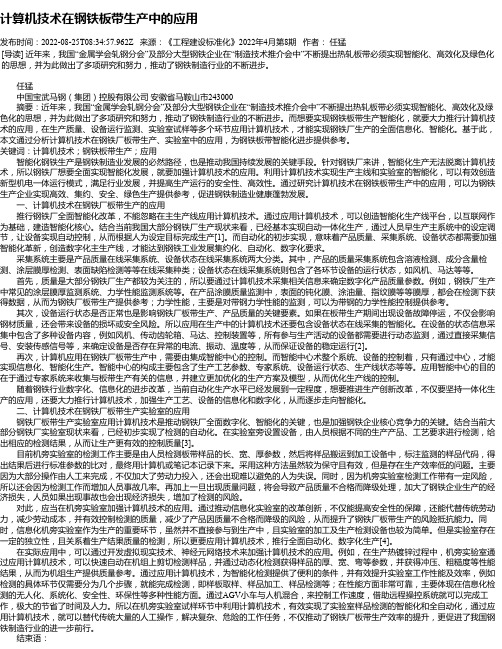
计算机技术在钢铁板带生产中的应用发布时间:2022-08-25T08:34:57.962Z 来源:《工程建设标准化》2022年4月第8期作者:任猛[导读] 近年来,我国“金属学会轧钢分会”及部分大型钢铁企业在“制造技术推介会中”不断提出热轧板带必须实现智能化、高效化及绿色化的思想,并为此做出了多项研究和努力,推动了钢铁制造行业的不断进步。
任猛中国宝武马钢(集团)控股有限公司安徽省马鞍山市243000摘要:近年来,我国“金属学会轧钢分会”及部分大型钢铁企业在“制造技术推介会中”不断提出热轧板带必须实现智能化、高效化及绿色化的思想,并为此做出了多项研究和努力,推动了钢铁制造行业的不断进步。
而想要实现钢铁板带生产智能化,就要大力推行计算机技术的应用,在生产质量、设备运行监测、实验室试样等多个环节应用计算机技术,才能实现钢铁厂生产的全面信息化、智能化。
基于此,本文通过分析计算机技术在钢铁厂板带生产、实验室中的应用,为钢铁板带智能化进步提供参考。
关键词:计算机技术;钢铁板带生产;应用智能化钢铁生产是钢铁制造业发展的必然路径,也是推动我国持续发展的关键手段。
针对钢铁厂来讲,智能化生产无法脱离计算机技术,所以钢铁厂想要全面实现智能化发展,就要加强计算机技术的应用。
利用计算机技术实现生产主线和实验室的智能化,可以有效创造新型机电一体运行模式,满足行业发展,并提高生产运行的安全性、高效性。
通过研究计算机技术在钢铁板带生产中的应用,可以为钢铁生产企业实现高效、集约、安全、绿色生产提供参考,促进钢铁制造业健康蓬勃发展。
一、计算机技术在钢铁厂板带生产的应用推行钢铁厂全面智能化改革,不能忽略在主生产线应用计算机技术。
通过应用计算机技术,可以创造智能化生产线平台,以互联网作为基础,建造智能化核心。
结合当前我国大部分钢铁厂生产现状来看,已经基本实现自动一体化生产,通过人员早生产主系统中的设定调节,让设备实现自动控制,从而根据人为设定目标完成生产[1]。
宝钢股份特钢事业部40T产线板带炼钢过程控制计算机系统

信 息 技 术43科技资讯 SCIENCE & TECHNOLOGY INFORMATION 随着网络和计算机技术的不断向前发展,在生产过程的自动化控制系统中,过程控制技术优势在于它的高频率处理,即时性,同时相比模拟控制和微控它具有极为强大的易修改性。
这些优势都是过去的任何一种控制无法比拟的。
炼钢、精炼、连铸是钢铁生产的一个非常重要的环节,它的运转性能及效率的高低直接影响到企业的效益及板坯产品的产量及质量。
作为一个现代化的钢厂尤其是特殊钢生产产线,产品的生产组织及各个工序的调度安排必须作到统一有序,对生产的各工序进行严格的质量控制,以适应市场的变化及需求。
为了有效地贯彻生产部门的统一调度,有效地控制生产、提高产品的质量和产量,正确地指导操作人员进行有效、合理的操作,就必须要有一套先进、强健的计算机控制系统作为支撑。
通过利用系统来帮助操作人员提高操作水平,系统对生产过程进行有效的跟踪控制,对生产作业实绩进行有效的收集、统计以及对生产线上的主要设备进行有效管理,将大大地减少人力,提高生产效率。
本系统开发投入后,已经实现了实时地跟踪现场的生产,为生产提供必要的生产指导,实时收集生产实绩,统计必要的消耗,为MES系统提供实绩数据。
1 系统结构本系统包含三大系统:电炉应用系统、精炼应用系统、连模铸应用系统。
其中电炉L2计算机系统:覆盖4个电炉的计算机系统;精炼L2计算机系统:覆盖5个LF炉、1个AOD炉、1个VD炉、1个VOD炉的计算机系统;连模铸L2计算机系统:覆盖1台连铸机本体、1套模铸工位的计算机系统。
1.1系统构成特点为了系统的先进可靠,同时尽可能地降低、节约成本,本系统采用的是基于PC和PC Server的CLIENT/SERVER体系结构。
数据库、应用服务器均采用市场上目前性能可靠、优越的PC服务器,以保证系统的可靠运行。
为了提高系统的安全性、可靠性和高效性,应用服务器、和数据库服务器的系统盘采用磁盘镜像技术RAID1;数据盘库系统采用双机热备的方式。
- 1、下载文档前请自行甄别文档内容的完整性,平台不提供额外的编辑、内容补充、找答案等附加服务。
- 2、"仅部分预览"的文档,不可在线预览部分如存在完整性等问题,可反馈申请退款(可完整预览的文档不适用该条件!)。
- 3、如文档侵犯您的权益,请联系客服反馈,我们会尽快为您处理(人工客服工作时间:9:00-18:30)。
宝钢股份特钢事业部40T产线板带炼钢过程控制计算机系统摘要:以宝钢股份公司特钢事业部40T板带炼钢产线计算过程控制工程为蓝本,简要阐述了特钢40T产线板带炼钢过程控制计算机的设计和开发过程中分布式计算机技术在该系统中的应用,主要包括设计思想、系统架构、软硬件平台应用系统架构、通信方式。
关键词:过程控制;出钢开始;Mutilink;XCOM;操作终端;电文;MES;随着网络和计算机技术的不断向前发展,在生产过程的自动化控制系统中,过程控制技术优势在于它的高频率处理,即时性,同时相比模拟控制和微控它具有极为强大的易修改性。
这些优势都是过去的任何一种控制无法比拟的。
炼钢、精炼、连铸是钢铁生产的一个非常重要的环节,它的运转性能及效率的高低直接影响到企业的效益及板坯产品的产量及质量。
作为一个现代化的钢厂尤其是特殊钢生产产线,产品的生产组织及各个工序的调度安排必须作到统一有序,对生产的各工序进行严格的质量控制,以适应市场的变化及需求。
为了有效地贯彻生产部门的统一调度,有效地控制生产、提高产品的质量和产量,正确地指导操作人员进行有效、合理的操作,就必须要有一套先进、强健的计算机控制系统作为支撑。
通过利用系统来帮助操作人员提高操作水平,系统对生产过程进行有效的跟踪控制,对生产作业实绩进行有效的收集、统计以及对生产线上的主要设备进行有效管理,将大大地减少人力,提高生产效率。
本系统开发投入后,已经实现了实时地跟踪现场的生产,为生产提供必要的生产指导,实时收集生产实绩,统计必要的消耗,为MES 系统提供实绩数据。
1 系统结构本系统包含三大系统:电炉应用系统、精炼应用系统、连模铸应用系统。
其中电炉L2计算机系统:覆盖4个电炉的计算机系统;精炼L2计算机系统:覆盖5个LF炉、1个AOD炉、1个VD炉、1个VOD炉的计算机系统;连模铸L2计算机系统:覆盖1台连铸机本体、1套模铸工位的计算机系统。
1.1 系统构成特点为了系统的先进可靠,同时尽可能地降低、节约成本,本系统采用的是基于PC和PC Server的CLIENT/SERVER体系结构。
数据库、应用服务器均采用市场上目前性能可靠、优越的PC服务器,以保证系统的可靠运行。
为了提高系统的安全性、可靠性和高效性,应用服务器、和数据库服务器的系统盘采用磁盘镜像技术RAID1;数据盘库系统采用双机热备的方式。
客户机将采用性能可靠的高中档PC机,以便保证性能可靠和画面显示的响应速度。
应用、数据库服务器的操作系统采用Windows 2003 Enterprise Server,数据库采用Oracle 10g Enterprise Version关系数据库。
应用程序的开发利用Microsoft Visual Studio .Net Prof。
客户机端操作系统采用Windows XP Professional,人机交互界面应用主要由利用ORACLE的前端开发工具Forms、Reports开发的人机界面系统(HMI System)和报表打印显示系统组成。
系统考虑了必要的病毒防治软件及系统备份软件。
系统的架构及开发基于宝信公司开发的中间件Plature99、XCOM、MultLink上进行。
整个过程计算机系统主要组成包括:机房服务器、操作终端和网络设备,其中机房服务器又包括通讯前置机、应用服务器和数据库服务器。
针对所处理工位的不同,本设计方案分别设计了冶炼区域(料场、EAF炉)、精炼(LF炉、VD炉、AOD炉和VOD炉)、铸造区域(连铸、模铸)三个过程计算机子系统、各系统分别处理本工位的二级计算机功能,且每套系统均配备各自的应用服务器和数据库服务器。
而各操作室的炉前终端主要提供实现数据显示和画面操作功能。
通讯前置机负责L2系统与L1系统之间的数据通讯,基于OPC 工业控制数据通讯的标准实现与不同PLC的数据通讯功能。
通讯服务器在获得相关PLC数据后将启动对应的应用处理功能。
应用服务器负责处理对应工位的应用处理功能(过程跟踪、实绩收集等),提供相关终端对数据库访问的统一接口,同时负责各L2系统之间以及其与L3系统之间的数据通讯功能。
数据库服务器存储相应工位的过程计算机系统的全部数据信息,包括冶炼计划、标准信息、过程状况、实绩信息、日志信息等。
电炉、精炼和连铸计算机系统之间的应用功能相互独立,各应用系统分别与本工序范围内的基础自动化系统进行数据通讯,处理本系统范围内的二级应用功能,并实现与L3系统的数据通讯功能。
上述各系统相互之间存在生产状态和实绩信息等信息的数据通讯,采用DB-LINK通讯方式。
各系统可以查询相关工序的冶炼状态和实绩信息。
1.2 计算机系统硬件配置PC服务器包括CCS2应用服务器3台、CCS2数据库服务器3台、备用服务器1台,HMI Server PC机一台,操作终端PC机48台,通信前置机3台。
彩色喷墨打印机4台,激光打印机2台。
网络设备包括:交换机机箱、SUP IV交换机引擎CPU模块、冗余电源、交换背板;24口多模光纤接口模块;24个10/100/1000M RJ接口;具有线速转发,分布式交换能力的6口千兆接口模块,提供1个单模和1个多模接口;支持OSPF路由协议所需的软件,24口10/100/1000M UTP接口,4口多模100M光纤接口模块,8个10/100M RJ45接口、1个100M多模接口可网管产品符合特钢网络设备选型要求,能够无缝兼容。
6个1000M接口,6个100M RJ45接口;32GBps背板能力,最大堆叠9个设备Switch Hub,符合特钢网络设备选型要求,能够无缝兼容。
1个1000M接口,8个100M RJ45接口。
2 系统功能概述系统实现了4个废钢料场称量的生产过程控制、4个EAF炉的生产过程控制、4个LF炉的生产过程控制、2个AOD炉的生产过程控制、1个VD炉的生产过程控制、1个VOD炉的生产过程控制,1台1机1流垂直连铸机的生产过程控制、1台模铸机的生产过程控制。
2.1 电炉工艺钢包到达指定位置时,电弧开始通电,当钢包内钢水达到目的状态时电弧通电结束。
电弧通电以后,要向炉内吹氧,吹氩,吹碳,为了加速冶炼过程,还需要对电压进行换档,共分为8个档位。
冶炼开始时,档位逐个升高,冶炼结束时,档位逐个降低。
在冶炼过程中,要抽取试样,并测定钢水温度,以确定钢水是否达到了要求。
钢水达到要求后,电炉冶炼结束,进入出钢流程。
由EBT出钢方式出来的钢水还要经过精练,连铸工序。
2.2 LF炉工艺吊车将钢水包吊到钢包车的吊包工位,进行吹氩。
然后将钢包车开至加热工位,钢包盖下降,测温加渣料,电极下降,开始通电加热,基本达到热平衡后,钢液温度不再下降,这时停止通电,提起电极,同时进行底吹搅拌,进行测温取样。
在等待快速化验结果的同时,继续进行通电加热。
获取取样结果后,投料,进行合金微调。
加入合金料后,吹氩,继续加热。
此时进行最后一次测温取样,然后进行喂丝处理,进行终脱氧、脱硫,作夹杂物的变性处理。
在喂丝完成后包盖生起,钢包车开至吊包工位。
2.3 VOD炉工艺准备阶段:钢水扒渣后,通过行车将钢包吊进真空罐,利用惰性气体连接装置连接氩气管线并开始吹氩,测温取样和测钢包净空。
脱硅:所有的硅必须在碳氧反应之前除去。
脱硅过程中必须进行灵活的压力控制。
吹氧脱碳:这个过程可以被分为:主吹:脱碳是一个连续过程,可以由供氧量来控制。
罐内压力可通过真空控制或专用泵级达到150-50动态吹炼:为了促进碳的反应,使真空罐压力和氧流量发生变化,可根据碳含量、钢水温度和脱碳效率来控制和结束吹氧,控制系统将监控所有这些参数。
沸腾:停止吹氧后,继续降低压力到深度真空,利用钢水中残余氧进行沸腾脱碳。
沸腾脱碳后,加入石灰和还原剂在深度真空下对渣中Cr进行还原,并进行合金化,还原结束后破真空,并可进行合金微调。
大气下处理阶段:破真空后进行测温取样,喂丝,并进行Ar气软吹,软吹后测温取样,将钢包吊离VOD处理站。
2.4 VD炉工艺钢包由行车吊运到VD工位,同时,接通钢包底吹氩,测温,盖好罐盖,启动蒸汽喷射泵进行真空脱气处理,保持约25分钟,使钢溶液气体含量达到要求,破坏真空后,移开真空罐盖车,进行测温取样、定氧、定氢,喂丝,钢水温度满足浇注条件后用行车吊运至连铸或模铸工位进行浇注。
2.5 连铸工艺经过精炼后温度、成分均合格的钢水,由起重机吊运到钢包回转台上。
连接好钢包滑动水口液压缸和钢包下渣检测装置接线。
钢包加盖,钢包回转台旋转180度,把钢包运送到浇注位置的中间罐小车的上方。
开启钢包滑动水口,钢水经过钢包到中间罐之间的保护套管流入中间罐,待中间罐内钢水液面上升至一定高度后,投入覆盖渣。
中间罐钢流控制系统自动打开,钢水通过浸入式水口流入结晶器。
结晶内的钢水上升到一定高度后,人工加入保护渣。
在自动开浇系统的控制下,结晶器振动装置和拉坯辊自动启动,在结晶器内已形成坯壳的铸坯在引锭杆的带动下缓缓拉出结晶器和足辊段,进入二冷导向段。
铸坯在二冷导向段中经过气雾喷淋冷却,坯壳不断加厚直至全凝固。
铸坯出了二冷导向段之后,由夹送辊夹送铸坯,此时夹送辊下方的火焰切割机将铸坯切成倍尺或定尺后,由接坯小车将铸坯送入处于等待位的斜出坯装置,斜出坯装置接受到铸坯后由接坯位转至斜出坯位。
之后,斜出坯装置将铸坯送入地面上的后部出坯辊道,铸坯在后部出坯辊道上去毛刺,去好毛刺的铸坯由起重机从辊道上运出至铸坯堆存区。
2.6 模铸工艺模铸工艺:在模铸四跨布置有钢锭模准备区,钢锭模的准备工作包括冷却、清刷。
冷却以空冷为主,冷却后,钢锭模要用钢铲、钢刷清理内壁,并用压缩空气吹去残钢,结渣和氧化铁皮,清理后的钢锭模放在堆放区以使用。
模铸作业时,起重机将钢包吊运至浇注车上,然后由浇注车将钢包运至浇注位。
待钢包按要求调整到位后,就可进行模铸浇铸。
3 过程应用系统宝钢股份特钢40T产线过程计算机应用系统主要分为两个模块,模块一:工程数据接收和数据发送模块,是指接收制造管理部门下发的计划、命令、标准、物料代码及工器具有关信息数据,写入数据表。
每一炉生产结束后将应用系统收集到的数据向MES发送计划状态、实绩及事件信息。
模块二:数据跟踪采集模块,是指电炉、精炼、连铸及模铸过程跟踪系统获取PLC数据后,据模块一MES下发的数据,进行有效地匹配,收集整理,调用模块一,向外发送。
3.1 工程数据收集及发送模块工程数据接收主要是指接收MES下发的计划、命令、配料代码、通用制造标准、工器具信息、连模铸制造命令及实绩应答等电文。
工程数据发送管理主要向MES发送电炉系统中的电炉及精炼两个系统的上位料仓装料信息、电炉料篮装料信息、电炉作业实绩、电炉事件信息、精炼作业实绩、精炼取样实绩、精炼事件信息、连铸炉次作业实绩、连铸板坯作业实绩、模铸炉次作业实绩、模铸钢锭作业实绩等电文。