热镀锌工艺
热镀锌工艺流程
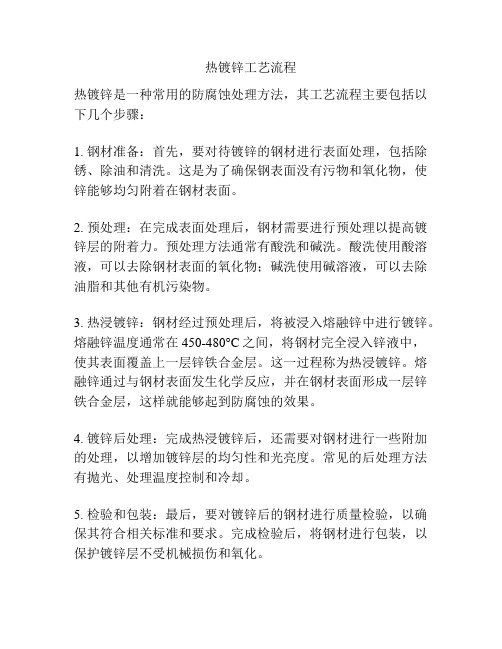
热镀锌工艺流程
热镀锌是一种常用的防腐蚀处理方法,其工艺流程主要包括以下几个步骤:
1. 钢材准备:首先,要对待镀锌的钢材进行表面处理,包括除锈、除油和清洗。
这是为了确保钢表面没有污物和氧化物,使锌能够均匀附着在钢材表面。
2. 预处理:在完成表面处理后,钢材需要进行预处理以提高镀锌层的附着力。
预处理方法通常有酸洗和碱洗。
酸洗使用酸溶液,可以去除钢材表面的氧化物;碱洗使用碱溶液,可以去除油脂和其他有机污染物。
3. 热浸镀锌:钢材经过预处理后,将被浸入熔融锌中进行镀锌。
熔融锌温度通常在450-480°C之间,将钢材完全浸入锌液中,
使其表面覆盖上一层锌铁合金层。
这一过程称为热浸镀锌。
熔融锌通过与钢材表面发生化学反应,并在钢材表面形成一层锌铁合金层,这样就能够起到防腐蚀的效果。
4. 镀锌后处理:完成热浸镀锌后,还需要对钢材进行一些附加的处理,以增加镀锌层的均匀性和光亮度。
常见的后处理方法有抛光、处理温度控制和冷却。
5. 检验和包装:最后,要对镀锌后的钢材进行质量检验,以确保其符合相关标准和要求。
完成检验后,将钢材进行包装,以保护镀锌层不受机械损伤和氧化。
总之,热镀锌的工艺流程主要包括钢材准备、表面处理、预处理、热浸镀锌、镀锌后处理、检验和包装等步骤。
这些步骤的完成可以确保钢材得到均匀的镀锌层,并具有良好的防腐蚀性能。
热镀锌生产工艺
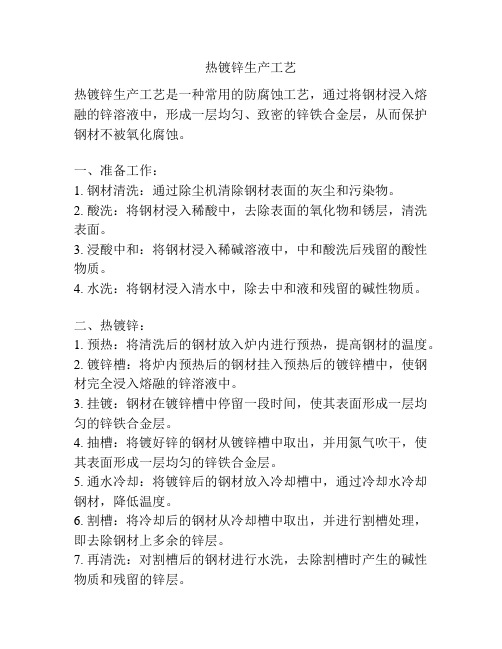
热镀锌生产工艺热镀锌生产工艺是一种常用的防腐蚀工艺,通过将钢材浸入熔融的锌溶液中,形成一层均匀、致密的锌铁合金层,从而保护钢材不被氧化腐蚀。
一、准备工作:1. 钢材清洗:通过除尘机清除钢材表面的灰尘和污染物。
2. 酸洗:将钢材浸入稀酸中,去除表面的氧化物和锈层,清洗表面。
3. 浸酸中和:将钢材浸入稀碱溶液中,中和酸洗后残留的酸性物质。
4. 水洗:将钢材浸入清水中,除去中和液和残留的碱性物质。
二、热镀锌:1. 预热:将清洗后的钢材放入炉内进行预热,提高钢材的温度。
2. 镀锌槽:将炉内预热后的钢材挂入预热后的镀锌槽中,使钢材完全浸入熔融的锌溶液中。
3. 挂镀:钢材在镀锌槽中停留一段时间,使其表面形成一层均匀的锌铁合金层。
4. 抽槽:将镀好锌的钢材从镀锌槽中取出,并用氮气吹干,使其表面形成一层均匀的锌铁合金层。
5. 通水冷却:将镀锌后的钢材放入冷却槽中,通过冷却水冷却钢材,降低温度。
6. 割槽:将冷却后的钢材从冷却槽中取出,并进行割槽处理,即去除钢材上多余的锌层。
7. 再清洗:对割槽后的钢材进行水洗,去除割槽时产生的碱性物质和残留的锌层。
8. 测厚:使用厚度测量仪,测量镀锌层的厚度,确保符合相关标准要求。
三、包装:对测厚合格的镀锌钢材进行包装,一般采用编织袋或木托盘包装,以避免钢材受到损坏。
四、质量检验:对镀锌钢材进行质量检验,包括外观检查、厚度测量、结合力测试等,确保质量符合相关标准要求。
以上是热镀锌生产工艺的基本流程,通过严格的操作控制和质量检验,可保证镀锌钢材的防腐蚀性能和使用寿命。
同时,为了提高生产效率和节约能源,可以采用先浸锌后切割的工艺,即在钢材切割成型前先进行热镀锌处理,以减少锌层割槽时的消耗。
热镀锌施工工艺及品控要点

热镀锌施工工艺及品控要点1.清洗:首先要对钢材进行清洗,去除钢材表面的油污和杂质。
清洗可以采用浸泡或喷洗的方式,使钢材表面净化。
2.打磨:清洗完毕后,需要对钢材表面进行打磨,去除表面的锈蚀和氧化层,使得锌涂层能够更好地与钢材表面结合。
3.预处理:打磨完毕后,需要对钢材进行预处理。
一般采用酸洗或喷射清理的方法,去除钢材表面的氧化物,增加镀锌的附着力。
4.浸泡:将预处理完的钢材通过吊篮或者滚筒浸入熔融的锌液中。
锌液的温度一般在440°C左右。
5.出锌:浸泡一定时间后,将钢材从锌液中取出,将多余的锌液滴落,然后钢材通过气刀吹干。
6.检验:热镀锌完成后,需要对镀锌层进行检验。
可以采用外观检验、厚度测量、附着力测试等方法,确保镀锌层的质量符合要求。
1.原材料检验:在选择钢材时,要对原材料进行检验,主要包括成分分析、力学性能、表面缺陷等方面的测试。
只有符合要求的钢材才能进行后续的热镀锌施工。
2.检验设备:为了保证热镀锌的质量,需要配备合适的检验设备,包括外观检验仪器、厚度测量仪器、附着力测试仪器等。
同时,检验设备需要定期校准,确保其准确性。
3.生产过程控制:在整个热镀锌施工过程中,要严格控制每个环节的操作过程。
包括清洗、打磨、预处理、浸泡、出锌等各个步骤,都要按照规定的工艺进行操作。
4.工艺参数控制:在热镀锌施工中,有一些关键的工艺参数需要控制,包括浸泡时间、浸泡温度、浸泡速度等。
这些参数对镀层的厚度、均匀性和附着力都有影响,需要严格控制。
5.严格检验要求:对于热镀锌施工完成的产品,要进行严格的检验。
只有符合要求的产品才能出厂,确保产品质量。
6.定期维护:热镀锌设备需要定期维护,保持设备的正常运转。
同时,要对生产过程中的各个环节进行回顾和总结,及时进行改进。
总结:。
热镀锌工艺规程

热镀锌工艺规程一、前期处理1、脱脂目的:去除金属表面的油脂、污垢等杂质,以保证后续处理的效果。
方法:可以采用化学脱脂或电解脱脂的方式。
化学脱脂通常使用碱性溶液,如氢氧化钠、碳酸钠等;电解脱脂则是在直流电的作用下,通过电极反应去除油脂。
2、酸洗目的:除去金属表面的氧化皮、锈蚀物等。
溶液:一般使用盐酸或硫酸溶液。
注意事项:酸洗时间要控制得当,避免过度酸洗导致金属基体受到侵蚀。
酸洗后要用清水冲洗干净,防止酸液残留。
3、水洗目的:洗掉脱脂和酸洗后残留在金属表面的化学药剂。
要求:采用流动的清水进行多次冲洗,确保金属表面干净。
4、助镀目的:提高镀锌层的附着力和均匀性。
助镀剂:通常是氯化锌和氯化铵的混合溶液。
操作:将经过水洗的工件浸入助镀剂中,然后取出烘干。
二、热镀锌操作1、锌液准备锌锭的选择:应选用纯度高、杂质少的锌锭。
锌液温度控制:一般保持在 440 460℃之间。
温度过低,锌液流动性差,镀锌层不均匀;温度过高,锌液容易氧化,消耗增加。
2、镀锌将经过助镀处理的工件浸入锌液中,保持一定时间,使锌层附着在工件表面。
浸入时间和提出速度:根据工件的材质、形状和厚度来确定。
一般来说,厚工件浸入时间长,提出速度慢;薄工件则相反。
3、冷却镀锌后的工件应迅速进行冷却,以防止锌层氧化和结晶粗大。
冷却方式:可以采用风冷或水冷。
三、后期处理1、钝化目的:提高镀锌层的耐腐蚀性和装饰性。
钝化液:常见的有铬酸盐钝化液、磷酸盐钝化液等。
操作:将冷却后的工件浸入钝化液中进行处理。
2、修整检查镀锌层的质量,如有局部缺陷,进行修整处理。
修整方法:可以采用打磨、补镀等方式。
3、检验外观检查:观察镀锌层表面是否光滑、均匀,有无漏镀、起泡、剥落等缺陷。
厚度检测:使用专门的仪器测量镀锌层的厚度,确保符合标准要求。
四、质量控制1、原材料控制对锌锭、助镀剂等原材料进行质量检验,确保符合工艺要求。
2、工艺参数控制严格控制脱脂、酸洗、镀锌等过程中的温度、时间、浓度等工艺参数,定期进行检测和调整。
热镀锌工艺流程及原理

热镀锌工艺流程及原理热镀锌是一种保护钢铁腐蚀的方法,通过在钢铁表面形成一层锌层来达到防腐的目的。
热镀锌工艺流程主要包括预处理、镀锌和后处理三个步骤。
首先是预处理,其目的是清除钢铁表面的油脂、氧化物和其他杂质,以便于锌层的附着和均匀性。
预处理包括碱洗、酸洗和镇静等步骤。
碱洗主要是使用碱性溶液清洁表面,并去除残留的油脂;酸洗则是使用酸性溶液将氧化物和锈蚀物质溶解;镇静则是利用草酸或陶瓷粉末等溶液来阻止表面的氧化。
接下来是镀锌步骤,镀锌可以通过浸镀或喷涂两种方式进行。
浸镀是将清洗过的钢铁浸入预热的镀锌槽中,槽中的锌溶液中的锌离子会与钢铁表面的铁原子发生电化学反应而形成锌层。
而喷涂则是将预热的钢铁表面喷涂上锌粉,然后加热使锌粉熔化并与钢铁表面反应形成锌层。
浸镀方式具有镀层均匀、质量稳定性好等优点,常用于大批量的生产。
而喷涂方式则适用于细小零件或特殊形状的工件。
最后是后处理,主要是为了提高锌层的光亮度和外观质量。
后处理包括烘干、光亮度调整和冷却等步骤。
烘干是将镀锌后的工件通过烘箱进行加热,除去残留的水分;光亮度调整则是通过化学处理或机械抛光来使锌层表面更加光亮;而冷却则是将工件快速冷却,以稳定锌层。
热镀锌的原理主要是利用锌与钢铁之间的电化学反应,形成一层紧密附着的锌层,从而对钢铁进行防腐。
在预处理中,通过碱洗和酸洗等方法清除钢铁表面的杂质,以利于锌层的附着。
而镀锌过程中,钢铁表面的铁原子与锌离子发生氧化还原反应,产生的锌层具有较好的防腐能力。
后处理则是为了提高锌层的光亮度和外观质量。
总的来说,热镀锌工艺流程包括预处理、镀锌和后处理三个步骤,通过清洁钢铁表面,使锌层与钢铁充分结合,从而实现对钢铁的防腐效果。
热镀锌的原理主要是利用铁与锌之间的电化学反应,形成锌层。
热镀锌工艺具有镀层均匀、防腐能力强等优点,在工业生产和建筑领域得到广泛应用。
镀锌管的生产工艺区分

镀锌管的生产工艺区分镀锌管是将钢管浸入熔融的锌液中,通过化学反应将钢管表面覆盖一层锌层的工艺。
镀锌管具有耐腐蚀、耐高温、外观美观等优点,广泛应用于建筑、化工、冶金、航空等领域。
根据生产工艺的不同,可将镀锌管分为热镀锌管和电镀锌管两种。
1. 热镀锌管的生产工艺热镀锌是一种通过将钢管浸入熔融的锌液中进行镀锌的工艺,热镀锌管具有镀层厚、耐腐蚀性好等特点。
下面是热镀锌管的生产工艺:(1)钢管准备:首先需要准备好待镀锌的钢管。
钢管应经过除锈、清洗等工序,确保钢管表面没有铁锈、油污等杂质。
(2)酸洗处理:将钢管浸入盛有稀酸的酸洗槽中,通过酸洗处理,去除钢管表面的氧化铁皮和锈蚀物。
(3)热浸镀锌:将经过酸洗处理的钢管浸入预热的锌液中,在高温下进行镀锌。
在熔融的锌液中,钢管表面的铁与锌发生化学反应,生成锌铁合金层。
(4)冷却、清洗:镀锌后的钢管经过冷却和清洗等处理,使其表面的锌层固化,并清除表面的铁锈、污垢等。
参数。
合格的镀锌管经过包装后可以出厂销售和使用。
2. 电镀锌管的生产工艺电镀锌管是通过电镀的方式在钢管表面形成一层锌层,电镀锌管的镀层薄、外观光亮、耐腐蚀性较好。
以下是电镀锌管的生产工艺:(1)钢管准备:同样需要准备待镀锌的钢管,对钢管进行除锈、清洗等处理,确保表面干净,无杂质。
(2)酸洗处理:将钢管浸入酸洗槽中,通过酸洗处理,去除钢管表面的氧化铁皮和锈蚀物。
(3)电解洗涤:将经过酸洗处理的钢管浸入电解槽中,通过电解的方式进行洗涤,去除表面的污垢和杂质。
(4)电镀锌:将经过电解洗涤的钢管浸入带有锌盐的电解液中,通过电流的作用,使钢管表面形成一层锌层。
(5)冷却、清洗:电镀后的钢管经过冷却和清洗等处理,使其表面的锌层固化,并清除表面的铁锈、污垢等。
等参数。
合格的电镀锌管经过包装后可以出厂销售和使用。
总结:热镀锌管和电镀锌管是两种常见的镀锌管,其生产工艺存在一定的区别。
热镀锌管是通过将钢管浸入熔融的锌液中进行镀锌,而电镀锌管是通过电解的方式在钢管表面形成一层锌层。
热镀锌工艺

热镀锌工艺
热镀锌工艺是高强度、耐腐蚀的金属材料表面处理技术。
它是一
种被广泛采用的电镀工艺,它可以在金属表面形成一层厚度小于10微
米的锌合金层,能有效地提高表面耐腐蚀性能,具有优异的附着力和
化学稳定性。
热镀锌通常采用三步处理制备锌合金层:先将待处理表
面洗涤干净,然后在表面连续溅射以锌为材料的合金层,最后在合金
层上熔炼涂装基体金层以使表面光洁平整;这样就可以形成一层厚度
小于10微米的锌合金层,使表面耐腐蚀性得到显著提高。
热镀锌工艺有三种常用实施方式,分别是喷射热镀锌、熔炼热镀
锌和溅射热镀锌。
喷射热镀锌工艺是最常用的处理方式,它采用喷雾
的方式先将水溶性的锌合金熔液溅射在表面,再在溅射的锌合金层上
加热,使之析出复合物,最终形成厚度小于10μm的锌合金层。
熔炼
热镀锌工艺采用将锌合金熔液倒入熔炉的方式,将其沉积在基体表面,然后将基体加热,使之析出复合物,形成厚度小于10µm的锌合金层。
溅射热镀锌工艺它采用电子束或超声束将锌合金涂覆在基体上,然后
将基体加热,使之析出复合物,形成厚度小于10μm的锌合金层。
热镀锌工艺主要用于金属表面处理,可以有效提高金属表面的抗
腐蚀性能,从而延长金属材料的使用寿命。
由于锌合金层的硬度比基
体表面低,因此可以起到润滑的作用,避免表面出现 wearing-
scratch等缺陷,大大提高了金属表面的外观质量和功能性能。
此外,
锌合金层具有良好的光泽度,可以改善表面的视觉效果,因此,热镀
锌工艺也被广泛应用于装潢、汽车等行业。
热镀锌工艺入门课程

热镀锌工艺入门课程热镀锌是一种常用的防腐蚀方法,具有广泛的应用领域,包括建筑、电力、交通等行业。
本文将介绍热镀锌工艺的入门课程,帮助读者了解其基本原理、工艺流程和操作要点。
一、基本原理热镀锌是指将铁制品(一般为钢材)在加热至一定温度后蘸入熔化的锌中,通过物理和化学反应在钢材表面形成一层锌铁合金镀层的工艺。
通过锌的阴极保护作用,为钢材提供了优异的防腐蚀性能。
二、工艺流程1. 原料准备:选择优质的钢材作为基材,并对其表面进行清洗、除油和除锈等预处理工作,确保镀层的附着力。
2. 酸洗:将钢材浸入酸性溶液中,去除表面的氧化物、锈蚀物和杂质,以提高镀层附着力。
3. 热镀锌:将经过酸洗的钢材通过起吊装置悬挂在镀锌槽中,控制锌槽内的液体温度保持在适当范围,使锌快速融化形成熔融锌液。
将钢材蘸入熔融锌液中,保持一定时间,使钢材表面和锌液中的铁发生反应,形成锌铁合金镀层。
4. 冷却:将锌化后的钢材从锌槽中提取出来,经过自然冷却或水冷却,使得镀层变硬并固定在钢材表面。
5. 检验:对热镀锌后的钢材进行外观检查和物理性能测试,确保镀层质量符合要求。
三、操作要点1. 控制镀液温度:热镀锌中的锌槽内的液体温度对于镀层质量至关重要,需要根据具体情况控制在合适范围。
2. 控制蘸锌时间:蘸锌时间的长短会影响镀层的厚度以及镀层结构,需要根据要求进行控制。
3. 避免过度晃动:在蘸锌过程中,要保持钢材稳定,避免过度晃动或与其他钢材相互碰撞,以保证镀层的均匀性和平整度。
4. 保护钢材的锌镀层:热镀锌后的钢材需要合理包装,避免与空气、水分或其他腐蚀性物质接触,以延长锌镀层的使用寿命。
通过本文的介绍,读者可以初步了解热镀锌工艺的基本原理、工艺流程和操作要点。
当然,热镀锌是一个较为复杂的工艺,对于实际操作还需要进一步的专业培训和实践经验。
四、镀层性能和应用热镀锌工艺可以提供均匀、致密、耐腐蚀的锌铁合金镀层,具有良好的防腐蚀性能和装饰性能。
镀锌钢材在户外环境下具有较长的使用寿命,能够有效延缓钢材的腐蚀速度,减少修补和更换的频率,降低使用成本。
热镀锌百度百科

1发展据《2013-2017年中国热镀锌行业发展前景与投资预测分析报告》[1]数据显示由于锌的标准电极电位负于铁,因此在水和潮湿的空气中镀锌层具有牺牲阳极保护钢基的作用,从而可以大大的延长钢材的使用寿命。
在工业上常用的镀锌层有热浸镀锌、电镀锌、机械镀锌和热喷涂(镀)锌等,其中热镀锌约占镀锌总量的95%,热镀锌用锌量在世界范围内占锌产量的40%,在中国约占锌产量的30%左右。
热镀锌是将钢、不锈钢、铸铁等金属浸入熔融液态金属或合金中获得镀层的一种工艺技术。
前瞻网认为热镀锌是当今世界上应用最广泛、性能价格比最优的钢材表面处理方法。
热镀锌产品对钢铁的减蚀延寿、节能节材起着不可估量和不可替代的作用,同时镀层钢材也是国家扶植和优先发展的高附加值短线产品。
随着西部大开发战略的实施,西电东送、西气东输、南水北调、三峡工程、农网及城市电网二网改造等项目的深入展开,我国热镀锌行业已进入新一轮的高速发展阶段。
2原理1 引言热镀锌也称热浸镀锌,是钢铁构件浸入熔融的锌液中获得金属覆盖层的一种方法。
近年来随高压输电、交通、通讯事业迅速发展,对钢铁件防护要求越来越高,热镀锌需求量也不断增加。
2 热镀锌层防护性能通常电镀锌层厚度5~15μm,而热镀锌层一般在35μm以上,甚至高达200μm。
热镀锌覆盖能力好,镀层致密,无有机物夹杂。
众所周知,锌的抗大气腐蚀的机理有机械保护及电化学保护,在大气腐蚀条件下锌层表面有ZnO、Zn(OH)2及碱式碳酸锌保护膜,一定程度上减缓锌的腐蚀,这层保护膜(也称白锈)受到破坏又会形成新的膜层。
当锌层破坏严重,危及到铁基体时,锌对基体产生电化学保护,锌的标准电位-0.76V,铁的标准电位-0.44V,锌与铁形成微电池时锌作为阳极被溶解,铁作为阴极受到保护。
显然热镀锌对基体金属铁的抗大气腐蚀能力优于电镀锌。
3 热镀锌层形成过程热镀锌层形成过程是铁基体与最外面的纯锌层之间形成铁-锌合金的过程,工件表面在热浸镀时形成铁-锌合金层,才使得铁与纯锌层之间很好结合,其过程可简单地叙述为:当铁工件浸入熔融的锌液时,首先在界面上形成锌与α铁(体心)固熔体。
什么是热镀锌加工工艺
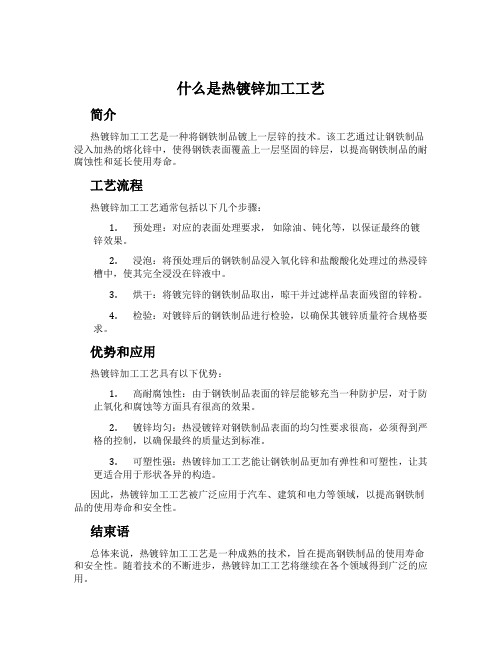
什么是热镀锌加工工艺
简介
热镀锌加工工艺是一种将钢铁制品镀上一层锌的技术。
该工艺通过让钢铁制品浸入加热的熔化锌中,使得钢铁表面覆盖上一层坚固的锌层,以提高钢铁制品的耐腐蚀性和延长使用寿命。
工艺流程
热镀锌加工工艺通常包括以下几个步骤:
1.预处理:对应的表面处理要求,如除油、钝化等,以保证最终的镀
锌效果。
2.浸泡:将预处理后的钢铁制品浸入氧化锌和盐酸酸化处理过的热浸锌
槽中,使其完全浸没在锌液中。
3.烘干:将镀完锌的钢铁制品取出,晾干并过滤样品表面残留的锌粉。
4.检验:对镀锌后的钢铁制品进行检验,以确保其镀锌质量符合规格要
求。
优势和应用
热镀锌加工工艺具有以下优势:
1.高耐腐蚀性:由于钢铁制品表面的锌层能够充当一种防护层,对于防
止氧化和腐蚀等方面具有很高的效果。
2.镀锌均匀:热浸镀锌对钢铁制品表面的均匀性要求很高,必须得到严
格的控制,以确保最终的质量达到标准。
3.可塑性强:热镀锌加工工艺能让钢铁制品更加有弹性和可塑性,让其
更适合用于形状各异的构造。
因此,热镀锌加工工艺被广泛应用于汽车、建筑和电力等领域,以提高钢铁制品的使用寿命和安全性。
结束语
总体来说,热镀锌加工工艺是一种成熟的技术,旨在提高钢铁制品的使用寿命和安全性。
随着技术的不断进步,热镀锌加工工艺将继续在各个领域得到广泛的应用。
热镀锌的工艺
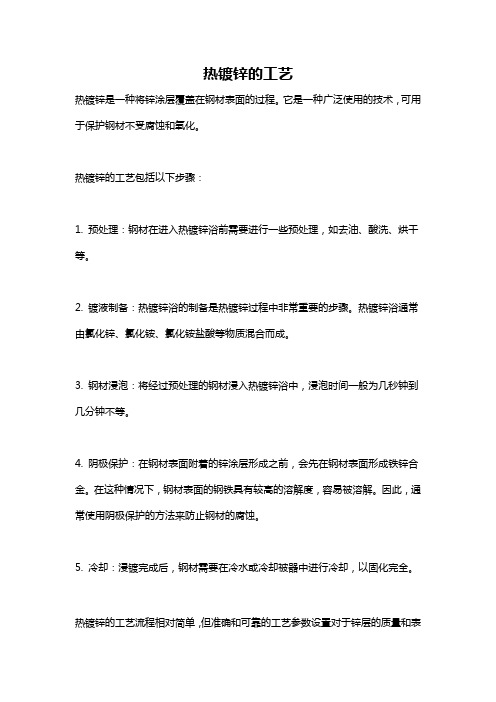
热镀锌的工艺
热镀锌是一种将锌涂层覆盖在钢材表面的过程。
它是一种广泛使用的技术,可用于保护钢材不受腐蚀和氧化。
热镀锌的工艺包括以下步骤:
1. 预处理:钢材在进入热镀锌浴前需要进行一些预处理,如去油、酸洗、烘干等。
2. 镀液制备:热镀锌浴的制备是热镀锌过程中非常重要的步骤。
热镀锌浴通常由氯化锌、氯化铵、氯化铵盐酸等物质混合而成。
3. 钢材浸泡:将经过预处理的钢材浸入热镀锌浴中,浸泡时间一般为几秒钟到几分钟不等。
4. 阴极保护:在钢材表面附着的锌涂层形成之前,会先在钢材表面形成铁锌合金。
在这种情况下,钢材表面的钢铁具有较高的溶解度,容易被溶解。
因此,通常使用阴极保护的方法来防止钢材的腐蚀。
5. 冷却:浸镀完成后,钢材需要在冷水或冷却被器中进行冷却,以固化完全。
热镀锌的工艺流程相对简单,但准确和可靠的工艺参数设置对于锌层的质量和表
面性质非常关键。
热镀锌的工艺流程
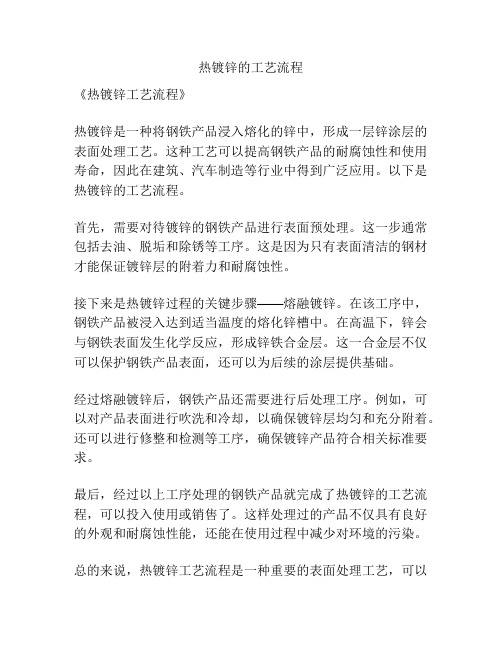
热镀锌的工艺流程
《热镀锌工艺流程》
热镀锌是一种将钢铁产品浸入熔化的锌中,形成一层锌涂层的表面处理工艺。
这种工艺可以提高钢铁产品的耐腐蚀性和使用寿命,因此在建筑、汽车制造等行业中得到广泛应用。
以下是热镀锌的工艺流程。
首先,需要对待镀锌的钢铁产品进行表面预处理。
这一步通常包括去油、脱垢和除锈等工序。
这是因为只有表面清洁的钢材才能保证镀锌层的附着力和耐腐蚀性。
接下来是热镀锌过程的关键步骤——熔融镀锌。
在该工序中,钢铁产品被浸入达到适当温度的熔化锌槽中。
在高温下,锌会与钢铁表面发生化学反应,形成锌铁合金层。
这一合金层不仅可以保护钢铁产品表面,还可以为后续的涂层提供基础。
经过熔融镀锌后,钢铁产品还需要进行后处理工序。
例如,可以对产品表面进行吹洗和冷却,以确保镀锌层均匀和充分附着。
还可以进行修整和检测等工序,确保镀锌产品符合相关标准要求。
最后,经过以上工序处理的钢铁产品就完成了热镀锌的工艺流程,可以投入使用或销售了。
这样处理过的产品不仅具有良好的外观和耐腐蚀性能,还能在使用过程中减少对环境的污染。
总的来说,热镀锌工艺流程是一种重要的表面处理工艺,可以
为钢铁产品提供良好的抗腐蚀性和使用寿命。
通过适当的工艺控制和后处理工序,可以确保镀锌产品的质量和性能。
热镀锌工艺流程完整版

热镀锌工艺流程HEN system office room 【HEN16H-HENS2AHENS8Q8-HENH1688】热镀锌工艺流程一、镀前检查目的:为锌浴提供清洁工件,以便钢基体表面和熔融锌充分反应。
◆洗前检查1、检查原则:认真、仔细,必要时做适当的记录。
2、检查内容:主要查来料材质、尺寸结构、有无变形,有无油漆、油脂及其它污垢粘附。
◆前处理针对待镀件结构形状,进行必要的打孔、栓挂等下料的准备。
◆脱脂:针对含有油漆、油脂类的待镀件,进行脱油脱脂处理。
脱脂温度:≥70℃;浓度:≥7%;时间:视待镀件情况而定。
◆水洗:将经脱脂的待镀件进行水洗处理,使其PH值在10以下,以便于下一阶段除锈。
◆酸洗除锈1、酸槽要求:有计划性、目的性的根据来料的材质、紧急情况、难易洗程度合理选择酸槽下料。
酸度:≤20%;时间:视待镀件情况定。
2、影响酸洗速度的因素:⑴氧化铁皮的结构和厚度:⑵酸洗液种类及浓度:⑶酸液中铁盐含量:⑷酸洗温度:⑸酸洗操作方式:⑹钢铁成分:3、下料、酸洗要求:⑴严格遵守行车使用规范进行下料操作。
⑵酸洗下料应根据待镀件的材质、数量、结构情况等选择合理的摆放方式。
对成打包捆洗的待镀件务必留一定空隙,杜绝叠加、积压。
⑶酸洗期间应勤翻动待镀件。
确保无漏洗、过洗、夹线、涡气、偏析等现象。
及时打捞漂浮物及因翻动等原因造成的落池镀件等。
⑷严格控制好酸洗时间,当班或交班时应交代清楚酸槽中的黑件。
禁止长时间将黑件浸泡在酸槽内。
⑸对于已洗好黑件,应及时进行下一工序,尽可能的杜绝再次酸洗或长时间放在空气中。
4、洗好镀件要控净酸液再进入下一工序处理。
◆水洗:水洗两道,确保酸被洗去,待镀件PH≥2。
◆助镀处理+作用:可保持在浸镀前工件具有一定活性,以增强镀层与基体结合。
机理:(1) 清洁钢铁表面,去除掉酸洗后钢件表面上的一些铁盐、氧化物及其它脏物。
(2) 净化钢件浸入锌液处的液相锌,使钢件与液态锌快速浸润并反应。
(3) 在钢件表面沉积一层盐膜,可将钢件表面与空气隔绝,防止进一步微氧化。
热镀锌工艺流程
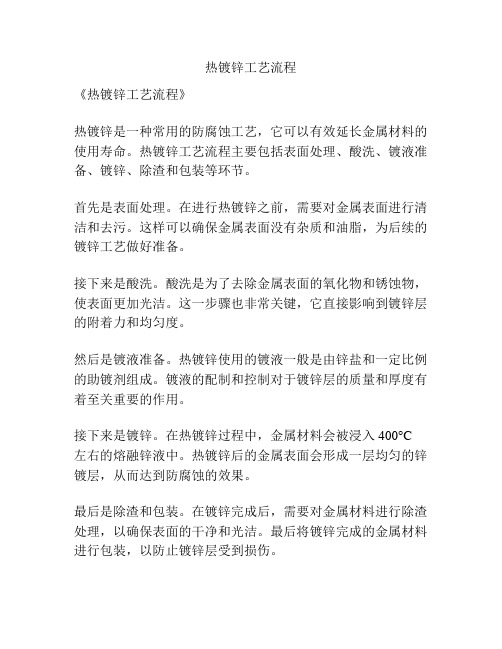
热镀锌工艺流程
《热镀锌工艺流程》
热镀锌是一种常用的防腐蚀工艺,它可以有效延长金属材料的使用寿命。
热镀锌工艺流程主要包括表面处理、酸洗、镀液准备、镀锌、除渣和包装等环节。
首先是表面处理。
在进行热镀锌之前,需要对金属表面进行清洁和去污。
这样可以确保金属表面没有杂质和油脂,为后续的镀锌工艺做好准备。
接下来是酸洗。
酸洗是为了去除金属表面的氧化物和锈蚀物,使表面更加光洁。
这一步骤也非常关键,它直接影响到镀锌层的附着力和均匀度。
然后是镀液准备。
热镀锌使用的镀液一般是由锌盐和一定比例的助镀剂组成。
镀液的配制和控制对于镀锌层的质量和厚度有着至关重要的作用。
接下来是镀锌。
在热镀锌过程中,金属材料会被浸入400°C
左右的熔融锌液中。
热镀锌后的金属表面会形成一层均匀的锌镀层,从而达到防腐蚀的效果。
最后是除渣和包装。
在镀锌完成后,需要对金属材料进行除渣处理,以确保表面的干净和光洁。
最后将镀锌完成的金属材料进行包装,以防止镀锌层受到损伤。
综上所述,热镀锌工艺流程是一个复杂的工艺过程,需要各个环节的精准控制和操作。
只有严格按照工艺要求进行操作,才能得到质量和效果都很好的热镀锌产品。
热镀锌的工艺流程
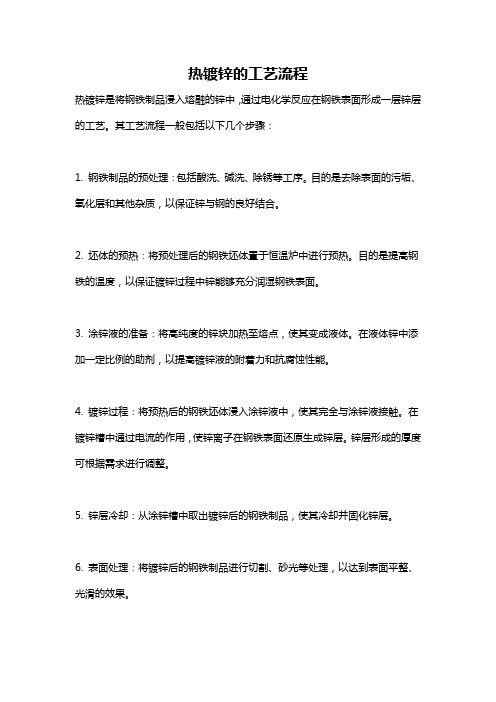
热镀锌的工艺流程
热镀锌是将钢铁制品浸入熔融的锌中,通过电化学反应在钢铁表面形成一层锌层的工艺。
其工艺流程一般包括以下几个步骤:
1. 钢铁制品的预处理:包括酸洗、碱洗、除锈等工序。
目的是去除表面的污垢、氧化层和其他杂质,以保证锌与钢的良好结合。
2. 坯体的预热:将预处理后的钢铁坯体置于恒温炉中进行预热。
目的是提高钢铁的温度,以保证镀锌过程中锌能够充分润湿钢铁表面。
3. 涂锌液的准备:将高纯度的锌块加热至熔点,使其变成液体。
在液体锌中添加一定比例的助剂,以提高镀锌液的附着力和抗腐蚀性能。
4. 镀锌过程:将预热后的钢铁坯体浸入涂锌液中,使其完全与涂锌液接触。
在镀锌槽中通过电流的作用,使锌离子在钢铁表面还原生成锌层。
锌层形成的厚度可根据需求进行调整。
5. 锌层冷却:从涂锌槽中取出镀锌后的钢铁制品,使其冷却并固化锌层。
6. 表面处理:将镀锌后的钢铁制品进行切割、砂光等处理,以达到表面平整、光滑的效果。
7. 检验与包装:对镀锌后的钢铁制品进行表面质量检验,如厚度测量、附着力测试、耐腐蚀性能检测等。
最后进行包装,以便运输和储存。
以上就是热镀锌的工艺流程,每个步骤都需要严格控制工艺参数和质量要求,以确保镀锌层的质量和性能。
热镀锌工艺流程
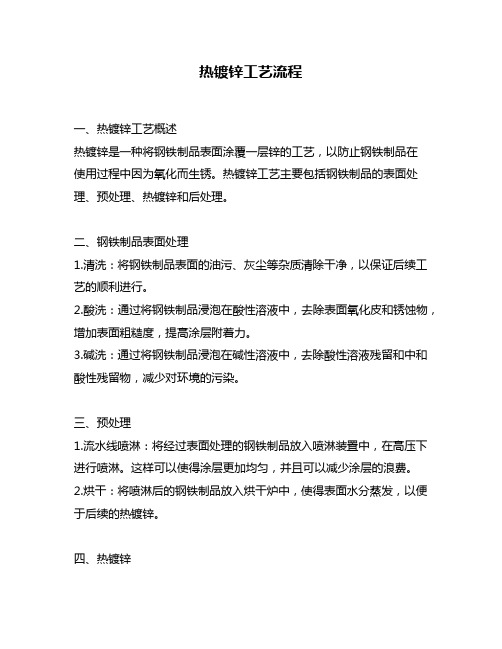
热镀锌工艺流程一、热镀锌工艺概述热镀锌是一种将钢铁制品表面涂覆一层锌的工艺,以防止钢铁制品在使用过程中因为氧化而生锈。
热镀锌工艺主要包括钢铁制品的表面处理、预处理、热镀锌和后处理。
二、钢铁制品表面处理1.清洗:将钢铁制品表面的油污、灰尘等杂质清除干净,以保证后续工艺的顺利进行。
2.酸洗:通过将钢铁制品浸泡在酸性溶液中,去除表面氧化皮和锈蚀物,增加表面粗糙度,提高涂层附着力。
3.碱洗:通过将钢铁制品浸泡在碱性溶液中,去除酸性溶液残留和中和酸性残留物,减少对环境的污染。
三、预处理1.流水线喷淋:将经过表面处理的钢铁制品放入喷淋装置中,在高压下进行喷淋。
这样可以使得涂层更加均匀,并且可以减少涂层的浪费。
2.烘干:将喷淋后的钢铁制品放入烘干炉中,使得表面水分蒸发,以便于后续的热镀锌。
四、热镀锌1.浸泡:将经过预处理的钢铁制品浸泡在预热好的锌液中。
在浸泡过程中,钢铁制品表面会与锌液发生反应,形成一层锌铁合金层。
2.振动:通过振动装置,使得钢铁制品在锌液中不断地摆动,以保证整个表面都能够均匀地被覆盖上一层锌铁合金层。
3.出池:将经过热镀锌的钢铁制品从锌液中取出,并且通过高压水枪冲洗表面残留的锌液。
五、后处理1.冷却:将经过高温处理的钢铁制品放入冷却池中进行冷却。
这样可以避免因为高温而导致表面氧化皮再次生成。
2.修整:对于热镀锌过程中出现的缺陷和不良现象进行修整和处理。
3.检测:对于经过热镀锌的钢铁制品进行严格的检测,以保证其质量符合相关标准。
六、总结热镀锌工艺是一种非常重要的表面处理工艺,可以有效地提高钢铁制品的耐腐蚀性能,延长其使用寿命。
在实际应用中,需要严格按照流程进行操作,并且加强质量控制,以保证最终产品的质量。
- 1、下载文档前请自行甄别文档内容的完整性,平台不提供额外的编辑、内容补充、找答案等附加服务。
- 2、"仅部分预览"的文档,不可在线预览部分如存在完整性等问题,可反馈申请退款(可完整预览的文档不适用该条件!)。
- 3、如文档侵犯您的权益,请联系客服反馈,我们会尽快为您处理(人工客服工作时间:9:00-18:30)。
热镀锌工艺
公司内部档案编码:[OPPTR-OPPT28-OPPTL98-OPPNN08]
什么是热镀锌
热镀锌又称为热浸镀锌,他是在高
温下把锌锭融化,在放入一些辅助材
料,然后把金属结构件浸入镀锌槽中,
使金属构件上附着一层锌层。
热镀锌的
优点在于他的防腐能力强,镀锌层的附
着力和硬度较好。
缺点在于价格较高,
需要大量的设备和场地,钢结构件过大
不易放入镀锌槽中,钢结构件过于单
薄,热镀又容易变形。
富锌涂料一般指
的是含有锌粉的防腐涂料。
市场上的富
锌涂料含锌量一。
备料—酸洗—水洗—助溶—热浸锌—冷却—钝化—清洗—分检—复检—包装—入库
一、热镀锌工艺过程及有关说明
工艺过程
工件→脱脂→水洗→酸洗→水洗→浸助镀溶剂→烘干预热→热镀锌→整理→冷却→钝化→漂洗→干燥→检验
有关工艺过程说明
(1)脱脂
可采用化学去油或水基金属脱脂清洗剂去油,达到工件完全被水浸润为止。
(2)酸洗
可采用H2SO4 15%,硫脲%,40~60℃或用HCl 20%,六次甲基四胺1~
3g/L,20~40℃进行酸洗。
加入缓蚀剂可防止基体过腐蚀及减少铁基体吸氢量。
脱脂及酸洗处理不好会造成镀层附着力不好,镀不上锌或锌层脱落。
(3)浸助镀剂
也称结合剂,可保持在浸镀前工件具有一定活性,以增强镀层与基体结合。
NH4Cl 15%~25%,ZnCl2 %~%,55~65℃,5~10min。
为减少NH4Cl挥发可适当加入甘油。
(4)烘干预热
为了防止工件在浸镀时由于温度急剧升高而变形,并除去残余水分,防止产生爆锌,造成锌液爆溅,预热一般为120~180℃。
(5)热镀锌
要控制好锌液温度、浸镀时间及工件从锌液中移出的速度。
温度过低,锌液流动性差,镀层厚且不均匀,易产生流挂,外观质量差;温度高,锌液流动性好,锌液易脱离工件,减少流挂及皱皮现象发生,附着力强,镀层薄,外观好,生产效率高;但温度过高,工件及锌锅铁损严重,产生大量锌渣,影响浸锌层质量,锌耗大,甚至无法施镀。
在同一温度下,浸镀时间长,镀层厚。
不同温度,要求同样的厚度时,高温浸镀所需时间长。
一般厂家为了防止工件高温变形及减少由于铁损造成锌渣,都采用450~470℃,~。
有些工厂对大工件及铸铁件采用较高温度,但要避开铁损高峰的温度范围。
为了提高在较低温度下热浸镀液的流动性,防止镀层过厚,并提高镀层外观,常常加入%~%的纯铝。
铝要少量多次加入。
(6)整理
镀后对工件整理主要是去除表面余锌及锌瘤,用震动或手工方法均可。
(7)钝化
目的是提高工件表面抗大气腐蚀性能,减少或延长白锈出现时间,保持镀层具有良好的外观。
都用铬酸盐钝化,如Na2Cr2O7 80~100g/L,硫酸3~
4ml/L。
(8)冷却
一般用水冷,但温度不可过低,防止工件,特别是铸件由于激冷回缩产生基体组织开裂。
(9)检验
镀层外观光亮、细致、无流挂、皱皮现象。
厚度检验可采用涂层测厚仪,方法比较简便。
也可通过锌附着量进行换算得到镀层厚度。
结合强度可采用弯曲压力机,将样件作90~180°弯曲,应无裂纹及镀层脱落。
也可用重锤敲击检验。
二、热镀锌层形成过程
热镀锌层形成过程是铁基体与最外面的纯锌层之间形成铁-锌合金的过程,工件表面在热浸镀时形成铁-锌合金层,才使得铁与纯锌层之间很好结合,其过程可简单地叙述为:当铁工件浸入熔融的锌液时,首先在界面上形成锌与α铁(体心)固熔体。
这是基体金属铁在固体状态下溶有锌原子所形成一种晶体,两种金属原子之间是融合,原子之间引力比较小。
因此,当锌在固熔体中达到饱和后,锌铁两种元素原子相互扩散,扩散到(或叫渗入)铁基体中的锌原子在基体晶格中迁移,逐渐与铁形成合金,而扩散到熔融的锌液中的铁就与锌形成金属间化合物FeZn13,沉入热镀锌锅底,即为锌渣。
当工件从浸锌液中移出时表面形成纯锌层,为六方晶体。
其含铁量不大于%。
三、热镀锌层防护性能
通常电镀锌层厚度5~15μm,而热镀锌层一般在65μm以上,甚至高达100μm。
热镀锌覆盖能力好,镀层致密,无有机物夹杂。
众所周知,锌的抗大气腐蚀的机理有机械保护及电化学保护,在大气腐蚀条件下锌层表面有ZnO、Zn(OH)2及碱式碳酸锌保护膜,一定程度上减缓锌的腐蚀,这层保护膜(也称白锈)受到破坏又会形成新的膜层。
当锌层破坏严重,危及到铁基体时,锌对基体产生电化学保护,锌的标准电位,铁的标准电位,锌与铁形成微电池时锌作为
阳极被溶解,铁作为阴极受到保护。
显然热镀锌对基体金属铁的抗大气腐蚀能力优于电镀锌。
四、热镀锌过程锌灰、锌渣形成控制
锌灰锌渣不仅严重影响到浸锌层质量,造成镀层粗糙,产生锌瘤。
而且使热镀锌成本大大升高。
通常每镀1t工件耗锌80~120kg,如果锌灰锌渣严重,其耗锌量会高达140~200kg。
控制锌炭主要是控制好温度,减少锌液表面氧化而产生的浮渣。
国内有些厂家用耐火砂、炭灰等覆盖。
国外采用热传导率小、熔点高、比重小、与锌液不发生反应,既可减少热量失散又可防止氧化的陶瓷或玻璃球覆盖,这种球状物易被工件推开,又对工件无粘附作用。
对于锌液中锌渣的形成主要是溶解在锌液中的铁含量超过该温度下的溶解度时所形成的流动性极差的锌铁合金,锌渣中锌含量可高达95%,这是热镀锌成本高的关键所在。
从铁在锌液中的溶解度曲线可以看出:不同的温度及不同的保温时间,其溶铁量即铁损量是不一样的。
在500℃附近时,铁损量随着加温及保温时间急剧增加,几乎成直线关系。
低于或高于480~510℃范围,随时间延长铁损提高缓慢。
因此,人们将480~510℃称为恶性溶解区。
在此温度范围内锌液对工件及锌锅浸蚀最为严重,超过560℃铁损又明显增加,达到660℃以上锌对铁基体是破坏性浸蚀,锌渣会急剧增加,施镀无法进行。
因此,施镀目前多在450~480℃及520~560℃两个区域内进行。
锌渣量的控制
要减少锌渣就要减少锌液中铁的含量,就是要从减少铁溶解的诸因素着手:
⑴施镀及保温要避开铁的溶解高峰区,即不要在480~510℃时进行作业。
⑵锌锅材料尽可能选用含碳、含硅量低的钢板焊接。
含碳量高,锌液对铁锅浸蚀会加快,硅含量高也能促使锌液对铁的腐蚀。
目前多采用08F优质碳素钢板。
其含碳%%~%),含硅≤%,并含有能抑制铁被浸蚀的元素镍、铬等。
不可
用普通碳素钢,否则耗锌量大,锌锅寿命短。
也有人提出用碳化硅制作熔锌槽,虽然可解决铁损量,但造型工艺也是一个难题。
⑶要经常捞渣。
先将温度升高至工艺温度上限以便锌渣与锌液分离,然后降至工艺温度以下,使锌渣沉于槽底后用勺捞取。
落入锌液中镀件也要及时打捞。
⑷要防止助镀剂中铁随工件带入锌槽,助镀剂使用一定时间就有红褐色含铁的化合物生成,要定期滤去。
助镀剂pH值维护在5左右为好。
⑸镀液中铝少于%会加快沉渣的生成,适量铝不仅提高锌液的流动性,增加镀层亮度,而且有利于减少锌渣、锌灰。
少量铝浮在液面对减少氧化有益,过多影响镀层质量,产生缺斑现象。
⑹加热、升温要均匀,防止爆烧及局部过热。