注塑模具设计项目书
注塑模具设计作业指导书(注塑部)

注塑模具设计作业指导书(注塑部)1. 背景本指导书旨在为注塑部门的设计人员提供注塑模具设计作业的指导,以确保设计工作的高效性和质量。
注塑模具的设计是注塑工艺的关键环节,直接影响产品的质量和生产效率。
因此,设计人员需要掌握相关的专业知识和技能,并遵循一定的设计原则和标准。
2. 设计作业流程2.1 确定设计要求在开始设计作业之前,设计人员需要与产品设计部门和生产部门进行沟通,了解产品的要求和预期性能。
这些要求可能包括产品尺寸、材料要求、生产量要求等。
2.2 分析注塑工艺在确定设计要求后,设计人员需要对注塑工艺进行分析。
这包括注塑机的选择、模具结构的确定、注塑工艺参数的设定等。
设计人员应该具备一定的注塑工艺知识,以确保设计的可实施性和优化注塑过程。
2.3 模具设计在分析注塑工艺后,设计人员可以开始进行模具设计。
模具设计应包括以下几个方面:- 模具结构设计:根据产品的形状和尺寸要求,确定模具的结构,包括模具基板、模腔、模芯、冷却系统等。
- 模具材料选择:选择适合注塑工艺的模具材料,考虑材料的强度、耐磨性、耐腐蚀性等因素。
- 模具加工工艺:确定模具的加工工艺,包括数控加工、电火花等。
- 模具的标准部件选型:选择符合标准的模具部件,以提高模具的通用性和可靠性。
- 模具装配和调试:完成模具的装配和调试工作,确保模具运行稳定和正常。
2.4 模具验收完成模具设计后,设计人员需要与生产部门进行模具验收。
在模具验收过程中,需要检查模具的尺寸精度、操作性能、模具寿命等。
如果存在问题,设计人员需要及时进行调整和修改。
3. 设计原则和注意事项在进行注塑模具设计时,设计人员需要遵循以下原则和注意事项:- 合理性原则:设计应合理,确保产品质量和生产效率。
- 简化原则:模具结构应简化,以提高制造和维修的便利性。
- 可靠性原则:模具的结构应稳定可靠,能够经受长时间的注塑生产。
- 标准化原则:尽量使用标准模具部件,以提高模具的通用性和可靠性。
注塑模具设计说明书
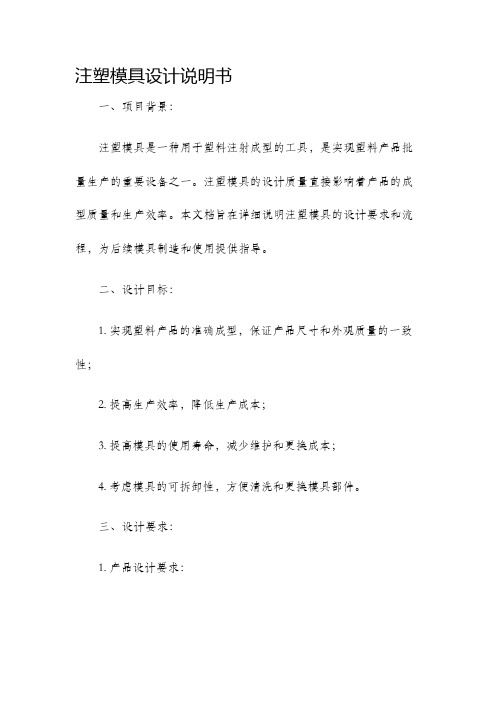
注塑模具设计说明书一、项目背景:注塑模具是一种用于塑料注射成型的工具,是实现塑料产品批量生产的重要设备之一。
注塑模具的设计质量直接影响着产品的成型质量和生产效率。
本文档旨在详细说明注塑模具的设计要求和流程,为后续模具制造和使用提供指导。
二、设计目标:1. 实现塑料产品的准确成型,保证产品尺寸和外观质量的一致性;2. 提高生产效率,降低生产成本;3. 提高模具的使用寿命,减少维护和更换成本;4. 考虑模具的可拆卸性,方便清洗和更换模具部件。
三、设计要求:1. 产品设计要求:a. 确定产品的尺寸和外观要求,提供详细的产品图纸和规格说明;b. 需要考虑产品的材料特性,如塑料的热胀冷缩性,流动性等;c. 确定产品的成型方式和注塑工艺参数。
2. 模具结构设计要求:a. 考虑产品的成型方式,确定模具的结构类型,如单腔模具、多腔模具等;b. 在满足产品尺寸和外观要求的基础上,尽量减小模具的尺寸和重量;c. 考虑模具的使用寿命,采用耐磨、耐腐蚀的材料,优化工艺和热处理;d. 考虑模具的冷却系统,保证注塑过程中材料的快速冷却和成型周期的缩短;e. 考虑模具的导向系统和定位系统,确保模具运动的准确性和稳定性;f. 考虑模具的拆卸性,方便清洗和更换模具部件。
3. 模具零件设计要求:a. 模具芯、模具腔、模具板等零件的尺寸要与产品尺寸要求一致;b. 避免尺寸过小、壁厚过薄等问题,确保零件的强度和刚性;c. 考虑零件的加工工艺,尽量减少加工难度和成本;d. 避免零件之间的干涉和碰撞,确保模具的正常运作;e. 采用标准化零件,方便制造和更换。
四、设计流程:1. 了解产品需求:与产品设计师沟通,收集产品图纸和规格说明;2. 制定模具设计方案:根据产品需求,确定模具的结构类型、尺寸和重量等;3. 进行模具设计:进行模具零件的设计,包括模具芯、模具腔、模具板等;4. 完善模具设计:考虑模具的冷却系统、导向系统、定位系统等;5. 优化模具设计:通过模拟和分析,优化模具结构和零件设计,提高模具的性能;6. 完成模具图纸:根据设计结果,绘制模具图纸,包括三维模型和二维工程图;7. 制造模具:将模具图纸提供给模具制造厂家,开始制造模具;8. 调试模具:完成模具制造后,进行模具调试和试模,保证模具的正常运行;9. 交付使用:完成模具调试后,交付给使用方,并提供模具的维护和保养指南。
典型注塑模设计-项目1-模块三

1.排气系统
大多数情况下可利用模具分型面或模具零件间的配合间隙自然地排气 ,其间隙值通常为0.01~0.03mm,以不产生溢料为限。
排气与引气系统的设计
相关理论知识
2.引气系统的设计 大型深壳形制品包紧型芯形成真空,难以脱模,需要引气装置。 镶拼式侧隙引气 气阀式引气 相关理论知识
能合理地设计浇注系统
能合理地进行成型零件设计
能正确地绘制模具装配图和零件工作图
1.能设计合理的冷却系统 2.能设计合理的排气系统 3.能绘制合理的冷却水道布置图
学习目标
工作任务
根据图示的塑件零件图以及已确定的总体结构方案,设计本模具的冷却系统和排气系统,并绘制冷却水道布置图。
冷却系统设计
低粘度-低模温
单击此处添加正文,文字是您思想的提炼,为了演示发布的良好效果,请言简意赅地阐述您的观点。您的内容已经简明扼要,字字珠玑,但信息却千丝万缕、错综复杂,需要用更多的文字来表述;但请您尽可能提炼思想的精髓,否则容易造成观者的阅读压力,适得其反。正如我们都希望改变世界,希望给别人带去光明,但更多时候我们只需要播下一颗种子,自然有微风吹拂,雨露滋养。恰如其分地表达观点,往往事半功倍。当您的内容到达这个限度时,或许已经不纯粹作用于演示,极大可能运用于阅读领域;无论是传播观点、知识分享还是汇报工作,内容的详尽固然重要,但请一定注意信息框架的清晰,这样才能使内容层次分明,页面简洁易读。如果您的内容确实非常重要又难以精简,也请使用分段处理,对内容进行简单的梳理和提炼,这样会使逻辑框架相对清晰。
根据图示的塑件零件图以及已确定的总体结构方案,设计本模具的冷却系统和排气系统并绘制冷却水道布置图。
练习
高粘度-高模温
注塑模具设计说明书

注塑模具设计说明书一、引言注塑模具是一种用于制造塑料制品的重要工具。
它具有精密设计和制造的特点,直接影响到注塑成型工艺的质量和效率。
本文档旨在提供一个注塑模具设计的详细说明书,以帮助使用者了解并正确使用注塑模具。
二、设计原则1. 功能性设计:注塑模具设计的首要目标是确保塑料制品的质量和精度。
需要考虑到产品的形状、尺寸、结构等因素,确保模具能够精确地复制产品的形状。
2. 可靠性设计:模具在长时间运行过程中需具有足够的可靠性和稳定性。
设计时应考虑到材料的选择、结构的合理性、工艺性能等因素,以确保模具能够长时间稳定运行。
3. 高效性设计:注塑模具的设计还要考虑到生产效率的提高。
在保证产品质量的前提下,优化流程、减少工序、提高生产速度等都是设计中需要考虑的因素。
三、设计要点1. 产品参数分析:仔细研究产品的形状、尺寸、材料等参数,并根据不同产品的要求进行合理设计。
2. 模具结构设计:根据产品的特点设计合理的模具结构,包括模具的分型面、脱模方式、冷却系统等。
3. 材料选择:根据产品和模具的要求选择合适的材料,考虑材料的韧性、硬度、耐磨性等因素。
4. 流道系统设计:设计合理的流道系统,以保证熔融塑料流动均匀,避免短流、死角等问题,提高注塑成型过程的效率。
5. 冷却系统设计:优化冷却系统的设计,保证塑料在注塑过程中能够迅速冷却固化,提高生产效率并减少翘曲、变形等问题。
6. 模具表面处理:根据产品的表面要求进行合适的模具表面处理,包括抛光、喷涂等,以提高产品的表面质量。
7. 模具装配:模具设计时应考虑装配的便利性和准确性,保证模具能够容易安装和拆卸。
四、注意事项1. 安全操作:在使用注塑模具时,必须严格遵守相关的操作规程和安全要求,保证操作人员的人身安全。
2. 维护保养:定期对模具进行清洁和维护保养,保证模具的正常运行和寿命的延长。
3. 记录维护:对模具的使用情况进行记录,包括使用次数、维修情况等,以便及时调整维修周期和保养计划。
塑料模具设计训练项目任务单

塑料模具设计训练项目任务单塑料模具设计训练项目任务单1.项目概述塑料模具是工业制品的重要部分,其质量和手感直接影响到整个产品的品质。
塑料模具设计是一项复杂的工程,需要涵盖多个学科领域的知识,包括材料科学、机械制造、工业设计等。
本训练项目旨在培养学员的塑料模具设计能力,通过系统的理论学习和实践技能训练,使学员能够掌握塑料模具设计的基础知识和技能,并能独立完成塑料模具的设计工作。
2.训练目标(1)掌握塑料模具设计的理论基础,包括模具结构、材料选择、加工工艺等方面的知识。
(2)熟练运用CAD、CAM等设计软件,能够使用该软件进行模具设计和图纸展开。
(3)了解塑料塑性变形规律,掌握模具壁厚设计、型腔表面处理、注塑机选择等技术。
(4)掌握模具加工、调试、大批量生产等工艺流程,能够独立完成模具设计、加工和调试等工作。
3.训练内容(1)理论学习:介绍塑料模具的种类、结构及其设计要求;介绍CAD、CAM 软件的使用方法及设计技巧;塑料塑性变形规律、模具壁厚设计、型腔表面处理、注塑机选择等技术。
(2)实践技能训练:通过实践操作,学员将通过CAD软件进行模具设计和图纸展开,并进行模具精铣、电脉冲加工等加工工艺操作,学习模具调试和生产的全过程。
4.训练方法(1)课堂讲述:采用直观的案例和实例,让学员感受到塑料模具设计的复杂性和重要性,激发学员的学习热情。
(2)实践操作:采取“理论与实践相结合”的方法,通过具体的实践操作,帮助学员更加深刻地理解和掌握塑料模具设计的基本原理和技能。
(3)讲解示范:通过对实际案例的讲解和操作示范,让学员进一步理解塑料模具设计的过程和方法,掌握塑料模具制造的全过程。
(4)实践演练:让学员进行模拟生产操作,通过模拟操作培训,让学员更加深入地了解塑料模具的加工制造过程,提高其实践技能水平。
5.训练成果(1)学员将掌握塑料模具设计的基础理论和技能,能够独立完成塑料模具的设计工作。
(2)学员将掌握CAD、CAM等设计软件的使用方法,能够进行模具设计和图纸展开。
注塑模具设计说明书

数码相机盖模具设计说明书班级:10材料专业:材料成型及控制工程姓名:刘树飞学号:100118019指导老师:引言 (2)一.产品工艺性分析 (3)1.1设计产品概述 (3)1.2产品工艺性分析 (3)二、注塑机的选择 (3)1、塑件的质量、体积计算 (4)2、浇注系统凝料体积的初步估算 (4)3、注射容量与锁模力校核 (4)(1)注射容量校核 (4)(2)锁模力的校核 (4)4.利用UG软件,设置工件尺寸。
(4)三、分型设计 (5)四、标准模架的选用 (6)(1)先定系列。
(6)(2)看型芯固定方式是否需要加支撑板。
(6)(3)确定模板尺寸。
(6)(4)模架厚度 (6)五、模具滑块设计 (6)(1)抽芯距离和抽芯力的计算 (6)(2)斜导柱设计 (7)①斜导柱倾斜角的确定 (7)②斜导柱的直径计算 (7)③斜导柱长度的计算 (7)④滑块其他零部件设计 (7)六、导向与顶出机构设计 (8)(1)顶出机构设计 (8)①脱模力计算 (8)②推出零件尺寸计算 (8)③创建顶管 (8)④创建拉料杆 (8)(2)导向机构的设计 (8)①导柱的选取 (8)②复位杆的选取 (9)七、浇注系统设计 (9)1.浇注系统整体方案确定 (9)2.主流道设计 (9)3、分流道、浇口和冷料穴设计 (9)八、冷却系统设计 (10)1、冷却水道的尺寸计算 (11)(1)计算单位重量的塑料熔体在凝固时所放出的热量Q1(kJ/kg) (11)(2)求冷却水的体积流量qv(m³/min) (11)(3)查表使冷却水处于紊流状态,取d (11)九、画模具装配图 (12)引言虽然受到全球金融危机影响,但是我国模具整体实力还是得到进一步加强。
近两年来中国的模具制造技术水平又有了新的提高。
从模具产品进出口的地域来看,华东地区的江苏、浙江、上海、山东均位列中国进口和出口模具的十大省市之中。
长江三角地区在模具制造整体水平的数量和质量上均已在国内处于行业重要位置。
蜜饯盒注塑模具设计任务书
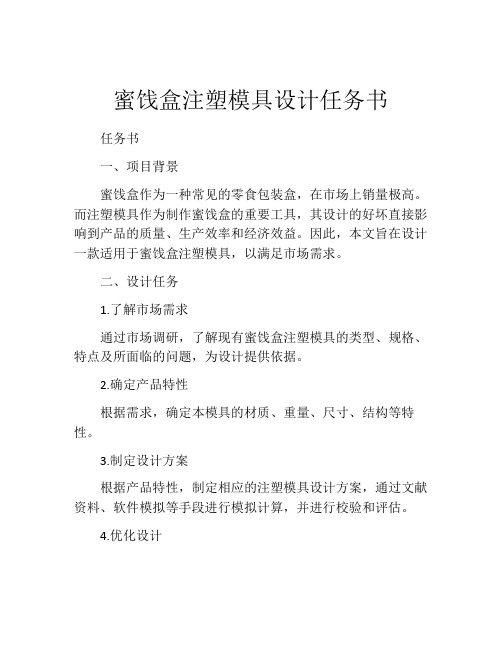
蜜饯盒注塑模具设计任务书任务书一、项目背景蜜饯盒作为一种常见的零食包装盒,在市场上销量极高。
而注塑模具作为制作蜜饯盒的重要工具,其设计的好坏直接影响到产品的质量、生产效率和经济效益。
因此,本文旨在设计一款适用于蜜饯盒注塑模具,以满足市场需求。
二、设计任务1.了解市场需求通过市场调研,了解现有蜜饯盒注塑模具的类型、规格、特点及所面临的问题,为设计提供依据。
2.确定产品特性根据需求,确定本模具的材质、重量、尺寸、结构等特性。
3.制定设计方案根据产品特性,制定相应的注塑模具设计方案,通过文献资料、软件模拟等手段进行模拟计算,并进行校验和评估。
4.优化设计在初步设计完成后,对其进行审查和评估,通过不断的修改和调整,优化设计,使设计更加符合实际生产需求。
5.确定模具的生产工艺在设计优化完成后,确定模具的生产工艺,并制定生产计划,确保模具的质量和交货时间。
6.模具测试将模具进行实验室测试,测试模具的使用寿命、生产效率等性能指标。
7.模具应用对于测试合格的模具,进行进一步的应用,进行生产,实现效益最大化。
三、设计要求1.设计的注塑模具必须符合相关的国家标准和技术要求,确保生产质量。
2.设计风格简洁大方,能够满足用户需求。
3.具备良好的耐热、耐磨、耐腐蚀、防腐蚀等性能,保证模具的使用寿命和生产效率。
4.必须采用先进的CAD和CAM软件,模拟计算和评估,保证模具的设计可靠性和合理性。
四、设计预算1. 设计费用:30000元人民币2. 设计材料费:2000元人民币3. 设计人工费:8000元人民币4. 其他杂费:2000元人民币五、设计进度1. 市场调研:7天2. 确定产品特性:5天3. 初步设计方案:20天4. 优化设计方案:15天5. 生产工艺确定和生产计划制定:7天6. 模具测试:5天7. 模具应用:30天六、责任人本设计项目的责任人为公司注塑模具设计部主管。
本文立足于蜜饯盒注塑模具的设计需求,针对设计任务和设计要求制定了详尽的计划,并明确责任人,以期能够满足市场需求,提升生产效率和经济效益。
(完整)注塑模具课程设计说明书范文+模版
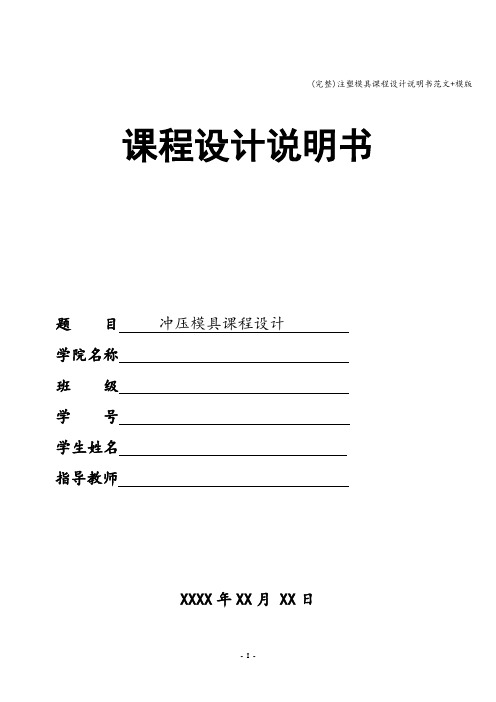
(完整)注塑模具课程设计说明书范文+模版课程设计说明书题目冲压模具课程设计学院名称班级学号学生姓名指导教师XXXX年XX月 XX日(完整)注塑模具课程设计说明书范文+模版摘要本文主要是关于酒瓶塞子的注塑工艺的分析及模具设计。
首先,对注塑工件进行了结构和工艺分析,确定了最佳成形方案;对整个塑件成形过程进行了模拟分析,预测了成形过程中可能出现的问题.根据分析结果,利用CAD等软件,完成了酒瓶塞子注塑模设计。
关键词;酒瓶塞子,CAD,注塑模(完整)注塑模具课程设计说明书范文+模版目录第一章概论 (1)1。
1 课题背景及意义 (1)1.2我国塑料模具现状及发展方向 (1)1.2。
1我国塑料模具的发展现状 (1)1。
2。
2我国塑料模具的发展方向 (3)第二章塑件工艺分析 (4)2.1塑件的工艺分析 (4)2。
1。
1分型面的选择 (5)2。
2塑件的材料分析 (5)2。
3塑件的表面分析 (1)2.4塑件的尺寸精度 (1)2。
5塑件的壁厚分析 (1)2.6塑件的脱模角度分析 (1)2.7塑件的圆角分析 (1)2。
8塑件的孔尺寸设计 (1)2。
9塑件的注塑工艺参数设置 (1)第三章模具设计 (3)3.1整体设计 (3)3.1.1模架结构选择 (3)3.1。
2注塑机的选择 (3)3.2系统设计 (4)3.2.1 浇注系统设计 (4)3。
2.2排气系统设计 (20)3。
2.3模温系统设计 (20)3。
3合模导向机构的设计 (21)3.3.1导套 (21)3。
3.2导柱 (22)3。
4侧向分型抽芯机构 ......................... 错误!未定义书签。
3.4.1抽芯距S .............................. 错误!未定义书签。
3.4。
2侧抽芯力FC .......................... 错误!未定义书签。
3.4.3斜导柱设计........................... 错误!未定义书签。
注塑模具设计说明书

绪论模具作为重要的生产工艺装备,在现代工业的规模生产中日益发挥着重在作用;通过模具进行产品生产具有优质、高效、节能、节材、成本低等显著特点,在汽车、机械、电子、轻工、家电、通信、军事和航空航天等领域获得了广泛应用,对塑料模具的需求越来越大,对产品质量要求越来越高,用不可代替;塑料模具是当今工业生产中利用特定的形状,通过一定的方式来成型塑料制品的工艺装配或工具,它属于型腔模的范畴;通常情况下,塑件质量的优劣及生产效率的高低,其模具的因素约占80%,然而模具的质量好坏又直接与模具的设计与制造有很大的关系随着国民经济的领域的各个部门对塑件的品种和产量需求愈来愈大,产品更新换代周期也和质量提出了更高的要求,这就促使塑料模具设计和制造技术不断向前发展,从而也推动了塑料工业以及机械加工工业的告诉发展,可以说,模具技术,特别是设计与制造大型,精密,长寿命的模具技术便成为衡量一个国家机械制造水平的重要标志;模具在世界上占有的比列大,我作为一个学模具专业的学生,应在学完所学的知识之后来很好的进行模具设计;我们进行设计之前,不许具备机械制图,公差与技术测量,机械原理及零件,模具材料及热处理,模具制造技术,塑料制品成型工艺及模具设计等方面必要的基础知识和专业知识,并且通过教学和生产实习,初步了解塑料制品的生产过程,熟悉多种塑料模具的典型结构;近几年来,我国模具工业的技术水平已取得了很大的进步,但总体上与工业发达的国家相比仍有较大的差距;例如,精密加工设备还很少,许多先进的技术如CAD/CAE/CAM技术的普及率还不高,特别是大型、精密、复杂和长寿命模具远远不能满足国民经济各行业的发展需要;纵观发达国家对模具工业的认识与重视,我们感受到制造理念陈旧则是我国模具工业发展滞后的直接原因;模具技术水平的高低,决定着产品的质量、效益和新产品开发能力,它已成为衡量一个国家制造业水平高低的重要标志;目前,我国模具工业的当务之急是加快技术进步,调整产品结构,增加高档模具的比重,质中求效益,提高模具的国产化程度,减少对进口模具的依赖;现代模具技术的发展,在很大程度上依赖于模具标准化、优质模具材料的研究、先进的设计与制造技术、专用的机床设备,更重要的是生产技术的管理等;21世纪模具行业的基本特征是高度集成化、智能化、柔性化和网络化;追求的目标是提高产品的质量及生产效率,缩短设计及制造周期,降低生产成本,最大限度地提高模具行业的应变能力,满足用户需要;在科技发展中,人是第一因素,因此我们要特别注重人才的培养,实现产、学、研相结合,培养更多的模具人才,搞好技术创新,提高模具设计制造水平;在制造中积极采用多媒体与虚拟现实技术,逐步走向网络化、智能化环境,实现模具企业的敏捷制造、动态联盟与系统集成;模具类型塑料模具分类的方法很多,按照塑料制作的成型方法不同可分为以下几类:注射模,压缩模,挤出模,压注模;本次设计主要是注射模,又叫注塑模,注射成型是根据金属压铸成型原理发展起来的,首先将粒状或粉末状的塑料原料加入到注射机的料筒中,经过加热熔融成粘流态,然后在柱塞或螺杆的推动下,以一定的流速通过料筒前端的喷嘴和模具的浇注系统,注射入闭合的模具型腔中,经过一定的时间后,模具在模内硬化成型,近几年来,热固性塑料注射成型的应用也在逐渐增加;塑料制件主要是靠成型模具获得的,而它的质量是靠模具的正确结构和模具成型零件的正确形状,精确尺寸及较低的表面粗糙度来保证的;由于塑料成型工艺的飞速发展,模具的结构也日益趋于多功能和复杂化,这对模具的设计工作提出了更高的要求;虽然模具制作的质量与许多因素有关,但合格的塑料制作首先取决于模具的设计与制造的质量,其次取决与合理的成型工艺;塑料成型加工技术发展很快,塑料模具的各种结构也在不断的创新,我们在学习成型的同时,还应注意了解塑料模具的新技术、新工艺和新材料的发展动态,学习和掌握新知识,为振兴我国的塑料成型加工技术做出贡献;塑料成型工艺分析1、制品的分析制品的设计要求本次设计制品的用途是线盒盖,该制品结构形状较简单,形状尺寸小,壁厚均匀,基本对称,精度要求中等;制品的生产批量本制品为大批量生产,为了缩短周期,提高生产率,制品使用一模四腔和全自动化生产,浇口形式可采用侧浇口;该塑件很小,壁不厚,因此只采用一个点进料,都可以满足充满型腔,利用模具的顶出机构,将制品推出模腔,再利用拉料杆和二次脱模机构使制品流道凝料脱落;为了提高生产率,制品在模具中直接成型;制品成型设计该制品使用二次分型机构,采用点浇口形式,虽然其他的浇口形式还有直接浇口、侧浇口、扇形浇口、薄片式浇口、环行浇口、轮辐浇口、爪形浇口、潜伏浇口、护耳浇口等,但他们都不容易在开模时实现自动切断,而点浇口就具有这个优点,而且其留于塑件的疤痕较小,不影响塑件外观;2、注射成型工艺的设计塑料制品分析本制品采用ABS为原料苯乙烯—丁二烯—丙烯氰共聚物;ABS主要技术指标:表1-1 热物理性能表1-2 力学性能表1-3 电气性能1无定性料,流动性中等,比聚苯乙烯、AS差,但比聚氯乙烯好,溢边值为0.04 mm左右;2吸湿性强,必须充分干燥,表面要求光泽的塑料须经长时间的预热干燥;3成型时宜取高料温,但料温过高易分解分解温度≥250℃,对精度较高的塑料,模温宜取50~60℃,对光泽要求较高的耐热塑料模温宜取注射压力高于聚苯乙烯;用柱塞式注射机成型时,料温为60~80℃,180~200℃,注射压力为1000~1400MPa,用螺杆式注射机成型时,料温为160~220℃,注射压力为700~1000×10MPa;4 ABS的其他成型工艺参数注射机类型:螺杆式制品收缩率:~%预热温度:80~85℃时间:2~3 h料筒温度:后段 150~170℃中段 165~180℃前段180~200℃喷嘴温度:170~180℃模具温度:50~80℃注射压力:60~100 MPa成型时间:注射时间20~90 s 保压时间0~5 s冷却时间20~120 s 总周期50~220 s螺杆转速:30 r/min适用注射机类型:螺杆、柱塞均可后处理方法:红外线灯、鼓风烘箱温度70℃时间2~4 h制品成型方法及工艺流程本制品采用注射成型,工艺流程包括模前准备,模塑成型和后处理及二次加工工艺流程步骤如下:1预热ABS吸湿性强,必须充分干燥,表面要求光泽的塑料须经长时间的预热干燥;2注射注射过程包括加料、塑化、注射冷却和脱模几个步骤;加料由于注射成型是一个间歇过程,因而须定量加料,以保证操作稳定,塑料塑化均匀,最终获得良好的塑件;加料过多;受热的时间过长等容易引起物料的热降解,同时注射及功率损耗增多;加料过少,料筒内缺少传压介质,型腔中塑料融化压力降低,难于补料,容易引起塑件出现收缩、凹陷、空洞等缺陷;塑化加入的塑料在料筒中进行加热,由固体颗粒转化成粘流态,并且受到良好的剪切力作用;通过料筒对物料加热,使聚合物分子松弛,出现由固体向液体转变;一定的温度使塑料得到变形、熔融和塑化的必要条件,螺杆的剪切作用能在塑料中产生更多的摩擦热,促进了塑料的塑化,因而螺杆式注射机对塑料的温度尽量均匀一致,还有使热分解物的含量达到最小值,并且能提供上述质量的足够的熔融塑料以保证产生连续并顺利的进行,这些要求与塑料的特性、工艺条件的控制及注射机的塑化装置的结构等密切相关;注射不论何种形式的注射机,注射的过程可分为充模,保压倒流,浇口冻结后的冷却和脱模等几个阶段;塑件的后处理注射成型的塑件经脱模或机械加工之后,常需要进行适当的后处理以消除存在的内应力,改善塑件的性能和提高尺寸稳定性;其主要方法是退火和调湿处理;退火处理是将注射塑件在定温的加热液体介质或热烘箱中静置一段时间,塑料制件的氧化,加快吸湿平衡速度的一种处理方法,其目的是使制作的颜色、性能以及尺寸得到稳定;本次设计采用退火后处理;工艺流程图解:成型工艺条件注射成型的核心问题,就是采用一切措施得到塑化良好的塑料;熔体,并把它注射到型腔中去,在控制条件下冷却定型,使塑件;达到所要求的质量,影响注射成型工艺的重要参数是塑化流动和;冷却的温度、压力以及影响的各个作用时间;1注射成型过程需要控制的温度有料筒温度,喷嘴温度和模具温度等;前两个温度主要影响塑件的塑化和流动,而后一个温度主要是影响塑件的流动和冷却,料筒温度的选择与各种塑料的特性有关;每种塑料都具有不同的粘流态温度,为了保证塑件溶体的正常流动不使物料发生质分解,料筒最合适的温度范围应在粘流态温度和热分解温度之间;柱塞式和螺杆式柱塞注射机由于其塑化过程不同,因而选择料筒也不同,通常后者选择的温度低一点,料筒温度在70~93℃之间,喷嘴温度稍低于料筒温度,在65~90℃之间,模温在要求塑件光泽时控制在60~80℃之间;2压力包括塑化压力和注射压力两种,他们直接影响塑料的塑化和塑料质量;塑化压力是指背压,是指采用螺杆式注射机时,螺杆头部熔体在螺杆转动后退时所受到的压力,塑化压力在保证塑件质量的前提下越低越好,其具体数值时随所用塑料的品种而异的,但通常很少超过20MP,注射压力是指柱塞式螺杆头部对塑件熔体所施加的压力;在注射机上常用表压指示注射压力的大小,一般在40~130MP之间;其作用式克服塑料熔体从料筒流向型腔的流动阻力,给予熔体一定的充型速率以及对熔体进行压实等;3完成一次注射成型过程所需要的时间称成型周期,成型周期直接影响到劳动生产率和注射机使用率,因此在生产中,在保证质量的前提下,尽量缩短成型周期中各个阶段的有关时间,一般生产中,充模时间为3~5S,保压时间为20~25S,冷冲压时间一般在30~120S;3 注射机的选用注射机的选用包括两方面的内容:一是要确定注射机的型号,使塑料、塑件、注射模、注射工艺等所要求的注射机的规格参数点在所选注射机的规格参数可调范围之内,即要满足所需的参数在额定的范围之内;二是调整注射机的技术参数至所需的参数点;注射机的两种类型的优缺点采用卧式注射机的优点是注射部分和锁模部分在同一水平线上,工作位置低,操作方便,稳定性好,顶出后塑件可以自动脱落,是应用广泛的注射机,适用于大、中、小个各型注射机,但唯一的缺点是占地面积大;采用立式注射机的优点是占地面积小,缺点是操作位置高,对于注射量大的注射机,势必使注射机高度增加,操作台升高,操作不方便,注射机的工作稳定性也减小;因此,立式注射机多限于小型注射机;选用注射机按流量选择注塑机,选择SZ—40/32立式注射机,表为该注射机的技术参数;模具结构的设计1、塑件成型位置及分型面的选择分型面即打开模具取出塑件或取出浇注系统凝料的面,分型面的位置影响着成型零部件的结构形状,型腔的排气情况也与分型面的开设密切相关;分型面的选择应注意以下几点:1不影响塑件外观,尤其是对外观有明确要求的制品;2有利于保证塑件的精度要求;3有利于模具加工,特别是型腔的加工;4有利于浇注系统、排气系统、冷却系统的设计;5便于制件的脱模,尽量使塑件开模时留在动模一边.6分型面应有利于侧向抽心;7分型面应取塑件尺寸最大处;8拔模斜度小或塑件较高时,为了便于脱模,可将分型面选在塑件的中间部位;2、型腔的排列形式及流道布局的确定型腔数目确定方法常见的有四种:1根据经济性确定型腔树木2根据注射机的额定锁模力确定型腔树木3根据注射机的最大注射量确定型腔数目4根据制品精度确定型腔数目对于高精度制品,由于多型腔模具难以使各型腔的成型条件均匀一致;故通常推荐型腔数目不超过6个,本设计为四型腔注射模;型腔数量的确定该制品精度要求不高,属于小零件,又要大量的生产,为了考虑生产效率和模具制造费用低点,给公司带来更多的效益,因此本设计初步拟定于一模八腔模具的形式生产;根据注射机的最大注射量确定型腔数目,即只要满足下式,就符合要求 210.8G W n W -≤ 式中:n —型腔数目G —注射机的最大注射量,g ;W 1—单个制品的质量,g ;W 2—浇注系统的质量,g ;210.8G W W -0.8600.910.64 1.421.4228.36⨯⨯-⨯⨯== 28.36>4,因此一模四腔符合要求;型腔的排列在设计时要注意以下几点1尽可能采用平衡式排列确保制品的质量的均一和稳定2型腔布置与浇口开设部位应力求对称,以便防止模具承受偏载而产生溢料现象,尽量使型腔排的紧凑,以便减少模具的外形尺寸;该塑件侧面有一个梯形槽,需要有侧向抽心,为了便于抽心及节省流道凝料,因此采用下列的型腔排列及流道布局;型腔的排列及流道布局3、 浇注系统的设计浇注系统通常由主流道 分流道 浇口料穴等组成;浇注系统是塑料容体由注射机的喷嘴向模具型腔的流动通道;因此它应该保证容体迅速顺利有序地充满型腔各处,获得外观清晰,内在优良的塑料件;对于浇注系统设计的具体要求有:①重点考虑型腔布局;②热量及压力损失要小,为此浇注系统流程应尽可能短,截面尺寸应尽可能大,弯折尽量少,表面粗糙度要低;③均衡进料,即分流道尽可能采用平衡式布置;④塑料耗量要少,满足各型腔充满的前提下,浇注系统容积尽量小,以减少塑料耗.⑤消除冷料,浇注系统应能收集温度较低的“冷料”;⑥排气良好;⑦防止塑件出现缺陷,避免熔体出现充填不足或塑件出现气孔、缩孔、残余应力;⑧保证塑件外观质量;⑨较高的生产效率;⑩塑料熔体流动特性;4、主流道的设计主流道是指连接注射机喷嘴与风流道或型腔的进料通道;负责将塑料溶体从喷嘴引入模具,其形状,大小直接影响塑料的流速及填充时间;主流道是塑料容体进入模具型腔时经过的部分,它将注射机的喷嘴注出的塑料容体导入分流道或型腔;其形状为圆锥形,便于容体顺利地向前流动,开模时主流道凝料又能顺利拉出来;主流道的尺寸直接影响到塑料容体的流动速度和充填时间;由于主流道要与高温塑料和喷嘴反复接触和碰撞,通常不直接开在定模板上,而是将它单独设计成主流道衬套镶入定模板内;主流道的尺寸①半锥角一般在1°~3°内选取,主流道带锥度是为了在模具打开时使主流道凝料容易脱离定模;本设计选取锥度为3°;②主流道径向尺寸的小端与喷嘴连接的一端应大于喷嘴口孔径~㎜;当主流道与喷嘴同轴度有偏差时,可以防止主流道凝料不易从定模一侧拉下来;D=d+~1㎜式中:d—注射机喷嘴口直径D—浇口套进料口直径③凹球面半径R应比喷嘴球径1R大1~2㎜,可以;保证注射过2程中喷嘴与模具紧密接触,防止两球面之间产生间隙而使容体充入这间隙中,妨碍主流道凝料顺利从定模上拉出;④主流道内壁的表面粗糙度R在以下,主流道的长度L一般根据a模板的厚度而定,为了减少压力损失和物料损耗;应尽可能减少主流道的长度,一般控制在60mm以内;主流道出口处的圆角半径较小,一D般取r=18⑤主流道上开设浇口套;将主流道开设在一个专用零件主流道衬套上而不是直接加工在定模板上的方法较好,因为主流道的表面粗糙度和硬度要求一般都比定模板高,可以选用较好的钢材;损坏后也容易更换,一般选用T8或T10制作,淬火硬度为50~55HRC,浇口套的形式如下图a b c e f g浇口套的形式(a)是浇口套和定位圈做成一体,仅适用于小型模具;(b)采用螺钉将定位圈和定模座板连接,防止浇口套受容体的反压力而脱出,是常用结构;(c)用定位圈的凸肩将其压在注射机的固定板下,当浇口套端面尺寸较小时,仅靠注射机喷嘴的推力就能将浇口套压紧,也是常用结构;(d)通过浇口套上挖出凹坑来减少主流道的长度;(e)直接在定模座板上开主流道,适用用于小型模具的小批生产,上述几种情况适用与注射机为球面的情况;(f)用于喷嘴头为平面的结构,优点是接触面积大,密封好容体不外溢,缺点是对注射机的精度要求很高;本设计采用b图的结构5、分流道的设计分流道是指主流道与模具型腔浇口之间的一段流道,在多型腔或单型腔多浇口塑件尺寸大时应设置分流道,分流道是指主流道末端与浇口之间这一段塑料熔体的流动通道;它是浇注系统中熔融状态的塑料由主流道流入型腔前,通过截面积的变化及流向变换以获得平稳流态的过渡段;因此分流道设计应满足良好的压力传递和保持理想的充填状态,并在流动过程中压力损失尽可能小,能将塑料熔体均衡地分配到各个型腔;分流道的布置常用塑料的分流道直径列于下表,由表可见,对于流动性极好的塑料,当分流道很短时,其直径可小到2mm左右;对于流动性差的塑料,分流道直径可以大到13mm;大多塑料所用分流道的直径为6mm~10mm;在多型腔模具中分流道的布置中有平衡式和非平衡式;平衡式布置是指分流道到各型腔浇口的长度、断面形状、尺寸都相等的布置形式;它要求各对应部分的尺寸相等,这种布置可实现均衡送料和同时充满型腔的目的,使成型的塑件力学性能基本一致;但是这种布置使分流道较长;非平衡式布置是指分流道到各个型腔浇口的长度相等的布置;这种布置使塑料进入各个型腔有先后顺序,因此不利于均衡送料,但对型腔数量多的模具,为不使流道过长,也常采用;为了达到同时充满型腔的目的,各个浇口的断面尺寸要制作得不相同,在试模的时候要多修改才能实现;a b分流道的平衡布置示意图分流道的非平衡布置示意图本设计中为了成型的塑件力学性能基本一致,采用图a结构,分流道的平衡布置;6、浇口的设计浇口亦称进料口,是连接分流道与型腔的通道,除直接浇口外,它是浇注系统中截面最小的部分,但却是浇注系统的关键部分,浇口的位置、形状及尺寸对塑件性能和质量的影响很大;浇口的主要作用:➢型腔充满后,熔体在浇口处首先凝结,防止其倒流;➢易于切除浇口尾料;➢对于多型腔模具,用以控制熔接痕的位置;当塑料熔体通过浇口时,剪切速率增高,同时熔体的内摩擦加剧,使料流的温度升高,黏度降低,提高流动性能,有利于充型,但是浇口尺寸过小会使压力增大,凝料加快,补缩困难,甚至形成喷射现象, 影响塑件质量;浇口类型的选择浇口是典型的矩形截面浇口,有以下优点:①浇口的位置一般都在分型面上,从塑件的外侧进料;②塑件容易形成熔接纹、缩孔,凹陷等缺陷,注射压力损失较大,对壳体件排气不良;③截面形状简单,加工方便;④位置选择灵活,去除浇口方便,痕迹小;⑤广泛用于两板式多型腔模具以及断面尺寸较小的塑件;本设计采用侧浇口的结构形式;浇口位置的选择模具设计时,浇口的位置及尺寸要求比较严格,初步试模后还需进一步修改浇口尺寸,无论采用何种浇口,其开设位置对塑件成型性能及质量影响很大,因此合理选择浇口的开设位置是提高质量的重要环节,同时浇口位置的不同还影响模具结构;总之要使塑件具有良好的性能与外表,一定要认真考虑浇口位置的选择,通常要考虑以下几项原则:①避免制件上产生喷射等缺陷②浇口应开设在塑件截面最厚处;③有利于塑件熔体流动;④有利于型腔排气;⑤考虑塑件使用时的载荷状况;⑥减少或避免塑件的熔接痕;⑦考虑分子取向对塑件性能的影响;⑧考虑浇口位置和数目对塑件成型尺寸的影响;⑨防止将型芯或嵌件挤歪变形;下图为本设计塑所选的浇口位置浇口位置浇注系统的平衡对于中小型塑件的注射模具己广泛使用一模多腔的形式,设计应尽量保证所有的型腔同时得到均一的充填和成型;一般在塑件形状及模具结构允许的情况下,应将从主流道到各个型腔的分流道设计成长度相等、形状及截面尺寸相同型腔布局为平衡式的形式,否则就需要通过调节浇口尺寸使各浇口的流量及成型工艺条件达到一致,这就是浇注系统的平衡;显然,我们设计的模具是平衡式的,即从主流道到各个型腔的分流道的长度相等,形状及截面尺寸都相同;7、冷料穴的设计冷料穴的作用是储存因两次注射间隔而产生的冷料头以及塥体流动的前锋冷料,以防止溶体冷料进入型腔;冷料穴一般设在主流道的末端,冷料穴底部常作成曲折的钩行或下陷的凹槽,使冷料穴兼有分模时将主流道衬套中拉出,并留在动模一侧的作用;在完成一次注射循环的间隔,考虑到注射机喷嘴和主流道入口这一小段熔体因辐射散热而低于所要求的塑料熔体的温度,从喷嘴端部到注射机料筒以内约10-25mm的深度有个温度逐渐升高的区域,这时才达到正常的塑。
注塑模具设计说明书

注塑模具设计说明书注塑模具设计说明书1.引言本文档旨在为注塑模具的设计提供详细指导和说明。
注塑模具是在注塑成型过程中必备的工具,准确的设计和制造对于生产高质量的注塑制品至关重要。
2.模具设计概述2.1 模具类型及用途2.2 模具材料选择2.3 模具尺寸和形状设定2.4 模具结构设计2.5 模具配件选择与设计3.模具主要零部件设计3.1 模具基板设计3.2 模具腔体与芯腔设计3.3 模具导向系统设计3.4 模具冷却系统设计3.5 模具强度校核3.6 模具表面处理4.注塑模具设计考虑因素4.1 塑料材料特性4.2 注塑工艺要求4.3 产品设计要求4.4 模具制造成本和周期5.模具设计流程5.1 需求分析与规划5.2 初始设计与草图5.3 详细设计与模拟分析5.4 模具制造与加工5.5 模具调试与试模5.6 模具验收和交付6.模具设计的注意事项6.1 常见设计错误与避免方法6.2 模具装配和拆卸注意事项6.3 模具维护与保养7.附件本文档涉及以下附件:- 附件1:注塑模具设计草图- 附件2:注塑模具3D模型文件- 附件3:模具设计分析报告8.法律名词及注释本文所涉及的法律名词及其相应注释如下:- 法律名词1:注塑成型工艺注释:指利用注塑设备将塑料加热并溶化,然后将熔融塑料注入模具腔中,并通过冷却固化成型的工艺。
- 法律名词2:模具基板注释:指注塑模具的基础组件,用于固定和支撑模具的其他部件,具有足够的强度和稳定性。
- 法律名词3:模具腔体与芯腔注释:模具腔体为模具中用于成型制品外形的部分,芯腔为模具中用于成型制品内部结构的部分。
9.结束语本文档详细介绍了注塑模具设计的各个方面。
通过遵循本文档中的指导和说明,设计师可以制定出高质量的注塑模具并实现优秀的注塑成型工艺。
注塑模课程设计说明书

二、设计题目设计主要内容一、塑件成型工艺分析1、塑料性能分析本塑件材料为聚丙烯,代号为PP。
聚丙烯的主要特点是密度小,约为0.9g/cm3。
它的力学性能如屈服强度、抗张强度、抗压强度及硬度等,均优于低压聚乙烯,并有很突出的刚性,耐热性较好。
可在100℃以上使用。
若不受外力,则温度升到150℃也不变形。
基本上不吸水,并且有较好的化学稳定性,除对浓硅酸、浓硝酸外,几乎都很稳定。
高频电性能优良,且不受温度影响,成形容易。
缺点是耐磨性不够高,成形收缩率较大,低温呈脆性。
热变形温度亦较低。
可做各种机械零件,如法兰、齿轮、接头、泵叶轮、汽车零件,化工管道及容器设备。
并可用于制造衬里,表面涂层、录音带,医疗仪器及手术仪器等。
2、成型工艺分析PP的成型条件如下:注射成型机类型螺杆式收缩率 1.0~2.0%(塑件壁厚t=3mm)预热温度80~100℃预热时间1~2h模具温度40~80℃注射压力80~120MPa料筒前段温度200~220℃料筒中段温度180~200℃料筒后段温度160~180℃(注:以上数据来自《塑料模具设计手册》)3、塑件结构分析塑件结构下图所示,此塑件的尺寸无精度要求,为自由尺寸,均按MT7级精度取公差值。
表面粗糙度没有特别要求。
此塑件外型为方形壳体类零件,腔体深120mm,壁厚均匀,除两凸缘外其余均为3mm,总体尺寸不大不小,塑件成型性能良好。
二、塑件分型面位置的分析分型面应选择在塑件截面最大处,尽量取在料流末端,利于排气,保证塑件表面质量。
该塑件的最大截面在尺寸L处,如图1所示。
所以分型面设置在尺寸L 处符合模具的开模要求,避免了在塑件表面留下分型线的痕迹。
另外塑件对型芯产生的包紧力足以保证塑件留在动模一侧,使得产品的推出并无太大阻碍。
考虑塑件收缩率的问题,可设置脱模斜度和表面粗糙度解决。
三、塑件型腔数量及排列方式的确定根据设计要求,模具结构为单型腔模具,型腔设置在模具中心,所以不存在排列问题。
注塑模具设计说明书

塑料模课程设计水杯盖注塑模具设计学院机电与建筑工程学院专业材料成型及控制工程姓名李瑞朝学号指导老师杨俊杰余五新目录1前言 (1)2设计任务书 (1)3塑件的结构工艺性分析 (1)4分型面及浇注系统的设计.............................5模具设计方案论证 (1)6主要零部件的设计计算 (1)7成型设备的校核计算 (1)8设计小结 (1)9参考文献 (1)1前言水杯盖在我们生活中随处可见,几乎每家每户都会用到。
市场上也有各种各样的杯盖,有时候一个灵巧鲜艳的造型便能吸引消费者的眼球,为生产厂家创造利润。
所以一个貌似简单的盖子也蕴含着无尽的商机,引人深思。
本次设计的顶盖结构非常简单,主要展现出一个最普通的生活用品的注塑成型过程,希望能有助于人们对身边事物的了解。
2设计任务书(1)塑料制品名称:水杯盖。
(2)成型方法:注塑成型。
(3)塑料原料:ABS。
(4)收缩率:0.4%~0.7%。
(5)生产批量:10万件。
3塑件的结构工艺性分析3.1塑件的几何形状分析本塑件为圆形的顶盖,尺寸中等,结构简单。
考虑到该制件精度要求较低,结合其材料性能,故选一般精度等级为:MT5。
3.2塑件原材料的成型特性分析ABS是目前产量最大,应用最广的工程塑料。
ABS是不透明非结晶型聚合物,无毒,无味,密度为1.02~1.05g/cm 3。
ABS具有突出的力学性能,坚韧,坚固;易于成型和机械加工,成型塑料油较好的光泽,经过调色可配成任何颜色。
ABS可采取注射,挤塑,吹塑,真空成型机表面涂饰等多种成型加工方法。
ABS成型性能如下:(1)易吸水,成型加工前需进行干燥处理,表面光泽要求高的塑件需长时间预热干燥。
(2)比热容低,塑化效率高,凝固也快,故成型周期短。
(3)顶出力过大或机械加工时塑件表面会留下白色痕迹,脱模斜度宜取2°以上。
(4)易产生熔接痕,模具设计是应注意尽量减少浇注系统对料流的阻力。
(5)宜采用高料温,高模温,高注射压力成型。
塑料夹子注塑模具方案设计书(2)

专科毕业论文题目塑料夹子注塑模具设计学院工业制造学院专业机械设计与制造学生姓名陈润超学号201020113220 年级2010级指导教师冯威职称讲师2013年5月28日论文声明本人声明所呈交的毕业论文是本人在导师指导下进行的研究工作及取得的研究成果。
据我所知,除了文中特别加以标注和致谢的地方外,论文中不包含其他人已经发表或撰写过的研究成果,也不包含获得成都学院或其它教育机构的学位或证书而使用过的材料。
与我一同工作的同志对本研究所做的任何贡献均己在论文中作了明确的说明并表示谢意。
学生签名:年月日关于论文使用授权的说明本毕业论文作者完全了解成都大学有关保留、使用学位论文的规定,有权保留并向国家有关部门或机构送交论文的复印件和磁盘,允许论文被查阅和借阅。
本人授权成都学院可以将毕业论文的全部或部分内容编入有关数据库进行检索,可以采用影印、缩印或扫描等复制手段保存、汇编学位论文。
(保密的学位论文在解密后应遵守此规定)学生签名:年月日塑料夹子注塑模具设计专业: 2010级机械设计与制造学号:201020113220学生:陈润超指导老师:冯威摘要:进入21世纪以来全球经济迅猛发展,我国的经济也得到长足进步。
随着经济的发展人们对物品的要求也相对提高,使得大量生产加工方法出现。
模具现在已经成为工业发展的基础,而塑料模占模具总量的比例达到35%~40%,塑料成型模具的应用在各类模具的应用中占有领先地位。
随着我国经济的发展,国家经济建设持续稳定的发展,塑料制件的生产越来越广泛,塑料成型工艺在基础工业中的地位日益重要。
注射模具就是塑料模具中的一种,因此注射模具也得到了很大发展。
本设计关于塑料夹子的注射模具设计,通过注射机注塑成型零件。
运用CAD/SolidWorks等软件进行绘制,对注塑机的选用,塑件的选材,浇注系统的设计,分型面及型腔数量及布局形式的设计,导向、脱模及冷却系统、排气系统的设计、推出方式、成型零件的结构形式等,进行了设计计算。
塑料模具课程设计说明书_2

塑料成型工艺及模具设计课程设计说明书题目: 塑料模具设计专业: 模具设计制造及其自动化班级: 机设07级**: ***学号: ****************: ***时间: 2011年1月5日目录第一部分产品的说明第二部分塑件分析第三部分注射机的型号和规格选择及校核第四部分型腔的数目决定及排布第五部分分型面的选择第六部分浇注系统的设计第七部分型零件的工作尺寸计算第八部分推出机构的设计第九部分模架的选用第十部分冷却系统设计第十一部分模具的动作过程第十二部分设计小结第十三部分参考资料第一部分产品的说明本塑件结构简单, 壁厚均匀, 模架结构较简单。
精度要求较高, 为四级精度, 材料为聚乙烯成型性能一般, 其他并无特殊要求。
图一: 塑件俯视图第二部分塑件的分析聚乙烯化学名称: PE材料分析:PE是乙烯经聚合制得的一种热固性树脂。
在工业上, 也包括乙烯与少量α-烯烃的共聚物。
聚乙烯无臭, 无毒,手感似蜡,具有优良的耐低温性能(最低使用温度可达-70~-100℃),化学稳定性好,能耐大多数酸碱的侵蚀(不耐具有氧化性质的酸),常温下不溶于一般溶剂,吸水性小,电绝缘性能优良。
聚乙烯无臭, 无毒, 手感似蜡, 具有优良的耐低温性能(最低使用温度可达-70~-100℃), 化学稳定性好, 能耐大多数酸碱的侵蚀(不耐具有氧化性质的酸), 常温下不溶于一般溶剂, 吸水性小, 但由于其为线性分子可缓慢溶于某些有机溶剂, 且不发生溶胀, 电绝缘性能优良;但聚乙烯对于环境应力(化学与机械作用)是很敏感的, 耐热老化性差。
聚乙烯的性质因品种而异, 主要取决于分子结构和密度。
塑件注射成型工艺参数的确定:根据该塑件的结构特点和得成型性能, 查相关手册得到ABS塑件的成型工艺参数:第三部分注射机的型号和规格选择及校核注射模是安装在注射机上的, 因此在设计注射模具时应该对注射机有关技术规范进行必要的了解, 以便设计出符合要求的模具, 同时选定合适的注射机型号。
注塑模具说明书【范本模板】

集美大学课程设计说明书题目:防尘罩塑料注塑模具设计姓名:专业:班级:学号:指导老师:2 0 1 6 年1 月18日集美大学机械与能源工程学院专业课程设计任务书——材料成型及控制工程专业--设计题目:防尘罩塑料注塑模具设计设计任务:设计一简单塑料零件,并根据该零件设计一副注射模具。
制件年产量:10万件完成的任务:1.注射成形工艺卡一份;2.产品零件图一份;3.注射模具装配图及模具成形零件工程图各一份;4.设计说明书一份。
时间安排:1。
借资料、产品的结构设计及绘制零件图;(1。
5天)2.确定零件生产的工艺方案,填写零件注射工艺卡;(1天)3.零件成形工艺分析;确定型腔的数目;模具胀型力的计算,选择注射设备;选定分型面;确定型腔配置、确定浇注系统、确定脱模方式;冷却系统和推出结构设计;凹模和型芯尺寸计算和结构设计;模具其它零件设计;模具有关零件的强度和刚度校核;模具与注射机有关尺寸校核。
模具结构三维设计。
(4天)4.绘制模具结构装配图、模具成型零件工程图;(2。
5天)5.编写设计说明书;(2天)6.答辩。
(1天)参考书目:[1]齐卫东。
《塑料模具设计与制造》[M].北京:机械工业出版社,2004[2]陈剑鹤.《模具设计基础》[M].北京:械工业出版社,2004。
04[3]齐晓燕.《塑料成型工艺与模具设计》[M]。
北京:机械工业出版社,2006.01[4]高济,申树义.《塑料模具设计》[M]。
北京:机械工业出版社,2005。
09[5]高锦张。
《塑性成形工艺与模具设计》[M]。
北京:机械工业出版社,2002.03[6]陈锡栋。
《实用模具设计简明手册》[M].北京:机械工业出版社,2001指导教师:2016年1月18 日材料成型及控制工程级班学生: 学号:防尘罩塑料注塑模具设计[摘要]本课程设计说明书主要讲述对防尘罩进行模具设计的过程。
通过对塑件的工艺分析,设计出塑料模具。
本论文首先简单介绍了模具设计与分类,然后对产品材料性能作了介绍,并初步选择注射机。
玩具外壳注塑模设计 任务书+开题报告+论文

毕业设计(论文)任务书专业模具设计与制造班级模具072 姓名一、课题名称:玩具外壳注塑模设计二、主要技术指标:塑件材料为ABS,颜色为红色,收缩率为0.6%,生产批量5万件,塑件表面为亚光面、平整,塑件表面不允许有缩壁和飞边三、工作内容和要求:1、设计内容:1)、设计产品的三维图;2)、塑件的注塑工艺分析;3)、模具的基本结构和模架的设计;4)、模具结构、尺寸的设计和计算;5)、模具主要零件图和加工工艺规程的设计;6)、完成模具总装配图和模具主要零件图;7)、调整模具的装配及试模;8)、编写计算说明书;9)、进行毕业答辩。
2、设计要求:1)、模具总装配图1张(A3图纸)。
2)、模具典型零件工作图14-16张。
3)、设计计算说明书一份(8000~10000字)。
四、主要参考文献:[1]齐卫东主编.塑料模具设计与制造.第一版.高等教育出版社.2004;[2]陈剑鹤.吴云飞.王桂林主编.塑料模具设计图册.第一版.清华大学出版社.2008[3]史新民主编.机械设计基础.第一版.东南大学出版社.2007学生(签名)年月日指导教师(签名)年月日教研室主任(签名)年月日系主任(签名)年月日毕业设计(论文)开题报告目录摘要--------------------------------------------------------------------------------------6前言--------------------------------------------------------------------------------------6 1、塑件的零件图-------------------------------------------------------------------7塑件三维造型-------------------------------------------------------------------7 2.产品的注塑模具结构分析2.1零件的注塑工艺分析----------------------------------------------------8-9 2.2注射机的选择------------------------------------------------------------9-10 2.3模具结构设计-----------------------------------------------------------10-14 2.3.1分型面的选择----------------------------------------------------------10 2.3.2模具型腔数目的设计-------------------------------------------------10 2.3.3模具结构的设计---------------------------------------------------10-11 2.3.4成形零件的设计--------------------------------------------------10-12 2.3.5标准模架的选择---------------------------------------------------12-13 2.3.6浇注系统的设计---------------------------------------------------13-14 2.3.7推出系统的设计---------------------------------------------------14-15 2.3.8冷却系统的设计------------------------------------------------------15 2.3.9排气系统的设计-------------------------------------------------------15 2.4注射机的校核---------------------------------------------------------------15 结论---------------------------------------------------------------------------------16答谢词-----------------------------------------------------------------------------16参考文献--------------------------------------------------------------------------16附录(零件图)-----------------------------------------------------------18-27摘要:随着现代塑件制品的使用广泛且形状要求越来越精确,塑料模具的设计的要求也越来越高。
- 1、下载文档前请自行甄别文档内容的完整性,平台不提供额外的编辑、内容补充、找答案等附加服务。
- 2、"仅部分预览"的文档,不可在线预览部分如存在完整性等问题,可反馈申请退款(可完整预览的文档不适用该条件!)。
- 3、如文档侵犯您的权益,请联系客服反馈,我们会尽快为您处理(人工客服工作时间:9:00-18:30)。
6黎明职业大学塑料成型工艺与模具设计课程设计设计课题3 外壳说明书院系:机电工程与自动化学院专业:模具设计与制造学号:xxxxxxxxxx姓名:xxxxxx指导老师:xxxxxxxx题目:塑料名称外壳图号SJ-03 材料ABS 生产批量10万件一、塑件成型工艺分析1、塑件原材料成型特性分析:ABS是聚苯乙烯的改性产品,是目前产量最大、应用最广的工程塑件。
ABS是不透明非结晶型聚合物,无毒、无味、密度为1.02~1.05g/cm3,ABS具有突出的力学性能,坚固、坚韧、坚硬;具有一定的化学稳定性和良好的介电性能;具有较好的尺寸稳定性,易于成型和机械加工,成型塑件表面有较好的光泽,经过调色可配成任何颜色,表面可镀铬。
其缺点是耐热性差,连续工作温度为70℃左右,热变形温度为93℃左右,但热变形温度比聚苯乙烯、聚氯乙烯、尼龙等都高;耐候性差,在紫外线作用下易变硬发脆。
ABS成型性能如下:(1)易吸水,成型加工前应进行干燥处理,表面光泽要求高的塑件应长时间预热干燥。
(2)流动性中等,溢边值为0.04mm左右。
(3)壁厚和熔料温度对收缩率影响极小,塑件尺寸精度高。
(4)比热容低,塑化效率高,凝固也快,故成型周期短。
(5)表观黏度对剪切速率的依赖性很强,因此模具设计中大都采用点浇口形式。
(6)顶出力过大或机械加工时塑件表面会留下白色痕迹,脱模斜度宜取2°以上。
(7)易产生熔接痕,模具设计是应注意尽量减少浇注系统对料流的阻力。
(8)宜采用高料温、高模温和高注射压力成型。
在要求塑件精度高时,模具温度可控制在50~60℃;而在强调塑件光泽和耐热时,模具温度应控制在60~80℃.2、塑件结构工艺性分析1)结构分析:①从图纸上看,该塑件外形为四方外壳加两个侧耳,圆角过渡且无尖角存在,壁厚均匀为2mm,符合最小壁厚要求。
②塑件型腔较大,在一侧面有一个孔,要考虑侧抽装置。
③在塑件的两边还有两个凸台,凸台上各有一个Φ4的孔,要考虑分型抽芯装置。
2)尺寸精度分析该塑件尺寸精度要求按MT3级,查表3-1得主要尺寸公差标注如下:3)表面质量分析该塑件是个外壳,所以要求表面外观光洁,不允许有斑点和溶解痕,外表面Ra为1.6,而内表面没多大要求可取Ra为3.2。
4)塑件的生产批量该塑件的生产类型是中批量生产,因此在模具设计要求提高塑件的生产率,倾向于采用多型腔,高寿命。
自动脱模模具,因此模具造价要适当控制。
3、初选注射机1)计算塑件的体积和质量通过pro-e可获得矩形上壳罩的体积V=12.96cm3.ABS的密度ρ=1.03g/cm3.所以塑件的质量:W=ρv=1.03x12.96=13.35g.2)确定型腔数目由于塑件需要单边侧抽,所以考虑采用一模四腔,型腔平衡布置在型腔板四周,以便加工、浇口排列和模具的平衡。
3)确定注射成型的工艺参数:根据该塑件的结构特点和ABS的成型性能,查看有关资料初步确定塑件的注射成型工艺参数,如下表:4)确定模具温度及冷却方式ABS为非结晶塑料,流动性中等,壁厚一般。
因此在保证顺利脱模的前提下应尽可能降低模温,以缩短冷却时间,从而提高生产率。
所以模具应考虑适当的水循环冷却,成型模具温度控制在60℃-80℃5)确定成型设备由于塑件采用注射成型加工,使用一模四腔,因此可计算出一次注射成型过程所用塑料量为:w=4w/(80%)=64g考虑其外形尺寸,注射时所需的压力等设备因数,初步选用XS-ZY-250型注射机。
记录下XS-ZY-250型注射机的主要技术参数,如下表:XS-ZY-250型注射机的主要技术参数二、分型面及浇注系统的设计1、分型面的选择要始终保持分型面应选在塑件外形最大轮廓处原则,所以分型面需在塑件的侧耳上。
由于该塑件是个外壳,表面质量要求高,所以采用如下的分型:2、确定型腔的排列方式为了满足生产时间要求,所以在注射时采用一模四件,既一模四腔,综合考虑浇注系统和模具结构的复杂程度等因素,拟采用如下的型腔排列方式:3、浇注系统的设计1)主流道设计主流到与注射机的高温喷嘴反复接触碰撞,故应设计独立可拆卸更换的浇口套,采用优质钢材制作,并统一处理提高硬度,定位圈与浇口套分开设计。
根据设计手册查XS-ZY-250型注射机喷嘴的有关尺寸为喷嘴前端孔径d1=4mm,喷嘴前端球面半径SR1=18mm.根据模具主流到尺寸与喷嘴尺寸的关系SR=SR1+(1~2)及d=d1+(0.5~1),取主流道球面半径SR=20mm,小端直径d=4.5mm。
为了便于将凝料从主流道中拔出,将主流道设计成圆锥形,其斜度为1°~3°,经换算的主流道大端直径D=8.5mm.为了使熔料顺利进入分流道,可在主流道出料端设计半径为5mm的圆弧过渡。
2)分流道设计:本设计采用梯形截面分流道,如图:梯形侧面斜角a取5°,b取5mm.3)浇口设计:本设计采用圆形的点浇口,直径取0.5mm4)冷料穴设计采用一级冷料穴设计,位于四个分流道末端。
三、模具设计方案论证1、型腔布置对于一模多件的模具布置,在保证浇注系统分流道德流程短,模具结构紧凑,模具能正常工作的前提下,尽可能使模具型腔对称,均衡,取件方便。
本案例的模具采用一模四腔,型腔平衡布置在型腔板两侧。
2、成型零件的结构确定成型零件直接与高温高压的塑料接触,它的质量直接影响塑件的质量。
该塑件的材料为ABS的工程塑料,对于表面的粗糙度和精度要求比较高,因此要求成型零件有足够的强度,钢度,硬度和耐磨性。
应用优质模具钢制作,还应进行热处理以使其具备50-55HRC的硬度。
1)凹模(型腔)设计用组合式凹模放在动模板一侧,主要从节省优质模具钢材,方便热处理,方便冷却水道位置。
2)凸模(型芯)设计型芯结构也采用组合式,可节省贵重钢材,减少加工工量。
成型塑件内壁的大型芯装在动模一侧,成型2*Φ4的小型芯加工在镶块上。
3、导向定位机构设计由于塑件基本对称且无单向侧压力,所以采用直导柱导向变可以满足合模导向的定位注意:导柱要比主型芯高出6-8mm4、推出机构设计根据该塑件的形状特点,起推出机构可才用推杆推出或推板出,其中推板推出机构结构可靠,顶出力均匀,不形象塑件的外观质量,但制造困难,成本高;推杆推出机构简单,推出平稳可靠,故采用推杆推出。
5、抽芯机构的确定塑件需单边侧抽且是一模四腔排布,则一快滑块有两个抽芯,采用应用最广泛的斜导柱侧向抽芯机构,结构简单制造方便,运作可靠。
6、冷却系统的设计采用冷却水冷却,模具冷却水道采用环绕型腔的单层式或塑件型腔上下个一组回路四、主要零部件的设计计算1、成型零件的成型尺寸查相关手册得ABS的收缩率为0.4%~0.7%得平均收缩率Scp=(0.4+0.7)%/2=0.55%=0.0055根据塑件尺寸公差要求,定模制造公差去δz=Δ/3成型尺寸如下2、模具型腔壁厚的确定本模具的凹模采用的是组合嵌入式,因此可用整体式矩形腔壁厚计算公式来确定型腔侧壁厚度S和型腔底板厚度T.1)型腔侧壁厚度S的计算C=0.177 P=40MP E=2.2×1.5 [δ]=26.1 W=0.176S强>=[(pH1l2)/(2H[σ])]1/2= [(40*38*522)/(2*68*300)] 1/2=10.10mm S刚>=[(pH1l4)/(32HE[δ])]1/3= [(40*38*524)/(32*68*2.2*105*26.1)] 1/3=0.97mm2)型腔底板厚度T的计算H强>=[(3pbl2)/(4B[σ])]1/2= [(3*40*44*522)/(4*104*300)] 1/2=10.70mmH刚>=[(5pbl4)/(32BE[δ])]1/3= [(5*40*44*524)/(32*104*2.2*105*26.1)] 1/3=0.03mm3、抽芯机构设计1)抽芯距S的计算S=h+(2~3)=2+3=5mm2)抽芯力的计算3)确定斜导柱的倾斜角该处的侧向抽芯距小,抽芯力不大,斜导柱倾斜度取20º4)确定斜导柱的直径根据抽芯力Fc和斜导柱的倾斜角α=20 º,查表4-9, 4-10得最大弯曲力Fw=1kN,斜导柱的直径d=10mm5)斜导柱的总长度计算,Lz=L1+L2+L3+L4+L5=(d2/2)tanα+h/cosα+(d/2)tanα+S/sinα+(5~10)=13/2*tan20º+35/cos20º+10/2*tan20º+5/sin20º+(5~10)=61~66mm根据经验得:Lz取62mm6)确定楔紧块的αº由于滑块移动方向与合模方向垂直,故αº=20º7)确定滑块装置的定位距离由于滑块移动方向与合模方向垂直,故滑块装置的定位距离S应等于实际抽芯距S=5mm4、推出机构的设计采用推杆推出机构,由于该塑件脱模力不是太大,推杆的布置空间足够,所以无需用繁琐的计算方法确定推杆尺寸大小,可根据经验选取d=4mm的国际推杆(GB/4169.1-2006),注意保证推出距离略大于型芯的突出长度2~3mm,即推出距离大于40mm5、标准模架的确定查表8-7选取标准模板的尺寸为350×350×A100×B 40×C100五、成型设备的校核计算1、锁模力的校核10 ×4=314.88KNF≥k PA=1.2×40×610×1.64×32、安装尺寸的校核实际模具闭合高度为H=H4+H3+A+B+C+H1=45+35+100+40+100+30=350mm注射机最大安装尺寸598mm*520mm,模具最小厚度Hmin=200mm,模具最大厚度Hmax=350mm,符合Hmin<=H<=Hmax故模具符合安装要求。
4、推出机构的校核:符合5、开模行程的校核:S=500>H1+H2+a+(5~10)=40+38+75+10=163mm符合要求。
绘制模具装配图。