预脱硅及高压溶出生产工艺技术
预脱硅及高压溶出生产工艺技术
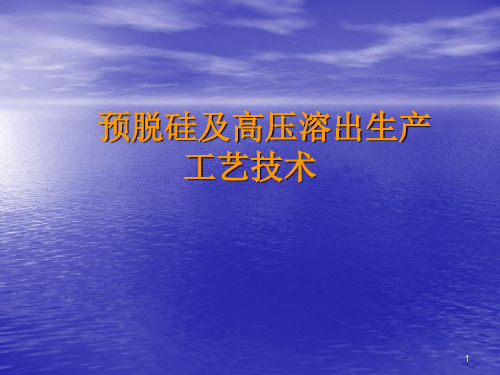
。
7
④脱硅停留时间。时间越长分解速度越快,溶液中最 终的SiO2含量越低。 ⑤铝土矿中存在的高岭石含量和质量。高岭石含量越 高分解速度越快,溶液中最终的SiO2含量越低。 2-2高压溶出 2-2-1相关名词 2-2-1-1铝硅比 铝土矿或赤泥中所含的Al2O3与SiO2的重量之比称为 铝硅比,用A/S表示。 2-2-1-2 αk值 αk值是指铝酸钠溶液中所含的氧化铝(Al2O3)与苛 性氧化钠(Na2OK或减称Nk)的分子比: αk =1.645*NK/A 2-2-1-3 循环效率 1m3循环母液在一次拜耳法循环过程中所能生产出的 氧化铝量称为循环效率,用E表示: 循环效率用αk表示为:
13
三水铝石在接近常压、温度140℃~150℃、循环母液较低的 情况下即可溶出,并能达到工业溶出的速度。而一水软铝石 型铝土矿则较难溶出,溶出温度160℃左右,苛性碱浓度要 求比三水铝石高。一水硬铝石最难溶出,温度要求在200℃ 以上,在高温、高压、高碱浓度时才能较好地溶出。 另外,铝土矿中的杂质含量(如TiO2、Fe2O3、SiO2等)越 多、越分散,氧化铝水合物被其包裹的程度越大,与碱溶液 接触越少,溶出越困难。 2、溶出温度: 温度是影响溶出过程中最重要的影响因素。 提高溶出温度,使溶出速度加快,溶液的粘度下降,有助于 矿石和碱液表面接触,从而提高氧化铝的溶出率。提高溶出 温度由于溶出速度快,可以缩短溶出时间。 随着温度的提高,Al2O3在碱溶液中的溶解度显著增加,溶 出液Rp值升高,有利于分解率的提高,从而可以提高碱液的 循环效率。提高溶出温度后,用浓度较低的循环母液亦可获
16
7、添加石灰: 在溶出一水硬铝石铝土矿时,氧化钛与碱液反应形成钛 酸钠薄膜包裹在矿粒表面,阻碍溶出过程的进行。加入石灰 可以破坏其薄膜,提高氧化铝的溶出率。但是加入石灰量太 多,不但增加赤泥量,而且由于3CaO.Al2O3.6H2O的生成, 造成大量氧化铝损失。 2-2-3各种杂质在溶出过程行为 铝土矿中杂质化学反应的结果,除极少量杂质溶于碱溶液 以外,绝大部分杂质都进入赤泥。铝土矿中的主要杂质: SiO2变成不溶的钠硅渣(Na2O.Al2O3.1.7SiO2. nH2O)和水 化石榴石(CaO.Al2O3.1.1SiO2.nH2O)而进入赤泥;氧化钛 生成不溶于碱溶液的2CaO.TiO2.2H2O而进入赤泥;铁的化 合物最终基本上都以铁的氧化物形态,进入赤泥。
原矿浆制备高压溶出
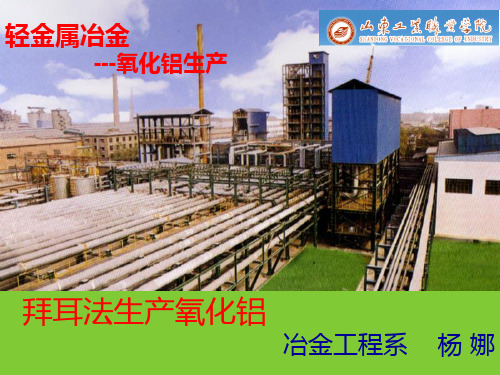
理
AS
A
100% ( 1
1 ) 100% A/S
氧化铝相对溶出率:氧化铝实际溶出率与理论溶出率之比。
相
实 (A / S ) 矿 ( A / S ) 泥 100% 理 (A / S ) 矿 1
氧化铝溶出率 拜耳循环
氧化铝实际溶出率:铝土矿与NaOH反应实际溶出到溶液中的
Al2O3量与铝土矿中Al2O3总量之比。
实
Q矿A矿 Q泥A泥 Q矿A矿 100% (A / S )矿 (A / S ) 泥 (A / S )矿 100%
氧化铝理论溶出率:理论上矿石中可以溶出的Al2O3量(扣除不
掌握的主要内容
氧化铝水合物的溶出行为 含硅矿物的溶出行为、产生的危害及防治措施
含铁矿物的溶出行为、产生的危害及防治措施
含钛矿物的溶出行为、 产生的危害及防治措施 含硫矿物的溶出行为、产生的危害及防治措施 有机物的溶出行为、产生的危害及防治措施
4.2.2 高压溶出
2NaAl(OH)4+aq
4.2 拜耳法生产氧化铝
拜耳循环 拜耳循环
至Al2O3· H2O 至 Al2O3· 3H2O 200℃ MR=1.65
60℃ B 30℃ MR=3.40
拜耳法生产Al2O3的主要工序 •铝土矿的溶出 •铝酸钠溶液的稀释 •晶种分解 •氢氧化铝的焙烧 •分解母液蒸发
A点:循环母液的组成点 AB线:溶出线 BC线:稀释线 CD线:分解线 DA线:蒸发线
开始分解
含硅矿物的溶出行为:含硅矿物与碱反应,首先分解成铝酸钠 和硅酸钠进入溶液,然后当硅酸钠浓度达一定值后与铝酸钠溶 液反应生成水合铝硅酸钠(钠硅渣)进入赤泥。
拜耳法生产氧化铝03溶出车间-sn

使硅矿物尽可能转变为钠硅渣结晶,这个过程称为
预脱硅。矿浆中生成的钠硅渣又可成为其他含硅矿 物在更高温度下反应生成钠硅渣的晶种,因而减小 了它们在加热表面上析出结疤的速度,从而使高压 溶出器的工作周期延长。
2.单管预热-压煮器间接加热溶出工艺
• 从原料车间送来的固含350g/l的原矿浆进入常压 脱硅工段的加热槽中,将温度从82-87 ℃提升到 100-105 ℃,然后在脱硅槽中进行连续脱硅。在 隔膜泵的进口处添加母液以调整矿浆RP和固含, 脱硅槽底部设有返砂泵,每班定期将粗砂返回原 料磨工段。 • 用隔膜泵将原矿浆送往溶出工段的套管预热器, 采用六级套管将原矿浆温度预热到174-180 ℃,再 用四级预热压煮器将原矿浆温度预热到210-220 ℃, 而后采用6.0Mpa高压新蒸汽加热,将原矿浆加热 至260 ℃后进入保温停留罐停留45-60分钟。
出液的浓度通常是180~240g/L的Na2O。
3.3一水硬铝石型铝土矿的溶出 • 在所有类型的铝土矿中,一水硬铝石型铝土矿 是最难溶出的。 • 一水硬铝石的溶出温度通常在260℃左右,溶 出液Na2O浓度为240~300g/L。我国的铝土矿 主要是一水硬铝石型铝土矿。 • 一水软铝石型或一水硬铝石型铝土矿在溶出过 程中发生反应为: AlOOH.H2O+NaOH+aq →NaAl(OH)4+ aq
• 溶出后矿浆经十级闪蒸,温度从260 ℃降至125 ℃, 然后送入稀释槽。从沉降来的洗液同时加入稀释槽 中,稀释后料浆用泵送往溶出后槽,停留2小时以 上,以进一步脱除溶液中的硅、铁、锌等杂质。 • 各级矿浆自蒸发器产生的二次蒸汽用于相对应的套 管预热器和预热压煮器中预热原矿浆,二次汽冷凝 水从预热器排出进入冷凝水罐,并经逐级闪蒸降压 后,汇总到末级冷凝水罐,一部分用作闪蒸注水, 一部分送往热水站。加热压煮器产生的新蒸汽冷凝 水送入新蒸汽冷凝水自蒸发器闪蒸后,二次汽去加 热脱硅槽,不带碱冷凝水去供热站,带碱冷凝水去 热水站。
氧化铝生产高压溶出新蒸汽冷凝水热能利用工艺优化研究

氧化铝生产高压溶出新蒸汽冷凝水热能利用工艺优化研究摘要氧化铝生产中溶出和蒸发等环节都会消耗大量的热,采取烟气余热回收技术来回收上述环节中所释放的热量就可有效降低氧化铝生产中的能源消耗,从而实现绿色化学的目标。
当前在氧化铝生产过程中,热能回收利用的效率较低,为了改变这一现状,应积极优化氧化铝生产流程,提高生产效益,保证生产安全。
关键词氧化铝;能源损耗;蒸发;溶出热能现阶段的氧化铝生产过中,能源消耗占到了总成本的3成左右。
故而为了达到节能降耗的效果,应采取积极的措施优化生产工艺及生产流程。
拜耳法是氧化铝生产中采用的主要方法。
1 高压溶出蒸发冷凝水概况以某氧化铝生产企业为例,企业氧化铝生产系统当中主要有2组高压溶出机组,矿浆处理达到了每小时900立方米,生产中采取间接加热的方式,并同步回收余热,实现再次利用。
使用压强为6.4MPa的新蒸汽加热,在加热时,单个机组每小时可生产90-100吨高温新蒸汽冷凝水,冷凝水的温度为150-160℃,设备正常运行时,冷却水导电率为5μs/cm。
除了部分冷却水要进行去氢铝洗涤以外,剩余的冷却水都要送入热电除氧器当中。
这一过程中还要开展换热降温处理,这也在一定程度上影响了冷凝水余热的利用率。
在蒸汽时,应使用两台流效降膜发机组,利用压强为0.6MPa的新蒸汽加热。
加之氧化铝生产中还要保证水盐处于平衡的状态,单台机组的蒸汽能力为每小时140-150吨,平均汽水比为0.3,需要每个小时释放100吨新蒸汽冷凝水,电导率为5μs/cm,且冷凝水温度为70℃,方可去热电。
2 新蒸汽冷凝水理化参数和水化性质分析分别从压力、温度、流量、电导率等方面对系统的理化参数进行分析,如表1。
实际的最大产水量为:高压溶出机组2×63=126m3/h,而蒸发机组为2×50=100m3/h,二者共计226m3/h。
对高压溶出新蒸汽冷凝水和蒸发工序新蒸汽冷凝水的可供热电的回水能力、回水温度、运转率、电导率和实际回水进行了深入研究,结果如表1和表2所示。
高压溶出工序试车方案

二期高压溶出工序试车方案一、前言:本工序的任务:是将原料车间送来的原矿浆在予脱硅槽中用蒸汽间接加热进行予脱硅,然后用高压隔膜泵打入10级套管用乏汽和熔盐加热并在溶出罐停留60分钟,使矿石中氧化铝与苛性碱反应生成铝酸钠溶液,其他成分反应后绝大多数以固相形式留在赤泥中。
溶出矿浆经稀释后送到下一工序—赤泥处理车间。
溶出过程是氧化铝生产的主要环节,二期扩建采用一期熔盐加热管道化加保温停留罐溶出技术。
其主要装备有:φ6×11M的予脱硅槽7台,其中三台为蒸汽间接加热予脱硅槽,德国产流量为60M3/h,出口压力为9~11MPa的隔膜泵4台。
管道化溶出装置一组,(包括三根φ114×10内管,φ356×10外管组成套管,用乏汽加热的予热段9级,每级4根预热器,每根69M,熔盐加热段为第10级,外管:φ406×10,由10根预热器组成,每根50M);φ2×12M的溶出停留罐4台;φ1.6~φ3.0×8.5M矿浆自蒸发器9台;φ5×8M稀释槽一台。
原料车间送来的固含为320~350g/L的矿浆进入前面两台带加热管束予脱硅槽,用0.5MPa、150℃的低压蒸汽间接加热至100~105℃,利用位差自流入后5台予脱硅槽,以减少后面溶出套管的硅结疤。
予脱硅后的矿浆配入循环母液固含降至200~240g/L后用高压隔膜泵以7~9MPa的压力打入溶出套管,1~9级用矿浆自蒸发器来的乏汽间接加热到200℃,到第10级用温度为420℃的高温熔盐继续加热至265℃,进入溶出停留罐保温60 min,完成溶出反应,溶出后的矿浆经9级矿浆自蒸发器逐级降压降温,温度从265℃降至130℃。
产生的二次蒸汽(乏汽)去1~9级溶出套管预热矿浆。
溶出矿浆去稀释槽加入赤泥洗液稀释到溶液中Na2O K为165g/L后送赤泥处理车间。
按设计溶出车间的主要技术条件:予脱硅温度:100~105℃予脱硅时间:10h脱硅矿浆固含:320~350g/L进高压隔膜泵的矿浆固含:200~240g/L进高压隔膜泵的矿浆温度:92℃隔膜泵工作压力:9~11MPa矿浆加热9级出来矿浆温度:200~210℃第10级熔盐加温后矿浆温度:265℃溶出温度:265℃溶出时间:60min矿浆自蒸发器经九级降温从265℃降至130℃稀释矿浆:Na2Ok 165g/L稀释温度:107~110℃试车期间按试车程序,分段进行,各段规定技术条件随着试车进程,技术条件逐步调整,最终达到设计技术条件。
氧化铝生产工艺

氧化铝生产工艺氧化铝生产工艺流程分为烧结法生产工艺流程、拜耳法生产工艺流程或两种混合(串联、并联、混联),大多采用的是拜耳法,其主要生产工序有:配矿、矿浆制备、预脱硅、高压溶出、赤泥分离与洗涤、粗液精制、种分分解、氢氧化铝洗涤过滤、焙烧、母液蒸发。
氧化铝生产工艺流程烧结法生产线:铝土矿破碎、堆料、取料、输送、生料磨制、料浆调配、熟料烧成、煤粉制备、熟料中碎、电收尘、风机螺旋、熟料溶出、赤泥分离、赤泥洗涤、粗液喂料泵、脱硅、叶滤硅渣、碳酸化分解、种子分解、氢铝过滤、母液蒸发、平盘过滤、焙烧。
氧化铝生产工艺流程拜耳法生产线:供矿、原料制备、单管溶出、沉降洗涤、分解系统、蒸发系统、焙烧炉。
氧化铝生产工艺流程联合法生产线:破碎、堆厂、翻车机、原燃料输送(一车间),化碱、原料磨、饲料机(二车间),卷扬、石灰炉(石灰炉车间),脱硅、压缩机。
氧化铝生产工艺流程拜耳法基本原理是用浓氢氧化钠溶液将氢氧化铝转化为铝酸钠,通过稀释和添加氢氧化铝晶种使氢氧化铝重新析出,剩余的氢氧化钠溶液重新用于处理下一批铝土矿,实现了连续化生产。
今日,世界上95%的铝业公司都在使用拜耳法生产氧化铝。
氧化铝生产工艺流程-拜耳法生产工艺流程主要有以下工序组成:1、矿浆制备(拜耳法氧化铝工艺原料工序)选矿、配矿。
2、溶出工序(拜耳法氧化铝工艺溶出工序)负责对原料配好的矿石进行高压或低压溶出。
3、沉降(拜耳法氧化铝工艺沉降工序)负责对上一工序处理的物料进行杂质分离。
4、分解工序。
5、焙烧工序(将分解来的料浆进行液固分离得到氢氧化铝、最终将氢氧化铝进行高温焙烧得到氧化铝。
6、蒸发工序负责对整个工艺流程所用水、碱的处理。
7、煤气站:负责对拜耳法氧化铝工艺最后一道工序焙烧工序所用燃气的供给。
氧化铝生产工艺流程-碱石灰烧结法生产工艺:用于处理高硅的铝土矿,将铝土矿、碳酸钠和石灰按一定比例混合配料,在回转窑内烧结成由铝酸钠(Na2O·Al2O3)、铁酸钠(Na2O·Fe2O3、原硅酸钙(2CaO·SiO2)和钛酸钠(CaO·TiO2)成的熟料。
浅析拜耳法氧化铝生产中预脱硅工艺

欧洲拜耳法 2 0 0 — 2 6 o ℃ N a 2 O k > 2 0 0 g / L
1 - 3 2
美洲拜耳法 1 4 5  ̄ C左右 N a 2 O k > 2 3 0 g / L
1 . 2 8
一水硬铝石 2 6 0 - 2 8 0 ℃ ' N a , O k > 3 4 ( ) g , L
浅析 拜耳 法氧化铝 生产 中预脱硅 工艺
蒙振 长
( 广 西 华银 铝 业 有 限公 司 广 西 百色 市 5 3 3 7 0 0 ) 摘 要: 随 着 社 会 经 济 的不 断 发 展 , 工业文 明的不断推进 。 氧 化 铝 的 生 产 规 模 受 到 市 场 的不 断刺 激 , 其产量不 断增加。 这 样 的 情 况 下, 对 于铝土矿 资源的消耗量 持续攀升 , 对于优质 铝土矿 的资源消耗不 断增加 , 造 成其资源 匮乏 , 从 而导致 目前 氧化铝 生产 中新 供铝 土矿 的 A / S持续减 少, 而其 中氧化 铁的含量却在不 断增加 。为了使保持氧化铝 的高效优质 生产 , 满足市场 需求 , 这就 要求对 于拜耳法 氧化铝 的生产 工艺进行新 的调整与优化 。另外 , 还要考虑到 目前氧 化铝对于石灰 的添加 量情况 。本文通过 对于氧化铝新工 艺的分析 , 以期为读 者提供氧化铝 生产 中预脱硅、 溶 出等 生产 工序的相关参考 资料与数据 。 关键词: 氧化铝 ; 拜耳法 ; 新 工 艺
石灰自身和燃料灰活性添加方式的回收率分中si02导致al20损失增大赤泥量促进针铁矿转变成赤铁矿沉降性能促进方钠石转变为钙添加量增加沉改善赤泥添加量溶出时间降杂质含量洗涤反苛化生成碳碱增负担加铝酸钠粘度霞石避免生成钛酸钠水合铝硅酸钠转变为水化石榴石方钠石转变为钙霞石添加量杂质含量增加
宝钢高炉炉前铁水预脱硅技术

宝钢高炉炉前铁水预脱硅技术王天球王士彬(上海宝山钢铁股份有限公司炼铁厂)摘要:本文介绍了宝钢高炉炉前铁水预脱硅技术,并根据现场实际生产数据及操作经验,分析总结出了影响脱硅效果和泡沫渣的诸多因素,通过采取一系列改进措施,使高炉炉前脱硅取得了很大的进步,为炼钢冶炼低磷低硫精品钢提供了优质低硅铁水。
关键词:炉前脱硅脱硅效果泡沫渣影响因素1.概述高炉炉前脱硅主要是为炼钢提供低硅铁水,冶炼高附加值精品钢。
以往铁水预处理都是由炼钢“三脱”来进行的。
由于其工艺复杂,处理时间长,铁水热损失大,渣量大,成本高,八十年代初以来,日本、韩国、台湾等国家和地区相继采用高炉炉前铁水脱硅技术。
其目的在于缩短钢铁冶炼全流程生产时间,降低炼钢熔剂消耗量,为生产低磷低硫高级钢,提高产品竞争力以及改善企业的经济效益提供必要条件。
高炉炉前脱硅所用的方法主要有投撒法和喷吹法两种。
脱硅剂靠自重撒落到铁水表面的称为投撒法,用载气将脱硅剂以一定速度喷入铁水中的称为喷吹法。
这两种方法都有使用实例。
比较而言,投撒法所用的脱硅剂在粒度和种类上可选范围较宽(如烧结矿粉和氧化铁皮等均可应用),其系统工艺流程及设备都比较简单,造价低,但脱硅剂消耗量大,脱硅剂与铁水搅拌不充分,脱硅产生泡沫渣多,脱硅效果欠佳。
日本福山4BF、千叶6BF、韩国光阳4BF等高炉所用的脱硅系统均属于投撒法。
喷吹法脱硅工艺及设备相对要复杂些,所用的脱硅剂粒度、水分等要求也较高,但脱硅剂与铁水的混合较好,反应界面大,有利于脱硅反应进行,脱硅效果较好。
所用的脱硅剂一般为烧结厂除尘灰和出铁厂除尘灰。
喷吹法是目前采用较多的一种炉前脱硅工艺。
日本的千叶5BF、水岛2BF、3BF、4BF、鹿岛2BF、3BF、福山2BF、神户3BF、加古川2BF 以及台湾中钢1BF等均采用了喷吹法脱硅。
宝钢采用铁水预处理技术,有利于调整公司产品结构,冶炼国内、外市场需求量不断增加的低磷、低硫、高纯度、高附加值的钢种,提高公司市场竞争力和经济效益。
熟料溶出脱硅操作规程
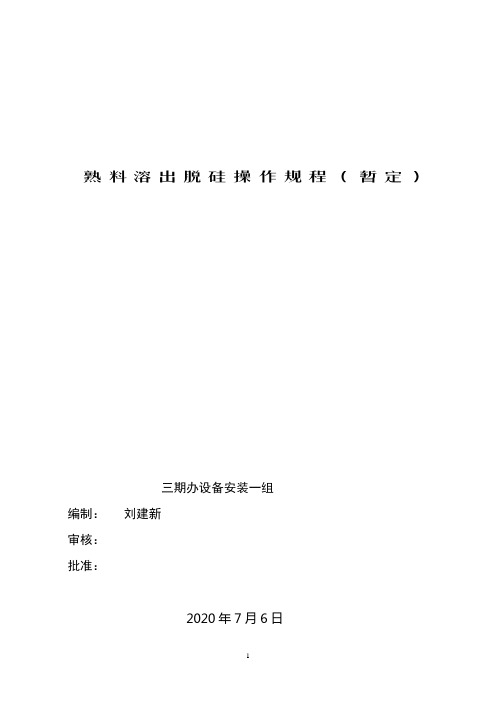
熟料溶出脱硅操作规程(暂定)三期办设备安装一组编制:刘建新审核:批准:2013年4月5日熟料溶出脱硅操作规程(暂定)一、工艺流程描述:由北固烧结厂来的粉状熟料,经溶出槽溶出后,送高效沉降槽快速分离,溢流进脱硅槽,同时加入一定量拜耳赤泥作为脱硅种子,进行常压脱硅,添加一定量的种分母液适当提高αK,(提高溶液的稳定性,减少二次反应损失),经过脱硅后的浆液送溶出车间稀释后槽,与稀释液合流,底流送赤泥车间洗涤槽,与拜耳赤泥一起经过数次洗涤后外排。
二、工艺流程:三、高效沉降槽工艺技术条件控制高效沉降槽进料温度:75℃~85℃;溢流浮游物≤0.6g/l;溶出液N C:10~15g/l;底流液固L/S≤2.0;进料液固比:8~12;清液层高度:≥1.5米絮凝剂添加量:为干赤泥量的0.5~0.6‰四、高效沉降槽规格:ф3.5×6.8m五、高效槽沉降槽开车前的准备工作。
略(参考《赤泥车间岗位操作规程》。
)六、高效沉降槽开停车步骤。
略(参考《赤泥车间岗位操作规程》。
)七、高效沉降槽的巡检方式、标准及内容八、熟料脱硅槽1.常压脱硅技术条件:脱硅温度:98~102℃蒸汽压力:0.3~0.4Mpa脱硅固含:50~60 g/l脱硅时间2~3小时脱硅粗液苛性比值:αk≤1.47脱硅出料硅量指数:>200九、脱硅槽开车前的准备工作1、联系电工检查电气绝缘是否合格。
2、检查槽内有无妨碍搅拌运转的杂物。
种分母液、拜耳赤泥、溢流进料管是否畅通,加热管束是否完好。
3、搅拌装置是否符合要求,各部位的紧固件是否紧固。
4、人工攀车2~3圈。
4、检查各转动部位润滑点油量是否充足,油质是否合格。
5、检查人孔门,是否密封好,进出料管流程是否正确,各个阀门、是否灵活好用。
6、检查各部位螺栓是否紧固。
7、检查、电机、减速机传动是否良好。
电机转向是否正确。
8、启动搅拌,试运转几圈,检查运转是否正常。
9、检查计量和检测仪器、仪表是否完好,指示是否准确。
氧化铝生产溶出技术工艺简介演示
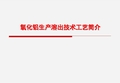
六、 氧化铝生产技术展望
基础理论研究 重点:为进一步简化流程、提高效率、降低能耗、 优化指标提供理论支持和技术支撑 1.氧化铝颗粒形貌、结构的变化规律与其物理性能的关 系研究 2.铝酸钠溶液的结构与化学的研究 3.生产过程热力学、动力学和反应工程学的研究 4.化学添加剂防垢技术与机理的研究 5.氧化铝生产短流程基础理论研究
四、 溶出区域设备介绍
高压溶出区域效果图
四、 溶出区域设备介绍
溶出高压进料隔膜泵
四、 溶出区域设备介绍
四、 溶出区域设备介绍
溶出套管
四、 溶出区域设备介绍
溶出预热加热套管 单套管 三套管
四、 溶出区域设备介绍
闪蒸槽(自蒸发器)
四、 溶出区域设备介绍
闪蒸槽(自蒸发器)
三、影响溶出工艺的主要因素
含铁矿物的危害
生产难以滤除的微小氧化铁水合物颗粒,进入成品氢 氧化铝之后影响质量。 生产大量沉降性能很差的赤泥。 以类质同晶形态进入针铁矿中的Al3+,降低矿石Al2O3 的提取率。
含钛矿物的危害
钛酸钠在铝矿物表面形成一层致密的保护膜,隔绝其 与溶液的接触。 生产钛酸钠造成苛性碱损失,细小钛酸钠会生产胶体, 恶化赤泥沉降。
一水硬铝石型
三水铝石—一水软铝石型 一水软铝石—一水硬铝石型
258~280
170~210 258~280
4.8~6.5
0.7~1.9 4.8~6.5
一、氧化铝生产溶出工艺现状
拜耳法溶出技术 大多采用间接加热强化溶出技术
单管预热—压煮器溶出技术 管道化溶出技术 管道间接加热—停留罐溶出技术 双流法溶出技术
一、氧化铝生产溶出工艺现状
铝土矿的分类 一水硬铝石型矿石 一水软铝石型矿石 三水型铝土矿 混合型铝土矿 我国铝土矿大多为一水硬铝石型铝土矿,具有高铝、 高硅、低铁、高硫等特点,其中一水硬铝石占98.46%
年产40万吨拜儿法氧化铝溶出车间工艺技术总结
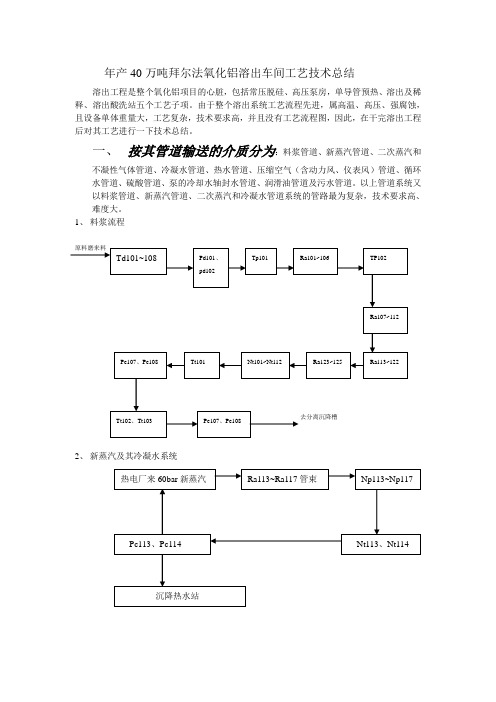
年产40万吨拜尔法氧化铝溶出车间工艺技术总结溶出工程是整个氧化铝项目的心脏,包括常压脱硅、高压泵房,单导管预热、溶出及稀释、溶出酸洗站五个工艺子项。
由于整个溶出系统工艺流程先进,属高温、高压、强腐蚀,且设备单体重量大,工艺复杂,技术要求高,并且没有工艺流程图,因此,在干完溶出工程后对其工艺进行一下技术总结。
一、按其管道输送的介质分为:料浆管道、新蒸汽管道、二次蒸汽和不凝性气体管道、冷凝水管道、热水管道、压缩空气(含动力风、仪表风)管道、循环水管道、硫酸管道、泵的冷却水轴封水管道、润滑油管道及污水管道。
以上管道系统又以料浆管道、新蒸汽管道、二次蒸汽和冷凝水管道系统的管路最为复杂,技术要求高、难度大。
1、料浆流程2、新蒸汽及其冷凝水系统3、闪蒸器NT101~NT112的二次蒸汽及其冷凝水系统4、新蒸汽自蒸发器Nt113、Nt114,热电厂来的6bar低压蒸汽及其冷凝水系统以上溶出车间的详细工艺流程见图(一)、图(二)、图(三)二、在施工过程中应注意的几个问题1、由于溶出的材料错综复杂,材质多、规格多、连接形式多、压力等级多,同种规格的管道就有很多种,例如φ273的无缝钢管就有φ273×15、φ273×13、φ273×12、φ273×11、φ273×10、φ273×86种。
法兰连接形式更是多种多样,有突面带颈平焊法兰、突面对焊法兰、凹凸面带颈平焊法兰、凹凸面对焊法兰、环接面带颈平焊法兰、环接面注:A型金属缠绕垫片为基本型,B型金属缠绕垫片为带内环型(即带有加强圈)C型金属缠绕垫片为带外环型(即带有定位环),D型金属缠绕垫片为内外环型(有加强圈和定位环)所以我们在提交材料预算时要仔细核对,确定其连接方式、材质及规格,不要混为一谈。
在使用材料时候一定要严格把关,不要错用、串用。
2、由于溶出的设备比较多:a、溶出主厂房有:19台压煮器、12台闪蒸器、2台脉冲缓冲器、17台冷凝水罐、2台新蒸汽自蒸发器、1台稀释槽、2台稀释后槽、6级单导管预热器、2台热水槽、3台污水槽、3台污水泵、2台稀释后泵、2台稀释泵、2台热水泵、2台二次气冷凝水泵、2台新蒸汽冷凝水泵、1台多级泵b、常压脱硅有:8台脱硅槽、1台脱硅冷凝水罐、2台除沙泵、2台循环泵、2台冷凝水泵、1台污水槽、1台污水泵c、高压泵房有:2台空压机、2台高压储气罐、3台隔膜泵(一期只上2台)d、溶出酸洗站有:1台浓酸槽、2台稀酸槽、1台回酸分离器、1台空气干燥器、2台浓酸泵、2台稀酸泵、1台污酸槽、1台污酸泵并且设备的压力等级也不一样,有1.0MPa、1.6MPa、2.0MPa、5.0MPa、11.0MPa等。
高压溶出设备安装方案
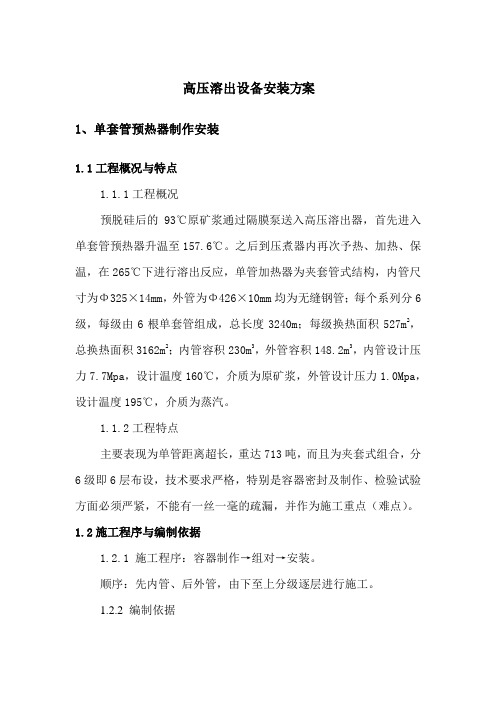
高压溶出设备安装方案1、单套管预热器制作安装1.1工程概况与特点1.1.1工程概况预脱硅后的93℃原矿浆通过隔膜泵送入高压溶出器,首先进入单套管预热器升温至157.6℃。
之后到压煮器内再次予热、加热、保温,在265℃下进行溶出反应,单管加热器为夹套管式结构,内管尺寸为Φ325×14mm,外管为Φ426×10mm均为无缝钢管;每个系列分6级,每级由6根单套管组成,总长度3240m;每级换热面积527m2,总换热面积3162m2;内管容积230m3,外管容积148.2m3,内管设计压力7.7Mpa,设计温度160℃,介质为原矿浆,外管设计压力1.0Mpa,设计温度195℃,介质为蒸汽。
1.1.2工程特点主要表现为单管距离超长,重达713吨,而且为夹套式组合,分6级即6层布设,技术要求严格,特别是容器密封及制作、检验试验方面必须严紧,不能有一丝一毫的疏漏,并作为施工重点(难点)。
1.2施工程序与编制依据1.2.1 施工程序:容器制作→组对→安装。
顺序:先内管、后外管,由下至上分级逐层进行施工。
1.2.2 编制依据1.2.2.1 中铝股份晋施招字第1号“施工招标文件”;1.2.2.2沈阳院编制的“80万吨氧化铝高压溶出初步设计”;1.2.2.3单套管预热器(Ⅰ─Ⅵ级)图纸;1.2.2.4施工规范及验评标准:(1)钢结构工程施工质量验收规范GB50205─2001;(2)工业金属管道工程施工及验收规范GB50235─97;(3)现场设备、工业管道焊接工程施工及验收规范GB50236─98;(4)工业设备、管道防腐工程施工及验收规范HGJ229─91;(5)涂装前钢材表面锈蚀及除锈等级GB8923─88;(6)钢结构制作安装施工规程YB9254─95;(7)钢制压力容器GB150─1998;(8)钢制焊接常压容器JB/T4735─1997;(9)压力容器无损检测JB4730─94;(10)工业安装工程质量检验评定统一标准GB50252─94;(11)工业金属管道工程质量检验评定标准GB50184─93;(12)山西铝建设工程质量验收评定统一标准;(13)工业设备及管道绝热工程施工及验收规范;(14)工业设备及管道绝热工程设计规范等。
- 1、下载文档前请自行甄别文档内容的完整性,平台不提供额外的编辑、内容补充、找答案等附加服务。
- 2、"仅部分预览"的文档,不可在线预览部分如存在完整性等问题,可反馈申请退款(可完整预览的文档不适用该条件!)。
- 3、如文档侵犯您的权益,请联系客服反馈,我们会尽快为您处理(人工客服工作时间:9:00-18:30)。
。
7
④脱硅停留时间。时间越长分解速度越快,溶液中最 终的SiO2含量越低。 ⑤铝土矿中存在的高岭石含量和质量。高岭石含量越 高分解速度越快,溶液中最终的SiO2含量越低。 2-2高压溶出 2-2-1相关名词 2-2-1-1铝硅比 铝土矿或赤泥中所含的Al2O3与SiO2的重量之比称为 铝硅比,用A/S表示。 2-2-1-2 αk值 αk值是指铝酸钠溶液中所含的氧化铝(Al2O3)与苛 性氧化钠(Na2OK或减称Nk)的分子比: αk =1.645*NK/A 2-2-1-3 循环效率 1m3循环母液在一次拜耳法循环过程中所能生产出的 氧化铝量称为循环效率,用E表示: 循环效率用αk表示为:
10
有,即使矿石中的SiO2完全反应,溶出反应后的 SiO2也析出进入赤泥,但生成的含硅矿物的A/S并不 能保证为1。由此可见用上式计算出的理论溶出率会 因溶出条件的不同产生一定的误差。 在处理难溶出的矿石时,其中的Al2O3常常不 能充分溶出。由此可见只用溶出率并不能说明某一 种作业条件的好坏,因为矿石本身就会造成溶出率 的差别。为了消除这种矿石本身品位(A/S)不同造 成的影响,通常采用相对溶出率作为比较各种溶出 作业条件好坏的标准之一。它是实际溶出率与理论 溶出率的比值,即 η相 = η实 / η理
5
在100℃的温度条件下,以高岭石(Al2O3.2SiO2.2H20)形 态存在的SiO2在苛性碱溶液中溶解生成硅酸钠进入溶液,当 溶液中的SiO2含量达到临界饱和状态时铝硅酸钠就会分解出 来,进入固相。
液相 SiO2 浓度
高岭石溶解
铝硅酸钠分解
脱硅时间
图-1铝土矿常压脱硅过程
二氧化硅的分解产物是方钠石 [3(Na2O.Al2O3.2SiO2.2H2O)Na2X],(分子式中的X代表CO2、 SiO2 、Cl……,)方钠石和赤泥一起被排除。
16
7、添加石灰: 在溶出一水硬铝石铝土石灰 可以破坏其薄膜,提高氧化铝的溶出率。但是加入石灰量太 多,不但增加赤泥量,而且由于3CaO.Al2O3.6H2O的生成, 造成大量氧化铝损失。 2-2-3各种杂质在溶出过程行为 铝土矿中杂质化学反应的结果,除极少量杂质溶于碱溶液 以外,绝大部分杂质都进入赤泥。铝土矿中的主要杂质: SiO2变成不溶的钠硅渣(Na2O.Al2O3.1.7SiO2. nH2O)和水 化石榴石(CaO.Al2O3.1.1SiO2.nH2O)而进入赤泥;氧化钛 生成不溶于碱溶液的2CaO.TiO2.2H2O而进入赤泥;铁的化 合物最终基本上都以铁的氧化物形态,进入赤泥。
12
因此,铝土矿的溶出过程可分为下列几个步骤: ①、经循环母液润湿矿粒表面。 ②、OH ̄与氧化铝水合物反应生成AlO(OH) ̄。 ③、形成AlO(OH) ̄的扩散层。 ④、AlO(OH) ̄从扩散层扩散出来,OH ̄从溶液中扩散到固 相接触界面上。 对于铝土矿来说第二个步骤(化学反应和第四个步骤(扩散) 在一定条件下起主导作用,在高压和高温的条件下扩散过程 决定着溶出反应速度。 2-2-3影响溶出过程的主要因素 1、铝土矿的矿物组成及结构: 铝土矿按其矿物组成可分为三水铝石、一水软铝石及一水硬 铝石,由于其矿物组成、结晶结构不同,因而溶出难易及对 溶出条件要求各异。溶出过程的困难程度,依三水铝石→一 水软铝石→一水硬铝石顺序递增。
2
第一节概述 1、预脱硅及高压溶出简介 高压溶出选用国内处理一水硬铝石铝土矿比较 成熟的单管预热器及压煮器间接加热工艺流程。此 方案最早于1992年底在山西铝厂建成投产第一系列, 后来又于1994年建成投产了第二系列。在此基础上 我国又相继建成了平果铝厂和贵州铝厂的四个系列 高压溶出。
单管预热器及压煮器间接加热工艺方案在处理 一水硬铝石铝土矿时表现出良好的技术指标和经济 效益,其特点主要表现在: ① 溶出温度高,可达260-270℃,山西铝厂、平果 铝厂和贵州铝厂的高压溶出温度都在260℃以上。 ② 十一级自蒸发,蒸汽间接加热。从进料温度
4
⑦预脱硅槽采用阶梯配置,每相邻两台预脱硅槽间高 度相差600mm,以便铝矿浆在进行预脱硅时能按顺序 逐台自流,这样就减少了采用泵输送而消耗的电能。 第二节 工艺原理 2-1 预脱硅 高压溶出所处理的矿石是一水硬铝石型铝土矿铝矿, 矿石中SiO2主要以高岭石(Al2O3.2SiO2.2H20)形态 存在,其余以石英(SiO2)形态存在。 铝土矿中的SiO2如果在热交换器中分解,将会造 成大量结疤,附着在热交换器管壁上,大大降低了管 束的传热系数,降低了热交换效率;因结疤的积累增 大了设备的清理量,使清理周期缩短。在分解阶段还 会与氢氧化铝一起分解,影响氧化铝的质量。因而, 必须在进溶出系统之前将SiO2分解,使之提前生成铝 硅酸钠。
η理 =(A-S)/A*100%
式中: A—铝土矿中Al2O3的含量 % S—铝土矿中SiO2的含量 % 上式计算出的溶出率称为理论溶出率。在实际的溶出过程中 SiO2并不能完全反应,另外反应后的SiO2也会有一部分停留 在溶液,并不生成铝硅酸钠,即赤泥中的SiO2量少于铝土矿 中的SiO2量,这样也会造成实际溶出率大于理论溶出率。还
13
三水铝石在接近常压、温度140℃~150℃、循环母液较低的 情况下即可溶出,并能达到工业溶出的速度。而一水软铝石 型铝土矿则较难溶出,溶出温度160℃左右,苛性碱浓度要 求比三水铝石高。一水硬铝石最难溶出,温度要求在200℃ 以上,在高温、高压、高碱浓度时才能较好地溶出。 另外,铝土矿中的杂质含量(如TiO2、Fe2O3、SiO2等)越 多、越分散,氧化铝水合物被其包裹的程度越大,与碱溶液 接触越少,溶出越困难。 2、溶出温度: 温度是影响溶出过程中最重要的影响因素。 提高溶出温度,使溶出速度加快,溶液的粘度下降,有助于 矿石和碱液表面接触,从而提高氧化铝的溶出率。提高溶出 温度由于溶出速度快,可以缩短溶出时间。 随着温度的提高,Al2O3在碱溶液中的溶解度显著增加,溶 出液Rp值升高,有利于分解率的提高,从而可以提高碱液的 循环效率。提高溶出温度后,用浓度较低的循环母液亦可获
预脱硅及高压溶出生产 工艺技术
1
第一节概述 1、 预脱硅及高压溶出简介 第二节 工艺原理 2-1 预脱硅 2-2 高压溶出及矿浆稀释 第三节 主要设备工作原理及作用 3-1 预脱硅主要设备 3-2 高压溶出主要设备 3-3 辅助主要设备 第四节 工艺流程描述 4-1 预脱硅 4-2 高压溶出 第五节 主要工艺条件和技术参数
11
2-2-2高压溶出原理 1、溶出反应: 脱硅后在隔膜泵进口与补充循环母液混合后的调整矿浆进入 溶出机组后主要发生以下反应: Al2O3.H2O+2NaOH+aq→2NaAl(OH)4+aq 反应产物NaAl(OH)4在一定的苛性碱浓度和温度下都可以在 苛性碱溶液中稳定存在,形成铝酸钠溶液,经过这一反应就 可将铝土矿中大部分的Al2O3提取出来,进入铝酸钠溶液。 2、溶出速度: 铝土矿的拜耳法溶出属于多相反应,反应过程发生于两相(矿 物和碱液)界面上。两相界面上的OH ̄不断反应而逐渐消耗, 靠近表面溶液的OH ̄浓度显著降低;同时这一层中反应产物 AlO(OH) ̄的浓度接近于饱和,形成扩散层。因而新的OH ̄ 必须不断地通过扩散层的固相表面移动,与氧化铝水合物反 应;而反应产物AlO(OH) ̄则不断的通过扩散层向外移动, 使反应继续进行下去。
由循环效率公式可以看出,在循环母液苛性碱浓度Nk一定时, 溶出液αk值降低,循环效率E下降;生产单位Al2O3所需循环 母液量增加;还会增加溶出后铝酸钠溶液的稳定性,不利于 分解过程的进行。因此工业实践中,往往尽可能获得较高αk 值的溶出液。 5、矿石细度: 铝土矿溶出过程是固相与液相多相反应过程,反应是在两相 界面上进行。溶出速度Vt与其两相接触面积F成正比。所以 矿石越细,其接触面积越大,溶出速度加快,溶出率提高。 但矿石磨得太细,不但增加磨矿费用,还将为赤泥分离带来 困难。因此,矿石磨矿细度必须根据生产工艺的要求确定。 6、搅拌强度: 搅拌可使矿粒表面的扩散层厚度δ减小,增加溶出物质的扩 散速度,使溶液成份趋于均匀,从而保证碱液与矿物之间的 充分接触,强化溶出过程。同时增加搅拌强度还可以避免矿 粒的沉积。
8
E=1.645*(αk 1-αk 2)/ (αk 1*αk 2)*NK(kg/m3) 式中: αk1—循环母液的αk值 αk2—溶出液的αk值
2-2-1-4 氧化铝的溶出率 铝土矿溶出过程中,由于溶出条件与矿石特性 等因素的影响矿石中的氧化铝并不能完全进入溶液。 实际反应后进入到铝酸钠溶液中的Al2O3与原料铝土 矿中的Al2O3总量之比,称为氧化铝的实际溶出率。
6
在添加石灰的情况下,Ca就可以取代方钠石中的Na从而 减少苛性碱的消耗量。 在预脱硅阶段主要发生以下两个反应: 1、高岭石的溶解: Al2O3.2SiO2.2H20(固)+6NaOH(液)→ 2NaAlO2(液) +2Na2SiO3(液)+5H2O 2、方钠石的分解: 2NaAlO2(液)+1.7 Na2SiO3(液)+(n+1.7)H2O→ Na2O.Al2O3.1.7SiO2. nH2O+3.4 NaOH 分解速度和溶液中最终的SiO2含量受以下因素影响: ①溶液中苛性碱(Na2Ok)浓度。苛性碱浓度越低分 解速度越快,溶液中最终的SiO2含量越低。 ②脱硅温度。温度越高分解速度越快,溶液中最终的 SiO2含量越低。 ③溶液中Al2O3浓度。Al2O3浓度越低分解速度越快, 溶液中最终的SiO2含量越低
14
得较好的溶出效果,从而减轻蒸发负担,节约蒸汽,降低能 耗。但是,当采用新蒸汽作为热源时,随着饱和蒸汽温度的 提高,压力急剧上升,使溶出设备的制作和操作都将增加难 以克服的困难。 3、循环母液的苛性碱浓度Na2Ok及αk值: 循环母液中的苛性碱浓度Na2Ok越高、αk越低,Al2O3溶解 度越大,未饱和程度即(C饱-C溶)值越大,溶出速度越快。 然而循环母液浓度太高,蒸水量则大,在加重蒸发负担的同 时,增加了新蒸汽的消耗。因此,在不同的生产工艺条件, 循环母液的浓度和αk值宜保持在一个适当的范围。 4、溶出后铝酸钠溶液αk值: 在一定条件下的溶出过程中,铝土矿中氧化铝达到理论溶出 率后,溶出液的αk的高低取决于配入的循环母液量的多少。 溶出液的最高αk值即是在一定溶出温度及碱浓度下的饱和αk 值。对单位重量的矿石配碱量越多,实际溶出液的αk值与平 衡αk值的数值差便越大,这样在溶出过程中,溶液始终保持 着较大的未饱和度,溶出速度加快。 15