焊料性质对焊接的影响
芯片虚焊不良产生的原因
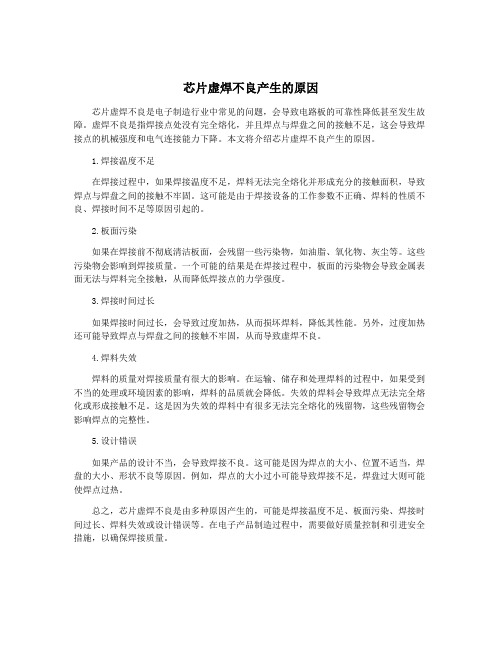
芯片虚焊不良产生的原因芯片虚焊不良是电子制造行业中常见的问题,会导致电路板的可靠性降低甚至发生故障。
虚焊不良是指焊接点处没有完全熔化,并且焊点与焊盘之间的接触不足,这会导致焊接点的机械强度和电气连接能力下降。
本文将介绍芯片虚焊不良产生的原因。
1.焊接温度不足在焊接过程中,如果焊接温度不足,焊料无法完全熔化并形成充分的接触面积,导致焊点与焊盘之间的接触不牢固。
这可能是由于焊接设备的工作参数不正确、焊料的性质不良、焊接时间不足等原因引起的。
2.板面污染如果在焊接前不彻底清洁板面,会残留一些污染物,如油脂、氧化物、灰尘等。
这些污染物会影响到焊接质量。
一个可能的结果是在焊接过程中,板面的污染物会导致金属表面无法与焊料完全接触,从而降低焊接点的力学强度。
3.焊接时间过长如果焊接时间过长,会导致过度加热,从而损坏焊料,降低其性能。
另外,过度加热还可能导致焊点与焊盘之间的接触不牢固,从而导致虚焊不良。
4.焊料失效焊料的质量对焊接质量有很大的影响。
在运输、储存和处理焊料的过程中,如果受到不当的处理或环境因素的影响,焊料的品质就会降低。
失效的焊料会导致焊点无法完全熔化或形成接触不足。
这是因为失效的焊料中有很多无法完全熔化的残留物,这些残留物会影响焊点的完整性。
5.设计错误如果产品的设计不当,会导致焊接不良。
这可能是因为焊点的大小、位置不适当,焊盘的大小、形状不良等原因。
例如,焊点的大小过小可能导致焊接不足,焊盘过大则可能使焊点过热。
总之,芯片虚焊不良是由多种原因产生的,可能是焊接温度不足、板面污染、焊接时间过长、焊料失效或设计错误等。
在电子产品制造过程中,需要做好质量控制和引进安全措施,以确保焊接质量。
电烙铁焊接原理

电烙铁焊接原理
电烙铁焊接是一种常见的电子元件焊接方式,它利用热量将焊料融化,从而将元件固定在电路板上。
电烙铁焊接原理涉及到热传导、热膨胀、焊料性质等多个方面的知识。
下面我们将逐一介绍电烙铁焊接的原理。
首先,电烙铁焊接的原理之一是热传导。
电烙铁通过加热铁头,将热量传导到焊接点和焊料上。
当电烙铁接触焊接点时,热量会迅速传导到焊料和焊接点附近的电路板上,从而使焊料融化并与焊接点接触,形成牢固的连接。
热传导是电烙铁焊接能够实现焊接的重要原理之一。
其次,热膨胀也是电烙铁焊接的原理之一。
当电烙铁加热时,铁头和周围材料会发生热膨胀。
这种热膨胀会使焊接点和焊料受到一定的压力,从而有助于焊料与焊接点形成良好的连接。
同时,热膨胀还可以帮助焊料在融化时填充焊接点和焊料之间的微小空隙,提高焊接的牢固性。
另外,焊料的性质也对电烙铁焊接起着重要作用。
不同类型的焊料具有不同的熔点和流动性,这直接影响到焊接的质量。
在电烙铁焊接中,选用合适的焊料可以确保焊接点得到充分润湿,形成均匀、牢固的焊接。
因此,了解焊料的性质对于掌握电烙铁焊接原理至关重要。
总的来说,电烙铁焊接原理涉及到热传导、热膨胀和焊料性质等多个方面的知识。
通过合理利用这些原理,可以实现高质量的焊接,确保电子元件在电路板上的稳固连接。
同时,深入理解电烙铁焊接原理也有助于我们在实际操作中更加准确、高效地进行焊接工作。
希望本文能够帮助大家更好地理解电烙铁焊接的原理,提高焊接技术水平,确保电子产品的质量和稳定性。
焊片的主要成分-概述说明以及解释

焊片的主要成分-概述说明以及解释1.引言1.1 概述焊片作为一种重要的材料,在工业生产和制造领域中具有广泛的应用。
它是由多种不同材料组成的复合材料,具有优异的导热性、导电性和可塑性等特点。
焊片的主要作用是将不同金属或其他材料连接在一起,形成稳定的接合点。
本文旨在探讨焊片的主要成分,了解其组成和结构,以及不同成分对焊接性能的影响。
通过对焊片的研究,我们可以更好地理解焊接技术的发展和应用。
在接下来的章节中,我们将对焊片的定义和分类进行介绍,包括常见的金属焊片、陶瓷焊片和复合焊片等。
然后,我们将重点关注焊片的主要成分,探讨各种材料在焊片中的使用情况和特性。
这些成分通常包括金属粉末、陶瓷粉末、有机胶粘剂等。
进一步地,我们还将介绍焊片的制备方法,包括粉末冶金法、化学法和物理法等。
这些制备方法具有不同的特点和适用范围,可以根据需要选择合适的方法。
最后,在结论部分,我们将总结焊片的主要成分对焊接性能的影响,并展望焊片在未来的应用前景。
随着科学技术的不断进步,我们相信焊片将在各个领域发挥更重要的作用。
通过本文的研究,我们可以更好地理解焊片的组成和制备方法,为焊接技术的应用提供有价值的参考。
同时,我们也可以进一步推动焊片的研究和发展,为工业制造和生产带来更多的创新和进步。
1.2 文章结构文章结构部分的内容可以包括以下几点:文章结构是为了让读者清晰地了解整篇文章的构架和内容安排。
本文主要分为引言、正文和结论三个部分。
在引言部分,需要对整个文章的背景和重要性进行概述,说明为何研究焊片的主要成分是有必要的。
同时,介绍文章的结构以及各部分的内容,让读者能够预览到整篇文章的框架。
正文部分是文章的核心内容,主要围绕焊片的主要成分展开。
在2.1部分,可以对焊片的定义和分类进行详细介绍,解释焊片在焊接工艺中的作用和种类。
在2.2部分,重点讨论焊片的主要成分,包括金属元素、非金属元素以及其他添加剂。
可以探讨不同成分对焊接性能的影响,并举例说明具体的应用场景。
锡膏成分对焊接强度的影响

锡膏成分对焊接强度的影响全文共四篇示例,供读者参考第一篇示例:锡膏是一种常用的焊接材料,通常由锡和铅组成。
在焊接过程中,锡膏会融化并涂抹在焊接的部件表面,以实现两个部件的连接。
锡膏的成分对焊接强度也有一定影响。
锡和铅的比例是影响焊接强度的重要因素之一。
一般来说,锡含量高的锡膏具有更好的焊接性能,因为锡具有较好的润湿性,能够更好地覆盖焊接表面并形成均匀的焊点。
而铅的作用是提高焊接的可塑性和延展性,使焊点更加韧性。
在选择锡膏时,需要根据具体的焊接要求来确定锡和铅的比例,以获得最佳的焊接强度。
锡膏的熔点也会影响焊接强度。
一般来说,熔点较低的锡膏具有更好的焊接性能,因为它们能够在较低的温度下融化并涂抹在焊接表面,减少焊接部件的热应力,从而减少焊接接头的裂纹和变形。
而熔点较高的锡膏则需要更高的焊接温度,容易导致焊接部件的损坏,降低焊接强度。
锡膏中的添加剂也会对焊接强度产生影响。
焊接通常会添加一些助焊剂来提高焊接质量。
助焊剂能够在焊接过程中清除氧化物和杂质,保持焊点的纯净度,提高焊接的可靠性和耐腐蚀性。
一些特殊的添加剂还可以改善锡膏的润湿性和减少焊接过程中的缺陷,提高焊接强度。
锡膏的成分对焊接强度有着重要的影响。
在选择锡膏时,需要综合考虑锡和铅的比例、熔点以及添加剂的影响,以获得最佳的焊接效果。
焊接过程中也需要注意控制焊接温度和时间,以避免焊接缺陷的产生,提高焊接接头的强度和稳定性。
希望以上内容能够对大家了解锡膏成分对焊接强度的影响有所帮助。
【2000字】第二篇示例:锡膏是焊接过程中常用的材料,它由锡和一种或多种助焊剂混合而成。
焊接是一种重要的连接工艺,通过在金属材料表面熔融焊接材料,形成牢固的连接。
在焊接过程中,焊接强度是一个关键指标,直接影响焊接件的质量和可靠性。
而锡膏的成分对焊接强度有着重要的影响。
锡膏的成分主要包括锡和助焊剂两部分。
锡膏中的锡是主要的焊接材料,它具有一定的流动性和润湿性,能够在焊接表面形成均匀的涂层,实现良好的焊接效果。
鋓料性质对焊接的影响

銲料性質對焊接的影響1.前言目前各種形式的合金焊料,其最權威的國際規範為J-STD-006。
此文獻之最新版本為1996.6的Amend ment 1,由於資料很新,故早已取代了先前甚為知名的美國聯邦規範QQ-S-571。
IPC還有一份重要的焊接手冊IPC-HDBK-001其中之4.1,曾定義“熔點”在430℃以下為“軟焊”(Soldering),也就是錫焊。
另熔點在430℃以上稱為“硬焊”(Brazing),係含銀之高溫高強度焊接。
早期歐美業界,亦稱熔點600℉(315℃)以下者為軟質銲錫,800℉(427℃)以上者為硬質焊錫。
原文Solder定義為錫鉛含金之焊料,故中譯從金旁為“銲錫”,而利用高熱能進行熔焊之Soldering(註意此一特定之單字,並非只加ing而已),則另從火旁用字眼的“焊接”,兩者涵義並不完全相同。
2.共熔(晶)銲錫銲錫焊料(Solder)主要成分為錫與鉛,其他少量成分尚有銀、鉍、銦等,各有不同的熔點(M.P.),但其主要二元合金中以Sn63/Pb37之183℃為最低,由於其液化熔點(Liquidus Point)與固化熔點(So lidus Point)的往返過程中,均無過渡期間的漿態(pasty)出現,也就是已將較高的“液化熔點”與較低的“固化熔點”兩者合而為一,故稱為“共熔合金”。
且因其粗大結晶內同時出現錫鉛兩種元素,於是又稱為“共晶合金”。
此種無雜質合金外表很光亮之“共熔組成”(Eutectic Composition)或“共熔銲錫”(Eutectic Solder),其固化後之組織非常均勻,幾無粒子出現。
其合金比例之不同將影響到熔點變化,該變化之“平衡相圖(Phase Diagram)”,圖請參考第12期TPCA會刊。
另一種組成接近共熔點的Sn60/Pb40合金,則在電子業界中用途更廣,主要原因是Sn較貴,在焊錫性(Solderability)與銲點強度(Joint Strength)幾無差異下,減少了3﹪的支出,自然有利於成本的降低。
锡膏成分对焊接强度的影响
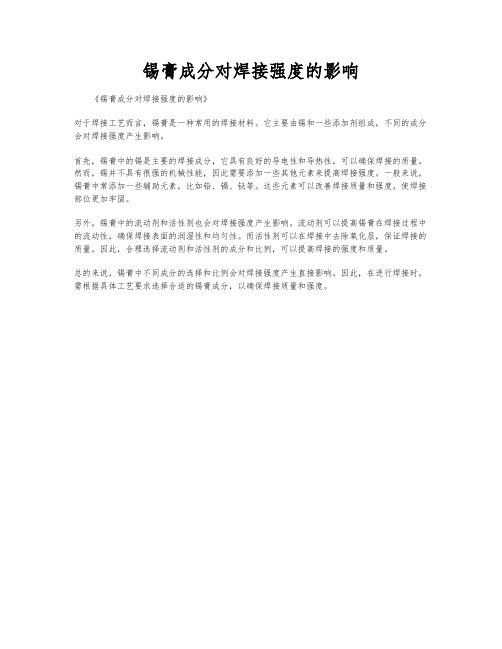
锡膏成分对焊接强度的影响
《锡膏成分对焊接强度的影响》
对于焊接工艺而言,锡膏是一种常用的焊接材料。
它主要由锡和一些添加剂组成,不同的成分会对焊接强度产生影响。
首先,锡膏中的锡是主要的焊接成分,它具有良好的导电性和导热性,可以确保焊接的质量。
然而,锡并不具有很强的机械性能,因此需要添加一些其他元素来提高焊接强度。
一般来说,锡膏中常添加一些辅助元素,比如铅、镉、铋等。
这些元素可以改善焊接质量和强度,使焊接部位更加牢固。
另外,锡膏中的流动剂和活性剂也会对焊接强度产生影响。
流动剂可以提高锡膏在焊接过程中的流动性,确保焊接表面的润湿性和均匀性。
而活性剂可以在焊接中去除氧化层,保证焊接的质量。
因此,合理选择流动剂和活性剂的成分和比例,可以提高焊接的强度和质量。
总的来说,锡膏中不同成分的选择和比例会对焊接强度产生直接影响。
因此,在进行焊接时,需根据具体工艺要求选择合适的锡膏成分,以确保焊接质量和强度。
3733-10焊材材料成分

3733-10焊材材料成分
焊材是一种用于焊接的材料,它在焊接过程中起到连接和填充作用。
3733-10焊材是一种常用的焊接材料,其成分对焊接质量和性能具有重要影响。
3733-10焊材的主要成分包括铜和镍。
铜是一种优良的导电和导热材料,它能够提供良好的电流和热量传导性能,有助于焊接过程的稳定进行。
镍是一种具有高熔点和优良耐腐蚀性能的金属,能够提供焊接接头的耐热和耐腐蚀性能。
除了铜和镍外,3733-10焊材还含有少量的其他金属元素,如锌、锡等。
这些元素的添加可以改善焊接接头的力学性能和抗腐蚀性能。
锌的添加可以增加焊接接头的强度和硬度,锡的添加可以提高焊接接头的耐腐蚀性能。
3733-10焊材的成分经过精心调配,使其具有适合不同焊接工艺和材料的特性。
它可以用于焊接不同种类的金属材料,如铜、铁、不锈钢等。
在焊接过程中,3733-10焊材能够提供稳定的电弧和熔化池,使焊接接头具有良好的焊缝形态和力学性能。
3733-10焊材是一种具有铜、镍等金属元素的焊接材料,它的成分经过精心调配,能够提供良好的焊接性能和接头品质。
它在焊接工艺中起到重要的作用,是焊接过程中不可或缺的材料之一。
无论是焊接工程师还是焊接爱好者,都应该对3733-10焊材的成分有所了
解,以确保焊接质量和性能的达到要求。
共晶锡锌合金焊料的性能及焊接特性

共晶锡锌合金焊料的性能及焊接特性J.Villain,U.Corradi,Chr.Weippert奥格斯堡应用技术大学德国奥格斯堡86161,Baumgartnerstr.16Villain@lrz.Ui3.i一=uenchen.de摘要:通过共晶锡锌合金的张力与蠕变性能测试,我们能够得出这种焊料与锡银合金及SAC合金(SAC--锡,银,铜合金)在机械性能方面的不同。
试验显示,锡锌焊料的强度大于含铅焊料及其他在研究范围之内的无铅焊料-其抗蠕变性也优于锡铅合金。
微1纳米硬度测量结果解释了共晶锡锌台金具备高强度的原因。
在回流焊特别是波峰焊过程中.高温是获得可湿性及高可靠性焊点的必要因素。
焊接过程结束后,锡锌焊料合金会表现出消光加工的特性,焊点也将具备较高的强度,但温度循环后其强度减少幅度会大于其他测试合金,不过其临界强度总是大干临界值。
抗腐蚀性测试取得了较为满意的结果。
根据金相剖面图可以看出这种台金与其他无铅焊料合金在结构上的不同。
有时铝层未完全溶解于焊料。
如果可靠性测试取得较好的效果.则锡锌焊料合金可被用于电子学领域。
关键词:无铅焊料合金,共晶锡锌焊料,可靠性,回流焊接,波峰焊接,纳米硬度介绍目前人们已开发出了数种无铅焊料,这些材料可在不同的产品及工作温度条件下取代含铅焊料。
研究人员己对锡银、锡银铜以及锡锌合金及其可靠性进行了深入的研究。
研究结果显示.无铅焊料在通常情况下总是具有较高的熔点和中等可湿性。
添加其他元素(如金和镍)会使无铅焊料的溶解性优于含铅焊料。
我们将锡锌台金研究取得的所有结果与SNAG3.5、Sn63Pb37以及SnA93.5Cu0.7Bi2焊料合金进行了对比。
锡锌合金焊料表1列出了某些锡锌二元及三元焊料合金【1】,图1是锡锌合金相团2】。
上述大多数合金都与其共晶合金结构相近。
焊料中的铋能够降低台金熔点,但与铅混合后(如为电子元件镀敷金属)将形成低熔点共晶结构,从而大幅度削弱焊点可靠性。
有铅焊料和无铅焊料在多个方面存在显著的差异

有铅焊料和无铅焊料在多个方面存在显著的差异:
1. 成分与定义:
a)有铅焊料,也被称为SnPb焊料,主要由锡(Sn)和铅(Pb)组成的金属合金。
它是电子、电工、机械等行业常见的焊接材料,以其低成本、易用性和良好的焊接效果而得到广泛应用。
b)无铅焊料则是由多种低熔点合金组成,其主要成分通常为锡和铜,并可能辅以少量钴、镍等金属元素。
这种焊材主要用于取代传统的含铅焊料,以实现电子元器件的拼接和连接,并且逐渐在电子制造业中占据主流地位。
2. 熔点与工艺要求:
a)有铅焊料的熔点通常较低,这使得焊接过程相对容易控制,且具有良好的润湿性。
b)无铅焊料的熔点温度相对较高,因此在进行无铅焊接时,需要更高的焊接温度,对
焊接设备和工艺的要求也相应提高。
此外,无铅焊料在焊接过程中可能产生更多的氧化物和残渣,因此,需要更加注意焊接环境的控制和焊接前的预处理工作。
3. 环保与安全性:
a)与有铅焊料相比,无铅焊料具有更好的环保性和安全性,更符合绿色生产和环保理念。
b) 使用有铅焊料时,应注意安全,特别是在焊接过程中产生的烟尘和有害气体可能对人体有害,应在通风良好的地方进行操作,避免直接吸入焊锡烟。
4. 成本:
一般来说,无铅焊接相对于有铅焊接具有更高的成本,这主要与其材料组成和工艺要求有关。
总结来说,有铅焊料和无铅焊料各有其特点和适用场景。
在追求环保和可持续性的今天,无铅焊料的应用越来越广泛,但在某些特定情况下,有铅焊料仍因其成本低廉和良好的焊接效果而得到使用。
在选择使用哪种焊料时,需要根据具体的工艺要求、成本预算和环保标准等因素进行综合考虑。
锡银铜合金焊料

锡银铜合金焊料
锡银铜合金焊料是一种常用于电子器件焊接的合金材料,由锡、银和铜组成。
它具有优异的导电性、导热性和耐腐蚀性能,能够提供可靠的焊接连接。
锡银铜合金焊料的优点包括:
1. 良好的导电性和导热性:锡银铜合金焊料中的银和铜元素可以提高焊料的导电性和导热性,使得焊接接头具有更好的电气性能。
2. 优异的耐腐蚀性能:锡银铜合金焊料中的锡和铜元素可以形成一种稳定的氧化膜,保护焊接接头不受腐蚀的影响。
3. 容易加工和成型:锡银铜合金焊料具有良好的可塑性和流动性,可以通过各种工艺方法进行加工和成型。
4. 低成本:相对于其他类型的焊料,锡银铜合金焊料的成本较低,因此在大规模生产中得到了广泛的应用。
锡银铜合金焊料的缺点包括:
1. 强度较低:由于锡银铜合金焊料中含有较多的有色金属元素,
其强度相对较低,容易发生变形或断裂。
2. 对某些材料的焊接适应性较差:锡银铜合金焊料对某些材料的焊接适应性较差,需要进行特殊处理才能获得良好的焊接效果。
铝焊料熔点
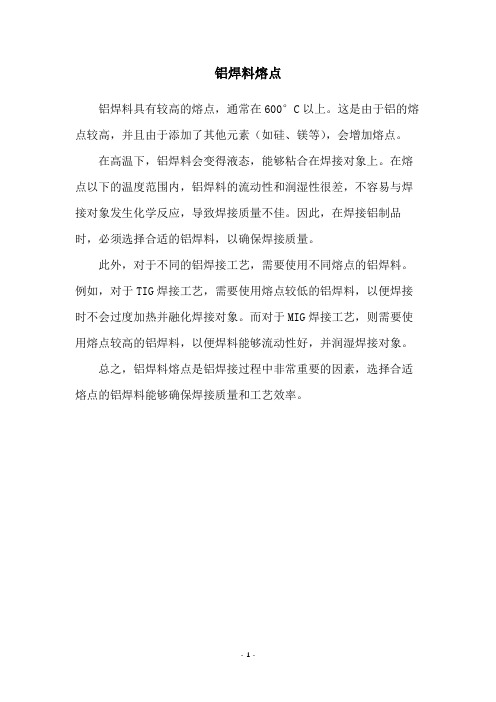
铝焊料熔点
铝焊料具有较高的熔点,通常在600°C以上。
这是由于铝的熔点较高,并且由于添加了其他元素(如硅、镁等),会增加熔点。
在高温下,铝焊料会变得液态,能够粘合在焊接对象上。
在熔点以下的温度范围内,铝焊料的流动性和润湿性很差,不容易与焊接对象发生化学反应,导致焊接质量不佳。
因此,在焊接铝制品时,必须选择合适的铝焊料,以确保焊接质量。
此外,对于不同的铝焊接工艺,需要使用不同熔点的铝焊料。
例如,对于TIG焊接工艺,需要使用熔点较低的铝焊料,以便焊接时不会过度加热并融化焊接对象。
而对于MIG焊接工艺,则需要使用熔点较高的铝焊料,以便焊料能够流动性好,并润湿焊接对象。
总之,铝焊料熔点是铝焊接过程中非常重要的因素,选择合适熔点的铝焊料能够确保焊接质量和工艺效率。
- 1 -。
锡膏成分对焊接强度的影响

锡膏成分对焊接强度的影响全文共四篇示例,供读者参考第一篇示例:锡膏是电子焊接中常用的一种焊料,其成分对于焊接强度具有重要影响。
焊接强度是评价焊接质量的重要指标之一,它直接影响着焊接件的稳固性和可靠性。
研究锡膏成分对焊接强度的影响,对于提高焊接质量具有重要意义。
一、锡膏的成分介绍锡膏是由导电颗粒、树脂和添加剂等组成的混合物,其中导电颗粒是决定焊接性能的主要组分。
常见的导电颗粒有铅、锡、铅锡合金等,树脂有树脂酸和乙基纤维素等。
锡膏的成分比例会影响其的流动性、附着性和机械性能。
二、锡膏成分对焊接强度的影响1. 导电颗粒导电颗粒是锡膏的主要成分之一,其种类和比例对焊接强度起着至关重要的作用。
一般来说,铅锡合金的焊接强度较高,但由于铅的毒性和环保问题,现在逐渐被锡替代。
锡的焊接强度虽然稍逊于铅锡合金,但在环保方面表现更优。
锡膏中导电颗粒的粒度也影响着焊接强度,粒度较细的导电颗粒有助于提高焊接性能。
2. 树脂树脂是锡膏中的另一个重要成分,它起着粘结和固化导电颗粒的作用。
树脂种类的选择和比例的调整会影响焊接件的表面张力和润湿性,进而影响焊接强度。
一般来说,树脂酸含量越高,焊接强度越高,但在高温下易发生气泡和焊接不良现象。
3. 添加剂锡膏中的添加剂可以改善焊接性能和机械性能,同时也会影响焊接强度。
常见的添加剂有活化助焊剂、增强剂等。
活化助焊剂可以提高焊接时的润湿性和活性,增强剂可以改善焊接接触面的机械连接强度。
三、锡膏成分优化的建议1. 在选用导电颗粒时,应根据实际焊接需求和环保要求选择合适的铅锡合金或锡材料,同时注意导电颗粒的粒度和形状。
2. 在选用树脂时,应根据焊接件的材料和表面状态选择合适的树脂种类和含量,以保证焊接件的润湿性和焊接强度。
3. 在选择添加剂时,应根据实际焊接条件选择合适的活化助焊剂和增强剂,以提高焊接质量和焊接强度。
通过以上分析,我们可以看出锡膏的成分对焊接强度具有重要影响。
针对不同的焊接需求和环境条件,我们可以根据实际情况对锡膏成分进行优化,以提高焊接质量和焊接强度。
焊料 相对介电常数-概述说明以及解释

焊料相对介电常数-概述说明以及解释1.引言1.1 概述焊料是一种广泛应用于焊接工艺中的材料,用于将金属或非金属材料连接在一起。
焊料的选择和性能对于焊接质量和连接强度具有重要影响。
在焊接过程中,焊料不仅起到连接材料的作用,还可以填充连接部位的空隙,并提供稳定的连接。
因此,焊料的性能和特性对于焊接过程的效果至关重要。
相对介电常数是焊料一种重要的物理特性,它用来描述焊料材料对外电场的响应能力。
相对介电常数越高,说明焊料对电场的响应能力越强,这可能会对焊接过程产生影响。
在本文中,我们将首先介绍焊料的定义和特性,包括它的成分和熔点等方面。
然后,我们将重点讨论焊料的相对介电常数的影响因素。
这些影响因素可以包括焊料的化学成分、形状和结构等方面。
通过对这些影响因素的深入研究,我们可以更好地理解焊料的相对介电常数与其性能之间的关系。
最后,我们将总结焊料相对介电常数的重要性,并展望未来的研究方向。
通过深入研究焊料的相对介电常数及其影响因素,我们可以改进焊接过程,提高焊接质量和连接强度。
同时,我们也可以探索新的焊料材料和技术,以满足不断变化的焊接需求。
总之,焊料的相对介电常数是影响焊接过程和连接强度的重要因素之一。
通过深入研究焊料的相对介电常数及其影响因素,我们可以为焊接工艺的改进和发展提供有力支持。
1.2文章结构文章结构是文章的骨架,它帮助读者理解文章的整体框架和逻辑顺序。
在本篇长文中,文章结构的安排如下:1. 引言1.1 概述:引言部分将概述文章的主题和焦点,介绍焊料相对介电常数的相关背景和意义。
这一部分可以介绍焊接技术在现代工业中的重要性,以及相对介电常数在焊接过程中的作用。
1.2 文章结构:本部分将介绍整篇文章的结构,概括性地列举本文各个章节的内容和顺序。
这样读者在阅读文章之前可以对整篇文章有一个整体的把握。
1.3 目的:这一部分需要明确指出撰写此篇文章的目的和意义,可能包括为了推进焊料相对介电常数的研究、解决实际问题或者促进学术交流等。
SMT焊接上锡不良分析

SMT焊接上锡不良分析SMT(Surface Mount Technology,表面贴装技术)焊接是一种常见的电子组装技术,它通过将电子元器件直接焊接在PCB(PrintedCircuit Board,印制电路板)的表面,从而实现更高的装配密度和更好的电气性能。
然而,由于焊接过程中的各种因素,有时会出现上锡不良的情况,影响产品的质量。
本文将针对SMT焊接上锡不良进行分析,分析其可能的原因,并提出相应的解决方案。
首先,上锡不良可能是由于焊接温度不当引起的。
焊接过程中,焊料需要达到足够的熔点才能进行焊接。
如果焊接温度过低,焊料无法完全熔化,导致焊点与PCB之间无法充分接触,从而造成上锡不良。
另一方面,如果焊接温度过高,焊料可能会过度熔化,融化PCB上的电路线路,导致短路或焊点与线路之间的断开。
因此,合理控制焊接温度是解决SMT焊接上锡不良的关键。
其次,上锡不良可能是由于焊接时间不足引起的。
焊接过程中,焊料需要适当的时间才能完全熔化,并形成牢固的连接。
如果焊接时间过短,焊料无法完全融化,焊点与PCB之间的接触不牢固,容易出现冷焊现象,导致上锡不良。
因此,合理控制焊接时间,确保焊料充分熔化是解决上锡不良的重要措施之一第三,上锡不良可能是由于焊接质量不良引起的。
焊接质量主要包括焊料的品质以及焊接工艺的控制。
焊料的成分和纯度会直接影响焊接质量,低质量的焊料容易引起上锡不良。
此外,焊接工艺的控制也十分重要。
例如,焊接时需要控制好焊料的质量,确保其不受空气中的氧气和水蒸气的影响;焊接过程中需要避免PCB或元器件受到机械冲击,以免造成焊接不牢;还需要定期检测焊接设备的状态,保证其正常运行。
最后,上锡不良可能是由于焊接材料不匹配引起的。
焊接材料包括焊料、PCB和元器件等。
如果焊料与PCB或元器件的材料不匹配,会导致焊接困难,从而出现上锡不良。
因此,在进行SMT焊接前,需要仔细选用合适的焊料、PCB和元器件,确保它们的材料相互匹配。
焊料、焊剂和焊接的辅助材料.

第 5 页
4、清洗剂
在完成焊接操作后,要对焊点进行清洗,避免焊 点周围的杂质腐蚀焊点。 常用的清洗剂有:
无水乙醇(无水酒精)
航空洗涤汽油
三氯三氟乙耐高温的涂料,其作用是保护印制电 路板上不需要焊接的部位。 阻焊剂的种类 热固化型阻焊剂 紫外线光固化型阻焊剂(光敏阻焊剂) 电子辐射固化型阻焊剂
常用的助焊剂有:
无机焊剂; 有机助焊剂; 松香类焊剂:电子产品的焊接中常用。
第 4 页
3、常用的锡铅合金焊料(焊锡)
锡铅合金焊料的有多种形状和分类。其形状有粉末
状、带状、球状、块状和管状等几种。
手工焊接中最常见的是管状松香芯焊锡丝。这种焊
锡丝将焊锡制成管状,其轴向芯内是优质松香添加一定
的活化剂组成的。
第 1 页
第 2 页
1、焊料
焊料是一种熔点低于被焊金属,在被焊金属不熔化的 条件下,能润湿被焊金属表面,并在接触面处形成合金层 的物质。 电子产品生产中,最常用的焊料称为锡铅合金焊料 (又称焊锡),它具有熔点低、机械强度高、抗腐蚀性能 好的特点。
第 3 页
2、焊剂(助焊剂)
焊剂是进行锡铅焊接的辅助材料。 焊剂的作用:去除被焊金属表面的氧化物,防止焊接 时被焊金属和焊料再次出现氧化,并降低焊料表面的张 力,有助于焊接。
锡膏中焊料合金的作用
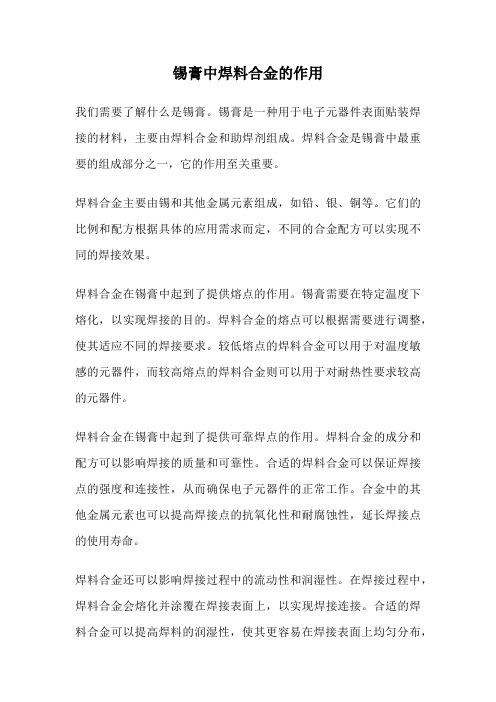
锡膏中焊料合金的作用我们需要了解什么是锡膏。
锡膏是一种用于电子元器件表面贴装焊接的材料,主要由焊料合金和助焊剂组成。
焊料合金是锡膏中最重要的组成部分之一,它的作用至关重要。
焊料合金主要由锡和其他金属元素组成,如铅、银、铜等。
它们的比例和配方根据具体的应用需求而定,不同的合金配方可以实现不同的焊接效果。
焊料合金在锡膏中起到了提供熔点的作用。
锡膏需要在特定温度下熔化,以实现焊接的目的。
焊料合金的熔点可以根据需要进行调整,使其适应不同的焊接要求。
较低熔点的焊料合金可以用于对温度敏感的元器件,而较高熔点的焊料合金则可以用于对耐热性要求较高的元器件。
焊料合金在锡膏中起到了提供可靠焊点的作用。
焊料合金的成分和配方可以影响焊接的质量和可靠性。
合适的焊料合金可以保证焊接点的强度和连接性,从而确保电子元器件的正常工作。
合金中的其他金属元素也可以提高焊接点的抗氧化性和耐腐蚀性,延长焊接点的使用寿命。
焊料合金还可以影响焊接过程中的流动性和润湿性。
在焊接过程中,焊料合金会熔化并涂覆在焊接表面上,以实现焊接连接。
合适的焊料合金可以提高焊料的润湿性,使其更容易在焊接表面上均匀分布,从而实现良好的焊接效果。
合金中的其他元素也可以调整焊料的流动性,使其更易于填充焊接间隙和微小的焊接孔隙。
焊料合金还可以影响焊接的电学性能。
焊料合金的电导率和电阻率可以影响焊接连接的电流传输能力和电阻特性。
合适的焊料合金可以确保焊接点的电导性和稳定性,从而保证电子元器件的正常工作。
总结起来,焊料合金在锡膏中起到了提供熔点、提供可靠焊点、调整流动性和润湿性以及影响电学性能的重要作用。
合适的焊料合金配方可以实现高质量的焊接连接,确保电子元器件的可靠性和性能。
因此,焊料合金在锡膏中的作用不可忽视,对于电子制造行业具有重要意义。
焊料片焊接空洞
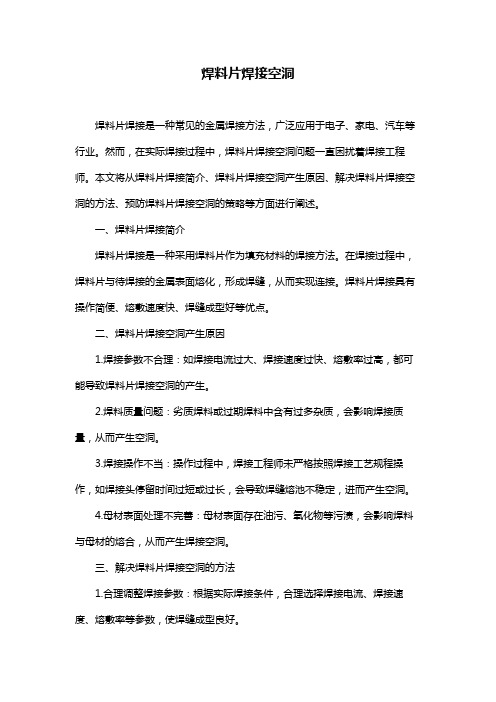
焊料片焊接空洞焊料片焊接是一种常见的金属焊接方法,广泛应用于电子、家电、汽车等行业。
然而,在实际焊接过程中,焊料片焊接空洞问题一直困扰着焊接工程师。
本文将从焊料片焊接简介、焊料片焊接空洞产生原因、解决焊料片焊接空洞的方法、预防焊料片焊接空洞的策略等方面进行阐述。
一、焊料片焊接简介焊料片焊接是一种采用焊料片作为填充材料的焊接方法。
在焊接过程中,焊料片与待焊接的金属表面熔化,形成焊缝,从而实现连接。
焊料片焊接具有操作简便、熔敷速度快、焊缝成型好等优点。
二、焊料片焊接空洞产生原因1.焊接参数不合理:如焊接电流过大、焊接速度过快、熔敷率过高,都可能导致焊料片焊接空洞的产生。
2.焊料质量问题:劣质焊料或过期焊料中含有过多杂质,会影响焊接质量,从而产生空洞。
3.焊接操作不当:操作过程中,焊接工程师未严格按照焊接工艺规程操作,如焊接头停留时间过短或过长,会导致焊缝熔池不稳定,进而产生空洞。
4.母材表面处理不完善:母材表面存在油污、氧化物等污渍,会影响焊料与母材的熔合,从而产生焊接空洞。
三、解决焊料片焊接空洞的方法1.合理调整焊接参数:根据实际焊接条件,合理选择焊接电流、焊接速度、熔敷率等参数,使焊缝成型良好。
2.选用优质焊料:选择质量过硬的焊料,避免使用过期、劣质焊料。
3.提高焊接操作技能:加强焊接工程师的操作技能培训,使其熟练掌握焊接工艺规程。
4.完善母材表面处理:对待焊接的母材表面进行严格的清洗、打磨等处理,去除油污、氧化物等污渍。
四、预防焊料片焊接空洞的策略1.加强焊接工艺研究,不断优化焊接参数,提高焊接质量。
2.注重焊料的储存和保管,确保使用合格焊料。
3.提高焊接操作人员的技能水平,确保焊接过程中能正确执行焊接工艺。
4.加强现场管理,严格执行焊接质量检验标准,及时发现和解决焊接质量问题。
五、总结焊料片焊接空洞问题是焊接过程中常见的质量问题,通过合理调整焊接参数、选用优质焊料、提高焊接操作技能、完善母材表面处理等措施,可以有效解决焊料片焊接空洞问题。
纳米银焊料比热容
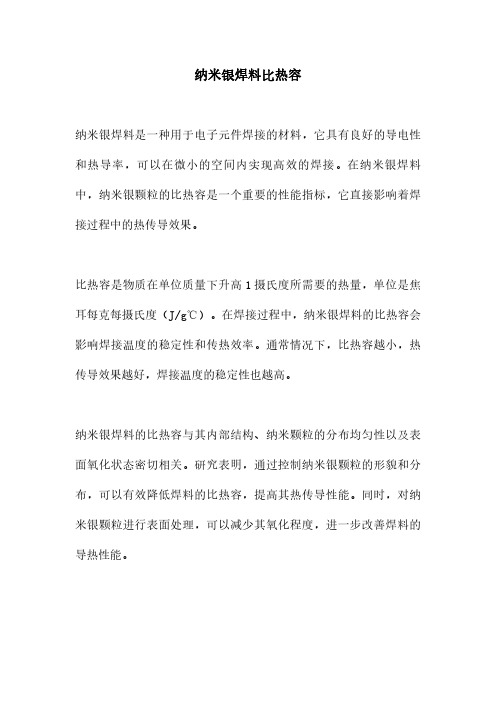
纳米银焊料比热容
纳米银焊料是一种用于电子元件焊接的材料,它具有良好的导电性和热导率,可以在微小的空间内实现高效的焊接。
在纳米银焊料中,纳米银颗粒的比热容是一个重要的性能指标,它直接影响着焊接过程中的热传导效果。
比热容是物质在单位质量下升高1摄氏度所需要的热量,单位是焦耳每克每摄氏度(J/g℃)。
在焊接过程中,纳米银焊料的比热容会影响焊接温度的稳定性和传热效率。
通常情况下,比热容越小,热传导效果越好,焊接温度的稳定性也越高。
纳米银焊料的比热容与其内部结构、纳米颗粒的分布均匀性以及表面氧化状态密切相关。
研究表明,通过控制纳米银颗粒的形貌和分布,可以有效降低焊料的比热容,提高其热传导性能。
同时,对纳米银颗粒进行表面处理,可以减少其氧化程度,进一步改善焊料的导热性能。
在实际应用中,选择具有低比热容的纳米银焊料进行微电子元件的焊接可以大大提高焊接质量和效率。
而且,随着纳米技术的不断发展,纳米银焊料的热导率和比热容还有望得到进一步的提升,从而满足日益复杂的微电子元件对焊接材料性能的需求。
总之,纳米银焊料的比热容是影响其热传导性能的重要因素,通过优化纳米颗粒的结构和表面状态,可以有效降低焊料的比热容,提高其热传导效率,从而实现高效、稳定的微电子元件焊接。
随着纳米技术的不断进步,相信纳米银焊料在电子焊接领域会有更广阔的应用前景。
高温焊料特点分析报告
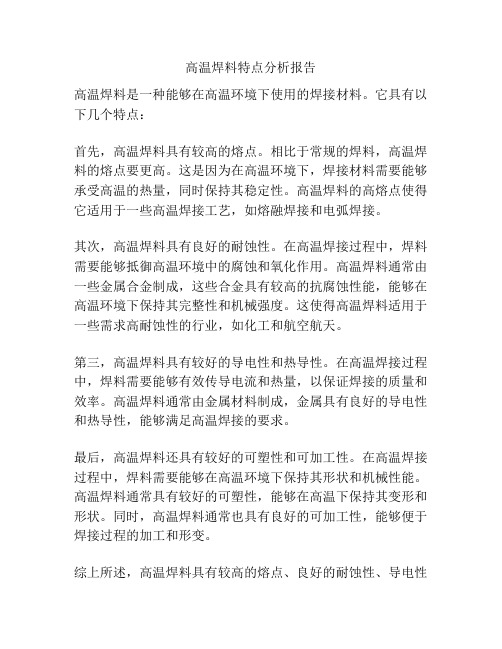
高温焊料特点分析报告
高温焊料是一种能够在高温环境下使用的焊接材料。
它具有以下几个特点:
首先,高温焊料具有较高的熔点。
相比于常规的焊料,高温焊料的熔点要更高。
这是因为在高温环境下,焊接材料需要能够承受高温的热量,同时保持其稳定性。
高温焊料的高熔点使得它适用于一些高温焊接工艺,如熔融焊接和电弧焊接。
其次,高温焊料具有良好的耐蚀性。
在高温焊接过程中,焊料需要能够抵御高温环境中的腐蚀和氧化作用。
高温焊料通常由一些金属合金制成,这些合金具有较高的抗腐蚀性能,能够在高温环境下保持其完整性和机械强度。
这使得高温焊料适用于一些需求高耐蚀性的行业,如化工和航空航天。
第三,高温焊料具有较好的导电性和热导性。
在高温焊接过程中,焊料需要能够有效传导电流和热量,以保证焊接的质量和效率。
高温焊料通常由金属材料制成,金属具有良好的导电性和热导性,能够满足高温焊接的要求。
最后,高温焊料还具有较好的可塑性和可加工性。
在高温焊接过程中,焊料需要能够在高温环境下保持其形状和机械性能。
高温焊料通常具有较好的可塑性,能够在高温下保持其变形和形状。
同时,高温焊料通常也具有良好的可加工性,能够便于焊接过程的加工和形变。
综上所述,高温焊料具有较高的熔点、良好的耐蚀性、导电性
和热导性,以及可塑性和可加工性。
这些特点使得高温焊料适用于高温焊接和对焊接质量要求较高的行业。
然而,高温焊料的使用也存在一定的限制,比如较高的成本和较独特的焊接工艺要求。
因此,在选择高温焊料时需要根据具体的焊接要求和应用领域进行合适的选择。
波峰焊盘间距
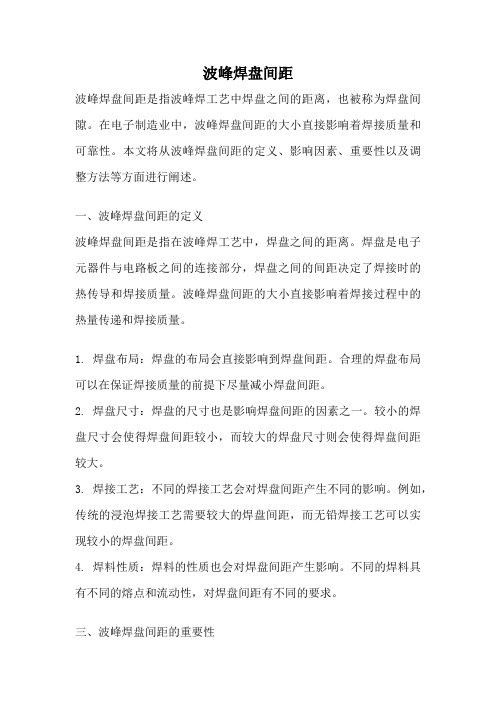
波峰焊盘间距波峰焊盘间距是指波峰焊工艺中焊盘之间的距离,也被称为焊盘间隙。
在电子制造业中,波峰焊盘间距的大小直接影响着焊接质量和可靠性。
本文将从波峰焊盘间距的定义、影响因素、重要性以及调整方法等方面进行阐述。
一、波峰焊盘间距的定义波峰焊盘间距是指在波峰焊工艺中,焊盘之间的距离。
焊盘是电子元器件与电路板之间的连接部分,焊盘之间的间距决定了焊接时的热传导和焊接质量。
波峰焊盘间距的大小直接影响着焊接过程中的热量传递和焊接质量。
1. 焊盘布局:焊盘的布局会直接影响到焊盘间距。
合理的焊盘布局可以在保证焊接质量的前提下尽量减小焊盘间距。
2. 焊盘尺寸:焊盘的尺寸也是影响焊盘间距的因素之一。
较小的焊盘尺寸会使得焊盘间距较小,而较大的焊盘尺寸则会使得焊盘间距较大。
3. 焊接工艺:不同的焊接工艺会对焊盘间距产生不同的影响。
例如,传统的浸泡焊接工艺需要较大的焊盘间距,而无铅焊接工艺可以实现较小的焊盘间距。
4. 焊料性质:焊料的性质也会对焊盘间距产生影响。
不同的焊料具有不同的熔点和流动性,对焊盘间距有不同的要求。
三、波峰焊盘间距的重要性波峰焊盘间距的大小直接影响着焊接的热传导和焊接质量。
过小的焊盘间距可能会导致热量传递不均匀,造成焊接不完全或焊接不牢固;过大的焊盘间距则会导致焊接质量下降,焊盘之间的接触面积减小,焊接点的可靠性降低。
因此,确定合适的波峰焊盘间距对于保证焊接质量和可靠性至关重要。
四、调整波峰焊盘间距的方法1. 调整焊盘布局:通过调整焊盘的布局,可以在保证焊接质量的前提下尽量减小焊盘间距。
合理的焊盘布局可以使得焊盘之间的间距更加均匀。
2. 优化焊盘尺寸:根据具体的焊接要求,可以优化焊盘的尺寸,使得焊盘间距更加合适。
较小的焊盘尺寸可以减小焊盘间距,提高焊接质量。
3. 选择合适的焊接工艺:根据具体的焊接要求和焊接材料,选择合适的焊接工艺。
不同的焊接工艺对焊盘间距有不同的要求,选择合适的焊接工艺可以实现更合理的焊盘间距。
- 1、下载文档前请自行甄别文档内容的完整性,平台不提供额外的编辑、内容补充、找答案等附加服务。
- 2、"仅部分预览"的文档,不可在线预览部分如存在完整性等问题,可反馈申请退款(可完整预览的文档不适用该条件!)。
- 3、如文档侵犯您的权益,请联系客服反馈,我们会尽快为您处理(人工客服工作时间:9:00-18:30)。
焊料性质对焊接的影响1.前言目前各种形式的合金焊料,其最权威的国际规范为J-STD-006。
此文献之最新版本为1996.6的Amendment 1,由于资料很新,故早已取代了先前甚为知名的美国联邦规范QQ-S-571。
IPC还有一份重要的焊接手册IPC-HDBK-001其中之4. 1,曾定义“熔点”在430℃以下为“软焊”(Soldering),也就是锡焊。
另熔点在430℃以上称为“硬焊”(Brazing),系含银之高温高强度焊接。
早期欧美业界,亦称熔点600℉(315℃)以下者为软质焊锡,800℉(427℃)以上者为硬质焊锡。
原文Solder定义为锡铅含金之焊料,故中译从金旁为“焊锡”,而利用高热能进行熔焊之Soldering(注意此一特定之单字,并非只加ing而已),则另从火旁用字眼的“焊接”,两者涵义并不完全相同。
2.共熔(晶)焊锡焊锡焊料(Solder)主要成分为锡与铅,其它少量成分尚有银、铋、铟等,各有不同的熔点(M.P.),但其主要二元合金中以Sn63/Pb37之183℃为最低,由于其液化熔点(Liquidus Point)与固化熔点(Solidus Point)的往返过程中,均无过渡期间的浆态(pasty)出现,也就是已将较高的“液化熔点”与较低的“固化熔点”两者合而为一,故称为“共熔合金”。
且因其粗大结晶内同时出现锡铅两种元素,于是又称为“共晶合金”。
此种无杂质合金外表很光亮之“共熔组成”(Eute ctic Composition)或“共熔焊锡”(Eutectic Solder),其固化后之组织非常均匀,几无粒子出现。
其合金比例之不同将影响到熔点变化,该变化之“平衡相图(Ph ase Diagram)”,图请参考第12期TPCA会刊。
另一种组成接近共熔点的Sn60/Pb40合金,则在电子业界中用途更广,主要原因是Sn较贵,在焊锡性(Solderability)与焊点强度(Joint Strength)几无差异下,减少了3﹪的支出,自然有利于成本的降低。
与前者真正共熔合金比较时,此60/40者必须经历少许浆态,故其固化时间稍长,外观也较不亮,但其焊点强度并无不同。
不过后者若于其固化过程中受到外力震动时,将出现外表颗粒粗麻之“扰焊”现象(Disturbed)之焊点,甚至还可能发生“缩锡”(Dewetting)之不良情形。
3.焊料之特性除了“焊锡性”好坏会造成生产线的困扰外,“焊点强度” (Joint Strength)更是产品后续生命的重点。
但若按材料力学的观点,只针对完工焊料的抗拉强度(T ensile Strength)与抗剪强度(Shear Strength)讨论时,则并不务实。
反而是高低温不断变换的长期热循环(Thermal Cycling,又称为热震荡Thermal Shoc k)过程中,其等焊点由于与被焊物之热胀系数(TCE)不同,而出现塑性变形(Plastic Deformation),再进一步产生潜变(Creep)甚至累积成疲劳(Fatig ue)才是重点所在。
因此等隐忧迟早会造成焊点破裂(Crack)不可收拾的场面,对焊点之可靠度危害极大。
组件的金属引脚与组件本体,及与板面焊垫之间的热胀系数(TCE)并不相同,因而在热循环中一定会产生热应力(Stress)进而也如响应斯的出现应变(Strai n),多次热应力之后将再因一再应变而“疲劳”(Fatique),终将使得焊点或封装体发生破裂,此种危机对无脚的SMD组件影响更大。
现将常见共熔焊料之一般机械性质整理如下:3.1共熔点63/37的焊料,其常温中的抗拉强度(Tensile Strength)为7250 P SI,而常见冷轧钢(Cold Rolled Steel)却高达64,000 PSI,但此抗拉强度对焊点强度的影响反不如抗剪强度(Shear Strength)来的大,若加入少量锑后成绩会较好。
至于展性(Ductility)与弹性模数(Elastic Modulus)则63/37者均比其它高熔点者二元合金要更好,两合金之导电导热则比纯锡差,且随铅量增加时会呈少许下降。
一般63/37者其强度较其它比例更好。
多锡者也比多铅者为强。
3.2各种比例的锡铅合金焊料,其强度均比单独锡铅金属较好。
比重值则随铅量愈多而增大,呈液态时表面张力与合金比例的关系不大。
3.3焊点抗潜度(Creep)能力的好坏,对可靠度的重要性将远超过抗拉强度。
不幸的是愈接近共晶比例而结晶粒子愈粗大者,其潜变也愈大。
而柱状结晶的抗潜变能力也不如等轴结晶(Equiaxial)者。
焊点合金在长期的负荷下会出现原子结晶格子(Atom Lattice)的重整;也就是焊点经长时间劣化下,最后终究会发生故障,原因当然是长时间应力而带来过度“应变”而成“疲劳”所致。
3.4焊点强弱与助焊剂,焊锡性及IMC有关,由许多试验结果可知,强度与填锡量多少无关,锡量太多反而无益。
焊接时间不宜超过5秒,愈久愈糟,焊温也不可太高。
4.低温与高温焊锡上述共熔焊锡之熔点为183℃,某些对高温敏感的组件而言,其组装时需用到熔点低于183℃者,称为“低温焊锡”(Low Temperature Solder),其实用配方中需另外加入铋(Bismuth,Bi)与铟(Indium,In)。
由于加入此二者所形成的焊料都存在着某些缺点(如强度不足),故量产工业尚无法以取代锡铅之共熔焊料。
加入铋之冷却后焊点,不易出现膨胀情形,会对焊点造成额外的应力,此种焊点强度不足的隐忧较焊锡性不良更糟。
而铟却由于价格太贵也无进入量产用途。
至于高温焊料者则以含银者最常见,现分述于后:4.1含铋焊料含铋焊料除了焊点会稍有膨胀之不良外,尚因其焊温甚低,有时会导致助焊剂无法全然发挥其活性,以致造成缩锡等焊锡性不良问题。
再者是含铋时容易氧化,致使焊点强不足。
此点对安全用电的保险丝(Fuses)而言尤其重要,一旦氧化后经常会造成该断而未断之情形,安全上将大打折扣。
4.2含铟焊料含铟之焊锡也会有焊点强度不足的烦恼,且价格不十分昂贵,但也具有一些优点,如:(1)沾锡性(Wettability)非常良好。
(2)展性(Ductility)良好,可呈现极佳的抗疲劳性(Fatigue Resistance),甚至还优于锡铅之共熔合金。
(3)焊接动作与锡铅共熔焊料相比较时,就黄金成份熔入所造成的缺失,则含铟焊点者较为轻微。
4.3含银焊料当零件脚或板面焊垫之表面处理为镀银表面时,则其焊料中若添加少许银份时,则可大大减缓外界银份熔入的缺点。
但此等熔点较高的含银焊料通常焊锡性都不好,焊点外表昏暗,机械强度也不足。
5.焊料与制程5.1合金互熔锡铅二元合金之焊料,事实上是锡熔进铅中,而所谓的Solder即是二者之“溶液”而已。
高温焊接中板面承垫中的铜份也会融入铅与锡中,也就是铜原子会扩散进入熔融的焊料内,并在焊料与底铜之间形成居中的接口层IMC(Cu6Sn5),也唯有如此才能真正的焊牢。
一但焊垫外表发生铜面氧化物或其它表面污染物时,则会阻止铜份的扩散而无IMC的产生,以致无法焊牢。
并出现所谓缩锡(Dewe tting)或不沾锡(Non-Wetting)等焊锡性不良的表征。
5.2沾锡过程沾锡(Wetting)亦称为Tining,其动作说时迟那时快,首先是高温中助焊剂展现活性(Activity),迅速去除金属焊垫表面的氧化物或污物或有机护铜剂等(如Entek),使熔融的焊锡与底铜(或底镍等其它可焊金属)之间,迅速产生如树根般的一薄层“界面合金共化物”(Inter Matalic Compound Intermetallic Co mpound Cu6Sn5),而沾锡及焊牢。
在焊点外观上可见到焊料向外向上扩张地盘的动作,其地盘外缘有一种“固/液/气”三相交会处,隐约中似乎出现“蓄势待发”而奔出的小角度,特称之为沾锡性的接触角(Contact Angle ,θ),亦称为如喷射机般的双反斜角(Dihedral Angl e)。
此接触角度愈小,则沾锡性或焊锡性也愈好。
实际上沾锡力量(Wetting Force)是受到几股力量的影响。
下图即为其等力量平衡及冷却后的焊点断面说明,现以浅显易懂的语言配合图面说明诠释(请参考第12期TPCA会刊)。
θ角=双反斜角,接触角,或常说的沾锡角。
r=接口之间所出现的表面能(Surface Energies)或力量,系指清洁铜面对焊锡金属的亲和力,亦即产生IMC(Cu6Sn5)时互亲的力量,也就所谓的焊键(Solder Bond)。
但铜对铅则不会产生任何亲和力。
r sr=地盘外缘固相与汽相之间的力量,即液锡向外扩张时所呈现的附着力(Adhes ive Force) 此力量愈大时沾锡角愈小,焊锡性也愈好。
r ls=液相与地盘内固相之间的亲合力量,必须要先生成IMC时才会表现出力量,且此力几乎是固定不变的。
对整体而言此力只会呈现液相本身向内收缩的内聚力(Cohesive Force),对向外扩张并无助益。
r lv=液相与汽相间的力量,此力又可再解析成为垂直分力(r lv˙sinθ) 与水平分力(r ˙cosθ); 后者表现得愈大时,沾锡性或焊锡性也愈好。
lv由图中公式r sr=r ls+r lv˙cosθ,向外扩张的沾锡力量想要最大时,则其水平分力(r lv˙cosθ) 也应最大,也就是θ角要愈小愈好。
当θ角=0 时,则cosθ=1,于是向外扩张的沾锡力量r sv也变成最大(亦即焊锡性最好)。
5.3 界面合金共化物IMC焊接动作之所以能够焊牢,最根本的原因就是焊锡与底金属铜面之间,已产生了IMC(Intermatallic Compound Layer) 之良性接口合金共化物Cu6Sn5,此种如同树根或家庭中子女般之接口层,正是相互结合力之所在。
但IMC有时也会在焊锡主体中发现,且呈现粒状或针状等不同外形。
其液态时成长之初的厚度约为0.5-1.0μm之间,一旦冷却固化IMC后还会缓缓继续长厚,而且环境温度升高时还将会长的更快,最好不要超2μm。
久了之后在原先Cu6,Sn5之η–phas e(注η为希腊字母,读做Eta)良性IMC,与底铜之间还会另外生出一层恶性ε-p hase(注: ε 读做Epsilon) 的Cu3Sn. 此恶性者与原先良性者本质上完全不同,一旦ε-phase出现后其焊点强度即将渐趋劣化,脆性逐渐增加,IMC本身松弛,甚至整体焊点逐渐出现脱裂浮离等生命终期的到来。
一般IMC的性质与所组成的金属完全不同,常呈现脆性高、导电差,且很容易钝化或氧化等进一步毁坏之境界。
并具有强烈惰性顽性,一般助焊剂均无法加以清除。
常见之IMC除了铜锡之间者,尚有锡镍、锡银、与锡金甚至锡铁等I MC,其等后续平均成长之速度与活化能等比较列表如下:※各种IMC后续平均成长速率之比较要注意的是上述铜锡之间IMC的成长情形,系针对其共熔组成的焊料(63/67)而言,其它锡铅比合金对铜生长IMC的速率,则又有不同;但其扩散的过程都是来自底铜中的铜原子而向焊锡中逐渐渗入,且随周遭温度之上升而加速。