烷基化工艺说明
危险化工工艺安全技术 烷基化工艺危险性分析及安全技术

物 质 类 物质名称 别 原料 苯
苯胺
烷 基 化 丙烯
剂
甲醇
闪 点 燃点/℃
/℃
11
538
70
12.2
497 473自
爆炸极限/% 1.3~7 1.3~4.2 2.0~11.1 6.0~36.5
毒性 腐蚀性 备注
有
麻醉 强
ห้องสมุดไป่ตู้甲类液体
见 光 变 丙类液体 色
易燃气体
甲类液体
十二烯
77
220
乙类液体
烷基化工艺危险性分析及安全技术
2、烷基化反应的危险性
续上表
物 质 物质名称 闪 点 燃点/℃ 爆炸极限/% 毒性
类别
/℃
催 化 三氯化铝 遇水分解放热 放 出 热 和 HCl
剂 三氯化磷 遇水或乙醇剧 烈 气体能引爆 有毒
分解
产品 异丙苯
35.5
434 0.68~4.2 中度
二甲基苯胺 61
371
中度
腐蚀性
强 有
备注
忌湿物品 忌湿液体
烷基化工艺危险性分析及安全技术
1、烷基化反应
烷基化是在有机化合物中的氮、氧、碳等原子上引入烷基(R—)的化学反 应。引入的烷基有甲基(—CH3)、乙基(—C2H5)、丙基(—C3H7)、丁 基(—C4H9)等。常用烯烃、卤化烃、醇等作烷基化剂。如苯胺和甲醇作 用制取二甲基苯胺。
烷基化工艺危险性分析及安全技术
乙类液体 丙类液体
烷基苯
127
丙类液体
2、烷基化反应的危险性
①被烷基化的物质大都具有燃烧、爆炸等危险。 ②烷基化剂一般比被烷基化物质的燃烧危险性要大。 ③烷基化过程所用的催化剂反应活性强。 ④烷基化反应都是在加热条件下进行。 ⑤烷基化的产品也有一定的火灾危险。
烷基化工艺作业安全操作规程
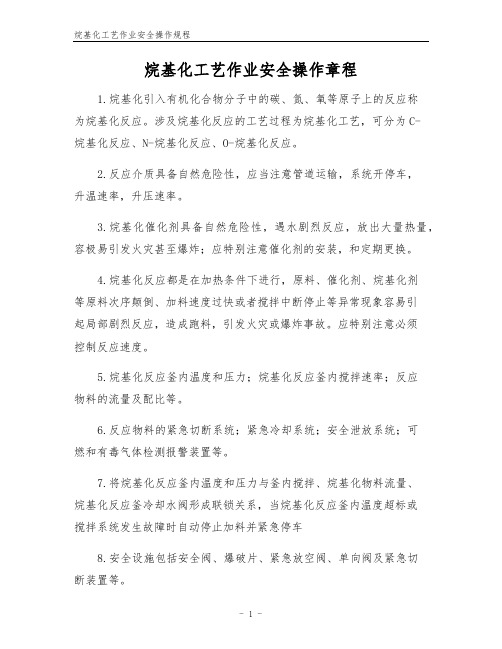
烷基化工艺作业安全操作章程1.烷基化引入有机化合物分子中的碳、氮、氧等原子上的反应称为烷基化反应。
涉及烷基化反应的工艺过程为烷基化工艺,可分为C-烷基化反应、N-烷基化反应、O-烷基化反应。
2.反应介质具备自然危险性,应当注意管道运输,系统开停车,升温速率,升压速率。
3.烷基化催化剂具备自然危险性,遇水剧烈反应,放出大量热量,容极易引发火灾甚至爆炸;应特别注意催化剂的安装,和定期更换。
4.烷基化反应都是在加热条件下进行,原料、催化剂、烷基化剂等原料次序颠倒、加料速度过快或者搅拌中断停止等异常现象容易引起局部剧烈反应,造成跑料,引发火灾或爆炸事故。
应特别注意必须控制反应速度。
5.烷基化反应釜内温度和压力;烷基化反应釜内搅拌速率;反应物料的流量及配比等。
6.反应物料的紧急切断系统;紧急冷却系统;安全泄放系统;可燃和有毒气体检测报警装置等。
7.将烷基化反应釜内温度和压力与釜内搅拌、烷基化物料流量、烷基化反应釜冷却水阀形成联锁关系,当烷基化反应釜内温度超标或搅拌系统发生故障时自动停止加料并紧急停车8.安全设施包括安全阀、爆破片、紧急放空阀、单向阀及紧急切断装置等。
9.应当定期检查,并经常注意低压系统压力变化,以避免高压气体窜入低压系统引起物理爆炸。
若发现低压系统压力突然升高,而原因不明时,应作紧急停车处理。
10.要经常检查合成机工作内件的运转、密封、润滑情况,如果发现撞击、震动、大量泄漏等异常现象,应快速进行处理,避免高压气体冲击发生着火和爆炸。
11. 操作人员要认真学习安全生产知识和消防安全知识,做到“三懂”、“三会”。
“三懂”是指懂得本岗位的火灾危险性;懂得预防火灾的措施;懂得扑救方法。
“三会”是指会报警;会使用灭火器材;会处置险肇事故。
烷基化操作规程

烷基化操作规程
《烷基化操作规程》
烷基化是一种化学反应,其目的是向有机化合物中引入烷基基团。
烷基化操作广泛应用于有机合成领域,可以用于合成各种类型的有机化合物。
为了确保烷基化反应的安全和有效进行,制定了一系列的烷基化操作规程。
首先,进行烷基化实验前,实验室人员应该熟悉烷基化反应的原理和操作方法。
在进行实验时,必须穿戴防护眼镜、实验服和手套,以防止化学药品对人体造成伤害。
另外,实验室应备有紧急应对药品和设备,以便在发生意外时及时采取措施。
其次,操作规程也包括了烷基化反应的具体步骤和条件。
在选择反应条件时,应考虑到底物的性质和要引入的烷基基团类型,以确保反应可以高效进行。
此外,还需要注意反应温度、搅拌速度和反应时间等参数的控制。
最后,对于烷基化反应产物的处理和纯化也需遵循规程。
产物的分离和纯化步骤需要谨慎进行,以保证产物的纯度和收率。
在处理废弃物时,应当按照相关的环保标准进行处理,确保对环境和人体的安全。
总之,《烷基化操作规程》的制定和遵守是确保烷基化反应安全进行的关键。
只有严格遵循规程,才能保证实验室人员的安全,同时也能够获得高质量的反应产物。
希望通过严格执行操作规程,可以有效地推动烷基化反应的应用和研究。
烷基化工艺说明

目录1 概述,,,,,,,,,,,,,,,,,,,,,,,,,,,,,, 32 工艺设计技术方案,,,,,,,,,,,,,,,,,,,,,,,, 43 原料及产品性质,,,,,,,,,,,,,,,,,,,,,,,,, 54 装置物料平衡,,,,,,,,,,,,,,,,,,,,,,,,,, 75 工艺流程简述,,,,,,,,,,,,,,,,,,,,,,,,,, 86 主要设备选型说明,,,,,,,,,,,,,,,,,,,,,,,,1 47 消耗指标及能耗,,,,,,,,,,,,,,,,,,,,,,,,, 148 装置定员,,,,,,,,,,,,,,,,,,,,,,,,,,,, 219 环境保护,,,,,,,,,,,,,,,,,,,,,,,,,,,, 2210 职业安全卫生,,,,,,,,,,,,,,,,,,,,,,,,, 2311 装置对外协作关系,,,,,,,,,,,,,,,,,,,,,,, 2912 设计执行的标准目录,,,,,,,,,,,,,,,,,,,,,, 311 概述该烷基化装置采用硫酸烷基化工艺,公称规模为16万吨/ 年。
1.1 设计依据1.1.2 DUPONT 公司提供的硫酸烷基化工艺包;1.2 装置概况1.2.1 装置原料:本装置原料为上游MTBE装置提供的未反应碳四馏分、加氢裂化液化气,前处理所需的少量氢气由制氢装置提供。
1.2.2 装置建设规模:根据MTBE装置所提供的液化气量及液化气中的烯烃含量,实际可生产烷基化油约13.13万吨/ 年,本装置设计规模为16万吨/ 年烷基化油。
1.2.3 装置建设性质:在酸催化剂的作用下,液化气中的异丁烷与烯烃反应生成高辛烷值汽油调合组分- 烷基化油。
1.3 设计原则:1)选用成熟可靠的工艺技术和控制方案,使设计的装置达到安、稳、长、满、优操作。
2)优化工艺流程并推广应用新工艺、新技术、新设备、新材料,降低生产成本同时降低装置能耗,提高产品质量档次。
烷基化工艺

烷基化工艺的反应类型包括质子酸烷基 化、路易斯酸烷基化、酶催化烷基化等。
烷基化反应的机理
质子酸烷基化反应机理
• 质子酸作为催化剂,与烷基化剂发 生质子交换,生成活性中间体。 • 活性中间体与有机化合物发生烷基 化反应,生成新的烷基化合物。
路易斯酸烷基化反应机理
• 路易斯酸作为催化剂,与烷基化剂 发生配位反应,生成活性中间体。 • 活性中间体与有机化合物发生烷基 化反应,生成新的烷基化合物。
点。
01
烷基化工艺在 石油化工、制 药、新材料等 领域有广泛的 应用,具有较 高的经济效益。
02
烷基化工艺的缺点
烷基化工艺的催化剂成本较高,且部分催化剂具有毒性。
烷基化工艺的产物分离和提纯过程较复杂,可能导致产物损失。
烷基化工艺的改进措施与发展方向
通过改进催化剂结构和性能,降低催化剂成本和毒性。 通过优化产物分离和提纯工艺,提高产物收率。 开发新型绿色烷基化工艺,提高工艺的环境友好性。
烷基化工艺的发展趋势
烷基化工艺的发展方向包括绿色烷基化 工艺的研究、新型催化剂的研究、智能 化生产技术的应用等。
烷基化工艺的发展将进一步提高工艺的 经济效益和环境友好性。
烷基化工艺在未来工业中的应用前景
01 烷基化工艺在未来工业中的应用前景广泛,包括石油化工、制药、新材料等领域。 02 烷基化工艺在未来工业中的应用将进一步提高产品的性能和价值,促进相关产业的发展。
烷基化工艺的催化剂研究
ห้องสมุดไป่ตู้
01 质子酸催化剂的研究
• 改进质子酸催化剂的结构,提高催化剂的活性和选择性。 • 通过添加助剂,改善催化剂的稳定性,延长使用寿命。
02 路易斯酸催化剂的研究
• 改进路易斯酸催化剂的结构,提高催化剂的活性和选择 性。 • 通过添加助剂,改善催化剂的稳定性,延长使用寿命。
碳四烷基化工艺指南

烷基化装置1、烷基化工艺采用硫酸为催化剂的硫酸烷基化工艺1) 原料(1) 不同烯烃原料的影响在硫酸烷基化反应条件下,大部分1-丁烯可以异构化为2-丁烯,使得烷基化产品的辛烷值得以提高。
(2) 原料中杂质的影响及其脱除方法大多数原料中的杂质在硫酸烷基化反应后进入酸相,使得硫酸被污染,从而降低了硫酸的催化活性。
①乙烯假如气体分馏装置未能很好的除去C2时,乙烯就可能被引入烷基化装置。
在硫酸催化时,由于乙烯不会与异丁烷反应发生烷基化反应,当乙烯进入烷基化反应器时,乙烯与硫酸生成呈弱酸性的硫酸氢乙酯,这个硫酸氢乙酯不再作为烷基化的催化剂使用。
这种乙烯杂质的影响还具有累积性,因此,即使原料中含有痕量的乙烯,也能造成每天数百公斤的乙烯进入酸相,从而出现数吨甚至十余吨的废酸。
假如突然有相当量的乙烯进入到烷基化反应器中,这些乙烯对酸的影响可以使烷基化反应不再发生,甚至发生叠合反应。
②丁二烯假如催化装置或焦化装置的裂化深度相当深,那么就可能在液化气中找到相当量的丁二烯,这些丁二烯也是不能发生烷基化反应的,它们与酸接触后新生成的反应产物也是酸溶性的。
与乙烯相比,丁二烯更难以用分馏的方法从烷基化原料中除去。
因此,当上游裂化装置的裂化深度无法改变的时候,可以考虑用选择性加氢的方法将丁二烯转化为丁烯。
③水水能造成硫酸的稀释是不言而喻的。
因此要重视烷基化原料中水的影响。
液化气中的水在呈溶解状态时大约在500ppm左右。
更应当引起重视的是C4馏分携带的超过饱和状态的游离水,上游装置操作不当可能使C4馏分所携带游离水的量是溶解水的几倍,对酸的稀释速度相当快。
脱除这种携带水的办法是在烷基化原料进装置前先进入一个填料容器,使携带的细小的水珠聚集后分离出去。
如果在进入填料分水器之前先用反应物冷却一下进料的物流,其效果就会更好。
从分馏部分循环到反应部分的异丁烷也可能携带相当数量的水分,为了干燥这部分异丁烷,可以将这个物流与废酸相接触,这种干燥法既经济效果又好。
烷基化操作规程
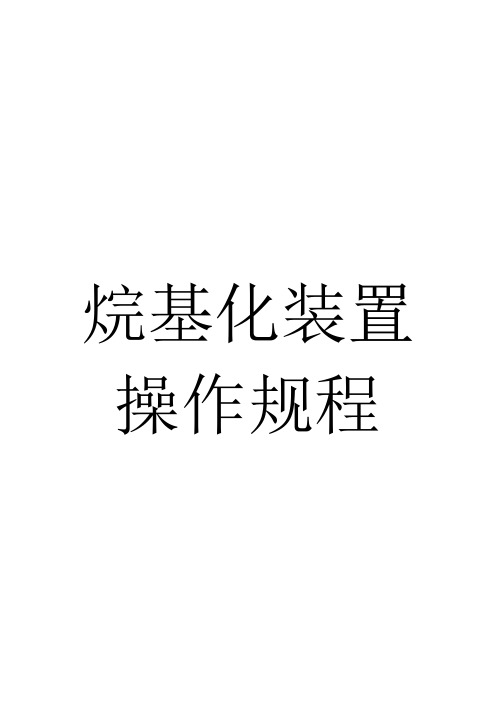
烷基化装置操作规程目录第一章 (4)第二章 (4)2.1 工艺原理 (4)2.2 工艺说明 (5)2.3 原料规格 (11)2.4 产品规格 (14)2.5 界区条件 (15)2.6 公用工程要求 (15)2.7 开车对工艺化学品的要求 (18)2.8 排放物和副产品 (19)2.9 设计考虑 (21)第三章 (22)3.1 烃类原料污染物的影响 (22)3.2 装置进料成分敏感度: (22)3.3 正操操作和控制 (22)第四章 (33)4.1 推荐的样品分析方法 (33)4.2 分析仪一览表 (34)4.3 取样一览表 (34)第五章 (37)5.1 安全淋浴器和洗眼器 (37)5.2 防火系统 (38)5.3 化学品处理和循环 (38)5.4 压力排放系统 (39)第六章 (40)6.0 开车步骤 (40)6.1 公用工程系统 (40)236.2 单机试车(预试车)和准备 (42)6.3 CDAIky装置钝化工艺 (44)6.4 正常开车 (46)第七章 (53)7.0 停车步骤 (53)7.1 从正常操作到全面停车程序 (54)7.2 短期停车 (60)7.3 长期停车 (62)7.4 事故停车步骤: (64)第八章 (65)8.1 反应危害 (65)第一章序言本手册含有烷基化工艺方面包括操作条件和生产能力在内的保密信息。
这些信息不能泄露给未经授权的人员。
本手册还提供了装置系统方和操作程序方面的信息,该手册的目的主要是为操作人员在进行装置详细操作手册准备和编制。
第二章工艺原理2.1 工艺简述该工艺涉及的反应是烯烃同异丁烷的烷基化反应。
同时副反应中有副产品产出。
烷基化初级烷基化反应涉及异丁烷同烯烃、如丁烯的反应,使用硫酸作为催化剂生成高辛烷值的三甲基戊烷异构物。
通常三甲基戊烷异构物被称之为烷基化油。
i-C4+C4H8→2,2,4-三甲基戊烷类似的反应也在异丁烷和其他烯烃如丙烯和戊烷之间发生,分别生成庚烷和壬烷异构物,但是就低选择性生产高辛烷值产品而言,选择丁烯进料更适宜。
烷基化操作规程
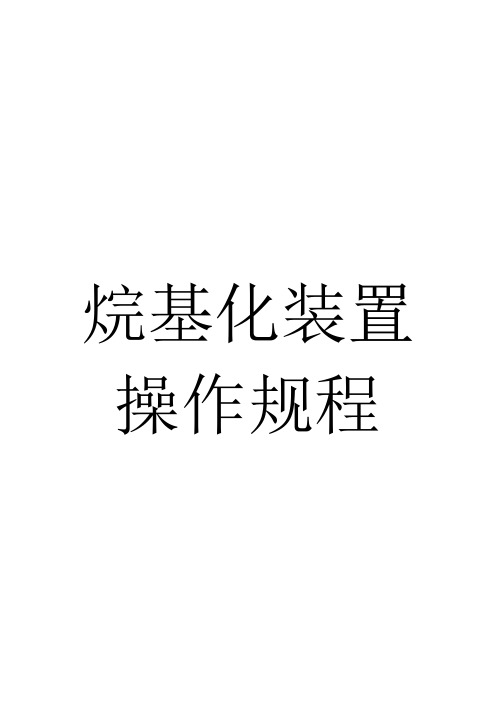
烷基化装置操作规程目录第一章 (4)第二章 (4)2.1 工艺原理 (4)2.2 工艺说明 (5)2.3 原料规格 (11)2.4 产品规格 (14)2.5 界区条件 (15)2.6 公用工程要求 (15)2.7 开车对工艺化学品的要求 (18)2.8 排放物和副产品 (19)2.9 设计考虑 (21)第三章 (22)3.1 烃类原料污染物的影响 (22)3.2 装置进料成分敏感度: (22)3.3 正操操作和控制 (22)第四章 (33)4.1 推荐的样品分析方法 (33)4.2 分析仪一览表 (34)4.3 取样一览表 (34)第五章 (37)5.1 安全淋浴器和洗眼器 (37)5.2 防火系统 (38)5.3 化学品处理和循环 (38)5.4 压力排放系统 (39)第六章 (40)6.0 开车步骤 (40)6.1 公用工程系统 (40)236.2 单机试车(预试车)和准备 (42)6.3 CDAIky装置钝化工艺 (44)6.4 正常开车 (46)第七章 (53)7.0 停车步骤 (53)7.1 从正常操作到全面停车程序 (54)7.2 短期停车 (60)7.3 长期停车 (62)7.4 事故停车步骤: (64)第八章 (65)8.1 反应危害 (65)第一章序言本手册含有烷基化工艺方面包括操作条件和生产能力在内的保密信息。
这些信息不能泄露给未经授权的人员。
本手册还提供了装置系统方和操作程序方面的信息,该手册的目的主要是为操作人员在进行装置详细操作手册准备和编制。
第二章工艺原理2.1 工艺简述该工艺涉及的反应是烯烃同异丁烷的烷基化反应。
同时副反应中有副产品产出。
烷基化初级烷基化反应涉及异丁烷同烯烃、如丁烯的反应,使用硫酸作为催化剂生成高辛烷值的三甲基戊烷异构物。
通常三甲基戊烷异构物被称之为烷基化油。
i-C4+C4H8→2,2,4-三甲基戊烷类似的反应也在异丁烷和其他烯烃如丙烯和戊烷之间发生,分别生成庚烷和壬烷异构物,但是就低选择性生产高辛烷值产品而言,选择丁烯进料更适宜。
烷基化反应及其工艺

§7.1概述
一、定义
二、种类
烷基化种类
1,C-烷基化
2,N-烷基化
3,O-烷基化
C-H → C-R N-H → N-R O-H → O-R
§7.2 C-烷基化反应
一、C-烷化剂 1,卤烷卤烷 作C-烷化剂 2,烯烃
乙烯、丙稀、异丁烯;一般AlCl3作催化剂,也可用BF3、HF
H2C(H2C) 16H3C NH
H2C(H2C) 16H3C
2CH 3Cl
H2C(H2C) 16H3C H2C(H2C) 16H3C
N+
CH3 ·Cl-
CH3
3,用酯类烷化
硫酸酯(ROSO2OR)、磷酸酯、芳磺酸 酯等
沸点高,故可在常压下进行;当价格比 醇和卤代烃高 ; ArNH2 + ROSO2OR → ArNHR + ROSO2OH ←需要碱中和生成的酸 ArNH2 + ROSO2ONa → ArNHR + NaHSO4 难于进行
三氯化铝与盐酸生成络合物以后,其质子与烯烃的加成符合 马尔科夫尼科夫规则
CH3 CH
CH3
CH3 C CH3 CH3
2,卤烷的烷基化
Байду номын сангаас
3,芳烃烷基化反应的特点
(1)C-烷基化是连串反应
(2)C-烷基化反应是可逆反应烷基的转移和歧化
(3)烷基可能重排
1-氯丙烷与苯反应产物
四、烷基化反应实例
C、酮类的C-烷基化(如双砜A)
2
+ OH
O H3C C CH3
H2SO 4 或 HCl
HO
CH3
C
OH
CH3
工艺流程教材 P77-7-4
烷基化反应及其工艺
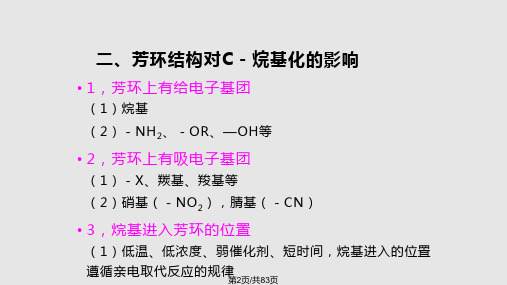
能够接受电子形成带负电荷的碱性试剂,同时形成活泼的亲电质点
第65页/共83页
AlCl3使卤烷转变为活泼的亲电质点—烷基正离子
第66页/共83页
液态烃溶剂中
• AlCl3能与HCl作用生成络合物,这种络合物又能 与烯烃反应,形成活泼的亲电质点。
第44页/共83页
第45页/共83页
氨或脂肪胺与环氧乙烷的反应,用于制备乙醇胺类化合物:
第46页/共83页
• -CN、-COOH、-COOR
2,用烯烃衍生物烷化
• 第47页/共83页
以丙稀腈为例的反应
第48页/共83页
• 伯胺一般可以引入两个烷基,但在引入第一个烷基衍生物后,反应活性下降 二烷基化时要加入铜盐作Cat,如氯化铜、氯化亚铜、醋酸铜 或者极性Cat:如乙酸、三乙胺、吡啶等
第5页/共83页
第6页/共83页
三氯化铝与盐酸生成络合物以后,其质子与烯烃的加成 符合马尔科夫尼科夫规则
CH3 CH CH3
第7页/共83页
CH3 C CH3 CH3
2,卤烷的烷基化
第8页/共83页
• (1)C-烷基化是连串反应
3,芳烃烷基化反应的特点
• (2)C-烷基化反应是可逆反应烷基的转移和歧化 • (3)烷基可能重排 1-氯丙烷与苯反应产物
第13页/共83页
(2)抗氧剂264的制备
HO
+ CH3 2 H2C
CH3浓H 2SO4 C
C(CH 3)3
HO
CH3
CH3
C(CH 3)3
第14页/共83页
第15页/共83页
• 醇类、醛类和酮类弱烷基化剂
烷基化工艺

• 选择合适的催化剂是提高烷基化反应效果的关键
反应条件
• 反应温度、压力、物料配比等因素都会影响烷基化反应的结果
• 合理控制反应条件是提高烷基化反应效果的重要手段
烷基化剂的选择
• 烷基化剂的类型、结构、纯度等因素都会影响烷基化反应的结果
• 选择合适的烷基化剂是提高烷基化反应效果的关键
20世纪中期
• 随着科学技术的发展,人们开始研究使用固体酸催化剂,
如沸石、氧化铝等
• 这些催化剂具有较高的选择性和活性,但仍有待提高
03
20世纪末至今
• 近年来,研究者通过改进催化剂、优化反应条件等手段,
使得烷基化工艺得到了广泛应用
• 烷基化工艺已成为现代工业生产中不可或缺的一部分
烷基化工艺在现代工业中的应用及重要性
效率
• 萃取分离是烷基化工艺
中常用的产物分离方法,
适用于极性不同的产物
• 需要选择合适的萃取
剂、萃取条件等,以提高
分离效率
产物提纯方法与技术研究
蒸馏提纯
• 蒸馏提纯是烷基化工艺中常用的产物提纯方法,适用于沸点不同的产物
• 需要选择合适的蒸馏塔、填料等,以提高提纯效率
结晶提纯
• 结晶提纯是烷基化工艺中常用的产物提纯方法,适用于溶解度不同的产物
⌛️
制药领域
• 烷基化工艺在制药领域也有应用,如生产药物中间体、靶向药物等
• 通过烷基化工艺,可以提高药物的疗效,降低药物的副作用,提高药
物的安全性
02
烷基化工艺的基本原理及反应机理
烷基化工艺的基本原理
烷基化工艺的基本原理是通过将烷基
基团引入到有机化合物中,形成新的
化工工艺学 烷基化

1. 化学反应
异丁烷与烯烃的化学反应可表述如下:
副反应有裂解、叠合、异构化、歧化和缩聚等, 生成众多的低沸点和高沸点副产物。↓副反应, 常使异丁烷大大过量。
2. 催化剂 (1) 硫酸
用作烷基化催化剂的硫酸浓度为86%~96%(w)。 硫酸浓度不能太低,以保证反应的顺利进行。硫酸
浓度太高,会促使烯烃氧化。同时,在浓酸中烷/ 烯比严重失调,副反应激烈,副产物增多。 为↑酸烃的接触面,在反应器内需使催化剂与作用 物处于良好的乳化状态,并适当↑酸烃比以↑烷基化 产物的收率和质量。
分子结合重又形成水合氢离子。
由上述机理,反应物和产物在酸膜中的扩散速 度、催化剂表面的酸浓度、反应物的浓度以及 反应温度都会对反应速度产生明显影响。动力 学试验表明,反应速度对乙烯分压是一级,而 水蒸气的分压的正面影响与乙烯相同,负面影 响是使催化剂表面酸浓度(即酸强度)↓,↓反应 速度,因此合适的水蒸气分压由实验确定。
三、乙烯水合制乙醇
1. 生产方法评述 (1) 硫酸水合法
第一步是乙烯与硫酸反应生成烷基硫酸酯 ,第 二步是烷基硫酸酯通直接蒸气加热水解蒸出醇, 硫酸浓度被稀释至50%左右。
提纯费用大,污染严重,副反应多,原料消耗 高。
(2) 直接水合法
乙烯单程转化率在5%左右,选择性94%~95%, 优点是不存在治理大量废酸问题,环境污染也比硫 酸水合法小得多。缺点是转化率低,绝大多数乙烯 需循环使用。
5-3 烷基化
利用取代反应或加成反应,在有机化合 物分子中的氮、氧、碳、硅、硫、金属 等原子上引入烷基或芳烃基的反应。
烷基化剂:烯烃、卤代烷烃、卤代芳烃、 硫酸烷酯、饱和醇
一、由异丁烷和烯烃合成烷基化汽油
烷基化
热烷基化 催化烷基化
烷基化装置生产工艺讲义

R1-CH=CH-R2 +
HF
R1-CH2-CH-R2
• 2、a烯烃反应
• R-CH=CH2 +
HF
R-CH-CH3
h
11
烷基化装置工艺化学原理
• 二、烷基化副反应 • 1、生成异构(支链)烷基苯的反应
R1-C=CH-R2 + CH3
HF
R1-C-CH2-R2 CH3
• 2、生成二烷基苯的反应
R1-CH-CH2-R2
水份/ % <
0.010
0.010
0.050
GB/T 7380
馏程/℃
体积分数5% >
280
280
270
GB/T 6536
体积分数95% <
310
315
320
• 备注:脱氢法生产工业烷基苯指标不得低于一等品, 目前国内LAB工厂执行标准是h 工业烷基苯优等的指标 9
烷基化装置工艺化学原理
• 装置的化学原理
• 烷基化装置PF图.doc
h
2
烷基化装置物料物化性质
• 1、烷基苯(LAB)
• 分子式:C18H30 (十二烷基苯)
• a、物化特性:无色液体
•
密度:0.855~0.870
•
熔点:-45℃
•
沸点:245 ℃
•
闪点:175 ℃
• b、危险特性:基本无毒,可燃
h
3
烷基化装置物料物化性质
• 2、氟化氢 • 分子式 HF • a.物化性质: • 外观及性质:无色发烟气体或液体,有强烈刺
烷基化装置生产工艺讲义
琪优势化工(太仓)有限公司
ห้องสมุดไป่ตู้
烷基化工艺流程简介

烷基化工艺流程简介
烷基化工艺是从烃类中分离出一种或多种烷烃的工艺过程。
它以烷烃为原料,在催化剂作用下生成烷基化油,或由烷基化油、烷基碳数不同的产物组成的混合碳氢化合物,从而生产出性能优良、用途广泛的烷基油产品。
它可以用于生产汽油、柴油和石脑油等,也可作为化工原料。
目前,它在工业上应用最广,因而得到了极大的发展。
烷基化工艺流程简图
(1)原料气(C)进入反应器与催化剂作用,生成烷烃和
相应的烷基化合物。
当反应温度达到200~300℃时,原料气中
的碳原子上的氢原子被烷基所取代。
因此,在此温度范围内原料气中碳原子上的氢原子几乎全部被取代而形成烷基化合物。
在催化剂作用下,烷基化合物之间通过相互加成、断裂和重排反应而生成烷基油和相应的产物。
(2)进入催化剂床层的反应产物气体一部分沿床层上升至
顶部冷却、冷凝,另一部分与催化剂作用形成烷基化合物。
由于反应器内温度较高,气体中的部分碳氢化合物在高温下气化,而另一部分则继续与催化剂作用。
—— 1 —1 —。
烷基化工艺概述

塔顶馏出物经冷凝器冷凝后进入塔顶回流罐。冷凝液经泵抽出,部分顶回流,另一部分经冷却器冷却至40℃送出装置。塔底烷基化油经泵抽出,两次换热,再冷却至40℃送出装置。
流出物精制和产品分馏部分
目的是脱除酸脂(99.2%的硫酸+12%的NaOH)。
换热后的反应流出物进入酸洗系统,与酸在酸洗混合器内进行混合后,进入流出物酸洗罐,绝大部分酸脂被吸收。流出物烃类和酸在酸洗罐中分离,烃类流出物酸含量低于10ppm,酸则连续进入反应器作为催化剂使用。
酸洗后的流出物与循环碱液在流出物碱洗混合器中混合后,进入碱洗罐脱除微量酸,进入流出物水洗罐含硫酸钠和亚硫酸盐的碱水经泵从罐底抽出换热后送回混合器入口循环使用。
反应部分
烯烃与异丁烷的烷基化反应,主要是在酸催化剂的作用下,二者通过中间反应生成汽油馏分的过程。
C4馏分与脱异丁烷塔来的循环异丁烷混合经换冷至11℃,经脱水器脱除游离水(10ppm)后与闪蒸罐来的循环冷剂直接混合,温降至3℃分两路进入烷基化反应器。反应完全的酸-烃乳化液经一上升管直接进入酸沉降器,分出的酸液循下降管返回反应器重新使用,90%浓度废酸排至废酸脱烃罐,从酸沉降器分出的烃相流经反应器内的取热管束部分汽化,汽-液混合物进入闪蒸罐。净反应流出物经泵抽出经换热、加热至约31℃去流出物精制和产品分பைடு நூலகம்部分继续处理。循环冷剂经泵抽出送至反应进料线与原料C4直接混合,从闪蒸罐气相空间出来的烃类气体至制冷压缩机。
烷基化过程
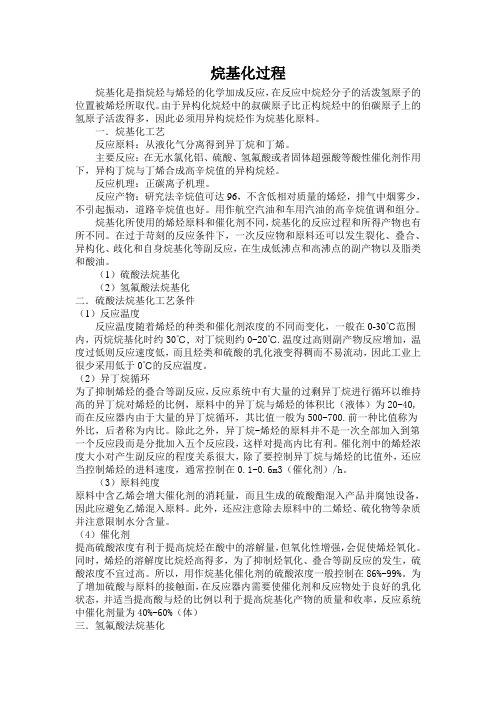
烷基化过程烷基化是指烷烃与烯烃的化学加成反应,在反应中烷烃分子的活泼氢原子的位置被烯烃所取代。
由于异构化烷烃中的叔碳原子比正构烷烃中的伯碳原子上的氢原子活泼得多,因此必须用异构烷烃作为烷基化原料。
一.烷基化工艺反应原料:从液化气分离得到异丁烷和丁烯。
主要反应:在无水氯化铝、硫酸、氢氟酸或者固体超强酸等酸性催化剂作用下,异构丁烷与丁烯合成高辛烷值的异构烷烃。
反应机理:正碳离子机理。
反应产物:研究法辛烷值可达96,不含低相对质量的烯烃,排气中烟雾少,不引起振动,道路辛烷值也好。
用作航空汽油和车用汽油的高辛烷值调和组分。
烷基化所使用的烯烃原料和催化剂不同,烷基化的反应过程和所得产物也有所不同。
在过于苛刻的反应条件下,一次反应物和原料还可以发生裂化、叠合、异构化、歧化和自身烷基化等副反应,在生成低沸点和高沸点的副产物以及脂类和酸油。
(1)硫酸法烷基化(2)氢氟酸法烷基化二.硫酸法烷基化工艺条件(1)反应温度反应温度随着烯烃的种类和催化剂浓度的不同而变化,一般在0-30℃范围内,丙烷烷基化时约30℃,对丁烷则约0-20℃.温度过高则副产物反应增加,温度过低则反应速度低,而且烃类和硫酸的乳化液变得稠而不易流动,因此工业上很少采用低于0℃的反应温度。
(2)异丁烷循环为了抑制烯烃的叠合等副反应,反应系统中有大量的过剩异丁烷进行循环以维持高的异丁烷对烯烃的比例,原料中的异丁烷与烯烃的体积比(液体)为20-40,而在反应器内由于大量的异丁烷循环,其比值一般为500-700.前一种比值称为外比,后者称为内比。
除此之外,异丁烷-烯烃的原料并不是一次全部加入到第一个反应段而是分批加入五个反应段,这样对提高内比有利。
催化剂中的烯烃浓度大小对产生副反应的程度关系很大,除了要控制异丁烷与烯烃的比值外,还应当控制烯烃的进料速度,通常控制在0.1-0.6m3(催化剂)/h。
(3)原料纯度原料中含乙烯会增大催化剂的消耗量,而且生成的硫酸酯混入产品并腐蚀设备,因此应避免乙烯混入原料。
- 1、下载文档前请自行甄别文档内容的完整性,平台不提供额外的编辑、内容补充、找答案等附加服务。
- 2、"仅部分预览"的文档,不可在线预览部分如存在完整性等问题,可反馈申请退款(可完整预览的文档不适用该条件!)。
- 3、如文档侵犯您的权益,请联系客服反馈,我们会尽快为您处理(人工客服工作时间:9:00-18:30)。
目录1概述 (3)2 工艺设计技术方案 (4)3 原料及产品性质 (5)4 装置物料平衡 (7)5 工艺流程简述 (8)6 主要设备选型说明 (14)7 消耗指标及能耗 (14)8 装置定员 (21)9 环境保护 (22)10 职业安全卫生 (23)11 装置对外协作关系 (29)12 设计执行的标准目录 (31)1 概述该烷基化装置采用硫酸烷基化工艺,公称规模为16万吨/年.1.1 设计依据1.1。
2 DUPONT 公司提供的硫酸烷基化工艺包;1。
2 装置概况1.2.1装置原料:本装置原料为上游MTBE装置提供的未反应碳四馏分、加氢裂化液化气,前处理所需的少量氢气由制氢装置提供。
1.2.2装置建设规模:根据MTBE装置所提供的液化气量及液化气中的烯烃含量,实际可生产烷基化油约13.13万吨/年,本装置设计规模为16万吨/年烷基化油。
1。
2。
3装置建设性质:在酸催化剂的作用下,液化气中的异丁烷与烯烃反应生成高辛烷值汽油调合组分-烷基化油.1。
3设计原则:1)选用成熟可靠的工艺技术和控制方案,使设计的装置达到安、稳、长、满、优操作。
2)优化工艺流程并推广应用新工艺、新技术、新设备、新材料,降低生产成本同时降低装置能耗,提高产品质量档次。
3)在保证技术先进、装置生产安全可靠的前提下,降低能耗并尽量降低工程造价,节省投资。
4)为了降低工程投资,按照“实事求是、稳妥可靠”的原则,提高国产化程度,所需设备立足国内解决,只引进在技术、质量等方面国内难以解决的关键设备、仪器、仪表。
5)采用DCS 集中控制,优化操作,以提高装置的运转可靠性,提高产品收率和质量。
6)严格执行国家、地方及主管部门制定的环保和职业安全卫生设计规定、规程和标准,减少“三废”排放,维护周边生态环境,实行同步治理,满足清洁生产的要求.1。
4 装置组成:本装置由原料精制、反应、流出物精制和产品分馏、化学处理等几部分组成。
装置运行时数和操作班次:装置年开工时间按8400小时计,操作班次按四班三倒。
1.5 设计范围本设计范围为本装置所涉及的设备、管道、仪表、配电等,装置有关分析化验项目由中心化验室承担.2 工艺设计技术方案烷基化装置是以液化气中的烯烃及异丁烷为原料,在催化剂的作用下烯烃与异丁烷反应,生成烷基化油的气体加工装置。
本装置包括原料加氢精制和烷基化两部分.原料加氢精制的目的是通过加氢脱除原料中的丁二烯。
因为丁二烯是烷基化反应中主要的有害杂质,在烷基化反应过程中,丁二烯会生成多支链的聚合物,使烷基化油干点升高,酸耗加大。
脱除原料中的丁二烯采用选择性加氢技术,该技术已在国内多套烷基化装置上应用,为国内成熟技术。
由于MTBE装置所提供的未反应碳四馏分中烷烯比不足,需补充部分异丁烷,因此引入部分加氢裂化液化气,与加氢后的碳四馏分混合进入脱轻烃塔,分离出满足烷烯比要求的碳四馏分.以液体酸为催化剂的烷基化工艺可分为硫酸烷基化和氢氟酸烷基化,两种工艺都为成熟的技术,在国内外都有广泛应用。
本设计采用的是DUPONT公司的硫酸烷基化工艺,该技术具有如下特点:1)采用反应流出物致冷工艺:利用反应流出物中的液相丙烷和丁烷在反应器冷却管束中减压闪蒸,吸收烷基化反应放出的热量。
反应流出物经过气液分离后,气相重新经压缩机压缩、冷凝,抽出部分丙烷后,再循环回反应器。
与闭路冷冻剂循环致冷或自冷式工艺相比,流出物致冷工艺可使得反应器内保持高的异丁烷浓度,而从脱异丁烷塔来的循环异丁烷量最低。
此外,在这种致冷流程中采用了节能罐,使部分富丙烷物流在中间压力下闪蒸汽化后进入压缩机第二段,从而节约能量。
2)STRATCO公司反应部分循环异丁烷与烯烃预混合后再经喷嘴进入反应器,酸烃经叶轮搅拌,在管束间循环,机械搅拌使酸烃形成具有很大界面的乳化液,烃在酸中分布均匀,减小温度梯度,减少副反应发生.3)反应流出物采用浓酸洗、碱水洗工艺:反应流出物中所带的酯类如不加以脱除,将在下游异丁烷塔的高温条件下分解放出SO2,遇到水份,则会造成塔顶系统的严重腐蚀。
因此,必须予以脱除,本装置采用浓酸洗及碱洗的方法进行脱除,与传统的碱洗相比,能有效脱除硫酸酯,即用99.2%的硫酸洗后再用12%的NaOH 脱除微量酸.3 原料与产品性质3。
1 原料3。
1.1 MTBE 装置所提供的液化气组成如下:2.1.2 加氢裂化液化气组成如下:3。
2 产品3.2.1 烷基化油:雷氏蒸气压RVP 0.030MPa比重 0。
69辛烷值 RON(C) 96.8±0.5MON(C) 93。
3±0.5 3。
2。
2 丁烷馏分:组分 wt%nC4H10 94。
00iC4H10 3。
86C5H12 2。
14合计 100.003。
2.3 循环异丁烷:组分 wt%C3H8 1.98iC4H10 87。
86nC4H10 10。
08C5H12 0.08合计 100.003.3 催化剂及化学药剂3.3。
1 加氢催化剂型号 LST-02外观灰褐色条状尺寸 mm φ(2.0∼2。
5)×5∼10堆比重 g/ml 0⋅90±0⋅05破碎强度 N/cm ≥200比表面 m2/g 100∼150比孔容 ml/g 0.30±0。
023。
3.2 硫酸H2SO4 99。
2%3.3.3活性炭4 装置物料平衡4.1根据MTBE 装置及加氢裂化装置所提供的液化气组成,本装置的物料平衡如下(按设计规模):5 工艺流程说明5。
1 工艺流程简述本装置由原料加氢精制、反应、致冷压缩、流出物精制和产品分馏及化学处理等几部分组成,现分别简述如下:5.1。
1 原料加氢精制自MTBE 装置来的未反应碳四馏分经凝聚脱水器(104—D-105)脱除游离水后进入碳四原料缓冲罐(104-D-101),碳四馏分由加氢反应器进料泵(104-P-101)抽出经碳四-反应器进料换热器(104—E-104)换热后,再经反应器进料加热器(104-E—101)加热到反应温度后与来自系统的氢气在静态混合器(104—M-101)中混合,混合后的碳四馏分从加氢反应器(104—R-101)底部进入反应器床层。
加氢反应是放热反应。
随混合碳四带入的硫化物是使催化剂失活的有害杂质。
催化剂失活后可用热氢气吹扫使其活化.反应后的碳四馏分从加氢反应器顶部出来与加氢裂化液化气混合.自液化气双脱装置过来的加氢裂化液化气进入加氢液化气缓冲罐(104—D—102),液化气由脱轻烃塔进料泵(104—P—102)抽出与反应器顶部出来的碳四馏分混合后进入脱轻烃塔(104—C-101)。
脱轻烃塔(104-C-101)的任务是脱去碳四馏分中的碳三以下的轻组分,同时将二甲醚脱除.脱轻烃塔是精密分馏的板式塔,塔顶压力控制在1。
7MPa(g).塔顶排出的轻组分经脱轻烃塔顶冷凝器(104—E-103)冷凝冷却后,进入脱轻烃塔回流罐(104—D-103)。
不凝气经罐顶压控阀后进入全厂燃料气管网。
冷凝液由脱轻烃塔回流泵(104-P-103)抽出,一部分做为脱轻烃塔(104—C-101)顶回流,另一部分作为液化气送出装置。
塔底抽出的碳四馏分经碳四进料换热器(104—E—104)与原料换热后再经碳四馏分冷却器(104-E—105)冷至40℃进入烷基化部分。
塔底重沸器(104-E—102)采用0.45MPa 蒸汽加热,反应器进料加热器使用1。
0MPa蒸汽加热,凝结水都送至凝结水回收罐(104-D-304)回收。
碳四馏分经加氢精制后,丁二烯含量≤100ppm,二甲醚≤100ppm。
5。
1。
2 反应部分碳四馏分中的烯烃与异丁烷的烷基化反应,主要是在硫酸催化剂的存在下,二者通过某些中间反应生成汽油馏份过程。
从原料加氢精制部分过来的碳四馏分与脱异丁烷塔(104-C—201)过来的循环异丁烷混合后,与反应器净流出物在原料—流出物换热器(104—E—201)中换冷至约11℃,进入原料脱水器(104-D-201)。
换冷后的碳四馏分中的游离水在此被分离出去,从而使原料中的游离水含量降至10ppm(重)。
脱除游离水的混合碳四馏分与来自闪蒸罐(104-D—203)的循环冷剂直接混合并使温度降低至约3.0℃后分两路分别进入烷基化反应器(104-R-201A/B)。
烷基化反应器是装有内循环夹套、取热管束和搅拌叶轮的压力容器,为STRATCO 公司的专利产品.在反应器操作条件下,进料中的烯烃和异丁烷在硫酸催化剂存在下,生成烷基化油。
反应完全的酸-烃乳化液经一上升管直接进入酸沉降器(104—D-202A/B),并在此进行酸和烃类的沉降分离,分出的酸液从下降管返回反应器重新使用。
反应-沉降系统中酸的循环是借助在上升管和下降管中物料的比重差自然循环的,90%浓度的废酸自酸沉降器排放至废酸脱烃罐.本装置设有2 台反应器,为并联操作,即混合碳四分两路分别进入104-R-201A和104—R—201B。
而做为催化剂的硫酸为串联操作,即补充的新酸进入104-D—202A,从104-D—202A 出来的中间酸进入104-D—202B,90%的废酸从104-D—202B 排出。
两组反应—沉降系统也可单独操作。
从酸沉降器分出的烃相经压力控制阀降压后,流经反应器内的取热管束部分汽化,吸收热量脱除反应热。
汽-液混合物进入闪蒸罐(104-D-203)。
闪蒸罐是一台带有中间隔板并有共同分离空间的卧式容器。
隔板一侧供反应流出物进行气液分离,另一侧供循环冷剂进行汽-液分离。
净反应流出物用流出物泵(104—P-201)抽出在104—E—201 与原料碳四换冷,加热至约31℃去流出物精制和产品分馏部分继续处理.循环冷剂则以循环冷剂泵(104-P-202A/B)抽出送至反应器进料管线与原料碳四直接混合。
从闪蒸罐气相空间出来的烃类气体至致冷压缩机(104-K—201)。
闪蒸罐有一个分酸罐(104—D—208)置于该容器下方,可借助分酸罐上的液面计观察酸烃界面。
正常情况下,分酸罐的酸位很低。
当反应器内的取热管束发生泄漏时,酸罐内将会发现大量硫酸。
99.2%的新鲜浓硫酸先连续进入流出物精制和产品分馏部分的流出物酸洗罐洗涤反应流出物,然后再补入反应器.随浓硫酸进入反应器的酸酯,在反应器中参加反应,增加烷基化油的产率。
5。
1。
3 致冷压缩部分反应器的进料温度要求为3~6.0℃,这一温度是由在反应器进料中混入低温循环冷剂来实现的.为此,需有一套相应的致冷系统来满足这一要求。
此外,为达到烷基化装置内的丙烷和异丁烷进出量平衡,特别是防止丙烷在装置内设备中的积聚,还需要从致冷部分引出一股抽出丙烷物流送出装置。
闪蒸罐气相空间的平衡蒸汽,由挡板两侧汇集至出口管,再进入压缩机。
致冷压缩机为中间加气式两级离心压缩机,由电机驱动。
从104—D-203 来的烃类气体进入压缩机一级入口,补充进入二级入口的气体来自节能罐(104-D-207)顶部。