过程检验程序
过程检验和试验程序

4.2各阶段操作者,应根据质量要求和质量计划进行自检、合格品和不
合格品须及时分隔并予以记录。
4.3在每阶段的检验或试验完成并获得相关人员认可之后,才能执行下
阶段的工作任务。
4.4如在工作中发现不合格现象,应及时提出,相关人员应视情况决定
是否发出更正行动(CAR)。
4.5如在工作中发现不合格品,则按《不合格品的控制程序》处理。
标题:过程检验和试验程序页码
1.0目的:
此文指导工程过程按规定的要求进行检验或试验,确保过程受控。
2.0范围:
此文适用于工程过程中各阶段的工序检验或试验。
3.0职责:
3.1总工程负责重大质量问题的决定。
3.2工程部经理负责技术方案及质量标准的审定、质量问题的处理及决
定。
3.3项目负责人负责质量检验和标准的设定、质量问题的处理及决定。
4.6必要时,可安排业主方面的人员参加检验或试验,并做好记录。
5.0参考文件
5.1《项目质量计划》
5.2《设计控制程序》
5.3《图纸审核程序》
5.4《软件编程控制程序》
5.5《设备成套/安装控制程序》
5.6《现场安装/调试控制程序》
5.7《纠正和预防措施程序》
5.8《静态测试指引》
6.0记录
6.1各质量记录文件
3.4项目工程师负责质量检验工作的执行及记录,质量问题的处理。
3.5工程秘书负责质量记录的统计及归档。
4.0程序:
4.1工程各阶段必须依据项目质量计划的任务分解表和《设计控制程序》
《静态测试指引》、《/调试控制程序》的要求,执行阶
施工过程检验程序

施工过程检验程序一、过程检验1.项目经理部主任工程师组织现场测量人员及公司技术质量部人员参与对建筑物定位、定高部位的检查, 由技术、测量、复测、施测人员签认, 由项目经理部主任工程师安排质量员将检查结果上传至项目综合管理信息系统相应模块。
2.公司技术质量部、建设、勘察、设计、监理单位参加验槽检查, 由项目经理部主任工程师填写《地基验槽记录》, 建设、勘察、设计、监理单位的相关人员签字确认, 并加盖单位公章。
由项目经理部主任工程师安排质量员将检查记录上传至项目综合管理信息系统相应模块。
3.公司技术质量部参加对单位(子单位)工程的主要部位(地基与基础、主体结构), 重点部位隐蔽工程和单位(子单位)工程的验收。
4.隐蔽工程检查由单位工程工长自检合格后, 报项目技术质量组对隐蔽部位进行检查。
工长填写《隐蔽工程检查记录》, 经监理单位检查后, 由监理工程师、施工项目经理部/专业公司技术负责人、质检员、工长签认, 标明此部位属合格状态。
由项目经理部主任工程师安排质量员将检查结果上传至项目综合管理信息系统相应模块。
5.需进行预检的部位由工长自检合格后, 报项目质量组对预检部位进行检查, 工长填写《预检记录》, 质检员、工长签认。
由项目经理部主任工程师安排质量员将检查结果上传至项目综合管理信息系统相应模块。
6.在施工操作过程中或工序完工后, 由所承担该项工程的工长组织班组进行自检、互检、交接检, 班组质检员负责填写《自检、互检记录》、《交接检记录》, 项目经理部质检员负责督促检查。
7、检验批工程完工后, 项目经理部/专业公司应对检验批的主控项目和一般项目的质量检验合格, 具有完整的施工操作依据、质量检查记录, 质量符合要求后由工长填写《检验批质量验收记录》, 由项目经理部/专业公司质量检查员签认后, 交监理工程师组织施工项目经理部/专业公司质检员、工长进行验收并签认。
8、分项工程完工后, 由项目经理部/专业公司质量检查员填写《分项工程质量验收记录》, 由主任工程师检查后签认, 交监理工程师签认。
过程检验程序

检验控制程序青海金安建设工程有限公司1.目的在生产过程中,对每道工序加工的零部件、半成品,按产品图样、工艺文件规定的技术要求进行检验,以保证不合格零部件、半成品不流入下道工序。
2.适用范围本程序适用于本公司产品制造中工序检验工作,也适用于外协生产的工序检验工作。
3.职责3.1 研发部制定各工序检验质量标准,编写工艺文件,绘制产品图样。
3.2 品管部负责生产过程产品的检验和试验,并做检验记录。
3.3 生产部指导、督促操作工作好自检工作。
4.工作程序、方法4.1 各工序操作工根据图纸、作业指导书等工艺文件规定的技术要求进行加工。
4.2 自检操作工加工完零件后,应按图纸、工艺文件的技术要求进行自我检验。
车间主任、班组长负责指导、督促操作工作好自检工作。
4.3 首检质检人员对木工加工的由设备的定位装置和模具决定其质量的零部件进行首检试验(电锯工序由操作工自检后,将结果记录与《工序流转单》上),以避免批量返工或不合格。
首检检验合格后,可继续加工;如首检检验不合格,应返工或重新加工首件,只只检验合格后才可加工其余零部件。
首检检验的结果应记录与《首件检验记录表》。
4.4 巡检质检人员应按照施工图及其他相关检验标准进行巡回检查。
巡检合格的可以继续操作。
发现不合格时,质检员应与操作工一起分析原因、制定措施,以便迅速调整,防止不合格品的再次发生。
4.5 终检4.5.1 操作工将完工的零部件整齐码放在机床或工作台旁的指定区域,并及时通知质检员报检。
4.5.2质检员接到报验后,即按照各工序检验质量标准进行终检,在《质量检验日报表》和工序流转单上记录终检结果,并按(检验和试验状态控制程序)的规定对检验后的产品进行标识,合格转入下道工序,不合格品则按《不合格品控制程序》的规定处理。
必要时采取纠正和预防措施。
4.6试装4.6.l当木工车间加工完成后,由装配工序操作工和质检员对经过检验合格的零件进行试装检查。
试装结果记录在《试装记录表》上。
机加工过程检验流程
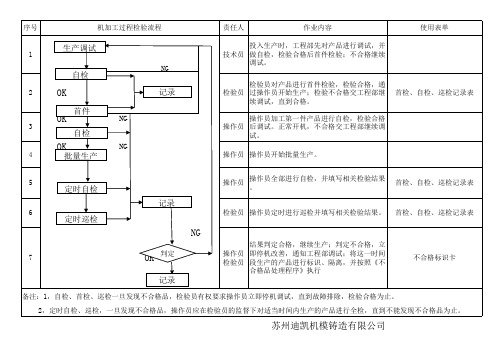
序号
机加工过程检验流程
责任人
作业内容
使用表单
1
生产调试 自检
NG
投入生产时,工程部先对产品进行调试,并 技术员 做自检,检验合格后首件检验;不合格继续 调试。 检验员对产品进行首件检验,检验合格,通 检验员 过操作员开始生产;检验不合格交工程部继 续调试,直到合格。 操作员加工第一件产品进行自检,检验合格 操作员 后调试。正常开机,不合格交工程部继续调 试。 操作员 操作员开始批量生产。 操作员全部进行自检,并填写相关检验结果 。
不合格标识卡
记录
备注:1,自检、首检、巡检一旦发现不合格品,检验员有权要求操作员立即停机调试,直到故障排除,检验合格为止。 2,定时自检、巡检,一旦发现不合格品,操作员应在检验员的监督下对适当时间内生产的产品进行全检,直到不能发现不合格品为止。
苏州迪凯机模铸造有限公司
2
OK OK OK
批量生产
首件
记录 NG NG
首检、自检、巡检记录表
3
自检
4ቤተ መጻሕፍቲ ባይዱ
5
定时自检
记录
操作员
首检、自检、巡检记录表
6
定时巡检
检验员 操作员定时进行巡检并填写相关检验结果。
首检、自检、巡检记录表
NG
7
OK
判定
结果判定合格,继续生产;判定不合格,立 操作员 即停机改善,通知工程部调试;将这一时间 检验员 段生产的产品进行标识、隔离,并按照《不 合格品处理程序》执行
过程检验作业指导书
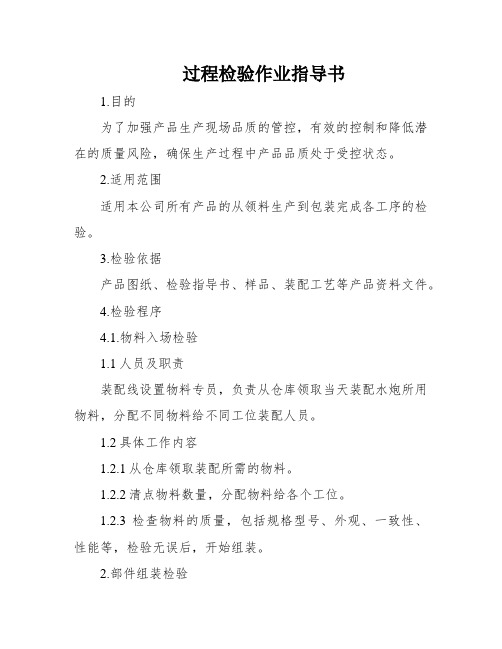
过程检验作业指导书1.目的为了加强产品生产现场品质的管控,有效的控制和降低潜在的质量风险,确保生产过程中产品品质处于受控状态。
2.适用范围适用本公司所有产品的从领料生产到包装完成各工序的检验。
3.检验依据产品图纸、检验指导书、样品、装配工艺等产品资料文件。
4.检验程序4.1.物料入场检验1.1人员及职责装配线设置物料专员,负责从仓库领取当天装配水炮所用物料,分配不同物料给不同工位装配人员。
1.2具体工作内容1.2.1从仓库领取装配所需的物料。
1.2.2清点物料数量,分配物料给各个工位。
1.2.3检查物料的质量,包括规格型号、外观、一致性、性能等,检验无误后,开始组装。
2.部件组装检验2.1自检装配人员每装配完成第一个部件后,进行自检合格后在装配剩余部分,整批装配完成后逐个进行自我检验,全部无误后,才能流到下一工序。
如果组装的部件有一部分部件组成,则装配人员需要对上一工序的部11件举行检验,合格后方能使用。
2.2互检装配人员在一批部件自检完成后,要求相邻工序装配人员或下一工序装配人员给做互检,互检完成后,检验人签字确认。
2.3巡检4巡检是出产过程中,检验员对出产出的产品举行巡回检验,质检员对产品举行抽样家宴,目的是为了避免成批不合格品的发生或工艺发生异常。
检验员对个生产工序产品品质状况进行巡回检查,在巡检过程中需特别注意物料加工的工位、常换人、有新人上岗的工位以及关键工位,如有发现异常及时通知生产管理负责人进行改善。
巡检过程中同时注意操作人员是否按照《作业指导书》进行操作,如发现操纵人未按照作业指导书进行操作,应立即要求作业人员改善。
检验员有权对不符合规定的操作,现场易引发质量问题和生产效率的操作,要求进行整改。
5.不合格的处理方法5.1由自检、互检发现的由装配人员引起的不合格品,由装配人员自行返工维修,返工后的产品需要重新检验。
返工返修仍然不能解决的,可以做报废处理。
5.2巡检发现不合格品,必须标识隔离零丁存放,举行集中同一处理。
过程检验程序(含表格)

过程检验程序(QC080000-2017)1.0目的:确保生产过程中在制品都符合品质要求,防止不良品流至下一工序而影响最终产品的质量。
2.0范围:适用于公司所有制程中的在制品。
3.0定义:3.1 IQC:进料检验3.2 IPQC:制程巡检3.3 PQC:制程抽检3.4 FQC:出货检验3.5 OQC:出货抽检4.0权责:4.1品管部主管:4.1.1详见《职责划分程序》;4.1.2制定品质目标及改善计划;4.1.3建立相关规范流程,使制定品质目标如期完成4.2 IPQC(制程巡检):4.2.1指导IPQC人员按各工序IPQC作业指导书及进行日常巡验工作,指导操作员按《作业指导书》进行生产制造。
4.2.2发现严重异常问题时,应及时按《纠正与预防措施程序》进行质量跟踪改善或按《特采控制程序》进行质量放行。
4.3 PQC(制程抽验):4.3.1按《MIL-STD-105E抽样计划》、《检验标准》及《量产技术规格书》进行品质检验。
4.3.2发现不良异常情况及时通过[异常单]向品管部汇报反馈,并按《不合格品控制程序》进行处理不合格品。
4.4 FQC(出货检验):4.4.1按《MIL-STD-105E抽样计划》、《检验标准》及《量产技术规格书》进行品质检验。
4.4.2发现不良异常情况及时通过[工艺异常单]向品管部汇报反馈,并按《不合格品控制程序》进行处理不合格品。
4.5 OQC(出货抽检):4.5.1按《成品及出货检验管理办法》、《检验标准》、《量产技术规格书》及《抽样计划》进行抽检;4.5.2发现不良异常情况及时通过[异常单]向品管部汇报反馈,并按《不合格品管理办法》进行处理不合格品。
4.5 统计员:4.5.1负责收集检验数据,并根据《统计分析控制程序》对数据进行汇总分析。
4.5.2对分析后的数据中出现的异常情况,按《纠正与预防措施程序》进行品质改善。
5.0内容: 5.1流程:流程 权责岗位使用表单IPQC 生产部 IPQC生产部检验人员 PQC FQC OQC 统计员 生产部 品管部《首件、过程作业检验记录表》《模块首检日报表》[IPQC 巡检报表][品管检验日报表][出货检验报告][纠正和预防措施处理单]制 造品质改善不良品汇总记录分析首检确认巡检自主检验过程抽检出货抽检入库抽检5.2内容:5.2.1首件确认:生产前必须经过首件确认,首件不合格或未进行首件确认严禁批量生产。
过程检验和试验程序
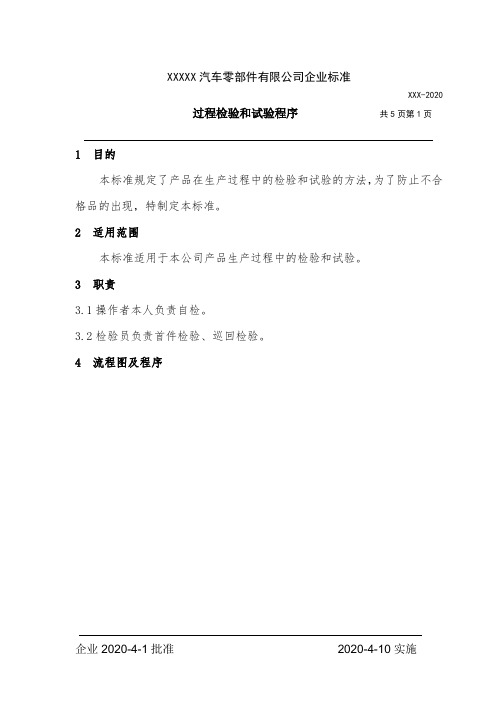
XXXXX汽车零部件有限公司企业标准
XXX-2020
过程检验和试验程序共5页第1页
1 目的
本标准规定了产品在生产过程中的检验和试验的方法,为了防止不合格品的出现,特制定本标准。
2 适用范围
本标准适用于本公司产品生产过程中的检验和试验。
3 职责
3.1操作者本人负责自检。
3.2检验员负责首件检验、巡回检验。
4 流程图及程序
企业2020-4-1批准2020-4-10实施
XXXXX-2020 第2页
企业2020-4-1批准2020-4-10实施
企业2020-4-1批准2020-4-10实施
企业2020-4-1批准2020-4-10实施
XXXXX-2020 第5页5 相关文件
首件检验单
巡回检验记录单
末件检验单
6 文件分发
本文件发至技术质保部、综合管理部、档案室。
起草人:XXX 校对人:XXX 共印3份。
过程检验程序范文

过程检验程序范文过程检验程序(Process Inspection Procedure)是一种用于评估制造过程中的产品质量和符合性的方法。
它通常由多个步骤和检查程序构成,以确保产品在制造过程中的各个阶段都符合规定的标准和要求。
以下将详细介绍过程检验程序的目的、步骤和实施要点。
一、目的二、步骤1.明确过程标准和要求:首先,制定和明确产品制造的过程标准和要求,包括工艺流程、关键控制点、质量指标、测试方法等。
这些标准和要求应该符合相关的规定和技术要求。
2.确定检验方法和时机:根据制造过程的特点和产品要求,确定适合的检验方法和时机。
可以采用物理测量、化学分析、非损伤测试等方法,以及在线检验、样品检验等时机。
3.建立检验记录和追踪表:建立适当的检验记录和追踪表,记录每个过程步骤的检验结果和相关数据。
这些记录和追踪表可以帮助评估过程的一致性和稳定性,并在需要时进行溯源和追溯。
4.执行过程检验:按照制定的过程标准和要求,执行过程检验并记录结果。
根据结果评估过程的符合性和质量稳定性,并及时发现和处理不符合要求的情况。
5.分析和改进过程:根据过程检验结果和评估情况,分析问题和改进过程。
如果发现问题和缺陷,需要采取适当的纠正措施和预防措施,以提高过程的质量和符合性。
6.监控和验证改进效果:监控改进后的过程,并验证改进效果。
通过比较改进前后的过程检验结果和评估情况,评价改进效果是否达到预期,并根据需要进行进一步优化和改进。
三、实施要点1.明确责任和权限:明确过程检验的责任和权限,包括负责人、检验人员和相关部门。
每个人都应了解和承担自己的责任,并有权采取必要的纠正和预防措施。
2.培训和宣传:针对过程检验程序的实施要求和方法,进行培训和宣传。
确保每个人都了解和理解过程检验的重要性和目的,并掌握必要的技能和知识。
3.合理分配资源:合理分配人力、物力和财力资源,以支持过程检验程序的实施。
确保有足够的检验设备、工具和材料,并充分利用现有的质量管理系统和信息技术手段。
过程检验程序

PQC
流程
等级
目标
输入
作业方法描述
输出
信息
时效/反馈
职责
A
9艺卡》
3.《图纸》
4.样板
5.《抽样方法规定》
5.3过程巡检
5.3.1
PQC应在过程控制中,利用《统计技术(SPC)管理程序》对特殊性进行分析,并由车间主任对过程进行分析。
1.X(Bar)~R图
2.X(Bar)—S图
车间
●
PQC
A
98%
1.《过程检验报告》(首检)
——不合格
5.1.2
生产车间应对批准为不合格的首件进行原因分析,进行设备的再次调试,必要时提交《质量异常报告》及首件检验报告作为附页,召集相关部门讨论并分析对策。
1.《质量异常报告》
品质科科长(含副)
●
车间
A
98%
1.《过程检验报告》(首检)
5.1.3
PQC应将《首件检验报告》的不合格次数进行统计,并分析《首检检验一次合格率》
《首检检验一次合格率》
车间
持续发展办
每月5日前
PQC
A
96%
1.《工艺卡》
2.样板
3.图纸
5.2自主检验:
5.2.1
在操作过程中,在有自主检验规定时,操作员应按《工艺卡》及相关文件做产品检验,并做《过程检验报告》(自检)。《过程检验报告》(自检)在操作时间有矛盾时可由PQC协助填写,但操作员必需签名确认。
车间主任
●
FQC
●
●
1.《过程转序检验报告》
5.5.2
《过程转序检验报告》由QE审核。
《过程转序检验报告》
——审核
施工过程质量检验工作程序

施⼯过程质量检验⼯作程序施⼯过程质量检验⼯作程序过程质量检验主要包括班组⾃检、质检员专职检、专业施⼯员间交接检、监理、建设单位参与的隐蔽⼯程检验、公司定期检验,分项、分部评定以及中间验收等程序:班组⾃检施⼯员应依照作业指导书、规范、规程和图纸设计要求等在⼯序开始施⼯前以书⾯形式对班组进⾏操作⼯艺,施⼯⽅法、次序等技术交底,班组应严格按照技术要求进⾏施⼯,在⼯序施⼯过程,专业施⼯员应时刻对班组操作⼯艺,施⼯⽅法进⾏监督检查和指导;在施⼯⼯序完成后,专业施⼯员应组织班组长及操作者按验评规范进⾏⾃检,做好⾃检记录。
质检员专职检专业施⼯员组织的⾃检合格后,由施⼯员整理好相关的质保资料提交质检员检查。
在项⽬技术管理组织下,质检员会同施⼯员,班组长按照验评规范要求进⾏专职检验。
专职检验合格后,才能转⼊下道⼯序施⼯。
同时应做好专职检记录,并将质保资料交技术内业员保管。
交接检在施⼯过程中,开展“三⼯序”活动,即“检查上道⼯序,保证本道⼯序,服务下道⼯序”,实现对⼯序检验的控制。
⼯序转换应在⾃检、专职检合格⼿续基础上,由本道专业施⼯员组织下道⼯序专业施⼯员、班组长及相关专业的施⼯员进⾏交接检验和交底,并办理交接⼿续、填写《⼯序⾃检、专职检、交接检记录》在不同⼯种进⾏交接和转换时,应办理交接会签⼿续,填写会签单。
如砼浇筑前的会签。
隐蔽⼯程检验隐蔽⼯程在隐蔽前,应由质检员先⾏检验。
检验合格后,由施⼯员填写报验单,向监理(业主)申请报验,经监理(业主)代表验证同意后,办理《隐蔽⼯程验收记录》的签证⼿续,⽽后⽅可隐蔽。
技术复核在每⼀个施⼯过程中,均要对轴线和标⾼以及预埋件,预留孔洞等进⾏技术复核。
由施⼯员进⾏放样,质检员随后进⾏复核。
复核的具体情况应记录在《技术复核记录》表中,未经技术复核或检查不合格的不得予以放⾏。
公司定期检验在公司总⼯程师的主持下,公司技术部每⽉组织有关⼈员对本⼯程进⾏⼀次全⾯质量检查,对专职检进⾏核定,对⾃检、交接检、隐蔽⼯程检验、技术复核、技术内业资料等⼯作情况进⾏抽查。
过程检验程序
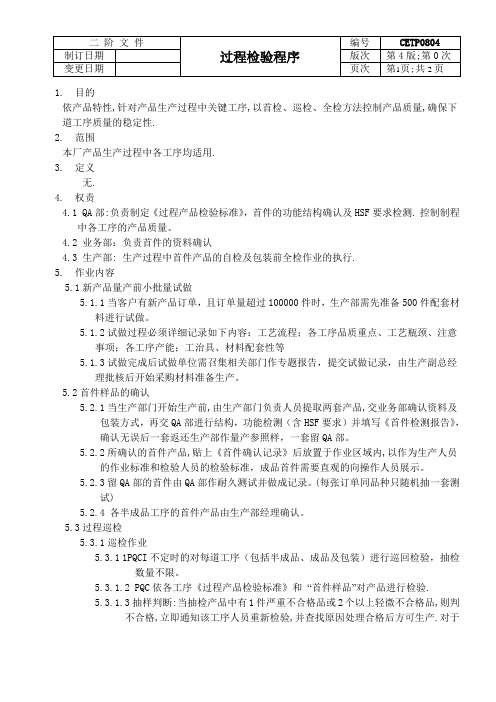
1.目的依产品特性,针对产品生产过程中关键工序,以首检、巡检、全检方法控制产品质量,确保下道工序质量的稳定性.2.范围本厂产品生产过程中各工序均适用.3.定义无.4.权责4.1 QA部:负责制定《过程产品检验标准》,首件的功能结构确认及HSF要求检测. 控制制程中各工序的产品质量。
4.2 业务部:负责首件的资料确认4.3 生产部: 生产过程中首件产品的自检及包装前全检作业的执行.5.作业内容5.1新产品量产前小批量试做5.1.1当客户有新产品订单,且订单量超过100000件时,生产部需先准备500件配套材料进行试做。
5.1.2试做过程必须详细记录如下内容:工艺流程;各工序品质重点、工艺瓶颈、注意事项;各工序产能;工治具、材料配套性等5.1.3试做完成后试做单位需召集相关部门作专题报告,提交试做记录,由生产副总经理批核后开始采购材料准备生产。
5.2首件样品的确认5.2.1当生产部门开始生产前,由生产部门负责人员提取两套产品,交业务部确认资料及包装方式,再交QA部进行结构,功能检测(含HSF要求)并填写《首件检测报告》,确认无误后一套返还生产部作量产参照样,一套留QA部。
5.2.2所确认的首件产品,贴上《首件确认记录》后放置于作业区域内,以作为生产人员的作业标准和检验人员的检验标准,成品首件需要直观的向操作人员展示。
5.2.3留QA部的首件由QA部作耐久测试并做成记录。
(每张订单同品种只随机抽一套测试)5.2.4 各半成品工序的首件产品由生产部经理确认。
5.3过程巡检5.3.1巡检作业5.3.1 1PQCI不定时的对每道工序(包括半成品、成品及包装)进行巡回检验,抽检数量不限。
5.3.1.2 PQC依各工序《过程产品检验标准》和“首件样品”对产品进行检验.5.3.1.3 抽样判断:当抽检产品中有1件严重不合格品或2个以上轻微不合格品,则判不合格,立即通知该工序人员重新检验,并查找原因处理合格后方可生产.对于前段时间生产的产品必须追查,按《不合格品控制程序》处理.检验后应及时将检验结果记录于《制程巡检记录》。
过程检验控制程序

并判定,并将检验项目及结果如实填写在《过程检验记录表》中。
5.2.3质量部注塑车间过程检验员在生产初始时必须按控制计划的要求对首件的克重进行监控,看是否符合控制计划要求,并记录在注塑过程检验记录单
5.3过程检验
8、流程图
输入
流程图
输出
过程所有者
生产计划、生产机台、物料
检验规范、待检产品、检验工具、空白表单
检验规范、待检产品、检验工具、空白表单
NG
OK
NG
OKቤተ መጻሕፍቲ ባይዱ
调机后生产
首件检验、首件称重、首件检验记录
报废/调换单
在制品流程卡、过程检验记录表
生产人员
过程检验员
生产人员
过程检验员
5、程序内容
5.1生产开始
车间接到“生产任务书”(或“生产计划单”)后,按“生产任务书”(或“生产计划单”)安排生产。
5.2首件检验
5.2.1质量部过程检验员在生产初始时必须按《生产过程控制程序》要求进行首件检验。如果首件检验合格,即通知生产车间进行正常生产。如果首件检验不合格,质量部立即通知生产车间停止生产并查找原因、分析,排除故障后重新送检。
5.3.1自主检验
生产过程中,作业人员在作业时及作业完成后应依据《生产作业指导书》对产品质量进行自主检验,操作人员应做到不接受不良品,不制造不良品,不传递不良品,如发现不合格应及时通知生产主管或班组长,由质检员确认,以确保不合格品不流入下一道工序
5.3.2巡回检验(定时抽检)
过程检验员应在其巡检过程中依控制计划、检验指导书及工程图纸对生产过程中各工序进行巡回检验,检验结果记录在《过程检验记录表》中。过程检验员在巡检过程中如发现质量问题,应根据严重程度进行不同处理,如为轻微质量问题应告之生产人员及时进行纠正,如为严重质量问题应立即与质量部主管、车间主管进行沟通,必要时上报公司领导,如质量问题严重无法及时解决,可以停止生产,报相关领导批准。待质量问题解决后,方可进行生产。检验中发现的不合格品,依照《不合格品控制程序》处理。
过程检验控制流程

责任部门
工作流程
工作标准
考核细则
操作人员
操作人员
操作人员
班组长
分厂
操作人员
班组长
操作人员
班组长
分厂
1.生产人员依据产品图纸、“技术通知单”、封样件、检验标准、作业指导书等产品要求,调试机器,开始试生产。
2.操作人员按照产品检验指导书、图纸、“技术通知单”、封样件等,对生产出来的前三片产品进行检验,合格后填写首检记录,通知班长进行确认合格后方可量产,若不合格,需重新调试,直至符合要求后方可进行量产。
3.若出现更换产品型号、产品异常调整后、5M1E变更的情况时,重新进行首件检验。
4.生产过程中操作人员,按首检项目2小时/次进行过程检验,发现不良品执行《生产过程不合格品处理流程》,并保持相应的检验记录。
5.每道工序的班长须对本班生产出的半成品/成品按《成品抽样方案》进行抽检,抽检确认合格后才能转入下道工序或临时库。
6.最后一道工序班组长依据产品检验标准对成品进行抽检,合格入库;若不合格,责任班组执行《生产过程不合格品处理流程》,并填写“成品入库检验记录”。
7.在所有的规定程序或检验完成之前,不得将产品放行或投入使用,必要时需得到分管副总或顾客的批准和许可,执行《制程不合格品处理流程》的规定。
8.分厂负责人或质量负责人,每周组织相关人员≥1次,对产品的过程控制、成品质量进行监督抽查。
9.分厂质量负责人每周、月对品质进行数据统计、分析,提出改进,分厂负责人审核。
未完成项,根据实际情况,考核20-50元/次/项。
过程输出:作业指导书、产品检验指导书、通用外观标准、首件确认单、检验记录、成品入库检验记录。
过程检验流程
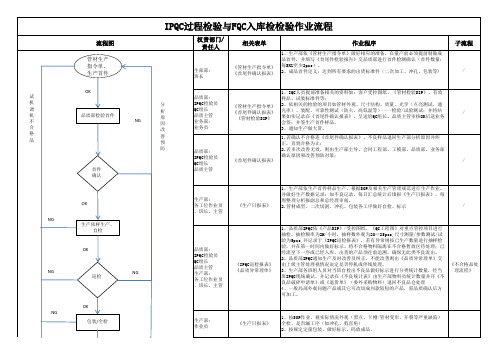
/
改
业务员
3、通知生产做大货。
善
1.若确认不合格连《首尾件确认报表》、不良样品退回生产部分析原因并纠
预
正,直到合格为止;
防
品质部:
2.若多次改善无效,则由生产部主导、会同工程部、工模部、品质部、业务部
IPQC检验员 QC组长
确认原因和改善预防对策; 《首尾件确认报表》
/
品质主管
1、生产部依生产首件样品生产、根据SOP及相关生产管理规范进行生产作业。
《不合格品处 理流程》
碎料员
品质部 生产部 仓库
《不良品破碎申请表》
1.生产部填写《不良品破碎申请表》生产经理审核 ,品质部负责核对物料质 量状况、仓库部负责数量清点和存放、上报副总经理以上批准执行。 2、数量大或批次多的不良,品质部统计,召开品质专题会议分析改善。
《不良品破碎 申请表流程》
《入库单》
子流程
/
1、IQC人员提前准备相关的资料如:客户受控图纸、《管材检验SIP》、有效
品质部:
样品、试装标准件等;
分 析 原 因
IPQC检验员 QC组长 品质主管 业务部:
《管材生产指令单》 《首尾件确认报表》
《管材检验SIP》
2、依相关的检验的项目如管材外观、尺寸结构、质量、光学(点亮测试、通 光率)、装配、可靠性测试(防火、高低温等)一一检验/试验测试;并将结 果如实记录在《首尾件确认报表》,呈送给QC组长、品质主管审核OK后送业务 会签;并签生产首件样品。
1、品质部IPQC依《产品SIP》/受控图纸、《QC工程图》对重点管控项目进行 抽检,抽检频率为2H/小时,抽样数外观为20∽25pcs,尺寸测量/参数测试/试 验为5pcs,并记录于《IPQC巡检报表》,若有异常则按已生产数量进行抽样检 验,并在第一时间内做好标示、将不合格物料隔离在不合格暂放区待处理;已 经流至下一序或已经入库、出货的产品须往前追溯,确保无此类不良流出。 2、品质部IPQC通知生产及时改善及纠正,不能改善则出《品质异常理单》交 由上级主管处理视情况决定是否停机或停线处理。 3、生产部各班组人员对当班自检出不良品做好标示进行分类统计数量,经当 班IPQC现场确认,并记录在《不良统计表》由生产部物料员统计数量并开《不 良品破碎申请单》或《退货单》(委外采购物料)退回不良品仓处理 4、一般局部外观问题产品或其它可改切成同款较短的产品,需品质确认后方 可加工。
过程检验规程

过程检验规程过程检验规程本规程旨在规定过程检验的方式和标准,以确保在生产过程中能够及时控制产品质量,防止不合格产品转入下道工序。
适用于本公司过程加工的产品。
职责分工如下:工序操作工:在加工过程中进行自检。
过程检验员:按照本规程的要求对加工过程进行首检、巡检和产品完工后的成品检。
定义如下:首件检验:在生产开始时上班或换班或工序因素调整后,对制造的第1件或前几件产品进行的检验,包括操作工自检、操作工互检和检验员首件确认。
巡回检验:检验员在生产现场按一定的时间间隔对有关工序的产品和生产条件进行监督检验。
半成品检:对全部加工活动结束的半成品零件进行的检验,包括验证前面各工序的检验是否已完成,检验结果是否符合要求,即对前面所有的检验数据进行复核。
运行程序如下:操作工首检:1.首次加工按图纸要求进行自检,确保合格。
2.向过程检验员报首检结果,并提交至少2件样件。
3.未经检验合格的首件不得继续加工或作业。
检验员首检:1.过程检验员对首次加工样件,按照《工序检验标准》要求进行首件检验。
2.首件检验合格后,过程检验员应对首件合格件打上确认标识,并保留到该批产品完工。
3.首检过程如实记录于【生产过程首检、巡检质量记录表】中。
操作工自检:1.首检合格后,过程加工可正式量产作业,操作工应在量产中保持一定频次的自检(每0.5小时一次自检),以保证质量的稳定。
2.个别装配难度大的零件或测量难度大的零件,首检按照操作工→车间管理人员→检验员,三方确认原则执行。
巡检:1.过程检验员应对量产过程进行巡检作业。
2.检验频次:2小时至少巡检1趟,每个机位产品最少抽样3-5件。
3.检验标准参见《工序检验标准》,根据实际情况对关键特性、重要特性、工艺上有特殊要求对下道工序的加工装配有重大影响的和内外部质量信息反馈中出现质量问题多的薄弱环节加强巡检频次。
在生产过程中,对于半成品的检验也是非常重要的。
在半成品的检验中,需要根据检验项目的标准要求进行检查,包括加工面是否有毛刺、砂眼、气孔、裂纹、塌陷、搭层、拉丝、伤痕等。
过程检验控制程序
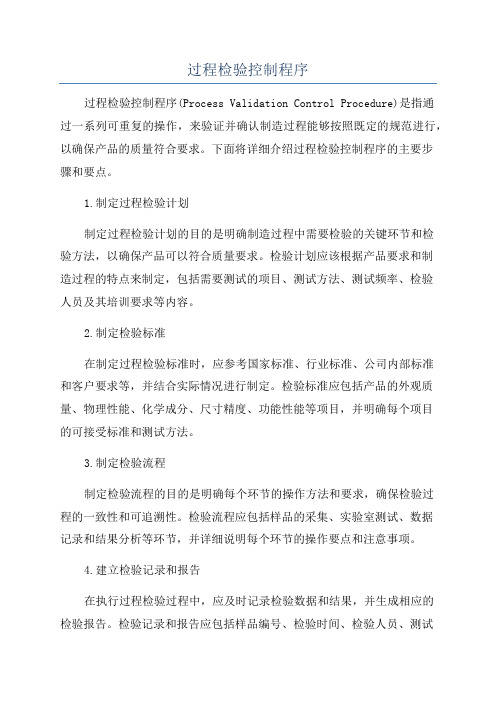
过程检验控制程序过程检验控制程序(Process Validation Control Procedure)是指通过一系列可重复的操作,来验证并确认制造过程能够按照既定的规范进行,以确保产品的质量符合要求。
下面将详细介绍过程检验控制程序的主要步骤和要点。
1.制定过程检验计划制定过程检验计划的目的是明确制造过程中需要检验的关键环节和检验方法,以确保产品可以符合质量要求。
检验计划应该根据产品要求和制造过程的特点来制定,包括需要测试的项目、测试方法、测试频率、检验人员及其培训要求等内容。
2.制定检验标准在制定过程检验标准时,应参考国家标准、行业标准、公司内部标准和客户要求等,并结合实际情况进行制定。
检验标准应包括产品的外观质量、物理性能、化学成分、尺寸精度、功能性能等项目,并明确每个项目的可接受标准和测试方法。
3.制定检验流程制定检验流程的目的是明确每个环节的操作方法和要求,确保检验过程的一致性和可追溯性。
检验流程应包括样品的采集、实验室测试、数据记录和结果分析等环节,并详细说明每个环节的操作要点和注意事项。
4.建立检验记录和报告在执行过程检验过程中,应及时记录检验数据和结果,并生成相应的检验报告。
检验记录和报告应包括样品编号、检验时间、检验人员、测试项目、测试结果和评定结论等内容,并有专门的存档和管理措施,以备后续的质量追溯和证明。
5.进行过程能力分析过程能力分析是对制造过程进行统计分析的一种手段,旨在评估制造过程是否具备稳定性和能够满足产品质量要求。
常用的过程能力指标有过程能力指数(Cp)、过程能力指数(Cpk)和过程能力比(CR)等。
通过过程能力分析,可以确定制造过程的容量以及需要改进的问题,以保证产品的稳定性和一致性。
6.建立纠正和预防措施当发现过程检验结果不合格时,应立即采取纠正措施,如调整工艺参数、更换设备等,以消除不合格因素,保证产品质量。
同时,还应进行原因分析,确定问题根源,并制定相应的预防措施,以防止不合格再次发生。
过程检验控制程序
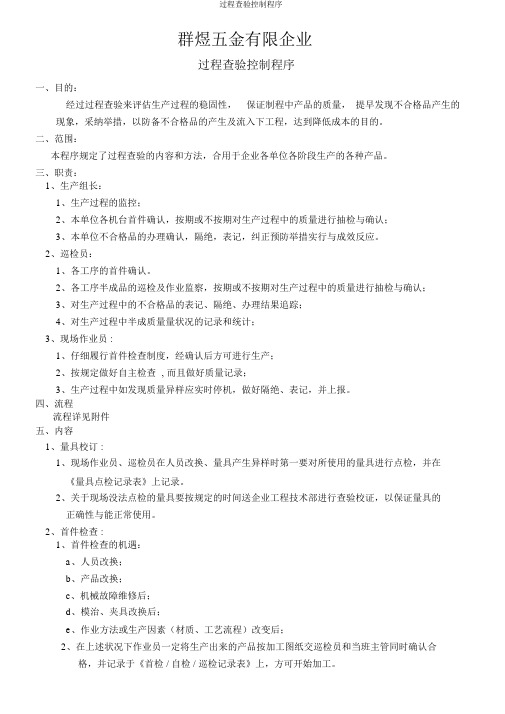
群煜五金有限企业过程查验控制程序一、目的:经过过程查验来评估生产过程的稳固性,保证制程中产品的质量,提早发现不合格品产生的现象,采纳举措,以防备不合格品的产生及流入下工程,达到降低成本的目的。
二、范围:本程序规定了过程查验的内容和方法,合用于企业各单位各阶段生产的各种产品。
三、职责:1、生产组长:1、生产过程的监控;2、本单位各机台首件确认,按期或不按期对生产过程中的质量进行抽检与确认;3、本单位不合格品的办理确认,隔绝,表记,纠正预防举措实行与成效反应。
2、巡检员:1、各工序的首件确认。
2、各工序半成品的巡检及作业监察,按期或不按期对生产过程中的质量进行抽检与确认;3、对生产过程中的不合格品的表记、隔绝、办理结果追踪;4、对生产过程中半成质量量状况的记录和统计;3、现场作业员 :1、仔细履行首件检查制度,经确认后方可进行生产;2、按规定做好自主检查 , 而且做好质量记录;3、生产过程中如发现质量异样应实时停机,做好隔绝、表记,并上报。
四、流程流程详见附件五、内容1、量具校订 :1、现场作业员、巡检员在人员改换、量具产生异样时第一要对所使用的量具进行点检,并在《量具点检记录表》上记录。
2、关于现场没法点检的量具要按规定的时间送企业工程技术部进行查验校证,以保证量具的正确性与能正常使用。
2、首件检查 :1、首件检查的机遇:a、人员改换;b、产品改换;c、机械故障维修后;d、模治、夹具改换后;e、作业方法或生产因素(材质、工艺流程)改变后;2、在上述状况下作业员一定将生产出来的产品按加工图纸交巡检员和当班主管同时确认合格,并记录于《首检 / 自检 / 巡检记录表》上,方可开始加工。
3、巡检员在首件检查时一定严格查对此刻生产产品工程图纸尺寸、产品状态、材质、商标与所检测的实物能否符合。
4、在未做首件确认的状况下禁止进行生产。
3、自主检查:1、生产部现场的各个工程在加工时,作业员一定依照《生产作业指导书》、《检查标准书》、标准样品对自己生产出来的产品随时进行自主检查,并将检查结果记录于《首检 / 自检 / 巡检记录表》上。
- 1、下载文档前请自行甄别文档内容的完整性,平台不提供额外的编辑、内容补充、找答案等附加服务。
- 2、"仅部分预览"的文档,不可在线预览部分如存在完整性等问题,可反馈申请退款(可完整预览的文档不适用该条件!)。
- 3、如文档侵犯您的权益,请联系客服反馈,我们会尽快为您处理(人工客服工作时间:9:00-18:30)。
对产品零件加工和成品装配的各工序的质量进行规定的检验和试验,防止不合格产品的流失,保证产品加工过程中符合标准要求。
⒉范围:
适用于指导产品零件加工,和成品装配过程中的工序检验工作。
⒊职责:
3·1 检验组是工序检验的归口管理部门,负责工序检验的组织实施工作。
3·2 技术部负责工序检验的技术标准等有关文件的编制工作。
4·2 过程检验
4·2·1 首检:
操作人员对上班加工的首件或首次产品,以及更换型号、工装、刀具后加工的首件产品,都要进行首检。首检按"作业指导书"的检验要求执行。操作者首检合格后交专职检验员进行确认。确认前,检验员首先核对仪表、标准件,确认无误后方可进行。首检一般查3——5件,有异常时加倍抽样。首检产品质量正常可继续加工,如发现问题则立即通知操作者进行机床、工装调整。出现异常现象时,向有关领导反馈,等候处理,首检记录由操作者负责在《工序质量检查记录表》上填写,检验员在"认可栏"签字确认。
3·3 生产部及有关产品加工车间负责工序的首检、自检等检验工作的管理。
⒋工作程序:
4·1·1 过程检验的策划:
技术部根据产品工艺流程图及产品质量特性等技术文件的要求,制定产品的工序检验流程,设立适当的工序检验点、站、网络,合理配置资源,生产部检验组按检验规程实施工序检验,以保证产品的工序加工质量。
4·1·2 生Biblioteka 车间要按作业指导书和工序检验要求组织有关人员进行首检、自检、完工检。工段长应确保工序产品质量,防止不合格品流入下工序。
4·2·2 巡检:
加工中,检验员按照检验规程要求的频次进行巡检,巡检间隔时间不大于二小时,对重点的工序或机床应当适当的增加巡检次数,巡检抽样一般为3——5件,异常时加倍抽样。巡检中发现异常波动,应立即通知操作者进行分析调整;如发现严重质量问题,按程序规定向有关部门及时反馈,等候处理。对巡检情况检验员要在《工序质量检验记录表》中做好记录。
⒍质量记录:
见清单。
4·2·3 工序间的下转验收:
工段或车间之间的转序检验,按下转产品的各项质量特性和技术条件由检验员进行抽检,抽检合格后和工段长共同在《工序流转单》中签字后方可后移交到下一道工序。
4·2·4 装前检:
为确保成品质量,对加工完毕的零件质量中的容易引起用户投诉的质量特性,在成品装配前实行100%全检。检验标准执行企业的内控标准。
4·2·6 自检:
各工序操作者要按工艺文件要求进行自检,操作者的自检记录须经检验员认可后方可生产。
⒌相关文件:
5·1 QS/TSB21301-2002 《不合格品控制程序》
5·2 QS/TSB21401-2002 《纠正和预防措施控制程序》
5·3 QS/TSB20801-2002 《产品标识和可追溯性控制程序》