汽车变速器箱体轻量化设计
某重型汽车变速箱箱体轻量化设计

( 上接第 3 9页)
[] 2 马香峰. 工业机 器人的操作机设计. 北京 : 工业 出版社 。 % 冶金 1 9 I 一
l一 一
喜
H
.h V e
cl cr e e
li
[] 3 谢存禧 , 张钝 机 器人技 术及 其应 用[ . M]北京 : 机械 工业 出版
社 . 05 20
董
十一 } . 一 _{ . . i
一
一 — 一
…一 — — m ’
[] 4 马香锋. 机器人机构学[ . M] 北京工业出版社 , 9 , 11 9 9
[] 自 机器人学[ 5 蔡 兴. M]. 清华大学 出 , O 版2O 0 [] 6 霍伟. 器人动力学与控制. 机 北京 : 高等教育 出版社 , O 2O O [] 7 范波涛 , 张 蒙特 卡洛方法在喷浆机 器人 工作空 间分析 中的应 用 [] 山东工业大 学学报 , 9 , ()1611 J. 1 92 2 : — 9 9 4 5 [] 8 郑建 惹 A A S D M 虚拟 样机技 术入 门与提 高[ M]. 械 工业 出版 机
表 2箱体结合面在倒档工况下受力情况表
用 O t t c计算得两种工况下 的位移和应力 , pS ut ir 计算 得2 个工况下的最大位移分别为6 1 x 0 Tn 12 . 1 1 和 .2 3 f X
1~ l , 0 nn最大单元应力分别为 5.4MP 和 1 . M a l 44 a 1 9 P 。 2
图2 变速 箱1 阶模 态振 形图
箱体 进行 模态 分 析, 求
解得第 1 自由模态 为 阶 56H , 4 z振形表现为离合
器盖轮廓 的伸缩变形振
乘用车车身零部件轻量化设计典型案例

乘用车车身零部件轻量化设计典型案例随着环境保护意识的提高和汽车工业的快速发展,乘用车的车身零部件轻量化设计成为了汽车制造业的一个重要课题。
轻量化设计不仅可以降低车辆的整体重量,提高燃油经济性,还可以减少对环境的影响。
下面将介绍几个乘用车车身零部件轻量化设计的典型案例。
1. 利用高强度材料:使用高强度的材料可以在不增加重量的情况下提高零部件的强度和刚性。
例如,许多乘用车现在采用了高强度钢材来替代传统的钢材。
高强度钢材可以提供相同强度的零部件,但重量更轻。
此外,还有一些先进的复合材料,如碳纤维增强塑料(CFRP)和铝合金等,也被广泛应用于车身零部件的制造中。
2. 结构优化设计:通过采用结构优化设计方法,可以将零部件的结构进行优化,以减少不必要的材料使用,从而降低整体重量。
例如,在车身的设计过程中,可以使用拓扑优化方法来确定最佳的结构形状,以最小化材料的使用量。
3. 部分集成设计:通过将不同的零部件进行部分集成设计,可以减少连接部件的数量,降低整体重量。
例如,一些车辆现在采用了一体成型的车顶和车身侧板设计,通过减少连接接口,可以减轻车身重量。
4. 利用轻量化技术:现代乘用车越来越多地采用一些先进的轻量化技术来设计车身零部件。
例如,采用铝合金替代传统的钢材可以显著减轻车身重量。
此外,还有一些其他的轻量化技术,如混合材料结构、可变厚度设计和3D打印等,也被广泛应用于乘用车的车身零部件设计中。
总之,乘用车车身零部件轻量化设计是当前汽车制造业的一个重要课题。
通过使用高强度材料、结构优化设计、部分集成设计和轻量化技术等方法,可以实现乘用车的轻量化,降低车辆油耗,减少对环境的影响。
这些典型案例的应用不仅可以提高汽车的性能和节能性,还可以为未来的汽车制造业发展提供借鉴和启示。
非公路用自卸车用变速器总成的轻量化设计与优化

非公路用自卸车用变速器总成的轻量化设计与优化随着城市建设的快速发展,非公路用自卸车在土石方工程、建筑工地和矿山等领域扮演着重要角色。
自卸车的可靠性和效率对工程进展至关重要。
变速器作为自卸车传动系统的核心部件之一,承担着变速和传递动力的重要任务。
为了提高非公路用自卸车的效率和降低能耗,轻量化设计与优化成为了变速器总成设计的重要方向。
轻量化设计是指在满足结构强度和耐久性的前提下,通过降低变速器总成的质量,实现整车质量的减轻,从而提高自卸车的搬运能力和燃油经济性。
在进行轻量化设计时,需综合考虑如下几个方面:首先,选用轻质材料。
合理选择具有高强度和轻质化特性的材料,如高强度钢、铝合金和碳纤维等。
这些材料具有优异的强度和刚度,能够在减轻总成质量的同时确保结构的稳定性和安全性。
其次,优化设计。
通过对各部件的结构和布局进行优化设计,可以减少零件数量和材料消耗。
例如,采用共享部件设计,将一些功能相似的部件进行合并或结构化设计,从而减少总成的重量和体积。
第三,运用先进的制造技术。
现代制造技术的应用可以提高工艺精度和表面质量,减少加工余量和材料浪费。
如采用数控机床加工、激光切割和精密压铸等技术,可以有效地降低材料消耗和制造成本。
最后,结构强度分析与优化。
通过有限元分析等工程手段,对变速器总成的结构强度进行精确计算和预测。
在此基础上,通过合理的结构调整和优化设计,提高变速器总成的强度和刚性,实现轻量化设计的目标。
轻量化设计与优化的实施有助于非公路用自卸车的性能提升和能源利用效率的提高。
根据实际需求和市场竞争,我们还可以从以下几个方面进行变速器总成的轻量化设计和优化:首先,采用智能控制技术。
利用汽车电子控制系统,可以实现变速器的智能化操作和优化控制。
通过智能传感器和控制单元的配合,可以根据车速、负载和工况等因素,实时调整变速器的工作模式和转速,提高传动效率和燃油利用率。
其次,引入先进的摩擦材料和润滑技术。
在摩擦片和齿轮副等关键部位应用新型的高温耐磨材料和低摩擦系数润滑材料,可以减少能量损耗和部件磨损,提高变速器的传动效率和使用寿命。
变速器的结构优化设计方法与实践

变速器的结构优化设计方法与实践随着汽车工业的迅速发展,汽车变速器作为传动系统的核心部件,对汽车性能和燃油经济性起着重要作用。
为了提高汽车的性能和降低燃油消耗,变速器结构的优化设计显得尤为重要。
本文将介绍变速器结构优化设计的方法与实践。
一、背景介绍变速器是一种用于改变汽车引擎传动比的装置,以实现汽车在不同速度和负载条件下的运行要求。
传统的变速器通常采用机械齿轮传动的方式,但其结构复杂、噪音大、能效低等问题制约了汽车的性能和经济性。
因此,对变速器结构进行优化设计具有重要意义。
二、变速器结构优化设计方法1. 确定设计指标和约束条件变速器的设计指标包括传动比范围、传动效率、噪音和振动水平等。
根据车辆的使用需求和性能要求,确定变速器设计指标。
同时,还需考虑制造成本、可靠性以及相关的法规要求等约束条件。
2. 分析与建模在进行变速器结构优化设计之前,需要对变速器进行全面的分析与建模。
通过计算机辅助设计软件,对变速器的传动力学特性、传动效率以及瞬态特性进行分析和模拟。
3. 优化算法的选择针对变速器结构优化问题,可以采用不同的优化算法,如遗传算法、粒子群算法等。
这些算法能够在设计空间中搜索最优解,并采用适应度函数来评估设计的好坏。
4. 变速器结构优化设计基于优化算法,对变速器的结构参数进行优化设计。
这包括齿轮的齿数、模数、压力角等关键参数的选择,以及输入轴、输出轴的布局和结构的设计等。
5. 仿真验证与调试通过建立变速器的仿真模型,对优化设计的结构进行验证和调试。
通过仿真结果,评估优化设计方案的有效性和可行性。
三、变速器结构优化设计实践以一款小型汽车的变速器设计为实例,介绍变速器结构优化的实践过程。
1. 设计指标与约束条件的确定根据该汽车的使用需求和性能要求,确定变速器的传动比范围、传动效率要求以及相关的法规要求等。
2. 变速器分析与建模通过计算机辅助设计软件,对变速器进行分析与建模,包括传动力学特性、传动效率以及瞬态特性的分析和模拟。
液压机械无级变速箱箱体轻量化设计
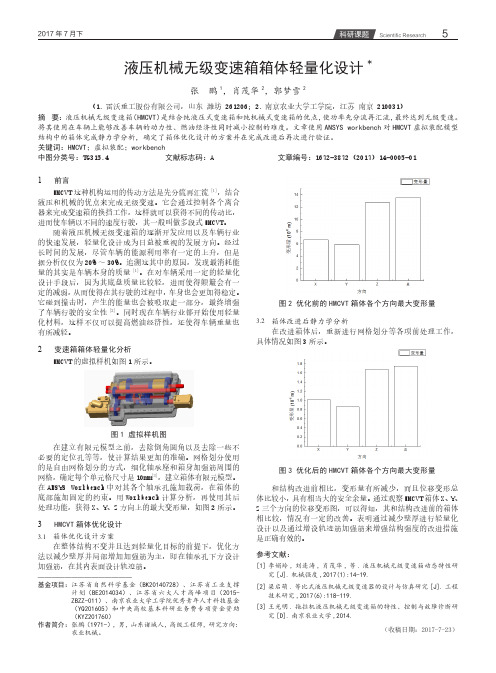
液压机械无级变速箱箱体轻量化设计*张 鹏1,肖茂华2,郭梦雪2(1.雷沃重工股份有限公司,山东 潍坊 261206;2.南京农业大学工学院,江苏 南京 210031)摘 要:液压机械无级变速箱(HMCVT)是结合纯液压式变速箱和纯机械式变速箱的优点,使功率先分流再汇流,最终达到无级变速。
将其使用在车辆上能够改善车辆的动力性、燃油经济性同时减小控制的难度。
文章使用ANSYS workbench 对HMCVT 虚拟装配模型结构中的箱体完成静力学分析,确定了箱体优化设计的方案并在完成改进后再次进行验证。
关键词:HMCVT;虚拟装配;workbench 中图分类号:TG315.4 文献标志码:A 文章编号:1672-3872(2017)14-0005-011 前言HMCVT 这种机构运用的传动方法是先分流再汇流[1],结合液压和机械的优点来完成无级变速。
它会通过控制各个离合器来完成变速箱的换挡工作,这样就可以获得不同的传动比,进而使车辆以不同的速度行驶,其一般叫做多段式HMCVT。
随着液压机械无级变速箱的逐渐开发应用以及车辆行业的快速发展,轻量化设计成为日益被重视的发展方向。
经过长时间的发展,尽管车辆的能源利用率有一定的上升,但是据分析仅仅为20%~30%。
追溯这其中的原因,发现最消耗能量的其实是车辆本身的质量[1]。
在对车辆采用一定的轻量化设计手段后,因为其底盘质量比较轻,进而使得颠簸会有一定的减弱,从而使得在其行驶的过程中,车身也会更加得稳定。
它碰到撞击时,产生的能量也会被吸取走一部分,最终增强了车辆行驶的安全性[2]。
同时现在车辆行业都开始使用轻量化材料,这样不仅可以提高燃油经济性,还使得车辆重量也有所减轻。
2 变速箱箱体轻量化分析HMCVT 的虚拟样机如图1所示。
图1 虚拟样机图——————————————基金项目: 江苏省自然科学基金(BK20140728)、江苏省工业支撑计划(BE2014034)、江苏省六大人才高峰项目(2015-ZBZZ-011)、南京农业大学工学院优秀青年人才科技基金(YQ201605)和中央高校基本科研业务费专项资金资助(KYZ201760)作者简介: 张鹏(1971-),男,山东诸城人,高级工程师,研究方向:农业机械。
汽车变速器的设计与优化毕业论文
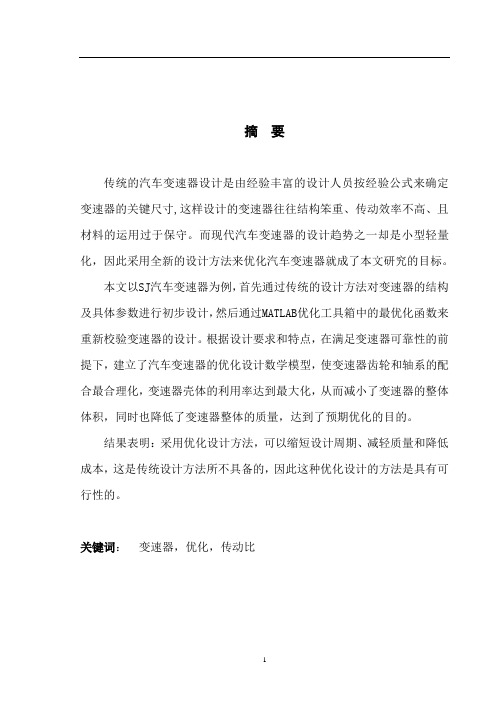
摘要传统的汽车变速器设计是由经验丰富的设计人员按经验公式来确定变速器的关键尺寸,这样设计的变速器往往结构笨重、传动效率不高、且材料的运用过于保守。
而现代汽车变速器的设计趋势之一却是小型轻量化,因此采用全新的设计方法来优化汽车变速器就成了本文研究的目标。
本文以SJ汽车变速器为例,首先通过传统的设计方法对变速器的结构及具体参数进行初步设计,然后通过MATLAB优化工具箱中的最优化函数来重新校验变速器的设计。
根据设计要求和特点,在满足变速器可靠性的前提下,建立了汽车变速器的优化设计数学模型,使变速器齿轮和轴系的配合最合理化,变速器壳体的利用率达到最大化,从而减小了变速器的整体体积,同时也降低了变速器整体的质量,达到了预期优化的目的。
结果表明:采用优化设计方法,可以缩短设计周期、减轻质量和降低成本,这是传统设计方法所不具备的,因此这种优化设计的方法是具有可行性的。
关键词:变速器,优化,传动比Optimize Design for SJ Automobile GearboxABSTRACTThe traditional design of Automobile gearbox used empirical formula to make sure the key sizes of gearbox,these designs always outdated,have lower efficiency,and the usage of material was too conservative. Along with the development of modern automobile industry,the design trends of gearbox are to request smaller volume and better function. So a new method which can get a small and lightweight gearbox becomes our target.In this thesis,SJ automobile gearbox was taken as an example. Firstly, traditional design was used to get the key sizes of gearbox;and then CAD was used to design its structure,such as shell、shaft、selector mechanism and so on;at last the toolbox of MATLAB was used to optimize the parameters of gearbox.The result manifests that using new method can shorten the design period,lower the costs for design,and the weight of gearbox can be reduced too. In conclusion,a satisfactory result can be achieved through optimizing the parameters of gearbox.Keyword:gearbox,optimization,transmitting ratioSJ汽车变速器的设计与优化0 引言随着时间的流逝,昔日的辉煌渐渐落下了尘埃;当轻轻的掸去岁月留下的痕迹,闪露的就是历史的光华。
轻型货车变速器设计
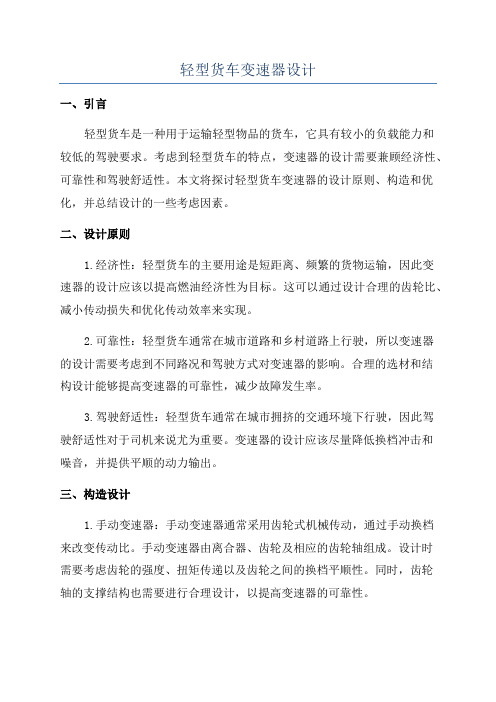
轻型货车变速器设计一、引言轻型货车是一种用于运输轻型物品的货车,它具有较小的负载能力和较低的驾驶要求。
考虑到轻型货车的特点,变速器的设计需要兼顾经济性、可靠性和驾驶舒适性。
本文将探讨轻型货车变速器的设计原则、构造和优化,并总结设计的一些考虑因素。
二、设计原则1.经济性:轻型货车的主要用途是短距离、频繁的货物运输,因此变速器的设计应该以提高燃油经济性为目标。
这可以通过设计合理的齿轮比、减小传动损失和优化传动效率来实现。
2.可靠性:轻型货车通常在城市道路和乡村道路上行驶,所以变速器的设计需要考虑到不同路况和驾驶方式对变速器的影响。
合理的选材和结构设计能够提高变速器的可靠性,减少故障发生率。
3.驾驶舒适性:轻型货车通常在城市拥挤的交通环境下行驶,因此驾驶舒适性对于司机来说尤为重要。
变速器的设计应该尽量降低换档冲击和噪音,并提供平顺的动力输出。
三、构造设计1.手动变速器:手动变速器通常采用齿轮式机械传动,通过手动换档来改变传动比。
手动变速器由离合器、齿轮及相应的齿轮轴组成。
设计时需要考虑齿轮的强度、扭矩传递以及齿轮之间的换档平顺性。
同时,齿轮轴的支撑结构也需要进行合理设计,以提高变速器的可靠性。
2.自动变速器:自动变速器采用液力变矩器和行星齿轮机构来实现换档,其能够根据车速和负载自动选择最佳的传动比。
自动变速器的设计需要考虑液力变矩器的工作效率、换档速度以及行星齿轮机构的精确性和可靠性。
同时,变速器控制系统也是关键,它需要准确地感知驾驶员的需求并进行相应的换档操作。
四、优化设计为了进一步提高轻型货车变速器的性能1.轻量化设计:通过选用高强度轻量材料、优化结构设计和减少无效部件,可以降低变速器的重量,提高车辆的载重能力。
2.多档设计:增加变速器的档位数,可以提供更加细腻的传动比选择,以满足不同路况和驾驶需求。
3.电子控制:引入电子控制系统可以精确地监测车辆状态并进行智能化的换档控制,进一步提高驾驶舒适性和燃油经济性。
基于拓扑优化的变速箱壳体轻量化设计

基于拓扑优化的变速箱壳体轻量化设计沈伟;廖敏;王强;王霜;易军;王川东;何旭【摘要】针对某丘陵山区小型联合收割机变速箱轻量化问题,对变速箱壳体进行结构优化设计.以变速箱壳体的柔顺度最小为目标函数,应用变密度法进行变速箱拓扑优化,去除部分多余材料,并进行了加强筋设计;基于响应面法建立变速箱壳体结构尺寸多目标优化模型,发现箱体壁厚和加强筋2宽度对变速箱壳体强度、刚度影响较大,再应用综合指数评价法得到壳体结构尺寸参数的最优解;最后,进行优化前后对比分析.结果表明:优化后壳体质量减少了17.1%,强度和刚度还有所提高.【期刊名称】《农机化研究》【年(卷),期】2018(040)004【总页数】8页(P234-241)【关键词】收割机;变速箱壳体;轻量化;拓扑优化;响应面【作者】沈伟;廖敏;王强;王霜;易军;王川东;何旭【作者单位】西华大学机械工程学院,成都 610039;西华大学机械工程学院,成都610039;西华大学流体与动力机械教育部重点实验室,成都 610039;四川省机械研究设计院,成都 610063;西华大学机械工程学院,成都 610039;西华大学流体与动力机械教育部重点实验室,成都 610039;成都主导科技有限责任公司,成都 610091;西华大学机械工程学院,成都 610039;西华大学机械工程学院,成都 610039【正文语种】中文【中图分类】S225.40 引言丘陵地区田块小、不平坦、形状不规则,分布较为分散,地形条件复杂多变[1-2]。
大型收割机无法正常使用,而小型联合收割机由于其质量相对较轻和体积相对较小,具有得天独厚的优势[3]。
在收获季节,收割机持续工作时间很长,且长期伴随着较大的载荷冲击和振动冲击,特别在高低不平和泥脚较深的田间作业时,变速箱需承受更大的负载,因此对变速箱壳体的可靠性提出了很高的要求。
变速箱是整机传动系统的重要部件,为行走动力传动轴系和割台动力传动轴系提供动力。
基于遗传算法的汽车变速箱轻量化设计

基于遗传算法的汽车变速箱轻量化设计褚永康;文桂林;崔中;文登【摘要】A method of lightweight optimization design for a gear box is proposed based on the approximation model and genetic algorithm(GA). The premise of lightweight optimization is to ensure the performance requirements, such as strength, stiffness and vibration resistance. The Latin method is used in the experimental design to generate test sample points, and the approximation model is built based on the Gaussian radial basis function. The global optimization design is also performed based on the GA. The mass of the optimized box is reduced by 21%. The results show that this method can provide certain engineering guidance for the lightweight optimization of gear box.%文章利用近似模型方法和遗传算法对某变速箱进行轻量化设计.在满足变速箱刚度强度及振动模态要求的基础上,采用拉丁方法进行试验设计,基于高斯径向基函数建立近似模型,最后利用遗传算法进行全局寻优设计.优化后箱体质量降低了21%.结果表明,该方法对汽车变速箱结构轻量化设计具有一定的指导意义.【期刊名称】《合肥工业大学学报(自然科学版)》【年(卷),期】2011(034)010【总页数】5页(P1461-1465)【关键词】变速箱箱体;轻量化;近似模型;遗传算法【作者】褚永康;文桂林;崔中;文登【作者单位】湖南大学汽车车身先进设计制造国家重点实验室,湖南长沙410082;湖南大学汽车车身先进设计制造国家重点实验室,湖南长沙410082;湖南大学汽车车身先进设计制造国家重点实验室,湖南长沙410082;湖南大学汽车车身先进设计制造国家重点实验室,湖南长沙410082【正文语种】中文【中图分类】U463.2120 引言当今汽车技术的发展由于受到环境、资源等问题制约,轻量化的汽车在燃油经济性、排放物等级方面都具有更强的市场竞争力,因此,汽车轻量化技术成为十分必要的研发课题。
基于ANSYS Workbench的变速器箱体轻量化分析

之后 , 需要 对 3 壳体 进行装 配 , 配成 组件 后 , 个 装 在 P o E 软 件 菜 单 选 项 中选 择 P r\ NS 1 . \ r/ at A Ys 1 O
第 5 期 ( 第 1 2期 ) 总 6
21 0 0年 l O月
机 械 工 程 与 自 动 化
M ECHANI CAL ENGI NEE NG & AUTOM AT1 RI 0N
N O. 5
0c. t
文 章 编 号 :6 26 1 (0 0 0— 0 70 1 7 — 4 3 2 1 ) 50 5 — 3
基 于 ANS r b n h的变速 器 箱 体 轻 量化 分 析 YSWok e c
张 小坤 ,陈 晓峰 ,殷 明 贵
( 国 重汽 集 团 大 同齿 轮 有 限公 司 , 山西 大 同 中 070) 3 0 6
摘 要 :介 绍 了变 速 器 箱 体 轻 量 化 分 析 的步 骤 。 应用 P o E软 件建 立 三 维数 模 ,应 用 AN Y rb nh软 件 r/ S SWok ec 进 行 有 限元 分 析 。通 过 对 ANS SW ok e c Y rb n h后处 理 数 据 进 行 分 析 ,得 出变 速 器 箱 体 应 力 、变形 的分 布 情 况 ,
P o E 软 件 建 立 箱体 的 三 维 数 学 模 型 并 进 行 重 量 对 r/
比,应 用 A YSWok e c NS r b n h软 件对 变速器 箱体 进行
变速器壳体轻量化设计浅析

AUTOMOBILE DESIGN | 汽车设计时代汽车 变速器壳体轻量化设计浅析陈丹上海汽车变速器有限公司 上海市嘉定区 201800摘 要: 本文主要针对一款汽车变速器壳体的结构优化设计、CAE仿真校核浅析壳体的轻量化设计方案,从而有效降低壳体重量,为提高汽车的动力性、减少燃油消耗,降低成本、提高产品竞争力提供有利支持。
关键词:变速器;壳体设计;轻量化1 引言如今,节能环保已成为社会广泛关注的话题,汽车轻量化技术已经成为汽车产业最为重要的发展方向。
变速器作为汽车动力总成的重要组成部分,其重量大约占整车的5%,而壳体作为整个变速器的外壳和支撑,其重量约占变速器总成的30%左右[1]。
本文主要从变速器壳体布局、材料选取、结构设计等方面,根据CAE拓扑优化完善结构设计,满足强度、刚度及良好的NVH性能的同时实现重量最轻,从而提高汽车的动力性、减少燃油消耗,降低排气污染。
2 变速器壳体结构设计变速器壳体总成主要由变速器前壳体和后壳体组成,采用螺栓连接形成整体封闭结构。
为保证轻量化,前、后壳体的材料均为压铸铝合金。
变速器壳体在变速器总成中主要起到支撑、包络和密封的作用,壳体功能决定了具有大体积、大重量的特征,同时要求其具有较高的结构强度、刚度及良好的NVH特性。
壳体在设计布局时,在保证与内部零部件间隙前提下,尽可能沿各零部件外轮廓布局,这样可最大情况下缩小变速器体积,从而减轻壳体重量。
一般情况下壳体与齿轮等运作零部件(机加工面)间隙3mm左右,与拨叉等运动零部件(非机加工面)的运动包络范围间隙3mm~5mm,与挡油板等固定零部件间隙1mm~2mm。
2.1 基础壁厚设计基本壁厚是构成压铸件基本形状的基体的厚度,变速器壳体是通过在基体壁厚上增加特征来构成的最终形状,一般情况下铝合金壳体的基础壁厚为3.5mm~4mm,轴承位壁厚为5.5mm~7.5mm,螺栓凸台壁厚为6mm~7mm。
另外壳体最大壁厚一般不超过基本壁厚的5倍,否则易产生气孔、缩孔等缺陷。
某双离合自动变速器箱体强度分析和轻量化设计
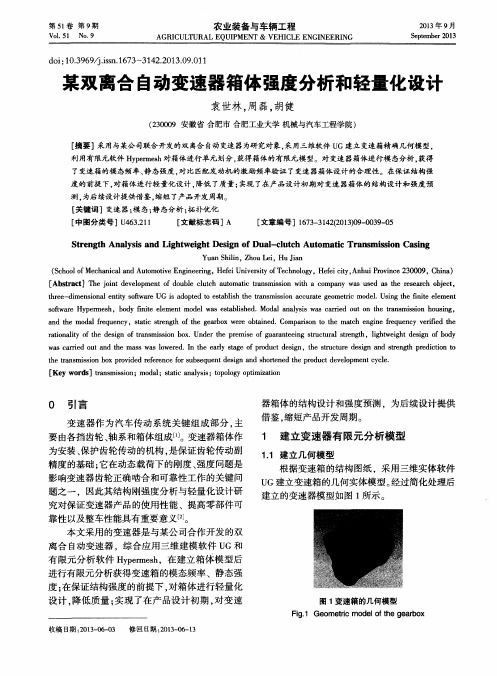
wa s c a r r i e d o u t a n d t h e ma s s wa s l o w e r e d .I n he t e a r l y s t a g e o f p r o d u c t d e s i g n,t h e s t uc r t u r e d e s i g n a n d s t r e n th g p r e d i c t i o n t o
t h r e e — — d i me n s i o n a l e n t i t y s o f t w a r e UG i s a d o p t e d t o e s t a b l i s h t h e t r a n s mi s s i o n a c c u r a t e g e o me t i r c mo d e 1 . Us i n g t h e i f n i t e e l e me n t s o f t wa r e Hy p e r me s h,b o d y i f n i t e e l e me n t mo d e l wa s e s t a b l i s h e d .Mo d a l a n ly a s i s w a s c a r r i e d o u t o n t h e t r a n s mi s s i o n h o u s i n g ,
测, 为后 续设 计 提供 借 鉴 。 缩短 了产 品 开发 周期 。
[ 关键词 ]变速器 ; 模 态; 静 态分析 ; 拓4 1 - /  ̄ 4  ̄
[ 中图分类号】U 4 6 3 . 2 1 1
[ 文献标 志码 ] A
[ 文章编号 ]1 6 7 3 — 3 1 4 2 ( 2 0 1 3 ) 0 9 — 0 0 3 9 — 0 5
如何进行汽车轻量化设计
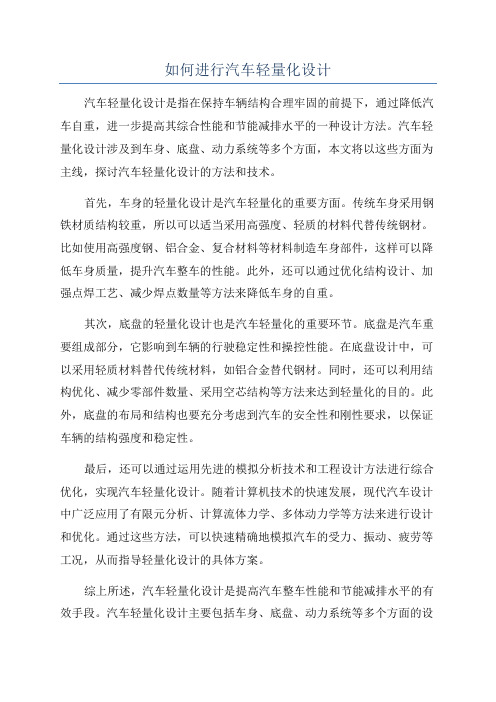
如何进行汽车轻量化设计汽车轻量化设计是指在保持车辆结构合理牢固的前提下,通过降低汽车自重,进一步提高其综合性能和节能减排水平的一种设计方法。
汽车轻量化设计涉及到车身、底盘、动力系统等多个方面,本文将以这些方面为主线,探讨汽车轻量化设计的方法和技术。
首先,车身的轻量化设计是汽车轻量化的重要方面。
传统车身采用钢铁材质结构较重,所以可以适当采用高强度、轻质的材料代替传统钢材。
比如使用高强度钢、铝合金、复合材料等材料制造车身部件,这样可以降低车身质量,提升汽车整车的性能。
此外,还可以通过优化结构设计、加强点焊工艺、减少焊点数量等方法来降低车身的自重。
其次,底盘的轻量化设计也是汽车轻量化的重要环节。
底盘是汽车重要组成部分,它影响到车辆的行驶稳定性和操控性能。
在底盘设计中,可以采用轻质材料替代传统材料,如铝合金替代钢材。
同时,还可以利用结构优化、减少零部件数量、采用空芯结构等方法来达到轻量化的目的。
此外,底盘的布局和结构也要充分考虑到汽车的安全性和刚性要求,以保证车辆的结构强度和稳定性。
最后,还可以通过运用先进的模拟分析技术和工程设计方法进行综合优化,实现汽车轻量化设计。
随着计算机技术的快速发展,现代汽车设计中广泛应用了有限元分析、计算流体力学、多体动力学等方法来进行设计和优化。
通过这些方法,可以快速精确地模拟汽车的受力、振动、疲劳等工况,从而指导轻量化设计的具体方案。
综上所述,汽车轻量化设计是提高汽车整车性能和节能减排水平的有效手段。
汽车轻量化设计主要包括车身、底盘、动力系统等多个方面的设计和优化。
通过采用高强度、轻质的材料、优化结构设计、减少焊点数量、优化动力系统等方法,可以实现汽车的轻量化设计。
此外,运用先进的模拟分析技术和工程设计方法,可以指导设计和优化过程,为汽车轻量化设计提供有效的支持。
汽车轻量化设计可以降低车辆重量,提高燃油经济性和安全性能,对于推动汽车技术进步和未来可持续发展有着重要意义。
变速器壳体轻量化设计浅析
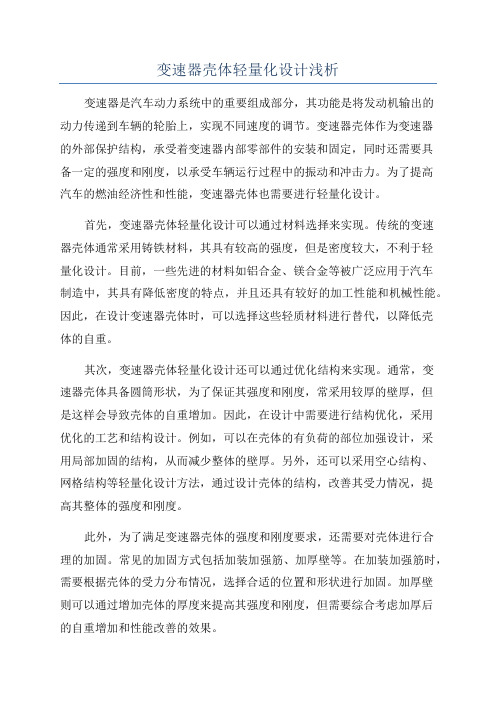
变速器壳体轻量化设计浅析变速器是汽车动力系统中的重要组成部分,其功能是将发动机输出的动力传递到车辆的轮胎上,实现不同速度的调节。
变速器壳体作为变速器的外部保护结构,承受着变速器内部零部件的安装和固定,同时还需要具备一定的强度和刚度,以承受车辆运行过程中的振动和冲击力。
为了提高汽车的燃油经济性和性能,变速器壳体也需要进行轻量化设计。
首先,变速器壳体轻量化设计可以通过材料选择来实现。
传统的变速器壳体通常采用铸铁材料,其具有较高的强度,但是密度较大,不利于轻量化设计。
目前,一些先进的材料如铝合金、镁合金等被广泛应用于汽车制造中,其具有降低密度的特点,并且还具有较好的加工性能和机械性能。
因此,在设计变速器壳体时,可以选择这些轻质材料进行替代,以降低壳体的自重。
其次,变速器壳体轻量化设计还可以通过优化结构来实现。
通常,变速器壳体具备圆筒形状,为了保证其强度和刚度,常采用较厚的壁厚,但是这样会导致壳体的自重增加。
因此,在设计中需要进行结构优化,采用优化的工艺和结构设计。
例如,可以在壳体的有负荷的部位加强设计,采用局部加固的结构,从而减少整体的壁厚。
另外,还可以采用空心结构、网格结构等轻量化设计方法,通过设计壳体的结构,改善其受力情况,提高其整体的强度和刚度。
此外,为了满足变速器壳体的强度和刚度要求,还需要对壳体进行合理的加固。
常见的加固方式包括加装加强筋、加厚壁等。
在加装加强筋时,需要根据壳体的受力分布情况,选择合适的位置和形状进行加固。
加厚壁则可以通过增加壳体的厚度来提高其强度和刚度,但需要综合考虑加厚后的自重增加和性能改善的效果。
综上所述,变速器壳体轻量化设计是汽车制造中的一个重要课题。
通过合理的材料选择和结构优化,可以有效降低变速器壳体的自重,提高汽车的燃油经济性和性能。
变速器壳体轻量化设计需要综合考虑材料的强度、密度、加工性能等因素,采用合适的加固方式和结构设计,从而实现轻量化和良好的工程性能的平衡。
汽车变速器箱体轻量化设计
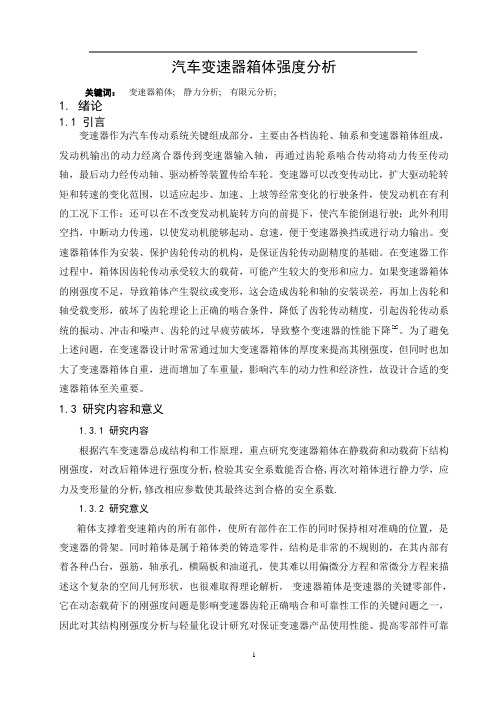
汽车变速器箱体强度分析关键词:变速器箱体; 静力分析; 有限元分析;1. 绪论1.1 引言变速器作为汽车传动系统关键组成部分,主要由各档齿轮、轴系和变速器箱体组成,发动机输出的动力经离合器传到变速器输入轴,再通过齿轮系啮合传动将动力传至传动轴,最后动力经传动轴、驱动桥等装置传给车轮。
变速器可以改变传动比,扩大驱动轮转矩和转速的变化范围,以适应起步、加速、上坡等经常变化的行驶条件,使发动机在有利的工况下工作;还可以在不改变发动机旋转方向的前提下,使汽车能倒退行驶;此外利用空挡,中断动力传递,以使发动机能够起动、怠速,便于变速器换挡或进行动力输出。
变速器箱体作为安装、保护齿轮传动的机构,是保证齿轮传动副精度的基础。
在变速器工作过程中,箱体因齿轮传动承受较大的载荷,可能产生较大的变形和应力。
如果变速器箱体的刚强度不足,导致箱体产生裂纹或变形,这会造成齿轮和轴的安装误差,再加上齿轮和轴受载变形,破坏了齿轮理论上正确的啮合条件,降低了齿轮传动精度,引起齿轮传动系统的振动、冲击和噪声、齿轮的过早疲劳破坏,导致整个变速器的性能下降[2]。
为了避免上述问题,在变速器设计时常常通过加大变速器箱体的厚度来提高其刚强度,但同时也加大了变速器箱体自重,进而增加了车重量,影响汽车的动力性和经济性,故设计合适的变速器箱体至关重要。
1.3 研究内容和意义1.3.1 研究内容根据汽车变速器总成结构和工作原理,重点研究变速器箱体在静载荷和动载荷下结构刚强度,对改后箱体进行强度分析,检验其安全系数能否合格,再次对箱体进行静力学,应力及变形量的分析,修改相应参数使其最终达到合格的安全系数.1.3.2 研究意义箱体支撑着变速箱内的所有部件,使所有部件在工作的同时保持相对准确的位置,是变速器的骨架。
同时箱体是属于箱体类的铸造零件,结构是非常的不规则的,在其内部有着各种凸台,强筋,轴承孔,横隔板和油道孔,使其难以用偏微分方程和常微分方程来描述这个复杂的空间几何形状,也很难取得理论解析,变速器箱体是变速器的关键零部件,它在动态载荷下的刚强度问题是影响变速器齿轮正确啮合和可靠性工作的关键问题之一,因此对其结构刚强度分析与轻量化设计研究对保证变速器产品使用性能、提高零部件可靠性以及整车性能具有重要意义[6]。
HMCVT箱体轻量化措施
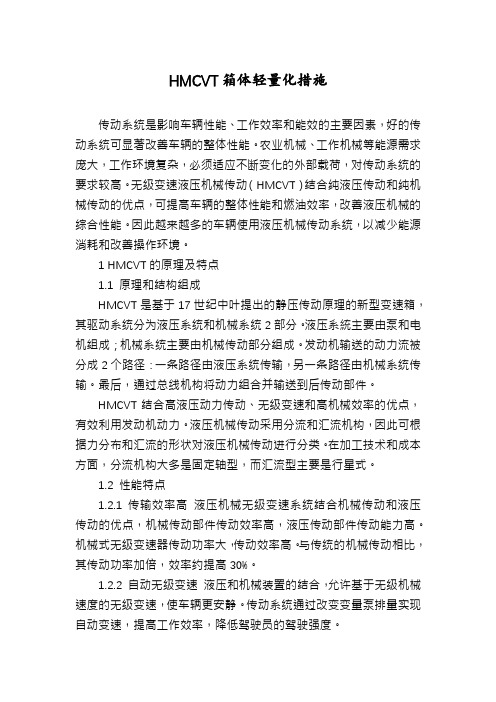
HMCVT箱体轻量化措施传动系统是影响车辆性能、工作效率和能效的主要因素,好的传动系统可显著改善车辆的整体性能。
农业机械、工作机械等能源需求庞大,工作环境复杂,必须适应不断变化的外部载荷,对传动系统的要求较高。
无级变速液压机械传动(HMCVT)结合纯液压传动和纯机械传动的优点,可提高车辆的整体性能和燃油效率,改善液压机械的综合性能。
因此越来越多的车辆使用液压机械传动系统,以减少能源消耗和改善操作环境。
1 HMCVT的原理及特点1.1 原理和结构组成HMCVT是基于17世纪中叶提出的静压传动原理的新型变速箱,其驱动系统分为液压系统和机械系统2部分。
液压系統主要由泵和电机组成;机械系统主要由机械传动部分组成。
发动机输送的动力流被分成2个路径:一条路径由液压系统传输,另一条路径由机械系统传输。
最后,通过总线机构将动力组合并输送到后传动部件。
HMCVT结合高液压动力传动、无级变速和高机械效率的优点,有效利用发动机动力。
液压机械传动采用分流和汇流机构,因此可根据力分布和汇流的形状对液压机械传动进行分类。
在加工技术和成本方面,分流机构大多是固定轴型,而汇流型主要是行星式。
1.2 性能特点1.2.1 传输效率高液压机械无级变速系统结合机械传动和液压传动的优点,机械传动部件传动效率高,液压传动部件传动能力高。
机械式无级变速器传动功率大,传动效率高。
与传统的机械传动相比,其传动功率加倍,效率约提高30%。
1.2.2 自动无级变速液压和机械装置的结合,允许基于无级机械速度的无级变速,使车辆更安静。
传动系统通过改变变量泵排量实现自动变速,提高工作效率,降低驾驶员的驾驶强度。
2 机械液压无级变速箱轻量化2.1 轻量化设计的重要性随着液压机械无级变速器的逐步发展和应用,轻量化结构成为汽车工业发展趋势。
经过长时间的开发,车辆的能源效率有所提高,但仍只有20%~30%。
车辆采用一定的轻质结构后,底盘质量相对较低,不均匀性减弱。
变速箱设计方案

变速箱设计方案变速箱设计方案一、引言变速箱是汽车传动系统中的重要组成部分,它负责将发动机的动力通过不同的齿轮比例传递给车轮,以实现不同速度和扭矩的输出。
本文将详细介绍一个全面的变速箱设计方案。
二、需求分析在开始设计变速箱之前,我们需要对需求进行充分的分析。
根据市场调研和用户反馈,我们得出以下需求:1. 高效能:变速箱应具备高效能,以提供更好的加速性能和燃油经济性。
2. 平顺换挡:换挡过程应平顺无感知,避免驾驶者和乘客的不适感。
3. 可靠性:变速箱应具备高可靠性和耐久性,以确保长时间使用不出现故障。
4. 多档位:变速箱应具备多档位设计,以满足不同驾驶条件下的需求。
5. 轻量化:为了减少整车重量并提高燃油经济性,变速箱应采用轻量化材料和结构。
三、设计方案基于以上需求分析,我们提出了以下详细的设计方案:1. 变速箱类型选择根据市场需求和技术可行性,我们选择了自动变速箱作为设计方案。
自动变速箱具有平顺换挡、高效能和多档位等优势,能够满足用户的需求。
2. 齿轮设计齿轮是变速箱的核心组件,其设计直接影响到传动效率和平顺性。
我们采用了先进的齿轮设计技术,包括精密制造工艺和优化的齿形参数。
通过这些措施,我们能够提高齿轮的传动效率,并减少噪音和振动。
3. 液力变矩器设计液力变矩器是自动变速箱中的重要部件,它通过液体传递扭矩,并实现起步、换挡和减速等功能。
我们采用了高效的液力变矩器设计,以提供平顺的起步和换挡过程,并减少能量损失。
4. 控制系统设计控制系统是自动变速箱中至关重要的一部分,它负责监测车辆状态并控制换挡过程。
我们采用了先进的电子控制单元(ECU)和传感器技术,以实现精准的换挡控制和自适应学习功能。
通过这些措施,我们能够提供更好的驾驶体验和燃油经济性。
5. 轻量化设计为了减少整车重量并提高燃油经济性,我们采用了轻量化材料和结构设计。
变速箱外壳采用高强度铝合金材料制造,以提高强度并降低重量。
我们还优化了内部结构,并采用高效的润滑系统,以减少能量损失和摩擦。
变速器轻量化设计探索

变速器轻量化设计探索随着汽车工业的不断发展,轻量化已经成为一个不得不关注的问题。
汽车的轻量化能够带来许多好处,如减少运动阻力、提高燃油效率,对于减少环境污染和降低成本也具有积极意义。
在这种情况下,变速器轻量化设计成为一个热门话题。
下面将探讨变速器轻量化设计的一些措施。
首先,可以通过改变变速器的材质来实现轻量化的目的。
材料的选择决定了变速器的重量。
一些轻质聚合物或金属材料,如铝合金等,可以用来制造变速器零件,从而有效减少其重量。
这些材料具有重量轻、强度高的特点,满足了变速器的要求。
其次,减少变速器的尺寸也能够实现轻量化的目的。
不能以牺牲性能为代价,但是可以通过提高设计水平来使得变速器体积更小。
例如,通过改进变速器的结构设计,降低零件数量并缩小零件尺寸,达到体积减小和重量降低的目的。
第三,减少变速器的工作损耗也是轻量化设计的另一个手段。
降低变速器的工作损耗,不仅可以减少变速器所需的驱动力,使汽车更加节能,还可以减少部件的磨损和热负荷,提高变速器使用寿命。
在这方面,一个高效的液压油系统是非常重要的。
轻量化设计的变速器必须能够在保持正常使用寿命的前提下,降低摩擦和磨损。
最后,为了实现轻量化,需要加强变速器的可靠性和稳定性的设计。
这意味着要确保变速器在任何时间、任何条件下都能够保持良好的性能和功能。
例如,可以在检测和检修过程中加强变速器的检查和维护,以保证其在正常使用情况下的可靠性和稳定性。
总的来说,在汽车工业中,变速器轻量化设计是一个重要的趋势,不仅可以减小车的重量,提高能效,还能保证汽车的性能和安全。
如果设计师以真正的创新精神来考虑轻质化设计问题,可实现更轻、更小、更强的变速器设计,从而进一步节省燃料并提高行驶舒适度。
暂无法回答,需要更具体的数据和分析对象。
以宝马汽车公司轻量化设计为例,进行分析和总结。
宝马汽车公司是全球首批开始采用轻量化设计的汽车公司之一。
自1990年代起,宝马坚持将轻量化作为最重要的设计理念之一,大力推进轻质材料在车身和零部件中的使用,如铝合金、高强度钢等。
变速箱用铝合金能减重108公斤厂商轻量化都爱玩什么套路?
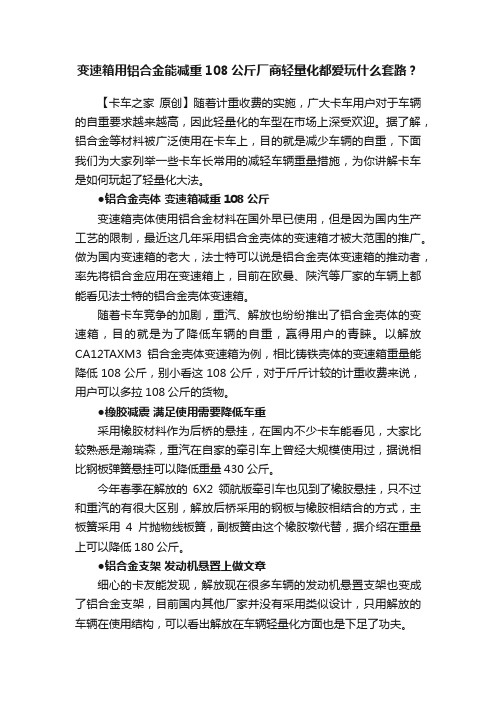
变速箱用铝合金能减重108公斤厂商轻量化都爱玩什么套路?【卡车之家原创】随着计重收费的实施,广大卡车用户对于车辆的自重要求越来越高,因此轻量化的车型在市场上深受欢迎。
据了解,铝合金等材料被广泛使用在卡车上,目的就是减少车辆的自重,下面我们为大家列举一些卡车长常用的减轻车辆重量措施,为你讲解卡车是如何玩起了轻量化大法。
●铝合金壳体变速箱减重108公斤变速箱壳体使用铝合金材料在国外早已使用,但是因为国内生产工艺的限制,最近这几年采用铝合金壳体的变速箱才被大范围的推广。
做为国内变速箱的老大,法士特可以说是铝合金壳体变速箱的推动者,率先将铝合金应用在变速箱上,目前在欧曼、陕汽等厂家的车辆上都能看见法士特的铝合金壳体变速箱。
随着卡车竞争的加剧,重汽、解放也纷纷推出了铝合金壳体的变速箱,目的就是为了降低车辆的自重,赢得用户的青睐。
以解放CA12TAXM3铝合金壳体变速箱为例,相比铸铁壳体的变速箱重量能降低108公斤,别小看这108公斤,对于斤斤计较的计重收费来说,用户可以多拉108公斤的货物。
●橡胶减震满足使用需要降低车重采用橡胶材料作为后桥的悬挂,在国内不少卡车能看见,大家比较熟悉是瀚瑞森,重汽在自家的牵引车上曾经大规模使用过,据说相比钢板弹簧悬挂可以降低重量430公斤。
今年春季在解放的6X2领航版牵引车也见到了橡胶悬挂,只不过和重汽的有很大区别,解放后桥采用的钢板与橡胶相结合的方式,主板簧采用4片抛物线板簧,副板簧由这个橡胶墩代替,据介绍在重量上可以降低180公斤。
●铝合金支架发动机悬置上做文章细心的卡友能发现,解放现在很多车辆的发动机悬置支架也变成了铝合金支架,目前国内其他厂家并没有采用类似设计,只用解放的车辆在使用结构,可以看出解放在车辆轻量化方面也是下足了功夫。
据了解,据称采用这样的设计,相比铁支架能降低一些重量,而且可以获得更好的隔震效果,至于强度来说一点问题没有,大家不用担心。
●铝合金车圈六轴挂车能轻半吨铝合金车圈目前的价格有点小贵,但是不少敢于尝鲜的用户已经开始使用,据说使用效果不错。
- 1、下载文档前请自行甄别文档内容的完整性,平台不提供额外的编辑、内容补充、找答案等附加服务。
- 2、"仅部分预览"的文档,不可在线预览部分如存在完整性等问题,可反馈申请退款(可完整预览的文档不适用该条件!)。
- 3、如文档侵犯您的权益,请联系客服反馈,我们会尽快为您处理(人工客服工作时间:9:00-18:30)。
汽车变速器箱体轻量化设计摘要:本文根据汽车变速器总成结构和工作原理,运用静力学分析,得到各挡离合器总成与箱体之间的最大轴承力,作为箱体有限元分析的边界载荷;采用有限元分析方法对箱体进行强度分析,得到最大应力与最大变形量分布情况;对箱体做轻量化处理后,以相同边界载荷进行强度校核;最终将汽车变速器箱体壁厚减去2mm.。
关键词:变速器箱体; 静力分析; 有限元分析; 轻量化1. 绪论1.1 引言随着汽车工业的快速发展和日益突出的能源问题,节能减排在汽车工业中越来越受到人们的重视。
目前,降低制造成本和提高整车燃油效率已成为汽车设计的要求,为实现这一目标,各大汽车制造商纷纷关注汽车轻量化技术的研究与应用。
研究表明,汽车约60%燃料消耗于自重,汽车质量每减轻10%,可降低油耗6%至8%[1]。
由此可见,汽车燃油消耗率同汽车整车整备质量密切相关,而汽车轻量化则通过对汽车结构的优化设计,最大程度内减小汽车整车整备质量,降低汽车的燃油消耗率,减少油耗。
除此之外,轻量化还可以减少汽车原材料的消耗,降低汽车的生产成本,提高汽车的操控性能,减小振动和冲击,降低噪音。
随着汽车技术的发展,现代汽车日益数字化、智能化、高级化,附加的汽车电子装置越来越多,导致汽车的质量不断增加,为控制汽车质量,必须加快汽车各组成部分的轻量化技术研究。
变速器作为汽车传动系统关键组成部分,主要由各档齿轮、轴系和变速器箱体组成,发动机输出的动力经离合器传到变速器输入轴,再通过齿轮系啮合传动将动力传至传动轴,最后动力经传动轴、驱动桥等装置传给车轮。
变速器可以改变传动比,扩大驱动轮转矩和转速的变化范围,以适应起步、加速、上坡等经常变化的行驶条件,使发动机在有利的工况下工作;还可以在不改变发动机旋转方向的前提下,使汽车能倒退行驶;此外利用空挡,中断动力传递,以使发动机能够起动、怠速,便于变速器换挡或进行动力输出。
变速器箱体作为安装、保护齿轮传动的机构,是保证齿轮传动副精度的基础。
在变速器工作过程中,箱体因齿轮传动承受较大的载荷,可能产生较大的变形和应力。
如果变速器箱体的刚强度不足,导致箱体产生裂纹或变形,这会造成齿轮和轴的安装误差,再加上齿轮和轴受载变形,破坏了齿轮理论上正确的啮合条件,降低了齿轮传动精度,引起齿轮传动系统的振动、冲击和噪声、齿轮的过早疲劳破坏,导致整个变速器的性能下降[2]。
为了避免上述问题,在变速器设计时常常通过加大变速器箱体的厚度来提高其刚强度,但同时也加大了变速器箱体自重,进而增加了车重量,影响汽车的动力性和经济性,故设计合适的变速器箱体至关重要。
1.2 轻量化技术国内外研究现状和发展趋势汽车轻量化实现途径主要有两种:一是使用轻金属、现代复合材料等低密度轻质料,达到减重目标;二是从结构出发,通过改变结构,在保证刚强度不变的前提下轻重量[3]。
第一种途径存在成本高,技术不成熟等困难,这表明通过材料的轻量化减轻汽车自重虽然具有巨大潜力,但在现阶段很难实施。
而随着CAD/CAE技术的不成熟,后一种途径已经广泛应用到汽车行业。
目前,汽车结构轻量化设计的思想已入到产品设计前期,以达到汽车轻量化、操控性、安全性及成本的统一。
另外,新制造工艺的使用,使得某些结构能实现“以空代实”,达到简化结构的目的。
这些关技术决定了汽车轻量化未来发展意义重大[4]。
80年代,国外学者将结构优化设计技术和刚柔体耦合动力学仿真技术结合起来实现变速器箱体轻量化,分析变速器箱体在动态载荷下结构刚强度,根据分析结果,对箱体进行整体或局部改进,达到优化设计的目的。
国内汽车变速器箱体结构优化设计方法的研究刚刚开始,国内汽车变速器箱体结构优化设计方法的研究刚刚开始,传统的变速器箱体设计多采用有限元分析和经验设计相结合的方法,以达到目的。
如赵丽娟,刘宏梅等人先利用软件Pro/E建立了矿用减速箱体的三维实体模型,再利用ANSYS软件对箱体进行结构刚强度分析,并找出了危险区域,对箱体结构进行再设计,这种优化方法效果显著,使箱体重量和材料成本均有降低[5]。
1.3 研究内容和意义1.3.1 研究内容根据汽车变速器总成结构和工作原理,重点研究变速器箱体在静载荷和动载荷下结构刚强度,并基于结构强度分析结果对箱体进行轻量化设计,实现变速器箱体轻量化的目的。
具体内容可分为以下五部分:1运用静力学分析,得到各挡离合器总成与箱体之间的最大轴承力,作为箱体有限元分析的边界载荷;2 采用有限元分析方法对箱体进行强度分析,得到最大应力与最大变形量分布情况;3 根据分析结果对变速箱体拟定轻量化处理计划.4对箱体做轻量化处理后,以相同边界载荷进行强度校核,选择适当部位增加凸台,增加面积避免个别部位的应力过于集中。
5 对改后箱体进行强度分析,检验其安全系数能否合格,若合格则此方案可行,反之则再次对箱体进行静力学,应力及变形量的分析,修改相应参数使其最终达到合格的安全系数.1.3.2 研究意义箱体支撑着变速箱内的所有部件,使所有部件在工作的同时保持相对准确的位置,是变速器的骨架。
同时箱体是属于箱体类的铸造零件,结构是非常的不规则的,在其内部有着各种凸台,强筋,轴承孔,横隔板和油道孔,使其难以用偏微分方程和常微分方程来描述这个复杂的空间几何形状,也很难取得理论解析式。
箱内分布着2轴和13 个齿轮,在工作过程中的受力情况不容易分析,各个齿轮承受各级轴给的作用力。
正因为箱体结构和受力的复杂性才决定箱体是整个变速箱强度分析的主要对象。
变速器箱体是变速器的关键零部件,它在动态载荷下的刚强度问题是影响变速器齿轮正确啮合和可靠性工作的关键问题之一,因此对其结构刚强度分析与轻量化设计研究对保证变速器产品使用性能、提高零部件可靠性以及整车性能具有重要意义[6]。
变速器箱体产品原型样机采用铝合金材料,由于铝合金材料技术工艺复杂,成本较高;企业为了降低制造成本,提高产品的市场竞争力,新开发的变速器产品采用铸铁箱体,但铸铁箱体最大的缺点是太重。
本文结合企业实际生产需要,针对汽车变速器研发过程中出现的重量超标以及可能出现的箱体结构强度不足等问题,采用基本静力学分析和有限元分析,实现变速器箱体轻量化。
通过本文的研究,可降低公司现有变速器产品生产和制造成本,达到降本增效的目的,使得该变速器产品能够以较高的性价比优势进入市场,比同类产品更具有竞争能力。
因而本研究具有很强的工程实用价值和重要的理论指导意义。
2. 变速器箱体静力学分析2.1 基本参数汽车基本参数:额定功率 50kw ; 额定转速 4500 r/min ; 额定输入扭矩 106 N.m2.2 受力分析变速器箱体的结构可划分为一个箱体和一个箱盖,并通过紧固螺栓及其组件将两部分紧固,紧固螺栓和它附近的受力不作为分析的重点,所以可以将其认为是刚性约束。
根据局部影响力定理,这种局部近似处理对远处的应力和应变结果不会有明显的影响,在这里将两个部分作为一个整体来分析。
我们需要知道各挡离合器总成与箱体之间的轴承载荷,才能得到箱体的受力情况。
在此,将各挡轴与齿轮作为整体,由齿轮力学分析得到齿轮力,利用理论力学原理向轴中简化,同时计算轴承对轴的支撑力根据变速器的结构及动力传动路线,若求解箱体的最大受力载荷,分析前进一挡受力情况即可。
以下给定输入轴转矩为106N.m 。
该变速器均为直齿轮传动,每对齿轮所受的力互为作用力与反作用力,齿轮间有圆周力与径向力,无轴向力,其计算公式为: ir d T 2=ti F (2-1) αtan ti ri F F = (2-2)式中:ti F ----各齿轮圆周力; ri F ----各齿轮径向力,N ;i T -----输入转矩,N.m ; i d -----分度圆直径,m ;i ------齿轮序号,i =1~13;α-----齿轮压力角,α =20°。
受力分析时参考的直角坐标系如图所示,其中,Z 轴平行于各轴轴线,各挡离合器总成与箱体之间的轴承力用N mn 表示,角标m 代表图1中的轴,m=1~2;n 表示对应轴上的轴承,n=1~2;lmn 为计算m 轴上n 轴承力所需的结构尺寸。
N mnx 和N mny 分别代表轴承力N mn 沿x 轴和y 轴方向的分量;r i 为第i 个齿轮啮合点出径向力与x 轴所夹的锐角。
前进一挡时受力分析如下,以输入轴Ⅰ轴为研究对象,发动机输入转矩为顺时针,整体受力情况及啮合力的空间作用方向示意图如图2-1 所示,图2-1 前进一档时输入轴受力分析示意图通过方程(3)—(8),求解一轴轴承力: 121d TF t = (2-3) αtan 11t r F F = (2-4)0cos sin 1111X 1211=+++r F r F N N T t X (2-5)0sin cos 1111Y 1211=+++r F r F N N T t Y (2-6)0)cos sin ()(111111121112=+++l r F r F l l N T t X (2-7)0)cos sin ()(111111121112=+++l r F r F l l N t r Y (2-8)同理,分别以前进一挡时,输入轴与输出轴为研究对象,进行受力分析,具体受力分析图及方程式在此省略,计算得到所有轴承力结果如表 2-2所示,正号代表与图示方向相同,负号代表与图示方向相反。
表2-2 前进一档时各轴承力 输入轴/N 输出轴/NX N 11Y N 11 X N 12 Y N 12 X N 21 Y N 21 X N 22 Y N 22 -10677 5865 -9476 5205 -20468 9882 -22515 218703. 箱体有限元分析3.1 有限元分析简介有限元法(FEM)是求解复杂工程问题的一种近似数值析方法。
他的基本思想可概括为“先分后合”或“化整为零又积零为整”,具体来讲就是将一个复杂结构的连续体离散为通过有限个节点连接的有限个单元,并为每个单元选择一个能近似表达单元物理量的函数,接着建立单元节点的平衡方程组,这些平衡方程组的集合就构成代表整个结构力学特性的代数方程组,通过引入边界条件求解代数方程组,将每个单元的力学特征的组合起来就可以得到整体结构的力学特性。
这种将连续体离散成为有限的单元数和有限的节点数目的方法称为有限元法[8]。
有限元法是一种近似的求解方法,其近似性表现在两个方面:(1)单元与单元之间是通过节点连接,所以力和约束也是通过节点传递;这与实际连续体的力和约束传递方式不同。
(2)由于为每个单元选择的表达单元物理量的函数是近似的,所以单元上物理量的分布规律是近似假定的。
有限元分析过程可划分为三个阶段——有限元分析的前处理、有限元分析的计算和有限元分析的后处理。