04_零部件试验大纲-内外饰
内外饰验收标准
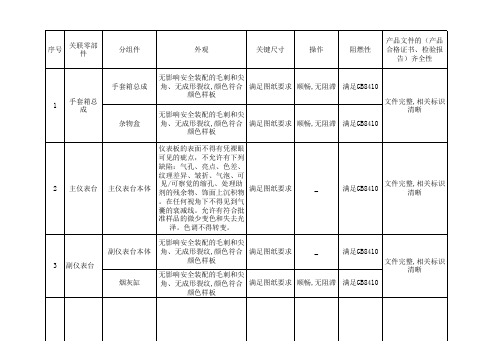
样板
无影响安全装配的毛刺和尖
清晰
序批准的色板或样品,其表面不应有毛刺、裂纹、污点、皱纹、凹凸及松弛等缺陷
泡沫对载体或表层的粘附力。
M:\试验大纲\
仪表板型式试验大纲.doc
枕强度要求和实验方法
(GB15083-2006)、汽车座椅头枕性能要求和实验方法(GB 抗拉强度、延伸率、剥离强度、耐磨性、缩水率、耐低温、抗褶皱、耐褪色牢度、压缩弹(GB 14167-2006)、汽车安全带动态性能要求和试验方法
(QC 244-1997)、乘用车正11551-2003)、汽车侧面碰撞
摩擦织物的评判、装饰材料抗洗涤性、饰件的耐摩擦色牢度
摩擦织物的评判、装饰材料抗洗涤性、饰件的耐摩擦色牢度
、表面抗刮伤性、相对光照的QCT 629-2005、弯曲刚度试验、折叠耐久性试验、摆动耐久性试验、抗高低温试验、抗温
度交变试验、镜盖翻转和开关
防夹力、安全性、滑动承载强度、面板保持强度、继电器烧
损、电机烧损、工作噪音、防水性(只试验天窗)、误操作M:\试验大纲\
天窗试验大纲.doc M:\试验大纲\
TEST\顶棚试验大纲.xls
屈服应力、球压硬度、缺口冲击韧性、老化温度、耐寒性、
温度存放试验、静态负载试验、回位时间及啪嗒声功能试验相应级别
M:\试验大纲\
TEST\试验大纲_遮阳板.doc。
零件试验大纲
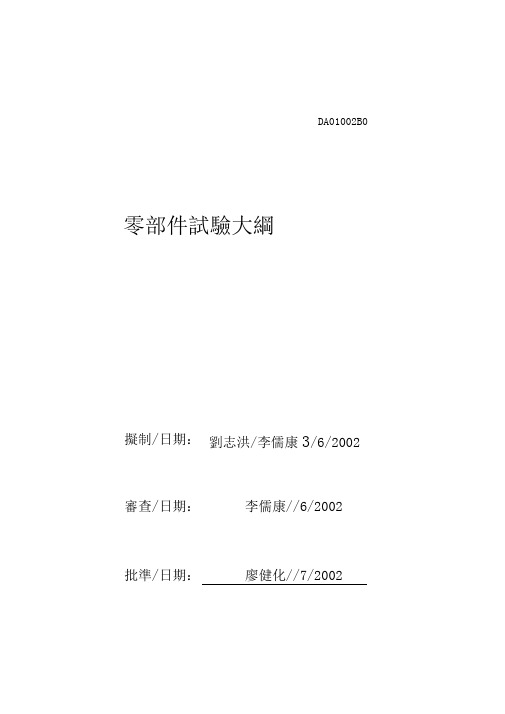
DA01002B0 零部件試驗大綱
擬制/日期:劉志洪/李儒康3/6/2002 審查/日期:李儒康//6/2002
批準/日期:廖健化//7/2002
2002-03-07
發布2002-03-07 實施
富士高產品開發部發布
表1.0
表1.0
表1.0
表1.0
表1.0
表1.0
表1.0
表1.0
表1.0
表1.0
表1.0
表1.0
表1.0
表1.0
表1.0
表1.0
表1.0
表1.0
表1.0
表1.0
表1.0
表1.0
注「本試驗大綱中帶號表示為選用項目,未注明的時間誤差為土 5秒,未注明的溫度誤差為土 2C .
2•在打樣和首批進料時需完成相關項目.
3•正常進料時IQC需要根据具体情況來定抽測頻次和項目
4 •實際操作中如產品有特別的要求,則應遵照執行.
Welcome To Download !!!
欢迎您的下载,资料仅供参考!
精品资料。
汽车整车benchmark介绍

(3)整车、车身和零部件点云测量
目的:获取整车、车身及零部件尺寸参数和硬点坐
标
1).整车三维坐标系
整车三维坐标系:指车辆制造厂在最初设计阶段确
定的三个正交平面组成的坐标系统,这三个基准平 面是: Y基准平面:车辆纵向对称平面, X基准平面:垂直于Y基准平面的铅垂平面, Z基准平面:垂直于Y和X基准平面的水平面。 注:规定X基准平面的前方,Y基准平面的左方和 Z基准平面的下方为负值。
YO平面的初步确定
整车坐标系建立
3.确定坐标系原点(前后垂直度) 根据扫描的设计状态下左右车轮分别取中心点,用
直线“线-3”连接两点。使“线-3”中点的坐标X=0。 选择一块前地板的下平面(纵梁的上平面)大面, 使坐标Z=0处于大面上。检查左右车轮中心坐标误 差在 1~3 mm 选择一块前地板的下平面(纵梁的上平面)大面, 工作坐标系沿着Z轴移动使坐标Z=0处于大面上。 激活世界坐标系(绝对坐标系),点击命令ModifyAlign-Align to Coordinate system ,在对话框中选 择全部点云,选择复选框Inverse Transform ,执行 该命令。 此时点云在世界坐标系中的位置就和步骤4.7中点云 在工作坐标系中的位置一样了
4.28前座椅与仪表板最小间距 215 4.29左前座椅与中柱护板间距 45 4.30左/右车门护板与仪表台间距 5.0/4.75 4.31方向盘下边缘与座椅上表面 200 4.32中/后排座椅靠背侧面与内饰面间距 40/60 4.33油门踏板与A柱护板Y向间距 40 4.34换档手柄与仪表台之间的最小距离 13 4.35方向盘与车门内把手间距 145 4.36右灯与轮罩内板 30 4.37膨胀水箱与纵梁间距 65 4.38继电器盒与左翼板内板间距 5 4.29排气管罩与水箱风扇护罩间距 42 4.30发动机与右侧边梁最小间距 25 4.41转向器与发动机后悬置螺栓中心 80 4.42排气管与发动机后悬置 60
上汽-内外饰零件与材料要求关注点
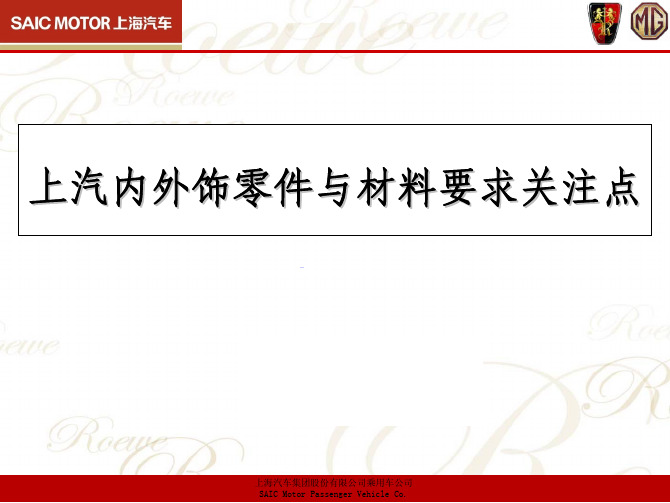
颜色要求与测定按照 SMTC 5 400 002要求
5 of
物理机械性能:
按上汽各材料性能企业标准或经批准的材料试验大纲
上海汽车集团股份有限公司乘用车公司 SAIC Motor Passenger Vehicle Co.
二,材料要求关注点
2,材料ELV要求关注点
样品要求:取自批量生产零件或与该状态一致的零件
¾ PP分子中存在叔碳原子,在光和热的作用下极易断裂降解。未加稳定 剂的PP在150℃下被加热半小时以上,或在阳光充足的地方曝晒12天 就会明显变脆。未加稳定剂的PP粉料在室内避光放置4个月也会严重 降解,散发出明显的酸味。在PP粉料造粒之前加入0.2%以上的抗氧剂 可以有效地防止PP在加工和使用过程中的降解老化。
No OK 等级C
∣ΔL*∣≤ 0.7
0.8≤∣ΔL*∣≤ 0.9
∣ΔL*∣≥ 1.0
∣Δa*∣≤ 0.3
0.4≤∣Δa*∣≤ 0.5
∣Δa*∣≥ 0.6
∣Δb*∣≤ 0.3
0.4≤∣Δb*∣≤ 0.5
∣Δb*∣≥ 0.6
2,对易起绒的织物(不具有纹理结构,如行李厢内饰、地毯)的公差 ; 3,非织物内饰件或零件具有非织物表面内饰件的样板基础公差 (黑色、棕色、米色和灰色)。
2,光照老化(内饰与外饰)
12 of
上海汽车集团股份有限公司乘用车公司
15
SAIC Motor Passenger Vehicle Co.
三,与材料有关的零件要求关注点
2,光照老化(内饰与外饰)
试验标准
PV3929
PV3930 (GB/T 16422.2)
氙灯类型
旋转式水冷氙灯
旋转式水冷氙灯
检测大纲整车检验过程检验零部件入厂检验关键部位检验成品入库检验

*****检测大纲版次/修改:A/0第1页/共34页检测大纲编号:***-**-004编制:审核:批准:会签:编制日期:2016年11月13日执行日期:2016年11月15日1 目的:为确保公司电动车辆产品能符合顾客要求,生产过程及出货时能准确、更快地掌握产品的检验标准,特制定***检测大纲,大纲包含零部件检验标准和整车检验标准。
2 适用范围:适用于******能源科技有限公司物料入厂、生产加工生产过程的质量控制。
3外观检验:3.1 整车外表及内饰表面要求3.1.1 车辆应周正,车身、底盘无明显扭曲、倾斜,车体外缘左、右对称部位的高度差≤30mm。
3.1.2 全车油漆外表不允许有锈蚀、起皱、气泡、虚漆、裂纹、脱落、涂膜不干等缺陷存在。
其色差:素色漆ΔΕ≤1.5;金属漆ΔΕ≤2.0。
3.1.3 全车油漆外表无划痕、碰伤、碰撞痕迹等表面缺陷;不得有油污、杂物及滴落的粘结剂等。
3.1.4 整车室内应清洁,内饰、座椅等无污损现象;无产品要求以外的杂物、标识、标记等。
3.1.5 车门密封条、左/右侧流水槽密封条装嵌平整,无褶皱、拱起、脱唇等缺陷,所有密封条圆角处应平顺,不脱空;对接部位的切口应整齐,对接部位间隙≤1mm。
3.1.6 顶盖装饰条扣装平整,无拱起,不脱空。
3.1.7 行李箱盖密封条应扣装平整、无皱折,拱起缺陷。
3.1.8 车身防擦条装贴牢靠,间隙均匀,相互平齐,不歪斜。
3.1.9 内饰件装配应牢固,相邻面安装平顺,间隙均匀,装配间隙≤10mm。
“三合一”CD机四周间隙0mm~3.1.10 仪表板各装配零件之间的高度差0mm~2mm,2mm,与面板高度差0mm~1mm。
3.1.11 底盘外露件不得有锈蚀现象。
3.1.12 各种商标及注意事项标贴必须粘贴在指定位置,且文字清晰、无误。
3.1.13 车辆的铭牌要求内容正确,打印字迹清晰,间隔均匀,排列整齐;铭牌铆接平整、可靠。
3.1.14 前盖与行李箱盖(后背门)包边应光滑、平齐、贴合紧密、无松动、无皱折。
JB-SJGF-0009-2012汽车内外饰零部件技术要求
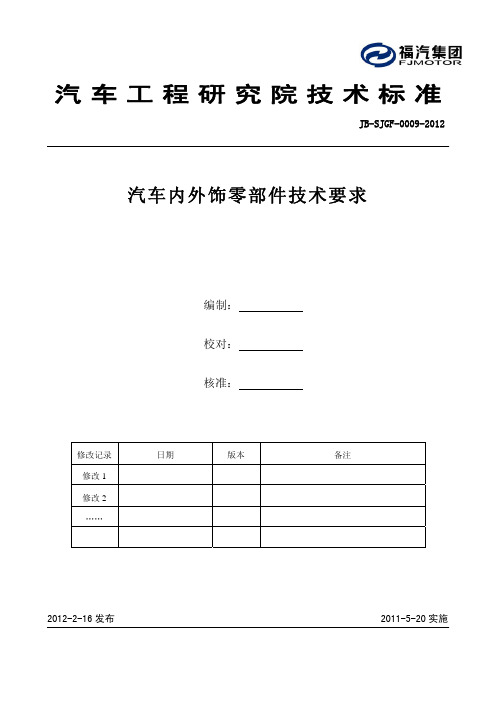
4.3 耐挥发性
4.3.1 样品条件
泡沫塑料材料,纺织品,皮革品或木制品要干燥至少 72 小时。将试样放在五氧化二磷上并用托架一
并放入干燥器中,在非真空的状态下干燥。
4.3.2 样品
3
应检测 5 个样品。按规定,测试样品应当从产品部件上截取。万一由于形状或尺寸的原因,不可能从
产品部件上截取的话,样品允许从与产品部件具备相同条件而制造的卷材或板材上截取。
面粘附及硬度变化等缺陷
15-1992
耐温度性(耐热、 - 不得有明显的脱色或褪色
5.1
耐寒、耐冷热循环) - 螺钉、螺母及密封部位不得产生松脱
- 不得有由于内在成分性能退化而产生的变形
- 试验后样件变形量不得超过±5mm
- 不得有明显的龟裂、剥落、溶胀、释出、发白、粉化、喷霜、表面粘附 QC/T
耐候性
陷
15-1992
- 表面不得出现软化或硬化等缺陷
5.5
- 不得有明显的变形、龟裂
QC/T
- 螺钉、螺母及密封部位不得产生松脱
15-1992
5.6
- 不得产生对表面质量有很大影响的像断裂、撕裂与变形等缺陷
QC/T
- 螺钉、螺母及密封部位不得产生松脱
15-1992
5.7
-重要外观件(如仪表板、门饰板、前后保险杠等):无明显磨损;非重要 QC/T
如果零件具有不同类型的表面,例如着色 PP 材料、喷漆或涂层,样件应从所有这些表面提取。
4.2.2 试验方法
样品应按 ISO 105(使用氙弧灯源)的试验条件:
- 黑板温度:89±3℃
- 实验室湿度:50±5%RH
- 辐照:65-100w/m2(范围 300-400nm)
关键零部件和材料COP-内外饰

关键零部件
或材料名称
检验项目
技术要求
方法
频次
抽样/判定
实施机构
记录
四门内饰板
外观、标识
1、零件不得有划痕、污损,飞边及缩痕等影响外观及使用性能的缺陷,零件颜色及皮纹按样板并参照配表,零件表面完好,光泽均匀。
2、产品应有永久标识(商标标记、供应商代码、零件代号、批次号、物料编码),标识内容清晰、完整、准确。
2、产品应有永久标识(商标标记、供应商代码、零件代号、批次号、物料编码),标识内容清晰、完整、准确
Hale Waihona Puke 目测每次采购每批随机抽5件,少于5件全检/(0,1)
质量部
零部件检查成绩书
目测
每次采购
每批随机抽5件,少于5件全检/(0,1)
质量部
零部件检查成绩书
性能
燃烧特性
符合GB 8410-2016要求
3C证书有效性确认
每年一次
产品中抽样
质量部
零部件检查成绩书
方向盘
外观、标识
1、零件表面无飞边、无残留物、无尖棱、无毛刺、无脱模划伤,不允许有气孔、脱皮、炫目或反光现象,表面外观颜色应均匀一致,并符合色板或初始认可的样件状态要求,条形码粘贴平整,牢固。
零件试验大纲

B: 20mm及以下振膜喇叭:
只有破壞跌落:讓喇叭從152cm高度, 任意方向,自由跌落于水泥地面,9次﹒(plantronic公司要求在此高度跌落18次)
2.紙盆喇叭的正常跌落按790/WI/034,從52cm高度,65±50光滑斜面上自由滑落到底部鐵板上.
將合格的產品放于-20℃的試驗箱中24hrs;取出室溫2hrs;檢查合格后,放于60℃的試驗箱;24hrs后,再取出室溫2hrs檢查.做兩個循環.
試驗后, 零部件/元件外觀功能正常.
喇叭
喇叭
頻響/靈敏度(紙盆)
P3
V=√P.R/G ; P=1W(當喇叭功率>1W)或P=0.25W(當喇叭功率≦1W); R=被測喇叭之阻值.
項目
序號
標准要求
試驗方法
合格標准
通用
濕度試驗
P1
零部件/元件經40℃溫度,93%RH濕度環境中儲存48hrs后, 應保持外觀功能正常.
將外觀功能正常的零部件,放于溫度為40℃,濕度為93%RH的試驗箱中,48hrs后取出檢查.
試驗后,零部件/元件外觀功能正常.
溫度試驗
P2
零部件/元件經(-20℃,24hrs→室溫2hrs→60℃,24hrs→室溫2hrs)2個溫度循環的儲存后,外觀功能正常.
電解電容防爆試驗
P21
8㎜以上的電容器之頂部需備有防爆結构.
對電容加上反向直流額定或交流電壓,使其發熱爆炸,檢查其是否從頂部爆出.
電容器從頂部爆出為正常.
電容泄漏電流
P22
電容器的漏電流值應符合元件SPEC.的允許接受范圍.
以DC額定電壓充電2分鐘后,測試漏電流值.
《xx汽车零部件公司TS16949实验室大纲(管理手册)》(48页)质量制度表格
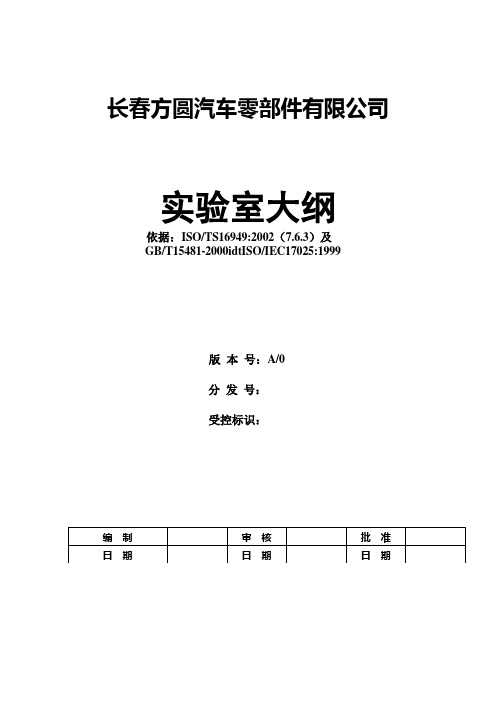
长春方圆汽车零部件有限公司实验室大纲依据:ISO/TS16949:2002(7.6.3)及GB/T15481-2000idtISO/IEC17025:1999版本号:A/0分发号:受控标识:长春方圆实验室大纲01目录文件编号Q/FY-SSC版次A/0共页第页长春方圆实验室大纲02发布实施令文件编号Q/FY-SSC版次A/0共页第页发布实施令公司为满足ISO/TS16949:2002标准中7.6.3条款“实验室要求”,依据ISO /IEC17025:1999《检测和校准实验室能力的通用要求》,并结合实验室实际情况重新编制了《实验室大纲》(第一版),现予以批准。
本手册于二○一○年十月一日起正式实施。
《实验室大纲》是描述实验室质量体系的纲领性文件,是实验室质量体系运行的行为准则和评审的依据,也是实验室质量保证能力的证实,手册所涉及的单位和员工都必须严格执行,确保实验室质量方针的实现。
总经理:年 月 日授 权 书长春方圆实验室大纲03授权书文 件 编 号Q/FY-SSC 版次 A/0 共 页第 页根据实验室质量体系要求,授权___为实验室负责人,并授予如下职责和权限:--在质量体系运行中代表部门经理行使权利;--按建立、实施和保持全面的质量体系;--对质量体系运行进行组织、协调、监督、检查,并负责外部质量保证的协调;--定期向部门经理报告有关质量状态;--描述实验室质量体系的有效性并且由此推进质量改进计划。
总经理:年月日授权人签字识别长春方圆实验室大纲04实验室概况文件编号Q/FY-SSC版次A/0共页第页实验室概况实验室是公司计量管理、理化试验的技术机构。
隶属于质量保证部。
实验室筹建于20XX年4月,并于20XX年8月正式投入使用。
主要业务是计量管理、化学分析、冲击检验、拉伸试验,为保证我公司产品的内在质量,起到相当大的作用。
20XX年,随着市场经济的发展、汽车生产量的加大,工厂扩建,为满足ISO/TS16949条款7.6.3“实验室要求”及ISO/IEC17025:1999实验室质量体系要求,持续改进的需要,新建实验室 20 平方米,实验室现有环境已符合标准要求。
汽车零部件试验汇总
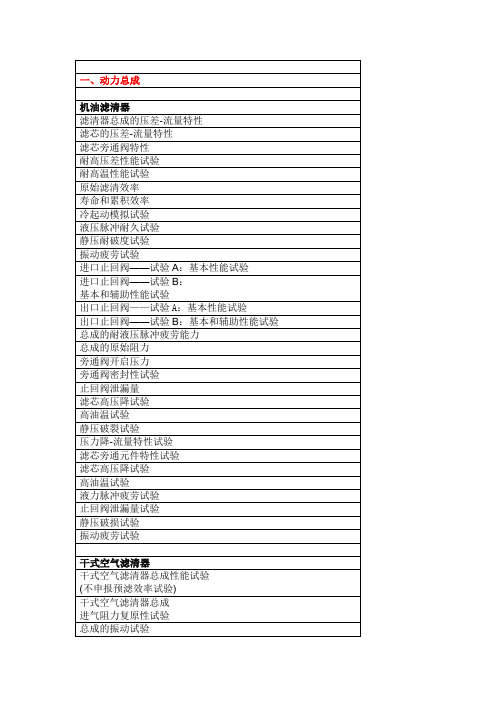
温升试验
低温工作和高温工作试验
温度变化试验
湿热试验
振动试验
耐久性试验
带点火开关的转向锁
外观检查
结构检查
档位转换试验
钥匙转动力矩试验
钥匙强度试验
转向锁强度试验
点火开关接线柱强度试验
绝缘电阻检查
触点压降试验
触点温升试验
耐温性试验
耐盐雾试验
耐振动试验
耐久性试验
翘板式开关
外形及安装尺寸检查
外壳防护等级试验
接头的耐腐蚀性试验
尼龙软管耐氯化锌试验
真空度试验
弯曲试验
耐汽油性试验
变形试验
结构
液压试验
缩颈试验
膨胀试验
吸水性试验
低温弯曲试验
动态条件下耐臭氧性
高温脉冲强度试验
盐雾试验
车轮
乘用车动态弯曲疲劳试验
乘用车动态径向疲劳试验
商用车辆辐板式车轮的
动态弯曲疲劳试验
商用车辆辐板式车轮和可拆卸式
轮辋的车轮动态径向疲劳试验
跑合试验Ⅱ
流量特性试验
效率试验
气密性试验
噪声试验
定转速冲击试验
变转速冲击试验
高温试验
真空助力器
密封性试验
空行程试验
反应时间试验
释放时间试验
输入一输出性能试验
振动耐久性试验
静强度试验
工作耐久性试验
耐腐蚀性试验
制动钳
扭转疲劳强度试验
清洁度
低压密封性试验
高压密封性试验
真空密封性试验
所需液量试验
拖滞扭矩试验
燃油箱盖的密封性
燃油箱内清洁度
燃油箱进气阀的通气试验
汽车研发流程【范本模板】
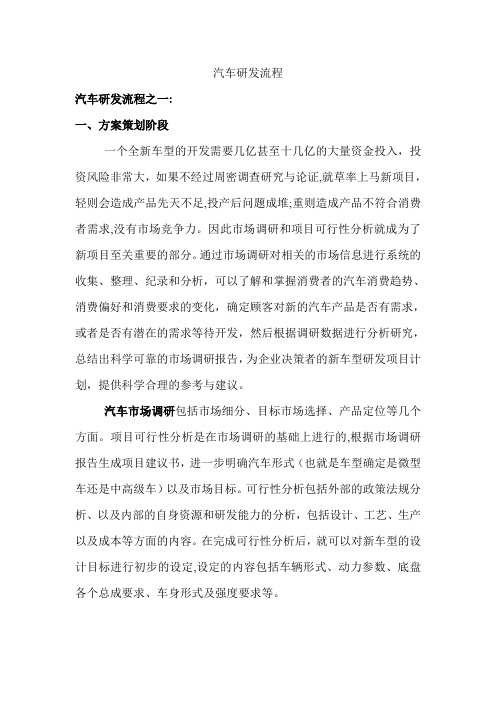
汽车研发流程汽车研发流程之一:一、方案策划阶段一个全新车型的开发需要几亿甚至十几亿的大量资金投入,投资风险非常大,如果不经过周密调查研究与论证,就草率上马新项目,轻则会造成产品先天不足,投产后问题成堆;重则造成产品不符合消费者需求,没有市场竞争力。
因此市场调研和项目可行性分析就成为了新项目至关重要的部分。
通过市场调研对相关的市场信息进行系统的收集、整理、纪录和分析,可以了解和掌握消费者的汽车消费趋势、消费偏好和消费要求的变化,确定顾客对新的汽车产品是否有需求,或者是否有潜在的需求等待开发,然后根据调研数据进行分析研究,总结出科学可靠的市场调研报告,为企业决策者的新车型研发项目计划,提供科学合理的参考与建议。
汽车市场调研包括市场细分、目标市场选择、产品定位等几个方面。
项目可行性分析是在市场调研的基础上进行的,根据市场调研报告生成项目建议书,进一步明确汽车形式(也就是车型确定是微型车还是中高级车)以及市场目标。
可行性分析包括外部的政策法规分析、以及内部的自身资源和研发能力的分析,包括设计、工艺、生产以及成本等方面的内容。
在完成可行性分析后,就可以对新车型的设计目标进行初步的设定,设定的内容包括车辆形式、动力参数、底盘各个总成要求、车身形式及强度要求等。
将初步设定的要求发放给相应的设计部门,各部门确认各个总成部件要求的可行性以后,确认项目设计目标,编制最初版本的产品技术描述说明书,将新车型的一些重要参数和使用性能确定下来。
在方案策划阶段还有确定新车型是否开发相应的变形车,确定变形车的形式以及种类。
项目策划阶段的最终成果是一份符合市场要求,开发可行性能够保证得到研发各个部门确认的新车型设计目标大纲。
该大纲明确了新车型的形式、功能以及技术特点,描述了产品车型的最终定位,是后续研发各个过程的依据和要求,是一份指导性文件。
汽车研发流程之二:二、概念设计阶段概念设计阶段开始后就要制定详细的研发计划,确定各个设计阶段的时间节点;评估研发工作量,合理分配工作任务;进行成本预算,及时控制开发成本;制作零部件清单表格,以便进行后续开发工作。
汽车法规-内外饰

EEC
7
机动车辆内饰件(操纵件、信号装置和指示 器的识别)方面法规
EEC
8
机动车辆发生正面碰撞时乘员的保护
EEC
9
机动车辆的后视镜
EEC
10
机动车辆及其挂车的法定铭牌及其内容,以 及铭牌安装的位置和方法
EEC
11
机动车辆车轮护板
EEC
12
机动车辆及其挂车安全玻璃及玻璃材料
EEC
13
机动车辆外部凸出物
中国 GB/T 11551-2003
12
汽车护轮板
中国
GB/T7063-1994
13
汽车前、后端保护装置
中国
GB/T17354-1998
14
车辆用植绒密封条磨损试验方法
中国
GB/T 12424-90
15
车辆用密封条的人工气候暴露试验方法
中国
GB/T 12425-90
16
车辆用密封条的污染性试验方法
中国
EEC
关于适应接近关于机动车和它们的拖车的法
14
定铭牌和标记及其固定位置和方法的成员国 法律的76/114/EEC理事会指令的技术进步,
EEC
而于1981年7月29日做出的委员会指令
2005/673/EC 78-316-EEC 96-79-EEC 71/127/EEC 76/114/EEC 78/549/EEC 92/22/EEC 74/483/EEC
1
关于机动车辆再可用性,再循环和再可复性 的型式认证和委员会70/156/EEC指令修正
EEC
机动车辆内饰件(除车内后视镜、操纵件、
2 车顶或滑动车顶、座椅靠背及其后部部件以
EEC
汽车内外饰的制造加工

5
1.2产品设计在模具设计 与制造中注意的问题(续)
• 3、优化产品结构 前提是满足产品设计和美观要求 主要有侧滑块(车灯面罩内抽、灯座外抽)、斜顶(前、后门护板),镶件 斜顶设计注意事项,一般情况下斜顶与z轴角度5—15 度,5度为最佳,最好 不要超过20度,特殊情况也可以为20度,斜顶胶位下垂直下为8---15mm,斜 顶前端距离水平方向的距离为15以上mm,一般取30---50mm 顶出垂直长度:产品高度(有时为产品2/3高度)+分型面最底端到底面距离 +15mm,注意水平方向斜顶产生干涉,和产品干涉,铲胶,曲面的曲率变化递 增或递减 ,中间不要产生峰值,在行位方向作拔模角,尽可能把斜顶作大, 因此注意筋的位置和其他卡扣的位置和方向 镶件设计为了加工方便,同时可以排气,如果产品需要拔模是分清分型线位 置,镶件大部分在后模 卡扣设计 方向尽量做外,向内造成模具结构复杂,成本高, 产品设计时,尽量不要产生到扣, 从加工角度来说,如果四周侧围高度大于30mm,圆角最好设计为大于3mm,最 少为2.5mm以上 对于侧抽芯来说,孔的 法向方向应最好与坐标轴垂直,
17
2.2成型加工性(续)
• ⑴.流变性能 聚合物的流变性能是聚合物成型加工过程中最基本的特征,主要指应 力作用下,塑料产生弹性,塑性和粘性变形的行为,以及这些行为与 塑料的结构,性质,温度,压力和作用方式,作用时间等的关系。直 接对聚合物材料的选用,加工工艺条件,加工设备,成型模具,产品 质量等产生重要影响。 • ⑵.热传导性能 塑料的成型一般先加热,成型后,再冷却定型。加热与冷却的实质就 是塑料的热传导。塑料在传热中,可能获得的温度梯度受到限制,由 于塑料是热的不良导体,热源与被加热的塑料之间温差太大,就会导 致局部温度过高,而引起塑料降解。塑料也不能冷却的过快,冷却介 质与熔体之间温差太大,就会导致制品内部产生较大的内应力。引起 制品变形。 塑料熔体的粘度很高,难于对流传热,而流动过程中 会产生剪切摩擦热,使熔体温度升高,有时会造成制品表面烧 焦。 许多塑料呈半结晶型,当受热熔融时,具有相态转变,从而 吸收较多的热量,当其冷却时,结晶度与冷却速度具有密切关系。
汽车内外饰零部件环境可靠性资料
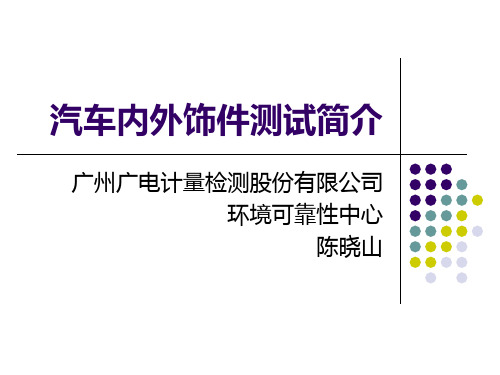
涂层类测试
油漆面是客户对车辆的第一品质感受。
涂层类测试
汽车涂层的组成
涂层类测试
常用涂料的评价方法与标准
涂膜的膜厚测试 附着力测试(百格法)
ISO 2808 2007(磁通量,涡流,金相等方法) ISO 2409-2007(划格子的方法与胶带)
硬度(铅笔硬度)
ISO 15184
漆膜耐冲击性测试
汽车内外饰件测试简介
广州广电计量检测股份有限公司 环境可靠性中心 陈晓山
目录
汽车内外饰件分类 材料类测试 涂层类测试 成品类测试
汽车内外饰件分类
按车身内外进行区分
-40ºC,大雪, 风力7
级。。。。
25º,微风, 湿度50%。。。
汽车外饰件分类
汽车内饰件分类
汽车内外饰件分类
外饰件光照测试条件
Content 内容
Pb
铅
Cd Cr6+
镉 六价铬
Hg
汞
PBB 多溴联苯
PBDE 多溴联苯醚
maximum concentration value
最大容许浓度
0.1% 1000ppm
0.01% 100ppm
0.1% 1000ppm
0.1% 1000ppm
0.1% 1000ppm
0.1% 1000ppm
密度
ISO 2811-1(比重瓶法)
粘度
旋转粘度计; ISO流量杯; 斯托默粘度计
细度
GB/T 1724
涂层类测试
常用涂料的评价方法与标准
干燥时间
ISO 1517
闪点 漆膜光泽度
ISO 3679 ASTM D523
漆膜耐水性(浸泡法) 漆膜耐化学试剂性(浸泡法)
试验条目-内外饰

乘用车--内外饰零件试验条目-20161028代码试验项目C-1C-1-1阻燃性试验C-1-2耐湿热试验C-1-3耐光老化性能试验C-1-4气味试验C-1-5高低温交变C-1-6热老化C-2C-2-1抗弯强度C-2-2冲击试验C-2-3耐高低温交变试验C-2-4耐光老化试验C-2-5气味试验C-2-6耐久试验C-2-7燃烧性能C-3顶棚总成C-3-1饰材与基材间粘结性试验C-3-2耐光色牢度试C-3-3燃烧特性C-3-4耐水污染性C-3-5抗低温冲击C-3-6气味试验C-3-7抗微生物性C-3-8挠度试验C-3-9耐摩擦性试验C-4C-4-1落球冲击性能C-4-2耐高、低温性能C-4-3燃烧性能C-4-4耐热老化性C-5行李架总成C-5-1抗冲击C-5-2耐湿热性C-5-3耐水性C-5-4耐酸碱性C-5-5盐雾试验C-5-6耐油性C-5-7耐划伤C-5-8耐热循环C-5-9复合循环试验C-6C-6-1耐高温性能C-6-2高低温循环试验C-6-3耐湿热性能C-6-4耐光色牢度C-6-5气味性C-6-6燃烧特性C-6-7耐摩擦性能C-6-8落球冲击性能ABC柱护板总成乘客扶手总成轮罩总成、轮罩装饰板行李箱盖板总成C-6-9面料剥离力C-7仪表板总成C-7-1耐气候交变C-7-2燃烧特性试验C-7-3振动耐久性C-7-4湿度高低温性试验C-7-5耐光老化试验C-7-6气味试验C-7-7耐磨性能C-7-8耐化学活性剂试验C-8地毯总成C-8-1单位面积总质量C-8-2断裂强力(N)C-8-3燃烧特性C-8-4耐光色牢度C-8-5摩擦色牢度C-8-6气味性C-8-7撕破强力C-8-8耐磨耗试验C-8-9热形状稳定性C-8-10浸水色牢度C-9C-9-1气候交变试验C-9-2耐石击试验C-9-3耐化学腐蚀C-9-4冷凝水恒定气候中的试验C-9-5盐雾试验C-9-6温度交变试验C-9-7耐高低温湿热性能C-10门护板总成C-10-2气味特性C-10-3冷凝成份C-10-4耐光色牢度C-10-5燃烧速度C-10-6耐热老化性能C-10-7耐高低温、湿热性能C-10-8耐臭氧老化性能C-11车门保护膜C-11-1粘接性能C-11-2耐寒性C-11-3耐摩擦及耐洗涤性C-11-4耐候性C-11-5耐光性C-11-6耐热性C-11-7抗热老化性C-12铁堵C-12-1强度试验C-12-2耐腐蚀性试验C-12-3耐温性C-13沥青板C-13-1断裂拉伸力散热器格栅总成C-13-2燃烧性能C-13-3耐候性C-13-4性能试验C-13-5气味性C-14橡胶密封条C-14-1力性能检测C-14-2耐候性C-14-3插拔力C-14-4压缩负荷C-15C-15-1强度\硬度C-15-2耐腐蚀C-16橡胶管路C-16-1耐高压性能C-16-2耐臭氧性能C-16-3高低温性能C-16-4清洁度C-16-5抗拉性能C-17前后保险杠C-17-1落球冲击性能C-17-2耐高、低温性能C-17-3燃烧性能C-17-4耐热老化性螺栓、支架(每种)。
汽车装饰技术实验报告(3篇)

第1篇一、实验目的本次实验旨在通过实际操作,了解和掌握汽车装饰的基本技术和方法,提高对汽车装饰材料的认识,培养动手能力和创新能力。
实验内容包括汽车装饰材料的识别、汽车装饰品的安装、汽车内饰的改造等。
二、实验时间2023年11月15日三、实验地点汽车维修与装饰实验室四、实验材料与工具1. 实验材料:- 汽车装饰材料:地胶、汽车装饰板、塑料卡扣、导光条、汽车装饰条、夜光粉等。
- 汽车内饰件:座椅、仪表盘、门板等。
2. 实验工具:- 电钻、螺丝刀、扳手、切割机、剪刀、打胶枪、热风枪等。
五、实验步骤1. 材料识别与准备- 对实验所需的汽车装饰材料进行识别,了解其特点、用途及安装方法。
- 根据设计要求,准备好所需的各种装饰材料。
2. 汽车装饰品的安装- 选择合适的汽车装饰品,如地胶、装饰条等。
- 使用电钻、螺丝刀等工具,将装饰品固定在汽车内饰件上。
- 注意装饰品的平整度和美观性。
3. 汽车内饰改造- 对座椅、仪表盘、门板等内饰件进行测量,确定改造方案。
- 使用切割机、剪刀等工具,对内饰件进行裁剪。
- 使用打胶枪、热风枪等工具,对内饰件进行粘贴或焊接。
- 对改造后的内饰件进行打磨、抛光等处理。
4. 汽车装饰照明系统改造- 选择合适的汽车装饰照明用发光管和背光源。
- 使用切割机、剪刀等工具,对内饰件进行裁剪,为发光管和背光源预留空间。
- 使用电钻、螺丝刀等工具,将发光管和背光源固定在内饰件上。
- 连接电源,检查照明效果。
5. 汽车装饰尾管安装- 选择合适的汽车装饰尾管。
- 使用电钻、螺丝刀等工具,将尾管固定在汽车尾部。
- 注意尾管的对称性和美观性。
六、实验结果与分析1. 实验过程中,成功完成了汽车装饰品的安装、汽车内饰的改造、汽车装饰照明系统改造以及汽车装饰尾管的安装。
2. 通过实验,掌握了汽车装饰的基本技术和方法,提高了动手能力和创新能力。
3. 实验过程中发现,汽车装饰材料的选择和安装方法对装饰效果有很大影响。
- 1、下载文档前请自行甄别文档内容的完整性,平台不提供额外的编辑、内容补充、找答案等附加服务。
- 2、"仅部分预览"的文档,不可在线预览部分如存在完整性等问题,可反馈申请退款(可完整预览的文档不适用该条件!)。
- 3、如文档侵犯您的权益,请联系客服反馈,我们会尽快为您处理(人工客服工作时间:9:00-18:30)。
4
耐振动性试验
1.共振点测定试验 试样应以接近使用状态的条件安装在振动台上。施加相对于试样的安装方式依次给予上 下,左右及前后的正交方向的简谐振动。但是,简谐振动的谐波含有率原则上为振动加速度的 按照QC/T15-92规定6进 25%以下。原则上试验温度定为标准温度23±5℃。 行检查 2.振动耐久性试验 振动耐久性试验是根据汽车的类别及其制品实际安装的部位,按表13规定的6级进行,也 就是2、3、4、7、9和11级。适用分类按表13规定,试验时间按表14规定。
2
耐候性试验
1.室外耐候性试验:曝露架按GB 3511第6.1条或GB 3681第6条或GB I767第3条的规定装置。 试样的安装按GB 3511第6.2条,GB 3681第9.4条、GB 1767第3.2条的规定。 2.室外耐光性:试样表面到玻璃板(厚3mm的磨光平板玻璃)的距离不小于5cm,并应保持玻 按照QC/T15-92规定6进 璃板的清洁。按QC/T17-92中8.2.2的规定,但用QC/T17-92表4中试样a时,应紧贴在框架上。 行检查 3.室外遮蔽试验:试样下端到地面的距离应大于50cm并按QC/T17-92中8.2.2规定安装。 4.强化耐候试验:方法按QC/T17-92表12; 5.强化耐光试验:方法按QC/T17-92表13; 6.强化耐臭氧试验:方法按QC/T17-92表14;
8
耐擦伤性试验
1.刮伤试验 制品表面用000#钢纤维摩擦,表面压力为6.5kpa,速度为6m/min,摩擦次数由供需双方 商定。 按照QC/T15-92规定6进 2.洗涤试验 行检查 用符合规定性质的泥水涂在制品表面,使表面均匀湿润,让其自然干燥,制品表面的泥 用水粗略除去,然后用海绵、布或塑料刷洗刷三至五次,最后 使制品自然干燥。
型 式 试 验 大 纲
Test List
产品名称(Part name): 产品型号(Product No.):
序号 试验项目 No.
隔热垫
Item
标准值 Standard value
试验方法 Test method
试验地点 Test place
试验周期 Test cycle
试验设备 Test equipment
1.供试验用的试样,取自实际装配使用状态下的制 品,在不影响制品性能的情况下,亦可采用试验片, 试验时模拟制品在汽车上的实用状态。 耐磨仪、天平 (精 2.试样应从制造后至少放置24h的制品中随机抽取, 度0.1g)、CS—10 并在试验前将试样按GB29184.1规定的环境放置不少 砂轮 于4h,再进行试验:如果需要也可由供需双方协商规 定其它条件。 3.试样数量不少于3件
1.供试验用的试样,取自实际装配使用状态下的制 品,在不影响制品性能的情况下,亦可采用试验片, 试验时模拟制品在汽车上的实用状态。 2.试样应从制造后至少放置24h的制品中随机抽取, 清洁布、化学介质 并在试验前将试样按GB29184.1规定的环境放置不少 于4h,再进行试验:如果需要也可由供需双方协商规 定其它条件。 3.试样数量不少于3件
振动试验台
1.供试验用的试样,取自实际装配使用状态下的制 品,试验时模拟制品在汽车上的实用状态。 2.试样应从制造后至9184.1规定的环境放置不少 于4h,再进行试验:如果需要也可由供需双方协商规 定其它条件。 3.试样数量不少于3件
5
耐化学介质性试验
1.供试验用的试样,取自实际装配使用状态下的制 品,在不影响制品性能的情况下,亦可采用试验片, 试验时模拟制品在汽车上的实用状态。 000#钢纤维、自来 2.试样应从制造后至少放置24h的制品中随机抽取, 水、尘 土、稀释 并在试验前将试样按GB29184.1规定的环境放置不少 20倍的清洁剂 于4h,再进行试验:如果需要也可由供需双方协商规 定其它条件。 3.试样数量不少于3件
4h-5h(冷 热交变试验 恒温箱 除外)
1.供试验用的试样,取自实际装配使用状态下的制 品,在不影响制品性能的情况下,亦可采用试验片, 试验时模拟制品在汽车上的实用状态。 2.试样应从制造后至少放置24h的制品中随机抽取, 并在试验前将试样按GB29184.1规定的环境放置不少 于4h,再进行试验:如果需要也可由供需双方协商规 定其它条件。 3.试样数量不少于3件
100h
恒温恒湿箱
1.供试验用的试样,取自实际装配使用状态下的制 品,在不影响制品性能的情况下,亦可采用试验片, 试验时模拟制品在汽车上的实用状态。 2.试样应从制造后至少放置24h的制品中随机抽取, 并在试验前将试样按GB29184.1规定的环境放置不少 于4h,再进行试验:如果需要也可由供需双方协商规 定其它条件。 3.试样数量不少于3件
样品要求 size
Sample
标准来源 (Standard) : QC/T15-92 《汽车塑料制品通用试验方法》、 GB8410-200×、 QC/T 17-92 、 Q/CC JT001-2005 、 Q/CC JT055 — 2007
1
耐温度性试验
1.常规耐热试验 按130±2℃的环境温度调整恒温箱的温度,在此温度下,将试样放置在恒温箱中1h后, 用红外灯加热,把试样表面温度提高到表5规定的温度,并在此温度下至少保持3h,然后将试 样取出,按第6条规定项目进行检查。 2.极限耐热试验 如果试样在130±2℃温度下未发现异常现象时,继续提高恒温箱的温度,每次提高10℃ 按照QC/T15-92规定6进 或5℃让试样在此温度下保持1h,观察试样的变化,由目测认定的变形温度,就作为极限耐热 行检查 温度。 3.耐寒性试验 按-40±2℃温度调整低温箱的温度,达到规定温度后,将试样放置在低温箱中至少4h, 然后从低温箱中取出,按第6条规定项目进行检查。 4.冷热交变试验 130±2℃高温、-40±2℃低温下循环试验后按表6规定,至少2次以上循环试验
7
耐磨损性试验
根据制品表面形状和磨损的性质,试验可分为三种形式: 1.曲面滑动磨损试验检查制品曲面的滑动磨损:操作条件按QC/T 15-92表17规定项目,也 可由供需双方商定,QC/T 15-92表17的操作条件仅作为转向盘试验时按照。将试样紧固在试 验装置上,在一定载荷下,水平前后移动规定的次数,注意不应使摩擦表面产生偏负荷,每次 试验均应换新的摩擦布,试验次数由供需双方商定。 2.平面滑动磨损试验检查制品平面的滑动磨损:操作条件按QC/T 15-92表18规定项目,也 按照QC/T15-92规定6进 可由供需双方商定。QC/T 15-92表18规定的操作条件仅作为烫印成型制品试验时按照。将试 行检查 样紧固在试验装置上,在一定载荷下,水平前后移动规定的次数,注意不应使摩擦表面产生偏 负荷,每次试验均应换新的摩擦布,试验次数由供需双方商定。 3.落砂磨损试验检查制品的耐擦伤性:从制品平坦部位截取规定尺寸的试样,经供需双方商 定进行测定。操作条件按QC/T 15-92表19规定进行。将试样固定在试样安装台上,当料斗旋 转时,将磨料倒入漏斗中进行试验,当所有磨料均通过导管时,改变试样的位置,用轻微的压 缩空气除去试样表面的磨耗粉尘,然后用另一试样重复试验。
9
燃烧特性试验
燃烧速度不大于 100mm/min并在60s 或 将处理过的试样,放在U形试样支架上,然后放入燃烧箱,点燃燃烧灯,记录火焰的传播速 度,计算试样的燃烧速度。公式:V=60x(L/T) 100mm内自熄 或按长城企业标准QCC_JT055-2007《隔热层技术条件》
1.试样的厚度为所试零件厚度,但不超过13mm 2.以不同种类材料进行燃烧性能比较时,试样必须具 有相同尺寸(长、宽、厚),通常采样时必须使试样 沿全长有相同横截面 3.若零件的形状和尺寸不足以制成规定尺寸的标准试 样时,则应保证下列最小尺寸试样,但要记录。 a.如果试样宽度介于3~60mm,长度应至少为356mm 。在这种情况下试样要尽量做成接近零件的宽度; b.如果试样宽度大于60mm,长度应至少为138mm,此 燃烧箱、试样支架 时,可能的燃烧距离相当于从第一条标线到火焰熄灭 、燃气灯、金属梳 时的距离或从第一条标线开始至试样末端的距离; 、温度计、钢板尺 c.若宽度小于60mm,且长度小于356mm或宽度大于 、通风橱 60mm,长度小于138mm的试样,则不能按本标准试验; 宽度小于3mm的试样也不能按本标准进行试验。 4.应从被试材料上取下至少5块试样。如果沿不同方 向有不同燃烧速度的材料,则应在不同方向截取试 样,并且要将5块(或更多)试样在燃烧箱中分别试 验,以测得最高燃烧速度。 5.试验前试样应在温度23±12℃和相对湿度45%~ 55%的标准状态下存放24h以上,且应一直保持到试 验前的片刻,但不超过168h
6
耐冲击性试验
落锤冲击试验、落下冲击试验、石子冲击试验 试验程序及操作:按下列程序进行有两种方法,一种是测定平均破裂强度,另一种是连续使用 同一试样测定平均破裂强度。 a.测定平均破裂强度 将试样牢固地安放在指定的位置上,重锤从适当高度自由落下,进行预备性试验,按这 种方法,调节重锤下落位置,假设试验初始高度h0为破裂高度,重锤从h0高度自由落下冲击 试样,如果试样出现碎裂,试验高度降低△h,重锤在h0-△h高度自由落下冲击下一个试样, 按照QC/T15-92规定6进 如果试样没有出现碎裂,试验高度提高△h,重锤在h0十△h高度自由落下冲击下一个试样, 行检查 用此方法,至少用二十个试样重复试验,可得出平均破裂强度和最小破裂强度。 b.用少量试样测定破裂强度的方法 将试样牢固地安放在指定的位置上,重锤从适当高度自由落下,进行预备性试验;按这种 方法,调节重锤下落位置,假设试验初始高度h0为破裂高度,重锤从、高度自由落下冲击试 样,如果试样出现碎裂,试验高度降低△h,重锤在h0-△h高度自由落下冲击下一个试样,如 果试样没有出现碎裂,试验高度提高△h,重锤在h0十△h高度自由落下冲击同一个试样,用 此方法,将所有试样重复试验,可测定出平均破裂强度和最小破裂强度。
曝露架、玻璃板
1.试样应是零、部件。若受试验条件限制,允许采用 参考QC/T17-92中表4规定的试样,涂层用的试片。 2.试样数不少于3件