高炉车间系统设计毕业论文
年产量500万吨高炉炼铁车间设计毕业论文
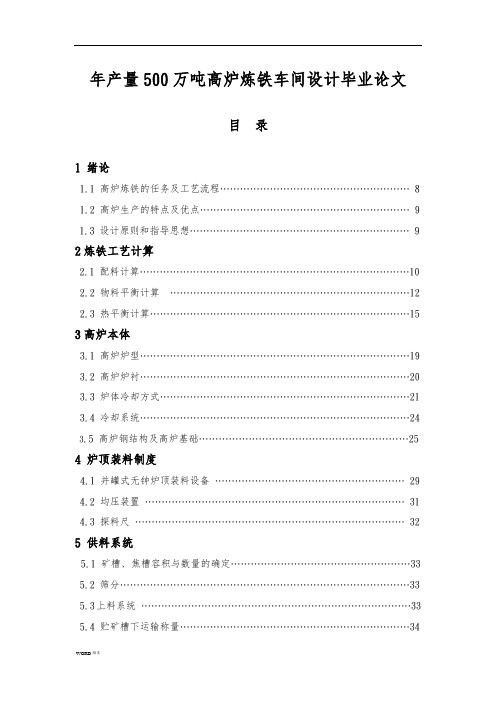
年产量500万吨高炉炼铁车间设计毕业论文目录1 绪论1.1 高炉炼铁的任务及工艺流程 (8)1.2 高炉生产的特点及优点 (9)1.3 设计原则和指导思想 (9)2炼铁工艺计算2.1 配料计算 (10)2.2 物料平衡计算 (12)2.3 热平衡计算 (15)3高炉本体3.1 高炉炉型 (19)3.2 高炉炉衬 (20)3.3 炉体冷却方式 (21)3.4 冷却系统 (24)3.5 高炉钢结构及高炉基础 (25)4 炉顶装料制度4.1 并罐式无钟炉顶装料设备 (29)4.2 均压装置 (31)4.3 探料尺 (32)5 供料系统5.1 矿槽、焦槽容积与数量的确定 (33)5.2 筛分 (33)5.3上料系统 (33)5.4 贮矿槽下运输称量 (34)6送风系统6.1 鼓风机的选择 (35)6.2 热风炉的结构 (35)6.3 热风炉常用耐火材料 (37)6.4 燃烧器及送风制度的选择 (37)6.5 热风炉主要管道直径的选定 (37)7.渣铁处理系统7.1 风口平台及出铁场 (39)7.2 炉前设备 (39)7.3 炉渣处理 (41)8 煤气除尘系统8.1 除尘设备及原理 (44)8.2 有关设备 (45)8.3 重力除尘器 (45)9 喷吹设备9.1 设计为喷吹煤粉 (47)9.2 高炉喷煤设备 (48)10车间布置形式10.1 车间布置 (50)10.2 本设计车间平面布置形式 (50)结束语 (52)参考文献 (53)1 绪论1.1 高炉炼铁的任务及工艺流程高炉炼铁的任务是用还原剂(焦炭、煤粉)在高温条件下将铁矿石或含铁原料还原成液态生铁的过程。
高炉生产要求以最小的投入获得最大的产出,即做到高产、优质、低耗、有良好的经济效益。
高炉生产时借助高炉本体和其辅助设备来完成的。
高炉本体是冶炼生铁的主体设备,它是由耐火材料砌筑的竖立式圆筒形炉体,最外层是由钢板制成的炉壳,在炉壳和耐火材料之间有冷却设备。
包头地区1500m3高炉本体结构设计毕业设计论文
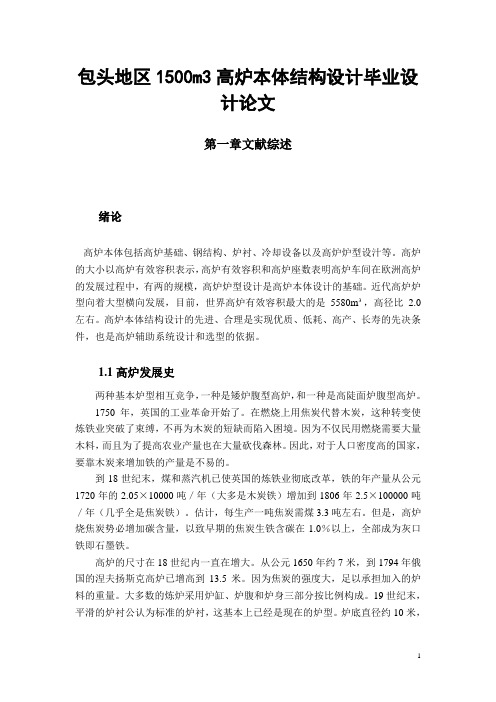
包头地区1500m3高炉本体结构设计毕业设计论文第一章文献综述绪论高炉本体包括高炉基础、钢结构、炉衬、冷却设备以及高炉炉型设汁等。
高炉的大小以高炉有效容积表示,高炉有效容积和高炉座数表明高炉车间在欧洲高炉的发展过程中,有两的规模,高炉炉型设计是高炉本体设计的基础。
近代高炉炉型向着大型横向发展,目前,世界高炉有效容积最大的是5580m³,高径比 2.0左右。
高炉本体结构设计的先进、合理是实现优质、低耗、高产、长寿的先决条件,也是高炉辅助系统设计和选型的依据。
1.1高炉发展史两种基本炉型相互竞争,一种是矮炉腹型高炉,和一种是高陡面炉腹型高炉。
1750年,英国的工业革命开始了。
在燃烧上用焦炭代替木炭,这种转变使炼铁业突破了束缚,不再为木炭的短缺而陷入困境。
因为不仅民用燃烧需要大量木料,而且为了提高农业产量也在大量砍伐森林。
因此,对于人口密度高的国家,要靠木炭来增加铁的产量是不易的。
到18世纪末,煤和蒸汽机已使英国的炼铁业彻底改革,铁的年产量从公元1720年的2.05×10000吨/年(大多是木炭铁)增加到1806年2.5×100000吨/年(几乎全是焦炭铁)。
估计,每生产一吨焦炭需煤3.3吨左右。
但是,高炉烧焦炭势必增加碳含量,以致早期的焦炭生铁含碳在1.0%以上,全部成为灰口铁即石墨铁。
高炉的尺寸在18世纪内一直在增大。
从公元1650年约7米,到1794年俄国的涅夫扬斯克高炉已增高到13.5米。
因为焦炭的强度大,足以承担加入的炉料的重量。
大多数的炼炉采用炉缸、炉腹和炉身三部分按比例构成。
19世纪末,平滑的炉衬公认为标准的炉衬,这基本上已经是现在的炉型。
炉底直径约10米,炉高约30米。
全部高炉都设有两只以上的风嘴。
另一个巨大的进步就是采用热风。
20世纪后,现代钢铁业就蓬勃发展起来。
1.2高炉炉型及展过程高炉是竖炉,高炉内部工作空间剖面的形状称为高炉炉型或高炉内型。
高炉冶炼的质是上升的煤气流和下降的炉料之间进行传热传质的过程,因此必须提供燃料燃烧的空间,提供高温煤气流与炉料进行传热传质的空问。
毕业论文:高炉炼铁系统设计-精品【范本模板】
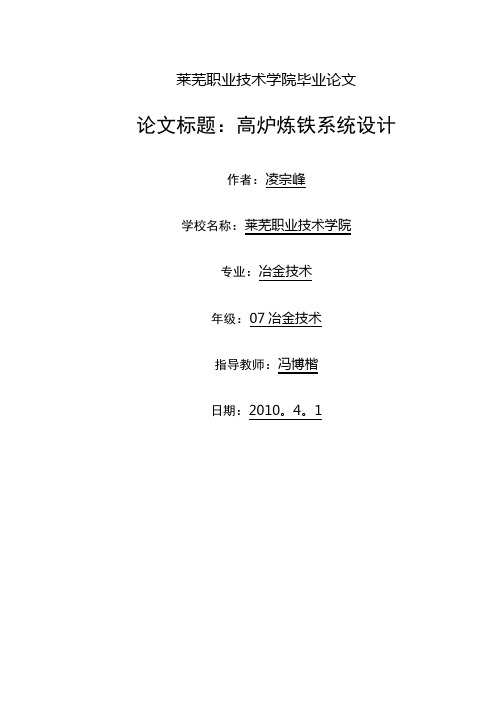
莱芜职业技术学院毕业论文论文标题:高炉炼铁系统设计作者:凌宗峰学校名称:莱芜职业技术学院专业:冶金技术年级:07冶金技术指导教师:冯博楷日期:2010。
4。
1目录内容提要与关键词¨¨¨¨¨¨¨¨¨¨¨3手抄在论文本上,最后再根据内容补填目录,要求手写!正文¨¨¨¨¨¨¨¨¨¨¨¨¨¨¨¨¨4参考文献¨¨¨¨¨¨¨¨¨¨¨¨¨¨¨¨58摘要本设计要求建年产量为200万吨生铁的高炉系统。
高炉车间的七大系统:即高炉本体系统、上料系统、渣铁处理系统、喷吹系统、送风系统、除尘系统和冷却系统都做了较为详细的叙述。
高炉炼铁是获得生铁的主要手段,是钢铁冶金过程中最重要的环节之一,在国民经济建设中起着举足轻重的作用。
高炉是炼铁的主要设备,本着优质、高产、低耗和对环境污染小的方针,在预设计建造一座年产生铁200万吨的高炉炼铁系统,本设计说明书详细的对其进行了高炉设计,其中包括绪论、工艺计算(包括配料计算、物料平衡和热平衡)、高炉炉型设计、高炉各部位炉衬的选择、炉体冷却设备的选择、风口及出铁场的设计、原料系统、送风系统、煤气处理系统、渣铁处理系统、高炉喷吹系统等。
设计的同时还结合国内外相同炉容高炉的一些先进的生产操作经验和相关的数据,力争使该设计的高炉做到高度机械化、自动化和大型化,以期达到最佳的生产效益. 关键词:高炉;炼铁;设计;煤气处理;渣鉄处理;1绪论1。
1概述钢铁是重要的金属材料之一,被广泛应用于各个领域,钢铁生产水平是一个国家发展程度的标志。
设计一座年产生铁300万吨的高炉车间

设计一座年产生铁 300 万吨的高炉车间毕业设计说明书设计(论文)题目:设计一座年产生铁 300 万吨的高炉车间学生姓名:学号:专业班级:学部:指导教师:摘要按照设计说明书的要求,设计一座年产300万吨的炼钢生铁的炼铁厂。
该厂的高炉车间由2座有效容积2163立方米的高炉,车间布置形式采用半岛式布置。
高炉炼铁生产工艺流程主要包括六个系统:高炉本体系统、高炉车间原料系统、高炉送风系统、高炉喷煤系统、煤气除尘系统渣?处理系统。
其中高炉的炉衬设计方法采用的是均衡炉衬的方法,根据不同的冶炼条件砌筑不同的砖。
冷却方式:炉身部分采用板壁结合的方式炉腰部分采用凸台冷却壁;炉缸和炉底采用光面冷却壁和水冷炉底结构。
设计的热风炉采用传统改进型内燃式热风炉。
蓄热式和燃烧室在同一炉壳内。
这部分同时包括热风炉各种设备和阀门的选取计算。
上料系统采用的皮带机连续上料,同时增加了皮带的速度和宽度,满足高炉冶炼的要求。
炉顶装料设备采用串罐式无料钟炉顶装料。
喷吹系统增加了煤的数量,采用了单管路串罐式直接喷吹。
煤气处理设备采用的是湿法除尘设备。
所涉及的计算有高炉和热风炉尺寸的计算、高炉的物料平衡和热平衡计算以及热风炉风机的选择等。
本设计依据现有的经验结合国内外先进生产技术,对设备及相应的参数进行选择并作了具体阐述和计算,同时对高炉车间工艺布置作了比较详细的叙述,并绘制里高炉本体砌砖与冷却设备图、热风炉剖面图、高炉车间平面布置图、高炉车间总剖面图四张图。
关键词: 高炉;设计;热风炉;湿法除尘;工艺流程; 布置ABSTRACTThe design’s task is to build an iron-making plant, which has two blast furnaces and each capacity is 2163m3. The plant generates 3000,000 tons iron every year. There are seven chapters in the design.The seven systems of the iron-making plant is follow: blast furnace system、raw material system、blast air blowing system、fuel injecting system、gas dust removal system、slag processing systems The BF lining adopted equalization lining method and was made of alumina brick and chayote in upper of BF and all carbon brick in the bottom of BF.The cooling methods were batten wall style in shaft, boss-cooling stave in bosh, smooth cooling stave in hearth and water-cooling stave in bottom of hearth.The air-stove was modified tradition style of internal combustion. The checker chamber and combustion chamber were in the same furnace shelland divided by heat insulation wall. And the combustion chamber was eye-style. Furthermore this part of the paper included the selection of various equipments and valves.The charging equipment used the belt machine to continuing supplying charge and the belt velocity and width were increased in order to meet the BF melting needs. The furnace roof equipment used string pot style of non-bell furnace roof. Injection system increased amount of coal and use single valve line sting pot direct injection. The gas treating system used hydro filter equipment.The computes in the paper have size of BF and air-stave, charge balance, heat balance and fan of air-stave choice, etc.The design experience based on the existing domestic and foreign advanced production technology, equipment and the appropriate choice of parameters and were calculated in detail and at the same time on the blast furnace process layout of the workshop were described in more detail, and ontology mapping in blast furnace bricklayer and cooling equipment, maps, profiles of hot gas, blast furnace workshop floor plan, the total cross-section of blast furnace workshop 4 maps.Keywords: blast furnace; process; plant; design; layout.目录摘要IABSTRACT II引言 11 文献综述 21.1 概述 21.2厂址的选择 21.2.1厂址选择应考虑的因素 21.2.2高炉炼铁车间平面布置应遵循的原则3 1.2.3车间布置形式 31.3高炉生产主要经济技术指标 41.4原燃料化学成分 41.5 本设计采用的新技术 52 工艺计算 62.1 配料计算 62.1.1 原燃料成分的整理 62.1.2 预定生铁成分72.1.3 原燃料的消耗72.1.4 渣量及炉渣成分的计算82.1.5 生铁成分的校对82.2 物料平衡计算 92.2.1 风量的计算 92.2.2炉顶煤气成分的计算92.2.3物料平衡表102.3 热平衡112.3.1 热收入的计算112.3.2 热支出的计算113 高炉本体设计153.1 高炉数目及总容量的确定153.2 炉型设计153.3 参数173.4 炉衬设计及高炉基础183.4.1 高炉炉基的形状及材料183.4.2 高炉炉底和各段炉衬的选择、设计和砌筑19 3.5 概述高炉冷却及钢结构213.5.1 炉底冷却型式选择213.5.2 炉底冷却型式选择213.5.3 高炉供水量、水压的确定223.5.4 风口数目及直径233.5.5 铁口233.5.6炉壳及钢结构确定234 原料系统264.1 焦矿槽容积的确定264.1.1 贮矿槽和附矿槽的布置、容积及数目的确定 26 4.1.2焦矿槽的布置、容积及数目的确定274.2 槽上、槽下设备及参数的确定 274.2.1 槽上设备274.2.2 槽下设备及参数选择274.3 皮带上料机能力的确定284.3.1.皮带机选择 284.3.2.为保证胶带安全运行,设计时采取了以下措施285 送风系统295.1 高炉鼓风机的选择295.1.1 高炉入炉风量295.1.2 鼓风机风量 295.1.3 高炉鼓风压力295.1.4 鼓风机的选择305.2 热风炉305.2.1 热风炉座数的确定305.2.2 热风炉工艺布置305.2.3 热风炉型式的确定305.2.4 热风炉主要尺寸的计算315.2.5 热风炉设备 335.2.6 热风炉管道及阀门336 炉顶设备356.1炉顶基本结构356.2布料方式367 煤气处理系统377.1 荒煤气管道377.1.1 导出管377.1.2上升管387.1.3下降管387.2 除尘系统的选择和主要设备尺寸的确定38 7.2.1 粗除尘装置 387.2.2 粗除尘装置 397.2.3 精细除尘装置407.2.4 布袋除尘器 407.2.5 附属设备408 渣铁处理系统418.1 风口平台及出铁场418.2 炉渣处理设备 418.3 铁水处理设备 428.3.1 铁水罐车428.3.2 铸铁机428.3.3 铸铁机428.4 铁沟流咀布置 428.4.1 渣铁沟的设计428.4.2 渣铁沟的设计438.5 炉前设备的选择438.5.1 开铁口机438.5.2堵铁口泥炮438.5.3堵渣机448.5.4换风口机448.5.5炉前吊车449 高炉喷吹煤粉系统459.1 煤粉制备工艺 459.1.1 煤粉制备工艺459.1.2 煤粉喷吹系统469.2 喷吹工艺流程 48结论49参考文献50谢辞51引言近些年来我国高炉生产各方面取得了显著进步, 但在资源和能源利用率、高炉大型化、提高产业集中度以及环保等方面还有很大差距, 有待进一步提高,努力向钢铁强国迈进我国高炉数量太多, 平均炉容过小,近年来又新建了一批1000m3以下的中小型高炉,使高炉结构不合理的问题进一步突出。
高炉本体毕业设计完整版

内蒙古科技大学本科生毕业设计说明书题目:内蒙古包头地区条件下2500m³高炉炉体系统设计学生姓名:张瑜学号:1176803442专业:冶金工程班级:4班指导教师:宋萍包头地区条件下2500m³高炉炉体系统设计摘要高炉炼铁的历史悠久,炼铁技术日益成熟,是当今主要的炼铁方式,随着炼铁技术的不断发展,高炉一代炉役寿命的不断提高,长寿高炉技术应用越来越广泛。
它是降低炼铁成本,提高钢铁企业经济效益的重要手段。
在大型高炉设计中,通过优化炉型、采用合理炉缸内衬结构、铜冷却壁、软水密闭循环冷却系统、薄壁内衬等技术为高炉长寿创造条件,提出了长寿高炉的基本设计思想。
为了适应这一发展趋势,.在本次长寿高炉设计中,对高炉合理内型、合理内衬结构和不同部位耐火材料的选择、冷却方式和冷却系统(包括冷却器的结构、材质与水质等)及其它有关方面作了综合考虑。
关键词:高炉长寿高炉内衬炉体冷却Design of Long Life BFABSTRACTHas a long history of BF ironmaking, is the main way of ironmaking,BF campaign life is continuously increased as unceasing development of iron making technology.It is being used more and more abroad. The long campaign technologies of blast furnace is one of the most important measures which reduce the iron making production cost and improve the economic profits of Iron and Steel Company. In the design of large BF,the technologies like optimized BF profile,reasonable hearth lining,copper stave,soft water closed circulating cooling system and thin-walled lining etc. were applied to prolong BF campaign life. The basic concept of designing long campaign blast furnace was put forward.In order to adapt to the trend,during designing long campaign blast furnace,the rational; furnace profile,rational furnace lining structure and selection of different refractories for various areas,cooling method and system (including cooler structure and material,cooling water and so on) and concerned aspects must be comprehensively considered.Key Words:Blast furnace life .Blast furnace lining. Furnace cooling目录摘要 (I)ABSTRACT (II)第一章文献综述 01.1我国高炉炼铁发展现状 01.2高炉概述 (2)1.2.1高炉本体概括 01.2.2高炉冶炼用的原料 (1)1.2.3高炉本体及附属设备 (1)1.2.4高炉炉型的发展现状 (2)1.3高炉炉底、炉缸对高炉长寿的影响 (3)1.3.1高炉长寿概述 (3)1.3.2 炉缸、炉底侵蚀的特征及原因 (3)1.3.3 炉腹、炉腰侵蚀的原因 (4)1.3.4 减少炉缸炉底侵蚀措施 (4)1.3.5 减少炉腹炉身侵蚀措施 (5)1.3.6陶瓷杯与热压小炭块的比较 (6)1.4高炉冷却设备对高炉长寿的影响 (6)1. 4. 1高炉冷却 (6)第二章高炉物料平衡计算 (9)2.1.原料条件 (10)2.2 矿石成分的补齐计算 (13)2.2.1烧结矿中成分的补齐计算 (13)2.2.2 球团矿中成分的补齐计算 (13)2.2.3 生矿成分的补齐计算 (14)2.3 矿石成分的平衡计算 (15)2.3.1 烧结矿平衡计算 (15)2.3.2 球团矿平衡计算 (16)2.3.3 生矿平衡计算 (17)2.4 配料计算 (18)2.4.2 使用熔剂时的配料计算 (19)2.5物料平衡计算 (23)2.5.1 鼓风量的计算 (23)2.5.2 煤气组分及煤气量的计算 (24)2.5.3煤气中水量计算 (26)2.5.4考虑炉料的机械损失后的实际入炉量 (26)2.6 高炉热平横计算 (27)2.6.1全炉热平衡计算(第二种) (27)2.6.2 高温区热平衡 (31)2.7 炼铁焦比计算 (33)第三章2500m3高炉炉体设计 (36)3.1 高炉内型设计 (36)3.1.1炉形设计 (37)3.1.2炉容校核,高径比校核Hu/D及h4/Hu (39)3.2高炉耐火材料 (41)3.2.1 高炉各部位耐火材料的选择 (41)3.3 高炉炉体设备设计 (42)3.3.1 炉体冷却设备设计 (42)3.3.1.1 高炉炉底及炉缸 (42)3.3.1.2 炉腹至炉身中下部 (42)3.3.1.3 炉身中上部 (43)3.3.2高炉冷却水设计 (45)3.3.3风口、铁口及炉底冷却设备的设计 (48)3.3.3.1风口设计 (48)3.3.3.3 炉底冷却设备 (50)3.4 炉壳设计 (50)3.5 高炉附属设备 (53)参考文献 (58)附表 (59)致谢 (67)第一章文献综述1.1我国高炉炼铁发展现状在经济发展的“新常态”下,钢铁行业正处于适应新常态之中转型升级、提质增效的重要阶段,技术创新对产业发展的支撑和引领作用日益突出。
年产量480万吨炼钢生铁和70万吨铸造生铁的高炉炼铁车间设计毕业论文

年产量480万吨炼钢生铁和70万吨铸造生铁的高炉炼铁车间设计毕业论文目录绪论 (1)1 高炉冶炼综合计算 (2)1.1 概述 (2)1.2 配料计算 (2)1.2.1 原燃料条件 (2)1.2.2 计算矿石需要量G矿 (4)1.2.3 计算熔剂需要量G熔 (5)1.2.4 炉渣成分的计算 (6)1.2.5 校核生铁成分 (8)1.3 物料平衡计算 (9)1.3.1 风量计算 (9)1.3.2 炉顶煤气成分及数量的计算 (11)1.3.3 编制物料平衡表 (14)1.4 热平衡计算 (15)1.4.1 热量收入q收 (15)1.4.2 热量支出q支 (17)1.4.3 热平衡表 (21)2 高炉本体设计 (23)2.1 高炉炉型 (23)2.2 炉型设计与计算 (23)2.3 高炉炉衬设计 (27)2.3.1 高炉对耐火材料的要求 (27)2.3.2 高炉炉衬的设计与砌筑 (28)2.4 高炉冷却设备 (29)2.4.1 冷却设备的作用 (29)2.4.2 冷却介质及水的软化 (30)2.4.3 冷却方式 (30)2.4.4 高炉冷却系统 (31)2.5 高炉送风管路 (32)2.5.1 热风围管 (33)2.5.2 送风支管 (33)2.5.3 直吹管 (33)2.5.4 风口装置 (34)2.6 高炉钢结构 (34)2.6.1 高炉本体钢结构 (35)2.6.2 炉壳 (35)2.6.3 炉体框架 (36)2.6.4 炉缸炉身支柱和炉腰支圈以及支柱坐圈 (36)2.7 高炉基础 (37)2.7.1 高炉基础的负荷 (37)2.7.2 对高炉基础的要求 (38)3 高炉炼铁车间供料系统 (39)3.1 车间的运转 (39)3.2 贮矿槽和贮焦槽及槽下运输筛分称量 (40)3.2.1 贮矿槽与贮焦槽 (40)3.2.2 槽下运输称量 (41)3.3 上料设备 (41)4 炉顶装料设备 (42)4.1 无钟式炉顶装料设备 (42)4.1.1 串罐式无钟炉顶装料设备 (42)4.1.2 无钟式炉顶的布料方式 (43)4.2 探料装置 (44)5 送风系统 (45)5.1 高炉用鼓风机 (45)5.1.1 高炉冶炼对鼓风机的要求 (45)5.1.2 高炉鼓风机的工作原理和特性 (46)5.1.3 高炉鼓风机的选择 (47)5.2 热风炉 (48)5.2.1 外燃式热风炉 (48)5.2.2 外燃式热风炉的特点 (49)6 高炉喷吹煤粉系统 (50)6.1 煤粉的制备设备 (50)6.2 高炉喷煤系统 (50)6.2.1 单管路串罐喷吹系统 (50)6.2.2 喷吹罐组有效容积的确定 (51)6.3 煤粉喷吹的安全措施 (53)6.3.1 制粉系统的安全措施 (53)6.3.2 喷吹系统的安全措施 (53)7 炉煤气处理系统 (54)7.1 煤气管道 (54)7.2 粗除尘装置 (54)7.2.1 重力除尘器除尘原理 (54)7.3 精细除尘装置 (54)8 渣铁处理系统 (56)8.1 风口平台及出铁场设计 (56)8.1.1 风口平台及出铁场 (56)8.1.2 渣铁沟和撇渣器 (57)8.1.3 摆动流嘴 (57)8.2 炉前主要设备 (58)8.2.1 开铁口机 (58)8.2.2 堵铁口泥炮 (58)8.2.3 炉前吊车 (58)8.3 铁水处理 (58)8.3.1 鱼雷罐车 (59)8.3.2 铸铁机 (59)8.4 炉渣处理设备 (59)8.4.1 拉萨法水淬渣 (59)8.4.2 干渣生产 (59)9 能源回收利用 (61)9.1 高炉炉顶余压发电 (61)9.2 热风炉烟道废气余热回收 (61)参考文献 (62)专题研究 (63)外文翻译 (77)附录 (91)致谢.............................................................................................. 错误!未定义书签。
高炉车间系统设计毕业论文
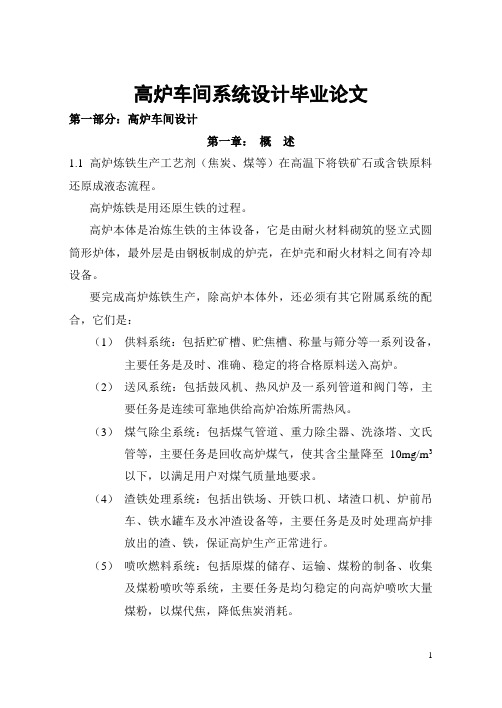
高炉车间系统设计毕业论文第一部分:高炉车间设计第一章:概述1.1 高炉炼铁生产工艺剂(焦炭、煤等)在高温下将铁矿石或含铁原料还原成液态流程。
高炉炼铁是用还原生铁的过程。
高炉本体是冶炼生铁的主体设备,它是由耐火材料砌筑的竖立式圆筒形炉体,最外层是由钢板制成的炉壳,在炉壳和耐火材料之间有冷却设备。
要完成高炉炼铁生产,除高炉本体外,还必须有其它附属系统的配合,它们是:(1)供料系统:包括贮矿槽、贮焦槽、称量与筛分等一系列设备,主要任务是及时、准确、稳定的将合格原料送入高炉。
(2)送风系统:包括鼓风机、热风炉及一系列管道和阀门等,主要任务是连续可靠地供给高炉冶炼所需热风。
(3)煤气除尘系统:包括煤气管道、重力除尘器、洗涤塔、文氏管等,主要任务是回收高炉煤气,使其含尘量降至10mg/m3以下,以满足用户对煤气质量地要求。
(4)渣铁处理系统:包括出铁场、开铁口机、堵渣口机、炉前吊车、铁水罐车及水冲渣设备等,主要任务是及时处理高炉排放出的渣、铁,保证高炉生产正常进行。
(5)喷吹燃料系统:包括原煤的储存、运输、煤粉的制备、收集及煤粉喷吹等系统,主要任务是均匀稳定的向高炉喷吹大量煤粉,以煤代焦,降低焦炭消耗。
1.2主要技术经济指标(1)高炉有效容积利用系数(ηv):高炉有效容积利用系数是指每昼夜生铁的产量P与高炉有效容积V有之比,即每昼夜,每1m³高炉有效容积的生铁产量。
ηv是高炉冶炼的一个重要指标,ηv俞大,高炉生产率俞大。
目前,一般大型高炉超过2.0 t / m3·d,一些先进高炉可达2.2~2.3 t / m3·d 。
小型高炉的ηv更高,100~300 m3高炉的利用系数为2.8~3.2t / m3·d。
本设计ηv =2.15 t / m3 ·d 。
(2)焦比(K):焦比即每昼夜焦碳消耗量Q K与每昼夜生铁产量P之比,即冶炼每吨生铁消耗的焦碳量。
K=Q K/P焦炭消耗量约占生铁成本的30%~40%,欲降低生铁成本必须降低焦比。
毕业设计--年产300万吨生铁高炉设计
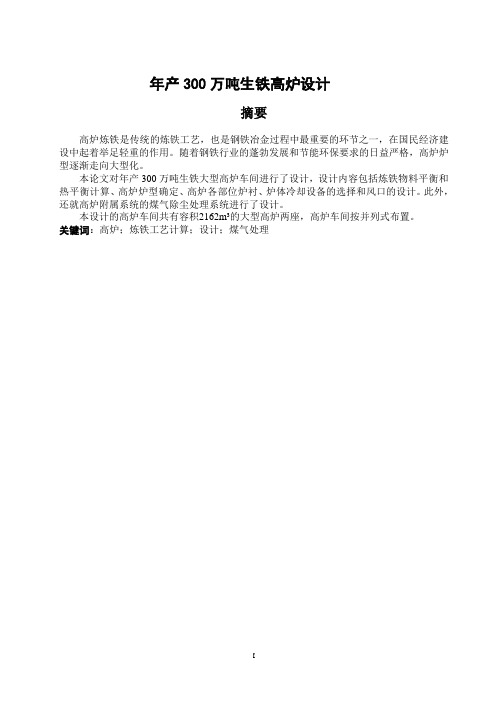
年产300万吨生铁高炉设计摘要高炉炼铁是传统的炼铁工艺,也是钢铁冶金过程中最重要的环节之一,在国民经济建设中起着举足轻重的作用。
随着钢铁行业的蓬勃发展和节能环保要求的日益严格,高炉炉型逐渐走向大型化。
本论文对年产300万吨生铁大型高炉车间进行了设计,设计内容包括炼铁物料平衡和热平衡计算、高炉炉型确定、高炉各部位炉衬、炉体冷却设备的选择和风口的设计。
此外,还就高炉附属系统的煤气除尘处理系统进行了设计。
本设计的高炉车间共有容积2162m³的大型高炉两座,高炉车间按并列式布置。
关键词:高炉;炼铁工艺计算;设计;煤气处理年产300万吨生铁高炉设计AbstractBlast furnace ironmaking was the traditional iron-making craft, also was one of the most important link in ferrous metallurgy, it played a decisive role in national economic construction. With the vigorous development of the steel industry and more and more strict requirement of energy conservation and environmental protection requirement, the BF became maximization gradually.A large scale BF plant which had annual output of 3 million tons of pig iron was designed in this thesis, design content includeed material balance and thermal equilibrium calculation, determination of BF profile, selection of lining and cooling equipment for each part of BF and design of taphole. In addition, the gas processing sytem which was one of the BF subsidiary system was designed.The ironmaking plant of this thesis has two 2162m³ BF, they were layouted side by side. Key words:blast furnace;Ironmaking process calculation;design;gas processing目录2011年 4 月17日...................................................................................... 错误!未定义书签。
年产630万吨生铁的高炉炼铁车间工艺设计毕业论文
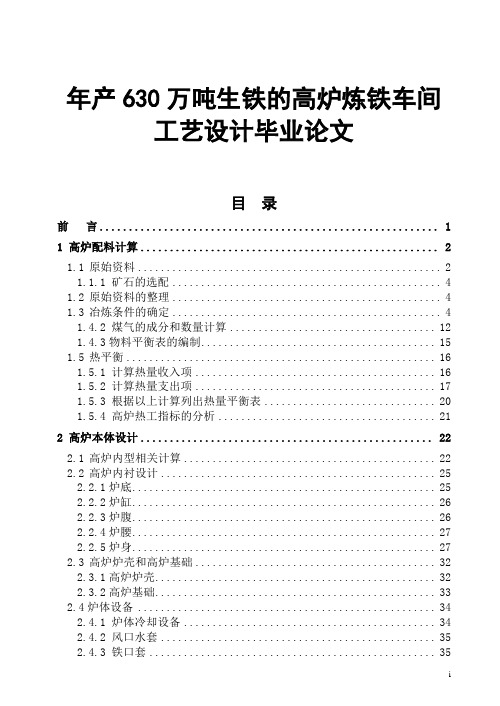
年产630万吨生铁的高炉炼铁车间工艺设计毕业论文目录前言 (1)1 高炉配料计算 (2)1.1原始资料 (2)1.1.1 矿石的选配 (4)1.2原始资料的整理 (4)1.3冶炼条件的确定 (4)1.4.2 煤气的成分和数量计算 (12)1.4.3物料平衡表的编制 (15)1.5热平衡 (16)1.5.1 计算热量收入项 (16)1.5.2 计算热量支出项 (17)1.5.3 根据以上计算列出热量平衡表 (20)1.5.4 高炉热工指标的分析 (21)2 高炉本体设计 (22)2.1高炉内型相关计算 (22)2.2高炉内衬设计 (25)2.2.1炉底 (25)2.2.2炉缸 (26)2.2.3炉腹 (26)2.2.4炉腰 (27)2.2.5炉身 (27)2.3高炉炉壳和高炉基础 (32)2.3.1高炉炉壳 (32)2.3.2高炉基础 (33)2.4炉体设备 (34)2.4.1 炉体冷却设备 (34)2.4.2 风口水套 (35)2.4.3 铁口套 (35)2.4.4炉喉钢砖 (35)2.4.5 炉顶保护板 (35)3 料运系统计算及装料布料设备 (36)3.1贮矿槽 (36)3.1.1 平面布置 (36)3.1.2 槽上运输方式 (36)3.1.3 储矿槽工艺参数 (36)3.1.4 槽下供料 (37)3.2料坑设备 (37)3.3碎焦运送设施 (38)3.4上料设备 (38)4 高炉鼓风机的选择 (39)4.1高炉鼓风量及鼓风压力的确定 (39)4.1.1 高炉入炉风量 (39)4.1.2 鼓风机出口风量 (39)4.1.3 高炉鼓风压力 (40)4.2高炉鼓风机能力的确定 (40)4.2.1 大气状况对高炉鼓风的影响 (40)4.2.2 鼓风机工况的计算 (40)4.2.3 鼓风机的选择 (41)4.3高炉鼓风机的工艺过程 (42)5 热风炉 (43)5.1计算的原始数据 (43)5.2燃烧计算 (44)5.2.1 煤气成分换算 (44)5.2.2 煤气发热值计算 (44)5.2.3 燃烧1标米3煤气的空气需要量 (45)5.2.4燃烧1标米3煤气生成的烟气量灰分分组成 (45)5.2.5理论燃烧温度和实际燃烧温度计算 (46)5.3热平衡计算 (48)5.3.1 计算鼓风从80℃提高到1200℃所增加的热含量 (48)5.3.2 加热1标米3鼓风需要的煤气量 (48)5.3.3 煤气消耗量及烟气量 (48)5.4蓄热室热工计算 (49)5.4.1 热工计算的原始条件 (51)5.4.2 蓄热室各部位的烟气及鼓风温度 (52)5.4.3 蓄热室面积及各段砖格子高度的计算 (53)5.4.4蓄热室面积及蓄热室各段高度的调整 (55)5.5热风炉的蓄热面积指标 (55)6 风口平台及渣铁处理系统 (57)6.1风口平台和出铁场布置 (57)6.1.1 铁口及出铁场数目的确定 (57)6.1.2 渣、铁沟及其流嘴布置 (58)6.2风口平台和出铁场设备 (58)6.2.1 泥炮 (58)6.2.2 开铁口机 (59)6.2.3堵渣口机 (59)6.2.4炉前吊车 (60)6.2.5铁水罐车 (60)6.2.6渣罐车 (61)6.3风口平台和出铁场结构 (62)6.3.1风口平台 (62)6.3.2 出铁场 (62)6.4铁水处理 (62)6.5渣的处理 (62)7 高炉煤气处理系统 (64)7.1工艺流程 (64)7.2煤气除尘设备 (64)7.2.1 粗除尘设备——重力除尘器 (64)7.2.2 精细除尘设备——布袋除尘器 (65)7.2.3 脱水器 (65)7.3煤气除尘系统附属设备 (66)7.3.1 粗煤气管道 (66)7.3.2 调节阀组 (66)7.3.3 煤气遮断阀 (66)7.3.4 煤气放散阀 (66)8 高炉喷吹煤粉系统 (67)8.1喷煤系统 (67)8.2喷吹工艺 (67)8.3主要设备 (68)8.3.1 混合器 (68)8.3.2 分配器 (68)8.3.3 喷煤枪 (68)8.3.4 喷氧枪 (68)9部分车间布置与总图运输 (69)9.1车间平面布置 (69)9.2厂区的选择 (69)9.3总图运输 (69)10参考文献 (70)致谢 (71)专题添加微量纳米铜粉在冶金制件烧结时的作用 (72)前言毕业设计是大学学习过程中的最后一个环节,对每个大学生的学习能力和以后的工作实践能力都会有很大的帮助与提高。
年产350万吨炼钢生铁高炉车间

目录前言 (1)1 设计条件 (2)1.1 主要技术经济指标 (2)1.2 高炉容量及座数的确定 (3)2 高炉炉型设计 (5)2.1 高炉炉型选择 (5)2.2 设计与计算 (5)2.3 校核炉容: (7)3 炉衬选择 (9)3.1 高炉炉基的形状及材质 (9)3.2 高炉炉底和各段炉衬的选择、设计和砌筑 (11)4 冷却设备选择、风口及铁口设计 (14)4.1 炉底冷却型式选择 (14)4.2 高炉各部位冷却设备的选择 (14)4.3 高炉供水量、水压的确定 (15)4.4 风口数目及直径 (16)4.5 风口平台、出铁场及铁口 (16)4.6 炉壳及钢结构确定 (17)结论 (20)参考文献 (21)致谢 (22)我国修筑现代化高炉始于1891 年,解放前期,铁的年产量惟独25 万吨,钢为15.8 万吨。
随着时代的变迁,新中国的炼铁工业从以中小高炉占绝对主导地位起步,到20 世纪50 年代末大办钢铁时大兴“平地吹”土法烧结和土高炉盛行,再到20 世纪8O 年代中期300 立方米、620 立方米、1000 立方米高炉通用设计,走过了一条随着时代的变迁的道路。
目前,我国正在生产的高炉有三千三百多座。
在21 世纪,我国高炉炼铁将继续在结构调整中发展。
高炉结构调整不能简单地概括为大型化,应该根据企业生产规模、资源条件来确定高炉炉容。
从目前的我国实际状况看,高炉座数必须大大减少,平均炉容大型化是必然趋势。
高炉大型化,有效容积从1000 立方米以上乃至3000 立方米以上超大型高炉。
有利于提高劳动生产率、便于生产组织和管理,提高铁水质量,有利于减少热量损失、降低能耗,减少污染点.污染容易集中管理,有利于环保。
所有这一切都有利于降低钢铁厂的生产成本,提高企业的市场竞争力。
创造更大的经济效益及社会效益。
一座年产 350 万吨炼钢铁水的高炉是较能适应唐山地区的原燃料条件和唐钢的工艺以及环境条件,并且在节能环保方面较小高炉有很大的优势,同时初期投资相对较小,对于唐山地区的许多钢铁厂都具有比较好的借鉴作用。
2580m高炉毕业设计方案

2580m高炉毕业设计方案摘要本文针对炼钢高炉的设计及操作问题,提出了一种新型的高炉设计方案,该高炉的高度为2580m,可满足现代工业对于大产量、高效率的需求。
该设计方案有利于提高钢铁行业的生产效率和降低成本,同时也具有一定的环保优势。
本文就该高炉的整体结构、燃烧系统、废气处理等主要问题进行了详细的研究及探讨。
关键词:高炉、设计方案、燃烧系统、环保概述高炉是炼钢采用的主要设备之一,其主要作用是通过高温下的还原反应使矿石中的铁氧化物还原成金属铁,同时去除其中的杂质,从而获得较为纯净的钢铁。
现代工业对于钢铁的产量和品质要求越来越高,因此需要一种新型的高炉设计,以满足这些要求。
该设计方案将高炉的高度增加至2580m,以达到更高的生产效率和更低的成本。
一、高炉设计该高炉的整体结构采用了较为先进的不锈钢材料,以保证高炉的稳定性和耐用性。
高炉的总高度为2580m,直径为30m,容积为1.3万立方米。
高炉底部为圆形的锅炉炉室,其上方为上部炉身,最后是顶部炉喉和罩壳。
高炉的整体设计符合国际环保标准,能够有效地降低废气排放量。
二、燃烧系统该高炉采用了较为先进的燃烧系统,其中主要包括喷嘴和燃料供应系统等部分。
喷嘴采用了新型的旋转喷雾技术,以确保燃料的均匀分布;燃料供应系统采用了液态环保燃料,可有效地降低废气的排放量。
该燃烧系统能够从根本上解决传统高炉设计中存在的燃烧不充分和排放量过大等问题。
三、废气处理该高炉的废气处理系统采用了多级净化技术,可将排放的废气中的二氧化碳、硫化氢等有害物质有效地清除。
此外,该系统还采用了高效的氮氧化物治理技术,以确保排放的废气不会对环境造成危害。
该废气处理系统的设计既能够满足高炉燃烧排放的要求,又能够有效地保护环境。
结论2580m高炉是一种新型的高炉设计方案,旨在提高钢铁行业的生产效率和降低成本,同时也具有一定的环保优势。
该设计方案采用了先进的不锈钢材料、新型的喷嘴和燃料供应系统,以及多级净化技术,能够有效地降低废气排放量,保护环境。
高炉车间设计毕业论文

高炉车间设计毕业论文高炉车间设计摘要:本论文以高炉车间设计为研究对象,通过调研和分析高炉生产过程中的工艺流程和设备需求,设计出一套合理有效的高炉车间布局方案。
通过优化车间内各工序之间的联系和协调,提高生产效率,减少能源消耗和材料浪费。
本论文从设计原则、车间布局、设备配置和工艺优化等方面进行探讨,为高炉车间设计提供一些参考。
关键词:高炉车间、设计、布局、工艺流程、设备配置第一章引言1.1 研究背景高炉是炼铁的核心设备,对于炼铁生产的效率和质量具有重要影响。
高炉车间作为高炉生产过程中的核心环节,其布局和设备配置对于生产效率和能耗有着直接的影响。
1.2 研究目的本论文的研究目的是设计出一套合理有效的高炉车间布局方案,提高高炉生产效率,减少能源消耗和材料浪费,为高炉生产提供一些参考和指导。
第二章设计原则2.1 生产效率原则高炉车间布局应当考虑生产过程中各工序之间的联系和协调,确保生产流程的顺畅和高效。
2.2 能源消耗原则高炉车间布局应当考虑能源消耗的最小化,通过优化设备配置和工艺流程,降低能源消耗和废气排放。
2.3 安全生产原则高炉车间布局应当符合相关的安全生产要求,确保生产过程中的安全性和稳定性。
第三章车间布局3.1 车间布局的基本要求高炉车间布局应当具备合理紧凑的特点,便于生产过程中的物流运输和设备维护。
3.2 高炉设备的布局高炉设备的布局应当考虑安全生产和生产效率的要求,确保设备的稳定性和可靠性。
3.3 原料和产物的流动高炉车间布局中应当合理安排原料和产物的流动,确保生产过程中的连续性和稳定性。
第四章设备配置4.1 设备的选型原则高炉车间的设备选型应当考虑设备的性能和稳定性,确保设备能够满足生产过程中的要求。
4.2 设备的布置原则高炉车间的设备布置应当考虑设备之间的联系和协调,确保设备之间的运输和操作的便利性。
4.3 设备的维护和保养高炉车间的设备维护和保养应当考虑设备的可维护性和可靠性,确保设备能够持续稳定地运行。
2023年高炉炼铁车间重点煤气处理系统论文方案模板

煤气处理系统存在的问题
1. 煤气处理系统存在问题一:煤气净化效率低下。当前煤气处理系统在煤气净化过程中存在着排放物浓度较高的情况,无法满足环境排放标准要求。原因可能包括设备老化、操作不规范等因素。
2. 经济效益:评估高炉炼铁车间煤气处理系统的经济效益,包括生产效率提升、资源利用率提高、节约能源等方面的好处。据此计算投资回收期,并讨论如何进一步提高经济效益,加速投资回收。
3. 风险评估:对高炉炼铁车间煤气处理系统的投资回收期进行风险评估,考虑外部因素(如市场需求、政策环境、竞争压力)和内部因素(如设备技术可靠性、运行维护成本)的影响。提出应对风险的措施和策略,以确保投资回收期的稳定和可持续。
2.
30%
3.
现状分析:改进措施
1.煤气处理系统优化对于高炉炼铁车间至关重要
2. 煤气处理效率低:我国大部分高炉炼铁车间煤气处理系统的处理效率低于90%,比国际先进水平低10-20个百分点。
3. 能源消耗高:我国高炉炼铁车间煤气处理系统的能耗普遍较高,比国际先进水平高20-30%。
4. 环保排放不达标:我国高炉炼铁车间煤气处理系统的尾气排放浓度较高,超过国家环保标准50%以上。
3. 优化能源结构,减少能耗:在煤气处理系统中,不同的能源存在着不同的能耗情况。因此,可以通过优化能源结构,选择更加节能的能源,从而降低能耗。例如,可以采用太阳能、风能等清洁能源,或者采用高效节能的设备。
2023/9/2 星期六
Alphdo
TEAM
3.煤气处理系统性能优化:关键因素分析
煤气处理系统介绍
高炉设计 毕业设计

第一章文献综述1.1 炼铁行业概述钢铁工业在过去的100多年里进行了快速发展,无论是在设备还是技术上都取得了重大的进步,但也存在这很大的缺陷,比如污染严重,矿石利用率低,严重耗能等等的问题。
在近些年里钢铁行业的重要性有了不小的下降,更为严重的是钢铁行业现在已经处于一个微利甚至是负利的产业,所以现在急需要我们的生产工作者更加努力,提高钢铁行业的技术进而扭转这一不利的局面。
我国钢铁工业现状如下[1]:行业集中度低, 生产专业化程度低, 尚不能达到规模经济, 在一定的程度上限制了我国钢业的竞争力,结构不合理,企业平均技术装备水平低,产业升级和任务技术改造非常艰巨。
我国钢铁企业不注重新技术新产品的开发利用,和国外一些企业形成了鲜明的对比。
钢铁产品质量有待进一步提高。
我国钢铁产品的实物质量水平比国外先进水平相比还有一段距离; 我国钢材产品销售服务水平较低。
钢材产品销售服务和产品的质量是提高产品竞争力的重要方面; 我国钢铁行业的信息迟缓,企业与企业间相互恶意压价竞争,而且没有一个统一的部门进行指导和规范,导致了现在我们钢铁行业的严重被动局面,加工服务中心基本上处于空白,而且我国的钢铁企业目光仅仅局限于国内,在国际上的竞争力不足,所以现在我国钢铁行业处于一个极为不利的局面,急需要一些措施来改变。
目前我国钢铁业产能过剩,严重超出了需求量,在2008年我国生铁产量已经到达4.6944亿t比去年度增长15. 19%,其增加幅度低于钢产量同期增加幅度,占剧全世界钢铁总产量的49.74%。
2007年全国重点钢铁企业产铁3. 69亿t,同去年的产量比增长了13.74%,其他非重点钢铁企业产量1.20亿t,增长19.60%。
2008年上半年我国产铁量2.4642亿t,与去年相比增加了 7.89%,但发展势头降低了。
预计, 2008年我国钢产量达到5.2亿t,生铁产量将达到4.9亿t。
2009年产铁5.43亿吨,占世界总产量的60.53%,2010年前十个月我国铁产4.96亿吨,比上年同期增长8.27%。
- 1、下载文档前请自行甄别文档内容的完整性,平台不提供额外的编辑、内容补充、找答案等附加服务。
- 2、"仅部分预览"的文档,不可在线预览部分如存在完整性等问题,可反馈申请退款(可完整预览的文档不适用该条件!)。
- 3、如文档侵犯您的权益,请联系客服反馈,我们会尽快为您处理(人工客服工作时间:9:00-18:30)。
高炉车间系统设计毕业论文第一部分:高炉车间设计第一章:概述1.1 高炉炼铁生产工艺剂(焦炭、煤等)在高温下将铁矿石或含铁原料还原成液态流程。
高炉炼铁是用还原生铁的过程。
高炉本体是冶炼生铁的主体设备,它是由耐火材料砌筑的竖立式圆筒形炉体,最外层是由钢板制成的炉壳,在炉壳和耐火材料之间有冷却设备。
要完成高炉炼铁生产,除高炉本体外,还必须有其它附属系统的配合,它们是:(1)供料系统:包括贮矿槽、贮焦槽、称量与筛分等一系列设备,主要任务是及时、准确、稳定的将合格原料送入高炉。
(2)送风系统:包括鼓风机、热风炉及一系列管道和阀门等,主要任务是连续可靠地供给高炉冶炼所需热风。
(3)煤气除尘系统:包括煤气管道、重力除尘器、洗涤塔、文氏管等,主要任务是回收高炉煤气,使其含尘量降至10mg/m3以下,以满足用户对煤气质量地要求。
(4)渣铁处理系统:包括出铁场、开铁口机、堵渣口机、炉前吊车、铁水罐车及水冲渣设备等,主要任务是及时处理高炉排放出的渣、铁,保证高炉生产正常进行。
(5)喷吹燃料系统:包括原煤的储存、运输、煤粉的制备、收集及煤粉喷吹等系统,主要任务是均匀稳定的向高炉喷吹大量煤粉,以煤代焦,降低焦炭消耗。
1.2主要技术经济指标(1)高炉有效容积利用系数(ηv):高炉有效容积利用系数是指每昼夜生铁的产量P与高炉有效容积V有之比,即每昼夜,每1m³高炉有效容积的生铁产量。
ηv 是高炉冶炼的一个重要指标,ηv俞大,高炉生产率俞大。
目前,一般大型高炉超过2.0 t / m3·d,一些先进高炉可达2.2~2.3t / m3·d。
小型高炉的ηv更高,100~300 m3高炉的利用系数为2.8~3.2t / m3·d。
本设计ηv=2.15 t / m3·d。
(2)焦比(K):焦比即每昼夜焦碳消耗量QK与每昼夜生铁产量P之比,即冶炼每吨生铁消耗的焦碳量。
K= QK/P焦炭消耗量约占生铁成本的30%~40%,欲降低生铁成本必须降低焦比。
焦比大小与冶炼条件密切相关,本设计的焦比为360 kg / t 。
(3)煤比(Y):冶炼每吨生铁消耗的煤粉量称为煤比。
当每昼夜煤粉的消耗量为QY时,则Y=Q Y /P本设计煤比为120 kg / t。
(4)冶炼强度(I)和燃烧强度(i):高炉冶炼强度是每昼夜每1m³有效容积燃烧的焦碳量,即高炉一昼夜焦炭的消耗量与有效容积V有的比值。
I=Q K /V有本设计I =1.03 t / m3· d燃烧强度即每小时每平方米炉缸截面所燃烧的焦碳数量。
本设计i =1.05 t / m2 ·h。
(5)休风率:休风率是指高炉休风时间占高炉规定作业时间的百分数。
休风率反映高炉设备维护的水平,先进高炉休风率小于1%,实践证明,休风率降低1%,产量可提高2%。
(6)生铁合格率:化学成分符合国家标准的生铁称为合格生铁。
合格生铁总产生铁量的百分数为生铁合格率。
它是衡量产品质量的指标。
本设计为100%。
(7)高炉一代寿命:高炉一代寿命是指从点火开炉到停炉大修之间的冶炼时间,或是指高炉相邻两次大修之间的冶炼时间。
大型高炉一代寿命为10~15年。
1.3 高炉炼铁厂的厂址选择确定厂址要作多方案比较,选择最佳者。
(1)要考虑工业布局,有利于经济协作。
(2)合理利用地形设计工艺流程,简化工艺,减少运输量,节省投资。
(3)尽可能接近原料产地及消费地点,以减少原料及产品的运输费用。
(4)地质条件要好,地层下不能有有开采价值的矿物,也不是已开采区。
(5)水电资源要丰富,供电要双电源。
(6)尽量少占农田。
(7)厂址要位于居民区主导风向的下风或侧风向。
第二章工艺计算2.1配料计算2.1.1物料成分表(%)焦炭成分(%)煤粉成分(%)2.1.2 预定铁水成分2.1.3 矿石配比的确定,依据唐钢同类高炉的实际生产数据确定为:烧结矿:球团矿:巴西矿=75:10:152.1.4 各元素分配表2.1.5 入炉料的用量假定焦比390 kg / t ,煤比138 kg / t ,鼓风湿度 1.3 % ,直接还原度r d =0.45 ,炉料碱度R=1.1 ,炉尘吹出量20Kg/t ,焦炭与喷吹燃料中总炭量的1.2%与H 2生成CH 4。
(1)矿石需要量的计算Qk=FekFemeFej Fech Feza Fet --++=%156502.0%106275.0%75563.0984.0%86.0138%62.096.0390486.020997.00003.02.9492.949⨯+⨯+⨯⨯⨯-⨯⨯-⨯+⨯+=1652Kg其中:Qk ——矿石的需要量,千克/吨铁Fet ——进入生铁的铁量 千克/吨铁 Feza ——进入炉渣的铁量 千克/吨铁 Feme ——煤粉带入的铁量 千克/吨铁Fej ——焦炭带入的铁量 千克/吨铁 (2)熔剂需要量的计算Ql=()()()()()[]()()lSiO R l CaO R ch SiO Si SiO me SiO j SiO k SiO 222222⨯-⨯--++()()()()()lSiO R l CaO ch CaO me CaO j CaO k CaO )2(⨯--++0136.01.15312.01.128607155.0200719.0984.01380565.096.0390054.01652⨯-⨯⨯-⨯-⨯⨯+⨯⨯+⨯⎪⎭⎫ ⎝⎛0136.01.15312.00466.0200049.0984.01380076.096.0390073.01652⨯-⨯-⨯⨯+⨯⨯⨯+⨯=5.3Kg式中:Ql ——熔剂的需要量 千克/吨铁 R ——炉渣碱度 (SiO 2)k ——矿石带入的SiO 2 千克/吨铁 (SiO 2)j ——焦炭带入的SiO 2 千克/吨铁(SiO 2)me ——煤粉带入的SiO 2 千克/吨铁(SiO 2)Si 还原硅消耗的SiO 2 千克/吨铁 (SiO 2)ch ——炉尘带走的SiO 2 千克/吨铁 (SiO 2)l ——熔剂中SiO 2 %(CaO )k —— 矿石带入的CaO 千克/吨铁 (CaO )j ——焦炭带入的 CaO 千克/吨铁 (CaO )me ——煤粉带入的 CaO 千克/吨铁(CaO)ch ——炉尘带走的CaO 千克/吨铁(CaO)l ——熔剂中的 CaO %每吨生铁原燃料消耗量2.1.6 渣量和炉渣成分的计算1.炉渣中S 的量 GS渣●原﹑燃料带入的总硫量:GS=1652×0.00162+390×0.96×0.0052+138×0.984×0.0058=5.40 kg●进入生铁的硫量: G S生铁 = 0.2kg●进入煤气的硫量: G S煤气= 5.40×5% = 0.27 kg●炉尘带走的硫量: G S炉尘=20×0.0012=0.024Kg故炉渣中的硫量: GS渣= 5.40﹣0.2﹣0.27-0.024 =4.91 kg2、炉渣中FeO的量GFeO渣:GFeO渣=949.2×997.0003.0×5672= 3.67 kg3、炉渣中MnO的量GMnO渣:GMnO渣=1652×0.00283×0.5= 2.34 kg4、炉渣中SiO2的量GSiO2渣:GSiO2渣=1652×0.052+390×0.96×0.0565+138×0.984×0.0719﹣20×0.155﹣7×60/28= 98.72 kg5、炉渣中CaO的量GCaO渣:GCaO渣=1652×0.073+390×0.96×0.0076+138×0.984×0.0049﹣20×0.0466 =123.186、炉渣中MgO的量GMgO渣:GMgO渣= 1652×0.023+390×0.96×0.0012+138×0.984×0.0024+5.3×0.006﹣20×0.0095=38.74 kg7、炉渣中Al2O3的量GAl2O3:GAl2O3渣=1652×0.018+390×0.96×0.0483+138×0.984×0.0594+5.3×0.014﹣20×0.0144 = 53.62 kg总渣量:G渣=4.91+3.67+98.72+123.18+2.34+38.74+53.62=325.18kg炉渣成分表2.1.7 生铁成分的校对[P]:(1652×0.01%+390×0.01%×0.9614262÷⨯-20×0.12%)/1000=0.1%[S]:0.02% [Si]:0.70% [Mn]:)715534.2(⨯/1000=0.18% [C] :(100-94.92-0.1-0.02-0.7-0.18)/100=4.08% 生铁成分表(%)2.2 物料平衡 2.2.1 风量的计算 1. 风口前燃烧的碳量G C 燃。
1) 燃料带入的总碳量为: G C 总=G 焦C%焦+G 煤C%煤-G 炉尘C%炉尘=390×0.8563+138×0.7461-20×0.062= 435.68 kg 2) 溶入生铁中的碳量为:G C 生铁=1000[C]%=1000×0.0408 = 40.8 kg3) 生成甲烷的碳量为:G CCH4=0.6%G C 总=0.012×435.68 = 5.23 kg 4) 直接还原消耗的碳量为:G C 直=G CFe 直+G CMn 直+G Csi 直+G CP 直=kg 89.98626012824755158.145.056122.949=⨯+⨯+⨯+⨯⨯风口前燃烧消耗的碳量为 : G C 燃=G C 总﹣G C 生铁﹣G CCH4﹣G C 直=435.68﹣40.8﹣5.23﹣98.89 = 291.28 kg2. 计算鼓风量V 风。
1) 鼓风中氧的浓度:N=0.21×(1﹣0.013)+0.5×0.013= 0.2138 2) G C 燃燃烧需要氧的体积为: 由 CO O C 222→+ 得 386.2711224.2228.2912m V O =⨯⨯= 3) 煤粉中的氧的体积为:V O2煤=394.3324.22%15.4%84.9138m =⨯⨯⨯ 4) 鼓风提供的氧的体积为:V O2风=V O2﹣V O2煤=271.86﹣3.94 = 267.92 m 3 故 V 风=2138.092.267=1253.13Nm 33/28.14.2218013.0987.079.032987.021.0m kg =⨯+⨯+⨯⨯=空气γkg W 160428.113.1253=⨯=空气 2.2.2 炉顶煤气成分的计算1. CH 4的体积V CH4:1) 由燃料碳素生成的CH 4的量为:V CH4碳=G CCH4124.22 = 376.9124.2223.5m =⨯ 2) 焦碳挥发分中CH 4的量: V CH4焦=G 焦CH 4%焦164.22 = 316.0164.22%03.096.0390m =⨯⨯⨯故 392.916.076.94m V CH =+= 2. 氢的体积V H2。