LNG接收站工艺设计介绍
lng站的工艺流程
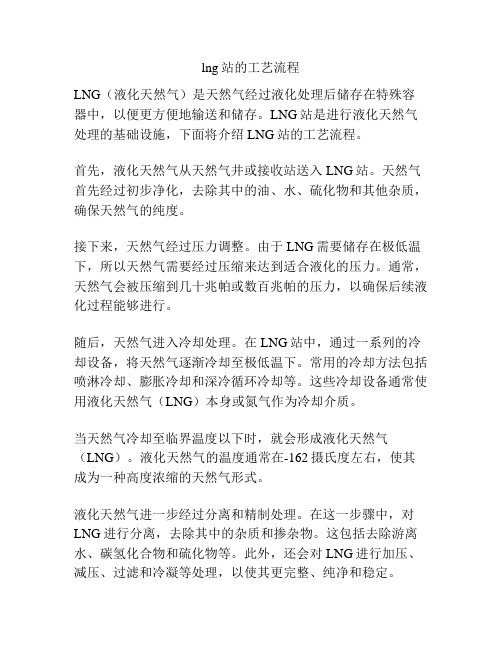
lng站的工艺流程LNG(液化天然气)是天然气经过液化处理后储存在特殊容器中,以便更方便地输送和储存。
LNG站是进行液化天然气处理的基础设施,下面将介绍LNG站的工艺流程。
首先,液化天然气从天然气井或接收站送入LNG站。
天然气首先经过初步净化,去除其中的油、水、硫化物和其他杂质,确保天然气的纯度。
接下来,天然气经过压力调整。
由于LNG需要储存在极低温下,所以天然气需要经过压缩来达到适合液化的压力。
通常,天然气会被压缩到几十兆帕或数百兆帕的压力,以确保后续液化过程能够进行。
随后,天然气进入冷却处理。
在LNG站中,通过一系列的冷却设备,将天然气逐渐冷却至极低温下。
常用的冷却方法包括喷淋冷却、膨胀冷却和深冷循环冷却等。
这些冷却设备通常使用液化天然气(LNG)本身或氮气作为冷却介质。
当天然气冷却至临界温度以下时,就会形成液化天然气(LNG)。
液化天然气的温度通常在-162摄氏度左右,使其成为一种高度浓缩的天然气形式。
液化天然气进一步经过分离和精制处理。
在这一步骤中,对LNG进行分离,去除其中的杂质和掺杂物。
这包括去除游离水、碳氢化合物和硫化物等。
此外,还会对LNG进行加压、减压、过滤和冷凝等处理,以使其更完整、纯净和稳定。
最后,液化天然气被储存于专门设计的LNG储罐中。
这些储罐通常由双层或多层的绝热材料构成,以便在未来储存和运输中保持LNG的低温状态。
这些储罐的容量可以达到几十万立方米,甚至更大。
总结起来,LNG站的工艺流程包括初步净化、压力调整、冷却处理、分离和精制以及储存等环节。
通过这些步骤,天然气可以被液化为LNG,以方便储存、运输和使用。
LNG站的建设和运营对于提供清洁能源和满足能源需求具有重要的意义。
lng接收站加工工艺流程

lng接收站加工工艺流程下载温馨提示:该文档是我店铺精心编制而成,希望大家下载以后,能够帮助大家解决实际的问题。
文档下载后可定制随意修改,请根据实际需要进行相应的调整和使用,谢谢!并且,本店铺为大家提供各种各样类型的实用资料,如教育随笔、日记赏析、句子摘抄、古诗大全、经典美文、话题作文、工作总结、词语解析、文案摘录、其他资料等等,如想了解不同资料格式和写法,敬请关注!Download tips: This document is carefully compiled by theeditor.I hope that after you download them,they can help yousolve practical problems. The document can be customized andmodified after downloading,please adjust and use it according toactual needs, thank you!In addition, our shop provides you with various types ofpractical materials,such as educational essays, diaryappreciation,sentence excerpts,ancient poems,classic articles,topic composition,work summary,word parsing,copy excerpts,other materials and so on,want to know different data formats andwriting methods,please pay attention!理解LNG接收站的加工工艺流程液化天然气(LNG)作为一种清洁、高效的能源,其在全球能源结构中的地位日益凸显。
LNG接收站有6大工艺系统

LNG接收站有6大工艺系统,其中之一就是蒸发器(BOG)处理工艺系统。
在LNG站场中,常用的BOG处理工艺有两种:BOG再液化工艺及BOG直接压缩工艺。
在大型LNG接收站,LNG运输船抵达码头后,经卸料臂将LNG输送到储罐储存,再由泵升压后送入汽化器,LNG汽化后输送到下游用户管网。
LNG在储存过程中,由于储罐不可避免的漏热,部分LNG将从液相蒸发出来,这部分蒸发气体即为BOG。
采用再液化工艺时,BOG先通过压缩机加压到1MP 左右,然后与LNG低压泵送来的压力为1MPa的LNG过冷液体换热,重新液化为LNG。
若采用BOG直接压缩工艺,则由压缩机将其加压到用户所需压力后直接进入外输管网。
该工艺需要将BOG直接升压至管网压力,在此过程中需要消耗大量的压缩功。
然而,BOG再液化工艺是将液体用泵升压,由于液体体积小很多,且液体压缩性很小,因此液体升压比BOG直接升压可节能50%左右。
如前所述,为防LNG在卸船过程中造成LNG船舱形成负压,一部分BOG需要返回LNG船船以平衡压力。
BOG由于低温贮罐与低温槽车内的LNG的日蒸发率(约为0.3%以下),这部分蒸发气体(温度较低)简称BOG,使贮罐气相空间的压力升高。
为保证贮罐的安全及装卸车的需要,在设计中设置了贮罐安全减压阀(可根据贮罐储存期间压力自动排除BOG),产生的BOG气体通过放空阀至BOG加热器加热后,再进入BOG储罐储存。
EAG低温系统安全阀放空的全部是低温气体,在大约-107℃以下时,天然气的重度大于常温下的空气,排放不易扩散,会向下积聚,容易产生安全隐患。
因此设置一台空温式放散气体加热器,放散气体先通过该加热器,经过与空气换热后的天然气比重会小于空气,高点放散后将容易扩散,从而不易形成爆炸性混合物。
[BOG]: boil off gas 一般称作闪蒸气闪蒸气是LNG气化后的产物,在一定的时间内一般温度很低可以对人造成低温灼伤。
天然气是常温气体。
LNG接收站工艺分析

LNG接收站工艺分析【摘要】LNG是天然气的液态形式,具有无色、无味、不易燃,无毒,易于储存或运输的优良性质。
LNG占天然气体积的1/600。
在大气压下约-162℃,-259℃时,变成液态。
自从1917年世界第一个液化天然气工厂在美国西佛吉尼亚建成之后,LNG作为天然气的一种储存运输模式,以其独特的优势在近年来迅猛发展。
世界生产的天然气中有26.5%被用来做贸易交易,而液化天然气LNG 只占贸易交易中的27.8%。
【关键词】天然气液化天然气LNG外输气化过程LNG以船运为主,通过接收站卸料进气至主干管网。
LNG接收站要求具备高可靠性,高安全性,设备备用的基本条件。
LNG接收站简要流程如下图1:LNG接收站接收,LNG流程主要由两个循环和两部分外输组成,一个循环是LNG卸船时,船体与储罐之间构成的回路循环以保障卸料过程中会产生蒸发气在压力控制下返回船舱,以填补卸下的LNG的空间。
其余的蒸发气由岸上的BOG(蒸发气)处理系统回收。
另外一个循环是由于热量传输和做功等原因在储罐顶部会不断产生BOG,此时利用BOG压缩机和再冷凝器对其进行回收循环,重新注入储罐中以保证储罐的液位和压力需求。
两个外输流程是指槽车灌装外输流程和天然气管线外输流程,其中以天然气管线外输流程为接收站主流程。
LNG通过低压输送泵排出储罐,低压输送泵完全浸没在LNG中,由匀速异步电机驱动,电缆从泵井顶部进入。
LNG从泵井底部吸入,从连接在泵井顶部的出口管线排出。
电源和仪表电缆在穿线管中进行氮气保护。
来自低压输送总管的LNG一部分进入再冷凝器,另一部分直接流到高压泵入口。
经高压输出总管进入气化器的高压输出泵出口LNG压力约为10.19MPag。
来自高压外输总管的LNG在气化器内的气化操作压力约为10MPag,然后进入天然气外输总管。
LNG外输气化过程主要通过开架式气化器或浸没式气化器两种气化方式进行。
开架式气化器(ORV)操作参数如下:LNG流:200t/h;NG出口温度:≥1oC;操作压力:7.7MPa;气化能力:180t/h;海水流量:8300m3/h;海水出口温度:≥5oC。
LNG接收站基本工艺程序

LNG(LiquefiedNaturalGas)即液化天然气。
先将气田生产的天然气净化处理,再经超低温(-162℃)液化就形成液化天然气。
LNG无色、无味、无毒且无腐蚀性,其体积约为同量气态天然气体积的1/620。
天然气作为清洁能源和重要的化工原料,得到了广泛的利用,世界各国把推广利用天然气,提高天然气在一次能源消费中的比重,作为优化能源结构,实现经济、社会和环境协调发展的重要途径。
目前天然气消费在世界能源消费结构中的比重已达35%,成为仅次于石油的第二大能源。
与世界LNG 的应用相比,我国刚刚起步,已建成及在建的LNG接收站还不多。
中国作为新兴的LNG市场,其LNG的需求量很大,随着中国经济的快速发展,在未来的5~10年间对天然气的需求将快速增长。
发气在再冷凝器中液化,再经高压泵增压后进入高压气化器气化外输。
再冷凝工艺可以利用LNG的冷量,减少蒸发气体压缩功的消耗,从而节省能量,比直接输出工艺更加先进、合理。
LNG专用船抵达接收站专用码头后,通过液相卸船臂和卸船管线,借助船上卸料泵将LNG送进接收站的储罐内。
在卸船期间,由于热量的传入和物理位移,储罐内将会产生蒸发气。
这些蒸发气一部分经气相返回臂和返回管线返回LNG船的料舱,以平衡料舱内压力;另一部分通过BOG压缩机升压进入再冷凝器冷凝后,与外输的LNG一起经高压输出泵送入气化器。
利用气化器使LNG气化成气态天然气,经调压、计量后送进输气管网。
LNG接收站工艺流程如图1所示。
接收站的工艺系统主要包括LNG卸船、LNG储存、BOG处理、LNG气化/外输和火炬放空系统。
外输开架式海水气化器1LNG接收站工艺概述LNG通常由专用运输船从生产地输出终端运到目的地接收终端,经再气化后外输至用户。
LNG接收站的工艺方案分为直接输出式和再冷凝式两种,两种工艺方案的主要区别在于对储罐蒸发气(BOG)的处理方式不同。
直接输出式是利用压缩机将LNG储罐的蒸发气压缩增压至低压用户所需压力后与低压气化器出来的气体混合外输;再冷凝式是将储罐内的蒸发气经压缩机增压后,进入再冷凝器,与由LNG储罐泵出的LNG进行冷量交换,使蒸LNG船BOG压缩机再冷凝器ORV液化开然气LNG蒸发气BOG天然气NG高压泵浸没式燃烧气化器SGV图1LNG接收站工艺流程1.1LNG卸船流程入再冷凝器与从储罐送出的LNG混合后,冷凝成LNG运输船在引航船的引领下驶入港口,在波轮的辅助下靠泊到LNG码头。
lng接收站工艺流程

lng接收站工艺流程LNG(液化天然气)接收站是用于接收和储存液化天然气的设施。
本文将介绍一个典型的LNG接收站的工艺流程。
LNG接收站的工艺流程可以分为四个主要步骤:卸船、储存、再气化和分配。
首先是卸船过程。
LNG接收站通常建在海港附近,以便能够方便地接收来自LNG运输船的液化天然气。
卸船过程中,LNG运输船靠泊在码头上,然后将液化天然气从船上泵入接收站内的储罐中。
在此过程中,需要确保液化天然气的安全传输并避免任何泄漏或事故。
接下来是储存阶段。
液化天然气被储存在接收站的储罐中。
这些储罐通常是巨大的钢制容器,能够承受高压并保持液化天然气的低温状态。
储罐内的液化天然气会被保持在恒定的温度和压力下,以确保气体的稳定和安全。
再气化是LNG接收站的下一个步骤。
在这一阶段,液化天然气从储罐中抽出并通过加热系统加热,使其转化为气体状态。
加热系统通常使用海水或其他低成本能源,通过换热器将热量传递给液化天然气。
这个过程的目的是将液化天然气恢复为原始的天然气形态,方便进一步处理和分配。
最后是分配阶段。
经过再气化后,天然气将进入管网或递送给消费者。
在管道网络中,天然气可以被输送到城市、工业区或其他地方进行使用。
分配过程需要确保天然气以安全和高效的方式流动,以满足消费者的需求。
总结起来,LNG接收站的工艺流程涵盖了卸船、储存、再气化和分配等步骤。
这些步骤确保了液化天然气能够安全地从运输船卸载并储存,然后再转化为气态并分配给消费者。
这个工艺流程在现代能源供应中起到了至关重要的作用,为我们提供了可靠和高效的天然气资源。
LNG接收站简介
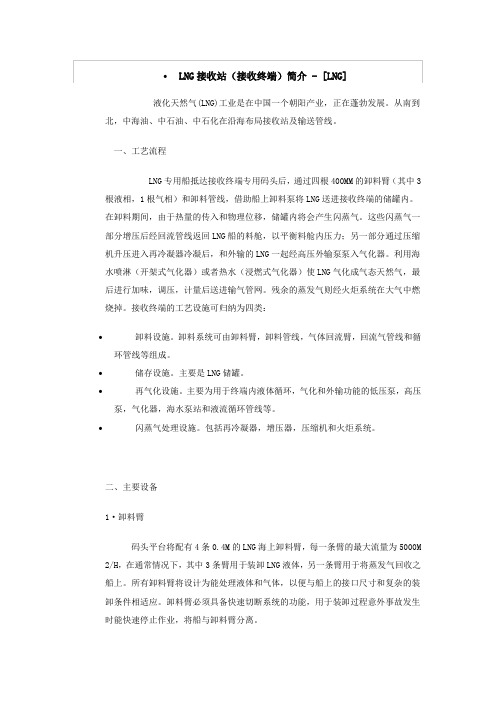
∙LNG接收站(接收终端)简介 - [LNG]液化天然气(LNG)工业是在中国一个朝阳产业,正在蓬勃发展。
从南到北,中海油、中石油、中石化在沿海布局接收站及输送管线。
一、工艺流程LNG专用船抵达接收终端专用码头后,通过四根400MM的卸料臂(其中3根液相,1根气相)和卸料管线,借助船上卸料泵将LNG送进接收终端的储罐内。
在卸料期间,由于热量的传入和物理位移,储罐内将会产生闪蒸气。
这些闪蒸气一部分增压后经回流管线返回LNG船的料舱,以平衡料舱内压力;另一部分通过压缩机升压进入再冷凝器冷凝后,和外输的LNG一起经高压外输泵泵入气化器。
利用海水喷淋(开架式气化器)或者热水(浸燃式气化器)使LNG气化成气态天然气,最后进行加味,调压,计量后送进输气管网。
残余的蒸发气则经火炬系统在大气中燃烧掉。
接收终端的工艺设施可归纳为四类:∙卸料设施。
卸料系统可由卸料臂,卸料管线,气体回流臂,回流气管线和循环管线等组成。
∙储存设施。
主要是LNG储罐。
∙再气化设施。
主要为用于终端内液体循环,气化和外输功能的低压泵,高压泵,气化器,海水泵站和液流循环管线等。
∙闪蒸气处理设施。
包括再冷凝器,增压器,压缩机和火炬系统。
二、主要设备1·卸料臂码头平台将配有4条0.4M的LNG海上卸料臂,每一条臂的最大流量为5000M2/H,在通常情况下,其中3条臂用于装卸LNG液体,另一条臂用于将蒸发气回收之船上。
所有卸料臂将设计为能处理液体和气体,以便与船上的接口尺寸和复杂的装卸条件相适应。
卸料臂必须具备快速切断系统的功能,用于装卸过程意外事故发生时能快速停止作业,将船与卸料臂分离。
2·储罐储罐容量取决于LNG运输船的大小和所需缓冲储存量。
目前世界上常用的储罐类型有地上双层罐壁和地下隔膜两种构造。
福建LNG和广东LNG前一种储罐,珠海BP LPG是地下隔膜构造。
单罐容量最大已达20万m3。
储罐有一个自由(无约束)直立的顶部开口的及由特种耐低温材料9%镍钢制成的内罐。
LNG接收站工艺流程的分析与研究

LNG接收站工艺流程的分析与研究摘要:LNG接收站作为天然气运输的关键环节,其发挥着重要的影响作用。
LNG接收站工艺的流程也是保障天然气资源质量的一个重要环节,其中的每一个步骤的作用及其的注意事项都是十分关键的。
本文即是针对LNG接收站的工艺流程进行了详细的阐述。
关键词:LNG接收站;工艺流程;作用及注意事项引言:自从进入21世纪以来,我国进入了全方位的发展,尤其是我国工业和运输业领域,近几十年得到了飞速的发展。
LNG接收站作为天然气接收、储存、在气化液化的总要环节,在天然气的运输的处理过程中发挥着巨大的作用。
在LNG接收站工艺的各个流程环节也是非常关键的,因此需要对这些环节进行深入的分析和研究。
1、LNG接收站工艺的概述LNG(液化天然气)接收站主要是用于接收、储存和再气化液化天然气,并通过天然气的管道向用户供气。
在LNG接收站进行的生产过程只涉及到物理过程。
在接收站中,天然气的接卸、储存、加压低温下进行的,然后再进行加热气化,最后通过管道进行输送。
1.1LNG接收站的作用LNG接收站主要的作用是对天然气进行接收、存储、再气化。
第一,接收天然气。
LNG接收站主要用于接收从天然气生产地通过船运输或管道输送而来的液化天然气。
第二,储存天然气。
LNG接收站将液化天然气储存在密封的储罐中,以供后续的使用和分配。
第三,天然气再气化。
液化天然气在再气化过程中转化为气态,以便输送到管道系统或直接用于供应天然气用户。
1.2LNG接收站的优势LNG接收站主要的优势是能够进行高密度的存储、安全性高、能够进行长距离的输送等。
液化天然气的体积约为气态天然气的1/600,因此可以有效地储存和运输大量的天然气,而且LNG接收站可以从各种渠道获取液化天然气[1],例如海外供应和液化的可再生能源,提供了更多的能源选择。
液化天然气是易燃易爆的物质,因此LNG接收站必须遵循严格的安全标准和操作规程,以确保运营过程的安全性。
LNG接收站工艺过程涉及到船舶卸液、储罐、泵站、蒸发器、再气化装置等复杂的设备,需要高水平的工程设计和运营管理。
(工艺技术)LNG接收站一般工艺方案
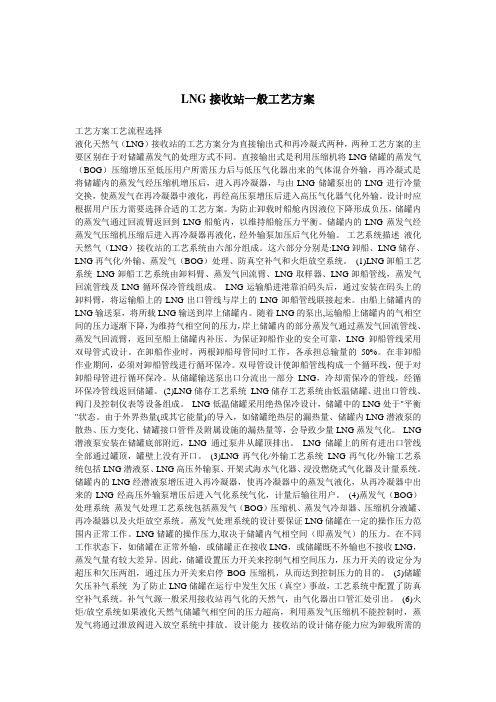
LNG接收站一般工艺方案工艺方案工艺流程选择液化天然气(LNG)接收站的工艺方案分为直接输出式和再冷凝式两种,两种工艺方案的主要区别在于对储罐蒸发气的处理方式不同。
直接输出式是利用压缩机将LNG储罐的蒸发气(BOG)压缩增压至低压用户所需压力后与低压气化器出来的气体混合外输,再冷凝式是将储罐内的蒸发气经压缩机增压后,进入再冷凝器,与由LNG储罐泵出的LNG进行冷量交换,使蒸发气在再冷凝器中液化,再经高压泵增压后进入高压气化器气化外输。
设计时应根据用户压力需要选择合适的工艺方案。
为防止卸载时船舱内因液位下降形成负压,储罐内的蒸发气通过回流臂返回到LNG船舱内,以维持船舱压力平衡。
储罐内的LNG蒸发气经蒸发气压缩机压缩后进入再冷凝器再液化,经外输泵加压后气化外输。
工艺系统描述液化天然气(LNG)接收站的工艺系统由六部分组成。
这六部分分别是:LNG卸船、LNG储存、LNG再气化/外输、蒸发气(BOG)处理、防真空补气和火炬放空系统。
(1)LNG卸船工艺系统LNG卸船工艺系统由卸料臂、蒸发气回流臂、LNG取样器、LNG卸船管线,蒸发气回流管线及LNG循环保冷管线组成。
LNG运输船进港靠泊码头后,通过安装在码头上的卸料臂,将运输船上的LNG出口管线与岸上的LNG卸船管线联接起来。
由船上储罐内的LNG输送泵,将所载LNG输送到岸上储罐内。
随着LNG的泵出,运输船上储罐内的气相空间的压力逐渐下降,为维持气相空间的压力,岸上储罐内的部分蒸发气通过蒸发气回流管线、蒸发气回流臂,返回至船上储罐内补压。
为保证卸船作业的安全可靠,LNG卸船管线采用双母管式设计。
在卸船作业时,两根卸船母管同时工作,各承担总输量的50%。
在非卸船作业期间,必须对卸船管线进行循环保冷。
双母管设计使卸船管线构成一个循环线,便于对卸船母管进行循环保冷。
从储罐输送泵出口分流出一部分LNG,冷却需保冷的管线,经循环保冷管线返回储罐。
(2)LNG储存工艺系统LNG储存工艺系统由低温储罐、进出口管线、阀门及控制仪表等设备组成。
LNG接收站工艺系统及主要设备

LNG接收站工艺系统及主要设备引言液化天然气(LNG)作为一种清洁、高效的能源正在成为全球能源市场的新热点,LNG已成为国际天然气贸易的重要部分。
我国对LNG 产业的发展越来越重视,分别在广东、福建、上海、江苏、浙江、山东、河北、辽宁等地区规划和实施了LNG项目。
上海LNG项目于2009年10月份正式投产试运行,成为继广东、福建后我国完成的第三个LNG项目。
上海液化天然气项目一期工程建设规模为年接收300万吨工程,包括:1座14.5万m3 LNG船专用码头和1座3000吨级工作船码头;3座16.5 m3 LNG储罐和相应的LNG回收、输送、气化及公用配套设施;52km输气管线(包括36km海底输气干线和16km陆域输气管线),在临港新城输气末站进入上海城市天然气高压主干网系统。
下文将以上海LNG一期项目为例,介绍LNG接收终端的工艺系统、主要设备和操作过程中主要控制参数。
2 LNG接收站工艺系统2.1 LNG主要物理性质在大气条件下,天然气是高易燃性的无色气体,无味或有很淡的臭味。
蒸汽对眼睛、鼻子或喉咙无刺激性,但吸入会导致头晕、呼吸困难或丧失意识,高气体浓度时可能导致窒息。
LNG液体可造成冻伤,气体的主要成分是甲烷。
LNG的体积约为其气态体积的1/620,主要成分(%,摩尔)为:CH4 85~90,C2H6 3~8,C3H8 1~3,C4H10 1~2,C+5 微量。
LNG再气化(约-162℃)时的蒸发潜热约为511 kJ/kg。
2.2 LNG产业链LNG利用是一项投资十分巨大、上下游各环节联系十分紧密的链状系统工程,由天然气开采、天然气液化、LNG运输、LNG接收与气化、天然气外输管线、天然气最终用户等六个环节组成,产业链如图1所示。
其中任何一个环节出现问题都将使整个系统停车,而且必须对上下游环节做出巨额赔偿。
因此LNG利用各个环节的工艺及设备必须安全可靠,LNG接收站是其中重要环节之一,要求更为严格。
LNG接受站工艺技术研究
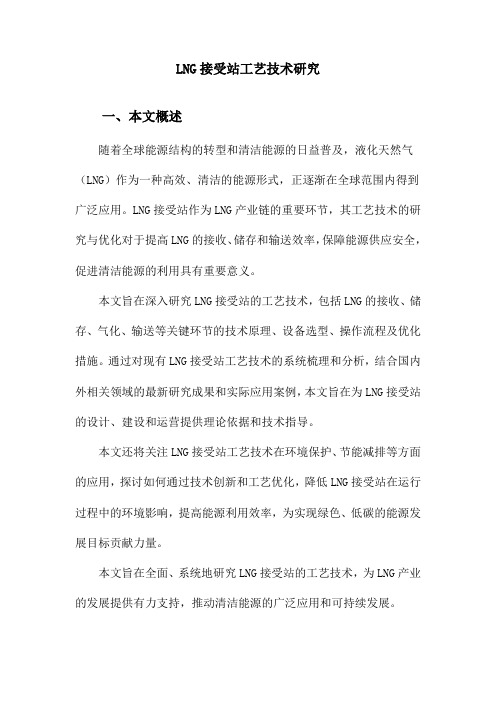
LNG接受站工艺技术研究一、本文概述随着全球能源结构的转型和清洁能源的日益普及,液化天然气(LNG)作为一种高效、清洁的能源形式,正逐渐在全球范围内得到广泛应用。
LNG接受站作为LNG产业链的重要环节,其工艺技术的研究与优化对于提高LNG的接收、储存和输送效率,保障能源供应安全,促进清洁能源的利用具有重要意义。
本文旨在深入研究LNG接受站的工艺技术,包括LNG的接收、储存、气化、输送等关键环节的技术原理、设备选型、操作流程及优化措施。
通过对现有LNG接受站工艺技术的系统梳理和分析,结合国内外相关领域的最新研究成果和实际应用案例,本文旨在为LNG接受站的设计、建设和运营提供理论依据和技术指导。
本文还将关注LNG接受站工艺技术在环境保护、节能减排等方面的应用,探讨如何通过技术创新和工艺优化,降低LNG接受站在运行过程中的环境影响,提高能源利用效率,为实现绿色、低碳的能源发展目标贡献力量。
本文旨在全面、系统地研究LNG接受站的工艺技术,为LNG产业的发展提供有力支持,推动清洁能源的广泛应用和可持续发展。
二、LNG接受站概述液化天然气(LNG)接受站,也称为液化天然气接收站或LNG终端,是专门用于接收、储存、气化并输送液化天然气的设施。
LNG接受站在整个天然气供应链中扮演着关键角色,它不仅连接了天然气的海上运输与陆地管网,还通过其高效、安全的运营确保了天然气供应的连续性和稳定性。
LNG接受站通常由以下几个主要部分组成:接收码头、储罐区、气化设施、外输管道以及相关辅助设施。
接收码头负责接收由LNG运输船运送的液化天然气,并将其通过管道输送至储罐区。
储罐区是LNG的主要储存场所,通常采用大型绝热储罐来保持LNG的低温状态。
气化设施则将LNG加热气化,转化为气态天然气,以便通过外输管道输送至用户。
LNG接受站的技术特点主要体现在其高效的液化、储存和气化过程中。
液化技术通过降低天然气的温度至-162°C左右,使其体积大幅缩小,便于运输和储存。
液化天然气接收站工艺及设备

液化天然气接收站工艺及设备2008-8-6分享到:QQ空间新浪微博开心网人人网LNG接收站地主要功能是接收、储存、再气化液化天然气,为区域管网用户稳定供气.近几十年来,随着工程建设地推进,先进、可靠地接收站技术已日趋成熟,可以为我们所用. b5E2RGbCAP一、接收站工艺LNG接收站按照对LNG储罐蒸发气(BOG>地处理方式不同,接收站工艺方法可以分为直接输出和再冷凝两种.直接输出法是将蒸发气压缩到外输压力后直接送至输气管网;再冷凝法是将蒸发气压缩到较低地压力(通常为0.9MPaG>与由LNG 低压输送泵从LNG储罐送出地LNG在再冷凝器中混合.由于LNG加压后处于过冷状态,可以使蒸发气再冷凝,冷凝后地LN G经LNG高压输送泵加压后外输.因此,再冷凝法可以利用LN G地冷量,并减少了蒸发气压缩功地消耗,节省了能量.对于大型LNG接收站大多采用再冷凝工艺.图6-1所示是典型地接收站再冷凝工艺流程[4].p1EanqFDPwDXDiTa9E3dRTCrpUDGiT接收站地生产系统包括:卸船系统、储存系统、蒸发气处理系统、输送系统、外输及计量系统等.(一> 卸船系统接收站地卸船系统包括专用码头、卸料臂、蒸发气返回臂和管路等.CNG专用码头地特点是接收品种单一、数量多、船型大.码头上除设有大型运输船靠泊、停泊设施外,LNG码头地专用设备是卸料臂.卸船操作在操作员地监控下进行,重点是控制系统压力.卸料臂通过液压系统操作.LNG运输船到达卸船码头后,通过运输船上地输送泵,经过多台卸料臂分别通过支管汇集到总管,并通过总管输送到LNG储罐中.LNG进入储罐后置换出地蒸发气,通过一根返回气管道,经气相返回臂,送到运输船地LNG储舱中,以保持系统地压力平衡.5PCzVD7HxA 在卸船操作初期,采用较小地卸船流量来冷却卸料臂及辅助设施,以避免产生较多地蒸发气,导致蒸发气处理系统超负荷而排放到火炬.当冷却完成后,再逐渐增加流量到设计值.j LBHrnAILg卸船作业完成后,使用氮气将残留在卸料臂中地LNG吹扫干净,并准备进行循环操作.,从各卸料支管中排除地LNG进入码头上设置地收集罐,并通过收集罐加热器将排除地LNG 气化后经气体返回管线送到蒸发气总管.xHAQX74J0X在无卸船期间,通过一根从低压输出总管来地循环管线以小流量LNG经卸料总管循环返回再冷凝器,以保持LNG卸料总管处于冷备用状态.LDAYtRyKfE(二> 储存系统1. 储罐储存系统是接收站重要地生产系统,而储罐是该系统地主要设备.进出储罐地所有管线接口都在罐顶.为了使不同密度地LNG以不同方式进入储罐,流程上安排卸船时LNG可以从储罐地上部管口直接进入储罐,也可通过内部插入管由底部进入储罐.通常在操作中,较重地LNG从上部进入,较轻地LN G从下部进入.同时,也可通过LNG低压输送泵将罐内LNG循环到上部或底部,从而有效防止分层、翻滚现象地产生.Zzz6 ZB2Ltk(1> 储罐地液位控制为了确保储罐地安全操作,储罐地液位、温度、密度监测十分重要.每个储罐都应设置足够地液位、温度、密度连续测量设施,以有效监控储罐地液位.连续测量设施由数字逻辑单元和电机驱动单元组成,可以在LNG储罐内垂直移动、连续测量.当温差超过0.2℃或密度差超过0.5kg/m3时,应用L NG低压输送泵对罐内LNG进行循环操作,以肪止出现分层翻滚现象.dvzfvkwMI1储罐设有高低液位自动保护装置,在液位不正常时,报警并联锁停止进料或停止罐内低压泵运行.(2> 储罐地压力控制LNG储罐是常压储存,全容罐地设计压力一般为29kPa,因而外界大气压地变化对储罐地操作影响很大,罐地压力控制采用绝对压力为基准.在正常操作条件下,储罐地绝对压力是通过BOG压缩机压缩回收储罐地蒸发气体来控制地.在两次操作间隔时间段,储罐地操作压力应维持在低压状态[通常为0.1073MPa(绝压>],以防压力控制系统发生故障时,储罐操作有一个缓冲空间.在卸船操作期间,储罐地压力将升高,储罐处于较高压力操作状态.rqyn14ZNXI储罐地压力保护采用分级制:第一级超压保护将排火炬,当储罐压力达到一定值(如储罐设计压力为0.029MPa,则储罐压力达到0.026MPa>时,控制阀打开,超压部分气体排入火炬系统.第二级超压保护排大气,当储罐压力达到设计压力时,储罐上压力安全阀打开,超压部分气体直接排入大气.第一级负压保护靠补压气体,当储罐在操作中压力降低到设计负压时,将通过高压外输天然气总管上来地经两级减压后地气体来维持储罐内压力稳定.第一级负压保护通过安装在储罐上地真空阀来实现.EmxvxOtOco(3> 储罐地温度监测LNG储罐地内罐底部和罐体上设有若干测温点,可监测预冷操作和正常操作时罐内地温度.在罐外也设有多个测温点,可监测LNG地泄漏.为防止储罐基础结冰而危及混凝土基础,在储罐基础上设有两套电加热系统,并在基础地不同位置设有温度检测设施以控制电加热系统.SixE2yXPq52. 罐内泵罐内泵地用途是将LNG储罐内地液体抽出并送到下游装置.在每台泵地出口管线上装有流量控制阀,用以调节各运行泵地出口在相同流量下工作和紧急情况时切断输出.为保护泵,在每台泵地出口管线上同时装有最小流量控制阀,该最小流量管线也可用于罐内LNG地混合以防止出现分层.6ewMyir QFL当接收站处于“零输出”状态时,站内所有地低、高压输送泵停止运行,仅开启一台罐内泵以确保少量地LNG在卸料总管中及LNG输送管线中进行循环,保持系统处于冷状态.ka vU42VRUs(三> 蒸发气处理系统1. 蒸发气增压由于外界能量地输入,如泵运转、周围环境热量地泄入、大气压变化、环境影响等都会使处于极低温地液化天然气受热蒸发,产生蒸发气(BOG>.当卸船作业LNG送入储罐时造成罐内LNG体积地变化也会加快蒸发.LNG接收站在卸船操作时产生地蒸发气地量是无卸船操作时地数倍.y6v3ALoS89储罐内地蒸发气压力很低,需要增压才能进入系统.采用蒸发气压缩机将储罐内地蒸发气抽出增压后送入处理系统.蒸发气压缩机地控制可以是自动地,也可以是手动地.在自动操作模式下,LNG储罐压力通过一个总地绝压控制器来控制,该绝压控制器可自动选择蒸发气压缩机地运行负荷等级(50%或100%>.在手动操作模式下,操作人员将根据储罐地压力检测情况来选择蒸发气压缩机地运行负荷等级.M2ub6vSTnP 如果蒸发气地流量比压缩机(或再冷凝器>地处理能力高,储罐和蒸发气总管地压力将升高,在这种情况下,多出地部分蒸发气将通过与蒸发气总管相接地压力控制阀排到火炬.0Yu jCfmUCw一般选用1台压缩机地能力足够处理不卸船操作条件下产生地蒸发气体,仅在卸船时,才同时开2台压缩机.2. 再冷凝采用再冷凝工艺地接收站,蒸发气增压后送入再冷凝器.再冷凝器主要有两个功能,一是在再冷凝器中,经加压后地蒸发气与低压输送泵送出地LNG混合,由于LNG加压后处于过冷状态,使蒸发气再冷凝为液体,经LNG高压输送泵加压后外输,因此再冷凝器地另一个功能是可用作LNG高压输送泵地入口缓冲容器.eUts8ZQVRd再冷凝器地内筒为不锈钢鲍尔环填充床.蒸发气和LNG都从再冷凝器地顶部进入,并在填充床中混合.此处地压力和液位控制保持恒定,以确保LNG高压输送泵地入口压力恒定.再冷凝器设有比例控制系统,根据蒸发气地流量控制进入再冷凝器地LNG流量,以确保进入高压输送泵地LNG处予过冷状态.sQsAEJkW5T在再冷凝器地两端设有旁路,未进入再冷凝器地LNG通过旁路与来自再冷凝器地LNG混合后进入高压输送泵,同时旁路也可以保证再冷凝器检修时,LNG地输出可继续进行.GMsI asNXkA如果再冷凝器气体入口压力在高值范围不规则波动,再冷凝器地操作压力控制器将通过释放部分气体到蒸发气总管来维持.TIrRGchYzg在外输量较低时,再冷凝器可能不能将压缩后地蒸发气体完全冷凝下来.这种情况可通过再冷凝器液体出口温度增加来检测.通过该温度信号调节控制蒸发气压缩机地能力.7EqZ cWLZNX(四> 输送系统LNG接收站输送系统地主要功能是实现LNG再气化,外输供气.该系统主要包括高压输送和LNG气化两部分.lzq7IGf0 2E1. LNG高压输送泵从再冷凝器出来地LNG直接进入LNG高压输送泵,加压后通过总管输送到气化器.根据外输气量地要求控制LNG高压输送泵启停台数.zvpgeqJ1hk在气化器地入口LNG管线上设有流量调节来控制LNG高压输送泵地外输流量.该流量调节可以由操作员手动控制,也可根据外输天然气总管上地压力变化来控制,通过LNG高压输送泵地外输流量来保证外输天然气总管上地压力稳定.在高压输送泵出口管上设有最小流量回流管线,以保护泵地安全运行.NrpoJac3v12. 气化器LNG在气化器中再气化为天然气,计量后经输气管线送往各用户.气化后地天然气最低温度一般为0℃.LNG接收站一般设有两种气化器:一种用于正常供气气化,长期稳定运行;另一种通常仅作为调峰或维修时使用,要求启动快.气化器通常用海水作热源,海水流量通过海水管线上地流量调节阀来控制,控制海水流量满足气化热负荷要求,同时限制海水温降不超过5℃.1nowfTG4KI(五> 外输及计量系统接收站天然气外输若有多条输气管线,可在外输总管管汇上接出.天然气总管上设有一套完善地压力保护系统,.以防输气管线超压.外输总管上设有压力控制阀,将气化器出口压力控制在要求地外输压力,以防止输气管线因压力过低而造成高压输送泵背压过低.计量成套设备要满足贸易计量要求,并设有1套备用回路.fjnFLDa5Zo(六> 接收站地操作按原料输入和产品输出地状况,LNG接收站地操作可分为正常输出操作、零输出操作和备用操作三种情况.1. 正常输出操作正常输出操作时按照有无卸船又可以分为两种模式.一种是在正常输出操作时无卸船作业,这种操作模式是L NG接收站运行中最常用地操作模式.此时,按照供气需求调节泵地排量,控制气化器地气化量,满足外输需求.同时为了保持卸船总管地冷状态,需要循环少量地LNG.当外输气量很大时,将从天然气输出总管上返回少量气体到LNG储罐来保持压力平衡.tfnNhnE6e5另一种是在正常输出操作时有卸船作业,此时,卸船总管地LNG循环将停止,并根据LNG地密度决定从LNG储罐地顶部或下部进料.主要操作有:LNG运输船靠岸、卸料臂与运输船联结、LNG卸料臂冷却、LNG卸料、卸料完成放净卸料臂、将卸料臂与运输船脱离.HbmVN777sL2. 零输出操作零输出操作是接收站停止向外供气时地状态.在此期间,不安排卸船.如果在卸船期间,接收站地输出停止,卸船应同时停止,以防止大量蒸发气不能冷凝而排放到火炬.V7l4jRB8 Hs3. 备用操作备用操作是LNG接收站处于无卸船和零输出时地操作.在备用操作时,通过少量地LNG循环来保持系统地冷状态.蒸发气将用作燃料气,多余地蒸发气则排放到火炬.83lcPA59W9二、接收站主要设备接收站地主要设备是储罐、蒸发气压缩机、高低压输送泵、再冷凝器、气化器等.第三章叙述天然气液化工艺和设备时,对有关设备性能已做了描述,本节着重对接收站如何配套选用这些设备方面作介绍.mZkklkzaaP(一> 储罐1. 罐容接收站储罐地容量决定了接收站地储存能力,而确定LNG 接收站储存能力地因素是多方面地,如LNG运输船地船容、码头最大连续不可作业天数、LNG接收站地外输要求及其他计划地或不可预料事件,如LNG运输船地延期或维修、气候变化等.AVktR43bpw接收站储存LNG地能力,所需要地最小罐容可以按下式计算Vs=(Vt+n×Qa-t1×q+r×Qc×t2> (6-1>式中K——LNG罐最小需求容积,m3;K——LNG船地最大容积,m3;n——LNG船地延误时间(n1码头不可作业天数、n2航程延误天数、n3码头调度延误天数>,d;Qa——高峰月平均日供气量,m3/d;t1——LNG卸料时间(12h>;g——最小送出气量,m3/d;r——LNG船航行期间市场变化系数;t2——LNG船航行时间,d;Qc——高峰月平均城市燃气日供气量,m3/d.计算得到地LNG罐最小需求容积,按此确定单罐容积和罐地台数.对于大型LNG接收站来说,单罐容积大、台数少,可以节省占地、减少投资.但是罐地数量也要考虑卸船作业等操作管理地需要,不宜太少.ORjBnOwcEd2. 罐型各种形式地LNG储罐地优缺点已在第四章做过叙述,一般做法是,对于罐容小于14×104m3,可以考虑单容、双容或全容三种形式;对于罐容在(14~16>×104m3之间地,一般选用双容或全容罐;而罐容大于16×104m3地,建议选用全容罐.大型LNG接收站从安全考虑,如果可能,一般选用全容式混凝土顶储罐(FCCR>.全容式混凝土顶储罐地最大操作压力比金属顶储罐地高.在卸船操作时,可利用罐内蒸发气自身压力直接返回到LNG运输船上,无需设置返回气风机加压.2MiJ Ty0dTT全容式混凝土顶储罐地设计压力一般为29kPa,设计温度为-175~+65℃.日蒸发率地要求按罐地容积大小而不同,罐容小,表/体比大,日蒸发率高.目前国际上对10×104m3以上地储罐,要求日蒸发率小于0.05%.10×104m3以下地储罐,日蒸发率小于0.08%.LNG储罐内罐材料为9%镍钢.为安全起见,所有地连接管口均设计在罐地顶部;在罐地底部设有隔离支撑平台,并设有加热系统,以防基础冻结现象发生.在LNG储罐上设有足够地报警和紧急停车设施以保证LNG储罐最大地安全.同时,在LNG储罐上设有液位、温度、密度连续检测仪表,以确保正常安全生产.gIiSpiue7A(二> 气化器LNG气化器是一种专门用于液化天然气气化地换热器,但由于液化天然气地使用特殊性,使LNG气化器也不同于其他换热器.低温地液态天然气要转变成常温地气体,必须要提供相应地热量使其气化.热量地来源可以从环境空气和水中获得,也可以通过燃料燃烧或蒸气来获得.uEh0U1Yfmh 对于基本负荷型系统使用地气化器,使用率高(通常在8 0%以上>,气化量大.首先考虑地应该是设备地运行成本,最好是利用廉价地低品位热源,如从环境空气或水中获取热量,以降低运行费用.以空气或水作热源地气化器,结构最简单,几乎没有运转部件,运行和维护地费用很低,比较适合于基本负荷型地系统.IAg9qLsgBX对于调峰型系统使用地气化器,是为了补充用气高峰时供气量不足地装置,其工作特点是使用率低,工作时间是随机牲地.应用于调峰系统地气化器,要求启动速度快,气化速率高,维护简单,可靠性高,具有紧急启动地功能.由于使用率相对较低,因此要求设备投资尽可能低,而对运行费用则不大苛求. WwghWvVhPE现在使用地LNG气化器有下列几种形式:开架式气化器(ORV>、浸没燃烧式气化器(SCV>、中间介质式气化器(IFV*丙烷>、中间介质管壳式气化器(IFV-强制循环>.在上述形式地气化器中,大量采用地是开架式气化器和浸没燃烧式气化器,值当海水质量不能满足开架式气化器要求或接收站附近有电厂废热可利用、其他工艺设施需要冷能时,通常也会采用中间介质式气化器.asfpsfpi4k1. 开架式气化器(Open Rack Vaporizer>开架式气化器是一种水加热型气化器.由于很多LNG生产和接受装置都是靠海建设,所以可以用海水作为热源.海水温度比较稳定,热容量大,是取之不尽地热源.开架式气化器常用于基本负荷型地大型气化装置,最大气化量可达180t/h.气化器可以在0~100%地负荷范围内运行.可以根据需求地变化遥控调整气化量.ooeyYZTjj1开架式气化器由一组内部具有星形断面,外部有翅片地铝合金管组成,管内有螺旋杆,以增加LNG流体地传热.管内为LNG,管外为喷淋地海水.为防止海水地腐蚀,外层喷涂防腐涂层.整个气化器用铝合金支架固定安装.气化器地基本单元是传热管,由若干传热管组成板状排列,两端与集气管或集液管焊接形成一个管板,再由若干个管板组成气化器.气化器顶部有海水地喷淋装置,海水喷淋在管板外表面上,依靠重力地作用自上而下流动.液化天然气在管内向上流动,在海水沿管板向下流动地过程中,LNG被加热气化.气化器外形见图6-2,其工作原理见图6—3.这种气化器也称之为液膜下落式气化器.虽然水流动是不停止地,但这种类型地气化器工作时,有些部位可能结冰,使传热系数有所降低.BkeGuInkxIPgdO0sRlMo3cdXwckm15开架式气化器地投资较大,但运行费用较低,操作和维护容易,比较适用于基本负荷型地LNG接收站地供气系统.但这种气化器地气化能力,受气候等因素地影响比较大,随着水温地降低,气化能力下降.通常气化器地进口水温地下限大约为5℃,设计时需要详细了解当地地水文资料.表6-2列出一些开架式海水加热型LNG气化器地技术参数[5].h8c52WOngM 表6-2 海水加热型LNG气化器地技术参数大型地气化器装置可由数个管板组组成,使气化能力达到预期地没计值,而且可以通过管板组对气化能力进行调整.v4 bdyGious水膜在沿管板下落地过程中具有很高地传热系数,可达到5800W/(m2·K>.在传热管内侧,LNG蒸发时地传热系数相对较低,新型地气化器对传热管进行了强化设计.传热管分成气化区和加热区,采用管内肋片来增加换热面积和改变流道地形状,增加流体在流动过程地扰动,达到增强换热地目地.J0b m4qMpJ9管外如果产生结冰,也会影响传热性能.为了改善管外结冰地问题,采用具有双层结构地传热管,LNG从底部地分配器先进入内管,然后进入内外管之间地夹套.夹套内地LNG直接被海水加热并立即气化,然而在内管内流动地LNG是通过夹套中已经气化地LNG蒸气来加热,气化是逐渐进行.夹套虽然厚度较薄,但能提高传热管外表面地温度,所以能抑制传热管外表结冰,保持所有地传热面积都是有效地,因此提高了海水与LNG之间地传热效率.XVauA9grYP新型地LNG气化器具有以下一些特点:设计紧凑,节省空间;提高换热效率,减少海水量,节约能源;所有与天然气接触地组件都用铝合金制造,可承受很低地温度,所有与海水接触地平板表面镀以铝锌合金,防止腐蚀;LNG管道连接处安装了过渡接头,减少泄漏,提高运行地安全性;启动速度快,并可以根据需求地变化遥控调整天然气地流量,改善了运行操作性能;开放式管道输送水,易于维护和清洁.bR9C6TJscw 开架式气化器使用天然热源(海水>,因此操作费用比较低.但由于LNG气化需要大量海水,对海水地品质有一定要求:(1> 重金属离子Hg“检测不出;Cu++≤10×10-9;(2> 固体悬浮物≤80×10-6;(3> pH值7.5~8.5;(4> 要求过滤器在海水取水处能够去除10mm以上地固体颗粒.为了防止海水对基体金属地腐蚀,可以在金属表面喷涂保护层,以增加腐蚀地阻力.涂层材料可采用质量分数为85%Al +15%Zn地锌铝合金.pN9LBDdtrd开架式气化器需要较高地投资,安装费用也很高.与浸没燃烧式气化器相比,开架式气化器是利用海水,操作消耗主要是海水泵地电耗,所以它地优点在于操作费用很低,两者之间地运行费用比为1:10.DJ8T7nHuGT2. 浸没燃烧式气化器在燃烧加热型气化器中,浸没式燃烧加热型气化器是使用最多地一种.其结构紧凑,节省空间,装置地初始成本低.它使用了一个直接向水中排出燃气地燃烧器,由于燃气与水直接接触,燃气激烈地搅动水,使传热效率非常高.水沿着气化器地管路向上流动,LNG在管路中气化,气化装置地热效率在9 8%左右.每个燃烧器每小时105GJ地加热能力,适合于负荷突然增加地要求,可快速启动,并且能对负荷地突然变化作出反应.可以在10%~100%地负荷范围内运行,适合于紧急情况或调峰时使用.运用气体提升地原理,可以在传热管外部获得激烈地循环水流,管外地传热系数可以达到5800~8000W/(m 2·K>.表6-3列出了浸没式燃烧加热型气化器地技术参数[5].QF81D7bvUA表6-3 浸没式燃烧加热型LNG气化器地技术参数① 标准状态下地空气体积流量.浸没式燃烧加热型气化器地工作原理如图6-4所示,燃料气和压缩空气在气化器地燃烧室内燃烧,燃烧后地气体通过喷嘴进入水中,将水加热.LNG经过浸没在水中地盘管,由热水加热而蒸发.4B7a9QFw9hix6iFA8xoXwt6qbkCyDE浸没燃烧式气化器优越性在于整体投资和安装费用很低,与海水气化器相比,外形较小,操作灵活.但是浸没式燃烧气化器地缺点是操作费用很高.Kp5zH46zRk3. 中间介质式气化器采用中间传热流体地方法可以改善结冰带来地影响,通常采用丙烷、丁烷或氟利昂等介质作中间传热流体.这样加热介质不存在结冰地问题.由于水在管内流动,因此可以利用废热产生地热水.换热管采用钛合金管,不会产生腐蚀,,对海水地质量要求也没有过多地限制.Yl4HdOAA61中间介质式气化器也有压同地形式,但皆有一个共同之处,就是用中间介质作为热媒,其中间介质可以是丙烷或醇(甲醇或乙二醇>水溶液,加热介质可为海水、热水、空气等,采用特殊形式地换热器或管壳式换热器来气化LNG.ch4PJx4BlI(1> 丙烷热媒中间介质气化器(IFV>该技术由日本神户制钢(Kobelco>提供.图6-5所示是这种气化器地工作原理,该类气化器以海水或邻近工厂地热水作为热源,并用此热源去加热中间介质(丙烷>并使其气化,再用丙烷蒸气去气化LNG.该气化器由两部分组成,一部分为利用丙烷气化冷凝地LNG气化器,第二部分为LNG气化后NG地加热器.在LNG气化部分,丙烷在管壳式气化器地壳程以气液两相形式循环.当使用海水为加热介质时采用钛管,海水在管程流动,所以抗海水中固体悬浮物地磨蚀较好.qd3YfhxCzo E836L11DO5S42ehLvE3M(2> 中间介质管壳式气化器(STV>该技术是采用一般管壳式换热器作气化器,水或甲醇(乙二醇>水溶液作为中间热媒气化LNG,初始热源可以用热水、海水或空气.先用初始热源将中间热媒加热,再用已被加热地中间热媒通过管壳式气化器去气化LNG.中间热媒需用循环。
液化天然气接收站工艺及设备(新编版)

液化天然气接收站工艺及设备(新编版)( 安全管理 )单位:_________________________姓名:_________________________日期:_________________________精品文档 / Word文档 / 文字可改液化天然气接收站工艺及设备(新编版)Safety management is an important part of production management. Safety and production are inthe implementation process液化天然气接收站工艺及设备(新编版)LNG接收站的主要功能是接收、储存、再气化液化天然气,为区域管网用户稳定供气。
近几十年来,随着工程建设的推进,先进、可靠的接收站技术已日趋成熟,可以为我们所用。
一、接收站工艺LNG接收站按照对LNG储罐蒸发气(BOG)的处理方式不同,接收站工艺方法可以分为直接输出和再冷凝两种。
直接输出法是将蒸发气压缩到外输压力后直接送至输气管网;再冷凝法是将蒸发气压缩到较低的压力(通常为0.9MPaG)与由LNG低压输送泵从LNG储罐送出的LNG在再冷凝器中混合。
由于LNG加压后处于过冷状态,可以使蒸发气再冷凝,冷凝后的LNG经LNG高压输送泵加压后外输。
因此,再冷凝法可以利用LNG的冷量,并减少了蒸发气压缩功的消耗,节省了能量。
对于大型LNG接收站大多采用再冷凝工艺。
图6-1所示是典型的接收站再冷凝工艺流程[4]。
接收站的生产系统包括:卸船系统、储存系统、蒸发气处理系统、输送系统、外输及计量系统等。
(一)卸船系统接收站的卸船系统包括专用码头、卸料臂、蒸发气返回臂和管路等。
CNG专用码头的特点是接收品种单一、数量多、船型大。
码头上除设有大型运输船靠泊、停泊设施外,LNG码头的专用设备是卸料臂。
卸船操作在操作员的监控下进行,重点是控制系统压力。
卸料臂通过液压系统操作。
LNG接收站运行工艺及设备综述
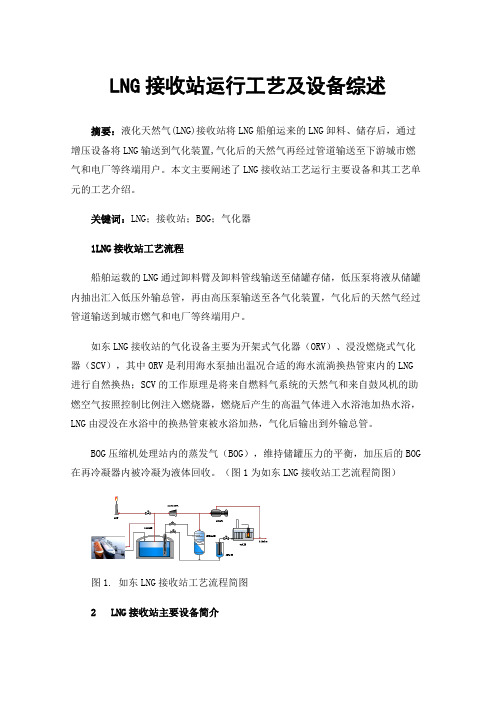
LNG接收站运行工艺及设备综述摘要:液化天然气(LNG)接收站将LNG船舶运来的LNG卸料、储存后,通过增压设备将LNG输送到气化装置,气化后的天然气再经过管道输送至下游城市燃气和电厂等终端用户。
本文主要阐述了LNG接收站工艺运行主要设备和其工艺单元的工艺介绍。
关键词:LNG;接收站;BOG;气化器1LNG接收站工艺流程船舶运载的LNG通过卸料臂及卸料管线输送至储罐存储,低压泵将液从储罐内抽出汇入低压外输总管,再由高压泵输送至各气化装置,气化后的天然气经过管道输送到城市燃气和电厂等终端用户。
如东LNG接收站的气化设备主要为开架式气化器(ORV)、浸没燃烧式气化器(SCV),其中ORV是利用海水泵抽出温况合适的海水流淌换热管束内的LNG 进行自然换热;SCV的工作原理是将来自燃料气系统的天然气和来自鼓风机的助燃空气按照控制比例注入燃烧器,燃烧后产生的高温气体进入水浴池加热水浴,LNG由浸没在水浴中的换热管束被水浴加热,气化后输出到外输总管。
BOG压缩机处理站内的蒸发气(BOG),维持储罐压力的平衡,加压后的BOG 在再冷凝器内被冷凝为液体回收。
(图1为如东LNG接收站工艺流程简图)图1. 如东LNG接收站工艺流程简图2 LNG接收站主要设备简介2.1卸料臂如东LNG接收站码头配置4台卸料臂用于连接船岸的工艺系统,3台液相臂用于LNG的装卸,设备能力4000~6000m3/h;1台气相臂用于向船方返气补压或给船泄压,设备能力12000m3/h。
2.2储罐如东接收站配置6座全容式混凝土穹顶储罐(FCCR)储罐,储罐主体结构均采用 9%Ni 钢内罐、带钢衬层的预应力混凝土外罐和外顶盖,内、外罐罐底与罐壁间填充珍珠岩等保冷材料。
内罐顶采用吊顶结构,吊顶设有通气孔,允许内罐里的 LNG 气体与外罐空间连通。
内、外罐各自有独立承受储存介质的能力。
全包容罐的外罐可以承受内罐泄漏的 LNG 及其气体,不会向外泄漏。
LNG接收站冷能发电工艺参数优化设计
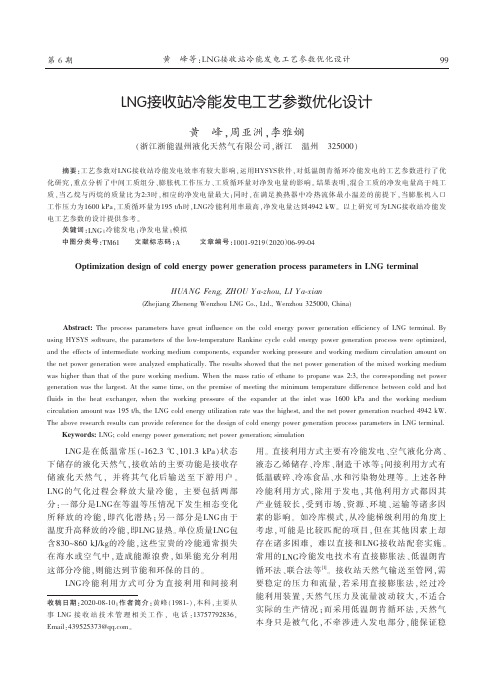
LNG是在低温常压(鄄162.3℃、101.3kPa)状态下储存的液化天然气,接收站的主要功能是接收存储液化天然气,并将其气化后输送至下游用户。
LNG的气化过程会释放大量冷能,主要包括两部分:一部分是LNG在等温等压情况下发生相态变化所释放的冷能,即汽化潜热;另一部分是LNG由于温度升高释放的冷能,即LNG显热。
单位质量LNG包含830~860kJ/kg的冷能,这些宝贵的冷能通常损失在海水或空气中,造成能源浪费,如果能充分利用这部分冷能,则能达到节能和环保的目的。
LNG冷能利用方式可分为直接利用和间接利用。
直接利用方式主要有冷能发电、空气液化分离、液态乙烯储存、冷库、制造干冰等;间接利用方式有低温破碎、冷冻食品、水和污染物处理等。
上述各种冷能利用方式,除用于发电,其他利用方式都因其产业链较长,受到市场、资源、环境、运输等诸多因素的影响。
如冷库模式,从冷能梯级利用的角度上考虑,可能是比较匹配的项目,但在其他因素上却存在诸多困难,难以直接和LNG接收站配套实施。
常用的LNG冷能发电技术有直接膨胀法、低温朗肯循环法、联合法等[1]。
接收站天然气输送至管网,需要稳定的压力和流量,若采用直接膨胀法,经过冷能利用装置,天然气压力及流量波动较大,不适合实际的生产情况;而采用低温朗肯循环法,天然气本身只是被气化,不牵涉进入发电部分,能保证稳LNG接收站冷能发电工艺参数优化设计黄峰,周亚洲,李雅娴(浙江浙能温州液化天然气有限公司,浙江温州325000)摘要:工艺参数对LNG接收站冷能发电效率有较大影响,运用HYSYS软件,对低温朗肯循环冷能发电的工艺参数进行了优化研究,重点分析了中间工质组分、膨胀机工作压力、工质循环量对净发电量的影响。
结果表明,混合工质的净发电量高于纯工质,当乙烷与丙烷的质量比为2:3时,相应的净发电量最大;同时,在满足换热器中冷热流体最小温差的前提下,当膨胀机入口工作压力为1600kPa,工质循环量为195t/h时,LNG冷能利用率最高,净发电量达到4942kW。
LNG接收站工程工艺流程

冲击投加泵
电解海水制取NaClO发生的总反应:N a C l H 2 O N a C lO H 2
16
大连LNG接收站工程工艺流程
浸没燃烧式气化器(SCV)运行流程
17
大连LNG接收站工程工艺流程
计量撬计量系统
18
大连LNG接收站工程工艺流程
4 LNG装车
大连LNG项目共有14台装车撬,国产装车撬4台,
-158.7℃/-161.9℃
最大操作压力: 25 kPaG
正常操作压力: 18kPaG
最小操作压力:
6.9kPaG
进料口直径:
40"
8
大连LNG接收站工程工艺流程
3 LNG气化
LNG储罐内的低压泵将LNG泵送至高压泵;在自然温度大于5摄氏度 时,高压泵将LNG泵送至开架式气化器(ORV)进行气化;在自然温度 低于5摄氏度时,高压泵将LNG泵送至浸没燃烧式气化器(SCV)进行 气化;气化后至计量撬,计量撬计量后通过外输管线外输。
进口装车撬10台。
在槽车灌装LNG 前,先要预冷装车臂和气相返回臂。
在槽车装车过程中,从槽车中置换出来的蒸发气通过管
线返回BOG总管。在装车操作时,LNG装车流量通过控
制阀来控制。
LNG装车相关参数:
装车形式
侧装
装卸能力
80m3/h
操作压力
0.03/0.6MPaG
操作温度
-130℃/-160℃
19
大连LNG接收站工程工艺流程
BOG压缩机再冷凝工艺必须是在具有外输的工作状态 下工作。
卸船结束,卸料臂需要氮气吹扫,然后收回卸料臂。 此期间注意防止卸料臂上积冰脱落伤人。
3
大连LNG接收站工程工艺流程
LNG液化和接收站工艺介绍

Boil Temperature 各构成物质的沸点温度
LNG (Methane, CH4) - 162 o C
Ethane, C2H6
- 88.6 o C
Propane, C3H8
- 42.0 o C
PROCESS-2> 5TH Re-Condenser
再液化工程 Re-Liquefaction Process
天然气开采及精制(Extraction)
天然气是指天然出现的,以碳氢化合物为主成份的, 可燃性燃气.通过地质探查后进行 钻探, 确认埋藏量, 生产性分析, 挖掘等阶段,从地下开采. 天然气成份 : 主成份 Methane Gas (90%) Ethane, Propane, Butane 等以外,还包括高分子碳氢 化合物 (Hydrocarbon), N2, He,一氧化碳 (CO2), 硫化氢 (H2S), 水分 (H2O) 等杂质 当天然气在不分离或除掉以上杂质的情况下直接使用的话,会对发热量及物理化学方面的性质有所 不同,尤其是因为硫磺类物质的影响下引起污染空气. 同时,把这种物质从天然气中分离后,提高天然气的质量,充分利用分离出的物质,将通过如下的分离 及精制过程制作出干净的燃料.
(为了回收 装船过程中所发生的蒸发燃气的设备)
液化天然气运输船 LNG-Carrier
液化天然气(LNG)是处于零下163度的 极低温状态. 在这种温度里放入金鱼时,会瞬 间冻结成S型,拿出后再放入水中时,过不了多久就能复活游动. 以前是因为极 低温材料的问题及600分之 1的浓缩液化天然气会爆炸等危险,只好按气体状 态下进行管道输送.但是,物流及需要方面很有竞争力的 LNG 输送船已经问 世,干燥技术的核心问题,就是防止燃气泄漏及安全问题.
简述lng接收站终端工艺流程
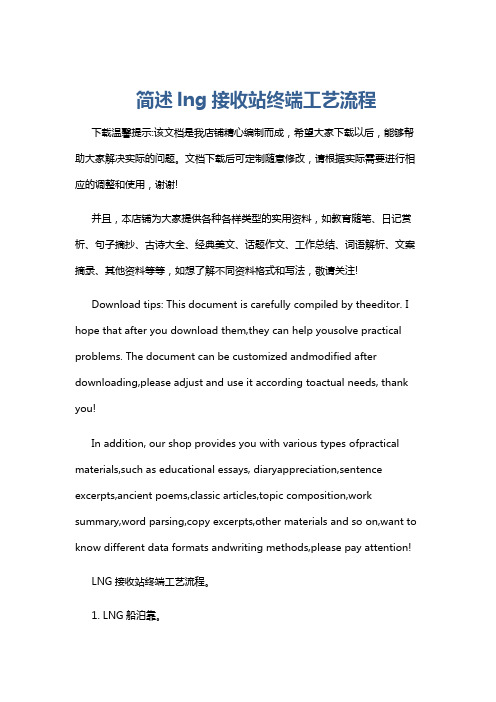
简述lng接收站终端工艺流程下载温馨提示:该文档是我店铺精心编制而成,希望大家下载以后,能够帮助大家解决实际的问题。
文档下载后可定制随意修改,请根据实际需要进行相应的调整和使用,谢谢!并且,本店铺为大家提供各种各样类型的实用资料,如教育随笔、日记赏析、句子摘抄、古诗大全、经典美文、话题作文、工作总结、词语解析、文案摘录、其他资料等等,如想了解不同资料格式和写法,敬请关注!Download tips: This document is carefully compiled by theeditor. I hope that after you download them,they can help yousolve practical problems. The document can be customized andmodified after downloading,please adjust and use it according toactual needs, thank you!In addition, our shop provides you with various types ofpractical materials,such as educational essays, diaryappreciation,sentence excerpts,ancient poems,classic articles,topic composition,work summary,word parsing,copy excerpts,other materials and so on,want to know different data formats andwriting methods,please pay attention!LNG接收站终端工艺流程。
1. LNG船泊靠。
接收站派引航员登船引领LNG船舶安全泊靠。
- 1、下载文档前请自行甄别文档内容的完整性,平台不提供额外的编辑、内容补充、找答案等附加服务。
- 2、"仅部分预览"的文档,不可在线预览部分如存在完整性等问题,可反馈申请退款(可完整预览的文档不适用该条件!)。
- 3、如文档侵犯您的权益,请联系客服反馈,我们会尽快为您处理(人工客服工作时间:9:00-18:30)。
LNG接收站工艺设计介绍第一节 工艺方案的确定一、工艺技术路线选择LNG接收站的主要功能是液化天然气(LNG)接收和储存、蒸发气(BOG)处理、LNG增压、LNG气化、天然气(NG)输出以及LNG的槽车或槽船输出。
LNG接收站的工艺技术路线分为两种:即直接输出工艺和再冷凝工艺。
两种工艺并无本质上的区别,只是在BOG的处理工艺上有所不同。
直接输出工艺是将BOG压缩到外输压力后直接送至输气管网,这需要消耗大量压缩功;而再冷凝工艺则是将蒸发气压缩到某一中间压力,然后与低压输送泵从储罐送出的LNG在再冷凝器中混合。
由于LNG加压后处于过冷状态,可以使BOG冷凝下来,冷凝后的LNG 经高压输出泵加压气化后外输。
直接输出工艺需要消耗大量压缩功,运行费用较高,一般用于外输气压力较低,最小外输量低于冷凝蒸发气需要LNG量的场合;再冷凝工艺不需要将BOG压缩到外输压力,而是压缩到一个较低的压力,然后利用LNG的冷量将BOG冷凝,从而减少了BOG压缩功的消耗,节省能量。
具体采取哪种工艺线路,还需要根据外输气的具体情况来进行综合分析确定。
目前国内已建和在建的大型LNG接收站均采用再冷凝工艺。
二、工艺系统配置LNG接收站工艺过程包含:LNG接卸、LNG储存、BOG回收处理、LNG低压输送、LNG加压气化、NG计量及外输、LNG装车/船等。
按工艺过程进行工艺系统划分如下:1)卸船系统2)LNG储存系统3)BOG处理系统4)LNG增压系统5)LNG气化外输系统6)LNG装车系统三、辅助设施及公用工程系统配置根据LNG接收站主要工艺流程的需要,一般LNG接收站主要配置以下辅助设施及公用工程系统:1)火炬系统2)燃料气系统3)氮气系统4)仪表空气、工厂空气系统5)海水系统6)生产生活用水系统7)消防系统8)废水处理系统9)中央控制室10)码头控制室11)分析化验室12)维修车间及仓库13)变电所四、工艺系统流程概述工艺流程按照工艺系统分别说明:1、卸船系统(1)运输船停泊/连接卸船臂LNG接收站具有专用的接卸码头,其接卸能力满足接收站的要求。
码头设有LNG卸载所需要的工艺和安全设施。
LNG船到岸时,港口操作员与领航员、拖船以及船只停泊监测系统控制运输船靠岸系泊。
在运输船安全系泊并和岸上建立了通信联系后,方可连接LNG卸料臂和气相返回臂。
随后需测试紧急切断系统,并使用氮气置换卸船臂中的空气达到要求,再用船上的LNG冷却运输船的输送管道和LNG卸船臂后再进行卸船作业。
(2)运输船卸载LNG运输船和卸料臂准备就绪后,LNG由运输船上的卸料泵,经过LNG卸船臂,并通过卸船总管输送到LNG储罐中。
为平衡船舱压力,LNG储罐内的部分蒸发气通过气相返回管线、气相返回臂返回LNG船舱中。
如果靠储罐和运输船之间的压差无法将蒸发气压回运输船,那么就需要通过回流鼓风机增压后将蒸发气送回运输船。
一般来讲,LNG卸料臂中有一台臂为气液两用臂。
这样,当气相返回臂发生故障不能使用时,气液两用臂将被用作气相返回臂,此时虽然卸船操作时间会延长,但一方面避免了大型LNG船滞港,另一方面又避免了产生的蒸发气无法回船而造成排放至火炬系统燃烧。
卸船操作时,实际卸船速率和同时接卸LNG储罐数量需根据LNG储罐液位和LNG船型来确定。
每座LNG储罐均设有液位计,可用来监测罐内液位。
卸船管线一般设有固定的取样分析系统,可对管道中的LNG进行在线分析,也可取样进行实验室分析。
卸船时可通过卖方提供的货运单上的LNG组分使LNG合理地通过储罐的顶部或底部进料阀注入储罐中,避免LNG产生分层,从而减少储罐内液体发生翻滚的可能性。
在卸船完成后,LNG运输船脱离前,用氮气从卸船臂顶部进行吹扫,将卸船臂内的LNG分别压送回LNG运输船、LNG卸船管线或LNG码头排净罐(如有),并解脱卸船臂与船的接头。
如果码头设有排净罐,但排净罐检修时,可将卸船臂和卸船管线中的LNG通过排净罐旁路直接排到LNG卸船管线中。
在无卸船操作期间,通过一根从低压输出总管来的冷循环管线以小流量LNG经卸船管线循环,以保持LNG卸船管线处于冷态备用。
冷循环的LNG大部分返回到去再冷凝器的LNG低压输出总管,其余部分通过LNG卸船总管经LNG储罐顶部和底部进料阀的旁路回到各LNG储罐。
2、LNG储存系统目前国内大型LNG接收站的LNG储罐均为全包容式混凝土顶储罐(简称FCCR),储罐的有效工作容积为16×104m3。
全包容式混凝土顶储罐内罐采用9%镍钢,外罐是预应力混凝土材料建成。
储罐的设计压力一般为-0.5kPaG/29kPaG,其环隙空间以及吊顶板都设有保冷层,以确保在设计环境下储罐的日最大蒸发量不超过储罐容量的0.05%。
为防止LNG泄漏,罐内所有的流体进出管道以及所有仪表的接管均从罐体顶部连接。
每座储罐设有2根进料管,既可以从顶部进料,也可以通过罐内插入立式进料管实现底部进料。
进料方式取决于LNG运输船待卸的LNG与储罐内已有LNG的密度差。
若船载LNG 比储罐内LNG密度大,则船载的LNG从储罐顶部进入,反之,船载的LNG从储罐底部进入。
这样可有效防止储罐内LNG出现分层、翻滚现象。
操作员可以通过操控顶部和底部的进料阀来调节LNG从顶部和底部进料的比例。
在LNG进料总管上设置切断阀,可在紧急情况时隔离LNG储罐与进料管线。
LNG储罐通过一根气相管线与蒸发气总管相连,用于输送储罐内产生的蒸发气和卸船期间置换的气体至BOG压缩机、回流鼓风机(如有)及火炬系统。
每座LNG储罐都设有连续的罐内液位、温度和密度监测仪表,以防止罐内LNG发生分层和溢流。
储罐的压力通过BOG压缩机压缩回收储罐内产生的蒸发气进行控制。
LNG储罐一般设有两级超压保护。
如遇到大气压降低较快等工况,压缩机不能及时处理大量的蒸发气时,可通过开启压力控制阀,将BOG气体排放至火炬系统来保护储罐,以防止系统超压,这是储罐的第一级超压保护。
每座储罐还配备数个安全阀,是储罐的第二级超压保护,安全阀的设定压力为储罐的设计压力,超压气体通过安装在罐顶的安全阀直接排入大气。
LNG储罐一般设有两级真空保护。
由于大气压快速增加导致储罐压力较低时,来自外输天然气总管的天然气通过破真空阀输送至LNG储罐,维持储罐内压力稳定,这是一级真空保护。
如果补充的破真空气体不足以维持储罐的压力在正常操作范围内,空气通过安装在储罐上的真空安全阀进入罐内,维持储罐压力正常,保证储罐安全。
低压外输管线设有混合管线,可以使单座罐内的LNG循环混合。
在储罐的内部空间和环隙空间设置氮气管线,可以干燥、吹扫以及惰化储罐。
储罐内顶部设有环状喷嘴,与卸船管线相连,用于LNG储罐的初次预冷。
3、蒸发气处理系统(1)蒸发气压缩处理蒸发气的产生主要是由于能量的输入造成,如泵运转电机发热、外界热量的传入、环境的影响等,另外大气压变化、LNG送入储罐时造成罐内蒸发气体积的变化也是蒸发气产生的原因。
蒸发气处理系统的目的是为了经济而有效地回收LNG接收站产生的蒸发气。
LNG接收站在卸船操作时产生的蒸发气的量远远大于不卸船操作的蒸发气量。
卸船时产生大量蒸发气,其中一部分蒸发气通过气相返回管线,经气相返回臂返回LNG船舱中,以保持卸船系统的压力平衡。
另一部分经BOG压缩机压缩到一定的压力后在再冷凝器中冷凝。
BOG压缩机采用低温压缩机,可通过负荷调节来实现流量控制。
BOG压缩机的开车/停车由操作员控制。
如果BOG流量高于压缩机或再冷凝器的处理能力,储罐和蒸发气总管的压力将升高,当压力超过压力控制阀的设定值时,过量的蒸发气将排至火炬燃烧。
卸船时,蒸发气量是不卸船时的数倍,需要所有压缩机同时工作。
一旦1台BOG压缩机出现故障,为了确保卸船时产生蒸发气能得到有效处理,可适当降低卸船速率以避免或减少蒸发气排至火炬燃烧。
BOG压缩机入口设缓冲罐,防止蒸发气夹带液滴进入压缩机。
(2)再冷凝器再冷凝器将BOG压缩机增压后的蒸发气与LNG 混合并将蒸发气冷凝为液体。
再冷凝器内填充不锈钢拉西环。
蒸发气与LNG在填充床中混合并实现冷凝。
根据再冷凝器出口压力和来自压缩机的BOG流量来调节进入再冷凝器的LNG /BOG流量比例,以确保蒸发气冷凝为液体。
4、LNG增压系统储罐内的LNG经低压输送泵一部分进入再冷凝器冷凝,另一部分直接进入高压输出泵,通过高压泵加压达到外输所需的压力,而后进入气化设备。
(1)低压输送泵低压输送泵为立式潜液泵,安装在储罐的泵井中。
低压输送泵均为定速运行,其运行流量由天然气外输量、装车/船量及保冷循环量等确定。
每台低压输送泵的出口管线上均设有最小流量调节阀,以保护泵的运行安全。
每座储罐的低压出口总管上设有紧急切断阀,既可用于隔离低压输送泵与LNG低压外输总管,又可在紧急情况时使储罐与低压LNG 外输总管隔离,同时可用于低压输送泵或低压LNG外输管线的检修操作。
(2)高压输出泵高压输出泵采用立式、电动、恒定转速离心泵,安装在专用的立式泵罐内。
高压输出泵的输出流量通过设在气化器入口管线的流量调节阀进行控制。
每台泵的进、出口管线均设有切断阀,以便于泵的切换和紧急情况下的切断隔离。
高压输出泵的出口设有最小流量控制阀以保证泵的安全运行。
5、LNG气化外输系统(1)气化器大型接收站比较常用的气化器有开架式气化器(ORV)、浸没燃烧式气化器(SCV)、中间介质气化器(IFV)等。
ORV使用海水作为气化LNG的热媒,SCV则以天然气作为热媒,IFV则除了海水还需要中间介质作为热媒。
一般接收站首选ORV作为气化器,但海水条件不能满足要求时,需要选择SCV或IFV来代替ORV或采用ORV+SCV的联合方案。
在气化器的入口设有流量调节阀,用以调节接收站的外输天然气输出量,并控制气化器出口天然气的温度和天然气输出总管的压力。
气化器的运行台数和运行流量由下游用户用气量确定。
当外输气体出口温度过低时,可通过气化器外输系统温度控制,减小入口LNG流量。
每台气化器还设有安全阀,超压时可将过量的气体就地排放至安全地点或排放至火炬。
(2)分析计量系统天然气外输总管上设有分析计量系统,用来分析外输天然气的热值、组分,同时实现接收站的外输贸易计量,重要的数据需要上传至外输管网的SCADA系统。
6、LNG装车系统LNG由LNG接收站低压输送进入槽车输送总管,后经各装车站支管和槽车装车臂进入LNG 槽车,装车流量由槽车控制室和就地控制完成。
槽车中的气相通过气相返回臂返回至槽车回气总管,然后接入BOG总管返回至LNG接收站。
在槽车输送总管末端设置冷循环管线,通过控制循环流量,保持槽车输送总管处于冷态。
可根据管线上的表面温度计的温升情况调节冷循环流量。
每次装车完成后,各装车位吹扫残液(气)和置换气排放进入LNG收集罐(如有)。