浅谈微细加工技术
微细加工技术在微电子器件制备中的应用研究

微细加工技术在微电子器件制备中的应用研究微电子器件制备是当今电子技术领域的热点研究方向之一。
微电子器件制备的核心就是微细加工技术,该技术主要以光刻、薄膜沉积、化学加工、离子注入、蚀刻等为基础。
这些微细加工技术在微电子制备中发挥着不可替代的作用,是现代信息和通信技术、计算机技术、医学和生物技术等方面的关键技术。
下面我们将从几个方面来探讨微细加工技术在微电子器件制备中的应用研究。
一、微电子器件制备的重要性微电子器件制备一直是电子技术领域的研究热点,已广泛应用于计算机、手机、数字化电视等高科技领域。
目前,在自动化控制、靶向治疗、生物芯片、智能传感等领域都有了广泛应用。
国家也将微电子产业作为发展战略,积极发展集成电路、显示器、微处理器等产业。
因此,微电子器件制备将在未来的高科技发展中扮演着越来越重要的角色。
二、微细加工技术的分类及应用1. 光刻技术:光刻技术是微细加工技术中的重要一环。
它的原理是将光照射到光刻胶上,形成图案,再通过蚀刻或其他化学反应形成图案,用于制作晶体管、太阳能电池、光子晶体器件等。
2. 薄膜沉积技术:薄膜沉积技术也是微电子器件制备中应用广泛的技术。
它主要包括化学气相沉积、物理气相沉积、电化学沉积等技术。
薄膜沉积技术的主要应用领域是微电子器件中的互连线的分离层等。
3. 化学加工技术:化学加工技术是用化学方法对微电子材料进行处理,以制备出微电子器件。
在化学加工技术中,蚀刻技术是最为常见的一种技术。
蚀刻技术主要是通过酸、碱等化学物质对材料进行腐蚀、溶解或者氧化等,然后按要求形成器件。
4. 离子注入技术:离子注入技术主要是将离子注入到半导体材料中去,以改变其电学性质和物理特性,进而形成微电子器件。
三、微细加工技术的研究方向1. 多维度控制技术在微电子器件制备中,需要对于个别的材料可实现严格的调控,比如要求薄膜良率高、晶圆表面平整度高等等。
因此,为提高整个加工过程的可控性,就要求多维度控制技术的发展,实现对于加工过程中每一环节的精细控制,比如对于温度、光照强度、反应时间等方面的控制。
微细加工技术

微细加工技术的概念:微细加工技术是一种
新的集光刻、电铸和模铸于一体的复合微细 加工技术。
主讲人:
班 级:
学 号;
一、微细加工技术的简介 二、微细加工的特点 三、加工方法及其特点 四、微细加工的发展 五、微细加工发展的前景
微细加工技术简介
微细加工技术是精密加工技术的一个分支,面向微细加工的 电加工技术,激光微孔加工、水射流微细切割技术微细加工技 术应满足下列功能: 1)为达到很小的单位去除率(UR),需要各轴能实现足够 小的微量移动,对于微细的机械加工和电加工工艺,微量移 动应可小至几十个纳米,电加工的UR最小极限取决于脉冲 放电的能量。 2)高灵敏的伺服进给系统,它要求低摩擦的传动系统和导 轨主承系统以及高精度跟踪性能的伺服系。 3)高平稳性的进给运动,尽量减少由于制造和装配误差引 起的各轴的运动误差。 4)高的定位精度和重复定位精度。 5)低热变形结构设计。 6)刀具的稳固夹持和高的重复夹持精度。 7)高的主轴转速及极低的动不平衡。 8)稳固的床身构件并隔绝外界的振动干扰。 9)具有刀具破损和微型钻头折断的敏感的监控系统。
微细加工发展前景
如果进入微观世界,能够捕获一个或多个单原子,然后 让它们重新排列组合,那么就会导致物质本身发生某些 变化,而这些变化将会对未来许多领域,及人类生活产 生巨大影响。例如,我们把组成水分子的氢和氧分开, 二者都是可以燃烧的。小的分子,只有足球体积的几亿 分之一,用机械方法,几乎是不可能捉住它,分子又是 由原子组成的,操纵一个原子,就更难了,而光可以做 到这一点。一束极细的激光,产生光子流,其动量转移 给物体,形成光压,再通过适当的光场分布,可以把那 种极小的原子俘获在一定的位置,并可方便把移动它。 实际上这就实现了对原子的操作。
微细加工工艺技术

微细加工工艺技术微细加工工艺技术是一种应用于微电子、光学、纳米学等领域的高精度加工技术,该技术能够实现对微细结构的精密加工。
在微细加工工艺技术中,常常采用的加工方法有激光刻蚀、化学蚀刻、光刻以及微电子束等。
激光刻蚀是一种应用激光照射,通过激光束的高能量将材料表面局部蚀刻的加工方法。
与传统的机械刻蚀相比,激光刻蚀具有高精度、高效率的优点。
在激光刻蚀中,光束的聚焦度和光斑直径是影响加工精度的重要参数。
化学蚀刻是一种利用特定的化学反应,在材料表面选择性地产生化学蚀刻产物,并将其去除的加工方法。
化学蚀刻通常需要制备特定的蚀刻溶液,通过控制溶液的浓度和温度,来影响化学反应的速率和选择性。
化学蚀刻可以实现微细结构的高精度加工,并被广泛应用于光学元件和微流控芯片等领域。
光刻是一种基于光化学反应的加工方法,通过光阻的选择性暴露和去除,来形成所需的图案结构。
在光刻过程中,首先在材料表面涂敷一层光刻胶,然后利用光刻机的紫外光照射和显影等步骤,实现图案的转移。
光刻具有高精度、高分辨率和高重复性的优点,是微细加工中不可或缺的工艺之一。
微电子束也是一种实现微细结构加工的重要方法。
微电子束利用高能电子束在材料表面定向照射,经过准直、聚焦和偏转等步骤,将电子束的能量转化为对材料的加工作用。
通过控制电子束的参数,如能量、聚焦度和扫描速度等,可以实现对微细结构的精密加工。
微电子束在高精度加工领域具有很大的应用潜力,尤其在微电子器件、光电器件以及半导体器件等方面,具有广阔的发展前景。
总的来说,微细加工工艺技术是一种实现高精度加工的重要方法,包括激光刻蚀、化学蚀刻、光刻和微电子束等。
这些加工方法在微电子、光学、纳米学等领域发挥着重要作用,推动了相关技术的进步和应用的发展。
未来随着科学技术的不断进步,微细加工工艺技术将继续发展壮大,为人类社会带来更多的科技成果和应用产品。
微细加工技术在机械制造中的应用研究
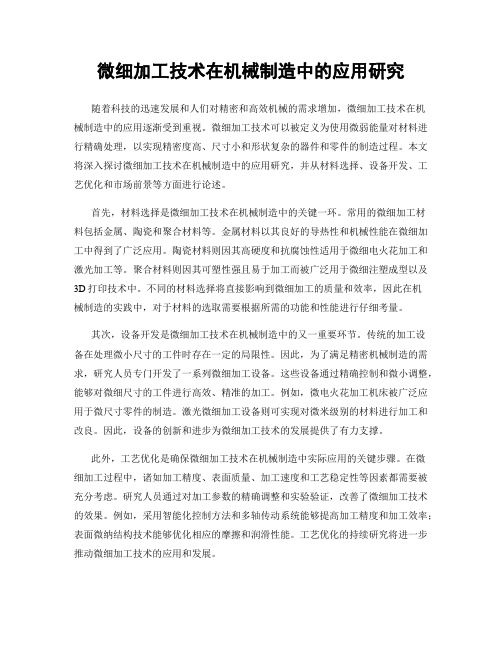
微细加工技术在机械制造中的应用研究随着科技的迅速发展和人们对精密和高效机械的需求增加,微细加工技术在机械制造中的应用逐渐受到重视。
微细加工技术可以被定义为使用微弱能量对材料进行精确处理,以实现精密度高、尺寸小和形状复杂的器件和零件的制造过程。
本文将深入探讨微细加工技术在机械制造中的应用研究,并从材料选择、设备开发、工艺优化和市场前景等方面进行论述。
首先,材料选择是微细加工技术在机械制造中的关键一环。
常用的微细加工材料包括金属、陶瓷和聚合材料等。
金属材料以其良好的导热性和机械性能在微细加工中得到了广泛应用。
陶瓷材料则因其高硬度和抗腐蚀性适用于微细电火花加工和激光加工等。
聚合材料则因其可塑性强且易于加工而被广泛用于微细注塑成型以及3D打印技术中。
不同的材料选择将直接影响到微细加工的质量和效率,因此在机械制造的实践中,对于材料的选取需要根据所需的功能和性能进行仔细考量。
其次,设备开发是微细加工技术在机械制造中的又一重要环节。
传统的加工设备在处理微小尺寸的工件时存在一定的局限性。
因此,为了满足精密机械制造的需求,研究人员专门开发了一系列微细加工设备。
这些设备通过精确控制和微小调整,能够对微细尺寸的工件进行高效、精准的加工。
例如,微电火花加工机床被广泛应用于微尺寸零件的制造。
激光微细加工设备则可实现对微米级别的材料进行加工和改良。
因此,设备的创新和进步为微细加工技术的发展提供了有力支撑。
此外,工艺优化是确保微细加工技术在机械制造中实际应用的关键步骤。
在微细加工过程中,诸如加工精度、表面质量、加工速度和工艺稳定性等因素都需要被充分考虑。
研究人员通过对加工参数的精确调整和实验验证,改善了微细加工技术的效果。
例如,采用智能化控制方法和多轴传动系统能够提高加工精度和加工效率;表面微纳结构技术能够优化相应的摩擦和润滑性能。
工艺优化的持续研究将进一步推动微细加工技术的应用和发展。
最后,微细加工技术在机械制造中的市场前景不容小觑。
微细加工技术的研究与应用
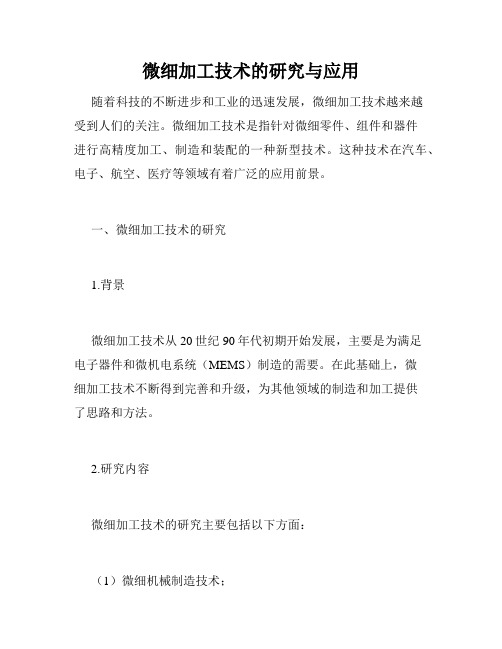
微细加工技术的研究与应用随着科技的不断进步和工业的迅速发展,微细加工技术越来越受到人们的关注。
微细加工技术是指针对微细零件、组件和器件进行高精度加工、制造和装配的一种新型技术。
这种技术在汽车、电子、航空、医疗等领域有着广泛的应用前景。
一、微细加工技术的研究1.背景微细加工技术从20世纪90年代初期开始发展,主要是为满足电子器件和微机电系统(MEMS)制造的需要。
在此基础上,微细加工技术不断得到完善和升级,为其他领域的制造和加工提供了思路和方法。
2.研究内容微细加工技术的研究主要包括以下方面:(1)微细机械制造技术;(2)微细电子制造技术;(3)微细光学制造技术;(4)微细生物制造技术。
其中,微细机械制造技术是应用最为广泛的一项技术,主要针对微型零部件、机械组件和器件等进行加工和制造。
3.研究难点微细加工技术的研究面临着许多难点,其中最主要的难点是如何实现高精度加工。
微细零部件的尺寸通常都在数微米至数百微米之间,而传统加工技术所能达到的精度却远远不够。
因此,如何在微小尺度下进行高精度加工,是微细加工技术研究的核心问题。
二、微细加工技术的应用1.汽车制造领域汽车制造领域是微细加工技术应用的主要领域之一。
在汽车制造中,许多零部件的尺寸都很小,而且对加工精度要求很高。
例如,发动机的火花塞、气门、燃油喷嘴等部件;车身的紧固件、密封件和缝合件等,都需要采用微细加工技术进行加工和制造。
2.电子制造领域电子制造领域也是微细加工技术应用的重要领域之一。
在电子制造中,许多IC芯片、闪存和存储器等器件的结构都非常微小,需要采用微细加工技术进行精密加工和制造。
同时,电子制造领域还需要采用微细加工技术进行导电薄膜的制造、微型电极的加工等工作。
3.医疗领域医疗领域也是微细加工技术应用的一个新兴领域。
在医疗领域中,微细加工技术可以用于制造微型手术器械、医用传感器、微型分析芯片等器件,从而为医疗诊断和治疗提供了新的手段和方法。
细微加工的特点及应用

细微加工的特点及应用细微加工是指通过采用精密的工艺和设备对原材料进行微小尺寸的加工处理的过程。
其特点包括:1. 高精度:细微加工需要达到高精度的要求,可以控制在微米甚至纳米级别。
这是通过使用高精密设备、工艺和精密测量工具来实现的。
2. 微小尺寸:细微加工的加工尺寸通常在微米或更小的范围内,需要对零件、工具和加工过程进行精确控制,以确保有效的加工完成。
3. 表面质量高:细微加工可以实现对零件表面的高质量加工。
通过控制工艺参数和使用合适的刀具,可以获得光滑、均匀的表面。
4. 加工效率低:细微加工通常需要更多的时间和努力来完成同样数量的零件。
这是由于加工尺寸小、精度高的特点所决定的。
细微加工具有广泛的应用领域,包括但不限于以下几个方面:1. 光电子学:在光电子学中,细微加工可以用于制造光学元件、微型激光器和光纤等。
通过精确的加工控制,可以获得高精度的光学元件,用于光纤通信、光栅测量等领域。
2. 微电子学:细微加工在微电子学领域中有着重要的应用。
通过细微加工,可以制造出微小的芯片、集成电路和导电薄膜等。
这些微小电子元件在电子产品和计算机中起着关键作用。
3. 生物医学:细微加工在生物医学领域中也有广泛的应用。
通过细微加工,可以制造出微型生物芯片、显微探针和微型手术工具等。
这些微小的生物医学器件可以实现快速、准确和无创的生物分析和治疗。
4. 纳米技术:细微加工在纳米技术领域也有重要的应用。
通过细微加工,可以制造出纳米级别的结构、纳米线和纳米颗粒等。
这些纳米材料可以应用于催化剂、传感器和纳米电子器件等领域。
5. 其他领域:细微加工还可以应用于其他领域,例如精密机械制造、航空航天、汽车制造和光学仪器制造等。
在这些领域中,细微加工可以帮助提高产品的精度、性能和可靠性。
总之,细微加工以其高精度、微小尺寸和优质表面的特点,在光电子学、微电子学、生物医学、纳米技术和其他领域中发挥着重要的作用。
随着工艺和设备的不断发展,细微加工将在更多领域中得到广泛应用,为人类创造更多的可能性。
精密制造中微细加工技术研究

精密制造中微细加工技术研究近年来,随着科学技术的快速发展,精密制造行业也迎来了快速的发展。
微细加工技术就是其中一个重要的研究领域,具有广泛的应用前景和潜力。
本文将对精密制造中微细加工技术的研究进展进行探讨。
一、微细加工技术的概念微细加工技术是指对工件进行微米级别的加工或制造的技术。
它基于微观尺度下的材料物理学和加工理论,使用精密的加工设备对材料进行微弱的处理,使其得到精确的结构和性能。
微细加工技术的主要应用领域是微电子、光学、生物医学等高科技领域。
比如微电子领域的芯片加工、光刻和光刻补偿;生物医学领域的人体组织样本制备和高分辨率成像等。
二、微细加工技术的分类微细加工技术可以根据加工方法和过程参数的不同进行分类。
主要分为机械加工、电化学加工、激光加工、等离子体加工和光电子束加工等。
1、机械加工机械加工是指使用刀具对工件上的材料进行切削、精加工、磨削等处理。
它包括车床加工、数控机床加工、线切割等。
机械加工的优点是加工速度快、成本低,但难以达到亚微米级别的精度。
2、电化学加工电化学加工是指使用电化学反应进行加工的一种技术。
它包括电解加工、电化学抛光和电化学蚀刻等。
其中,电化学蚀刻技术是最常用的电化学加工技术之一,它对高硬度材料和形状复杂工件具有良好的加工效果。
3、激光加工激光加工是指使用高能量激光对工件进行加热、熔化和蒸发等处理。
它包括激光切割、激光打孔、激光焊接等。
激光加工的优点是能够实现高速度、高精度和高质量的加工,但过程中容易产生热应力和材料变形。
4、等离子体加工等离子体加工是指通过等离子体弧放电加工材料的技术。
它包括等离子体切割、等离子体熔覆和等离子体表面处理等。
等离子体加工的优点是可加工高硬度和高熔点材料,并能够实现高质量的加工表面。
5、光电子束加工光电子束加工是指使用电子束或质子束对工件进行加工的一种技术。
它包括电子束切割、电子束焊接和电子束表面处理等。
光电子束加工的优点是能够实现高精度和高质量的加工,并可以加工高硬度和高熔点材料。
应用于光学和激光器的微细加工技术

应用于光学和激光器的微细加工技术微细加工技术是一种可制备微小结构和精密设备的技术,它被广泛应用于光学和激光器领域。
在这个领域中,微细加工技术可以用于制造微透镜、微结构和微电子机械系统等高精度零部件。
本文将介绍微细加工技术在光学和激光器领域的应用以及其中的一些技术细节。
一、微细加工技术在光学领域的应用光学元件是指能够调节或控制题目光波传输的元件,它们对于光学系统的性能至关重要。
在光学元件的制造中,微细加工技术可以用于制造微透镜、微透镜阵列、微凹凸面和微结构等。
这些微小的结构对于控制题目光波传输起着重要的作用。
(一)微透镜及其阵列微透镜是一种非常小的凹透镜,它可以制镶在芯片表面,使光线通过微透镜后汇聚,去掉散射问题,提高光学器件的分辨率。
而微透镜阵列由多个微透镜组成,可以对一块芯片进行大规模的光学加工,加工效率高,制造精度高,批量化生产。
微细加工技术可以用于制造微透镜和微透镜阵列,提高光学器件的性能和制造效率。
(二)微凹凸面和微结构微凹凸面可以用于光学器件的纹理处理和表面增强拉曼光谱技术。
微凹凸面和微结构可以通过微细加工技术进行制造。
二、微细加工技术在激光器领域的应用激光器是光学器件中的重要一环,其工作原理是利用各种物质(包括气体、晶体、半导体和液体等)在外部刺激下产生的放电、激发或光学相互作用,从而产生一束有特定波长、特定方向和相干的光。
微细加工技术在激光器的制造和调整中具有广泛的应用。
(一)激光器的制造微细加工技术可以用于激光器的零部件加工和装配。
例如,使用 Micro Electro Mechanical Systems(MEMS)技术可以制造激光器的振荡器,而微细加工技术中的纳米制造技术可用于制造激光器的金属反射镜。
(二)激光器的调整激光器的调整是指在制造完成后对其进行调整和改进以达到特定的性能指标。
微细加工技术可以对激光器进行微调,例如利用微镜或微齿轮结构来调节激光器内的折射率和驱动电压等参数以改进激光器的性能。
微细加工技术

MEMS是Micro Electro Mechanical Systems的缩写。即 微机电系统,它是在微电子技术的基础上发展起来的,融合 了硅微加工、LIGA技术和精密机械加工等多种微加工技术, 并应用现代信息技术构成的微型系统。它包括感知和控制外 界信息(力、热、光、生、磁、化等)的传感器和执行器,以 及进行信号处理和控制的电路。 它是指可以批量制作的集微型机构、微型传感器、微型 执行器以及信号处理和控制电路、甚至外围接口、通信电路 和电源等一体的微型器件或系统,其特征尺寸范围为1nm~ 10mm 美国:MEMS—Micro Electro-Mehanical System 欧洲:Micro System 日本:Micro Machine 其它:Micro & Nano 技术
SLA(立体光刻)工艺
液槽中盛满液态光固化树脂, 激光束在偏转镜作用下,能在液态 表面上扫描,扫描的轨迹及光线的 有无均由计算机控制,光点打到的 地方,液体就固化。当一层扫描完 成后,未被照射的地方仍是液态树 脂。然后升降台带动平台下降一层 高度,已成型的层面上又布满一层 树脂,刮平器将粘度较大的树脂液 面刮平,然后再进行下二层的扫描, 新固化的一层牢固地粘在前一层上, 如此重复直到整个零件制造完毕, 得 到 一 个 三 维 实 体 模 型 。
1.4 微制造中的材料去除技术
LIGA由 深层 同 步 X射线 光刻、电铸成形、塑注成形 组合而成。包括三个主要工 序(图1-4): 1)以同步加速器放射的短 波长(<1nm)X射线作为 曝光光源,在厚度达0.5mm 的光致抗蚀剂上生成曝光图 形的三维实体; 2)用曝光蚀刻图形实体作 电铸模具,生成铸型; 3)以生成的铸型作为模具, 加工出所需微型零件。
1.2 微细加工的发展历程
微细加工技术的发展与应用

微细加工技术的发展与应用随着科技的不断发展,微细加工技术成为现代工业中不可或缺的一部分。
微细加工技术是指对微小物体进行加工的技术,通常用于制造那些需要高精度或者微小尺寸的零件、设备和器件。
微细加工技术的应用范围非常广泛,包括微型机器人、光学器件、医疗器械、生物传感器等领域。
本文将探讨微细加工技术的发展历程、应用和未来发展趋势。
一、微细加工技术的发展历程微细加工技术源远流长。
在过去的几百年间,人们使用了各种手工工具和机械设备进行微细加工。
例如,19世纪英国人约瑟夫·温斯洛在1822年发明了摆线拖动齿轮切削机,实现了金属齿轮的精细加工。
这一技术被广泛应用于英国的纺织工业,并为工业革命的发展做出了贡献。
20世纪初,随着电气工程和电子学的发展,半导体器件的出现推动了微细加工技术的发展。
1947年,贝尔实验室的威廉·肖克利发明了第一个晶体管,奠定了现代电子工业的基础。
从此以后,微细加工技术得到了巨大的发展,出现了各种各样的微细加工工具和设备。
例如,扫描电子显微镜可以对微小物体进行高分辨率成像和表征,电子束光刻机可以用来制造半导体芯片、具有纳米尺度精度的纳米定位台可以用来进行精细的纳米加工等等。
二、微细加工技术的应用微细加工技术已经广泛应用于多个领域。
以下是一些例子:1. 光学器件光学器件包括激光器、光开关、波导器、光电探测器等。
微细加工技术可以提供高精度和可重复加工,适用于制造这些器件的需求。
例如,电子束光刻机已经被广泛应用于制造半导体激光器和光子晶体器件。
2. 医学器械微细加工技术可以用于制造医学器械,例如微型手术器械和医用传感器。
这些器械需要高精度和微小尺寸,以减少对患者的创伤和疼痛。
微细加工技术可以提供这些要求。
3. 生物传感器生物传感器利用生物体内的化学反应或者生物特性来检测生物分子和细胞。
微细加工技术可以用于制造这些传感器。
例如,电子束光刻机可以用来制造生物芯片,这些芯片可以用于生命科学研究和医学诊断。
综述微细加工的主要技术和特点

综述微细加工的主要技术和特点一、微细加工近几年展望21世纪,人类进入微观世界。
在原子分子尺度上,对物质进行操作和加工,无疑会展现出一种相当美好的前景,并引起各方面的广泛重视。
微细加工技术的产生和发展一方面是加工技术自身发展的必然,同时也是新兴的微型机械技术发展对加工技术需求的促进。
超精加工在20世纪的科技发展中做出了巨大的贡献。
东京工业大学的谷口纪男教授首先提出了纳米技术术语,明确提出以纳米精度为超精密加工的奋斗目标。
在超精密加工技术领域起步最早和技术领先的国家是美国,其次是日本和欧洲的一些国家。
美国超精密加工技术的发展得到了政府和军方的财政支持,近年,美国执行了"微米和纳米级技术"国家关键技术计划,国防部陆、海、空三军组成了特别委员会,统一协调研究工作。
美国至少有30多个厂家和研究单位研制和生产各种超精密加工机床,国家劳伦斯.利佛摩尔实验室、联合碳化物公司、摩尔公司、杜邦公司等在国际上均久负盛名。
美国最早研制了能加工硬脆材料的6轴数控超精密研磨抛光机;联合碳化物公司开发了直径为800mm的非球面光学零件的超精密加工机床;劳伦斯.利佛摩尔实验室还开发了能加工陶瓷、硬质合金、玻璃和塑料等难加工材料的超精密切削机床,在半导体工业、航空工业和医疗器械工业中投入使用;珀金-埃尔默等公司用超精密加工技术加工各种军用红外零部件。
日本对超精密技术的发展也十分重视,70年代初,日本成立了超精密加工技术委员会,制定了技术发展规划,成为此项技术发展速度最快的国家。
日本现有20多家超精密加工机床研制公司,重点开发民用产品所需的加工设备并力图使设备系列化,成批生产了多品种商品化的超精密加工机床。
在超精密切削技术发展比较成熟后,日本已将黑色金属、陶瓷和半导体功能材料的超精密加工技术作为重要的研究开发项目。
日本的研究创新意识强,不是单纯地模仿国外的做法,而是积极地利用外国技术并结合本国特点和生存环境,走出了一条自己的发展道路。
机械加工中的微细加工技术研究
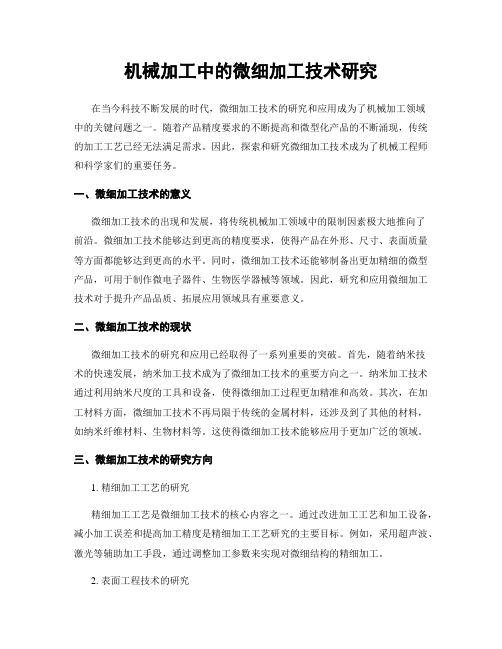
机械加工中的微细加工技术研究在当今科技不断发展的时代,微细加工技术的研究和应用成为了机械加工领域中的关键问题之一。
随着产品精度要求的不断提高和微型化产品的不断涌现,传统的加工工艺已经无法满足需求。
因此,探索和研究微细加工技术成为了机械工程师和科学家们的重要任务。
一、微细加工技术的意义微细加工技术的出现和发展,将传统机械加工领域中的限制因素极大地推向了前沿。
微细加工技术能够达到更高的精度要求,使得产品在外形、尺寸、表面质量等方面都能够达到更高的水平。
同时,微细加工技术还能够制备出更加精细的微型产品,可用于制作微电子器件、生物医学器械等领域。
因此,研究和应用微细加工技术对于提升产品品质、拓展应用领域具有重要意义。
二、微细加工技术的现状微细加工技术的研究和应用已经取得了一系列重要的突破。
首先,随着纳米技术的快速发展,纳米加工技术成为了微细加工技术的重要方向之一。
纳米加工技术通过利用纳米尺度的工具和设备,使得微细加工过程更加精准和高效。
其次,在加工材料方面,微细加工技术不再局限于传统的金属材料,还涉及到了其他的材料,如纳米纤维材料、生物材料等。
这使得微细加工技术能够应用于更加广泛的领域。
三、微细加工技术的研究方向1. 精细加工工艺的研究精细加工工艺是微细加工技术的核心内容之一。
通过改进加工工艺和加工设备,减小加工误差和提高加工精度是精细加工工艺研究的主要目标。
例如,采用超声波、激光等辅助加工手段,通过调整加工参数来实现对微细结构的精细加工。
2. 表面工程技术的研究微细加工技术中,表面工程技术是一个重要的研究方向。
通过对加工表面进行处理,改善表面质量和性能,提高其耐磨、耐腐蚀等特性。
例如,通过纳米材料涂层、等离子体注入等方法来实现对加工表面的改良。
3. 仿生加工技术的研究仿生加工技术是近年来兴起的一个新兴研究领域。
通过借鉴生物界中的微细加工原理,如植物细胞分裂、生物矿化等,来实现对微细结构的加工。
这种仿生加工技术具有极大的潜力和应用前景。
微细加工技术

微细加工技术佚名【期刊名称】《机械工程师》【年(卷),期】2001(000)001【摘要】微细加工原指加工尺度约在微米级范围的加工方法。
在微机械研究领域中,微细加工是微米级精细加工、亚微米级微细加工、纳米级微细加工的通称。
广义上的微细加工,其方式十分丰富,几乎涉及现代特种加工、高能束加工等方式。
而微机械制造过程又往往是多种加工方式的组合。
rn 从基本加工类型看,微细加工可大致分四类:分离加工;接合加工;变形加工;材料处理或改性和热处理或表面改性等。
微细加工技术曾广泛用于大规模集成电路的加工制作,正是借助于微细加工技术才使得众多的微电子器件及相关技术和产业蓬勃兴起。
目前微细加工技术已逐渐被赋予更广泛的内容和更高的要求。
微细加工技术已在特种新型器件、电子零件和电子装置、机械零件和装置、表面分析、材料改性等方面发rn挥日益重要的作用,特别是微机械研究和制作方面,微细加工技术已成为必不可少的基本环节。
【总页数】1页(P54)【正文语种】中文【中图分类】TH16【相关文献】1.复杂微细形状高技术模具的高速、高品位微细电火花加工技术的开发 [J], 桥川荣二;宇野義幸;冈田三郎;里本正纯;中村祥司2.复杂三维微细加工技术创新与研究 [J], 曾增权;冯洪华;张鑫3.超声辅助等离子体中微细电火花加工技术研究 [J], 张从阳;邹日貌;余祖元4.厚镍板的微细电解线切割加工技术研究 [J], 许银海; 于洽; 贺潮淼; 吴帆5.水辅助激光微细加工技术进展 [J], 郭兵;刘文超;赵清亮;SATA Habib;AMR Monier因版权原因,仅展示原文概要,查看原文内容请购买。
微细加工技术在电子行业中的应用

微细加工技术在电子行业中的应用随着时代的进步和科技的发展,人们对电子设备的需求越来越高,使得电子行业得到了长足的发展。
而微细加工技术正是推动电子行业发展的重要力量之一。
什么是微细加工技术?微细加工技术是指通过各种生产加工技术和设备,对微小物体(如纳米级别的材料和器件)进行制造、加工、修补和检测的技术。
它的出现和发展可以追溯到上个世纪50年代初期,随着微电子学的兴起,这项技术也得到了快速的发展。
微细加工技术不仅能够制造出微型化的电子器件,而且可以使器件的尺寸更小、性能更强,从而提高其在各种应用场景中的竞争力。
现在,微细加工技术在电子行业中已经是不可或缺的一环。
1.晶圆加工晶圆加工是指将硅晶圆上的器件进行加工、制造和测试的过程。
在微细加工技术的帮助下,制造出来的晶圆制品可以更小、更精准,对于半导体行业来说能够使得生产成本更低、生产效率更高,并且器件的性能和可靠性更好。
2.光学元件制造现代的电子设备中很少能够不使用到光学元件,如LED、LCD以及激光器等。
微细加工技术可以制造出光学元件,使得这些设备的尺寸更小、成本更低,并且拥有更高的性能和效率。
3.微型电子元件制造微型电子元件是微细加工技术在电子行业中最常见的应用之一。
通过微细加工技术,可以制造出微型的内存条、存储器、微处理器等电子元件,这些微型设备在大量使用的情况下,具备更高的耐用性、性能优势和长期稳定性。
4.纳米技术纳米技术是一种微细加工技术的分支领域,它使得电子产品的尺寸达到了纳米级别。
对于纳米级别的制造、加工和检测,要求工艺控制能力越强、尺寸精度越高。
利用纳米技术,可以制造出更加精细的电子器件,具有优异的性能表现和更长久的耐久性。
微细加工技术在电子行业中的优势1.精度性高微细加工技术可以将设备的尺寸达到纳米级别,相较于常规生产设备,精度性大大提高。
2.高可靠性微细加工技术制造出来的设备具有更高的性能表现,同时也拥有更长久的耐久性,这使得它们在实际使用中具有更高的可靠性。
机械加工中的微细加工技术研究

机械加工中的微细加工技术研究近年来,随着科技的不断发展,各行各业对机械加工的需求也越来越高。
然而,一些特殊材料的加工却成为了工程师们面临的难题。
微细加工技术的引入,为这一难题提供了新的解决途径。
微细加工技术是指在机械加工中,对细小尺寸或特殊材料进行精细加工的方法和技巧。
它在半导体、生物医学、微电子等领域中起着重要作用。
该技术的研究不仅能满足高新技术对微细加工工艺的需求,还能探索更深入的材料研究。
首先,我将介绍微细加工技术在半导体领域的应用。
在半导体制造过程中,需要对晶圆进行微细加工,以形成细小的电子元件。
传统的机械加工方法往往无法满足精度要求,而微细加工技术通过激光加工、等离子体刻蚀等手段,能够实现微米级的定位和加工。
这不仅提高了生产效率,还保证了产品的质量。
其次,微细加工技术在生物医学领域也得到了广泛的应用。
在生物医学研究中,常常需要对细胞进行精确的切割和操纵。
传统的手工操作难以实现,而微细加工技术则能够利用微操纵器械对细胞进行精细操作。
例如,通过纳米级的切割技术,可以实现细菌细胞的单个分离,进而进行更深入的研究和分析。
此外,微细加工技术在微电子领域的应用也日益增多。
随着电子器件的不断小型化,对零部件的精细加工要求也越来越高。
微细加工技术通过高精度的光刻和薄膜沉积等技术,能够在微米或纳米级别上进行精细加工,以满足电子器件的要求。
例如,通过实现纳米尺度上的金属薄膜沉积,可以提高电子器件的性能,拓展电子技术的应用领域。
微细加工技术的研究可谓涉及众多学科,如力学、材料学、光学等。
其中,光学是一门重要的研究方向。
激光加工技术作为微细加工技术的重要组成部分,以其高精度、高效率的特点,被广泛应用于各个领域。
激光加工技术通过高能量的激光束将材料层层蒸发或氧化,实现精细的加工。
目前,激光加工技术已经发展到纳米级,成为微细加工技术中的重要手段之一。
在微细加工技术的研究中,仪器设备的不断更新也起到了关键作用。
高精度的微细加工需要精密的设备来支持。
微细加工技术

LIGA 技术首先由德国卡尔斯鲁厄核物理研究所提出来,LIGA 是lithographie(制版术)、 galvanoformung(电铸成形)、abformung(微注塑)这3个德文单词的缩写,被公认为是一种全新 的三维立体微细加工技术。
1. 技术原理与工艺过程 图所示为典型的LIGA 工艺过程,主要包括以下内容。 (1)深层同步辐射X光曝光 (2)显影 (3)电铸 (4)塑铸(铸模)
先进制造技术
微细加工与纳米制造技术
1.1 硅基微细加工技术
单晶硅是微机械采用最广泛的材料,硅基微细加工技术是微结构制造中的一种常用技术。 硅基微细加工技术主要指以硅材料为基础制作各种微机械零部件的加工技术,总体上可 分为体加工与面加工两大类。体加工主要指各种硅刻蚀(腐蚀)技术,而面加工则指各种薄膜制 备技术。这些技术在实际应用过程中还要借助于集成电路加工工艺,如光刻、扩散、离子注入、 外延和淀积等技术。
离子束加工出的2刃、4刃和6刃微细端铣刀
微细加工与纳米制造技术
日本FANUC公司和有关大学合作研 制的车床型超精密铣床,在世界上首次用 切削方法实现了自由曲面的微细加工。这 种超精密切削加工技术使用切削刀具,可 对包括金属在内的各种可切削材料进行微 细加工,也可利用CAD/CAM 技术实现三 维数控加工,具有生产率高、相对精度高 的优点。
微细加工技术及其在微型器件制造中的应用

微细加工技术及其在微型器件制造中的应用近年来,微细加工技术得到了广泛的关注和应用,它被广泛运用在微型器件制造等领域。
随着国家在技术创新领域不断推进,微细加工技术的应用也越来越广泛。
微细加工技术是指在微米级别下进行的精细加工,它是微米级别下的制造和加工技术。
与传统的加工技术不同,微细加工技术具有高精度、高效率、高自动化程度和高可靠性的优点。
它在微型器件制造中有着重要的应用价值。
一、微细加工技术的种类及特点微细加工技术包括激光加工技术、电解加工技术、原子力显微镜加工技术、电子束加工技术、离子束加工技术等。
这些技术各有特点,能够在微米级别下进行高精度加工,具有非常好的应用前景。
激光加工技术是指利用激光器产生激光束,在微米级别下进行高精度加工的一种技术。
激光加工技术具有高效率、高精度、无接触等优点。
它被广泛运用在微型器件的制造、加工和维护等方面。
电解加工技术是一种电化学加工技术,它在微米级别下进行高精度加工。
与传统加工技术相比,电解加工技术具有高精度、高效率、无振动、无热影响等优点。
它被广泛运用在制造的精密部件、微型加工计量和微型传感器等领域。
原子力显微镜加工技术是一种利用原子力显微镜对微米级别下的原子进行精细加工的一种技术。
与传统加工技术相比,原子力显微镜加工技术具有高精度、高效率、无接触、无振动等优点。
它被广泛用于制造、加工和观测微型器件。
二、微细加工技术在微型器件制造中的应用微细加工技术在微型器件制造中有着重要的应用价值。
例如,微机电系统(MEMS)中的传感器和执行器等部件需要进行微细加工,以实现高精度、高灵敏度、高性能等特点。
其中,微细加工技术在MEMS加工中发挥着重要的作用。
MEMS是在单个晶片上集成化微型机械和电子成分的系统,它是微细加工技术的集大成者。
MEMS 系统具有非常广泛的应用前景,如生物医疗、通信、工业制造等领域。
在MEMS加工中,需要应用激光加工技术、离子束加工技术、电子束加工技术等微细加工技术。
浅谈微细加工技术

浅谈微细加工技术xx(xx学院机自1001班430205)[摘要] 特种微细加工技术已成为许多工业领域产品制造技术群中不可缺少的分支,在难切削材料、复杂型面、精细表面、低刚度零件及模具加工等领域中,已成为重要的工艺方法.目前,特种微细加工技术正处于蓬勃发展的阶段。
[关键词]特种微细加工光刻技术发展成果引言一、微细加工技术发展研究微细加工技术是集成电路(lC)工业的基础,是半导体器件研究的必要手段。
其中的lC以动态随机存储器(ORAM)为代表,具有肉眼无法看见的记忆功能结构,而半导体器件以小尺寸器件为主。
为了制备大规模集成电路(VL引)、超大规模集成电路(ULSI)和量子器件,微细加工技术正由微米、亚微米、亚半微米一直向纳米级和量子化方向发展。
除了lC技术外,液晶显示器(LCO)技术、微机械技术和光电子技术的发展同样离不开微细加工技术水平的提高。
人们越来越感到以微细加工技术为支柱的微电子技术正在成为一个国家综合国力的重要体现,成为国际竞争的焦点。
因此许多发达国家目前都加大了在微细加工技术研究方面的投资强度,以期取得微细加工技术领域的领先地位。
微细加工技术包括曝光技术(即光刻技术)、刻蚀技术、浅结掺杂技术、超薄膜形成技术等。
其中的曝光技术是微细加工技术的核心。
作者简介: xx(xx年-);男;汉族;机械工程方向:机械制造与自动化1、国外微细加工技术在Ic方面的成就。
国外微细加工技术在IC工业方面取得了很大的成就。
表1是ORAM发展所要求达到的光刻技术水平和近年来ORAM的发展趋势。
需要特别提到的是,1991年,日本日立公司研制成功64MORAM,其加工线宽为0.3微米,芯片面积为9.74X20.28平方毫米,集成度为1.21火1护个元器件;1992年,日本富士通公司推出256MORAM,加工线宽为0.2微米,芯片面积为16火25平方毫米,集成度为5.6x1了个元器件。
由表5不难看到,国外在微细加工技术研究方面取得的进展是很快的,以致于每隔几年就能推出一代产品。
- 1、下载文档前请自行甄别文档内容的完整性,平台不提供额外的编辑、内容补充、找答案等附加服务。
- 2、"仅部分预览"的文档,不可在线预览部分如存在完整性等问题,可反馈申请退款(可完整预览的文档不适用该条件!)。
- 3、如文档侵犯您的权益,请联系客服反馈,我们会尽快为您处理(人工客服工作时间:9:00-18:30)。
浅谈微细加工技术xx(xx学院机自1001班430205)[摘要] 特种微细加工技术已成为许多工业领域产品制造技术群中不可缺少的分支,在难切削材料、复杂型面、精细表面、低刚度零件及模具加工等领域中,已成为重要的工艺方法.目前,特种微细加工技术正处于蓬勃发展的阶段。
[关键词]特种微细加工光刻技术发展成果引言一、微细加工技术发展研究微细加工技术是集成电路(lC)工业的基础,是半导体器件研究的必要手段。
其中的lC以动态随机存储器(ORAM)为代表,具有肉眼无法看见的记忆功能结构,而半导体器件以小尺寸器件为主。
为了制备大规模集成电路(VL引)、超大规模集成电路(ULSI)和量子器件,微细加工技术正由微米、亚微米、亚半微米一直向纳米级和量子化方向发展。
除了lC技术外,液晶显示器(LCO)技术、微机械技术和光电子技术的发展同样离不开微细加工技术水平的提高。
人们越来越感到以微细加工技术为支柱的微电子技术正在成为一个国家综合国力的重要体现,成为国际竞争的焦点。
因此许多发达国家目前都加大了在微细加工技术研究方面的投资强度,以期取得微细加工技术领域的领先地位。
微细加工技术包括曝光技术(即光刻技术)、刻蚀技术、浅结掺杂技术、超薄膜形成技术等。
其中的曝光技术是微细加工技术的核心。
作者简介: xx(xx年-);男;汉族;机械工程方向:机械制造与自动化1、国外微细加工技术在Ic方面的成就。
国外微细加工技术在IC工业方面取得了很大的成就。
表1是ORAM发展所要求达到的光刻技术水平和近年来ORAM的发展趋势。
需要特别提到的是,1991年,日本日立公司研制成功64MORAM,其加工线宽为0.3微米,芯片面积为9.74X20.28平方毫米,集成度为1.21火1护个元器件;1992年,日本富士通公司推出256MORAM,加工线宽为0.2微米,芯片面积为16火25平方毫米,集成度为5.6x1了个元器件。
由表5不难看到,国外在微细加工技术研究方面取得的进展是很快的,以致于每隔几年就能推出一代产品。
以下是生产256MORAM所需达到的微细加工技术水平:光刻0.25微米(套刻精度士0.08微米,线宽控制0.04微米),无机且能真空处理的全干刻蚀剂技术,0.1微米以下浅结技术,低温工艺仁平坦化,全干法加工、刻蚀、清洗,CVO 铝和铜金属化,全自动化。
表52、国外微细加工技术在半导体器件研究方面的成就。
国外微细加工技术在半导体器件研究方面也取得了很大的成就。
1993年,日本东芝公司的研究开发中心研制成功门长度仅为0.04微米的n沟道MOSFE丁,并且可在室温下工作。
德仪(TI)公司在工993年也研制成功晶体管特征尺寸为0.02微米的集成电路,在该特征尺寸下,电子已经停止了粒子活动,开始转化为类似波的活动。
目煎国外研制的日EM下器件的最小栅长仅为25纳米。
另外,国外也利用高水平的微细加工技术制作出了与电子相干长度相当的纳米结构(包括量子线、量子点阵、量子点接触等),并对其物理过程进行了广泛的研究,提出了电子波器件的可能性。
美国《物理评论》杂志指出,以量子效应为基础的电子波器件有可能成为ULsl技术的基础,并将导致未来电子学发展的一场新革命。
国外在lC工业和半导体器件研究方面所取得的成就无一不得益于微细加工技术的发展。
可以说,国外的微细加工技术正在朝着物理加工极限发展。
二、我国的微细加工技术水平我国自从1985年研制出第一块IC芯片以来,微细加工技术取得了较大的进步。
在ORAM研制方面,1986年研制成功64KDRAM,1990年研制出iM汉字ROM,其加工线宽为1.5微米,集成度为1.06Xl护个元器件。
1986年我国开始批量生产5微米技术产品,1994年开始批量生产3微米技术产品。
“八五”科技攻关项目安排了0.8微米技术,“攀登”计划安排了0.5微米基础技术研究。
预计这些安排将会使我国在未来的IC工业竞争中取得一些主动权。
但是必须清楚地看到,我国的微细加工水平与国外确实存在着较大的差距。
在同步辐射X线光刻研究方面,我国已建立了BSRF和NSRL两个同步辐射X射线光刻站。
1990年6月,成功地进行了首次同步辐射X射线光刻实验。
1993年11月,同步辐射深光刻技术(即UGA技术)取得了较大进展。
1、对微细加工的认识。
鉴于微细加工技术是IC工业发展的关键,微细加工技术的突破将会带来一场新的技术革命。
我们认为:(1)必须提高对微细加工技术研究重要性的认识,制订好提高我国微细加工技术水平的战略规划,对有全局作用的微细加工关键技术要有重点突破。
(2)加快提高我国微细加工设备的研制水平。
一代设备推出一代技术,一代技术推出一代产品,微细加工设备已成为制约微细加工技术发展水平的重要因素。
因此,研制出高精度、高度自动化的微细加工设备已成为摆在我们面前的紧要任务。
(3)加强基础技术研究。
几十年来我们在半导体器件研制和IC工业发展中一直处于较为被动的局面,一个主要的原因就是对于带有基础性的、全局性的基础技术研究缺乏足够的重视。
对于电子束光刻技术、同步辐射X线光刻技术、反应离子刻蚀技术、电子束掺杂技术以及小尺寸器件的制作技术等都重视不够。
(4)统盘全局,克服现在在微细加工技术研究方面技术力量比较分散的缺点,象抓系统工程那样抓微细加工技术研究,利用各研究单位的技术优势,联合攻关。
(5)加快微细加工技术人才的培养。
技术竞争的结果最终必然是人才的竞争,因此必须注重对微细加工技术研究人才的培养。
2、微细加工技术的原理和应用研究20 世纪80 年代以来, 微机械、微机电系统(MEMS) 这一门新兴交叉学科开始兴起, 微细加工技术作为获得微机械、微机电系统的必要手段得到了快速的发展。
微细加工技术起源于平面硅工艺, 但随着半导体器件、集成电路、微型机械等技术的发展与需求, 微细加工技术已经成为一门多学科交叉的制造系统工程和综合高新技术, 广泛应用于医疗、生物工程、信息、航空航天、半导体工业、军事、汽车等领域, 给国民经济、人民生活和国防、军事等带来了深远的影响, 被列为21 世纪关键的技术之一。
微细加工技术是由瑞士公司发明的一种新型加工工艺, 在2004 年法国巴黎举办的国际表面处理展览会( SITS) 和2004 年在法国里昂举办的ALLIANCE 展览会上荣获2 项发明奖。
微细加工工艺和设备拥有国际专利保护。
3、微细加工的技术原理与分类。
微细加工技术结合了超精增亮和超精抛光两项革新技术, 能够有选择性地保留表面的微观结构, 以提高表面的摩擦和滑动性能( 表面技术) , 以机械化和自动化取代传统的手工抛光, 提高表面的美学功能。
这种微细加工技术应用于切削刀具、冲压和锻造工具, 航空、汽车、医疗器械、塑料注射模具等机械零件的表面处理,能够极大地改善零件表面的性能。
微细加工技术采用全自动方式对金属零件表面进行超精加工, 通过一种机械化学作用来清除金属零件表面上1~40μm 的材料, 实现被加工表面粗糙度达到或者好于ISO 标准的N1 级的表面质量。
微细加工技术主要应用于超精抛光和超精增亮这两个领域。
超精抛光使传统的手工抛光工艺自动化; 而超精增亮则生成新的表面拓扑结构。
微细加工技术的一个突出优点是能够赋予零件表面新的微观结构。
这些微观结构能提高零件表面对特定应用功能的适应性。
如减小摩擦和机械差异、提高抗磨损性能、改善涂镀前后表面的沉积性能等。
总的说来, 超精增亮可去除次级微观粗糙表面, 次级粗糙表面的厚度在0~20μm 之间, 位于零件表面初级微观粗糙面的峰尖之间。
而超精抛光则部分或整体去除初级微观粗糙表面, 其值在10~40μm 之间, 当然这取决于零件材料表面的初始状态。
微细加工与常规尺寸加工的激励特点区别主要体现在:(1)加工精度的表示方法不同。
一般尺度加工精度常用相对精度表示, 微细加工精度用尺寸的绝对值来表示, 并引入了加工单位的概念。
(2)加工机理存在很大的差异。
由于微细加工中加工单位的极小化而产生了微动力学、微流体力学、微热力学等方面的微观机理, 常规的加工方法及理论已不适用。
(3)加工特征明显不同。
在机电产品中, 一般常规加工都是以尺寸、形状、位置精度为特征, 而微细加工多以分离或结核原子、分子为特征。
目前, 国际上微细加工技术的研究与发展, 主要形成了以美国为代表的硅基MEMS 技术, 以德国为代表的LICA 技术和以日本为代表的传统加工方法的微细化等主要流派, 他们的研究与应用情况代表了国际微细加工的水平和发展方向。
由于微机械和微细加工零件尺寸或加工尺度的微小化, 许多宏观状态下的物理量和机械量在加工过程中都将发生很大的变化, 并在微观状态下呈现出特有的规律, 因而涉及到了与常规理论不同的微机械学、微电子学、微光学和分子装配技术等多种理论学说。
在各种微观理论学说的基础上, 发展起了各种各样的现代技术。
依据微细加工中加工机理的不同, 可以将微细加工技术分为以下四类:(1) 分离加工—将材料的某一部分分离出去的加工方式, 如切削、分解、刻蚀、蒸发、溅射、破碎等。
(2) 结合加工—同种和不同种材料的附加或相互结合的加工方式, 如蒸馏、沉淀、生长、渗入、黏结等。
(3) 变形加工—使材料形状发生改变的加工方式,如塑性变形加工、流体变形加工等。
(4) 材料处理或改性。
三、微细加工技术发展前景与展望自1958年美国首先研制成功集成电路起,1963年MoS场效应晶体管研制成功,1964年出现PMOS集成电路,1971年以来相继推出了4K、16K、256K、IM、4M、16M、64M、256M 和lG的DRAM(动态存贮器),并形成规模生产。
从集成电路制作技术的发展历史可以看出,到目前为止,国际上集成电路芯片的发展基本上还是遵循摩尔定律和等比例缩小规律,即每隔3年集成度增加4倍,因硅电子器件随着其特征尺寸的缩小,工作速度将会增加,功耗将会降低,其特征尺寸随之相应缩小30 ,同时引发了一系列微细加工技术“极限”问题,见表1。
1、延伸“极限"束缚的技术。
微电子技术的发展与进步主要是靠工艺技术的不断改进,使得器件特征尺寸的“极限”获得一次次突破,从而使集成度不断提高,功耗降低,器件性能得到改善,然而特征尺寸的不断缩小,使得集成电路的微细加工技术不断受到物理学“极限”的困扰,同时对工艺中所采用的材料、介质以及超微细加工技术、各种掺杂技术、金属化及多层金属互连技术水平的要求也越来越高。
2、微细加工的基本流程。
以硅为衬底的微细加工技术实际就是实现图形转移整个过程中的处理技术,一般的微细加工过程包括基片预处理、光刻、掺杂、腐蚀、互连线制作等基本流程。
将预处理后的基片通过多次光刻技术、腐蚀技术,把电路图形永久地保留在硅片上,同时采用一定的掺杂技术,在硅片上形成满足IC设计要求的半导体结构。