锻件图的绘制
2.3 锻造工艺解析

机械制造工艺基础——锻压工艺
5、平锻机上模锻:
• 平锻机的主要结构与曲柄压力机相同。只因 滑块是作水平运动,故称平锻机。
机械制造工艺基础——锻压工艺
5、平锻机上模锻:
•平锻机上模锻的特点: (1)有两个分模面,可以锻出其他模锻方 法无法锻出的锻件。 (2)生产率高,400-900件/小时。 (3)锻件尺寸精确,表面粗糙度低。 (4)材料利用率达85-95%。 (5)非回转体及中心不对称的锻件较难锻 造。平锻机造价高。 (6)适合于带头部的杆类和有孔零件的模 锻成型。
机械制造工艺基础——锻压工艺
补充: 典型零件模锻工艺过程: (1)零件图纸的分析
(2)选择分模面
(3)确定锻孔
(4)确定模锻工序
(5)绘制锻件图
(6) 锻模设计
机械制造工艺基础——锻压工艺
(1)零件图纸的分析
• 汽车后闸传动杆零件,上下端面、四个大孔、 20.3孔的端面和8孔需机械加工,其余均需模 锻锻出。
机械制造工艺基础——锻压工艺
1、模锻件图的绘制:
4)锻模圆角: •所有两表面交角处都应 有圆角。一般内圆角半 径(R)应大于其外圆半 径(r)。 5)留出冲孔连皮: •锻 件 上 直 径 小 于 25mm 的孔,一般不锻出,或 只压出球形凹穴。
机械制造工艺基础——锻压工艺
1、模锻件图的绘制:
• 大于25mm的通孔,也不能直接模锻出通孔, 而必须在孔内保留一层连皮。 • 冲孔连皮的厚度s与孔径d有关,当d =30~ 80mm时,s =4~8mm。
机械制造工艺基础——锻压工艺
3.摩擦压力机上模锻
④ 摩擦压力机承受偏心载荷能力差,通 常只适用于单膛锻模进行模锻。对于形 状复杂的锻件,需要在自由锻设备或其 它设备上制坯。 •应用: 适合于中小件的小批生产。如铆钉、 螺钉、螺母、气门、齿轮和三通阀体等。
自由锻件图绘制例题
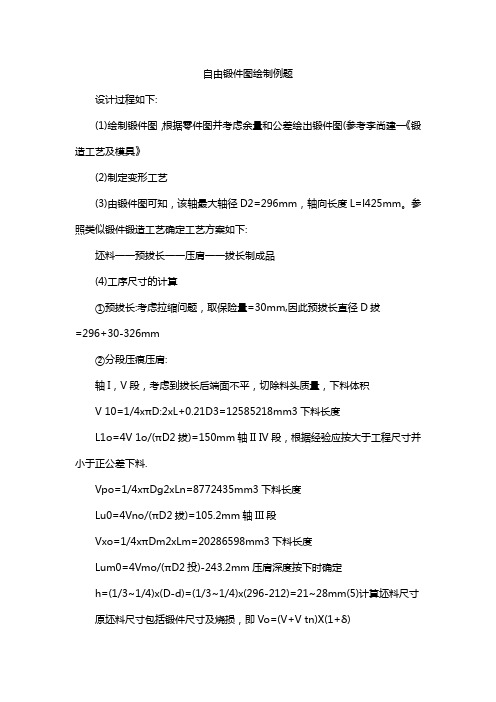
自由锻件图绘制例题
设计过程如下:
(1)绘制锻件图,根据零件图并考虑余量和公差绘出锻件图(参考李尚建一《锻造工艺及模具》
(2)制定变形工艺
(3)由锻件图可知,该轴最大轴径D2=296mm,轴向长度L=l425mm。
参照类似锻件锻造工艺确定工艺方案如下:
坯料一一预拔长一一压肩一一拔长制成品
(4)工序尺寸的计算
①预拔长:考虑拉缩问题,取保险量=30mm,因此预拔长直径D拔
=296+30-326mm
②分段压痕压肩:
轴I,V段,考虑到拔长后端面不平,切除料头质量,下料体积
V 10=1/4xπD:2xL+0.21D3=12585218mm3下料长度
L1o=4V 1o/(πD2拔)=150mm轴II IV段,根据经验应按大于工程尺寸并小于正公差下料.
Vpo=1/4xπDg2xLn=8772435mm3下料长度
Lu0=4Vno/(πD2拔)=105.2mm轴III段
Vxo=1/4xπDm2xLm=20286598mm3下料长度
Lum0=4Vmo/(πD2投)-243.2mm压肩深度按下时确定
h=(1/3~1/4)x(D-d)=(1/3~1/4)x(296-212)=21~28mm(5)计算坯料尺寸原坯料尺寸包括锻件尺寸及烧损,即Vo=(V+V tn)X(1+δ)
V-59000168 mm'
V n=-4001813 mm3取烧损率δ=3.5%
得Vo=65207051 mm3选择圆柱坯料中340,即Do-340mm Ho-4Vo/(πD'o)=718mm
锻件重量Gx=ρx Vo=515Kg。
锻件图绘制要领

200
大于
至
至 63
100
140
200
280
25
2.0
-
-
-
-
25
40
2.0
2.6
-
-
-
40
63
2.0
2.6
3.0
-
-
63
100
2.5
3.0
3.0
4.0
-
100
160
2.6
3.0
3.4
4.0
4.6
160
250
3.0
3.0
3.4
4.0
4.6
锻件公差分为普通级和精密级。
1.长度、宽度和高度公差
长度、宽度和高度公差是指在分模面一侧,同一块模具上,沿长度、宽度和高度方向
2. r—外圆角半径;R—内圆角半径。 3.本表适用于在热模锻压力机、模锻锤、平锻机及螺旋压力机上生产的模锻件。
分模线(面)的选择
在模锻锤、热模锻压力机、螺旋压力机和平锻机上成批生产的重量不超过 250kg,长 度不超过 2500mm 的钢质(碳钢和合金钢)模锻件(以下简称模钢件),在制订锻件图时, 需要正确的选择分模面,选定机械加工余量及公差,选用模锻斜度与圆角半径,确定冲孔 连皮,并在技术条件内说明交货要求和在锻件图上所不能标明的技术要求与允许偏差。
利于充满终锻模膛,但对机械加工并不完全有利。
第 4 页 共 24 页
图 19 锻件上的盲孔
模锻斜度
(一)模锻斜度的确定 锻件侧面设有模锻斜度便于模锻后脱模。模锻斜度分外斜度和内斜度。锻件冷却时趋 向离开模壁的部分称为外斜度,用 α 表示;反之称为内斜度,用 β 表示(见图 14)。 锤上模锻的锻件外斜度值根据锻件各部分的高度与宽度之比值 H/B,及长度与宽度之 比值 L/B(见图 14),查表 13 确定。内斜度按外斜度增大 2°或 3°。如上下模膛深度不 相等,应按模膛较深一侧计算模锻斜度。 热模锻压力机和螺旋压力机上使用顶料机构时,模锻斜度可比表 13 数值减小 2°或 3°。 平锻件模锻斜度由表 14 查得。
第二章锻造

弯曲模膛:对于弯曲的杆类模锻件,需采用弯 曲模膛来弯曲坯料。坯料可直接或先经其它 制坯工步后放入弯曲模膛进行弯曲变形。
切断模膛:它是在上模与下模的角部组成的一 对刃口,用来切断金属。单件锻造时,用它 从坯料上切下锻件或从锻件上切下钳口;多 件锻造时,用它来分离成单个锻件。
4.模锻圆角半径
模锻圆角:指模锻件中断面形状和平面形状变
化部位棱角的圆角和拐角处的圆角。
作用:圆角结构可使金属易于充满模膛,避免锻
模的尖角处产生裂纹,减缓锻件外尖角处的磨损, 从而提高锻模的使用寿命。同时可增大锻件的强 度。
大小:模锻件外圆角半径(r)取1.5~12mm,内
圆角半径(R)比外圆角半径大 2~3倍。模膛越深 圆角半径的取值就越大。
二、坯料重量和尺寸的确定
坯料重量可按下式计算:
G坯料=G锻件+G烧损+G料头
式中:G坯料——坯料重量; G锻件——锻件重量; G烧损——加热中坯料ቤተ መጻሕፍቲ ባይዱ面因氧化而烧损的重量; 第一次加热取被加热金属重量的2%~3%; 以后各次加热的烧损量取1.5%~2.0%。 G料头——锻造过程中冲掉或被切掉的那部分金属
第4二.2节锻锻造造
锻造:在加压设备及工具作用下,使坯料、 铸锭产生局部或全部的塑性变形,以获得 一定尺寸、形状和质量的锻件的加工方法。
第一节 锻造方法
一、自由锻
定义:指用简单的通用工具,或在锻造设备的上
下砧间直接使坯料变形而获得所需的几何形状及 内部质量锻件的方法。
设备:
锻锤 中小型锻件 液压锤 大型件
适用范围:大批量生产中锻制中小型锻件。
优点:锻件精度高、生产率高、劳动条件好、节
2-自由锻模锻工艺
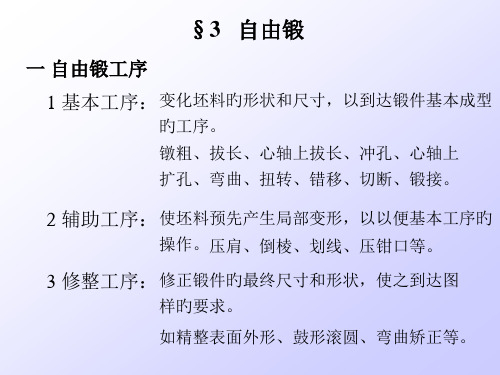
弯曲连杆旳模锻过程
三 锤上模锻工艺规程(锻件图)旳制定
1 绘制锻件图: 设计和制造锻模旳根据;计算坯料旳根据;检验锻件旳根据。 工艺参数旳拟定: (1)分模面: 即锻模上、下模或凸、凹模旳分界面。
选择分模面旳原则: 要确保锻件能从模膛中取出;
d
有利于发觉上下模错移,预防出废品;
a b
a 使模膛有最浅旳深度,便于充斥; b
四 模锻件旳构造工艺性
具有合理旳分模面、斜度和圆角半径,以便于从模膛中取出锻件; 非配合表面设计成不加工表面; 使模锻成形轻易,降低工序:
零件力求简朴、平直、对称; 截面差不要过大,Fmax/Fmin≤2 不宜过于扁薄; 应防止高旳凸起和深凹。 防止小孔、多孔构造,防止窄沟、深槽构造;
4 -φ20
c
c 分模面最佳是平面;
降低余块,节省金属。 d
a-a
b-b
c-c
d-d
(2)加工余量和铸造公差: 余量1~4mm,公差±0.3~3mm, 冲孔连皮4~8mm。 (3) 斜度: 斜度一般为5~12° (4) 圆角半径:在锻件上全部两平面交角处都需做成圆角,
目旳是降低模具旳磨损和便于金属旳充填。
2 拟定模锻工步 3 算料 4 选择模锻设备 5 模锻旳后续工序
(六)填写工艺卡
三 自由锻零件构造工艺性
1 尽量防止锥面和斜面以及不规则曲面;
2 两部分连接处不用弧面(采用截柱体);
3 锻件上不得有加强筋和小凸台; 4 形状复杂件可分几种部分锻出。
§2-4 模锻
将金属坯料放在锻模旳模膛内,在锻压力旳作用下,迫 使金属料依模膛旳形状而变形旳一种铸造措施。
一 锻模和模膛
样旳要求。 如精整表面外形、鼓形滚圆、弯曲矫正等。
锻件图设计要素

锻件图设计要素
1、锻件分模位置应选在具有最大水平投影尺寸的位置上:保证锻件形状尽可能与零件形状相同,并容易从模腔中取出。
2、分模平面尽可能采用直线状,并应使分模线选在锻件侧面的中部:使分模结构尽量简单和便于发现上下模在模锻过程中的错移。
3、对金属流线有要求的锻件,为避免纤维组织被切断,应尽可能沿锻件截面外形分模,同时应考虑锻件工作时的受力情况,应使纤维组织与剪应力方向垂直。
4、圆角半径直接影响着模锻时的金属流动、模膛充满、模锻力、模具磨损、锻件切削加工量和锻件转角处流线的切断。
内圆角半径:
⑴内圆角半径大:有利于金属平滑地沿模膛流动;
⑵内圆角半径小:横向流动的金属越过内圆角,在模具壁附近形成一个空穴,当金属由顶部返流时,形成折叠。
外圆角半径:
⑴外圆角半径大:减小模膛圆角处的应力集中;
⑵外圆角半径小:增大模膛圆角处的应力集中。
锻造工艺锻件图

零件名称钢号45钢
锻件单个质量30.301kg 锻件级别特钢坯质量35.8kg 设备
每个钢坯制锻件数 1 每个锻件制零件数 1 锻件图
技术要求:
1.按照零件技术条件生产验收;
2.钢坯第一热处理按专业工艺进行;
3.各工序必须严格执行工艺,精心操作;
4.生产路线:加热—锻造—胎模锻—整修—发送金工;
5.印记内容:生产编号、图号、熔炼炉号;
编制校对批准
火次温度/℃操作说明及变形过程简图
1 1200~800 任取D=100mm,根据体积不变原则,算得
H=196mm,1≤H/D=1.96≤2.5,符合要求。
2 1200~800 将所下的料进行自由镦粗,镦粗后坯料的直径略小于胎模的内
径。
3 1200~800 将镦粗了的配料放入胎模中锻出所需的形状。
4 1200~800 冲去连皮、飞边、整修。
第5章自由锻工艺过程

3.钢锭规格的选择
1)首先确定钢锭的各种损耗,求钢锭的利用率
1 冒口 锭底 烧损 100%
碳素钢钢锭: 冒口 18% - 25%,锭底 5% - 7%
合金钢钢锭: 冒口 25% - 30%,锭底 7% -10%
计算钢锭质量:
G锭
G锻 G损
2)根据锻件类型,参照资料选取 G锭 G锻 /
•
每一次的加油,每一次的努力都是为 了下一 次更好 的自己 。20.12. 820.12. 8Tuesday, December 08, 2020
•
天生我材必有用,千金散尽还复来。0 5:51:04 05:51:0 405:51 12/8/20 20 5:51:04 AM
•
安全象只弓,不拉它就松,要想保安 全,常 把弓弦 绷。20. 12.805: 51:0405 :51Dec-208-De c-20
4.4.3. 选择锻造设备
•空气锤利用电动机带动活塞产生 压缩空气,使锤头上下往复运动 进行锤击。
特点:结构简单,操作方便,维护 容易,但吨位较小,只能用来锻 造100kg以下的小型锻件。
•蒸汽-空气锤采用蒸汽和压缩空 气作为动力,其吨位稍大,可用 来生产质量小于1500kg的锻件,
5.3 自由工艺过程规程的制定
5.3 自由工艺过程规程的制定
4.4.3. 选择锻造设备
(1)在水压机上锻造
最大变形力 F pA
平均单位压力p根据不同情况分别计算
1)圆形截面锻件镦粗
当
H D
0.5时,
p
s (1
3
当
H D
0.5
时,
p
s (1
4
D) H D) H
D、H分别是锻造终了锻件的直径和高度, s 在相应变 形温度和速度下的真实流动应力
锻造工艺锻件图
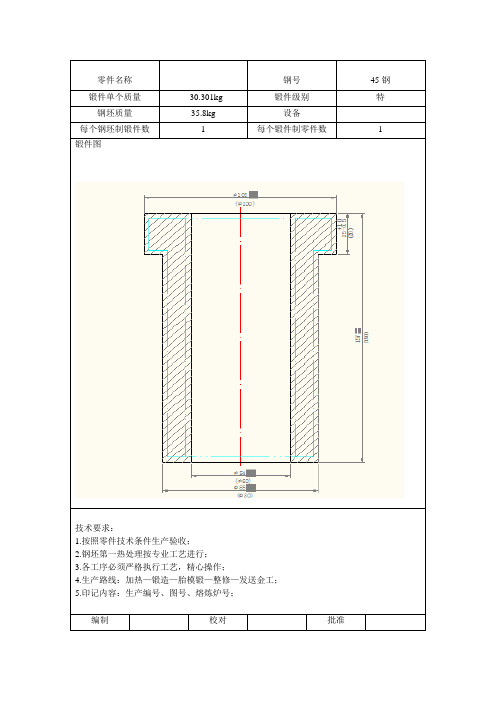
零件名称钢号45钢锻件单个质量30.301kg 锻件级别特钢坯质量35.8kg 设备
每个钢坯制锻件数 1 每个锻件制零件数 1 锻件图
技术要求:
1.按照零件技术条件生产验收;
2.钢坯第一热处理按专业工艺进行;
3.各工序必须严格执行工艺,精心操作;
4.生产路线:加热—锻造—胎模锻—整修—发送金工;
5.印记内容:生产编号、图号、熔炼炉号;
编制校对批准
火次温度/℃操作说明及变形过程简图
1
1200~800 任取D=100mm,根据体积不变原则,算得H=196mm,1≤H/D=1.96≤2.5,符合要求。
2
1200~800 将所下的料进行自由镦粗,镦粗后坯料的直径略小于胎模的内径。
3 1200~800 将镦粗了的配料放入胎模中锻出所需的形状。
4 1200~800 冲去连皮、飞边、整修。
课程设计锻件图的设计

课程设计锻件图的设计一、教学目标本课程旨在让学生掌握锻件图的设计方法和技巧,培养他们的工程图纸阅读和绘制能力。
通过本课程的学习,学生将能够理解锻件图的基本组成、标注和表达方式,熟练运用绘图软件进行锻件图的设计和绘制。
此外,学生还将在实践中培养观察能力、创新能力和团队合作精神。
具体教学目标如下:1.知识目标:(1)掌握锻件图的基本组成和表达方式;(2)了解锻件图的标注方法和规则;(3)熟悉绘图软件的基本操作和功能。
2.技能目标:(1)能够独立完成锻件图的阅读和理解;(2)能够运用绘图软件进行锻件图的设计和绘制;(3)具备一定的创新能力和解决问题的能力。
3.情感态度价值观目标:(1)培养学生的团队合作精神和责任感;(2)增强学生对工程图纸重要性的认识;(3)激发学生对工程制图学科的兴趣和热情。
二、教学内容本课程的教学内容主要包括以下几个部分:1.锻件图的基本组成和表达方式;2.锻件图的标注方法和规则;3.绘图软件的基本操作和功能;4.锻件图的设计和绘制方法;5.实践练习和案例分析。
教学进度安排如下:第1-2课时:介绍锻件图的基本组成和表达方式;第3-4课时:讲解锻件图的标注方法和规则;第5-6课时:学习绘图软件的基本操作和功能;第7-8课时:教授锻件图的设计和绘制方法;第9-10课时:进行实践练习和案例分析。
三、教学方法本课程采用多种教学方法相结合的方式,以激发学生的学习兴趣和主动性:1.讲授法:教师讲解锻件图的基本概念、标注方法和设计技巧;2.讨论法:学生分组讨论,分享学习心得和经验;3.案例分析法:分析实际案例,培养学生解决实际问题的能力;4.实验法:上机操作,让学生亲手绘制锻件图,提高实践能力。
四、教学资源本课程所需教学资源包括:1.教材:《工程制图基础》;2.参考书:《锻件图设计与绘制手册》;3.多媒体资料:PPT、视频教程等;4.实验设备:计算机、绘图软件、绘图板等。
以上教学资源将有助于实现课程目标,提高学生的学习效果。
第三章 自由锻造分析

• (1)拔长过程中要将毛坯料不断反复地 翻转90°,并沿轴向送进操作(图a)。 螺旋式翻转拔长(图b),是将毛坯沿一 个方向作90°翻转,并沿轴向送进的操 作。单面顺序拔长(图c),是将毛坯沿 整个长度方向锻打一遍后,再翻转90°, 同样依次沿轴向送进操作。用这种方法 拔长时,应注意工件的宽度和厚度之比 不要超过2.5,否则再次翻转继续拔长时 容易产生折叠。
• (4)锻件拔长后须进行修整,修整方形或 矩形锻件时,应沿下砧子的长度方向送 进(图3-30a ),以增加工件与砧子的接 触长度。拔长过程中若产生翘曲应及时 翻转180°轻打校平。圆形截面的锻件用 型砧或摔子修整(图3-30b )。
三、冲孔
在坯料中冲出透孔或不透孔的工序。根据冲孔所 用的冲子的形状不同,冲孔分实心冲子冲孔和 空心冲子冲孔。实心冲子冲孔分单面冲孔和双 面冲孔。
注意事项: 1)冲孔前坯料必需镦粗,使端面平整,高度减小, 直径增大; 2)冲头必须放正,打击方向应和冲头端面垂直; 3)在冲出的初孔内应撒上煤末或木炭粉,以便取 出冲头; 4)冲制深孔时要经常取出冲头在水中冷却;
四、弯曲 将毛坯弯成所规定的外形的锻造工序叫弯曲。
注意事项: 1)当锻件有数处弯曲时,弯曲的次序一般是先弯 端部及弯曲部分与直线部分交界的地方,然后 再弯其余的圆弧部分。
• ⑵ 镦粗的始锻温度采用坯料允许的最高 始锻温度,并应烧透。坯料的加热要均 匀,否则镦粗时工件变形不均匀,对某 些材料还可能锻裂。
⑶ 镦粗的两端面要平整且与轴线垂直,否 则可能会产生镦歪现象。矫正镦歪的方 法是将坯料斜立,轻打镦歪的斜角,然 后放正,继续锻打(如下图)。如果锤 头或抵铁的工作面因磨损而变得不平直 时,则锻打时要不断将坯料旋转,以便 获得均匀的变形而不致镦歪。
《工程材料与热加工基础》第十章锻压生产

第一节 金属的锻造性能
一、金属的塑性变形概述 金属塑性变形的实质,对于单晶体是由于金属原子某晶面两侧受切应力
作用产生相对滑移,或晶体的部分晶格相对于某晶面沿一定方向发生切变, 即滑移理论和孪生理论。
二、热锻、冷锻、温锻、等温锻
从金属学的观点划分锻压加工的界限为再结晶温度。 1.热锻 在金属再结晶温度以上进行的锻造工艺称为热锻。在变形过程中 冷变形强化和再结晶同时存在,属于动态再结晶。 2.冷锻 在室温下进行的锻造工艺称为冷锻。冷锻可以避免金属加热出现 的缺陷,获得较高的精度和表面质量,并能提高工件的强度和硬度。但冷 锻变形抗力大,需用较大吨位的设备,多次变形时需增加再结晶退火和其 它辅助工序。目前冷锻主要局限于低碳钢、有色金属及其合金的薄件及小 件加工。 3.温锻 在高于室温和低于再结晶温度范围内进行的锻造工艺称为温锻。 与热锻相比,坯料氧化脱碳少,有利于提高工件的精度和表面质量;与冷 锻相比,变形抗力减小、塑性增加,一般不需要预先退火、表面处理和工 序间退火。温锻适用于变形抗力大、冷变形强化敏感的高碳钢、中高合金 钢、轴承钢、不锈钢等。 4.等温锻 在锻造全过程中,温度保持恒定不变的锻造方法称为等温锻。
避免锥形、楔形结构
三、自由锻零件结构工艺性
3、应避免圆柱面与圆柱面、圆柱面与棱柱面相交; 避免圆柱面与圆柱面、圆柱面与棱柱面相交
三、自由锻零件结构工艺性 4、零件上不允许有加强筋;
三、自由锻零件结构工艺性 5、对横截面尺寸相差很大或形状复杂的零件,应尽可能分别对其进 行锻造,然后用螺纹连接。
如下图:螺纹连接
(四)高合金钢的锻后冷却 由于高合金钢的导热性差,塑性低,终锻温度较高,如果冷却速度
快,会因热应力和组织应力使锻件出现裂纹。因此,终锻后应尽快采取 工艺措施保证锻件缓慢冷却。
金属模锻工艺
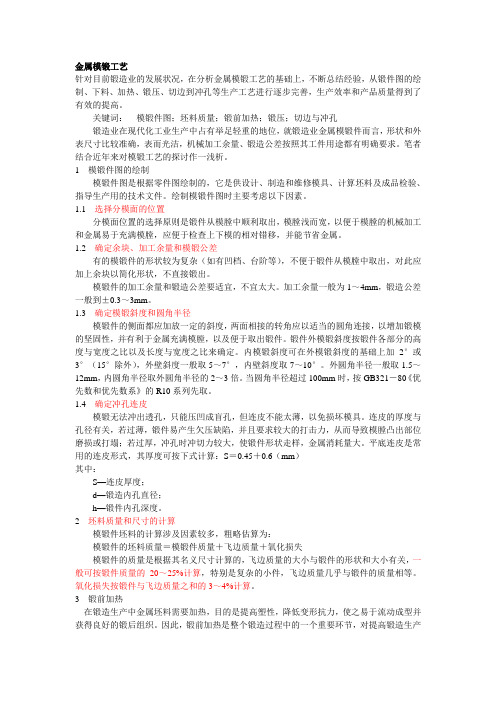
金属模锻工艺针对目前锻造业的发展状况,在分析金属模锻工艺的基础上,不断总结经验,从锻件图的绘制、下料、加热、锻压、切边到冲孔等生产工艺进行逐步完善,生产效率和产品质量得到了有效的提高。
关键词:模锻件图;坯料质量;锻前加热;锻压;切边与冲孔锻造业在现代化工业生产中占有举足轻重的地位,就锻造业金属模锻件而言,形状和外表尺寸比较准确,表而光洁,机械加工余量、锻造公差按照其工件用途都有明确要求。
笔者结合近年来对模锻工艺的探讨作一浅析。
1模锻件图的绘制模锻件图是根据零件图绘制的,它是供设计、制造和维修模具、计算坯料及成品检验、指导生产用的技术文件。
绘制模锻件图时主要考虑以下因素。
1.1选择分模面的位置分模面位置的选择原则是锻件从模膛中顺利取出,模膛浅而宽,以便于模膛的机械加工和金属易于充满模膛,应便于检查上下模的相对错移,并能节省金属。
1.2确定余块、加工余量和模锻公差有的模锻件的形状较为复杂(如有凹档、台阶等),不便于锻件从模膛中取出,对此应加上余块以简化形状,不直接锻出。
模锻件的加工余量和锻造公差要适宜,不宜太大。
加工余量一般为1~4mm,锻造公差一般到±0.3~3mm。
1.3确定模锻斜度和圆角半径模锻件的侧面都应加放一定的斜度,两面相接的转角应以适当的圆角连接,以增加锻模的坚固性,并有利于金属充满模膛,以及便于取出锻件。
锻件外模锻斜度按锻件各部分的高度与宽度之比以及长度与宽度之比来确定。
内模锻斜度可在外模锻斜度的基础上加2°或3°(15°除外),外壁斜度一般取5~7°,内壁斜度取7~10°。
外圆角半径一般取1.5~12mm,内圆角半径取外圆角半径的2~3倍。
当圆角半径超过100mm时,按GB321-80《优先数和优先数系》的R10系列先取。
1.4确定冲孔连皮模锻无法冲出透孔,只能压凹成盲孔,但连皮不能太薄,以免损坏模具。
连皮的厚度与孔径有关,若过薄,锻件易产生欠压缺陷,并且要求较大的打击力,从而导致模膛凸出部位磨损或打塌;若过厚,冲孔时冲切力较大,使锻件形状走样,金属消耗量大。
锻件图的绘制

锻件图的绘制圆角半径(一)圆角半径的确定锻件上的凸角圆角半径为外圆角半径r,凹角圆角半径为内圆角半径R(见图14)。
外圆角作用是避免锻模的相应部分因产生应力集中造成开裂;内圆角作用是使金属易于流动充满模膛,避免产生折叠,防止模膛压塌变形。
为保证锻件凸角处的最小余量,按下式计算:r1=余量+零件的倒角值若零件无倒角,按:r2=余量圆角半径(r、R)的数值根据锻件各部分的高度与宽度比值H/B(见图14),查表16确定。
表16 圆角半径计算表(JB3835-85)为了简化制造模具所用刀具的规格,圆角半径应按以下系列选用:1 1.52 2.53456 8 10 12 15mm。
圆角半径大于15mm时,逢5递增。
(二)圆角半径公差一般情况下内外圆角半径公差不要求检查,需要时可按表15查得。
示例某一齿轮零件的外径为171.8mm,全高48mm,计算其锻件重量为4.63kg,包容体重量为10.18kg,形状复杂系数为S3级;材料牌号18CrMnTi,材质系数为M1级;精度等级为普通级。
由表1、表2、表3、表5、表8查得锻件的机械加工余量及公差绘制出锻件图(见图20)。
由于需方未提出特殊要求,其技术要求按一般锻件质量要求列于锻件图下方。
图20 齿轮锻件图技术要求1.未注明模锻斜度7°2.未注明圆角半径R3mm3.错差可达1mm4.残留飞边可达1mm5.平面度可达0.8mm6.表面缺陷深度在加工表面不大于实际加工余量的1/2;不加工面不大于厚度公差的1/3。
7.热处理硬度d B≥4.2~4.8(HB156~207)8.清除氧化铁皮冲孔连皮及肓孔当孔径d≥25mm,冲孔深度h不大于冲头直径d时,此类锻件可在模锻过程中进行冲孔,然后在切边压力机上冲去连皮,获得带透孔的锻件。
冲孔连皮肓孔可分为如下四类:(一)平底连皮按照锻件的孔径和高度尺寸由图15查出平底连皮的厚度尺寸。
图15 平底连皮图16 斜底连皮(二)斜底连皮当锻件的孔径较大(d>60mm),平底连皮较薄,阻碍金属外流,易使锻件内孔产生折叠和造成冲头号压塌。
锻件图设计

第三节 锻件图的设计锻模设计、工艺规程制订、模锻生产过程、锻模加工及锻件检验,都离不开锻件图。
锻件图分为冷锻件图和热锻件图,冷锻件图用于最终锻件检验和热锻件图设计;热锻件图用于锻模设计与加工制造。
习惯上将冷锻件图称为锻件图。
1.1 冷锻件图的设计冷锻件图根据零件图设计,通常要解决下列问题。
1.1.1 确定分模面模锻件是在可分的模腔中成形,组成模具型腔的各模块的分合面称为“分模面”;分模面与锻件表面的交线称为锻件的“分模线”。
锻件分模位置合适与否,直接关系到锻件成形、出模,材料利用率等一系列问题。
因此,分模线是模锻件最重要、最基本的结构要素。
确定分模位置最基本的原则是:保证锻件形状尽可能与零件形状相同,容易从模腔中取出;此外应争取获得镦粗成形。
故此,锻件分模位置应选在具有最大水平投影尺寸的位置上,如图6-5所示。
为了提高锻件质量和生产过程的稳定性,除满足上述分模原则外,确定开式模锻件的分模位置还应考虑下列要求:1. 为使分模结构尽量简单和便于发现上下模在模锻过程中的错移,分模平面尽可能采用直线状,并应使分模线选在锻件侧面的中部,如图6-5和图6-6所示。
2.头部尺寸较大的长轴类锻件,不宜直线分模,而应改用折线分模,如图6-7所示,使上下模型腔深度大致相等,以确保尖角处能充填饱满。
3. 为便于锻模加工制造和锻件切边,同时也为了节约金属材料,当圆饼类锻件的H ≤(2.5~3)D 时,则无论是在锤上锻造还是在曲柄压力机上锻造或螺旋压力机上锻造,都应考虑径向分模(图4-8a ),而尽量不采用轴向分模(图6-8b )。
因径向分模的锻模型槽可车削加工,效率高,工时省,切边模刃口形状简单,制造方便;径向分模还可锻出内腔,节约金属。
但当H/D 较大时,锤上模锻时,显然不能再考虑 图6-5 直线类锻件分模位置图6-6 分模位置选择 图6-7 折线分模径向分模。
若仍采用径向分模,则因模具高度尺寸太大,锻造困难,锻锤打击能量下降,需要的出模力也大。
- 1、下载文档前请自行甄别文档内容的完整性,平台不提供额外的编辑、内容补充、找答案等附加服务。
- 2、"仅部分预览"的文档,不可在线预览部分如存在完整性等问题,可反馈申请退款(可完整预览的文档不适用该条件!)。
- 3、如文档侵犯您的权益,请联系客服反馈,我们会尽快为您处理(人工客服工作时间:9:00-18:30)。
锻件图的绘制圆角半径(一)圆角半径的确定锻件上的凸角圆角半径为外圆角半径r,凹角圆角半径为内圆角半径R(见图14)。
外圆角作用是避免锻模的相应部分因产生应力集中造成开裂;内圆角作用是使金属易于流动充满模膛,避免产生折叠,防止模膛压塌变形。
为保证锻件凸角处的最小余量,按下式计算:r1=余量+零件的倒角值若零件无倒角,按:r2=余量圆角半径(r、R)的数值根据锻件各部分的高度与宽度比值H/B(见图14),查表16确定。
表16 圆角半径计算表(JB3835-85)为了简化制造模具所用刀具的规格,圆角半径应按以下系列选用:1 1.52 2.53456 8 10 12 15mm。
圆角半径大于15mm时,逢5递增。
(二)圆角半径公差一般情况下内外圆角半径公差不要求检查,需要时可按表15查得。
示例某一齿轮零件的外径为171.8mm,全高48mm,计算其锻件重量为4.63kg,包容体重量为10.18kg,形状复杂系数为S3级;材料牌号18CrMnTi,材质系数为M1级;精度等级为普通级。
由表1、表2、表3、表5、表8查得锻件的机械加工余量及公差绘制出锻件图(见图20)。
由于需方未提出特殊要求,其技术要求按一般锻件质量要求列于锻件图下方。
图20 齿轮锻件图技术要求1.未注明模锻斜度7°2.未注明圆角半径R3mm3.错差可达1mm4.残留飞边可达1mm5.平面度可达0.8mm6.表面缺陷深度在加工表面不大于实际加工余量的1/2;不加工面不大于厚度公差的1/3。
7.热处理硬度d B≥4.2~4.8(HB156~207)8.清除氧化铁皮冲孔连皮及肓孔当孔径d≥25mm,冲孔深度h不大于冲头直径d时,此类锻件可在模锻过程中进行冲孔,然后在切边压力机上冲去连皮,获得带透孔的锻件。
冲孔连皮肓孔可分为如下四类:(一)平底连皮按照锻件的孔径和高度尺寸由图15查出平底连皮的厚度尺寸。
图15 平底连皮图16 斜底连皮(二)斜底连皮当锻件的孔径较大(d>60mm),平底连皮较薄,阻碍金属外流,易使锻件内孔产生折叠和造成冲头号压塌。
采用斜底连皮(见图16),连皮斜度增加了连皮和内孔接触处的连皮厚度,促进金属往外流动,避免产生折叠,冲头不易损坏,斜底连皮的尺寸如下:S max=1.35SS min=0.65Sd1=(0.25~0.35)d式中S—采用平底连皮的厚度。
在连皮中部d1处为平底,以便坯料摆放在模膛上定位;并使连皮有更大斜度,以利金属流动。
(三)带仓连皮在锻模的预锻模膛(或镦粗模膛)采用斜底连皮,而终锻模膛采用带仓连皮(见图17),终锻时将锻件的斜底连皮部分金属不是大量外流,而是流向仓部,仓部体积应考虑能容纳预锻后锻件斜底连皮的金属体积,避免锻件产生折叠。
带仓连皮的厚度S及宽度 b 采用锻模飞边桥口的厚度与宽度。
终锻后,因连皮厚度较薄,容易冲切,在冲孔时锻件不易变形。
图17 带仓连皮图18 拱式带仓连皮对孔径较大而高度较小的锻件可采用拱式带仓连皮(见图18),可促使孔内金属排向四周,又可容纳相当部分的金属,避免锻件产生折叠,减轻冲头磨损,减小锻击变形力。
(四)肓孔对于孔径较小(d<25mm=,且高度较大的锻件,只在锻件上压出凹穴,模锻后不再将孔冲穿,锻件上留下有肓孔(见图19a、b)。
肓孔可以缩小该部分截面的面积,且有利于充满终锻模膛,但对机械加工并不完全有利。
图19 锻件上的盲孔模锻斜度(一)模锻斜度的确定锻件侧面设有模锻斜度便于模锻后脱模。
模锻斜度分外斜度和内斜度。
锻件冷却时趋向离开模壁的部分称为外斜度,用α表示;反之称为内斜度,用β表示(见图14)。
锤上模锻的锻件外斜度值根据锻件各部分的高度与宽度之比值H/B,及长度与宽度之比值L/B(见图14),查表13确定。
内斜度按外斜度增大2°或3°。
如上下模膛深度不相等,应按模膛较深一侧计算模锻斜度。
热模锻压力机和螺旋压力机上使用顶料机构时,模锻斜度可比表13数值减小2°或3°。
平锻件模锻斜度由表14查得。
图14 模锻斜度表13 锤上模锻件模锻斜度数值表(JB3835-85)表14 平锻件各类模锻斜度数值表(JB3835-85)(二)模锻斜度公差模锻斜度公差值根据锻件高度尺寸和精度级别在表15中查得,一般情况下,不作要求和检查。
表15 模锻件的内外圆角半径和模锻斜度公差(JB3834-85)注:1.在测量模锻斜度公差时,其锻件高度尺寸应去掉R值,只测量到α点。
在R(r)部分,按R(r)公差测量。
2. r—外圆角半径;R—内圆角半径。
3.本表适用于在热模锻压力机、模锻锤、平锻机及螺旋压力机上生产的模锻件。
分模线(面)的选择在模锻锤、热模锻压力机、螺旋压力机和平锻机上成批生产的重量不超过250kg,长度不超过2500mm的钢质(碳钢和合金钢)模锻件(以下简称模钢件),在制订锻件图时,需要正确的选择分模面,选定机械加工余量及公差,选用模锻斜度与圆角半径,确定冲孔连皮,并在技术条件内说明交货要求和在锻件图上所不能标明的技术要求与允许偏差。
分模面分两类:1)平面分模面和对称弯曲分模面(见图1a、b)2)不对称的弯曲分模面(见图1c)。
图1 分模线形状选择分模面应考虑下列主要条件:能自由地从模膛中取出锻件;最佳的金属充满模膛条件(镦粗比挤入更容易将金属充满模膛);力求减少余块和飞边损耗;简化模锻工艺和模膛制造工艺(如圆形短轴类锻件尽量选用圆形的分模面)等。
锻件的技术要求凡有关锻件的质量及其检验等问题,在图样中无法表示或不便表示时,均应在锻件图的技术要求中用文字说明,其主要内容如下:1)未注模锻斜度;2)未注圆角半径;3)表面缺陷深度的允许值,必要时应分别注明锻件在加工表面和不加工表面的表面缺陷深度允许值;4)分模面错差的允许值;5)残留飞边与切入深度的允许值。
根据锻件形状特点及不同工艺方法,必要时应分别注明周边、内孔、叉口、纵向、横向等不同部位残余飞边和切入深度的允许值;6)热处理方法及硬度值;7)表面氧化皮的清理方法及要求;8)锻件杆部局部变粗的允许值;9)对未注明的锻件尺寸公差,应注明其公差标准代号及尺寸精度级别或具体公差数值;10)其他要求:如探伤、低倍组织、纤维组织、力学性能、过热和脱炭、质量公差、特殊标记、防腐及包装发运要求等。
锻件技术要求的允许值,除特殊要求外均按JB3835-85和JB3834-85的规定确定。
技术要求的顺序,原则上应按锻件生产过程中检验的先后进行排列。
机械加工余量和锻件尺寸公差的确定(一)主要参数及影响因素1.锻件重量(G1)根据锻件图的尺寸计算锻件的重量。
对于杆部不参与变形(不锻棒料部分)的平锻件重量只计算镦锻部分(见图2a)。
若不锻棒料部分的长度与其直径之比小于2时,可看作一个完整的锻件来计算其重量(见图2b)。
若平锻件的两端分两次镦锻时,前一道镦锻成形部分连同不锻棒料杆部部分,视为第二道镦锻部分的不锻棒料部分(见图2c)。
2.锻件形状复杂系数(S)锻件形状复杂系数为锻件重量(G1)与相应的锻件外廓包容体重量(G2)的比值。
即:S=图2 镦锻件重量计算特点a)一头一长杆;b)一头一短杆;c)二头一杆;A 镦锻部分;B 不锻棒料部分;C 第一道成形圆形锻件的外廓包容体重量(见图3):式中:ρ—密度(7.85/cm3)图3 圆形锻件的外廓包容体非圆形锻件外廓包容体重量(见图4):图4 非圆形锻件外廓包容体锻件形状复杂系数分为四级:简单:S1>0.63~1一般:S2>0.32~0.63较复杂:S3>0.16~0.32复杂:S4≤0.16特例:当锻件为薄形圆盘或法兰件(见图5a),其圆盘厚度和直径之比L/d≤0.2时,取形状复杂系数S4。
当L1/d1≤0.2或L2/d2>4时(见图5b),采用形状复杂系数S4。
当冲孔深度大于直径的1.5倍时,形状复杂系数提高一级。
图5 锻件形状复杂特例3.锻件的材质系数锻件的材质系数分为二级:M1:钢的含碳量小于0.65%的碳钢,或合金元素总含量小于3.0%的合金钢。
M2:钢的含碳量大于或等于0.65%的碳钢,或合金元素总含量大于或等于3.0%的合金钢。
4.零件的机械加工精度零件表面粗糙度低于R a1.6,机械加工余量从余量表查得;粗糙度高于R a1.6,加工余量要适当加大;对扁薄截面或在锻件相邻部位截面变化较大的零件(如图6),在长度L 范围内应适当加大局部的余量。
图6 应局部增大余量的零件5.加热条件采用煤气或油炉加热钢坯时,机械加工余量和公差从余量表和公差表查得;当采用煤加热钢坯,或经二火进行加热时,适当增大加工余量和公差。
6.其他条件锻件轮廓尺寸、采用工序、锻件精度等若有特殊要求,可适当增大或减小加工余量和公差。
(二)机械加工余量确定机械加工余量时,根据锻件估算质量,形状复杂系数和零件加工精度要求,由表1、表2查得。
对于需要附加工序的锻件,其余量值由供需双方协商确定。
(三)锻件公差造成模锻件尺寸波动的主要原因有:欠压;金属不充满模膛;模具磨损或变形;模具设计时锻件收缩率选取的不准确;终锻模膛制造公差;锻造设备精度变化;模具错移;工人操作误差等。
表2 锻件内孔直径的单边机械加工余量(JB3834-85)锻件公差分为普通级和精密级。
1.长度、宽度和高度公差长度、宽度和高度公差是指在分模面一侧,同一块模具上,沿长度、宽度和高度方向的尺寸公差(见图7a),由表3,表4查得。
当锻件形状复杂系数为S1、S2级,且长宽比小于3.5时,选用同一公差值,以简化工作量。
平锻件的杆部长度尺寸公差是指镦锻部分的内侧到锻件末端之间的距离,包括不锻的棒料长度及台阶部分的总长度尺寸公差,按总长度和质量在表3中查得杆部长度公差。
对于两端都进行镦锻的平锻件,其长度公差是指某一端的镦锻部分的内侧至相对端面之间的距离(如图7b中长度尺寸L1和L2)的公差,但只可选L1或L2之中公差较大的一个标注在锻件图上。
图7 锻件长度、宽度和高度公差a—长度方向尺寸;b—宽度方向尺寸;c—高度方向尺寸;d—跨越分模线的厚度尺寸表1 模锻件内外表面加工余量(JB3834-85)度度10.0注:本表适用于热模锻压力机,模锻锤,平锻机及螺旋压力机上生产的模锻件。
例:当锻件重量为3kg,在16000kN热模锻压力机上生产,零件无磨削精加工工序,锻件复杂系数S3锻件长度480mm,查出该零件的余量:厚度方向1.7-2.2mm,水平方向:2.0-2.7mm。
表3 模锻件的长度、宽度、高度公差及错差、残留飞边量(普通级)(JB3834-85)0.5 0 0.40.6 .00.7 .80.8 .21.0 .01.2 101.4 10 20注:锻件高度台阶尺寸公差,按±1/2的比例分配。