立装可转位槽铣刀的设计开发
整体硬质合金立铣刀的创新结构
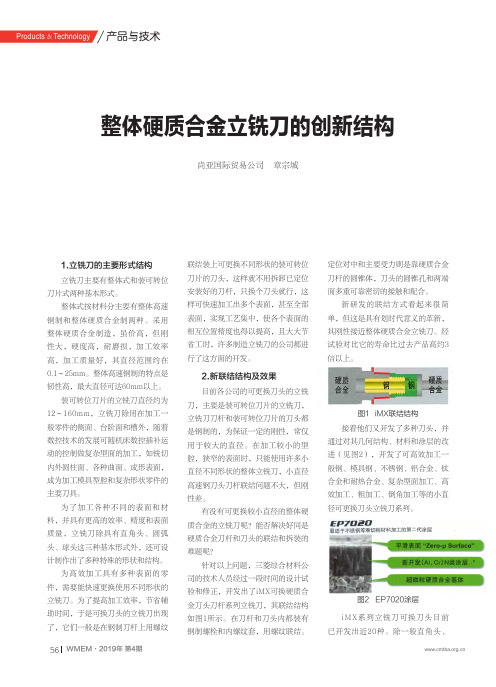
56WMEM·2019年 第4期Products & Technology产品与技术图1 iMX联结结构整体硬质合金立铣刀的创新结构尚亚国际贸易公司 章宗城1.立铣刀的主要形式结构立铣刀主要有整体式和装可转位刀片式两种基本形式。
整体式按材料分主要有整体高速钢制和整体硬质合金制两种。
采用整体硬质合金制造,虽价高,但刚性大,硬度高,耐磨损,加工效率高,加工质量好,其直径范围约在0.1~25mm。
整体高速钢制的特点是韧性高,最大直径可达60mm以上。
装可转位刀片的立铣刀直径约为12~160mm,立铣刀除用在加工一般零件的侧面、台阶面和槽外,随着数控技术的发展可随机床数控插补运动的控制做复杂型面的加工,如铣切内外圆柱面、各种曲面、成形表面,成为加工模具型腔和复杂形状零件的主要刀具。
为了加工各种不同的表面和材料,并具有更高的效率、精度和表面质量,立铣刀除具有直角头、圆弧头、球头这三种基本形式外,还可设计制作出了多种特殊的形状和结构。
为高效加工具有多种表面的零件,需要能快速更换使用不同形状的立铣刀。
为了提高加工效率,节省辅助时间,于是可换刀头的立铣刀出现了,它们一般是在钢制刀杆上用螺纹联结装上可更换不同形状的装可转位刀片的刀头,这样就不用拆卸已定位安装好的刀杆,只换个刀头就行,这样可快速加工出多个表面,甚至全部表面,实现工艺集中,使各个表面的相互位置精度也得以提高,且大大节省工时,许多制造立铣刀的公司都进行了这方面的开发。
2.新联结结构及效果目前各公司的可更换刀头的立铣刀,主要是装可转位刀片的立铣刀,立铣刀刀杆和装可转位刀片的刀头都是钢制的,为保证一定的刚性,常仅用于较大的直径。
在加工较小的型腔,狭窄的表面时,只能使用许多小直径不同形状的整体立铣刀,小直径高速钢刀头刀杆联结问题不大,但刚性差。
有没有可更换较小直径的整体硬质合金的立铣刀呢?能否解决好同是硬质合金刀杆和刀头的联结和拆装的难题呢?针对以上问题,三菱综合材料公司的技术人员经过一段时间的设计试验和修正,开发出了iMX可换硬质合金刀头刀杆系列立铣刀,其联结结构如图1所示。
国际刀具标准(车削、铣削、钻削、铰削、锯削、螺纹刀具)
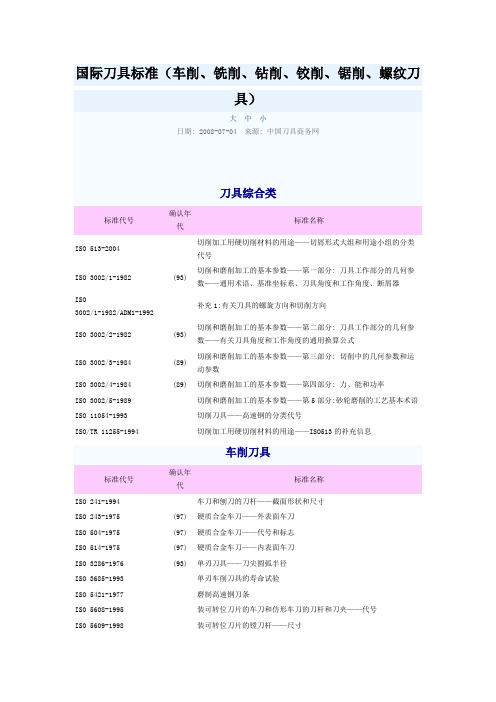
直孔平键传动的三面刃铣刀——米制系列
ISO 2940/1-1974
(97)
装在7/24锥柄定心刀杆上的铣刀——配合尺寸——定心刀杆
ISO 2940/2-1974
(97)
装在7/24锥柄心轴上的镶齿套式面铣刀
ISO 3337-2000
直柄和莫氏锥柄T型槽铣刀
ISO 3338/1-1996
铣刀直柄——第一部分:普通直柄的尺寸
ISO 3338/2-2000
铣刀直柄——第二部分:削平型直柄的尺寸
ISO 3338/4-1996
铣刀直柄——第四部分:螺纹柄的尺寸
ISO 3855-1977
铣刀——名词术语
ISO 3855-1977/Coa1:1996
技术勘误1
ISO 3859-2000
直柄反燕尾槽铣刀和直柄燕尾槽铣刀
ISO 3860-1976
ISO 10889/4-1997
直柄刀夹——第四部分:带矩形轴向刀座的C型刀夹
ISO 10889/5-1997
直柄刀夹——第五部分:带两个以上矩形刀座的D型刀夹
ISO 10889/6-1997
直柄刀夹——第六部分:带圆形刀座的E型刀夹
ISO 10889/7-1997
直柄刀夹——第七部分:带锥形刀座的F型刀夹
国际刀具标准(车削、铣削、钻削、铰削、锯削、螺纹刀具)
大中小
日期:2008-07-04来源:中国刀具商务网
刀具综合类
标准代号
确认年代
标准名称
ISO 513-2004
切削加工用硬切削材料的用途——切屑形式大组和用途小组的分类代号
ISO 3002/1-1982
(93)
切削和磨削加工的基本参数——第一部分:刀具工作部分的几何参数——通用术语、基准坐标系、刀具角度和工作角度、断屑器
肯纳金属公司推出新的可转位铣刀

、 z 幕朋 、 … I I 等
7 .
新 的 B y n K P 2 e o d C M 0目标 是 成 为 同 类 纯 钢 及 合 金 端 面 、 方 肩 和 仿 形 铣
削 的 理想 选 择 。
用 ,例 如 : 钢 梁 和 铝 基 板 ,最 高 可 允 许 缓 慢 动 态 移 动 2 货 物 。这 就 意 味 着 t 仅 需 4 “ r L n 滑 动 垫 片 , 就 能 块 D yi”
诺德推 出新型两 阶段螺旋 斜面 变速箱
肯纳金属公 司推 出新的 可转位铣刀
在 此次新产 品发布会上 ,山高向 市场推 出 了多款 新产 品 ,既有 设计新
颖 、 结 构 独 特 的 全 新 刀 具 , 也 有 众 多
推 陈 出新的换代 产 品,新产 品涵盖 了 车 、铣 、钻 、铰 、新材 质等级 等几乎
有 限公 司给 予 了高度 的重视 和做 了充 分 的准 备 。 山高 集 团市 场 发 展 经 理 Mra Alos a i h f r 、山高 中国技术总监王 玮 、市场 总监王 魄、北方 区销售 经理 康博 、产 品管理部 经理相华 峰等 公司
领 导 悉 数 到 场 。近 7 名 客 户 代 表 出 席 0 了新 产 品发 布 会 。
・
系列、M 槽型 、P D 5 C 钻头C 3 系列、小 X1
内切 圆 刀 片 、S U R 6 0 魔 方 方 肩 Q AE - 4 铣 刀 、P e i a t r 材 质 等 级 X 0 0 r em se新 20 & R 1 0 、T R O 0 肩 铣 。与 此 同 X 5 0 U B 1方
材 料 。 由此 材 料 构 成 的 新 的滚 珠 轴 承 ,耐磨 性和 使用寿 命远远 高 于现 有
可转位车刀的设计方案

一、车刀的结构机夹可转位车刀是将可转位硬质合金刀片用机械的方法夹持在刀杆上形成的车刀,一般由刀片、刀垫、夹紧元件和刀体组成(见图1)。
图1 机夹可转位车刀组成根据夹紧结构的不同可分为以下几种形式。
·偏心式(见图2)偏心式夹紧结构利用螺钉上端的一个偏心心轴将刀片夹紧在刀杆上,该结构依靠偏心夹紧,螺钉自锁,结构简单,操作方便,但不能双边定位。
当偏心量过小时,要求刀片制造的精度高,若偏心量过大时,在切削力冲击作用下刀片易松动,因此偏心式夹紧结构适于连续平稳切削的场合。
图2 偏心式夹紧结构组成·杠杆式(见图3)杠杆式夹紧结构应用杠杆原理对刀片进行夹紧。
当旋动螺钉时,通过杠杆产生夹紧力,从而将刀片定位在刀槽侧面上,旋出螺钉时,刀片松开,半圆筒形弹簧片可保持刀垫位置不动。
该结构特点是定位精度高、夹固牢靠、受力合理、适用方便,但工艺性较差。
图3 杠杆式夹紧结构组成·楔块式(见图4)刀片内孔定位在刀片槽的销轴上,带有斜面的压块由压紧螺钉下压时,楔块一面靠紧刀杆上的凸台,另一面将刀片推往刀片中间孔的圆柱销上压紧刀片。
该结构的特点是操作简单方便,但定位精度较低,且夹紧力与切削力相反。
图4 楔块式夹紧结构不论采用何种夹紧方式,刀片在夹紧时必须满足以下条件:①刀片装夹定位要符合切削力的定位夹紧原理,即切削力的合力必须作用在刀片支承面周界内。
②刀片周边尺寸定位需满足三点定位原理。
③切削力与装夹力的合力在定位基面(刀片与刀体)上所产生的摩擦力必须大于切削振动等引起的使刀片脱离定位基面的交变力。
夹紧力的作用原理如表1所示。
可转位车刀片的形状有三角形、正方形、棱形、五边形、六边形和圆形等,是由硬质合金厂压模成形,使刀片具有供切削时选用的几何参数(不需刃磨);同时,刀片具有3个以上供转位用的切削刃,当一个切削刃磨损后,松开夹紧机构,将刀片转位到另一切削刃,即可进行切削,当所有切削刃都磨损后再取下,换上新的同类型的刀片。
山特维克在可转位铣刀领域的专利技术综述
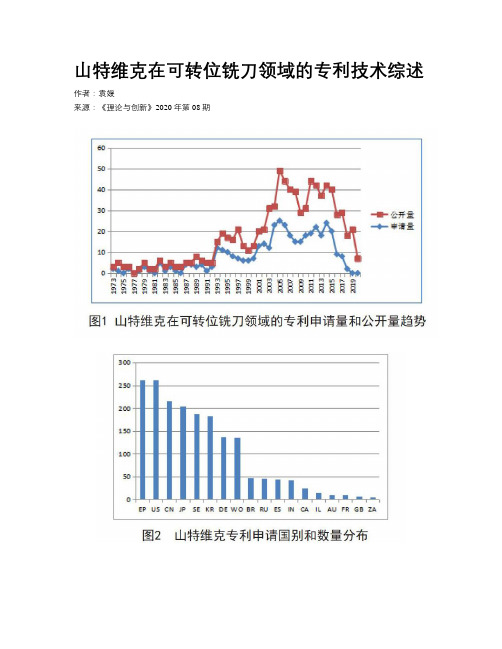
山特维克在可转位铣刀领域的专利技术综述作者:袁媛来源:《理论与创新》2020年第08期引言山特维克集团是全球领先的先产品制造商,在中国的专利申请量达到了1583件,刀具作为山特维克的优势产业,资金投入和研发力度也很可观,专利申请量为564件。
目前可转位铣刀的专利申请主要分为五个方向。
山特维克在中国的专利申请中,可转位铣刀领域的申请量为209件。
1.山特维克在可转位铣刀领域的专利概况图1中可以看出,早在1971年,山特维克就已经有涉及可转位铣刀的专利申请,1993年,专利申请量达到12件。
2000年以后,山特维克兼并收购了多家刀具巨头公司,通过一系列的战略收购,增强研发实力,确立了强大的市场地位,专利申请量大幅度提升。
图2所示为山特维克公司的专利申请国别分布,可以看出该公司的专利布局情况。
早在1987年,中国专利局建立之初,就开始了在中国的专利申请,说明山特维克特别重视中国市场。
图3为山特维克公司在该领域的专利申请方向。
该公司在可转位刀片的夹固方向的申请量最大,其次是可转位刀片的结构。
该公司在这两个技术分支的研发投入相对比较大。
2.专利技术发展路线可转位铣刀的研究始终围绕高精度、高效率以及高经济型这一主线展开,尤其是在高速高效切削技术产生之后,可转位铣刀的新技术不断涌现,形成了其特定的多分支发展路线,参见图4。
其中主要在可转位刀片的结构和夹固这两个方向改进,山特维克公司的专利申请和研发的方向与国际在该领域的发展方向是一致的。
2.1可转位刀片方向的技术发展路线图3为山特维克公司在可转位刀片方向的发展路线,主要包括以下四个方面:(1)从增加单面刀片刃数到双面刃刀片,不断提高经济性。
初期的可转位刀片仅有2-3个切削刃,各生产厂家为提高自身产品的竞争力,不断试图增加切削刃的数量。
从单面刀片到双面刀片,需要避免装夹过程中对刀刃的磨损。
山特维克的可转位刀片从FR2145291(1972年)的正方形单面四刃,到CN1035785(1987年)的正方形双面多刃,再到US2003210961(2001年)圆形单面多刃,不断的改进刀片的形状,在满足装夹和加工精度的基础上,增加刀片的刃数,以使得刀片能够多次转位使用。
可转位球头立铣刀的建模
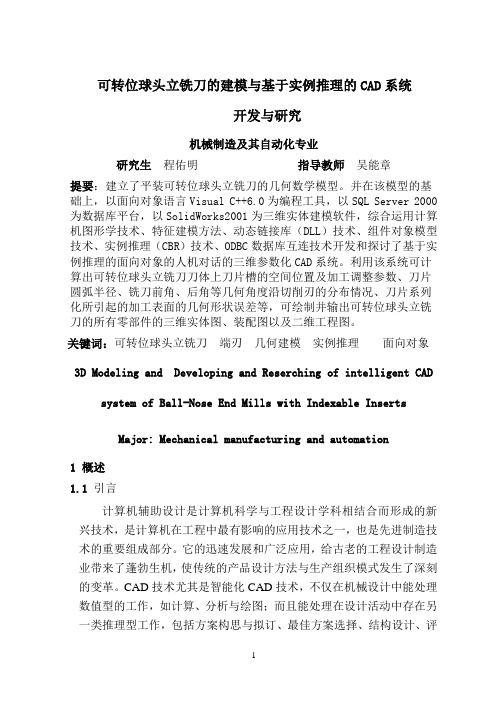
可转位球头立铣刀的建模与基于实例推理的CAD系统开发与研究机械制造及其自动化专业研究生程佑明指导教师吴能章提要:建立了平装可转位球头立铣刀的几何数学模型。
并在该模型的基础上,以面向对象语言Visual C++6.0为编程工具,以SQL Server 2000为数据库平台,以SolidWorks2001为三维实体建模软件,综合运用计算机图形学技术、特征建模方法、动态链接库(DLL)技术、组件对象模型技术、实例推理(CBR)技术、ODBC数据库互连技术开发和探讨了基于实例推理的面向对象的人机对话的三维参数化CAD系统。
利用该系统可计算出可转位球头立铣刀刀体上刀片槽的空间位置及加工调整参数、刀片圆弧半径、铣刀前角、后角等几何角度沿切削刃的分布情况、刀片系列化所引起的加工表面的几何形状误差等,可绘制并输出可转位球头立铣刀的所有零部件的三维实体图、装配图以及二维工程图。
关键词:可转位球头立铣刀端刃几何建模实例推理面向对象3D Modeling and Developing and Reserching of intelligent CAD system of Ball-Nose End Mills with Indexable Inserts Major: Mechanical manufacturing and automation1 概述1.1引言计算机辅助设计是计算机科学与工程设计学科相结合而形成的新兴技术,是计算机在工程中最有影响的应用技术之一,也是先进制造技术的重要组成部分。
它的迅速发展和广泛应用,给古老的工程设计制造业带来了蓬勃生机,使传统的产品设计方法与生产组织模式发生了深刻的变革。
CAD技术尤其是智能化CAD技术,不仅在机械设计中能处理数值型的工作,如计算、分析与绘图;而且能处理在设计活动中存在另一类推理型工作,包括方案构思与拟订、最佳方案选择、结构设计、评论、决策以及参数选择和形成专家系统等,这就为企业缩短产品设计周期、增强市场应变能力、参与国际市场竞争提供了强有力的技术手段,已经产生、必将继续产生巨大的社会经济效益。
可转位车刀课程设计

机械设计制造及其自动化专业(卓越工程师)设计说明书(金属切削原理与刀具)题目:楔块式90 强力车刀学院:机械工程学院专业:机械设计制造及其自动化姓名:指导教师:完成日期:2013年11月1日佳木斯大学机械工程学院2013年11月目录第一章设计要求 (3)第二章设计步骤 (4)(1)选择刀片夹固结构 (4)(2)选择刀片材料 (4)(3)选择车道合理角度 (4)(4)选择切削用量 (4)(5)选择刀片型号和尺寸 (5)(6)选择硬质合金刀垫型号和尺寸 (6)(7)计算刀槽角度 (7)(8)计算铣制刀槽时需要的角度 (9)(9)选择刀杆材料和尺寸 (11)参考文献 (12)第一章设计要求设计要求楔块式90°强力车刀工件材料:2Cr13 Ra=12.5机床:C620推荐数据:v c=140~200m/min,a p=4~8mm,f=0.5~0.7mm/r第二章 设计步骤(1)选择刀片夹固结构按要求选择楔块式夹固结构。
(2)选择刀片材料由原始条件给定:被加工工件材料为2Cr13不锈钢,按照硬质合金的选用原则,查表4-11[]1可知选择刀片材料为YG8。
(3)选择车道合理角度根据车刀合理几何参数的选择原则,并考虑到可转位车刀几何角度的形成特点,选取如下四个主要角度:1)前角0γ=15︒; 2)后角0α=8︒; 3)主偏角r κ=90︒; 4)刃倾角s λ=-6︒;后角o α的实际数值以及副后角'o α和副偏角'r K 在计算刀槽角度时,经校验后确定。
(4)选择切削用量根据切削用量的选择原则,查表4-11[]1及按照推荐值确定切削用量为:背吃刀量p a =5mm ;进给量f=0.6mm/r ; 切削速度V c =150m/min ;(5)选择刀片型号和尺寸1)选择刀片有无中心固定孔:由于刀片夹紧结构已选为压块式,因此应选有中固定孔的刀片。
2)选择刀片形状:按选定的主偏角K r =90︒,根据硬质合金可转位刀片的选择原则[]2,在这里选用三角形刀片。
可转位车刀几何角度的设计、加工及检测
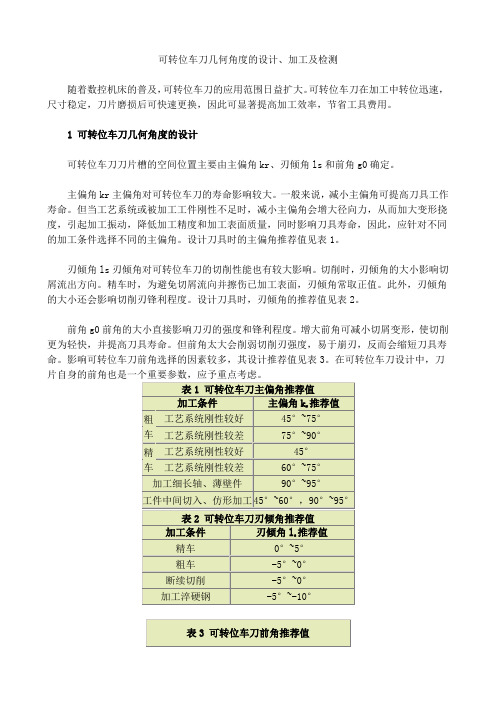
可转位车刀几何角度的设计、加工及检测随着数控机床的普及,可转位车刀的应用范围日益扩大。
可转位车刀在加工中转位迅速,尺寸稳定,刀片磨损后可快速更换,因此可显著提高加工效率,节省工具费用。
1 可转位车刀几何角度的设计可转位车刀刀片槽的空间位置主要由主偏角kr、刃倾角ls和前角g0确定。
主偏角kr主偏角对可转位车刀的寿命影响较大。
一般来说,减小主偏角可提高刀具工作寿命。
但当工艺系统或被加工工件刚性不足时,减小主偏角会增大径向力,从而加大变形挠度,引起加工振动,降低加工精度和加工表面质量,同时影响刀具寿命,因此,应针对不同的加工条件选择不同的主偏角。
设计刀具时的主偏角推荐值见表1。
刃倾角ls刃倾角对可转位车刀的切削性能也有较大影响。
切削时,刃倾角的大小影响切屑流出方向。
精车时,为避免切屑流向并擦伤已加工表面,刃倾角常取正值。
此外,刃倾角的大小还会影响切削刃锋利程度。
设计刀具时,刃倾角的推荐值见表2。
前角g0前角的大小直接影响刀刃的强度和锋利程度。
增大前角可减小切屑变形,使切削更为轻快,并提高刀具寿命。
但前角太大会削弱切削刃强度,易于崩刃,反而会缩短刀具寿命。
影响可转位车刀前角选择的因素较多,其设计推荐值见表3。
在可转位车刀设计中,刀片自身的前角也是一个重要参数,应予重点考虑。
后角后角主要用于减小切削过程中后刀面与过渡表面之间的摩擦。
设计可转位车刀时,需要对后角与前角进行综合考虑,选定刀片后角后,再根据刀片槽前角确定刀片槽后角。
可转位车刀后角的设计推荐值见表4。
造型设计及图纸标注可转位车刀切削参数的图纸标注如图1所示。
用AutoCAD2000的实体功能设计可转位车刀时,首先根据加工条件选择刀片,然后减去刀片本身的前角和后角,即可确定设计可转位车刀所需全部参数。
进行实体造型设计时,不能完全按照所需刃倾角和前角来旋转刀片,而应将其换算为法向前角,换算公式为tangn=tang0cosls (1)实体造型时刀片旋转的顺序应为:主偏角→刃倾角→法向前角。
可转位车刀的选择及设计

可转位车刀的选择及设计1.在工程应用中的优点与缺点可转位车刀就是机夹式刀具,有刀片,刀排锁紧装置组成,车削时遇刀具磨损了,只要松开锁紧转一个角度紧固就能继续使用了,比焊接式普通刀具方便,可转位车刀:价格较高,形状是标准的,如果工件有临时变化那又要重新买了,因为这不能重磨。
由于不需要磨刀所以工人上手比较快,适合于大批量高精度的数控加工。
避免了硬质合金钎焊时容易产生裂纹的缺陷;可转位刀片适合用气相沉积法在硬质合金刀片表面沉积薄层更硬的材料(碳化钛氮化钛和氧化铝),以提高切削性能;换刀时间较短;由于可转位刀片是标准化和集中生产的,刀片几何参数一致性强,切屑控制稳定。
因此可转位刀具得到广泛应用,如各种车刀、镗刀、铣刀、外表面拉刀、大直径深孔钻和套料钻等2.主要应用领域可转位式刀具取代了焊接刀具,并且,应用,显示了它的优越性。
但是,推广速度仍然比较缓慢。
当然,原因是多方面的,其中,刀杆结构与刀片的精化(重磨)问题,在部份企业不易解决,是影响推广的因素之一。
3.刀片材料,选型中注意的几类问题多数可转位刀具的刀片采用硬质合金,也有采用陶瓷、多晶立方氮化硼或多晶金刚石车外圆的刀片:选用原则主要是根据加工工艺的具体情况决定。
一般要选通用性较高的及在同一刀片上切削刃数较多刀片。
粗车时选较大尺寸,精、半精车时选较小尺寸。
S形:四个刃口,刃口较短(指同等内切圆直径),刀尖强度较高,主要用于75°、45°车刀,在内孔刀中用于加工通孔。
T形:三个刃口,刃口较长,刀尖强度低,在普通车床上使用时常采用带副偏角的刀片以提高刀尖强度。
主要用于90°车刀。
在内孔车刀中主要用于加工盲孔、台阶孔。
C形:有两种刀尖角。
100°刀尖角的两个刀尖强度高,一般做成75°车刀,用来粗车外圆、端面,80°刀尖角的两个刃口强度较高,用它不用换刀即可加工端面或圆柱面,在内孔车刀中一般用于加工台阶孔。
硬质合金可转位车刀设计(待修改)
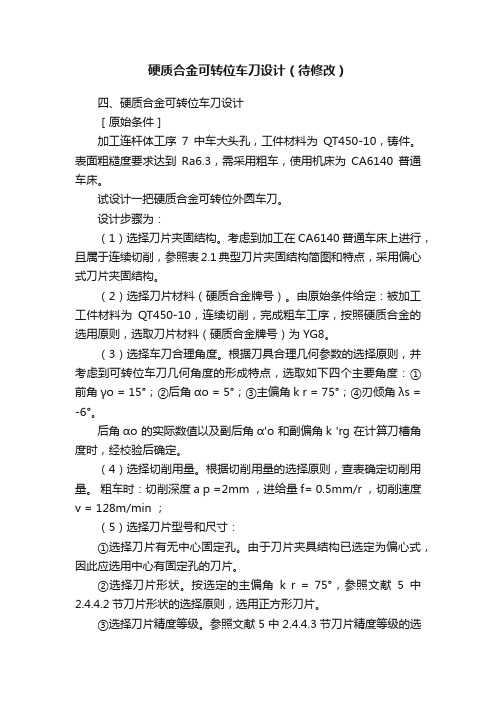
硬质合金可转位车刀设计(待修改)四、硬质合金可转位车刀设计[原始条件]加工连杆体工序7中车大头孔,工件材料为QT450-10,铸件。
表面粗糙度要求达到Ra6.3,需采用粗车,使用机床为CA6140普通车床。
试设计一把硬质合金可转位外圆车刀。
设计步骤为:(1)选择刀片夹固结构。
考虑到加工在CA6140普通车床上进行,且属于连续切削,参照表2.1典型刀片夹固结构简图和特点,采用偏心式刀片夹固结构。
(2)选择刀片材料(硬质合金牌号)。
由原始条件给定:被加工工件材料为QT450-10,连续切削,完成粗车工序,按照硬质合金的选用原则,选取刀片材料(硬质合金牌号)为YG8。
(3)选择车刀合理角度。
根据刀具合理几何参数的选择原则,并考虑到可转位车刀几何角度的形成特点,选取如下四个主要角度:①前角γo = 15°;②后角αo = 5°;③主偏角k r = 75°;④刃倾角λs = -6°。
后角αo 的实际数值以及副后角α'o 和副偏角k 'rg 在计算刀槽角度时,经校验后确定。
(4)选择切削用量。
根据切削用量的选择原则,查表确定切削用量。
粗车时:切削深度a p =2mm ,进给量f= 0.5mm/r ,切削速度v = 128m/min ;(5)选择刀片型号和尺寸:①选择刀片有无中心固定孔。
由于刀片夹具结构已选定为偏心式,因此应选用中心有固定孔的刀片。
②选择刀片形状。
按选定的主偏角k r = 75°,参照文献5中2.4.4.2节刀片形状的选择原则,选用正方形刀片。
③选择刀片精度等级。
参照文献5中2.4.4.3节刀片精度等级的选择原则,选用U 级。
④选择刀片内切圆直径d (或刀片边长L )。
根据已确定的a p =2.0mm ,k r = 75°和λs = -6°,将a p 、k r 和λs 代入文献5公式(2.5),可求出刀刃的实际参加工作长度L se 为L se =s r pk a λcos sin =)6cos(75sin 2?-?k =2.082mm则所选用的刀片边长L 应为L >1.5 L se =1.5×2.082=3.123mm因为是正方形刀片,所以 L=d >3.123mm⑤选择刀片厚度s 。
21472916

各个刀片分布合理 , 既要保证刀片空 间位置不发生
干涉 , 同时也要保证刀具切削平稳 。根据上述设计 原理 , 设计时依据用户提供的转子型线坐标, 合理选 用专用形状 的刀片: 阴螺杆转子铣刀齿顶部分采用 凸圆弧刃刀片, 阳螺杆转子铣刀齿顶部分采用簿的 、
陶瓷刀片材料具有高硬度 、 高耐磨性 、 高耐热性 、 优 良的化学稳定性和低 磨擦 系数等优点 , 因此可 以加 工高硬度的材料并能极大地提高被加工材料 的表面
加工件 : 车床床身 , 材质为铸铁 H 20 铸件 留量大 T0 ,
(5 m左右)不均匀并有夹砂。 1m ,
阴篡杆 转予铣刀型线简图 阳篡杆转子铣刀型线简图
图2
铣削试验在宁波欣达螺杆压缩机有限公司进 行 。试切条件 :
刀具 :20 m阴螺杆转子铣 刀 ,  ̄3m 有效齿数为 4 组; 试切机床 : 国产半 自 动螺杆专用机床 ; 被加工件 :
的端面跳动可 达到 O0m .1 m以内; 加工表面精度能 达转位螺杆转子铣刀是用于粗加工螺 杆压缩机转子 的专用铣刀。如图 2 所示 , 该类铣 刀
由阴、 阳两把铣刀组成 , 分别用于螺杆阴转子与阳转 子 的粗加工 。这种铣 刀科技含量高 , 设计难度较大 , 刀具选用的刀片型号较 多, 设计型线时要考虑保证 刀片充分搭接 , 型线符合公差要求 ; 实体造型时要使
一
厂 进行 。试 切 条件 为 :
刀具 :20 m陶瓷可 转位微调平 面精铣 刀,  ̄0m 6 齿, 铣刀端面跳 动 O0r .1 m以内; a 试切机床 : 龙门铣
维普资讯
20 06年第 4 0卷N 3 o
l5 l
进行。试切条件 : 刀具 : 硬质合金可转位机床床身组合铣刀 , 最小 处直径为  ̄4m , 22 m 每把铣刀有效齿数一般为 8 ; 组 试切机床 : 改制的龙门铣床 , 机床功率仅为 lK ; l w 被
几种典型的国外可转位滚刀介绍

几种典型的国外可转位滚刀介绍韩以滨;张国福【摘要】文中主要介绍几种典型的国外可转位滚刀,从它们的加工范围、结构形式、刀片特点等方面分别进行了阐述,并指出不同刀具厂家生产的可转位滚刀的独特之处,从而为可转位滚刀的选用以及该类刀具的国产化提供参考.【期刊名称】《机械工程师》【年(卷),期】2012(000)010【总页数】2页(P142-143)【关键词】滚刀;可转位;刀夹模块;刀片【作者】韩以滨;张国福【作者单位】哈尔滨第一工具制造有限公司,哈尔滨150078;哈尔滨第一工具制造有限公司,哈尔滨150078【正文语种】中文【中图分类】TG7211 引言滚齿是按展成法加工齿轮的一种传统方法,可进行无变位的直齿齿轮、斜齿齿轮以及相应的变位齿轮的加工,而且滚切的齿轮模数范围大,滚刀是使用最广泛的齿轮加工刀具,同一把滚刀加工的齿轮不受齿数限制,传统的滚刀按结构形式分为整体滚刀和镶片滚刀[1],传统结构滚刀用钝后均需重新修磨前刀面,如刀齿损坏后,容易导致整件滚刀报废。
随着数控加工技术的发展,可转位刀具的制造精度不断提高,国外陆续出现了可转位齿轮滚刀,这种刀具采取装配式,其刀齿为可转位刀片,刀片刃口用钝后直接转位即可,无需重磨,从而无重磨成本,刀片的损坏不影响刀体继续使用,更换刀片可在机床上进行,无需卸刀,减少辅助工时,而且该类滚刀具有比高速钢滚刀更高的金属去除率。
2 几种典型国外可转位滚刀国外生产可转位滚刀的厂家主要是英格索尔、菲特、肯纳、山特维克等几大刀具厂商,他们生产的可转位滚刀结构均不相同,各有特色,但均采用螺钉将刀片固定在刀体模块上,刀片安装形式多为切向立装结构。
(1)英格索尔公司可转位滚刀[2]。
该公司属于国际金属加工集团,从1980年代就生产可转位滚刀,模数范围为6~20mm,直径范围为180~450mm,不同模数范围内,设计不同的刀片,一般不采用刀片搭接的形式,即由一个刀片形成单侧齿形(凸角或倒角刀片除外)。
哈工大机械制造技术基础——可转位车刀设计
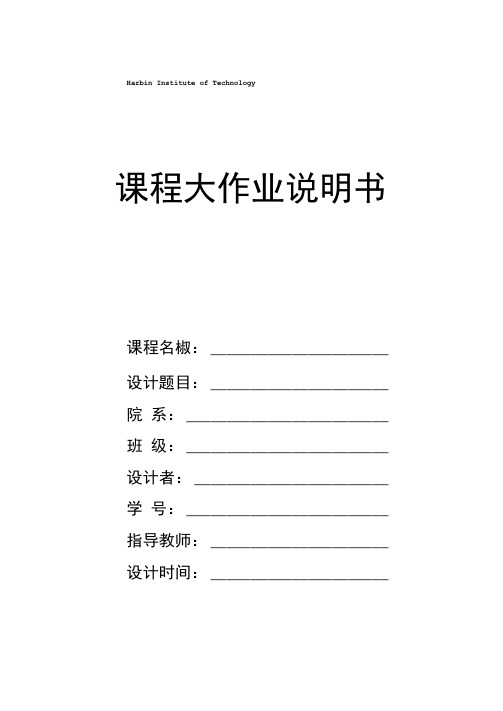
Harbin Institute of Technology课程大作业说明书课程名椒:______________________ 设计题目:______________________ 院系:_________________________ 班级:_________________________ 设计者:________________________ 学号:_________________________ 指导教师:______________________ 设计时间:______________________哈尔滨工业大学目录设计题目 (3)可转位端面车刀设计 (3)一、选择刀片夹固结 (3)二、选择刀片结构材料 (3)三、选择车刀合理角度 (3)四、选择切屑用量 (4)五、刀片型号和尺寸 (4)六、选择硬质合金刀垫型号和尺寸 (5)七、计算刀槽角度 (5)八、计算铳制刀槽时所需的角度 (7)九、选择刀杆材料和尺寸 (8)十、上压式结构 (8)十一、绘制车刀结构简图 (9)参考文献 (10)设计题目设计车小端端面的可转位车刀可转位端面车刀设计一、选择刀片夹固结工件的直径D为160mm,工件长度L二200mm。
因此可以在普通机床CA6140 ±加工。
表面粗糙度要求U ni,为精加工,但由于可转为车刀刃倾角人通常取负值,切屑流向已加工表面从而划伤工件,因此只能达到半精加工,按题设要求,采用上压式的夹紧方式。
二、选择刀片结构材料加工工件材料为HT200,且加工工序为粗车,半精车了两道工序。
由于加工材料为铸铁, 因此刀片材料可以采用YG系列,YG8用于粗加工脆性材料,YG6用于半精加工脆性材料,本题要求达到半精加工,因此材料选择YG6硬质合金。
三、选择车刀合理角度根据《机械制造技术基础》刀具合理几何参数的选择,并考虑可转位车刀几何角度的形成特点,四个角度做如卞选择:前角人:根据参考文献[1]表,工件材料为HT200,半精车,因此前角可选/0=8°,后角%:根据参考文献[1]表,工件材料为HT200,半精车,因此后角可选心=4。
数控铣刀设计与优化技术研究综述

Journal of Mechanical Strength2023,45(2):414-422DOI :10.16579/j.issn.1001.9669.2023.02.022∗20210728收到初稿,20210902收到修改稿㊂江苏省青年基金项目(BK20190676),江苏省高校自然科学基金项目(19KJB460019)资助㊂∗∗汪东明,男,1972年生,江苏响水人,汉族,江苏电子信息职业学院副教授,工学硕士,主要研究方向为机械制造及其自动化㊁汽车电子控制技术㊂∗∗∗孟龙晖(通信作者),男,1985年生,江苏高邮人,汉族,南京工业大学机械与动力工程学院讲师,博士,主要研究方向为精密制造,智能制造,加工变形控制㊂数控铣刀设计与优化技术研究综述∗RESEARCH ON DESIGNING AND OPTIMIZATION OFMILLING TOOL :A REVIEW汪东明∗∗1㊀孟龙晖∗∗∗2㊀张㊀浩2㊀王㊀华2(1.江苏电子信息职业学院智能交通学院,淮安223003)(2.南京工业大学机械与动力工程学院,南京211816)WANG DongMing 1㊀MENG LongHui 2㊀ZHANG Hao 2㊀WANG Hua 2(1.School of Intelligent Transportation ,Jiangsu Vocationnal College of Electronics and Information ,Huaiᶄan 223003,China )(2.School of Mechanical and Power Engineering ,Nanjing Tech University ,Nanjing 211816,China )摘要㊀主要针对目前的铣刀设计优化方面的研究进展进行了相应的综合和描述㊂根据目前切削加工制造领域所存在的问题,刀具的设计过程也会针对这些问题而进行相应的改进和优化㊂主要从加工质量㊁刀具磨损㊁加工振动㊁排屑性能㊁加工效率这个五个方面对刀具所做的改进和优化的研究进展进行了较为详细的描述和总结,最后对目前已有的技术的问题进行了分析,并对后期数控铣刀技术的研究提出了相应的展望㊂关键词㊀铣刀㊀设计㊀优化㊀切削中图分类号㊀TG71Abstract ㊀The research progress of designing and optimization of milling tool is summarized.The design process of cuttingtools has greatly improved and optimized according to the existing problems in the field of cutting and manufacturing.The research progresses of the improvement and optimization of the milling tool in five aspects,such as:Machining quality,tool wear,machining vibration,chip removal performance and machining efficiency are mainly described and summarized.Finally,it analyzes the existing technical problems,and puts forward the corresponding prospects for the later research of NC milling tool technology.Key words㊀Milling tool ;Design ;Optimization ;MachiningCorresponding author :MENG LongHui ,E-mail :menglonghui @ ,Tel :+86-25-58139352,Fax :+86-25-58139352The project supported by the Natural Science Foundation of Jiangsu Province (No.BK20190676),and the Natural Science Foundation of the Jiangsu Higher Education Institutions of China (No.19KJB460019).Manuscript received 20210728,in revised form 20210902.0㊀引言㊀㊀国家的强大和日益兴盛离不开国家的制造业发展,而一个国家的机械制造业的水平也从一定程度上体现着整个国家的制造业发展水平㊂机械制造属于我国基础性工业,需要持续优化生产效率与质量㊂尽管我国机械制造技术研究起步较晚,但目前已获得良好成果,增强了我国工业制造在国际市场中的竞争力[1]㊂虽然目前制造领域不断发展,出现很多新兴产业和制造技术,而切削加工作为机械制造领域中的传统加工方式,其目前的地位仍然无法被取代,而切削加工中数控刀具技术的发展,会对该领域产生举足轻重的影响㊂近年来,数控加工技术的快速发展进一步促进了数控刀具结构基础研究的快速发展和新产品的研发㊂世界各大数控刀具厂商生产的数控机床用刀具种类规㊀第45卷第2期汪东明等:数控铣刀设计与优化技术研究综述415㊀㊀格繁多㊁数量庞大,往往令人眼花缭乱[2],相应的出发点基本可以总结为加工效率㊁加工精度,以及加工成本(经济性)等方面[3]㊂而刀具技术的改进往往是从刀具材料㊁刀柄结构㊁涂层以及刀具几何特征等方面着手而进行的设计和改进㊂本文对前人在数控铣刀的设计和优化方面的代表性的研究进行介绍,并对相应的研究进展进行相应的分析,最后对该领域的研究进行总结和展望㊂1㊀刀具设计方法㊀㊀刀具设计主要考虑到加工质量㊁刀具寿命㊁加工成本以及环境保护等方面㊂被加工件表面质量除了受切削参数影响外,还会受刀具参数影响,特别是几何参数,有研究给出了相应答案[4-8],同样,刀具的基体材料[9-12]㊁涂层[13-17]㊁刀具振动[18-22]以及排屑性能[23-25]均会对工件表面产生重要影响㊂目前数控刀具的设计和优化绝大部分是根据实际需求对刀具多方面同时优化,且主要还是基于刀具几何参数㊁材料㊁涂层这些方面进行展开[26][27]954-959[28]933-941[29]12-25,同时与切削参数和切削条件优化配合,最终满足相应工艺要求㊂2㊀刀具设计优化的不同方面2.1㊀加工质量㊀㊀机械加工表面质量包含表面形貌㊁表面粗糙度㊁微观组织㊁显微硬度㊁位错密度以及表面残余应力等方面[30],目前针对加工质量对刀具所做的优化主要是针对表面粗糙度[31-33]㊂文献[27]954-959对硬质合金铣刀进行了设计㊁优化和评价,从四个方面对刀具设计过程进行表述,即刀具材料㊁涂层㊁几何参数以及切削条件㊂在刀具材料方面,给出了几种常用刀具材料:碳钢㊁合金钢㊁高速钢(HSS)㊁硬质合金等,其指出由于硬质合金钢诸多方面的优越性能,目前为最常用的刀具材料;在几何参数方面,指出与三刃铣刀相比,两刃铣刀具备更好的排屑空间;其提到三种刀具涂层,氮化钛(TiN)㊁碳氮化钛(TiCN)和氮化铝钛(AlTiN),不同涂层有自身相应运用,不过碳氮化钛涂层适用于高速㊁高进给和高温下的切削过程㊂其通过实验和仿真进行分析,结果表明相应刀具能有效加工MS200工具钢,获得较高的表面光洁度㊂文献[28]933-941基于Taguchi法,采用试验㊁信噪比和方差分析,确定表面粗糙度主要影响因素㊂基于高速钢刀具铣削6061铝合金,设计刀具轴向前角29ʎ,刀尖圆半径0.15mm,导程角45ʎ,最终得出在主轴转速884r/min,进给量243mm/min,轴向前角0ʎ下,表面粗糙度达到最优㊂文献[29]12-25主要从表面加工质量和刀具寿命两方面分析了某特殊硬质合金刀具设计对AISI D3钢端铣加工的影响㊂实验所用WC刀片(AlCrN涂层)和刀柄如图1所示㊂图1㊀AISI D3硬质钢端铣实验刀具Fig.1㊀AISI D3hard steel end milling tool used in the experiment结果表明,在可接受的刀具寿命下,可获得表面粗糙度R a在0.1~0.3μm之间㊂针对参数的优化,建立了铣削工艺参数(切削速度v c和进给量f z)㊁表面粗糙度和刀具磨损形态之间的关系分布,得到了R a分布直方图㊂结果表明,刀具几何参数,如倒角,切削角以及刀尖圆弧半径等参数对精加工质量有至关重要的影响㊂文献[34]提出了将剪切/锯齿切削(主刃切削)和断裂/剪切复合切削(主刃和微切削刃依次切削)两种切削方式组合的新型刀具设计,如图2所示㊂在不同切削用量下,材料去除机理依次发生变化,使得加工面损坏量最小并保证相应的加工质量㊂图2㊀复合切削方式的刀具设计Fig.2㊀Compound cutting mode tool design2.2㊀刀具磨损㊀㊀刀具一定程度磨损后若不及时更换,会产生振动[35]㊁切削温度急剧升高[36],使得表面粗糙度[37-38]和表面残余应力发生恶化[39-40]㊂高效优化刀具寿命不仅降低加工成本,同时也保证加工质量㊂目前有研究通过优化切削参数提高刀具寿命[41-42],其属于被动优化,以牺牲加工效率来提高刀具寿命,如果以材料去除量来评价刀具耐磨性,其并不具备明显优势㊂文献[43]根据508III钢的材料性能和铣削条件,设计了分层面铣刀的阶梯结构,铣削加工件断面图和实验设备如图3所示㊂通过单因素实验,分析切削力随轴向和径向前角的变化规律;根据刀具后刀面磨损状态选择最佳前角㊂其基于模糊数学理论建立分层面铣刀性能的多级模糊㊀416㊀机㊀㊀械㊀㊀强㊀㊀度2023年㊀图3㊀阶梯结构分层面铣刀加工件断面和实验设备Fig.3㊀Section of part machined with stepped structure layered facemilling cutter and the experimental equipment综合评价体系,对四种结构刀具进行了性能评价㊂结果表明,采用多齿二级结构的T1型平面铣刀性能最优,其径向前角γf ㊁轴向前角γp 以及切削刃角κr 分别为3ʎ㊁5ʎ㊁75ʎ㊂文献[44]提出计算刀体刀片分布的数学方法,目的为使刀片的刃口磨损率相等㊂其选择商用标准刀片,将其放置于成形铣刀轴向截面中,如图4所示;根据刀具切削用量和磨损率,估算各位置的刀具寿命㊂为均匀刀片磨损和优化刀具寿命,可在同一位置使用多个刀片㊂确定刀片位置和每个位置刀片数量后将刀片螺旋分布于刀体外围㊂该成形铣刀成本远低于特殊定购刀片的铣刀,其刀片均从标准刀片中选取,刀刃变钝可及时更换㊂图4㊀在成形铣刀轴向部分的刀片布置Fig.4㊀Blade arrangement in axial part of forming milling cutter文献[45]通过PCBN 和硬质合金刀具端铣AISI13㊁AISID6和DIN1273材料(切削速度在60~100m /min)㊂结果表明,刀具后刀面磨损很大程度取决于切削速度㊂PCBN 刀具所加工表面粗糙度R a 可达0.2~0.35μm,硬质合金刀具加工表面质量也算好,但刀具寿命较短,PCBN 刀具端铣加工AISI13和DIN1273过程刀具寿命可接受㊂相应的刀具磨损如图5所示;当工件材料含硬质合金颗粒时,刀具后刀面会出现严重磨损,端铣过程冷却液的使用会增大表面下裂纹出现的可能㊂文献[46]指出在CFRP 螺旋铣削制孔过程中,刀具磨损是加工表面损伤的主要因素㊂为优化刀具寿命,其结合碳纤维布双向螺旋铣削成孔技术,对阶梯式双向铣刀的设计㊁制造和切削性能进行分析㊂利用微分几何法,建立阶梯式双向铣刀齿形几何模型和螺旋图5㊀PCBN 和硬质合金刀具端铣加工DIN12713的磨损状态(v =60m /min)Fig.5㊀Wear state of PCBN and cemented carbide end millingtools in machining DIN12713(v =60m /min)刃数学模型㊂对所设计的阶梯式双向铣刀的磨削过程和精度进行测试㊂结果表明,阶梯式双向铣刀(图6a)轴向切削力比对称式双向铣刀(图6b)轴向切削力小,且反向铣削波动更为平缓㊂特别在后向切削刃上,前刀面磨损分布均匀,磨损较慢,加工质量优于后者㊂图6㊀阶梯式双向铣刀和对称双向铣刀对比图Fig.6㊀Comparison between stepped bidirectional milling cutter andsymmetrical bidirectional milling cutter文献[47]指出,球头铣刀(图7a)在钛合金加工过程中存在效率低㊁磨损严重㊁加工表面质量难以保证等问题,对钛合金加工用旋转摆线铣刀(图7b)进行了相应的优化㊂建立旋转摆线铣刀廓面数学模型,提出旋转摆线铣刀正交螺旋线刃口曲线参数方程;基于刃口曲线方程和坐标变换,推导了旋转摆线铣刀前刀面的五轴磨削轨迹方程;制作了旋转摆线铣刀,并对刀具轮廓和几何角度的磨削精度进行检测;对旋转摆线铣刀和球头铣刀切削TC11合金过程进行对比实验㊂结果表明,与球头铣刀相比,旋转摆线铣刀的轴向力与切向力之比较小㊂其侧面磨损缓慢,可保证良好的表面加工质量㊂2.3㊀切削振动㊀㊀切削振动与多因素有关,如机床结构[48-49],切削力(切削参数)[50-51]以及刀具磨损[52-53],切削振动造成加工表面质量恶化和刀具加剧磨损,形成恶性循环㊂目前通过优化切削参数降低切削振动的研究有不少,其依然属于被动优化,其在一定程度上可达到降低振㊀第45卷第2期汪东明等:数控铣刀设计与优化技术研究综述417㊀㊀图7㊀球头铣刀与旋转摆线铣刀示意图Fig.7㊀Schematic diagram of ball end milling cutter androtary cycloid milling cutter动的效果,但大部分时候会对加工效率产生影响㊂文献[54]对两自由度被动阻尼器进行建模并优化,并运用于长悬伸减振铣刀的优化设计中㊂对两自由度被动阻尼器的动力学进行建模;对两自由度阻尼器减振铣刀提出设计方案;对两种结构的铣刀进行实验测试,如图8所示,以证实所设计减振铣刀的优越性㊂图8㊀无阻尼器铣刀和减振铣刀切削效果对比Fig.8㊀Comparison of cutting effect under non damper millingcutter and vibration damping milling cutter文献[55]在分析传统立铣刀加工过程振动机理的基础上,提出不等螺旋角立铣刀结构,如图9所示㊂通过理论分析,推导出不等螺旋角立铣刀在圆周方向等分隔处的刃长表达式㊂通过软件模拟验证表达式的可靠性㊂分析立铣刀各刃等分隔影响因素,提出不等螺旋角立铣刀结构㊂结果表明,与传统立铣刀相比,不等螺旋角立铣刀有较好的抗震效果㊂图9㊀不等齿距抗振铣刀结构设计Fig.9㊀Structural design of anti-vibration milling cutterwith unequal tooth pitch文献[56]指出通过在刀盘上布置不均匀分布刀片可避开系统固有频率,避免产生共振,从而降低加工过程振动幅度,其通过实验验证了自己的观点;文献[57]提出并制造了一种面铣刀,以改善加工过程动态特性,刀具结构包括双阶梯刀片,刀盘上固定两组刀片,外圆刀片A 和内圆刀片B,内圆刀片B 介于相邻两个外圆刀片之间,如图10a 所示,内圆刀片呈现不均匀分布,角度呈现2ʎ~4ʎ的差别,实验过程所用刀具如图10b 所示㊂图10㊀刀盘和刀片示意图和实物图Fig.10㊀Schematic diagram and picture of cutter disk and blade最终发现该刀具加工过程中,振动幅值在时域内减小20%~40%,频域振动谱峰值比传统商用刀具低15%~25%,实验与仿真结果吻合度较高,进一步验证了其优化观点㊂文献[58]指出铣刀采用变节角可提高加工效率,抑制颤振,应用变螺距刀具可提高加工稳定性㊂其提出设计变螺距铣刀的解析法㊂相应的等螺距和变螺距刀具如图11所示㊂结果表明,在期望主轴转速下,与等螺距刀具相比,变螺距刀具能使得临界稳定轴向切深提高126%;切削力降低53%,证实了其颤振抑制设计的实用性㊂图11㊀等螺距刀具和变螺距刀具对比图Fig.11㊀Comparison between constant pitch tools and variable pitch tools文献[59]基于深腔和深孔特征结构件的加工需求,指出随着刀具悬伸量的增加易发生颤振,其基于单自由度被动减振器,设计了一种阻尼铣刀,采用等峰值准则对嵌入式阻尼器进行刚度和阻尼设计,实验过程所用刀具如图12所示㊂模态分析表明,长径比约为8的阻尼刀具在所有方向都能达到75%的振幅减小量㊂文献[60]针对大长径比铣刀在工作过程发生强烈颤振现象,提出被动式阻尼动力减振铣刀,如图13所示㊂分别从颤振稳定性㊁切削力和表面质量等方面将其与普通铣刀对比,结果表明,减振铣刀模态参数得到显著优化,颤振幅值减小约35.3%,加工表面质量㊀418㊀机㊀㊀械㊀㊀强㊀㊀度2023年㊀图12㊀实验过程中所用铣刀Fig.12㊀Milling cutter used in the experiment显著提高㊂图13㊀减振铣刀三维装配模型Fig.13㊀Three dimensional model of vibration damping milling cutter2.4㊀排屑顺畅性㊀㊀切削过程中所产生的切屑,如果不能顺畅地流出,缠绕在刀具上,与刀具前刀面产生剧烈摩擦,加剧前刀面磨损,产生更多切削热,使得切削温度升高,最终影响刀具切削性能[61]332-339㊂文献[61]332-339指出,安装双面八角形 ON 可转位铣刀片的45ʎ平面铣刀目前应用较为广泛,通过分析该刀具使用情况并结合该刀具结构特点,基于市面常见的ON 刀片,如图14a 所示,提出一款新切削刃结构 ON 刀片 ,如图14b 所示,安装ON 刀片后的可转位铣削刀具如图14c 所示㊂图14㊀双面八边形可转位铣削刀片和安装ON 刀片可转位铣削刀具Fig.14㊀Double sided octagonal indexable milling blade andindexable milling tool with ON blade文献[62]基于激光在PCD 刀具前刀面加工出断屑槽,相应的断屑槽设计主要有5个参数,即棱带宽度㊁倾角㊁反屑角㊁槽宽和反屑面转角;其工作可归纳为三个方面:确立PCD 刀具断屑槽棱带宽度和反屑角的关系;对槽宽值的表达式进行了改进;对于倾角和反屑面转角范围进行了确定㊂最终通过实验和仿真验证了相应设计的有效性㊂文献[63]对不同刀具倾角和切削参数组合下的结果进行分析,实验装置如图15a 所示㊂结果表明,铣刀片倾角对于加工面粗糙度和切屑断面形状有重要影响,切削断面形状受刀片倾角影响程度达95%,不同刀具倾角下的切屑形态如图15b 所示,其给出合理的倾角范围为30ʎ~45ʎ,指出在该区间内可得到较好的表面加工质量和切屑断面形态㊂图15㊀不同刀具倾角的实验装置和不同切屑形态Fig.15㊀Experimental device for different tool inclination anddifferent chip morphologies文献[64]对自行式和可转位刀具加工TC11合金过程进行分析,相应的刀具结构如图16a 所示㊂结果表明,相对于可转位刀具,自行式旋转刀具的切削力更小,且具有更好的耐磨性;两种刀具均产生锯齿状切屑,但自行式旋转刀具下的切屑卷曲度大于可转位铣刀,随着铣削时间的增加,自行式旋转刀具下的切屑形态更加规则,锯齿分布更加均匀,如图16b 所示;不仅如此,随着时间推移,可转位铣刀加工表面质量急剧恶化,而自行式旋转铣刀加工表面仍呈现较规则平整形貌㊂图16㊀自行式旋转刀具和不同刀具下的切屑Fig.16㊀Self propelled rotary tool and chips obtained underdifferent cutting tools文献[65]以生产实际需求为目标,设计了三种齿形的倒角铣刀,分别为双层齿倒角铣刀㊁直齿倒角铣刀和斜齿倒角铣刀,同时进行了相应的铣削实验分析,根据实验结果发现,双层齿结构倒角铣刀的结构相对较为合理,刀尖部位有更大的容屑空间,在很大程度上改善了切屑堵塞现象,有良好的分屑排屑性能,在铣削加㊀第45卷第2期汪东明等:数控铣刀设计与优化技术研究综述419㊀㊀工过程中受到的铣削力要明显小于斜齿和直齿倒角铣刀,在三种齿形倒角铣刀中性能表现最优,最终提高了加工质量及生产效率㊂文献[66]基于能耗和断屑问题提出在刀刃上设计相应的凹槽,如图17a 所示,结果表明,其加工过程能耗大幅降低,同时在断屑方面具备相应优势,如图17b ~图17c 所示㊂图17㊀新型铣刀结构和切屑对比Fig.17㊀New milling cutter structure and comparison of chips2.5㊀生产效率㊀㊀单纯靠增大切削用量提高加工效率会加剧刀具磨损,目前有研究通过提高刀具耐磨性来提高切削用量㊂文献[67]针对碳钢和高速钢刀具,优化刀具涂层,基于相应涂层增大刀具耐磨性㊂文献[68]表明,刀具前角14ʎ㊁主间隙角10ʎ的几何特征最适合低温加工条件,同时其分析了切削速度对刀具寿命的影响,结果表明,切速110m /min 时可得最长刀具寿命91min㊂其指出,在Ti6Al4V 合金精加工过程中,采用液氮低温冷却与所提出的刀具相结合可使材料去除效率提高83%㊂文献[69]针对钛合金侧铣加工,对铣刀几何参数进行了优化,优化结果为:前角10ʎ,后角12ʎ,螺旋角38ʎ,相应的设计角示意图如图18所示㊂通过实验和仿真表明,优化后的刀具配合优化后的切削参数,在保证加工效率基础上进一步提高加工质量㊂图18㊀铣刀圆横截面各几何参数示意图Fig.18㊀Schematic diagram of geometric parameters ofcircular cross section of milling cutter文献[70]将锯齿立铣刀的形状转换为圆形可转位铣刀,如图19所示㊂切削力㊁边界条件和刀具几何参数间的高度非线性说明了该设计方案的必要性;传统的矩形可转位刀片可得到较平整的加工面,而圆形可转位刀片加工表面质量不具备优势,不过其可降低径向切削力和切削力矩㊂作为工艺限制性因素之一的最大径向力,圆形可转位铣刀可将其降低14%,进而在一定程度上提高切削用量和加工效率㊂图19㊀矩形可转位铣刀和圆形可转位铣刀Fig.19㊀Rectangular indexable milling cutter and circularindexable milling cutter3㊀结论与展望㊀㊀作为传统加工领域中的刀具技术,经过这几十年的发展,从刀具的材料㊁几何参数以及涂层等方面,都取得了不错的发展㊂不过目前刀具技术依然存在以下问题:1)目前高端刀具制造成本依然较高,且一直是该领域的一个制约因素,虽然刀具技术在进步,但刀具的价格依然居高不下,从而使得加工成本的降低出现瓶颈㊂2)对于难加工材料,如钛合金,镍基合金等,会造成刀具的快速磨损,目前的刀具技术均难以较好地克服该问题,许多时候需要很苛刻的切削条件,如相应的冷却液等,而由于冷却液使用会造成环境的污染,目前大环境下提倡干切削,因此对刀具提出了更严格的要求㊂3)刀具设计应与智能系统结合,不能仅依靠刀具本身实现加工过程优化,加工过程刀具磨损无法避免,如何在线准确检测刀具状态并及时调整工艺参数㊁加工条件或更换刀具,最大限度地延长刀具使用时间并保证加工质量,还有待多个学科的共同进步㊁融合发展㊂参考文献(References )[1]㊀王新甲,张㊀燕.我国现代机械制造技术的发展趋势研究[J].南方农机,2021,52(12):138-140.WANG Xinjia,ZHANG Yan.Research on the development trend of modern machinery manufacturing technology in China [J].ChinaSouthern Agricultural Machinery,2021,52(12):138-140(InChinese).[2]㊀杨晓晶.数控刀具的现状与发展趋势[J].装备制造技术,2011(12):103-105.YANG Xiaojing.The current stage and development trend of the NC cutting tools[J].Equipment Manufacturing Technology,2011(12):103-105(In Chinese).[3]㊀亓㊀军.绿色制造技术在金属加工中刀具的选择应用[J].内燃机与配件,2021(11):117-118.㊀420㊀机㊀㊀械㊀㊀强㊀㊀度2023年㊀QI Jun.Selection and application of green manufacturing technologyin metal processing[J].Internal Combustion Engine&Parts,2021(11):117-118(In Chinese).[4]㊀GÖKKAYA H,NALBANT M.The effects of cutting tool geometryand processing parameters on the surface roughness of AISI1030steel[J].Materials&Design,2007,28(2):717-721. [5]㊀REDDY N S K,RAO P V.Selection of optimum tool geometry andcutting conditions using a surface roughness prediction model for endmilling[J].The International Journal of Advanced ManufacturingTechnology,2005,26(11):1202-1210.[6]㊀GARA S,TSOUMAREV O.Effect of tool geometry on surfaceroughness in slotting of CFRP[J].The International Journal ofAdvanced Manufacturing Technology,2016,86(1):451-461.[7]㊀ÖZEL T,HSU T K,ZEREN E.Effects of cutting edge geometry,workpiece hardness,feed rate and cutting speed on surface roughnessand forces in finish turning of hardened AISI H13steel[J].TheInternational Journal of Advanced Manufacturing Technology,2005,25(3):262-269.[8]㊀ZHAO T,ZHOU J M,BUSHLYA V,et al.Effect of cutting edgeradius on surface roughness and tool wear in hard turning of AISI52100steel[J].The International Journal of AdvancedManufacturing Technology,2017,91(9):3611-3618. [9]㊀GöK F,ORAK S,SOFUŎGLU M A.The effect of cutting toolmaterial on chatter vibrations and statistical optimization in turningoperations[J].Soft Computing,2020(24):17319-17331. [10]㊀WEI T,CHEN X,LI D.A design of combined pipe cleaning andspraying robot based on new cutting tool material[C].Journal ofPhysics:Conference Series.IOP Publishing,2020,1676(1):012092.[11]㊀SAMANTARAYA D,LAKADE S.Hard turning cutting toolmaterials used in automotive and bearing manufacturing applications-a review[C].IOP Conference Series:Materials Science andEngineering.IOP Publishing,2020,814(1):012005. [12]㊀GRIGORIEV S N,FEDOROV S V,HAMDY K.Materials,properties,manufacturing methods and cutting performance ofinnovative ceramic cutting tools-a review[J].ManufacturingReview,2019(6):19.[13]㊀AL-TAMEEMI H A,AL-DULAIMI T,AWE M O,et al.Evaluationof cutting-tool coating on the surface roughness and hole dimensionaltolerances during drilling of Al6061-T651alloy[J].Materials,2021,14(7):1783.[14]㊀GöKKAYA H,NALBANT M.The effects of cutting tool coating onthe surface roughness of AISI1015steel depending on cuttingparameters[J].Turkish Journal of Engineering and EnvironmentalSciences,2007,30(5):307-316.[15]㊀UCUN I,ASLANTA K,GÖKÇE B,et al.Effect of tool coatingmaterials on surface roughness in micromachining of Inconel718super alloy[J].Proceedings of the Institution of MechanicalEngineers,Part B:Journal of Engineering Manufacture,2014,228(12):1550-1562.[16]㊀NALBANT M,ALTıN A,GÖKKAYA H.The effect of coatingmaterial and geometry of cutting tool and cutting speed onmachinability properties of Inconel718super alloys[J].Materials&Design,2007,28(5):1719-1724.[17]㊀CAKIR M C,ENSARIOGLU C,DEMIRAYAK I.Mathematicalmodeling of surface roughness for evaluating the effects of cuttingparameters and coating material[J].Journal of Materials ProcessingTechnology,2009,209(1):102-109.[18]㊀KASSAB S Y,KHOSHNAW Y K.The effect of cutting tool vibrationon surface roughness of workpiece in dry turning operation[J].Engineering&Technology,2007,25(7):879-889. [19]㊀GEORGE J A,LOKESHA K.Optimisation and effect of tool rakeand approach angle on surface roughness and cutting tool vibration[J].SN Applied Sciences,2019,1(9):1-9.[20]㊀AMBHORE N,KAMBLE D,Chinchanikar S.Evaluation of cuttingtool vibration and surface roughness in hard turning of AISI52100steel:An experimental and ANN approach[J].Journal of VibrationEngineering&Technologies,2019:1-8.[21]㊀HESSAINIA Z,BELBAH A,YALLESE M A,et al.On theprediction of surface roughness in the hard turning based on cuttingparameters and tool vibrations[J].Measurement,2013,46(5):1671-1681.[22]㊀ÖZBEK O,SARUHAN H.The effect of vibration and cutting zonetemperature on surface roughness and tool wear in eco-friendly MQLturning of AISI D2[J].Journal of Materials Research andTechnology,2020,9(3):2762-2772.[23]㊀JOCH R,PILC J,DANIŠI,et al.Analysis of surface roughness inturning process using rotating tool with chip breaker for specificshapes of automotive transmission shafts[J].Transportation ResearchProcedia,2019(40):295-301.[24]㊀YLDRM C V,KVAK T,SARKAYA M,et al.Evaluation of toolwear,surface roughness/topography and chip morphology whenmachining of Ni-based alloy625under MQL,cryogenic cooling andCryoMQL[J].Journal of Materials Research and Technology,2020,9(2):2079-2092.[25]㊀DAS S R,PANDA A,DHUPAL D.Hard turning of AISI4340steelusing coated carbide insert:Surface roughness,tool wear,chipmorphology and cost estimation[J].Materials Today:Proceedings,2018,5(2):6560-6569.[26]㊀NARASIMHA M,SRIDHAR K,KUMAR R R,et al.Improvingcutting tool life a review[J].International Journal of EngineeringResearch and Development,2013,7(1):67-75. [27]㊀PHOKOBYE S N,DANIYAN I A,TLHABADIRA I,et al.Modeldesign and optimization of carbide milling cutter for milling operationof M200tool steel[J].Procedia CIRP,2019(84):954-959. [28]㊀IBRAHIM M R,ISMAIL N,LEMAN Z,et al.Experimentalinvestigation of HSS face milling to AL6061using Taguchi method[J].Procedia Engineering,2012(50):933-941. [29]㊀SILLER H R,VILA C,RODRíGUEZ C A,et al.Study of facemilling of hardened AISI D3steel with a special design of carbidetools[J].The International Journal of Advanced ManufacturingTechnology,2009,40(1):12-25.[30]㊀康仁科,宋㊀鑫,董志刚,等.钨合金超声椭圆振动切削表面完整性研究[J/OL].表面技术:1-14[2021-07-07].KANG RenKe,SONG Xin,DONG ZhiGang,et al.Study on surfaceintegrity of tungsten alloy processed by ultrasonic elliptical vibrationcutting[J/OL].Surface Technology:1-14[2021-07-07](InChinese).[31]㊀SAHIN Y,MOTORCU A R.Surface roughness model in machininghardened steel with cubic boron nitride cutting tool[J].International㊀第45卷第2期汪东明等:数控铣刀设计与优化技术研究综述421㊀㊀Journal of Refractory Metals and Hard Materials,2008,26(2):84-90.[32]㊀CHEN C C,CHIANG K T,CHOU C C,et al.The use of D-optimaldesign for modeling and analyzing the vibration and surface roughnessin the precision turning with a diamond cutting tool[J].TheInternational Journal of Advanced Manufacturing Technology,2011,54(5):465-478.[33]㊀HRICOVÁJ.Influence of cutting tool material on the surfaceroughness of AlMgSi aluminium alloy[J].ManufacturingTechnology,2013,13(3):324-329.[34]㊀LIAO Z,AXINTE D A,GAO D.A novel cutting tool design to avoidsurface damage in bone machining[J].International Journal ofMachine Tools and Manufacture,2017(116):52-59. [35]㊀MÓRICZ L,VIHAROS Z J,N METH A,et al.Off-line geometricaland microscopic&on-line vibration based cutting tool wear analysisfor micro-milling of ceramics[J].Measurement,2020(163):108025.[36]㊀TAMERABET Y,BRIOUA M,TAMERABET M,et al.Experimental investigation on tool wear behavior and cuttingtemperature during dry machining of carbon steel SAE1030usingKC810and KC910coated inserts[J].Tribology in Industry,2018,40(1),52-65.[37]㊀ARAúJO R P,ROLIM T L,OLIVEIRA C A,et al.Analysis of thesurface roughness and cutting tool wear using a vapor compressionassisted cooling system to cool the cutting fluid in turning operation[J].Journal of Manufacturing Processes,2019(44):38-46. [38]㊀NATASHA A R,GHANI J A,HARON C H C,et al.The influenceof machining condition and cutting tool wear on surface roughness ofAISI4340steel[C].IOP Conference Series:Materials Science andEngineering.IOP Publishing,2018,290(1):012017. [39]㊀NIAKI F A,MEARS L.A comprehensive study on the effects of toolwear on surface roughness,dimensional integrity and residual stressin turning IN718hard-to-machine alloy[J].Journal of ManufacturingProcesses,2017(30):268-280.[40]㊀LIANG X,LIU Z,WANG B,et al.Prediction of residual stress withmulti-physics model for orthogonal cutting Ti6Al4V under varioustool wear morphologies[J].Journal of Materials ProcessingTechnology,2021(288):116908.[41]㊀TIAN C,ZHOU G,ZHANG J,et al.Optimization of cuttingparameters considering tool wear conditions in low-carbonmanufacturing environment[J].Journal of Cleaner Production,2019(226):706-719.[42]㊀XU L,HUANG C,Li C,et al.Estimation of tool wear andoptimization of cutting parameters based on novel ANFIS-PSOmethod toward intelligent machining[J].Journal of IntelligentManufacturing,2021,32(1):1-14.[43]㊀CHENG Y,JIA W,NIE W,et al.Optimum design and performanceevaluation of layer face milling cutter for cutting508III steel[J].TheInternational Journal of Advanced Manufacturing Technology,2018,98(1):729-740.[44]㊀CHIANG C J,FONG Z H.Design of form milling cutters withmultiple inserts for screw rotors[J].Mechanism and MachineTheory,2010,45(11):1613-1627.[45]㊀BRAGHINI J A,COELHO R T.An investigation of the wearmechanisms of polycrystalline cubic boron nitride(PCBN)toolswhen end milling hardened steels at low/medium cutting speeds[J].The International Journal of Advanced Manufacturing Technology,2001,17(4):244-251.[46]㊀TAO C,RUI L,JIUPENG X,et al.Study on the design and cuttingperformance of stepped bi-directional milling cutters for hole makingof CFRP[J].The International Journal of Advanced ManufacturingTechnology,2020,108(9):3021-3030.[47]㊀WANG G,LIU X,GAO W,et al.Study on the design and cuttingperformance of a revolving cycloid milling cutter[J].AppliedSciences,2019,9(14):2915.[48]㊀KISHORE R,CHOUDHURY S K,ORRA K.On-line control ofmachine tool vibration in turning operation using electro-magnetorheological damper[J].Journal of Manufacturing Processes,2018(31):187-198.[49]㊀LI Z,FU X,LI C,et al.Modeling of instantaneous cutting force forlarge pitch screw with vibration consideration of the machine tool[J].The International Journal of Advanced Manufacturing Technology,2020,108(11):3893-3904.[50]㊀CHUANGWEN X,JIANMING D,YUZHEN C,et al.Therelationships between cutting parameters,tool wear,cutting forceand vibration[J].Advances in Mechanical Engineering,2018,10(1):1687814017750434.[51]㊀SAHU N K,ANDHARE A B,ANDHALE S,et al.Prediction ofsurface roughness in turning of Ti6Al4V using cutting parameters,forces and tool vibration[C].IOP Conference Series:MaterialsScience and Engineering.IOP Publishing,2018,346(1):012037.[52]㊀YI S,LI J,ZHU J,et al.Investigation of machining Ti6Al4V withgraphene oxide nanofluids:Tool wear,cutting forces and cuttingvibration[J].Journal of Manufacturing Processes,2020(49):35-49.[53]㊀HUI Y,MEI X,JIANG G,et ling tool wear state recognitionby vibration signal using a stacked generalization ensemble model[J].Shock and Vibration,2019:1-16.[54]㊀杨毅青,余㊀玉.基于两自由度被动阻尼器的减振铣刀设计[J].计算机集成制造系统,2016,22(11):2588-2593.YANG YiQing,YU Yu.Design of damped milling cutter based ontwo-DOF passive damper[J].Computer Integrated ManufacturingSystems,2016,22(11):2588-2593(In Chinese). [55]㊀许㊀晋,庞安定,刘鹏程,等.不等螺旋角立铣刀的抗振性及设计研究[J].工具技术,2018,52(8):111-115.XU Jin,PANG AnDing,LIU PengCheng,et al.Study on vibration-resist mechanism and design of variable helix end mill[J].ToolEngineering,2018,52(8):111-115(In Chinese). [56]㊀CHOUDHURY S K,MATHEW J.Investigations of the effect of non-uniform insert pitch on vibration during face milling[J].International Journal of Machine Tools and Manufacture,1995,35(10):1435-1444.[57]㊀LEE W Y,KIM K W,SIN H C.Design and analysis of a millingcutter with the improved dynamic characteristics[J].InternationalJournal of Machine Tools and Manufacture,2002,42(8):961-967.[58]㊀MEI J,LUO M,GUO J,et al.Analytical modeling,design andperformance evaluation of chatter-free milling cutter with alternatingpitch variations[J].IEEE Access,2018(6):32367-32375. [59]㊀YANG Y,WANG Y,LIU Q.Design of a milling cutter with largelength-diameter ratio based on embedded passive damper[J].。
可转位车刀课程设计说明书

可转位车刀课程设计说明书可转位车刀课程设计说明书课题名称: 可转位车刀设计专业:机械设计制造及其自动化班级:机械120姓名:学号: A071201 要求工件材料35钢、GPab/σ0.52、HB143-178、D70±0.1mm、L250mm、热处理状态正火处理1.选择刀片夹固结构工件的直径D为70mm,工件长度L=250mm。
因此可以在普通机床CA6140上加工。
表面粗糙度要求1.6μm,为精加工,但由于可转为车刀刃倾角sλ通常取负值,切屑流向已加工表面从而划伤工件,因此只能达到半精加工。
参照《机械制造技术基础课程补充资料》表2.1典型刀片结构简图和特点,采用偏心式刀片加固结构较为合适。
2.选择刀片结构材料由原始给定条件:被加工工件材料为35钢,正火处理,按照硬质合金的选择原则,选取刀片材料为YT15。
3.刀具合理几何参数的选择和切削用量的选择3.1刀具合理集合参数的选择根据《机械制造技术基础》刀具合理几何参数的选择,并考虑可转位车刀几何角度的形成特点,四个角度做如下选择:1.前角γ:根据《刀具课程设计指导书》图2.5,工件材料为35钢(正火),半精车,因此前角可选γ=15°;2.后角0∂:根据《刀具课程设计指导书》图2.5,工件材料为35钢(正火),半精车,因此后角可选0∂=5°;3.主偏角γκ:主偏角γκ=75°;4.刃倾角s λ:为获得大于0°的后角0∂及大于0°的副刃后角'0∂,刃倾角s λ=-6°;5.后角0∂:后角0∂的实际数值及副刃后角'0∂和副偏角'γκ在计算刀槽角度时经校验确定。
3.2切削用量的选择根据《刀具课程设计指导书》附录II :粗车时,背吃刀量p a =3mm ,进给量f=0.6mm/r ,切削速度v=110m/min ;半精车时,背吃刀量p a =1mm ,进给量f=0.3mm/r ,切削速度v=130m/min 。
x52k立铣床说明书修订稿
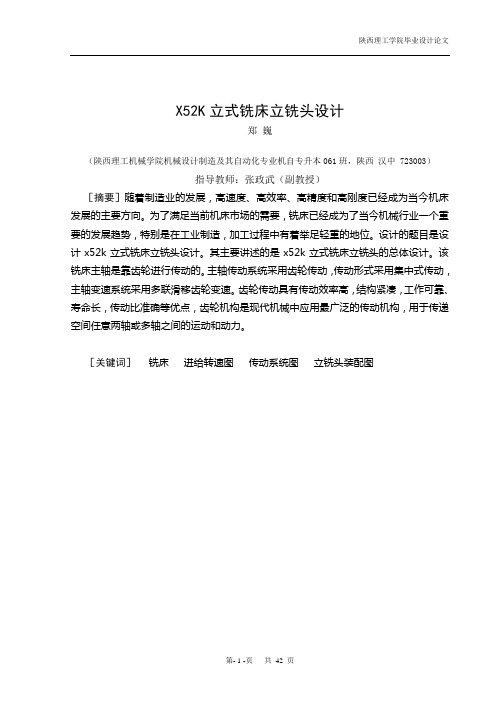
X52K立式铣床立铣头设计郑巍(陕西理工机械学院机械设计制造及其自动化专业机自专升本061班,陕西汉中 723003)指导教师:张政武(副教授)[摘要]随着制造业的发展,高速度、高效率、高精度和高刚度已经成为当今机床发展的主要方向。
为了满足当前机床市场的需要,铣床已经成为了当今机械行业一个重要的发展趋势,特别是在工业制造,加工过程中有着举足轻重的地位。
设计的题目是设计x52k立式铣床立铣头设计。
其主要讲述的是x52k立式铣床立铣头的总体设计。
该铣床主轴是靠齿轮进行传动的。
主轴传动系统采用齿轮传动,传动形式采用集中式传动,主轴变速系统采用多联滑移齿轮变速。
齿轮传动具有传动效率高,结构紧凑,工作可靠、寿命长,传动比准确等优点,齿轮机构是现代机械中应用最广泛的传动机构,用于传递空间任意两轴或多轴之间的运动和动力。
[关键词]铣床进给转速图传动系统图立铣头装配图X52K vertical milling machine legislation XitouZheng wei(Grade04,Class061,Major Mechanical Design and Manufacturing Automation,Mechanical engineering institute Dept.,Shaanxi University of Technology,HanZhong 723003,Shaanxi)tutor: Zhang Zheng Wu【Abstract】With the development of the manufacturing sector, high-speed, high efficiency, high precision and high rigidity of the current machine has become the main direction. In order to meet the needs of the market at present machine, milling machine has become today's machinery industry an important development trend, especially in the industrial manufacturing, processing is a pivotal position. Design is the subject of legislation designed x52k Xitou vertical milling machine design. The main x52k is on the vertical milling machine legislation Xitou the overall design. The main axis milling machine is relying on the power transmission gear. Spindle drive system using gear transmission, transmission using centralized form of transmission, multi-spindle transmission system of sliding gear transmission. Gear transmission with high efficiency, compact, reliable, long life and accurate transmission than the advantages of modern machinery is gearing the application of the most extensive transmission mechanism for the transfer of space or any multi-axis between the two axes of movement and Momentum.【Keywords】Milling machine Progressive plans to speed Transmission System plans1.前言1.1概述图1X52k立式升降台铣床,它是铣床中应用最多的一种。
铣削零件的数控加工工艺及编程设计
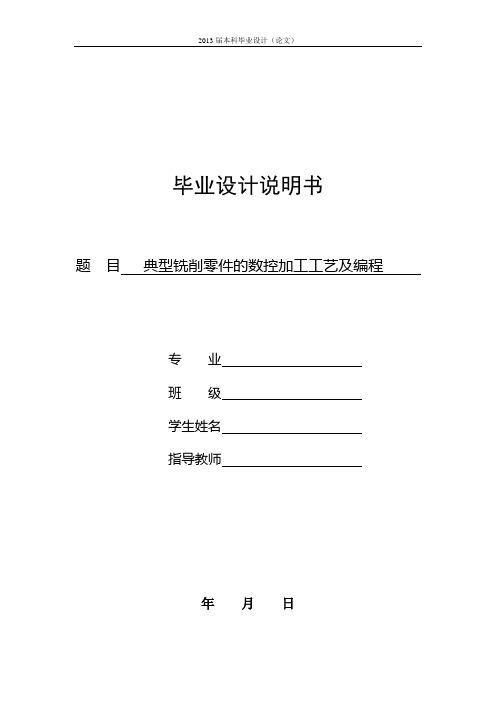
毕业设计说明书题目典型铣削零件的数控加工工艺及编程专业班级学生姓名指导教师年月日此零件为一平面槽形零件,本文主要通过分析零件图纸,找出所需的数据,确定零件形状;然后确定加工的装夹方案,设计合理的夹具;接着就是根据分析图纸所得的数据,以及装夹的方法,编写加工工艺路线及设定铣削参数与铣削用量;最后就是根据前面的分析,编写加工程序,进行零件加工。
关键词:工艺路线切削用量数控编程1 零件图 (5)1.1 零件图的分析 (6)1.2 技术要求分析 (6)2 设备的选择 (6)3 工件的装夹 (7)3.1 毛坯的选择 (7)3.2 零件的装夹 (7)4 工艺路线 (7)4.1 表面加工方法的选择 (8)4.2 加工阶段的划分 (8)4.3 加工顺序的安排 (8)4.4 工序的集中和分散 (9)5 合理的选择刀具 (10)5.1 刀具的选择原则 (10)5.2 数控铣削刀具的选择 (10)6 切削用量的选择 (11)6.1 切削用量的具体参数 (12)6.2 切削用量的选取 (13)7 拟定数控加工工艺卡 (14)8 数控编程 (14)8.1 数控编程的分类 (14)8.2 加工程序清单 (14)9 走刀路线图 (21)设计总结 (22)参考文献 (23)致谢 (24)附录 (25)典型铣削零件的数控加工工艺及编程前言数控技术和数控装备是制造工业现代化的重要基础。
这个基础是否牢固直接影响到一个国家的经济发展和综合国力,关系到一个国家的战略地位。
因此,世界上各工业发达国家均采取重大措施来发展自己的数控技术及其产业。
在我国,数控技术与装备的发展亦得到了高度重视,近年来取得了相当大的进步。
特别是在通用微机数控领域,以PC平台为基础的国产数控系统,已经走在了世界前列。
但是,我国在数控技术研究和产业发展方面亦存在不少问题,特别是在技术创新能力、商品化进程、市场占有率等方面情况尤为突出。
在新世纪到来时,如何有效解决这些问题,使我国数控领域沿着可持续发展的道路,从整体上全面迈入世界先进行列,使我们在国际竞争中有举足轻重的地位,将是数控研究开发部门和生产厂家所面临的重要任务。
- 1、下载文档前请自行甄别文档内容的完整性,平台不提供额外的编辑、内容补充、找答案等附加服务。
- 2、"仅部分预览"的文档,不可在线预览部分如存在完整性等问题,可反馈申请退款(可完整预览的文档不适用该条件!)。
- 3、如文档侵犯您的权益,请联系客服反馈,我们会尽快为您处理(人工客服工作时间:9:00-18:30)。
立装可转位槽铣刀的设计开发摘要可转位刀具具有切削效率高、刀具寿命长、加工质量好、综合经济效益显著等优点,因此在我国机械制造等行业的应用日益广泛。
随着国内先进数控机床的应用不断增加,与之配套的可转位刀具的应用也日益显示出其重要性,同时数控加工也对可转位刀具的设计提出了更高要求。
随着计算机硬件与软件的发展,CAD技术不断向着智能化、集成化、网络化和参数化的方向发展。
用CAD方法开发产品时,零件设计模型的建立速度是决定整个产品开发效率的关键。
本课题中,现代可转位刀具不仅应能满足高速切削、干式切削等先进切削技术的需要,而且对产品功能的多样化、结构的合理化、外观造型的美观等方面也提出了更高要求。
由于可转位刀具形状及装配关系复杂,排屑槽多为曲面,尺寸大都为投影尺寸,设计工作繁琐,采用传统的手工绘图设计方法效率很低,费时费力,且不易保证设计质量。
应用UG(Unigraphics)软件的三维实体造型(3D Solid Mod-eling)及数控编程(Manufacture)功能,使可转位刀具的设计变得简单、方便,大大提高了设计效率和设计精度,且易于实现产品的CAD/CAM一体化开发,大大加快了刀具的研发周期。
关键词立装刀具;可转位刀具;三维实体造型Design and development of vertically mountedindexable slot milling cutterAbstractIndexable cutting tool with high efficiency, long tool life, good processing quality, comprehensive and significant economic benefits, etc., and therefore in China's machinery manufacturing industry is increasingly widespread. With the application of advanced CNC machine tools increasing ancillary indexable cutting tool applications are increasingly shows its importance, but also for the CNC machining of indexable cutting tool design put forward higher requirements. With the development of computer hardware and software, CAD technology continues toward intelligent, integrated, networked and parametric direction. When developing products using CAD methods to establish the speed part design model is to determine the key to the entire product development efficiency.In this topic, modern indexable cutting tool should not only be able to meet the needs of high-speed cutting, dry cutting and other advanced cutting technology, and diversification of product features, rationalizing the structure, appearance and other aspects of appearance also put forward higher requirements . Due to the shape of indexable cutting tools and assembly complex relationship, flutes and more curved, size mostly projection size, design work tedious, using traditional hand-drawing low design efficiency, time-consuming, and difficult to guarantee the quality of design.Three-dimensional solid modeling applications UG (Unigraphics) software (3D Solid Mod-eling) and NC programming (Manufacture) function, so indexable tool design simple, convenient, greatly improving design efficiency and accuracy, and easy to implement integrated CAD / CAM product development, greatly accelerating the development cycle of the tool.Keywords vertical installation tool; indexable cutting tools; 3D solid modeling目录摘要 (I)Abstract (II)第1章绪论 (1)1.1 本课题研究的背景和意义 (1)1.2 国内外金属切削刀具的技术现状及发展趋势 (2)1.2.1 刀具材料的现状及发展趋势 (2)1.2.2 刀具结构的现状及发展趋势 (3)1.2.3 国内外可转位刀具的发展现状及趋势 (4)1.3 研究的主要内容主要问题和解决方法 (7)第2章可转位槽铣刀分析 (8)2.1 铣刀的种类 (8)2.1.1 几种常见的可转位铣刀的类型 (8)2.2 平装刀具与立装刀具的区别与立铣刀 (9)2.3 可转位刀具 (11)2.4 可转位铣刀的合理选用 (11)2.4.1 采用合适的铣刀结构 (11)2.4.2 可转位铣刀的角度选择 (12)2.4.3 可转位铣刀齿数(齿距)的合理确定 (14)2.4.4 可转位铣刀的直径 (14)2.4.5 可转位铣刀的最大切削深度 (15)2.4.6 刀片牌号的选择合理选择 (15)2.4.7 夹紧方式的选择 (16)2.5本章小结 (17)第3章立装可转位槽铣刀的设计 (18)3.1 硬质合金可转位刀片技术要求 (18)3.2铣削效率的计算 (19)3.3 立装可转位槽铣刀角度计算 (20)3.4 可转位槽铣刀的直径计算 (22)3.5 刀片端面伸出量F与刀体宽度L的计算 (23)3.6 可转位铣刀齿数(齿距)的合理确定 (24)3.7本章小结 (24)第4章可转位槽铣刀几何模型的建立 (25)4.1刀片的建模 (25)4.2刀体的建模 (25)4.3螺钉建模 (26)4.4装配关系 (26)4.5渲染效果 (27)4.6可转位槽铣刀二维工程图的生成 (28)4.7本章小结 (30)结论 (31)致谢 (32)参考文献 (33)附录A (35)附录B................................................................................... 错误!未定义书签。
第1章绪论1.1本课题研究的背景和意义随着机械工业的发展,金属切削的作业量日益增多。
全世界钢材年产量的15一30%都要经过切削加工,因此金属切削加工耗资巨大。
美国从1970一1995年,金属切削加工的费用从400亿美元增加到6500亿美元,近些年仍在继续增加。
国内虽无详细统计,估计每年耗资不少于1000亿元[1]。
因此刀具在机械加工中具有举足轻重的地位。
制造业的加工技术水平受刀具行业整体水平的影响较大,而制造业的发展也会促进刀具行业的发展。
根据制造业发展的需要,多功能复合刀具、高速高效刀具将成为刀具发展的主流[2]。
面对日益增多的难加工材料,刀具行业必须研发新的刀具材料和更合理的刀具结构。
近10年来,随着硬质合金刀片数控周边磨床、刃磨加工中心等机床的发展,硬质合金可转位刀片的几何精度大大提高,刀刃的转位精度可控制在2um[3]内。
由于数控加工技术的发展也使刀体上刀片槽加工的位置精度和形状精度达到了很高的水平,从而使可转位多齿刀具刀刃间的相互搭接精度得以改善。
国内大多金属加工行业仍在使用比较滞后的刀具,抗振性和耐磨性差,切削效率低,加工质量不稳定,一旦崩刃或非恢复性磨损,整体刀具无法再利用,浪费严重。
由于人们对刀具的发展认识不足,缺乏刀具理论与实践,轻视刀具和排斥刀具的现象比较普遍,上述种种问题是造成加工成本高的主要因素之一[4]。
而推广使用可转位刀具具有很大的优势[5]与焊接刀具和整体刀具相比,可转位刀具有下述优点:(1)刀具刚性好,寿命高。
由于刀片避免了由焊接和刃磨高温引起的缺陷,刀具几何参数完全由刀片和刀杆槽保证,切削性能稳定,经得起冲击和振动,从而提高了刀具寿命。
(2)生产效率高,定位精度高。
刀片转位或更换新刀片后,刀尖位置的变化应在工件精度允许的范围内,可大大减少停机换刀等辅助时间。
(3)可转位刀具有利于推广使用涂层、陶瓷等新型刀具材料。
(4)加工成本低。
可转位刀具的刀片、体的机械夹固方式相联接,可以实现多品种搭配,通用性好,能做到一体多用(一个刀体可以装不同牌号的硬质合金刀片),一片多用(同一块刀片可以安装在不同用途的多种结构的刀体上)。
大大简化了刀具的管理;刀体可多次重复使用,大大减少了刀体的消耗与库存量;刀具可以标准化集中生产,降低了刀具制造成本;用过的刀片可以作为硬质合金原材料回收。
总结起来,可转位刀具具有切削效率高、刀具寿命长、加工质量好、综合经济效益显著等优点,因此在我国机械制造等行业的应用日益广泛。
随着国内先进数控机床的应用不断增加,与之配套的可转位刀具的应用也日益显示出其重要性,同时数控加工也对可转位刀具的设计提出了更高要求。
随着计算机硬件与软件的发展,CAD技术不断向着智能化、集成化、网络化和参数化的方向发展。
用CAD方法开发产品时,零件设计模型的建立速度是决定整个产品开发效率的关键。