第六章模具表面处理技术
冲压模具的表面处理技术

冲压模具的表面处理技术1. 引言冲压模具是在工业生产中广泛应用的一种工具。
它用于将金属板材等材料加工成所需形状的零件。
冲压模具的表面处理技术对于提高模具的耐磨性、延长使用寿命、增加工件的精度和减少摩擦阻力等方面起着至关重要的作用。
本文将介绍几种常用的冲压模具表面处理技术及其优缺点。
2. 高温气体渗氮高温气体渗氮是一种常用的冲压模具表面处理技术。
该技术通过在高温下将氮气渗入模具表面,使其形成氮化层。
这种氮化层具有高硬度、良好的耐磨性和抗腐蚀性能。
同时,氮化层能够降低摩擦系数,减少摩擦损失,提高模具的使用寿命。
然而,高温气体渗氮技术存在一些缺点。
首先,该技术的成本较高,需要投资大量的设备和材料。
其次,渗氮过程中需要严格控制温度和氮气流量,以保证氮化层的质量。
因此,该技术在应用中需要一定的专业知识和技术支持。
3. 离子氮化离子氮化是另一种常用的冲压模具表面处理技术。
该技术通过在真空环境中施加高电压,使模具表面形成氮化层。
离子氮化技术具有渗层速度快、渗氮层厚度均匀等优点。
此外,离子氮化过程中还可以控制温度和离子能量,以调节氮化层的硬度和结构。
然而,离子氮化技术也有一些局限性。
首先,该技术对模具材料的要求较高,只有一些特定的金属材料才能通过离子氮化得到理想的氮化层。
其次,由于离子氮化需要在真空环境下进行,因此设备的成本较高,操作难度较大。
4. 涂层涂层技术是一种简单且广泛应用的冲压模具表面处理技术。
该技术通过在模具表面涂覆一层特殊的涂层材料,以提高模具的表面硬度、耐磨性和抗腐蚀性能。
常见的涂层材料包括钛、钨、碳化物等。
涂层技术具有成本较低、适用性广等优点。
此外,涂层技术还可以根据不同的需求选择不同的材料和涂层厚度,以满足不同工艺要求。
然而,涂层技术也存在一些问题。
首先,涂层的附着力和耐磨性较低,容易剥落或磨损。
其次,涂层的加工工艺复杂,需要控制好涂层的厚度和均匀性。
5. 表面喷丸处理表面喷丸处理是一种常用的冲压模具表面处理技术。
模具表面处理
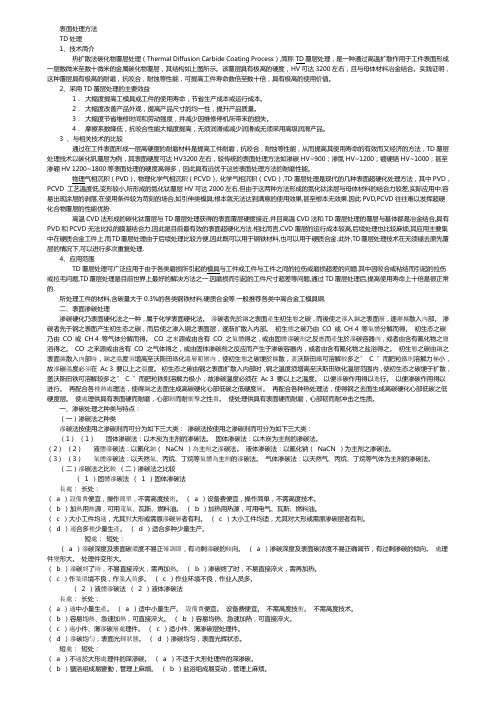
表面处理方法TD处理1、技术简介热扩散法碳化物覆层处理(Thermal Diffusion Carbide Coating Process),简称TD覆层处理,是一种通过高温扩散作用于工件表面形成一层数微米至数十微米的金属碳化物覆层,其结构如上图所示。
该覆层具有极高的硬度,HV可达3200左右,且与母体材料冶金结合。
实践证明,这种覆层具有极高的耐磨,抗咬合,耐蚀等性能,可提高工件寿命数倍至数十倍,具有极高的使用价值。
2、采用TD覆层处理的主要效益1.大幅度提高工模具或工件的使用寿命,节省生产成本或运行成本。
2.大幅度改善产品外观,提高产品尺寸的均一性,提升产品质量。
3.大幅度节省维修时间和劳动强度,并减少因维修停机所带来的损失。
4.摩擦系数降低,抗咬合性能大幅度提高,无须润滑或减少润滑或无须采用高级润滑产品。
3 、与相关技术的比较通过在工件表面形成一层高硬度的耐磨材料是提高工件耐磨,抗咬合,耐蚀等性能,从而提高其使用寿命的有效而又经济的方法,TD覆层处理技术以碳化钒覆层为例,其表面硬度可达HV3200左右,较传统的表面处理方法如渗碳HV~900;渗氮HV~1200;镀硬铬HV~1000;甚至渗硼HV 1200~1800等表面处理的硬度高得多,因此具有远优于这些表面处理方法的耐磨性能。
物理气相沉积(PVD),物理化学气相沉积(PCVD),化学气相沉积(CVD),TD覆层处理是现代的几种表面超硬化处理方法,其中PVD,PCVD 工艺温度低,变形较小,所形成的氮化钛覆层HV可达2000左右,但由于这两种方法形成的氮化钛涂层与母体材料的结合力较差,实际应用中,容易出现涂层的剥落,在使用条件较为苛刻的场合,如引伸类模具;根本就无法达到满意的使用效果,甚至根本无效果.因此PVD,PCVD往往难以发挥超硬化合物覆层的性能优势.高温CVD法形成的碳化钛覆层与TD覆层处理获得的表面覆层硬度接近,并且高温CVD法和TD覆层处理的覆层与基体都是冶金结合,具有PVD 和PCVD无法比拟的膜基结合力,因此是目前最有效的表面超硬化方法.相比而言,CVD覆层的运行成本较高,后续处理也比较麻烦,其应用主要集中在硬质合金工件上.而TD覆层处理由于后续处理比较方便,因此既可以用于钢铁材料,也可以用于硬质合金.此外,TD覆层处理技术在无须褪去原先覆层的情况下,可以进行多次重复处理.4、应用范围TD覆层处理可广泛应用于由于各类磨损所引起的模具与工件或工件与工件之间的拉伤或磨损超差的问题.其中因咬合或粘结而引起的拉伤或拉毛问题,TD覆层处理是目前世界上最好的解决方法之一.因磨损而引起的工件尺寸超差等问题,通过TD覆层处理后,提高使用寿命上十倍是很正常的.所处理工件的材料,含碳量大于0.3%的各类钢铁材料,硬质合金等.一般推荐各类中高合金工模具钢.二、表面渗碳处理渗碳硬化乃表面硬化法之一种,属于化学表面硬化法。
分析模具制造中的表面处理技术的发展趋势和应用
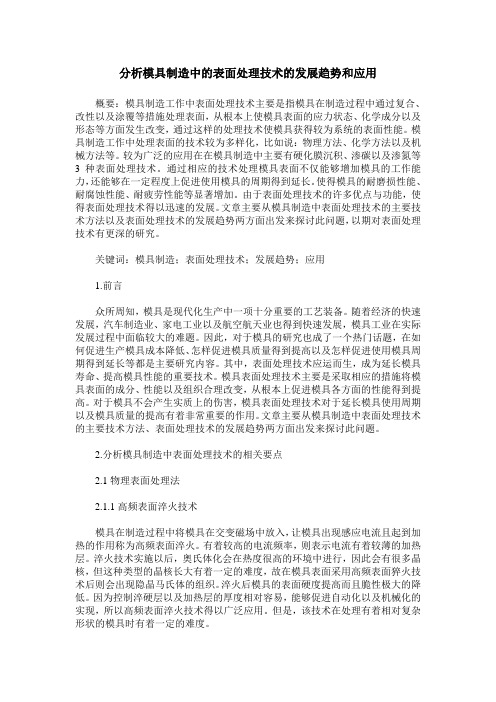
分析模具制造中的表面处理技术的发展趋势和应用概要:模具制造工作中表面处理技术主要是指模具在制造过程中通过复合、改性以及涂覆等措施处理表面,从根本上使模具表面的应力状态、化学成分以及形态等方面发生改变,通过这样的处理技术使模具获得较为系统的表面性能。
模具制造工作中处理表面的技术较为多样化,比如说:物理方法、化学方法以及机械方法等。
较为广泛的应用在在模具制造中主要有硬化膜沉积、渗碳以及渗氮等3种表面处理技术。
通过相应的技术处理模具表面不仅能够增加模具的工作能力,还能够在一定程度上促进使用模具的周期得到延长。
使得模具的耐磨损性能、耐腐蚀性能、耐疲劳性能等显著增加。
由于表面处理技术的许多优点与功能,使得表面处理技术得以迅速的发展。
文章主要从模具制造中表面处理技术的主要技术方法以及表面处理技术的发展趋势两方面出发来探讨此问题,以期对表面处理技术有更深的研究。
关键词:模具制造;表面处理技术;发展趋势;应用1.前言众所周知,模具是现代化生产中一项十分重要的工艺装备。
随着经济的快速发展,汽车制造业、家电工业以及航空航天业也得到快速发展,模具工业在实际发展过程中面临较大的难题。
因此,对于模具的研究也成了一个热门话题,在如何促进生产模具成本降低、怎样促进模具质量得到提高以及怎样促进使用模具周期得到延长等都是主要研究内容。
其中,表面处理技术应运而生,成为延长模具寿命、提高模具性能的重要技术。
模具表面处理技术主要是采取相应的措施将模具表面的成分、性能以及组织合理改变,从根本上促进模具各方面的性能得到提高。
对于模具不会产生实质上的伤害,模具表面处理技术对于延长模具使用周期以及模具质量的提高有着非常重要的作用。
文章主要从模具制造中表面处理技术的主要技术方法、表面处理技术的发展趋势两方面出发来探讨此问题。
2.分析模具制造中表面处理技术的相关要点2.1物理表面处理法2.1.1高频表面淬火技术模具在制造过程中将模具在交变磁场中放入,让模具出现感应电流且起到加热的作用称为高频表面淬火。
第六章 模具表面强化技术
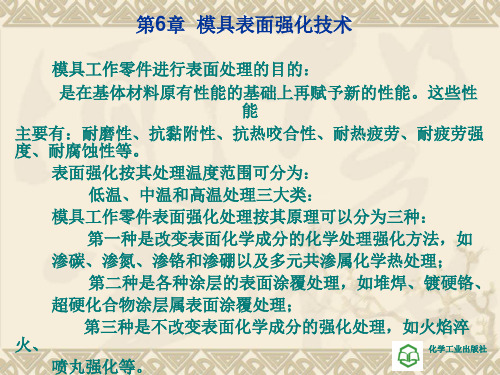
6.1表面热处理技术 表面热处理技术
6.1.1渗碳 渗碳 6.1.1.1渗碳的基本原理 渗碳的基本原理 为了增加钢件表层的含碳量和一定碳浓度梯度, 为了增加钢件表层的含碳量和一定碳浓度梯度,将钢件 在渗碳介质中加热并保温使碳原子深入表层的化学热处理工 艺称为渗碳。 艺称为渗碳。 渗碳是将钢件加热到奥氏体状态,进行渗碳及扩散, 渗碳是将钢件加热到奥氏体状态,进行渗碳及扩散,其 后经淬火+低温回火得到具有高硬度和高耐磨性的表面渗碳层 后经淬火 低温回火得到具有高硬度和高耐磨性的表面渗碳层 和高的强韧性的心部组织。 和高的强韧性的心部组织。 生产上所采用的渗碳温度一般在900~950℃间进行,渗 生产上所采用的渗碳温度一般在 ~ ℃间进行, 碳深度一般在0.5~ 范围内。 碳深度一般在 ~2.5mm范围内。 范围内 渗碳层中碳质量分数为0.85~1.10%时最好,渗碳层硬 时最好, 渗碳层中碳质量分数为 ~ 时最好 度不低于56HRC。 度不低于 。 渗碳剂有固体、液体和气体三种。 渗碳剂有固体、液体和气体三种。 近年来,新发展了真空渗碳、 近年来,新发展了真空渗碳、离子渗碳和碳氮共渗等工 可以达到常规渗碳难以达到的质量效果,而且周期短、 艺,可以达到常规渗碳难以达到的质量效果,而且周期短、 能耗低、无污染。 能耗低、无污染。 化学工业出版社
化学工业出版社
6.1表面热处理技术 表面热处理技术
6.1.5多元共渗 多元共渗 6.1.5.1碳氮共渗 碳氮共渗 6.Байду номын сангаас.5.2氮碳共渗 氮碳共渗 6.1.5.3硼砂盐浴铬钒共渗 硼砂盐浴铬钒共渗 6.1.5.4铬铝共渗 铬铝共渗
化学工业出版社
6.2涂镀技术 涂镀技术
6.2.1电镀 电镀 利用电解的方法从一定的电解质溶液中, 利用电解的方法从一定的电解质溶液中,在经过处理的 基体金属表面沉积各种所需性能或尺寸的连续、 基体金属表面沉积各种所需性能或尺寸的连续、均匀而附着 沉积的一种电化学过程的总称。 沉积的一种电化学过程的总称。 电镀可以镀各种金属镀层。 电镀可以镀各种金属镀层。 在进行电镀时,将被镀 在进行电镀时, 的工件与直流电源的负极相 要镀覆的金属(镀铬除外) 连,要镀覆的金属(镀铬除外) 与直流电源的正极相连, 与直流电源的正极相连,并放 在渡槽中。 在渡槽中。当电源与渡槽接通 时,在阴极上析出欲镀的金属 层。
模具表面涂层处理的6种方式
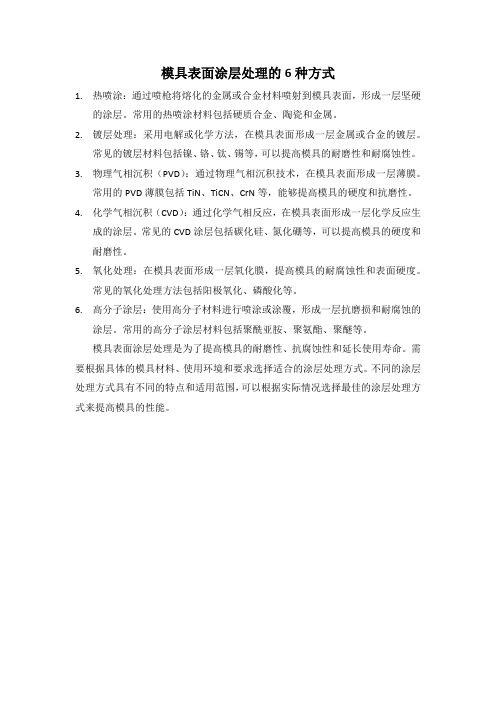
模具表面涂层处理的6种方式
1.热喷涂:通过喷枪将熔化的金属或合金材料喷射到模具表面,形成一层坚硬
的涂层。
常用的热喷涂材料包括硬质合金、陶瓷和金属。
2.镀层处理:采用电解或化学方法,在模具表面形成一层金属或合金的镀层。
常见的镀层材料包括镍、铬、钛、锡等,可以提高模具的耐磨性和耐腐蚀性。
3.物理气相沉积(PVD):通过物理气相沉积技术,在模具表面形成一层薄膜。
常用的PVD薄膜包括TiN、TiCN、CrN等,能够提高模具的硬度和抗磨性。
4.化学气相沉积(CVD):通过化学气相反应,在模具表面形成一层化学反应生
成的涂层。
常见的CVD涂层包括碳化硅、氮化硼等,可以提高模具的硬度和耐磨性。
5.氧化处理:在模具表面形成一层氧化膜,提高模具的耐腐蚀性和表面硬度。
常见的氧化处理方法包括阳极氧化、磷酸化等。
6.高分子涂层:使用高分子材料进行喷涂或涂覆,形成一层抗磨损和耐腐蚀的
涂层。
常用的高分子涂层材料包括聚酰亚胺、聚氨酯、聚醚等。
模具表面涂层处理是为了提高模具的耐磨性、抗腐蚀性和延长使用寿命。
需要根据具体的模具材料、使用环境和要求选择适合的涂层处理方式。
不同的涂层处理方式具有不同的特点和适用范围,可以根据实际情况选择最佳的涂层处理方式来提高模具的性能。
模具表面处理
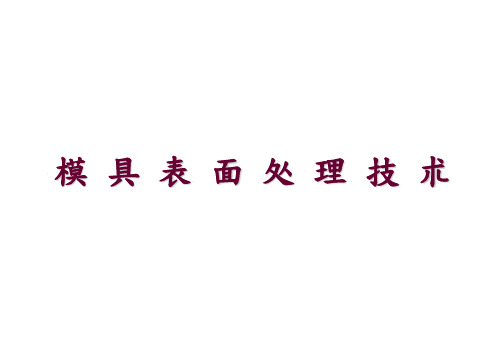
目
录
一﹑模具常規热处理 二﹑模具強韌化处理 三﹑模具化学热处理 四﹑其它表面強化技朮 五﹑真空镀硬质涂层 真空镀硬质涂层
前
言
模具是機械工業重要的基礎工藝裝備. 模具是機械工業重要的基礎工藝裝備. 模具成形具 有效率高﹑質量好﹑節約原材料﹑降低成本等優點. 有效率高﹑質量好﹑節約原材料﹑降低成本等優點. 模具的服役条件是选择模具材料及热处理的依据. 模具的服役条件是选择模具材料及热处理的依据. 影响模具失效的因素包括模具结构﹑模具材料﹑ 影响模具失效的因素包括模具结构﹑模具材料﹑热处理 及加工工艺等. 及加工工艺等. 主要用于金屬或非金屬冷態成形,承受拉伸﹑ 冷作模具主要用于金屬或非金屬冷態成形,承受拉伸﹑彎 壓縮﹑沖擊﹑疲勞等不同應力作用, 曲﹑壓縮﹑沖擊﹑疲勞等不同應力作用,而用于金屬冷 冷镦﹑冷拉伸的模具还要承受300℃ 300℃左右的交變溫 挤﹑冷镦﹑冷拉伸的模具还要承受300℃左右的交變溫 度作用. 度作用. 薄板冲压模主要失效形式是磨损,所以模具用钢要求 薄板冲压模主要失效形式是磨损, 主要失效形式是磨损 Cr4 MoV(120) CrNiSiMnMoV(GD) 具有高的耐磨性.Cr4W2MoV(120)﹑6CrNiSiMnMoV(GD)﹑
淬火后必须回火. 淬火后必须回火.
回火: 回火:
将淬火钢重新加热到A1点以下的预热温度, 将淬火钢重新加热到A1点以下的预热温度,保温预 A1点以下的预热温度 定时间,然后冷却下来.以消除含碳过饱和之马氏体、 定时间,然后冷却下来.以消除含碳过饱和之马氏体、 过冷残余奥氏体以及高密度位错、 过冷残余奥氏体以及高密度位错、大量相界面等晶体 缺陷、淬火应力等不稳定因素. 缺陷、淬火应力等不稳定因素. •低温回火: (150~200℃),得到回火马氏体组织,硬而耐 低温回火: (150~200℃),得到回火马氏体组织 得到回火马氏体组织, 低温回火 强度高,耐疲劳.多用于刃具, 冷冲模具等. 磨,强度高,耐疲劳.多用于刃具,量,冷冲模具等. •中温回火: (400~500℃),得到回火屈氏体组织,弹性好, 中温回火: (400~500℃),得到回火屈氏体组织 弹性好, 得到回火屈氏体组织, 中温回火 用于弹簧处理. 用于弹簧处理. •高温回火: (500~650℃),得到回火索氏体组织,强度和 高温回火: (500~650℃),得到回火索氏体组织 得到回火索氏体组织, 高温回火 韧性综合性能高. 用于轴类,连杆,连接件. 韧性综合性能高. 用于轴类,连杆,连接件.高温软化 回火,回火温度低于A1(20~24℃),得到回火珠光体组织, A1(20~24℃),得到回火珠光体组织 回火,回火温度低于A1(20~24℃),得到回火珠光体组织, 工艺性能好. 工艺性能好.
模具表面处理技术
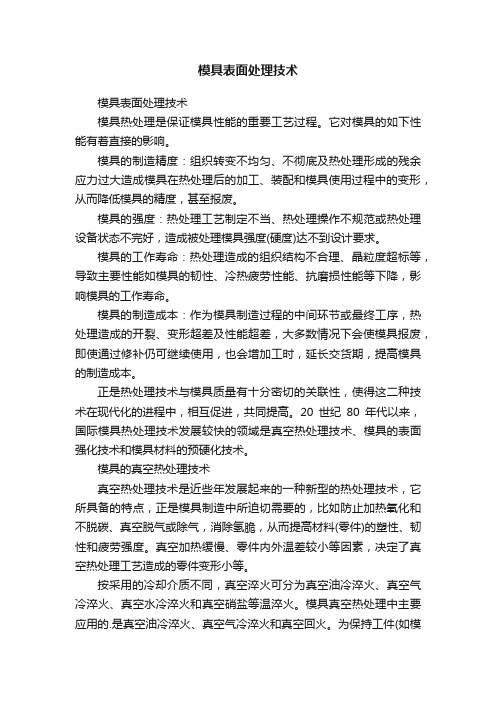
模具表面处理技术模具表面处理技术模具热处理是保证模具性能的重要工艺过程。
它对模具的如下性能有着直接的影响。
模具的制造精度:组织转变不均匀、不彻底及热处理形成的残余应力过大造成模具在热处理后的加工、装配和模具使用过程中的变形,从而降低模具的精度,甚至报废。
模具的强度:热处理工艺制定不当、热处理操作不规范或热处理设备状态不完好,造成被处理模具强度(硬度)达不到设计要求。
模具的工作寿命:热处理造成的组织结构不合理、晶粒度超标等,导致主要性能如模具的韧性、冷热疲劳性能、抗磨损性能等下降,影响模具的工作寿命。
模具的制造成本:作为模具制造过程的中间环节或最终工序,热处理造成的开裂、变形超差及性能超差,大多数情况下会使模具报废,即使通过修补仍可继续使用,也会增加工时,延长交货期,提高模具的制造成本。
正是热处理技术与模具质量有十分密切的关联性,使得这二种技术在现代化的进程中,相互促进,共同提高。
20世纪80年代以来,国际模具热处理技术发展较快的领域是真空热处理技术、模具的表面强化技术和模具材料的预硬化技术。
模具的真空热处理技术真空热处理技术是近些年发展起来的一种新型的热处理技术,它所具备的特点,正是模具制造中所迫切需要的,比如防止加热氧化和不脱碳、真空脱气或除气,消除氢脆,从而提高材料(零件)的塑性、韧性和疲劳强度。
真空加热缓慢、零件内外温差较小等因素,决定了真空热处理工艺造成的零件变形小等。
按采用的冷却介质不同,真空淬火可分为真空油冷淬火、真空气冷淬火、真空水冷淬火和真空硝盐等温淬火。
模具真空热处理中主要应用的.是真空油冷淬火、真空气冷淬火和真空回火。
为保持工件(如模具)真空加热的优良特性,冷却剂和冷却工艺的选择及制定非常重要,模具淬火过程主要采用油冷和气冷。
对于热处理后不再进行机械加工的模具工作面,淬火后尽可能采用真空回火,特别是真空淬火的工件(模具),它可以提高与表面质量相关的机械性能,如疲劳性能、表面光亮度、而腐蚀性等。
模具表面处理技术PPT课件
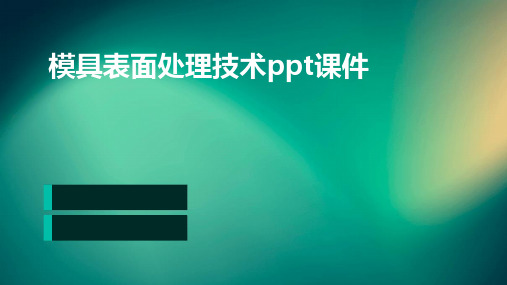
要点二
等离子喷涂技术
通过等离子喷涂将金属或非金属粉末熔融并喷射到模具表 面,形成均匀、致密的涂层,提高表面耐久性和抗腐蚀性 。
智能化和自动化技术的应用
智能监控系统
利用传感器和监测技术实时监测模具表面处理过程,实 现自动化控制和处理。
自动化处理设备
开发自动化表面处理设备,减少人工干预,提高处理效 率和一致性。
耐久性。
提高产品质量和生产效率
提高产品精度和一致性
通过表面处理技术,可以改善模具表 面的粗糙度和形貌,减小产品尺寸和 形状的误差,提高产品的精度和一致 性,从而提高生产效率。
降低生产成本
通过表面处理技术,可以提高模具的 耐磨性和耐久性,减少维修和更换模 具的频率和成本,降低生产成本。
降低生产成本
04 模具表面处理技术的优势 与挑战
提高模具使用寿命
增强模具表面硬度和耐磨 性
通过表面处理技术,可以在模具表面形成一 层高硬度的硬化层,从而提高模具的耐磨性 和抗疲劳性能,延长模具的使用寿命。
降低摩擦系数
通过表面处理技术,可以在模具表面形成一 层低摩擦系数的涂层,减小模具与材料之间 的摩擦力,降低磨损和摩擦热,提高模具的
优化生产流程
通过表面处理技术,可以优化模具的 设计和制造流程,减少加工时间和成 本,提高生产效率。
降低能耗和资源消耗
一些表面处理技术可以降低模具的能 耗和资源消耗,例如离子注入和激光 熔覆等,从而降低生产成本。
技术更新换代快
技术发展迅速
随着科学技术的不断发展,模具 表面处理技术也在不断更新换代 ,新的技术和工艺不断涌现。
常用的五金模具表面处理技术包括喷涂、电镀和化学热处理等。这些技术可以提 高模具表面的硬度和耐久性,降低生产成本和提高产品质量。
分析模具制造中的表面处理技术的发展趋势和应用
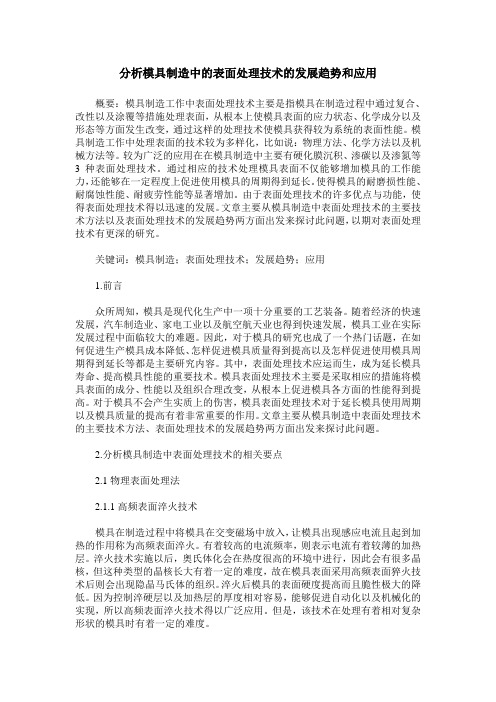
分析模具制造中的表面处理技术的发展趋势和应用概要:模具制造工作中表面处理技术主要是指模具在制造过程中通过复合、改性以及涂覆等措施处理表面,从根本上使模具表面的应力状态、化学成分以及形态等方面发生改变,通过这样的处理技术使模具获得较为系统的表面性能。
模具制造工作中处理表面的技术较为多样化,比如说:物理方法、化学方法以及机械方法等。
较为广泛的应用在在模具制造中主要有硬化膜沉积、渗碳以及渗氮等3种表面处理技术。
通过相应的技术处理模具表面不仅能够增加模具的工作能力,还能够在一定程度上促进使用模具的周期得到延长。
使得模具的耐磨损性能、耐腐蚀性能、耐疲劳性能等显著增加。
由于表面处理技术的许多优点与功能,使得表面处理技术得以迅速的发展。
文章主要从模具制造中表面处理技术的主要技术方法以及表面处理技术的发展趋势两方面出发来探讨此问题,以期对表面处理技术有更深的研究。
关键词:模具制造;表面处理技术;发展趋势;应用1.前言众所周知,模具是现代化生产中一项十分重要的工艺装备。
随着经济的快速发展,汽车制造业、家电工业以及航空航天业也得到快速发展,模具工业在实际发展过程中面临较大的难题。
因此,对于模具的研究也成了一个热门话题,在如何促进生产模具成本降低、怎样促进模具质量得到提高以及怎样促进使用模具周期得到延长等都是主要研究内容。
其中,表面处理技术应运而生,成为延长模具寿命、提高模具性能的重要技术。
模具表面处理技术主要是采取相应的措施将模具表面的成分、性能以及组织合理改变,从根本上促进模具各方面的性能得到提高。
对于模具不会产生实质上的伤害,模具表面处理技术对于延长模具使用周期以及模具质量的提高有着非常重要的作用。
文章主要从模具制造中表面处理技术的主要技术方法、表面处理技术的发展趋势两方面出发来探讨此问题。
2.分析模具制造中表面处理技术的相关要点2.1物理表面处理法2.1.1高频表面淬火技术模具在制造过程中将模具在交变磁场中放入,让模具出现感应电流且起到加热的作用称为高频表面淬火。
模具表面强化处理技术
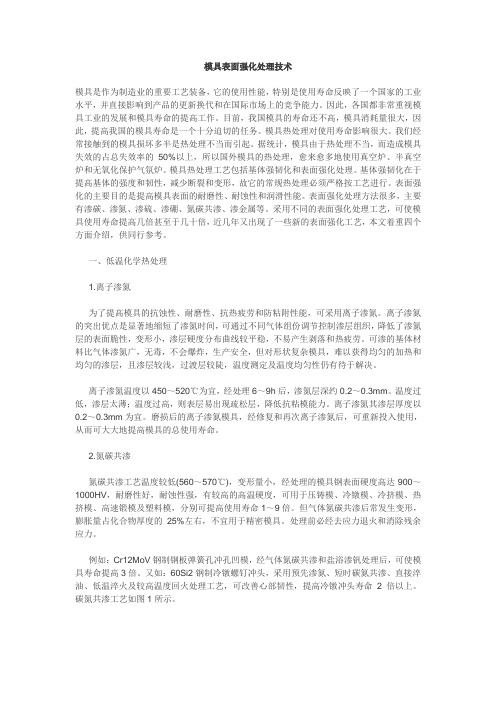
模具表面强化处理技术模具是作为制造业的重要工艺装备,它的使用性能,特别是使用寿命反映了一个国家的工业水平,并直接影响到产品的更新换代和在国际市场上的竞争能力。
因此,各国都非常重视模具工业的发展和模具寿命的提高工作。
目前,我国模具的寿命还不高,模具消耗量很大,因此,提高我国的模具寿命是一个十分迫切的任务。
模具热处理对使用寿命影响很大。
我们经常接触到的模具损坏多半是热处理不当而引起。
据统计,模具由于热处理不当,而造成模具失效的占总失效率的50%以上,所以国外模具的热处理,愈来愈多地使用真空炉、半真空炉和无氧化保护气氛炉。
模具热处理工艺包括基体强韧化和表面强化处理。
基体强韧化在于提高基体的强度和韧性,减少断裂和变形,故它的常规热处理必须严格按工艺进行。
表面强化的主要目的是提高模具表面的耐磨性、耐蚀性和润滑性能。
表面强化处理方法很多,主要有渗碳、渗氮、渗硫、渗硼、氮碳共渗、渗金属等。
采用不同的表面强化处理工艺,可使模具使用寿命提高几倍甚至于几十倍,近几年又出现了一些新的表面强化工艺,本文着重四个方面介绍,供同行参考。
一、低温化学热处理1.离子渗氮为了提高模具的抗蚀性、耐磨性、抗热疲劳和防粘附性能,可采用离子渗氮。
离子渗氮的突出优点是显著地缩短了渗氮时间,可通过不同气体组份调节控制渗层组织,降低了渗氮层的表面脆性,变形小,渗层硬度分布曲线较平稳,不易产生剥落和热疲劳。
可渗的基体材料比气体渗氮广,无毒,不会爆炸,生产安全,但对形状复杂模具,难以获得均匀的加热和均匀的渗层,且渗层较浅,过渡层较陡,温度测定及温度均匀性仍有待于解决。
离子渗氮温度以450~520℃为宜,经处理6~9h后,渗氮层深约0.2~0.3mm。
温度过低,渗层太薄;温度过高,则表层易出现疏松层,降低抗粘模能力。
离子渗氮其渗层厚度以0.2~0.3mm为宜。
磨损后的离子渗氮模具,经修复和再次离子渗氮后,可重新投入使用,从而可大大地提高模具的总使用寿命。
模具的表面硬化处理
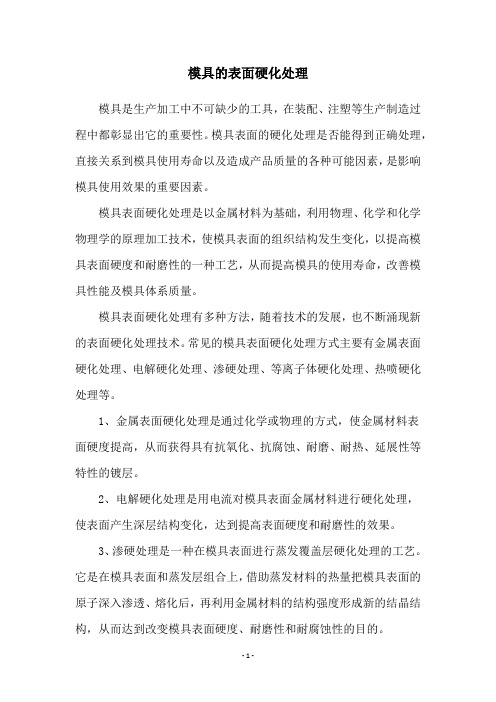
模具的表面硬化处理模具是生产加工中不可缺少的工具,在装配、注塑等生产制造过程中都彰显出它的重要性。
模具表面的硬化处理是否能得到正确处理,直接关系到模具使用寿命以及造成产品质量的各种可能因素,是影响模具使用效果的重要因素。
模具表面硬化处理是以金属材料为基础,利用物理、化学和化学物理学的原理加工技术,使模具表面的组织结构发生变化,以提高模具表面硬度和耐磨性的一种工艺,从而提高模具的使用寿命,改善模具性能及模具体系质量。
模具表面硬化处理有多种方法,随着技术的发展,也不断涌现新的表面硬化处理技术。
常见的模具表面硬化处理方式主要有金属表面硬化处理、电解硬化处理、渗硬处理、等离子体硬化处理、热喷硬化处理等。
1、金属表面硬化处理是通过化学或物理的方式,使金属材料表面硬度提高,从而获得具有抗氧化、抗腐蚀、耐磨、耐热、延展性等特性的镀层。
2、电解硬化处理是用电流对模具表面金属材料进行硬化处理,使表面产生深层结构变化,达到提高表面硬度和耐磨性的效果。
3、渗硬处理是一种在模具表面进行蒸发覆盖层硬化处理的工艺。
它是在模具表面和蒸发层组合上,借助蒸发材料的热量把模具表面的原子深入渗透、熔化后,再利用金属材料的结构强度形成新的结晶结构,从而达到改变模具表面硬度、耐磨性和耐腐蚀性的目的。
4、等离子体硬化处理是利用等离子体的强烈热量,使表面材料发生变化,从而产生一种极强的硬化涂层,从而达到提高表面硬度和耐磨性的效果。
5、热喷硬化处理是将金属材料溶解成熔融态,并在模具表面形成一层薄膜,从而达到提高表面硬度和耐磨性的目的。
选择模具表面硬化处理的方式,需要仔细研究材料、工艺、硬化温度以及表面硬度等技术参数,以及了解模具使用的环境条件,选择硬度、抗腐蚀性和抗氧化性能比较高的表面硬化处理方式,以提高模具的使用寿命,满足生产过程中对模具表面性能要求。
此外,模具表面硬化处理后,还要进行表面处理,使表面光滑、平整,以提高模具的表面质量,减少生产过程中发生的异物污染,保证模具的安全使用。
模具表面处理
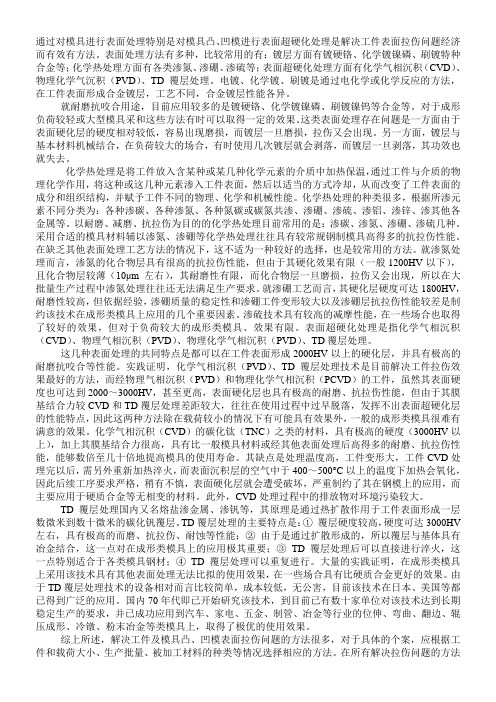
通过对模具进行表面处理特别是对模具凸、凹模进行表面超硬化处理是解决工件表面拉伤问题经济而有效有方法。
表面处理方法有多种,比较常用的有:镀层方面有镀硬铬、化学镀镍磷、刷镀特种合金等;化学热处理方面有各类渗氮、渗硼、渗硫等;表面超硬化处理方面有化学气相沉积(CVD)、物理化学气沉积(PVD)、TD覆层处理。
电镀、化学镀、刷镀是通过电化学或化学反应的方法,在工件表面形成合金镀层,工艺不同,合金镀层性能各异。
就耐磨抗咬合用途,目前应用较多的是镀硬铬、化学镀镍磷、刷镀镍钨等合金等。
对于成形负荷较轻或大型模具采和这些方法有时可以取得一定的效果。
这类表面处理存在问题是一方面由于表面硬化层的硬度相对较低,容易出现磨损,而镀层一旦磨损,拉伤又会出现。
另一方面,镀层与基本材料机械结合,在负荷较大的场合,有时使用几次镀层就会剥落,而镀层一旦剥落,其功效也就失去。
化学热处理是将工件放入含某种或某几种化学元素的介质中加热保温,通过工件与介质的物理化学作用,将这种或这几种元素渗入工件表面,然后以适当的方式冷却,从而改变了工件表面的成分和组织结构,并赋予工件不同的物理、化学和机械性能。
化学热处理的种类很多,根据所渗元素不同分类为:各种渗碳、各种渗氮、各种氮碳或碳氮共渗、渗硼、渗硫、渗铝、渗锌、渗其他各金属等。
以耐磨、减磨、抗拉伤为目的的化学热处理目前常用的是:渗碳、渗氮、渗硼、渗硫几种。
采用合适的模具材料辅以渗氮、渗硼等化学热处理往往具有较常规钢制模具高得多的抗拉伤性能。
在缺乏其他表面处理工艺方法的情况下,这不适为一种较好的选择,也是较常用的方法。
就渗氮处理而言,渗氮的化合物层具有很高的抗拉伤性能,但由于其硬化效果有限(一般1200HV以下),且化合物层较薄(10μm左右),其耐磨性有限,而化合物层一旦磨损,拉伤又会出现,所以在大批量生产过程中渗氮处理往往还无法满足生产要求。
就渗硼工艺而言,其硬化层硬度可达1800HV,耐磨性较高,但依据经验,渗硼质量的稳定性和渗硼工件变形较大以及渗硼层抗拉伤性能较差是制约该技术在成形类模具上应用的几个重要因素。
模具表面处理技术

挤压模、拉深模
提高硬度、强度、耐磨性、耐疲劳性、抗蚀性
挤压模、冲头针尖
提高硬度、耐磨性、耐热疲劳性、抗蚀性、抗粘附性、 抗氧化性
挤压模
提高硬度、耐磨性、抗蚀性、抗粘附性、抗氧化性
挤压模、拉深模
降低表面粗糙度,提高表面硬度、耐疲劳性、抗蚀性 挤压模、拉深模等
钴基合金堆焊 电火花表面强化 喷丸处理
提高硬度、耐磨性、热硬性 提高硬度、强度、耐磨性、耐疲劳性、抗蚀性 提高硬度、强度、耐磨性、耐疲劳性、抗蚀性
一段
490
24
15~35 0.2~0.3 ≥600HV
40Cr 二段
Ⅰ Ⅱ
480±10 500±10
20 15~20
20~30 50~60
0.3~0.5 ≥600HV
4Cr5MoV1 Si
一段
—
530~550ቤተ መጻሕፍቲ ባይዱ
12
30~60
0.15~0.2
760~ 800HV
第九页,共48页。
6.1 表面化学(huàxué)热处理技 术
(2) 碳氮共渗使共渗层的奥氏体相温度降低。
(3) 氮的渗入使共渗层的奥氏体的稳定性提高,渗层的淬火 性提高,这样共渗后除可以用冷却速度较缓慢的介质进行 淬火而减少变形外,还可以用较便宜的碳素钢代替低合金 钢制造某些模具。 (4) 气体碳氮共渗的速度大于单独渗碳或渗氮的速度,缩 短了生产周期。
第十五页,共48页。
二、渗氮(氮化)
(二)离子(lízǐ)渗氮
离子(lízǐ)渗氮有如下特点:
(1) 渗氮速度快,生产周期短。
(2) 渗氮层质量高。
(3) 工件的变形小。
(4) 对材料的适应性强。
第十页,共48页。
模具表面处理
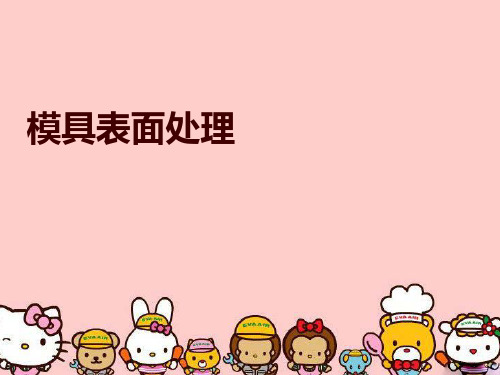
三、模具表面处理分类
2.3 TD覆层工艺流程
温度:通常在850-1050℃之间,核心工艺在900-960℃之间,不同的 材料有 不 同的处理温度。 加工周期:核心工序约12-20小时,全部工序大约为40-60小时之间。
工件收入检查 抛光 装夹 预热
清洗
回火 TD核心工艺
预检测 抛光 检测 公差调整
三、二模、具冲表压面尺处寸理类分型类
3.2 PPD原理 PPD 技术是通过氮离子渗透到模具基体表面来形成超硬抗磨损表面。 在真空环境中,通过腔体壁之间的电压和载荷,氮气和氢气分子电离(工具表面可
见)。气体离子开始与模具基体离子反应形成硬化渗氮区域。处理工艺是通过渗透扩散而 非涂层进行的。
3.3 PPD工艺流程
三、模具表面处理分类
分类 通过对模具进行表面处理特别是对模具进行表面超硬化处理是解决工件表面拉伤问题经
济而有效的方法。表面处理方法有多种,比较常用的如下。
镀层方面
表面超硬化处理方面
镀刷化
化学气 物理气
物理化
TD
硬镀学
相沉积 相沉积
学气相
覆
铬特镀
CVD PVD
沉积
层
种镍
PCVD
处
合磷
理
金
渗入处理方面
类、翻边模具
类、翻边模具
型类模具
模具镶块
4.3 优点
工艺
二四、、冲优压缺尺点寸对类比型
PPD
镀硬铬
PVD,PCVD
TD覆层处理
场合
工艺环保、抗磨损效 果好
成本低、处理周期短
具有极高的耐磨抗 咬合等性能
耐磨、成本低、工 艺环保
4.4 缺点
工艺
模具表面处理对塑件质量
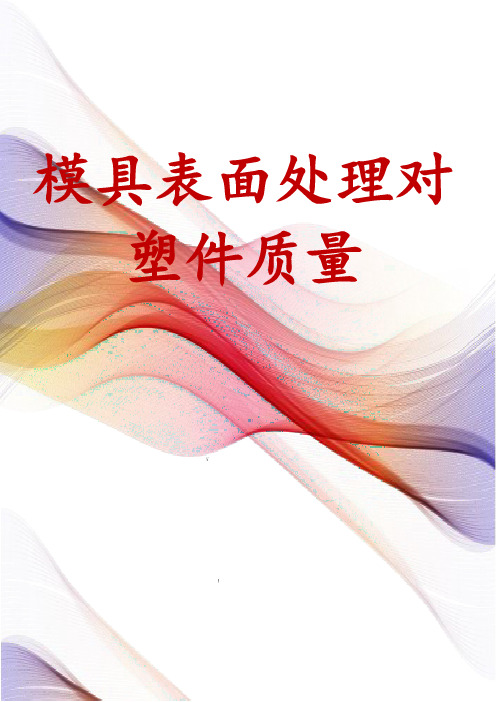
模具表面处理对塑件质量一、模具表面处理技术概述模具表面处理技术是塑料加工行业的一项关键技术,它直接影响到塑料制品的质量和生产效率。
模具表面处理技术主要包括表面抛光、表面涂层、表面硬化处理等。
通过这些处理方式,可以显著提高模具的耐用性、减少生产过程中的摩擦、提高塑件的表面质量等。
模具表面处理技术的发展,不仅能够推动塑料加工行业的进步,还将对整个制造业产生深远的影响。
1.1 模具表面处理技术的核心特性模具表面处理技术的核心特性主要包括以下几个方面:- 耐磨性:通过表面处理,模具表面能够抵抗磨损,延长模具的使用寿命。
- 耐腐蚀性:模具表面处理能够提高模具的耐腐蚀性,减少因腐蚀而导致的模具损坏。
- 表面光洁度:通过表面抛光和涂层处理,模具表面能够达到更高的光洁度,从而提高塑件的表面质量。
- 减少粘附性:表面处理可以减少模具与塑料材料之间的粘附性,降低生产过程中的不良品率。
1.2 模具表面处理技术的应用场景模具表面处理技术的应用场景非常广泛,包括但不限于以下几个方面:- 汽车零部件:汽车零部件对模具的耐磨性和表面光洁度要求极高,模具表面处理技术在这一领域应用广泛。
- 家用电器:家用电器如冰箱、洗衣机等的塑料外壳,需要模具表面处理技术来保证其外观和耐用性。
- 医疗器械:医疗器械的塑料部件需要模具表面处理技术来提高其耐腐蚀性和表面光洁度。
- 包装行业:包装行业的塑料制品如瓶子、盒子等,也需要模具表面处理技术来提高其外观和耐用性。
二、模具表面处理技术的分类与工艺模具表面处理技术的种类繁多,每种技术都有其独特的工艺和应用领域。
以下是几种常见的模具表面处理技术及其工艺。
2.1 表面抛光技术表面抛光技术是通过对模具表面进行物理或化学处理,使其达到所需的光洁度。
常见的表面抛光技术包括:- 机械抛光:通过机械摩擦的方式,去除模具表面的毛刺和不平整,提高表面光洁度。
- 化学抛光:通过化学腐蚀的方式,去除模具表面的氧化物和杂质,提高表面光洁度。
- 1、下载文档前请自行甄别文档内容的完整性,平台不提供额外的编辑、内容补充、找答案等附加服务。
- 2、"仅部分预览"的文档,不可在线预览部分如存在完整性等问题,可反馈申请退款(可完整预览的文档不适用该条件!)。
- 3、如文档侵犯您的权益,请联系客服反馈,我们会尽快为您处理(人工客服工作时间:9:00-18:30)。
•(3) 氮的渗入使共渗层的奥氏体的稳定性提高,渗层的 淬火性提高,这样共渗后除可以用冷却速度较缓慢的介 质进行淬火而减少变形外,还可以用较便宜的碳素钢代 替低合金钢制造某些模具。 •(4) 气体碳氮共渗的速度大于单独渗碳或渗氮的速度, 缩短了生产周期。
•(4) 共渗层硬而具有一定的韧性,不易剥落。
PPT文档演模板
第六章模具表面处理技术
6.1 表面化学热处理技术
•五、渗硼
•渗硼的特点如下:
•(1) 渗硼层的硬 度很高。
•(3) 热硬性高。
•(2) 耐蚀性高。
•(4) 耐热性高。
PPT文档演模板
第六章模具表面处理技术
6.1 表面化学热处理技术
•五、渗硼
•(4) 沉积速度快,生产率高。
•(5) 操作安全,对环境污染小。
PPT文档演模板
第六章模具表面处理技术
6.2 涂 镀 技 术
•三、化学镀
•化学镀是利用合适的还原剂, 使溶液中的金属离子在经催化的 表面上还原出金属镀层化学方法。
PPT文档演模板
第六章模具表面处理技术
6.2 涂 镀 技 术
•四、热浸镀
6.2 涂 镀 技 术
•二、电刷镀
PPT文档演模板
•图6-4 电刷镀工作原理示意图
第六章模具表面处理技术
6.2 涂 镀 技 术
•二、电刷镀
•电刷镀具有以下特点: •(1) 镀层质量高。 •(2) 不受镀件、模具形状和大小的限制,设备 简单,工艺灵活,操作方便,可在现场作业。 •(3) 可以进行槽镀困难或实现不了的局部电镀。
•(2) 渗氮后钢的疲劳极限可提高15%~35%。这是由于渗氮层的 体积增大,使工件表面产生了残余压应力。
•(3) 渗氮后的钢具有很高的抗腐蚀能力。
•(4) 渗氮处理后,工件的变形很小,适合精密模具的表面强化。
PPT文档演模板
第六章模具表面处理技术
6.1 表面化学热处理技术
•二、渗氮(氮化)
•(一)气体渗氮
6.1 表面化学热处理技术
•四、碳氮共渗与氮碳共渗
•(一)碳氮共渗
•低温(500~ 600℃)
•高温(900~950℃)
•根据共渗温 度的不同
PPT文档演模板
•中温(700~880℃)
第六章模具表面处理技术
6.1 表面化学热处理技术
•四、碳氮共渗与氮碳共渗
•气体碳氮共渗的特点如下: •(1) 共渗层的力学性能综合了渗碳和渗氮的优点。
•二、渗氮(氮化)
•(二)离子渗氮
•离子渗氮有如下特点: •(1) 渗氮速度快,生产周期短。
•(2) 渗氮层质量高。
•(3) 工件的变形小。
•(4) 对材料的适应性强。
PPT文档演模板
第六章模具表面处理技术
6.1 表面化学热处理技术
•二、渗氮(氮化)
•(二)离子渗氮
•表6-3 部分模具钢的离子渗氮工艺与使用效果
6.3 其他表面处理技术
•二、激光表面处理
•图6-5 激光表面处理装置示意图
PPT文档演模板
第六章模具表面处理技术
6.3 其他表面处理技术
•三、离子注入
PPT文档演模板
•图6-6 离子注入装置示意图
第六章模具表面处理技术
6.3 其他表面处理技术
•三、离子注入
•离子注入技术与气相沉积、等离子喷涂、电子束和激光 束热处理等表面处理工艺不同,其主要特点是:
•二、激光表面处理
•激光表面处理的特点有:
•(3) 畸变极小,可大大减少后续加工工时。
•(4) 利用高能束可以对材料的表面实现相变 硬化、微晶化、冲击加热硬化、覆层镀层合 金化等多种表面改性处理,可产生用其他表 面加热处理淬火强化难以达到的表面成分、 组织、性能的改变。
PPT文档演模板
第六章模具表面处理技术
40Cr 二段
Ⅰ Ⅱ
480±10 500±10
20 15~20
20~30 50~60
0.3~0.5
表面硬度
>58HRC 720~ 860HV
≥600HV
≥600HV
4Cr5MoV1 Si
一段
—
530~550
12
30~60
0.15~0.2
பைடு நூலகம்
760~ 800HV
PPT文档演模板
第六章模具表面处理技术
6.1 表面化学热处理技术
第六章__模具表面处理 技术
PPT文档演模板
2020/11/30
第六章模具表面处理技术
•表6-1 模具表面处理技术的作用及应用
处理工艺 渗碳 渗氮
离子渗碳
碳氮共渗
氮碳共渗
渗硼 碳氮硼三元共渗 盐浴覆层 (TD处理) 渗铬
作用
应用
提高硬度(52~56HRC)、耐磨性、耐疲劳性
挤压模、穿孔工具等
提高硬度、耐磨性、抗粘附性、热硬性、耐疲劳性、抗 蚀性(但周期长,表面有白色脆化层)
6.3 其他表面处理技术
•一、热喷涂
•喷涂前预处 理
•喷后处理
•热喷涂工艺过 程
•喷涂
•利用热源将金属或非金属材料熔化、半熔化或软化, 并以一定速度喷射到基体表面,形成涂层的方法
PPT文档演模板
第六章模具表面处理技术
6.3 其他表面处理技术
•一、热喷涂
•根 据所 用热 源的 不同 来分 类
•燃气法 •气体放电法 •电热法 •激光热源法
挤压模、冷挤模等
可消除表面白色的脆化层,耐磨性、耐疲劳性和变形均 优于氮化
挤压模、挤压工具等
相比渗碳和渗氮,具有更高的硬度、耐磨性、耐疲劳性、成型模、冷挤模、热挤模和模
热硬性、热强性,生产周期短
架等
提高硬度、耐磨性、抗粘附性、抗蚀性、耐热疲劳性
冷挤模、拉深模、挤压模穿孔 针
具有极好的表面硬度、耐磨性、抗粘附性、抗氧化性、 热硬性、良好的抗蚀性
•热浸镀简称热镀,是将基体金 属浸在熔融状态的另一种低熔点 金属中,在其金属表面发生一系 列物理和化学反应,形成一层保 护膜的方法。
PPT文档演模板
第六章模具表面处理技术
6.2 涂 镀 技 术
•四、热浸镀
•根 据热 浸镀 前处 理的 方法 不同
•溶剂法 •保护气法
PPT文档演模板
第六章模具表面处理技术
提高硬度、耐磨性、热硬性 提高硬度、强度、耐磨性、耐疲劳性、抗蚀性 提高硬度、强度、耐磨性、耐疲劳性、抗蚀性
挤压模冲头、芯杆针尖 冷、热挤压模等 热挤压模、冲头针尖
PPT文档演模板
第六章模具表面处理技术
6.1 表面化学热处理技术
•表面化学热处理的作用主要有以下两个方面。 •(1) 强化工件表面 •(2) 保护工件表面
•渗硼的特点如下:
•固体渗硼
•液体渗硼
•渗硼的方法
PPT文档演模板
•气体渗硼
第六章模具表面处理技术
6.1 表面化学热处理技术
•五、渗硼
•表6-4 部分模具渗硼的强化效果
模具名称
钢号
淬火、回火态寿命
冷冲裁模
CrWMn
0.5万件
热挤压模
30Cr3W5V
100h
热锻模
5CrNiMo
0.5万件
热锻用冲头
55 Ni2CrMnMo
PPT文档演模板
第六章模具表面处理技术
6.3 其他表面处理技术
•三、离子注入
•离子注入技术与气相沉积、等离子喷涂、电子束和激光 束热处理等表面处理工艺不同,其主要特点是:
•(3) 离子注入层相对于基体材料没有边缘清晰的界面, 因此表面不存在粘附破裂或剥落的问题,与基体结合牢 固。 •(4) 离子注入控制电参量,故易于精确控制注入离子的密 度分布,浓度分布可以通过改变注入能量加以控制。
挤压模、拉深模
提高硬度、强度、耐磨性、耐疲劳性、抗蚀性
挤压模、冲头针尖
提高硬度、耐磨性、耐热疲劳性、抗蚀性、抗粘附性、 抗氧化性
挤压模
提高硬度、耐磨性、抗蚀性、抗粘附性、抗氧化性 挤压模、拉深模
镀硬铬
降低表面粗糙度,提高表面硬度、耐疲劳性、抗蚀性 挤压模、拉深模等
钴基合金堆焊 电火花表面强化 喷丸处理
•表6-2 部分模具钢的气体渗氮工艺规范
牌号
处理 方法
30CrMnSi A
一段
Cr12MoV 二段
阶段 — Ⅰ Ⅱ
渗氮工艺规范 渗氮温度/℃ 时间/h
500±5
25~30
480
18
530
25
氨分解率 /%
20~30
渗氮层 深度/mm
0.2~0.3
14~27 36~60
≤0.2
一段
490
24
15~35 0.2~0.3
100h
连杆热成型模
5CrMnMo
2万件
冷镦六方螺母凹模
Cr12MoV
0.5万件
冷轧顶头凸模
65Mn
0.4万件
渗硼态寿命 1万件 261h 1万件 240h 6万件 6万件 2万件
PPT文档演模板
第六章模具表面处理技术
6.1 表面化学热处理技术
•六、渗金属
•渗铬 •渗钒及TD法渗钒 •渗铌 •渗铝
PPT文档演模板
第六章模具表面处理技术
6.1 表面化学热处理技术
•二、渗氮(氮化)
•气体渗氮
•常
用
•离子渗氮
的
渗
•真空渗氮
氮
方
•电解催渗渗氮
法
•氮碳共渗
PPT文档演模板
第六章模具表面处理技术
6.1 表面化学热处理技术