实验3 聚丙烯塑料注射成型 (2)
聚丙烯的注塑成型实验

实验二、聚丙烯的注塑成型实验一、实验原理1.了解塑料注塑成型的基木原理;2.了解注塑机的构成,熟悉其基木实验操作3.掌握温度、压力、转速和时间等工艺参数对塑料成型性能和质量的关系。
二、实验原理注射成型时热塑性塑料的一种重要成型方法。
迄今为止,除氟塑料外,几乎所有的热塑性塑料都可以采用此方法成型;它的特点是生产周期快、适应性强、生产率高和易于自动化等,因此广泛地用于塑料制品的生产过程中。
塑料注射成型是利用塑料的可挤压性和可模塑性,首先将松散的粒料或粉状成型物料从注塑机的料斗送入高温的机筒内加热熔融塑化, 使其逐渐溶解,并呈粘流状态,然后在螺杆或柱塞的高压推动下,以很大的流速通过料筒前端的喷嘴将熔体注入到低温闭合的模具中,经一段时间保压冷却定型时间后,开模取出具有一定形状和尺寸的塑料制件。
移动螺杆式和柱塞式注射机主要由注射系统、锁模系统和塑模三大部分组成。
①注射系统。
注射系统是注射机的主要部分,其作用是使塑料塑化和均化,并在很高的压力和较快的速度下,通过螺杆和柱塞的推挤将熔料注射人模具。
注射系统包括加料计量装置、料筒、柱塞和分流棱、螺杆、喷嘴及加压和驱动装置等部件。
②锁模系统。
在注射机上实现锁合模具、启闭模具(又称合模装置)和顶出制件的机构总称为锁模系统。
锁模装置是保证成型模具可靠的闭锁、开启并取出制品的部件。
③ 模塑。
塑模亦称模具,是在成型中赋予塑料制件以形状和尺寸的部件组合体。
塑模的作用是:完成塑料制品所需的外形尺寸、强度及性能要求。
整个注射模塑过程包括加料、塑化、注射入模、稳压冷却和脱模几个步骤。
而注射模塑最重要的工艺条件是影响塑化流动和注射冷却的温度、压力和相应的各个作用时间。
总之,要获得一个满意的注射制品,必须综合运用以下四个方面的有利因素:①制品形状的合理设计和塑料品种的恰当选择;②合理的模具结构;②注射机的种类和结构;④成型工艺条件的选择和控制。
三、主要仪器设备及其技术特征和实验原料主要仪器设备:EM80-V精密注射成型机。
聚丙烯注塑工艺(3篇)

第1篇一、引言聚丙烯(PP)是一种常用的热塑性塑料,具有良好的耐化学性、耐热性、绝缘性、机械强度和加工性能。
聚丙烯注塑工艺是将聚丙烯颗粒加热熔化,通过注塑机将熔体注入模具中,冷却固化后得到所需形状的塑料制品。
本文将详细介绍聚丙烯注塑工艺的原理、设备、工艺参数及注意事项。
二、聚丙烯注塑工艺原理聚丙烯注塑工艺主要包括以下几个步骤:1. 预塑:将聚丙烯颗粒加入注塑机料斗,通过料斗加热使颗粒熔化。
2. 注塑:将熔化的聚丙烯熔体通过注塑机的螺杆推进,注入模具腔内。
3. 冷却:注塑完成后,模具中的熔体开始冷却固化。
4. 开模取件:冷却固化后,打开模具取出成品。
5. 后处理:对成品进行清洗、干燥等处理。
三、聚丙烯注塑设备1. 注塑机:注塑机是聚丙烯注塑工艺的核心设备,主要有螺杆式注塑机和柱塞式注塑机两种类型。
2. 模具:模具是注塑工艺中另一个重要设备,用于成型聚丙烯制品。
3. 辅助设备:辅助设备包括料斗、加热器、冷却器、控制系统等。
四、聚丙烯注塑工艺参数1. 加热温度:聚丙烯的熔化温度一般在160℃~220℃之间,具体温度根据聚丙烯牌号和注塑机型号进行调整。
2. 注塑压力:注塑压力一般在60MPa~120MPa之间,具体压力根据制品的壁厚和形状进行调整。
3. 注塑速度:注塑速度分为慢速、中速和快速,应根据聚丙烯的熔化性能和制品的形状进行调整。
4. 冷却时间:冷却时间取决于制品的壁厚和冷却效果,一般控制在15~30秒之间。
5. 模具温度:模具温度一般在50℃~100℃之间,具体温度根据聚丙烯的熔化性能和制品的形状进行调整。
五、聚丙烯注塑工艺注意事项1. 聚丙烯颗粒的干燥:聚丙烯颗粒在注塑前应进行干燥处理,以防止注塑过程中产生气泡和降解。
2. 模具预热:注塑前应对模具进行预热,以防止模具温度过低导致制品表面出现缩痕。
3. 螺杆转速:螺杆转速应根据聚丙烯的熔化性能和注塑速度进行调整,以防止熔体过热或过冷。
4. 注塑压力:注塑压力应根据制品的壁厚和形状进行调整,以防止制品出现变形和缺陷。
塑料成型实验报告

一、实验目的1. 理解塑料成型工艺的基本原理和过程。
2. 掌握塑料成型过程中主要工艺参数对成型质量的影响。
3. 通过实验,验证理论知识的正确性,并提高动手操作能力。
4. 学习使用塑料成型设备,了解不同成型方法的适用范围。
二、实验原理塑料成型是将塑料原料加热熔化,然后在压力和(或)模具的作用下,使其成型为所需形状和尺寸的制品。
根据成型方法的不同,塑料成型可分为挤出成型、注塑成型、吹塑成型、压塑成型等。
三、实验器材1. 塑料原料:聚乙烯(PE)、聚丙烯(PP)等。
2. 塑料成型设备:挤出机、注塑机、吹塑机、压塑机等。
3. 模具:挤出模具、注塑模具、吹塑模具、压塑模具等。
4. 辅助设备:加热器、冷却水系统、物料输送设备等。
四、实验方法与步骤1. 挤出成型实验(1)将塑料原料放入挤出机料斗,调整温度和压力,使塑料熔化。
(2)打开挤出机,使熔融塑料通过挤出模具,形成所需形状的制品。
(3)调整模具和设备参数,观察制品的质量,记录实验数据。
2. 注塑成型实验(1)将塑料原料放入注塑机料斗,调整温度和压力。
(2)将模具闭合,注入熔融塑料,使其充满模腔。
(3)保压一定时间,使塑料冷却固化。
(4)打开模具,取出制品,观察质量,记录实验数据。
(1)将塑料原料放入吹塑机料斗,调整温度和压力。
(2)将熔融塑料通过挤出机挤出,形成型坯。
(3)将型坯放入吹塑模具,通入压缩空气,使其吹胀成型。
(4)冷却、脱模,取出制品,观察质量,记录实验数据。
4. 压塑成型实验(1)将塑料原料放入压塑机料斗,调整温度和压力。
(2)将模具闭合,使塑料熔化。
(3)施加压力,使塑料充满模腔。
(4)保压一定时间,使塑料冷却固化。
(5)打开模具,取出制品,观察质量,记录实验数据。
五、实验结果与分析1. 挤出成型实验实验结果表明,挤出成型过程中,温度和压力对制品质量有显著影响。
温度过高或过低会导致熔体流动性差,制品表面出现气泡、熔接痕等缺陷;压力过大或过小会影响制品尺寸精度和外观。
塑料注射成型实验报告
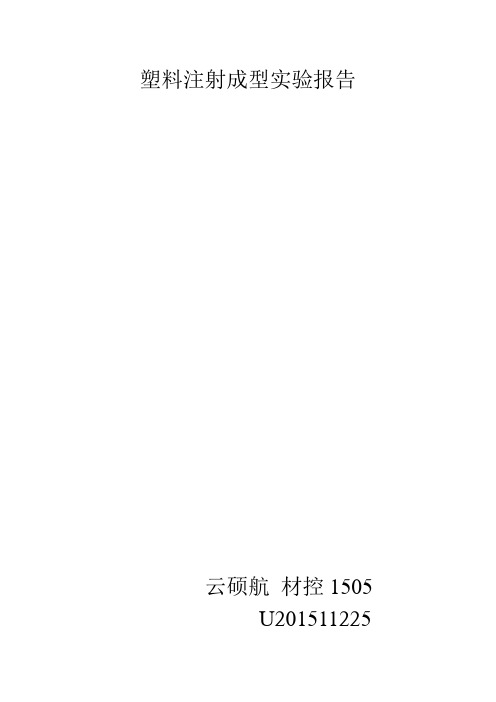
云硕航材控1505U2015112251.预习部分1)塑料注射成型的概念(1)注射成型周期注射成型周期是指模具连续生产时,完成一次注射成型工艺过程所需的时间,它由注射时间、保压时间、冷却时间和辅助时间组成。
(2)注射成型的主要缺陷短射(Short shot):短射又称欠注、充填不足、制件不满、走胶不齐等,是指型腔未完全充满,使得制件不饱满、塑件外形残缺不完整的现象。
产生的机理是熔体在流向末端的过程中冷却。
飞边(Flash):飞边又称溢料、溢边、毛边、批锋等,是指在模具的不连续处(通常是分模面、排气孔、排气顶针、滑动机构等)过量充填造成塑料外溢的瑕疵。
产生的机理是注射和保压过程中锁模力不够,或是无法沿分型面将模具锁紧,模板间隙超过了塑料的溢料值。
熔合纹(Weld/meld lines)熔合纹又称熔接痕、熔接不良、熔合缝、缝合线等,是指各塑料流体前端相遇时在制品表面形成的一条线状痕迹,不仅有碍制品的美观,而且影响制品的力学性能。
产生的机理是由若干熔体在型腔中汇合在一起时,在其交汇处彼此不能熔合为一体而形成线状痕迹。
翘曲(Warpage)翘曲是指制品产生弯曲或扭曲现象,导致平坦的地方有起伏,直边朝里或朝外弯曲或扭曲,产生的机理是高分子链在成形中产生残余应力,脱模时制品的外部约束去除,残余应力的存在造成不同程度的变形。
还有喷射(Jetting)气穴(Air Traps)滞流(Hesitation)过保压(Overpacking)凹陷/空洞(Sink marks and voids)烧痕(Burn marks)Flow marks)银线痕(Silver streaks)裂纹(Crack)等等。
(3)成型的主要工艺对于缺陷,质量的影响注射速度:主要影响熔体在型腔内的流动行为,通常伴随着注射速度的增大,熔体流速增加,剪切力作用增强,熔体内温度因剪切发热而升高,粘度降低,所以有利于充模。
并且制品的融合纹强度也增加。
注射成型实验报告
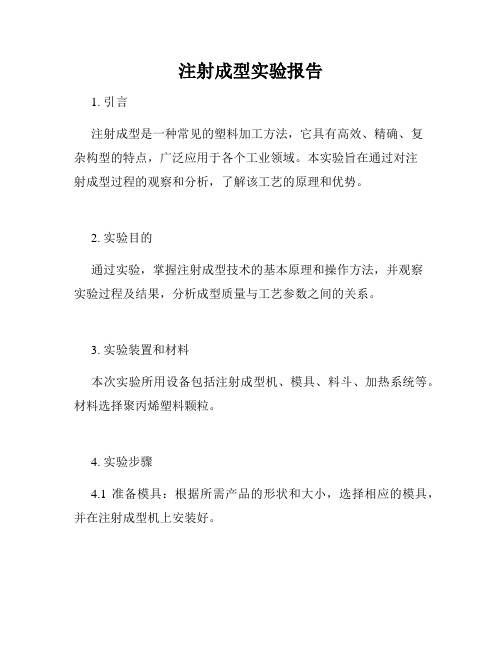
注射成型实验报告1. 引言注射成型是一种常见的塑料加工方法,它具有高效、精确、复杂构型的特点,广泛应用于各个工业领域。
本实验旨在通过对注射成型过程的观察和分析,了解该工艺的原理和优势。
2. 实验目的通过实验,掌握注射成型技术的基本原理和操作方法,并观察实验过程及结果,分析成型质量与工艺参数之间的关系。
3. 实验装置和材料本次实验所用设备包括注射成型机、模具、料斗、加热系统等。
材料选择聚丙烯塑料颗粒。
4. 实验步骤4.1 准备模具:根据所需产品的形状和大小,选择相应的模具,并在注射成型机上安装好。
4.2 加热系统设置:将合适的温度设定在注射成型机上的加热系统中,调试加热管的位置和温度,以确保塑料颗粒能够均匀加热并熔化。
4.3 塑料颗粒准备:将聚丙烯塑料颗粒倒入料斗内,并保证颗粒的充填量和均匀度。
4.4 操作注射成型机:启动注射成型机,将塑料颗粒通过螺杆加热、熔化,并注入模具中。
根据实验要求调节注射速度、注射压力和料斗的温度等参数。
4.5 冷却和脱模:完成注射后,辅助冷却系统将热塑料迅速冷却并固化。
最后,通过脱模系统将成品从模具中取出。
5. 实验结果与分析观察实验得到的成品,评价其质量与各个工艺参数的关系。
分析注射速度、注射压力、冷却时间等因素对成型质量的影响。
6. 注射成型工艺优缺点6.1 优点注射成型工艺可以实现批量生产,有效提高生产效率和产品质量。
注射成型可制作的产品形状丰富,适用范围广泛,可满足不同领域的需求。
注射成型过程中,材料利用率高,减少浪费,有利于环境保护和节约资源。
6.2 缺点注射成型设备投资较高,需要专业的操作技术和模具制造。
工艺参数的调试相对复杂,对生产操作人员的要求较高。
对于特殊材料和大尺寸产品,注射成型工艺的设备和模具尺寸限制较大。
7. 结论通过本次实验,了解了注射成型技术的基本原理和操作方法。
注射成型工艺具有很多优点,但也存在一些限制。
在实际应用中,根据产品的需求和要求,选择合适的注射成型工艺参数以及材料,可以获得高质量的成品。
实验三 热塑性塑料注射成型

实验三热塑性塑料注射成型一、概述注射成型是热塑性塑料的主要成型方法,已配好的粒料或粉料加入料斗后,进入机筒,在外部加热和内部摩擦热的作用下,树脂熔化成为塑化均匀、温度均匀、组分均匀的混合物堆积在机筒内螺杆或柱塞的前部。
通过柱塞或螺杆向前推进,使一定量的熔体在压力下通过喷嘴进入模具内腔,经过一定时间的保压和冷却,便可开模取出制品。
温度、压力和时间是注塑工艺的三大要素,除了考虑它们对制品的质量影响之外,还需考虑生产周期的长短。
二、实验目的1、了解塑料注射机的基本结构,掌握注塑成型的基本工艺过程。
2、对影响注塑制品质量的工艺因素有感性认识。
三、原料和仪器设备聚丙烯(注塑级)、HIPS 注射机、秒表、半导体点湿计、表面温度计。
四、实验步骤1、拟实验方案,按下列内容,根据原料成型工艺条件和试样质量要求,拟出实验方法。
①树脂干燥条件;②机筒各段温度和喷嘴加热;③注射压力、注射速度④注射时间、保压时间、冷却时间;⑤制品后处理。
2、操作①按注射机操作规程调整注射机并安装模具。
②按电源加热;③注射机各段温度指示达到规定值后,恒温10~20min。
进料、对空注射如喷出物料光滑明亮,无变色、银丝、气泡,则表明料筒和喷嘴温度较适合,即可用手动操作方式进行注射试样。
④制样过程中,用点温度计直接测量料温两次,用表面温度计测模具型腔温度(动、定模各取三点)两次。
⑤注射压力可读压力表值,注射速度用秒表测定螺杆前进速度。
⑥成型周期各阶段时间用秒表测量。
⑦制备试样过程中,模具型腔和流道不可涂擦润滑性物质。
⑧长条形试样和冲击试样在两组不同成型条件下,各取六模,取样前必须在达到稳定操作条件后,舍去五模以上。
⑨对试样作外观质量检查。
⑩将实验编号以备作力学性能测试。
五、按下表记录注射成型1、原料名称规格:名称_____ 牌号______2、干燥条件:干燥时间_____ 湿含量______%3、注射机:型号_____ 螺杆结构_______喷嘴结构_________ (自锁式)4、模具________型式_________ 每模试样数_____进料口尺寸(mm)_______5、成型条件6、后处理条件:后处理方法介质________ 温度________时间________六、思考题1.用自己的话叙述注射工艺过程。
塑料的综合性实验 二

塑料的综合性实验二一.前言(1)聚丙烯(PP)作为通用树脂之一,和其它通用树脂相比,具有较好的综合机械性能,并且相对密度较小,透明性及表面光泽好,耐热性能高,其维卡软化温度高于HDPE 和ABS,可在120℃下连续使用。
其加工方式可采用挤出、注射等成型方法,广泛应用于汽车工业、家用电器、化学建材等行业。
但是,尽管聚丙烯具有如此优良的性能,在许多实际应用中,由于是使用目的不同,对某些性能的侧重要求也不相同,因此,许多改性专用料就相应而生。
利用纳米无机材料来改性PP 就是一种。
综合性实验一中,大部分都是手工进行生产,包括炼塑、铣床等都是人工操作,在科技进步的今天,这些机器和技术与现代相比都显得比较落后而且没有任何的生产力可比性。
所以有必要对比较先进的自动化生产线有一些了解,这个就是实验二的目的。
在这个实验里,将会利用具有较高自动化的双螺杆挤出机制备聚合物基纳米复合材料,掌握一种新的制备复合材料的方法,这对拓展聚合物的种类、改善其性能具有重要的科学意义。
本实验通过CTE-35 型双螺杆挤出机达到用纳米材料改性聚丙烯的目的。
(2)CTE-35 双螺杆挤出机工作原理CTE-35 双螺杆挤出机主要用于热塑性聚合体的填充和增强。
聚合体和添加剂预混合后,通过合适的计量喂料装置连续地加入双螺杆混炼机的第一节筒体。
挤出机的第一节筒体通过水冷却方式不断地进行冷却,这是它与其他筒体不同的地方。
其它筒体在生产过程中根据生产工艺的需要和各区的温度调节,通过电加热或冷却。
在最后一节筒体中,设备通过足够的压力,将物料从机头中挤出。
通过装在挤出部分上的熔体温度表和熔体压力表,可以检测物料是否稳定,可否再加工。
螺杆元件是用来喂入并传送物料的。
CTE系列挤出机可以喂入粉末、颗粒、片状、熔融状、糊状物等。
两根螺杆同向旋转、紧密啮合,这使得物料崛起、传送并压缩。
然后,物料开始熔融。
物料的熔融主要是通过捏合元件来实现的。
在熔融的过程中,将添加剂和稳定剂均匀地加入高聚物的熔体中。
聚丙烯注射工艺参数确定.

聚丙烯的注塑工艺条件
工艺条件
机筒温度/℃ 后部 中部 前部
喷嘴温度/℃ 模具温度/℃ 注射压力/MPa 注射时间/s 冷却时间/s 螺杆转速/RPM
PP
160~180 180~200 200~230 180~190 20~60 70~100 20~60 20~90
<80
二、聚丙烯(PP)
聚丙烯的收缩,85~95%在成型加工后的24小时内出现,要 经过大约一周时间收缩才大体完成。如果出模后将制件泡在沸水 中10-15分钟,可以因应力造成的尺寸变化基本固定下来。
二、聚丙烯(PP)
聚丙烯的熔体在压力作用下有比较强的穿越能力,容易产生 飞边毛刺,在生产中要特别注意模具的维护。
二、聚丙烯(PP)
在分析聚丙烯制件出现收缩变型和凹陷原因时,不难发现主要在于注射压力或 注射速度不足。聚丙烯的收缩率的大小主要取决于注射压力、注射温度、模具温度、 加入的模料及有无成核剂等。
凡能降低结晶生长速度的因素将有于减小收缩率。例如,模具温度越低,熔体 越容易冷却,收缩率就越小;提高熔体温度也可以降低收缩率。这可能是由于熔体 温度越高,大分子链的无序性程序也越高,因此不容易结晶,收缩率就低。而当熔 体温度的结晶熔触温度(120~125)高得不太多的时候,某个分子的有序性是可能存 在的,这样的有序区将成为晶核生成的中心,因而在冷却时,结晶进行得也越快, 所以收缩率就大。
注射成型实验报告
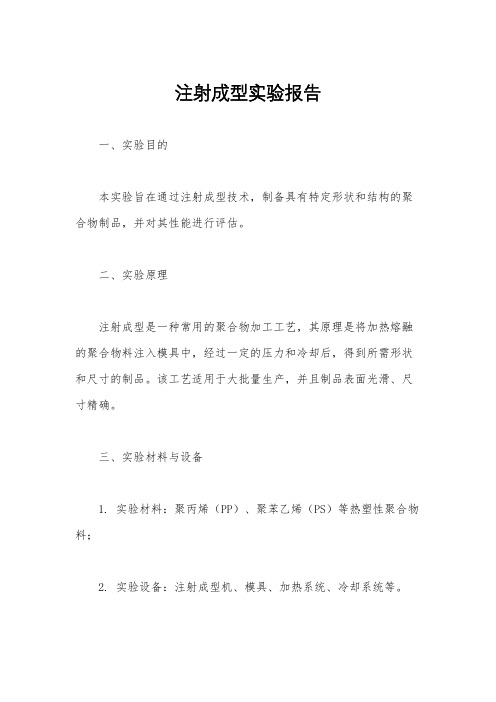
注射成型实验报告一、实验目的本实验旨在通过注射成型技术,制备具有特定形状和结构的聚合物制品,并对其性能进行评估。
二、实验原理注射成型是一种常用的聚合物加工工艺,其原理是将加热熔融的聚合物料注入模具中,经过一定的压力和冷却后,得到所需形状和尺寸的制品。
该工艺适用于大批量生产,并且制品表面光滑、尺寸精确。
三、实验材料与设备1. 实验材料:聚丙烯(PP)、聚苯乙烯(PS)等热塑性聚合物料;2. 实验设备:注射成型机、模具、加热系统、冷却系统等。
四、实验步骤1. 准备工作:清洁注射成型机和模具,将所需聚合物料加入注射成型机的料斗中;2. 开机预热:启动注射成型机,将聚合物料加热至熔融状态;3. 调试参数:根据所需制品的尺寸和性能要求,调整注射成型机的注射压力、注射速度、冷却时间等参数;4. 注射成型:将熔融的聚合物料注入模具中,施加一定的压力,使其充填模具腔体,并进行冷却;5. 取模检验:冷却后,取出成型制品,进行外观质量、尺寸精度、物理性能等方面的检验。
五、实验结果与分析经过注射成型制备的聚丙烯制品外观光滑,尺寸精确,表面无明显缺陷。
经过拉伸测试,其拉伸强度为25MPa,弯曲强度为30MPa。
经过冲击测试,其冲击强度为10KJ/m²。
而经过注射成型制备的聚苯乙烯制品外观光滑,尺寸精确,表面无明显缺陷。
经过拉伸测试,其拉伸强度为30MPa,弯曲强度为35MPa。
经过冲击测试,其冲击强度为15KJ/m²。
六、实验结论通过注射成型技术,成功制备了具有特定形状和结构的聚合物制品,并对其性能进行了评估。
实验结果表明,注射成型制备的聚合物制品具有良好的外观质量、尺寸精度和物理性能,符合预期要求。
因此,注射成型技术在聚合物制品加工中具有重要的应用价值。
七、参考文献1. 刘明,杨华. 注射成型技术在聚合物制品加工中的应用[J]. 中国塑料, 2018(6): 45-49.2. 张三,李四. 聚合物注射成型工艺及其应用[M]. 北京: 化学工业出版社, 2017.以上为注射成型实验报告。
注塑实验总结报告

注塑实验总结报告注塑实验总结报告注塑实验是材料工程专业学生必修的一门实验课程。
通过这门实验课程,我们学习了注塑技术的原理和操作方法,掌握了塑料材料的特性及其在注塑过程中的变化规律。
本次实验使用了聚丙烯(PP)作为塑料材料,通过调整注塑工艺参数,如温度、压力、注塑时间等,获得了不同的注塑产品,并对其进行了测试分析。
以下是本次注塑实验的总结报告。
一、实验目的本次实验的目的是通过注塑工艺制作出符合要求的聚丙烯产品,并对其进行性能测试,以评估注塑工艺参数对产品性能的影响。
二、实验步骤1. 准备工作:将聚丙烯颗粒加入注塑机的料斗中,根据要求设置好注塑机的温度、压力等参数。
2. 开始注塑:启动注塑机,使其预热到设定温度,然后将熔融状态的聚丙烯注入模具腔内,开始注塑过程。
3. 注塑完毕:注塑时间结束后,等待注塑产品冷却,然后取出注塑产品。
4. 进行性能测试:对注塑产品进行拉伸强度、抗冲击性等性能测试,记录测试结果。
三、实验结果通过调整温度、压力等参数,我们成功制作出了一批聚丙烯注塑产品。
在测试过程中,我们发现不同的工艺参数对注塑产品的性能有着明显的影响。
首先,我们发现调节温度对产品质量有着重要影响。
过高或过低的温度都会导致产品的性能下降。
在合适的温度范围内,产品的拉伸强度、抗冲击性等性能指标较好。
其次,压力的控制也十分关键。
过高的压力会导致产品变形不完整或出现气孔等缺陷,而过低的压力则会影响产品的密实性。
我们通过调整压力,找到了最佳的注塑条件,从而获得了质量较好的产品。
最后,注塑时间的控制也非常重要。
过长的注塑时间会导致产品的热变形,而过短的注塑时间则会使产品缺乏韧性。
我们通过实验发现,适当的注塑时间能够保证产品的良好性能。
四、存在的问题与改进在本次实验中,我们发现了一些问题,需要进行改进。
首先,需要加强对注塑机操作方法的学习,以提高操作的熟练度。
其次,对于工艺参数的调整还需要进一步的研究和实践,以获得更好的产品质量。
注塑产品实验报告
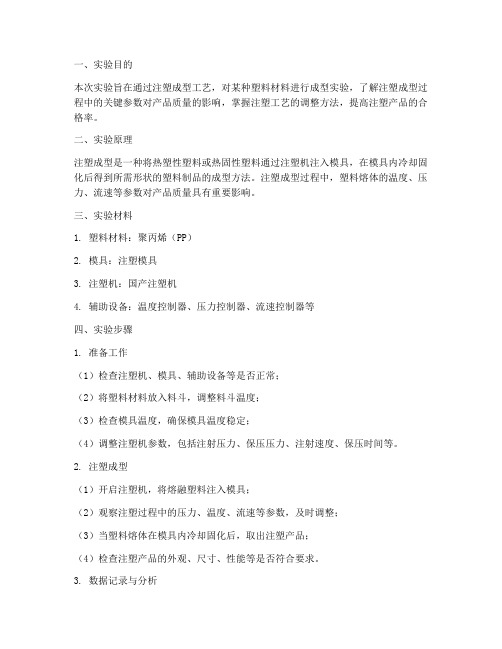
一、实验目的本次实验旨在通过注塑成型工艺,对某种塑料材料进行成型实验,了解注塑成型过程中的关键参数对产品质量的影响,掌握注塑工艺的调整方法,提高注塑产品的合格率。
二、实验原理注塑成型是一种将热塑性塑料或热固性塑料通过注塑机注入模具,在模具内冷却固化后得到所需形状的塑料制品的成型方法。
注塑成型过程中,塑料熔体的温度、压力、流速等参数对产品质量具有重要影响。
三、实验材料1. 塑料材料:聚丙烯(PP)2. 模具:注塑模具3. 注塑机:国产注塑机4. 辅助设备:温度控制器、压力控制器、流速控制器等四、实验步骤1. 准备工作(1)检查注塑机、模具、辅助设备等是否正常;(2)将塑料材料放入料斗,调整料斗温度;(3)检查模具温度,确保模具温度稳定;(4)调整注塑机参数,包括注射压力、保压压力、注射速度、保压时间等。
2. 注塑成型(1)开启注塑机,将熔融塑料注入模具;(2)观察注塑过程中的压力、温度、流速等参数,及时调整;(3)当塑料熔体在模具内冷却固化后,取出注塑产品;(4)检查注塑产品的外观、尺寸、性能等是否符合要求。
3. 数据记录与分析(1)记录实验过程中各参数的设置值;(2)对注塑产品进行外观、尺寸、性能等方面的检测;(3)分析实验数据,找出影响产品质量的关键因素。
五、实验结果与分析1. 外观检测注塑产品的外观应光滑、无气泡、无变形、无粘模等缺陷。
通过观察实验结果,发现注塑产品的外观质量良好,符合要求。
2. 尺寸检测注塑产品的尺寸应符合模具设计要求。
通过测量实验结果,发现注塑产品的尺寸误差在允许范围内,符合要求。
3. 性能检测注塑产品的性能应符合设计要求。
通过实验,发现注塑产品的性能指标如下:(1)拉伸强度:≥30MPa;(2)弯曲强度:≥50MPa;(3)冲击强度:≥5kJ/m2;(4)热变形温度:≥100℃。
分析实验数据,得出以下结论:(1)注射压力、保压压力、注射速度等参数对注塑产品质量有显著影响;(2)调整模具温度、料斗温度等参数对注塑产品质量有重要影响;(3)注塑成型过程中,应严格控制各参数,以确保产品质量。
聚丙烯PP的注塑成型工艺
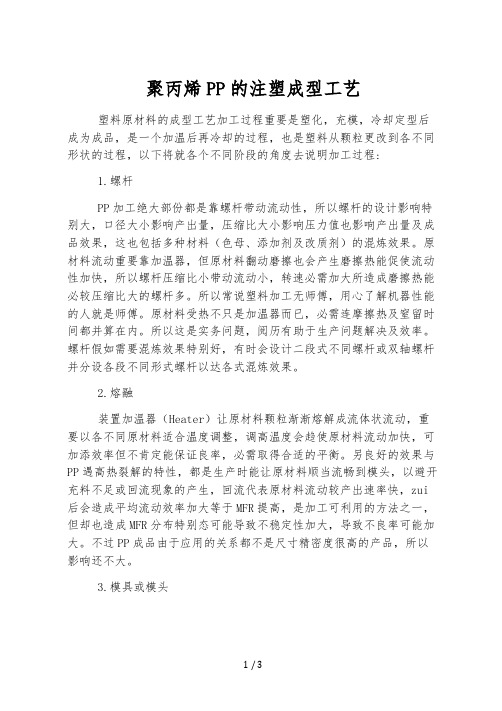
聚丙烯PP的注塑成型工艺塑料原材料的成型工艺加工过程重要是塑化,充模,冷却定型后成为成品,是一个加温后再冷却的过程,也是塑料从颗粒更改到各不同形状的过程,以下将就各个不同阶段的角度去说明加工过程:1.螺杆PP加工绝大部份都是靠螺杆带动流动性,所以螺杆的设计影响特别大,口径大小影响产出量,压缩比大小影响压力值也影响产出量及成品效果,这也包括多种材料(色母、添加剂及改质剂)的混炼效果。
原材料流动重要靠加温器,但原材料翻动磨擦也会产生磨擦热能促使流动性加快,所以螺杆压缩比小带动流动小,转速必需加大所造成磨擦热能必较压缩比大的螺杆多。
所以常说塑料加工无师傅,用心了解机器性能的人就是师傅。
原材料受热不只是加温器而已,必需连摩擦热及窒留时间都并算在内。
所以这是实务问题,阅历有助于生产问题解决及效率。
螺杆假如需要混炼效果特别好,有时会设计二段式不同螺杆或双轴螺杆并分设各段不同形式螺杆以达各式混炼效果。
2.熔融装置加温器(Heater)让原材料颗粒渐渐熔解成流体状流动,重要以各不同原材料适合温度调整,调高温度会趋使原材料流动加快,可加添效率但不肯定能保证良率,必需取得合适的平衡。
另良好的效果与PP遇高热裂解的特性,都是生产时能让原材料顺当流畅到模头,以避开充料不足或回流现象的产生,回流代表原材料流动较产出速率快,zui 后会造成平均流动效率加大等于MFR提高,是加工可利用的方法之一,但却也造成MFR分布特别态可能导致不稳定性加大,导致不良率可能加大。
不过PP成品由于应用的关系都不是尺寸精密度很高的产品,所以影响还不大。
3.模具或模头塑料重新定型依靠的是模具或模头,射出成型成品是立体的,模具也比较多而杂更要考虑收缩率问题,其它皆为平面、条状、针状连续式产品模头,若为特别形状则归为异型,需要注意立刻冷却定型问题。
塑料机器的设计大部份皆像注射针筒,螺杆带动的挤压气力都会在小小出口造成巨大压力,提高生产效率。
当模头设计为平面时如何让原材料平均分布整个面上,衣架模头的设计就非常紧要,讲究的压出机会加添鱼鳃式帮浦稳定原材料供应量。
聚丙烯如何成型

聚丙烯如何成型聚丙烯是一种常用的热塑性塑料,具有良好的可加工性和广泛的应用领域。
在工业生产中,聚丙烯的成型是一个关键的步骤,影响着制品的质量和形状。
本文将介绍聚丙烯的成型方法以及其中的一些关键技术。
注塑成型注塑成型是一种常见的聚丙烯成型方法。
该过程通常包括原料加热、溶融、注射、加压保压、冷却和脱模等步骤。
首先,将聚丙烯颗粒加入注塑机的料斗中,通过加热和旋转的螺杆使聚丙烯颗粒溶解成液态状。
然后,液态聚丙烯被注射到模具中,经过一定的加压保压时间确保塑件成型。
最后,待聚丙烯冷却凝固后,开模取出成品。
吹塑成型吹塑成型是另一种常见的聚丙烯成型方法,适用于制作中空或空心形状的制品,如瓶子、桶等。
该方法主要包括挤出、吹塑和冷却等步骤。
首先,通过挤出机将聚丙烯加热并压缩成管状物,然后将管状物移入吹塑模具中,通过气流吹气使管状物膨胀成模具形状。
最后,经过冷却使聚丙烯固化成型,脱模得到最终产品。
热压成型热压成型是一种将聚丙烯加热至一定温度后,通过压力将其压制成所需形状的成型方法。
这种方法适用于制作薄壁结构、复杂形状的制品。
首先,将聚丙烯放置在热压机模具中,加热至聚丙烯的软化温度,然后施加一定的压力使其成型。
最后,待聚丙烯冷却后,即可取出成品。
拉伸成型拉伸成型是一种将预制的聚丙烯坯料在一定温度下通过拉伸的方式成型的方法。
该方法适用于制作薄膜、容器等制品。
在拉伸成型过程中,首先将聚丙烯坯料加热至一定温度,然后通过拉伸使其成型。
拉伸过程中要注意控制温度和速度,以保证成品的质量和形状。
聚丙烯的成型方法多种多样,每种方法都有其适用的场合和特点。
在实际生产中,根据制品的要求和生产规模选择合适的成型方法是至关重要的。
希望本文介绍的聚丙烯成型方法对您有所帮助。
聚丙烯成型工艺

聚丙烯成型工艺一、简介聚丙烯是一种常见的塑料材料,具有良好的韧性、耐热性和化学稳定性,因此在工业生产中得到广泛应用。
聚丙烯的成型工艺是将聚丙烯颗粒经过一系列加工步骤,加热、压力等处理后,制成所需的形状和结构的工艺过程。
本文将介绍聚丙烯成型工艺的原理、方法和应用。
二、成型原理聚丙烯成型的基本原理是先将聚丙烯颗粒或粉末通过加热熔融成液态状,然后将熔融的聚丙烯注入模具中,经过冷却后得到所需的成型制品。
在成型过程中,需要控制好加热温度、压力、冷却速度等参数,以确保成型制品的质量。
三、成型方法1. 注塑成型注塑成型是聚丙烯成型中常用的一种方法。
首先将聚丙烯颗粒加热熔融,然后通过注射机将熔化的聚丙烯注入模具中,在模具中冷却成型后,取出成品。
注塑成型适用于生产量大、成型精度要求高的制品。
2. 吹塑成型吹塑成型是将聚丙烯预制坯料放入吹塑机中,在加热的同时通过气压吹塑成型。
这种方法适用于生产中空制品,如瓶子、容器等。
3. 真空吸塑成型真空吸塑成型是将预热的聚丙烯薄膜放入模具中,在模具内部施加真空吸力,使薄膜贴合模具表面成型。
真空吸塑成型适用于生产薄壁制品,如包装盒、托盘等。
4. 挤出成型挤出成型是将聚丙烯颗粒通过挤出机加热熔融,然后在挤出口模具中冷却成型。
这种方法适用于生产管材、板材等形状简单的制品。
四、成型应用聚丙烯成型工艺广泛应用于日常生活和工业领域。
在日常生活中,聚丙烯制品包括塑料瓶、食品包装盒、家具等。
在工业领域,聚丙烯制品广泛应用于汽车零部件、电子产品外壳、建筑材料等领域。
总的来说,聚丙烯成型工艺是一种快速、高效的制造方法,能够满足各种形状和结构要求的制品生产,为现代工业生产提供了重要支持。
以上就是关于聚丙烯成型工艺的介绍,希望对您有所帮助。
聚丙烯(PP)的注塑工艺
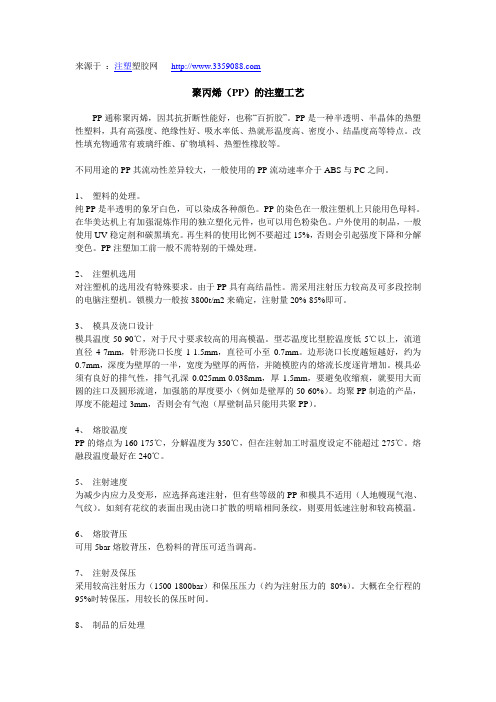
来源于:注塑塑胶网聚丙烯(PP)的注塑工艺PP通称聚丙烯,因其抗折断性能好,也称“百折胶”。
PP是一种半透明、半晶体的热塑性塑料,具有高强度、绝缘性好、吸水率低、热就形温度高、密度小、结晶度高等特点。
改性填充物通常有玻璃纤维、矿物填料、热塑性橡胶等。
不同用途的PP其流动性差异较大,一般使用的PP流动速率介于ABS与PC之间。
1、塑料的处理。
纯PP是半透明的象牙白色,可以染成各种颜色。
PP的染色在一般注塑机上只能用色母料。
在华美达机上有加强混炼作用的独立塑化元件,也可以用色粉染色。
户外使用的制品,一般使用UV稳定剂和碳黑填充。
再生料的使用比例不要超过15%,否则会引起强度下降和分解变色。
PP注塑加工前一般不需特别的干燥处理。
2、注塑机选用对注塑机的选用没有特殊要求。
由于PP具有高结晶性。
需采用注射压力较高及可多段控制的电脑注塑机。
锁模力一般按3800t/m2来确定,注射量20%-85%即可。
3、模具及浇口设计模具温度50-90℃,对于尺寸要求较高的用高模温。
型芯温度比型腔温度低5℃以上,流道直径4-7mm,针形浇口长度1-1.5mm,直径可小至0.7mm。
边形浇口长度越短越好,约为0.7mm,深度为壁厚的一半,宽度为壁厚的两倍,并随模腔内的熔流长度逐肯增加。
模具必须有良好的排气性,排气孔深0.025mm-0.038mm,厚1.5mm,要避免收缩痕,就要用大而圆的注口及圆形流道,加强筋的厚度要小(例如是壁厚的50-60%)。
均聚PP制造的产品,厚度不能超过3mm,否则会有气泡(厚壁制品只能用共聚PP)。
4、熔胶温度PP的熔点为160-175℃,分解温度为350℃,但在注射加工时温度设定不能超过275℃。
熔融段温度最好在240℃。
5、注射速度为减少内应力及变形,应选择高速注射,但有些等级的PP和模具不适用(人地幔现气泡、气纹)。
如刻有花纹的表面出现由浇口扩散的明暗相间条纹,则要用低速注射和较高模温。
6、熔胶背压可用5bar熔胶背压,色粉料的背压可适当调高。
注塑成型实验报告

注塑成型实验报告注塑成型实验报告一、实验目的本次实验旨在通过注塑成型技术,制作出具有特定形状和尺寸的塑料制品,并探究注塑成型的工艺流程、参数调节以及成品质量的影响因素。
二、实验原理注塑成型是一种常见的塑料加工方法,它通过将塑料颗粒加热熔融后注入模具中,经过冷却后得到所需的塑料制品。
该技术具有成型周期短、生产效率高、制品精度高等优点,广泛应用于工业生产中。
三、实验装置和材料1. 注塑机:用于塑料颗粒的加热和熔融,以及注入模具中。
2. 模具:用于塑料成型,包括模具芯和模具腔。
3. 塑料颗粒:本次实验采用聚丙烯颗粒作为原料。
四、实验步骤1. 准备工作:清洁注塑机和模具,将聚丙烯颗粒装入注塑机的料斗中。
2. 设定注塑机参数:根据实验要求,调节注塑机的温度、压力和注射速度等参数。
3. 开始注塑:启动注塑机,等待塑料颗粒熔化并达到所需温度后,开始注入模具中。
4. 冷却和固化:注塑后,等待塑料在模具中冷却并固化,时间根据塑料种类和厚度而定。
5. 取出成品:打开模具,取出成品,检查其质量和尺寸是否符合要求。
6. 清理工作:清理注塑机和模具,准备下一次实验。
五、实验结果与分析通过多次实验,我们得到了一系列不同形状和尺寸的注塑成品。
在实验中,我们发现注塑机参数的调节对成品质量有重要影响。
温度过高或过低都会导致塑料熔化不均匀或无法熔化,从而影响成品的外观和性能。
压力和注射速度的调节也会影响成品的密度和表面质量。
因此,在实际生产中,需要根据不同的塑料种类和成品要求,合理调节注塑机参数,以获得满足要求的成品。
此外,我们还发现模具的设计和制造对成品的质量和形状有重要影响。
模具的结构和尺寸需要与成品设计相匹配,以确保成品的精度和一致性。
同时,模具的材料选择也需要考虑到塑料的熔点和流动性,以避免模具损坏或成品缺陷。
六、实验总结通过本次实验,我们深入了解了注塑成型技术的工艺流程和参数调节。
注塑成型作为一种常用的塑料加工方法,在工业生产中具有广泛应用。
实验3 聚丙烯塑料注射成型 (2)

实验三聚丙烯塑料注射成型一、目的要求1.了解移动螺杆式注射机的结构特点及操作程序;掌握热塑性塑料注射成型的实验技能。
2.了解注射成型工艺条件与注射制品质量的关系。
二、原理注射成型适用于热塑性和热固性塑料,是高聚物的一种重要的成型工艺。
注射成型的设备是注射机和注塑模具。
它是使固体塑料在注射机的料筒内通过外部加热、机械剪切力和摩擦热等作用,熔化成流动状态,后经柱塞或移动螺杆以很高的压力和较快的速度,通过喷嘴注入到闭合的模具中,经过一定的时间保压固化后,脱模取出制品。
注射成型机主要的有柱塞式和螺杆式两种,以后者为常用。
不同类型的注射机的动作程序不完全相同,但塑料的注射成型原理及过程是相同的。
热塑性塑料注射时,模具温度比注射料低,制品是通过冷却而定型的;热固性塑料注射时,其模具温度要比注射料温度高,制品是要在一定的温度下发生交联固化而定型的。
本实验是以聚丙烯为例,采用移动螺杆式注射机的注射成型。
下面是热塑性塑料的注射成型工艺原理。
(一)模具的闭合动模前移,快速闭合。
在与定模将要接触时,依靠和模系统的自动切换成低压,提供适合模压力、低速;最后切换成高压将模具合紧。
(二)充模模具闭合后,注射机机身前移使喷嘴与模具贴合。
油压推动与油缸活塞杆相连接的螺杆前进,将螺杆头部前面已均匀塑化的物料以规定的压力和速度注射入模腔,直到熔体充满模腔为止。
螺杆作用于熔体的压力为注射压力,螺杆移动的速度为注射速度。
熔体充模顺利与否,取决于注射压力和速度,熔体的温度和模具的温度等。
这些参数决定了熔体的粘度和流动特性。
注射压力是为了使熔体克服料筒、喷嘴、浇铸系统和模腔等处的阻力,以一定的速度注射入模了;一旦充满,模腔内压迅速到达最大值,充模速度则迅速下降。
模腔内物料受压紧,密实,符合成型制品的要求。
注射压力的过高或过低,造成充模的过量或不足,将影响制品的外观质量和材料的大分子取向速度。
注射速度影响熔体填充模腔时的流动状态。
速度快,充模时间短,熔体温差小,制品密度均匀,熔接强度高,尺寸稳定性好,外观质量好;反之,若速度慢,充模时间长,由于熔体流动过程的剪切作用使大分子取向过程大,制品各向异性。
气相法聚丙烯注射成型工艺的研究

文章编号:1001-4934(2004)03-0034-05气相法聚丙烯注射成型工艺的研究李德军,古连宝,刘志芳(北京燕山石化树脂研究所,北京 102500)摘 要:该试验对气相法聚丙烯的注射成型工艺进行了研究,阐述了注射成型工艺对样品微观结构与力学性能的影响。
关键词:聚丙烯;注射工艺;形态结构中图分类号:TG241 文献标识码:B Abstract :Injection process of gas -phase polypropylene is studied.The influence of injection mold parameters on microstructure and mechanical properties of parts are discussed in detail.K ey w ords :gse polypropylene ;injection process ;morphology structure0 引言注射成型因其具有许多优点,现已成为塑料加工中重要的成型方法之一。
目前,注塑制品量已占塑料制品生产的20%~30%。
2001年世界注塑成型树脂的消费量在2496.2~3744.3万吨之间。
注射成型是一个复杂的工艺过程,整个工艺周期往往是一到几分钟,其中最关键的充模过程一般只有几十秒。
然而就是在这非常短促的工艺周期中,塑料却经历了非常复杂的热史和流变史。
注塑件的好坏既与被加工塑料本身的性能(如材料的流动性、分子量及其分布、分子链的柔顺性、结晶性等)有关,也与工艺条件(如熔体温度、注射压力、注射时间、模具温度、注射速度等)有关。
因此,在注射过程中,严格控制各工艺参数是获得优质塑件的重要手段[1]。
1 实验部分样品及来源PP K7726 燕化公司气相法生产PP K7708 燕化公司气相法生产2 结果与讨论2.1 成型工艺条件是对样品形态结构的影响在注射过程中,高聚物熔体在模腔内的流动速度是中央最大,越靠近模壁越小,而剪切速率则相反。
- 1、下载文档前请自行甄别文档内容的完整性,平台不提供额外的编辑、内容补充、找答案等附加服务。
- 2、"仅部分预览"的文档,不可在线预览部分如存在完整性等问题,可反馈申请退款(可完整预览的文档不适用该条件!)。
- 3、如文档侵犯您的权益,请联系客服反馈,我们会尽快为您处理(人工客服工作时间:9:00-18:30)。
实验三聚丙烯塑料注射成型一、目的要求1.了解移动螺杆式注射机的结构特点及操作程序;掌握热塑性塑料注射成型的实验技能。
2.了解注射成型工艺条件与注射制品质量的关系。
二、原理注射成型适用于热塑性和热固性塑料,是高聚物的一种重要的成型工艺。
注射成型的设备是注射机和注塑模具。
它是使固体塑料在注射机的料筒内通过外部加热、机械剪切力和摩擦热等作用,熔化成流动状态,后经柱塞或移动螺杆以很高的压力和较快的速度,通过喷嘴注入到闭合的模具中,经过一定的时间保压固化后,脱模取出制品。
注射成型机主要的有柱塞式和螺杆式两种,以后者为常用。
不同类型的注射机的动作程序不完全相同,但塑料的注射成型原理及过程是相同的。
热塑性塑料注射时,模具温度比注射料低,制品是通过冷却而定型的;热固性塑料注射时,其模具温度要比注射料温度高,制品是要在一定的温度下发生交联固化而定型的。
本实验是以聚丙烯为例,采用移动螺杆式注射机的注射成型。
下面是热塑性塑料的注射成型工艺原理。
(一)模具的闭合动模前移,快速闭合。
在与定模将要接触时,依靠和模系统的自动切换成低压,提供适合模压力、低速;最后切换成高压将模具合紧。
(二)充模模具闭合后,注射机机身前移使喷嘴与模具贴合。
油压推动与油缸活塞杆相连接的螺杆前进,将螺杆头部前面已均匀塑化的物料以规定的压力和速度注射入模腔,直到熔体充满模腔为止。
螺杆作用于熔体的压力为注射压力,螺杆移动的速度为注射速度。
熔体充模顺利与否,取决于注射压力和速度,熔体的温度和模具的温度等。
这些参数决定了熔体的粘度和流动特性。
注射压力是为了使熔体克服料筒、喷嘴、浇铸系统和模腔等处的阻力,以一定的速度注射入模了;一旦充满,模腔内压迅速到达最大值,充模速度则迅速下降。
模腔内物料受压紧,密实,符合成型制品的要求。
注射压力的过高或过低,造成充模的过量或不足,将影响制品的外观质量和材料的大分子取向速度。
注射速度影响熔体填充模腔时的流动状态。
速度快,充模时间短,熔体温差小,制品密度均匀,熔接强度高,尺寸稳定性好,外观质量好;反之,若速度慢,充模时间长,由于熔体流动过程的剪切作用使大分子取向过程大,制品各向异性。
熔体充模的压力和速度的确定比较麻烦,要考虑原料、设备和模具等因素,要结合其他工艺条件通过分析制品外观,实践相结合而决定的。
(三)保压熔体充模完全后,螺杆施加一定的压力,保持一定的时间,是为了模腔内熔体因冷却收缩而进行补塑,使制品脱模时不致于缺料。
保压时螺杆将向前稍作移动。
保压过程包括控制保压压力和保压时间的过程,它们均影响制品的质量。
保压压力可以等于或低于充模压力,其大小以达到补塑增密为宜。
保压时间以压力保持到浇口凝封时为好。
若保压时间不足,模腔内的物料会倒流,制品缺料;若时间过长或压力过大,充模量过大,将使制品的浇口附近的内压力增大,制品易开裂。
(四)冷却保压时间到达后,模腔内熔体自由冷却到固化的过程,其间需要控制冷却的温度和时间。
模具冷却温度的高低和塑料的结晶性、热性能、玻璃化温度、制品形状复杂与否及制品的使用要求等有关;此外,与其他的工艺条件也有关。
模具的冷却温度不能高于高聚物的玻璃化温度或热变形温度。
模温高,有利于熔体在模腔内流动,于充模有利,而且能使塑料冷却速度均匀。
模温高,利于大分子热运动,利于大分子的松弛,可以减少厚壁和形状复杂制品可能因为补塑不足、收缩不均和内应力大的缺陷。
但模温高,生产周期长,脱模困难,是不适宜的。
对于聚丙稀等结晶型塑料,模温直接影响结晶度和晶体的构型。
采用适宜的模温,晶体生长良好,结晶速率也较大,可以减少制品成型后的结晶现象,也能改善收缩不均、结晶不良的现象。
冷却时间的长短与塑料的结晶性、玻璃化温度、比容、导热率和模具温度等有关,应以制品在开模顶出时既有足够的刚度而又不致于变形为宜。
时间太长,生产率下降。
(五)塑料预塑化制品冷却时,螺杆转动并后退,塑料则进入料筒进行塑化并计量,为下一次注射作准备,此为塑料的预塑化。
预塑化时,螺杆的后移速度决定于后移的各种阻力,如机械摩擦阻力及注射油缸内液压油的回泄阻力。
塑料随螺杆旋转,塑化后向前堆积在料筒的前部,此时塑料熔体的压力称之为塑化压力。
注射油缸内液压油回泄阻力称为螺杆的背压。
这两种压力的增大,塑料的塑化量都降低。
预塑化是要求得到定量的、均匀塑化的塑料熔体。
塑化是靠料筒的外加热、摩擦热和剪切力等而实现的,剪切作用与螺杆的背压和转速有关。
料筒温度高低与树脂的种类、配合剂、注射量与制品大小比值、注射机类型、模具结构、喷嘴及模具的温度、注射压力和速度、螺杆的背压和转速,以及成型周期等很多因素都有关。
料筒温度总是定在材料的熔点(软化点)与分解温度之间,而且通常是分段控制,各段之间的温差约为30~50℃。
喷嘴加热在于维持充模的料流有良好的流动性,喷嘴温度等于或略低于料筒的温度。
过高的喷嘴温度,会出现流涎现象;过低也不适宜,会造成喷嘴的堵塞。
螺杆的背压影响预塑化效果。
提高背压,物料受到剪切作用增加,熔体温度升高,塑化均匀性好,但塑化量降低。
螺杆转速低则延长预塑化时间。
螺杆在较低背压和转速下塑化时,螺杆输送计量的精确度提高。
对于热稳定性差和熔融粘度高的塑料应选择转速低些;对于热稳定性差或熔体粘度低的则选择较低的背压。
螺杆的背压一般为注射压力的5%~20%。
塑料的预塑化与模具内制品的冷却定型是同时进行的,但预塑时间必定小于制品的冷却时间。
热塑性塑料的注射成型,主要是一个物理过程,但高聚物在热和力的作用下难免发生某些化学变化。
注射成型应选择合理的设备和模具设计,制订合理的工艺条件,以使化学变化减少到最小的程度。
三、机器设备和原料1.主要设备(1)SZA-YY-60塑料预塑注射成型机。
(2)注射模具(力学性能试样模具)。
(3)温度计、秒表等。
SZA-YY-60螺杆式塑料预塑注射成型机是通用型、全液压的,适用于热塑性塑料,是一台较小型的设备。
其结构特点是卧式直列式,包括注射装置、锁模装置、液压传动系统和电路控制系统。
注射装置是使塑料均匀化并以足够的压力和速度将一定量的塑料注射到模腔中。
注射装置位于机器的右上部,由料筒、螺杆和喷嘴、加料斗、计量装置、驱动螺杆的液压马达、螺杆和注座的移动油缸及电热线圈等组件构成。
锁模装置是实现模具的开启与闭合以及脱出制品的装置。
它位于机器的左上部,是全液压式、充液直压锁模机构。
它由前模板、移动模板、后模板连接锁模油缸、大活塞、拉杆和机械顶出杆等部件组成。
液压和电器控制系统能保证注射机按照工艺过程设定的要求和动作程序准确而有效地工作。
液压系统由各种液压元件和回路及其附属设备组成。
电器控制系统由各种电器仪表组成。
SZA-YY-60塑料预塑注射成型机的技术特征:螺杆直径35mm螺杆行程80mm螺杆转速25~160r/min 无级变速注射压力133.5Mpa最大注射量62cm3/次液压马达扭矩40kg·m注射率69 cm3/s塑化容量30kg/h注射机座推力22kN锁模力440kN动模板行程270mm模板开距420mm允许模具厚度150~250mm成型制品面积160 cm2拉杆间距330*300mm电动机功率 15kW油泵压力 14Mpa油泵流量 48L/min(1000r/min)2.原料聚丙烯(MFR2-10)四、实验程序1.准备工作:(1)详细观察、了解注射机的结构,工作原理,安全操作等。
(2)了解聚丙烯的规格及成型工艺特点,拟定各项成型工艺条件,并对原料进行预热干燥备用。
(3)安装模具并进行试模。
2.闭模及低压闭模。
由行程开关切换实现慢速-快速-低压慢速-充压的闭模过程。
3.注射机机座前进后退及高压闭紧。
4.注射。
5.保压。
6.加料预塑。
可选择固定加料或前加料或后加料等不同方式。
7.开模。
由行程开关实现慢速-快速-慢速-停止的启模过程。
8.螺杆退回。
上述操作程序重复几次,观察注射取得样品的情况,调整工作正常。
五、注意事项:根据实验的要求可选用点动、手动、半自动、全自动和光电启动等五种操作方式,进行实验演示。
选择开关设在操作箱内。
(1)点动:调整模具适宜选用慢速点动操作,以保证校模操作的安全性(料筒必须没有塑化的冷料存在)。
(2)手动:选择开关在“手动”位置,调整注射和保压时间继电器,关上安全门。
每揿一个钮,就相当完成一个动作,必须顺序一个动作做完才按另一个动作按钮。
一般是在试车、试制、校模时选用手动操作。
(3)半自动:将选择开关转至“半自动”位置,关好安全门,则各种动作会按工艺程序自动进行。
即依次完成闭模、稳压、注座前进、注射、保压、预塑(螺杆转动并后退)、注座后退、冷却、启模和顶出。
开安全门,取出制品。
(4)全自动:将选择开关至“全自动”位置,关上安全门,则机器会自行按照工艺程序工作,最后由顶出杆顶出制品。
由于光电管的作用,各个动作周而复始,无须打开安全门,要求模具由完全可靠的自动脱模装置。
(5)不论采用哪一种操作方式,主电动机的启动、停止及电子温度控制通电的按钮主令开关均须手动操作才能进行。
(6)除点动操作外,不论何种操作方式,均设有冷螺杆保护作用。
在加热温度没有达到工艺要求的温度之前,即电子温度控制仪所调正的温度,螺杆不能转动,防止机筒内冷料起动,造成机筒或螺杆的损坏。
但为了空车运行,自动循环时,可将温控仪的温度指示调到零位。
(7)在行驶操作时,须把限位开关及时间继电器调整到相应的位置上。
六、实验结果分析实验过程的操作为注射得到国家标准的“工”字形样条、长方体样条,中间带有一定深度的凹槽(缺口)的长方形样条,他们大多数样条没有出现气泡,裂痕等影响性能的缺陷。
但少部分出现下列现象:A、现象:部分产品出现飞边现象;解释:充摸压力加大,使得模腔内的压力较大,物料可以从边沿缝隙流出,出现飞边现象;熔体温度较高,黏度较小,是的物料的流动容易,同样使得物料更容易沿缝隙流出,出现飞边现象;冲模速度较大,模具温度较高等这些都可能带来飞边现象。
模具温度的高低对取向内应力和冷却内应力的影响都很大。
一方面,模具温度过低,会造成冷却加快,易使冷却不均匀而引起收缩上的较大差异,从而增大冷却内应力;另一方面,模具温度过低,熔体进入模其后,温度下降加快,熔体粘度增加迅速,造成在高粘度下充模,形成取向应力的程度明显加大。
模温对塑料结晶影响很大,模温越高,越有利于晶粒堆砌紧密,晶体内部的缺陷减小或消除,从而减少内应力。
另外,对于不同厚度塑料制品,其模温要求不同。
对于厚壁制品其模温要适当高一些。
B、现象:产品出现结合线;甚至是断的,没有连接;分析:由于模具没有加热系统,温度较低;当物料的温度不是很高,充到模具中的物料会迅速冷却,从不同的进料口充进的物料还没有交汇连接,就被冷却下来。
同时冲模的压力不大时,冲模速度较慢,物料也会在连接交汇前冷却,而不能熔融连接。