Pcb规模设计技术规范
PCB设计规范参考

PCB设计规范参考PCB(Printed Circuit Board)设计规范是为了确保PCB设计符合电气工程的要求,并且在制造和组装过程中能够得到良好的性能和可靠性。
以下是一些常见的PCB设计规范参考。
1.尺寸和形状:PCB的尺寸和形状应根据所使用的设备和封装来确定。
必须确保PCB能够适配于所需要的外壳和连接器,并且不会与其他组件发生干涉。
2.连接器布局:各个连接器应根据其功能和信号类型来布局。
必须确保连接器之间有足够的间距,以便于正确连接和散热。
3.元件布局:元件应根据电路设计的要求进行布局。
需要尽量减少导线的长度,并且避免交叉线路和环路。
4.导线布局:导线应尽量维持直线和平行布局,以减少信号的串扰和延迟。
必须确保导线宽度足够以承载所需的电流,并减少电阻。
5.路径规划:路径规划通常可分为两类:模拟信号和数字信号。
对于模拟信号,需要避免信号之间的干涉和串扰。
对于数字信号,需要确保信号的传输速度和正确性。
6.管脚布局:元件的管脚布局应符合相关的标准和规范。
需要确保每个管脚能够正确连接到相应的焊盘。
7.PCB层数:PCB的层数取决于所需的信号和功率平面。
通常,多层PCB具有更好的电磁兼容性和抗干扰性能。
8.焊盘和焊接规范:焊盘应根据元件的封装和引脚布局进行设计。
必须符合焊接标准,并确保焊接质量和可靠性。
9.接地和电源规范:必须确保正确的接地和电源布局。
需要提供足够的接地和电源引脚,并减少回流和过渡电流。
10.纹理和涂层规范:必须确保PCB的纹理和涂层符合相关的标准和规范。
需要考虑到制造和组装过程中的要求。
11.引脚和标记规范:必须对每个引脚进行正确的标记和编号。
需要在PCB上标明元件的名称和数值。
12.温度和湿度规范:PCB需要经受住各种温度和湿度条件的考验。
必须保证能够在设计规范范围内工作。
以上是一些常见的PCB设计规范参考。
根据具体的应用和需求,还可以有其他的规范和要求。
PCB设计者应根据实际情况,选择恰当的规范,并确保PCB设计能够满足相关的标准和要求。
PCB电路板PCB设计工艺规范
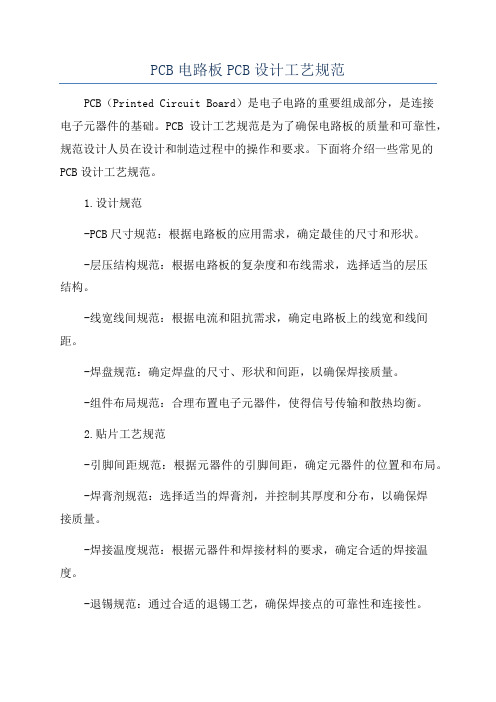
PCB电路板PCB设计工艺规范PCB(Printed Circuit Board)是电子电路的重要组成部分,是连接电子元器件的基础。
PCB设计工艺规范是为了确保电路板的质量和可靠性,规范设计人员在设计和制造过程中的操作和要求。
下面将介绍一些常见的PCB设计工艺规范。
1.设计规范-PCB尺寸规范:根据电路板的应用需求,确定最佳的尺寸和形状。
-层压结构规范:根据电路板的复杂度和布线需求,选择适当的层压结构。
-线宽线间规范:根据电流和阻抗需求,确定电路板上的线宽和线间距。
-焊盘规范:确定焊盘的尺寸、形状和间距,以确保焊接质量。
-组件布局规范:合理布置电子元器件,使得信号传输和散热均衡。
2.贴片工艺规范-引脚间距规范:根据元器件的引脚间距,确定元器件的位置和布局。
-焊膏剂规范:选择适当的焊膏剂,并控制其厚度和分布,以确保焊接质量。
-焊接温度规范:根据元器件和焊接材料的要求,确定合适的焊接温度。
-退锡规范:通过合适的退锡工艺,确保焊接点的可靠性和连接性。
3.线路布线规范-信号完整性规范:根据信号传输特性和电磁兼容性要求,确定合适的线路布线规范。
-电源和地线规范:保持电源和地线的稳定性和布线规范,以提供可靠的电源和接地。
-信号层划分规范:根据布线需求和层压结构,确定信号层的划分和连接方式。
4.工艺控制规范-正确的板材选择:根据电路板的应用和环境要求,选择合适的板材。
-禁忌设计规范:避免设计不合理的布线,如绕线锯齿状、封装阻挡焊盘等。
-高速信号特殊处理规范:对于高速信号,需要特殊处理,如规范的阻抗匹配、信号层堆叠等。
-容错性设计规范:在设计过程中考虑到制造过程中的不确定因素,增强电路板的容错性。
5.丝印和标识规范-丝印的位置和内容规范:确定电路板上的标识位置和内容,包括元器件的位置和器件类型。
-标示符规范:标示电路板的版本号、日期、厂家等信息,以便追踪和维护。
PCB设计工艺规范的目的是确保电路板的质量和可靠性,避免在制造和使用过程中的潜在问题。
PCB设计规范
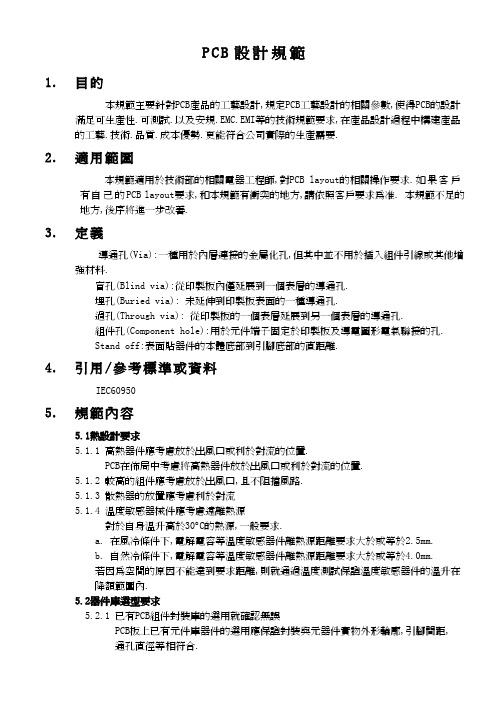
P C B設計規範1.目的本規範主要針對PCB產品的工藝設計,規定PCB工藝設計的相關參數,使得PCB的設計滿足可生產性.可測試.以及安規.EMC.EMI等的技術規範要求,在產品設計過程中構建產品的工藝.技術.品質.成本優勢.更能符合公司實際的生產需要.2.適用範圍本規範適用於技術部的相關電器工程師,對PCB layout的相關操作要求.如果客戶有自己的PCB layout要求,和本規範有衝突的地方,請依照客戶要求為准. 本規範不足的地方,後序將進一步改善.3.定義導通孔(Via):一種用於內層連接的金屬化孔,但其中並不用於插入組件引線或其他增強材料.盲孔(Blind via):從印製板內僅延展到一個表層的導通孔.埋孔(Buried via): 未延伸到印製板表面的一種導通孔.過孔(Through via): 從印製板的一個表層延展到另一個表層的導通孔.組件孔(Component hole):用於元件端子固定於印製板及導電圖形電氣聯接的孔.Stand off:表面貼器件的本體底部到引腳底部的直距離.4.引用/參考標準或資料IEC609505.規範內容5.1熱設計要求5.1.1 高熱器件應考慮放於出風口或利於對流的位置.PCB在佈局中考慮將高熱器件放於出風口或利於對流的位置.5.1.2 較高的組件應考慮放於出風口,且不阻擋風路.5.1.3 散熱器的放置應考慮利於對流5.1.4 溫度敏感器械件應考慮遠離熱源對於自身溫升高於30 C的熱源,一般要求.a.在風冷條件下,電解電容等溫度敏感器件離熱源距離要求大於或等於2.5mm.b.自然冷條件下,電解電容等溫度敏感器件離熱源距離要求大於或等於4.0mm.若因為空間的原因不能達到要求距離,則就通過溫度測試保證溫度敏感器件的溫升在降額範圍內.5.2器件庫選型要求5.2.1 已有PCB組件封裝庫的選用就確認無誤PCB板上已有元件庫器件的選用應保證封裝與元器件實物外形輪廓,引腳間距, 通孔直徑等相符合.插裝器件管腳應與通孔公差配合良好(通孔直徑大於管腳直徑80mil),考慮公差可適當增加,確保透錫良好.組件的孔徑形成序列化,40mil以上按5mil遞加,即40mil,45mil,50mil,55mil40mil以下按4mil遞減,即36mil,32mil,28mil,24mil, 20mil,16mil,12mil,8mil器件引腳直徑與PCB焊盤孔徑的對應關係,以及二次電源插針焊腳與通孔回流焊的焊盤孔徑對應關係如下表建立組件封裝庫存時應將孔徑的單位換算為英制(mil),並使孔徑滿足序列化要求.5.2.2 新器件的PCB元件封裝庫存應確定無誤.PCB上尚無件封裝庫的器件,應根據器件資料建立打撈的元件封裝庫,並保證絲印庫存與實物相符合,特別是新建立的電磁元件,自製結構件等的元件庫存是否與元件的資料(承認書,圖紙)相符合.新器件應建立能夠滿足不同工藝(回流焊,波峰焊,通孔回流焊)要求的元件庫.5.2.3 錳銅絲等作為測量用的跳線的焊盤要做成非金屬化,若是金屬化焊盤,那麼焊接後,焊盤內的那段電阻將被短路,電阻的有效長度將變小而且不一致,從而導致測試結果不準確.5.2.4 在對PCB設計時,對PCB元件封裝庫要符合公司的AI,SMT設備實際作業規格為准.如下表5.2.5 有些客戶對PCB元件封裝庫有客戶自己的要求,和本規範有衝突的地方,請依照客戶要求為准.5.3 基本佈局要求5.3.1 波峰焊加工的製成板進板方向要求有絲印標明.波峰焊加工的製成板進板方向應在PCB上標明,並使進板方向合理,若PCB可以從兩個方向進板,應採用雙箭頭的進板標識.(對於回流焊,可考慮採用工裝夾具來確定其過5.3.2 需波峰焊加工的單板背面器件不形成陰影效應的安全距離已考慮波峰焊工藝的SMT器件距離要求如下:1)相同類型器件距離相同類型器件的封裝尺寸與距離關係2)不同類型器件距離(如下圖)5.3.3 大於0805封裝的陶瓷電容,佈局時儘量靠近傳送邊或受應力較小區域,其軸向儘量與進板方向平行(如下圖),儘量不使用1825以上尺寸的陶瓷電容5.3.4 經常插拔器件或板邊連接器周圍3mm範圍內儘量不佈置SMD,以防止連接器插拔時產生的應力損壞器件.如下圖5.3.5 過波峰焊的外掛程式組件焊盤間距大於1.0mm.為保證過波峰焊時不連錫,過波峰焊的外掛程式組件焊盤邊緣間距應大於1.0mm.(包括組件本身引腳的焊盤邊緣間距).優選外掛程式組件引腳間距(pitch) 2.0mm,焊盤邊緣間距 1.0mm在器件本體不相互干涉的前提下,相鄰器件焊盤邊緣間距滿足下圖.外掛程式組件每排引腳為較多,以焊盤排列方向平行於進板方向佈置器件時,當相鄰焊盤邊緣間距為0.6mm-1.0mm時,推薦採用橢圓形焊盤或加偷錫焊盤如下圖5.3.6 貼片元件之間的最小間距離滿足要求機械貼片之間器件距離要求(如下圖)同種器件: 0.3mm異種器件: 0.13*+0.3mm(h為周圍近鄰組件最大高度差)只能手工貼片的元件之間距離要求: 1.5mm5.3.7 測試焊盤要求在PCB的每個網羅之間,均需要放置一個測試焊盤,以方便ICT設備作業.測試焊盤直徑: 1.0mm.兩個測試焊盤的中心間隔距離: 不小於2.0mm.5.4 走線要求5.4.1 印刷板距板邊距離:V-CUT邊大於0.75mm,銑槽邊大於0.3mm.為了保證PCB加工時不出現露銅的缺陷,要求所有的走線及銅箔距離板邊:V棧UT邊大於0.75mm, 銑槽邊大於0.3mm.(銅箔離板邊的距離還應滿足安裝要求)5.4.2 散熱器正面下方無走線(或已作絕緣處理)為了保證電氣絕緣性,散熱器下方周圍應無走線(考慮到散熱器安裝的偏位及安規距離),若需要在散熱器下佈線,則應採用絕緣措施使散熱器與走線絕緣,或確認走線與散熱器是同等電位.5.4.3 金屬拉手條底下無走線為了保證電氣絕緣性,金屬拉手條底下應無走線5.5 安規要求5.5.1 保險管的安規標識齊全保險絲附近是否有6項完整的標識,包括保險絲序號,熔斷特性,額定電流值,防爆特性,額定電壓值,英文警告標識.如F101 F3.15AH, 250Vac,揅AUTION: For Continued Protection Against Rist of Fire,Replace Only With Same Type and Rating of Fuse.若PCB上沒有空間排布英文警告標識,可將工,英文警告標識放到產品的使用說明書中說明.5.5.2 PCB板安規標識應明確PCB板五項安規標識(UL認證標識,生產廠家,廠家型號,UL認證檔號,阻燃等級)齊全.5.5.3 加強絕緣隔離帶電氣間隙和爬電距離滿足要求PCB上加強絕緣隔離帶電氣間隙和爬電距離滿足要求,具體參數要求參見相關的<資訊技術設備PCB安規設計規範>靠隔離帶的器件需要在10N推力情況下仍然滿足上述要求除安規電容的外殼到引腳可以認為是有效的基本絕緣處,其他器件的外殼均不認為是有效絕緣,有認證的絕緣套管,膠帶認為是有效絕緣.5.5.4 基本絕緣隔離帶電氣間隙和爬電距離滿足要求原邊器件外殼對接地外殼的安規距離滿足要求.原邊器件外殼對接地螺釘的安規距離滿足要求.原邊器件外殼接地散熱器的安規距離滿足要求.(具體距離尺寸通過查表確定)5.5.5 製成板上跨接危險和安全區域(原付邊)的電纜應滿足加強絕緣的安規要求5.5.6 裸露的不同電壓的焊接端子之間要保證最小2mm的安規距離,焊接端子在插入焊接後可能發生傾斜和翹起而導致距離變小下表列出的是缺省的對稱結構及層間厚度的設置5.5.7 PCB尺寸,板厚已在PCB檔中標明,確定,尺寸標注應考慮廠家的加工公差.板厚(±10%公差)規格:0.8mm;1.0mm;1.2mm;1.6mm;2.0mm;2.5mm;3.0mm;3.5mm.5.5.8 尺寸小於50mmx50mm的PCB應進行拼板 (鋁基板和陶瓷基板除外)一般原則:當PCB單元板的尺寸<50mmx50mm時,必須做拼板:當拼板需要做V-CUT時,拼板的PCB板厚應小於3.5mm.最佳:平行傳送邊方向的V-CUT線數量 3 (對於細長的單板可以例外)如下圖5.5.9 BOTTOM面表貼器件需過波峰時,應確定貼裝阻容件與SOP的佈局方向正確,SOP器件軸向需與波峰方向一致1).SOP器件在過波峰尾端需接增加一對偷錫盤,尺寸滿足下圖要求2)SOP器件過波峰儘量滿足最佳方向3).片式全端子器件(電阻,電容)對過波峰方向不作特別要求.4).片式非全端子器件(鉭電容,二極體)過波峰最佳時方向需滿足軸向與進板方向平行. 如下圖:6.附錄距離及其相關安全要求6.1 電氣間隙的決定:根據測量的工作電壓及絕緣等級,即可決定距離一次側線路之電氣間隙尺寸要求,見表二次側線路之電氣間隙尺寸要求,見表但通常:1).一次側交流部分:保險絲前L-N 3.0mm, L.N PE(大地) 3.0mm,保險絲裝置之後可不做要求,但盡可能保持一定距離以避免發生短路損壞電源.2).一次側交流對直流部分 2.0mm3).一次側直流地對大地 3.0mm (一次側浮接地對大地)4).一次側部分對二次側部分 4.0mm,跨接於一二次側之間之元器件5).二次側部分之電隙間隙 0.5mm即可6).二次側地對大地 1.0mm即可附注:決定是否符合要求前,內部零件應先施於10N力,外殼施以30N力,以減少其距離,使確認為最情況下,空間距離仍符合規定.6.2 爬電距離的決定:但通常:1).一次側交流部分:保險絲前L-N 3.0mm, L.N PE(大地) 3.0mm,保險絲裝置之後可不做要求,但盡可能保持一定距離以避免發生短路損壞電源.2).一次側交流對直流部分 2.0mm3).一次側直流地對大地 4.0mm (如一次側地對大地)4).一次側對二次側 6.4mm,如光耦,Y電容等元器件腳間距 6.4mm要開槽5).二次側部分之電隙間隙 0.5mm即可6).二次側地對大地 2.0mm以上7).變壓器兩級間 8.0mm以上6.3 放電針的要求:1).初次級間放電針要求原則上只用一個放電針其尖端角度為30 C.如圖所示30︒C 30︒ 20︒20︒2).兩個放電針間的距離為6.4mm.3).放電針距對邊的有組件的距離需保持8mm.6.4 有關於防燃材料要求:熱縮套管V-1或VT M-2以上;PVC套管V-1或VTM-2以上鐵氟龍套管V-1或VT M-2以上;塑膠材質如矽膠片,絕緣膠帶V-1或VTM-2以上PCB板94V-1以上6.5 有關於絕緣等級1).工作絕緣:設備正常工作所需的絕緣.2).基本絕緣:對防電擊提供基本保護的絕緣3).附加絕緣:除基本絕緣以外另施加的獨立絕緣,用以保護在基本絕緣一旦失效時仍能防止電擊.4).雙重絕緣:由基本絕緣加上附加絕緣構成的絕緣.5).加強絕緣:一種單一的絕緣結構,在本標準規定的條件下,其所提供的防電擊的保護等級相當於雙重絕緣.6.6 各種絕緣的適用情形如下:A.操作絕緣oprational insulationa.介於兩不同電壓之零件.b.介於ELV電路(或SELV電路)及接地的導電零件間.B.基本絕緣basic insulationa.介於具危險電壓零件及接地的導電零件之間.b.介於具危險電壓及依賴接地的SELV電路之間.c.介於一次側的電源導體及接地遮罩物或主電源變壓器的鐵心之間.d.做為雙重絕緣的一部分.C.補充絕緣supplementary insulationa.一般而言,介於可觸及的導體零件及在基本絕緣損壞後有要能帶有危險電壓的零件之間,如:1)介於把手,旋鈕,提柄或類似物的外表及其未接地的軸心之間.2)介於第二類設備的金屬處殼與穿過此外殼的電源線外皮之間.3)介於ELV電路及未接地的金屬外殼之間.b.做為雙重絕緣的一部分D.雙重絕緣Double insulation Reinforced insulation一般而言,介於一次側路及a.可觸及的未接地導電零件之間,或b.浮接(floating)的SELV的電路之間或c.TNV電路之間雙重絕緣 = 基本絕緣+補充絕緣注:ELV線路:特低電壓電路.在正常工作條件下,在導體之間或任一導體之間的交流峰值不超過42.4V或直流值不超過60V二次電路.SELV電路:安全特低電壓電路.作了適當的設計和保護的二次電路,使得在正常條件下或單一故障條件下,任意兩個可觸及的零部件之間,以及任意的可觸及零部件和設備的保護接地端子(僅I類設備)之間的電壓,均不會超過安全值.TNV:通訊網路電壓電路在正常工作條件下,攜帶通信信號的電路.。
PCB板设计规则
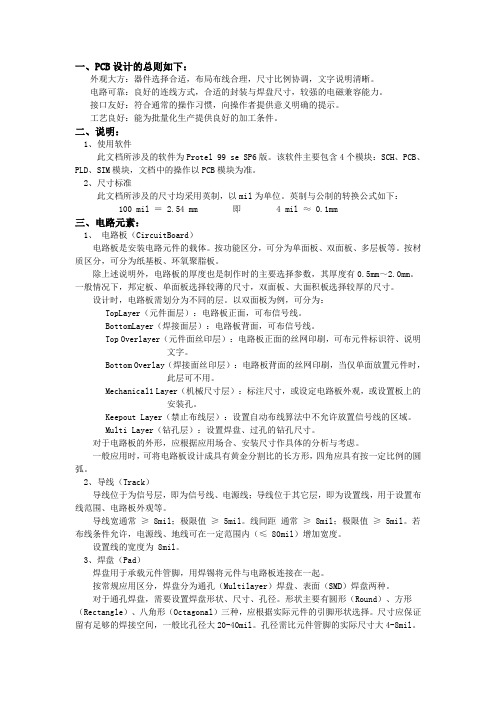
一、PCB设计的总则如下:外观大方:器件选择合适,布局布线合理,尺寸比例协调,文字说明清晰。
电路可靠:良好的连线方式,合适的封装与焊盘尺寸,较强的电磁兼容能力。
接口友好:符合通常的操作习惯,向操作者提供意义明确的提示。
工艺良好:能为批量化生产提供良好的加工条件。
二、说明:1、使用软件此文档所涉及的软件为Protel 99 se SP6版。
该软件主要包含4个模块:SCH、PCB、PLD、SIM模块,文档中的操作以PCB模块为准。
2、尺寸标准此文档所涉及的尺寸均采用英制,以mil为单位。
英制与公制的转换公式如下:100 mil = 2.54 mm 即 4 mil ≈ 0.1mm三、电路元素:1、电路板(CircuitBoard)电路板是安装电路元件的载体。
按功能区分,可分为单面板、双面板、多层板等。
按材质区分,可分为纸基板、环氧聚脂板。
除上述说明外,电路板的厚度也是制作时的主要选择参数,其厚度有0.5mm~2.0mm。
一般情况下,邦定板、单面板选择较薄的尺寸,双面板、大面积板选择较厚的尺寸。
设计时,电路板需划分为不同的层。
以双面板为例,可分为:TopLayer(元件面层):电路板正面,可布信号线。
BottomLayer(焊接面层):电路板背面,可布信号线。
Top Overlayer(元件面丝印层):电路板正面的丝网印刷,可布元件标识符、说明文字。
Bottom Overlay(焊接面丝印层):电路板背面的丝网印刷,当仅单面放置元件时,此层可不用。
Mechanical1 Layer(机械尺寸层):标注尺寸,或设定电路板外观,或设置板上的安装孔。
Keepout Layer(禁止布线层):设置自动布线算法中不允许放置信号线的区域。
Multi Layer(钻孔层):设置焊盘、过孔的钻孔尺寸。
对于电路板的外形,应根据应用场合、安装尺寸作具体的分析与考虑。
一般应用时,可将电路板设计成具有黄金分割比的长方形,四角应具有按一定比例的圆弧。
PCB设计规范范文

PCB设计规范范文PCB(Printed Circuit Board)是电子产品中不可或缺的关键组件之一、它承载着电子元件并提供电气连接,为电子设备的正常运行提供支持。
为了确保PCB的正常工作和受到适当的维护,有一套规范和指南来指导PCB的设计和生产。
以下是一些常见的PCB设计规范:1.尺寸规范:PCB的尺寸应根据实际应用需求进行设计,并应考虑到电子产品的外部尺寸要求。
尺寸的准确性对于PCB和组装工艺的成功都至关重要。
2.电气规格:PCB设计应符合应用需求的电气规范。
其中包括电压、电流、频率等参数的限制。
电气规格的合理设计可以确保电路的稳定性、可靠性和性能。
3.材料选用:PCB的材料选择应考虑到产品应用场景和要求,包括高温环境、潮湿环境、抗震性能等。
常见的PCB材料有FR-4、铝基板、陶瓷基板等。
4.敏感电路隔离:PCB设计中敏感电路应与其他电路隔离,以避免相互之间的干扰。
敏感电路包括模拟电路和高频电路。
5.地线规划:良好的地线规划可以降低电路中的噪声和干扰。
地线应尽可能宽,避免共线回流路径,减小回流电流的磁场。
6.线宽距规范:PCB中导线的线宽和间隔距离应根据电流和电压要求设计。
较大的电流需要较宽的线宽,较大的电压需要较大的间距。
7.最小孔径:PCB设计中应注意最小孔径的限制,以确保钻孔的准确性和稳定性。
通常情况下,最小孔径应大于钻头直径的两倍。
8.贴片元件安装规范:PCB设计中应合理安排贴片元件并留出足够的安装空间。
贴片元件的布置应符合组装工艺的要求,并确保元件之间的电气连接。
9.GPIO引脚排列:PCB设计中应按照IC的GPIO引脚功能进行排列。
相同功能的引脚应相邻,以方便信号的连接和布线。
10.PCB标记和标识:PCB设计中应包含元件的标记和标识。
标记包括元件的名称和编号,以方便组装和维护。
11.焊盘设计:PCB设计中应合理设计焊盘,确保良好的焊接质量。
焊盘的尺寸和形状应适应元件的尺寸和引脚间距。
PCB设计规范
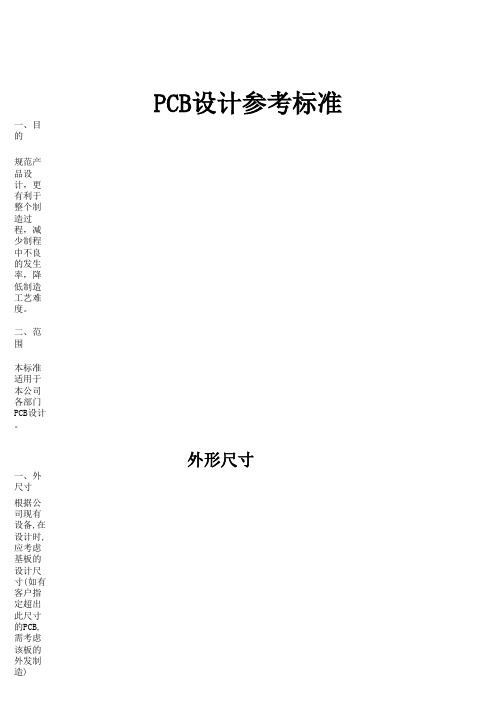
一、目的规范产品设计,更有利于整个制造过程,减少制程中不良的发生率,降低制造工艺难度。
二、范围本标准适用于本公司各部门PCB设计。
一、外尺寸根据公司现有设备,在设计时,应考虑基板的设计尺寸(如有客户指定超出此尺寸的PCB,需考虑该板的外发制造)根据公司设备情况.模板时应避免将PCB窄边作为制造用板边.或在窄边布置工艺板边.注:②.自动插件部品脚距离制造板边<5 mm(图中②)③.手动插件、自动插件部品表面任意部分距离制造板边尺寸<2.00mm;(图中③)⑤.<1.00mm空电路线距离制造板边尺寸<3.00mm(图中⑤)⑥.定位孔中心距离制造板边>7.00mm或定位孔边缘距离制造板边距离>8.50(图中⑥)④.手动插件的背面焊盘距离制造板边<1.00mm;(图中④)PCB设计参考标准1、公司当前设备可制造最大PCB外尺寸为330.00*250.00mm;但最小整板不得低于64.00mm.2、当有以下情况之一,需要增加工艺板边:①.SMD贴装部品焊盘距离制造板边尺寸<5.00mm;(图中①)外形尺寸无工艺板边布板时需要特别注意禁止布置SMD元件区域,不得安放任何SMD元件.释义:工艺板边——工艺边其实就是为了辅助生产插件走板、焊接过波峰在PCB板两边或者四边增加的部分,主要为了辅助生产,不属于PCB板的一部分,生产完成需去除。
制造板边——是指在完全没有工艺板边的情况下PCB四周的边缘部分,常常被视作板边在制造过程中使用。
二、定位标示释义:定位孔——用于制造过程中安装夹具或机械定位的通孔。
定位开孔与安装孔可通用.螺丝孔——产品组装时用于固定或安装产品的通孔。
因受力较大。
在设计时需要做加强其机械应力.1.定位孔的设计根据制造工艺来定,公司现行使用定位孔的工艺段分别为:自动插件印刷ICT FCT高压测试公司现行AI采用弹簧爪片对PCB进行定位作业,故对PCB定位孔有一定的技术要求.①.爪片的可定位尺寸在3.00-6.00mm.最佳生产状态为3.00mm(中心距离板边5.00mm)②.定位孔大小定∅4.00mm,允许误差为+0.05③.所有定位孔或螺丝孔周围5*5mm范围内,禁止布置SMD元件.以避免基板加工或螺丝紧定时产生外力导致部品损坏.(定位孔设计在工艺板边时,则无需考虑此问题)2、MARK点的设置.焊盘外径D一般不小于(d+1.5)mm,其中d为孔径,对于一些密度比较大的元件的焊盘最小直径可取(d+1.2)①MARK点为1*1mm露铜圆形,可以选用镀锡,在周围再围绕∮3.00mm圆环,以增强与隔绝外围线路。
某公司PCB设计规范样本

某公司PCB设计规范样本1. 引言PCB(Printed Circuit Board,印刷电路板)是现代电子设备中常见的一种重要组成部分,它承载着电子元器件,并提供了电子元器件之间的电气连接。
为了保证PCB的质量和可靠性,某公司制定了一套严格的PCB设计规范样本,本文将介绍该规范样本的具体内容和要求。
2. PCB设计规范2.1 PCB尺寸和层数根据不同的应用需求,PCB的尺寸和层数会有所不同。
在某公司的设计规范样本中,PCB的尺寸通常不超过20cm×20cm,并且层数不超过4层。
若需要超出这个范围,需要额外申请和审批。
2.2 PCB布局和布线2.2.1 元器件布局•元器件应按照电路图要求合理布局,尽量缩短信号传输路径,降低信号干扰。
•元器件之间应保留足够的间距,以便于安装和维修。
•高功率元器件和高频元器件应与敏感元器件保持一定的间距,防止互相干扰。
2.2.2 信号和电源平面•PCB上应划分信号和电源平面,以降低信号串扰和提供稳定的电源供应。
•信号和电源平面之间应保持一定的距离,以减少互相干扰。
2.2.3 信号走线•信号走线应尽量保持短、直、对称。
•临近平面的信号线应与平面保持一定距离,以减少互电容和互感。
•若有高速信号或高频信号,应采取差分走线或者层间引线走线方式,以减少信号衰减和串扰。
2.3 焊盘和焊接2.3.1 焊盘设计•焊盘的大小应根据元器件引脚的尺寸和数量合理确定,避免太小或太大。
•焊盘的形状应选择圆形或方形,避免使用带尖角的形状。
2.3.2 焊盘与元器件引脚的间距•焊盘与元器件引脚之间应保留一定的间距,避免短路或接触不良。
2.3.3 焊接工艺•焊接工艺应符合IPC标准,并采用无铅焊接方式。
•焊接时应遵循良好的工艺控制,如控制温度、焊接时间和焊接扩展量等。
2.4 丝印和字体2.4.1 PCB丝印•PCB上的丝印应清晰、易读,方便组装和维修。
•丝印的颜色应与PCB背景颜色形成明显对比,以提高可视性。
PCB设计工艺规范

PCB设计工艺规范一、概述二、布局规范1.PCB布局应符合电信号传输、电源分离和散热等特殊要求。
2.元器件应尽量按照功能分类,并根据其引脚数和电压等级进行合理排布。
3.PCBA板边缘应保留足够的空间用于安装和装配。
4.PCB上应有足够的装配间距,以便于元器件的安装和调试。
5.控制板的高频电路应尽量远离其他板块,减少相互干扰。
三、阻抗控制规范1.对于高频信号线路,应根据信号频率计算并控制阻抗。
2.对于差分信号线,应保持两个信号线的阻抗匹配。
3.PCB的阻状变化应符合信号传输的需求。
4.使用符合工艺要求且稳定的材料和工艺来控制阻抗。
四、封装规范1.元器件在PCB上的封装应符合国际标准,如IPC-7351等。
2.封装的引脚应正确标识,并与器件的引脚一一对应。
3.封装的安装方向应正确且一致。
五、布线规范1.信号线和地线应分开布线,以减少干扰。
2.信号线和电源线应相互垂直布线,以减少串扰。
3.控制板的重要信号线应尽量短且直接。
4.高速布线应使用差分布线技术,减少串扰和信号失真。
六、焊接规范1.针对手焊和自动焊两种焊接方式,设计合适的焊盘和焊垫。
2.焊盘和焊垫应具有合适的大小和间距,以方便焊接操作。
3.焊盘和焊垫的形状、位置和尺寸应符合焊接工艺要求。
七、质量控制规范1.PCB设计应符合ISO9001等国际质量管理体系认证要求。
2.在布局和布线过程中,应预留合适的测试点和测试接口,以便后续的功能测试和故障排除。
3.PCB设计应经过严格的验证和检验,确保电气性能满足要求。
4.PCB制造过程中应严格按照工艺规范进行生产操作,确保产品质量。
八、总结PCB设计工艺规范是保证设计质量和可靠性的重要依据。
遵循规范可以提高设计效率、减少错误和故障,确保PCB制造过程的顺利进行。
通过制定和实施一套完整的工艺规范,可以提高产品的品质水平和竞争力,满足客户的需求和要求。
PCB设计规范范文

PCB设计规范范文pcb设计规范PCB(Printed Circuit Board)设计规范是指在进行电路板设计时,应遵循的相关规范和要求。
遵循这些规范可以确保设计的精度和可靠性,并提高生产的效率和质量。
以下是一些常见的PCB设计规范。
1.尺寸和布局规范:2.电路分布规范:在布局电路时,需要将功能相似的电路元件归为一组,并保持它们之间的距离尽可能短,以便减少信号传输时的干扰。
同时,需要将高频电路和低频电路分开,以避免相互干扰。
3.电源规范:在PCB设计中,电源线路应注意保持稳定的供电。
此外,对于高频电路和模拟电路,需要提供相应的电源滤波器和去耦电容,以降低噪声和交叉干扰。
4.信号走线规范:为了保证信号传输的稳定性和可靠性,需要遵循一些信号走线的规范。
信号线应尽量避免走并行,并尽量保持直线走向。
对于高频信号,应采用差分走线方式,并与地线或屏蔽层相邻,以减少干扰。
5.地线规范:地线在PCB设计中起到连接、屏蔽和引流的作用。
因此,需要确保地线宽度足够,且与信号线保持相邻,并尽量缩短长度。
在布局时,需要将地线划分为数个区域,以避免大面积的地线循环引起的回流问题。
6.散热规范:对于功耗较大的电路或存在散热问题的电路元件,需要考虑散热的设计。
可以通过增加散热片、散热器或增大散热面积来提高散热效果。
7.符号和标注规范:8.禁忌规范:在PCB设计过程中,需要遵循一些禁忌规范,以避免常见的错误。
例如,避免信号线和电源线重叠,避免不必要的直角走线,避免不合理的走线方式等。
总结:。
原理图PCB板设计制作规范标准
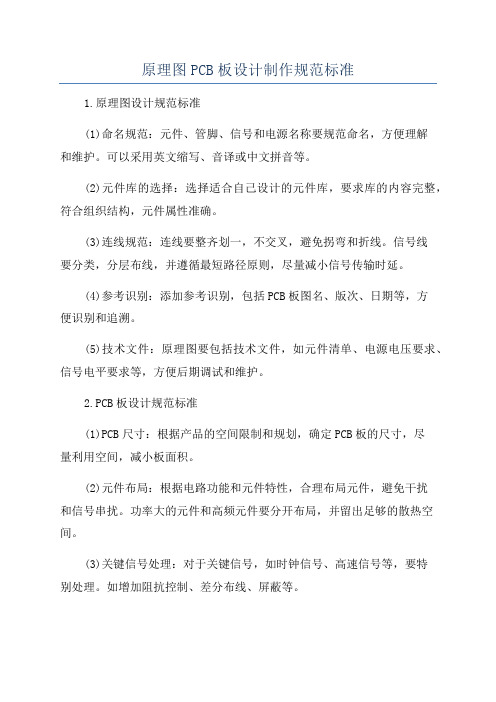
原理图PCB板设计制作规范标准1.原理图设计规范标准(1)命名规范:元件、管脚、信号和电源名称要规范命名,方便理解和维护。
可以采用英文缩写、音译或中文拼音等。
(2)元件库的选择:选择适合自己设计的元件库,要求库的内容完整,符合组织结构,元件属性准确。
(3)连线规范:连线要整齐划一,不交叉,避免拐弯和折线。
信号线要分类,分层布线,并遵循最短路径原则,尽量减小信号传输时延。
(4)参考识别:添加参考识别,包括PCB板图名、版次、日期等,方便识别和追溯。
(5)技术文件:原理图要包括技术文件,如元件清单、电源电压要求、信号电平要求等,方便后期调试和维护。
2.PCB板设计规范标准(1)PCB尺寸:根据产品的空间限制和规划,确定PCB板的尺寸,尽量利用空间,减小板面积。
(2)元件布局:根据电路功能和元件特性,合理布局元件,避免干扰和信号串扰。
功率大的元件和高频元件要分开布局,并留出足够的散热空间。
(3)关键信号处理:对于关键信号,如时钟信号、高速信号等,要特别处理。
如增加阻抗控制、差分布线、屏蔽等。
(4)电源和地线:电源和地线要分层布局,减小干扰。
同时要考虑电源电流的分布和供电稳定性,合理设计电源网络。
(5)线宽和间距:根据电流和信号传输要求,选择适当的线宽和间距。
高速信号要考虑传输线的阻抗匹配。
(6)引脚和焊盘:确定元件的引脚和焊盘布局,要考虑元件安装和焊接时的易用性和可靠性。
(1)层数和堆叠:根据电路复杂度和性能要求,确定PCB板的层数和堆叠方式。
(2)板材选择:根据电路功率、频率等要求,选择适合的板材,如FR4、高TG板等。
(3)焊接工艺:确定焊接工艺和焊接方式,如SMT、DIP等。
要考虑焊点的可靠性和焊接质量。
(4)表面处理:根据焊接方式和要求,选择适当的表面处理方式,如HASL、ENIG等,保证焊点的可靠性。
(5)丝印和标识:在PCB板上添加丝印和标识,包括元件位置、极性标识、工艺信息等,方便组装和维护。
(完整word版)PCB设计规范

先进制造技术研究所智能车辆技术研究中心嵌入式硬件PCB设计规范(初稿)整理编制:王少平1、目的1.1 本规范规定车辆中心PCB设计规范, PCB设计人员必须遵循本规范。
1。
2 提高PCB设计质量和设计效率,提高PCB的可生产性、可测试、可维护性.2、设计任务2。
1 PCB设计申请流程硬件设计工程师按照本设计规范要求完成PCB设计,提交给嵌入式硬件开发组组长进行审核,审核通过后递交硬件评审小组评审,评审通过后才能进行PCB制作,并将设计图纸归档。
2.2 设计过程注意事项2。
2.1 创建PCB板,根据单板结构图或对应的标准板框,创建PCB设计文件;注意正确选定单板坐标原点的位置,原点的设置原则:(1)单板左边和下边的延长线交汇点;(2)单板左下角的第一个焊盘。
2.2。
2 布局(1) 根据结构图设置板框尺寸,按结构要素布置安装孔、接插件等需要定位的器件,并给这些器件赋予不可移动属性. 按工艺设计规范的要求进行尺寸标注。
(2) 根据结构图和生产加工时所须的夹持边设置印制板的禁止布线区、禁止布局区域。
根据某些元件的特殊要求,设置禁止布线区,如下图所示。
(3)综合考虑PCB性能和加工的效率选择加工流程加工工艺的优选顺序为:元件面单面贴装—〉元件面贴、插混装(元件面插装焊接面贴装一次波峰成型)—>双面贴装—>元件面贴插混装、焊接面贴装。
(4)布局操作的基本原则a、遵照“先大后小,先难后易"的布置原则,即重要的单元电路、核心元器件应当优先布局;b、布局中应参考原理框图,根据单板的主信号流向规律安排主要元器件:c、连线尽可能短,关键信号线最短,高电压、大电流信号与小电流,低电压的弱信号完全分开,模数信号分开,高低频信号分开,高频元器件的间隔要足够;d、相同结构电路部分,尽可能采用“对称式”标准布局;e、按照均匀分布、重心平衡、版面美观的标准优化布局;f、器件布局栅格的设置,一般IC器件布局时,栅格应为50~100 mil,小型表面安装器件,如表面贴装元件布局时,栅格设置应不少于25mil;g、电路板推荐布局。
PCB板设计规范
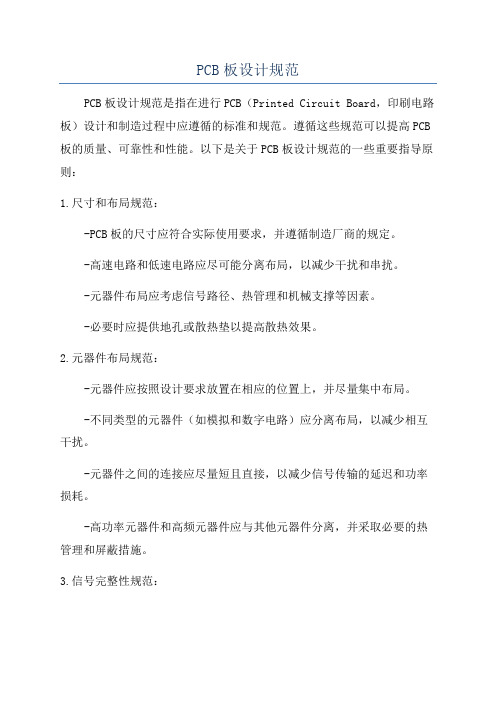
PCB板设计规范PCB板设计规范是指在进行PCB(Printed Circuit Board,印刷电路板)设计和制造过程中应遵循的标准和规范。
遵循这些规范可以提高PCB 板的质量、可靠性和性能。
以下是关于PCB板设计规范的一些重要指导原则:1.尺寸和布局规范:-PCB板的尺寸应符合实际使用要求,并遵循制造厂商的规定。
-高速电路和低速电路应尽可能分离布局,以减少干扰和串扰。
-元器件布局应考虑信号路径、热管理和机械支撑等因素。
-必要时应提供地孔或散热垫以提高散热效果。
2.元器件布局规范:-元器件应按照设计要求放置在相应的位置上,并尽量集中布局。
-不同类型的元器件(如模拟和数字电路)应分离布局,以减少相互干扰。
-元器件之间的连接应尽量短且直接,以减少信号传输的延迟和功率损耗。
-高功率元器件和高频元器件应与其他元器件分离,并采取必要的热管理和屏蔽措施。
3.信号完整性规范:-控制线、时钟线和高速信号线应尽可能短,且避免平行走线,以减少串扰和时钟抖动。
-高速信号线应采用阻抗匹配技术,以确保信号的正确传输和减少反射。
-高速差分信号线应保持恒定的差分阻抗,并采用差分匹配技术,以减少干扰和降低功耗。
4.电源和接地规范:-电源线和地线应尽可能粗,以降低电阻和电压降。
-电源和地线应尽量采用平面形式,以减少电磁干扰和提供良好的电源和接地路径。
-多层PCB板应设有专用层用于电源和接地,以提高板层的抗干扰能力和电源噪声的影响。
5.焊接规范:-设计带有相应的焊接垫和焊盘,以便于元器件的焊接和可靠连接。
-焊盘和焊接垫的尺寸应符合元器件和制造工艺的要求,并考虑到热膨胀和热应力等因素。
-导线和焊盘间的间距应符合焊接工艺的要求,以确保焊接质量和可靠性。
6.标记和文档规范:-PCB板应有清晰的标记,包括元器件名称、值和位置、网络名称等。
-为了提供必要的参考和维护,应有详细的PCB设计文档,包括原理图、布线图和尺寸图等。
总的来说,遵循PCB板设计规范可以提高PCB板的可靠性、性能和一致性,减少制造和调试过程中的问题和风险。
PCB线路板设计规范

PCB线路板设计规范1.尺寸和形状:2.层次结构和层数:根据电路的复杂程度和信号传输要求,选择适当的层数和层次结构设计。
多层线路板可以提高信号的传输速度和抗干扰能力。
3.布局和走线:合理的布局和走线是确保线路板性能稳定和可靠的重要因素。
布局应考虑到信号传输的路径和距离,避免信号串扰和电流回环。
同时,还要合理安排元件的位置,方便组装和维修。
4.电源和地线分布:电源和地线的设计是PCB线路板中最关键和常见的问题。
电源线和地线应尽量短且粗,以降低线路的电阻和电感。
同时,应按照规定的顺序布置和连接电源和地线。
5.信号传输线的匹配和阻抗控制:对于高频信号或差分信号传输线,需要进行信号匹配和阻抗控制。
匹配和阻抗控制可以提高信号传输的质量和稳定性,减少信号的失真和干扰。
6.元件布局和封装选择:合理的元件布局可以减少线路板的面积和线路长度,提高线路板的稳定性和性能。
同时,要选择合适的元件封装,确保元件与线路板之间的连接可靠。
7.温度和热量控制:8.防静电保护:在PCB线路板设计中,要考虑到防静电的问题,以避免静电对元件和电路的损坏。
可以采用电路设计和元件封装等手段来进行防静电保护。
9.标志和标注:在PCB线路板上应标注清晰的标志和标注,以方便组装、维修和调试。
标志和标注应包括线路板的名称、版本号、日期等信息。
10.制造和测试可行性:在设计PCB线路板时,要考虑到制造和测试的可行性。
应选择合适的材料和制造工艺,以确保线路板的质量和可靠性。
同时,要设计适合的测试点和测试方法,方便对线路板进行测试和调试。
总之,PCB线路板设计规范是确保线路板性能和可靠性的基本要求。
根据具体的应用需求和制造工艺,可进一步完善并优化线路板设计规范。
PCB设计规范

PCB工艺设计规范1.目的规范产品的PCB工艺设计,规定PCB工艺设计的相关参数,使得PCB的设计满足可生产性、可测试性、安规、EMC、EMI等的技术规范要求,在产品设计过程中构建产品的工艺、技术、质量、成本优势。
2.适用范围本规范适用于所有电了产品的PCB工艺设计,运用于但不限于PCB的设计、PCB投板工艺审查、单板工艺审查等活动。
本规范之前的相关标准、规范的内容如与本规范的规定相抵触的,以本规范为准。
3.定义导通孔(via):一种用于内层连接的金属化孔,但其中并不用于插入元件引线或其它增强材料。
盲孔(Blind via):从印制板内仅延展到一个表层的导通孔。
埋孔(Buried via):未延伸到印制板表面的一种导通孔。
过孔(Through via):从印制板的一个表层延展到另一个表层的导通孔。
元件孔(Component hole):用于元件端子固定于印制板及导电图形电气联接的孔。
Stand off:表面贴器件的本体底部到引脚底部的垂直距离。
4.引用/参考标准或资料TS—S0902010001 <<信息技术设备PCB安规设计规范>>TS—SOE0199001 <<电子设备的强迫风冷热设计规范>>TS—SOE0199002 <<电子设备的自然冷却热设计规范>>IEC60194 <<印制板设计、制造与组装术语与定义>> (Printed Circuit Board design manufacture and assembly-terms and definitions)IPC—A—600F <<印制板的验收条件>> (Acceptably of printed board)IEC609505.规范内容5.1 PCB板材要求5.1.1确定PCB使用板材以及TG值确定PCB所选用的板材,例如FR—4、铝基板、陶瓷基板、纸芯板等,若选用高TG值的板材,应在文件中注明厚度公差。
公司PCB设计规范

公司PCB设计规范PCB设计规范是现代电路设计的重要组成部分,它对保证电路的品质、生产效率和设计成本等方面具有重要的作用。
为了确保公司生产的PCB设计符合规范要求,我们需要建立一套完整的PCB设计规范。
一、规范的内容PCB设计规范应包括以下内容:1.设计固定参数:包括PCB厚度、金属化孔壁厚度、印刷电路板(PCB)尺寸、焊盘间距、引脚排列等。
这些参数对于设计电路的尺寸和布局非常重要,需要在设计前定义清楚。
2.热量和尺寸限制:PCB设计需要考虑热量传递和排放,尤其是在高压和高频电路中,需要特别注意。
因此,在规范中需要约定热量和尺寸的限制条件,以确保设计符合实际需求。
3.层级规定:在PCB设计中,常常会涉及到不同电路层的设计和布局,这时需要约定不同电路层的名称和编号,并定义所在电路板的顺序、颜色、布线等等。
4.标称值和偏差规定:在PCB设计中,各元件的标称值和偏差会对设计造成很大影响,因此需要定义各元件的标称值和偏差范围。
5.重点部分的细节规定:对于设计中一些比较特殊的部分,如高压射频、高速信号传输等,需要定义设计的参数和限制。
这些细节规定有助于确保重点部分的设计符合实际要求。
二、规范的实施为了确保规范的有效实施,公司需要建立相应的管理体系。
具体措施如下:1.明确责任:规范的实施需要有明确的责任人。
由部门主管或生产管理人员负责制定规范,并确定实施的计划和步骤。
2.培训和普及:为了让所有参与设计的人员能够理解和遵守规范,公司需要开展相应的培训和普及工作。
可以通过内部培训、讲座、技术交流等方式进行普及,让人员了解和掌握规范的要求。
3.监督检查:在实施过程中需要对设计文档进行监督检查,确保设计符合规范。
监督检查的方式可以通过审核、抽查等,查出不符合规范要求的设计文档,及时进行改正。
4.完善修改:规范随着技术和工艺的变化而不断完善,一旦有新的要求和调整,需要及时进行修改和更新,确保规范与实际情况相符。
三、规范带来的好处1.提高生产效率:规范可以固定设计参数和部分设计细节,减少重复设计、修改和排版,同时通过提高设计的质量,减少产生错误、漏洞和灾难的概率,从而提高生产效率。
华为pcb设计规范
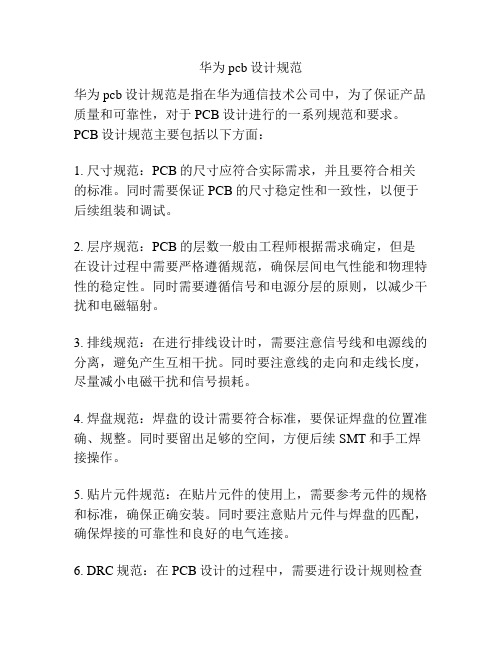
华为pcb设计规范华为pcb设计规范是指在华为通信技术公司中,为了保证产品质量和可靠性,对于PCB设计进行的一系列规范和要求。
PCB设计规范主要包括以下方面:1. 尺寸规范:PCB的尺寸应符合实际需求,并且要符合相关的标准。
同时需要保证PCB的尺寸稳定性和一致性,以便于后续组装和调试。
2. 层序规范:PCB的层数一般由工程师根据需求确定,但是在设计过程中需要严格遵循规范,确保层间电气性能和物理特性的稳定性。
同时需要遵循信号和电源分层的原则,以减少干扰和电磁辐射。
3. 排线规范:在进行排线设计时,需要注意信号线和电源线的分离,避免产生互相干扰。
同时要注意线的走向和走线长度,尽量减小电磁干扰和信号损耗。
4. 焊盘规范:焊盘的设计需要符合标准,要保证焊盘的位置准确、规整。
同时要留出足够的空间,方便后续SMT和手工焊接操作。
5. 贴片元件规范:在贴片元件的使用上,需要参考元件的规格和标准,确保正确安装。
同时要注意贴片元件与焊盘的匹配,确保焊接的可靠性和良好的电气连接。
6. DRC规范:在PCB设计的过程中,需要进行设计规则检查(DRC),用于排查设计中的错误和不符合规范的地方。
DRC规范包括禁止过于靠近边缘、禁止过小的过孔和过小的线宽等。
7. 环保规范:在设计中要尽量减少对环境的影响,选用环保的材料和工艺。
同时要注意废弃物的处理和回收,确保环保意识贯穿整个设计过程。
8. EMI规范:在PCB设计中,要尽量减小电磁干扰的影响,采取屏蔽、隔离和滤波的措施。
同时要遵守相关的EMI标准,确保产品在电磁兼容性方面符合要求。
9. 热管理规范:在高性能的电子产品设计中,要考虑散热问题,采用散热片、散热模组和散热孔等技术手段,确保PCB的温度控制在合理范围内。
10. 防静电规范:防静电措施是PCB设计中必不可少的一项规范。
要考虑电路的结构布局,使用合适的防静电元器件和防护措施,预防静电对电路和器件的损害。
综上所述,华为PCB设计规范是为了确保产品质量和可靠性,对PCB设计进行的一系列规范和要求。
pcb设计规范

pcb设计规范PCB设计规范是指在进行PCB(印刷电路板)设计时需要遵守的一系列规范和要求。
它是为了确保PCB设计能够满足电路功能、可靠性、性能和制造要求而制定的一套准则。
下面是一个包括以下几个方面的PCB设计规范的简要介绍:布局规范、连接规范、尺寸规范、排线规范、屏蔽规范、引脚规范、焊盘规范、维护规范、供电规范、阻抗控制规范、信号完整性规范和电磁兼容规范等。
一、布局规范:1. 分区:将电路分成不同区域,例如:模拟区和数字区,以保证信号隔离和降低干扰。
2. 元件间距:为了防止短路和易于维修,元件之间应有足够的间距。
3. 元件定位:同一类元件应按一定方向或排列位置的顺序来布置,方便组装和维护。
4. 散热:大功率元件应注意散热,通过散热铺铜、散热片等方式来确保元件正常工作。
二、连接规范:1. 自上而下:信号在PCB板上的走向应该尽量遵循由上到下的原则,使得PCB板的布线更加整洁、直观。
2. 避开高频:要尽量避免高频信号和低频信号之间的相互干扰,可以使用屏蔽或扩大引脚间的距离来降低干扰。
3. 引脚的选择:应该根据现有的条件优先选择靠近与所连接元件引脚的导线,减少有钟信号线的影响。
三、尺寸规范:1. PCB板的大小:要注意PCB板的大小与所在设备的大小相匹配,确保PCB板可以适应所在设备中的空间限制。
2. 引脚排列的紧凑性:要选择适当的引脚封装,使得PCB板的线路布线更加紧凑,减小占用空间。
四、排线规范:1. 频率分离:要分离高频和低频信号,以减少信号之间的干扰。
2. 避免平行:尽量避免平行排线,以减少互相之间的串扰。
3. 差分信号的布线:对差分信号进行特殊配置,使两个信号线的长度、宽度和间距保持一致,以减少干扰。
五、屏蔽规范:1. 地平面:在PCB板的一层铜皮上进行足够的地线平面,以减少地线的串扰。
2. 分离高频和低频信号:在高频和低频信号之间设置屏蔽层,以降低互相之间的干扰。
六、引脚规范:1. 引脚类型:根据元件的类型和功能,选择适当的引脚类型,例如标准引脚、表面贴装引脚或插针引脚等。
PCB电路设计规范与要求内容
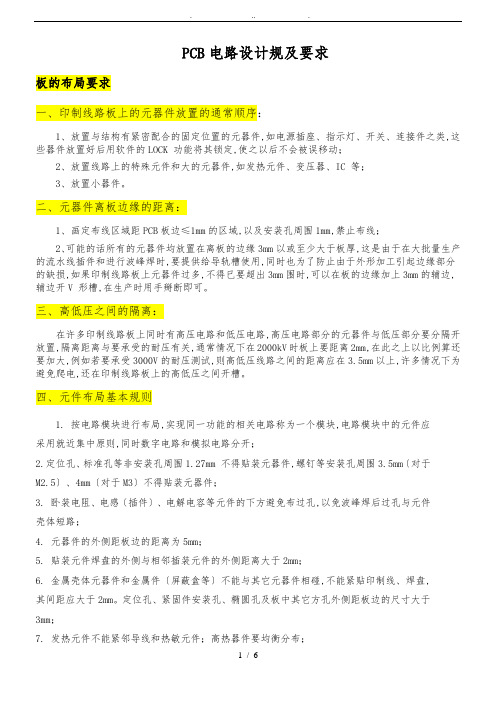
PCB电路设计规及要求板的布局要求一、印制线路板上的元器件放置的通常顺序:1、放置与结构有紧密配合的固定位置的元器件,如电源插座、指示灯、开关、连接件之类,这些器件放置好后用软件的LOCK 功能将其锁定,使之以后不会被误移动;2、放置线路上的特殊元件和大的元器件,如发热元件、变压器、IC 等;3、放置小器件。
二、元器件离板边缘的距离:1、画定布线区域距PCB板边≤1mm的区域,以及安装孔周围1mm,禁止布线;2、可能的话所有的元器件均放置在离板的边缘3mm以或至少大于板厚,这是由于在大批量生产的流水线插件和进行波峰焊时,要提供给导轨槽使用,同时也为了防止由于外形加工引起边缘部分的缺损,如果印制线路板上元器件过多,不得已要超出3mm围时,可以在板的边缘加上3mm的辅边,辅边开V 形槽,在生产时用手掰断即可。
三、高低压之间的隔离:在许多印制线路板上同时有高压电路和低压电路,高压电路部分的元器件与低压部分要分隔开放置,隔离距离与要承受的耐压有关,通常情况下在2000kV时板上要距离2mm,在此之上以比例算还要加大,例如若要承受3000V的耐压测试,则高低压线路之间的距离应在3.5mm以上,许多情况下为避免爬电,还在印制线路板上的高低压之间开槽。
四、元件布局基本规则1. 按电路模块进行布局,实现同一功能的相关电路称为一个模块,电路模块中的元件应采用就近集中原则,同时数字电路和模拟电路分开;2.定位孔、标准孔等非安装孔周围1.27mm 不得贴装元器件,螺钉等安装孔周围3.5mm〔对于M2.5〕、4mm〔对于M3〕不得贴装元器件;3. 卧装电阻、电感〔插件〕、电解电容等元件的下方避免布过孔,以免波峰焊后过孔与元件壳体短路;4. 元器件的外侧距板边的距离为5mm;5. 贴装元件焊盘的外侧与相邻插装元件的外侧距离大于2mm;6. 金属壳体元器件和金属件〔屏蔽盒等〕不能与其它元器件相碰,不能紧贴印制线、焊盘,其间距应大于2mm。
pcb之设计规范(DFM要求)
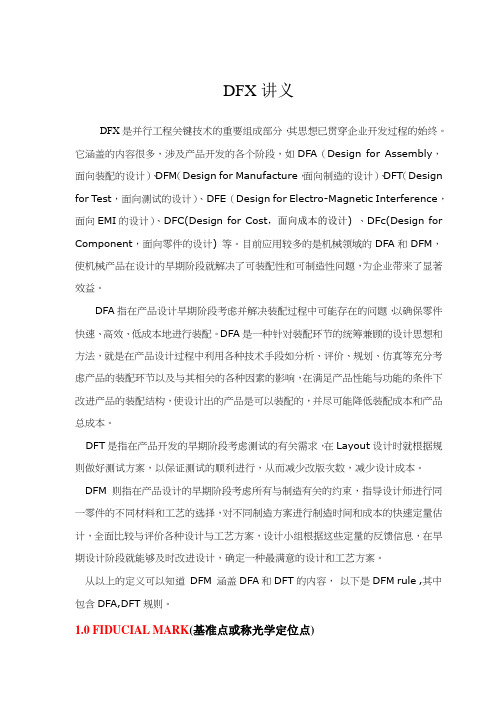
DFX讲义DFX是并行工程关键技术的重要组成部分,其思想已贯穿企业开发过程的始终。
它涵盖的内容很多,涉及产品开发的各个阶段,如DFA(Design for Assembly,面向装配的设计)、DFM(Design for Manufacture,面向制造的设计)、DFT(Design for Test,面向测试的设计)、DFE(Design for Electro-Magnetic Interference,面向EMI的设计)、DFC(Design for Cost,面向成本的设计) 、DFc(Design for Component,面向零件的设计) 等。
目前应用较多的是机械领域的DFA和DFM,使机械产品在设计的早期阶段就解决了可装配性和可制造性问题,为企业带来了显著效益。
DFA指在产品设计早期阶段考虑并解决装配过程中可能存在的问题,以确保零件快速、高效、低成本地进行装配。
DFA是一种针对装配环节的统筹兼顾的设计思想和方法,就是在产品设计过程中利用各种技术手段如分析、评价、规划、仿真等充分考虑产品的装配环节以及与其相关的各种因素的影响,在满足产品性能与功能的条件下改进产品的装配结构,使设计出的产品是可以装配的,并尽可能降低装配成本和产品总成本。
DFT是指在产品开发的早期阶段考虑测试的有关需求,在Layout设计时就根据规则做好测试方案,以保证测试的顺利进行,从而减少改版次数,减少设计成本。
DFM则指在产品设计的早期阶段考虑所有与制造有关的约束,指导设计师进行同一零件的不同材料和工艺的选择,对不同制造方案进行制造时间和成本的快速定量估计,全面比较与评价各种设计与工艺方案,设计小组根据这些定量的反馈信息,在早期设计阶段就能够及时改进设计,确定一种最满意的设计和工艺方案。
从以上的定义可以知道DFM 涵盖DFA和DFT的内容,以下是DFM rule ,其中包含DFA,DFT规则。
1.0FIDUCIAL MARK(基准点或称光学定位点)为了SMT机器自动放置零件之基准设定,因此必须在板子四周加上FIDUCIAL MARK1.1 FIDUCIAL MARK之形状,尺寸及SOLDER MASK大小1.1.1 FIDUCIAL MARK放在对角边φ1mm为喷锡面φ3mm为NO MASKφ3mm之内不得有线路及文字3.1.2φ1mm的喷锡面需注意平整度1.2 FIDUCIAL MARK之位置,必须与SMT零件同一平面(Component Side),如为双面板,则双面亦需作FIDUCIAL MARK1.3 FIDUCIAL放在PCB四角落,边缘距板边至少5mm1.4 板边的FIDUCIAL MARK需有3个以上,若无法做三个FIDUCIAL MARK时,则最少需做两个对角的FIDUCIAL MARK1.5 所有的SMT零件必须尽可能的包含在板边FIDUCIAL MARK所形成的范围内1.6 PITCH 20 mil(含)以下之零件(QFP)及BGA对角处需加FIDUCIAL MARK, 25mil之QFP不强制加FIDUCIAL MARK.但若最接近PCB四对角处之QFP PITCH 为25mil(非20mil以下)该零件亦需加FIDUCIAL MARK.2.0 SOLDER MASK (防焊漆)2.1 任何SMD PAD之Solder Mask,由pad外缘算起3mil +- 1mil作SOLDER MASK.2.2 除了PAD与TRACE之相接触任何地方之Solder Mask不得使TRACE露出2.3 SMD PAD与PAD间作MASK之问题:因考虑SMD PAD与PAD 间的密度问题, 除SMD(QFP Fine pitch)196 PIN&208 PIN不强制要求作MASK,其余均要求作MASK2.4 SMD QFP,PLCC或PGA 等四边皆有PAD(四边有PIN) 之方形零件底下所有VIA HOLE均必须作SOLDER MASK,及该零件底下之VIA HOLE均盖上防焊漆2.5 测试点之防焊2.5.1仍以Component Side 测试点全部防焊但不盖满,且Solder Side不被Solder Mask盖到,为最佳状况2.5.2 为防止Component Side被盖满,或Solder Side被Solder Mask盖到,故以DIA VIA PLATED外加2mil 露锡为可接受范围(如下图)2mil2.6 其它非测试点之VIA Hole, Component Side仍以不露锡为可接受范围2.7 VIA HOLE与SMD PAD相邻时,必须100% Tenting防焊漆3.0 SILK SCREEN (文字面)3.1 文字面与VIA HOLE不可重叠避免文字残缺3.2 文字面的标示每个Component必须标示清楚以目视可见清晰为主3.2.1每种字皆得完整3.2.2通电极性与其它记号都清楚呈现3.2.3字码中空区不可被沾涂(如:0,6,8,9,A,B,D,O,P,Q,R等)若已被沾涂,以尚可辨认而不致与其它字码混淆者3.3 各零件之图形应尽量符合该零件的外形无脚零件(R,C,CB,L)于PAD间之文字面须加上油墨划,视需求自行决定图形3.4 有方向性之零件应清楚标示脚号或极性3.4.1 IC四脚位必须标示各脚位,及第1 PIN方向性3.4.2 CONNECTOR 应标示四周前后之脚号3.4.3 Jumper应标示第1 PIN及方向性3.4.4 BGA 应标示第1 PIN及各角之数组脚号3.5 文字距板边最小10mil3.6 人工贴图时,文字,符号,图形不可碰到PAD(包括VIA HOLE PAD 非不得已,以尚可辨认而不致与其它字码混淆者)3.7 CAD作业时, 文字,符号,图形不可碰到PAD,FIDUCIAL MARK,而VIA HOLEPAD 则尽量不去碰到3.8 由上而下,由左而右顺序,编列各零件号码4.0 TOOLING HOLE (定位孔)4.1 为配合自动插件设备,板子必须作TOOLING HOLE(φ4mm+-) TOOLING HOLE中心距板边为5mm(NON-PTH孔),须平行对称,至少两个孔,如遇板边(V-CUT)须有第三孔,且两孔间间距误差于+-20mil(0.5mm)以内the third hole4.2 如板子上零件太多,无法做三个TOOLING HOLE时,则于最长边作两个TOOLINGHOLE或可作于V-CUT上5.0 PLACEMENT NOTES (零件布置)5.1 DIP 所有零件方向(极性)应朝两方向,而相同包装类形之零件方向请保持一致5.2 DIP 零件周围LAYOUT SMD零件时应预留>1mm的空间,以不致妨碍人工插拔动作5.3 SMD零件距板边至少5mm,若不足时须增加V-CUT至5mm;M/I DIP 零件由实体零件外缘算起各板边至少留3mm3mm5mm5.4 DIP零件之限制:5.4.1 排阻尽可能不要LAYOUT于排针之间5.4.2 MINI-Jumper的数量尽量减少;且MINI-Jumper与Slot, Heat-Sink至少两公分5.4.3 尽量勿于BIOS SOCKET底下LAYOUT其它零件5.4.4 M/I DIP 零件周围LAYOUT SMD 零件时,应预留1mm 空间,以防有卡位情形5.4.5 M/I DIP 零件之方向极性须为同方向,最多两种方向5.4.6 M/I DIP 零件PIN 必须超出PCB 面1.2~1.6mm5.5 VIA HOLE 不可LAYOUT 于SMD PAD 上,须距PAD ≧10mil 以免造成露锡5.6 SMD 零件分布Fine-pitch 208 pin QFP 或较大之QFP, PLCC, SMD SOCKET 等零件,在LAYOUT 时应尽量避免皆集中于某个区域,必须分散平均布置;尤以在2颗Fine-pitch 208 pin QFP 之间放置较小之CHIPS(R,C,L……),应尽量避免过于集中5.7 双面板布置限制SMD 形式之CONNECTOR 应尽量与Fine-pitch, QFP,PLCC 零件同一面5.8 请预留BAR CODE 位置于PCB 之正面5.9 零件放在两个连接器之间,零件长边要和连接器长边平行排放,零件和连接器的间距至少要有零件高度的一倍5.10 SMD 零件须与 mounting hole 中心距离 500 mil.5.11 周为DIP 零件的地方背面不能放SMD 零件。
浅析PCB电路板设计规范

浅析PCB电路板设计规范在PCB电路板设计中,设计规范是非常重要的,它可以确保电路板的性能和可靠性。
设计规范包括电路板外形尺寸、元件、布线、层次结构、电源和接地等方面,本文将从这些方面简要地浅析PCB电路板设计规范。
一、电路板外形尺寸设计规范基本上,电路板的长宽比应该不超过4:3,而且两边的长度不能超过455mm,这样可使电路板方便快捷地制造。
在设计电路板布局时,应注意保持元器件之间的正确位置和间距。
对于大型的元器件或高功率器件,需要更多的空间来散热,这样可以有效地防止限制热量的堵塞,导致设备出现故障。
此外,在布线时,应注意避免元器件之间的相互干扰和短路现象,确保电路板的可靠性和稳定性。
二、PCB电路板元器件规范在元器件规范中,应该注意以下几点:1. 保证元器件的排列合理:在PCB电路板设计中,排列合理的元器件布局可以减少电路板的面积,还可以减少电路板上电路的数量,这样可以提高电路板的可靠性和性能。
2. 保证元器件的可替换性:在设计PCB电路板时,应该留出足够的空间,以便更换故障器件或升级电路。
3. 元器件的选取和使用应符合国家和行业标准,使电路工作安全可靠。
在选择元器件时,应注意材料的质量和厚度,以保证电路板的耐用性和可靠性。
三、PCB电路板布线规范1.保持布线的整洁:在电路板设计中,布线的整洁很重要,可以使电路板更加安全可靠,也可以使电路工作更加稳定。
同时,整洁的布线可以使电路板的维修和改装更加方便。
2.分层布线:分层布线可以有效地降低电路板的干扰和噪声,在布线时应注意避免信号线和电源线的干扰,并保持正确的距离。
3.应避免长路径线和盲孔:长路径线和盲孔是可能引起电路噪声和干扰的因素之一,因此,应该尽量避免使用和布线这种类型的电路。
四、层次结构、信号质量和电源/接地规范在电路板设计时,应注意以下几点:1.层次结构:层次结构是一种设计布局的方法,可以使电路板更加规范化、易于布线和易于组装。
在设计PCB电路板时,应考虑实际情况,选择最适合的层次结构布局方法。
- 1、下载文档前请自行甄别文档内容的完整性,平台不提供额外的编辑、内容补充、找答案等附加服务。
- 2、"仅部分预览"的文档,不可在线预览部分如存在完整性等问题,可反馈申请退款(可完整预览的文档不适用该条件!)。
- 3、如文档侵犯您的权益,请联系客服反馈,我们会尽快为您处理(人工客服工作时间:9:00-18:30)。
PCB设计基本概念1、“层(Layer) ”的概念与字处理或其它许多软件中为实现图、文、色彩等的嵌套与合成而引入的“层”的概念有所同,Protel的“层”不是虚拟的,而是印刷板材料本身实实在在的各铜箔层。
现今,由于电子线路的元件密集安装。
防干扰和布线等特殊要求,一些较新的电子产品中所用的印刷板不仅有上下两面供走线,在板的中间还设有能被特殊加工的夹层铜箔,例如,现在的计算机主板所用的印板材料多在4层以上。
这些层因加工相对较难而大多用于设置走线较为简单的电源布线层(如软件中的Ground Dever和Power Deve r),并常用大面积填充的办法来布线(如软件中的ExternaI P1 a11e和Fill)。
上下位置的表面层与中间各层需要连通的地方用软件中提到的所谓“过孔(Via)”来沟通。
有了以上解释,就不难理解“多层焊盘”和“布线层设置”的有关概念了。
举个简单的例子,不少人布线完成,到打印出来时方才发现很多连线的终端都没有焊盘,其实这是自己添加器件库时忽略了“层”的概念,没把自己绘制封装的焊盘特性定义为”多层(Mulii一Layer)的缘故。
要提醒的是,一旦选定了所用印板的层数,务必关闭那些未被使用的层,免得惹事生非走弯路。
2、过孔(Via)为连通各层之间的线路,在各层需要连通的导线的文汇处钻上一个公共孔,这就是过孔。
工艺上在过孔的孔壁圆柱面上用化学沉积的方法镀上一层金属,用以连通中间各层需要连通的铜箔,而过孔的上下两面做成普通的焊盘形状,可直接与上下两面的线路相通,也可不连。
一般而言,设计线路时对过孔的处理有以下原则:(1)尽量少用过孔,一旦选用了过孔,务必处理好它与周边各实体的间隙,特别是容易被忽视的中间各层与过孔不相连的线与过孔的间隙,如果是自动布线,可在“过孔数量最小化” (Vi a Minimiz8tion)子菜单里选择“on”项来自动解决。
(2)需要的载流量越大,所需的过孔尺寸越大,如电源层和地层与其它层联接所用的过孔就要大一些。
3、丝印层(Overlay)为方便电路的安装和维修等,在印刷板的上下两表面印刷上所需要的标志图案和文字代号等,例如元件标号和标称值、元件外廓形状和厂家标志、生产日期等等。
不少初学者设计丝印层的有关内容时,只注意文字符号放置得整齐美观,忽略了实际制出的PCB效果。
他们设计的印板上,字符不是被元件挡住就是侵入了助焊区域被抹赊,还有的把元件标号打在相邻元件上,如此种种的设计都将会给装配和维修带来很大不便。
正确的丝印层字符布置原则是:”不出歧义,见缝插针,美观大方”。
4、SMD的特殊性Protel封装库内有大量SMD封装,即表面焊装器件。
这类器件除体积小巧之外的最大特点是单面分布元引脚孔。
因此,选用这类器件要定义好器件所在面,以免“丢失引脚(Missing Plns)”。
另外,这类元件的有关文字标注只能随元件所在面放置。
5、网格状填充区(External Plane )和填充区(Fill)正如两者的名字那样,网络状填充区是把大面积的铜箔处理成网状的,填充区仅是完整保留铜箔。
初学者设计过程中在计算机上往往看不到二者的区别,实质上,只要你把图面放大后就一目了然了。
正是由于平常不容易看出二者的区别,所以使用时更不注意对二者的区分,要强调的是,前者在电路特性上有较强的抑制高频干扰的作用,适用于需做大面积填充的地方,特别是把某些区域当做屏蔽区、分割区或大电流的电源线时尤为合适。
后者多用于一般的线端部或转折区等需要小面积填充的地方。
6、焊盘( Pad)焊盘是PCB设计中最常接触也是最重要的概念,但初学者却容易忽视它的选择和修正,在设计中千篇一律地使用圆形焊盘。
选择元件的焊盘类型要综合考虑该元件的形状、大小、布置形式、振动和受热情况、受力方向等因素。
Protel在封装库中给出了一系列不同大小和形状的焊盘,如圆、方、八角、圆方和定位用焊盘等,但有时这还不够用,需要自己编辑。
例如,对发热且受力较大、电流较大的焊盘,可自行设计成“泪滴状”,在大家熟悉的彩电PCB的行输出变压器引脚焊盘的设计中,不少厂家正是采用的这种形式。
一般而言,自行编辑焊盘时除了以上所讲的以外,还要考虑以下原则:(1)形状上长短不一致时要考虑连线宽度与焊盘特定边长的大小差异不能过大;(2)需要在元件引角之间走线时选用长短不对称的焊盘往往事半功倍;(3)各元件焊盘孔的大小要按元件引脚粗细分别编辑确定,原则是孔的尺寸比引脚直径大0.2- 0.4毫米。
7、各类膜(Mask)这些膜不仅是PcB制作工艺过程中必不可少的,而且更是元件焊装的必要条件。
按“膜”所处的位置及其作用,“膜”可分为元件面(或焊接面)助焊膜(Top or Bottom 和元件面(或焊接面)阻焊膜(Top or BottomPaste Mask)两类。
顾名思义,助焊膜是涂于焊盘上,提高可焊性能的一层膜,也就是在绿色板子上比焊盘略大的各浅色圆斑。
阻焊膜的情况正好相反,为了使制成的板子适应波峰焊等焊接形式,要求板子上非焊盘处的铜箔不能粘锡,因此在焊盘以外的各部位都要涂覆一层涂料,用于阻止这些部位上锡。
可见,这两种膜是一种互补关系。
由此讨论,就不难确定菜单中类似“solder Mask En1argement”等项目的设置了。
8、飞线,飞线有两重含义:(1)自动布线时供观察用的类似橡皮筋的网络连线,在通过网络表调入元件并做了初步布局后,用“Show 命令就可以看到该布局下的网络连线的交叉状况,不断调整元件的位置使这种交叉最少,以获得最大的自动布线的布通率。
这一步很重要,可以说是磨刀不误砍柴功,多花些时间,值!另外,自动布线结束,还有哪些网络尚未布通,也可通过该功能来查找。
找出未布通网络之后,可用手工补偿,实在补偿不了就要用到“飞线”的第二层含义,就是在将来的印板上用导线连通这些网络。
要交待的是,如果该电路板是大批量自动线生产,可将这种飞线视为0欧阻值、具有统一焊盘间距的电阻元件来进行设计.一、过孔的概念过孔(via)是多层PCB的重要组成部分之一,钻孔的费用通常占PCB制板费用的30%到40%。
简单的说来,PCB上的每一个孔都可以称之为过孔。
从作用上看,过孔可以分成两类:1、用作各层间的电气连接。
2、用作器件的固定或定位。
如果从工艺制程上来说,这些过孔一般又分为三类,即盲孔(blind via)、埋孔(buried via)和通孔(through via)。
盲孔位于印刷线路板的顶层和底层表面,具有一定深度,用于表层线路和下面的内层线路的连接,孔的深度通常不超过一定的比率(孔径)。
埋孔是指位于印刷线路板内层的连接孔,它不会延伸到线路板的表面。
上述两类孔都位于线路板的内层,层压前利用通孔成型工艺完成,在过孔形成过程中可能还会重叠做好几个内层。
第三种称为通孔,这种孔穿过整个线路板,可用于实现内部互连或作为元件的安装定位孔。
由于通孔在工艺上更易于实现,成本较低,所以绝大部分印刷电路板均使用它,而不用另外两种过孔。
以下所说的过孔,没有特殊说明的,均作为通孔考虑。
从设计的角度来看,一个过孔主要由两个部分组成,一是中间的钻孔(drill hole),二是钻孔周围的焊盘区,见下图。
这两部分的尺寸大小决定了过孔的大小。
很显然,在高速,高密度的P CB设计时,设计者总是希望过孔越小越好,这样板上可以留有更多的布线空间,此外,过孔越小,其自身的寄生电容也越小,更适合用于高速电路。
但孔尺寸的减小同时带来了成本的增加,而且过孔的尺寸不可能无限制的减小,它受到钻孔(drill)和电镀(plating)等工艺技术的限制:孔越小,钻孔需花费的时间越长,也越容易偏离中心位置;且当孔的深度超过钻孔直径的6倍时,就无法保证孔壁能均匀镀铜。
比如,现在正常的一块6层PCB板的厚度(通孔深度)为50Mil左右,所以PCB厂家能提供的钻孔直径最小只能达到8Mil。
二、过孔的寄生电容过孔本身存在着对地的寄生电容,如果已知过孔在铺地层上的隔离孔直径为D2,过孔焊盘的直径为D1,PCB板的厚度为T,板基材介电常数为ε,则过孔的寄生电容大小近似于:C=1.41εTD1/(D2-D1)过孔的寄生电容会给电路造成的主要影响是延长了信号的上升时间,降低了电路的速度。
举例来说,对于一块厚度为50Mil的PCB板,如果使用内径为10Mil,焊盘直径为20Mil的过孔,焊盘与地铺铜区的距离为32Mil,则我们可以通过上面的公式近似算出过孔的寄生电容大致是:C=1.41x4.4x0.050x0.020/(0.032-0.020)=0.517pF,这部分电容引起的上升时间变化量为:T10-9 0=2.2C(Z0/2)=2.2x0.517x(55/2)=31.28ps 。
从这些数值可以看出,尽管单个过孔的寄生电容引起的上升延变缓的效用不是很明显,但是如果走线中多次使用过孔进行层间的切换,设计者还是要慎重考虑的。
三、过孔的寄生电感同样,过孔存在寄生电容的同时也存在着寄生电感,在高速数字电路的设计中,过孔的寄生电感带来的危害往往大于寄生电容的影响。
它的寄生串联电感会削弱旁路电容的贡献,减弱整个电源系统的滤波效用。
我们可以用下面的公式来简单地计算一个过孔近似的寄生电感:L=5.08h[ln(4h/d)+1]其中L指过孔的电感,h是过孔的长度,d是中心钻孔的直径。
从式中可以看出,过孔的直径对电感的影响较小,而对电感影响最大的是过孔的长度。
仍然采用上面的例子,可以计算出过孔的电感为:L=5.08x0.050[ln(4x0.050/0.010)+1]=1.015nH 。
如果信号的上升时间是1ns,那么其等效阻抗大小为:XL=πL/T10-9 0=3.19Ω。
这样的阻抗在有高频电流的通过已经不能够被忽略,特别要注意,旁路电容在连接电源层和地层的时候需要通过两个过孔,这样过孔的寄生电感就会成倍增加。
四、高速PCB中的过孔设计通过上面对过孔寄生特性的分析,我们可以看到,在高速PC B设计中,看似简单的过孔往往也会给电路的设计带来很大的负面效应。
为了减小过孔的寄生效应带来的不利影响,在设计中可以尽量做到:1.从成本和信号质量两方面考虑,选择合理尺寸的过孔大小。
比如对6-10层的内存模块PCB设计来说,选用10/20Mil(钻孔/焊盘)的过孔较好,对于一些高密度的小尺寸的板子,也可以尝试使用8/18Mil的过孔。
目前技术条件下,很难使用更小尺寸的过孔了。
对于电源或地线的过孔则可以考虑使用较大尺寸,以减小阻抗。
2.上面讨论的两个公式可以得出,使用较薄的PCB板有利于减小过孔的两种寄生参数。
3.PCB板上的信号走线尽量不换层,也就是说尽量不要使用不必要的过孔。
4.电源和地的管脚要就近打过孔,过孔和管脚之间的引线越短越好,因为它们会导致电感的增加。