天津红日AES70说明书
Pacific Steamex 翻转氧发热喷头 操作手册说明书

READ THIS BOOKThis operator’s book has important information for the use and safe operation of this machine. Read this book care-fully before starting the machine. Keep this book and tell all operators to read the book. If you do not follow the instructions, you can cause an injury or damage equipment,furniture or buildings.For new books write to: Pacific2259 S. SheridanMuskegon, MI 49442-6252Carefully inspect all components to ensure that there is no concealed freight damage. If such damage is discovered,file a “CONCEALED DAMAGE REPORT” immediately with the delivering carrier.The contents of this manual are based on the latest product information available at the time of publication. Pacific Steamex reserves the right to make changes or improve-ments to its machines without notice.FOR YOUR CONVENIENCE, RECORD THE FOLLOWING IMPORT ANT INFORMATION:MODEL _______________________________SERIAL NUMBER _______________________PART NUMBER ________________________DATE PURCHASED _____________________OPERATING & MAINTENANCEINTRODUCTION INSTRUCTIONSWET/DRY V ACUUMSPWD 600PWD 609PWD 612PWD 615Gulper 600S Gulper 609S Gulper 612S Gulper 615SIMPORTANT SAFETY INSTRUCTIONSREAD AND UNDERSTAND ALL WARNINGS AND INSTRUCTIONSBEFORE USING THIS MACHINE!WARNING! To reduce the risk of fire, electric shock, or injury:1.You must be trained to operate this machine. This machine is to be operated for its intended useonly.2.Do not operate this machine unless it is completely assembled.3.Always use a three-wire electrical system connected to the electrical ground. For maximum protec-tion against electrical shock, use a circuit that is protected by a ground fault circuit interrupter. Con-sult your electrical contractor.4.To prevent electrical shock: Always remove the electrical plug from the electrical outlet before per-forming any repairs, maintenance or cleanup and when leaving the machine unattended.5.To prevent electrical shock: Keep the machine surface dry; Do not subject to rain; Store the machinein a dry building area; Clean the machine with a dry cloth only.6.Machines can cause an explosion when near flammable materials and vapors. Do not use or storethis machine with or near fuels, grain dust, solvents, thinners, or other flammable materials. Do not use flammables to clean this machine.7.Maintenance and repairs must be done by a qualified or authorized person.8.If the machine is not working as it should, has been dropped, damaged, left outdoors, or dropped intowater, return it to a service center.9.To avoid damage to the machine’s electrical cord, always lift the machine over the cord. Do not runthe machine over the electircal cord.10.Make sure all labels, decals, warnings, cautions and instructions are fastened to the machine.This machine must be grounded. If it should malfunction or break down, grounding provides a path of least resistance for electric cur-rent to reduce the risk of electric shock. This machine is equipped with a cord having an equipment-grounding conductor and grounding plug. The plug must be inserted into an appropriate outlet that is properly installed and grounded in accordance with all local codes and ordinances.WARNING - Improper connection of the equipment-grounding con-ductor can result in a risk of electric shock. Check with a qualified electrician or service person if you are in doubt as to whether the outlet is properly grounded. Do not modify the plug provided with the machine - if it will not fit the outlet, have a proper outlet installed by a qualified electrician.This machine is for use on a nominal 120-volt circuit, and has a grounded plug that looks like the plug illustrated in figure A. A temporary adapter that looks like the adapter illustrated in figures B and C may be used to connect this plug to a 2-pole receptacle as shown in figure B if a properly grounded outlet is not available. The temporary adapter should be used only until a properly grounded outlet (figure A) can be installed by a qualified electrician. The green colored rigid ear, lug, or the like extending from the adapter must be connected to a permanent ground such as a properly grounded outlet box cover. Whenever the adapter is used, it must be held in place by a metal screw.NOTE: In Canada, the use of a temporary adapter is not permitted by the Canadian Electrical CodeEXTENSION CORDSUse only three-wire 16/3 or larger gauge approved extension cords that have three-prong grounding type plugs and three-pole receptacles that accept the appliance’s plug. Replace or repair any damaged cords or plugs.When servicing, refer to authorized person only. Use only identical replace-ment parts.Grounding InstructionsNOTE: Do not use adapters shown in figures B & C in CanadaMAINTENANCEGood maintenance procedures assure better operation, fewer repairs and longer life to your machine.DISCONNECT THE ELECTRICAL PLUG OF THE MA-CHINE FROM THE ELECTRICAL OUTLET BEFORE DOING ANY CLEANUP, REPAIRS OR MAINTENANCE OF THE MACHINE AND WHEN LEA VING THE MACHINE UNA TTENDED.CLEAN THE MACHINE AFTER EACH USE:1. Wipe the outside with a clean cloth.2. Clean the collector tank: Release the clamps on each sideof the tank and head assembly. Lift the head assembly off and set aside. Lift the filter assembly out of the collector tank and set aside. Then wipe the inside of the collector tank with a clean cloth.3. Empty and check the filter assembly: Empty the recoveredsoilage into a suitable container and shake to remove clinging dirt. Brush the outside of the filter bag to remove embedded dirt. Check the filter assembly for tears or holes; repair or replace if necessary. Install the clean filter assembly into the ELECTRICAL CABLE:Check the cord for any nicks, cuts or damage. Report these to your supervisor for correction.V ACUUM HEAD ASSEMBLY:1. Gaskets: Clean the vacuum head gasket and the float shut-offgasket.2. Float Shut-Off Device: This should move freely. Removeany debris or strings from the float cage.3. Head Assembly: Replace and leave ajar if the collector tank isdamp to prevent mildew.WHEELS AND CASTERS:Check these for cuts and nicks. Remove any strings or debris that may restrict the free movement of the wheels. Wipe the treads clean.CARBON BRUSH INSPECTION:Check for wear at six month intervals or every 600 hours of operation. The carbon brushes must be replaced if worn shorter than 3/8 inch.OPERATING PROCEDURESWARNING! For the safe operation of this machine follow the instructions given in this booklet and the training given by your supervisor. Failure to do so can result in personal injury and/or damage to machine and property!DO NOT OPERA TE MACHINE IN AN EXPLOSIVE ENVIRONMENT!To prepare the machine for operation, make sure it is of the correct voltage and properly assembled. If in doubt, ask your supervisor. FOR DRY PICK-UP:“Dry” refers to material such as dust, dirt, debris and dry foam shampoo.1.Release the clamp on each side of the tank and head assembly.Lift the head assembly off and set it aside.2.Then lift the cloth filter assembly out of the collector tank.Clean the cloth filter if needed (reference the “Maintenance”section).3.Empty the collector tank of all dust and debris. If the debrisis wet, empty and dry the inside of the tank thoroughly. 4.Place the cloth filter assembly back into the collector tank.Check for a good seal around the outer filter lip and tank rim.5.Replace the head assembly and fasten both clamps. Attachthe hose, wand and floor tool of choice (reference page 5).6.Plug the power cord into a 115-volt, 60 cycle grounded outlet.7.Turn the machine’s motor on by pressing the rocker switchwhich is located on the head assembly.W ARNING! NEVER USE THIS MACHINE TO PICK UP VOLA TILE OR EXPLOSIVE MA TERIALS.FOR WET PICK-UP:“Wet” refers to liquids such as water, scrub solutions and deter-gents; NOT VOLATILE OR EXPLOSIVE MA TERIALS. 1.Release the clamp on each side of the tank and head assembly.Lift the head assembly off and set it aside.2.Then lift the cloth filter assembly out of the collector tank.Store the filter assembly for future, dry pick-up use. DO NOT REINSTALL.3.Empty the collector tank of all dust and debris. Also wipethe inside of the collector tank to remove clinging dust.4.Check the float shut-off device on the lower portion of thehead assembly. The float should have free movement. When the recovered liquid soilage reaches the collector tank capac-ity, the float will rise to shut off the air flow, stopping the liquid recovery. This prevents damaging overflow and signals the operator when to empty the collector tank.5.Replace the head assembly and fasten both clamps. Attachthe hose, wand and floor tool of choice (reference page 5).6.Plug the power cord into a 115-volt, 60 cycle grounded outlet.7.Turn the machine’s motor on by pressing the rocker switchwhich is located on the head assembly.123457891011121314151617181920212223152425262728293031333435363738394032123912134567810111415161920171821222425233334353632262728293938374042414344453031123457810111213149615161718192021222324252627282930313233343536373839404142434445464847495051525354555657585933PWD 615 and Gulper 615S2314568911128131415161712181920OPTIONAL ACCESSORY CARPET TOOL- ITEM 218912DELUXE TOOL KIT PART #608510TOOL KIT ASSEMBL Y :1.Connect the hose to the collector tank by inserting thelarge, grooved hose adapter end into the tank adapter.Pull the locking pin up to allow the hose adapter to slide further in. Release the locking pin to engage the large groove.2.Insert the upper wand half firmly into the lower wand assembly. The dimple on the lower wand aligns with the groove of the upper half to assure a rigid fit.3.Insert the wand end into the free end of the vacuum hose.Then fasten the proper floor tool to the to the wand by inserting the mating end of the floor tool into the adapter collar of the wand assembly. Pull the tool locking pin to allow total engagement of the adapter and tool. Release the pin to lock the tool to the wand.4.The hand tools may also be used by inserting their adapter directly into the free end of the vacuum hose.5.Tool Selection: Choosing the proper tool will give the best results. To vacuum dust and debris from floors or walls-select the bristle floor tool. To remove water, liquid waste, strip solution, etc. from hard surfaced floors-use the squeegee floor tool. When vacuuming carpets or rugs-choose the carpet tool.11OPTIONAL SQUEEGEE ASSEMBLYPART #6085191234567891011121314151617451863002010/01W ARRANTY POLICY WET/DRY V ACUUMSThe Pacific Steamex Inc. Wet/Dry Vacuum has been manufactured, tested and inspected in accordance with specific engi-neering requirements and is W ARRANTED to be free from defects in workmanship and materials as follows:One (1) year parts & labor - All components unless excluded below.This warranty extends to the original user/purchaser and only when used, operated and maintained in accordance with Pacific Steamex Inc. Operating and Maintenance instructions.This warranty does not apply to certain wear parts and accessories of the machine such as electrical cords, carbon motor brushes, floor brushes, hoses, tools, filters, casters, wheels, etc. Nor does it apply to damage or failure caused by improper use, abuse or neglect. Warranty credit or replacement of return parts including motors, etc., is subject to incoming inspection of those items.To secure repair under this warranty, the following procedure should be taken:•The inoperative machine or warranted parts must be delivered to the authorized dealer with shipping and deliverycharges prepaid. If unable to locate the Dealer, you may contact Pacific Steamex Inc. at the address listed herein for the location of the nearest Pacific Steamex Inc. repair center or agent or for other instructions pertaining to your warranty difficulty.•Upon compliance with the above warranty procedure, all warranted repairs would be completed at no additional charge or cost to the user.•Only Pacific Steamex Inc. or its authorized dealers and agents may make no charge warranty repairs on this product. All others do so at their own risk.This warranty limits Pacific Steamex Inc. liability to the repair of the product and/or warranted parts replacement and does not include incidental or consequential damages arising from the use of a Pacific Steamex Inc. machine whether defective or not.This warranty is in lieu of all other expressed or implied warranties and is extended to the original purchaser/user.2259 SheridanMuskegon, Michigan 49442Ph: (800) 968-1332 Fax: (231) 773-1642。
VICTOR_70F说明书按键英汉翻译版.讲义
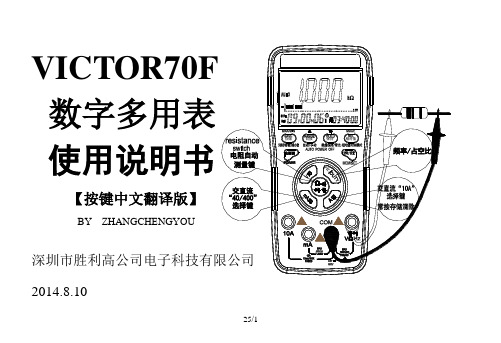
BY ZHANGCHENGYOU2014.8.10厂商声明胜利高公司向最初购买该仪表的购买者承诺:自购买之日起一年内在正常使用情况下给予保修,并免费更换材料(不包括保险丝、测试表笔)。
本公司不承担在不正常的条件下操作使用万用表而造成的对仪表和人员造成的损害。
要获得本公司的服务,请与本公司最近的仪器服务中心联系或将产品连同有关产生问题的说明、邮资一起寄到最近的仪器服务中心。
本公司不承担在邮递当中的损害,本公司将免费维修或更换出错的产品或退还您所购买产品的费用。
然而,如果本公司检测出这些错误是由于误用、更换、事故或不正常的条件下使用或操作而引起的,您将要为维修而付维修费,维修好的产品将退回给您。
运回产品维修或校准仪表应该经过统一包装“快递”到本公司。
仪表应该被装在出厂纸板箱里以便运输。
如果没有可用的纸箱,使用大小合适的牢固的容器进行包装,如果使用替代品,仪表应该用纸预先包装,并且用类似的减震材料围在周围。
对最初购买者有关在运输中的损坏声明仪表运送到购买者处,购买者应立即全面检查仪表,盒子里的所有材料应该对照附带的包装单进行核对检查。
如果仪表以任何方式损坏,应及时通知运送者。
如要修理由于运输而损坏的仪表,请与最近的胜利仪器服务中心联系。
由于运输损坏与运输公司的赔偿协商应由顾客来完成。
使用本手册注意事项●本用户手册内容如有改变,恕不另行通知。
●本用户手册的内容被认为是正确的,若用户发现有错误、遗漏等,请与生产厂家联系。
●本公司不承担由于用户错误操作所引起的事故和危害。
●本用户手册所述的功能不作为将本产品用作特殊用途的理由。
25/2目录1、概述 (4)2、开箱检查 (5)3、安全注意事项 (6)4、安全符号说明 (7)5、仪表面板及按键功能说明 (8)6、按键开关………………………………………………………………………………………9-107、显示屏幕………………………………………………………………………………………11-128、特性 (13)9、直流电压(DCV) (14)10、交流电压(ACV) (15)11、直流电流(DCA) (16)12、交流电流(ACA) (17)13、电阻 (18)14、二极管及通断测试 (19)15、电容(C) (20)16、频率(Hz)及仪表保养………………………………………………………………………21-2325/3一.概述VICTOR70F一种智能型、性能稳定、高可靠性、3 3/4数字多用表,仪表采用33mm字高LCD 显示器,读数清晰,显示直观,操作方便,可用来测量直流电压、交流电压、直流电流、交流电流、电阻、电容、频率、二极管及通断测试;同时还有单位符号显示、数据保持(HOLD)、最大最小値测量(MAX/MIN),相对值测量(REL),数据存储(SAVE),数据读取(MEM),时间显示(year/month/day/hour/minute/second),自动/手动量程转换(AUTO/RANGE)、自动断电及报警功能(15分钟)、采用面板校准技术。
FPD-7024 火灾报警控制器用户手册说明书

Panel de control de alarma de incendio FPD-7024Represante del servicio localNombre Dirección TeléfonoModos de funcionamiento del sistemaEl LED amarillo de falla se enciende cuando el sistema detecta un problema con el cableado o el circuitointerno y permanece encendido hasta que se corrija el problema. El LED de falla parpadea mientras el modo ma o alarma y se apaga cuando se corrige la condición que se silenció.El LED verde de alimentación se enciende cuan-sistema registra uns alarma y no se resetea.(salidas) y el discador.gramación.eventos anarmales indicados en pantella.246La tecla Simulacro se usa para activar los circuitos de dispositivos de notifcación locales manualmente.La tecla Silenciar silencia las campanas/sirenas de una condición de alarma.el sistema se encuentra en el modo de programación.Funcionamiento normal: Cuando el sistema funciona normalmente, aparece SIST NORMAL (sistema normal) en la línea superior de la pantalla y únicamente está iluminado el LED de encendido. Si el sistema está programado para requerir un PIN, aparecerá I NGR PIN: (i ngresar PIN:) en la segunda línea de la pantalla LCD. De lo contrario, el panel de control omite esta pantalla y muestra la fecha y la hora.Funcionamiento de la alarma: Cuando se activa una alarma, la línea superior de la pantalla muestra ALARMA (xxx). Esta pantalla anula cualquier otra pantalla del sistema. La segunda línea de la pantalla muestra USAR TEC ACK/FNC (usar tecla ACK/FUNC) y alterna con la descripción programada para el punto afectado. La sirena integrada se activa con un tono continuo y se encienden las salidas programadas para activarse con la condición de alarma actual.Funcionamiento de falla: Cuando se produce una falla (por ejemplo, se corta el cableado en un punto, falla la alimentación de CA, etc.), el dispositivo de aviso acústico se activa brevemente, cada 10 segundos. El LED de falla se enciende y aparece FAL-LA (xxx) en la línea superior de la pantalla. La segunda línea de la pantalla muestra USAR TEC ACK/FNC (usar tecla ACK/FUNC) y alterna con la descripción programada para la falla.Funcionamiento de supervisión: Cuando se produce una falla de supervisión, el dispositivo de aviso acústico se activa breve-mente, cada 10 segundos. El LED de supervisión se enciende y aparece SUPERVISIÓN(xxx) en la línea superior de la pantalla. La segunda línea de la pantalla muestra USAR TEC ACK/FNC (usar tecla ACK/FUNC) y alterna con la descripción programada para l a falla de supervisión.Uso de los números de PIN: en sistemas configurados para no requerir un PIN, los comandos como Reset y Silenciar se ejecutan presionando la tecla correspondiente, a la que se accede luego de abrir el panel. En sistemas que requieren un número de PIN, ingrese primero el PIN de cuatro dígitos asignado al usuario. Cuando aparece la lista de opciones disponibles, simplemente presione la tecla del comando deseado.El se usa como botón de Reconocimiento. Al presionar el botón, el teclado y la sirena piezoeléctrica del panel de control se silenciarán, pero los circuitos de dispositivos de notificación (NAC) no se verán afectados. Presionar permite desplazarse por los grupos de condiciones anormales. Presionar o permite ver los detalles de una condición anormal dentro del grupo se-leccionado. Al presionar se regresa al menú principal. El control del panel se libera si se presiona la tecla nuevamente o, caso contrario, de forma automática luego de 3 minutos.Instrucciones de funcionamiento del FPD7024Información del teclado integradoEl teclado integrado en el panel de control es un teclado LCD alfanumérico. Posee una pantalla con dos líneas y 16 caracteres que ofrece información sobre varias funciones del panel de control. En la mayoría de los casos, la línea superior de la pantalla muestra información general sobre el estado del sistema, mientas que la segunda línea describe los dispositivos específicos que podrían ser relevantes para el estado actual del sistema. Al presionar las teclas, la pantalla muestra la acción actual en la línea superior, mientras que en la segunda línea se muestran opciones de menú que van rotando. El dispositivo de aviso acústico integrado se usa para anunciar las entradas con el teclado y como dispositivo de aviso interior.Este documento debe enmarcarse y colocarse en un lugar visible junto a la FACP .El LED amarillo de supervisión se enciende siempre que elsupervisión.especiales de prueba.programación.El LED amarillo Falla Tierra se enciende cuando el© 2016 Bosch Security Systems, Inc.130 Perinton Parkway, Fairport, NY 14450-9199 USA(800) 289-009604/16FPD-7024Page 2 of 2 F01U311876-02Operating Instructions。
CARBOCAP GM70 手持二氧化碳百分比仪用户手册说明书

Here the FPI is tuned to a nearby non-absorbing reference wavelength, where the IR Detector measures the full intensity of light, creating a baseline for comparison. Any changes in the performance of the light source, FPI or IR Detector effect both measurments equally, preserving the difference between both measurements and therefore the calibration of the sensor.
5. Why is the CO2 concentration reading higher than expected when using the pump sampling method?
1. How does the CARBOCAP®, NDIR (non-dispersive infrared), single beam, dual wavelength sensor work?
2. How do temperature and pressure effect CO2 measurement?
3. How can temperature and pressure errors be corrected when using Vaisala CO2 products?
4. How can condensation be avoided when sampling from incubators?
SICK SES SEM70 旋转电机反馈系统 HIPERFACE 手册说明书

P R O D U C T I N F O R M A T I O NSES/SEM70, SES/SEM90MOTOR FEEDBACK SOLUTION FORHOLLOW SHAFT MOTORS AND DIRECT DRIVESMotor feedback system rotary HIPERFACE ®M o t o r f e e d b a c k s y s t e M s|s I c k Subject to change without notice 38021252/2018-05-23MOTOR FEEDBACK SYSTEMS ROTARY HIPERFACE®ses/seM70Fields of application• Hollow shafts and torque motors• Applications with axial movements, e.g. extrusion ma-chines, injection molding machines • Revolving machines and woodworking machines • Rotary table applications• Robot applicationsDetailed technical dataPerformanceInterfacesElectrical data2) At 7 V DC and without load.Mechanical dataM o t o r f e e d b a c k s y s t e M s | s I c k Subject to change without notice48021252/2018-05-23ses/seM70 MOTOR FEEDBACK SYSTEMS ROTARY HIPERFACE ®Ambient data2)Every encoder has been tested with a half-sine-shaped shock.3)The EMC according to the standards quoted is achieved when the motor feedback system is mounted in an electrically conductive housing, which is connected to the central earthing point of the motor controller via a cable shield. Users must perform their own tests when other shield designs are used.Ordering information Singleturn for integration• Available memory area: E 2PROM 2048• Electrical interface: HIPERFACE®Multiturn for integration• Available memory area: E 2PROM 2048• Electrical interface: HIPERFACE®Dimensional drawings (Dimensions in mm (inch))1 Measuring point for operating temperatureM o t o r f e e d b a c k s y s t e M s | s I c k Subject to change without notice58021252/2018-05-23MOTOR FEEDBACK SYSTEMS ROTARY HIPERFACE ® ses/seM70Proposed fitting7 (0.28)3 x M33 x Ø 12 (0.47)Min. 24 (0.94)Min. 1.5 (0.06)0.05AØ 73 ±0.1 (2.87)Ø 67 G7 (2.64) 3 x 120°3x 120°AØ 25 h 6(0.98)0.05A0.05A Read out axial position: negative value shows movement of rotor away from the motor flange; positive value shows movement of rotor towards the motor flangePIN assignmentView of the plug-in faceSupported resources for HIPERFACE®M o t o r f e e d b a c k s y s t e M s | s I c k Subject to change without notice68021252/2018-05-23ses/seM70 MOTOR FEEDBACK SYSTEMS ROTARY HIPERFACE ®Overview of warnings and fault indicationsM o t o r f e e d b a c k s y s t e M s|s I c k Subject to change without notice 78021252/2018-05-23MOTOR FEEDBACK SYSTEMS ROTARY HIPERFACE®ses/seM70AccessoriesConnection systemsPlug connectors and cablesCables (ready to assemble)Connecting cables with female connectorDimensional drawings g page 7Connection cables with female connector and male connectorDimensional drawings g page 7Further accessoriesProgramming and configuration toolsDimensional drawings g page 9Dimensional drawings for accessories (Dimensions in mm (inch)) Plug connectors and cablesDOL-0J08-G0M2XB6shrunk areaDOL-0J08-G0M5XC31 red2 wht3 brn4 pnk5 blk6 blu7 gra8 grnM o t o r f e e d b a c k s y s t e M s | s I c k Subject to change without notice88021252/2018-05-23ses/seM70 MOTOR FEEDBACK SYSTEMS ROTARY HIPERFACE ®DSL-2317-G01MJB62 blu3 red 7 blk à pnk á vi ã yel ä brn å whtM o t o r f e e d b a c k s y s t e M s|s I c k Subject to change without notice 98021252/2018-05-23MOTOR FEEDBACK SYSTEMS ROTARY HIPERFACE®ses/seM70Programming and configuration tools PGT-11-S LANPGT-11-S WLANM o t o r f e e d b a c k s y s t e M s|s I c k Subject to change without notice 118021252/2018-05-23MOTOR FEEDBACK SYSTEMS ROTARY HIPERFACE®ses/seM90Fields of application• Hollow shafts and torque motors• Applications with axial movements, e.g. extrusion ma-chines, injection molding machines • Revolving machines and woodworking machines • Rotary table applications• Robot applicationsDetailed technical dataPerformanceInterfacesElectrical data2) At 7 V DC and without load.Mechanical dataM o t o r f e e d b a c k s y s t e M s | s I c k Subject to change without notice128021252/2018-05-23ses/seM90 MOTOR FEEDBACK SYSTEMS ROTARY HIPERFACE ®Ambient data1) 2)Every encoder has been tested with a half-sine-shaped shock.3)The EMC according to the standards quoted is achieved when the motor feedback system is mounted in an electrically conductive housing, which is connected to the central earthing point of the motor controller via a cable shield. Users must perform their own tests when other shield designs are used.Ordering information Singleturn for integration• Available memory area: E 2PROM 2048• Electrical interface: HIPERFACE®Multiturn for integration• Available memory area: E 2PROM 2048• Electrical interface: HIPERFACE®Dimensional drawings (Dimensions in mm (inch))+0.31 Measuring point for operating temperatureM o t o r f e e d b a c k s y s t e M s|s I c k Subject to change without notice 138021252/2018-05-23MOTOR FEEDBACK SYSTEMS ROTARY HIPERFACE®ses/seM90Proposed fittingRead out axial position: negative value shows movement of rotor away from the motor flange; positive value shows movement of rotor towards the motor flange PIN assignmentView of the plug-in faceSupported resources for HIPERFACE®M o t o r f e e d b a c k s y s t e M s | s I c k Subject to change without notice148021252/2018-05-23ses/seM90 MOTOR FEEDBACK SYSTEMS ROTARY HIPERFACE ®Overview of warnings and fault indicationsM o t o r f e e d b a c k s y s t e M s|s I c k Subject to change without notice 158021252/2018-05-23MOTOR FEEDBACK SYSTEMS ROTARY HIPERFACE®ses/seM90AccessoriesConnection systemsPlug connectors and cablesCables (ready to assemble)Connecting cables with female connectorDimensional drawings g page 15Connection cables with female connector and male connectorDimensional drawings g page 15Further accessoriesProgramming and configuration toolsDimensional drawings g page 17Dimensional drawings for accessories (Dimensions in mm (inch)) Plug connectors and cablesDOL-0J08-G0M2XB6shrunk areaDOL-0J08-G0M5XC31 red2 wht3 brn4 pnk5 blk6 blu7 gra8 grnM o t o r f e e d b a c k s y s t e M s | s I c k Subject to change without notice168021252/2018-05-23ses/seM90 MOTOR FEEDBACK SYSTEMS ROTARY HIPERFACE ®DSL-2317-G01MJB62 blu3 red 7 blk à pnk á vi ã yel ä brn å whtM o t o r f e e d b a c k s y s t e M s|s I c k Subject to change without notice 178021252/2018-05-23MOTOR FEEDBACK SYSTEMS ROTARY HIPERFACE®ses/seM90Programming and configuration tools PGT-11-S LANPGT-11-S WLANM o t o r f e e d b a c k s y s t e M s | s I c k Subject to change without notice188021252/2018-05-23NOTESSERVICES FOR MACHINES AND PLANTS: SICK LifeTime ServicesOur comprehensive and versatile LifeTime Services are the perfect addition to the comprehensive range of products from SICK. The services range from product-independent consulting to traditional product services.Training and educationPractical, focused, and professionalUpgrade and retrofitsEasy, safe, and economicalConsulting and designSafe and professionalVerification and optimizationSafe and regularly inspectedProduct and system supportReliable, fast, and on-siteSERVICESREGISTER AT TO TAKE ADVANTAGE OF OUR FOLLOWING SERVICES FOR YOUAccess information on net prices and individual discounts. Easily order online and track your delivery.Check your history of all your orders and quotes.Create, save, and share as many wish lists as you e the direct order to quickly order a big amount of products.Check the status of your orders and quotes and get infor-mation on status changes by e-mail. Save time by using past orders.Easily export orders and quotes, suited to your systems.m m m m m m mm M o t o r -F e e d b a c k -S y S t e M e | S I c k Subject to change without notice198021252/2018-05-23SICK AG | Waldkirch | Germany | SICK AT A GLANCESICK is a leading manufacturer of intelligent sensors and sensor solutions for industrial applications. With more than 8,000 employees and over 50 subsidiaries and equity investments as well as numerous agencies worldwide, we are always close to our customers. A unique range of products and services creates the perfect basis for controlling processes securely and efficiently, protecting individuals from accidents and preventing damage to the environment.We have extensive experience in various industries and understand their processes and requirements. With intelligent sensors, we can deliver exactly what our customers need. In application centers in Europe, Asia and North America, system solutions are tested and optimized in accordance with customer specifica -tions. All this makes us a reliable supplier and development partner.Comprehensive services round out our offering: SICK LifeTime Services provide support throughout the machine life cycle and ensure safety and productivity.For us, that is “Sensor Intelligence.”Worldwide presence:Australia, Austria, Belgium, Brazil, Canada, Chile, China, Czech Republic, Denmark, Finland, France, Germany, Great Britain, Hungary, Hong Kong, India, Israel, Italy, Japan, Malaysia, Mexico, Netherlands, New Zealand, Norway, Poland, Romania, Russia, Singapore, Slovakia, Slovenia, South Africa, South Korea, Spain, Sweden, Switzerland, Taiwan, Thailand, Turkey, United Arab Emirates, USA, Vietnam.Detailed addresses and further locations - 8021252/2018-05-23 ∙ J S _07 ∙ P r e U S m o d e n 47。
清晨太阳防光聚酯顶层防护剂安全资料单说明书

CLEAR SUNSHIELD POLYESTER TOPCOATSafety Data Sheetaccording to Federal Register / Vol. 77, No. 58 / Monday, March 26, 2012 / Rules and RegulationsRevision date: 08/28/201908/28/2019 EN (English US) Page 1 1.1. IdentificationProduct form : MixtureTrade name : CLEAR SUNSHIELD POLYESTER TOPCOATCAS-No. : mixtureProduct code : 904-061Formula : na1.2. Recommended use and restrictions on useUse of the substance/mixture : COATING1.3. SupplierDura Technologies, Inc.2720 South Willow Avenue #ABloomington, CA 92316909-546-1162ChemTrec US: 800.424.9300ChemTrec Int: +1 70 3527 38871.4. Emergency telephone numberEmergency number : ChemTrec US: 800.424.9300 Int: +1 70 3527 38872.1. Classification of the substance or mixtureGHS US classificationFlammable liquids Category 2 H225 Highly flammable liquid and vapourSkin corrosion/irritation Category 2 H315 Causes skin irritationSerious eye damage/eye irritation Category 2 H319 Causes serious eye irritationSkin sensitization, Category 1 H317 May cause an allergic skin reactionCarcinogenicity Category 2 H351 Suspected of causing cancerReproductive toxicity Category 2 H361 Suspected of damaging fertility or the unborn childSpecific target organ toxicity (single exposure) Category 3 H335 May cause respiratory irritationSpecific target organ toxicity (repeated exposure) Category 1 H372 Causes damage to organs through prolonged or repeated exposure Aspiration hazard Category 1 H304 May be fatal if swallowed and enters airwaysHazardous to the aquatic environment - Acute Hazard Category 2 H401 Toxic to aquatic lifeFull text of H statements : see section 162.2. GHS Label elements, including precautionary statementsGHS US labelingHazard pictograms (GHS US):Signal word (GHS US) : DangerHazard statements (GHS US) : H225 - Highly flammable liquid and vapourH304 - May be fatal if swallowed and enters airwaysH315 - Causes skin irritationH317 - May cause an allergic skin reactionH319 - Causes serious eye irritationH335 - May cause respiratory irritationH351 - Suspected of causing cancerH361 - Suspected of damaging fertility or the unborn childH372 - Causes damage to organs through prolonged or repeated exposureH401 - Toxic to aquatic lifePrecautionary statements (GHS US) : P201 - Obtain special instructions before use.P202 - Do not handle until all safety precautions have been read and understood.P210 - Keep away from heat, hot surfaces, sparks, open flames and other ignition sources. Nosmoking.P233 - Keep container tightly closed.P240 - Ground/Bond container and receiving equipmentP241 - Use explosion-proof electrical, lighting, ventilating equipmentP242 - Use only non-sparking tools.P243 - Take precautionary measures against static discharge.P260 - Do not breathe dust/fume/gas/mist/vapors/spray.P261 - Avoid breathing dust/fume/gas/mist/vapors/spray.P264 - Wash exposed area. thoroughly after handling.P270 - Do not eat, drink or smoke when using this product.P271 - Use only outdoors or in a well-ventilated area.P272 - Contaminated work clothing must not be allowed out of the workplaceP273 - Avoid release to the environment.P280 - Wear eye protection, protective clothing, protective gloves.P301+P310 - If swallowed: Immediately call a poison center or doctorP302+P352 - If on skin: Wash with plenty of waterP303+P361+P353 - If on skin (or hair): Take off immediately all contaminated clothing. Rinseskin with water/showerP304+P340 - If inhaled: Remove person to fresh air and keep comfortable for breathingP305+P351+P338 - If in eyes: Rinse cautiously with water for several minutes. Remove contactlenses, if present and easy to do. Continue rinsingP308+P313 - If exposed or concerned: Get medical advice/attention.P312 - Call a poison center or doctor if you feel unwellP314 - Get medical advice/attention if you feel unwell.P321 - Specific treatment (see none listed. on this label)P331 - Do NOT induce vomiting.P332+P313 - If skin irritation occurs: Get medical advice/attention.P333+P313 - If skin irritation or rash occurs: Get medical advice/attention.P337+P313 - If eye irritation persists: Get medical advice/attention.P362+P364 - Take off contaminated clothing and wash it before reuse.P363 - Wash contaminated clothing before reuse.P370+P378 - In case of fire: Use carbon dioxide (CO2), dry chemical powder, foam toextinguish.P403+P233 - Store in a well-ventilated place. Keep container tightly closed.P403+P235 - Store in a well-ventilated place. Keep cool.P405 - Store locked up.P501 - Dispose of contents/container to in accordance with local, state, and federal regulations.2.3. Other hazards which do not result in classificationNo additional information available2.4. Unknown acute toxicity (GHS US)Not applicable3.1. SubstancesNot applicable3.2. MixturesFull text of hazard classes and H-statements : see section 16SECTION 4: First-aid measures4.1. Description of first aid measuresFirst-aid measures general : Never give anything by mouth to an unconscious person. If you feel unwell, seek medicaladvice (show the label where possible).First-aid measures after inhalation : Remove person to fresh air and keep comfortable for breathing. Allow affected person tobreathe fresh air. Allow the victim to rest. Remove victim to fresh air and keep at rest in aposition comfortable for breathing. Call a POISON CENTER or doctor/physician if you feelunwell.First-aid measures after skin contact : Rinse skin with water/shower. Remove/Take off immediately all contaminated clothing. Washwith plenty of soap and water. Wash contaminated clothing before reuse. If skin irritationoccurs: wash throughly for five minutes. seek medical attention. Get medical advice/attention.Specific treatment (see seek medical attention. on this label).First-aid measures after eye contact : Rinse cautiously with water for several minutes. Remove contact lenses, if present and easy todo. Continue rinsing. If eye irritation persists: SEEK IMMEDIATE MEDICAL ATTENTION. Getmedical advice/attention.First-aid measures after ingestion : Rinse mouth. Do NOT induce vomiting. Obtain emergency medical attention. Call a poisoncenter/doctor/physician if you feel unwell.4.2. Most important symptoms and effects (acute and delayed)Potential Adverse human health effects and: Harmful if inhaled.symptomsSymptoms/effects : May cause genetic defects (avoid skin contact and inhalation.). May cause cancer (avoid skincontact and inhalation.).Symptoms/effects after inhalation : Danger of serious damage to health by prolonged exposure through inhalation. Harmful ifinhaled.Symptoms/effects after skin contact : Causes skin irritation.Symptoms/effects after eye contact : Causes serious eye irritation.4.3. Immediate medical attention and special treatment, if necessaryTreat symptomatically.SECTION 5: Fire-fighting measures5.1. Suitable (and unsuitable) extinguishing mediaSuitable extinguishing media : Sand. Water spray. Dry powder. Foam. Carbon dioxide.Unsuitable extinguishing media : Do not use a heavy water stream.5.2. Specific hazards arising from the chemicalFire hazard : Highly flammable liquid and vapour.Explosion hazard : May form flammable/explosive vapor-air mixture.Reactivity in case of fire : No reactivity hazard other than the effects described in sub-sections below.5.3. Special protective equipment and precautions for fire-fightersFirefighting instructions : Use water spray or fog for cooling exposed containers. Exercise caution when fighting anychemical fire. Prevent fire-fighting water from entering environment.Protection during firefighting : Do not enter fire area without proper protective equipment, including respiratory protection. Donot attempt to take action without suitable protective equipment. Self-contained breathingapparatus. Complete protective clothing.SECTION 6: Accidental release measures6.1. Personal precautions, protective equipment and emergency proceduresGeneral measures : Remove ignition sources. Use special care to avoid static electric charges. No open flames. Nosmoking.6.1.1. For non-emergency personnelProtective equipment : Gloves. Protective goggles. Protective clothing.Emergency procedures : Ventilate spillage area. Evacuate unnecessary personnel.6.1.2. For emergency respondersProtective equipment : Do not attempt to take action without suitable protective equipment. Equip cleanup crew withproper protection. For further information refer to section 8: "Exposure controls/personalprotection".Emergency procedures : Ventilate area.6.2. Environmental precautionsAvoid release to the environment. Prevent entry to sewers and public waters. Notify authorities if liquid enters sewers or public waters.6.3. Methods and material for containment and cleaning upFor containment : Dam up the liquid spill. Contain released product, pump into suitable containers.Methods for cleaning up : Take up liquid spill into absorbent material. Soak up spills with inert solids, such as clay ordiatomaceous earth as soon as possible. Collect spillage. Store away from other materials. Other information : Dispose of materials or solid residues at an authorized site.6.4. Reference to other sectionsSee Heading 8. Exposure controls and personal protection. For further information refer to section 13.7.1. Precautions for safe handlingAdditional hazards when processed : Handle empty containers with care because residual vapors are flammable.Precautions for safe handling : Wear personal protective equipment. Wash hands and other exposed areas with mild soap andwater before eating, drinking or smoking and when leaving work. Provide good ventilation inprocess area to prevent formation of vapor. No open flames. No smoking. Use only non-sparking tools. Use only outdoors or in a well-ventilated area. Avoid breathing DUST, FUMES,MIST, OR VAPORS. Obtain special instructions before use. Do not handle until all safetyprecautions have been read and understood. Eliminate all ignition sources if safe to do so. Hygiene measures : Wash HANDS thoroughly after handling. Do not eat, drink or smoke when using this product.Always wash hands after handling the product.7.2. Conditions for safe storage, including any incompatibilitiesTechnical measures : Proper grounding procedures to avoid static electricity should be followed. Ground/bondcontainer and receiving equipment. Use explosion-proof electrical, ventilating and lightingequipment. equipment.Storage conditions : Keep only in the original container in a cool, well ventilated place away from : HEAT SPARKSOR OPEN FLAMES. Keep in fireproof place. Keep container tightly closed. Store in a well-ventilated place. Keep cool.Incompatible products : Strong bases. Strong acids.Incompatible materials : Sources of ignition. Direct sunlight. Heat sources.8.1. Control parametersAppropriate engineering controls : Ensure exposure is below occupational exposure limits (where available). Ensure goodventilation of the work station.Environmental exposure controls : Avoid release to the environment.8.3. Individual protection measures/Personal protective equipmentPersonal protective equipment:Avoid all unnecessary exposure.Hand protection:Wear protective gloves.Eye protection:Chemical goggles or safety glasses. Safety glassesSkin and body protection:Wear suitable protective clothingRespiratory protection:Wear appropriate maskOther information:Do not eat, drink or smoke during use.SECTION 9: Physical and chemical properties9.1. Information on basic physical and chemical propertiesPhysical state : LiquidColor : clearOdor : characteristicOdor threshold : No data availablepH : No data availableMelting point : Not applicableFreezing point : No data availableBoiling point : >= 79.4 °CFlash point : 21 - 24 °CRelative evaporation rate (butyl acetate=1) : No data availableFlammability (solid, gas) : Highly flammable liquid and vapour.Vapor pressure : No data availableRelative vapor density at 20 °C : No data availableRelative density : <= 1.07Solubility : No data availableLog Pow : No data availableAuto-ignition temperature : No data availableDecomposition temperature : No data availableViscosity, kinematic : No data availableViscosity, dynamic : No data availableExplosion limits : No data availableExplosive properties : No data availableOxidizing properties : No data available9.2. Other informationNo additional information availableSECTION 10: Stability and reactivity10.1. ReactivityNo reactivity hazard other than the effects described in sub-sections below.10.2. Chemical stabilityPolymerization can result in formation of solid deposits, even in vapour space. Not established. Highly flammable liquid and vapour. May form flammable/explosive vapor-air mixture.10.3. Possibility of hazardous reactionsNot established.10.4. Conditions to avoidDirect sunlight. Extremely high or low temperatures. Open flame.10.5. Incompatible materialsStrong acids. Strong bases.10.6. Hazardous decomposition productsfume. Carbon monoxide. Carbon dioxide. May release flammable gases.11.1. Information on toxicological effectsAcute toxicity (oral) : Not classifiedAcute toxicity (dermal) : Not classifiedAcute toxicity (inhalation) : Not classifiedSkin corrosion/irritation : Causes skin irritation.Serious eye damage/irritation : Causes serious eye irritation.Respiratory or skin sensitization : May cause an allergic skin reaction.Germ cell mutagenicity : Not classifiedCarcinogenicity : Suspected of causing cancer.Reproductive toxicity : Suspected of damaging fertility or the unborn child.STOT-single exposure : May cause respiratory irritation.STOT-repeated exposure : Causes damage to organs through prolonged or repeated exposure.Aspiration hazard : May be fatal if swallowed and enters airways.Viscosity, kinematic : No data available: Harmful if inhaled.Potential Adverse human health effects andsymptomsSymptoms/effects : May cause genetic defects (avoid skin contact and inhalation.). May cause cancer (avoid skincontact and inhalation.).Symptoms/effects after inhalation : Danger of serious damage to health by prolonged exposure through inhalation. Harmful ifinhaled.Symptoms/effects after skin contact : Causes skin irritation.Symptoms/effects after eye contact : Causes serious eye irritation.SECTION 12: Ecological information12.1. ToxicityEcology - general : The product is not considered harmful to aquatic organisms or to cause long-term adverseeffects in the environment.12.4. Mobility in soil12.5. Other adverse effectsOther information : Avoid release to the environment.SECTION 13: Disposal considerations13.1. Disposal methodsWaste treatment methods : Dispose of contents/container in accordance with licensed collector’s sorting instructions. Product/Packaging disposal recommendations : Dispose in a safe manner in accordance with local/national regulations. Dispose ofcontents/container to approved disposal site.Additional information : Handle empty containers with care because residual vapors are flammable.Ecology - waste materials : Avoid release to the environment.SECTION 14: Transport informationDepartment of Transportation (DOT)In accordance with DOTTransport document description : UN1866 Resin solution, 3, IIUN-No.(DOT) : UN1866Proper Shipping Name (DOT) : Resin solutionClass (DOT) : 3 - Class 3 - Flammable and combustible liquid 49 CFR 173.120Packing group (DOT) : II - Medium DangerHazard labels (DOT) : 3 - Flammable liquidDOT Packaging Non Bulk (49 CFR 173.xxx) : 173DOT Packaging Bulk (49 CFR 173.xxx) : 242DOT Special Provisions (49 CFR 172.102) : 149 - When transported as a limited quantity or a consumer commodity, the maximum netcapacity specified in 173.150(b)(2) of this subchapter for inner packaging may be increased to5 L (1.3 gallons).383 - Packages containing toy plastic or paper caps for toy pistols described as “UN0349,Articles, explosive, n.o.s. (Toy caps), 1.4S” or “NA0337, Toy caps, 1.4S” are not subject to thesubpart E (labeling) requirements of this part when offered for transportation by motor vehicle,rail freight, cargo vessel, and cargo aircraft and, notwithstanding the packing method assignedin §173.62 of this subchapter, in conformance with the following conditions:B52 - Notwithstanding the provisions of 173.24b of this subchapter, non-reclosing pressurerelief devices are authorized on DOT 57 portable tanks.IB2 - Authorized IBCs: Metal (31A, 31B and 31N); Rigid plastics (31H1 and 31H2); Composite(31HZ1). Additional Requirement: Only liquids with a vapor pressure less than or equal to 110kPa at 50 C (1.1 bar at 122 F), or 130 kPa at 55 C (1.3 bar at 131 F) are authorized.T4 - 2.65 178.274(d)(2) Normal............. 178.275(d)(3)TP1 - The maximum degree of filling must not exceed the degree of filling determined by thefollowing: Degree of filling = 97 / 1 + a (tr - tf) Where: tr is the maximum mean bulk temperatureduring transport, and tf is the temperature in degrees celsius of the liquid during filling.TP8 - A portable tank having a minimum test pressure of 1.5 bar (150 kPa) may be used whenthe flash point of the hazardous material transported is greater than 0 C (32 F).DOT Packaging Exceptions (49 CFR 173.xxx) : 150: 5 LDOT Quantity Limitations Passenger aircraft/rail(49 CFR 173.27): 60 LDOT Quantity Limitations Cargo aircraft only (49CFR 175.75)DOT Vessel Stowage Location : B - (i) The material may be stowed ‘‘on deck’’ or ‘‘under deck’’ on a cargo vessel and on apassenger vessel carrying a number of passengers limited to not more than the larger of 25passengers, or one passenger per each 3 m of overall vessel length; and (ii) ‘‘On deck only’’ onpassenger vessels in which the number of passengers specified in paragraph (k)(2)(i) of thissection is exceeded.Emergency Response Guide (ERG) Number : 127Other information : No supplementary information available.Transportation of Dangerous GoodsTransport by seaTransport document description (IMDG) : UN 1866 RESIN SOLUTION, 3, IIUN-No. (IMDG) : 1866Proper Shipping Name (IMDG) : RESIN SOLUTIONClass (IMDG) : 3 - Flammable liquidsPacking group (IMDG) : II - substances presenting medium dangerAir transportTransport document description (IATA) : UN 1866 Resin solution, 3, IIUN-No. (IATA) : 1866Proper Shipping Name (IATA) : Resin solutionClass (IATA) : 3 - Flammable LiquidsPacking group (IATA) : II - Medium Danger15.1. US Federal regulations15.2. International regulations CANADAEU-RegulationsNo additional information available National regulations15.3. US State regulationsaccording to Federal Register / Vol. 77, No. 58 / Monday, March 26, 2012 / Rules and RegulationsRevision date : 08/28/2019Data sources : REGULATION (EC) No 1272/2008 OF THE EUROPEAN PARLIAMENT AND OF THECOUNCIL of 16 December 2008 on classification, labeling and packaging of substances andmixtures, amending and repealing Directives 67/548/EEC and 1999/45/EC, and amendingRegulation (EC) No 1907/2006.Other information : None.NFPA health hazard : 2 - Materials that, under emergency conditions, can causetemporary incapacitation or residual injury.NFPA fire hazard : 3 - Liquids and solids (including finely divided suspendedsolids) that can be ignited under almost all ambienttemperature conditions.NFPA reactivity : 2 - Materials that readily undergo violent chemical changeat elevated temperatures and pressures.Hazard RatingHealth : 2 Moderate Hazard - Temporary or minor injury may occurFlammability : 3 Serious Hazard - Materials capable of ignition under almost all normal temperatureconditions. Includes flammable liquids with flash points below 73 F and boiling points above100 F. as well as liquids with flash points between 73 F and 100 F. (Classes IB & IC)Physical : 1 Slight Hazard - Materials that are normally stable but can become unstable (self-react) at hightemperatures and pressures. Materials may react non-violently with water or undergohazardous polymerization in the absence of inhibitors.Personal protection : HH - Splash goggles, Gloves, Synthetic apron, Vapor respiratorSDS US (GHS HazCom 2012)To the best of our knowledge this SDS is accurate. The the extent allowed by law, this statement is made in lieu of an other warranties, expressed or implied including but not limited to any implied warranty of merchantability or fitness for a particular purpose and is in lieu of any other obligations or liability on the part of Dura Technoligies, Inc.。
ISE70中文说明书

②请具有充分知识和经验的人员使用本产品。
在此所述的产品若被误操作,将会损害其安全性能。 请具有充分知识和经验的人进行机械・设备的组装,操作,维修保养等作业。
③未确认机械・设备安全前,绝对禁止使用或拆卸。
1、请确认已经采取了预防被驱动物体掉落和失控的对应措施后,再对机械•设备进行维护保养。 2、拆卸产品时,请确认已采取了上述安全措施,并切断了能量源和设备电源等,以保证系统安全。同时, 请参考并理解所使用设备的产品个别注意事项,然后方可进行产品的拆卸。 3、重新启动机械•设备时,请采取预防发生意外动作及错误操作的对应措施。
※3) 真空吸盘不适用开始使用 1 年内的保证期限。 真空吸盘是消耗品,保证期为购入后的 1 年之内。 但是,即使在保证期内,若因使用而造成磨损或橡胶材质劣化等情况,都不在产品保证的适用范围内。
※3)
『适合用途的条件』
出口海外时,请务必遵守经济产业省规定的法令(外汇及外国贸易法),手续。
-3No.PS※※-OMH0002CN-D
指示
■操作要求
○选定,使用压力开关时,请严守下述内容。 ●选定(请严守以下有关使用时的安装・配线・使用环境・调整・使用・维护点检的操作内容。)
*产品规格等 ・请不要在有腐蚀性以及引火性的气体,流体上。(ISE70 系列)
请不要使用腐蚀 SUS630・SUS430・SUS304 的气体,流体,或者具有引火性的气体,流体。 压缩空气中不能含有那些化学药品或有机溶剂的合成油,盐份,腐蚀性气体。 如果混入这些物质,可能导致数字式压力开关的破损或作动不良。 具体请在确认完规格后再使用。
■安全注意事项
警 告
■禁止分解・改装(包括印刷电路板的重装)・修理
否则可能会造成人身伤害或机器故障。
6干熄焦用SE70变频器基本知识

6SE70变频器的基本功能设置
2.下载:
6SE70变频器的基本功能设置
四、基本参数设置
6SE70变频器的基本功能设置
6SE70变频器的基本功能设置
6SE70变频器的基本功能设置
五、故障的查询:
对于每一个故障事件可提供的信息包括以下参 数:
参数: r947 故障数字 r949 故障值 r951 故障文本 r952 故障数目 r748 故障时间 如果一个故障信息没有复位,而去再次送电故
6SE70变频器的常用参数介绍
6SE70变频器的常用参数介绍
6SE70变频器的常用参数介绍
6SE70变频器的常用参数介绍
6SE70变频器的常用参数介绍ຫໍສະໝຸດ 6SE70变频器的功能图介绍
自由块
6SE70变频器的功能图介绍
源
6SE70变频器的功能图介绍
源
6SE70变频器的功能图介绍
模拟量
6SE70变频器的功能图介绍
6SE70变频器常用检测工具介绍
UCER,UCES,UCET: 用于检测IGBT的UCE电压,正常时灯灭。当安全停车使能,触发
电路损坏(如P15OK没有),触发片损坏,IGBT损坏(或性能 变差,导通压降增大)时,都会触发UCE报警。另:对于室内 维修常见的A-D尺寸的机器,只对V相的IGBT进行UCE检测,即 只可能UCES灯亮。 UZKN: 检测直流母线电压。 IRN,ISN,ITN: 检测U,V,W三相电流。IRN,ITN为电流互感器测得,ISN为根据其 他两相电流计算得来。VREFU,VREFI: 当测试盒的插线排和PEU上的插槽连接正常时,灯亮。VREFU为 过压报警的参考点。 TWRN: 检测逆变器的温度。
6SE70变频器的常用参数介绍
akei70机说明书

吹瓶机专用控制系统操作手册AO-50/70-TS目录系统特性简介 (3)控制器各部件介绍 (4)控制器操作面板 (4)控制画面切换键 (5)数字及特殊功能键 (5)手动功能键 (6)下位PCC控制器 (7)各操作画面说明 (8)系统启动画面 (8)状态画面 (9)温度画面 (10)打飞边及机头设定画面 (11)移模画面 (12)开合模画面 (13)功能选择设定画面 (14)时间设定画面 (15)输入输出画面 (16)日期密码设定画面 (17)模具参数保存画面 (18)系统电子尺设定画面 (19)吹针画面 (20)温度曲线设定画面 (21)温控参数画面 (22)压力流量线性化画面 (24)机器操作说明 (25)手动操作 (25)温度控制设定 (25)壁厚控制设定 (26)机器复位操作 (33)空循环操作 (33)自动操作 (33)附件 (34)提示和报警原因及处理 (34)硬件接线图 (38)系统特性简介本控制系统的主要功能特色包括:1. 硬件采用欧洲B&R公司可靠,紧凑的X20控制系统。
用户操作界面采用10.4寸TFT真彩人机界面,中英文图形显示,操作直观方便。
2. 硬件系统的模块化设计,可以针对一些特殊用户的要求方便的扩充功能。
3. 功能完善的壁厚控制及直线运动控制。
4. 独特的液压力传动控制技术,用户仅需对开锁模,移模等液压运动轴简单设定一些基本的运动参数,系统自动计算出最佳的运动控制曲线,运动快速平稳,定位精度高,大大缩短了加工循环时间。
5. 智能PID温控技术,用户无需设定烦琐的温控参数,系统自动优化整定,温控精度高,温度变化过程可用曲线记录,且温控区可以任意扩展。
6. 强大的内嵌式网络功能,可将该单机设备方便的连接到生产过程网络,进行生产过程控制(备选)。
7. 方便易用的模具配方管理功能,可储存多达120套工艺配方。
控制器各部件介绍控制器操作面板图1显示面板的技术参数如下:显示器:10.4" (264 mm)TFT 真彩色,亮度200 cd/m2 使用寿命不少于20000小时 使用环境:温度0-50度,相对湿度5%-95%,面板IP65防护D 区C 区 B 区A 区控制画面切换键参见图1的键A区及键B区。
依爱EIN70型气体灭火控制系统安装使用说明书V14.1
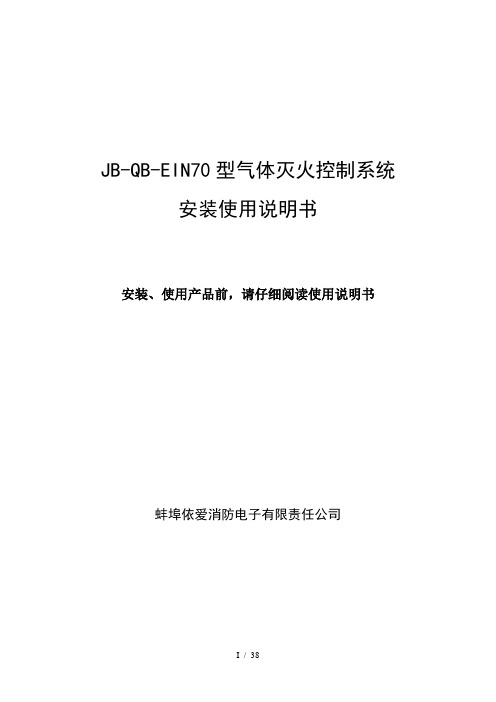
一、JB-QB-EIN70型气体灭火控制器………………………………………………………………………1
5.5编程……………………………………………………………………………………………….18
5.6功能试验………………………………………..………….……………………………………..18
6.维护、保养及故障处理…………………………………………………………………………..…19
6.1维护、保养………………………………..………………………………………………………19
4.1键盘/显示说明..................................................................……………….....……........................6
4.1.1指示灯…...………………………...…………………………………………………………..7
3.1安装…………………………………………………………………….…………….……….……3
3.2接线盘及接线说明………………………………………………………….………………..……4
3.3布线要求.…………….…………….…………….…………….…………….…………….………6
4.操作使用说明........................................................................……..…………………..........................6
Graco XP70多组件涂料喷雾器说明书

2Two-Component Spraying –made Easy and AffordableThe trend for the coatings industry is toward high solids coatings.Formulated with less solvent, these coatings reduce VOCemissions and speed production with faster cure times.The Graco XP70 Plural-Component Sprayer is designed to pump,mix and atomize high-viscosity, materials with superior results.The spray system handles:• E nvironmentally-friendly high solids coatings,with little or no solvent• Hybrid polyurethanes• Epoxies• V ery high solids coatings – up to 100% solids content• M aterials requiring heat (requires optional heaters)• F ast-curing materialsIf you spray several different materials each week, the XP70is the right choice. That’s because you can change the ratioby simply changing one or two pump lowers. Six fixed mixratios are available: 1:1, 1.5:1. 2:1, 2.5:1, 3:1 and 4:1.Applications• Tanks• Pipes• Marine/shipbuilding• Bridges• Wind towers• Railcars• Water towers• Wastewater treatment• Manhole and sewer reconditioning• Secondary containment• Structural steel• Refineries• Roof coatings3Engineered specifically for Two-Component CoatingsThe Graco XP70 Plural-Component Sprayer provides the high-pressure performance you need to spray high-viscosity, high-solids coatings. In addition, the unit is designed to maximize gravity feed, which may eliminate the need for feed pumps, saving you money.Mix Manifold• P rovides simple fluid control for mixing or flushing• A ccurately dispenses A and B fluids to the static mix tube• H andles high-solids coatings with large ports and low pressure drop • C hoose to use mix manifold remotely to reduce solvent and material wasteOutlet Manifold and Valves• Fluid pressure gauges to monitor pump output • Provides automatic overpressure relief • I ncludes circulation back to the supply for pump priming, purging, or relieving outlet pressure• A llows fluid warm-up circulation when optional heaters are usedNXT Air Motor• S tandard anti-icing feature means production won’t stop due to motor icing • M odular design for easier maintenance • R ugged body armor won’t rust or dentMaterial Hoppers• Side-mounted 26 liter (7-gallon)hoppers hold A and B components until it’stime to spray • Made of rugged polyethylene –unaffected by harsh solvents• Optimized for directpump feedCompact Cart-mounted• Designed for easy handling by one person• Can be floor mounted afterremoving wheels • Easy mounting of optionalflush pump and heatersHigh-pressure to handle High-viscosity Coatings• Rated for 500 bar (50 MPa, 7250 psi) to handleviscous materials and long hose lengthsXtreme ® Pump Lowers• Standard Severe Duty coatingon rods and cylinder maximizes wear life• Quick knockdown design and throat seal cartridges provide fast and easy maintenance• Six sizes available to providevarious fixed mix ratios• Easily change one or both lowers to getdesired mix ratio (see pg. 5)Visit and upgrade from hand-mixing today!4Visit Quick Return on your InvestmentYou’ll discover that the Graco XP70 Plural-Component Sprayer pays for itself when you switch from hand-mixing. Here’s how:Reduces material costsWith the Graco XP70, you eliminate waste and save money because you only mix as much material as you need. No more throwing away unused material at the end of the day. No more residue left over in smaller pails or cans. You can buy material in bulk as well.Saves money by using less clean-up solventOnly the parts that come in contact with mixed material must be cleaned. Instead of flushing out an entire pump system that contains mixed material, you only need to flush the static mix tube and hose to the gun. Reduced cleaning time means you save labour costs and increase uptime.Provides consistent material qualityNo more guesswork or human error in measuring means you can improve throughput, cut back on material waste, andreduce rework. Materials are proportioned by precision positive displacement pumps and mixed accurately and on-ratio at the mix manifold.Easy to operateOperators are up and running in just minutes, with a minimum amount of training time. The Graco XP70 runs right out of the box with nothing to set up.Reduces maintenance costsEngineered to proportion with two pumps instead of three, the Graco XP70 cuts preventive maintenance by at least one-third. It reduces cost of ownership because you only rebuild two pumps instead of three. Built with standard components, quick knock-down Xtreme lowers and NXT Air Motors, you use standard spare parts and repair kits that are readily available from Graco’s global network of distributors.5Typical Pay Back in less than 12 monthsCompare XP70 to hand-mixing and see how much you’ll save. XP70 provides a substantial return on investment compared to hand mixing because you throw away less mixed material, and you use less solvent. Visit to calculate an ROI for your application.XP Ratio Selection GuideAverage cost of coating per liter Amount of wasted material per day Average cost of wasted coating per dayTOTAL SAVINGS (assumes 200 working days per year)Material volume in shortened hose (assumes 3/8" hose x 15 m = 1.1 l)Average cost of wasted coating per day (F = E x A)TOTAL SAVINGS (assumes 200 working days per year) Average cost of potlife extender/reducer per literAmount of potlife extender/reducer used per day (assumes 2l solvent per 20 l)Average cost of potlife extender/reducer used per dayTOTAL SAVINGS (assumes 200 working days per year) Average cost of solvent per literMaterial volume of pump, siphon hose, siphon tube(220 cc pump + 1320 cc from siphon hose and tube)Amount of solvent used per day (N = M x 3 flush factor x L)TOTAL SAVINGS (assumes 200 working days per year)12.002.75 l 33.006.6001.10 l 13.202.6404.0016 l 64.0012.8004.001.50 l 18.003.60025.640A B C = AxB D = Cx200E FG = Fx200H I J = Hxl K = Jx200L M NO = Nx200Example is based on spraying 160 l in an 8-hour shift1:176:1Xtreme 85 (L085CO)Xtreme 85 (L085CO)173 6.5 (95)500 (7250) 6.92 (1.83)1.5:191:1Xtreme 85 (L085CO)Xtreme 58 (L058CO)144 5.5 (80)500 (7250) 5.76 (1.52)2:176:1Xtreme 115 (L115CO)Xtreme 58 (L058CO)174 6.5 (95)500 (7250) 6.96 (1.84)2.5:165:1Xtreme 145 (L14ACO)Xtreme 58 (L058CO)203 6.9 (100)448 (6500)8.12 (2.14)3:168:1Xtreme 145 (L14ACO)Xtreme 48 (L048CO)193 6.9 (100)469 (6800)7.72 (2.04)4:173:1Xtreme 145 (L14ACO)Xtreme 36 (L036CO)1816.9 (100)500 (7250)7.24 (1.91)6Technical SpecificationsXP70 Options for Added ProductivityFluid filtrationXP pump outlets ........................................................................................... 30 mesh XTR-7 Spray Gun .......................................................................................... 60 mesh Air inlet filtration ........................................................................................... 40 micron Ambient temperature rangeOperating ........................................................................... 4° to 54°C (40° to 130°F) Storage............................................................................. -1° to 71°C (30° to 160°F)Max fluid temperature ............................................................................. 71°C (160°F) Environmental rating .............................................................................Indoor/Outdoor Hazardous areas ........................................................................................... Ex II 2 G Fluid viscosity range (gravity feed hoppers) ............................ 200-20,000 cps (pourable)Higher viscosities with pump feed ........... Pump feed recommended for mix-at-the-gunapplications to pre-compress fluids Max air pressure supply to the machine .............................. 12 bar (1.2 MPa, 175 psi) Sprayer air consumption (see performance charts in 3A0420) ....... 0.56 m 3/min at 7 bar/liter/min(75 cfm at 100 psi inlet/gpm) DimensionsBare machine ............................................................................ 132 x 152 x 81.6 cm With 26 liter (7 gal) hoppers ........................................................... 132 x 152 x 89 cmWeightBare system ................................................................................................... 192 kg(No heaters, hoppers or junction box)Full system ..................................................................................................... 260 kg(Includes 2 heaters, solvent pump and empty hoppers)Air inlet connection ............................................. 3/4" npsm (f) union in 3/4" npt (f) port Fluid pump inlets (for non-hopper models) ........................................... 1-1/4" npt (m)Fluid gauge manifold “A” and “B” outlets ...................................................1/2" npt (f)Fluid gauge manifold ................................................................................ 1/4" npt (m)(combination pressure relief / circulatioin / prime) outlets back to supplyFluid mix manifold inlets .......................................................... 3/8" npt (m) ball valves Mix manifold material outlet .......................................................................1/2" npt (f)Static mix tube outlet ............................................................................... 3/8" npt (m)Wetted partsHard parts ......................... Nickel or zinc plated carbon steels, stainless steels, carbide Soft parts ................................. PTFE, UHMWPE, nylon, acetal, solvent resistant o-rings Max recommended feed pressure .............................. Less than 15% of outlet pressure Sound pressure ....................................................... 86 dBA at 7 bar (0.7 MPa, 100 psi)Sound power ........................................................... 98 dBA at 7 bar (0.7 MPa, 100 psi)Operation and repair manual (English) ............................................................ 3A0420Merkur ™ Solvent Flush Pump• Q uickly flushes mixed materials from hose and gun• P rovides enough pressure to push good paint out the mix hose with a spray pattern, resulting in less wasted material• M ounts easily to slotted holes provided on XP cart• P rime valve can be used to supply flush solvent for tip cleaning, or to flush a second hose and gun that have been removed from the tee in the mix lineViscon ® Fluid Heaters• R educes coating viscosity so it can be sprayed at lower pressure • P rovides consistent spray temperature, resulting in consistent spray pattern and better thickness control • M ounts easily to slotted holes on XP cart (requires heater mounting kit 262450)• A vailable in standard or hazardous atmosphere designRemote Mount Mix Manifold• M ix manifold on cart is removable and can be located closer to the spray gun to reduce mixedcoatings and the volume of flush solvent required - results in less wasted materials• A and B hoses from the XP cart to the mix manifold don’t need to be flushed and can be sized for less pressure loss over long runs • G reat for materials with very short pot life• U se carriage 262522 to protect mix manifold and valvesXtreme Pump Lowers• C hange one or both lowers for desired mix ratio (see page 5)• X P uses specific Xtreme pump lowers with spring-loaded inlet valves, Tuff stack packings, 30 mesh filters, and no prime valves• O ver pressure rupture protection included on 36 cc, 48 cc and 58 cc sizes• S ix sizes available to provide fixed mix ratios: 1:1, 1.5:1, 2:1, 2.5:1, 3:1, and 4:17Sprayers - All cart-mounted pump packages include material hoses and XTR -7 gun, and use an NXT 6500 Air Motor (N65DN)Pump Lowers - All Xtreme XP pump lowers include built-in filter and Tuff-Stack™ (carbon filled PTFE packings)Supply Processing EquipmentTemperature Controlling EquipmentMixing and AtomizingWater Jacketed Heated Hoses - (Approved for explosive atmospheres) 15.2 m (50 ft) sectionsXtreme-Duty ™ 500 bar (7250 psi) High-Pressure Hoses571100 1:1 Bare sprayer, no cart, no guns, no hose 571101 1:1 Cart-mounted sprayer without hoppers 571102 1:1 Cart-mounted sprayer with hoppers571150 1.5:1 Bare sprayer, no cart, no guns, no hose 571151 1.5:1 Cart-mounted sprayer without hoppers 571152 1.5:1 Cart-mounted sprayer with hoppers 571200 2:1 Bare sprayer, no cart, no guns, no hose 571201 2:1 Cart-mounted sprayer without hoppers 571202 2:1 Cart-mounted sprayer with hoppers 571250 2.5:1 Bare sprayer, no cart, no guns, no hose 571251 2.5:1 Cart-mounted sprayer without hoppers 571252 2.5:1 Cart-mounted sprayer with hoppers 571300 3:1 Bare sprayer, no cart, no guns, no hose 571301 3:1 Cart-mounted sprayer without hoppers 571302 3:1 Cart-mounted sprayer with hoppers 571400 4:1 Bare sprayer, no cart, no guns, no hose 571401 4:1 Cart-mounted sprayer without hoppers 571402 4:1 Cart-mounted sprayer with hoppersL036C0 Xtreme XP 36 lower L048C0 Xtreme XP 48 lower L058C0Xtreme XP 58 lowerL085C0 Xtreme XP 85 lower L115C0 Xtreme XP 115 lower L14AC0Xtreme XP 145 lower245866Heated hose kit (Includes diaphragm pump, fittings, tubes, mounting bracket and reservoir tank.Actual hose assembly and heater must be ordered separately.) Ref. manual 309525.245841 1/4" (6.3 mm), 500 bar (50 MPa, 7250 psi)245843 3/8" (9.5 mm), 500 bar (50 MPa, 7250 psi)245845 1/2" (12.7mm), 500 bar (50 MPa, 7250 psi)248118 Dual hose bundles, 1/2" & 1/2" (12.7 mm) 345 bar (34.5 MPa, 7250 psi)248119 Dual hose bundles, 3/8" & 3/8" (9.5 mm) 345 bar (34.5 MPa, 7250 psi)248120 Dual hose bundles, 1/2" & 3/8" (12.7 mm x 9.5 mm) 345 bar (34.5 MPa, 7250 psi)248121 Dual hose bundles, 3/8" & 1/4" (9.5 mm x 6.3 mm) 345 bar (34.5 MPa, 7250 psi)246078 Scuff Guard, 15.2 m (50 ft) braided polyester mesh. Blue 63 mm nominal diameter 246456 Scuff Guard, 15.2 m (50 ft) polyethylene clear tubing 130 mm diameterH72503 0.9 m (3 ft), 6.3 mm (1/4"), 500 bar (50 MPa, 7250 psi), 1/4" npsm (f) H72506 1.8 m (6 ft), 6.3 mm (1/4"), 500 bar (50 MPa, 7250 psi), 1/4" npsm (f)H72510 3.0 m (10 ft), 6.3 mm (1/4"), 500 bar (50 MPa, 7250 psi), 1/4" npsm (f)H72525 7.6 m (25 ft), 6.3 mm (1/4"), 500 bar (50 MPa, 7250 psi), 1/4" npsm (f)H72550 15.2 m (50 ft), 6.3 mm (1/4"), 500 bar (50 MPa, 7250 psi), 1/4" npsm (f)H7251X 30.5 m (100 ft), 6.3 mm (1/4"), 500 bar (50 MPa, 7250 psi), 1/4" npsm (f)H73803 0.9 m (3 ft), 9.5 mm (3/8"), 500 bar (50 MPa, 7250 psi), 3/8" npsm (f)H738061.8 m (6 ft), 9.5 mm (3/8"), 500 bar (50 MPa, 7250 psi), 3/8" npsm (f)H73810 3.0 m (10 ft), 9.5 mm (3/8"), 500 bar (50 MPa, 7250 psi), 3/8" npsm (f)H73825 7.6 m (25 ft), 9.5 mm (3/8"), 500 bar (50 MPa, 7250 psi), 3/8" npsm (f)H73850 15.2 m (50 ft), 9.5 mm (3/8"), 500 bar (50 MPa, 7250 psi), 3/8" npsm (f)H7381X 30.5 m (100 ft), 9.5 mm (3/8"), 500 bar (50 MPa, 7250 psi), 3/8" npsm (f)H75010 3.0 m (10 ft), 12.7 mm (1/2"), 500 bar (50 MPa, 7250 psi), 1/2" npsm (f)H75025 7.6 m (25 ft), 12.7 mm (1/2"), 500 bar (50 MPa, 7250 psi), 1/2" npsm (f)H75050 15.2 m (50 ft), 12.7 mm (1/2"), 500 bar (50 MPa, 7250 psi), 1/2" npsm (f)H7501X30.5 m (100 ft), 12.7 mm (1/2"), 500 bar (50 MPa, 7250 psi), 1/2" npsm (f)Remote Mix Manifold258989 Mix manifold, no carriage 262522 Carriage only - no mix manifold Static Mixing, 500 bar (50 MPa, 7250 psi)248927 25 pack, disposable, 1/2" (12 mm), 12 element 262478 Static mix housing, 12 mm x 127 mm (1/2" x 5")511352 Static mixer, SST, 9.5 mm x 241 mm (3/8" x 9.5")Spray Guns, 500 bar (50 MPa, 7250 psi)XTR700 XTR-7, round handle, four-finger trigger, no tip XTR701 XTR-7, round handle, four-finger trigger, flat tip XTR702 XTR-7, oval insulated handle, four-finger trigger, HD RAC tip XTR703 XTR-7, oval insulated handle, two-finger trigger, HD RAC tip XTR704 XTR-7, round handle, four-finger trigger, HD RAC tip XTR705 XTR-7, round handle, two-finger trigger, HD RAC tip Hoppers 24F376 Blue for resin side(26 liter (7-gallon) hopper kits with bracket and hardware to mount on an XP cart)24F377 Green for hardener side(26 liter (7-gallon) hopper kits with bracket and hardware to mount on an XP cart)262454 Desiccant dryer kit. Bulkhead fitting and 2-pack of cartridges for one hopper 119974 Replacement 2-pack of desiccant cartridges Pressure Monitoring kitMonitors pressure of two pump lowers and shuts down sprayer if off-pressure condition exists 262940 Kit, pressure monitor, wall power with Light-Tower 262941 Kit, pressure monitor, wall power, no Light-Tower 262942 Kit, pressure monitor, Turbine power with Light-Tower 262943 Kit, pressure monitor, Turbine power, no Light-Tower Miscellaneous 234026 Gun splitter manifold. Allows two spray guns to be individually selected and/or flushed NXT606 DataTrak conversion kit. Can be added to the NXT 6500 Air Motor for totalizer and flow rate data, and to provide runaway protection. Approved for hazardous atmospheres 24F375 Ratio check kit (see manual 3A0421 for details)Supply Pump Kits (see manual 312769 for more selections)256275 T 2 2:1 drum pump with 3/4 x 3.0 m (10 ft) fluid hose, air regulator kit,air hose, fluid strainer, ball valve and pump union256276 M onark 5:1, drum pump with 3/4 x 3.0 m (10 ft) fluid hose, air regulator kit, air hose,fluid strainer, ball valve and pump unionAgitator Kit248824 Twistork with air connection to work with feed pump kits (reference manual 310863)Solvent Flush Kit 262393M erkur 45:1. Mounts to XP cart. Includes air controls, pail siphon, prime valve and 0.9 m (3 ft) hose to mix manifold (reference manual 310863)262450H eater mounting kit. Includes hose and fittings to mount one heater on the XP cart. Two heaters can be mounted on an XP cart.Viscon Fluid HeatersApproved for explosive atmospheres 245848 Hazardous location, 120 VAC single phase, 2300 watts, 19.2 amps 245862 Hazardous location, 200 VAC single phase, 4000 watts, 20 amps 245863 Hazardous location, 240 VAC single phase, 4000 watts, 16.7 amps 246254 Hazardous location, 380 VAC single phase, 4000 watts, 10.5 amps 245864Hazardous location, 480 VAC single phase, 4000 watts, 8.3 ampsNot approved for explosive atmospheres 245867 Non-hazardous location, 120 VAC single phase, 2300 watts, 19.2 amps 245868 Non-hazardous location, 200 VAC single phase, 4000 watts, 20 amps 245869 Non-hazardous location, 240 VAC single phase, 4000 watts, 16.7 amps 246276 Non-hazardous location, 380 VAC single phase, 4000 watts, 10.5 amps 245870Non-hazardous location, 480 VAC single phase, 4000 watts, 8.3 ampsBand Heaters - Not approved for explosive atmospheres 15F028 Heater, drum, 1000 watts, 240V+32 89 770 700。
Fujikura 70R联合式连接手推说明书

Fujikura 70R Fusion Splicer
Accessories Recommended for the 70R
DESCRIPTION Cleavers and Strippers CT-30 Cleaver RS02 Thermal Stripper Fiber Holders (pairs) FH-50-12 FH-50-10 FH-50-8 FH-50-6 FH-50-4 FH-50-2 FH-50-250 (250 μm coated single fiber) FH-50-900 (900 μm jacketed single fiber) FH-60-LT900 (pair) FUSEConnect® Accessories FH-FC-20 (900 µm within 2.0 mm sheathing) (each) FH-FC-30 (900 µm within 3.0 mm sheathing) (pair) FH-FC-900 (900 µm cable) (each) CLAMP-FC-2000 (pair)
70R Fusion Splicer Kit (with cleaver, battery and cord) Includes: BTR-09 Battery, DCC-18 Battery Charge Cord, CT30 Cleaver, RS02 Stripper, ADC-18 AC Adapter, ACC-14 AC Cord, ELCT2-20A Spare Electrodes (pair), FH-50-12 Fiber Holder, USB Cable, Alcohol Dispenser, Screw Driver, Sleeve Loader, Splicer Carrying Strap, Quick Reference Guide, Video Instruction Manual and CC30 Transit Case with Carrying Strap
3500 70M收窄液泵收振速度 监测仪说明书

Part Number 166766-01Rev. C (11/08)3500/70M Recip Impulse/Velocity MonitorBently Nevada™ Asset Condition MonitoringDescriptionThe 3500/70M Recip Impulse Velocity / Monitor is a 4-channel monitor that can be used as part of the reciprocating compressor solutions package for monitoring compressor crankcase and crosshead vibration. The monitoraccepts input from seismic transducers, conditions the signal to derive various vibration measurements, and compares the conditioned signals with user-programmable alarms. Each channel of the 3500/70M can be programmed using the 3500 Rack Configuration Software to perform one of the following functions:• Impulse Acceleration • Recip Acceleration • Recip VelocityNote: The monitor channels are programmed in pairs and perform up to two of these functions at a time. Channels 1 and 2 can perform one function, while Channels 3 and 4 perform another (or the same) function.The primary purposes of the 3500/70M monitor are to provide:1. machinery protection by continuously comparing monitoredparameters against configured alarm set points to drive alarms, and2. essential machine information for both operations and maintenancepersonnel. Each channel, depending on configuration, typically conditions its input signal into various parameters called “static values”. Users can configure Alertsetpoints for each active static value and Danger set points for any two of the active static values.SpecificationsSpecified at 25 °C (77 °F), voltages referenced to monitor common unless specified otherwise. InputsSignalAccepts from 1 to 4 velocity oracceleration transducer signals. InputImpedance10 k Ω (Acceleration Input),>1 MΩ (Velocity Input).SensorCompatibility330500 Velomitor® Piezo-VelocitySensor330525 Velomitor XA Piezo-Velocity Sensor190501 Velomitor CT VelocityTransducer330400 AccelerometerAcceleration Transducer330425 AccelerometerAcceleration TransducerSpecial InhibitContact closure, 5 Vdc @ 390µAtypical.PowerConsumption7.7 watts, typicalSensitivityImpulseAcceleration10 mV/(m/s2) (100 mV/g), oruser-selected 0.51 – 11.72mV/(m/s2) (5 – 115 mV/g).RecipAcceleration10 mV/(m/s2) (100 mV/g), oruser-selected 0.51 – 11.72mV/(m/s2) (5 – 115 mV/g). Recip Velocity3.94 mV/(mm/s) (100 mV/(in/s)), oruser-selected 3.54 – 22.64mV/(mm/s) (90 – 575 mV/(in/s). OutputsFront PanelLEDsOK LEDIndicates the 3500/70M isoperating properly.TX/RX LEDIndicates the 3500/70M iscommunicating with othermodules in the 3500 rack. Bypass LEDIndicates the 3500/70M is inBypass Mode.TransducerPower SupplyVoltage-22 Vdc minimumCurrent40 mA maximum; (15 mAmaximum on startup toguarantee no fold back)OutputImpedance20 Ω typical operating; 1000 Ωtypical under fold back conditions. ProtectionFoldback current 15.4 to 24.9 mA BufferedTransducerOutputs:The front of each monitor has onecoaxial connector for eachchannel.OutputImpedance550 Ω typical.Specifications and Ordering InformationProtectionEach connector is short-circuitprotected.Recorder:+4 to +20 mA proportional tomonitor full-scale. The userselects one static data value fromeach channel to be used for thatchannel’s recorder value. VoltageCompliance+12 Vdc maximum.Load Resistance600 Ω maximumResolution0.3662 µA maximumUpdate rate<100 msec.AccuracyWithin ±0.05 mA,±0.14 mA over temperaturerange.Signal ConditioningImpulseAccelerationAccuracyWithin ± 0.33% of full-scaletypical, ± 1% maximum. Exclusiveof filters.Band start0 to 359°, 1° resolution.Band duration1 to 360°, 1° resolution. FrequencyResponseBias Filter-3 dB at 0.01 Hz, 1-pole, Low-PassNot OK Filter-3 dB at 2400 Hz, 1-pole, Low-PassStatic valuesSmoothing filter, 8-revolutionaverage value.Filter QualityHigh-Pass4-pole (80 dB per decade, 24 dBper octave).Low-Pass4-pole (80 dB per decade, 24 dBper octave).Cornerselection:Peak 3 dbcornerRMS 3 dBcorner High-Pass 3-3000 Hz 10-3000 HzLow-Pass 30-30000 Hz 40-30000 HzRecipAccelerationAccuracyWithin ± 0.33% of full-scaletypical, ± 1% maximum. Exclusiveof filters.FrequencyResponseBias Filter-3 dB at 0.01 Hz, 1-pole, Low-Pass Not OK Filter-3 dB at 2400 Hz, 1-pole, Low-PassPeak staticvalues-3 dB at 0.3 Hz, 1-pole, Low-Pass RMS staticvalues-3 dB at 0.1 Hz, 1-pole, Low-PassSpecifications and Ordering InformationFilter QualityHigh-Pass4-pole (80 dB per decade, 24 dBper octave).Low-Pass4-pole (80 dB per decade, 24 dBper octave).CornerselectionPeak 3 db cornerIntegrate and/or RMS 3 dB corner High-Pass3-3000 Hz10-3000 HzLow-Pass30-30000 Hz40-30000 HzRecip VelocityAccuracyWithin ± 0.33% of full-scaletypical, ± 1% maximum. Exclusiveof filters.VelomitorAdditional accuracy degradationoccurs when full scale signallevels are low:Full Scale 0-0.5: ±3% TypicalFull Scale 0-1.0: ±2% TypicalFull Scale 0-2.0: ±1% Typical FrequencyResponseBias filter-3dB at 0.09 Hz, 1-pole, Low Pass Not OK filter-3 dB at 2400 Hz, 1-pole, LowPassIntegrationfilter-3 db at 0.34 Hz, 1-pole, Low-PassRMS staticvalues-3 dB at 0.1 Hz, 1-pole, Low-Pass Peak staticvalues-3 dB at 0.3 Hz, 1-pole, Low-Pass 1X & 2X VectorFilterConstant Q filter with bandwidth =± 3% running speed (Q=16.7).FilterQualityHigh-Pass4-pole (80 dB per decade, 24 dBper octave).Low-Pass:2-pole (40 dB per decade, 12 dBper octave).Cornerselection:Non-RMS 3dB cornerRMS 3 dB cornerHigh-Pass 3-400 Hz1-400 Hz (CT)10-400 HzLow-Pass 40-5500 Hz 60-5500 Hz AlarmsAlarm Setpoints:Users can set Alert levels for each value measured by the monitor. In addition, users can set Danger set points for any two of the values measured by the monitor. All alarm set points are set using the 3500 Rack Configuration Software. Alarms are adjustable and can normally be set from 0 to 100% of full-scale for each measured value. The exception is when the full-scale range exceeds the range of the transducer. In this case, the software will limite the setpoint to the range of the transducer. Accuracy of alarms is within 0.13% of the desired value.Alarm TimeDelays:Alarm delays can be programmedusing software, and can be set asfollows for all channel types:Specifications and Ordering InformationAlertFrom 1 to 60 seconds in 1 secondintervals.DangerFrom 1 to 60 seconds in 0.5second intervals or 0.1 seconds. Static ValuesStatic values are measurementsused to monitor the machine. TheRecip Impulse / Velocity Monitorreturns static values from one ofthe following channel types: ImpulseAccelerationDirect, Bias Voltage, six (6) user-adjustable crank angle bandswith peak or RMS acceleration inthe band.RecipAccelerationDirect, 1X Amplitude, 2XAmplitude (defined as: RMS orpeak acceleration or velocity) and1X Phase, 2X Phase and BiasVoltage.Recip VelocityDirect, 1X Amplitude, 2XAmplitude (defined as: RMS orpeak velocity or peak-to-peakdisplacement),and 1X Phase, 2XPhase and Bias VoltageNote: Bias Voltage contains no information about the condition of the machinery being monitored but is provided only for monitor system diagnostics.Barrier ParametersThe following parameters applyfor both CSA-NRTL/C andCENELEC approvals.Proximitor®BarrierCircuitParametersVmax (PWR) = 26.80 V(SIG) = 14.05 VImax (PWR) = 112.8 mA(SIG) = 2.82 mARmin (PWR) = 237.6 Ω(SIG) = 4985 ΩChannelParameters(Entity)Vmax = 28.0 VImax = 115.62 mARmin (PWR) = 237.6 Ω(SIG) = 4985 ΩSeismic BarrierCircuitParametersVmax (PWR) = 27.25 VImax (PWR) = 91.8 mARmin (PWR) = 297 ΩChannelParameters(Entity)Vmax = 27.25 VImax = 91.8 mARmin (PWR) = 297 ΩEnvironmental LimitsOperatingTemperatureWith Internal/ExternalTermination I/O Module-30 °C to +65 °C (-22 °F to +150°F)With Internal Barrier I/OModule (InternalTermination):0 °C to +65 °C (32 °F to +150° F) StorageTemperature-40 °C to +85 °C (-40 °F to +185°F).Humidity95%, non-condensing.Specifications and Ordering InformationCE Mark DirectivesEMC Directives:Certificate ofConformity:136669EN50081-2RadiatedEmissionsEN 55011, Class A ConductedEmissionsEN 55011, Class AEN50082-2ElectrostaticDischargeEN 61000-4-2, Criteria B RadiatedSusceptibilityENV 50140, Criteria A ConductedSusceptibilityENV 50141, Criteria A Electrical FastTransientEN 61000-4-4, Criteria B SurgeCapabilityEN 61000-4-5, Criteria B Magnetic FieldEN 61000-4-8, Criteria A Power SupplyDipEN 61000-4-11, Criteria B RadioTelephoneENV 50204, Criteria B CE Mark LowVoltageDirectives:Certificate ofConformity:134036EN 61010-1:Safety Requirements Hazardous Area ApprovalsCSA/NRTL/CApproval Option(01)Class I, Div 2Groups A, B, C, DT4 @ Ta = -30 °C to +65 °C(-22 °F to +150 °F)CertificationNumberCSA 150268-1002151 (LR 26744)Note: When used with Internal Barrier I/OModule, refer to specification sheet141495-01 for approvals information. PhysicalMonitor Module(Main Board)Dimensions(Height x Widthx Depth):241.3 mm x 24.4 mm x 241.8 mm(9.50 in x 0.96 in x 9.52 in). Weight:0.91 kg (2.0 lb.).I/O Modules(non-barrier)Dimensions(Height x Widthx Depth):241.3 mm x 24.4 mm x 99.1 mm(9.50 in x 0.96 in x 3.90 in). Weight:0.20 kg (0.44 lb.).Specifications and Ordering InformationI/O Modules(barrier)Dimensions(Height x Widthx Depth):241.3 mm x 24.4 mm x 163.1 mm(9.50 in x 0.96 in x 6.42 in). Weight:0.46 kg (1.01 lb.).Rack Space RequirementsMonitor Module:1 full-height front slot.I/O Modules:1 full-height rear slot. Ordering ConsiderationsGeneralExternal Termination Blocks cannot be used with Internal Termination I/O Modules.When ordering I/O Modules with External Terminations, the External Termination Blocks and Cables must be ordered separately.The 3500 Internal Barrier specification sheet (part number 141495-01) should be consulted if the Internal Barrier Option is selected.Software / Firmware CompatibilityThe 3500/70M Module requires the following (or later) firmware and software revisions: Software:3500/01ConfigurationSoftwareVersion 3.703500/02 DataAcquisitionSoftwareVersion 2.503500/03OperatorDisplaySoftwareVersion 1.50 System 1T®SoftwareVersion 5.10Firmware:3500/70MFirmwareVersion 2.303500/22M TDIFirmwareVersion 1.30Ordering InformationRecip Impulse/Velocity Monitor3500/70-AXX-BXXA: I/O Option0 1Prox/Velom I/O Module withInternal Terminations0 2Prox/Velom I/O Module withExternal Terminations0 3Internal Barrier, 4accelerometers0 4Internal Barrier, 2accelerometers, 2 Velomitors0 5Internal Barrier, 4 Velomitors B: Agency Approval Option00None01CSA/NRTL/CExternal Termination Blocks128702-01Recorder External TerminationBlock (Euro Style connectors). 128710-01Recorder External TerminationBlock (Terminal Strip connectors). 125808-08Proximitor/Velomitor ExternalTermination Block (Euro Styleconnectors).128015-08Proximitor/Velomitor ExternalTermination Block (Terminal Stripconnectors).Specifications and Ordering InformationCables3500 Transducer (XDCR) Signal to External Termination (ET) Block Cable129525 -AXXXX-BXXA: Cable Length0 0 0 5 5 feet (1.5 metres)0 0 0 77 feet (2.1 metres)0 0 1 010 feet (3 metres)0 0 2 525 feet (7.5 metres)0 0 5 050 feet (15 metres)0 1 0 0100 feet (30.5 metres) B: Assembly Instructions0 1Not Assembled0 2Assembled3500 Recorder Output to External Termination (ET) Block Cable129529-AXXXX-BXXA: Cable Length0 0 0 5 5 feet (1.5 metres)0 0 0 77 feet (2.1 metres)0 0 1 010 feet (3 metres)0 0 2 525 feet (7.5 metres)0 0 5 050 feet (15 metres)0 1 0 0100 feet (30.5 metres) B: Assembly Instructions0 1Not Assembled0 2AssembledSpares176449-093500/70M Impulse/VelocityMonitor.166226-013500/70M Recip Impulse/VelocityMonitor Manual. 135489-01I/O Module with Internal Barriers(Internal Terminations)(4 x Prox/Accel).135489-02I/O Module with Internal Barriers(Internal Terminations)(2 x Prox/Accel + 2 x Velomitor). 135489-03I/O Module with Internal Barriers(Internal Terminations)(4 x Velomitor).140471-01Prox/Velom I/O Module withInternal Terminations.140482-01Prox/Velom I/O Module withExternal Terminations. 005619413500/70M Prox/Velom I/O Moduleten-pin connector shunt. 00580434Internal I/O Module connectorheader, Euro Style, 8 pin. Used onI/O modules 128229-01 and138708-01.00580432Internal I/O Module connectorheader, Euro Style, 10 pin. Usedon I/O modules 128229-01,138708-01.00502133Internal I/O Module connectorheader, Euro Style, 12 pinSpecifications and Ordering InformationSpecifications and Ordering InformationGraphs and Figures1. Status LEDs2. Buffered Transducer Outputs3. Prox/Velom I/O Module, Internal Terminations, 140471-014.Prox/Velom I/O Module, External Terminations, 140482-01Figure 1: Front and rear view of the Recip Impulse / Velocity Monitor1. Barrier I/O module for connecting four Accelerometer sensors. 135489-012. Barrier I/O module for connecting two Accelerometer sensors and two Velomitor® sensors.135489-023. Barrier I/O module for connecting four Velomitor® sensors. 135489-03Figure 2: Barrier I/O Modules for the ImpulseRecip Impulse / Velocity MonitorSpecifications and Ordering InformationCopyright © 2003. Bently Nevada LLC.1631 Bently Parkway South, Minden, Nevada USA 89423Phone: 775.782.3611 Fax: 775.215.2873/bentlyAll rights reserved.Bently Nevada, Proximitor, System 1, and Velomitor are trademarks of General Electric Company.Specifications and Ordering InformationPart Number 166766-01Rev. C (11/08)Page 11 of 11。
A E S 70系 列使用说明2

目录一、前言 (2)二、产品优点 (2)三、AES70 系列全数字交流电子开关主要技术数据 (3)四、选型说明 (4)五、AES70 系列全数字交流电子开关功能一览表 (5)六、操作面板说明 (6)七、参数说明 (6)八、故障代码说明 (10)九、控制电源电路 (11)十、信号输入电路 (11)十一、信号输出电路 (11)十二、故障检测与保护电路 (11)十三、全数字交流电子开关的空载试验 (11)十四、使用注意事项 (12)十五、维护事项 (12)附件:电机专用数字信号处理器(简称DSP)TMS320F240简介 (13)AES70全数字电子开关使用说明一、前言:AES70系列全数字交流电子开关是本公司在原AES2X系列全数字交流电子开关基础上,软、硬件及主体结构全面升级的新型系列产品,其核心技术采用了当今最先进的马达控制专用芯片—美国德克萨斯州仪器公司生产的TMS320F240数字信号处理器,确保运算精确、响应迅速,控制特性优异、可靠性高。
主电路的功率器件采用晶闸管可控硅模块,结构先进、轻巧、合理,方便使用和维护。
AES70系列产品将交流电机的控制、操作、显示、联锁、故障保护集于一身,真正做到了全数字化、无触点。
极大地简化了电路,提高了产品的可靠性,本系列产品可广泛应用于需频繁正、反转,启、制动的交流异步电动机,适用于单机和成组电机的传动。
可全压启动或软启动,是替代模拟式电子开关或交流接触器的理想换代产品。
二、产品优点:1、结构灵活:主要结构为两类:1)抽屉式(提供抽屉柜),以适应不同场合的需要。
2)控制箱式(可壁挂或装于控制柜内)2、外型轻巧:比传统的模拟式电子开关重量减轻了三分之一。
将散热风机安装于抽屉内,取消了传统的风机抽屉,提高了单位面积的带载能力。
3、使用方便:面板按键对系统运行所需参数的设定、修改进行数字设定,数码管显示各设定参数、检测参数、故障信息,使用方便且直观明确。
4、启动灵活:可全压启动或软启动,以适应不同场合、不同负载的需要。
日积电空调制作商品说明书

If Necessary, Get Help
These instructions are all you need for most installation sites and maintenance conditions. If you require help for a special problem, contact our sales/service outlet or your certified dealer for additional instructions.
When Connecting Refrigerant Tubing
• Use the flare method for connecting tubing. • Apply refrigerant lubricant to the matching surfaces of
the flare and union tubes before connecting them, then tighten the nut with a torque wrench for a leak-free connection. • Check carefully for leaks before starting the test run.
Cherry GH-702A 轻型电源工具维护指南说明书

Lightweight Power ToolGH-702AMAINTENANCE MANUAL1224 East Warner Ave, Santa Ana, Ca 92705 Tel: 1-714-545-5511THE GH-702A TOOLTABLE OF CONTENTSDescription (1)Specifications For GH-702A (1)Safety Warnings (2)How To Use The GH-702A (3)Maintenance And Repair (3)Fill And Bleed Instructions (4)Trouble Shooting (4)Overhaul (5)Air Valve (5)Head Sub-Assembly (5)Handle Sub-Assembly (6)Pulling Heads (6)Installing Pulling Heads (7)Cross Section Drawing Of GH-702A (8)Parts List For GH-702A Riveter (9)Exploded View Of GH-702A (10)Declaration Of Conformity ......................................................................................................................................Back Cover DESCRIPTIONThe Cherry GH-702A is a pneumatic-hydraulic tool designedspecifically for the most efficient installation ofcommercial fasteners. Its durable, all metal housing makesthis extremely robust tool ideal for use in rugged shopenvironments. It has many ergonomic features: very lightweight, comfortable fit in the operator's hand and it can beoperated in any position with one hand.SPECIFICATIONS FOR GH-702ACherry Aerospace's policy is one of continuousdevelopment. Specifications shown in this documentmay be subject to change which may be introducedafter publication. For the latest information alwaysconsult Cherry Aerospace.AIR PRESSURE 90 PSI (6.2 bar) Min. / 110 PSI (7.6 bar) Max.STROKE .75 inch (19 mm)PULLING FORCE 1100 Pounds (4.9 kN) @ 90 PSI (6.2 bar)CYCLE TIME Approximately One SecondWEIGHT 3.5 Pounds (1.59 kg)NOISE LEVEL 65 dB (A)VIBRATION less than 2.5 m/s2AIR CONSUMPTION .066 SCF/cycle (1.87 L/cycle)The GH-702A comes equipped with nosepiece 728A9-4, included for setting:N Rivets - 1 /8” diameterQ Rivets - 1 /8” diameterCherrymate® Rivets- 3/16” diameter There is also a spare nosepiece728A9-6 to set:N Rivets -3/16” diameterQ Rivets -3/16” diameter Cherrymate® Rivets - 1 /4” diameterSAFETY WARNINGS∙Operating this tool with a damaged or missing stem deflector, or using the deflector as a handle, may result in severe personal injury. The pin deflector should be rotated until the aperture is facing awayfrom the operator and other persons working in the vicinity.∙Approved eye protection should be worn when operating, repairing, or overhauling this tool.∙Do not use beyond the design intent.∙Do not use substitute components for repair.∙Any modification to the tool, pulling heads, accessories or any component supplied by Cherry Aerospace, or their representatives, shall be the customer's entire responsibility. Cherry Aerospace will be pleased to advise on any proposed modification.∙The tool must be maintained in a safe working condition at all times and examined at regular intervals for damage.∙Before disassembling the tool for repair, refer to the maintenance instructions. All repairs shall be undertaken only by personnel trained in Cherry Aerospace installation tools. Contact Cherry Aerospace with your training requirement.∙Always disconnect the air line from the tool inlet before attempting to service, adjust, fit or remove any accessory.∙Do not operate the tool when it is directed at any person.∙Ensure that the vent holes do not become blocked or covered and that air line hoses are always in good condition.∙Excessive contact with the hydraulic oil should be avoided to minimize the possibility of rashes. Care should be taken to wash thoroughly.∙Operating air pressure should not exceed 110 psi (7.6 bar).∙Do not operate the tool without the pulling head in place.∙Do not operate the tool unless the handle base (25) is fully secured by the retaining rings (26) and (28) and base cover (27).∙All retaining rings, screwed end caps, air fittings, trigger valves and pulling heads should be attached securely and examined at the end of each working shift.∙Do not pull rivet in the air.∙The precautions to be used when using this tool must be explained by the customer to all operators. Any questions regarding the correct operation of the tool and operator safety should be directed to Cherry Aerospace.∙Do not pound on the rear of the tool head to force rivets into holes as this will damage the tool.∙Do not depress the trigger while disconnecting the air bleeder and replacing the cap screw when bleeding the tool.HOW TO USE THE GH-702AAfter selecting the proper pulling head and attaching it securely to the GH-702A, connect the air line to the tool. Insert the rivet stem into the pulling head until the head of the rivet is in contact with the pulling head sleeve. This will ensure full engagement between the jaws and the rivet stem and will prevent slippage.Once the rivet stem is inserted in the pulling head, the rivet must be installed. Insert the rivet into the application and pull the trigger to activate the tool. Upon the release of the trigger, the stem will eject to the rear of the tool. MAINTENANCE AND REPAIRThe GH-702A has been manufactured to give maximum service with minimum care. In order that this may be accomplished, the following recommendations should be followed:1. The hydraulic system should be full of oil and free from air at all times.2. Keep excessive moisture and dirt out of air supply to prevent wear of air valve, air cylinder and air piston.3. Tool should be routinely inspected for oil leaks.Use automatic transmission fluid Type "A" (no substitutes). Cherry Aerospace recommends using ATF, Dexron III oil.DEXRON III OIL SAFETY DATAFIRST AIDSkin: Wash thoroughly with soap and water as soon as possible. Casual contact requires no immediate attention. Ifirritation develops, consult a physician.Ingestion: Seek medical attention immediately. DO NOT INDUCE VOMITING.Eyes: Flush with copious amounts of water. If irritation develops, consult a physician.Inhalation: No significant adverse health effects are expected to occur on short term exposure. Remove from contaminated area.Apply artificial respiration if needed. If unconscious, consult physician.FIRESuitable extinguishing media: CO2, dry powder, foam or water fog. DO NOT use water jets.ENVIRONMENTWaste Disposal: In accordance with local, state and federal regulations.Spillage: Prevent entry into drains, sewers and water courses. Soak up with diatomaceous earth or other inert material. Store in appropriate container for disposal.HANDLINGEye protection required. Protective gloves recommended. Chemically resistant boots and apron recommended. Use in well ventilated area.COMBUSTIBILITYSlightly combustible when heated above flash point. Will release flammable vapor which can burn in open or be explosive inconfined spaces if exposed to source of ignition.STORAGEAvoid storage near open flame or other sources of ignition.PROPERTIESSpecific gravity 0.863Weight per gallon 7.18 lbs.FILL AND BLEED INSTRUCTIONSTo replace a small amount of oil in the tool, remove cap screw (15), attach the Cherry air bleeder (700A77), connect the tool to the air line and cycle several times. This will ensure the removal of any air from the hydraulic system and its replacement with fluid. Should it become necessary to completely refill the tool (such as would be required after the tool has been dismantled and re- assembled), take the following steps:1. Remove head assembly (1) from handle (32) byunscrewing cap screws (50).2. Fill handle assembly (32) with the recommended oil towithin 1/8" (3.175mm) of the top of the handle casting.3. Place head assembly (1) on handle (32), being suregasket (49), and 0-ring (48), are properly in place.Tighten cap screws (50) uniformly to prevent leakagearound gasket.4. Remove cap screw (15) and attach the Cherry airbleeder (700A77). Connect the tool to the air line andcycle a number of times. This will ensure the removal ofany air from its hydraulic system and its replacementwith fluid.TROUBLESHOOTING1. Check the air line for correct pressure at the tool. Itmust be 90 to 110 psi (6.2 to 7.6 bar).2. Check the tool for lack of oil (see Fill and Bleedinstructions).3. Check for oil leakage:∙Oil leaking around the cap screw (15) in the headindicates that the screw is loose or the Stat-O-Seal(14) needs replacing.∙If oil should leak through the by-pass hole at thebase ofthe handle (32) the 0-rings (34) are worn ordamaged.∙Oil leaking from the front of the head (1) indicatesthat 0-rings (2) are worn or damaged.4. Check for excessive air leakage from the air valve:∙If spring (39) is broken or dislodged, air willbleed directly through the bottom of the air valveand the head piston retreats to its full strokewithout returning. See air valve instructions onpage 5.∙If 0-ring (44) on plug (45) is worn or damaged,replace.∙If 0-rings (36) on valve spool (41) are wornor damaged, replace. 5. Check movement of the head piston (4). If it does notmove freely or is slow in operation:∙0-rings (2), (5), (7) and (8) may be damaged andrequire replacement.∙Head piston (4) may be mechanically lockeddue to damaged parts.∙The 0-ring (36) on power piston rod (37)may be damaged; replace.∙Muffler (46) or air filter (42) inside valve spool (41)may be plugged with dirt. Clean them thoroughlywith normal solvent and back-blow with compressedair.∙Hole in metering screw (43) in valve spool (41)may be blocked or damaged. Hole diameter shouldbe .028" (.711 mm). Clear and size or replacevalve spool assembly (40).6. Rivet stem sticks in the pulling head:∙Pulling head components need maintenance.Disassemble the pulling head, clean and replaceworn parts. Re-assemble following instructions onpage 7.∙Spent rivet stems are wedged side by side in thepulling head. Disassemble the pulling head, removestems and re-assemble following the instructions onpage 7.(15)OVERHAULTHE G701/G704KT TOOL KITAIR VALVERemove retaining ring (47) and muffler (46). Insert a valve plug extractor (P1178) into end of valve plug (45) and pull it out. Using the same procedures, pull out valve spool sub-assembly (40).Use needle nose pliers to grasp the end of the spring (39), turn clockwise and pull out to dislodge from groove in handle. With spring removed, valve sleeve (38) can be pulled out using the valve sleeve removal tool (837B700).To re-assemble, reverse the above procedures, being certain that all 0-rings are properly lubricated. To avoid damaging the 0-rings (2), carefully install sleeve (38) with your finger. Gently push and wiggle sleeve to allow 0-rings to slip past inner ports. Spring (39) is best installed using a valve spring installation tool (836B700) to push the large diameter coil into the groove. This requires care as the tool will not operate if the spring is not anchored firmly.HEAD SUB-ASSEMBLYDisconnect the air supply and remove the complete pulling head from the tool before attempting to disassemble the head assembly.Remove the four socket head cap screws (50). Lift head assembly from the handle (32). Remove 0-ring (48) and gasket (49). Empty the oil into a container by pouring from the handle. Dispose of the oil according to environmental regulations. Remove end cap (10). Push against threaded end of head piston (4) and slide it out of head cylinder (1). Be careful not to damage threads or cause burrs on polished head piston rod surface.0-rings (2) and back-up ring (3) can now be removed using a bent hook. 0-ring (8) can be removed in the same manner. Upon re-assembly, be sure to install 0-rings and back-up rings carefully to avoid cutting them. Always lubricate all 0-rings. Just prior to placing the head sub-assembly onto the handle, see Fill and Bleed Instructions. Also make sure to place 0-ring (48) on top of the handle in its groove, and then the gasket (49) over the 0-ring (48).Tighten the four socket head cap screws (50) uniformly to prevent leakage around the gasket. Purge system of air using Cherry air bleeder (700A77) according to Fill & Bleed Instructions.The disassembly and re-assembly proce-dures can be accomplished by following the instructions below and the drawings on pages 8 & 10. Use extreme care during disassembly and re-assembly not to mar, nick or burr any smooth surface that comes in contact with 0-rings. Before installing 0-rings, be sure to apply an 0-ring lubricant. It is recommended that special assembly tools, which can be ordered under part number G7O1/G7O4KT, be used to overhaul this tool. Service kit, G7O2AKS, which contains a complete set of 0-rings, back-up rings, screws, washers and gaskets should be ordered.Not shown, but included: 701A67 Seal Guide, 702862 Power Cylinder Tool, 703A53 Seal Guide, 702A64 Seal Guide.700477Air Bleeder700A460Seal Guide700A61Piston Rod WrenchP1178Valve Plug Extractor700A62Power Cylinder Tool700B65Packing Plug Wrench8375700Valve Sleeve Removal Tool836B700Valve Spring Installation ToolHANDLE SUB-ASSEMBLY∙Disconnect tool from air supply and remove parts (25) through (29).∙Remove the head sub-assembly using the instructions in the head sub-assembly section.∙Place piston rod wrench (700A61) down into the top of the handle (32), into the hex socket in the head of the power piston rod (37). While holding this wrench, remove the locknut (24) using the 7/16" socket in packing plug wrench (700B65).∙Still holding the piston rod wrench, remove the air piston (22) using the packing plug wrench (700B65) by turningcounterclockwise. When air piston (22) is completely freed from the piston rod, tap or push on the piston rod wrench to eject the piston from bottom of handle.∙Slide power piston rod (37) back up to the end of its travel. Using the packing plug wrench (700B65), removepacking plug (19). It may be necessary to hold the handle upside down in a vise while removing the packing plug.∙Power cylinder (33) can be tapped out by lowering power cylinder tool (700A62) down into the top of the handle on to top of cylinder. The 0-rings (16) and backup rings (17) are best removed and replaced by using a thin bent hook.To re-assemble the handle, reverse the above procedure, being certain that all the 0-rings are properly lubricated before installa-tion. Attach the seal guide (700A60) to the piston rod (37) and with a mallet, tap the piston rod through the packing plug (19). When re-assembling a replacement air piston, items (20) through (23), follow the instructions given below:∙Clamp piston rod wrench (700A61) in a vise with the hex shaft pointed up.∙Turn the handle upside down and place the hex end of the power piston rod (37) onto the wrench. Push handle casting down until it stops.∙Assemble 0-ring (20) to air piston (22).∙Place large washer (21) over the threaded end of the power piston rod (37).∙Place the air piston (22) into handle bore. IMPORTANT: Be sure that the radial pattern embossed on the side of air piston is facing downward towards the large washer (21) and the smooth side of the air piston is facing you.∙Place the small washer (23) over the threaded end of the power piston rod (37). Thread the locknut (24) onto the power piston rod (37) and tighten between 50 in.-lb (5.65 N-m) and 59 in.-lb (6.67 N-m).INSTALLING H702 PULLING HEAD ON RIVETER1. Connect tool to air supply and withoutdepressing trigger, place spring (G) over tube (F) as shown and insert as far as possible into head piston (4). 2. Place jaws (E) inside collet (D) and screwthis assembly onto end of head piston (4). Tighten snugly, using wrenches on the flats provided. NOTE: Make sure tapered end of tube (F) is aligned properly in bevel in back end of jaws (E). 3. Thread nose piece (A) completely intosleeve (B) and place this assembly over the collet and jaw assembly. Screw sleeve (B) into end of tool head (1) while depressing trigger and tighten snugly.4. Tighten jam nut (C) securely.5. These pulling heads will give long life ifproperly maintained. This includes keeping the head clean and dry and all the parts securely tightened. The only lubrication required is a little Lubriplate inside the cone of the collet to assure a sliding action against the back of the jaws. 6. In case of damage or wear to pulling headparts, dismantle and replace with parts selected from the list below.N RIVET Q RIVET CherryMate RIVET 728A9-3Z 3/32ALL ——728A9-41/8ALL ALL —728A9-1045/32AAP,BSP, SSP AAA,BSP, SSP —728A9-43/16——ALL 728A9-6AAP, BSPAAP —728A9-61/4——BALM, BSLMB 1702B19C 1671A16D 1702A20E 1 SET 728B4F 1743A8-8Z G1732A8COMMERCIAL FASTENER TYPE PART NUMBER JAM NUT COLLET REF. NO.QTY. REQ.RIVET DIAM.ASEE CHART AT RIGHTJAW SPRINGJAWS (2 PIECE) JAW FOLLOWER SLEEVECROSS SECTION OF GH-702APART LIST FOR THE GH-702A RIVETER ASSEMBLY"Not furnished with riveter. Must be ordered separately if desired.**No substitutions.***These parts can not be ordered separately, but must be ordered as a sub-assembly.All dimensions are in inches.EXPLODED VIEW OF GH-702A 101224 East Warner Ave, Santa Ana, Ca 92705 Tel: 1-714-545-5511 Fax: 1-714-850-6093© 2010 Cherry AerospaceSupplier’s Federal Identification Code: 11815 TM-GH-702ARev.: CDate: 9-01-10CR# 10-0990LOCTITE ® is a registered trademark of Henkel CorporationDEXRON ® is a registered trademark of GM corporation. PARKER ® is a trademark of Parker Hannifin CorporationLUBRRIPLATE ® is a trademark of Fiske Brothers Refining Co.11。
CTEK SWEDEN AB MXTS 70 专业电池充电器说明书.pdf_1719496774.0

CONGRATULATIONSto the purchase of your new professional switch mode battery charger. This charger is included in a series of professional chargers from CTEK SWEDEN AB and represents the latest technology in batterycharging. MXTS 70 is the first charger with multiple adjustable parameters.• THE CHARGER IS DESIGNED FOR CHARG-ING ONLY FOR BATTERIES ACCORDING TO THE TECHNICAL SPECIFICATION. DO NOT USE THE CHARGER FOR ANY OTHER PUR-POSE. ALWAYS FOLLOW BATTERY MANU-FACTURERS RECOMMENDATIONS.• NEVER TRY TO CHARGE NON RECHARGE-ABLE BATTERIES.• CHECK THE CHARGER CABLES PRIOR TO USE. ENSURE THAT NO CRACKS HAVE OCCURRED IN THE CABLES OR IN THE BEND PROTECTION. A CHARGER WITH DAMAGED CORD MUST BE RETURNED TO THE RETAILER. A DAMAGED MAINS CABLE MUST BE REPLACED BY A CTEK REPRESENTATIVE.• NEVER CHARGE A DAMAGED BATTERY.• NEVER CHARGE A FROZEN BATTERY.• NE VE R PLACE THE CHARGE R ON TOP OF THE BATTERY WHEN CHARGING.• ALWAYS PROVIDE FOR PROPE R VE NTILA-TION DURING CHARGING.• AVOID COVERING THE CHARGER.• A BATTE RY BE ING CHARGE D COULD E MIT EXPLOSIVE GASSES. PREVENT SPARKS CLOSE TO THE BATTE RY. WHE N BATTE RIE S ARE RE ACHING THE E ND OF THE IR LIFE CYCLE INTERNAL SPARKS MAY OCCUR.SAFETY• ALL BATTE RIE S FAIL SOONE R OR LATE R. A BATTERY THAT FAILS DURING CHARGING IS NORMALLY TAKEN CARE OF BY THE CHARG-RS ADVANC D CONTROL, BUT SOM RARE ERRORS IN THE BATTERY COULD STILL EXIST. DON’T LEAVE ANY BATTERY DURING CHARGING UNATTENDED FOR A LONGER PERIOD OF TIME.• E NSURE THAT THE CABLING DOE S NOT JAM OR COMES INTO CONTACT WITH HOT SURFACES OR SHARP EDGES.• BATTERY ACID IS CORROSIVE. RINSE IMME-DIATELY WITH WATER IF ACID COMES INTO CONTACT WITH SKIN OR EYES, SEEK IMME-DIATE MEDICAL ADVICE.• ALWAYS CHE CK THAT THE CHARGE R HAS SWITCHED TO STEP 7 BEFORE LEAVING THE CHARGER UNATTENDED AND CONNECTED FOR LONG PE RIODS. IF THE CHARGE R HAS NOT SWITCHE D TO STE P 7 WITHIN 55 HOURS, THIS IS AN INDICATION OF AN E RROR. MANUALLY DISCONNE CT THE CHARGER.• BATTERIES CONSUME WATER DURING USE AND CHARGING. FOR BATTE RIE S WHE RE WATE R CAN BE ADDE D, THE WATE R LE VE L SHOULD BE CHE CKE D RE GULARLY. IF THE WATER LEVEL IS LOW ADD DISTILLED WATER.• THIS APPLIANCE IS NOT DESIGNED FOR USE BY YOUNG CHILDRE N OR PE OPLE WHO CAN-NOT READ OR UNDERSTAND THE MANUAL UNLESS THEY ARE UNDER THE SUPERVISION OF A RESPONSIBLE PERSON TO ENSURE THATTHE Y C AN U SE T HE B ATTE RY C HARGE R S AFE LY. THIS APPLIANCE CAN BE USED BY CHILDREN AGED FROM 8 YEARS AND ABOVE AND PER-SONS WITH REDUCED PHYSICAL, SENSORY OR MENTAL CAPABILITIES OR LACK OF EXPE-RIE NCE AND KNOWLE DGE IF THE Y HAVE BE E N GIVE N SUPE RVISION OR INSTRUC-TION CONCERNING USE OF THE APPLIANCE IN A SAFE WAY AND UNDE RSTAND THE HAZARDS INVOLVED. CHILDREN SHALL NOT PLAY WITH THE APPLIANCE. CLEANING AND USER MAINTENANCE SHALL NOT BE MADE BY CHILDREN WITHOUT SUPERVISION.• CONN E CTION TO TH E MAINS SUPPLY MUST BE IN ACCORDANCE WITH THE NATIONAL REGULATIONS FOR ELECTRICAL INSTALLATIONS.• THE CHARGER MUST ONLY BE CONNECTED TO AN EARTHED SOCKET OUTLET.• THE CHARGER IS DESIGNED FOR INDOOR USE. DO NOT EXPOSE TO RAIN OR SNOW.*OptionalE NQUICK GUIDETo charge, with last used program settingsWARNING!Batteries and electronics will be damaged if 12V batteriesare charged in 24V-setting.the chargerto the batterythe chargerto mains supply*Press START/STOP-button to start chargingPress the START/STOP-button to interrupt charging23*Supply plugs may differ to suit your mains supply.5341–+–+2Some vehicles may have positively earthed batteries • C onnect the blackclamp 3 to the battery´s negative terminal.• C onnect the red clamp 4 to the vehicle chassis remote from the fuel pipe and the battery.Disconnect the cables • D isconnect the red clamp 4 before the black clamp 3.CONNECT THE CABLESIf the battery clamps are incorrectly connected, the reverse polarity protection will ensure that the battery and charger are not damaged.• C onnect the battery cable 1, including the temperature sensor, to the charger.• Connect the mains cable 2 to the charger.• Connect the red clamp 3 to the battery´s positive pole.• C onnect the black clamp 4 to the vehicle chassis remote from the fuel pipe and the battery.• Connect the charger 5 to the mains supply.• Turn on mains switch 6.DISCONNECT THE CABLES• Turn off mains switch 6.• D isconnect the charger from the mains supply 5 before disconnecting the battery.• Disconnect the black clamp 4 before the red clamp 3.6MOUNTINGWhen permanently mounting the charger, mount the charger on a firm surface. Fix the charger with screws in the four holes. Use screws intended for the surface. Allow space around the charger to not interfere with air cooling.READY TO USEThe table shows the estimated time for empty battery to 80% chargeUSB TYPE B CONTACTUsed for downloading of customized charging programs.Contact ************* for information.NOTE: Not to be used for mobile phone charging!FULLY CHARGEDPOWER LAMP ERROR LAMPTEMPERATUR SENSOR LAMPSTART/STOP-BUTTONMODE-BUTTONNORMAL PROGRAMDISPLAY (V)SET-BUTTONDECREASE BUTTONINCREASE BUTTONDISPLAY (h)DISPLAY (A)DISPLAY (Ah & info)SUPPLY PROGRAMAGM PROGRAM Ca/Ca PROGRAM BOOST PROGRAMREADY TO STARTCHARGINGFor best possible charging of your batteries the voltage and current is adjustable. In addition to that temperature compensated charging isselectable. See below how to set the parameters for customized charging.1. Connect the charger cables to the charger(see quickguide)2. Connect the charger to the battery(see quickguide)3. Connect the charger to the mains supplyThe power lamp will indicate that the mains cable is connected to the mains supply. The error lamp will indicate if the battery clamps are incorrectly connected. The reverse polarity protection will ensure that the battery or charger will not be damaged.4. Turn on the mains switch5. Press the MODE-button to select charging program6. Press SET-button to set parameters7. Select voltage•Display (h) will indicate that voltage (U ) is selectable •Display (V) will indicate set voltage •Press +/- to change•Press SET-button to confirm 8. Select current•Display (h) will indicate that current (A ) is selectable •Display (A) will indicate set current •Press +/- to change•Press SET-button to confirm9. Select temperature compensation•Display (h) will indicate that temperature compensation () is selectable •Temperature sensor lamp will indicate activated temperature sensor •Press +/- to change•Press SET-button to confirm 10. Press the START/STOP-button to start charging cycleor press MODE-button to change charging program 11. Follow the 8-step display through the chargingprocessThe battery is ready to start the engine when STEP 4 is lit. The battery is fully charged when STEP 7 is lit.12. Stop charging at any time by pressing the START/STOP-button 13. Press START/STOP-button to start charging cycleE NSUPPLYFor best possible float maintenance charging or voltage supply function for your vehicle the voltage and max current limit are adjustable from the front panel. See below how to set the voltage supply program and it's parameters.1. Connect the charger cables to the charger(see "Cable connection")2. Connect the charger to the battery(see "Cable connection")3. Connect the charger to the mains supplyThe power lamp will indicate that the mains cable is connected to the mains supply. The error lamp will indicate if the battery clamps are incorrectly connected. The reverse polarity protection will ensure that the battery or charger will not be damaged.4. Turn on the mains switch5. Press the MODE-button to select Supply mode6. Press SET-button to set parameters7. Select voltage•Display (h) will indicate that voltage (U ) is selected •Display (V) will indicate set voltage •Press +/- to change•Press SET-button to confirm 8. Select Supply voltage•Display (h) will indicate that Supply voltage (Su ) is selected •Display (V) will indicate Supply voltage level •Press +/- to change•Press SET-button to confirm 9. Select current•Display (h) will indicate that current (A ) is selected •Display (A) will indicate set current •Press +/- to change•Press SET-button to confirm10. Press the START/STOP-button to start Supply mode 11. Supply mode indicationSTEP 7 is lit to indicate that Supply mode is running.12. Stop Supply at any time by pressing the START/STOP-button 13. Press START/STOP-button to resume Supply modeFULLY CHARGEDPOWER LAMPERROR LAMPTEMPERATUR SENSOR LAMPSTART/STOP-BUTTONMODE-BUTTONNORMAL PROGRAMDISPLAY (V)SET-BUTTONDECREASE BUTTONINCREASE BUTTONDISPLAY (h)DISPLAY (A)DISPLAY (Ah & info)SUPPLY PROGRAMAGM PROGRAM Ca/Ca PROGRAM BOOST PROGRAMREADY TO STARTINDICATION LAMPS, DISPLAYS AND ERRORCODESSETTINGS BEFORE START:DISPLAY (V)Indicates voltage setOptions: 12/24 Vo ltsDISPLAY (A)Indicates current setOptions: 70/50/40/30/20/10A in 12V settingOptions: 50/40/30/20/10A in 24V setting70A could only be selected for SUPPLY program.DISPLAY (h)Indicates which parameter to setOptions: U/SU/A//U = Nominal VoltageSU = Supply VoltageA = Current limit= Temperature compensation= Recond time in BOOST programDISPLAY (Ah & info)Displays error codesREAL TIME INDICATION DURING CHARGING: DISPLAY (V)Displays output voltageDISPLAY (A)Displays output currentDISPLAY (h)Alt. 1. Displays total elapsed charging time (minutes/hours)Alt. 2. Displays time elapsed until error occuredDISPLAY (Ah & info)Alt.1. Displays total charge delivered since start (minutes/hours) Alt.2. Displays error codes together with ERROR lamp ERROR CODES:E01REVERSE POLARITYC onnect the charger according to “quickguide”E02OVER VOLTAGEB attery voltage to high for the chosen charging program, checkbattery voltage.E03TIME OUT STEP 1: DESULPHATIONR estart the charger. If charging is still being interrupted the bat-tery is seriously sulphated and may need to be replaced.E04TIME OUT STEP 2: SOFT STARTR estart the charger. If charging is still being interrupted the batterycan not accept charge and may need to be replaced.E05TIME OUT STEP 5: ANALYSER estart the charger. If charging is still being interrupted the bat-tery can not keep charge and may need to be replaced.E06BATTERY OVERHEATEDT he battery is too hot to charge. The battery is damaged andmay need to be replaced.E07LOW BATTERY VOLTAGE IN SUPPLY PROGRAMB attery voltage too low or too large consumers connected. Checkif 12V battery connected in 24V battery setting or disconnectlarge consumers.E08HIGH CURRENT IN SUPPLY PROGRAMC heck if clamps are short circuited or connected reversed polarity. E99OVER VOLTAGE PROTECTIONI f battery voltage is below 17V the ERROR lamp is lit when 24Vsetting has been selected.A lt 1. Press START/STOP button to charge with 12V setting.To set the parameters for customized charging proceed with“CHARGING” step 6 to 9Alt 2. Press INCREASE button to change to 24V setting. PressSTART/STOP button to resume. To set the parameters for custom-ized charging proceed with “CHARGING” step 6 to 9.10-7012/24E01-E99E01INDICATION LAMPS:S TART/STOP LAMPIndicates that charging has not started or has been interrupted.Press START/PAUSE-button to start/resume.P OWER LAMPIndicates that mains supply is connected.E RROR LAMPIndicates that a fault has occurred.Se ERROR CODES for description.Press START/PAUSE-button to clear error and interrupt charging.T EMPERATURE SENSOR LAMPIndicates that the temperature sensor is activated.Voltage is automatically adjusted to optimize charge atambient temperature.8 • ENE NCHARGING PROGRAMSChoose program by pressing the MODE-button.Adjust parameters according to "CHARGING" (6–9). Press START/STOP button to start the selected program.WARNING!Risk for short circuiting the battery cables. Connect charger cablesto the charger before connecting the battery WARNING!Risk for electrical shock if touching positive and negative terminalswhen charging• U sing higher current than recommended may result in batteries not being completely charged.•Using lower current than recommended will prolong the charging time. • T he currents are the maximum recommended current for battery charg-ing. If a parallel consumer is connected then the current setting could be increased with this current value. • S ome battery manufacturer could recommend different values. Please check with the manufacturer if uncertain. The main recommendations are that Gel batteries should be charged in the lower current range, Power AGM’s in the upper range and most other battery types in the mid-range.Model number 1045Rated Voltage AC 220–240VAC, 50–60HzCharging voltageNormal 14.4V/28.8V Max 15.8V/31.6VSupply 13.6V/27.2V, 14.0V/28.0V 14.4V/28.8, 14.8V/29.6VStart voltage 2.0V Output current Max 50A; 70A in supply 12V Current, mains Max 7.2A rms (at full charging current in 24V)Back current drain*<1Ah/month Ripple**<4% of actual DC current Ambient temperature -20°C to +50°C (-4°F to +122°F)Charger type 8 step fully automatic charging cycle Battery types All types of 12V and 24V lead-acid batteries(WET, MF, Ca/Ca, AGM and GEL) Check with your battery supplier for appropriate charge informationBattery capacity 20Ah–1500Ah Dimensions 338x178x80mm (L x W x H) Insulation class IP20Weight 3.3kg, without cables Warrenty 2 years*) Back current drain is the current that drains the battery if the charger is not connected to the mains. CTEK chargers has a very low back current.**) The quality of the charging voltage and charging current is very important. A high current ripple heats up the battery which has an aging effect on the positive electrode. High voltage ripple could harm other equipment that is connected to the battery. CTEK battery chargers produce very clean voltage and current with low ripple.TECHNICAL SPECIFICATIONLIMITED WARRANTYCTEK SWEDEN AB, issues this limited warranty to the original purchaser of this product. This limited warranty is not transferable. The warranty applies to manufacturing faults and material defects for 2 years from the date of purchase. The customer must return the product together with the receipt of purchase to the point of purchase. This warranty is void if the battery charger has been opened, handled carelessly or repaired by anyone other than CTEK SWEDEN AB or its authorised representatives. Thecharger is sealed. Removing or damaging the seal will void the warranty. CTEK SWEDEN AB makes no warranty other than this limited warranty and is not liable for any other costs other than those mentioned above, i.e. no consequential damages. Moreover, CTEK SWEDEN AB is not obligated to any other warranty other than this warranty.SUPPORTCTEK offers a professional customer support: . For latest user manual see .By e-mail: *************, by telephone: +46(0) 225 351 80, by fax +46(0) 225 351 95.CTEK PRODUCTS ARE PROTECTED BYCHARGING PROGRAMSSTEP 1 DESULPHATIONDetects sulphated batteries. Pulsing current and voltage, removes sulfates from the lead plates of the battery restoring the battery capacity.STEP 2 SOFT STARTTests if the battery can accept charge. This step prevents charging a defect battery.STEP 3 BULKCharging with maximum current until approximately 80% battery capacity. STEP 4 ABSORPTIONCharging with declining current to maximize up to 100% battery capacity.STEP 5 ANALYSETests if the battery can hold charge. Batteries that can not hold charge may need to be replaced.STEP 6 RECONDChoose the Ca/Ca program to add the recondition step to the charging program. This step can also be selected separately by choosing the BOOST-program. During the recondition step voltage increases to create controlled gassing in the battery. Gasing mixes the battery acid and gives back energy to the battery. STEP 7 FLOATThis step maintains the battery voltage by providing a constant voltage charge. This step can also be selected separately by choosing the SUPPLY-program and then it is possible to select different voltage settings.STEP 8 PULSEMaintaining the battery at 95–100% capacity. The charger monitors the battery voltage and gives a pulse when necessary to keep the battery fully charged.*) SUPPLY program is not time limited **) F or 12V only, max current is delivered for 30 seconds followed by a 90 second rest time.The 30 second counter starts when current has exceeded 50A. 50A is delivered continuously.20019214B2012–05–30。
hvp-70-manual-chinese

b).保持在吊桿成直線下,將控速器連座鎖於車板下方
車板
控 速 器
鎖裝螺絲釘
吊
桿
鎖裝螺絲釘時,需以螺絲起子全程鎖裝。
3
控 制 箱
c).安裝後示意圖
(4).皮帶護蓋上的調整 :
A.手指保護桿柱的安裝調整 : ( 限 CE 規格的外掛式馬達才有 )
1). 出廠時【手指保護柱】均預裝在 ( B ) 點處 (平車型式轉向)。
8.選針盒的使用與操作 ……………………………………………………………………………… 19
9.端子座 Pin 功能配置圖
(1). HVP-70- 3/4 -BR (T1) …………………………………………………………………………………21 (2). HVP-70- 3/4 -7W ………………………………………………………………………………………22 (3). HVP-70- 3/4 -H1 (H1、H2) ………………………………………………………………………… 23 (4). HVP-70- 4 -66 (V7) ……………………………………………………………………………………24 (5). HVP-70- 4 -46 (T2) ……………………………………………………………………………………25 (6). HVP-70- 4 -70 ………………………………………………………………………………………… 26 (7). HVP-70- 4 -98 ………………………………………………………………………………………… 27 (8). HVP-70- 4-GD …………………………………………………………………………………………28
一般標準尺寸圖 (USA 標準)
鉆 9 mm 孔
216
dsc701和dsc720系列防撞柱的设计和安装手册说明书
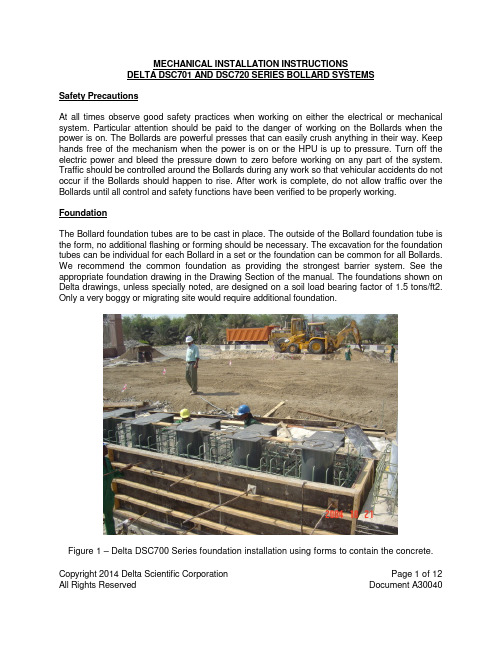
Copyright 2014 Delta Scientific CorporationPage 1 of 12 All Rights Reserved Document A30040 MECHANICAL INSTALLATION INSTRUCTIONSDELTA DSC701 AND DSC720 SERIES BOLLARD SYSTEMSSafety PrecautionsAt all times observe good safety practices when working on either the electrical or mechanical system. Particular attention should be paid to the danger of working on the Bollards when the power is on. The Bollards are powerful presses that can easily crush anything in their way. Keep hands free of the mechanism when the power is on or the HPU is up to pressure. Turn off the electric power and bleed the pressure down to zero before working on any part of the system. Traffic should be controlled around the Bollards during any work so that vehicular accidents do not occur if the Bollards should happen to rise. After work is complete, do not allow traffic over the Bollards until all control and safety functions have been verified to be properly working.FoundationThe Bollard foundation tubes are to be cast in place. The outside of the Bollard foundation tube is the form, no additional flashing or forming should be necessary. The excavation for the foundation tubes can be individual for each Bollard in a set or the foundation can be common for all Bollards. We recommend the common foundation as providing the strongest barrier system. See the appropriate foundation drawing in the Drawing Section of the manual. The foundations shown on Delta drawings, unless specially noted, are designed on a soil load bearing factor of 1.5 tons/ft2. Only a very boggy or migrating site would require additional foundation.Figure 1 – Delta DSC700 Series foundation installation using forms to contain the concrete.Copyright 2014 Delta Scientific CorporationPage 2 of 12 All Rights Reserved Document A30040Figure 2 – Delta DSC700 Series foundation installation in an excavation of an existing roadway. Note that wooden beams bolted to the top plates are used to level and anchor the Bollards priorto the pour. The trench for the hydraulic lines and electrics has not yet been made.Care should be taken to mount the Bollards in an area that is not subject to flooding. Additionally, the roadway should be crowned in the area of the Bollards to prevent standing water from draining into the Bollard foundation tubes.It is not necessary for the Bollards to be level or plumb to operate. If the roadway is not level the Bollards may be placed to match the contour; however, be sure the appearance factor is considered. An installation where the equipment is not level even if it follows the terrain can be distracting.The Bollards can be secured in the foundation by leveling with concrete blocks, held to temporary wooden frames, or if desired, steel straps or rolled shapes can be welded to the foundation tube exteriors to hold a group in alignment during the pour.Environmental ControlDelta Scientific Corporation's vehicle Bollard systems can be used in all geographical areas. Since the early 1980's, Delta Bollards have been successfully installed in locations just south of the Arctic Circle (Oslo and Stockholm), in extremely cold areas of the United States such as Idaho Falls and Grand Forks, and in all the capital cities of Europe. Tropical installations include more than thirty locations within ten degrees latitude of the Equator. In between, installations run from temperate areas to Middle East desert sands.HeatingCold climate installations require the use of heaters to maintain proper oil viscosity and to eliminate the possibility of snow or ice blocking the Bollard mechanism. Depending on the hydraulic power unit size and rating, Delta supplies heaters ranging from 60 to 500 watts @ 120/240 volts for the oil reservoirs. The hydraulic hoses to the Bollards are to be run below the frost line where temperatures are a relatively constant 45 to 55ºF [7 to 13ºC]. If desired, the ducts carrying these hoses can be heat traced at time of installation.The Bollards themselves will require heaters rated at 200 watts. The Bollard heater installation is simple, with the elements contained in an easily accessible pouch in the Bollard foundation tube.Delta strongly recommends that the entire roadway in the immediate vicinity of the Bollards be heat traced. This is to minimize the chance that a vehicle could lose control or traction in front of the Bollards. Also, in many cases, guard and/or inspection personnel will need to work on a vehicle in front of the Bollards. The heat tracing will reduce the personnel dangers of working on snow and ice.Roadways containing Bollards cannot be plowed. The snow plows will shear top plate bolts and damage inspection covers. Only hand clear snow around the Bollards. Snow removing chemicals such as salt should also not be used around the Bollards as the corrosion of the steel components will be greatly accelerated.Drainage provisions in Bollards subject to freezing will also need some consideration. Heat tracing of the drain lines and/or sump well heaters may be needed to help remove the melted snow and ice from the Bollard foundations.CoolingBollard installations in areas where the temperatures are frequently above 100ºF [38ºC] should have the hydraulic power units located in temperature controlled equipment rooms or be equipped with oil coolers. The simplest but least effective method is an air cooled heat exchanger. Very large surface areas are required to cool oil to 160ºF [71ºC] when only 130ºF [55ºC] cooling air is available. A more compact installation can be realized if a water cooled heat exchanger is located in the reservoir tank. Typically, less than one gallon per minute [4 liters per minute] of water at 100ºF [38ºC] or less is required. If the water stream can be returned to a cooling tower or other closed loop system, no waste of water is incurred.Sand and DustBollard locations in sand or dust areas require a few additional precautions. The hydraulic power units should be mounted in equipment rooms that can be pressurized to maintain positive air flow out of the room. This minimizes the accumulation of sand, dust and other abrasive materials on the hydraulic equipment where it could find its way into the oil and sensitive mechanical devices. Filter and fluid changes may be more frequent than at other installations.Bollards in sand swept areas may need to have the foundation tubes cleaned frequently. This isCopyright 2014 Delta Scientific Corporation Page 3 of 12 All Rights Reserved Document A30040usually accomplished by using an industrial type vacuum to sweep out the accumulated debris. Sand accumulation can be minimized by placement of suitable fences or walls around the Bollard area.Good Drainage – The Key to a Successful InstallationPoor drainage of the Bollard system is one of the top reasons for a poorly operating Bollard system. The steel structure of the Bollard deteriorates and the mechanical components fail. Attention to drainage begins before the actual installation. The selection of the drainage method must be made with knowledge of the conditions that exist on the ground. Actual conditions must be known and not guessed.Figure 3 – Delta DSC700 Series Bollards set on a mud slab prior to the concrete pour. The drains in the Bollards’ undersides are readily accessible to plumb to a sump well or storm drain. The white PVC piping visible is the duct work for the Bollards hydraulic lines. These ducts willbe sealed in the concrete of the foundation.Copyright 2014 Delta Scientific Corporation Page 4 of 12 All Rights Reserved Document A30040SitingCare should be taken to mount the Bollards in an area that is not subject to flooding. Do not allow the Bollards to be the drainage for the surrounding roadway. If the Bollards are mounted on a slope, a trench drain should be installed uphill of the Bollards to remove water flowing down the road (see Figure 4).Drain TypesThe best results will be had by providing hard drain lines to a sump well. The sump well can be connected directly to the storm drain or sewer system, or water in the well may be pumped to another location for disposal. The sump well also allows skimmers and other devices to remove tramp oil or contaminants from the water as needed. This type of drainage is mandatory where the water table is within the depth of the Bollard foundation. See Delta drawing 90900 for a suggested sump well design. Drain lines should be sized for the expected rainfall.Figure 4 – Delta DSC700 Series Bollards (with decorative castings) installed in pavers. Note the trench drain grating immediately behind the red colored pavers. This drain takes the bulk of any rainwater that falls in the courtyard behind the Bollards. The Bollard drains will only have tohandle the rainwater in their immediate area.Copyright 2014 Delta Scientific Corporation Page 5 of 12 All Rights Reserved Document A30040Copyright 2014 Delta Scientific CorporationPage 6 of 12 All Rights Reserved Document A30040French drains or other gravel trench drains can only be used in areas of relatively light rainfall and with soils that have an ability to disperse water. Do not expect a French drain to function in clay or soils with an impervious layer of mineralized soil (hardpan) or relatively impervious rock layers underlying shallow soils.Bollard PlacementThe roadway should be crowned in the area of the Bollards to prevent standing water from draining into the Bollard foundation tubes (see Figure 5). It is not necessary for the Bollards to be level or plumb to operate. If the roadway is not level the Bollards may be placed to match the contour; however, be sure the appearance factor is considered. An installation where the equipment is not level even if it follows the terrain can be distracting.Mount the Bollards above the surrounding roadway surface by 1 inch [25mm]. See Figure 5. By doing this, only the water falling in the immediate area of the Bollards can find its way to Bollard drains. (The slight bump is also desirable to help keep vehicle speeds low around the Bollards.) If the Bollards must be installed flush to the roadway for operational considerations, provide trench drains in a perimeter about the Bollards to minimize roadway water from finding its way down into the Bollards (see Figure 4).Figure 5 – Delta DSC700 Series Bollards (with decorative castings) installed in a car park entrance across a sidewalk. The sidewalk forms a berm preventing rainwater in the street fromflooding the Bollards.Copyright 2014 Delta Scientific CorporationPage 7 of 12 All Rights Reserved Document A30040CorrosionVery occasionally a site is both wet and unfriendly, i.e., either highly acid or basic. In these cases, anodic protection is recommended. Delta can review specific job locations and make suitable recommendations where such protection is needed.InterconnectProvisions for electrical and hydraulic (or pneumatic) feed should be made prior to pouring the foundation of the Bollards.Figure 6 – Trenching for the Bollards hydraulic hose ducts (3” [76mm] PVC) and electrical conduit. Note the circular sump well adjacent the closest Bollard, and the small PVC dischargepipe in the trench. Bury these lines below the frost line in cold climates.The access box of the Bollard is provided with a 3.5" IPS pipe sleeve. We recommend that 3"[76mm] PVC pipe be run from the power unit to this sleeve to provide a conduct through which hoses can be pulled. Alternately, rigid steel pipe can be run from the power unit to the Bollards directly buried in the ground. See the Mechanical Theory section of this manual for a discussion of the various ways to interconnect the Bollards with the power unit.The optional limit switch and/or Bollard heater conduits are located on the bottom of the access box. Rigid metallic conduit or equal is to be run to them. Be sure that appropriate fittings are used that will allow wire to be pulled. It is too late to correct this error after the concrete is poured! The heater wires can be run with the limit switches if the insulation voltage rating of the wiring exceeds the highest voltage applied to either of these devices.Concrete Notes and Specifications Note, these are minimum requirements only. You may exceed these requirements with no reduction in the rating of the equipment.1) Contractor shall verify and be responsible for all dimensions and conditions at the job site.2) Foundation concrete may be placed directly into neat excavations, provided the sides ofthe excavation are stable. Where caving occurs, provide shoring. Type and method of shoring shall be at the contractor's option.3) The excavation shall be kept dry at all times. Groundwater, if encountered, shall bepumped from the excavation.4) Concrete shall be laboratory designed, machine mixed, producing 3,000 psi [20,68 Mpa] at28 days.5) Cement shall be tested Portland cement conforming to ASTM C150, Type I or II.6) Aggregates shall conform to ASTM C33. Maximum size of aggregate shall be 1.5 inch [38MM].7) Reinforcing steel shall be deformed bars conforming to ASTM A615, Grade 60 (60,000 psi[413,7 Mpa]).8) Hooks and bends shall conform to ACI standard 318, latest revision. Inside diameter ofhooks and bends shall be at least 6 bar diameters.9) Provide spacer bars, chairs, spreaders, blocks, etc, as required to positively hold the steelin place. All dowels shall be firmly wired in place before concrete is poured.10) Concrete shall be conveyed from the mixer to final deposit by methods that will preventseparation or loss of materials. Troughs, buckets or the like may be used to convey concrete. In no case shall concrete be allowed to free drop more than 5 feet [1,5 M].11) Concrete shall be thoroughly consolidated by suitable means during placement and shallbe thoroughly worked around reinforcement and embedded fixtures and into corners of forms.12) Concrete shall be maintained above 50ºF [10ºC] and in a moist condition for at least 7days after placement. Adequate equipment shall be provided for heating concrete materials and protecting concrete during freezing or near freezing weather.Copyright 2014 Delta Scientific Corporation Page 8 of 12 All Rights Reserved Document A3004013) Where exterior wall face requires shoring and/or forming, the forms shall be substantialand sufficiently tight to prevent leakage. Forms shall not be removed until the concrete is 7 days old.14) Backfilling shall be done by depositing and tamping into place clean sand or pouring leanconcrete. Water jetting shall not be allowed.15) Conduits and pipes of aluminum shall not be embedded in concrete unless effectivelycoated or covered to prevent aluminum/concrete reaction or electrolytic action between aluminum and steel.16) Construction joints not indicated on the drawings shall not be allowed. Where aconstruction joint is to be made, the surface of concrete shall be thoroughly cleaned and all laitance and standing water removed.17) Contractor shall be responsible for the protection of all adjacent areas against damageand shall repair or patch all damaged areas to match existing improvements.18) Contractor shall keep the construction area clean at all times and at completion of workremove all surplus materials, equipment and debris and leave the premises in a clean condition acceptable to the owner or owner's representative.Figure 7 – Bollard installation in a roadway with pavers. Notice the Bollards are centered with jacks. The base of the Bollards will be poured with concrete to set. The jacks will then be removed and the pour continued to the setting level of the pavers.Copyright 2014 Delta Scientific Corporation Page 9 of 12 All Rights Reserved Document A30040Copyright 2014 Delta Scientific CorporationPage 10 of 12 All Rights Reserved Document A30040Figure 8 – Bollard installation in a roadway with pavers. The concrete has been finish pouredand the base for the pavers placed and leveled.Figure 9 – Bollard installation in a roadway with pavers after the final paver placement andcleanup.Figure 10 – Bollard installation using steel beams to aligned the the Bollards prior to theconcrete pour.Figure 11 – Bollard installation placed into a vault preformed prior to the Bollards being received on site. Drainage has been installed, ready for the Bollards to be placed and concrete poured. Copyright 2014 Delta Scientific Corporation Page 11 of 12 All Rights Reserved Document A30040Copyright 2014 Delta Scientific CorporationPage 12 of 12 All Rights Reserved Document A30040Figure 12 – Concrete being poured during Bollard installation. Note that the Bollard tops are protected from sticking concrete by plastic taped to them. Also note the grating for the trench drain placed up slope from the Bollards. This drain will carry away rainwater from a large paved courtyard above the Bollards. The Bollard drains will only have to handle the rainwater that fallsin their immediate vicinity.。