数控冲床编程
自动数控冲床软件编程代码
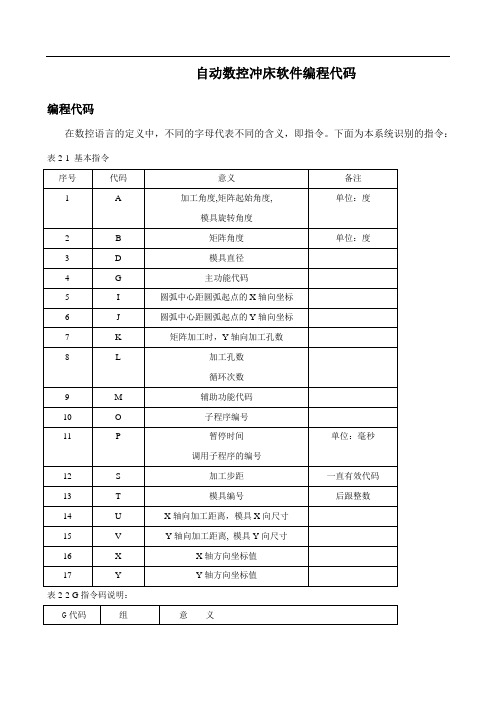
编程代码
在数控语言的定义中,不同的字母代表不同的含义,即指令。下面为本系统识别的指令:
表2-1基本指令
序号
代码
意义
备注
1
A
加工角度,矩阵起始角度,
模具旋转角度
单位:度
2
B
矩阵角度
单位:度
3
D
模具直径
4
G
主功能代码
5
I
圆弧中心距圆弧起点的X轴向坐标
6
J
圆弧中心距圆弧起点的Y轴向坐标
A
矩阵冲压,偶数行比奇数行孔数少一个
G63
A
矩阵冲压,下一行比上一行递减一个
G64
A
矩阵每行的偶数向右移动X轴向步距的一半对齐
G65
A
矩阵每行的偶数向左移动X轴向步距的一半对齐
G78
A
程序块循环开始
G79
A
程序块循环结束
G80
A
圆形区域内矩形栅格冲孔固定循环
G81
A
多层同心圆每层孔数不变的固定循环
G82
拟合曲线无效
%
另起一行
加工板材的尺寸
青岛东和科技股份有限公司(商标:DOOHE),2002年开始研发、设计、生产、销售冲孔机(数控冲床、数控转塔冲床、冲厚板数控冲床、汽车纵梁冲孔数控生产线)、数控送料机、数控折弯机等加工设备,是多年的高新技术企业。
G代码
组
意 义
G00
A
快速定位
G01
A
直线步冲和直线冲孔(孔数由L指定)
G02
A
圆弧步冲和圆弧冲孔(孔数由L指定) 顺时针CW
G03
A
圆弧步冲和圆弧冲孔(孔数由L指定) 逆时针CCW
数控冲床G代码
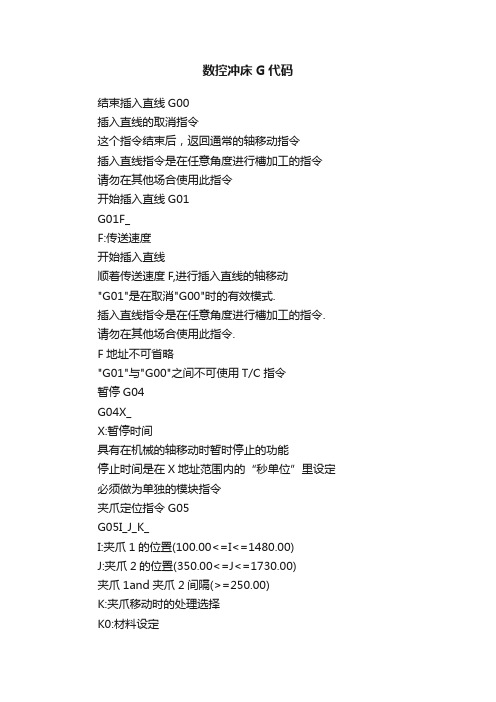
数控冲床G代码结束插入直线G00插入直线的取消指令这个指令结束后,返回通常的轴移动指令插入直线指令是在任意角度进行槽加工的指令请勿在其他场合使用此指令开始插入直线G01G01F_F:传送速度开始插入直线顺着传送速度F,进行插入直线的轴移动"G01"是在取消"G00"时的有效模式.插入直线指令是在任意角度进行槽加工的指令. 请勿在其他场合使用此指令.F地址不可省略"G01"与"G00"之间不可使用T/C指令暂停G04G04X_X:暂停时间具有在机械的轴移动时暂时停止的功能停止时间是在X地址范围内的“秒单位”里设定必须做为单独的模块指令夹爪定位指令G05G05I_J_K_I:夹爪1的位置(100.00<=I<=1480.00)J:夹爪2的位置(350.00<=J<=1730.00)夹爪1and夹爪2间隔(>=250.00)K:夹爪移动时的处理选择K0:材料设定K1:回避死区(同G25)K2:回避死区(同G27)请勿在G5前输入装载指令材料设定(板厚/材质代码)G06G06A_B_A:板厚.B:材质序号0:SPC(钢)1:SUS(不锈钢)2:AL(铝)请在程序开始使用"G06"模块指令性当"G06"没有设定材料,将自动设为板厚. 6.3mm/材质0:SPC(钢)卸载指令G10G10X_X:材料X方向尺寸附加L-UL的材料卸载指令输入材料的X轴方向尺寸取出材料指令G10G10X_Y_Q_M_X:材料X尺寸Y:材料Y尺寸Q:吸附近方法(0:缓冲器/1:电磁/2:缓冲器+电磁/3:夹爪)M:卸载类型前后装置类型在卸载,卸载种类可以松下的情况下指令骨架及宏接合点加工薄板加工指令G10G10X_Y_M_X:材料X尺寸Y:材料Y尺寸M:骨架制品面板积聚指令以下情况可:1)L/UL类型卸载2)卸载类型为"Tsukata"或"Ookuma".G18X_Y_I_J_P_K_P_Q_M_T_C_X:X方向冲切基准点Y:Y方向冲切基准点I:冲孔(路径)最终座标X开始到TK左端为止的距离XJ:TK吸附范围K:冲孔(路径)最终座标Y开始到TK基准位置为止的距离Y P:集积序号Q:吸附近方法(0:缓冲器,1:电磁,2:缓冲器+电磁)M:吸附列取消M代码T:模具序号C:AI角特殊G代码:G18直线距离(LAD):G22自动移位II G25G25X_X:移动距离G25在更换夹子的时候,夹爪往Y轴方向退后一点的位置这个指令在材料端的间隙的情况下有效G25实行时的Y轴偏移由NC自动进行修正必须以单独的模式进行指令BHC G26G26I_J_K_T_C_I:圆半径J:开始角度K:个数T:模具序号C:AI角任意数等分圆周,并加工各个点的模式自动移位1G27X:移动距离进行材料夹爪.必须以单独的模式进行指令冲直线排列孔(LAA)G28G28I_J_K_T_C_I:间隔J:角K:个数T:模具序号C:AI角直线上多个等角度冲孔的加工模式。
数控冲床编程操作程序 AMADA
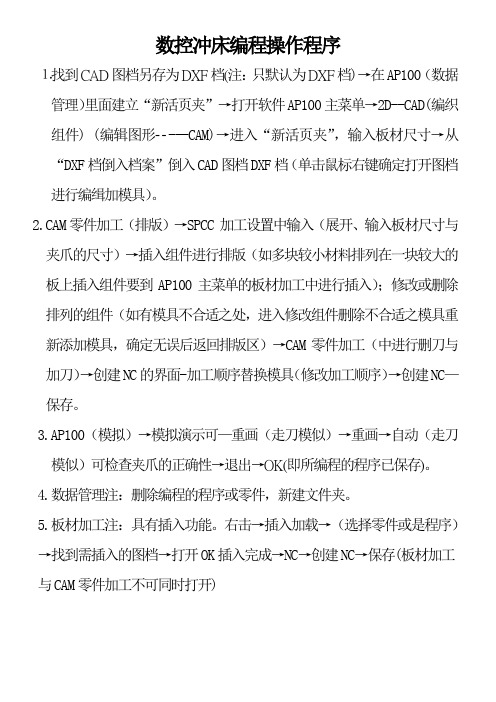
数控冲床编程操作程序
⒈找到CAD图档另存为DXF档(注:只默认为DXF档)→在AP100(数据
管理)里面建立“新活页夹”→打开软件AP100主菜单→2D--CAD(编织组件) (编辑图形---CAM)→进入“新活页夹”,输入板材尺寸→从“DXF档倒入档案”倒入CAD图档DXF档(单击鼠标右键确定打开图档进行编缉加模具)。
2.CAM零件加工(排版)→SPCC 加工设置中输入(展开、输入板材尺寸与夹爪的尺寸)→插入组件进行排版(如多块较小材料排列在一块较大的板上插入组件要到AP100主菜单的板材加工中进行插入);修改或删除排列的组件(如有模具不合适之处,进入修改组件删除不合适之模具重新添加模具,确定无误后返回排版区)→CAM零件加工(中进行删刀与加刀)→创建NC的界面-加工顺序替换模具(修改加工顺序)→创建NC—保存。
3.AP100(模拟)→模拟演示可—重画(走刀模似)→重画→自动(走刀
模似)可检查夹爪的正确性→退出→OK(即所编程的程序已保存)。
4.数据管理注:删除编程的程序或零件,新建文件夹。
5.板材加工注:具有插入功能。
右击→插入加载→(选择零件或是程序)→找到需插入的图档→打开OK插入完成→NC→创建NC→保存(板材加工与CAM零件加工不可同时打开)。
通快数控冲床编程手册

完整文件/NC 编程
4
注释
注意:在第 2 点内,首先说明数据的全部形式(特征说 明程序块),然后它们在第 4 点中列出。(特征数据块)。 几个表程序块可以一个接一个列出。特征文件的结尾 应由一明显结束码来标明: 例:END_SHEET_LOAD
注意:字符“ LF ”不需写上去,它换行时自动加上。
程序块中各字的次序是由编程表来定的。为了使块的 安排更清楚,块中字和字之间可以放上空格。
N200 G01 X320.5 Y32 F12000 LF
块号
字
块结尾
程序字 单个指令称为字。
一个字由地址字母和一数字符顺序组成,地址(例如:X, Y, G, M 等)说明资料意义或存储地点。数目字符顺序 说出存储内容。
,,’min’,Z
MM,AT,1 160, 1,1,,‘ Comment’
,,”,T
MM,AT,1 170, 1,1,,‘ Flag automated’
,,’Bool’,Z
MM,AT,1 180, 1,1,,‘ Flag ToPsxxx-Program’
,,’Bool’,Z
C
ZA,DA,1
DA,‘TC2000’,1,’Bo Type3’,1,’Trumpf’,’1997,’USER’,
3.3 块的选择性压制
定义
不必在每次程序运行时执行的程序块可以除去。 应除去的程序块在块号前加以标扦 “ / ”(斜杠)。 几个程序块可以连续除去。除去的程序块中的指令 就不执行,程序继续走到下一(未除去的)程序块。
数控冲床编程手册(PDF 113页)
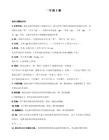
确认使用模具 模具位置编号
请确认加工所必要的模具、的规格而不同。 当大直径模具占用的位置不够时,在运行中途换模不如采用步冲、补充冲切加工等方法 会更有效率。 位置分配图,请参考《模具手册》的《模具位置排列》。
决定加工顺序
在考虑缩短加工时间及保持精度的同时,请决定加工位置的顺序。顺序决定后,在图纸上 编号分色,会变得很清楚。 备 注
5
决定工件夹钳位置
●各工件夹钳间隔,请尽量大。 ●请确认死点。 (请参考第 4 章《运行》之《中断运行和重新启动》之《过载检知功能为“ON”时》) ● 当使用成形或变形了的材料时,在调位时,请确认工件夹钳是否真能再次夹好工件(确 认工件夹钳夹得是否牢靠)。 备 注
●在编程时,为了防止工件夹钳进入死点,请使用如下方法。 ·将整个加工形状旋转 180°夹住相反的一端。 ·变更工件夹钳的位置(间隔)。 ·变更模具的转塔位置。 ·使用重定位功能。 ·设夹钳费。
5 5 5 10 11 11 11 16 17 17 18 18 19 20 21 21 22 23 24 25 25 26 27 28 28 29 31 34 35 36 39 41
直线冲切 “K”的扩张
G67:矩形 G68:步冲圆弧
2
G69:步冲-线 G78:冲切-圆弧 G79:冲切-线 G93:坐标偏置-1 G94:坐标偏置-2 辅助功能 M00:程序停止 M01:任选功能停止 M08:冲切结束延迟开始 M09:冲切结束延迟结束 M80:工件导向器“开”(可选) M81:工件导向器“闭”(可选) M690:气吹开始(可选) M691:气吹取消(可选) M692:冲切上升开始 M693:冲切上升取消 M681~683:冲切速度 M686:冲切速度取消 M120:软方式 M121:软方式取消 冲切模式读出功能 M13:冲切模式取消 M500、M501:冲切模式 M696:NEX模具指令 M697:NEX模具指令取消 M12:步冲模式 M510~559,800~999:成形模式 M560~569:刻印模式 M502~505,570~575:半冲切模式 M506~509:剪切模式 重定位功能 G27:重定位Ⅰ G25:重定位Ⅱ 加工模式存储,读出功能 A、B代码:加工模式存储,读出功能
数控冲床编程教程
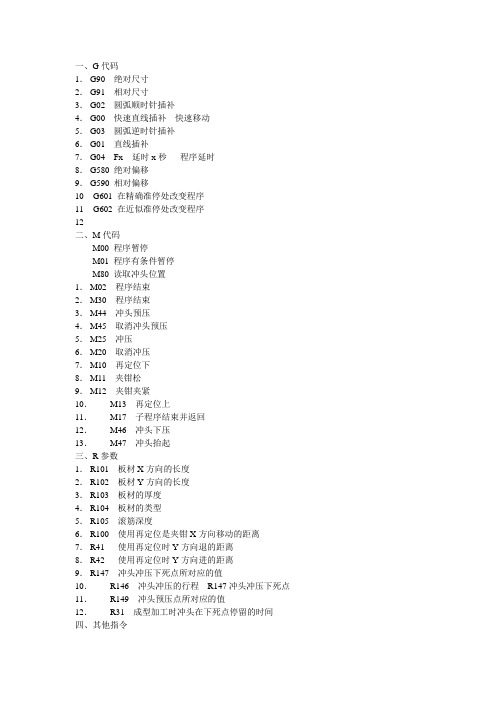
一、G代码1.G90 绝对尺寸2.G91 相对尺寸3.G02 圆弧顺时针插补4.G00 快速直线插补快速移动5.G03 圆弧逆时针插补6.G01 直线插补7.G04 Fx 延时x秒程序延时8.G580 绝对偏移9.G590 相对偏移10G601 在精确准停处改变程序11G602 在近似准停处改变程序12二、M代码M00 程序暂停M01 程序有条件暂停M80 读取冲头位置1.M02 程序结束2.M30 程序结束3.M44 冲头预压4.M45 取消冲头预压5.M25 冲压6.M20 取消冲压7.M10 再定位下8.M11 夹钳松9.M12 夹钳夹紧10.M13 再定位上11.M17 子程序结束并返回12.M46 冲头下压13.M47 冲头抬起三、R参数1.R101 板材X方向的长度2.R102 板材Y方向的长度3.R103 板材的厚度4.R104 板材的类型5.R105 滚筋深度6.R100 使用再定位是夹钳X方向移动的距离7.R41 使用再定位时Y方向退的距离8.R42 使用再定位时Y方向进的距离9.R147 冲头冲压下死点所对应的值10.R146 冲头冲压的行程R147冲头冲压下死点11.R149 冲头预压点所对应的值12.R31 成型加工时冲头在下死点停留的时间四、其他指令1.F60000 进给速率为每分钟60米2.N 后面跟的是程序段序号3.TOOL 该指令后面跟的是所选用的工位号4.LP 普通冲压所调用的子程序5.LP1 成型冲压所调用的子程序6.LF 滚筋所调用的子程序7.L99 回参考点子程序8.L100 再定位子程序9.LT1(301)1(301)号旋转工位角度补偿子程序10.LT14(314)14(314)号旋转工位角度补偿子程序11.LACC 轴加速度计算子程序12.SPP= 后面所跟的为相邻两次冲压的步距13.SPP=0 取消步距14.GOTOF 向前跳转15.GOTOB 向后跳转五、典型程序N10 F75000 进给速率为每分钟75米N20 R103=1 板厚1毫米N30 LP 普通冲压子程序N40 BB: 程序段名称N50 G90 G01 X1000 Y1000 TOOL1 直线插补到绝对位置(1000,1000)并调用1号工位N60 LT1 1号旋转工位角度补偿子程序N70 X1000 Y1000 C90 M44 M25 1号工位旋转90度预压、冲压N80 G91 X-500 SPP=50 X方向坐标从1000开始每隔50冲压一次总行程为500N90 Y-50 Y方向坐标向负方向减少50冲压一次N100 SPP=0 取消步距N120 M20 取消冲压N130 M45 取消预压N140 G90 G01 X800 Y800 TOOL8 M44 M25 直线插补到绝对位置(800,800)换8号工位预压、冲压N170 M45 取消预压N180 M20 取消冲压N190 G90 G01 X150 Y200 TOOL14 直线插补到绝对位置(150,200)并换14号旋转工位N200 LT14 调用14号旋转工位角度补偿计算子程序N210 X150 Y200 C45 M44 M25 用14号旋转工位45度方向在(150,200)的位置预压、冲压N320 M45 取消预压N330 M20 取消冲压N1580 G91 C360 旋转工位在原有的角度基础上逆时针旋转360度N1590 G4 F1 等待1秒N1600 G91 C-360 旋转工位在原有的角度基础上顺时针旋转360度N1910 GOTOB BB 向后跳转到以BB为程序段名的程序段上N1920 M02 程序结束。
数控冲床编程
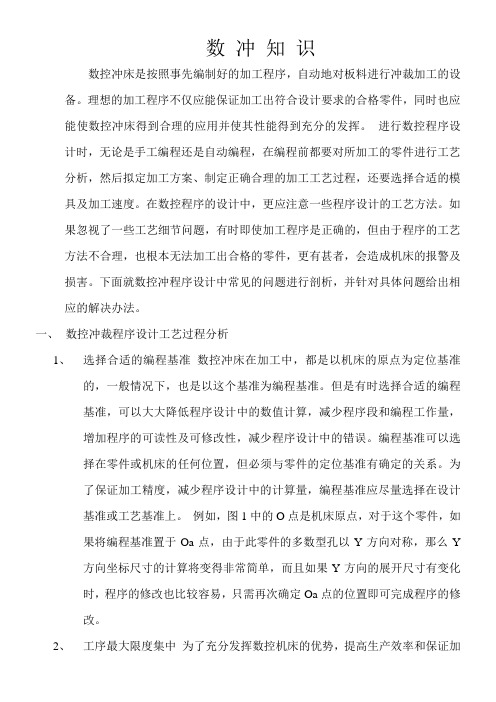
数冲知识数控冲床是按照事先编制好的加工程序,自动地对板料进行冲裁加工的设备。
理想的加工程序不仅应能保证加工出符合设计要求的合格零件,同时也应能使数控冲床得到合理的应用并使其性能得到充分的发挥。
进行数控程序设计时,无论是手工编程还是自动编程,在编程前都要对所加工的零件进行工艺分析,然后拟定加工方案、制定正确合理的加工工艺过程,还要选择合适的模具及加工速度。
在数控程序的设计中,更应注意一些程序设计的工艺方法。
如果忽视了一些工艺细节问题,有时即使加工程序是正确的,但由于程序的工艺方法不合理,也根本无法加工出合格的零件,更有甚者,会造成机床的报警及损害。
下面就数控冲程序设计中常见的问题进行剖析,并针对具体问题给出相应的解决办法。
一、数控冲裁程序设计工艺过程分析1、选择合适的编程基准数控冲床在加工中,都是以机床的原点为定位基准的,一般情况下,也是以这个基准为编程基准。
但是有时选择合适的编程基准,可以大大降低程序设计中的数值计算,减少程序段和编程工作量,增加程序的可读性及可修改性,减少程序设计中的错误。
编程基准可以选择在零件或机床的任何位置,但必须与零件的定位基准有确定的关系。
为了保证加工精度,减少程序设计中的计算量,编程基准应尽量选择在设计基准或工艺基准上。
例如,图1中的O点是机床原点,对于这个零件,如果将编程基准置于Oa点,由于此零件的多数型孔以Y方向对称,那么Y方向坐标尺寸的计算将变得非常简单,而且如果Y方向的展开尺寸有变化时,程序的修改也比较容易,只需再次确定Oa点的位置即可完成程序的修改。
2、工序最大限度集中为了充分发挥数控机床的优势,提高生产效率和保证加工质量,在数控冲床加工编程中应遵循工序最大限度集中的原则,即零件在一次装夹中,力求完成本台数控机床所能加工的全部型孔及外形的加工,防止出现重复定位误差。
对于有些必须重复定位的零件,也应充分考虑重复定位的方法,而且在出现重复定位的情况下,也应使有相关尺寸的孔尽量在一次加工定位中能够完成,如图1中8-Ф6.0及方孔(120mm×80mm)等。
机械制造专业赛课数控冲床操作与编程
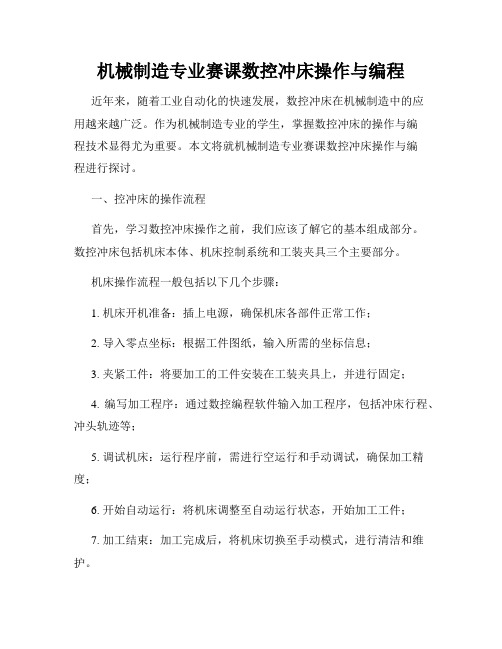
机械制造专业赛课数控冲床操作与编程近年来,随着工业自动化的快速发展,数控冲床在机械制造中的应用越来越广泛。
作为机械制造专业的学生,掌握数控冲床的操作与编程技术显得尤为重要。
本文将就机械制造专业赛课数控冲床操作与编程进行探讨。
一、控冲床的操作流程首先,学习数控冲床操作之前,我们应该了解它的基本组成部分。
数控冲床包括机床本体、机床控制系统和工装夹具三个主要部分。
机床操作流程一般包括以下几个步骤:1. 机床开机准备:插上电源,确保机床各部件正常工作;2. 导入零点坐标:根据工件图纸,输入所需的坐标信息;3. 夹紧工件:将要加工的工件安装在工装夹具上,并进行固定;4. 编写加工程序:通过数控编程软件输入加工程序,包括冲床行程、冲头轨迹等;5. 调试机床:运行程序前,需进行空运行和手动调试,确保加工精度;6. 开始自动运行:将机床调整至自动运行状态,开始加工工件;7. 加工结束:加工完成后,将机床切换至手动模式,进行清洁和维护。
二、数控冲床编程技术数控冲床编程是制定加工工件路径和指令的过程。
良好的编程能力对于高效、精确的加工非常关键。
以下是数控冲床编程技术的几个方面:1. 零点坐标系的确定:零点坐标系是决定工件加工位置的基准。
在编程时,需要根据工件图纸确定坐标系的原点和方向。
2. 加工路径规划:根据工件形状和加工顺序,规划冲头路径。
要注意路径的合理性和避免冲突。
3. 周期时间控制:通过编程设定冲床的进给速度、冲击频率等参数,控制工件的加工速度和质量。
4. 刀具选择:根据不同材料和工件形状,合理选择刀具类型和规格。
5. 编程调试:编写完程序后,应进行测试和调试,确保程序的正确性和可靠性。
三、数控冲床操作与编程的注意事项1. 安全第一:在操作数控冲床时,要时刻关注安全问题。
遵守相关操作规程和安全操作规范,注意个人防护。
2. 学习软件技术:数控冲床编程需要应用专业的软件,因此需要学习掌握相关软件的使用技能。
在编程前,要对软件进行充分了解。
第七章数控冲床编程
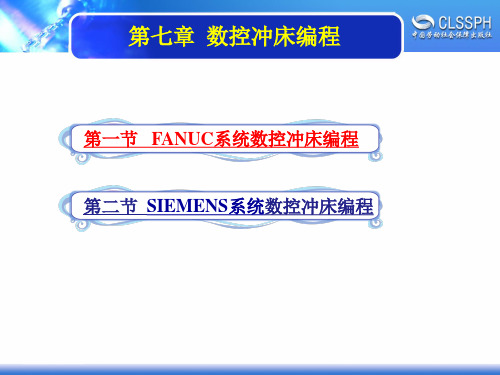
冲制任意方向长方形槽
第七章 数控冲床编程
7.圆弧形槽的冲制
指令格式:G68 I__J__K__P__Q__。各参数含义见图。 其中,I—圆弧半径R,取正值。
J—最初冲压点X轴所成角度,逆时针为正,顺时针为负。 K—圆弧形槽的圆心角,正值沿逆时针方向冲切,负值沿 顺时针方向冲切。 P—冲模直径,取正值沿圆弧外侧冲切,取负值沿圆弧内 侧冲切。若为0,则冲模中心落在指定的半径为I的圆弧上进行
第七章 数控冲床编程
4.圆弧上等距孔的循环
以当前位置或G72指定的点为圆心,在半径为I的圆弧上, 以与X轴成角度J的点为冲压起始点,冲制K个角度间距为P的孔。 指令格式:G29 I J P K T××× I:圆弧半径,为正数。 J:冲压起始点的角度,逆时针方向为正,顺时针方向为负。 P:角度间距,为正值时按逆时针方向进行,为负值时按顺 时针方向进行。 K:冲孔个数。
TANG(FAchse,LAchse1,LAchse2,Koppel,KS,Opt) ; 切 向 耦 合 的定义 TANGON(FAchse,Winkel, Dist, Winkeltol);接通切向控制 TANGOF(FAchse) ; 关闭切向控制 TLIFT(FAchse); 在轮廓拐角处插入中间程序段 TANGDEL(FAchse); 删除切向耦合
J:角度,逆时针方向为正,顺时针方向为负。
P:冲模长度(直线方向的长度)。 Q:冲模宽度(与直线成90º 方向的宽度)。
P和Q的符号必须相同。P=Q时可省略Q。
第七章 数控冲床编程
如图所示长方形槽的冲压加工指令为:
G72 G90 X350.0Y210.0;
G66 1120.OJ45.0P30.OQ20.OT210;
K个将圆周等分的孔。
数控冲床G代码

数控冲床G代码数控冲床是一种高精度、高效率的加工设备,它可以用于制造各种形状的零部件。
数控冲床的加工过程需要使用数控编程语言,其中最重要的就是G代码。
本文将着重介绍数控冲床G代码的概念、语法规则及其使用方法。
一、数控冲床G代码的概念G代码是数控编程语言中用于控制加工轴的指令代码,它是数控冲床加工过程中不可或缺的一部分。
数控冲床G代码通过程序控制工具刀具在运动过程中沿着特定的路径、速度、切削方式等参数加工工件的过程。
数控冲床G代码是一种类似于机器语言的指令代码,它通过特定的语法规则进行编写,最终生成数控程序并发送给数控冲床进行加工操作。
常见的数控冲床G代码有G00、G01、G02、G03、G04、G28等。
二、数控冲床G代码的语法规则1.代码组成数控冲床G代码由字母G和数字组成,其中,字母G用于定义动作或功能,数字表示该动作或功能的参数。
例如,G01表示线性插补,G02表示圆弧插补,G28表示回零操作。
2.代码格式数控冲床G代码的格式一般为:“G代码编号+参数值”,其中,“+”表示连接符号,参数值可以是整数或小数,例如,“G01 X100 Y50”表示进行线性插补,X轴坐标为100,Y轴坐标为50。
3.坐标系坐标系是数控冲床加工过程中非常重要的概念,通常有绝对坐标系和相对坐标系两种。
绝对坐标系表示的是工件相对于床台的绝对位置,在加工过程中任何时刻不会发生变化;相对坐标系表示的是工件相对于上一次命令的位置的差值。
4.圆弧插补数控冲床加工过程中,经常需要进行圆弧插补操作,其代码格式为:“G02/G03 X Y I J”,其中,G02表示顺时针方向插补,G03表示逆时针方向插补;X、Y分别表示终点坐标;I、J表示圆弧的圆心偏移量。
5.多重指令在一个程序中,可以包含多个G代码指令,每个指令之间用“;”隔开,例如:“G01 X100 Y50;G02 X120 Y70 I10 J10”。
数控冲床根据程序的先后顺序一步一步地进行加工操作,按照程序中的G代码进行加工运动。
数控冲床编程指导书
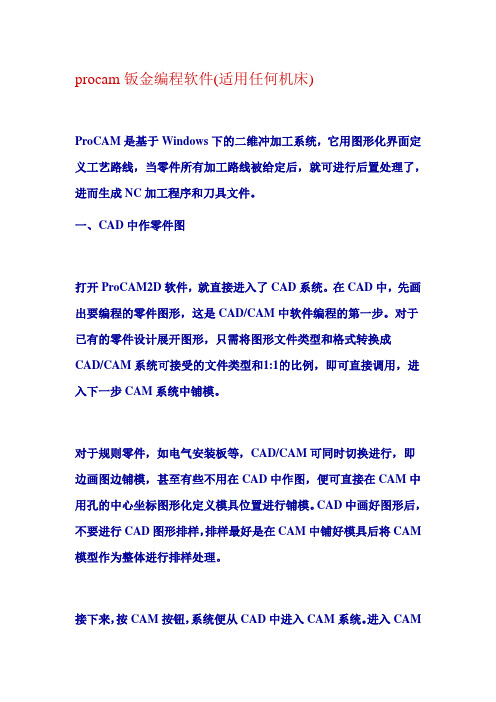
procam钣金编程软件(适用任何机床)ProCAM是基于Windows下的二维冲加工系统,它用图形化界面定义工艺路线,当零件所有加工路线被给定后,就可进行后置处理了,进而生成NC加工程序和刀具文件。
一、CAD中作零件图打开ProCAM2D软件,就直接进入了CAD系统。
在CAD中,先画出要编程的零件图形,这是CAD/CAM中软件编程的第一步。
对于已有的零件设计展开图形,只需将图形文件类型和格式转换成CAD/CAM系统可接受的文件类型和1:1的比例,即可直接调用,进入下一步CAM系统中铺模。
对于规则零件,如电气安装板等,CAD/CAM可同时切换进行,即边画图边铺模,甚至有些不用在CAD中作图,便可直接在CAM中用孔的中心坐标图形化定义模具位置进行铺模。
CAD中画好图形后,不要进行CAD图形排样,排样最好是在CAM中铺好模具后将CAM 模型作为整体进行排样处理。
接下来,按CAM按钮,系统便从CAD中进入CAM系统。
进入CAM时,需要根据实际使用的数控机床,选择后处理器(或称控制系统),这一点至关重要,不能选错。
二、CAM中铺模、排样这一步,是CAD/CAM编程过程中的重点。
数控冲编程,关键在于铺模,即选择适当的模具,图形化地确定适当的冲裁工艺路线。
铺模有手动铺模、自动铺模及手动和自动相结合铺模三种方式,也就是通常所说的手动编程、自动编程和半自动编程。
铺模之前,我们首先根据零件的尺寸精度、规格大小及铗钳位置等来确定,是冲裁零件的整个内外轮廓,还是只冲部分内外轮廓,或不冲外轮廓。
熟练后,这一点很快就可以确定了。
其次,建立模具库Tool Library,将常用的模具及其装载方式设置成标准模具文件Tool Files (如Punch Tools转塔模具清单文件)并保存起来,在实际工作中可省去重复定义常用模具的步骤。
如以处理器名称附上*.ptf 后缀保存模具文件,进入CAM系统打开相应的后处理控制系统时,该标准模具库自动打开,即可直接调用模具。
数控冲床程序操作

数控冲床程序操作数控冲床是一种通过计算机控制的自动化设备,用于冲压加工。
通过编写程序可以实现复杂的冲压操作。
下面是数控冲床程序操作的流程:1.确定冲床加工内容:根据产品设计图纸,确定所需加工的零件数量、形状、尺寸以及材料要求等。
2.编写程序:使用数控编程软件,将产品的加工要求翻译成机床能够识别和执行的指令。
数控冲床的程序一般采用G代码和M代码组成。
a.G代码:用于指定机床的运动路径和加工轨迹。
常用的G代码包括G00(快速定位)、G01(线性插补)、G02(圆弧插补)、G03(圆弧插补,逆时针方向)等。
编写程序时需要根据零件几何形状和加工要求选择合适的G代码指令。
b.M代码:用于控制机床的辅助功能和行程。
常用的M代码包括M03(主轴正转)、M04(主轴反转)、M05(主轴停止)、M08(冷却液开启)、M09(冷却液关闭)等。
编写程序时需要根据加工要求选择合适的M代码指令。
3.连接计算机和冲床:将编写好的程序通过通信线缆连接到数控冲床的控制系统。
确保连接稳定可靠,并进行相应的软硬件设置。
4.调试程序:在连接好的环境下,通过试切试冲等操作,对程序进行调试和优化。
检查和调整数控冲床的各项参数,确保加工过程中的精度和稳定性。
5.加工设备准备:在进行实际加工之前,需要对数控冲床进行一些准备工作。
包括安装刀具、材料固定、工件装夹等。
6.开始加工:按照设定好的程序和参数,启动数控冲床进行加工操作。
操作人员需要监控加工过程的稳定性,检查刀具磨损情况,及时进行调整和更换。
7.检查和修正:完成加工后,需要对零件的尺寸、形状、表面质量等进行检查。
如有不符合要求的地方,可以通过调整程序或者刀具等进行修正。
8.保存和备份:将调试好的程序进行保存和备份,以便下次加工使用。
同时,也要将零件的加工数据和质量记录下来,以备查证。
通过以上步骤,我们可以完成数控冲床程序操作。
这种方式可以提高生产效率和产品质量,减少人为错误和浪费。
数控冲床程序操作的关键在于准确理解加工要求,灵活运用G代码和M代码指令,及时调试和修正加工过程中的问题。
数控冲床手动编程的所有代码与指令
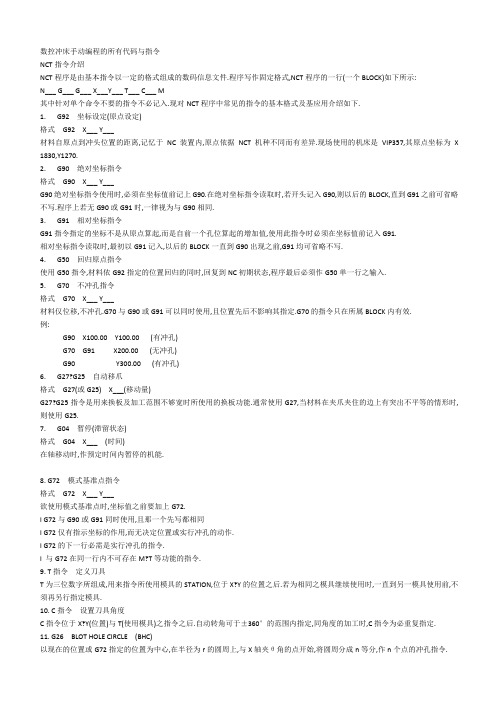
数控冲床手动编程的所有代码与指令NCT指令介绍NCT程序是由基本指令以一定的格式组成的数码信息文件.程序写作固定格式,NCT程序的一行(一个BLOCK)如下所示:N___ G___ G___ X___Y___ T___ C___ M其中针对单个命令不要的指令不必记入.现对NCT程序中常见的指令的基本格式及基应用介绍如下.1. G92 坐标设定(原点设定)格式G92 X___ Y___材料自原点到冲头位置的距离,记忆于NC装置内,原点依据NCT机种不同而有差异.现场使用的机床是VIP357,其原点坐标为X 1830,Y1270.2. G90 绝对坐标指令格式G90 X___ Y___G90绝对坐标指令使用时,必须在坐标值前记上G90.在绝对坐标指令读取时,若开头记入G90,则以后的BLOCK,直到G91之前可省略不写.程序上若无G90或G91时,一律视为与G90相同.3. G91 相对坐标指令G91指令指定的坐标不是从原点算起,而是自前一个孔位算起的增加值,使用此指令时必须在坐标值前记入G91.相对坐标指令读取时,最初以G91记入,以后的BLOCK一直到G90出现之前,G91均可省略不写.4. G50 回归原点指令使用G50指令,材料依G92指定的位置回归的同时,回复到NC初期状态,程序最后必须作G50单一行之输入.5. G70 不冲孔指令格式G70 X___ Y___材料仅位移,不冲孔.G70与G90或G91可以同时使用,且位置先后不影响其指定.G70的指令只在所属BLOCK内有效.例:G90 X100.00 Y100.00 (有冲孔)G70 G91 X200.00 (无冲孔)G90 Y300.00 (有冲孔)6. G27?G25 自动移爪格式G27(或G25) X___(移动量)G27?G25指令是用来换板及加工范围不够宽时所使用的换板功能.通常使用G27,当材料在夹爪夹住的边上有突出不平等的情形时,则使用G25.7. G04 暂停(滞留状态)格式G04 X___ (时间)在轴移动时,作预定时间内暂停的机能.8. G72 模式基准点指令格式G72 X___ Y___欲使用模式基准点时,坐标值之前要加上G72.l G72与G90或G91同时使用,且那一个先写都相同l G72仅有指示坐标的作用,而无决定位置或实行冲孔的动作.l G72的下一行必需是实行冲孔的指令.l 与G72在同一行内不可存在M?T等功能的指令.9. T指令定义刀具T为三位数字所组成,用来指令所使用模具的STATION,位于X?Y的位置之后.若为相同之模具继续使用时,一直到另一模具使用前,不须再另行指定模具.10. C指令设置刀具角度C指令位于X?Y(位置)与T(使用模具)之指令之后.自动转角可于±360°的范围内指定,同角度的加工时,C指令为必重复指定.11. G26 BLOT HOLE CIRCLE (BHC)以现在的位置或G72指定的位置为中心,在半径为r的圆周上,与X轴夹θ角的点开始,将圆周分成n等分,作n个点的冲孔指令.格式G26 I r J±θK n T___ (C___ ) G26 I4.50 J0 K4 T30 (C10)I=圆的半径r.输入正值J=冲孔起始点与X轴之夹±θ.反时针方向为正(+),顺时针方向为负(-)K=冲孔个数,反时针方向加工为正(+),顺时针方向为负(-)12. G28 LINE AT ANGLE (LAA)以现在的位置或G72指令的位置算起,与X轴夹θ角的方向,间隔d的距离,冲n个孔的指令.格式G28 I d J±θK n T___ (C___ )I=间隔±d.d为负时,以模式基准点作为中心,于对称方向冲孔J=角度±θ,反时针方向为正(+),顺时针方向为负(-)K=冲孔个数n.不包括模式基准点13. G29 圆弧(ARC)以现在的位置或G72所指定的基准点为中心,半径为r的圆周上,与X轴夹角为θ的开始点,角度间隔Δθ,排列n个点的冲孔指令. 格式G28 I r J±θP±ΔθK n T___ (C___ )I=圆的半径r,为正数J=最初冲孔起始点,角度±θ,反时针方向为正(+),顺时针方向为负(-)P=角度间隔为±Δθ,为正时,以反时针方向冲孔,为负时,以顺时针方向冲孔K=冲孔的个数14. G36?G37 格状孔此模式从G72指定的位置开始,X轴方向以d1为间隔.做n个,Y轴方向以d2为间隔,做n2个格子状冲孔的指令.G36是以X轴方向为优先加工指令,G37是以Y轴方向为优先加工指令,考虑到板料在运动中的稳定性,一般选用G36.格式G36 I±d1 P n1 J±d2 K n2 T___ (C___ )G36 I±d1 P n1 J±d2 K n2 T___ (C___ )I=间隔±d1,正(+)时为X轴方向,负(-)时为-X方向取间隔P=X轴方向的冲孔数n1(不含基准点)J=间隔±d2,正(+)时为Y轴方向,负(-)时为-Y方向取间隔K=Y轴方向的冲孔数n2(不含基准点)15. G66 切边(SHP)此模式是由G72所指定之基准点开始,在与X轴夹角为θ°的方向上,以W1×W2之模具,作长度为±d的连续冲孔指令.格式G66 I e J±θP±W1 Q±W2 D±d T___I=连续冲孔加工之长度eJ=角度±θ.反时针为(+)时针为(-)P=模具边长±W1(J方向的模具尺寸)Q=模具边±W2(与J成90°方向的模具尺寸)W1与W2必需同号,若W1=W2时Q可省略不写.D=对加工长度作补正之值±d(d=0时,D项可省略)l D若为负时连续冲也的长度比I短少2倍D的长,为正时则比I长2 倍D.l 连续冲孔的长度I,至少需为P(W1)之1.5倍以上方可.16. G67 矩形(SQR)此模式是由G72所指定的基准点开始,平行X轴方向长度e1,Y轴方向长e2的矩形,以长W1W2的模具连续冲孔的指令.格式G67 I±e1 J±e2 P W1 Q W2 T___I=X轴方向冲孔长度±e1.正为X方向.负为X轴负方向J=Y轴方向冲孔长度±e1.正为Y方向.负为Y轴负方向P=X方向模具长度W1,为正值Q=Y方向模具长度W2,为正值.若W1=W2时,Q可省略因通常使用正方形模,帮Q不使用.17. G68 蚕食圆弧(NBL-A)此模式是以G72所指定的基准点为中心,半径为r的圆周上,与X轴夹角为θ1的点开始,增加θ2的角度,以直径为ψ的模具,间隔为d来作蚕食加工之指令.格式G68 I r J±θ1 K±θ2 P±ψQ d T___I=圆的半径r,输入正值(但I<5700mm)J=加工起始点自X轴算起之角度±θ1,反时针方向为正,顺时针方向为负K=蚕食加工的角度±θ2,(+)时为逆时针加工,(-)时为顺时针加工P=模具直径±ψ,正时在圆的外侧加工,负时在圆的内侧加工Q=蚕食的间隔为d,输入正数(最大d值为8mm)l 板厚3.2mm以上场合,或是间隔超过8mm时,以G78代替G68使用之.l 蚕食所使用之模具,必须小于所蚕食之圆的半径.18. G69 I e J±θ P±ψ Q d T___此模式是从G72指定的基准点开始,与X轴成θ角方向,长度e,以直径ψ模具,间隔d来蚕食的加工模式.格式G69 I e J±θP±ψQ d T___I=蚕食执行的长度,为模式起点至模式终点的长度J=角度±θ,反时针为正,顺时针为负P=模具直径±ψ,正时加工方向在直线之左侧,负时加工于直线右侧Q=蚕食间隔d,正值输入,最大值为8mm19. G78 冲孔圆弧(PNC-A)此模式是以G72所指定之基准点为中心,半径为r的圆周上,与X轴夹角为θ1的点开始,增加θ2之角度,以直径ψ的模具,间隔为d 来作蚕食加工之指令.格式G78 I r J±θ1 K±θ2 P±ψQ d D t T___I=圆的半径r.输入正值J=加工起始点自X轴算起之角度±θ1.反时针方向为正,顺时针方向为负K=蚕食加工的角度±θ2.(+)时逆时针加工,(-)时顺时针加工P=模具直径±ψ.(+)时在圆的外侧加工,(-)时在圆的内侧加工Q=蚕食的间隔为dD=使用板厚t,(d≥t)20. G79 冲孔长圆(PNC-L)此模式是从G72指令的基准点开始,与X轴成θ1角方向,长度e,直径ψ的模具,间隔d来蚕食的加工模式.格式G79 I e J±θ1 P±ψQ d D t T____I=蚕食执行的长度,为模式起点至模式终点的长度J=角度±θ1,反时针为正,顺时针为负P=模具直径±ψ.正时加工方向在直线之左侧,负时加工于直线右侧Q=蚕食间隔dD=使用板厚t.(d≥t)21. G98 多数取的基准点与排列间隔之设定多数取加工时,制品对于材料作何种排列的指令格式G98 Xx0 Yy0 Ixp Jyp Pnx Knyx0……排列在左下方制品的左下角点的X坐标y0……排列在左下方制品的左下角点的Y坐标xp……X方向上制品排列的间隔yp……Y方向上制品排列的间隔nx……X方向上排列的间隔数ny……Y方向上排列的间隔数22. G7576 多数取执行指令除多数取程序外,UOO~VOO为止,为一个制品的子程序,此编号的MACRO对应WOO,根据G98所设定之排列,令材料全部执行的指令. 格式G75 W___ Q___ ……以X方向为优先级执行G76 W___ Q ___……以Y方向为优先级执行W=为MACRO编号,与程序中的UOO~VOO对应Q=为加工开始的角落.Q1—左下角;Q2—右下角;Q3—左上角;Q4—右上角23. MACRO机能(U)MACRO记忆机能,UOO与VOO为程序中数个BLOCK之记忆OO则为不限次数之记忆呼出时使用,这时U所对应读取之数值,需为相同格式UOO...VOOWOO注:一个U…V对应一个W.U~V之间不可有M02M03及50之指令存在.24. M13 加工结束指令加工结束之后单一行输入25. M510~M559 冲凸台形强筋前之指令.在冲凸台形强筋前单一行输入.指令可在M510~M559中任选一个,但在同一程序中,不同模具前不能用同一M指令.26. M560~M563 打标记色拉孔前之指令在打标记色拉孔前单一行输入,可在M560~M505中任选一个,但在同一程序中,不同的模具前不能使用同一M指令.27. M502~M505 冲敲落孔前之指令在冲敲落孔前单一行输入,可在M502~M505中任选一个,但在同一程序中不同模具前不能使用同一M指令.注:在实际运用中,为配合NCT现场的操作,使NCT程序转换与NCT现场对M指令的添加达到共识,对常用的特殊刀具指定了固定的M指令,具体运用参考第三章.。
村田数控冲床冲压操作指令【大全】

指令O;程序号M00;程序停止N;顺序号M02;程序结束X;X轴绝对值M03;无冲压(只定位)Y;Y轴绝对值MO5;卸料(上料器可选件)DX;X轴增量值M06;冲压后停止DY;Y轴增量值M08;成型模式启动T;转塔分度指令MO9;成型模式取消C;C轴绝对值M12;步冲模式启动M;M功能(辅助功能)M13;步冲模式取消FRM/;坐标格式设置M14;UP/DOWN成型刀具上模式OFS/;本地坐标格式设置M15;UP/DOWN成型刀具上模式取消MOV/;图形功能基点设置M30;程序复位及反绕REP/;自动重新定位M40;卸掉(上料器可选件)INC/;增量M41;降下REPO垫和开启工件夹持器GRD/;网格M42;关闭工件夹持器和并提升REPO垫LAA/;角度M55;外部减速模式(可选件)ARC/;弧度M58;外部减速模式和工件滑槽打开模式BHC/;螺栓孔圆M59;工件滑槽关闭(与M58成对使用)RAD/;半径(沿半径切割)M60;工件卸料M代码HOL/;孔(切割圆)M62;选择外轨OPEN/;开孔(开圆孔)M63;选择内轨CAA/;角切割(用圆冲头切割角线)M80;工作台速度100%REC/;矩形(切割矩形孔)M81;工作台速度75%OBL/;矩形(切割矩形孔)M82;工作台速度50%TGL/;切三角(45°内角切割)M83;工作台速度25%RRC/;可圆矩形(开圆内角矩形孔)M98;调用子程序SAA/;角斜度(用分度刀具开角线)M99;结束子程序NBL/;步冲M610;滑枕速度取消DWL/;暂停M611;滑枕高速PAT/;宏程序功能存储开始M613;滑枕中速END;宏程序功能存储结束M615;滑枕低速MGR/;宏程序网格M620;滑枕TDC取消PTP/;点至点(在2点间开线)M621;移动滑枕TDCPPA/;点至点弧度(在两点间开圆弧线)M630;以低速步冲(缺省)节距低于5mm SYM/;镜像设置M631;以低速步冲(编程举例)节距低于1mm SYC/;镜像取消MAT/;指定工件材料M;代码指令可启动各种机床或程序成分(如同开关)。
简述数控冲床编程步骤
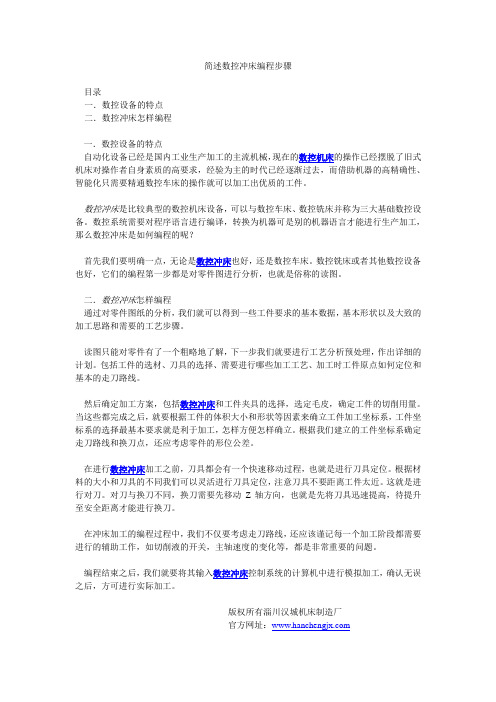
简述数控冲床编程步骤目录一.数控设备的特点二.数控冲床怎样编程一.数控设备的特点自动化设备已经是国内工业生产加工的主流机械,现在的数控机床的操作已经摆脱了旧式机床对操作者自身素质的高要求,经验为主的时代已经逐渐过去,而借助机器的高精确性、智能化只需要精通数控车床的操作就可以加工出优质的工件。
数控冲床是比较典型的数控机床设备,可以与数控车床、数控铣床并称为三大基础数控设备。
数控系统需要对程序语言进行编译,转换为机器可是别的机器语言才能进行生产加工,那么数控冲床是如何编程的呢?首先我们要明确一点,无论是数控冲床也好,还是数控车床。
数控铣床或者其他数控设备也好,它们的编程第一步都是对零件图进行分析,也就是俗称的读图。
二.数控冲床怎样编程通过对零件图纸的分析,我们就可以得到一些工件要求的基本数据,基本形状以及大致的加工思路和需要的工艺步骤。
读图只能对零件有了一个粗略地了解,下一步我们就要进行工艺分析预处理,作出详细的计划。
包括工件的选材、刀具的选择、需要进行哪些加工工艺、加工时工件原点如何定位和基本的走刀路线。
然后确定加工方案,包括数控冲床和工件夹具的选择,选定毛皮,确定工件的切削用量。
当这些都完成之后,就要根据工件的体积大小和形状等因素来确立工件加工坐标系,工件坐标系的选择最基本要求就是利于加工,怎样方便怎样确立。
根据我们建立的工件坐标系确定走刀路线和换刀点,还应考虑零件的形位公差。
在进行数控冲床加工之前,刀具都会有一个快速移动过程,也就是进行刀具定位。
根据材料的大小和刀具的不同我们可以灵活进行刀具定位,注意刀具不要距离工件太近。
这就是进行对刀。
对刀与换刀不同,换刀需要先移动Z轴方向,也就是先将刀具迅速提高,待提升至安全距离才能进行换刀。
在冲床加工的编程过程中,我们不仅要考虑走刀路线,还应该谨记每一个加工阶段都需要进行的辅助工作,如切削液的开关,主轴速度的变化等,都是非常重要的问题。
编程结束之后,我们就要将其输入数控冲床控制系统的计算机中进行模拟加工,确认无误之后,方可进行实际加工。
数控冲床编程
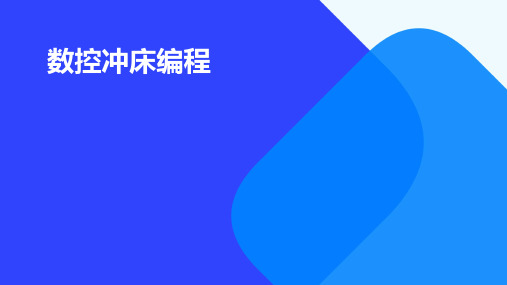
目录
• 数控冲床编程基础 • 数控冲床编程技术 • 数控冲床编程实践 • 数控冲床编程安全 • 数控冲床编程发展趋势
01
数控冲床编程基础
数控冲床编程简介
数控冲床编程是一种使用计算机程序来控制数控冲床进行加工的技术。通 过编程,可以精确地控制冲床的加工过程,实现自动化生产。
数控冲床编程广泛应用于金属加工行业,尤其在钣金加工领域,能够高效 地完成各种复杂形状的加工任务。
编程实例分析
01
02
03
实例一
某金属板材的冲孔加工, 分析如何根据板材尺寸、 孔径和孔间距等参数进行 编程。
实例二
某异形零件的轮廓加工, 探讨如何根据零件形状、 材料特性和加工研究如何通过程序优化提 高加工效率和降低成本。
03
数控冲床编程实践
在模拟环境中校验加工程 序,发现问题及时修改。
程序后处理与传输
将加工程序后处理为数控 冲床能识别的格式,通过 数据传输软件发送到数控 冲床。
实际操作流程
首件试切
在正式批量加工前,进行首件试切, 确认加工效果是否满足要求。
批量加工
若首件试切合格,则进行批量加工。
常见问题与解决方案
01
程序错误
检查编程代码,确保语法和逻辑正 确。
数控冲床编程可以提高加工精度、加工效率、降低劳动强度,为企业带来 经济效益。
编程语言和工具
数控冲床编程通常使用G代码、M代码等数控编程语 言,这些语言通过特定的指令来控制冲床的运动和加
工过程。
输标02入题
常用的数控编程软件包括Mastercam、Fusion 360、 SolidWorks等,这些软件提供了友好的用户界面和丰 富的功能,方便用户进行编程操作。
数控冲床编程
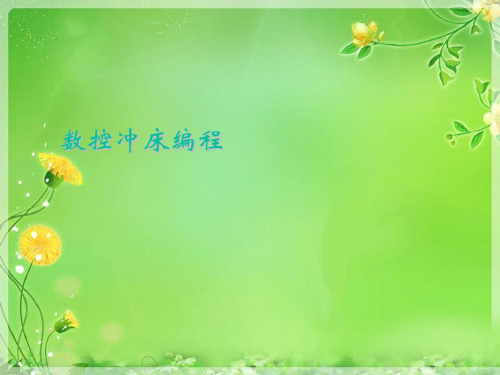
8.1 数控冲床概述
近年来,随着数控技术的发展,数控技术在 冲床上的应用日趋成熟,数控冲床在我国逐渐普 及,大大地提高了冲压加工的生产效率,降低了 生产成本。数控冲床也是数控机床的一种,其组 成和工作原理与一般数控机床相类似。
冲床属于压力加工机床,主要应用于钣金加 工,如冲孔、裁剪和拉伸。数控冲床又称为“钣 金加工中心”,即任何复杂形状的平面钣金零件 都可在数控冲床上完成其所有孔和外形轮廓的冲 裁等加工。
8.2.4 模具(刀具)的确定 ① 根据被加工面的形状,尽量选用通用模具( 刀具),以降低成本,但有时为简化编程和提高 加工质量,也选用专用模具(刀具)。
数控冲床可以根据模具(刀具)形状形成工 件形状,因此,模具(刀具)规格形状较多。
通用模具(刀具)使用得较多的有圆形、方 (矩)形,还有跑道形、十字形、(等腰)三角 形、直角三角形、单D形、双D形等。
8.2.2 工件的安装
在数控冲床上安装工件相对比较简单 。为了安装方便,机床应在参考点上进行 工件安装。
首先根据板料的尺寸,选择和调整夹 钳的位置;松开夹钳并抬起原点定位块, 将板料与之靠实;夹钳夹紧,放下原点定 位块,工件装夹完成,
8.2.3 编程原点的设定
编程原点是编程员在编制加工程序时 设置的基准。编程原点应力求与设计基准 和工艺基准相一致,使编程中的数值计算 简单。
图8-7 模具结构
表8-2
模具间隙
材料
板厚/mm
低碳钢
铝
不锈钢
0.8~1.6
0.2~0.3
0.2~0.3
0.2~0.35
1.6~2.3
0.3~0.4
0.3~0.4
0.4~0.5
2.3~3.2
数控冲床指令

数控冲床指令NCT程序是由基本指令以一定的格式组成的数码信息文件.程序写作固定格式,NCT程序的一行(一个BLOCK)如下所示: N___ G___ G___ X___Y___ T___ C___ M其中针对单个命令不要的指令不必记入.现对NCT程序中常见的指令的基本格式及基应用介绍如下.1. G92 坐标设定(原点设定)格式G92 X___ Y___材料自原点到冲头位置的距离,记忆于NC装置内,原点依据NCT机种不同而有差异.现场使用的机床是VIP357,其原点坐标为X 1830,Y1270.2. G90 绝对坐标指令格式G90 X___ Y___G90绝对坐标指令使用时,必须在坐标值前记上G90.在绝对坐标指令读取时,若开头记入G90,则以后的BLOCK,直到G91之前可省略不写.程序上若无G90或G91时,一律视为与G90相同.3. G91 相对坐标指令G91指令指定的坐标不是从原点算起,而是自前一个孔位算起的增加值,使用此指令时必须在坐标值前记入G91.相对坐标指令读取时,最初以G91记入,以后的BLOCK一直到G90出现之前,G91均可省略不写.4. G50 回归原点指令使用G50指令,材料依G92指定的位置回归的同时,回复到NC初期状态,程序最后必须作G50单一行之输入.5. G70 不冲孔指令格式G70 X___ Y___材料仅位移,不冲孔.G70与G90或G91可以同时使用,且位置先后不影响其指定.G70的指令只在所属BLOCK内有效. 例:G90 X100.00 Y100.00 (有冲孔)G70 G91 X200.00 (无冲孔)G90 Y300.00 (有冲孔)6. G27?G25 自动移爪格式G27(或G25) X___(移动量)G27?G25指令是用来换板及加工范围不够宽时所使用的换板功能.通常使用G27,当材料在夹爪夹住的边上有突出不平等的情形时,则使用G25.7. G04 暂停(滞留状态)格式G04 X___ (时间)在轴移动时,作预定时间内暂停的机能8. G72 模式基准点指令格式G72 X___ Y___欲使用模式基准点时,坐标值之前要加上G72.l G72与G90或G91同时使用,且那一个先写都相同l G72仅有指示坐标的作用,而无决定位置或实行冲孔的动作.l G72的下一行必需是实行冲孔的指令.l 与G72在同一行内不可存在M?T等功能的指令.9. T指令定义刀具T为三位数字所组成,用来指令所使用模具的STA TION,位于X?Y 的位置之后.若为相同之模具继续使用时,一直到另一模具使用前,不须再另行指定模具.10. C指令设置刀具角度C指令位于X?Y(位置)与T(使用模具)之指令之后.自动转角可于±360°的范围内指定,同角度的加工时,C指令为必重复指定.11. G26 BLOT HOLE CIRCLE (BHC)以现在的位置或G72指定的位置为中心,在半径为r的圆周上,与X 轴夹θ角的点开始,将圆周分成n等分,作n个点的冲孔指令.格式G26 I r J±θ K n T___ (C___ )I=圆的半径r.输入正值J=冲孔起始点与X轴之夹±θ.反时针方向为正(+),顺时针方向为负(-)K=冲孔个数,反时针方向加工为正(+),顺时针方向为负(-)12. G28 LINE AT ANGLE (LAA)以现在的位置或G72指令的位置算起,与X轴夹θ角的方向,间隔d的距离,冲n个孔的指令.格式G28 I d J±θ K n T___ (C___ )I=间隔±d.d为负时,以模式基准点作为中心,于对称方向冲孔J=角度±θ,反时针方向为正(+),顺时针方向为负(-)K=冲孔个数n.不包括模式基准点13. G29 圆弧(ARC)以现在的位置或G72所指定的基准点为中心,半径为r的圆周上,与X轴夹角为θ的开始点,角度间隔Δθ,排列n个点的冲孔指令.格式G28 I r J±θ P±Δθ K n T___ (C___ )I=圆的半径r,为正数J=最初冲孔起始点,角度±θ,反时针方向为正(+),顺时针方向为负(-) P=角度间隔为±Δθ,为正时,以反时针方向冲孔,为负时,以顺时针方向冲孔K=冲孔的个数14. G36?G37 格状孔此模式从G72指定的位置开始,X轴方向以d1为间隔.做n个,Y轴方向以d2为间隔,做n2个格子状冲孔的指令.G36是以X轴方向为优先加工指令,G37是以Y轴方向为优先加工指令,考虑到板料在运动中的稳定性,一般选用G36.格式G36 I±d1 P n1 J±d2 K n2 T___ (C___ )G36 I±d1 P n1 J±d2 K n2 T___ (C___ )I=间隔±d1,正(+)时为X轴方向,负(-)时为-X方向取间隔P=X轴方向的冲孔数n1(不含基准点)J=间隔±d2,正(+)时为Y轴方向,负(-)时为-Y方向取间隔K=Y轴方向的冲孔数n2(不含基准点)15. G66 切边(SHP)此模式是由G72所指定之基准点开始,在与X轴夹角为θ°的方向上,以W1×W2之模具,作长度为±d的连续冲孔指令.格式G66 I e J±θ P±W1 Q±W2 D±d T___I=连续冲孔加工之长度eJ=角度±θ.反时针为(+)时针为(-)P=模具边长±W1(J方向的模具尺寸)Q=模具边±W2(与J成90°方向的模具尺寸)W1与W2必需同号,若W1=W2时Q可省略不写.D=对加工长度作补正之值±d(d=0时,D项可省略)l D若为负时连续冲也的长度比I短少2倍D的长,为正时则比I长2 倍D.l 连续冲孔的长度I,至少需为P(W1)之1.5倍以上方可.16. G67 矩形(SQR)此模式是由G72所指定的基准点开始,平行X轴方向长度e1,Y轴方向长e2的矩形,以长W1W2的模具连续冲孔的指令. 格式G67 I±e1 J±e2 P W1 Q W2 T___I=X轴方向冲孔长度±e1.正为X方向.负为X轴负方向J=Y轴方向冲孔长度±e1.正为Y方向.负为Y轴负方向P=X方向模具长度W1,为正值Q=Y方向模具长度W2,为正值.若W1=W2时,Q可省略因通常使用正方形模,帮Q不使用.17. G68 蚕食圆弧(NBL-A)此模式是以G72所指定的基准点为中心,半径为r的圆周上,与X轴夹角为θ1的点开始,增加θ2的角度,以直径为ψ的模具,间隔为d来作蚕食加工之指令.格式G68 I r J±θ1K±θ2 P±ψ Q d T___I=圆的半径r,输入正值(但I<5700mm)J=加工起始点自X轴算起之角度±θ1,反时针方向为正,顺时针方向为负K=蚕食加工的角度±θ2,(+)时为逆时针加工,(-)时为顺时针加工P=模具直径±ψ,正时在圆的外侧加工,负时在圆的内侧加工Q=蚕食的间隔为d,输入正数(最大d值为8mm)l 板厚3.2mm以上场合,或是间隔超过8mm时,以G78代替G68使用之.l 蚕食所使用之模具,必须小于所蚕食之圆的半径.18. G69 I e J±θ P±ψ Q d T___此模式是从G72指定的基准点开始,与X轴成θ角方向,长度e,以直径ψ模具,间隔d来蚕食的加工模式.格式G69 I e J±θ P±ψ Q d T___I=蚕食执行的长度,为模式起点至模式终点的长度J=角度±θ,反时针为正,顺时针为负P=模具直径±ψ,正时加工方向在直线之左侧,负时加工于直线右侧Q=蚕食间隔d,正值输入,最大值为8mm19. G78 冲孔圆弧(PNC-A)此模式是以G72所指定之基准点为中心,半径为r的圆周上,与X轴夹角为θ1的点开始,增加θ2之角度,以直径ψ的模具,间隔为d来作蚕食加工之指令.格式G78 I r J±θ1 K±θ2 P±ψ Q d D t T___I=圆的半径r.输入正值J=加工起始点自X轴算起之角度±θ1.反时针方向为正,顺时针方向为负K=蚕食加工的角度±θ2.(+)时逆时针加工,(-)时顺时针加工P=模具直径±ψ.(+)时在圆的外侧加工,(-)时在圆的内侧加工Q=蚕食的间隔为dD=使用板厚t,(d≥t)20. G79 冲孔长圆(PNC-L)此模式是从G72指令的基准点开始,与X轴成θ1角方向,长度e,直径ψ的模具,间隔d来蚕食的加工模式.格式G79 I e J±θ1 P±ψ Q d D t T____I=蚕食执行的长度,为模式起点至模式终点的长度J=角度±θ1,反时针为正,顺时针为负P=模具直径±ψ.正时加工方向在直线之左侧,负时加工于直线右侧Q=蚕食间隔dD=使用板厚t.(d≥t)21. G98 多数取的基准点与排列间隔之设定多数取加工时,制品对于材料作何种排列的指令格式G98 Xx0 Yy0 Ixp Jyp Pnx Knyx0……排列在左下方制品的左下角点的X坐标y0……排列在左下方制品的左下角点的Y坐标xp……X方向上制品排列的间隔yp……Y方向上制品排列的间隔nx……X方向上排列的间隔数ny……Y方向上排列的间隔数22. G7576 多数取执行指令除多数取程序外,UOO~VOO为止,为一个制品的子程序,此编号的MACRO对应WOO,根据G98所设定之排列,令材料全部执行的指令.格式G75 W___ Q___ ……以X方向为优先级执行G76 W___ Q ___……以Y方向为优先级执行W=为MACRO编号,与程序中的UOO~VOO对应Q=为加工开始的角落.Q1—左下角;Q2—右下角;Q3—左上角;Q4—右上角23. MACRO机能(U)MACRO记忆机能,UOO与VOO为程序中数个BLOCK之记忆OO 则为不限次数之记忆呼出时使用,这时U所对应读取之数值,需为相同格式UOO ..VOOWOO注:一个U…V对应一个W.U~V之间不可有M02M03及50之指令存在.24. M13 加工结束指令加工结束之后单一行输入25. M510~M559 冲凸台形强筋前之指令.在冲凸台形强筋前单一行输入.指令可在M510~M559中任选一个,但在同一程序中,不同模具前不能用同一M指令.26. M560~M563 打标记沙拉孔前之指令在打标记沙拉孔前单一行输入,可在M560~M505中任选一个,但在同一程序中,不同的模具前不能使用同一M指令.27. M502~M505 冲敲落孔前之指令在冲敲落孔前单一行输入,可在M502~M505中任选一个,但在同一程序中不同模具前不能使用同一M指令.注:在实际运用中,为配合NCT现场的操作,使NCT程序转换与NCT 现场对M指令的添加达到共识,对常用的特殊刀具指定了固定的M指令,。
- 1、下载文档前请自行甄别文档内容的完整性,平台不提供额外的编辑、内容补充、找答案等附加服务。
- 2、"仅部分预览"的文档,不可在线预览部分如存在完整性等问题,可反馈申请退款(可完整预览的文档不适用该条件!)。
- 3、如文档侵犯您的权益,请联系客服反馈,我们会尽快为您处理(人工客服工作时间:9:00-18:30)。
8.2
数控冲压加工工艺
8.2.1 确定机床和数控系统 根据被加工零件的尺寸和技术要求, 考虑各项技术经济指标,合理地选择机床。 当有多台机床可选择时,要根据被加工零 件的形状,编程的方便性,选择具有相应 功能的数控系统机床。当然,在满足要求 的情况下,可尽量选用成本低的数控机床, 以降低加工成本。
8.2.6 折弯件展开长度的计算
1.展开长度计算公式 展开长=直线部分长+圆弧部分展开长 圆弧部分展开长=圆弧中性层弧长=(r+K· t)/180。 式中,r为内圆弧半径; K为弯曲系数; T为板材厚度; 为板材变曲所转过的角度。
2.弯曲系数K 弯曲系数K是展开计算中一个重要的 参数。它的选定,直接影响计算结果的准 确度。K值如表8-3所示。生产使用时,要 根据实际情况确定。
② 模具结构。冲床用模具分上模具和下模具两 部分。对转塔数控冲床,上模具安装在转塔上转 盘上,下模具安装在转塔下转盘上。工作时,上、 下转盘同时转到冲压位置。冲锤打击上模具,实 现冲压加工。 模具根据机床结构确定,有直联式和分离式 两种,如图8-7所示。一般上模具由打击头、弹 簧、键销、冲模架、冲头、塑料脱模等组成,下 模具由下模、下模座、下模固定块等组成。直联 式由于当撞杆回到上止点时,冲模也肯定回到上 止点,因此不会发生冲模尚未从板料中退出而工 作台已经移动的现象。分离式弹簧力必须足够大。
图8-8 斜刃冲时凸凹模刃口部分的布置方式
斜刃冲削力可用下列简化公式计算: P斜′= KLτt 式中,K=0.4~0.6(当h=t时),当为平刃口冲削 时,K取1.3; L——剪切周长/mm; τ ——板料抗剪强度/MPa; t ——材料厚度/mm; h——斜刃高度/mm。 可以看出,斜刃口冲削力大约是平刃口冲削力的 1/2~1/3。 适当加大刃口转角处或曲率半径较小处的刃 口间隙(加大量不超过直边部分的40%),可以 有效改善这些部位的受力状况,减小局部冲削力, 均化刃口磨损,延长模具使用寿命。
第8章 数控冲床编程
8.1
数控冲床概述
8.2
数控冲压加工工艺
8.3
数控冲压编程
8.4
编程实例
8.1 数控冲床概述
近年来,随着数控技术的发展,数控技术在 冲床上的应用日趋成熟,数控冲床在我国逐渐普 及,大大地提高了冲压加工的生产效率,降低了 生产成本。数控冲床也是数控机床的一种,其组 成和工作原理与一般数控机床相类似。 冲床属于压力加工机床,主要应用于钣金加 工,如冲孔、裁剪和拉伸。数控冲床又称为“钣 金加工中心”,即任何复杂形状的平面钣金零件 都可在数控冲床上完成其所有孔和外形轮廓的冲 裁等加工。
8.1.3 数控冲床的组成
数控冲床的加工对象为板材,在机床结构上 只有板材的移动为数控驱动,数控冲床的数控伺 服系统多为半闭环控制或闭环控制。冲削运动有 机械式和液压式两种。目前常见的数控冲床是冲 模(刀具)装在可以旋转的转塔上,称转塔数控 冲床。转塔上可以容纳的刀具数量由转盘的大小 决定,一般从16把~58把不等。还有链式刀库的 形式。刀具也可装在机床外,经机械手把所用的 刀具换到冲压位置进行冲削加工。
加工程序指令的坐标值是刀位点在工件坐标 系中的坐标值。冲削加工的机床,X、Y轴的刀 位点亦在主轴中心上。程序设计人员在编程时, 可以用绝对坐标值,也可以用相对坐标值。 用绝对坐标值指令时,刀具(或机床)运动轨迹 是根据工件坐标原点给出的。 用相对坐标值指令时,刀具(或机床)运动轨迹 是相对于前一个位置计算的,又称增量坐标值。
图8-4 数控冲床坐标轴及方向
2.电气坐标系 电气坐标系是与标准坐标系平行的坐 标系,是数控系统在处理编程数据时的坐 标系。在数控系统中坐标轴所用的位置检 测元件确定之后,检测元件的零点即是电 气坐标系的原点。
3.机床坐标系 机床坐标系也是与标准坐标系平行的坐标系。 它是在电气坐标原点的基础上,沿电气坐标轴偏 移一个距离。这个偏移距离,由机床制造者调试 后将其设置在参数中,此点即参考点。参考点即 是机床原点。如果数控系统采用相对位置检测元 件时,在机床通电后,需做手动返回参考点操作, 以建立机床坐标系。机床参考点是电气坐标系上 的一个固定点,它是机床补偿功能和行程软限位 的基准点,机床使用者不要随意更动。 在机床坐标轴返回到参考点时,机床在机床 零点上,刀具基准点与机床零点重合,此时机床 坐标系坐标轴的显示值为0。冲削加工的机床,X、 Y轴的基准点在主轴中心上。
(1)工序简图 包括工件的装夹方式,编程原点及坐标轴方向, 加工原点编码,注明工序加工表面及应达到的尺 寸和公差。 (2)工序卡 包括工步顺序及内容,加工表面及应达到的尺寸 和公差,刀具编号及名称,刀具尺寸及半径补偿 号,主轴转速及进给速度(步长)等。 (3)刀具卡 包括刀具编号及名称,尺寸及半径补偿号。
8.1.1 数控冲床主要技术参数
参数Specification SKYY31225C KN 300
公称压力 Punching force
最大加工板材厚度 Max. punching sheet thickness(Mild steel) 最大加工板材尺寸(一次重定位) Max. sheet size(One reposition) 冲孔精度 Punching accuracy 最高行程次数 Max. hit speed 模位数 Number of stations 分度工位数 Number of index
8.2.2 工件的安装 在数控冲床上安装工件相对比较简单。 为了安装方便,机床应在参考点上进行工 件安装。 首先根据板料的尺寸,选择和调整夹 钳的位置;松开夹钳并抬起原点定位块, 将板料与之靠实;夹钳夹紧,放下原点定 位块,工件装夹完成,
8.2.3 编程原点的设定 编程原点是编程员在编制加工程序时 设置的基准。编程原点应力求与设计基准 和工艺基准相一致,使编程中的数值计算 简单。
8.2.7 数控冲压加工工艺文件
编写数控加工技术文件是数控加工工艺设计 的内容之一。这些技术文件既是数控加工和产品 验收的依据,也是需要操作者遵守和执行的规程。 有的则是加工程序的具体说明或附加说明,使操 作者更加明确程序的内容、工件的装夹方式、各 加工部位所选用的刀具及其他需要说明的事项, 以保证程序的正确运行。因目前尚无统一标准, 这里仅介绍几种数控加工技术文件,供自行设计 时参考。
mm
6
mm mm
1250×2500 ±0.10
h.p.m
个 个 个 T mm
400
20 2 3或4 12 4840×2800×2110
数控轴数 Controlling axes
机床重量 Machine weight 外形尺寸 Outline dime控冲床也是数控机床的一种类型,具有数 控机床的一般特点,在此不再赘述。此外,现代 数控冲床的冲压运动有机械式和液压式两种。由 于液压式具有纯机械式冲床无法比拟的优点,被 工业界公认为钣金柔性加工系统的发展方向。液 压数控冲床具有以下特点。 (1)“恒冲力”加工 一般机械式冲床的冲压力是由小到大,到达顶点 时只是一瞬间,无法实现在全冲程的任何位置都 具有足够的冲压力。而液压式冲床完全克服了机 械式冲床的缺点,建立了液压冲床“恒冲力”的 全新概念。
0.2~0.35 0.4~0.5 0.5~0.7 0.7~1.2
冲头和下模之间的间隙根据板厚和材料性 质,按表8-2所示选用,也可以根据机床情况, 按0.1mm的间隙制作模具最小冲孔直径:对低 碳钢和铝料可等于板厚,对不锈钢可等于2倍板 厚。也可按1.5倍板厚选取。
8.2.5 确定工步顺序
工步的顺序安排应考虑以下几点。 ① 应保证被加工零件的精度和质量。先内后外, 最后将工件与板料分离或仅留连接筋;最小冲削 量要大于或等于板料厚度,避免因冲头歪斜形成 啃边并影响模具寿命;应使加工后工件变形最小。 ② 在多件加工时,应使工步集中,以减少选 (换)模具(刀具)时间。 ③ 尽量用模具成形或选用大尺寸模具步冲加工, 以提高生产率。
图8-7 模具结构
表8-2
板厚/mm
0.8~1.6 1.6~2.3 2.3~3.2 3.2~4.5 0.6~6
模具间隙
材 料
低 碳 钢
0.2~0.3 0.3~0.4 0.4~0.6 0.6~0.9 0.9~1.2
铝
0.2~0.3 0.3~0.4 0.4~0.5 0.5~0.7 0.7~0.9
不 锈 钢
(3)冲裁精度与寿命 由于液压冲头的滑块与衬套之间存在一层不 可压缩的静压油膜,其间隙几乎为零,且不会产 生磨损,这就是液压冲床精度高、寿命长的原因 所在。 数控液压冲床的机身有桥形框架、O形框架、C 形框架等结构。数控液压冲床的冲模一般采用转 塔式的安装方式,并具有特定的自动分度装置, 每个自动分度模位中的模具均能自行转位,给冲 剪加工工艺带来了极大的柔性。
4.工件坐标系 工件坐标系是以机床坐标系为基准平 移而成的。这个偏移量由机床操作者设置 在工件坐标系设定指令中或坐标偏移存储 器中。程序设计人员在工件坐标系内编程, 编程时,不必考虑工件在机床中的实际位 置。
图8-5 机床与工件坐标系
工件坐标系的建立,是设定工件坐标 系原点与机床坐标原点的距离关系。实际 上,就是设定工件坐标系原点与机床在参 考点上时的基准点之间的距离,如图8-5所 示。当机床在参考点上时,由原点定位块 和工件夹钳定位面决定工件的坐标原点, 实际上就是机床的左下行程极限。
(2)智能化冲头 液压冲床的冲头具有软冲功能(即冲头速度 可实现快进、缓冲),既能提高劳动生产率,又 能改善冲压件质量所以液压冲床加工时振动小、 噪声低、模具寿命长。数控液压冲床的冲压行程 长度的调节可由软件编程控制,从而可完成步冲、 百页窗、打泡、攻螺纹等多种成形工序。液压系 统中采用了安全阀和减压阀元件,一旦冲压发生 超负荷时,能提供瞬间减压及停机保护,避免机 床、模具损坏,而且复机简易、快速。
8.3 数控冲压编程
目前,许多数控冲床系统,都配备了自动编 程软件,自动将CAD程序、图形转化为冲床 CNC加工指令,具有模具库管理,自动选模加工, 专用模具优化,优化加工路径,后置处理,自动 完成微连接,自动重复定位等功能。本节介绍的 是手工编程。前面介绍过,数控冲床加工编程, Z轴运动由液压或机械系统控制,所以数控冲压 编程没有Z轴,只是二维编程。有了数控车床和 数控铣床的编程基础,数控冲压加工编程是比较 简单的。 下面以“GE—FANUC”数控系统为例,介绍 数控冲床的加工编程。