国内外精密加工技术最新进展
超精密加工技术及其影响因素

超精密加工技术及其影响因素摘要:超精密加工是处于发展中的跨学科综合技术。
随着科技的发展,各个领域对零件的加工精度要求越来越高,传统的加工方法已满足不了需求,超精密加工依靠自动化技术可以达到纳米级的加工精度。
本文就国内外超精密机床加工研究现状做了简单介绍,概述了超精密加工的关键技术以及影响超精密加工的环境因素,为超精密加工在各行业的应用提供理论参考。
关键词:超精密加工;机床;纳米加工1 引言超精密加工技术在国防建设与国民经济发展中具有不可替代的作用,它是现代高技术战争的重要支撑技术,也是现代基础科学技术发展的重要保障。
超精密加工技术在航空航天、光学、医学和民用设备等都用很大作用。
从某种意义上说,超精密加工技术是衡量一个国家科技实力的重要标志之一。
超精密机床是实现超精密加工的关键载体,它直接决定了零件加工的精度、效率和可靠性。
由于超精密机床的重要性和特殊性,发达国家长期对我国进行技术封锁,因此研究和发展超精密机床对我国科技和工业的发展而言既具有重要的现实意义,也是必由之路[1]。
2 国内外超精密机床研究现状当前,超精密加工技术处于国际领先地位的主要有美国、英国和日本等,为此他们都曾设有专门研究机构,制定专门的研究计划,如20世纪80年代美国制定面向超精密机床研究的计划。
在工业界,美国,日本,德国,英国和源于精密工程研究所的等都研制了多种高端超精密机床,并有成熟的商品化产品,在20世纪60年代初就已开发了单点金刚石刀具切削技术及相应的超精密机床,以应对国防航天领域尖端技术的需要。
我国于20 世纪80年代初才开始超精密加工技术与机床方面的研究,起步较晚,近30年来,经过政府和相关研究单位的努力,取得了很大进步,某些方面达到了世界先进水平,如目前已经成功研制出回转精度达0. 025 μm的超精密轴系,并装备到超精密车床和铣床,解决了长期以来由于国外技术封锁给超精密机床开发带来的巨大阻力.但是,与国外发达国家相比,总体上还有不小的差距.目前,我国研究和开发超精密机床的单位主要有:北京机床研究所,北京航空精密机械研究所,哈尔滨工业大学,天津大学等。
精密冲裁技术国内外现状及其发展趋势
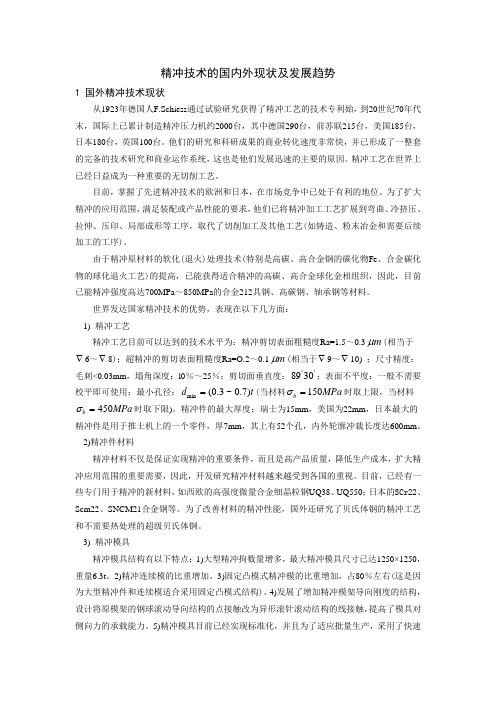
精冲技术的国内外现状及发展趋势1 国外精冲技术现状从1923年德国人F.Schiess 通过试验研究获得了精冲工艺的技术专利始,到20世纪70年代末,国际上已累计制造精冲压力机约2000台,其中德国290台,前苏联215台,美国185台,日本180台,英国100台。
他们的研究和科研成果的商业转化速度非常快,并已形成了一整套的完备的技术研究和商业运作系统,这也是他们发展迅速的主要的原因。
精冲工艺在世界上已经日益成为一种重要的无切削工艺。
目前,掌握了先进精冲技术的欧洲和日本,在市场竞争中已处于有利的地位。
为了扩大精冲的应用范围,满足装配或产品性能的要求,他们已将精冲加工工艺扩展到弯曲、冷挤压、拉伸、压印、局部成形等工序,取代了切削加工及其他工艺(如铸造、粉末冶金和需要后续加工的工序)。
由于精冲原材料的软化(退火)处理技术(特别是高碳、高合金钢的碳化物Fe 、合金碳化物的球化退火工艺)的提高,已能获得适合精冲的高碳、高合金球化金相组织,因此,目前已能精冲强度高达700MPa ~850MPa 的合金212具钢、高碳钢、轴承钢等材料。
世界发达国家精冲技术的优势,表现在以下几方面:1) 精冲工艺精冲工艺目前可以达到的技术水平为:精冲剪切表面粗糙度Ra=1.5~0.3m μ(相当于∇6~∇8);超精冲的剪切表面粗糙度Ra=O.2~0.1m μ(相当于∇9~∇10) ;尺寸精度:毛刺<0.03mm ,塌角深度:l0%~25%;剪切面垂直度:'8930︒;表面不平度:一般不需要校平即可使用;最小孔径:min (0.3~0.7)d t =(当材料150b MPa σ=时取上限,当材料450b MPa σ=时取下限)。
精冲件的最大厚度:瑞士为15mm ,美国为22mm ,日本最大的精冲件是用于推土机上的一个零件,厚7mm ,其上有52个孔,内外轮廓冲裁长度达600mm 。
2)精冲件材料精冲材料不仅是保证实现精冲的重要条件,而且是高产品质量,降低生产成本,扩大精冲应用范围的重要需要,因此,开发研究精冲材料越来越受到各国的重视。
精密制造发展现状

精密制造发展现状精密制造是指采用先进的技术和设备,通过精密的加工和组装过程,生产出高精度、高质量的产品的制造领域。
它广泛应用于各个行业,包括航空航天、汽车、电子、医疗器械等领域。
目前,精密制造在全球范围内取得了长足的发展。
首先,技术水平不断提升。
随着科技的进步,精密加工和制造技术不断创新,包括数控机床、激光加工、三维打印等新技术的应用,使得产品的精度、质量和效率得到了大幅度提高。
其次,产业链完善。
精密制造涉及到多个环节,从原材料提供商到零部件生产,再到最后的组装和测试,形成了一个完整的产业链。
越来越多的企业加大了精密制造的投入,形成了强大的供应链体系,进一步促进了精密制造的发展。
第三,市场需求旺盛。
精密制造的产品广泛应用于各个行业,市场需求量巨大。
特别是一些高科技行业,对于产品的精度和质量要求非常高,因此精密制造的市场潜力非常大。
然而,精密制造仍然面临一些挑战。
首先,成本较高。
精密制造需要使用高精度的机器和设备,而这些设备的价格较高,投入成本大。
其次,技术人才短缺。
精密制造对于技术人才的要求非常高,需要具备专业的知识和丰富的实践经验,而目前技术人才的供给严重不足。
此外,精密制造还面临着不断变化的市场需求和新兴技术的冲击,需要不断进行创新和转型。
因此,未来精密制造需要进一步努力,以应对挑战并取得更大的发展。
首先,需要加强技术创新,推动精密制造技术的发展,提高产品精度和质量,减少成本,提高效率。
其次,需要加大对技术人才的培养和引进力度,加强人才队伍建设,提高企业的竞争力。
此外,还需要加强合作,建立更加紧密的产业链,提高整个产业的协同效应。
最后,需要加强与市场的紧密联系,了解市场需求,及时调整生产和销售策略,以适应市场变化。
综上所述,精密制造在全球范围内得到了迅猛的发展,但仍然面临一些挑战。
未来,精密制造需要继续努力,加强技术创新、人才培养和市场合作,以取得更大的发展。
精密制造业的现状及发展趋势
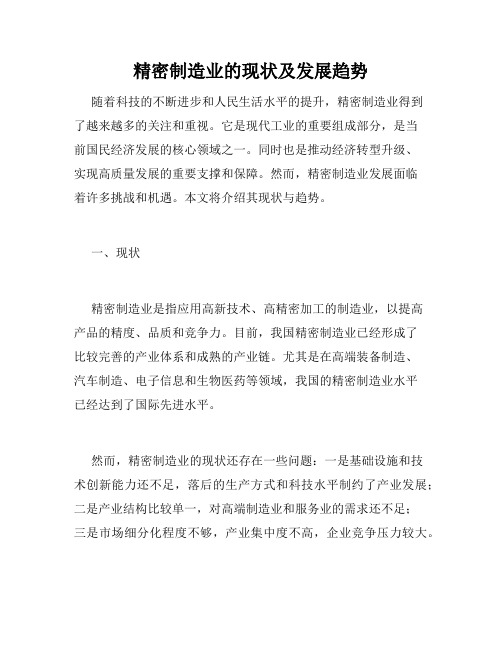
精密制造业的现状及发展趋势随着科技的不断进步和人民生活水平的提升,精密制造业得到了越来越多的关注和重视。
它是现代工业的重要组成部分,是当前国民经济发展的核心领域之一。
同时也是推动经济转型升级、实现高质量发展的重要支撑和保障。
然而,精密制造业发展面临着许多挑战和机遇。
本文将介绍其现状与趋势。
一、现状精密制造业是指应用高新技术、高精密加工的制造业,以提高产品的精度、品质和竞争力。
目前,我国精密制造业已经形成了比较完善的产业体系和成熟的产业链。
尤其是在高端装备制造、汽车制造、电子信息和生物医药等领域,我国的精密制造业水平已经达到了国际先进水平。
然而,精密制造业的现状还存在一些问题:一是基础设施和技术创新能力还不足,落后的生产方式和科技水平制约了产业发展;二是产业结构比较单一,对高端制造业和服务业的需求还不足;三是市场细分化程度不够,产业集中度不高,企业竞争压力较大。
二、发展趋势1. 聚焦高端装备制造制造业是国家经济的重要支撑,高端装备制造是制造业的核心和重点。
在高端装备制造领域,我国已逐渐成为全球的制造业强国之一。
未来,我国在这方面的投入和发展将继续加大,发展高端装备制造业已成为生产力和技术进步的关键。
2. 升级转型发展随着大数据、云计算、人工智能等科技的发展,未来制造业发展将越来越依赖于数字化和智能化。
制造企业需要在传统制造领域实现智能制造,同时进行电气化、自动化、信息化、网络化等方面的全面升级。
这样可以实现制造更加高效、灵活、智能。
3. 推动绿色制造制造业生产会伴随着不可避免的资源消耗和环境污染。
为了减少制造业的环境负担,未来精密制造业需要大力推进绿色制造,积极开展节能减排工作,推广清洁能源和环保型工艺、材料和产品等环保技术。
4. 加强环节协作生产制造目标的实现需要各个环节之间的密切配合与协同。
未来,我国精密制造业需要加强和完善协作机制,实现上下游产业链的紧密连接和无缝衔接。
同时,要加强各级政府之间的协调,为制造业的发展提供积极的政策支持。
超精密加工技术的发展现状
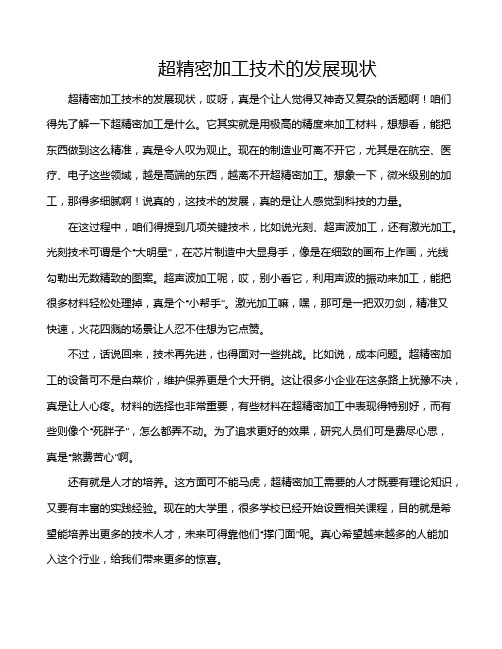
超精密加工技术的发展现状超精密加工技术的发展现状,哎呀,真是个让人觉得又神奇又复杂的话题啊!咱们得先了解一下超精密加工是什么。
它其实就是用极高的精度来加工材料,想想看,能把东西做到这么精准,真是令人叹为观止。
现在的制造业可离不开它,尤其是在航空、医疗、电子这些领域,越是高端的东西,越离不开超精密加工。
想象一下,微米级别的加工,那得多细腻啊!说真的,这技术的发展,真的是让人感觉到科技的力量。
在这过程中,咱们得提到几项关键技术,比如说光刻、超声波加工,还有激光加工。
光刻技术可谓是个“大明星”,在芯片制造中大显身手,像是在细致的画布上作画,光线勾勒出无数精致的图案。
超声波加工呢,哎,别小看它,利用声波的振动来加工,能把很多材料轻松处理掉,真是个“小帮手”。
激光加工嘛,嘿,那可是一把双刃剑,精准又快速,火花四溅的场景让人忍不住想为它点赞。
不过,话说回来,技术再先进,也得面对一些挑战。
比如说,成本问题。
超精密加工的设备可不是白菜价,维护保养更是个大开销。
这让很多小企业在这条路上犹豫不决,真是让人心疼。
材料的选择也非常重要,有些材料在超精密加工中表现得特别好,而有些则像个“死胖子”,怎么都弄不动。
为了追求更好的效果,研究人员们可是费尽心思,真是“煞费苦心”啊。
还有就是人才的培养。
这方面可不能马虎,超精密加工需要的人才既要有理论知识,又要有丰富的实践经验。
现在的大学里,很多学校已经开始设置相关课程,目的就是希望能培养出更多的技术人才,未来可得靠他们“撑门面”呢。
真心希望越来越多的人能加入这个行业,给我们带来更多的惊喜。
说到应用,超精密加工的舞台可大了!像航天器、手术刀、手机的内部零件等等,几乎无处不在。
你看看,航天器上那些复杂的零部件,没有超精密加工,恐怕就飞不起来了!还有手术刀,医生可不能用个普通的刀子,精细的切口直接关系到手术的成功与否,这可是关乎生命的大事啊!而手机的微小零件,哪个能离开超精密加工的加持?所以说,这技术的重要性,不用多说,大家都懂。
微纳米级精密加工技术最新进展

微纳米级精密加工技术最新进展微纳米级精密加工技术是当代科技发展的关键技术之一,它在信息技术、生物医疗、航空航天、光学制造等领域发挥着至关重要的作用。
随着科学技术的飞速进步,微纳米级精密加工技术不断取得突破,推动着相关产业的创新与升级。
以下是该领域最新进展的六个核心要点:一、超精密光刻技术的新突破超精密光刻技术作为微纳加工的核心技术,在半导体芯片制造中占据主导地位。
近年来,极紫外光刻(EUV)技术取得了重大进展,其波长缩短至13.5纳米,极大提高了图案分辨率,使得芯片上的元件尺寸进一步缩小,推动了摩尔定律的延续。
同时,多重曝光技术和计算光刻技术的结合应用,进一步提高了光刻精度,为实现更小特征尺寸的集成电路铺平了道路。
二、聚焦离子束加工技术的精细化聚焦离子束(FIB)技术以其高精度、灵活性强的特点,在微纳米结构的直接写入、修改及分析方面展现出了巨大潜力。
最近,通过优化离子源和束流控制系统,FIB技术实现了亚纳米级别的加工精度,为纳米器件的制备、纳米电路的修复及三维纳米结构的构建提供了强有力的技术支持。
此外,双束系统(FIB-SEM)的集成,即在同一平台上集成了聚焦离子束与扫描电子显微镜,大大提高了加工的准确性和效率。
三、激光微纳加工技术的创新应用激光加工技术在微纳米尺度上展现出了新的应用潜力,尤其是超短脉冲激光技术的出现,如飞秒激光,能够在材料表面进行无热影响区的精确加工,适用于复杂三维结构的制造。
通过调控激光参数,如脉冲宽度、能量密度和重复频率,可实现从材料表面改性到内部结构雕刻的广泛加工能力,被广泛应用于生物医疗植入物、微光学元件及微流控芯片的制造中。
四、化学气相沉积与电化学加工的精细化化学气相沉积(CVD)作为一种薄膜沉积技术,近年来在微纳米材料合成方面取得了显著进展,特别是在石墨烯、二维材料及其异质结构的可控生长方面。
通过精确调控反应条件,如温度、压力和气体配比,实现了单层或多层纳米薄膜的高质量沉积,为纳米电子学、能源存储及传感技术的发展提供了关键材料。
国外数控机床的发展现状
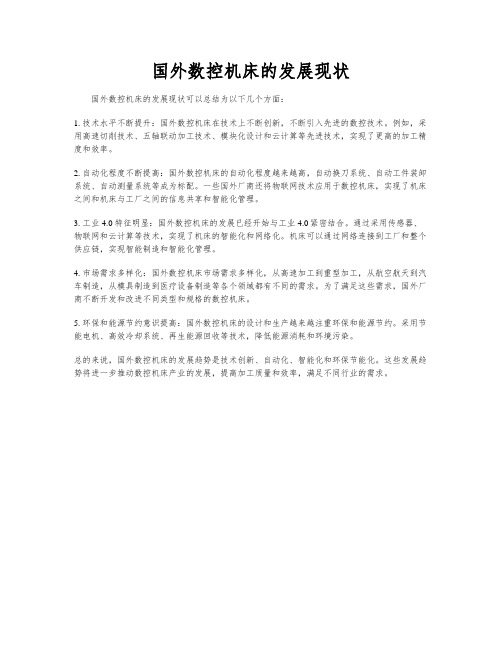
国外数控机床的发展现状
国外数控机床的发展现状可以总结为以下几个方面:
1. 技术水平不断提升:国外数控机床在技术上不断创新,不断引入先进的数控技术。
例如,采用高速切削技术、五轴联动加工技术、模块化设计和云计算等先进技术,实现了更高的加工精度和效率。
2. 自动化程度不断提高:国外数控机床的自动化程度越来越高,自动换刀系统、自动工件装卸系统、自动测量系统等成为标配。
一些国外厂商还将物联网技术应用于数控机床,实现了机床之间和机床与工厂之间的信息共享和智能化管理。
3. 工业
4.0 特征明显:国外数控机床的发展已经开始与工业4.0紧密结合。
通过采用传感器、物联网和云计算等技术,实现了机床的智能化和网络化。
机床可以通过网络连接到工厂和整个供应链,实现智能制造和智能化管理。
4. 市场需求多样化:国外数控机床市场需求多样化,从高速加工到重型加工,从航空航天到汽车制造,从模具制造到医疗设备制造等各个领域都有不同的需求。
为了满足这些需求,国外厂商不断开发和改进不同类型和规格的数控机床。
5. 环保和能源节约意识提高:国外数控机床的设计和生产越来越注重环保和能源节约。
采用节能电机、高效冷却系统、再生能源回收等技术,降低能源消耗和环境污染。
总的来说,国外数控机床的发展趋势是技术创新、自动化、智能化和环保节能化。
这些发展趋势将进一步推动数控机床产业的发展,提高加工质量和效率,满足不同行业的需求。
国外模具制造技术的现状和发展趋势
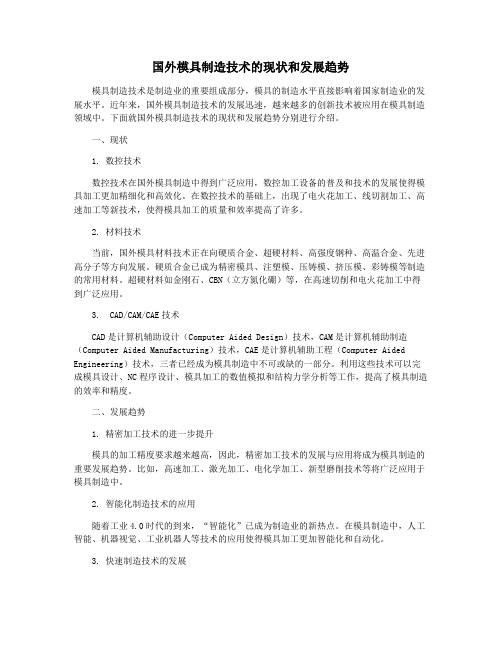
国外模具制造技术的现状和发展趋势模具制造技术是制造业的重要组成部分,模具的制造水平直接影响着国家制造业的发展水平。
近年来,国外模具制造技术的发展迅速,越来越多的创新技术被应用在模具制造领域中。
下面就国外模具制造技术的现状和发展趋势分别进行介绍。
一、现状1. 数控技术数控技术在国外模具制造中得到广泛应用,数控加工设备的普及和技术的发展使得模具加工更加精细化和高效化。
在数控技术的基础上,出现了电火花加工、线切割加工、高速加工等新技术,使得模具加工的质量和效率提高了许多。
2. 材料技术当前,国外模具材料技术正在向硬质合金、超硬材料、高强度钢种、高温合金、先进高分子等方向发展。
硬质合金已成为精密模具、注塑模、压铸模、挤压模、彩铸模等制造的常用材料。
超硬材料如金刚石、CBN(立方氮化硼)等,在高速切削和电火花加工中得到广泛应用。
3. CAD/CAM/CAE技术CAD是计算机辅助设计(Computer Aided Design)技术,CAM是计算机辅助制造(Computer Aided Manufacturing)技术,CAE是计算机辅助工程(Computer Aided Engineering)技术,三者已经成为模具制造中不可或缺的一部分。
利用这些技术可以完成模具设计、NC程序设计、模具加工的数值模拟和结构力学分析等工作,提高了模具制造的效率和精度。
二、发展趋势1. 精密加工技术的进一步提升模具的加工精度要求越来越高,因此,精密加工技术的发展与应用将成为模具制造的重要发展趋势。
比如,高速加工、激光加工、电化学加工、新型磨削技术等将广泛应用于模具制造中。
2. 智能化制造技术的应用随着工业4.0时代的到来,“智能化”已成为制造业的新热点。
在模具制造中,人工智能、机器视觉、工业机器人等技术的应用使得模具加工更加智能化和自动化。
3. 快速制造技术的发展在大型化、多品种、小批量的生产需求下,快速制造技术的发展势头迅猛。
精密加工行业报告

精密加工行业报告精密加工是一种高精度的机械加工技术,它在各种行业中都有着广泛的应用。
随着科技的不断发展和进步,精密加工行业也在不断壮大和壮大。
本报告将对精密加工行业的发展现状、市场需求、技术趋势等方面进行分析和展望。
一、精密加工行业的发展现状。
随着科技的不断进步和发展,精密加工行业也在不断壮大。
目前,全球精密加工行业的市场规模已经达到了数千亿美元。
在中国,精密加工行业也在快速发展,成为了国民经济中不可或缺的一部分。
从国内外市场来看,精密加工行业的需求量也在不断增加,市场潜力巨大。
二、精密加工行业的市场需求。
精密加工行业的市场需求主要来自于汽车、航空航天、电子、医疗器械、光学仪器等行业。
随着这些行业的不断发展,对精密加工零部件的需求也在不断增加。
特别是在汽车和航空航天行业,对零部件的精度和质量要求非常高,这就对精密加工行业提出了更高的要求。
三、精密加工行业的技术趋势。
随着科技的不断进步,精密加工行业的技术也在不断更新和改进。
目前,数控机床、激光加工、电火花加工、超声波加工等先进技术已经在精密加工行业中得到了广泛应用。
这些先进技术不仅提高了加工效率,还提高了加工精度,降低了成本,提高了产品质量。
四、精密加工行业的发展趋势。
未来,精密加工行业将会朝着智能化、自动化、数字化的方向发展。
随着人工智能、大数据、云计算等技术的不断发展,精密加工行业将会迎来新的发展机遇。
同时,随着全球制造业的转移和升级,精密加工行业也将会面临更大的市场机遇和挑战。
总之,精密加工行业是一个充满活力和发展潜力的行业。
随着科技的不断发展和进步,精密加工行业也将迎来新的发展机遇。
我们相信,在政府的政策支持和企业的不懈努力下,精密加工行业一定会迎来更加美好的未来。
精密和超精密加工技术的发展
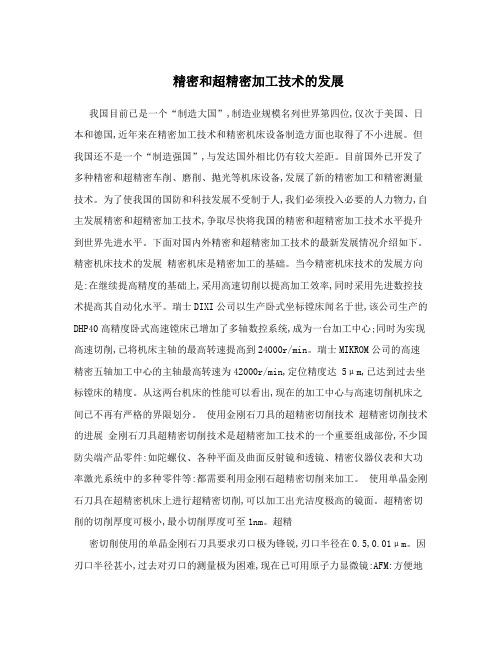
精密和超精密加工技术的发展我国目前已是一个“制造大国”,制造业规模名列世界第四位,仅次于美国、日本和德国,近年来在精密加工技术和精密机床设备制造方面也取得了不小进展。
但我国还不是一个“制造强国”,与发达国外相比仍有较大差距。
目前国外已开发了多种精密和超精密车削、磨削、抛光等机床设备,发展了新的精密加工和精密测量技术。
为了使我国的国防和科技发展不受制于人,我们必须投入必要的人力物力,自主发展精密和超精密加工技术,争取尽快将我国的精密和超精密加工技术水平提升到世界先进水平。
下面对国内外精密和超精密加工技术的最新发展情况介绍如下。
精密机床技术的发展精密机床是精密加工的基础。
当今精密机床技术的发展方向是:在继续提高精度的基础上,采用高速切削以提高加工效率,同时采用先进数控技术提高其自动化水平。
瑞士DIXI公司以生产卧式坐标镗床闻名于世,该公司生产的DHP40高精度卧式高速镗床已增加了多轴数控系统,成为一台加工中心;同时为实现高速切削,已将机床主轴的最高转速提高到24000r/min。
瑞士MIKROM公司的高速精密五轴加工中心的主轴最高转速为42000r/min,定位精度达5μm,已达到过去坐标镗床的精度。
从这两台机床的性能可以看出,现在的加工中心与高速切削机床之间已不再有严格的界限划分。
使用金刚石刀具的超精密切削技术超精密切削技术的进展金刚石刀具超精密切削技术是超精密加工技术的一个重要组成部份,不少国防尖端产品零件:如陀螺仪、各种平面及曲面反射镜和透镜、精密仪器仪表和大功率激光系统中的多种零件等:都需要利用金刚石超精密切削来加工。
使用单晶金刚石刀具在超精密机床上进行超精密切削,可以加工出光洁度极高的镜面。
超精密切削的切削厚度可极小,最小切削厚度可至1nm。
超精密切削使用的单晶金刚石刀具要求刃口极为锋锐,刃口半径在0.5,0.01μm。
因刃口半径甚小,过去对刃口的测量极为困难,现在已可用原子力显微镜:AFM:方便地进行测量。
我国精密加工的现状及发展趋势

我国精密加工的现状及发展趋势内容摘要:近十年来,美国十分注重发展精密热加工和提高性能一体化技术。
如:铝锂合金粉制件精密热成形可使零件比刚度提高30%;碳化硅/铝复合材料可使零件的比刚度提高30%一75%;单晶叶片精铸可以提高涡轮温度55℃、节省燃料10%;快速凝固粉末层压式涡轮叶片,可使发动机涡轮温度提高220℃、油耗降低8.4%、飞机起飞质量降低7.4%,发动机推重比提高30%一50%。
发展精密热加工技术,并与提高零部件性能研究一体化,符合我国国防科技发展对关键基础加工技术研究所提出的要求。
正文:一、精密和超精密加工的概念与范畴通常,按加工精度划分,机械加工可分为一般加工、精密加工、超精密加工三个阶段。
目前,精密加工是指加工精度为1~0.1?;m,表面粗糙度为Ra0.1~0.01?;m的加工技术,但这个界限是随着加工技术的进步不断变化的,今天的精密加工可能就是明天的一般加工。
精密加工所要解决的问题,一是加工精度,包括形位公差、尺寸精度及表面状况;二是加工效率,有些加工可以取得较好的加工精度,却难以取得高的加工效率。
精密加工包括微细加工和超微细加工、光整加工等加工技术。
传统的精密加工方法有砂带磨削、精密切削、珩磨、精密研磨与抛光等。
a.砂带磨削是用粘有磨料的混纺布为磨具对工件进行加工,属于涂附磨具磨削加工的范畴,有生产率高、表面质量好、使用范围广等特点。
b.精密切削,也称金刚石刀具切削(SPDT),用高精密的机床和单晶金刚石刀具进行切削加工,主要用于铜、铝等不宜磨削加工的软金属的精密加工,如计算机用的磁鼓、磁盘及大功率激光用的金属反光镜等,比一般切削加工精度要高1~2个等级。
c.珩磨,用油石砂条组成的珩磨头,在一定压力下沿工件表面往复运动,加工后的表面粗糙度可达Ra0.4~0.1?;m,最好可到Ra0.025?;m,主要用来加工铸铁及钢,不宜用来加工硬度小、韧性好的有色金属。
d.精密研磨与抛光通过介于工件和工具间的磨料及加工液,工件及研具作相互机械摩擦,使工件达到所要求的尺寸与精度的加工方法。
国内外先进制造技术的新发展现状和趋势解读[5篇范例]
![国内外先进制造技术的新发展现状和趋势解读[5篇范例]](https://img.taocdn.com/s3/m/0d674a71b207e87101f69e3143323968011cf42a.png)
国内外先进制造技术的新发展现状和趋势解读[5篇范例]第一篇:国内外先进制造技术的新发展现状和趋势解读国内外先进制造技术的新发展现状和趋势1 当前制造科学要解决的问题(1)制造系统是一个复杂的大系统,为满足制造系统敏捷性、快速响应和快速重组的能力,必须借鉴信息科学、生命科学和社会科学等多学科的研究成果,探索制造系统新的体系结构、制造模式和制造系统有效的运行机制。
制造系统优化的组织结构和良好的运行状况是制造系统建模、仿真和优化的主要目标。
制造系统新的体系结构不仅对制造企业的敏捷性和对需求的响应能力及可重组能力有重要意义,而且对制造企业底层生产设备的柔性和可动态重组能力提出了更高的要求。
生物制造观越来越多地被引入制造系统,以满足制造系统新的要求。
(2)为支持快速敏捷制造,几何知识的共享已成为制约现代制造技术中产品开发和制造的关键问题。
例如在计算机辅助设计与制造(CAD/CAM)集成、坐标测量(CMM)和机器人学等方面,在三维现实空间(3-Real Space)中,都存在大量的几何算法设计和分析等问题,特别是其中的几何表示、几何计算和几何推理问题;在测量和机器人路径规划及零件的寻位(如Localization)等方面,存在C-空间(配置空间Configuration Space)的几何计算和几何推理问题;在物体操作(夹持、抓取和装配等)描述和机器人多指抓取规划、装配运动规划和操作规划方面则需要在旋量空间(Screw Space)进行几何推理。
制造过程中物理和力学现象的几何化研究形成了制造科学中几何计算和几何推理等多方面的研究课题,其理论有待进一步突破,当前一门新学科--计算机几何正在受到日益广泛和深入的研究。
3)在现代制造过程中,信息不仅已成为主宰制造产业的决定性因素,而且还是最活跃的驱动因素。
提高制造系统的信息处理能力已成为现代制造科学发展的一个重点。
由于制造系统信息组织和结构的多层次性,制造信息的获取、集成与融合呈现出立体性、信息度量的多维性、以及信息组织的多层次性。
精密加工技术的发展现状与应用
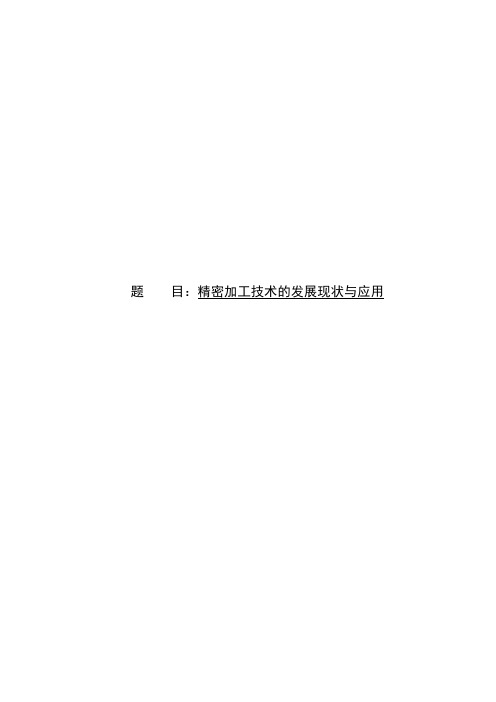
题目:精密加工技术的发展现状与应用内容摘要通过砂带研磨、精密切削、超精密磨削、珩磨、精密研磨、抛光等几种传统精密加工方法的论述对比,论述现有的传统精密加工方法;再通过对孔加工技术等技术的最新精密加工发展来论述目前国内精密加工发展趋势及前景;同时通过对美日欧等发达国家最新的精密加工技术发展情况来论述目前国外精密加工技术的发展方向及前景。
关键词:精加工;发展;应用内容摘要 (I)引言 (1)1 精密加工技术的发展现状 (1)1.1 砂带研磨 (1)1.2 精密切削 (1)1.3 超精密磨削 (2)1.4 珩磨 (3)1.5 精密研磨 (3)1.6 抛光 (3)2 国内精密加工技术发展趋势 (5)2.1 北京机床研究所 .............................................................. 错误!未定义书签。
2.2 航天航空工业部三零三部所 .......................................... 错误!未定义书签。
3.3 其他研究所 ...................................................................... 错误!未定义书签。
3.4 超精密加工技术发展趋势 .............................................. 错误!未定义书签。
3 国外精密加工技术发展前景 (8)3.1 美国 (8)3.1 欧洲 (8)3.2 日本 (8)4 研究和探讨 (9)4.1 精密加工技术 (9)4.2 开发精密的机械机构 (9)4.3 开发高精度的测试系统 (9)4.4 开发适用于精密加工并能取得高精度、高表面质量的新型材料 (10)5 结论 (11)参考文献 (12)为了满足现代先进制造与加工技术的需要,提高生产效率和改善零件的加工质量,精密加工技术和超精密加工技术已成为目前高科技技术领域的基础,超精密加工技术已成为社会生产发展的一个重大趋势。
精密和超精密加工技术的新进展
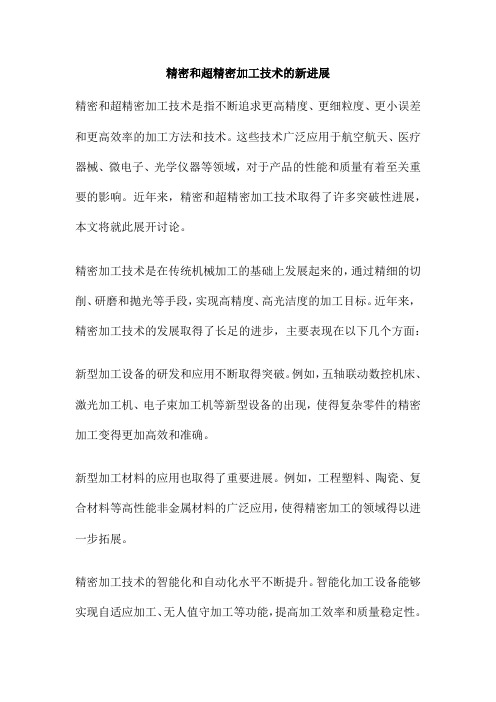
精密和超精密加工技术的新进展精密和超精密加工技术是指不断追求更高精度、更细粒度、更小误差和更高效率的加工方法和技术。
这些技术广泛应用于航空航天、医疗器械、微电子、光学仪器等领域,对于产品的性能和质量有着至关重要的影响。
近年来,精密和超精密加工技术取得了许多突破性进展,本文将就此展开讨论。
精密加工技术是在传统机械加工的基础上发展起来的,通过精细的切削、研磨和抛光等手段,实现高精度、高光洁度的加工目标。
近年来,精密加工技术的发展取得了长足的进步,主要表现在以下几个方面:新型加工设备的研发和应用不断取得突破。
例如,五轴联动数控机床、激光加工机、电子束加工机等新型设备的出现,使得复杂零件的精密加工变得更加高效和准确。
新型加工材料的应用也取得了重要进展。
例如,工程塑料、陶瓷、复合材料等高性能非金属材料的广泛应用,使得精密加工的领域得以进一步拓展。
精密加工技术的智能化和自动化水平不断提升。
智能化加工设备能够实现自适应加工、无人值守加工等功能,提高加工效率和质量稳定性。
超精密加工技术是指比精密加工技术更为精细、精确的加工方法和技术。
随着科技的不断进步,超精密加工技术的应用越来越广泛,主要包括以下几个方面:超精密加工技术广泛应用于微电子领域。
微电子产业对于芯片的精度和光洁度要求极高,超精密加工技术能够实现高精度、高效率的微米级加工,对于提升微电子产业的发展水平和竞争力具有重要意义。
超精密加工技术在光学仪器领域也有着广泛的应用。
光学仪器对于透镜、反射镜等光学元件的精度和表面质量要求极高,超精密加工技术能够实现高精度、高稳定性的光学元件加工,对于提高光学仪器的性能和精度具有重要作用。
再次,超精密加工技术在航空航天领域也有着重要的应用。
航空航天领域对于零件的精度和可靠性要求极为严格,超精密加工技术能够实现高精度、高稳定性的零件加工,对于提升航空航天领域的产品质量和性能具有重要意义。
近年来,精密和超精密加工技术的研究和应用不断取得新的进展,在新型加工设备、新型加工材料和智能化加工等方面都取得了重要突破。
国内外精密加工技术最新进展
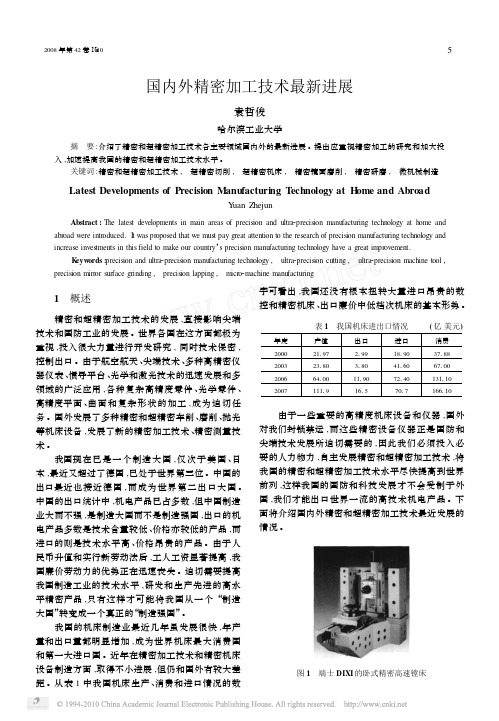
国内外精密加工技术最新进展袁哲俊哈尔滨工业大学摘 要:介绍了精密和超精密加工技术各主要领域国内外的最新进展。
提出应重视精密加工的研究和加大投入,加速提高我国的精密和超精密加工技术水平。
关键词:精密和超精密加工技术, 超精密切削, 超精密机床, 精密镜面磨削, 精密研磨, 微机械制造Latest Developments of Precision Manu facturing T echnology at H ome and AbroadY uan ZhejunAbstract:The latest developments in main areas of precision and ultra2precision manu facturing technology at home and abroad were introduced.I t was proposed that we must pay great attention to the research of precision manu facturing technology and increase investments in this field to make our country’s precision manu facturing technology have a great im provement.K eyw ords:precision and ultra2precision manu facturing technology, ultra2precision cutting, ultra2precision machine tool, precision mirror sur face grinding, precision lapping, micro2machine manu facturing 1 概述精密和超精密加工技术的发展,直接影响尖端技术和国防工业的发展。
国外超精密加工技术的现状和发展趋势

国外超精密加工技术的现状和发展趋势1. 引言在当今世界,超精密加工技术已经成为了制造业的重要组成部分。
随着科技的不断发展,国外的超精密加工技术也取得了长足的进步。
本文将从多个角度对国外超精密加工技术的现状和发展趋势进行评估和探讨。
2. 现状分析超精密加工技术是指在微米或纳米级别进行加工的技术,其精度和表面质量要求非常高。
当前,国外一些先进制造业发达国家,如日本、德国和美国等,都在超精密加工技术领域具有举足轻重的地位。
这些国家的企业和研究机构不断推动着超精密加工技术的发展,不断推陈出新,取得了许多创新成果。
3. 技术发展趋势未来,国外超精密加工技术将朝着更高精度、更复杂形状、更多材料的加工方向发展。
随着人工智能、大数据和物联网等新一代信息技术的不断涌现,超精密加工技术将更加智能化、数字化和柔性化。
新型材料、纳米技术的应用,也将极大地拓展超精密加工技术的应用范围。
4. 我的观点我认为,国外超精密加工技术的快速发展将为全球制造业带来深远影响。
随着超精密加工技术在航空航天、医疗器械、电子器件等领域的广泛应用,将极大地推动相关产业的发展。
超精密加工技术的不断突破也将为人类社会带来更多便利和可能性。
5. 总结国外超精密加工技术的现状和发展趋势令人振奋。
技术不断创新,应用领域不断拓展,为制造业注入了新的活力。
我对超精密加工技术的未来充满信心,相信它将在全球范围内发挥越来越重要的作用。
通过本文的介绍和分析,相信您已经对国外超精密加工技术的现状和发展趋势有了更深入的了解。
希望本文能够为您带来一些启发和思考,并对您在相关领域的学习和工作有所帮助。
超精密加工技术在国外的发展已经取得了显著的进步,但仍有许多挑战和机遇。
在不断推动超精密加工技术的发展的国外也在积极探索新的技术路径和应用领域,以应对日益复杂的市场需求和竞争压力。
国外超精密加工技术在材料加工和表面处理方面取得了重大突破。
随着新型材料的广泛应用和纳米技术的发展,超精密加工技术已经能够处理更多种类的材料,包括金属、陶瓷、复合材料等。
精密和超精密加工技术现状和发展趋势

精密和超精密加工技术现状和发展趋势1.引言国际上在超精密加工技术方面处于领先地位的国家有美国、德国和日本发达国家中,美国、日本、德国等在高技术领域(如国防工业、集成电路、信息技术产业等)之所以一直领先,与这些国家高度重视和发展精密、超精密制造技术有极其重要的关系。
由于加工技术水平的发展,精密和超精密加工划分的界限逐渐向前推移,但在具体数值上没有确切的定义。
被加工零件的尺寸精度在 1.0~0.1μm,表面粗糙度Ra在0.1~0.03μm之间的加工方法称为精密加工。
超精密加工当前是指被加工零件的尺寸精度高于0.1μm,表面粗糙度Ra小于0.025μm,以及所用机床定位精度的分辨率和重复性高于0.01μm的加工技术,亦称之为亚微米级加工技术,且正在向纳米级加工技术发展超精密加工技术主要包括:超精密加工的机理,超精密加工的设备制造技术,超精密加工工具及刃磨技术,超精密测量技术和误差补偿技术,超精密加工工作环境条件。
2.发展现状美国是开展研究最早的国家,也是迄今处于世界领先地位的国家。
早在50年代末,由于航天等尖端技术发展的需要,美国首先发展了金刚石刀具的超精密切削技术,并发展了相应的空气轴承主轴的超精密机床,用于加工激光核聚变反射镜、战术导弹及载人飞船用球面、非球面大型零件。
20世纪80年代后期,美国通过能源部“激光核聚变项目”和陆、海、空三军“先进制造技术开发计划”,对超精密金刚石切削机床的开发研究,投入了巨额资金和大量人力,实现了大型零件的微英寸超精密加工。
如美国劳伦斯利弗莫尔国家实验室已经研制出一台大型光学金刚石车床(Large Op tics Diam ond Turn ing Machine, LODTM ), 是一台最大加工直径为1.63m的立式车床,定位精度可达28nm,借助在线误差补偿能力,它已实现了距离超过1m而直线度误差只有±25nm 的加工。
在美国能源部支持下,LLI实验室和Y-12工厂合作,与1983年成功地研制出大型超精密金刚石车床(DTM—3型)。
精密与超精密加工技术现状和发展展望

精密与超精密加工技术现状和发展展望精密加工技术是一种在当今制造业中非常重要的技术,它的发展与制造业的发展息息相关。
精密加工技术是通过对材料进行高精度的加工来制造出各种精密零部件,这些精密零部件被广泛应用于汽车、航空航天、医疗器械、电子产品等各个领域。
现阶段,精密加工技术已经取得了很大的进步,各种高精度的加工设备和加工工艺层出不穷。
在这些技术发展的基础上,超精密加工技术应运而生。
超精密加工技术是一种相对于精密加工技术更加高端、更加精密的加工技术,它可以实现对材料的超高精度加工,甚至可以达到纳米级的精度。
这种技术对于一些特殊材料的加工非常重要,比如硬质合金、钢、陶瓷等材料。
超精密加工技术的发展展望是非常乐观的。
随着科学技术的不断进步,各种先进的加工设备和工艺将不断涌现。
在这种趋势下,超精密加工技术将会得到更加广泛的应用。
在汽车工业中,超精密加工技术可以用于制造高压油泵的零部件,提高汽车发动机燃油的利用率;在医疗器械领域,超精密加工技术可以用于制造各种医疗器械的零部件,提高医疗器械的精度和安全性。
在未来的发展中,我们还可以看到超精密加工技术将会在航空航天领域得到更广泛的应用。
超精密加工技术可以制造出更加轻巧和高强度的航空零部件,提高航空器的性能和安全性。
超精密加工技术在电子产品领域也有很大的潜力,它可以制造出更小巧、更精密的电子元件,提高电子产品的性能和可靠性。
精密加工技术和超精密加工技术的发展是非常重要的。
它们直接关系到制造业的发展和产品的质量。
相信随着科学技术的不断进步,这些技术将会取得更大的突破,为各个领域带来更多的创新和发展。
精密与超精密加工技术的现状和发展展望精密加工技术是制造业中至关重要的一环,它的发展与制造业的发展密不可分。
精密加工技术通过对材料进行高精度的加工,制造出各种精密零部件,广泛应用于汽车、航空航天、医疗器械、电子产品等各个领域。
当前,精密加工技术已取得了长足的发展,各种高精度加工设备和工艺不断涌现。
低应力高效精密加工国外发展现状
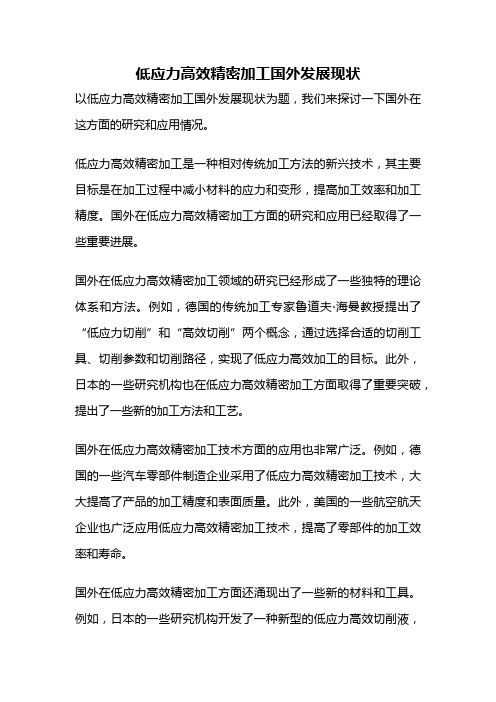
低应力高效精密加工国外发展现状
以低应力高效精密加工国外发展现状为题,我们来探讨一下国外在这方面的研究和应用情况。
低应力高效精密加工是一种相对传统加工方法的新兴技术,其主要目标是在加工过程中减小材料的应力和变形,提高加工效率和加工精度。
国外在低应力高效精密加工方面的研究和应用已经取得了一些重要进展。
国外在低应力高效精密加工领域的研究已经形成了一些独特的理论体系和方法。
例如,德国的传统加工专家鲁道夫·海曼教授提出了“低应力切削”和“高效切削”两个概念,通过选择合适的切削工具、切削参数和切削路径,实现了低应力高效加工的目标。
此外,日本的一些研究机构也在低应力高效精密加工方面取得了重要突破,提出了一些新的加工方法和工艺。
国外在低应力高效精密加工技术方面的应用也非常广泛。
例如,德国的一些汽车零部件制造企业采用了低应力高效精密加工技术,大大提高了产品的加工精度和表面质量。
此外,美国的一些航空航天企业也广泛应用低应力高效精密加工技术,提高了零部件的加工效率和寿命。
国外在低应力高效精密加工方面还涌现出了一些新的材料和工具。
例如,日本的一些研究机构开发了一种新型的低应力高效切削液,
可以在加工过程中有效减小材料的应力和变形。
此外,德国的一些研究机构还开发了一种新型的低应力切削工具,可以实现更高效的切削和更精确的加工。
总的来说,国外在低应力高效精密加工方面的研究和应用已经取得了一些重要进展。
未来,我们可以借鉴国外的经验和成果,进一步推动我国低应力高效精密加工技术的发展,提高我国制造业的竞争力和创新能力。
激光加工技术的现状及国内外发展趋势

激光加工技术的现状及国内外发展趋势目前,激光加工技术在国内外都得到了快速发展。
在国内,激光加工领域的研究和应用逐渐增多,涉及的领域包括电子、汽车、航天航空、医疗器械等。
随着高新技术的不断推广和应用,激光加工技术也在向多领域、高价值的方向发展。
在国外,激光加工技术早已发展到一定程度,拥有许多成熟的应用案例。
尤其是在汽车工业和航空航天领域,激光切割和激光焊接等技术已经得到广泛应用。
同时,一些发达国家也对激光加工技术进行了深入研究,投入大量资金用于激光加工设备的研发和创新。
随着激光加工技术的不断发展,国内外的发展趋势也逐渐清晰。
首先,激光加工技术将实现高速化和高精度化。
通过提高激光功率、优化激光光束质量和加工参数等手段,实现激光加工速度的提升和加工精度的提高。
其次,激光加工技术将越来越多地应用于大型工件和复杂结构的加工。
通过引入机器人、自动化设备和在线测量系统等,解决大型工件加工难题,提高生产效率和质量。
同时,激光加工技术也将拓展到新材料和特殊材料的加工领域,如复合材料、高温合金等。
最后,激光加工技术将更加注重绿色环保和能源节约。
通过改进激光加工工艺,提高能源利用率和降低废料产生,实现绿色环保的加工方式。
在国内,政府将进一步加大对激光加工技术的支持力度,加大对激光科研机构的投入和培养激光加工人才的力度。
同时,国内一些大型企业也会加大对激光加工设备的研发和引进力度,提高自主创新能力。
国外方面,一些发达国家将加强对激光加工技术的研究和应用,进一步提高激光加工设备的性能和质量。
总的来说,激光加工技术在国内外都有着广阔的发展前景。
未来,激光加工技术将继续向高速、高精度、多功能的方向发展,为各个行业提供更加高效、绿色、智能的加工解决方案。
- 1、下载文档前请自行甄别文档内容的完整性,平台不提供额外的编辑、内容补充、找答案等附加服务。
- 2、"仅部分预览"的文档,不可在线预览部分如存在完整性等问题,可反馈申请退款(可完整预览的文档不适用该条件!)。
- 3、如文档侵犯您的权益,请联系客服反馈,我们会尽快为您处理(人工客服工作时间:9:00-18:30)。
国内外精密加工技术最新进展袁哲俊哈尔滨工业大学摘 要:介绍了精密和超精密加工技术各主要领域国内外的最新进展。
提出应重视精密加工的研究和加大投入,加速提高我国的精密和超精密加工技术水平。
关键词:精密和超精密加工技术, 超精密切削, 超精密机床, 精密镜面磨削, 精密研磨, 微机械制造Latest Developments of Precision Manu facturing T echnology at H ome and AbroadY uan ZhejunAbstract:The latest developments in main areas of precision and ultra2precision manu facturing technology at home and abroad were introduced.I t was proposed that we must pay great attention to the research of precision manu facturing technology and increase investments in this field to make our country’s precision manu facturing technology have a great im provement.K eyw ords:precision and ultra2precision manu facturing technology, ultra2precision cutting, ultra2precision machine tool, precision mirror sur face grinding, precision lapping, micro2machine manu facturing 1 概述精密和超精密加工技术的发展,直接影响尖端技术和国防工业的发展。
世界各国在这方面都极为重视,投入很大力量进行开发研究,同时技术保密,控制出口。
由于航空航天、尖端技术、多种高精密仪器仪表、惯导平台、光学和激光技术的迅速发展和多领域的广泛应用,各种复杂高精度零件、光学零件、高精度平面、曲面和复杂形状的加工,成为迫切任务。
国外发展了多种精密和超精密车削、磨削、抛光等机床设备,发展了新的精密加工技术、精密测量技术。
我国现在已是一个制造大国,仅次于美国、日本,最近又超过了德国,已处于世界第三位。
中国的出口最近也接近德国,而成为世界第二出口大国。
中国的出口统计中,机电产品已占多数,但中国制造业大而不强,是制造大国而不是制造强国,出口的机电产品多数是技术含量较低、价格亦较低的产品,而进口的则是技术水平高、价格昂贵的产品。
由于人民币升值和实行新劳动法后,工人工资显著提高,我国廉价劳动力的优势正在迅速丧失。
迫切需要提高我国制造工业的技术水平,研发和生产先进的高水平精密产品,只有这样才可能将我国从一个“制造大国”转变成一个真正的“制造强国”。
我国的机床制造业最近几年虽发展很快,年产量和出口量都明显增加,成为世界机床最大消费国和第一大进口国。
近年在精密加工技术和精密机床设备制造方面,取得不小进展,但仍和国外有较大差距。
从表1中我国机床生产、消费和进口情况的数字可看出,我国还没有根本扭转大量进口昂贵的数控和精密机床、出口廉价中低档次机床的基本形势。
表1 我国机床进出口情况(亿美元)年度产值出口进口消费2000211972199181903718820032318031804116067100200664100111907214013111020071111916157017166110由于一些重要的高精度机床设备和仪器,国外对我们封锁禁运,而这些精密设备仪器正是国防和尖端技术发展所迫切需要的,因此我们必须投入必要的人力物力,自主发展精密和超精密加工技术,将我国的精密和超精密加工技术水平尽快提高到世界前列,这样我国的国防和科技发展才不会受制于外国,我们才能出口世界一流的高技术机电产品。
下面将介绍国内外精密和超精密加工技术最近发展的情况。
图1 端士DIXI的卧式精密高速镗床图2 瑞士MIKR ON 高速精密五轴加工中心 2 精密机床技术的发展精密机床是精密加工的基础。
现在精密机床技术的发展方向是:在继续提高精度的基础上采用高速切削以提高效率,同时采用数控使其自动化。
瑞士DIXI 公司以生产卧式坐标镗床闻名于世,现在该厂生产的高精度镗床DHP40(图1)已加上多轴数控系统成为加工中心,同时为使用高速切削,已将主轴最高转速提高到24000r/min 。
图2所示是瑞士MIK ROM 公司的高速精密五轴加工中心,它的主轴最高转速为42000r/min ,定位精度达到5μm ,已达到过去坐标镗床的精度。
从这两台机床的性能看,现在精密机床、加工中心和高速切削机床已不再有严格的界限区分。
3 金刚石刀具超精密切削311 超精密切削技术的进展金刚石刀具超精密切削是超精密加工中的很重要部份,不少国防尖端产品零件,如陀螺仪、各种平面曲面反射镜和透镜、精密仪器仪表和大功率激光系统中的多种零件等,需要用超精密切削来加工。
超精密切削使用单晶金刚石刀具,在超精密机床上可以加工出镜面。
超精密切削的切削厚度可以极小,最小切削厚度可以到1nm (如图3所示)。
超精密切削使用的单晶金刚石刀具是重要关键,要求刃口磨得极为锋锐,刃口半径在015~0101μm 。
因刃口半径甚小,过去测量极为困难,现在可以用原子力显微镜(AF M )进行测量,测量就比较方便。
图4中是用AF M 测量金刚石刀具刃口半径得到的测量结果。
图3 超精密切削的切削厚度(Ik a w a)图4 使用AFM 检测金刚石刀具刃口半径312 超精密切削机理的研究超精密切削机理的研究近年来亦有不少进展。
例如超精密切削脆性材料时,加工表面可以不产生脆性破裂痕迹而得到镜面,这涉及极薄切削时的脆性材料塑性切除的脆塑转换问题,最近提出不少新见解。
图5中所示,是超精密切削玻璃时的实验结果,可见到开始时切削厚度甚小,切除为塑性去除,加工表面无脆性破损痕迹。
随切削厚度增加,塑性切除逐渐转化成脆性破裂去除,加工表面可看到明显的脆性破损痕迹。
图5 超精密切削玻璃时的脆塑转变图6 超精密切削表面形貌的仿真图7 超精密切削的分子动力学模拟对于超精密切削的过程机理研究,现在使用计算机仿真和分子动力学模拟等方法,获得很好的效果,它一方面可以加深对极薄层材料切削去除机理的认识,同时可对切削效果作预报。
图6中所示是超精密切削时所形成的加工表面的计算机仿真模拟预测。
图7中所示,是对超精密切削过程的计算机仿真分子动力学模拟,采用该方法可看到切削极薄层材料时的动态切除过程,能对切除过程作动画演示。
超精密切削单晶材料时,由于单晶材料的各向异性、晶向不同,将明显影响加工表面质量和切削力。
图8中所示,是超精密车削单晶LiNbO 3端面,可明显看到由于晶向不同而使表面粗糙度有差别。
图9所示,是超精密车削单晶铜的不同晶面时实测所得切削力,可看到晶向不同时切削力有较大差别。
计算机仿真预测超精密切削单晶铜的不同晶面时的切削力,得到类似的结果。
图8 超精密车削单晶LiNbO 3(110)晶面时的表面粗糙度(a )(110)晶面 (b )(100)晶面 (c )(111)晶面图9 超精密切削单晶铜时不同晶面的切削力313 金刚石刀具晶体的新定向方法单晶金刚石刀具由于金刚石硬度极高,且晶体各向异性,刃磨极为不易。
制造金刚石刀具和刃磨都需要晶体定向,过去使用X 光晶体定向仪来定向,需要很贵重的仪器并且定向很费事。
哈尔滨工业大学研制成功激光晶体定向新方法,设备较简单,且操作方便,使金刚石晶体的定向大大简化。
图10是金刚石激光晶体定向原理图,图11中是金刚石不同晶面的代表符号(上)、不同晶面的激光定向图像(中)和显示晶体结构的各晶面的扫描电子显微镜(SE M )图像(下)。
图10 金刚石激光晶体定向原理图11 金刚石不同晶面激光定向图像 4 超精密机床的进展411 国外超精密机床发展情况发展超精密机床是发展超精密加工的极重要内容。
各发达国家都发展了多种超精密机床。
超精密机床的发展方向:进一步提高超精密机床的精度,发展大型超精密机床,发展多功能和高效专用超精密机床。
美国、英国、德国等在上个世纪70年代、日本在80年代,即开始生产超精密机床产品,可以批量供应。
大型超精密机床方面,美国于1986年由LLL 国家实验室研制成功加工直径211m 的卧式DT M -3金刚石车床和加工直径1165m 的LODT M 立式大型光学金刚石车床等两台大型超精金刚石车床,其中LODT M 立式大型光学金刚石车床被公认为世界上精度最高的超精密机床。
美国后来又研制了大型6轴数控精密研磨机,用于加工大型光学反射镜。
英国Cran field 精加工中心于1991年研制成OAG M -2500(工作台面积2500mm ×2500mm )多功能三坐标联动数控磨床,可加工(磨削、车削)和测量精密自由曲面,并且用此机床采用加工件拼合方法,加工成天文望远镜中的直径715m 的大型反射镜。
日本的多功能和高效专用超精密机床发展较好,促进了日本微电子和家电工业的发展。
现在国外生产的中型超精密机床产品的精度已明显提高,美国M oore 公司2000年生产的五轴联动500FG 超精密机床(见图12),可作为典型代表,该机床不仅可加工精密回转体非球曲面,并可加工精密自由曲面。
机床空气轴承主轴转速20~2000r/min ,主轴回转误差≤01025μm 。
液体静压导轨由无刷直线电机驱动,直线度误差≤013μm/300mm ,定位精度013μm。
图12 美国Moore 的500FG 五轴超精密机床乌克兰某研究所研制成新工作原理超精密机床,如图13a 所示,工作原理如图13b 所示。
工作时金刚石车刀围绕刀具转轴O -O 2旋转,刀尖的运动轨迹为通过工件中心点的一个圆,工件旋转而形成加工的球面。
调整刀具转轴箱轴心OO 2,以得到不同的转角θ,可以加工出不同曲率半径的球面。
θ为正值时,加工出的工件表面为凹球面;θ=0时,可切出工件的平端面;θ为负值时,加工出的工件表面为凸球面。
加工非球曲面时,先将机床调整到接近的球面,加工时金刚石车刀再作补充进给f ,即可加工出要求的非球曲面。
这机床的主要优点是加工球面和平面时,完全不需导轨的直线运动(直线导轨很难加工到如此高的精度),故加工精度和表面质量都很高,此外这种机床结构比较简单和紧凑。
(a )机床外观(b )工作原理图13 乌克兰新工作原理超精密机床412 我国超精密机床发展情况过去相当长时期,由于受到禁运限制,我们难以进口国外的超精密机床。