组合机床的PLC控制
基于PLC的组合机床控制系统设计

基于PLC的组合机床控制系统设计1引言可编程控制器(plc)是以微处理机为基础,综合了计算机技术、自动控制技术和通信技术等现代科技而发展起来的一种新型工业自动控制装置,其具有逻辑控制、计时、计数、数据处理、联网与通信等强大功能,同时,由于plc具有很高的可靠性和极大的应用灵活性,用它来替代传统的继电接触控制系统巳成为必然。
大量采用传统继电一接触控制系统的设备通过改造更新,成为plc控制的自动化系统,而且具有改造成本低、周期短和可靠性高等特点。
本文介绍双面单工位液压传动组合机床plc控制系统的设计与应用。
2组合机床的运动及控制要求组合机床指可同时进行多种或多处加工的机床,组合机床的加工动作常常是按预定的步骤安排的,类似于简单的程序控制,这也正是plc最擅长的。
双面单工位液压传动组合机床采用三台电动机进行拖动,m1、m2为左右动力头电动机,m3为冷却泵电动机,其对应的控制交流接触器分别为km1、km2、km3。
sa1为左动力头单独调整开关,sa2为右动力头单独调整开关,通过它们可实现左、右动力头的单独调整。
sa3为冷却泵电动机工作选择开关。
该机床的左、右动力头的工作循环如图1所示,电磁铁动作顺序表见表1。
图1动力头的工作循环图由图1和表1可知,组合机床为自动循环状态时,按下启动按钮后,左、右动力头电动机m1、m2同时旋转,按下“快进”按钮,电磁阀yv1、yv3通电,左、右动力头快速进给并离开原位,行程开关sq1、sq2、sq5、sq6先复位,行程sq3、sq4后复位。
当sq3、sq4复位后,在动力头进给过程中,靠各自行程阀自动变快进为工进,同时压下行程开关sq,冷却泵电动机m3工作,供给冷却液。
当左动力头加工完毕,将压下sq7并顶在死挡铁上,其油路油压升高使kp1动作,当右动力头加工完毕,将压下sq8并使kp2动作,yv2、yv4将通电,同时yv1、yv3也将失电,左、右动力头将快退。
当左动力头使sq复位后,冷却泵电动机将停转。
plc项目7.2【液压组合机床的PLC控制】ppt课件

●工序 原点灯 ·I/O分配图 ·程序组成 步0灯 ●初始程序 ●切换程序顺 ·切换程序梯 步1灯 ·输出程序 步2灯 ●信号程序 ●电气原理图
步3灯 步4灯
●实操1-接线 ·实操2-编程 ●实操3-调试 ·关键点提醒 ·实操任务单 ·实况点评 ·第7章链接
近
上
10
下
QF L1 U11 V11 W11
●实操1-接线 ·实操2-编程 ●实操3-调试 【提醒】图中:PLC的Y1-Y7输出端,依序改接信号灯HL1-HL7;点动按钮2SB0、 ·关键点提醒 SB11-SB14依次用按钮P3替代;限位开关SQ1改用手控开关K1代替,其它依此类推。 ·实操任务单 ·实况点评 ·第7章链接
近
上
12
下
7.2
Plc应用案例 液压组合机床
●工序 ·I/O分配图 ·程序组成 ●初始程序 ●切换程序顺 ·切换程序梯 ·输出程序 ●信号程序 ●电气原理图
●实操1-接线 ·实操2-编程 ●实操3-调试 ·关键点提醒 ·实操任务单 ·实况点评 ·第7章链接
1 S M2 步2 态 0 R M1 步1× S M3 步3 R M2 步2× 1 S M4 步4 态 0 R M3 步3× S M0 步0 R M4 步4× 1 态0 1 态0
目录
[基本项目] 1 原理初步 2 基本指令 3 经典法案例 [高端项目] 4 工序法案例 5 功能指令 6 联网监控 [综合项目] 7 机床控制 8 仿真调试 9 课程设计 PLC实操考1 PLC实操考2
鄂东职业技术学院●教研项目优秀成果
电气控制
项目7.2
策划:陈新耘 设计:胡汉文 制作:胡汉文 余 贵 管
近
上
2
下
7.2
PLC在组合机床的控制应用

技术采用继 电器控制 ,尽管在一定程度上促进 首先需要进行控制设计 ,而设计需要遵循 以下 了组合机床的应用效率, 但组合机床 的精度低 , 几点原则 : 可靠性也不高 ,实现组合机床的 自动化控制不 仅可 以提高生产加工效率 ,还能 降低成本 ,有 2 . 1任务分析评估 效提高加工精度 ,增加可靠性 。因此 ,自动化 由于 P L C控制的全面性, 在 任务设置 中, 控制系统 P L C在组合机床 的应用 中逐渐广泛 。 根据 P L C的控制 范围 ,选 择合适 组合 机床 的 1 P L C 控制 系统 与组合机床 应用操作模块
3 . 1对P L C 进行准确的i / o 模块选择
i / o模 块承担着应用程 序执行命 令数据。 准确 的 i / o电位选择 ,不仅可 以实现 控制程序 的控制编程, 还能保留P L C的输入和输 出空间 , 对今后组合机床功 能控制升级奠定基础 。P L C 的控制具有的全面性 ,有助于实现机床组件操 作的精准度 ,准确的定位编程使程序具有可靠
性。
【 关键词】P L C组合机床 控制
随着 科技 的不 断进 步, 自动化 技术 的控 P L c 控制系统在组合机床的控制设计原则 制程序加快发展 ,越来越符合各项社会工业的 2
要 求 。 在 组 合 机 床 的 控 制 应 用 中 ,传 统 的控 制
3 . 2编制组合机床控制程序
左右滑 台再后退至原位,松开工件 ,完成一个 周期工作。通过设置周期次数 ,实现完整循环 加工过程。 由于现代 工业 生产 更加 多样 化 ,对 设备 部件 的要求也更加严格 ,通用部件 的标准化和 系列化 ,就需要配备灵活 的控制系统 ,实现工 程设计和生产周期的高效性 ,完善工业生产的 自动化运用 。因此,P L C控 制系统在组合机床 的控制应用中有很好的发展前景。
深孔钻组合机床的PLC控制系统设计

深孔钻组合机床的PLC控制系统设计一、PLC的选型和硬件设计在深孔钻组合机床的PLC控制系统中,首先要选择适合的PLC型号。
根据深孔钻组合机床的控制要求,应选择具有高性能、高可靠性的PLC。
同时,还应考虑PLC的扩展性和兼容性,以便后续的功能扩展和升级。
在硬件设计方面,需要根据机床的实际情况,确定控制系统所需的输入/输出点数,并选择合适的输入/输出模块。
在选择输入/输出模块时,应考虑信号的稳定性和抗干扰能力,确保控制系统的可靠性。
二、PLC程序的设计和编写1.确定控制策略:根据深孔钻组合机床的工作原理和要求,确定控制策略,包括钻削、加工循环灌注、冷却水控制等。
2.制定程序流程:根据控制策略,制定PLC程序的流程。
需要考虑机床的各个部分之间的协调和顺序,确保机床的正常运行。
3.编写程序代码:根据程序流程,编写PLC程序代码。
代码的编写应符合国际标准和规范,保证代码的可读性和可维护性。
同时,还需要考虑代码的优化,以提高程序的执行效率。
4.进行仿真测试:在编写完PLC程序后,需要进行仿真测试,模拟机床的实际工作环境,检查程序的逻辑正确性和稳定性。
必要时,还可以进行调试和优化。
三、PLC控制系统的监控和安全保护为了确保深孔钻组合机床的安全运行,PLC控制系统需要进行监控和安全保护。
包括以下几个方面:1.监控机床状态:PLC控制系统可以实时监控机床的状态,包括温度、压力、润滑油位等。
当机床出现异常情况时,PLC可以发出警报,并采取相应的措施,保护机床的安全运行。
2.安全保护功能:PLC控制系统可以实现一系列安全保护功能,包括急停按钮、保护罩监控、限位开关等。
当发生安全事故时,PLC可以迅速采取措施,切断机床的运行,保护操作人员的安全。
3.数据记录与分析:PLC控制系统可以实现对机床的工作数据进行记录和分析。
可以记录机床的工作状态、工作时间、故障信息等,为机床的维护和优化提供参考。
四、完善的人机界面设计PLC控制系统的人机界面设计是提高机床操作和维护效率的关键。
PLC(可编程逻辑控制器)在组合机床控制系统中的应用 2

PLC在合机组床控制系统中的应用摘要组合机床是集机电于一体的综合自动化程度较高的制造技术和成套工艺装备。
它的特征是高效、高质、经济实用,因而被广泛应用于工程机械、交通、能源、军工、轻工、家电等行业。
我国传统的组合机床主要采用机、电、气、液压控制,其精度低,可靠性不高,已不适合社会发展需要。
随着PLC控制技术的迅速发展,以PLC为核心的组合机床控制系统已凸显出其优势.本文以两工位钻孔攻镙组合机床为研究对象,通过对主要结构和运动形式的探究以及对机床的工作过程和控制要求分析,给出了机床动作循环图,并采用PLC控制系统的设计方法, 进行了软硬件设计,列出了PLC的I/O地址分配表,绘制了PLC的I/O分配图和单循环自动工作流程图,编写PLC控制程序的梯形图和指令表;由iFIX设计的人机界面(HMI),使整个控制系统的操作变得简单方便,大大提高了系统的自动化程度和实用性。
关键词组合机床可编程逻辑控制器控制系统程序设计目录PLC在合机组床控制系统中的应用 (I)1 引言 (I)2 组合机床控制系统的系统分析 (3)2.1 组合机床控制系统的特点 (3)2.2 组合机床常见的几种控制方式 (3)2.3 组合机床控制系统的选择 (4)3 组合机床PLC控制系统的硬件设计 (7)3.1 组合机床控制系统工作过程 (7)3.2 PLC的硬件选型 (8)3.3 I/O端子的地址分配 (9)3.4 控制系统PLC的外围电气接线 (10)4 组合机床PLC控制系统的软件设计 (12)4.1 PLC程序设计思想 (12)4.2 组合机床控制系统的功能流程图 (12)4.3 组合机床控制系统的软件整体设计 (13)4.3.1 原位指示程序 (14)4.3.2 钻孔加工程序 (15)4.3.3 攻螺纹程序 (15)4.3.4 自动循环控制和手动控制的转换程序 (16)5 监控系统设计 (18)5.1 组态软件iFIX的简介 (18)5.2 系统环境的选取 (18)5.3 组态界面的设计 (19)5.4 仿真运行情况 (19)参考文献 (22)附录 (23)1.1 引言组合机床一般采用多轴、多刀、多工序、多面或多工位同时加工的方式,生产效率比通用机床高几倍至几十倍。
关于组合机床中运用PLC控制技术的探讨
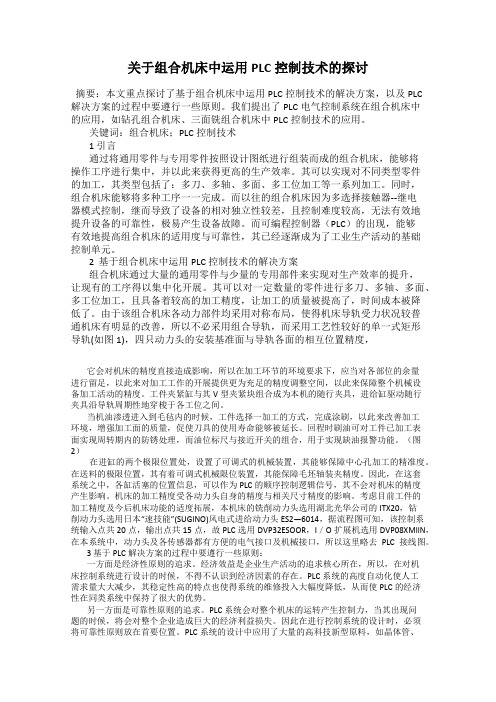
关于组合机床中运用PLC控制技术的探讨摘要:本文重点探讨了基于组合机床中运用PLC控制技术的解决方案,以及PLC解决方案的过程中要遵行一些原则。
我们提出了 PLC电气控制系统在组合机床中的应用,如钻孔组合机床、三面铣组合机床中PLC控制技术的应用。
关键词:组合机床;PLC控制技术1 引言通过将通用零件与专用零件按照设计图纸进行组装而成的组合机床,能够将操作工序进行集中,并以此来获得更高的生产效率。
其可以实现对不同类型零件的加工,其类型包括了:多刀、多轴、多面、多工位加工等一系列加工。
同时,组合机床能够将多种工序一一完成。
而以往的组合机床因为多选择接触器--继电器模式控制,继而导致了设备的相对独立性较差,且控制难度较高,无法有效地提升设备的可靠性,极易产生设备故障。
而可编程控制器(PLC)的出现,能够有效地提高组合机床的适用度与可靠性,其已经逐渐成为了工业生产活动的基础控制单元。
2 基于组合机床中运用PLC控制技术的解决方案组合机床通过大量的通用零件与少量的专用部件来实现对生产效率的提升,让现有的工序得以集中化开展。
其可以对一定数量的零件进行多刀、多轴、多面、多工位加工,且具备着较高的加工精度,让加工的质量被提高了,时间成本被降低了。
由于该组合机床各动力部件均采用对称布局,使得机床导轨受力状况较普通机床有明显的改善,所以不必采用组合导轨,而采用工艺性较好的单一式矩形导轨(如图1),四只动力头的安装基准面与导轨各面的相互位置精度,它会对机床的精度直接造成影响,所以在加工环节的环境要求下,应当对各部位的余量进行留足,以此来对加工工作的开展提供更为充足的精度调整空间,以此来保障整个机械设备加工活动的精度。
工件夹紧缸与其V型夹紧块组合成为本机的随行夹具,进给缸驱动随行夹具沿导轨周期性地穿梭于各工位之间。
当机油渗透进入到毛毡内的时候,工件选择一加工的方式,完成涂刷,以此来改善加工环境,增强加工面的质量,促使刀具的使用寿命能够被延长。
PLC程序设计与调试 项目6 组合机床PLC控制实现

7
目录
项目六 组合机床PLC控制实现
任务实施
➢
1、分析双面单工位液压传动组合机床的工作状况
➢ 双面单工位液压传动组合机床左右动力头的循环工作示意 图如图6-2所示,两动力头左右对称,每个动力头有快进、 工进和快退三种运动状态,由行程开关发出转换信号。组
合机床的液压执行元件状态见表6-1,其中YV表示电磁阀, KP表示压力继电器。
2023年4月6日
8
目录
项目六 组合机床PLC控制实现
表6-1 组合机床的液压执行元件状态
工步
YV1
YV2
YV3
YV4
KP1
KP2
原位停止
-
-
-
-
-
-
快进
+
-
+
工进
+
-
+
死挡铁停留 +
-
+
-
-
-
-
-
-
-
+
+
快退
-
+
-
+
-
-
2023年4月6日
9
目录
项目六 组合机床PLC控制实现
➢
2、分析双面单工位液压传动组合机床控制电路
它们可实现对左右动力头的单独调整;SA3为冷却泵电动机工作选择
开关。
2023年4月6日
11
目录
项目六 组合机床PLC控制实现
➢ 自动循环的工作过程如下:SA1、SA2处于自动循环位置,按下启动 按钮SB2,接触器KM1、KM2线圈通电并自锁,左右动力头电动机同 时启动旋转。按下“前进”按钮SB3,中间继电器KA1、KA2通电并 自锁,电磁铁YV1、YV3通电,左右动力头快速进给并离开原位,行 程开关SQ1、SQ2、SQ5、SQ6先复位,行程开关SQ3、SQ4后复位, 并使KA通电自锁。在动力头进给过程中,由各自的行程阀自动将快 进变为工进,同时压下行程开关SQ,接触器KM3线圈通电,冷却泵 电动机M3工作,供给冷却液。左动力头加工完毕后压下SQ7并顶在死 挡铁上,使其油路油压升高,KP1动作,使KA3通电并自锁;右动力 头加工完毕后压下SQ8并使KP2动作,KA4将接通并自锁,同时KA1、 KA2将失电,YV1、YV3也将失电,而YV2、YV4将通电,使左右动 力头快退。当左动力头使SQ复位后,KM3将失电,冷却泵电动机将 停转。左右动力头快退至原位时,先压下SQ3、SQ4,再压下SQ1、 SQ2、SQ5、SQ6,使KM1、KM2线圈断电,动力头电动机M1、M2 断电停转,同时KA、KA3、KA4线圈断电,YV2、YV4断电,动力头 停止动作,机床循环结束。加工过程中,如按下SB4,可随时使左右 动力头快退至原位停止
关于PLC在组合机床控制中的应用与展望
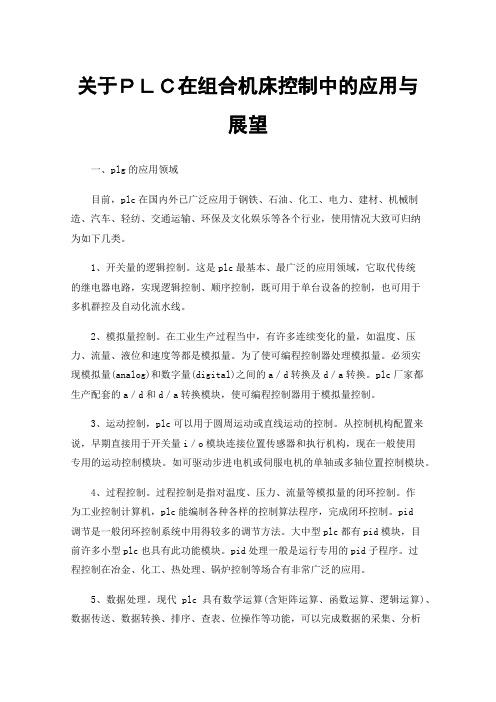
关于PLC在组合机床控制中的应用与展望一、plg的应用领域目前,plc在国内外已广泛应用于钢铁、石油、化工、电力、建材、机械制造、汽车、轻纺、交通运输、环保及文化娱乐等各个行业,使用情况大致可归纳为如下几类。
1、开关量的逻辑控制。
这是plc最基本、最广泛的应用领域,它取代传统的继电器电路,实现逻辑控制、顺序控制,既可用于单台设备的控制,也可用于多机群控及自动化流水线。
2、模拟量控制。
在工业生产过程当中,有许多连续变化的量,如温度、压力、流量、液位和速度等都是模拟量。
为了使可编程控制器处理模拟量。
必须实现模拟量(analog)和数字量(digital)之间的a/d转换及d/a转换。
plc厂家都生产配套的a/d和d/a转换模块,使可编程控制器用于模拟量控制。
3、运动控制,plc可以用于圆周运动或直线运动的控制。
从控制机构配置来说,早期直接用于开关量i/o模块连接位置传感器和执行机构,现在一般使用专用的运动控制模块。
如可驱动步进电机或伺服电机的单轴或多轴位置控制模块。
4、过程控制。
过程控制是指对温度、压力、流量等模拟量的闭环控制。
作为工业控制计算机,plc能编制各种各样的控制算法程序,完成闭环控制。
pid调节是一般闭环控制系统中用得较多的调节方法。
大中型plc都有pid模块,目前许多小型plc也具有此功能模块。
pid处理一般是运行专用的pid子程序。
过程控制在冶金、化工、热处理、锅炉控制等场合有非常广泛的应用。
5、数据处理。
现代plc具有数学运算(含矩阵运算、函数运算、逻辑运算)、数据传送、数据转换、排序、查表、位操作等功能,可以完成数据的采集、分析及处理。
数据处理一般用于大型控制系统,如无人控制的柔性制造系统;也可用于过程控制系统,如造纸、冶金、食品工业中的一些大型控制系统。
6、通信及联网。
plc通信含plc间的通信及plc与其它智能设备间的通信。
随着计算机控制的发展,工厂自动化网络发展得很快,各plc厂商都十分重视pie的通信功能,纷纷推出各自的网络系统。
PLC课程设计---组合机床加工过程PLC自动控制设计
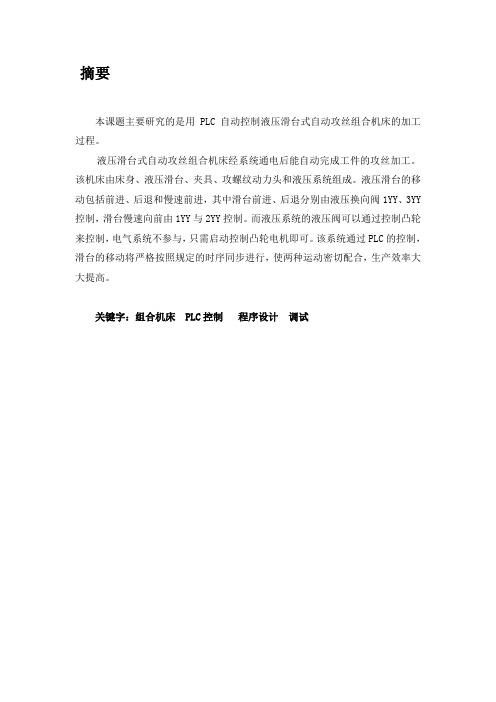
本课题主要研究的是用PLC自动控制液压滑台式自动攻丝组合机床的加工过程。
液压滑台式自动攻丝组合机床经系统通电后能自动完成工件的攻丝加工。
该机床由床身、液压滑台、夹具、攻螺纹动力头和液压系统组成。
液压滑台的移动包括前进、后退和慢速前进,其中滑台前进、后退分别由液压换向阀1YY、3YY 控制,滑台慢速向前由1YY与2YY控制。
而液压系统的液压阀可以通过控制凸轮来控制,电气系统不参与,只需启动控制凸轮电机即可。
该系统通过PLC的控制,滑台的移动将严格按照规定的时序同步进行,使两种运动密切配合,生产效率大大提高。
关键字:组合机床 PLC控制程序设计调试第一章设计任务 (1)第二章总体方案选择和控制方式选择 (2)第三章电路图的设计 (3)第四章控制程序的设计 (6)小结 (10)参考文献 (11)第一章设计任务1.1 控制要求:如图1—1,,是一台液压滑台式自动攻丝组合机床及其工作循环图。
该机床的攻螺纹动力头安装在液压驱动的滑台上。
滑台在原位启动后,快速向前到设定的位置时转为慢速前进,滑台前进到达攻丝进给位置时停止前进,转为攻螺纹主轴转动。
主轴正转,丝锥离开原位向前攻入,攻螺纹到达规定深度时,主轴快速制动,接着反转,丝锥退出,丝锥退到原位即快速制动,同时滑台快速退回,到达原位停下。
电气执行元件为:滑台前进后退分别由液压换向阀1YY、3YY控制,滑台慢速向前由1YY与2YY控制,攻螺纹机主轴电动机由1KM、2KM控制正反转。
行程开关安排:滑台原位:1SQ 滑台终点:3SQ 丝锥原位:4SQ 丝锥终点:5SQ图1—1 液压滑台式自动攻丝组合机床1.2 设计要求:1.2.1 PLC型号:西门子公司S7系列,S7-3001.2.2编程环境:SIMATIC Manager /Step7 V5.4或更高版本1.2.3根据控制要求分配PLC I/O地址,画出PLC与控制对象的接线图,设计控制流程,按照模块化的方式设计程序,既可以采用LAD编程,也可以采用STL编程,还可以采用组合方式编程。
基于PLC的四工位组合机床控制系统设计

基本内容
基本内容
摘要: 本次演示介绍了一种基于可编程逻辑控制器(PLC)的四工位组合机床控制系 统设计。该系统通过优化硬件和软件配置,实现了高效、准确的工位控制,提高 了生产效率。本次演示详细阐述了PLC控制技术
基本内容
的原理和特点,并对四工位组合机床控制系统的硬件和软件进行了设计。最 后,通过实验验证了该控制系统的可靠性和有效性。
3.3输入输出接口
3.3输入输出接口
PLC作为控制系统的核心,需要与外围设备进行交互。因此,输入输出接口的 设计也至关重要。常见的输入接口包括按钮、开关和传感器信号接口;输出接口 则包括继电器、伺服电机等执行机构接口。这些接口通过相应的硬件和软件配置 实现与外围设备的连接与控制。
实际应用
实际应用
三、基于PLC的组合机床控制系 统设计
1、硬件设计
1、硬件设计
基于PLC的组合机床控制系统的硬件设计主要包括输入输出模块、中央处理单 元、通信接口等。输入模块主要接收操作面板、各个传感器等输入信号;输出模 块主要控制各个执行元件;中央处理单元是整个控制系统的核心,主要负责处理 输入信号,
1、硬件设计
一、组合机床的结构与工作原理
一、组合机床的结构与工作原理
组合机床主要由动力头、滑台、夹具、冷却系统、液压系统、电控制系统等 组成。其工作原理是利用动力头带动刀具进行切削,滑台负责带动工件进行移动, 夹具对工件进行定位和夹紧,液压系统提供动力,电控制系统控制整个加工过程 的运行。
二、PLC在组合机床中的应用
基本内容
2、灵活性:PLC可通过编程实现不同的控制逻辑,满足各种不同的生产需求。 3、易于维护:PLC具有自诊断功能,便于排查故障,维护简单。
组合机床的PLC控制

行 娟娟
【 摘
西 安外 事学 院工学 院
要】文中针对机床电器 的控制特 点,将P C L 技术应用于组合机床 ,可以充分发挥P c L 可靠性高、调试方便和使用灵活等优点。进 而大大缩短产品的开发周
期,降低设计成本,提高控制系统的可靠性和产品的合格率 , 生产效率大幅提升。 使
屑、润滑等装置以及机械手、定位、夹紧、 导 向等部 件 。 2组合机床的拖动要求与控制特点 . 组合机床 的控制系统大多采用机械、 液压 ( 或气动) 、电气相结合的控制方式。组 合机床的电气控制系统由通用部件的典型控 制 线路 及基本 控制 环节 ,再根 据加 工 、操 作 要 求 以及 自动 循环过 程综合 而成 。 由于加 工工 件 和 工 序 要求 不 同 ,组 合 机床的配置各不相 同,它的电气控制线路亦 不相同,电气控制的主要对象是通用部件和 专用部件 。加工过程中电动机大 多不需调 速,运动部件状态即 自动工作循环流程 ( 快 进 、工进 、快 退等 ) 的转换 ,多 由行 程开 关 控制和发出转换信号,控制电路大多采用继 电器一接触器控制系统。 动力滑台配置不 同的控制 电路 ,可完 成多种 自动循环。在一次循环 中,要实现速 度差别很大的快进和工进,快进、快退由快 进电动机实现 ,工进 由工进 电动机实现。 动 力 滑 台 与 动 力 头 相 比 较 , 前 者 配 置成 的组 合机床 较动 力头 更为 灵活 。在 动力 头上 只安装 多轴 箱 ,而滑 台还 可安 装 各 种 切 削 头 组 成 的 动 力 头 ,广 泛 用 来 组成 卧式 、立 式组合 机床 及其 自动 线 , 以完 成 钻 、扩 、铰 、镗 、 刮 端 面 、 倒 角 、铣削和攻螺纹等加 工工序 。 3 系 统 设 计 要 求 . 本 系统 有连 续全 自动 工作循 环及 手 动 工 作 方 式 。 由按 钮 对 每 一 加 工 进 行 单 独控 制 。手动 方式 可供维 修用 ,每 按一 次 启动按 钮 ,回转 台转一 个工 位 ,铣、 钻 、 扩 、 攻 同 时 加 工 ,加 工 完 毕 自 动 停 止 。全 自动方 式供 正常工 作使 用 ,当按 下 启动按 钮时 ,组 合机床 周而 复始 地执 行各步动作 ,直到按下停止按钮为止 。 根 据组 合机床 的加工 特点 ,其 动作 过程要求如下:
基于s7-200PLC液压组合机床的控制设计

基于s7-200PLC液压组合机床的控制设计1.引言随着现代制造业的发展,组合机床在生产中的应用越来越广泛。
组合机床具有高效率、高精度、高自动化程度等特点,是制造业的重要设备。
西门子S7-200PLC作为一种广泛应用于工业控制领域的可编程控制器,具有性能稳定、编程简单、扩展性强等特点。
本文主要介绍基于S7-200PLC的液压组合机床控制系统设计,包括硬件选型、软件设计、控制系统运行原理等方面。
2.液压组合机床概述液压组合机床是一种采用液压驱动的复合加工设备,集成了多种加工功能,如铣削、钻孔、镗孔、切削等。
它具有高效率、高精度、高自动化程度等特点,适用于批量生产。
液压组合机床的核心部件是液压系统,其性能直接影响到机床的加工能力和稳定性。
3. S7-200PLC简介西门子S7-200PLC是一款性能稳定、编程简单、扩展性强的可编程控制器。
它具有以下特点:(1)高速度、高可靠性(2)丰富的指令集(3)强大的扩展能力(4)友好的编程环境4.基于S7-200PLC的液压组合机床控制系统设计4.1硬件设计(1)PLC选型:根据液压组合机床的加工需求和性能要求,选择西门子S7-200PLC作为控制核心。
(2)传感器选型:选择合适的传感器,如温度传感器、压力传感器等,实现对液压系统状态的实时监测。
(3)执行器选型:根据加工工艺要求,选择合适的液压马达、电磁阀等执行器。
4.2软件设计(1)系统架构:采用模块化设计,主要包括输入输出模块、控制算法模块、通信模块等。
(2)控制算法:根据液压组合机床的加工过程,设计合适的控制算法,如PID控制、模糊控制等。
(3)人机界面:设计直观、易操作的人机界面,实现对机床状态的实时监控和参数设置。
4.3控制系统运行原理(1)实时监测:通过传感器对液压系统状态进行实时监测,如压力、温度等。
(2)信号处理:将监测到的信号传输至S7-200PLC,进行数据处理。
(3)控制执行:根据处理后的数据,通过PLC输出信号,控制执行器实现对液压系统的精确控制。
四工位组合机床的plc控制系统设计 正文

正文第一章绪论一、组合机床概述组合机床是针对特定工件,进行特定加工而设计的一种高效率自动化专用加工设备,这类设备大多能多刀同时工作,并且具有自动循环的功能。
组合机床是随着机械工业的不断发展,由通用机床、专用机床发展起来的。
通用机床一般用一把刀具进行加工,自动化程度低、辅助时间长、生产效率低,但通用机床能够重新调整,以适应加工对象的变化。
专用机床可以实现的多刀切削,自动化程度较高,结构较简单,生产效率也较高。
但是,专用机床的设计,制造周期长,造价高,工作可靠性也较差。
专用机床是针对某工件的一定工序设计的,当产品进行改进,工件的结构,尺寸稍有变化时,它就不能继续使用。
在综合了通用机床、专用机床优点的基础上产生了组合机床。
组合机床通常由标准通用部件和加工专用部件组合构成,动力部件采用电动机驱动或采用液压系统驱动,由电气系统进行工作自动循环的控制,是典型的机电或机电液一体化的自动加工设备。
常见的组合机床,标准通用部件有动力滑台各种加工动力头以及回转工作台等,可用电动机驱动,也可用液压驱动。
各标准通用动力部件组合构成一台组合机床时,该机床的控制电路可由各动力部件的控制电路通过一定的连接电路组合构成。
多动力部件构成的组合机床,其控制通常有三方面的工作要求:第一方面是动力部件的点动和复位控制。
第二方面是动力部件的半自动循环控制。
第三方面是整批全自动工作循环控制。
组合机床具有生产率高、加工精度稳定的优点。
因而,在汽车、柴油机、电机、机床等一些具有一定生产批量的企业中得到了广泛应用。
目前,组合机床的研制正向高效、高精度、高自动化和柔和性化方向发展。
本文所用组合机床为四工位组合机床,该机床由四个滑台,各载一个加工动力头,组成四个加工工位,除了四个加工工位外,还有夹具,上下料机械手和进料器,四个辅助装置以及冷却和液压系统共14个部分。
机床的四个加工动力头同时对一个零件的四个端面以及中心孔进行加工,一次加工完成一个零件,由上料机械手自动上料,下料机械手自动取走加工完成的零件,零件每小时可加工80件。
如何用PLC改造组合机床
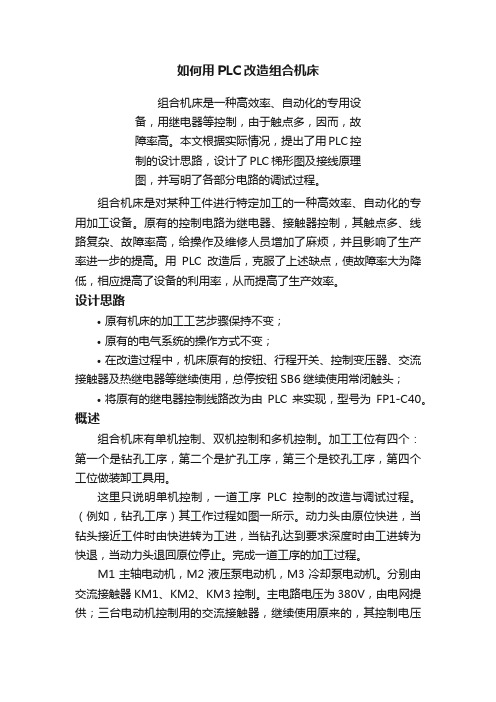
如何用PLC改造组合机床组合机床是一种高效率、自动化的专用设备,用继电器等控制,由于触点多,因而,故障率高。
本文根据实际情况,提出了用PLC控制的设计思路,设计了PLC梯形图及接线原理图,并写明了各部分电路的调试过程。
组合机床是对某种工件进行特定加工的一种高效率、自动化的专用加工设备。
原有的控制电路为继电器、接触器控制,其触点多、线路复杂、故障率高,给操作及维修人员增加了麻烦,并且影响了生产率进一步的提高。
用PLC改造后,克服了上述缺点,使故障率大为降低,相应提高了设备的利用率,从而提高了生产效率。
设计思路•原有机床的加工工艺步骤保持不变;•原有的电气系统的操作方式不变;•在改造过程中,机床原有的按钮、行程开关、控制变压器、交流接触器及热继电器等继续使用,总停按钮SB6继续使用常闭触头;•将原有的继电器控制线路改为由PLC来实现,型号为FP1-C40。
概述组合机床有单机控制、双机控制和多机控制。
加工工位有四个:第一个是钻孔工序,第二个是扩孔工序,第三个是铰孔工序,第四个工位做装卸工具用。
这里只说明单机控制,一道工序PLC控制的改造与调试过程。
(例如,钻孔工序)其工作过程如图一所示。
动力头由原位快进,当钻头接近工件时由快进转为工进,当钻孔达到要求深度时由工进转为快退,当动力头退回原位停止。
完成一道工序的加工过程。
M1主轴电动机,M2液压泵电动机,M3冷却泵电动机。
分别由交流接触器KM1、KM2、KM3控制。
主电路电压为380V,由电网提供;三台电动机控制用的交流接触器,继续使用原来的,其控制电压为220V,仍然用原有的控制变压器提供;电磁阀的直流控制电压为24V,由原来的整流电路提供,PLC中也有24V输出,考虑到PLC的输出功率,所以不采用。
主电路部分不做改动,控制电路原理由梯形图体现,如图二所示,控制电路接线如图三所示。
调试过程1、主电路调试:原电路要求M1、M2电动机同时启动工作。
由复合开关SA3、SA4可控制M1与M2个之单独启动、停止(机床调试用);M3电动机在动力头工进时自动启动,也可以由按钮SB2单独控制。
组合机床的PLC控制

3.JCS-02N 压力继电器 压力继电器是利用液体的压力来启闭电 气触点的液压电气转换元件。当系统压 力达到压力继电器的调定值时,发出电 信号,使电气元件(如电磁铁电机。时间 继电器。电磁离合器等)动作,使油路卸 压。换向,执行元件实现顺序动作,或 关闭电动机使系统停止工作,起安 全保 护作用等。
T0 Y001 Y005
S22
Y006
延时 K50 钻头下降进 刀 铣刀下降进
多件加工
单件加工
5、程序的调试与仿真
●组合机床得电后,程序开始运行,系统处于S0原点状态:
●当钻头、铣刀处于上限位,LS1、LS3闭合,启动按钮SB1, X000接通,进入S20状态,原点指示灯亮,刀具旋转,即Y000输 出;
Y000 Y001 Y002
KM1 KM2
LS1 LS2 LS3 LS4 LS5 SA KV
钻头进刀 钻头退刀 工作头夹紧 工作头松开
PLC
Y003 Y004 Y005 Y006
KM3 KM4
铣刀进刀 铣刀退刀
COM
COM SB3 SB4 KM KM
急停
2、PLC的I/O控制和分配
PLC点名 称 X000 连接的外部设备 启动按钮 PLC点名称 Y000 连接的外部设备 原点指示
●待退刀达到上限位时,LS3、LS5闭合,即X002和X004接 通,进入S24状态,夹紧工作头松开,即Y004输出,延时3秒;
需求分析:
1、输入点数为16,输出点数为16。 2、电机起停频率一般。 3、没有其他特殊功能要求。
因此本设计选择三菱FX1s系列中的FX1s-32MR-001,其输入点数 为16,输出点数为16满足项目需求,其具体参数如下: 辅助继电器512点 MO-M511 特殊辅助继电器256点 M8000--M8255 数据寄存器256点 D0-D255 特殊数据寄存器256点 D8000--D8255 定时器 64点 T0-T63 计数器 16位增模式32点 C0-C31 32位高速双向计数器6点 C235-C255
10.2.1组合机床的PLC自动控制液压动力滑台采用电磁-山东英才学院

Date: 2019/6/10
返回
(可编程控制器原理及应用)
Page: 20
山东英才学院
CH10 可编程控制器应用系统设计
10.2.2 PLC在交通灯自动控制中的应用
2. PLC的I/O端口分配和接线图
外设 SB
I/O
功能
I0.0
起停旋钮
HL1(HL7) HL2(HL8) HL3(HL9) HL4(HL10) HL5(HL11) HL6(HL12)
2. PLC的I/O端口分配和接线图
CPU224
SB I0.0
Q0.0
HL1
PLC每一个输出触点需要驱动 同一路口(对面)2只相同 颜色的信号灯,在接线图中 仅画出一只做示意。
Q0.1
HL2
M
Q0.2
HL3
1L
Q0.4
HL4
Q0.5
HL5
Q0.6
HL6
+24V
2L + -
24 V
GND
L1 220VAC
24 V
GND
L1 220VAC
N
Date: 2019/6/10
图7.7 液压动力滑台PLC接线图
(可编程控制器原理及应用)
Page: 14
山东英才学院
CH10 可编程控制器应用系统设计
10.2.1 组合机床的PLC自动控制
5.自动循环工艺流程图
SB2
开始 SB1
快进 SQ1
工进 SQ2
延时 T37
SQ1
工进 YV1、KM1
横进YV5
SQ2 停,延时3s
YV3横退
SQ4
纵退YV4
SQ3
基于PLC的组合机床控制系统设计

第2页
为了充分发挥设备效能,快速提升加工技术与精度,越来越多企业每年投入大量资金和技术对传统传统组合机床进行技
术改造,取得了良好效果。用PLC模块、操控监控设备等组成电气数字控制系统,以实现编程输入、人机交互、自动化加工
引言 控制方式,扩大加工能力,降低故障,提升效率,已成为企业进行技术改造有效路径。 依据我国当前情况,传统控制方式采取物理电子器件和大量而又复杂硬接线,使得系统工作效率低,可靠性差,故障诊疗和排 除困难,严重影响了工厂生产效率。伴随科学技术发展,可编程控制器出现,采取可编程控制系统,不论在性能上或者效率上
PLC基于组合机床控制系统设计
姓 名: 指导老师:
PLC基于组合机床控制系统设计
姓 名: 指导老师:
PLC基于组合机床控制系统设计
姓 名: 指导老师:
第1页
本文研究对象是三面铣组合机床,经过对主要结构和运动形式探究以及对机床工作过程和控制要求分析,给出了机床动作循 环图、液压元件动作表;并采取PLC控制系统设计方法, 进行了软硬件设计,列出了PLCI/O地址分配表,绘制了PLCI/O分配图和单
组合机床与万能机床和专用机床相比,有以下几个特点: 1、组合机床结构稳定、工作可靠,使用和维修方便。 2、组合机床设计和制造周期短,投资少,经济效果好。 3、组合机床生产效率高,产品质量稳定,劳动强度低。 4、组合机床其通用部件和标准零件能够重复利用,无须另行设计和制造。 5、组合机床因为采取专用夹具、刀具和导向装置等,对操作工人水平要求不高, 加工质量靠工艺装备确保。 6、组合机床易于联成组合机床自动线,以适应大规模生产需要。
设备,其作用对象是Z512W型台式钻床主轴箱Ф80、Ф90孔端面及定位面。
PLC在组合机床控制中应用

常州工学院PLC课程设计课题名称:PLC 在组合机床控制中应用专业:电气工程及其自动化学院:电子信息与电气工程学院姓名:周森华苏建佘一峰沃凌霄李国锋肖孙波班级: 02 电二指导老师:罗慧芳二 00 五年九月目录一任⋯⋯⋯⋯⋯⋯⋯⋯⋯⋯⋯⋯⋯⋯⋯⋯⋯⋯⋯⋯⋯..1二内容⋯⋯⋯⋯⋯⋯⋯⋯⋯⋯⋯⋯⋯⋯⋯⋯⋯⋯⋯⋯..3 ( 一) 控制要求⋯⋯⋯⋯⋯⋯⋯⋯⋯⋯⋯⋯⋯⋯⋯⋯⋯⋯⋯⋯3 ( 二)体程⋯⋯⋯⋯⋯⋯⋯⋯⋯⋯⋯⋯⋯⋯⋯⋯⋯⋯.51.件⋯⋯⋯⋯⋯⋯⋯⋯⋯⋯⋯⋯⋯⋯⋯⋯⋯⋯⋯ .. 52.硬件⋯⋯⋯⋯⋯⋯⋯⋯⋯⋯⋯⋯⋯⋯⋯⋯⋯⋯⋯ ..3.故障⋯⋯⋯⋯⋯⋯⋯⋯⋯⋯⋯⋯⋯⋯⋯⋯⋯⋯⋯ ..三小⋯⋯⋯⋯⋯⋯⋯⋯⋯⋯⋯⋯⋯⋯⋯⋯⋯⋯⋯⋯ ..四附⋯⋯⋯⋯⋯⋯⋯⋯⋯⋯⋯⋯⋯⋯⋯⋯⋯⋯⋯⋯⋯⋯..1. 合机床表示⋯⋯⋯⋯⋯⋯⋯⋯⋯⋯⋯⋯⋯⋯⋯⋯⋯..2. 程序指令表⋯⋯⋯⋯⋯⋯⋯⋯⋯⋯⋯⋯⋯⋯⋯⋯⋯⋯⋯..3. 参照文件⋯⋯⋯⋯⋯⋯⋯⋯⋯⋯⋯⋯⋯⋯⋯⋯⋯⋯⋯..二设计内容〔一〕控制要求:1.组合机床归纳两工位钻孔,攻丝组合机床,能自动完成工件的转孔和攻丝加工,自动化程度高,生产效率高。
机床主要由床身,搬动工作台,夹具,钻孔动力头,攻丝滑台,攻丝动力头,滑台搬动控制凸轮和液压系统等组成,如附录一。
搬动工作台和夹具用以完成工件的搬动和加紧,实现自动加工。
转孔滑台和转孔动力头用以实现转孔加工量的调整和转孔加工。
攻丝滑台和攻丝动力头用以实现攻丝加工量的调整和攻丝加工。
工作台的搬动〔左移,右移〕,夹具的动作〔夹紧,放松〕,转孔滑台和和攻丝滑台的搬动〔前移,后移〕,都由液压系统执行,其中的来年感个滑台的液压系统由滑台搬动控制凸轮来控制,工作台的搬动和夹具的夹紧和放松电磁阀的控制。
依照设计要求,工作台的搬动和华东台的搬动应按严格要求规定的时序同步进行,两种运动亲近配合,以提高生产效率。
2.加工工艺及控制要求系统通电,自动启动液压泵电机M1。
- 1、下载文档前请自行甄别文档内容的完整性,平台不提供额外的编辑、内容补充、找答案等附加服务。
- 2、"仅部分预览"的文档,不可在线预览部分如存在完整性等问题,可反馈申请退款(可完整预览的文档不适用该条件!)。
- 3、如文档侵犯您的权益,请联系客服反馈,我们会尽快为您处理(人工客服工作时间:9:00-18:30)。
6 目录 返回
上页 下页 退出
第4章 电工测量与工厂输配电和安全用电
8.3.5 控制程序及说明
8.3.5控制程序及说明
8 目录 返回
上页 下页 退出
第4章 电工测量与工厂输配电和安全用电
8.3.5 控制程序及说明
9 目录 返回
上页 下页 退出
§8.3 组合机床的PLC控制
8.3.1 8.3.2 8.3.3 8.3.4 8.3.5
概述 加工工艺及控制要求 PLC选型及I/O地址表 I/O电气接线图 控制程序及说明
第4章 电工测量与工厂输配电和安全用电
8.上页 下页 退出
第4章 电工测量与工厂输配电和安全用电
32/32,配输入扩展模块FX2N-16E, 共有输入点48个,输出点32个,留有一定余量。
其输入/输出地址编排如表8-1所示。
4 目录 返回
上页 下页 退出
第4章 电工测量与工厂输配电和安全用电
8.3.3 I/O地址表
5 目录 返回
上页 下页 退出
第4章 电工测量与工厂输配电和安全用电
8.3.4 I/O电气接线图
8.3.2 加工工艺及控制要求
8.3.1 加工工艺及控制要求
3 目录 返回
上页 下页 退出
第4章 电工测量与工厂输配电和安全用电
8.3.3 PLC选型及I/O地址表
8.3.3 PLC选型及I/O地址表 四个工位组合机床的输入信号共有39个,
输出有21个,均为开关量。 选用三菱公司FX-2N-64MR,其输入/输出点数