典型零件加工工艺分析
典型零件加工与工艺分析
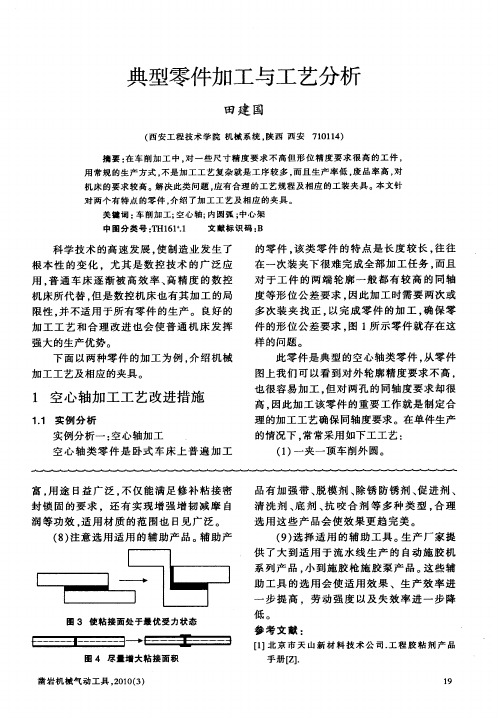
处。
( ) 连 杆 时 , 须 保 证 轴 线 与 工 件 轴 2 装 必
图 3
线平 行 。 ( ) 板 导 轨 要 与工 件 轴 线 平 行 , 的 3 托 它 摇 动用 于控 制 每次 的切 削 深度 。
如果 在 车床 上 安 装一 个 支 点 . 用 一个 再
【】 陆 英 . T rz 与 技 能 训 练 【 . 动 与 社 会 保 障 1孟 车 J劳 】
的零 件 。 类 零 件 的特 点 是 长 度 较 长 , 往 该 往
在一 次 装夹 下 很 难 完 成 全部 加 工任 务 , 而且
对 于 工 件 的 两 端 轮廓 一般 都 有 较 高 的 同轴 度 等 形 位公 差 要 求 , 因此 加 工 时需 要 两 次或 多 次装 夹 找 正 , 完 成 零 件 的加 工 , 保 零 以 确
V
● _ _
8 0 + :
8o o .
8 ( 0 二 三 o
图 1
◎ . A O2 0
( ) 四爪 , 软爪 夹 持一 端 , 2用 或 一端 搭 中
心架 , 以外 圆作 为 基 准 , 正 后 粗 精 加 工 一 找
端 内孔 。
床精度要求高 、 正麻烦 。 找 很难 能保 证 产 品
2 0
① 因两支撑架在第一次调整后 , 后续加
工过 程 中不 再调 整 。 以加 工 时能始 终 保 证 所
凿 岩 机械 气 动 工 具 .0 0 3 21()
两 中心 架 三爪 中心 在 同一 轴 线 上 , 决 了调 解 头 时存在不 同心 的问题 , 保证 了 同轴度 要求 。
典型零件加工工艺总结

典型零件加工工艺总结一、零件概述本次工艺总结以某机械加工企业的典型零件为例,该零件为传动轴,主要用于传递动力和运动。
零件材料为45号钢,具有一定的强度和耐磨性。
二、加工工艺流程1. 毛坯准备:根据零件图纸,制备毛坯。
本例中,采用直径为Φ50mm的45号钢棒料,长度略大于图纸要求。
2. 粗加工:对毛坯进行粗车和粗铣,初步去除余量,加工出大致的几何形状。
3. 半精加工:进一步精加工,使零件达到半成品状态,为精加工做准备。
4. 精加工:对零件进行精车、精铣和磨削等加工,确保尺寸精度和表面粗糙度达到要求。
5. 热处理:对精加工后的零件进行淬火和回火处理,提高其力学性能。
6. 质量检测:对处理后的零件进行全面的质量检测,确保满足图纸要求。
7. 表面处理:根据需要,对零件进行喷漆、镀铬等表面处理,以提高其耐腐蚀性和美观度。
8. 包装入库:将处理后的零件进行包装,并存入成品库。
三、工艺总结1. 优点:a. 采用了合理的加工顺序,保证了加工质量和效率。
b. 使用了先进的数控机床和加工中心,提高了加工精度和自动化程度。
c. 对关键尺寸进行了有效的质量检测和控制,确保了产品的一致性和可靠性。
2. 不足之处:a. 在热处理环节中,部分零件出现了裂纹,需要进一步优化热处理工艺参数。
b. 在表面处理环节中,部分零件表面处理效果不佳,需加强表面处理质量控制。
3. 改进措施:a. 对热处理工艺进行优化,调整淬火和回火温度、时间等参数,减少裂纹的产生。
b. 加强表面处理设备维护和质量控制,提高表面处理效果。
c. 在质量检测环节中增加抽检频次,及时发现并处理不合格品,提高产品质量稳定性。
四、结论通过对典型零件的加工工艺总结,我们可以得出以下结论:在机械加工过程中,要注重加工顺序的合理安排、先进设备的选用、关键尺寸的质量检测和控制等方面;同时也要关注热处理和表面处理等环节中存在的问题,并采取相应的改进措施,以提高零件的加工质量和效率。
典型轴类零件数控加工工艺分析
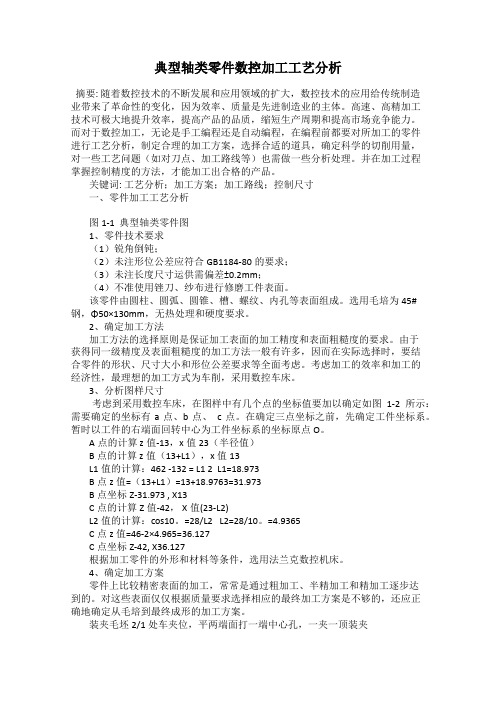
典型轴类零件数控加工工艺分析摘要: 随着数控技术的不断发展和应用领域的扩大,数控技术的应用给传统制造业带来了革命性的变化,因为效率、质量是先进制造业的主体。
高速、高精加工技术可极大地提升效率,提高产品的品质,缩短生产周期和提高市场竞争能力。
而对于数控加工,无论是手工编程还是自动编程,在编程前都要对所加工的零件进行工艺分析,制定合理的加工方案,选择合适的道具,确定科学的切削用量,对一些工艺问题(如对刀点、加工路线等)也需做一些分析处理。
并在加工过程掌握控制精度的方法,才能加工出合格的产品。
关键词: 工艺分析;加工方案;加工路线;控制尺寸一、零件加工工艺分析图1-1 典型轴类零件图1、零件技术要求(1)锐角倒钝;(2)未注形位公差应符合GB1184-80的要求;(3)未注长度尺寸运供需偏差±0.2mm;(4)不准使用锉刀、纱布进行修磨工件表面。
该零件由圆柱、圆弧、圆锥、槽、螺纹、内孔等表面组成。
选用毛培为45#钢,Φ50×130m m,无热处理和硬度要求。
2、确定加工方法加工方法的选择原则是保证加工表面的加工精度和表面粗糙度的要求。
由于获得同一级精度及表面粗糙度的加工方法一般有许多,因而在实际选择时,要结合零件的形状、尺寸大小和形位公差要求等全面考虑。
考虑加工的效率和加工的经济性,最理想的加工方式为车削,采用数控车床。
3、分析图样尺寸考虑到采用数控车床,在图样中有几个点的坐标值要加以确定如图1-2所示:需要确定的坐标有a点、b点、c点。
在确定三点坐标之前,先确定工件坐标系。
暂时以工件的右端面回转中心为工件坐标系的坐标原点O。
A点的计算 z值-13,x值23(半径值)B点的计算 z值(13+L1),x值13L1值的计算:462 -132 = L1 2 L1=18.973B点z值=(13+L1)=13+18.9763=31.973B点坐标Z-31.973 , X13C点的计算Z值-42, X值(23-L2)L2值的计算:cos10。
典型零件机械加工工艺与实例

典型零件机械加工工艺与实例典型零件机械加工工艺与实例机械加工是制造业中一种重要的工艺技术,它可以将原材料加工成特定的形状和尺寸的零件。
在机械加工过程中,不同的零件需要采用不同的加工工艺,下面将介绍一些典型的零件机械加工工艺并给出实例。
1.车削加工车削是一种常见的切削加工工艺,它可以将圆柱形的工件加工成不同形状和尺寸的零件。
车削加工通常使用车床进行加工,将工件固定在车床上,然后通过旋转刀具的方式将工件加工成所需形状和尺寸。
例如,汽车发动机的曲轴就是通过车削加工加工而成的。
2.铣削加工铣削是一种将工件放置在铣床上进行加工的工艺技术。
铣削加工可以将工件从不同角度进行加工,可以加工出各种形状的凹凸面和倒角等。
例如,机床上的床身、工作台和立柱等零件,都是通过铣削加工加工而成的。
3.钻孔加工钻孔是一种加工孔洞的工艺技术,可以将工件上的孔洞加工成不同形状和尺寸的孔洞。
钻孔加工通常使用钻床进行加工,将工件固定在钻床上,然后通过旋转钻头的方式将工件加工成所需形状和尺寸。
例如,电器设备中的插座、开关和电线等,都是通过钻孔加工加工而成的。
4.冲压加工冲压是一种加工薄板材料的工艺技术,可以将材料加工成各种形状和尺寸的零件。
冲压加工通常使用冲床进行加工,将材料固定在冲床上,然后通过冲床上的模具将材料加工成所需形状和尺寸。
例如,汽车车身、电器外壳和日常生活中的金属制品等,都是通过冲压加工加工而成的。
以上是一些典型的零件机械加工工艺,虽然加工工艺不同,但都需要精确的加工工艺和技术,以达到所需的加工效果。
在实际加工中,应根据不同的工件选择合适的加工工艺,以提高生产效率和加工质量。
[精编]典型零件加工工艺分析
![[精编]典型零件加工工艺分析](https://img.taocdn.com/s3/m/8c8b3258a517866fb84ae45c3b3567ec102ddc82.png)
[精编]典型零件加工工艺分析
零件加工工艺分析是设计、制造过程中一个重要环节,是实现目标产品功能性能要求
的关键技术手段。
因此,在设计制造各项工艺参数之前,都需要对零件加工工艺进行仔细
分析。
一般来说,零件加工工艺分析包括了材料分析、过程分析、方法分析以及可行性分析。
一般从这四个方面进行系统分析零件加工工艺,以更好地确定加工的方式、材料的选择,
既节省生产成本,又能保证加工质量。
首先,在进行零件加工工艺分析之前,要对零件的形状、尺寸、强度要求等基本参数
进行分析研究,由此决定该类零件的材料,并确定加工工艺。
其次,在选择加工过程前,应该全面分析以下情况:比如说零件加工过程中所耗费的
多少工序、每个工序耗费的时间、加工设备的选型、零件的表面处理等,以此确定最适合
的加工过程及做工的方法。
再者,在确定加工精度和质量时,要根据零件的加工精度要求、外观质量和内部质量
来进行评估,同时考虑加工工艺及其所使用的设备,以确定分析出加工工艺、材料等方面
的技术指标,对比加工质量达标程度。
最后,在加工技术分析中,还要进行可行性分析,旨在确定加工工艺是否可行,综合
考虑加工所需设备和设施、加工工艺、加工费用、质量等要素,实施零件的加工成本控制
及经济性分析,从而更好地将零件加工工艺应用于实践。
总之,准确评估零件加工工艺瓶颈,分析大量的工艺参数,实施有效的加工成本控制,是每一个零件加工企业的目标。
要更好地实现这一目标,必须对零件加工工艺进行全面系
统的分析,以帮助企业在生产加工过程中实施科学管理、有效控制成本。
典型零件的选材及加工工艺路线分析讲解材料

轻量化
减轻材料重量,提高产品机动性,降低能源 消耗和排放。
环保化
发展可再生、可回收、可降解的材料,减少 对环境的污染。
智能化
研究具有自适应、自修复、自感应等功能的 智能材料。
新材料的研究与开发
碳纤维复合材料
具有高强度、轻质、耐高温等优点,广 泛应用于航空航天、汽车等领域。
高分子合成材料
具有优良的化学稳定性、绝缘性、耐 磨性等,在建筑、电子、化工等领域
03
材料的应用与发展趋势
材料的应用领域
01
航空航天
用于制造飞机、火箭等高强度、轻 质材料。
建筑领域
用于制造桥梁、高层建筑等高强度、 高耐久性材料。
03
02
汽车工业
用于制造发动机、变速器等耐磨、 耐高温材料。
电子产品
用于制造集成电路、晶体管等精密、 小型化材料。
04
材料的发展趋势
高性能化
提高材料的强度、硬度、耐高温等性能,以 满足更高要求的工业应用。
可加工性原则
材料应具有良好的可加工性, 以便于零件的制造和加工。
可维修性原则
材料应易于维修和更换,以提 高零件的使用寿命和降低维修 成本。
常用材料介绍
钢铁
钢铁是机械制造业中应用最广泛的材料之一,具 有高强度、良好的韧性和耐磨性。
铜及铜合金
铜及铜合金具有良好的导电性、导热性、耐腐蚀 性和加工性能,广泛应用于电气、电子、化工等 领域。
实例二:齿轮类零件的选材与加工工艺
灰铸铁
用于制造一般用途的齿轮,如减速器齿轮等。
球墨铸铁
用于制造高强度、高耐磨性的齿轮,如汽车变速毛坯准备
根据零件材料和尺寸要求,准备毛坯。
粗加工
[精选]典型零件加工工艺
![[精选]典型零件加工工艺](https://img.taocdn.com/s3/m/50ec52ca690203d8ce2f0066f5335a8102d2661f.png)
[精选]典型零件加工工艺(一)数控车削加工典型零件工艺分析实例1.编写如图所示零件的加工工艺。
(1)零件图分析如图所示零件,由圆弧面、外圆锥面、球面构成。
其中Φ50外圆柱面直径处不加工,而Φ40外圆柱面直径处加工精度较高。
零件材料:45钢毛坯尺寸:Φ50×110(2)零件的装夹及夹具的选择采用机床三爪自动定心卡盘,零件伸出三爪卡盘外75mm左右,以外圆定位并夹紧。
(3)加工方案及加工顺序的确定以零件右端面和中心轴作为坐标原点建立工件坐标系。
根据零件尺寸精度及技术要求,零件从右向左加工,将粗、精加工分开来考虑。
加工工艺顺序为:车削右端面→复合型车削固定循环粗、精加工右端需要加工的所有轮廓(粗车Φ44、Φ40.5、Φ34.5、Φ28.5、Φ22.5、Φ16.5外圆柱面→粗车圆弧面R14.25→精车外圆柱面Φ40.5→粗车外圆锥面→粗车外圆弧面R4.75→精车圆弧面R14→精车外圆锥面→精车外圆柱面Φ40→精车外圆弧面R5)。
(4)选择刀具选择1号刀具为90°硬质合金机夹偏刀,用于粗、精车削加工。
(5)切削用量选择粗车主轴转速n=630r/min,精车主轴转速V=110m/min,进给速度粗车为f=0.2mm/r,精车为f=0.07mm/r。
2.编写如图1-26所示的轴承套的加工工艺(1)零件图分析零件表面由内圆锥面,顺圆弧,逆圆弧和外螺纹等组成。
有多个直径尺寸与轴向尺寸有较高的尺寸精度和表面粗糙度要求(如果加工质量要求较高的表面不多可列出)。
零件材料:45号钢毛坯尺寸:φ80×112(2)零件的装夹及夹具的选择内孔加工时,以外圆定位,用三爪自动定心卡盘夹紧,需掉头装夹;加工外轮廓时,以圆锥心轴定位,用三爪卡盘夹持心轴左端,右端利用中心孔顶紧。
(3)加工方案及加工顺序的确定以零件右端面中心作为坐标原点建立工件坐标系。
根据零件尺寸精度及技术要求,确定先内后外,先粗后精的原则。
典型零件的机械加工工艺分析

第4章典型零件的机械加工工艺分析本章要点本章介绍典型零件的机械加工工艺规程制订过程及分析,主要内容如下:1.介绍机械加工工艺规程制订的原则与步骤。
2.以轴类、箱体类、拨动杆零件为例,分析零件机械加工工艺规程制订的全过程。
本章要求:通过典型零件机械加工工艺规程制订的分析,能够掌握机械加工工艺规程制订的原则和方法,能制订给定零件的机械加工工艺规程。
§4.1 机械加工工艺规程的制订原则与步骤§4.1.1机械加工工艺规程的制订原则机械加工工艺规程的制订原则是优质、高产、低成本,即在保证产品质量前提下,能尽量提高劳动生产率和降低成本。
在制订工艺规程时应注意以下问题:1.技术上的先进性在制订机械加工工艺规程时,应在充分利用本企业现有生产条件的基础上,尽可能采用国内、外先进工艺技术和经验,并保证良好的劳动条件。
2.经济上的合理性在规定的生产纲领和生产批量下,可能会出现几种能保证零件技术要求的工艺方案,此时应通过核算或相互对比,一般要求工艺成本最低。
充分利用现有生产条件,少花钱、多办事。
3.有良好的劳动条件在制订工艺方案上要注意采取机械化或自动化的措施,尽量减轻工人的劳动强度,保障生产安全、创造良好、文明的劳动条件。
由于工艺规程是直接指导生产和操作的重要技术文件,所以工艺规程还应正确、完整、统一和清晰。
所用术语、符号、计量单位、编号都要符合相应标准。
必须可靠地保证零件图上技术要求的实现。
在制订机械加工工艺规程时,如果发现零件图某一技术要求规定得不适当,只能向有关部门提出建议,不得擅自修改零件图或不按零件图去做。
§4.1.2 制订机械加工工艺规程的内容和步骤1.计算零件年生产纲领,确定生产类型。
2.对零件进行工艺分析在对零件的加工工艺规程进行制订之前,应首先对零件进行工艺分析。
其主要内容包括:(1)分析零件的作用及零件图上的技术要求。
(2)分析零件主要加工表面的尺寸、形状及位置精度、表面粗糙度以及设计基准等;(3)分析零件的材质、热处理及机械加工的工艺性。
典型零件的加工工艺分析案例
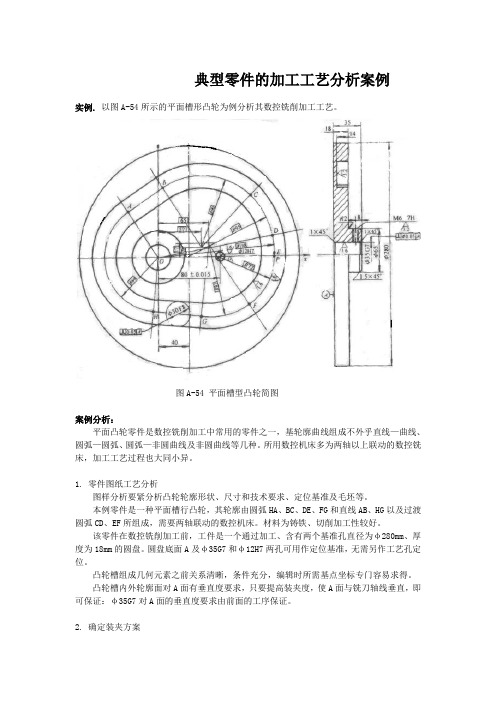
典型零件的加工工艺分析案例实例. 以图A-54所示的平面槽形凸轮为例分析其数控铣削加工工艺。
图A-54 平面槽型凸轮简图案例分析:平面凸轮零件是数控铣削加工中常用的零件之一,基轮廓曲线组成不外乎直线—曲线、圆弧—圆弧、圆弧—非圆曲线及非圆曲线等几种。
所用数控机床多为两轴以上联动的数控铣床,加工工艺过程也大同小异。
1. 零件图纸工艺分析图样分析要紧分析凸轮轮廓形状、尺寸和技术要求、定位基准及毛坯等。
本例零件是一种平面槽行凸轮,其轮廓由圆弧HA、BC、DE、FG和直线AB、HG以及过渡圆弧CD、EF所组成,需要两轴联动的数控机床。
材料为铸铁、切削加工性较好。
该零件在数控铣削加工前,工件是一个通过加工、含有两个基准孔直径为φ280mm、厚度为18mm的圆盘。
圆盘底面A及φ35G7和φ12H7两孔可用作定位基准,无需另作工艺孔定位。
凸轮槽组成几何元素之前关系清晰,条件充分,编辑时所需基点坐标专门容易求得。
凸轮槽内外轮廓面对A面有垂直度要求,只要提高装夹度,使A面与铣刀轴线垂直,即可保证:φ35G7对A面的垂直度要求由前面的工序保证。
2. 确定装夹方案一样大型凸轮可用等高垫块垫在工作台上,然后用压板螺栓在凸轮的孔上压紧。
外轮廓平面盘形凸轮的垫板要小于凸轮的轮廓尺寸,不与铣刀发生干涉。
对小型凸轮,一样用心轴定位,压紧即可。
依照图A-54所示凸轮的结构特点,采纳〝一面两孔〞定位,设计一〝一面两销〞专用夹具。
用一块320mm×320mm×40mm的垫块,在垫块上分别精镗φ35mm及φ12mm两个定位销孔的中心连接线与机床的x轴平行,垫块的平面要保证与工作台面平行,并用百分表检查。
图A-55为本例凸轮零件的装夹方案示意图。
采纳双螺母夹紧,提高装夹刚性,防止铣削时因螺母松动引起的振动。
图A-55凸轮装夹示意图3. 确定进给路线进给路线包括平面内进给和深度进给两部分路线。
对平面内进给,对外凸轮廓从切线方向切入,对内凹轮廓从过渡圆弧切入。
典型零件机械加工工艺与实例

典型零件机械加工工艺与实例一、引言在制造业中,机械加工是一项至关重要的工艺,它用于将原材料加工成各种形状和尺寸的零件。
典型零件机械加工工艺是指那些在机械加工过程中常见且广泛应用的工艺方法。
本文将探讨几种典型的零件机械加工工艺,并提供实例进行说明。
二、铣削加工铣削加工是一种常见的机械加工工艺,通过旋转刀具将工件上的材料切削掉,从而得到所需形状和尺寸的零件。
铣削加工可以分为平面铣削、立铣、端铣等多种形式。
2.1 平面铣削平面铣削是将刀具与工件平行或近似平行于工件表面进行切削的加工方式。
它适用于平面、凸轮槽、直齿轮等零件的加工。
平面铣削的实例包括制作平面底座、平面销轴等。
2.2 立铣立铣是将刀具与工件垂直或近似垂直于工件表面进行切削的加工方式。
它适用于开槽、钻孔、倒角等零件的加工。
立铣的实例包括制作键槽、孔加工等。
2.3 端铣端铣是将刀具与工件端面进行切削的加工方式。
它适用于平面、凹槽、凸齿轮等零件的加工。
端铣的实例包括制作平面销轴端面、齿轮端面等。
三、车削加工车削加工是通过旋转工件,并将刀具沿工件轴向移动,将工件上的材料切削掉的加工方式。
车削加工可分为外圆车削和内圆车削两种形式。
3.1 外圆车削外圆车削是将刀具与工件外表面接触,并进行切削的加工方式。
它适用于制作轴、销轴、螺纹等零件。
外圆车削的实例包括制作轴、销轴等。
3.2 内圆车削内圆车削是将刀具放置在工件内部,并进行切削的加工方式。
它适用于制作孔、内螺纹等零件。
内圆车削的实例包括制作孔、内螺纹等。
四、钻削加工钻削加工是通过旋转刀具,使刀具的尖端与工件接触,并将工件上的材料切削掉的加工方式。
钻削加工适用于制作孔、沉孔等零件。
4.1 钻孔钻孔是将刀具的尖端放置在工件上,并进行切削的加工方式。
它适用于制作各种规格和深度的孔。
钻孔的实例包括制作螺纹孔、沉孔等。
五、铣床加工铣床加工是一种常用的机械加工工艺,它通过铣刀在工件上进行切削,得到所需形状和尺寸的零件。
典型套筒类零件的加工工艺分析

典型套筒类零件的加工工艺分析引言:套筒类零件是机械零件中常见的一种,广泛应用于各种机械设备中。
其加工工艺分析对于提高零件的加工质量和降低成本具有重要意义。
本文将从设计、材料选择、工艺规划以及加工工艺等方面对典型套筒类零件的加工工艺进行详细分析。
一、设计:二、材料选择:三、工艺规划:1.工艺路线规划:根据零件的形状、材料和加工要求,确定合适的工艺路线。
典型的工艺路线包括铣削、车削、钻孔、镗孔、磨削等工序。
2.切削参数选择:根据零件的材料和加工要求,选择合适的切削参数,包括切削速度、进给速度、切削深度等。
通过试切试验和经验总结,不断优化和调整切削参数。
3.夹具设计:根据零件的形状和加工要求,设计合适的夹具,以保证零件在加工过程中的稳定性和精度。
四、加工工艺:1.车削工艺:车削是加工套筒类零件常用的工艺之一、根据零件的形状和加工要求,选择合适的切削工具和切削参数进行车削。
2.镗削工艺:镗削用于加工孔的精度要求较高的套筒类零件。
根据零件的尺寸和加工要求,选择合适的镗削刀具和切削参数进行镗削。
3.铣削工艺:铣削常用于加工套筒类零件的外形轮廓。
根据零件的形状和加工要求,选择合适的铣削刀具和切削参数进行铣削。
4.钻孔工艺:钻孔通常用于套筒类零件的孔加工。
根据零件的尺寸和加工要求,选择合适的钻孔刀具和切削参数进行钻孔。
5.磨削工艺:磨削常用于加工套筒类零件的表面精加工。
根据零件的表面粗糙度要求,选择合适的磨削工具和切削参数进行磨削。
五、加工装备和工具选择:根据零件的工艺要求,选择合适的加工装备和工具。
常用的加工设备包括车床、铣床、钻床、磨床等。
根据工艺要求和经济性考虑,选择合适的设备和工具。
六、检验和质量控制:在加工过程中,需要进行适当的检验和质量控制,以确保零件的加工质量。
常用的检验方法包括尺寸检验、形状检验、表面粗糙度检验等。
结论:典型套筒类零件的加工工艺分析对于提高零件的加工质量和降低成本具有重要意义。
通过合理的设计、材料选择、工艺规划和加工工艺,可以实现零件的精确加工和高效生产。
- 1、下载文档前请自行甄别文档内容的完整性,平台不提供额外的编辑、内容补充、找答案等附加服务。
- 2、"仅部分预览"的文档,不可在线预览部分如存在完整性等问题,可反馈申请退款(可完整预览的文档不适用该条件!)。
- 3、如文档侵犯您的权益,请联系客服反馈,我们会尽快为您处理(人工客服工作时间:9:00-18:30)。
套筒类零件的安装
§6.2.3 套类零件孔的加工方法
套类零件的孔加工方法常用的有:钻孔、扩孔、 镗孔、车孔、铰孔、磨孔、拉孔、珩孔、研磨孔 及孔表面滚压加工。其中钻孔、扩孔、镗孔、车 孔常作为粗加工与半精加工;而铰孔、磨孔、拉 孔、珩孔、研磨孔及孔表面滚压加工作为精加工 方法。
1. 磨孔 内圆磨削具有以下特点:
(1) 孔与外圆的精度要求。 (2) 几何形状精度要求。 (3) 相互位置精度要求。
3、套筒类零件的材料及毛坯
材料 套类零件一般用钢、铸铁、青铜、黄铜制成。有 些滑动轴承可选用双金属结构,对一些强度和硬度要求 较高的套类零件(如镗床主轴套筒、伺服阀套),可选用 优质合金钢(38CrMoALA、18CrNiWA)。
深孔钻削
深孔镗削
浮动镗孔
深孔加工
精细镗孔 珩磨内孔 内孔研磨 滚压孔
精加工
§6.3 齿轮加工
§6.3.1 概述
齿轮的功用
圆柱齿轮是机械传动中的重要零件,其功用是按规 定的传动比传递运动和动力。它具有传动比准确、 传动力大、效率高、结构紧凑、可靠性好等优点, 广泛应用于各种现代机器和仪表中。
圆柱齿轮的结构与分类
• 圆柱齿轮可以看成由齿圈和轮体两部分所构成,
在轮圈上切出直齿、斜齿或人字齿(图6-9)等就 形成了齿轮。 • 按齿形曲线性质可分为渐开线、摆线、鼓形和圆 弧等。 • 齿轮的结构分类常以轮体结构的形状为依据,即 可分为单联齿轮、双联齿轮、三联齿轮、连轴齿轮、 内齿轮、装配齿轮、齿条及扇形齿轮等(图6-10)
图c) • 4 以顶尖孔安装——顶尖孔定心、定位。图d)
图6-12 齿形加工安装实例
• 二 齿坯的加工方式 • 1 内孔安装 控制端面跳动与内径公差。
• 2 外圆找正安装 控制端面跳动与外径公差。
• 3 轴颈安装 控制轴颈端面跳动、外径公差与同轴 度。
常用的材料如45、40Cr、20CrMnTi、35CrMoV等。大型 齿轮为了节省贵重金,可做成装配式的。如轮体用铁做,齿 圈用合金钢做。
齿轮的热处理 ① 轮体热处理。是在齿坯锻造及粗加工之后,安排的 预先热处理,一般为正火或调质处理,其目的是消除锻造及 粗加工引起的残余应力,改善材料的切削性能,提高综合力 学性能并为齿面热处理做好准备。 ② 齿面热处理。是在齿形加工后,对轮齿齿面进行渗 碳淬火、高频淬火、氮化处理等表面热处理,其目的是提高 齿面硬度及耐磨性。
• 1 用中心孔定位安装 • 2 用孔定位安装 • 3 以外圆表面定位安装
主轴零件主要工序的加工方法
1. 外圆的加工 2. 中心孔的加工 3. 锥孔的精加工 4. 花键表面加工
主轴的检验
精度检验 表面质量检验
尺寸精度、位置精度、形状精度 表面粗糙度和表面力学物理性能
单件小批生产中,尺寸精度可采用外径千分尺检验; 大批量生产中,为节省时间,可采用光滑极限量规 检验。
齿轮的毛坯 齿轮的毛坯形式主要有棒料、锻件和铸件。棒料用于 小尺寸、结构简单且对强度要求低的齿轮;当齿轮要求强 度高、耐磨、耐冲击时多选用锻件;对于结构复杂、直径 大于400 mm~600 mm的齿轮,一般用铸造方法制造毛坯。
对大尺寸、低精度的齿轮可以直接铸出轮齿,以减少机械 加工量;结构复杂的小齿轮可采用精密铸造、压力铸造、 热轧及冷挤、粉末冶金等新工艺制造出具有轮齿的齿坯, 以提高劳动生产率。
相互位置精度
• 为保证轴上传动件的传动精度,必须规定配合轴颈相对支 撑轴颈的位置精度,一般通过径向圆跳动或同轴度来保证。 普通精度轴的配合轴颈对支撑轴颈的径向圆跳动,一般规 定为0.01 mm~0.03 mm,高精度轴为 0.001 mm~0.005 mm。
表面粗糙度
• 一般地,轴上与轴承相配合的支撑轴颈的表面质 量要求最高,表面粗糙度Ra值为0.63 µm~ 0.16 µm;其次是配合轴颈和工作表面,其表面 粗糙度Ra值为2.5 µm~0.63 µm。
撑轴颈一般与轴承配合,是 轴类零件的主要表面,它影响轴的回转精 度和工作状态,对其尺寸精度要求较高, 为IT5~IT7;配合轴颈尺寸精度可低些, 为IT6~IT9。
几何形状精度
轴类零件的形状精度(如圆度、圆柱度、直 线度等)应控制在直径公差之内;对精度要求高的 轴,应在图样上标注其形状公差。
公法线 长度变动公差/mm 径向综合公差/mm 一齿 径向综合公差/mm 齿向公差/mm 公法线 平均长度/mm
3.5 66 20° 766KM GB10095—88
0.036 0.08
0.016 0.009
W= 80.7200..1149
§6.3.2 齿轮材料及毛坯
齿轮材料种类较多,如锻钢、型材、铸钢、铸铁、铸铜 、工程塑料等。
轴类零件的材料及热处理
材料和热处理
• 一般轴类零件常选用45钢,这种材料经调质或正 火后,能获得一定的切削性能、强度和韧性,具 有较好的综合力学性能;中等精度而转速较高的 轴类零件可选用40Cr等合金结构钢,经调质和 表面淬火处理获得较好的综合力学性能;高精度 的轴可选用轴承钢GCr15和弹簧钢65Mn等材料, 经调质和表面淬火获得更好的耐磨性和耐疲劳性; 高转速、重载荷等条件下工作的轴可以选用 20CrMnTi、20Mn2B、20Cr等低碳合金钢或 38CrMoAI氮化钢,经过淬火或氮化处理获得 高的表面硬度、耐磨性和心部强度。
件孔径与长度的限制,刚性较差,容易弯曲变形,并引起 振动,影响加工质量。
(5) 排屑困难。为了排屑方便,可采用干磨。因为切削 液不易进入磨削区,排屑比较困难,对于脆性材料有时可 采用干磨。
2. 深孔加工
一般将孔的长度L与直径d之比L/d>5的孔,称为深孔,
深孔加工与一般孔加工比较,具有生产率低、难度大 的特点。
2、车床主轴加工工艺过程
3. 车床主轴加工工艺过程分析
(1) 定位基准的选择。 (2) 加工阶段的划分 (3) 加工顺序的安排
影响工艺路线的因素及安装
一 影响因素
1 轴的尺寸及精度要求。 2 轴的长径比,即是刚性轴还是柔性轴。
3 是否进行中间热处理。 二 安装方式
为保证轴的相互位置精度,选择定位基准面时应尽量符合 基准重合和基准统一的原则。安装方式有三种
§6.1 轴类加工
轴类零件的功用、结构与分类
• 主要功用有:
•
支承传动件(齿轮、皮带轮等)、传递转矩、承受载荷。
• 轴的结构特点:
•
长度大于直径,一般由同轴心的外圆、圆锥、内孔、螺纹、
键槽等组成。
• 轴的种类有:
•
光轴(a)、阶梯轴(b)、花键轴(c)、偏心轴(d)、曲轴(e)、
凸轮轴(f)、空心轴(g)、十字轴等。如图6-1所示:
圆柱齿轮的技术要求
(1) 圆柱齿轮传动精度要求
① 传递运动的准确性。 ② 传递运动的平稳性。 ③ 载荷分布的均匀性。 ④ 传动侧隙的合理性。
(2) 精度等级与公差组
技术条件 1. 1∶12锥度塞规检查,接触面不少于75% 2. 材料:45钢
3. 热处理:齿部G54
模数/mm 齿数 压力角 精度等级
对于钢质齿轮,除尺寸小且不太重要的齿轮采用棒料 外,一般都要采用锻造毛坯。根据生产批量的不同,可分 别采用自由锻和模锻。
§6.3.3 齿坯加工
• 一、齿形加工时的安装(图6-11) • 1 以心轴安装——内孔定心、端面定位。图a)
2 以外圆找正安装——外径定心、端面定位。图b) • 3 以轴径、齿圈安装——轴径定心、齿圈端面定位。
深孔加工的工艺特点: ① 刀具的使用寿命降低。刀具几乎在封闭的状态下 工作,切削温度很高,冷却散热条件比较差。 ② 深孔刀具较细长,强度和刚性比较差,深孔加工 中容易引起轴线歪斜和振动,孔的精度不易保证。 ③ 由于排屑比较困难,易堵塞深孔,会加快刀具磨 损,严重时还会引起刀具崩刃甚至折断。
粗加工与半精加工
毛坯 孔径较大时,常选择无缝钢管或带孔的铸件和锻 件;孔径较小时,一般选择热轧或冷拉棒料。大批量 生产时,采用冷挤压、粉末冶金等先进毛坯制造工艺, 不仅节约材料,而且可提高生产率和毛坯精度。
6.2.2 套类零件加工工艺分析
套类零件由于功用、尺寸、结构形状、材料、热处 理方法的不同,其工艺过程差别很大。但大多数在加 工中都要保证内孔与外圆的同轴度及端面与内、外圆 轴线的垂直度要求。按结构形状来分,大体上可分为 短套筒和长套筒两类。它们在加工中对工件的装夹方 法有很大区别。
第六章 典型零件加工工艺
教学目标
学习机械制造技术的重要目的之一,是熟 悉和掌握机器零件的加工工艺,能合理地编制 出中等复杂程度零件的机械加工工艺规程。本 章通过对几种常见典型机器零件的加工工艺过 程的分析及其重要表面的加工方法介绍,使读 者能够达到综合运用所学知识,分析和解决实 际加工问题的目的。
毛坯
• 轴类零件最常用的毛坯是圆棒料和锻件。 重要的轴尤其要使用锻件,以保证金属内 部纤维组织均匀连续分布,获得较高的强 度。有些大型轴或结构复杂的轴采用铸件 毛坯。
轴类零件加工工艺分析
1. 主轴的技术条件分析 从图6-1车床主轴零件图可以看出,主轴的支撑轴颈是主轴部件的装配基 准,其制造精度直接影响到主轴部件的回转精度,支撑轴颈A、B的圆度 公差为0.003 mm。相对于A、B基准公共轴线的径向圆跳动公差为 0.005 mm。支撑轴颈与配合轴颈的尺寸精度根据使用要求通常为IT6~IT5。 主轴前端锥孔,必须与支撑轴颈严格同轴。其要求为在轴端处相对A、B 基准的径向圆跳动公差为0.005 mm,在离轴端300 mm处的径向圆跳动公 差为0.01 mm。主轴前端圆锥面必须与支撑轴颈同轴,端面与轴线垂直。 其相对A、B基准的斜向圆跳动公差为0.008 mm,端面圆跳动公差为 0.008 mm。主轴上的螺纹是用来固定与调节主轴轴承间隙的,必须控制 螺纹中径与支撑轴径的同轴度。 主轴加工的关键是保证支撑轴颈本身的尺寸精度、表面粗糙度以及形位 公差要求。