生产三不原则生产过程不良品控制
生产三不原则-生产过程不良品控制
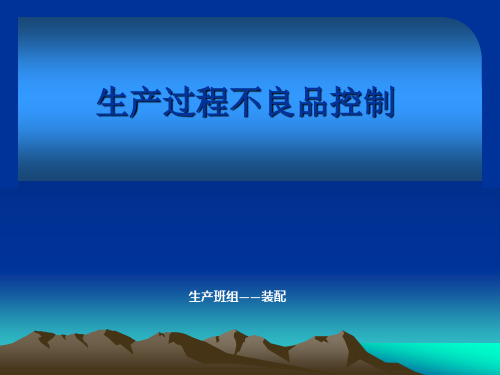
生产班组——装配
目录
➢1.不良品的产生 ➢2.造成不良品因素 ➢3.避免生产不良品方法 ➢4.本区域不良品分析 ➢5.故事分享
第2页
不良品的产生
有生产就有不良品的产生
2013年4月度临港装不位位、漏
装统计 漏装位统计
5 单位:件
4
前保 后保
3
2012来自011
0
0
0
装配不到位统计
把好的经验做好培训,让大家共享,培训好了, 可以少犯错误,少走弯路,大家都会向同一个 方向,也是正确的方向使力,这样的团队或公 司会战无不胜的。
2.制度就是要无条件执行的。
因为制度是经验的总结。不遵守制度是要 犯错误或受惩罚的。
经验分享 经验固化
共享
金子与石子 一个人整天抱怨生活对他不公平,抱怨自己的才能不被人欣赏,终于这
1月
2月
3月
4月
5 单位:件
4
1
前保 后保
3
1
1
2
3
1
2
2
1
0
0
1月
2月
3月
4月
2013年4月度临港报废统计
单位:件
20 19
报废缺陷明细
18
16
15 15
14
12
11
10
8
6
5
4
333
2
1111111
0
划 伤
断 裂
碰 伤
卡 脚 断 裂
修 边 过 头 变 形 缺 料 色 差 滴 液
冲 孔 开 裂
冲 孔 变 形
件事让上帝知道了。上帝来到这个人的身边,捡起地上的一颗石子扔到了石 堆里,说:假如石子就是你,把自己找出来。那人找了好久也没找到,上帝 又往石堆里扔了块金子,说:假如金子就是你,把自己找出来。结果当然是 那人一眼就认出了代表自己的金子。
现场品质管理:三不原则(1)
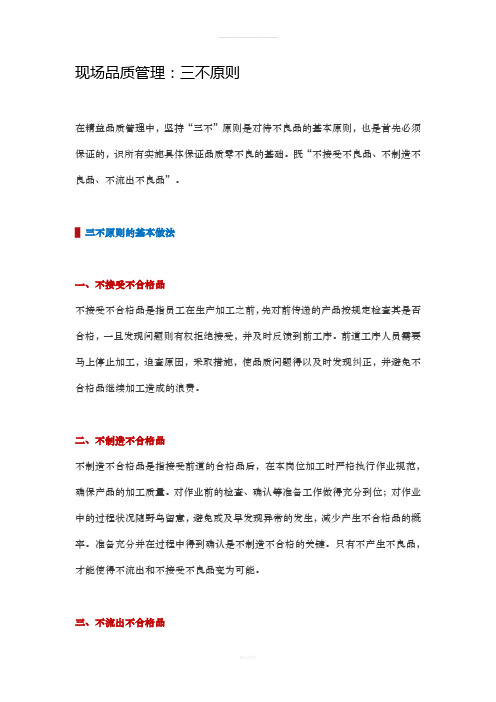
现场品质管理:三不原则在精益品质管理中,坚持“三不”原则是对待不良品的基本原则,也是首先必须保证的,识所有实施具体保证品质零不良的基础。
既“不接受不良品、不制造不良品、不流出不良品”。
▌三不原则的基本做法一、不接受不合格品不接受不合格品是指员工在生产加工之前,先对前传递的产品按规定检查其是否合格,一旦发现问题则有权拒绝接受,并及时反馈到前工序。
前道工序人员需要马上停止加工,追查原因,采取措施,使品质问题得以及时发现纠正,并避免不合格品继续加工造成的浪费。
二、不制造不合格品不制造不合格品是指接受前道的合格品后,在本岗位加工时严格执行作业规范,确保产品的加工质量。
对作业前的检查、确认等准备工作做得充分到位;对作业中的过程状况随野鸟留意,避免或及早发现异常的发生,减少产生不合格品的概率。
准备充分并在过程中得到确认是不制造不合格的关键。
只有不产生不良品,才能使得不流出和不接受不良品变为可能。
三、不流出不合格品不流出不合格品是指员工完成本工序加工,需检查确认产品质量,一旦发现不良品,必须及时停机,将不良品在本工序截下,并且在本工序内完成不良品处置并采取防止措施。
本道工序应保证传递的是合格产品,会被下道工序或“客户”拒收。
▌三不原则的实施要点一、谁制造谁负责一旦产品设计开发结束,工艺参数流程明确,则产品的质量波动就是制造过程的问题。
每个人的质量责任从接受上道工序合格产品开始,规范作业确保本道工序的产品质量符合要求是员工最大的任务。
一旦在本道工序发现不良或接到后道工序反馈的不良信息后,员工必须立即停止生产,调查原因,采取对策对产品的质量负责到底。
二、谁制造谁检查产品的生产者,同时出是产品的检查者,产品的检查只是生产过程的一个环节。
通过检查,确认生产合格,才能确保合格产品流入下道工序。
通过自身检查,作业者对本工序加工产品的状态可以了解得更清楚,从而有利于员工不断提升加工水平,提高产品质量。
三、作业标准化产品从设计开发、设定工艺参数开始,就要对所有的作业流程中作业步骤,作业细节进行规范化、标准化,并使其不断完善。
生产的三不原则
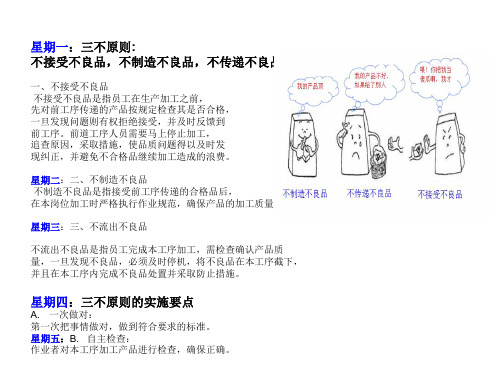
不流出不良品是指员工完成本工序加工,需检查确认产品质 量,一旦发现不良品,必须及时停机,将不良品在本工序截下, 并且在本工序内完成不良品处置并采取防止措施。
星期四:三不原则的实施要点
A. 一次做对: 第一次把事情做对,做到符合要求的标准。 星期五:B.
星期一:三不原则: 不接受不良品,不制造不良品,不传递不良品。
一、不接受不良品 不接受不良品是指员工在生产加工之前, 先对前工序传递的产品按规定检查其是否合格, 一旦发现问题则有权拒绝接受,并及时反馈到 前工序。前道工序人员需要马上停止加工, 追查原因,采取措施,使品质问题得以及时发 现纠正,并避免不合格品继续加工造成的浪费。 星期二:二、不制造不良品 不制造不良品是指接受前工序传递的合格品后, 在本岗位加工时严格执行作业规范,确保产品的加工质量。 星期三:三、不流出不良品
质量管理的“三检”和“三不”原则

质量管理的“三检”和“三不”原则前言三检制度,即为三级检验制度。
为保证产品质量,一般运用自检互检(一级)、班级检验(二级)、专职检验(三级)而最终确定。
因产品生产过程的不同,在不同行业有不同的说法与含义。
三检制度和三不原则是品质理念中最基本的内容,在平时的品质管理活动中一定要渗透到最基层员工!三不原则不接受不良品,不制造不良品,不流出不良品基本要求为:一、不接受不合格品不接受不合格品是指员工在生产加工之前,先对前传递的产品按规定检查其是否合格,一旦发现问题则有权拒绝接受,并及时反馈到前工序。
前道工序人员需要马上停止加工,追查原因,采取措施,使品质问题得以及时发现纠正,并避免不合格品继续加工造成的浪费。
二、不制造不合格品不制造不合格品是指接受前道的合格品后,在本岗位加工时严格执行作业规范,确保产品的加工质量。
对作业前的检查、确认等准备工作做得充分到位;对作业中的过程状况随野鸟留意,避免或及早发现异常的发生,减少产生不合格品的概率。
准备充分并在过程中得到确认是不制造不合格的关键。
只有不产生不良品,才能使得不流出和不接受不良品变为可能。
三、不流出不合格品不流出不合格品是指员工完成本工序加工,需检查确认产品质量,一旦发现不良品,必须及时停机,将不良品在本工序截下,并且在本工序内完成不良品处置并采取防止措施。
本道工序应保证传递的是合格产品,会被下道工序或“客户”拒收。
1、三不原则的实施要点一、谁制造谁负责一旦产品设计开发结束,工艺参数流程明确,则产品的质量波动就是制造过程的问题。
每个人的质量责任从接受上道工序合格产品开始,规范作业确保本道工序的产品质量符合要求是员工最大的任务。
一旦在本道工序发现不良或接到后道工序反馈的不良信息后,员工必须立即停止生产,调查原因,采取对策对产品的质量负责到底。
二、谁制造谁检查产品的生产者,同时出是产品的检查者,产品的检查只是生产过程的一个环节。
通过检查,确认生产合格,才能确保合格产品流入下道工序。
三不原则
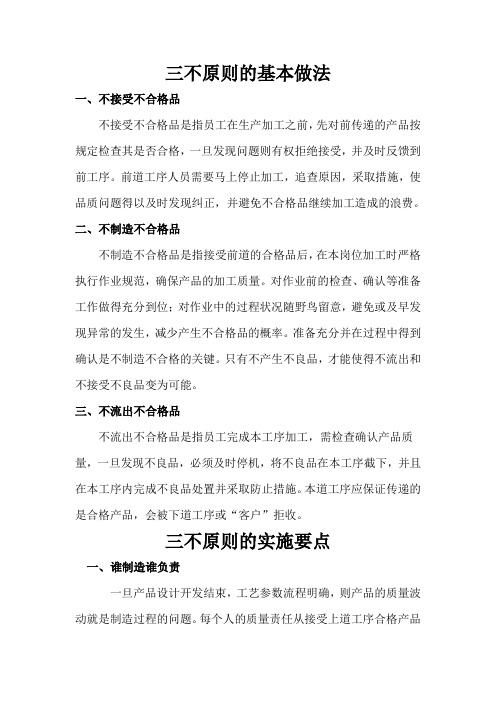
三不原则的基本做法一、不接受不合格品不接受不合格品是指员工在生产加工之前,先对前传递的产品按规定检查其是否合格,一旦发现问题则有权拒绝接受,并及时反馈到前工序。
前道工序人员需要马上停止加工,追查原因,采取措施,使品质问题得以及时发现纠正,并避免不合格品继续加工造成的浪费。
二、不制造不合格品不制造不合格品是指接受前道的合格品后,在本岗位加工时严格执行作业规范,确保产品的加工质量。
对作业前的检查、确认等准备工作做得充分到位;对作业中的过程状况随野鸟留意,避免或及早发现异常的发生,减少产生不合格品的概率。
准备充分并在过程中得到确认是不制造不合格的关键。
只有不产生不良品,才能使得不流出和不接受不良品变为可能。
三、不流出不合格品不流出不合格品是指员工完成本工序加工,需检查确认产品质量,一旦发现不良品,必须及时停机,将不良品在本工序截下,并且在本工序内完成不良品处置并采取防止措施。
本道工序应保证传递的是合格产品,会被下道工序或“客户”拒收。
三不原则的实施要点一、谁制造谁负责一旦产品设计开发结束,工艺参数流程明确,则产品的质量波动就是制造过程的问题。
每个人的质量责任从接受上道工序合格产品开始,规范作业确保本道工序的产品质量符合要求是员工最大的任务。
一旦在本道工序发现不良或接到后道工序反馈的不良信息后,员工必须立即停止生产,调查原因,采取对策对产品的质量负责到底。
二、谁制造谁检查产品的生产者,同时出是产品的检查者,产品的检查只是生产过程的一个环节。
通过检查,确认生产合格,才能确保合格产品流入下道工序。
通过自身检查,作业者对本工序加工产品的状态可以了解得更清楚,从而有利于员工不断提升加工水平,提高产品质量。
三、作业标准化产品从设计开发、设定工艺参数开始,就要对所有的作业流程中作业步骤,作业细节进行规范化、标准化,并使其不断完善。
每一个员工也必须严格执行标准化作业。
标准化是该工序最佳的作业方法,是保证产品质量一致性的唯一途径,否则制造一大堆不良品却找不到不良的根本原因,这个时候“三不原则”只能制造混乱,而不是品质。
工厂质量管理三不原则的实施要点(标准版)

工厂质量管理三不原则的实施要点1、谁制造谁负责一旦产品设计开发结束,工艺流程参数明确,则产品的质量波动就是制造过程的问题。
每个人的质量责任从接受上道工序合格产品开始,规范作业,确保本道工序的产品质量符合要求是作业者最大的任务。
一旦在本道工序发现不良或接到后道工序反馈的不良信息后,作业者必须立即停止生产,调查原因,采取对策对产品的质量负责到底。
2、谁制造谁检查产品的制造者,同时也是产品的检查者,产品的检查只是生产过程的一个环节。
通过检查确认生产合格,才能确保合格产品流入下道工序。
通过自身检查,作业者对本工序加工产品的状态可以了解得更清楚,从而有利于作业者不断提升加工水平,提高产品质量。
3、作业标准化产品从设计开发、设定工艺参数开始,就要对所有的作业流程中步骤,作业细节进行规范化、标准化,并使其不断完善。
每一个作业者也必须严格执行标准化作业。
标准化是保证该工序最佳的作业方法,是保证产品质量一致性的唯一途径,否则制造一大堆不良品却找不到不良的根本原因,这个时候“三不”原则只能制造混乱,而不是品质。
4、全数检查所有产品,所有工序无论采取什么形式都必须由作业者实施全数检查。
5、工序内检查质量是作业者制造出来的,如果安排另外的检查人员在工序外对产品进行检查或修理,即会造成浪费,也不能提高作业者的责任感,还会姑息作业者对其产品质量的漠视。
6、不良停产在工序内一旦发现不良产品,作业者有权利也有责任停止生产,并及时采取调查对策活动。
7、现时处理在生产过程中,产生不合格品时,作业者必须从生产状态转变到调查处理状态,马上停止作业并针对产生不良品的人、机、料、法、环等现场要素及时确认,调查造成不良的“真正元凶”并及时处理。
8、不良曝光在生产过程中出现的任何不良,必定有其内在的原因,只有真正解决了发生不良的每个原因,才能控制制造不合格品,实现零不良,才能让客户真正满意。
因此对于发生不良,不仅作业者要知道,还必须让管理层知道,质量保证的人员知道,让设计开发的人员知道,大家一起认真分析对策,并改善作业标准,而不是简单地由作业者对不合格品自行返工或报废;否则,下一次还会发生同样的问题。
质量管理的三检和三不原则

三不原则不接受不良品,不制造不良品,不流出不良品。
▌基本要求为:一、不接受不合格品不接受不合格品是指员工在生产加工之前,先对前传递的产品按规定检查其是否合格,一旦发现问题则有权拒绝接受,并及时反馈到前工序。
前道工序人员需要马上停止加工,追查原因,采取措施,使品质问题得以及时发现纠正,并避免不合格品继续加工造成的浪费。
二、不制造不合格品不制造不合格品是指接受前道的合格品后,在本岗位加工时严格执行作业规范,确保产品的加工质量。
对作业前的检查、确认等准备工作做得充分到位;对作业中的过程状况随野鸟留意,避免或及早发现异常的发生,减少产生不合格品的概率。
准备充分并在过程中得到确认是不制造不合格的关键。
只有不产生不良品,才能使得不流出和不接受不良品变为可能。
三、不流出不合格品不流出不合格品是指员工完成本工序加工,需检查确认产品质量,一旦发现不良品,必须及时停机,将不良品在本工序截下,并且在本工序内完成不良品处置并采取防止措施。
本道工序应保证传递的是合格产品,会被下道工序或“客户”拒收。
▌三不原则的实施要点一、谁制造谁负责一旦产品设计开发结束,工艺参数流程明确,则产品的质量波动就是制造过程的问题。
每个人的质量责任从接受上道工序合格产品开始,规范作业确保本道工序的产品质量符合要求是员工最大的任务。
一旦在本道工序发现不良或接到后道工序反馈的不良信息后,员工必须立即停止生产,调查原因,采取对策对产品的质量负责到底。
二、谁制造谁检查产品的生产者,同时出是产品的检查者,产品的检查只是生产过程的一个环节。
通过检查,确认生产合格,才能确保合格产品流入下道工序。
通过自身检查,作业者对本工序加工产品的状态可以了解得更清楚,从而有利于员工不断提升加工水平,提高产品质量。
三、作业标准化产品从设计开发、设定工艺参数开始,就要对所有的作业流程中作业步骤,作业细节进行规范化、标准化,并使其不断完善。
每一个员工也必须严格执行标准化作业。
标准化是该工序最佳的作业方法,是保证产品质量一致性的唯一途径,否则制造一大堆不良品却找不到不良的根本原因,这个时候“三不原则”只能制造混乱,而不是品质。
三不五检原则

三不、五检原则整个生产过程中所有操作者、班组长、架模工、检验人员都必须按照三不五检原则执行,必须确保产品从开始生产到结束的整个过程有效、可控。
三不、五检原则:即“不生产不良品、不传递不良品、不接受不良品;生产前做好自检、互检、首检、巡检、末检”一、“三不原则”1、不生产不良品:指操作者、架模工在发现产品存在质量问,或者明知模具工装不能产出合格品时仍继续生产。
生产过程中任何一道工序操作工人、架模工、检验人员都应该确认零件合格、有效之后才开始生产,从源头控制不良品出现。
2、不传递不良品:指操作者、架模工明知道该道工序生产出来的产品由缺陷、不合格,仍流转到下工序,而且没有告知给下工序操作者、检验人员。
所以生产过程中,发现问题产品应该及时隔离、按照《不合格品处理流程》进行处理。
3、不接受不良品:指操作者、架模、班长知道该产品存在缺陷、不合格,仍然接收,继续生产。
所以生产过程中,操作者在接收产品之前,应该做到认真相互检查、确认、交检合格之后才能接收该产品,才能开始下道工序生产。
二、“五检原则”1、自检:指操作者、架模工在架好模具工装后,开始生产的、货生产过程中的产品,自己应该认真检查零件外观、尺寸等是否存在缺陷、是否合格,自己确认合格之后才交到检验人员确认。
2、互检:指在生产开始、或生产过程中、或接到上道工序产品时,操作者对产品进行自检,自己不能确定的情况下可以向其他员工、架模工、班组长寻求帮组检查。
3、首检:指操作者、架模工在模具工装安装好后、或者更换工装、或者每班开始时,生产出来的3~5件产品必须交到检验人员进行外观尺寸检查,并记录签字。
只有首检检验人员确认合格之后,才可正式开始生产。
4、巡检:指检验人员、班组长在生产过程中对正在生产的产品进行随机抽取,检验外观尺寸,确保生产过程模具工装继续有效、合格。
所以自由加强巡检力度、频次才能更好的监控生产过程及时发现控制产品状态。
5、末检:指操作者生产结束、或者该班结束,最后生产的3~5件交检验人员、班组长进行外观尺寸检查。
品质管理的三不原则

品质管理的三不原则
品质管理三不原则:不生产不良品,不接受不良品,不流送不良品。
从采购工作开始:建立严格的原材料检验制度与工作法,不接受不良品。
按技术标准与工艺要求生产:技术部门在产前一定要提出技术标准与工艺要求,以及相关的图纸,并且要组织全员学习。
只有技术人员知道的技术标准是没有意义的标准。
错误的图纸是最可怕的不良品。
产品检验支持标准落实。
是说好产品是生产出来的,不是检验出来的。
但是计件管理、定额管理,若没有生产过程品质检验管理工作,品质标准无法得到有效的保证。
不负责任的检验人员是造成不良品流送的主要原因。
生产过程工序互检:上道责任工序对下道责任工序负责不生产不良品。
下道责任工序对上道工序进行监督不接受不良品。
最后包装检验:不流送不良品出厂。
若为了暂时利益将不良品流送出厂,那么实际上是在砸企业的饭碗。
车间质量管理的三不原则

车间质量管理的三不原则(总3页)本页仅作为文档封面,使用时可以删除This document is for reference only-rar21year.March生产车间产品质量的三不原则◆三不原则的基本做法一、不接受不合格品©不接受不合格品是指员工在生产加工之前,先对前传递的产品按规定检查其是否合格,一旦发现问题则有权拒绝接受,并及时反馈到前工序。
前道工序人员需要马上停止加工,追查原因,采取措施,使品质问题得以及时发现纠正,并避免不合格品继续加工造成的浪费。
二、不制造不合格不制造不合格品是指接受前道的合格品后,在本岗位加工时严格执行作业规范,确保产品的加工质量。
对作业前的检查、确认等准备工作做得充分到位;对作业中的过程状况随时留意,避免或及早发现异常的发生,减少产生不合格品的概率。
准备充分并在过程中得到确认是不制造不合格的关键。
只有不产生不良品,才能使得不流出和不接受不良品变为可能。
三、不流出不合格品不流出不合格品是指员工完成本工序加工,需检查确认产品质量,一旦发现不良品,必须及时停机,将不良品在本工序截下,并且在本工序内完成不良品处置并采取防止措施。
本道工序应保证传递的是合格产品,不会被下道工序或“客户”拒收。
◆三不原则的实施要点一、谁制造谁负责一旦产品设计开发结束,工艺参数流程明确,则产品的质量波动就是制造过程的问题。
每个人的质量责任从接受上道工序合格产品开始,规范作业确保本道工序的产品质量符合要求是员工最大的任务。
一旦在本道工序发现不良或接到后道工序反馈的不良信息后,员工必须立即停止生产,调查原因,采取对策对产品的质量负责到底。
二、谁制造谁检查产品的生产者,同时出是产品的检查者,产品的检查只是生产过程的一个环节。
通过检查,确认生产合格,才能确保合格产品流入下道工序。
通过自身检查,作业者对本工序加工产品的状态可以了解得更清楚,从而有利于员工不断提升加工水平,提高产品质量。
三、作业标准化产品从设计开发、设定工艺参数开始,就要对所有的作业流程中作业步骤,作业细节进行规范化、标准化,并使其不断完善。
现场品质管理:三不原则

现场品质管理:三不原则在精益品质管理中,坚持“三不”原则是对待不良品的基本原则,也是首先必须保证的,识所有实施具体保证品质零不良的基础。
既“不接受不良品、不制造不良品、不流出不良品”。
▌三不原则的基本做法一、不接受不合格品不接受不合格品是指员工在生产加工之前,先对前传递的产品按规定检查其是否合格,一旦发现问题则有权拒绝接受,并及时反馈到前工序。
前道工序人员需要马上停止加工,追查原因,采取措施,使品质问题得以及时发现纠正,并避免不合格品继续加工造成的浪费。
二、不制造不合格品不制造不合格品是指接受前道的合格品后,在本岗位加工时严格执行作业规范,确保产品的加工质量。
对作业前的检查、确认等准备工作做得充分到位;对作业中的过程状况随野鸟留意,避免或及早发现异常的发生,减少产生不合格品的概率。
准备充分并在过程中得到确认是不制造不合格的关键。
只有不产生不良品,才能使得不流出和不接受不良品变为可能。
三、不流出不合格品不流出不合格品是指员工完成本工序加工,需检查确认产品质量,一旦发现不良品,必须及时停机,将不良品在本工序截下,并且在本工序内完成不良品处置并采取防止措施。
本道工序应保证传递的是合格产品,会被下道工序或“客户”拒收。
▌三不原则的实施要点一、谁制造谁负责一旦产品设计开发结束,工艺参数流程明确,则产品的质量波动就是制造过程的问题。
每个人的质量责任从接受上道工序合格产品开始,规范作业确保本道工序的产品质量符合要求是员工最大的任务。
一旦在本道工序发现不良或接到后道工序反馈的不良信息后,员工必须立即停止生产,调查原因,采取对策对产品的质量负责到底。
二、谁制造谁检查产品的生产者,同时出是产品的检查者,产品的检查只是生产过程的一个环节。
通过检查,确认生产合格,才能确保合格产品流入下道工序。
通过自身检查,作业者对本工序加工产品的状态可以了解得更清楚,从而有利于员工不断提升加工水平,提高产品质量。
三、作业标准化产品从设计开发、设定工艺参数开始,就要对所有的作业流程中作业步骤,作业细节进行规范化、标准化,并使其不断完善。
质量管理三不原则

质量管理三不原则▌三不原则的基本做法一、不接受不合格品不接受不合格品是指员工在生产加工之前,先对前传递的产品按规定检查其是否合格,一旦发现问题则有权拒绝接受,并及时反馈到前工序。
前道工序人员需要马上停止加工,追查原因,采取措施,使品质问题得以及时发现纠正,并避免不合格品继续加工造成的浪费。
二、不制造不合格品不制造不合格品是指接受前道的合格品后,在本岗位加工时严格执行作业规范,确保产品的加工质量。
对作业前的检查、确认等准备工作做得充分到位;对作业中的过程状况随野鸟留意,避免或及早发现异常的发生,减少产生不合格品的概率。
准备充分并在过程中得到确认是不制造不合格的关键。
只有不产生不良品,才能使得不流出和不接受不良品变为可能。
三、不流出不合格品不流出不合格品是指员工完成本工序加工,需检查确认产品质量,一旦发现不良品,必须及时停机,将不良品在本工序截下,并且在本工序内完成不良品处置并采取防止措施。
本道工序应保证传递的是合格产品,会被下道工序或“客户”拒收。
▌三不原则的实施要点一、谁制造谁负责一旦产品设计开发结束,工艺参数流程明确,则产品的质量波动就是制造过程的问题。
每个人的质量责任从接受上道工序合格产品开始,规范作业确保本道工序的产品质量符合要求是员工最大的任务。
一旦在本道工序发现不良或接到后道工序反馈的不良信息后,员工必须立即停止生产,调查原因,采取对策对产品的质量负责到底。
二、谁制造谁检查产品的生产者,同时出是产品的检查者,产品的检查只是生产过程的一个环节。
通过检查,确认生产合格,才能确保合格产品流入下道工序。
通过自身检查,作业者对本工序加工产品的状态可以了解得更清楚,从而有利于员工不断提升加工水平,提高产品质量。
三、作业标准化产品从设计开发、设定工艺参数开始,就要对所有的作业流程中作业步骤,作业细节进行规范化、标准化,并使其不断完善。
每一个员工也必须严格执行标准化作业。
标准化是该工序最佳的作业方法,是保证产品质量一致性的唯一途径,否则制造一大堆不良品却找不到不良的根本原因,这个时候“三不原则”只能制造混乱,而不是品质。
生产制造过程中的三不原则

生产制造过程中的三不原则在生产制造的过程中,有个小道理大家都应该知道,那就是“三不原则”。
你问这原则啥意思?简单说就是:不良品、不安全、不环保。
听起来好像有点严肃,但其实说白了就是要让我们的生产更顺利、产品更靠谱。
想象一下,咱们在车间里,正忙着做产品,这时突然发现一堆不合格的零件。
哎呀,那可真是“竹篮打水一场空”啊,浪费时间不说,心情也得一落千丈。
谁愿意把心血都投进去,结果出来的还是个“四不像”呢?先说不良品。
生产线上,大家都在拼命赶工,想要按时交货。
可是一不小心,就可能出现一些瑕疵。
这个时候,得仔细检查哦。
就像买衣服,试穿的时候发现有线头没处理好,心里可不舒服。
为了避免不良品,我们得制定严格的检验标准,不能心存侥幸。
毕竟,客户手里拿到的产品是咱们的“脸面”,可不能随便丢掉啊。
再想想,有时候生产过程中的粗心大意,真是让人“掉了进水里还不知”的状态,麻烦可大了。
接下来聊聊安全。
这可是大事。
工厂里机器轰鸣,操作员忙得不可开交,安全意识得时刻放在心上。
不少事故都是因为忽视了安全规程。
想象一下,那个机器像个“猛兽”一样在那儿,万一不小心,就会造成大麻烦。
所以,安全帽、护目镜、手套这些防护装备可得备齐了,简直就是“保命符”啊。
大家在工作的时候,心里得有个警钟长鸣,不要等到出了事才后悔,这可不是小打小闹,损失可大了。
再说环保,这也是不得不提的。
在制造业,环保意识越来越重要。
我们可不能像“马虎”的小孩一样,随便把垃圾扔到一边。
想想,如果大家都不注意,环境被破坏了,那日子可就没法过了。
生产过程中产生的废气、废水,得妥善处理,不能让它们污染了周围的环境。
毕竟,天蓝水清是我们共同的家园,谁都希望能在一个美丽的环境里生活。
为了绿色发展,咱们得行动起来,做个“环保小卫士”。
说到这,大家可能会觉得,这三不原则是个“死规矩”。
其实不然,灵活运用才能实现最佳效果。
生产过程中,不良品的检测、安全的维护和环保的措施,这三者相辅相成,缺一不可。
三不原则
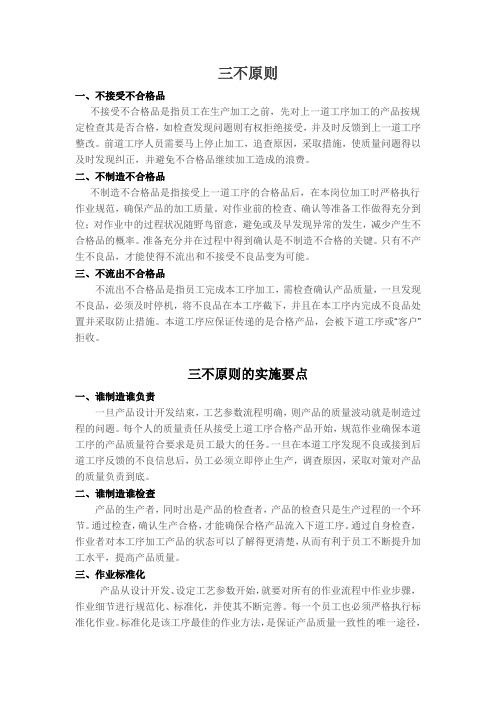
三不原则一、不接受不合格品不接受不合格品是指员工在生产加工之前,先对上一道工序加工的产品按规定检查其是否合格,如检查发现问题则有权拒绝接受,并及时反馈到上一道工序整改。
前道工序人员需要马上停止加工,追查原因,采取措施,使质量问题得以及时发现纠正,并避免不合格品继续加工造成的浪费。
二、不制造不合格品不制造不合格品是指接受上一道工序的合格品后,在本岗位加工时严格执行作业规范,确保产品的加工质量。
对作业前的检查、确认等准备工作做得充分到位;对作业中的过程状况随野鸟留意,避免或及早发现异常的发生,减少产生不合格品的概率。
准备充分并在过程中得到确认是不制造不合格的关键。
只有不产生不良品,才能使得不流出和不接受不良品变为可能。
三、不流出不合格品不流出不合格品是指员工完成本工序加工,需检查确认产品质量,一旦发现不良品,必须及时停机,将不良品在本工序截下,并且在本工序内完成不良品处置并采取防止措施。
本道工序应保证传递的是合格产品,会被下道工序或“客户”拒收。
三不原则的实施要点一、谁制造谁负责一旦产品设计开发结束,工艺参数流程明确,则产品的质量波动就是制造过程的问题。
每个人的质量责任从接受上道工序合格产品开始,规范作业确保本道工序的产品质量符合要求是员工最大的任务。
一旦在本道工序发现不良或接到后道工序反馈的不良信息后,员工必须立即停止生产,调查原因,采取对策对产品的质量负责到底。
二、谁制造谁检查产品的生产者,同时出是产品的检查者,产品的检查只是生产过程的一个环节。
通过检查,确认生产合格,才能确保合格产品流入下道工序。
通过自身检查,作业者对本工序加工产品的状态可以了解得更清楚,从而有利于员工不断提升加工水平,提高产品质量。
三、作业标准化产品从设计开发、设定工艺参数开始,就要对所有的作业流程中作业步骤,作业细节进行规范化、标准化,并使其不断完善。
每一个员工也必须严格执行标准化作业。
标准化是该工序最佳的作业方法,是保证产品质量一致性的唯一途径,否则制造一大堆不良品却找不到不良的根本原因,这个时候“三不原则”只能制造混乱,而不是品质。
- 1、下载文档前请自行甄别文档内容的完整性,平台不提供额外的编辑、内容补充、找答案等附加服务。
- 2、"仅部分预览"的文档,不可在线预览部分如存在完整性等问题,可反馈申请退款(可完整预览的文档不适用该条件!)。
- 3、如文档侵犯您的权益,请联系客服反馈,我们会尽快为您处理(人工客服工作时间:9:00-18:30)。
3:自检确认 来料检查
本岗作业是否合格
4:互检互检 是否按标准化作业操作 上道工序作业是否合格
解决方法 及时反馈 隔离使用 立刻改进 现场排查 跟踪确认
临港质量目标
➢总合格率>99.9% ➢一次合格率>99% ➢报废率<0.1% ➢错漏装=0 ➢装配不到位=0
共享
1.提高质量,总是有方法! 2.许多人做事时常有“差不多”的心态 3. 换一个角度想问题. 4.品质没有折扣。
1:来料蒙皮装 配孔有飞边, 装配时产生装 配不到位。 2:来料尺寸不 相符造成装配 不良。 3:清洗盖板来 料变形造成装 配不良。
1:密封条在凹模 胎具上装配时不 能看到装配的状 态。 2:反射片在凹模 装配时须在胎具 下操作。 3:预装配光亮格 栅总成时从上面 开始装配容易不 到位。
1:焊机间的距 离太小,拿取 产品时容易划 伤。 2:产品须人工 翻箱搬运至二 楼,搬运过程 容易造成产品 碰划伤。
生产过程不良品控制
生产班组——装配
目录
➢1.不良品的产生 ➢2.造成不良品因素 ➢3.避免生产不良品方法 ➢4.本区域不良品分析 ➢5.故事分享
第2页
不良品的产生 有生产就有不良品的产生
2013年4月度临港装不位位、漏装统计
漏装位统计
5 单位:件
4
前保 后保
3
2
0
1
2
0
1
1
0
0
0
装配不到位统计
质量方针
质量是检验的事情 质量是生产出来的
质量方针
三不原则
不制造不良品 不接受不良品 不传递不良品
控制不良品方法——检
点检
巡检
自检
互检
人人都是 检验员
控制不良品方法——检
检什么?
1:点检发现 设备、工具是否正常 设备、胎具保护措施有无坏损
Hale Waihona Puke 2:巡检发现 工艺参数是否正常
变化点是否在控制范围
产生不良品因素分析
人
人的因素才是造成不良品的最大因素
新员工
不熟悉装配工序及标准,未完全培训 上岗
未按区域 作业过程中未装配过多成放置在装配 规范操作 台、胎具上或料架内
未按标准化 作业过程中没有按照要求进行作业、 作业操作 检验、确认
检验意识
质量是检验的事,反正有他们在后面 ,就算是有不良品检验也能检的出来
冲 孔 变 形
表 面 烤 焦 开 裂 缩 瘪
油 漆 脱 落
第5页
不良品分类
不良品
不可控
突发情况
可控
可预见的 可改进的
产生不良品原因分析
设备问题
来料问题
方法问题
环境问题
1:冲机拿取产 品时容易碰到 冲刀造成产品 碰伤。 2:胎具上胎布 破损造成产品 划伤。 3:料架破损拿 放产品时造成 产品碰、划伤
共享
1.培训的重要性.
把好的经验做好培训,让大家共享,培训好了, 可以少犯错误,少走弯路,大家都会向同一个 方向,也是正确的方向使力,这样的团队或公 司会战无不胜的。
2.制度就是要无条件执行的。
因为制度是经验的总结。不遵守制度是要 犯错误或受惩罚的。
经验分享 经验固化
共享
金子与石子
一个人整天抱怨生活对他不公平,抱怨自己的才能不 被人欣赏,终于这件事让上帝知道了。上帝来到这个人的 身边,捡起地上的一颗石子扔到了石堆里,说:假如石子 就是你,把自己找出来。那人找了好久也没找到,上帝又 往石堆里扔了块金子,说:假如金子就是你,把自己找出 来。结果当然是那人一眼就认出了代表自己的金子。
1月
2月
3月
4月
5 单位:件
4
1
前保 后保
3
1
1
2
3
1
2
2
1
0
0
1月
2月
3月
4月
2013年4月度临港报废统计
单位:件
20 19
报废缺陷明细
18
16
15 15
14
12
11
10
8
6
5
4
333
2
1111111
0
划 伤
断 裂
碰 伤
卡 脚 断 裂
修 边 过 头 变 形 缺 料 色 差 滴 液
冲 孔 开 裂