工厂防尘的综合措施
综合防尘安全技术专项措施
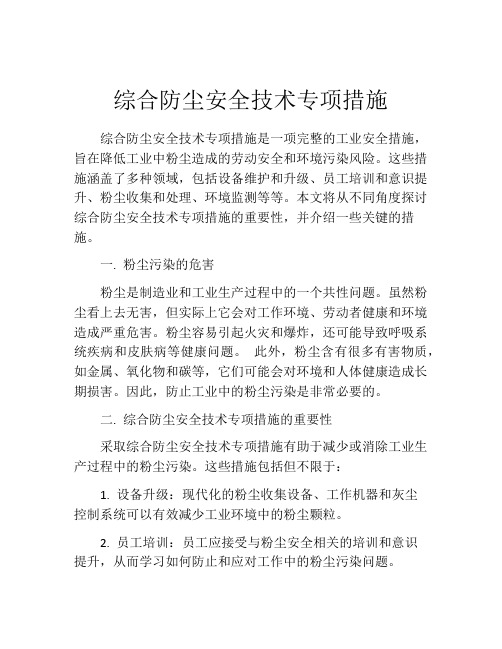
综合防尘安全技术专项措施综合防尘安全技术专项措施是一项完整的工业安全措施,旨在降低工业中粉尘造成的劳动安全和环境污染风险。
这些措施涵盖了多种领域,包括设备维护和升级、员工培训和意识提升、粉尘收集和处理、环境监测等等。
本文将从不同角度探讨综合防尘安全技术专项措施的重要性,并介绍一些关键的措施。
一. 粉尘污染的危害粉尘是制造业和工业生产过程中的一个共性问题。
虽然粉尘看上去无害,但实际上它会对工作环境、劳动者健康和环境造成严重危害。
粉尘容易引起火灾和爆炸,还可能导致呼吸系统疾病和皮肤病等健康问题。
此外,粉尘含有很多有害物质,如金属、氧化物和碳等,它们可能会对环境和人体健康造成长期损害。
因此,防止工业中的粉尘污染是非常必要的。
二. 综合防尘安全技术专项措施的重要性采取综合防尘安全技术专项措施有助于减少或消除工业生产过程中的粉尘污染。
这些措施包括但不限于:1. 设备升级:现代化的粉尘收集设备、工作机器和灰尘控制系统可以有效减少工业环境中的粉尘颗粒。
2. 员工培训:员工应接受与粉尘安全相关的培训和意识提升,从而学习如何防止和应对工作中的粉尘污染问题。
3. 粉尘收集和处理:收集和处理工业生产过程中产生的粉尘颗粒,可以有效减少劳动安全和环境污染风险。
粉尘收集器和过滤器是经常使用的工具。
4. 环境监测:实施环境监测有助于监测粉尘浓度,并定期维护、保养和评估收集设备以确保其有效性。
三. 综合防尘安全技术专项措施的好处1. 保护工人安全和健康:通过采取适当的技术防范措施防止粉尘污染,可以减少呼吸道、皮肤、眼睛等方面的职业病风险,从而保护工人安全和健康。
2. 减少火灾和爆炸的危险:粉尘是潜在的火灾和爆炸的来源。
通过有效收集和处理,可以减少这些风险,从而保护员工和设备免受威胁。
3. 降低环境污染:粉尘污染对环境也有很大危害。
有效的粉尘控制措施可以降低环境污染,促进环境保护,保护生态环境的和谐发展。
4. 提高生产效率:通过采取综合防尘安全技术措施,可以降低生产线维护/停机时间及工人输出,从而提高生产效率和产出。
工厂防尘综合措施

工厂防尘综合措施工厂是一个容易产生灰尘和污染的场所,防尘是保证员工工作安全和环境卫生的重要任务。
为了有效减少工厂的粉尘和污染物,需要综合考虑以下几方面的措施。
首先,对于生产过程中产生的粉尘和污染物,可以通过优化生产工艺和设备来减少其产生。
比如,通过改进设备和工艺,减少物料的破碎和磨削过程,可以减少空气中的粉尘浓度。
此外,使用封闭式设备和管道,减少物料的扬尘和排放,也是一种有效的措施。
在设计和改造工厂时,应考虑设置联动控制系统,当排放超标时自动报警并采取相应的措施。
其次,加强对员工的培训和教育,提高其防尘意识和操作技能。
通过开展培训课程,普及防尘知识,教育员工正确佩戴防护用品的方法,有效控制粉尘产生和扩散的途径。
同时,加强对员工的监督和检查,发现不符合防尘要求的行为及时纠正,并对不遵守规定的员工进行处罚,以起到约束作用。
第三,设置合理的通风系统和防尘设备,改善工作场所的空气质量。
通风系统的设计应考虑到生产过程中产生的污染物及时排出,新风的补给量要适当,以保持良好的室内空气质量。
此外,可以安装空气过滤器和净化设备,对空气中的粉尘颗粒进行过滤和净化,确保室内空气质量符合相关标准。
第四,加强工厂的清洁管理,保持工作场所的整洁和干净。
定期进行地面、设备和机器的清洁,清除积尘和沉积物,减少粉尘迁移和扩散的可能。
对于无法清除的粉尘,可以采取湿拖、冲洗等方法进行处理。
此外,要加强垃圾分类和处理,减少废弃物对环境的污染。
最后,定期进行维护和检修,确保设备和设施的正常运行和平稳工作。
定期检查和更换损坏的密封件和滤芯,保证密闭性和过滤效果;及时清理磨损的防尘装置和除尘设备,保证其正常工作;对于老化和不可修复的设备,及时进行更换或升级。
总之,工厂防尘综合措施需要从工艺改进、员工培训、通风设备、清洁管理、设备维护等多个方面入手,通过综合施策,才能有效减少粉尘和污染物的产生和扩散,保障员工的健康和工作环境的清洁。
综合防尘措施和管理制度(5篇)

综合防尘措施和管理制度一、防尘供水系统1、为满足生产和防尘洒水的需要,井下必须必须建立完善的防尘供水系统,没有防尘供水管路的采掘工作面不得生产。
2、防尘管路必须敷设到所有的采掘工作面、煤仓放煤口、溜煤眼放煤口、卸煤点等地点,防尘供水管路接至距采每煤工作面不小于____米,距掘进工作面不小于____米。
3、皮带巷管路每隔____米设一组三通阀门,其它巷道管路每隔____米设一组三通阀门。
二、回采工作面1、工作面煤层注水回采工作面必须进行煤层注水工作,工作面采用动压注水,孔距、注水时间、注水量要符合设计要求,探放队负责建立煤层注水台帐。
2、水幕、喷雾洒水设施(1)采煤工作面进、回风巷口以里____米范围内,安全出口距工作面以内____米范围内各安装一道净化水幕,回风顺槽必须安设捕尘网。
水幕要覆盖全断面、灵敏可靠,出煤期间要正常使用,并有专人看管。
(2)回采工作面必须在每组支架的放煤口处安装自动喷雾装置,降柱、移架或放煤时起到喷雾降尘作用。
(3)其他各皮带、煤溜转载点喷雾要做到设置适当、雾化良好、使用正常。
坚持谁使用谁负责的原则,确保其使用完好。
回采工作面必须配备兼职防尘设施维护管理人员。
3、巷道冲洗采煤工作面煤壁每班至少冲洗一次,工作面顺槽每天至少冲一次。
其他粉尘积聚地点及时冲洗,严禁出现积尘。
三、掘进工作面1、防尘系统(1)掘进工作面防尘系统必须完善,三通阀门必须按规定设置齐全。
(2)掘进队组打眼时必须采用湿式钻眼。
2、除尘设施(1)掘进巷道净化水幕设置两道,开口以里____米处一道,距掘进工作面20—____米范围安装一道(巷道长度未超过____米可以设置1道防尘水幕),炮掘工作面距工作面20—____米处必须安设放炮自动喷雾装置。
(2)其他各皮带、煤溜转载点喷雾要做到设置适当、雾化良好、使用正常。
坚持谁使用谁负责的原则,确保其使用完好。
掘进工作面必须配备兼职防尘设施维护管理人员。
3、巷道冲洗掘进工作面____米以内每班至少冲洗一次,____米以外每天至少冲一次。
综合防尘措施
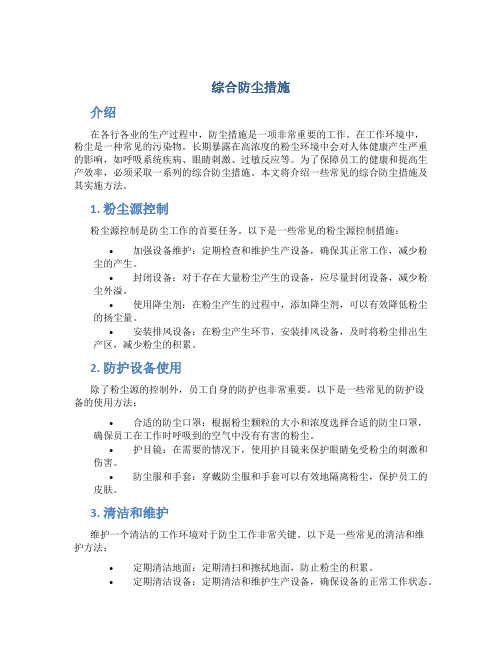
综合防尘措施介绍在各行各业的生产过程中,防尘措施是一项非常重要的工作。
在工作环境中,粉尘是一种常见的污染物。
长期暴露在高浓度的粉尘环境中会对人体健康产生严重的影响,如呼吸系统疾病、眼睛刺激、过敏反应等。
为了保障员工的健康和提高生产效率,必须采取一系列的综合防尘措施。
本文将介绍一些常见的综合防尘措施及其实施方法。
1. 粉尘源控制粉尘源控制是防尘工作的首要任务。
以下是一些常见的粉尘源控制措施:•加强设备维护:定期检查和维护生产设备,确保其正常工作,减少粉尘的产生。
•封闭设备:对于存在大量粉尘产生的设备,应尽量封闭设备,减少粉尘外溢。
•使用降尘剂:在粉尘产生的过程中,添加降尘剂,可以有效降低粉尘的扬尘量。
•安装排风设备:在粉尘产生环节,安装排风设备,及时将粉尘排出生产区,减少粉尘的积累。
2. 防护设备使用除了粉尘源的控制外,员工自身的防护也非常重要。
以下是一些常见的防护设备的使用方法:•合适的防尘口罩:根据粉尘颗粒的大小和浓度选择合适的防尘口罩,确保员工在工作时呼吸到的空气中没有有害的粉尘。
•护目镜:在需要的情况下,使用护目镜来保护眼睛免受粉尘的刺激和伤害。
•防尘服和手套:穿戴防尘服和手套可以有效地隔离粉尘,保护员工的皮肤。
3. 清洁和维护维护一个清洁的工作环境对于防尘工作非常关键。
以下是一些常见的清洁和维护方法:•定期清洁地面:定期清扫和擦拭地面,防止粉尘的积累。
•定期清洁设备:定期清洁和维护生产设备,确保设备的正常工作状态。
•定期更换滤芯:对于使用过滤器的设备,定期更换滤芯,确保过滤系统的有效性。
4. 培训和教育为了确保防尘措施的有效实施,员工的培训和教育也是必不可少的。
以下是一些培训和教育的方法:•提供防尘知识:向员工提供有关防尘的知识和信息,让他们了解与粉尘相关的健康风险和防护措施。
•培训正确使用防护设备:为员工提供正确使用防护设备的培训,包括如何佩戴和维护防护设备。
•定期的健康检查:定期组织员工进行健康检查,及早发现和处理与粉尘相关的健康问题。
综合防尘措施和管理制度范本
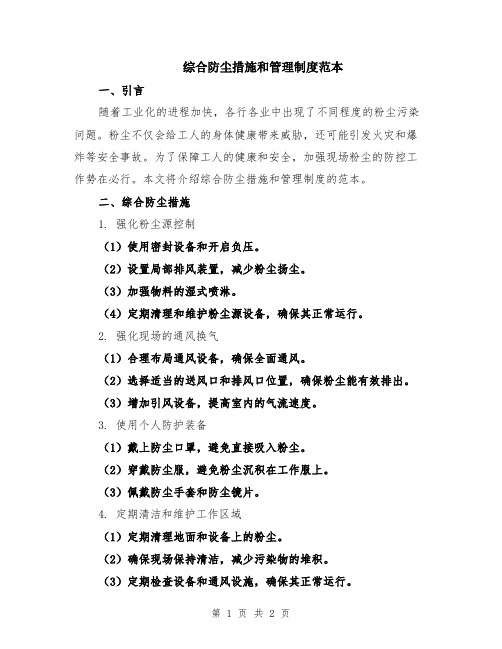
综合防尘措施和管理制度范本一、引言随着工业化的进程加快,各行各业中出现了不同程度的粉尘污染问题。
粉尘不仅会给工人的身体健康带来威胁,还可能引发火灾和爆炸等安全事故。
为了保障工人的健康和安全,加强现场粉尘的防控工作势在必行。
本文将介绍综合防尘措施和管理制度的范本。
二、综合防尘措施1. 强化粉尘源控制(1)使用密封设备和开启负压。
(2)设置局部排风装置,减少粉尘扬尘。
(3)加强物料的湿式喷淋。
(4)定期清理和维护粉尘源设备,确保其正常运行。
2. 强化现场的通风换气(1)合理布局通风设备,确保全面通风。
(2)选择适当的送风口和排风口位置,确保粉尘能有效排出。
(3)增加引风设备,提高室内的气流速度。
3. 使用个人防护装备(1)戴上防尘口罩,避免直接吸入粉尘。
(2)穿戴防尘服,避免粉尘沉积在工作服上。
(3)佩戴防尘手套和防尘镜片。
4. 定期清洁和维护工作区域(1)定期清理地面和设备上的粉尘。
(2)确保现场保持清洁,减少污染物的堆积。
(3)定期检查设备和通风设施,确保其正常运行。
三、管理制度1. 责任分工(1)明确粉尘防控工作的责任部门和责任人员。
(2)制定具体的工作职责和任务分工。
2. 岗位培训和教育(1)对从业人员进行粉尘防控的相关培训和教育。
(2)定期组织技术交流和经验分享。
3. 监测和评估(1)建立粉尘污染源的监测系统,定期对现场粉尘进行监测。
(2)建立评估制度,对粉尘防控工作进行定期评估和改进。
4. 紧急预案(1)制定粉尘污染事故的应急预案。
(2)组织演练,提高应急处置能力。
5. 纠违制度(1)建立违规行为的纠违制度。
(2)对违规行为进行处罚和整改。
四、总结通过综合防尘措施和管理制度的实施,可以有效降低粉尘污染对工作环境和工人健康的影响。
只有在各个环节都严格执行,并不断进行监测和改进,才能实现持续有效的粉尘防控。
综合防尘措施和管理制度

综合防尘措施和管理制度
是指对于建筑工地、工厂车间、矿山开采等场所的粉尘污染进行综合的预防和控制措施的设立和管理制度的建立。
综合防尘措施可包括以下几个方面:
1. 环境控制:封闭或隔离粉尘源,减少粉尘扩散至空气中的程度,例如在建筑工地使用防尘网、设置喷淋设备等措施。
2. 设备改造:对于易产生粉尘的设备进行改造,例如在挖掘机或搅拌机等设备上增加粉尘抑制装置。
3. 作业控制:规范作业流程,采取不产生或减少粉尘产生的方法进行作业,例如使用湿法进行清扫而不是干扫。
4. 个体防护:工人进行作业时佩戴适合的个体防护装备,如口罩、防护眼镜和防尘服等。
管理制度方面可以包括以下几个方面:
1. 规章制度:制定科学合理的防尘操作规程和作业规范,明确责任分工及管理要求。
2. 培训教育:加强对工人的防尘培训和教育,提高其防尘意识和操作能力。
3. 监测监管:建立定期检测和监测制度,对粉尘浓度进行监测和评估,及时采取相应的控制措施。
4. 处罚机制:明确违反防尘管理制度的违规行为及相应的处罚措施,严厉打击违法行为。
通过综合防尘措施和管理制度的建立和执行,可以有效预防和减少粉尘污染,维护工作环境的清洁和健康,保护工人的身体健康。
综合防尘的主要措施
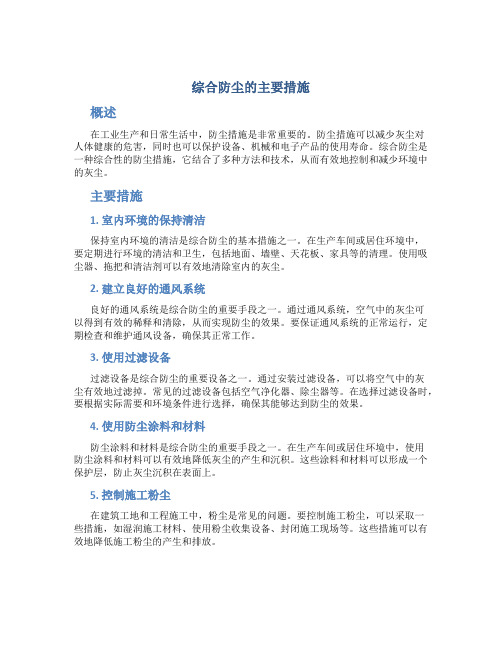
综合防尘的主要措施概述在工业生产和日常生活中,防尘措施是非常重要的。
防尘措施可以减少灰尘对人体健康的危害,同时也可以保护设备、机械和电子产品的使用寿命。
综合防尘是一种综合性的防尘措施,它结合了多种方法和技术,从而有效地控制和减少环境中的灰尘。
主要措施1. 室内环境的保持清洁保持室内环境的清洁是综合防尘的基本措施之一。
在生产车间或居住环境中,要定期进行环境的清洁和卫生,包括地面、墙壁、天花板、家具等的清理。
使用吸尘器、拖把和清洁剂可以有效地清除室内的灰尘。
2. 建立良好的通风系统良好的通风系统是综合防尘的重要手段之一。
通过通风系统,空气中的灰尘可以得到有效的稀释和清除,从而实现防尘的效果。
要保证通风系统的正常运行,定期检查和维护通风设备,确保其正常工作。
3. 使用过滤设备过滤设备是综合防尘的重要设备之一。
通过安装过滤设备,可以将空气中的灰尘有效地过滤掉。
常见的过滤设备包括空气净化器、除尘器等。
在选择过滤设备时,要根据实际需要和环境条件进行选择,确保其能够达到防尘的效果。
4. 使用防尘涂料和材料防尘涂料和材料是综合防尘的重要手段之一。
在生产车间或居住环境中,使用防尘涂料和材料可以有效地降低灰尘的产生和沉积。
这些涂料和材料可以形成一个保护层,防止灰尘沉积在表面上。
5. 控制施工粉尘在建筑工地和工程施工中,粉尘是常见的问题。
要控制施工粉尘,可以采取一些措施,如湿润施工材料、使用粉尘收集设备、封闭施工现场等。
这些措施可以有效地降低施工粉尘的产生和排放。
6. 做好个人防护在防尘过程中,个人防护是非常重要的。
使用防尘口罩、防护眼镜、防尘手套等个人防护装备,可以有效地保护自己免受灰尘的侵害。
同时要注意个人卫生,尽量避免接触灰尘和污染源。
结论综合防尘是一种综合性的防尘措施,它结合了多种方法和技术,从而有效地控制和减少环境中的灰尘。
通过保持室内环境的清洁、建立良好的通风系统、使用过滤设备、使用防尘涂料和材料、控制施工粉尘以及做好个人防护,可以有效地实施综合防尘措施,保护人体健康,延长设备使用寿命。
工厂防尘的综合措施

工厂防尘的综合措施工厂生产过程中,会伴随着大量的粉尘排放,如果不采取相应的防尘措施,将会给工人的健康和环境保护带来严重的威胁。
因此,制定一套综合的工厂防尘措施是非常必要的。
下面将详细介绍一些常见的工厂防尘措施。
1.设立防尘墙和防尘带:在工厂内设置一些固定的防尘墙和可移动的防尘带,用于隔离和封堵可能产生粉尘的区域。
这样可以有效地减少粉尘扩散的范围和速度,保护周围的工作区域和设备免受粉尘的污染。
2.定期清洁和维护:定期清洁和维护能够有效地减少粉尘的积累和堆积。
比如,定期清洁生产线、设备和工作区域,清除粉尘和污垢,确保工作环境的整洁和卫生。
3.使用高效过滤设备:在工厂的通风系统中安装高效过滤设备,能够有效地捕捉和过滤掉空气中的粉尘颗粒。
这样可以减少室内空气中的粉尘浓度,改善工人的工作环境,防止粉尘对身体健康的影响。
4.使用湿式除尘设备:在工厂的生产过程中,可以采用湿式除尘设备来处理产生的粉尘。
湿式除尘设备通过将水喷洒到粉尘中,使其吸湿沉降,从而达到净化空气的效果。
5.粉尘收集和处理:对生产过程中产生的粉尘进行收集和处理。
可以使用除尘器、收尘器等设备将粉尘集中起来,然后进行处理或转运,防止粉尘扩散到环境中。
6.采用封闭式生产工艺:对于那些产生大量粉尘的生产工艺,可以考虑采用封闭式生产工艺,通过使用密封设备和管道,将粉尘产生的区域与其他区域隔离开来,减少粉尘的扩散。
7.加强职业健康教育:加强对工人的职业健康教育,提高他们对粉尘危害的认识,学习正确的防护知识和使用防护装备的方法。
同时,加强职业病防护知识的培训和普及,提高工人的职业健康意识,减少工人受到粉尘危害的风险。
综上所述,采取综合的工厂防尘措施对于保护工人的健康和环境保护至关重要。
这些措施包括建立防尘墙和防尘带,定期清洁和维护,使用高效过滤设备和湿式除尘设备等,还需要加强职业健康教育和定期检测监测工作。
通过综合应用这些措施,可以有效地减少粉尘的扩散和污染,提高工作环境的质量和安全性。
工厂防尘的综合措施

工厂防尘的综合措施工厂防尘是指在生产过程中采取一系列综合措施来防止灰尘的生成和扩散,以维护生产环境的清洁和员工的健康。
下面是一些可能的综合措施:1.操作规范和培训:建立相关的操作规范,确保员工正确操作设备和工具,并且了解防尘措施的重要性和正确使用方法。
通过定期培训和考核,提高员工的意识和技能,减少灰尘产生的可能性。
2.设备保养和更新:保持设备的正常运行和良好状态,定期清洁和维护设备,包括清理过滤器、油脂润滑、排除故障等。
根据需要,及时更换老化或损坏的设备,以减少灰尘的产生。
3.空气过滤系统:安装高效的空气过滤系统,能有效去除空气中的颗粒物和粉尘。
根据实际情况,选择合适的过滤器类型和规格,制定过滤器更换周期。
定期检查和清洁过滤器,确保其正常工作。
4.气流控制:合理设计空气流动,通过设置通风系统和风扇,控制和改善空气流向,将产生灰尘的地方与工作区隔离开,控制灰尘的扩散。
并且要定期清理通风管道和排气口,保持其通畅。
5.封闭设备和工艺:对于产生大量灰尘的设备和工艺,可以采取封闭的措施,如加装密封罩、使用封闭式传送和物料处理系统,以减少灰尘的产生和扩散。
6.做好清洁工作:定期进行彻底的清洁工作,包括清理地面、墙壁、设备表面等,以去除已经产生的灰尘。
选择合适的清洁工具和方法,如湿拖地、抽尘器等,以减少扬尘。
同时,及时清理和更换使用的工具和设备中的过滤器和滤芯。
7.粉尘捕集与处理:对于容易产生粉尘的工序,可以设置粉尘捕集设备,如除尘器、静电吸尘器等,将粉尘有效地捕集和处理,以减少空气中的粉尘含量。
同时,妥善处理和处置捕集的粉尘,防止再次扩散。
8.个体防护措施:根据实际情况,为员工提供合适的个体防护装备,如防尘口罩、防护眼镜、防尘服等。
并确保员工正确佩戴和使用个体防护装备。
9.健康监测:定期对员工进行健康监测,包括呼吸系统检查、肺功能测定等,及早发现和处理与灰尘相关的健康问题,保障员工的身体健康。
10.管理监督:建立完善的防尘管理体系,制定相关的管理制度和标准,定期检查和评估防尘措施的实施情况,及时发现和解决问题。
工厂防尘的综合措施
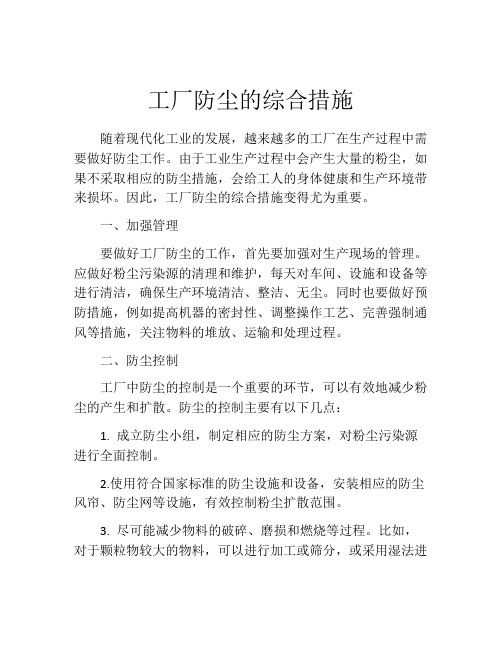
工厂防尘的综合措施随着现代化工业的发展,越来越多的工厂在生产过程中需要做好防尘工作。
由于工业生产过程中会产生大量的粉尘,如果不采取相应的防尘措施,会给工人的身体健康和生产环境带来损坏。
因此,工厂防尘的综合措施变得尤为重要。
一、加强管理要做好工厂防尘的工作,首先要加强对生产现场的管理。
应做好粉尘污染源的清理和维护,每天对车间、设施和设备等进行清洁,确保生产环境清洁、整洁、无尘。
同时也要做好预防措施,例如提高机器的密封性、调整操作工艺、完善强制通风等措施,关注物料的堆放、运输和处理过程。
二、防尘控制工厂中防尘的控制是一个重要的环节,可以有效地减少粉尘的产生和扩散。
防尘的控制主要有以下几点:1. 成立防尘小组,制定相应的防尘方案,对粉尘污染源进行全面控制。
2.使用符合国家标准的防尘设施和设备,安装相应的防尘风帘、防尘网等设施,有效控制粉尘扩散范围。
3. 尽可能减少物料的破碎、磨损和燃烧等过程。
比如,对于颗粒物较大的物料,可以进行加工或筛分,或采用湿法进行处理。
对于需要燃烧的物料,则需要控制燃烧的温度和氧气浓度等参数。
4. 采用有利于降低粉尘浓度的作业技术。
例如,在排烟口加装高效过滤器和排气扇,对于易产生粉尘的设备,在设备进出口安装密封装置。
三、防护措施防护措施是在控制好粉尘产生和扩散范围的前提下,进一步保护工人的身体健康和生产环境的安全。
防护措施也可以分为以下几个方面:1. 使用适当的个人防护装备。
包括口罩、防尘服、防护眼镜、防噪耳塞等,有效地减少吸入粉尘量和保障工人的安全。
2. 对于容易接触粉尘的工程师,应该进行定期的身体检查和健康监护。
及时发现和治疗患者,确保工人身体健康。
3. 进行员工培训,提高员工对防尘的认识和意识。
员工需要了解工作场所存在的粉尘源和防尘设备,学会使用防尘设备和进行防尘作业。
综上所述,工厂防尘工作的重要性不言而喻。
通过加强管理、控制粉尘产生和采取适当的防护措施,可以保障工厂生产的顺利和安全,同时也是企业对员工健康的负责任态度。
掘进工作面综合防尘规定范文
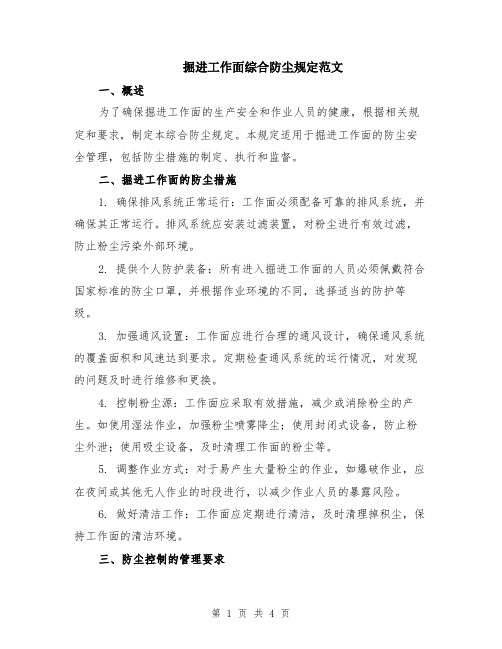
掘进工作面综合防尘规定范文一、概述为了确保掘进工作面的生产安全和作业人员的健康,根据相关规定和要求,制定本综合防尘规定。
本规定适用于掘进工作面的防尘安全管理,包括防尘措施的制定、执行和监督。
二、掘进工作面的防尘措施1. 确保排风系统正常运行:工作面必须配备可靠的排风系统,并确保其正常运行。
排风系统应安装过滤装置,对粉尘进行有效过滤,防止粉尘污染外部环境。
2. 提供个人防护装备:所有进入掘进工作面的人员必须佩戴符合国家标准的防尘口罩,并根据作业环境的不同,选择适当的防护等级。
3. 加强通风设置:工作面应进行合理的通风设计,确保通风系统的覆盖面积和风速达到要求。
定期检查通风系统的运行情况,对发现的问题及时进行维修和更换。
4. 控制粉尘源:工作面应采取有效措施,减少或消除粉尘的产生。
如使用湿法作业,加强粉尘喷雾降尘;使用封闭式设备,防止粉尘外泄;使用吸尘设备,及时清理工作面的粉尘等。
5. 调整作业方式:对于易产生大量粉尘的作业,如爆破作业,应在夜间或其他无人作业的时段进行,以减少作业人员的暴露风险。
6. 做好清洁工作:工作面应定期进行清洁,及时清理掉积尘,保持工作面的清洁环境。
三、防尘控制的管理要求1. 确保防尘设备的有效使用:对于工作面的防尘设备,必须经过合格的安装和调试后方可使用,在使用过程中要保持设备的良好状态,定期进行维护和保养。
2. 严格执行人员防尘要求:所有进入掘进工作面的人员,必须佩戴防尘口罩,并按照操作规程正确佩戴和使用,严禁擅自卸下或不正确使用防尘口罩。
3. 强化培训和教育:掘进工作面的作业人员必须经过专业的培训和教育,了解防尘规定和防尘措施的重要性,掌握正确的使用方法和注意事项。
4. 配备专职防尘管理人员:工作面应配备专职的防尘管理人员,负责工作面的防尘工作,包括检查设备、教育培训、监督执行等。
5. 定期检查和评估:工作面的防尘措施应定期进行检查和评估,发现问题及时提出改进意见,并进行整改。
防尘的综合措施

防尘的综合措施在解决粉尘危害问题时,必须综合考虑各种有害物质的散发情况,采取综合措施。
防尘综合措施既有各种技术措施,又有各种组织措施,两者不能偏废,应是相辅相成。
概括起来就是“革”、“水”、“密”、“风”、“护”、“管”、“教”、“查”八个字。
1.革即革新工艺与设备。
生产工艺和生产设备的技术革新,逐步用先进设备,使生产过程中不生产或少生产粉尘,以低毒性粉尘代替高毒性粉尘,以至消除粉尘危害的基本措施。
2.水即湿式作业。
湿式作业可有效防止粉尘飞扬。
在有较大粉尘的作业环境中通常使用湿式作业降低粉尘,除尘效果较好并且经济方便。
3.密即把粉尘发生源密闭,防止粉尘向外飞扬。
将粉尘发生源密闭在独立的区域内,减少人员接触粉尘的频次和浓度,将有效减少粉尘对人体的危害。
4.风即通风。
包括自然通风系统和机械通风装置。
自然通风主要通过设计合理的通风通道,使含尘空气沿设计的方向自然排出。
通风防尘工作,主要是在扬尘点密闭基础上再安装合理的通风除尘装置。
在不易密闭防尘的作业点,可采用局部抽出式排风装置,抽风方向尽可能与粉尘运动方向一致。
5.护即加强个人防护和增强体质。
个人防护的目的是防止粉尘进入呼吸道。
主要通过做业人员佩戴防尘口罩来进行防护。
此外,注意个人卫生、开展体育活动,增强体质也可以有效地增强个人的防护功能。
6.管即加强除尘工作的技术管理。
依据法规要求建立科学的防尘制度和除尘通风设备的维护保养管理制度。
除尘设备必须进行经常性和定期的技术检测、检查维修,以发挥其防尘作用。
同时,还要落实新建、扩建、改建、技术改造和技术引进项目“三同时”制度,保证职业卫生措施必须与主题工程同时设计,同时施工、同时投入生产和使用。
7.革既做好防尘工作的宣传教育。
通过学习职业危害和防尘方面的法律、法规,粉尘危害,粉尘防止的基本知识,使作业人员了解粉尘的危害、防治肺癌的基本知识,了解肺癌是完全可以防治的。
发动从业人员做好各自岗位的防尘、除尘职责,提高粉尘危害治理、尘肺病防治的意识和自觉性。
掘进工作面综合防尘规定(三篇)

掘进工作面综合防尘规定是指工作场所对于掘进工作面产生的粉尘进行综合防护的一系列规定。
下面是一些常见的掘进工作面综合防尘规定:1. 安装有效的通风系统,保证工作面的空气流通,及时清除积尘。
2. 在掘进工作面设立防尘墙或防尘帘,阻挡粉尘的扩散,减少粉尘对工作人员的侵害。
3. 使用防尘设备,如防尘口罩、防尘服等,为工作人员提供个人防护装备。
4. 定期对掘进工作面进行湿法喷淋,将粉尘湿化,降低粉尘浓度。
5. 定期进行粉尘检测,确保粉尘浓度在安全范围内。
6. 加强职业健康教育,培养工作人员的防尘意识和防护能力。
7. 对掘进工作面进行定期清洁,清除积尘和杂物。
8. 定期对防尘设备进行检修和更换,确保其正常工作和有效性。
9. 建立相关的监测和报告机制,及时发现和处理防尘问题。
以上是一些常见的掘进工作面综合防尘规定,具体要根据不同的工作场所和具体情况来制定。
为了保障工作人员的健康和安全,各工作单位应按照相关法规和标准制定合理的防尘措施,并加强监督和执行。
掘进工作面综合防尘规定(二)是为了保护工作人员的健康与安全,减少尘肺病和其他相关疾病的发生,提高工作场所的环境质量而制定的一系列规定。
1. 确定尘肺危害评估与监测:对工作面进行定期的尘肺危害评估与监测,了解尘肺危害程度及发展趋势。
2. 加强通风设备建设与管理:工作面应配备适当的通风设备,保证空气流通,并定期检查和维护设备的运行情况。
3. 使用防尘措施:工作面必须采取有效的防尘措施,如湿法除尘、覆盖尘源、加喷雾等,控制尘埃的产生和扩散。
4. 佩戴防尘口罩:工作人员应佩戴合适的防尘口罩,有效阻隔尘埃进入呼吸道。
5. 职业健康教育与培训:对工作人员进行职业健康教育培训,提高对尘肺危害的认识和防护措施的应用能力。
6. 定期体检:对从事掘进作业的工作人员进行定期的尘肺体检,及时发现和治疗尘肺病。
7. strict personal protective equipment(PPE):为工作人员提供适当的个人防护装备,如防尘服、防护眼镜等,加强个体防护。
综合防尘措施和管理制度模版
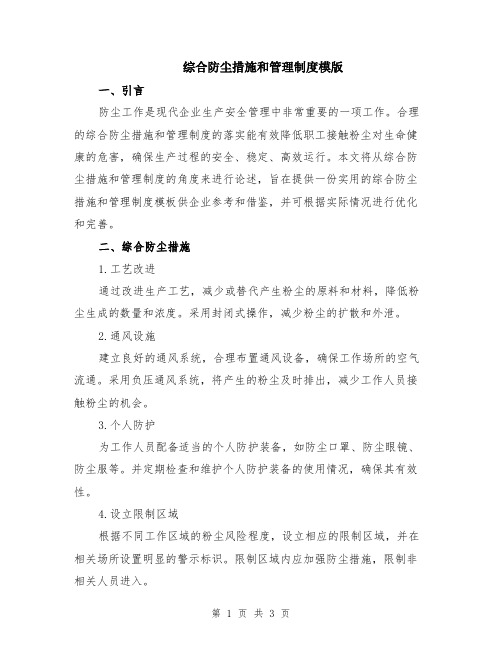
综合防尘措施和管理制度模版一、引言防尘工作是现代企业生产安全管理中非常重要的一项工作。
合理的综合防尘措施和管理制度的落实能有效降低职工接触粉尘对生命健康的危害,确保生产过程的安全、稳定、高效运行。
本文将从综合防尘措施和管理制度的角度来进行论述,旨在提供一份实用的综合防尘措施和管理制度模板供企业参考和借鉴,并可根据实际情况进行优化和完善。
二、综合防尘措施1.工艺改进通过改进生产工艺,减少或替代产生粉尘的原料和材料,降低粉尘生成的数量和浓度。
采用封闭式操作,减少粉尘的扩散和外泄。
2.通风设施建立良好的通风系统,合理布置通风设备,确保工作场所的空气流通。
采用负压通风系统,将产生的粉尘及时排出,减少工作人员接触粉尘的机会。
3.个人防护为工作人员配备适当的个人防护装备,如防尘口罩、防尘眼镜、防尘服等。
并定期检查和维护个人防护装备的使用情况,确保其有效性。
4.设立限制区域根据不同工作区域的粉尘风险程度,设立相应的限制区域,并在相关场所设置明显的警示标识。
限制区域内应加强防尘措施,限制非相关人员进入。
三、综合防尘管理制度1.责任分工设立专门的职能部门或委派专人负责综合防尘工作,明确对综合防尘工作负有责任的岗位和人员,并做好相应的培训和教育。
2.制度建立建立综合防尘管理制度,明确综合防尘的目标、原则、要求和措施,并确保制度的贯彻执行。
同时,制定相关的操作规程和标准,确保综合防尘工作的科学性和规范性。
3.培训教育定期组织综合防尘知识和技能的培训,使工作人员了解综合防尘的重要性、掌握综合防尘的技能,并提供相关的教育材料和宣传资料。
4.检查与监测建立健全的综合防尘检查和监测制度,对工作场所的粉尘情况进行定期检查和监测,及时发现和解决存在的问题,并建立相应的档案记录。
5.事故应急预案制定综合防尘事故应急预案,明确应急响应措施、应急指挥人员和应急物资储备等,并进行相应的演练和培训,以提高应急处置的能力和效果。
四、总结综合防尘措施和管理制度是企业加强生产安全管理的重要手段。
综合防尘安全技术措施

综合防尘安全技术措施在各行各业中,尘埃和粉尘对人体健康和生产安全都有着不可忽视的影响。
在工程施工、制造业、矿山开采等工作中,如何采取正确的防尘措施保障工作安全和健康成为了当务之急。
在这篇文章中,我们将介绍一些综合防尘安全技术措施。
安全防护设施1.护目镜和口罩在工作中应当佩戴防护口罩和护目镜,以隔离空气中的尘埃。
防护口罩应当选择质量可靠的医用口罩,同时需要根据实际工作环境对口罩进行选择。
而护目镜则有多种材质可供选择,例如塑料、玻璃、钢化玻璃等,可以根据需要选择不同的镜片材质。
2.防护手套和工作服在工作中应当穿戴防护手套和工作服,以避免因工作环节中的化学品和其他污染物接触而引起的皮肤病和过敏反应。
防护手套和工作服材质应当符合国家标准。
3.通风设备在尘埃较大的环境中,需要设置通风设备。
通风设备可以改善空气质量,减少空气中的尘埃浓度,从而保障工作环境安全。
工作场所安全1.工作区域粉尘控制为了减少工作区域中的尘埃浓度,应当采取各种控制措施,例如使用工业吸尘器等设备及其它适当的防尘设备,阻止尘埃的外溢和扩散。
2.清洁控制定期进行清洁工作是维持工作环境整洁的重要措施。
通过定期清洁,可以清除工作区域内的尘埃、污垢和其他杂质,从而减少空气中的尘埃浓度。
3.禁止吸烟在尘埃较大的区域,禁止吸烟是非常重要的。
吸烟会影响空气质量,增加人体吸入尘埃和有害气体的几率。
个人防护1.登记台和卫生间为了避免传染病的传播,需要在工作场所设置完善的登记台和卫生间设施。
工作人员应当经常清洗双手以保持个人卫生。
2.健康检查工人需要进行定期的健康检查。
检查的项目应当主要针对呼吸道和皮肤状况等与工作环境有直接或间接联系的方面,以及内部器官的功能状态。
3.健康教育健康教育应当包括职业病的预防、常规个人防护和安全教育、应对燃气泄漏等不同情况下的抢救措施等等。
这些都是为了让工人更好地理解和控制工作环境中的风险,以及如何预防和应对工作中的意外事件。
总结针对尘埃污染对人体健康和工作安全产生的影响,我们介绍了一些综合防尘安全技术措施。
煤矿综合防尘管理经验措施

煤矿综合防尘管理经验措施煤矿作为一个具有高风险和危险性质的行业,在生产过程中必须加强防尘管理,保障工人的安全与健康。
下面将介绍一些煤矿综合防尘管理的经验措施。
1.优化设备配置在煤矿生产过程中,使用一些先进的设备和技术可以有效地降低粉尘的产生量。
例如,采用湿式破碎和喷淋冲洗等工艺可以减少破碎和传输过程中的粉尘产生。
此外,通过安装集尘设备和过滤器等设备可以有效地捕捉和处理粉尘,降低环境中粉尘的浓度。
2.严格执行作业规程煤矿作业规程对工人进行管理和指导,确保他们遵守安全操作规程,并采取必要的防护措施。
作业规程中应包括对于防尘设备的正确使用和维护的要求,以及进入作业现场前的准备工作,如佩戴防尘口罩、防尘服等个人防护装备。
3.加强宣传教育定期对煤矿工人进行防尘知识的培训和宣传教育,提高他们的安全意识和防尘意识。
通过多种形式的培训,如讲座、现场演示等,向工人传授正确的防尘措施和使用设备的方法。
此外,还可以通过制作宣传海报、标语等,加强对防尘工作的重视,形成全员参与的氛围。
4.定期检查和维护设备煤矿防尘设备的正常运行对于保持矿井环境的清洁和安全至关重要。
定期对设备进行检查和维护,保证其正常工作,并及时处理发现的问题。
如发现设备存在故障或磨损,应立即进行修理或更换,以保证防尘设备的有效性。
5.建立防尘管理制度煤矿应建立健全的防尘管理制度,明确责任分工和流程,并加强对执行情况的监督和督促。
制度中要包括对作业现场粉尘浓度的监测要求,对不达标的情况进行及时处理,并追究责任。
此外,还要制定相应的处罚措施,对不遵守规定和违反操作规程的行为进行处理,以起到警示作用。
6.加强科技支撑利用现代科技手段对煤矿防尘管理进行支撑,如应用粉尘监测仪器、视频监控系统等,实现对粉尘浓度和作业现场状况的实时监测。
通过数据分析和预警系统,及时发现问题,并采取相应的措施进行处理。
7.加大对防尘技术的研发和推广煤矿防尘技术的研发和推广对于改善煤矿作业环境具有重要意义。
综合防尘措施和管理制度

综合防尘措施和管理制度综合防尘措施和管理制度随着人们对健康环保的日益重视,防尘已经成为了我们工作和生活中的一项特别紧要的任务。
特别是在工业、矿山等行业,防尘工作更是至关紧要。
为了保障员工的身体健康和企业的长远进展,必需实行一系列有效的综合防尘措施和管理制度。
一、防尘措施1、机械防尘法机械防尘是指利用机械气力对生产环境中的粉尘进行掌控和减排,重要包括通风、除尘、集尘等措施。
这种方式的优点是:可以在技术上实现全封闭,削减人员的劳动强度;可以将产生的废气、废渣等清除,削减环境的污染。
但是,机械防尘的缺点是:设备成本较高,效果不一、2、化学防尘法化学防尘是掌控和削减粉尘污染的常用方法之一,重要是通过喷洒化学药剂的方式削减粉尘的危害。
化学防尘重要包括:喷洒油剂、喷洒水剂、喷洒乳化剂等。
这种方式的优点是:成本相对较低,易于实施;可以对空气中的微小粉尘进行有效掌控。
但是,应注意化学药剂在使用过程中的可能产生的其他环境污染。
3、风道防尘法通过设立风道,将空气中外来的粉尘、异味等分别起来,从而有效掌控粉尘的危害。
风道防尘法的优点是:效果稳定,成本低廉,安全易于管理。
二、防尘管理制度1、安全管理制度依据国家安全生产法律法规,建立企业安全管理制度,落实管理责任;定期进行安全检查,发觉缺陷适时整改;加强安全教育,防止事故的发生。
2、劳动防护制度建立完善的劳动防护制度,为员工供给必要的劳动防护用品和设备;定期进行身体健康检查;强化员工的安全意识和防护学问教育。
3、环境保护制度建立完善的环境保护制度,加强企业环境管理,实行防尘、除尘等措施;定期检测企业的环境质量,保证生产过程中的废水、废气、废渣等均得到有效掌控。
4、经营管理制度建立健全的经营管理制度,定期对企业管辖内的设备、设施、生产过程等进行检查和维护,确保其正常运行;落实生产计划,合理布置生产过程,削减机器的闲置时间,提高生产效率。
综上所述,通过建立科学的综合防尘措施和管理制度,可以有效掌控粉尘污染,保护员工的健康和环境的质量,促进企业的可持续进展。
工厂防尘的综合措施
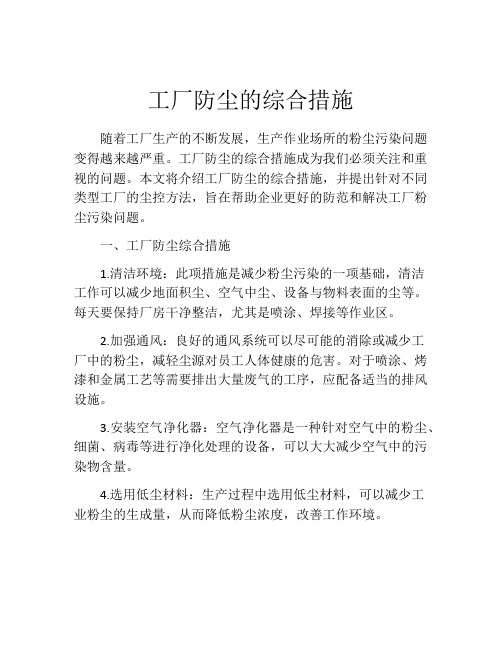
工厂防尘的综合措施随着工厂生产的不断发展,生产作业场所的粉尘污染问题变得越来越严重。
工厂防尘的综合措施成为我们必须关注和重视的问题。
本文将介绍工厂防尘的综合措施,并提出针对不同类型工厂的尘控方法,旨在帮助企业更好的防范和解决工厂粉尘污染问题。
一、工厂防尘综合措施1.清洁环境:此项措施是减少粉尘污染的一项基础,清洁工作可以减少地面积尘、空气中尘、设备与物料表面的尘等。
每天要保持厂房干净整洁,尤其是喷涂、焊接等作业区。
2.加强通风:良好的通风系统可以尽可能的消除或减少工厂中的粉尘,减轻尘源对员工人体健康的危害。
对于喷涂、烤漆和金属工艺等需要排出大量废气的工序,应配备适当的排风设施。
3.安装空气净化器:空气净化器是一种针对空气中的粉尘、细菌、病毒等进行净化处理的设备,可以大大减少空气中的污染物含量。
4.选用低尘材料:生产过程中选用低尘材料,可以减少工业粉尘的生成量,从而降低粉尘浓度,改善工作环境。
5.生产加工过程的无尘化:采用洁净生产工艺、改进工艺流程、设备以及使用新工艺方法如高温烧结、激光等,减少生产过程中产生的粉尘。
6.员工防护:员工防护是一个大问题,总体的员工防护需要包括劳保用具、防护衣、面罩、防毒面具等。
这些设备在未使用时应存放在专门的防尘柜中,以便防止受到灰尘的污染。
7.加强宣传教育:尤其是对新入职员工对防尘知识的培训,让他们认识到粉尘危害的重要性,重视自我保护。
二、针对不同类型工厂的尘控方法1.粮食加工厂:粮食加工厂的工艺流程中存在磨碎等机械加工步骤,大量的粉尘会通过空气散布到运输、储存等其他工序,对所在区域造成危害。
因此,可采取设置除尘器、密闭集尘等方式来防止粉尘外泄,还可以采取环保屏障、湿法除尘等技术手段进行治理。
2.建材制造厂:建材制造厂对尘控的要求也非常高。
因为生产过程中会产生大量的粉尘,采用加水、闭路等湿法除尘,选用降尘剂,还可以采购尘控设备,如:装卸物料尘控系统、粉料运输尘控系统等。
综合防尘措施规程
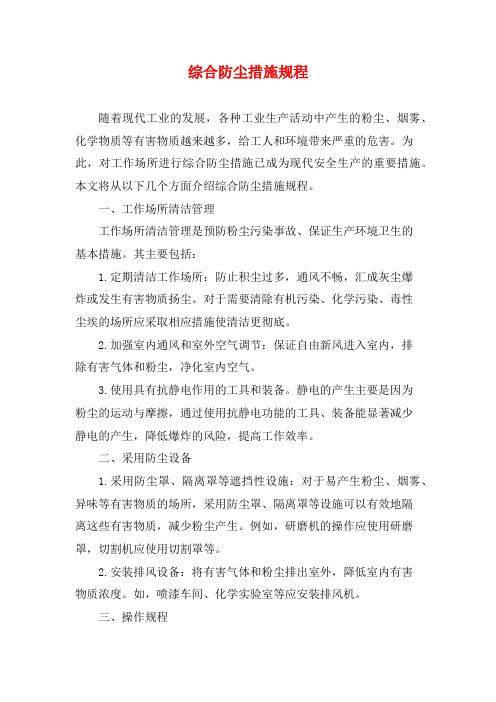
综合防尘措施规程随着现代工业的发展,各种工业生产活动中产生的粉尘、烟雾、化学物质等有害物质越来越多,给工人和环境带来严重的危害。
为此,对工作场所进行综合防尘措施已成为现代安全生产的重要措施。
本文将从以下几个方面介绍综合防尘措施规程。
一、工作场所清洁管理工作场所清洁管理是预防粉尘污染事故、保证生产环境卫生的基本措施。
其主要包括:1.定期清洁工作场所:防止积尘过多,通风不畅,汇成灰尘爆炸或发生有害物质扬尘。
对于需要清除有机污染、化学污染、毒性尘埃的场所应采取相应措施使清洁更彻底。
2.加强室内通风和室外空气调节:保证自由新风进入室内,排除有害气体和粉尘,净化室内空气。
3.使用具有抗静电作用的工具和装备。
静电的产生主要是因为粉尘的运动与摩擦,通过使用抗静电功能的工具、装备能显著减少静电的产生,降低爆炸的风险,提高工作效率。
二、采用防尘设备1.采用防尘罩、隔离罩等遮挡性设施:对于易产生粉尘、烟雾、异味等有害物质的场所,采用防尘罩、隔离罩等设施可以有效地隔离这些有害物质,减少粉尘产生。
例如,研磨机的操作应使用研磨罩,切割机应使用切割罩等。
2.安装排风设备:将有害气体和粉尘排出室外,降低室内有害物质浓度。
如,喷漆车间、化学实验室等应安装排风机。
三、操作规程1.佩戴工作服和个人防护用品:如,防护口罩、防护镜、耳塞、或防尘头套等,以隔绝粉尘对人体的危害。
对于特别危险的作业场所,还应配备抗化学物品、防化服等。
2.合理操作,减少粉尘产生:操作时注意减少机械摩擦和粉尘落地,避免喷洒松扫作业。
在铁艺制品加工、木工作业、沙磨作业等中,应采取喷水降尘,粘合防护、垂直流水降尘等方法。
3.工作之后清理:工作结束之后,应及时清理机器和地面上的粉尘,降低粉尘的存在。
四、员工培训针对不同的岗位和工种,进行相关技术的培训,增强员工的安全意识和防护意识。
培训内容包括粉尘的危害、预防粉尘污染的措施、清扫工作的方法、应急措施等,以确保员工了解其所在工作场所粉尘的性质、来源、危害和防护措施,并能自觉做好防护工作。
- 1、下载文档前请自行甄别文档内容的完整性,平台不提供额外的编辑、内容补充、找答案等附加服务。
- 2、"仅部分预览"的文档,不可在线预览部分如存在完整性等问题,可反馈申请退款(可完整预览的文档不适用该条件!)。
- 3、如文档侵犯您的权益,请联系客服反馈,我们会尽快为您处理(人工客服工作时间:9:00-18:30)。
工厂防尘的综合措施防止粉尘危害的具体措施同其他事物一样不是孤立的,而是与其有关事物密切相关。
因此,必须从设计、设备制造到施工安装,尤其是使用和维护管理等各个方面积极主动配合,采取综合性防尘措施,才能使除尘设施充分发挥效能,真正起到防止粉尘危害、保护劳动者健康的作用。
否则就难于发挥除尘设施的作用,就不能达到国家有关标准规定的要求,必须给予足够的重视。
根据我国的实践经验,综合防尘措施,基本上归纳为以下几个方面。
一、厂房位置和朝向的选择(1)产尘车间在工厂总平面图上的位置,对于集中采暖地区应位于其他建筑物的非采暖季节主导风向的下风侧;在非集中采暖地区,应位于全年主导风向的下风侧。
(2)厂房主要进风面应与夏季风向频率最多的两个象限的中心线垂直或接近垂直。
即与厂房纵轴成60°~90°角。
(3)对形平面的厂房,开口部分应朝向夏季主导风向,并在0°~45°之间。
(4)在考虑风向的同时,应尽量使厂房的纵墙朝南北向或接近南北向,以减少西晒,在太阳辐射热较强及低纬度地区尤须特别注意。
二、工艺方法和工艺布置合理化(1)采用新工艺、新设备、新材料,达到机械化、自动化来消灭尘源或减少粉尘飞扬是最重要的措施。
在工艺改革中,首先应当采取使生产过程不产生粉尘危害的治本措施,其次才是产生粉尘以后通过治理减少其危害的治标措施。
例如,用压力铸造、金属模铸造代替型砂铸造,用磨液喷射加工新工艺取代沿用近一个世纪的磨料喷射加工方法,可以从根本上消除粉尘的污染和对人体的危害;采用配备有气力输送设备的密闭罐车和气力输送系统储运、装卸和输送各种粉粒状物料,用风选代替筛选,能避免在储运、装卸、输送和分级过程中粉尘的飞扬;采用高效的轮碾设备可以减少砂处理设备的台数,从而减少了扬尘点;采用高压静电技术对开放性尘源实行就地抑制,可以有效地防止粉尘扩散,使作业点的含尘浓度大大降低;以不含或少含游离二氧化硅的物料或工艺代替游离二氧化硅含量高的物料或工艺也是从根本上解决粉尘危害的好办法,如用游离二氧化硅含量很低的石灰石砂代替游离二氧化硅含量很高的石英砂制作型砂,可以大大减轻粉尘对人体的危害。
(2)工艺布置必须合理,在工艺流程和工艺设备布局时,应使主要操作地点位于车间内通风良好和空气较为清洁的地方。
一般布置在夏季主导向风的上风侧。
严重的产尘点应位于次要产尘点的下风侧。
在工艺布置时,尽可能为除尘系统(包括管道敷设、平台位置、粉尘的集送及污泥处理等方面)的合理布置提供必要的前提条件。
三、粉尘扩散的控制1.密闭控制这是对产尘点的设备进行密闭,防止粉尘外逸的措施,它常与通风除尘措施配合使用。
所有破碎、筛分、清理、混碾、粉状物料的运输、装卸、储存等过程均应尽量密闭。
密闭装置必须做到不妨碍操作,并以便于拆卸检修、结构严密坚固等为原则。
根据不同的扬尘特点,采取不同的密闭方式。
一般分为局部密闭、整体密闭和密闭小室。
例如,某耐火材料厂的硅砖车间原设有整套通风除尘装置,由于密闭不好,车间内含尘浓度仍高达400mg/m3。
设备进行严格密闭后,含尘浓度降到2~3mg/m3。
国外玻璃行业的粉料加工、称量、配料、混合等工序,广泛采用电子计算机控制,在密闭通风的条件下进行,不但提高了产量和质量,而且粉尘危害也得到控制。
目前,一些技术发达的国家(如英、美、瑞土等国)已出现无人车间、无人生产线。
在粉尘浓度很高、劳动条件十分恶劣的作业中,使用机械手或机器人隔离操作,从而避免了粉尘与人体的直接接触、防止了发生肺尘埃沉着病的可能。
2.消除正压粉尘从生产设备中外逸的原因之一是由于物料下落时诱导了大量空气,在密闭罩内形成正压。
为了减弱和消除这种影响,各种密闭装置除均应保持有足够的空间外,尚须采取下列措施。
(1)降低落料高差按照物料颗粒尺寸,空气诱导量分别与降落距离的1/2或2/3次幂成比例,距离越短,物料诱导空气量就越少;(2)适当减少溜槽倾斜角可以增加颗粒与溜槽壁之间的摩擦或碰撞,以降低诱导空气的能量;(3)隔绝气流,减少诱导空气量在溜槽内采取挡板型溜槽隔流装置。
(4)降低下部正压可采取如下方法。
①连通管法。
将下部正压区和上部负压区连通。
进行泄压,使空气循环流通。
②将导料槽的空间增高,形成缓冲箱。
③在导料槽上加长缓冲箱,其中设迷宫挡板,使空气可以迅速排出而达到泄压的目的。
3.消除“飞溅”现象如图3—1(a)所示。
虽然密闭罩内有排风,但由于飞溅作用,含尘空气高速冲击罩壁,结果从孔隙中逸出。
采用较大密闭罩时,使得含尘气流在到达罩壁上的孔口之前已消耗掉了能量,这样便可减少或不再外逸。
如图3—1(b)所示。
飞溅和诱导空气造成扬尘的区别在于后者会使含尘空气从任何位置的孔口逸出,而飞溅仅从发生飞溅处附近的孔口向外流动。
图3—1 从密闭罩内飞溅为了克服这种现象,首先应避免在飞溅区域内有孔口,装置较宽大的密闭罩,如在皮带运输机的受料点下部不采用托辊,而改用钢板,则可以避免皮带因受到物料冲击而下陷,以致在导料槽和皮带之间形成间隙,而这往往是造成粉尘外逸的原因。
如果将皮带运输机的受料点的排风罩做成双层,对防止飞溅效果更显著。
4.消除空气扰动造成扬尘的另外一个原因是由于设备的转动、振动或摆动而产生的空气扰动。
为解决此类问题,可将设备进行整体密闭或采用密闭小室。
这种装置应做得宽大些,并避免把排风口设在直接扬尘处。
由于空气只是在密闭装置内被搅动,所以风量不必很大,但罩子的气密性要好。
其措施有:门斜口接触;法兰垫料;砂封盖板;毡封轴孔、柔性连接;堵跟糊缝等。
四、静电消尘与湿法消尘1.静电消尘静电消尘装置是建立在电除尘和尘源控制方法的基础上。
它主要包括高压供电设备和电收尘装置(包括密闭罩和排风管)两部分。
直接利用生产设备的密闭罩和排风管作为阳极,在其空间中装设电晕线,并接上高压电源,就构成简易的电除尘器。
含尘气流通过电场,在高压(60~100kV)静电场中,气体被电离成正、负离子,这些离子碰到尘粒,使之带电。
带正电的粉尘很快回到负极电晕线上。
带负电的尘粒趋向正极(密闭罩和风管的内壁),采取简易振打或自行脱落,掉入皮带上或料仓中,净化后的气体经排风管排出。
这种装置的特点是效率高(一般都在99%以上)、设备较简单、施工方便、运行可靠、管理方便、粉尘容易回收。
用于产尘点分散的工艺流程之中,显得特别灵活。
它无需管网复杂的除尘系统,但必须有一套整流升压的供电设备,造价较高。
2.湿法消尘在工艺允许的条件下,可以首先采用湿法消尘的措施来达到防尘的目的,这是一种比较简便和有效的措施。
水对大多数粉尘有良好的“亲和力”,如将物料的干法破碎、研磨、筛分、混合改为湿法操作,在物料的装卸、转运过程中往物料中加水,可以减少粉尘的产生和飞扬。
一般有喷水雾及喷蒸汽降尘两种方法。
(1)喷水雾防尘在工艺允许的条件下,在物料的装卸、破碎、筛分、运转等过程中,在扬尘点采用喷水雾来降尘。
采用这种方法时,应注意以下几点。
①喷嘴喷水雾的方向可与物料流动方向顺向平行或成一定的角度。
②布置喷嘴时应注意防止水滴或水雾被吸到排风系统中去,也不应溅到工艺设备的运转部分,以免影响设备的正常运转。
③喷嘴到物料层上面的距离不宜小于300mm,射流的宽度不应大于物料输送时所处空间位置的最大宽度。
在排风罩和喷嘴之间应装橡皮挡帘。
④喷水管可配置在物料加湿点。
水阀应和生产设备的运行实行联锁。
喷水雾除尘对供水的要求如下。
①水中不应含有病原菌和腐蚀性物质。
②水中固体悬浮物应不致堵塞喷嘴,并应根据喷嘴性能决定允许悬浮物最大颗粒直径。
如对角型等常用喷嘴水中固体悬浮物的颗粒不应大于300pm;含量小于200mg/L。
③水压应保证喷嘴造雾的最低要求,其大小应根据喷嘴的性能决定。
一般喷嘴前的压力应不小于196.133kPa。
喷水雾除尘的加水方法和喷嘴的选择如下。
用于喷水雾除尘的加水工具统称为喷嘴。
喷嘴种类很多,可按需要选用。
专门用于物料加湿的,一般采用简单的不易堵塞的丁字形多孔眼喷水管(见图3—2)和砸扁了的鸭嘴形喷水管(见图3—3)。
丁字形喷水管适用于固定加水点之用,喷水管的长度、孔眼的数量和直径可根据加水宽度和用水量决定;鸭嘴形喷水管可用软胶管连接,作移动加湿物料之用。
图3—2 丁字形多孔眼喷水管图3—3 鸭嘴形喷水管为使物料加湿得更均匀,同时对扬起的粉尘有一定的捕获作用,应采用喷射水滴较细的角形(见图3—4)、直形(见图3—5)和圆形(见图3—6)等喷嘴。
它们的技术性能见表3—1。
图3—4 角形喷嘴图3—5 直形喷嘴图3—6 圆形喷嘴I″=25.4mm表3—1 喷嘴技术性能对于矿槽和露天堆放场等大面积产尘地点,可采用压气喷嘴(见图3—7)。
由于它是用压缩空气引射造雾,水滴细而密集,喷射距离较大,并且可用调节垫和供气压力来调节。
这种喷嘴对水压无严格要求,一般大于49.0333kPa(0.5kgf/cm2)便可;对气压要求不小于196.133kPa(2.0kgf/cm2)。
因雾滴很细可能漂浮于空气中被人吸入体内,故要求用生活用水为宜。
它可以用于定点加水,也可装在移动的支架(见图3—8)上,随时调整加水地点。
图3—7 压气喷嘴1—水套管;2—喷嘴;3—气套管;4—混合管;5—调节垫I″=25.4mm图3—8 压气喷嘴移动式支架图3—9所示为喷嘴喷射特性:图中l为喷射距离,简称射程;D为喷射直径;α为喷射角。
图3—9 喷嘴喷射特性喷水雾除尘喷嘴的布置与计算如下。
为使物料加湿均匀和对扬起的粉尘有较好的捕获效果,合理地布置喷水是很重要的。
对局部产尘地点(见图3—10)和大面积产尘地点(见图3—11),均应按水滴布满整个产尘面且避免水滴喷至设备上的原则布置喷嘴,同时要符合加水量的要求。
图3—10 胶带运输机喷嘴布置图3—11 大面积产尘地点的喷嘴布置喷嘴的布置和计算可按如下步骤进行。
①根据物料加湿的要求初选喷嘴的型号,并从表3—1中查出技术性能。
②根据加水地点所需加的水量Wi 和选定的喷嘴的喷水量W 0,按下式确定喷嘴数量n 1:01W W n i= (3—1)③喷嘴布置的计算。
对于局部产尘地点,如胶带运输机(见图3—10)、板式给料机、摆式给料机等,喷嘴的布置可按下式确定:)2/tan(22αh bn = (3—2)式中 n 2——每排喷嘴数量,个;h ——喷嘴与料面的距离,m ;b ——料层宽度,m ;α——喷嘴的喷射角,按表3—1选取,(°)。
根据n 1与n 2之比确定喷嘴排数。
大面积产尘地点,如翻车机、矿车卸料点等的喷嘴布置如图3—11所示,喷嘴数量按下式确定:202203)()(KD D KD ab n 或= (3—3)式中 n 3——喷嘴数量,个;a ,b ——产尘面长度和宽度,m ;D 0——喷嘴有效射程的喷射直径,m ;K ——喷嘴密度系数,根据加水量的需要在K =0.5~1.0之间选取。