发动机可靠性试验方法..
发动机可靠性试验方法

汽车发动机可靠性试验方法南京汽车质量监督检验鉴定试验所前言本标准与GB/T 18297-2001《汽车发动机性能试验方法》属于同一系列标准,系汽车发动机试验方法的重要组成部分。
本标准自实施之日起,代替QC/T 525—1999。
本标准的附录A为规范性附录。
本标准由中国汽车工业协会提出。
本标准由全国汽车标准化技术委员会归口。
本标准起草单位:东风汽车工程研究院。
本标准主要起草人:方达淳、吴新潮、饶如麟、鲍东辉、周明彪。
引言本标准系在JBn 3744—84即QC/T 525—1999《汽车发动机可靠性试验方法》长期使用经验的基础上参考国外的先进技术,制定了本标准。
本标准对QC/T 525—1999的重大技术修改如下:——拓展了标准适用范围,不仅适用于燃用汽、柴油的发动机,还适用于燃用天然气、液化石油气和醇类等燃料的发动机;——修改了可靠性试验规范,对最大总质量小于3.5t的汽车用发动机采用更接近使用工况的交变负荷试验规范;对最大总质量在3.5t〜12t之间的汽车用发动机采用混合负荷试验规范,以改进润滑状态;冷热冲击试验过去仅在压燃机上进行,现扩展到点燃机,并增加了“停车”工况,使零部件承受的温度变化率加大;——修改了全负荷时最大活塞漏气量的限值,首次推出适用于不同转速范围的非增压机、增压机、增压中冷机的限值计算公式,使评定更为合理;——为使汽车发动机满足国家排放标准对颗粒排放物限值的要求,修改了额定转速全负荷时机油/燃料消耗比的限值(由原来1.8%改为0.3%);——增加“试验结果的整理”的内容,并单独列为一事,要求对整机性能稳定性、零部件损坏和磨损等进行更为规范和详尽的评定;——增加“试验报告”的内容,并单独列为一章,明确试验报告主要内容,使试验报告更为规范。
——增加了附录A《汽车发动机可靠性评定方法》,使评定更为准确和全面,——鉴于汽车发动机排放污染物必须满足国家排放标准的要求,在认证时按排放标准进行专项考核,故本标准不再涉及。
发动机可靠性试验方法

GB/T 19055-2003汽车发动机可靠性试验方法南京汽车质量监督检验鉴定试验所.GB/T 19055-2003前言本标准与GB/T 18297-2001《汽车发动机性能试验方法》属于同一系列标准,系汽车发动机试验方法的重要组成部分。
本标准自实施之日起,代替QC/T 525—1999。
本标准的附录A为规范性附录。
本标准由中国汽车工业协会提出。
本标准由全国汽车标准化技术委员会归口。
本标准起草单位:东风汽车工程研究院。
本标准主要起草人:方达淳、吴新潮、饶如麟、鲍东辉、周明彪。
引言本标准系在JBn 3744—84即QC/T 525—1999《汽车发动机可靠性试验方法》长期使用经验的基础上参考国外的先进技术,制定了本标准。
本标准对QC/T 525—1999的重大技术修改如下:——拓展了标准适用范围,不仅适用于燃用汽、柴油的发动机,还适用于燃用天然气、液化石油气和醇类等燃料的发动机;——修改了可靠性试验规范,对最大总质量小于3.5t的汽车用发动机采用更接近使用工况的交变负荷试验规范;对最大总质量在3.5t~12t之间的汽车用发动机采用混合负荷试验规范,以改进润滑状态;冷热冲击试验过去仅在压燃机上进行,现扩展到点燃机,并增加了“停车”工况,使零部件承受的温度变化率加大;——修改了全负荷时最大活塞漏气量的限值,首次推出适用于不同转速范围的非增压机、增压机、增压中冷机的限值计算公式,使评定更为合理;——为使汽车发动机满足国家排放标准对颗粒排放物限值的要求,修改了额定转速全负荷时机油/燃料消耗比的限值(由原来1.8%改为0.3%);——增加“试验结果的整理”的内容,并单独列为一事,要求对整机性能稳定性、零部件损坏和磨损等进行更为规范和详尽的评定;——增加“试验报告”的内容,并单独列为一章,明确试验报告主要内容,使试验报告更为规范。
——增加了附录A《汽车发动机可靠性评定方法》,使评定更为准确和全面,——鉴于汽车发动机排放污染物必须满足国家排放标准的要求,在认证时按排放标准进行专项考核,故本标准不再涉及。
发动机可靠性、耐久性试验大纲

发动机可靠性、耐久性试验大纲1试验目的全面检测发动机的各项性能技术参数是否满足设计和使用要求。
2 引用标准下列标准包含的条文,在编写本文时,所示版本均为有效,所有标准都会被修订,在实际使用中应探讨使用下列标准最新版本的可能性。
GB/T 725—1991 内燃机产品名称和型号编制规则GB/T 1105—1987 内燃机台架性能试验方法GB/T 1883—1989 往复活塞式内燃机术语GB 3100—1993 国际单位制及其应用JB/T 5135.3—2001 通用小型汽油机技术条件3 标准环境状况、功率修正3.1 标准环境状况按GB/T 1105—1987的规定,标准环境状况为:大气压力:p0=100KP a(750mmHg);相对湿度:φ0=30%;环境温度:T0=298K(25°C)3.2 有效功率的修正用下式修正有效功率P0=αa P …………………………………………… ( 1 )其中:αa———修正系数;P0———标准环境状况下的有效功率,Kw;P———现场环境状况下的有效功率,Kw。
修正系数的计算式αa=(99/P s)1.2(T/298)0.6……………………………( 2 )其中:P s=P-φP swP———现场环境状况下的大气压力,KP a;P sw———现场环境状况下的饱和蒸汽压力,KP a;φ———现场环境温度下的相对湿度;T———现场环境温度,T。
式(2)仅当0.93≤αa≤1.07和288K≤T≤308K及80KP a(600mmHg)≤P s≤110KP a(825mmHg)时才适用;否则应在试验报告中详细说明试验时的现场环境状况。
4 试验条件4.1 附件试验时发动机应装上必需的全部附件,附件的名称应在相应的试验记录表或者试验报告中详细记录。
如果试验台上不能安装原排气管、消声器时,应选择与原排气管、消声器的排气阻力相当的排气管道。
4.2 冷却发动机需使用自身的冷却系统进行冷却,不得另加冷却风源或者冷却介质进行冷却。
汽车发动机可靠性试验方法

汽车发动机可靠性试验方法汽车发动机是汽车的核心部件,高可靠性是其重要的用户性能指标。
因此,为了确保汽车发动机的可靠性,必须进行相应的可靠性试验。
一、可靠性测试的内容1、静态可靠性测试:主要通过对发动机本身及其所配件的拆装、外观检查、抗压测试等一系列静态测试,以确定发动机的各种性能指标是否达到规定的要求。
2、动态可靠性测试:主要是测试发动机在正常工作状态下的可靠性,其方法通常是利用外部特定的机械设备进行动态加载,模拟发动机正常运行时的各种状态,检查发动机是否能够稳定发挥其功能。
3、热力学可靠性测试:主要是测试发动机加热运行时的热可靠性,其方法是将发动机置于特定的热环境中,检查其在正常工作条件下是否可以正常正常运行而不出现热故障现象。
二、可靠性测试的要求1、测试试验应采取科学有效的技术方法,保证测试结果的准确性和可靠性;2、测试设备应能够有效模拟真实的使用状况,避免极端情况的出现;3、测试结果应与实际使用状况相一致,使用前应对发动机进行充分的测试;4、应严格按照规定的质量标准进行可靠性测试,确保测试结果的精确性和准确性;5、应保证检测过程的安全性,裁减检测误差,使可靠性测试结果尽可能准确。
三、可靠性测试的方法1、采用统计学的方法进行可靠性测试:过对发动机的累计耗用量、失效日期和失效概率等指标的统计,可以推断出发动机的可靠性,从而确定其可靠性水平。
2、采用物理学的方法进行可靠性测试:过分析发动机内部结构和装配关系,可以发现可能存在的缺陷,指出发动机的可靠性水平。
3、采用计算机仿真技术进行可靠性测试:过使用计算机仿真技术,可以模拟发动机在实际使用状况下的性能,从而可以准确预测发动机在正常工作状态下的可靠性。
综上所述,汽车发动机可靠性试验是确保汽车发动机可靠性的重要手段。
其内容包括静态可靠性测试、动态可靠性测试、热力学可靠性测试等,要求采用科学有效的技术方法,严格按照质量标准进行测试,可以采用统计学、物理学、计算机仿真技术等多种测试方法,以确保发动机的可靠性。
汽车发动机可靠性试验方法

汽车发动机可靠性试验方法1概述汽车发动机可靠性试验是汽车发动机开发过程中不可或缺的重要一环,其目的是快速、准确地评估发动机的可靠性。
它可以用来检查发动机的性能,以及确定在设计、制造和使用过程中可能出现的质量问题。
通过可靠性试验,生产厂家可以提前知晓问题并采取措施,从而提高发动机的性能并减少生产成本。
2试验方法汽车发动机可靠性试验,主要由室内试验和室外试验组成,室内试验包括真空试验、压力台试验、摩擦损失试验、振动试验和动态性能试验等,室外试验包括高速试验、负载试验、燃油经济性试验和连续启动试验等。
①真空试验:真空试验是汽车发动机试验中最为重要的一项。
真空状态下试验发动机是否能够正常工作,可以评估发动机密封件、压缩比比例、凸轮轴定位精度和活塞等部件的质量等可靠性。
②压力台试验:压力台试验可以用来检测发动机的空转、滑移、负荷情况下的工作性能以及温度、噪音等参数。
通过该试验,可以得到发动机的最大功率,以便对发动机的可靠性进行评估。
③摩擦损失试验:摩擦损失试验是通过测量发动机运行时,活塞、曲轴旋转而引起的摩擦损失来评估发动机可靠性。
④振动试验:振动试验可以在发动机运行时,测量发动机的运动特性,如发动机的转速、转矩、转动惯性和摩擦损失等。
⑤动态性能试验:动态性能试验可以用来检测发动机运行时的温度变化、空气流量及其他参数,以确定发动机在不同条件下的可靠性水平。
⑥高速试验:高速试验可以用来测量发动机在高转速下的工作情况,以及它产生的噪音和振动,为发动机的寿命和质量评估提供有效参考。
3结语汽车发动机可靠性试验可以有效提高发动机的可靠性和工作性能,为生产厂家节省额外的投入,最终达到减少成本、提高产品质量的目的。
发动机启动器的可靠性设计与验证

发动机启动器的可靠性设计与验证引言:在现代交通工具中,发动机是最为重要的部件之一。
而发动机的启动器则是发动机的关键组成部分之一,它负责提供足够的转速和转矩,以便使发动机正常启动。
发动机启动器的可靠性设计与验证对于确保发动机可靠启动具有重要意义。
本文将讨论发动机启动器的可靠性设计与验证的相关内容,包括设计原则、验证方法和优化措施。
发动机启动器的可靠性设计原则:1. 强度与可靠性的平衡:发动机启动器需要具备足够的强度,以承受高强度的启动负荷,同时也需要具备稳定性和耐久性,以确保长期可靠运行。
2. 系统化设计:发动机启动器是一个复杂的系统,需要进行系统化的设计。
在设计过程中,需要考虑启动器的各个组成部分之间的相互关系,并进行全面的分析和评估。
3. 提高制造质量:制造质量对于发动机启动器的性能和可靠性具有重要影响。
因此,在设计过程中,需要注重制造质量的控制,确保每一个部件都符合设计要求。
4. 备件可替代性:发动机启动器是一个消耗性零部件,需要定期更换。
因此,在设计过程中,需要考虑备件的可替代性,以便在发生故障时能够及时更换。
发动机启动器的可靠性验证方法:1. 功能性验证:通过实际测试,验证发动机启动器的启动功能是否正常。
这可以通过模拟实际的工作条件,将发动机启动器连接到测试台上,并进行连续启动和停止测试,以确保其正常工作。
2. 耐久性验证:发动机启动器需要能够承受长期的启动负荷,因此需要进行耐久性验证。
通过进行连续启动和停止测试,以及长时间高速转动测试,评估发动机启动器的耐久性能。
3. 环境适应性验证:发动机启动器需要适应不同的环境条件,包括温度、湿度、振动等。
因此,需要进行环境适应性验证,模拟不同的环境条件,评估发动机启动器在不同环境下的性能表现。
4. 可靠性测试:通过进行可靠性测试,评估发动机启动器的故障率和失效模式。
可以使用可靠性试验台或进行可靠性试验,以模拟发动机启动器在实际使用过程中的故障情况。
发动机台架试验-可靠性试验讲解

学生实验报告实验课程名称:发动机试验技术_______________开课实验室:内燃机实验室2013年5月29日目录一、试验目的二、试验内容1.试验依据2.试验条件3.试验仪器设备4.试验样机5.试验内容与方案(1)交变负荷试验(2)混合负荷试验(3)全速负荷试验(4)冷热冲击试验(5)活塞机械疲劳试验(6)活塞热疲劳试验三、试验进度安排四、试验结果的提供摘要国外在可靠性试验方面己做了许多有益的研究工作,但到目前为止尚未形成统一的试验方法,而且考虑到该试验的非普遍性及技术保密性,将来也不可能形成统一的试验规范。
相对于热疲劳研究状况来讲,国内对机械疲劳的研究还比较少。
为适应发动机比功率和排放法规日益提高的苛刻要求,发动机面临着更高机械负荷和热负荷的严峻考验。
国内高强化发动机最大爆发压力已超过22 Mpa。
活塞的机械疲劳损伤主要体现在销孔、环岸等部位。
活塞环岸、销座及燃烧室等部位由于在较高的工作温度下承受着高频冲击作用的爆发压力,润滑状况较差,摩擦磨损,其他破坏可靠性的腐蚀磨损(缸套一环换向区、排气门/排气门座锥面等)、疲劳磨损(挺杆、轴瓦、齿轮表面等)、微动磨蚀(轴瓦钢背、飞轮压紧处、飞轮壳压紧处、湿缸套止口处等)、电蚀(火花塞电极等)和穴蚀(水泵叶轮等)这些都是可靠性试验的主要目标,也是实施可靠性设计、试验研究的重点部位。
众所周知,在内燃机整机上进行零部件可靠性试验成本昂贵。
本文将参照原有的可靠性试验方法,通过看一些关于可靠性的零部件加速寿命实验技术制定一种评价内燃机可靠性的考核规范,包括活塞机械疲劳试验和活塞热疲劳试验,可迅速做出其可靠性恰当的评价,可以降低研发成本、缩短研发时间。
一、试验目的1通过理解内燃机可靠性评估,评定发动机的可靠性。
1.1了解评估的多种理论方法,如数学模型法、上下限法、相似设备法、蒙特卡洛法、故障分析(包括故障模式影响分析和故障树分析)等。
并掌握故障分析法。
1.2学会可靠性试验评估,为进行可靠性设计奠定基础理论,为发动机及相关零部件提供测试、验证以及改进的技术支持。
汽车发动机可靠性试验方法 GBT 19055-2003
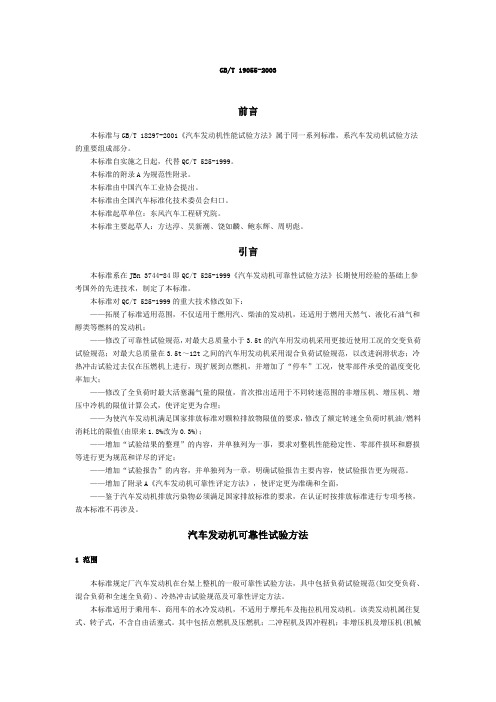
GB/T 19055-2003前言本标准与GB/T 18297-2001《汽车发动机性能试验方法》属于同一系列标准,系汽车发动机试验方法的重要组成部分。
本标准自实施之日起,代替QC/T 525-1999。
本标准的附录A为规范性附录。
本标准由中国汽车工业协会提出。
本标准由全国汽车标准化技术委员会归口。
本标准起草单位:东风汽车工程研究院。
本标准主要起草人:方达淳、吴新潮、饶如麟、鲍东辉、周明彪。
引言本标准系在JBn 3744-84即QC/T 525-1999《汽车发动机可靠性试验方法》长期使用经验的基础上参考国外的先进技术,制定了本标准。
本标准对QC/T 525-1999的重大技术修改如下:——拓展了标准适用范围,不仅适用于燃用汽、柴油的发动机,还适用于燃用天然气、液化石油气和醇类等燃料的发动机;——修改了可靠性试验规范,对最大总质量小于3.5t的汽车用发动机采用更接近使用工况的交变负荷试验规范;对最大总质量在3.5t~12t之间的汽车用发动机采用混合负荷试验规范,以改进润滑状态;冷热冲击试验过去仅在压燃机上进行,现扩展到点燃机,并增加了“停车”工况,使零部件承受的温度变化率加大;——修改了全负荷时最大活塞漏气量的限值,首次推出适用于不同转速范围的非增压机、增压机、增压中冷机的限值计算公式,使评定更为合理;——为使汽车发动机满足国家排放标准对颗粒排放物限值的要求,修改了额定转速全负荷时机油/燃料消耗比的限值(由原来1.8%改为0.3%);——增加“试验结果的整理”的内容,并单独列为一事,要求对整机性能稳定性、零部件损坏和磨损等进行更为规范和详尽的评定;——增加“试验报告”的内容,并单独列为一章,明确试验报告主要内容,使试验报告更为规范。
——增加了附录A《汽车发动机可靠性评定方法》,使评定更为准确和全面,——鉴于汽车发动机排放污染物必须满足国家排放标准的要求,在认证时按排放标准进行专项考核,故本标准不再涉及。
汽车发动机可靠性试验方法

汽车发动机可靠性试验方法
随着汽车市场的发展,汽车发动机的可靠性也变得越来越重要。
车主希望拥有高可靠性的汽车发动机,而且汽车制造商也认识到必须做好可靠性试验才能获得更好的产品质量。
本文旨在介绍汽车发动机可靠性试验的方法。
首先,汽车发动机可靠性试验是通过模拟和真实使用环境来评估发动机可靠性的一种方法。
汽车发动机可靠性试验要求反映汽车发动机在极端使用环境(例如高温和低温)下的性能。
其次,汽车发动机可靠性测试是通过非结构性测试和结构性测试完成的。
非结构性测试是指对发动机的功能和性能进行测试,确保汽车发动机在各种工况下能正常运转;而结构性测试是指对发动机结构和部件进行检查,以确保发动机结构和部件良好。
此外,汽车发动机可靠性试验还可以使用虚拟测试系统,通过计算机模拟运行汽车发动机,精确模拟发动机的各种工况,以达到有效的测试目的。
最后,为了提升汽车发动机的可靠性,可以利用汽车发动机控制系统来实现,可以通过汽车发动机控制系统的控制策略来提高发动机的可靠性。
总之,汽车发动机可靠性试验是一种非常重要的试验方法,其目的是为了确保汽车发动机在各种极端环境下能够正常工作,以满足消费者的要求。
汽车发动机可靠性试验通过模拟和真实使用环境来完成,它利用虚拟测试系统和汽车发动机控制系统来提高发动机的可靠性,
以完成汽车发动机可靠性试验。
发动机可靠性试验方法

发动机可靠性试验方法试验前准备:1.确定试验目标:明确试验的目的,如验证发动机的可靠性和性能。
2.确定试验项目:制定试验项目清单,包括项目名称、测试要求、和测试标准等。
3.确定试验工况:根据实际使用条件和设计要求,确定试验工况,包括转速、负荷、环境温度等参数。
4.准备试验台架:搭建适合试验的台架,包括动力系统、传动系统和冷却系统等。
5.准备试验设备:选择合适的数据采集设备和传感器,用于采集并记录各项试验数据。
试验过程:1.就地试验和安装试验:首先进行就地试验,对发动机的各项参数进行测试,确保性能符合要求。
然后将发动机安装到试验台架上,进行安装试验,测试其运行状态和性能。
2.耐久性试验:在规定的试验工况下,让发动机连续运行一定的时间,通常为几百到几千小时。
期间定期检查发动机的工作情况,如发动机的功率输出、燃油消耗、排放情况等。
3.环境试验:将发动机放入特定的环境中,如低温、高温、高海拔等,测试其在不同环境下的工作状况和性能表现。
4.重启试验:在发动机热机状态下进行多次尝试重新启动发动机,测试其重启性能和可靠性。
5.运动试验:在不同的道路条件下,测试发动机的振动性能和各项参数的变化情况。
6.故障模拟试验:通过对发动机进行特定的负荷和环境刺激,模拟可能发生的故障情况,测试发动机对故障的应对能力和自动保护装置的可靠性。
试验后处理:1.数据分析:对试验期间采集到的数据进行分析和处理,提取关键信息,评估发动机性能和可靠性。
2.故障分析:对试验过程中发生的故障进行分析,确定故障的原因和解决方案,做出相应的改进和优化。
以上是一种常见的发动机可靠性试验方法,根据不同的需求和试验对象,还可以进行其他的试验项目和方法。
发动机可靠性试验是一个复杂的过程,需要经验丰富的技术人员进行设计和操作。
通过可靠性试验,可以不断改进产品,提高发动机的可靠性和性能,满足用户的需求。
论“汽车发动机可靠性试验方法”

摘 要 : 台 架 上 考 核 发 动 机 可靠 性 , 用 强 化试 验 方法 , 运 行 规 范 分 为 限 内 、 在 采 其 限外 两 种 , 者 使发 动 机 所 受 应 力 及 前 热 负 荷 不 超 过 使 用 工 况 , 决一 般性 可 靠性 的 问 题 , 者 属 超过 使用 应 力 , 解 后 旨在 对 某 些 零 部 件 的 可 靠 性 作 出快 速 判 断 ; 热 冲击 限 外 试 验 规 范 被 录用 于 标 准 ; 者 推 出 十 条 发 动 机 可 靠性 评 定 原 则 。 冷 作 关 键 词 : 动 机 ; 靠 性 ; 准 ; 验 方 法 发 可 标 试 中图分类号 :472 U 6 . 文 献 标 识 码 : A 文章 编 号 :0 52 5 {0 20 .0 90 10 .5 0 2 0 )20 1.4
A s us i n a t m o i ng ne r la iiy t s o dic son o u o tve e i ei b l e tc de t Fa g Da h , W u Xi c a , Ra u i,Ba n h i h u Mig io n c un nho oR l n o Do g u ,Z标 准 技术 委 员会 的计 划 ,修 订行 业 内 部标 准 J n34 — 8 “ 车 发 动机 可 靠 性试 验 B 74 4 汽 方法 ”为 G / B T国家推 荐 标 准 ,在 总结 经验 的基 础 上 , 考 了国 内外 资料 , 出 了征求 意 见稿 , 参 提 征集 了
id v d a a tr l bl y T e a t o a e p vd d t e o ie re g n ei bl y a s s me t n ii u p r ei i t . h uh r h v r i e h n n t sf n i e rl i t s e s n . l a i s o c o a i Ke r s e g n ;r l bl y s n ad y wo d : n ie ei i t ; t d r ;o r t n p ga a i a e p a i r r m o o
摩托艇发动机可靠性试验规范研究及加速试验方法探索

成 本 等 方 面 的要 求 高 。影 响 发 动 机 质 量 维 修 、寿命 短 也 是 不能 被接 受 的 。 因 时间 内,完成规 定功能的能力 ”。①此 和 性 能 的 因 素 有 很 多 , 即使 在 设 计 和 制 此 , 任 何 一 款 发 动 机 在 研 发 过 程 中 都 定 义 中 包 括 4 要 素 , 即试 验 对 象 、 规 个 造 上 已经 考 虑 的 非 常 充 分 ,也 必须 经 过 要 制 定 合 理 、有 效 的可 靠 性 试 验 规 范 , 试 验 来 检 验 。 发 动 机 试 验 分 为 产 品 试 用 于 验 证 发 动 机 的可 靠 性 。 验 、 性 能 试 验 、 专 项 研 究 试 验 等 , 而 摩 托 艇 作 为 近 l 年 来 在 国 际 上 非 0
国 内各 类 发动 机 可靠 性 试验 标准 的基
础 上 , 必 须 结 合 产 品 特 点 和 运 行 工 况 等 进 行 研 究 和 试 验 , 并 不 断 改 进 , 才
能形成有指 导意义 的行业规范 。
摩 托 艇 发 动 机 可 靠 性 试 1、发 动机 可 靠 性 试 验 的 定 义 及意 义 验 规 范 研 究 及 加 速 试 验 方 法 探 索
立 合 理 的 维 修 制 度 , 考 核 产 品 的 使 用 耐 久 性 的 两 个 指 标 。 效果和经济合理性 。 13发 动 机 可 靠 性 试 验 分 类 .
行 工 况 是 通 过 不 断 的 试 验 改 进 , 并 结
通 过 两 个 定 义 的 对 比 , 很 明 显 的 合 产 品 实 际 运 行 情 况 , 通 过 大 量 数 据 可 以 看 出 , 耐 久 性 是 在 可 以 维 修 的 条 积 累 形 成 的 经 验 值 , 必 然 有 一 定 的 指
汽车发动机ECU的可靠性实验

1设计实验系统并进行 实验
E CU可 靠性 实验 需要基 于不 同 的环 境条 件进行 ,因此 需要在 不同环境参数条件下 ,完 成实验 。
1 . 1具体设备
1 . 1 . 1自主研发 的 E C U仿真运行测试平 台 在该 平 台下 进行 实验 ,能和 E CU的通信切 换,并实 时监控 E C U 对 故障类型和时 间做一监控 。 1 . 1 . 2可控制温度的试验箱 在 该 试验 箱 内,实 验者 可 以控 制温 度, 使 温度 快速升 降或渐 变 ,并观 察 E C U在 不同 的温度 条件下的不 同变化 。 1 . 1 - 3可控制 湿度的试验箱 在 该 试验 箱 内,可 以通 过人 工控 制或 编 程 控制 调节作 业湿度 ,并观 察 E CU在不 同的 湿度条件 下的不同变化 。 1 . 1 . 4可控制 振动的试验箱 在 该试验 箱 内,对 E CU实行 不同的振 动 条件 ,一方 面观 察在不 同振动 条件 下 E C U 的 不 同作业 情况 ;另一方 面测试 E C U 的抗振 能 力。 1 . 1 . 5可控温度 、湿度 、振动综合实验箱 在 该试验 箱 内,对 汽车发 动机 的 E C U 进 行综合测 试,并结合前面的单 向测试验证其 可
行可靠性增长实验,本次实验选用无替换定时 截 尾实验 ,设定结尾时间为参数 t O( t 0 = 1 0 d ), 1 . 2具体实验 过程 实验 结束数据如表 1 。 对第一 轮可 靠性增长 实验 被淘汰 的 E C U 1 . 2 . 1可靠性筛选 实验 进 行原因分析,一是由于 电路设计时 曲轴位置 作为汽 车发动机 E C U 可靠性 实验 的第 一 传感器为 单信号输 入,无法有效排除干扰:二 步,即初次筛选过程。通常用于大批量生产后 是 由于点火脉冲 过高,易产生过高温度。针对 的E C U 产品进 行 ‘ 海 选 ’ 的过 程 。该 步 骤 是 这两个 问题提 出改进措施 : 为 了淘 汰一 批有 较 明显瑕疵 的 E C U。一般情 ( I )将 电子控制单 元 内的曲轴位置传感 况下 ,是在 上文所 提到的具体设备 中,对试验 器 改为差分 曲轴位置 信号处 理并且将 E C U内 品施加 合理的压力,通常采用温度循环 、不规 部 曲轴位置传感 同时改为差分信号 。 则振动频 率和恒定高温测试,从而使那些有 明 ( 2 )对 点火脉冲不 稳定 的现象,应增加 显缺陷或潜在缺陷的 E CU在 压 力 下显 出鼓 掌 , 泄放二极管 ,分散一部分 点火脉冲 的能量,同 然后将其剔 除。大量实验数据表 明,该筛选实 时提高焊接质量等制造工艺 问题 。 验剔 除 的残次 品可达 9 0 % 准确度 。其余 产品 就第 一轮 可靠 性增 长实 验所表 现 出来 的 进入下一轮实验 。 问题进行针对性 的改善后 ,在实验参数不变 的 1 . 2 . 2可靠性增长实验 情况下继续进行第二轮可靠性增长实验 ,得 出 在 可靠 性筛 选实 验结 束后 ,通过 筛选 的 的实验数据如表 2 。 产品应投入不 同的实验环 境进行测试, 比如同 对该轮 实验失 效 E C U 再 次 进 行 分 析 : 是 时 以电应力和温度应 力作 为双加速应力进一步 因为密封失效导致水汽进入 , 从而烧坏 了电路 , 检测不合格 的产 品,该步实验 需使 产品缺陷暴 使其无法正常工作 。改进措施为密封圈再造加 露为硬件故障 ,如 电路设计 不合格 的产 品暴露 强 内部 控 制 系 统 , 使 E CU 可 靠 性得 到 提升 。 为 电容元件失效 。将 失效样 品进 行原因分析并 无论 是单 纯看 实验 数据 结果 ,还 是 同样 改进,元件失效则改进元件 ,生产 工艺不足则 在置信水平为 0 , 9的单侧置信下限 内进行计算 , 提升 工艺 ,并使 这些 改进 后 的产 品再 次进 行 可靠性 水平 已从 第一轮 的 6 9 4 h上升为 该轮结 可靠性筛选和可靠性增长 实验 ,使汽 车发动机 束的 2 0 6 4 h , 可 靠 性 水 平 大 大 提 升 。证 明 了 汽 E CU的可靠性实验不断得到提升 。 车发动机 E C U 实验的有 效性 。 1 . 2 . 3可 靠 性 鉴 定 实 验 通 过 最 后 的 可 靠 性 鉴 定 实 验 ,在 经 过 改 作为 可靠 性 实验 的最后 一 步,可 靠性 鉴 进的E CU样品中随机 选取 1 O件 样品,持续进 定实验 是确 定产品是否能够定型投产 ,所 以它 行1 0 0 h的 实 验 ,最 终 只有 1 个E C U产品失效, 的运 行条件 应尽可能和真实运行条件相一致 。 小于最初设 定的失效数判定标准 c = 3 ,可以考 该次实验选 用无 替换定时截尾 试验方 案, 虑接受 该样 品设计 ,并将其投入生产 。 即样 品测试过程中,一旦到达规定 的截至 时间 T c ,必须马上停止实验 ,且将不合格产 品数 予 3结论 以记录 ,判 断是否符合接收标准。 通过可靠性筛选实验 、可靠性增长实验和 若 该批 样 品残次 品 数量 小于初 始设 定 的 可 靠性 鉴定 实验 ,对 某 品牌 汽车 发动机 E CU 不合格 标准,可对其进行定型 ,并投入量产 : 若未通 过可靠 性实验,应该拒收该批样 品并对 进 行检测 暴 露其 现有 问题 并进行 针对 性 的改 故 障原 因进 行分 析和 改 进, 以求进 一步 提高 进 ,提高其平均 寿命从 l 1 5 9 h到 4 7 5 2 h ,一方 C U可 靠性 ,另一 E C U 可靠性 ;若 实验过 程 中, 尚未 达到 规定 面 大大提 高该 品牌 发动机 E 截至时 间但不合格样 品数 已超出规定标准 ,也 方面证 明实验 方案 可行且 实验系 统可以满 足实 可停止实验并拒收该批产 品。 际 的生 产 需 求 。
汽车发动机可靠性试验方法

汽车发动机可靠性试验方法汽车发动机可靠性试验方法前言汽车发动机可靠性试验是为保证发动机正常工作、防止故障、改善使用性能、预防事故和提高经济效益而对发动机进行的检测试验。
可靠性试验是以发动机为对象的动态或静态试验。
试验是以实际使用时的各种负荷为目标,通过科学的设计与试验程序确定的参数来评价发动机可靠性的试验,称为可靠性试验。
可靠性试验有主要部件可靠性试验和系统可靠性试验之分。
可靠性试验可用于以下各类型发动机的研究开发项目:汽油机、柴油机、内燃机电喷(喷油泵、喷油器)系统等。
1汽车发动机可靠性试验的目的和任务试验的主要目的是:测定汽车发动机在不同环境条件下工作的可靠性。
在现代汽车的生产中,可靠性已成为汽车质量控制的一个重要环节。
从经济上考虑,发动机的可靠性是最大的经济效益所在,同时也是反映汽车制造质量水平的指标。
可靠性试验是利用机械或电子等手段模拟汽车的实际工况进行测试,其中以汽车发动机可靠性试验最具代表性,通过可靠性试验可以确定出发动机是否存在隐患,检查出影响可靠性的因素,从而采取相应措施消除隐患,减少不合格品,保证产品符合使用要求。
2汽车发动机可靠性试验的环境条件根据国家标准(GB50029-2005),发动机可靠性试验应在环境温度( 20±10)℃,空气相对湿度不超过85%,空气中尘埃粒子的数量和分布不大于一般地区风速0.3 m/s的条件下进行。
在进行发动机可靠性试验时,必须满足上述环境条件,否则会影响可靠性试验的结果。
3.柴油机可靠性试验方法柴油机的性能特点是功率大、转速高,柴油机的转速可达20000转/分,有利于提高加速性能和传递动力。
但柴油机转速高,结构复杂,零件加工精度要求高,润滑条件要求较高,并且易发生振动和噪声。
因此,柴油机的工作条件比汽油机要苛刻得多,要求具有更高的可靠性。
国家标准(GB50058-1997)规定,柴油机可靠性试验是根据汽车发动机可靠性试验方法的原理,模拟实际工况进行,试验可在标准规定的环境条件下进行。
论汽车发动机可靠性试验方法

车辆工程技术65车辆技术 发动机可靠性指的是发动机在规定条件下的使用过程中,其需要在规定的时间间隔内完成规定功能的一项可靠性能力。
同时发动机可靠性是评估当前发动机设计质量与使用质量的一项重要指标内容,其同时受到设计人员、制造人员与使用人员的共同关注。
以汽车发动机为例,其在发动机可靠性的指标上必须要充分满足我国《汽车发动机可靠性试验方法》GB/T 19055-2003中的多项规范要求,如此才能在符合规范的基础上完成设计并以此为基础装配于汽车产品上。
基于此,本文将针对汽车发动机可靠性试验的主要方法进行分析总结,同时针对汽车发动机可靠性试验的其余方法进行阐述讨论。
1 汽车发动机可靠性试验的主要方法 依照我国《汽车发动机可靠性试验方法》GB/T 19055-2003中的具体规定内容,当前我国范围内汽车发动机可靠性试验在具体开展过程中主要涉及到以下内容:1.1 汽车发动机交变负荷循环试验 汽车发动机交变负荷循环试验涵盖矩形循环试验与锯齿形循环试验两种类型,且上述两种试验方法均能针对汽车发动机在实际使用过程中的各项情况进行有效模拟,以此通过重复循环的措施有效模拟汽车发动机在出现零件故障时的具体表现,还能通过加速强化试验来有效提升交变负荷循环试验的开展进程。
同时在汽车发动机交变负荷循环试验的开展过程中,相关人员也可以结合当前汽车发动机的实际要求内容,确定当前汽车发动机是否存在特殊考核要求,以此通过对不同试验规范的设计全面满足对当前汽车发动机可靠性的试验目的。
汽车发动机交变负荷循环试验能够针对汽车发动机在行驶过程中其零件的强度、耐磨性等进行全面考核,也能够针对汽车发动机内部各项零件对于冲击力的抵抗能力、对于长期使用的抗疲劳强度能力进行重点考核。
1.2 汽车发动机热冷冲击试验 汽车发动机冷热冲击试验指的是在冷却液温度变化范围为34~110℃的情况下,针对汽车发动机在冷热不断冲击的情况下所产生的各项零部件的状态变化进行有效探查。
QCT 525-1999 汽车发动机可靠性 试验方法

全速 全负荷试验时活塞漏气量 的测定 每 25h 测定一次 。
6 测且项 目及数据整f
运 行 持 续时 间(d、时数 )、转速 、扭矩 、燃油 消耗量 、机油 压力 、进气状态 ,全速全 负荷试验的机 油消耗 量 、活塞 漏气量、烟度 值等 。
随 时 记 录故 障停 车内容及排除时间 ,保养 内容及所用时 间,更换的零件及损坏情况等 。 绘 制 运 行持 续时间(小时数 )与全速全负荷的实测及校正有效功率 、超 速超 负荷 的实测有效功率、机油
凡 新 设 计或重大改进 的发动机定 型试验 、转厂生产 的发动机验证试验 等均按本标准规定的方法进行 。 1.2 本标准与 汽车发动机性能试验方法 的关 系
本 标 准 是 汽车发动 机试 验方法 的可靠性试验部分 ,QC/T 524- 1999《汽车发动 机性能试验 方法 》系 性 能 试 验 部 分 ,该 标 准 的 有 关 规 定 均 适 用 于本 标 准 。
︐
走 全速全负荷试 验规范(见表 2), 表 2 全速全负荷试验规范
额 定 转 速 的 百 分数
额定功 率的百分数 10 0( 油 门全开)
5.1.3 超 速超 负荷 试验规范(见表 3)a 表 3 超速超负荷试验规范
工 况号 1 2 3 4
额定转速 的百分数
105
怠速
105
停车
额定功率的百分数
100
试验程序
4门 磨合 4.2 精密测量 。 4.3 汽油机怠速 排放量(一氧化碳及碳 氢化合 物)测定 按 QC/T 524 汽 车发 动机性能试验方法 、中 8.3 条的规定 4.4 总功率试验 :按 QC/T 524中 8.4条 的规定。 4.5 负荷特性试验 :按 QC/T5 24中 8.5条 的规定。 4.6 柴油机调速特性试验 :按 QC/T 524中 8.7 条的规定 。 4.7 机械损失功率试验 :按 QC/T 524中 8.8条的规定 。 4.8 机油消耗量试验 :按 QC/T 524中 8.10条 的规定 。 4.9 活塞漏气量试验 :按 QC/T 524中 8.11条的规定 4门 0 可靠性试验
发动机可靠性试验与耐久性试验的区别

发动机可靠性试验与耐久性试验的区别
一内燃机可靠性试验
可靠性是指产品在规定条件下和规定时间内完成规定功能的能力。
由可靠性的定义可知,产品的可靠性并非是一个定值,它随规定条件(环境、使用及维护等条件)、规定时间(时间起点和时间间隔等)、规定功能(例如,可靠是指要求内燃机只要能转动,还是要求内燃机必须能输出一定的功率,还是要求内燃机必须能在低油耗、高效率的状态下工作等)的不同而具有不同的数值。
产品的可靠性是产品的一种内在属性,它是在产品的设计、产生和使用过程中通过一系列保障措施和手段得来的。
这一系列保障措施和手段形成一个完整的可靠性系统工程。
其内容包括可靠性设计、可靠性评估、可靠性预测、可靠性试验、可靠性检验、可靠性管理、可靠性信息收集。
二内燃机的耐久性试验
内燃机的工作寿命长短涉及到内燃机产品设计,制造,材料,工艺,制造过程中的质量管理以及用户使用维修的水平等条件。
因此,工作寿命是一个系统工程问题,在新产品开发定型试验或生产工艺,材料有重大变更时,要进行内燃机产品的耐久性试验,耐久试验的试验时间一般都长于可靠性试验,通过耐久试验,找出产品设计制造中哪些零件可靠性方面存在问题,以便进行改进设计或提高工艺水平,同时通过测量主要件的磨损量变化,可计算出发动机的使用寿命。
同可靠性试验相类似,耐久性试验过程中也需记率何时哪个零件出现了故障及因故障而停机的情况。
试验前后应对内燃机进行性能试验,对主要运动件配合尺寸进行测量,并根据用途,标定功率的不同选用行业标准中规定的试验循环进行试验。
航空发动机可靠性增长试验设计方法研究

航空发动机可靠性增长试验设计方法研究摘要:航空发动机可靠性要求高、试验费用昂贵,为了实现可靠性设计的预期目标,需要研究基于可靠性增长模型的增长试验设计方法。
通过系统性开展航空发动机可靠性增长试验设计,确定可靠性增长模型、增长参数,划分可靠性增长试验阶段,绘制可靠性增长曲线,进行过程跟踪与控制,提出航空发动机可靠性增长试验设计方法,实现有目标有计划的促进发动机可靠性指标达标的目的。
最后通过一个应用举例说明了该方法可在航空发动机研制中进行应用。
关键词:航空发动机;可靠性;杜安模型;增长试验中图分类号:V231.31 引言部分可靠性研究始于第二次世界大战期间,当时的针对电子管故障的研究成为了可靠性研究的起点,之后逐步从电子产品拓展到机电、机械产品领域[1]。
可靠性是指产品在规定的条件下和规定的时间内,完成规定功能的能力,可靠性科学是一门面向故障世界、研究和化解故障,以实现系统最优化的技术科学,是在与故障做斗争的时间过程中生成和发展起来的[2][3]。
可靠性是设计和制造出来的,也是试验出来的。
可靠性试验的目的是:一方面是为了暴露产品潜在缺陷或薄弱环节,为设计改进提供依据;另一方面是评估产品可靠性是否达到规定要求[4]。
早在20世纪50年代,美国开始开展可靠性增长技术的研究,美国先后于20世纪60年代~80年代后期,将可靠性增长技术包括试验的有关内容纳入到有关美军标准中,后续不断完善;中国在20世纪80年代后期,开始将可靠性增长试验有关要求纳入国军标,后续迭代更新。
作为飞机的“心脏”,航空发动机被誉为“现代工业之花”,其制造和研究水平是一个国家工业水平和综合国力的具体体现,目前世界上只有极少数国家能研制[5][6]。
航空发动机是一个国家科技、工业、经济和国防实力的重要标志,具有技术密集度高、军民融合性强、产业带动面广的特点,需要满足推力大、可靠性高、寿命长等使用要求。
近年来随着航空工业的不断发展,航空发动机可靠性越来越引起人们的关注,对航空发动机的可靠性要求越来越高。
- 1、下载文档前请自行甄别文档内容的完整性,平台不提供额外的编辑、内容补充、找答案等附加服务。
- 2、"仅部分预览"的文档,不可在线预览部分如存在完整性等问题,可反馈申请退款(可完整预览的文档不适用该条件!)。
- 3、如文档侵犯您的权益,请联系客服反馈,我们会尽快为您处理(人工客服工作时间:9:00-18:30)。
GB/T 19055-2003汽车发动机可靠性试验方法南京汽车质量监督检验鉴定试验所GB/T 19055-2003前言本标准与GB/T 18297-2001《汽车发动机性能试验方法》属于同一系列标准,系汽车发动机试验方法的重要组成部分。
本标准自实施之日起,代替QC/T 525—1999。
本标准的附录A为规范性附录。
本标准由中国汽车工业协会提出。
本标准由全国汽车标准化技术委员会归口。
本标准起草单位:东风汽车工程研究院。
本标准主要起草人:方达淳、吴新潮、饶如麟、鲍东辉、周明彪。
引言本标准系在JBn 3744—84即QC/T 525—1999《汽车发动机可靠性试验方法》长期使用经验的基础上参考国外的先进技术,制定了本标准。
本标准对QC/T 525—1999的重大技术修改如下:——拓展了标准适用范围,不仅适用于燃用汽、柴油的发动机,还适用于燃用天然气、液化石油气和醇类等燃料的发动机;——修改了可靠性试验规范,对最大总质量小于3.5t的汽车用发动机采用更接近使用工况的交变负荷试验规范;对最大总质量在3.5t~12t之间的汽车用发动机采用混合负荷试验规范,以改进润滑状态;冷热冲击试验过去仅在压燃机上进行,现扩展到点燃机,并增加了“停车”工况,使零部件承受的温度变化率加大;——修改了全负荷时最大活塞漏气量的限值,首次推出适用于不同转速范围的非增压机、增压机、增压中冷机的限值计算公式,使评定更为合理;——为使汽车发动机满足国家排放标准对颗粒排放物限值的要求,修改了额定转速全负荷时机油/燃料消耗比的限值(由原来1.8%改为0.3%);——增加“试验结果的整理”的内容,并单独列为一事,要求对整机性能稳定性、零部件损坏和磨损等进行更为规范和详尽的评定;——增加“试验报告”的内容,并单独列为一章,明确试验报告主要内容,使试验报告更为规范。
——增加了附录A《汽车发动机可靠性评定方法》,使评定更为准确和全面,——鉴于汽车发动机排放污染物必须满足国家排放标准的要求,在认证时按排放标准进行专项考核,故本标准不再涉及。
汽车发动机可靠性试验方法1 范围本标准规定厂汽车发动机在台架上整机的一般可靠性试验方法,具中包括负荷试验规范(如交变负荷、混合负荷和全速全负荷)、冷热冲击试验规范及可靠性评定方法。
本标准适用于乘用车、商用车的水冷发动机,不适用于摩托车及拖拉机用发动机。
该类发动机属往复式、转子式,不含自由活塞式。
其中包括点燃机及压燃机;二冲程机及四冲程机;非增压机及增压机(机械增压及涡轮增压、水对空及空对空中冷);适用于燃用汽油、柴油、天然气、液化石油气和醇类等燃料的发动机。
新没计或重大改进的汽车发动机定型、转厂生产的发动机认证以及现生产的发动机质量检验均可按本标准规定的办法进行可靠性试验。
本标准还可作为发动机制造厂和汽车制造厂之间交往的技术依据。
2 规范性引用文件下列文件中的条款通过本标准的引用而成为本标准的条款。
凡是注日期的引用文件,其随后所有的修改单(不包括勘误的内容)或修订版均不适用于本标准,然而,鼓励根据本标准达成协议的各方研究是否可使用这些文件的最新版本。
凡是不注日期的引用文件,其最新版本适州于本标准。
GB/T 15089 机动车辆及挂车分类GB/T 17754 摩擦学术语GB/T 18297-2001 汽车发动机性能试验方法3 术语和定义GB/T17754和GB/T 18297确立的以及下列术语和定义使用于本标准。
3.1气门下沉量valve sinkage气门与气门座的接触锥面在工作中磨蚀,气门沿其轴线方向陷入气门座的距离。
3.2最大净功率转速 speed of maximum net power不高于额定转速的情况下,发动机带全套车用附件(见GB/T18297-2001第7章)所输出的最大有效功率时的转速,符号为np。
3.3最大净扭矩转速 speed of maximum net torque发动机带全套车用附件(见GB/T 18297-2001第7章)所输出的最大有效扭矩时的转速,符号为nM3.4额定净功率 raled net power发动机带全套车用附件(见GB/T 18297-2001第7章),在额定转速下、全负荷时所输出的校正有效功率。
4 试验发动机试验发动机2台(A发动机及B发动机)应符合发动机制造厂的技术条件,所有紧固件应拧紧至规定值,气门间隙调整至规定值,采用制造厂规定的润滑脂及密封胶。
5 试验一般要求试验所用仪表精度、测量部位及试验数据的计算按GB/T 18297--2001第4章和第5章的规定。
6 对试验一般条件的控制6.1 燃料燃料牌号按发动机制造厂的规定。
汽油温度控制在298K±5 K,柴抽温度控制在311K±5K;其他燃料温度控制按发动机制造厂的规定。
6.2 机油机油牌号按发动机制造厂的规定。
机油温度控制在363K到398K之间或按发动机制造厂的规定。
6.3 冷却液采用软水(钙、镁含量均低于200mg/ke)或采用发动机制造厂规定的冷却液。
冷却液温度控制在361K到383K之间或按发动机制造厂规定的温度;冷热冲击试验时,水温的控制按9.4表4的规定。
6.4 异常燃烧的避免点燃机在台架可靠性试验全过程中,不应发生爆震、早燃及过高燃烧室温度,可按发动机制造厂的规定对火花塞热值、燃料辛烷值、点火提前角及混合气浓度进行适当调整,并在试验报告中注明。
7 试验时发动机所带附件及各系统的调整7.1 进气系统采用装车的标准进气系统.7.2 排气系统采用装车的标准排气系统或具有相等阻力(在额定功率工况下,与标准排气系统的背压相差不大于2 kPa)的试验室排气系统。
7.3 排放控制装置除特殊规定外,均应安装并处于工作状态7.4 冷却系统不装车用风扇,可用外加吹风机对发动机吹拂。
节温器置定在全开的位置。
冷却系统应密封,能建立起厂家规定的放气阀开启压力,压力超过时能自动放气,在试验中(尤其是冷热冲击试验),冷却水在水套里的流量及流向应与装车状态一致。
7.5 点火系统点燃式发动机的点火提前角按发动机制造厂的规定。
7.6 燃料供给系统采用试验室供给系统,即在装车的供给系统中增加燃料消耗量测量、燃料温控等装置,试验室供给系统需满足发动机制造厂的要求,如燃料压力、温度、流量、清洁度等。
压燃式发动机的供油提前角按发动机制造厂的规定。
7.7 发电系统应安装装车的发电机、调压器及蓄电池(在充满电状态)等,并处于工作状态。
8 工作程序本程序在2台发动机(A发动机、B发动机)上进行。
8.1 试前精密测量a) A发动机测量曲轴轴颈/轴瓦、缸筒/活塞组、凸轮/挺杆/摇臂和气门/导管摩擦副的尺寸和间隙(确定磨损用);测量曲轴、凸轮轴止推间隙及齿隙;测量气门/气门座接触带宽和气门下沉量(试前为基准点)等;b) B发动机测量缸垫自由状态厚度及尺寸、缸体上平面及缸盖下平面的平面度、排气歧管密封面的平面度和尺寸(确定变形用)等。
8.2 磨合按发动机制造厂的规范磨合。
发动机安装到台架后,第一次起动前,检查并清除整个进气系统内的尘埃及异物。
在磨合初期及末期按10.4.1取机油油样和未使用过的机油油样一起进行分析。
8.3 性能初试净功率、负荷特性、机械损失功率、活塞漏气量及机油消耗量试验按GB/T 18297—2001的8.3、8.4、8.7、8.10及8.9.3的规定进行。
机油消耗量测量仅在额定转速全负荷下运行24 h。
8.4 可靠性试验按第9章的规定进行8.5 性能复试重复8.3。
8.6 拆检拆检A发动机和B发动机:a) 检测紧固件(如螺栓、螺母等)拧紧力矩松动量。
即拧松紧固件,再准确地拧回到原来的位置(事先应做好记号),此拧回力矩与试验前的拧紧力矩之差为松动量;b) 对主要摩擦副的表面拍摄局部清晰照片。
主要摩擦副有轴颈/轴瓦、缸筒(头环换向处)/活塞(裙部)/环、凸轮/挺杆/摇臂、气门/气门座等;c) 拍摄断口的断面及裂纹的放大照片;d) 拍摄活塞顶上、下表面、火花塞瓷体与电极、油嘴的照片;e) 拍摄在油底壳、罩盖、缸盖上表面、活塞和凸轮等表面上的沉积物、油泥及漆膜的照片;f) 拍摄密封件,如缸垫、进排气管垫、排气管及油封等窜漏的印迹。
其中d)、e)及f)所指零部件,拍照前不应清洗。
在每张照片下方均应附有说明。
8.7 试后精密澜量重复8.1。
精测后要妥善保管所有零部件,以备进一步检查和分析。
9.可靠性试验规范按发动机装车类别进行可靠性试验,试验规范及运行持续时间见表1。
表1 不同最大总质量汽车用发动机可靠性试验规范及运行持续时间单位为小时3500kg<汽车最大总质- 1000 - 300 量≤12000kg汽车最大总质量>- - 1000 500 12000kga 装乘用车及商用车的发动机均按本表分类。
9.1 交变负荷试验规范交变负荷试验规范如图1。
油门全开。
从最大净扭矩的转速(n M)均匀地升至最大净功率的转速(n p),历时1.5min;在n p稳定运行3.5min;随后均匀地降至n M,历时1.5min;在n M稳定运行3.5min。
重复上述交变工况,运行到25min。
油门关闭,转速下降至怠速(n i)运行到29.5min;油门开大,无负荷,使转速均匀上升到105%额定转速(105%n r)或上升到发动机制造厂规定的最高转速,历时0.25min±0.1min;随即均匀地关小油门,使转速降至n M,历时O.25 min±0.1 min。
至此完成了一个循环,历时30 min。
运行800个循环,运行持续时间400h。
9.2 混合负荷试验规范混合负荷试验规范见图2及表2,不同工况间转换在1min内完成,均匀地改变转速2负荷。
每循环历时60min,共1000个循环,运行持续时间1000h。
表2 混合负荷试验规范工况序号发动机转速负荷工况时间1 怠速 n i0 52 最大净扭矩的转速n M油门全开103 最大净扭矩的转速n p油门全开404 额定转速n r油门全开 59.3 全速全负荷试验规范全速全负荷试验规范见表3。
表3 全速全负荷试验规范转速负荷运行持续时间h 额定转速n t油门全开10009.4 冷热冲击试验规范冷热冲击试验规范见图3及表4,表中工况1到2,2到3的转换在5s以内完成;工况3到4,4到1的转换在15s以内完成,均匀地改变转换及负荷。
每循环历时6min。
不同最大总质量汽车用发动机运行持续时间(h)见表1。
表4 冷热冲击试验规范工况序号转速负荷冷却水出口温度K 工况时间s1(热)最大净功率的转速n p油门全开升至378±2°或385±2btp c2 怠速n i0 自然上升153 0 0 自然上升154(冷)最大净功率的转速n pi或高怠速n h降至311-4360-t p-15-15a 散热器盖在绝对压力150kPa放气时,冷却水温升至378K±2K,或按发动机制造厂的规定。