起重机械事故原因及预防
五大伤害及起重伤害原因与预防措施

五大伤害及起重伤害原因预防措施一、高处坠落事故(一)高处坠落事故发生的原因人不安全行为:1、施工人员患有不适合高处作业的疾病,如高血压、心脏病、贫血等。
2456、洞口、临边、交叉作业、攀登作业悬空作业,必须按规范使用安全帽、安全网、安全带,并严格加强防护措施。
7、提升机具要经常维修保养、检查,禁止超载和违章作业。
二、触电事故(一)触电事故发生的原因人的不安全行为:1、电工不按规定穿戴劳动保护用品。
2、作业人员无证操作,私自接电或拆除设备电源线。
物的不安全状态:1、建筑物或脚手架与户外高压线距离太近,不设置防护网。
2、电气设备、电气材料不符合规范要求,绝缘受到磨损破坏。
3、机电设备的电气开关无防雨、防潮设施。
4、施工现场电线架设不当、拖地、与金属物接触、高度不够。
3456、根据不同的施工环境正确选择和使用安全电压。
7、电动机械设备按规定接地接零。
8、手持电动工具应增设漏电保护装置。
9、施工现场应按规范要求高度搭建机械设备,并安装相应的防雷装置。
三、物体打击事故(一)物体打击事故发生的原因人不安全行为:1、交叉作业劳动组织不合理。
2、起重吊装未按“十不吊”规定执行。
3、从高处往下抛掷建筑材料、杂物、垃圾或向上递工具、小材料。
物的不安全状态:1、拆除工程未设置警示,周围未设置护栏和搭防护隔离栅。
152、不按操作规程正确操作机械,违章操作。
物的不安全状态:1、机械设备超负荷运作或带病工作。
2、传动带、砂轮、电锯以及接近地面的联轴节、皮带轮和飞轮等,未设安全防护装置。
3、平刨无护手安全装置,电锯无防护挡板,手持电动工无断电保安器。
4、起重设备未设置卷扬限制器、起重量控制、联锁开关等安全装置。
(二)预防机械伤害事故的措施1、机械设备要安装固定牢靠。
2、增设机械安全防护装置和断电保护装置。
(二)预防坍塌事故的措施1、按照建筑施工安全技术标准、规范编制施工方案,制定专项安全技术措施。
2、基坑开挖前必须做好降(排)水工作,并采取保护措施。
起重机械事故的原因与预防措施
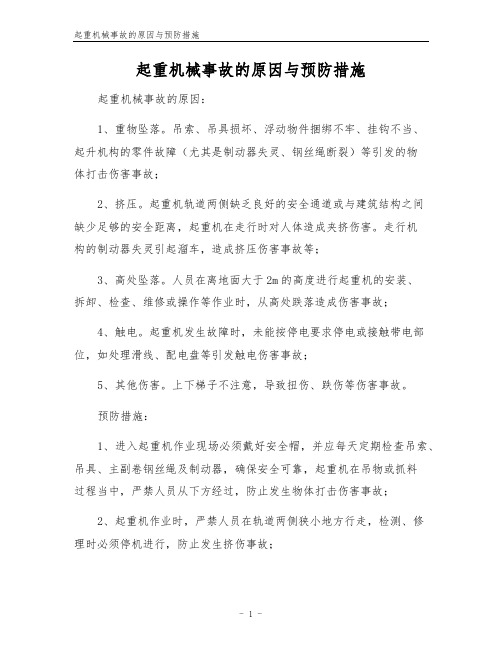
起重机械事故的原因与预防措施
起重机械事故的原因:
1、重物坠落。
吊索、吊具损坏、浮动物件捆绑不牢、挂钩不当、
起升机构的零件故障(尤其是制动器失灵、钢丝绳断裂)等引发的物
体打击伤害事故;
2、挤压。
起重机轨道两侧缺乏良好的安全通道或与建筑结构之间
缺少足够的安全距离,起重机在走行时对人体造成夹挤伤害。
走行机
构的制动器失灵引起溜车,造成挤压伤害事故等;
3、高处坠落。
人员在离地面大于2m的高度进行起重机的安装、
拆卸、检查、维修或操作等作业时,从高处跌落造成伤害事故;
4、触电。
起重机发生故障时,未能按停电要求停电或接触带电部位,如处理滑线、配电盘等引发触电伤害事故;
5、其他伤害。
上下梯子不注意,导致扭伤、跌伤等伤害事故。
预防措施:
1、进入起重机作业现场必须戴好安全帽,并应每天定期检查吊索、吊具、主副卷钢丝绳及制动器,确保安全可靠,起重机在吊物或抓料
过程当中,严禁人员从下方经过,防止发生物体打击伤害事故;
2、起重机作业时,严禁人员在轨道两侧狭小地方行走,检测、修
理时必须停机进行,防止发生挤伤事故;
3、起重机作业时,严禁人员在大小车轨道两侧行走,检测、修理时必须系好安全带,防止发生高处坠落事故;
4、起重机发生故障时,必须停电、挂有人检测、修理,禁止合闸的警示牌后,在进行处理,并要保持各线路绝缘完好。
发现漏电严重时,应通知专业人员处理,防止发生触电事故;
5、上下车必须手扶扶手走安全通道,天车作业时不得强行上车,工作中严禁嬉戏打闹,地面上的油污应时清理,以防滑倒跌伤。
建筑起重机械事故的分析和预防

建筑起重机械事故的分析和预防随着建筑业的飞速发展,建筑起重机械的数量和种类不断增多,应用也更加广泛,但生产厂家在产品的质量稳定性、生产效率、自动化水平、安全装置灵敏可靠程度以及管理水平等方面与世界发达国家相比还是有一定差距,而且还有诸多问题一时适应不了起重机械发展的需要,因此发生在建筑起重机械作业中的伤亡事故屡见不鲜。
发生在起重机作业中常见的伤亡事故及其原因,主要有以下几种:挤压碰撞人是指作业人员被运行中的起重机械挤压碰撞。
起重机械挤压碰撞人也是发生在起重机械作业中常见的伤亡事故,其危险性也很大,后果也很严重,往往也会导致人员死亡。
起重机械作业中挤压碰撞人主要有以下几种状况。
〔1〕吊物〔具〕在起重机械运行过程中摆挤压碰撞人。
发生此种状况原因:一是由于司机操作不当,运行中机构速度变化过快,使吊物〔具〕产生较大惯性;二是由于指挥有误,吊运路线不合理,致使吊物〔具〕在剧烈摆动中挤压碰撞人。
〔2〕吊物〔具〕摆放不稳发生倾倒碰砸人。
发生此种状况原因:一是由于吊物〔具〕放置方式不当,对重大吊物〔具〕放置不稳没有采用必要的安全防护措施;二是由于吊运作业现场管理不善,致使吊物〔具〕突然倾倒碰砸人。
〔3〕在指挥或检修流动式起重机作业中被挤压碰撞,即作为人员在起重机机械运行机构与回转机构之间,受到运行〔回转〕中的起重机机械的挤压碰撞。
发生此种状况原因:一是由于指挥作业人员站位不当〔如站在回转臂架与机体之间〕;二是由于检修作业中没有采用必要的安全防护措施,致使司机在贸然启动起重机械〔回转〕时挤压碰撞人。
〔4〕在巡检查或修理桥式起重机作业中被挤压碰撞,即作业人员在起重机械与建〔构〕筑物之间〔如站在桥式起重机大车运行轨道上或站在巡检人行通道上〕,受到运行中的起重机械的挤压碰撞。
发生此种状况原因:大部份在桥式起重机检修作业中,一是由于巡检人员或修理作业人员与司机缺乏互相联系;二是由于检修作业中没有采用必要的安全防护措施〔如将起重机固定在大车运行区间的装置〕,致使在司机贸然启动起重机时挤压碰撞人。
起重机械安全管理与事故预防
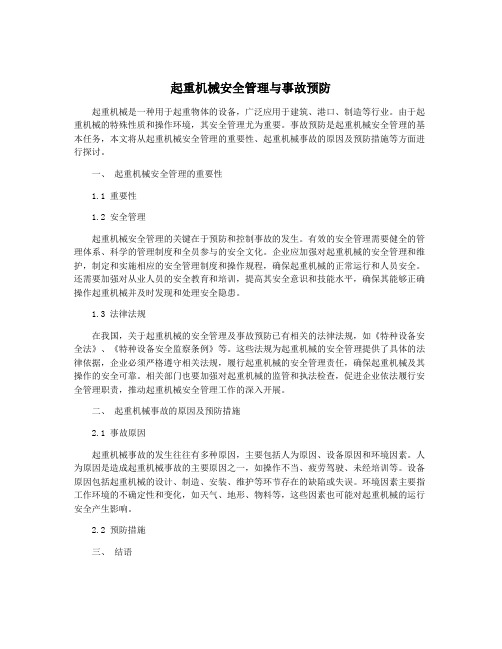
起重机械安全管理与事故预防起重机械是一种用于起重物体的设备,广泛应用于建筑、港口、制造等行业。
由于起重机械的特殊性质和操作环境,其安全管理尤为重要。
事故预防是起重机械安全管理的基本任务,本文将从起重机械安全管理的重要性、起重机械事故的原因及预防措施等方面进行探讨。
一、起重机械安全管理的重要性1.1 重要性1.2 安全管理起重机械安全管理的关键在于预防和控制事故的发生。
有效的安全管理需要健全的管理体系、科学的管理制度和全员参与的安全文化。
企业应加强对起重机械的安全管理和维护,制定和实施相应的安全管理制度和操作规程,确保起重机械的正常运行和人员安全。
还需要加强对从业人员的安全教育和培训,提高其安全意识和技能水平,确保其能够正确操作起重机械并及时发现和处理安全隐患。
1.3 法律法规在我国,关于起重机械的安全管理及事故预防已有相关的法律法规,如《特种设备安全法》、《特种设备安全监察条例》等。
这些法规为起重机械的安全管理提供了具体的法律依据,企业必须严格遵守相关法规,履行起重机械的安全管理责任,确保起重机械及其操作的安全可靠。
相关部门也要加强对起重机械的监管和执法检查,促进企业依法履行安全管理职责,推动起重机械安全管理工作的深入开展。
二、起重机械事故的原因及预防措施2.1 事故原因起重机械事故的发生往往有多种原因,主要包括人为原因、设备原因和环境因素。
人为原因是造成起重机械事故的主要原因之一,如操作不当、疲劳驾驶、未经培训等。
设备原因包括起重机械的设计、制造、安装、维护等环节存在的缺陷或失误。
环境因素主要指工作环境的不确定性和变化,如天气、地形、物料等,这些因素也可能对起重机械的运行安全产生影响。
2.2 预防措施三、结语起重机械安全管理是保障企业生产安全和人员健康的重要环节,其重要性不言而喻。
只有加强对起重机械的安全管理,提高从业人员的安全意识和技能水平,才能有效预防起重机械事故的发生,确保生产和工程的安全可靠。
起重事故资料

起重事故起重机作为一种重要的工业装备,在现代建筑、制造和运输行业中得到广泛应用。
然而,起重机使用过程中的安全问题也经常引起关注。
起重事故是指在使用起重机进行吊装作业时发生的意外事件,可能导致人员伤亡、财产损失等严重后果。
本文将从起重事故的原因、预防措施和事故处理等方面进行探讨。
起重事故的原因起重事故的发生通常是由于多种原因综合作用所致。
常见的引发起重事故的原因包括:1. 设备故障起重机设备本身存在设计缺陷、制造缺陷或者长期使用导致的磨损等问题,可能引发设备故障,从而导致起重事故的发生。
2. 人为原因操作人员在使用起重机时造成的操作失误、操作不当、疲劳驾驶等行为也是起重事故的常见原因之一。
此外,操作人员对起重机的技术不熟悉、未经培训等也容易造成事故。
3. 环境原因恶劣的天气条件、施工现场狭窄、地基不稳等环境因素也是导致起重事故的原因之一。
预防措施为了有效防范起重事故的发生,需要采取一系列的预防措施:1. 定期检查维护设备对起重机设备进行定期的检查维护,确保设备处于良好的工作状态,减少设备故障可能性。
2. 培训操作人员提供专业的起重机操作培训,确保操作人员熟悉起重机的使用方法和操作程序,减少人为原因引发的事故。
3. 加强安全管理建立健全的安全管理制度,加强对施工现场的安全监督和管理,提高安全意识,及时发现和解决潜在的安全隐患。
事故处理一旦发生起重事故,应当按照以下步骤进行处理:1.确保现场安全2.报告并通知相关部门3.现场救援和处理伤者4.对事故进行调查和分析,查明事故原因5.提出事故处理报告,总结教训,完善安全管理措施起重事故的发生给人们的生命财产造成了巨大的损失,因此预防起重事故,加强安全管理至关重要。
只有通过科学的预防措施和事故处理措施,才能有效降低起重事故的发生率,确保施工现场的安全。
塔式起重机常见事故的原因及防范措施

塔式起重机常见事故的原因及防范措施一、日常使用过程中常见的事故及防范措施1. 原因分析:①由于起升机构输出轴的花键与起升卷筒的花键严重磨损超过极限,提升电动机轴上与变速机第一级传动轴上的螺旋伞齿轮副的齿被打掉而引起提升机构失控,在吊物时造成吊物从高处坠落伤人事故。
②采用电磁离合器控制的系统,电磁离合器烧毁或电刷磨损过多不能接触通电,致使在换档过程中造成相似空挡,吊钩失控坠落伤人。
③主钢丝绳或吊钩、吊索卸夹的辅助工具在使用过程中过度磨损后未及时更换,在起吊重物过程中断裂,致使塔机突然失重而倾覆。
④塔身在使用过程中,由于标准节斜杆连接螺栓松动、脱落致使斜杆失去支撑作用,导致斜杆破坏,造成塔身失稳而倾覆。
⑤起重力矩限制器及重量限制器在规定范围内作吊重实验或检查,致使长期受雨水腐蚀而导致内部触点氧化失灵,在吊重过载时不工作而发生事故。
2. 防范措施①加强定期检查,其方法:由经验丰富的修理工和优秀电工组成一组,先将主钢丝绳用绳卡固定在塔身上,便于钢丝绳“松动”,再转动滚轴就可判断齿轮磨损的情况及间隙,必要时可拆开减速机检查。
②断点后拆下电磁离合器上的电刷,观察磨损是否过度,内部弹簧有无伸缩劲,如不行或不灵活就必须中心更换。
用万用表测量离合器线圈是否在规定阻值内,再认真观察吸片是否烧坏,线圈工作时是否产生磁场,并检查夹谷吸片的卡簧是否有效。
待确认正常后再投入使用。
③认真检查钢丝绳、卸夹、吊钩、吊索等,严格执行钢丝绳的磨损规定,发现绳股断裂、纤维芯损坏或钢芯断裂而造成绳径显著减小、笼状畸变、严重扭结等问题立即更换,杜绝事故发生。
④定期用专用扳手检查标准节连接螺栓并紧固。
⑤定期对各限位器进行试验,并调试确认灵敏后作业。
二、塔机拆装过程中常见的事故及防范措施1. 常见事故:①顶升油缸作业中出现事故前面已介绍,此处再在重复。
②吊起重臂时,吊点不准,吊绳选择错误致使起重臂不平稳,使吊绳脱离吊钩造成坠落伤亡事故。
③钢丝绳捆缚方法不对,致使在下放拉杆过程中钢丝绳挂到拉杆连接销,由于中立的作用拉杆突然失重下落,致使塔机摆幅较大造成倒塌事故。
起重机械作业的安全防护:从危险因素到有效措施

起重机械作业的安全防护:从危险因素到有效措施起重机械作业的危险因素及防护措施起重机械是一种重要的工业设备,广泛应用于各种行业,如建筑、制造、港口和采矿等。
然而,起重机械作业也存在一些危险因素,如果不采取有效的防护措施,可能会导致事故的发生。
本文将探讨起重机械作业的危险因素及相应的防护措施,具体包括以下七个方面:1.机械故障起重机械的机械故障可能引发事故。
例如,轴承故障、齿轮故障等可能导致设备无法正常运转或突然停机,从而带来安全隐患。
为防止这类事故,应定期对起重机械进行维护和检查,发现故障及时进行维修和更换。
2.操作失误操作失误是起重机械作业中常见的危险因素。
例如,吊钩悬挂位置不当、司机疲劳驾驶等都可能导致事故发生。
为避免操作失误,应加强对司机的培训,确保他们具备操作起重机械的资格。
同时,对于疲劳驾驶问题,应严格执行司机工作时间和休息时间的规定。
3.过度负荷起重机械过度负荷运转可能导致设备损坏,甚至引发事故。
为避免过度负荷,应正确选用导线,并经常对其进行检查,确保导线的安全承载能力。
同时,应定期检查起重机械的承重部件,确保其能够安全承载额定重量。
4.挤压和剪切起重机械挤压和剪切危险因素主要来自设备运行过程中对人员和物品的物理伤害。
为了降低这种风险,应正确选用防护罩、安全距离控制装置等安全设施,并确保轨道的平整度和固定性,以减少设备运行过程中的颠簸和晃动。
同时,应定期检查设备的安全附件,如限位开关、过载保护装置等,确保其正常工作,防止设备挤压和剪切事故的发生。
5.高处坠落起重机械在高处作业时,如果不采取有效的安全措施,容易导致高处坠落事故的发生。
为了降低高处坠落的风险,应加强安全培训,使操作人员了解高处作业的安全知识和操作规程。
同时,应落实安全管理制度,确保安全措施的执行和监督。
另外,应定期检查起重机械的固定装置和安全附件,确保其完好无损,防止设备坠落伤人。
6.重物掉落起重机械吊装和运输重物的过程中,如果操作不当或设备故障,容易导致重物掉落,从而造成严重的安全事故和财产损失。
典型的起重机械事故及预防措施
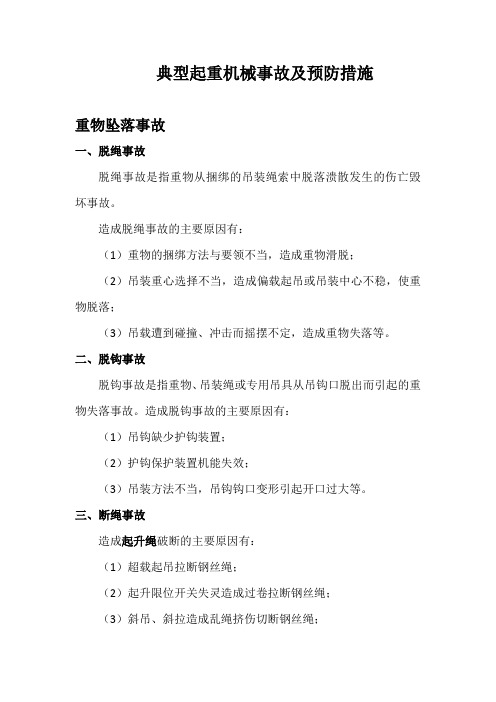
典型起重机械事故及预防措施重物坠落事故一、脱绳事故脱绳事故是指重物从捆绑的吊装绳索中脱落溃散发生的伤亡毁坏事故。
造成脱绳事故的主要原因有:(1)重物的捆绑方法与要领不当,造成重物滑脱;(2)吊装重心选择不当,造成偏载起吊或吊装中心不稳,使重物脱落;(3)吊载遭到碰撞、冲击而摇摆不定,造成重物失落等。
二、脱钩事故脱钩事故是指重物、吊装绳或专用吊具从吊钩口脱出而引起的重物失落事故。
造成脱钩事故的主要原因有:(1)吊钩缺少护钩装置;(2)护钩保护装置机能失效;(3)吊装方法不当,吊钩钩口变形引起开口过大等。
三、断绳事故造成起升绳破断的主要原因有:(1)超载起吊拉断钢丝绳;(2)起升限位开关失灵造成过卷拉断钢丝绳;(3)斜吊、斜拉造成乱绳挤伤切断钢丝绳;(4)钢丝绳因长期使用又缺乏维护保养,造成疲劳变形、磨损损伤;(5)达到或超过报废标准仍然使用等。
造成吊装绳破断的主要原因有:(1)吊钩上吊装绳夹角太大(>120°),使吊装绳上的拉力超过极限值而拉断;(2)吊装钢丝绳品种规格选择不当,或仍使用已达到报废标准的钢丝绳捆绑吊装重物,造成吊装绳破断;(3)吊装绳与重物之间接触处无垫片等保护措施,造成棱角割断钢丝绳。
四、吊钩断裂事故吊钩断裂事故是指吊钩断裂造成的重物失落事故。
造成吊钩断裂事故的原因有:(1)吊钩材质有缺陷;(2)吊钩因长期磨损,使断面减小却仍然使用或经常超载使用,造成疲劳断裂。
每根起升钢丝绳两端的固定也十分重要,如钢丝绳在卷筒上的极限安全圈是否能保证在 2 圈以上,是否有下降限位保护,钢丝绳在卷筒装置上的压板固定及模块固定是否安全可靠。
另外,钢丝绳脱槽(脱离卷筒绳槽)或脱轮(脱离滑轮),也会造成失落事故。
坠落事故坠落事故主要是指从事起重作业的人员,从起重机机体等高空处坠落至地面的摔伤事故,也包括工具、零部件等从高空坠落,使地面作业人员受伤的事故。
1、从机体上滑落摔伤事故2、机体撞击坠落事故3、轿箱坠落摔伤事故4、维修工具零部件坠落砸伤事故5、振动坠落事故6、制动下滑坠落事故触电事故1、触电安全防护措施(1)保证安全电压。
起重机械的危险因素及预防事故措施

起重机械的危险因素及预防事故措施起重机械在现代生产中应用很广,从工矿企业到繁忙的港口、建筑工地以及铁路枢纽,到处都有起重机械在那里承担着成千上万吨的物料搬运和设备安装等任务。
在减轻人民负担、提高工作效率的同时,人们应当高度重视起重机械的安全生产工作,辨识起重机械的危险因素,采取措施,避免安全生产事故的发生。
起重机械事故按其发生的原因可分为挤压事故、高处坠落事故、重物坠落事故、起重机械倒、折断及倾翻事故、触电事故、撞击事故等。
常见的起重机械对安全影响较大的零部件主要有吊钩、钢丝绳、滑轮和滑轮组、卷铜及制动装置等。
因此,我们在充分认识发生事故的类型及设备关键部件的同时,认真做好以下几个方面的工作:一、起重机械应配备相应的安全防护装置,包括:超载限制器、力矩限制器、上升极限位置限制器、下降极限位置限制器、运行极限位置限制器、偏斜调整和显示装置、幅度指示器、防止吊臂后倾装置、极限力矩限制装置、缓冲器、夹轨钳、锚定装置、回转定位装置等安全装置。
二、起重作业必须由经过培训、考核合格并持有《特种作业操作证》的司机操作。
三、作业前要对制动器、吊钩、钢丝绳等安全装置进行检查,发现性能不正常时,应在作业前排除。
四、作业时应按指挥信号进行,开车前应鸣铃或报警,闭合主电源时,应把所有控制器手柄回到零位,作业结束时应将起重机秒定锚定。
五、起重机作业时,不能对运动机件进行检查和检修,不能在有载荷情况下,调整起升、变幅机构的制动器。
六、吊运时,重物不能从人头顶通过,吊臂下严禁站人。
七、起重机工作时,其各部件、机构,必须要与输电线路保持一定安全距离。
八、自行式起重机,工作前应将停机场地平整好,牢固可靠地打好支腿。
九、起重机驾驶人员要求身体健康,凡患有色盲、双眼视力在0.8以下,患有听力障碍症或癫痫病的人不能从事此项工作。
十、起重机驾驶人员要了解并保证做到"十不吊':即:超过额定负荷不吊、指挥信号不明、吊物重量不明、光线暗淡不吊、吊索和附件捆绑不牢不吊、行车吊挂重物直接进行加工不吊、歪拉斜拽不吊、吊物上站人或有浮放物不吊、氧气瓶、乙炔放生器等具有易燃易爆危险的物品不吊、吊物有刃角不垫好不吊、埋在地下或凝固在地面上的物件不吊、违章指挥不吊。
起重机械五种安全事故的主要原因及预防措施

起重机械五起安全事故的主要原因及预防措施起重机械五起事故的主要原因及预防措施如下:1.挤压并与人碰撞是指作业人员在运行中的起重机械挤压碰撞。
在起重机械作业中很常见的伤亡事故,其危险性很大,后果很严重,往往也会导致人员死亡。
起重机械作业中挤压并与人碰撞主要有以下几种情况:(a)吊物在起重机械运行过程中摆动挤压并与人碰撞。
主要原因是:一是由于司机操作不当,运行中机构速度变化过快,使吊物产生较大的惯性。
二是由于指挥有误,吊运路线不合理,致使吊物在剧烈摆动中挤压并与人碰撞。
(b)吊物摆放不稳定发生倾倒砸碰人。
原因是:一是由于吊物放置方式不当,未采取必要的安全保护措施,以防止主要起重物体失稳。
二是由于吊运作业现场管理不善。
(c)在指挥或检修流动式起重机作业中被挤压碰撞,即作为人员在起重机械运行机构与回转机构之间,受到运行中的起重机械的挤压碰撞。
原因是:一是由于指挥作业人员站位不当;二是由于检修作业中没有采取必要的安全防护措施。
(d)在巡回检查或维修桥式起重机作业中被挤压碰撞,即作业人员在起重机械与建筑物之间,受到运行中起重机械的挤压碰撞。
主要原因:一是由于巡检人员或维修人员与司机缺乏相互联系;二是由于检修作业中没有采取必要的安全防护措施。
2.触电触电是指起重机械作业中作业人员触及带电体而发生触电。
起重机械作业大部分处在有点的作业环境中,触电伤亡事故也是发生在起重机械作业中常见的伤亡事故。
主要有以下几种情况:(a)司机触碰滑触线当起重机械司机室设置在滑触线同侧,司机在上下起重视触碰滑线而触电。
主要原因:一是由于司机室位置不合理;二是由于起重机在靠近滑线端侧没有设置防护板,致使司机触电。
(b)触及高压输电线主要原因:首先,起重机械在高压电线下工作时没有采取必要的安全保护措施;二是由于指挥不当,操作有误,致使起重机带电,导致操作人员触电。
(c)电气设施漏电主要原因:一是由于起重机械电气设施不及时,发生漏电;二是由于司机室没有设置安全防护绝缘垫板,致使司机因漏电而触电。
起重机械的危险因素及预防事故措施

起重机械的危险因素及预防事故措施起重机械是现代工业生产中不可或缺的重要设备,广泛应用于建筑、物流、制造等领域。
然而,由于其工作环境复杂、操作难度大以及设备本身的特点,起重机械在使用过程中存在着诸多危险因素,如果不加以重视和防范,极易引发严重的安全事故,给人员生命和财产带来巨大损失。
一、起重机械的危险因素1、起重机械本身的缺陷起重机械的设计、制造和安装质量直接影响其安全性能。
例如,结构强度不足、零部件老化或损坏、控制系统故障等,都可能导致起重机械在运行过程中发生意外。
2、操作人员失误操作人员的技能水平、工作经验和责任心对起重机械的安全运行至关重要。
常见的操作失误包括违规操作、操作不当、判断错误等。
例如,超载起吊、斜拉斜吊、吊运过程中注意力不集中等,都可能引发事故。
3、吊运物品的不稳定性吊运的物品如果重量分布不均匀、形状不规则、捆绑不牢固等,在吊运过程中容易发生晃动、脱落甚至坠落,从而造成人员伤亡和财产损失。
4、环境因素恶劣的天气条件(如大风、暴雨、雷电等)会影响起重机械的稳定性和操作人员的视线,增加事故发生的风险。
此外,施工现场的混乱、通道不畅、照明不足等环境因素也会对起重机械的安全运行产生不利影响。
5、维护保养不当起重机械需要定期进行维护保养,以确保其性能良好、运行可靠。
如果维护保养工作不到位,设备容易出现故障,从而引发安全事故。
二、预防起重机械事故的措施1、严格遵守操作规程操作人员必须经过专业培训,取得相应的资格证书,并严格遵守起重机械的操作规程。
在操作过程中,要保持注意力集中,不得擅自离岗或让无证人员操作。
2、定期检查和维护制定科学合理的检查和维护计划,定期对起重机械进行全面检查和维护。
重点检查结构件的变形和裂纹、零部件的磨损和损坏、控制系统的可靠性等。
发现问题及时处理,严禁设备带故障运行。
3、确保吊运物品的稳定性在吊运物品前,要对物品的重量、形状和重心进行准确评估,并采取合理的捆绑和固定措施,确保物品在吊运过程中保持稳定。
施工现场起重机械事故案例分析与预防

施工现场起重机械事故案例分析与预防近年来,随着城市建设的迅猛发展,施工现场起重机械事故频繁发生,给人们生命财产安全带来了巨大威胁。
本文将从施工现场起重机械事故的案例分析着手,探讨预防这类事故的有效方法。
案例一:高空起重机倾倒某城市高楼大厦施工现场,一台高空起重机因不明原因突然倾倒,造成多名工人被埋压在废墟下。
经初步调查发现,起重机的基础固定不牢固,施工现场没有进行相应的钢筋混凝土浇筑以加固地基,导致起重机倾倒。
分析:这起事故虽然是因基础不牢固引起的,但是可以看出,管理者对施工现场的安全要求并不严格,对于基础加固等关键环节存在疏忽。
缺乏专业安全技术人员进行全面检查和把关,最终导致了这起惨剧的发生。
预防方法:首先,要从根本上加强对施工现场的安全管理,建立安全责任制度,确保每一个环节都有专人负责。
其次,要加强对现场安全技术人员的培训和选拔,提高他们在现场管理中的专业水平。
最后,在施工前,要进行全面细致的安全检查,确保所有设备、材料及人员都符合安全要求。
案例二:起重机吊臂脱离在某工地,一台起重机正在对施工现场进行装载作业时,起重机的吊臂突然脱离,造成周边设施的严重损坏,幸好无人员伤亡。
经技术人员调查发现,起重机的吊臂连接螺栓未按规定进行定期检查和更换,并且在使用过程中没有进行定期维护。
分析:这起事故暴露出管理者在设备维护和检修方面存在较大漏洞,没有按照规定进行定期检查,导致连接螺栓失效,进而发生吊臂脱离事故。
预防方法:加强设备的定期检查和维护,严格按照规定进行螺栓的更换,确保设备连接件的完好性。
制定合理的维护计划,提前预防设备损坏,而不是事故发生后再进行修复。
案例三:重型机械滑移某工地进行土地平整作业时,一台重型机械在操作过程中突然滑移,造成运输车辆无法正常行驶。
经过事故分析,发现是因为工地未进行良好的地面处理,导致重型机械在操作中失去平衡。
分析:这起事故反映出施工现场对地面处理存在严重不足。
由于地面未经过充分的夯实和加固,导致重型机械在操作中容易发生滑移事故。
起重机械事故原因与安全管理分析
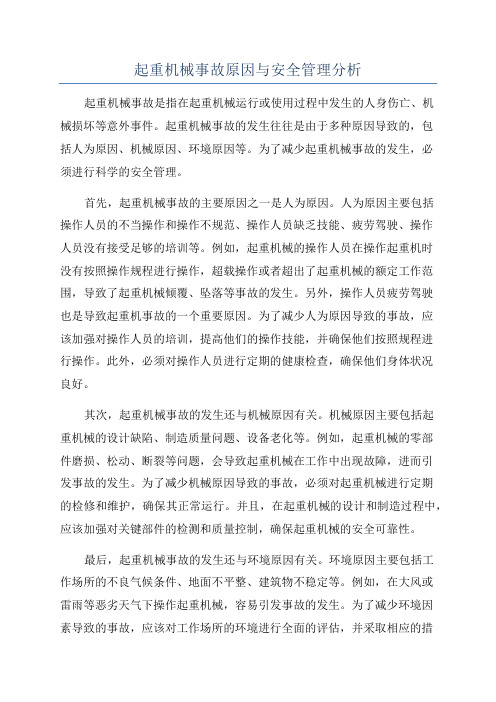
起重机械事故原因与安全管理分析起重机械事故是指在起重机械运行或使用过程中发生的人身伤亡、机械损坏等意外事件。
起重机械事故的发生往往是由于多种原因导致的,包括人为原因、机械原因、环境原因等。
为了减少起重机械事故的发生,必须进行科学的安全管理。
首先,起重机械事故的主要原因之一是人为原因。
人为原因主要包括操作人员的不当操作和操作不规范、操作人员缺乏技能、疲劳驾驶、操作人员没有接受足够的培训等。
例如,起重机械的操作人员在操作起重机时没有按照操作规程进行操作,超载操作或者超出了起重机械的额定工作范围,导致了起重机械倾覆、坠落等事故的发生。
另外,操作人员疲劳驾驶也是导致起重机事故的一个重要原因。
为了减少人为原因导致的事故,应该加强对操作人员的培训,提高他们的操作技能,并确保他们按照规程进行操作。
此外,必须对操作人员进行定期的健康检查,确保他们身体状况良好。
其次,起重机械事故的发生还与机械原因有关。
机械原因主要包括起重机械的设计缺陷、制造质量问题、设备老化等。
例如,起重机械的零部件磨损、松动、断裂等问题,会导致起重机械在工作中出现故障,进而引发事故的发生。
为了减少机械原因导致的事故,必须对起重机械进行定期的检修和维护,确保其正常运行。
并且,在起重机械的设计和制造过程中,应该加强对关键部件的检测和质量控制,确保起重机械的安全可靠性。
最后,起重机械事故的发生还与环境原因有关。
环境原因主要包括工作场所的不良气候条件、地面不平整、建筑物不稳定等。
例如,在大风或雷雨等恶劣天气下操作起重机械,容易引发事故的发生。
为了减少环境因素导致的事故,应该对工作场所的环境进行全面的评估,并采取相应的措施来应对不良气候条件。
此外,应该定期对起重机械运行环境进行检查,确保环境条件符合起重机械的使用要求。
对于起重机械事故的安全管理,应该采取以下措施:1.制定严格的操作规程和安全操作规定,确保操作人员按照规程进行操作。
2.加强对操作人员的培训,提高他们的操作技能,增强他们的安全意识。
起重机械安全事故多发的原因及预防
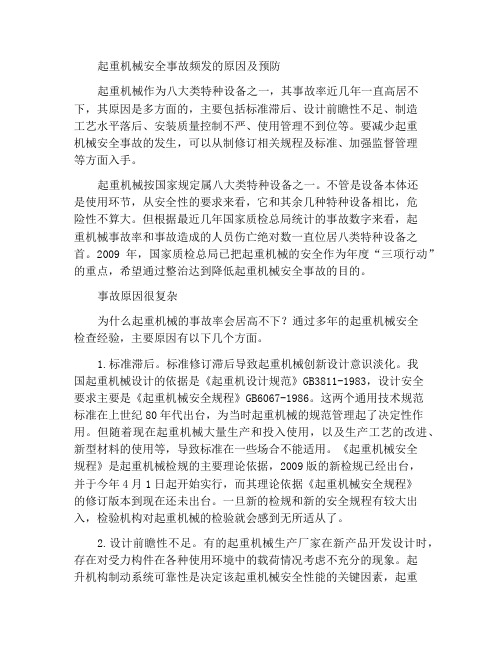
起重机械安全事故频发的原因及预防起重机械作为八大类特种设备之一,其事故率近几年一直高居不下,其原因是多方面的,主要包括标准滞后、设计前瞻性不足、制造工艺水平落后、安装质量控制不严、使用管理不到位等。
要减少起重机械安全事故的发生,可以从制修订相关规程及标准、加强监督管理等方面入手。
起重机械按国家规定属八大类特种设备之一。
不管是设备本体还是使用环节,从安全性的要求来看,它和其余几种特种设备相比,危险性不算大。
但根据最近几年国家质检总局统计的事故数字来看,起重机械事故率和事故造成的人员伤亡绝对数一直位居八类特种设备之首。
2009年,国家质检总局已把起重机械的安全作为年度“三项行动”的重点,希望通过整治达到降低起重机械安全事故的目的。
事故原因很复杂为什么起重机械的事故率会居高不下?通过多年的起重机械安全检查经验,主要原因有以下几个方面。
1.标准滞后。
标准修订滞后导致起重机械创新设计意识淡化。
我国起重机械设计的依据是《起重机设计规范》GB3811-1983,设计安全要求主要是《起重机械安全规程》GB6067-1986。
这两个通用技术规范标准在上世纪80年代出台,为当时起重机械的规范管理起了决定性作用。
但随着现在起重机械大量生产和投入使用,以及生产工艺的改进、新型材料的使用等,导致标准在一些场合不能适用。
《起重机械安全规程》是起重机械检规的主要理论依据,2009版的新检规已经出台,并于今年4月1日起开始实行,而其理论依据《起重机械安全规程》的修订版本到现在还未出台。
一旦新的检规和新的安全规程有较大出入,检验机构对起重机械的检验就会感到无所适从了。
2.设计前瞻性不足。
有的起重机械生产厂家在新产品开发设计时,存在对受力构件在各种使用环境中的载荷情况考虑不充分的现象。
起升机构制动系统可靠性是决定该起重机械安全性能的关键因素,起重机械在使用中的安全事故大多与起重机构有关。
起升机构基本上是采用电磁铁机电式制动器,动作可靠性的关键是对电磁铁线圈的控制,而起重机械电气控制系统设计正是我国生产企业20多年来一直存在的薄弱环节。
起重机械事故多发原因及预控措施
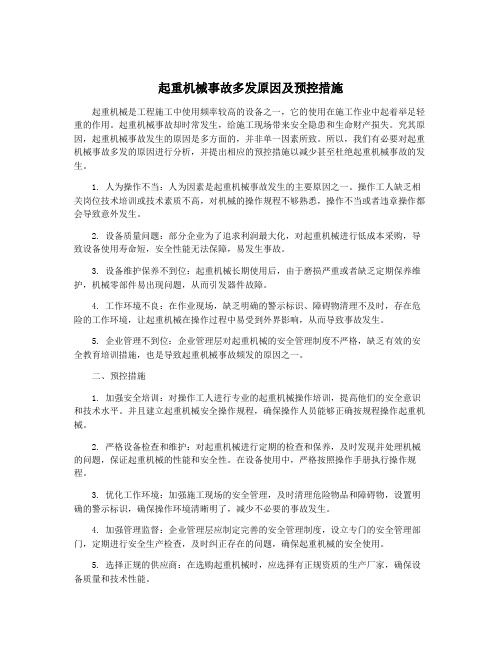
起重机械事故多发原因及预控措施起重机械是工程施工中使用频率较高的设备之一,它的使用在施工作业中起着举足轻重的作用。
起重机械事故却时常发生,给施工现场带来安全隐患和生命财产损失。
究其原因,起重机械事故发生的原因是多方面的,并非单一因素所致。
所以,我们有必要对起重机械事故多发的原因进行分析,并提出相应的预控措施以减少甚至杜绝起重机械事故的发生。
1. 人为操作不当:人为因素是起重机械事故发生的主要原因之一。
操作工人缺乏相关岗位技术培训或技术素质不高,对机械的操作规程不够熟悉,操作不当或者违章操作都会导致意外发生。
2. 设备质量问题:部分企业为了追求利润最大化,对起重机械进行低成本采购,导致设备使用寿命短,安全性能无法保障,易发生事故。
3. 设备维护保养不到位:起重机械长期使用后,由于磨损严重或者缺乏定期保养维护,机械零部件易出现问题,从而引发器件故障。
4. 工作环境不良:在作业现场,缺乏明确的警示标识、障碍物清理不及时,存在危险的工作环境,让起重机械在操作过程中易受到外界影响,从而导致事故发生。
5. 企业管理不到位:企业管理层对起重机械的安全管理制度不严格,缺乏有效的安全教育培训措施,也是导致起重机械事故频发的原因之一。
二、预控措施1. 加强安全培训:对操作工人进行专业的起重机械操作培训,提高他们的安全意识和技术水平。
并且建立起重机械安全操作规程,确保操作人员能够正确按规程操作起重机械。
2. 严格设备检查和维护:对起重机械进行定期的检查和保养,及时发现并处理机械的问题,保证起重机械的性能和安全性。
在设备使用中,严格按照操作手册执行操作规程。
3. 优化工作环境:加强施工现场的安全管理,及时清理危险物品和障碍物,设置明确的警示标识,确保操作环境清晰明了,减少不必要的事故发生。
4. 加强管理监督:企业管理层应制定完善的安全管理制度,设立专门的安全管理部门,定期进行安全生产检查,及时纠正存在的问题,确保起重机械的安全使用。
起重机械事故多发原因及预控措施
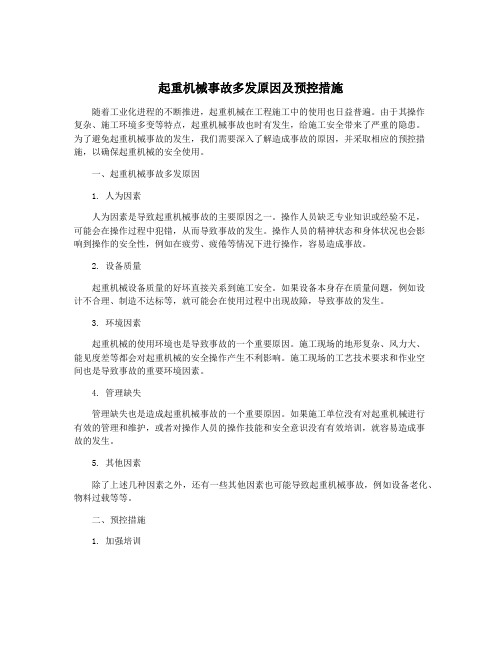
起重机械事故多发原因及预控措施随着工业化进程的不断推进,起重机械在工程施工中的使用也日益普遍。
由于其操作复杂、施工环境多变等特点,起重机械事故也时有发生,给施工安全带来了严重的隐患。
为了避免起重机械事故的发生,我们需要深入了解造成事故的原因,并采取相应的预控措施,以确保起重机械的安全使用。
一、起重机械事故多发原因1. 人为因素人为因素是导致起重机械事故的主要原因之一。
操作人员缺乏专业知识或经验不足,可能会在操作过程中犯错,从而导致事故的发生。
操作人员的精神状态和身体状况也会影响到操作的安全性,例如在疲劳、疲倦等情况下进行操作,容易造成事故。
2. 设备质量起重机械设备质量的好坏直接关系到施工安全。
如果设备本身存在质量问题,例如设计不合理、制造不达标等,就可能会在使用过程中出现故障,导致事故的发生。
3. 环境因素起重机械的使用环境也是导致事故的一个重要原因。
施工现场的地形复杂、风力大、能见度差等都会对起重机械的安全操作产生不利影响。
施工现场的工艺技术要求和作业空间也是导致事故的重要环境因素。
4. 管理缺失管理缺失也是造成起重机械事故的一个重要原因。
如果施工单位没有对起重机械进行有效的管理和维护,或者对操作人员的操作技能和安全意识没有有效培训,就容易造成事故的发生。
5. 其他因素除了上述几种因素之外,还有一些其他因素也可能导致起重机械事故,例如设备老化、物料过载等等。
二、预控措施1. 加强培训为了避免因为人为因素而导致的事故,施工单位应该加强对操作人员的培训,确保其具备良好的操作技能和安全意识。
培训的内容应该包括起重机械的使用方法、相关法律法规等,同时也要加强对操作人员的身体状况和精神状态的管理。
2. 强化管理施工单位要加强对起重机械的管理和维护,定期对设备进行检查、保养和维修,确保设备的正常运行。
同时对操作人员进行安全教育和管理,建立健全的安全管理制度,明确各项操作规程和安全责任,严格执行各项操作流程,以确保施工的安全。
- 1、下载文档前请自行甄别文档内容的完整性,平台不提供额外的编辑、内容补充、找答案等附加服务。
- 2、"仅部分预览"的文档,不可在线预览部分如存在完整性等问题,可反馈申请退款(可完整预览的文档不适用该条件!)。
- 3、如文档侵犯您的权益,请联系客服反馈,我们会尽快为您处理(人工客服工作时间:9:00-18:30)。
编号:SM-ZD-80368 起重机械事故原因及预防Through the process agreement to achieve a unified action policy for different people, so as to coordinate action, reduce blindness, and make the work orderly.
编制:____________________
审核:____________________
批准:____________________
本文档下载后可任意修改
起重机械事故原因及预防
简介:该方案资料适用于公司或组织通过合理化地制定计划,达成上下级或不同的人员
之间形成统一的行动方针,明确执行目标,工作内容,执行方式,执行进度,从而使整
体计划目标统一,行动协调,过程有条不紊。
文档可直接下载或修改,使用时请详细阅
读内容。
深入调查分析各类起重机械事故的成因,能够发现个案中都有其共性,据有关资料统计,目前我国各地区、各行业发生在起重机械作业中的伤亡事故,约占全部伤亡事故的25%左右。
积极探讨其预防措施,对减少事故的发生具有重要的意义。
1 起重机械事故种类及发生的原因
1.1 挤压碰撞
(1)吊物(具)在起重机械运行过程中,由于操作不当,运行中机构速度变化过快,使吊物(具)产生较大惯性力;或指挥有误,吊运路线不合理,致使吊物(具)剧烈摆动。
(2)吊物(具)旋转方式不当,对重大吊物(具)旋转不稳没有采取必要的安全防护措施;或吊运作业现场管理不善,致使吊物(具)突然倾倒。
(3)指挥作业人员站位不当;或检修作业中没有采取必要
的安全防护措施,巡检人员或维修作业人员与司机缺乏相互联系,致使司机贸然启动起重机械(回转)挤压碰撞人或发生其他事故。
1.2 触电(电击)
(1)操作室设置不合理,在操作上下起重机时碰触滑触线而触电;或起重机在靠近滑触线端侧没有设置防护板(网),致使司机触电。
(2)露天作业的流动式起重机在高压输电线下或塔式起重机在高压输电线旁侧,在伸臂、弯幅和回转过程中触及高压输电线,使起重机械带电,致使作业人员触电。
发生的原因:①没有采取必要的安全防护措施(如加装屏护隔离);②指挥不当,操作有误,致使起重机触电带电。
(3)起重机械电气设施维修不及时,发生漏电;或操作室没有设置安全绝缘垫板,致使设施漏电而触电。
1-3 高处坠落
(1)检修吊笼坠落。
造成的原因:①检修吊笼设计结构不合理(如防护杆高度不够,材质选用不符合规定要求,设计强度不够等);②检修作业人员操作不当,没有采取必要的安全
防护措施(如系安全带),致使检修吊笼作业人员坠落。
(2)跨越起重机时坠落。
造成的原因:①检修作业人员没有采取必要的安全措施(如系安全带、挂安全绳、架安全网等);
②作业人员麻痹大意,违章作业,致使发生高处坠落。
(3)安装或拆卸可升降塔身(节)式塔式起重机塔身(节)作业中,塔身(节)连同作业人员坠落。
发生的原因:①塔身(节)设计结构不合理(拆装固定结构存有隐患);②拆装方法不当,作业人员与指挥配合有误,致使塔身(节)连同作业人员一起坠落。
(4)设备超期使用或带病运行。
1.4 吊物(具)坠落砸人
(1)捆绑吊挂方法不当。
发生的原因:①由于捆绑钢丝绳间夹角过大,无平衡梁,捆绑钢丝绳拉断;②由于吊运带棱角的吊物未加防护板,捆绑钢丝绳被切断。
(2)吊索具有缺陷。
发生的原因:起升机构钢丝绳折断,吊钩有缺陷(如吊钩变形、吊钩材质不合要求折断、吊钩组件松等)。
(3)超负荷。
发生的原因:①作业人员对吊物的重量不清
楚(如吊物部份埋在地下、冻结地面上,地脚螺栓末松开等),贸然、盲目起吊,发生超负荷拉断索具,致使吊索具坠落(甩动);②歪拉斜吊发生超负荷而拉断吊索具。
(4)过(超)卷扬。
发生的原因:①没有安装上升极限位置限制器或限制器失灵。
致使吊钩继续上升直到卷(拉)断起升钢丝绳,导致吊物(具)坠落;②起升机构主接触器失灵(如主触头熔接、因机构故障或电磁的剩磁过大使主触头释放动作迟缓),不能及时切断起升直到卷(拉)断起升钢丝绳,导致吊物(具)坠落砸人。
2 起重机械事故特点
(1)发生在起重机械安装、维修作业中的伤害事故较多。
起重机械安装、维修作业是危险性较大的作业,如起重机械挤压碰撞人、高处坠落等伤害事故,主要是在起重机械安装、维修作业中发生的。
(2)起重机械伤害事故的伤害类型比较集中。
本文论述的造成起重机械伤害的直接原因,主要有吊物坠落、挤压碰撞、触电、高处坠落4类,根据初步统计,伤害类型比较集中在吊物坠落和挤压碰撞两类。
(3)由于管理原因造成的伤害事故较多:发生在起重机械作业中的伤害主要管理原因有:一是安全管理规章制度不健全,不落实;二是对起重机械作业有关人员缺乏安全教育,无证操作现象时有发生;三是管理不严格,监督检查力度不够,违章作业现象屡禁不止;四是维修保养不及时,带病运行现象屡见不鲜;五是对起重机械的设计、制造、使用、维修等缺乏系统安全管理。
(4)起重机械伤害事故的机种比较集中:桥门式起重机、流动式起重机、升降机和塔式起重机4类起重机械发生的伤害事故较多,4类合计发生伤害事故接近全部起重机械伤害事故总数的80%。
3 起重机械事故的预防和对策
(1)建全完善制度。
要建立和建全起重机械安全管理岗位责任制,起重机机械安全技术档案管理制度。
真正落实好各项安全操作规程、维修保养制度等,要分工明确,落实责任,奖罚分明。
(2)加强培训教育。
要对起重机械作业人员进行安全技术培训,提高他们的安全技术素质,做到持证上岗,并增强“我
要安全的意识”。
(3)推行系统管理。
必须对起重机械的设计,制造、安装、使用、维修等进行全过程的管理工作。
(4)强化监察力度。
相关职能部门要加强对起重机械的安全监察。
做好“四关工作”,一要把好起重机械产品制造的安全质量关,安全质量不合格的起重机械产品不得出厂;二要把好起重机械安装、维修的安全质量关,不具备从事起重机械安装、维修能力的企业,不得承担起重机械安装,维修业务;三要把好起重机械安全技术监检关。
对新安装的、大修的、改变重要性能的起重机械进行安全技术监验、经监验合格并发给使用合格证后方准投入运行。
对在用的起重机械进行定期监验制度,未经检验的起重机械不准使用;四要把好事故处理关。
对起重机械作业中发生的伤亡事故,应该按照“四不放过”原则进行调查处理。
这里填写您的企业名字
Name of an enterprise。