MRP与库存管理
mrp与库存控制

MRP与库存控制物料需求计划(material requirements planning,MRP)起源于20世纪60年代初,最初是针对当时制造企业生产管理中存在的普遍问题以及传统库存控制方法的不足而提出的一种生产组织管理技术。
它是一种生产计划与控制技术,以控制整个生产过程中的库存水平为出发点,围绕物料为中心组织生产的一种新的生产方式,也是一种新的库存控制思想。
一、订货点法的缺陷订货点法是传统的库存计划与控制方法,其基本思想是根据过去的经验预测未来的需求,根据物料的需求情况来确定订货点和订货批量。
订货点法的基本假设点是:①对各种物料的需求是相互独立的;②物料的需求是稳定、连续的;③订货提前期是已知的、固定的。
订货点法适合于需求比较稳定的物料库存控制与管理。
然而,在实际生产中,随着市场环境发生变化,需求常常是不稳定的、不均匀的,在这种情况下使用订货点法便暴露出一些明显的缺陷。
1.盲目性由于需求的不均匀以及对需求的情况不了解,企业不得不保持一个较大数量的安全库存来应付这种需求。
这样盲目地维持一定量的库存会造成资金积压,产生浪费。
例如,对某种零件的需求可能有如下表所示的三种情况,假定通过经济订货批量计算出该零件的订货批量为50件。
那么,对于情况1,第1周需要10件,若一次订50件,则余下40件还需存放9周,但到第10周真正需要时,余下的40件又不够,必须再次订货50件。
同样地,对于情况2和情况3也存在类似情况。
2.高库存与低服务水平传统的订货点方法使得低库存与高服务水平两者不可兼得。
一般认为,要达到高服务水平,则必须保持高库存,即使高库存也还会常常造成零件积压与短缺共存的局面。
例如:如果装配一个部件,需要5个零件,当以95%的服务水平供给每种零件时,每种零件的库存水平很高。
装配该部件时,5种零件都不发生缺货的概率是(0.95)5=0.774,大致每4次就有一次会发生缺货。
3.形成“块状”需求订货点法的假设条件是均匀需求,但在制造过程中物料的需求是块状的:不需要的时候为零,需要时为一批。
MRP与库存管理

降低库存成本
实施有效的库存管理可以降低库存积 压,减少资金占用,降低库存成本。
提升客户服务水平
准确的库存管理和订单履行可以提高 客户满意度,提升企业形象。
增强企业竞争力
优化生产和库存管理可以帮助企业在 激烈的市场竞争中获得优势。
如何更好地实施MRP与库存管理
制定合理的需求预测和计划
建立完善的库存管理制度
库存管理基本概念
02
库存的定义与分类
定义
库存是指企业或仓库中存放的商 品或物料的总和,包括原材料、 在制品、产成品等。
分类
按用途可分为生产库存、销售库 存和储备库存;按存放地点可分 为原材料库存、半成品库存和成 品库存。
库存管理的重要性
保障生产
01
库存管理能够确保生产所需原材料的及时供应,避免生产中断。
持续改进
通过持续改进MRP与库存管理的流程和方法,不断优化库存结构 和管理效率,提高企业的整体竞争力。
MRP与库存管理案
04
例分析
成功实施MRP与库存管理的企业案例
案例一
某大型制造企业
案例二
某零售巨头
案例三
某医疗器械生产企业
案例四
某汽车零配件供应商
MRP与库存管理实施过程中的挑战与解决方案
挑战一
MRP与库存管理
contents
目录
• MRP(材料需求计划)概述 • 库存管理基本概念 • MRP与库存管理的关系 • MRP与库存管理案例分析 • 结论
MRP(材料需求计
01
划)概述
MRP的定义与原理
定义
MRP,即材料需求计划,是一种基于产品结构和销售预测,计算原材料和零部 件的需求量,以支持生产计划和库存管理的方法。
MRP库存控制法

MRP库存控制法
1 . MRP库存控制法简介
物料需求计划(Material Requirement Planning,简称MRP)库存控制法,是指根据主生产计划、物料清单、库存余额等对每种物料进行计算,并指出何时将会发生物料短缺,以最小库存量来满足需求并避免物料短缺的方法。
MRP被设计并应用于制造业库存管理信息处理系统,它解决了如何实现制造业库存管理目标一一在正确的时间按正确的数量得到所需的物料这一难题。
MRP可以通过主生产计划(MPS)明确企业要生产什么,并通过物料清单( BOM )明确企业的物料需求状况,其逻辑关系如图9-2所示。
图9-2 MRP逻辑关系示意图
2. MRP库存控制法实施步骤
实施MRP库存控制法一般需要如下四个步骤,具体如图9-3所示。
编制主生产计划 录入物料清单 输入物料库存状态 \ 编制物料需求计划 \ ◊生产部根据产品实际 ◊生产部应提供产品的 ◊仓储部负责向生产 ? ◊物料控制人员根据各1 步骤1
步骤2 步骤3 步骤4 种资料计算岀物料的 净需求量和需求时间 部提供物料实时存 储状态和数量 需求量和需求时间,确 定
产品生产计划 ◊产品生产计划的计划 期
需长于最长的产品
物料分解结构清单,并 据此编制物料清单表 物料清单需包括产品 项目结构层次及制成 所提供的数据需 包括物料现有存 根据采购前置期(即 发岀订单到物料入库 生产周期,以确保物
料投入计划的顺利
制订
最终产品的各个阶段 先后顺序,并应及时 录入MRP 系统中 储量、预计到货 量、最低安全存量 等数据 之间的时间)和交期 确定订购时间,编制 物料需求计划 I 图9-3 MRP 实施步骤示意图。
库存管理与MRP
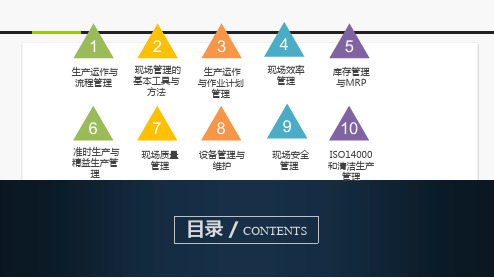
主计划信息 能力平衡信息 车间加工任务
供 应 商
车间作业 事务成本 信息
发货 发货 信息 应收账款
固定资产 发票
固定资产 资产事务信息
成本 成本信息
发票、支付信息 报销信息
发票、收款核销 总账
图5-12 MRPⅡ系统功能结构图
16
5.4 MRP、MRPⅡ和ERP
5.4.5 ERP系统简介
ERP系统功能
1
生产运作与 流程管理
2
现场管理的 基本工具与 方法
3
生产运作 与作业计划 管理
4
现场效率 管理
5
库存管理 与MRP
6
准时生产与 精益生产管 理
7
现场质量 管理
8
设备管理与 维护
9
现场安全 管理
10
ISO14000 和清洁生产 管理
目录 / CONTENTS
第5章
库存管理与 MRP
学习目标
• 了解库存控制的作用和目标 • 了解库存控制系统的构成,两种独立需 求库存控制系统 • 掌握确定两种库存模型的经济订货批量 和ABC库存分类法 • 理解物料需求计划MRP的逻辑流程和计 算模型 • 掌握MRP、MRPⅡ和ERP的组成及其应 用
MRP (Material Requirements Planning)即物 料需求计划 是一个计算机的信息系统, 是一种根据需求和预测来决 定未来物料供应和生产计划 与控制的方法
10
5.4 MRP、MRPⅡ和ERP 5.4.2 MRP的组成
5.4.2 MRP的成
第 5章 库存管理与 MRP
MRP的结 构
8
5.3 库存控制系统及其模型
5.3.2 库存控制模型
库存管理与MRP原理

库存管理与MRP原理库存管理是指通过科学的方法和手段,合理地支配和利用企业内外的物资资源,以满足企业持续生产和经营需要的一项管理工作。
其目的是在减少存货风险、提高客户满意度和降低资金占用的前提下,通过优化库存水平和库存管理过程,实现企业的经济效益最大化。
库存管理的核心思想是找到一个平衡点,既能够确保供应链高效运作,又能够避免过多的库存带来的成本和风险。
对于库存管理的方法和原则有很多种,其中MRP(材料需求计划)原理是一种应用广泛的管理工具。
MRP原理是在企业生产过程中,根据销售订单和生产计划,通过分析物料清单、库存状况和供应商信息等,确定所需物料的数量、时间和采购/生产计划的一种方法。
通过MRP系统的运作,能够准确地计算出各种物料的需求量,并及时采购或生产,避免库存短缺和过剩。
MRP原理的核心是将整个生产过程分解为一个个子计划,按照先后顺序安排物料的采购和生产。
在计算需求量的过程中,需要考虑到物料的预期销售数量、安全库存、采购/生产周期等因素。
通过MRP系统可以实时地监控物料的库存情况和供应链的状态,并根据情况及时地调整计划,以保证物料的及时供应和库存水平的合理控制。
库存管理与MRP原理的核心目标都是提高企业的运作效率和经济效益。
库存管理通过合理的库存控制和优化的库存管理方法,可以减少过多的库存和不必要的资金占用,并缩短供应链的响应时间。
而MRP原理则可以有效地协调供应链中的各个环节,提前预测需求,避免库存短缺和过剩的情况发生。
总之,库存管理与MRP原理是现代企业运作中不可或缺的管理工具。
它们通过优化库存水平和供应链运作,帮助企业节约成本,提高效率和灵活性,从而赢得市场竞争优势。
库存管理与MRP原理是现代企业管理中非常重要的环节,它们对于企业的经营效益和市场竞争力有着直接的影响。
首先,库存管理的核心目标是降低存货风险,提高客户满意度和降低资金占用。
过多的库存会造成资金的长时间占用,并且容易过期、损坏或过时,导致资产负担加重。
MRP原理及其应用

MRP原理及其应用1. 什么是MRPMRP(Material Requirements Planning)即物料需求计划,是一种主要用于生产计划及库存管理的方法。
它通过分析客户需求、当前库存情况以及供应链的其他相关信息,来确定物料的需求及其合理的采购或生产计划。
2. MRP的原理MRP的原理基于以下几个关键概念:2.1 主计划(Master Production Schedule)主计划是指根据企业内外部的需求信息,确定特定时间段内的产品生产计划。
主计划通常根据销售预测、订单和库存水平等数据来制定。
2.2 物料清单(Bill of Materials)物料清单是表示产品所需各个组件及其数量的列表。
它描述了产品的层次结构和组成关系,为MRP提供了基础数据。
2.3 库存状态记录(Inventory Status Record)库存状态记录是记录当前库存情况的数据库。
它包含了每个物料的库存数量、批次、有效期等信息。
MRP通过读取库存状态记录来进行需求计算和库存调整。
2.4 运算逻辑(Logic Calculation)MRP的运算逻辑包括两个核心计算:净需求计算和进行批量推算。
净需求计算是指根据主计划和物料清单,通过逐级展开和扣减,计算出每个物料在每个时间点上的净需求量。
批量推算是指根据净需求量和物料的生产批量等因素,推算出具体的采购或生产计划。
2.5 周期触发(Time Fence)周期触发是指设定一个时间点,在该时间点之前的需求变动不会影响已经计划的采购或生产计划。
周期触发可以保证计划的稳定性,在一定程度上降低需求变动对供应链的影响。
3. MRP的应用MRP可以应用于各种制造行业,如生产制造、加工制造等。
它可以帮助企业进行更精细化的生产计划和库存管理,提高生产效率、降低库存成本,并确保及时交付客户需求。
下面是MRP在实际应用中的几个主要场景:3.1 产品生产计划MRP可以根据销售预测和订单需求,结合库存状态记录和物料清单,计算出具体的产品生产计划。
mrp与传统采购和库存管理的区别

MRP 与传统采购和库存管理的区别介绍在现代企业的供应链管理中,材料需求计划(Material Requirements Planning,MRP)是一个重要的概念。
MRP 旨在有效地规划和控制企业的物料供应,以满足生产计划,并最小化库存损失。
与传统的采购和库存管理相比,MRP 在效率和准确性方面有很大的优势。
本文将探讨 MRP 与传统采购和库存管理的区别。
传统采购和库存管理的缺点在传统的采购和库存管理系统中,采购员根据预测的需求和库存水平来确定采购订单的数量。
这种方法存在以下缺点:1.预测误差:传统方法依赖于对未来需求的预测,但这种预测经常出现误差。
如果预测不准确,采购员可能会采购过多或过少的物料,导致库存过剩或短缺。
2.手工计算:传统方法通常需要采购员手工计算所需的物料数量和时机。
这种手工计算容易出错,并耗费大量时间和精力。
3.缺乏综合性视角:传统方法只关注当前的库存水平和本次采购需求,没有综合性地考虑企业的整体需求计划和生产计划。
4.信息不透明:传统方法的采购和库存管理过程通常缺乏可见性和透明度。
信息的不透明性使得企业难以做出准确的决策,并可能导致资源的浪费和效率低下。
MRP 的优势相对于传统的采购和库存管理方法,MRP 具有以下优势:1.基于需求计划:MRP 根据企业的需求计划和生产计划,自动地生成所需的物料采购订单。
这消除了预测误差,并确保物料的及时供应。
2.自动计算:MRP 通过计算当前库存水平、预测需求和供应链 leadtime,自动地确定正确的采购订单数量和时机。
这消除了手工计算的错误和延误。
3.综合性视角:MRP 能够整合企业的各个部门(如销售、生产和采购),综合考虑其需求计划和生产计划。
这确保了物料的合理采购和利用,避免了库存过剩或短缺。
4.可见性和透明度:MRP 提供了对采购和库存管理过程的可见性和透明度。
通过清晰的报表和数据展示,企业能够准确地了解物料的供应情况和采购活动,从而做出更准确的决策。
四章库存管理与MRP-PPT精品
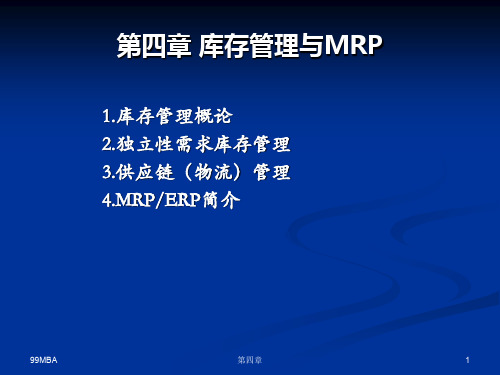
用数学方程拟合趋势曲线,考虑如下几个
中短期
projection 变形:斜率、多项式、对数等。
12集中预测法 Focus
在未来的三个月内,通过计算机模拟测试
中期
forecasting 几个简单的决策方法,看哪个更精确。
99MBA
第四章
胡松评版权所有,侵权8 必究
方法 13谱分析法 Spectra analysis
求:最佳订货批量EOQ? 订货点? 年保管费用?
解: Q* = 1000 只/次
年保管费用:Q×C×h = 120 元/年
年订货次数: 订货点:
n = 12 次 R = d × LT = 148 只
99MBA
第四章
33
某产品市场需求10000件/年,一年工作日为250天。 生产率100件/天,生产提前期为4天。 单位生产成本为50元,单位产品库存费用100元/年。 每次生产准备费用30元。
99MBA
第四章
19
弊: 加长生产周期 占用大量资金,闲置资源 掩盖了管理中的各种内外矛盾 麻癖各级管理人员思想 — 万恶之源!
99MBA
第四章
20
合理 库存
航道深浅?
库存水平
失控 库存
人
生
职员
产 不 均 衡
计 划 不 周
能 力 不 足
设 备 故 障
质 量 问 题
责 不 清 楚
培 训 不 足
14回归模型 Regression Model
简介
预测期
将时间序列分解为几个基本成分,称作谱, 中短期
以几何的正玄余玄曲线来代表,重新组合写
出数学表达式,用来预测。
通过计算机统计将需求与其他变量或解释变 中短期 量联系在一起,用回归模型来预测。
供应链中的物料需求计划与库存管理

供应链中的物料需求计划与库存管理随着全球化的发展和市场竞争的加剧,供应链管理成为企业成功的关键因素之一。
在供应链中,物料需求计划和库存管理是两个重要的环节,对于企业的运营和效益有着重要的影响。
一、物料需求计划物料需求计划(Material Requirement Planning,简称MRP)是供应链管理中的一项重要工具,它通过预测和计划企业的物料需求,以确保生产和供应的顺畅进行。
物料需求计划的核心是根据销售预测、库存水平和生产计划等数据,通过计算和分析,确定所需的物料数量和时间,以便及时采购和生产。
物料需求计划的关键是准确的销售预测。
企业需要通过市场调研、历史数据分析等方法,预测未来一段时间内的销售量和趋势。
基于销售预测,物料需求计划可以帮助企业合理安排生产计划,避免过剩和缺货的情况发生。
另外,物料需求计划还需要考虑库存水平。
库存是企业运作中的重要资产,但过高的库存会增加企业的成本,而过低的库存则可能导致无法满足客户需求。
物料需求计划可以通过分析库存水平和销售预测,帮助企业合理控制库存水平,以达到成本和服务水平的平衡。
二、库存管理库存管理是供应链中另一个重要的环节,它涉及到物料的采购、储存和分配等方面。
库存管理的目标是最大限度地提高供应链的效率和效益,同时减少库存成本和风险。
首先,库存管理需要合理的采购策略。
企业需要根据物料需求计划和供应商的情况,制定合理的采购计划。
采购计划应考虑物料的价格、质量、交货时间等因素,以及供应商的可靠性和稳定性。
通过与供应商的紧密合作,企业可以确保及时获得所需的物料,并降低采购成本。
其次,库存管理需要有效的储存和分配。
企业需要建立适当的仓储设施和管理系统,以确保物料的安全和准确。
仓储设施应具备合理的布局和仓位管理,以最大限度地提高仓储效率。
同时,企业还需要建立合理的物料分配机制,以确保物料能够按时送达客户,提高客户满意度。
最后,库存管理需要有效的库存控制和监控。
企业需要建立库存管理系统,实时跟踪和监控库存水平、周转率等指标。
库存管理与练习题答案
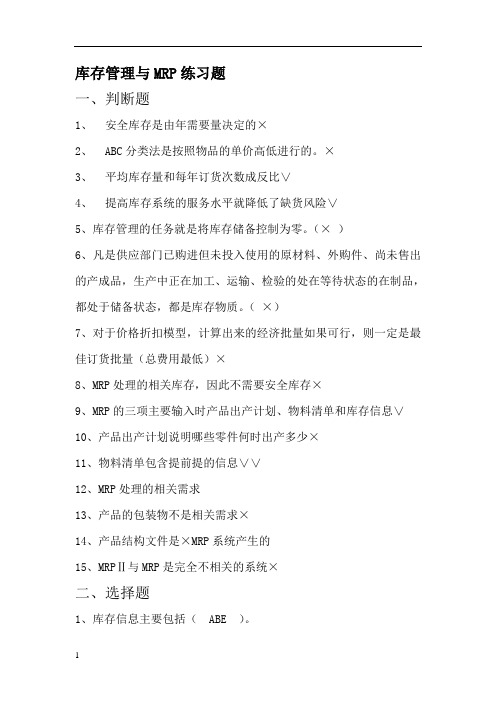
库存管理与MRP练习题一、判断题1、安全库存是由年需要量决定的×2、ABC分类法是按照物品的单价高低进行的。
×3、平均库存量和每年订货次数成反比∨4、提高库存系统的服务水平就降低了缺货风险∨5、库存管理的任务就是将库存储备控制为零。
(×)6、凡是供应部门已购进但未投入使用的原材料、外购件、尚未售出的产成品,生产中正在加工、运输、检验的处在等待状态的在制品,都处于储备状态,都是库存物质。
(×)7、对于价格折扣模型,计算出来的经济批量如果可行,则一定是最佳订货批量(总费用最低)×8、MRP处理的相关库存,因此不需要安全库存×9、MRP的三项主要输入时产品出产计划、物料清单和库存信息∨10、产品出产计划说明哪些零件何时出产多少×11、物料清单包含提前提的信息∨∨12、MRP处理的相关需求13、产品的包装物不是相关需求×14、产品结构文件是×MRP系统产生的15、MRPⅡ与MRP是完全不相关的系统×二、选择题1、库存信息主要包括( ABE )。
2020/3/27A 现有库存量B 预计入库量C 提前期 D 订购批量E 安全库存量2.下列属于相关需求的是( CD )。
A 客户订购的产品B 科研试制需要的样品 C 售后维修需要的备品备件 D 半成品、零部件、原材料需求3.是否考虑生产活动与财务活动的联系是(B )的主要区别。
A 基本MRP与闭环MRPB 闭环MRP与MRPⅡ C MRPⅡ与ERPD 敏捷制造与传统制造模式4. MRP的发展经历了的阶段是( ABCD)。
A 基本MRPB 闭环MRPC MRPⅡ D ERP5、下列关于基本MRP,说法正确的是( B )。
A 涉及企业与市场的界面B 一个完整的生产计划与控制系统C 涉及公司与工厂(车间)的界面D 考虑了市场需求与生产能力的平衡6.基本MRP的依据是( ACD )。
库存管理名词解释
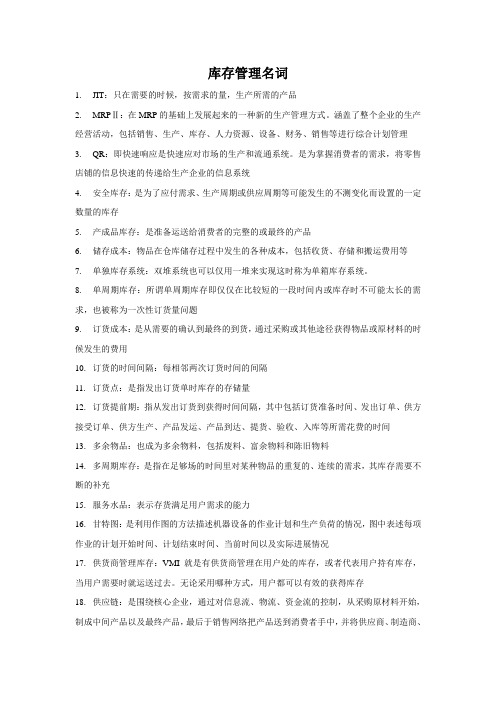
库存管理名词1. JIT:只在需要的时候,按需求的量,生产所需的产品2. MRPⅡ:在MRP的基础上发展起来的一种新的生产管理方式。
涵盖了整个企业的生产经营活动,包括销售、生产、库存、人力资源、设备、财务、销售等进行综合计划管理3. QR:即快速响应是快速应对市场的生产和流通系统。
是为掌握消费者的需求,将零售店铺的信息快速的传递给生产企业的信息系统4. 安全库存:是为了应付需求、生产周期或供应周期等可能发生的不测变化而设置的一定数量的库存5. 产成品库存:是准备运送给消费者的完整的或最终的产品6. 储存成本:物品在仓库储存过程中发生的各种成本,包括收货、存储和搬运费用等7. 单独库存系统:双堆系统也可以仅用一堆来实现这时称为单箱库存系统。
8. 单周期库存:所谓单周期库存即仅仅在比较短的一段时间内或库存时不可能太长的需求,也被称为一次性订货量问题9. 订货成本:是从需要的确认到最终的到货,通过采购或其他途径获得物品或原材料的时候发生的费用10. 订货的时间间隔:每相邻两次订货时间的间隔11. 订货点:是指发出订货单时库存的存储量12. 订货提前期:指从发出订货到获得时间间隔,其中包括订货准备时间、发出订单、供方接受订单、供方生产、产品发运、产品到达、提货、验收、入库等所需花费的时间13. 多余物品:也成为多余物料,包括废料、富余物料和陈旧物料14. 多周期库存:是指在足够场的时间里对某种物品的重复的、连续的需求,其库存需要不断的补充15. 服务水品:表示存货满足用户需求的能力16. 甘特图:是利用作图的方法描述机器设备的作业计划和生产负荷的情况,图中表述每项作业的计划开始时间、计划结束时间、当前时间以及实际进展情况17. 供货商管理库存:VMI就是有供货商管理在用户处的库存,或者代表用户持有库存,当用户需要时就运送过去。
无论采用哪种方式,用户都可以有效的获得库存18. 供应链:是围绕核心企业,通过对信息流、物流、资金流的控制,从采购原材料开始,制成中间产品以及最终产品,最后于销售网络把产品送到消费者手中,并将供应商、制造商、分销商、零售商、直到最终用户连成一个整体的功能网络结构模型19. 供应链中的库存:是指供应链中的所有原材料、在制品和成品20. 固定订货系统:是订货点和订货量都为固定的库存控制系统。
MRP生产运作管理

MRP生产运作管理MRP,即物料需求计划(Material Requirements Planning),是一种通过计算和控制企业物料需求量的生产管理方式。
它基于企业的销售计划和采购计划,通过运用相关数学模型和计算方法,确定制造企业在未来一段时间内所需要的物料数量和供应时间,在此基础上进行生产安排,以满足市场需求,并保持合理的库存水平。
1.提高生产效率:通过精确计划和控制物料需求,减少了生产过程中的浪费和缺货情况,提高了生产效率。
2.简化库存管理:MRP将物料需求与库存水平直接关联,实现了精确的库存控制,避免了过度库存或缺货的问题。
3.降低成本:MRP通过提升生产运作的效率和减少库存水平,从而降低了企业的生产成本。
4.提升客户满意度:准确满足市场需求,通过及时交付和优质产品,提升了客户的满意度。
1.制定销售计划:基于市场需求和销售预测,制定未来一段时间内的销售计划,确定销售量和交货时间要求。
2.制定物料需求计划:根据销售计划和产品结构,确定所需物料的数量和供应时间,建立物料清单和需求计划。
3.确定物料采购计划:根据物料需求计划,确定采购数量和采购时间,保证物料供应的及时性。
4.制定生产计划:基于物料需求计划和现有资源,制定生产计划,包括生产任务分配、生产量和生产时间安排。
5.跟踪和控制生产过程:监控生产进程,及时反馈实际情况,对生产计划进行调整和优化,确保生产进度和质量的达到预期目标。
6.监控物料库存:基于物料需求计划和物料采购计划,定期进行库存盘点和补充,确保物料供应的及时性和准确性。
总之,MRP生产运作管理是一种基于物料需求计划的生产管理方式,通过准确计划和控制物料需求,实现了生产运作的高效性和准确性。
它可以提高生产效率、简化库存管理、降低成本,并提升客户满意度。
企业在实施MRP时,应根据销售计划和物料需求计划,确定物料采购计划和生产计划,并及时跟踪和控制生产过程,以确保生产进度和质量的达到预期目标。
第8章库存管理与MRP原理
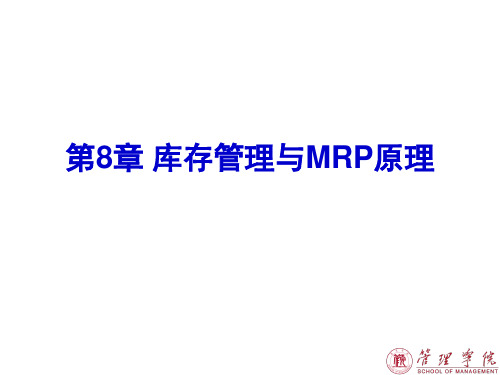
应用范例7-2:某公司的采购部门正准备向某供应商进购一批商品,该公
司根据需求分析,每年需要的量相对稳定,每年需要2000台,订货费用每次 是50元,单位物品的年库存费用为价格的20%。供应商为了刺激该公司多采 购,采用了一定的价格优惠条件,如表7-1所示。确定最佳的订货策略。
表7-1 数量折扣
订货量
X
MPS
Y
MRP
1层
A(1)
B(1)
C(1)
E(1)
2层
C(2)
D(1
)
F(1)
G(1)
低层码
• 物料的低层码是分配给物料清单上的每个物品一 个从0至N的数字码。
– 在产品结构的物料清单中,最上层的低层码为0,下一 层则为1,依次类推
– 一个物品只能有一个MRP低层码。当一个物品在多个 产品中出现,或在同一个产品结构的不同层次出现时, 则取处在最低层的低层码为该物品的低层码。
(一) 库存问题分类
库存问题
单周期需求库存 多周期需求库存
独立需求库存 相关需求库存
随机型 确定型
图8-1 库存问题的分类图
(二)库存成本
(1)存储成本 (2)订货(准备)成本 (3)缺货成本 (4)货物成本
(三)库存控制系统
(1)连续检查库存补给系统 (2)周期检查库存补给系统 (3)不同的补给系统的应用选择
物料清单BOM
• 物料清单BOM(Bill of Materials):是产 品结构的技术性描述文件,它表明了产品 组件、子件、零件直到原材料之间的结构 关系,以及每个组装件所需要的各下属部 件的数量。
• 物料清单是一种树型结构,又称为产品结 构树。
物流工程学院-陈敏
产品BOM
MRP库存管理技术

仓储管理
(三)MRP采购系统的运行 1.MRP的输入
MRP的输入有3个文件:
(1)主生产进度计划(MPS) (2)主产品结构文件(BO LT=1
C(1) LT=3
D(1) LT=1
C(1) LT=3
表示自制 表示外购
(3)库存状态文件 ①总需求量 ②计划到货量
③库存量 2.MRP的输出 (1)净需求量 (2)计划接受订货量 (3)计划发出订货量
仓储管理
MRP库存管理技术 一、基本MRP的提出及原理 (一)MRP采购的产生 (二)MRP的基本原理
MRP逻辑原理图
主生产进度计 划 MPS
主产品结构 清单BOM
物料需求计划 MRP
库存文件
制造任务单
采购任务单
1.主产品 2.主产品的结构文件BOM(Bill of Materials) 3.主生产进度计划MPS(Master Production Schedule) 4.产品库存文件 5.制造任务单和采购订货单
(四) MRP采购的注意事 项 (五)MRP采购的特点 1. 需求的相关性 2. 需求的确定性 3. 计划的精细性 4. 计算的复杂性
二、闭环MRP (一)闭环MRP的原理 (二)能力需求计划(Capacity Requirement Planning,CRP) (三)由MRP输出的零部件作业 计划
能力需求计划报表生成过程
计划 下达
加工任务
确定
需用负荷
需求能力
可用能力
工艺路线
能力需求计划
工作中心能力
平衡负荷
1.车问订单下达 2.作业排序 3.投入产出控制 4.作业信息反馈
三、MRPⅡ (一)MRPⅡ的产生及思想原理 (二)MRPⅡ的特点 1.计划的一贯性与可行性 2.管理的系统性 3.数据共享性 4.动态应变性 5.模拟预见性 6.物流、资金流的统一 四、MRPⅢ
- 1、下载文档前请自行甄别文档内容的完整性,平台不提供额外的编辑、内容补充、找答案等附加服务。
- 2、"仅部分预览"的文档,不可在线预览部分如存在完整性等问题,可反馈申请退款(可完整预览的文档不适用该条件!)。
- 3、如文档侵犯您的权益,请联系客服反馈,我们会尽快为您处理(人工客服工作时间:9:00-18:30)。
• 粗能力计划(RCCP)是对生产计划所需的关键生产能 力作一简单的估算,给出能力需求的概貌,主要用于 编制生产计划大纲或主生产计划,它将主计划转换成 相关的工作中心能力的需要。粗能力计划忽略了一些 基本的信息,只是针对设置为“关键工作中心”的工 作中心能力进行运算。
–MRPⅡ的思想集中体现了制造企业生产经营过程中 的客观规律和需求,其功能覆盖了市场预测、订单 接收、生产计划、物料需求、能力需求、库存控制、 车间管理直到产品销售的整个生产经营过程以及相 关的所有财务活动。为制造业提供了有效的计划和 控制工具。
MRPⅡ系统(企业整体效益)
订货
否
营销计划
财
生产计划
D(3) B(2)
E(2) A (1)
C(3)
T》=T?
每层的i完成?
t=t+1 i=i+1
各层是否完成? 结束
l=l+1
举例
设零件i现存量为10单位,前置时间为2周,批量为25单 位。各时段的总需求量如下表(每个时段长为1周)。 要求通过MRP系统计算表计算得出各时段的计划订货发 出量(已知时段1和时段2的预计到达量分别为10和25 单位)。 前置时间:2周 批量:≥25单位
零件i各时段的总需求量
时段序号 1 2 3 4 5 6 7 8
总需求量 10 15 25 25 30 45 20 30
计算过程
• 前置时间:2周 • 批量:≥25单位
零件i的MRP计算表
总需求量G(t) 预计到达量S(t) 预计现存量H(t)
净需求量N(t) 计划订货到达量P(t) 计划发出订货量R(t)
品中所处的产品结构层次不同或即使处于同
一产品结构中的但却处于不同产品结构层次
时,则取处在最低层的层级码作为该物品的 低层码,也既取数字最大的层级码。
作用:在展开MPS进行物料需求计算时,计算的顺 序是从上而下进行的,既从产品的0层次开始计算, 按低层码的顺序从低层码数字小的物料往低层码数
字高的顺序进行计算,当计算到该产品的某一层次 (如1层),但低层码不同时(物料的低层码为2), 只计算层级高(低层码数字小)的物料(按顺序),
– Ni(t)= [Gi(t)-Si(t)]-Hi(t-1) • 计划收到订货量Pi(t)
– 按需计算时(适用生产或订购数量和时间基本能够给予 保证的物料,或者是A类物料) : Pi(t)=Ni(t)
– 按固定批量计算时(适用订货费用较大的物料或生产准 备费用较大的物料) : Pi(t) = Q
• 预计库存量Hi(t) – Hi(t)=Si(t)+Pi(t)+Hi(t-1)-Gi(t) t=1,2...,L; i=1,2,...,n
园珠笔
笔筒
笔芯
笔油墨
笔芯头
笔芯杆
笔帽
Q产品的零件结构层次图
Q 0层 (L=2)
C 1层 (L=2)
E 1层 (L=2)
D 2层 (L=1)
E(2) 2层 (L=2)
低层码(low-level code,简称LLC)
概念:物料的低层码是系统分配给物料清单 上的每个物品一个从0至N的数字码。在产品 结构中,最上层的层级码为0,下一层的部 件的层级码则为1,依此类推。一个物品只 能有一个MRP低层码,当一个物品在多个产
Q产品的零件结构层次图
Q 0层 (L=2)
C 1层 (L=2)
D 2层 (L=1)
E(2) 2层 (L=2)
E 2层 (L=2)
Q产品的加工时间结构图
E Q
E C
D
0 1 2 34 56
库存信息
• 就是保持每一种零件的有关数据,如 总需求量、现有库存量、前置时间、 净需求量、预计到达量、计划发出订 货量等。
–生产计划是可行的,即假定有足够的设备、人力和资 金来保证生产计划的实现;
–假设采购计划是可行的,即有足够的供货能力和运输 能力来保证完成物料供应。
• 但在实际生产中,能力资源和物料资源总是有限 的,因而往往出现生产计划无法完成的情况。
• 20世纪70年代人们在此基础上,一方面把生产 能力作业计划,车间作,加入来 自车间,供应商和计划人员的反馈信息,并利 用这些信息进行计划的平衡调整,从而围绕着 物料需求计划,使生产的全过程形成一个统一 的闭环系统,这就是闭环式MRP。
层级比计算层次低(低层码数字大于计算的产品层
次)的物料的计算结果(毛需求量、净需求量)暂
时存储起来,总的需求量可以汇总存储,但不进行 MRP需求计算与原材料(或构成的组件)的库存分 配,这样可用的库存量优先分配给了处于最低层的
物料,保证了时间上最先需求的物料先得到库存分
配,避免了晚需求的物品提前下达计划,并占用库 存。因此,低层码是MRP的计算顺序。
总需求量G(t) 预计到达量S(t) 预计现存量H(t)
时段: 0 1 5
20 15
净需求量N(t) 计划订货到达量P(t) 计划发出订货量R(t)
23 10 18 20
25 7
3
4 5 67 8 0 10 6 0 14
7 0 00 0
36
14
36
14
6
14
课堂练习
• 前置时间:2周 • 批量:≥15单位
• MRP主要解决物料的相关需求的一系列问 题。相关需求(即与其他需求相关联) 主要包括:纵向需求,如上一级需求项 目派生出下一级需求项目,及横向需求, 如随同产品发货的附件等。
MRP的产生与发展
• 1、上世纪70年代初 MRP系统**
• 2个假设:生产提前期可靠;有足够生产能力;
• 2、上世纪70年代中期 闭环MRP系统** • 3、上世纪80年代初 MRP Ⅱ系统**
MRP的输出
• 零部件投入出产计划。 • 原材料需求计划。 • 库存状态记录。 • 零部件完工情况、原材料到货情况统计等。 • 工艺装备需求计划。 • 计划将要发出的订货。 • 已发出订货的调整。 • 对生产及库存费用进行预算的报告。 • 交货期模拟报告。 • 优先权计划。
MRP的特点
• 优点:
时段: 0 10
1 2 3 4 5 67 8 10 15 25 25 30 45 20 30 10 25 10 20 20 20 15 0 5 0
5 5 10 30 20 25
25 25 25 30 25 25
25 25 25 30 25 25
例2
• 前置时间:2周 • 批量:按需订货
零件i的MRP计算表
山米与白鹤
贝特西.贝尔斯
MRP与库存管理
MRP的概念
• MRP(Material requirement planning,物料需求 计划)定义
• MRP是一种工业制造企业内的物料计划管理模式。 通过综合分析订单、当前库存以及生产顺序的信息, 协调生产的物料需求和库存之间的差距,使得正确 的物料在正确的时间到达,以此来减少库存、降低 劳动力成本、增加按时发货率。
• CRP则是依据MRP的输出为输入,并结合生产制 造信息,对工作中心的能力进行详尽的需求分 析,计算出人员负荷和设备负荷,进行瓶颈预 测,调整生产负荷,做好生产能力与设备符合 的平衡工作,制定出CRP。
• CRP一方面能充分利用人力与设备;另一方面, 可以减少产品的加工等待时间,缩短生产周期, 为生产人员提供能力及相符合信息。
资源需求量计划
务
预测
与
主生产计划 (MPS)
成 粗生产能力计划 本
管
物料需求计划
理
(MRP)
能力需求计划 (CRP)
能力计划满足否?
是
执行能力计划 执行物料计划
MRP系统
• MRP系统的目标** • MRP系统的输入** • MRP的输出** • MRP的特点** • MRP计算**
MRP系统的目标
– MPS的计划期间:>最长的产品生产周期长。
• 物料清单(BOM,Bill of Material )
• 库存信息**
主生产计划
• 主生产计划是确定每一个具体的产品在每一个具 体的时间段的生产计划。计划的对象一般是最终 产品,即企业的销售产品,但有时也可能是组件 的MPS计划,然后再下达最终装配计划。主生产计 划是一个重要的计划层次。
MRP系统作用
• MRP是MPS需求的进一步展开,也是实现 MPS的保证和支持,它根据MPS、物料清 单和物料库存信息,计算出企业要生产 的全部加工件和采购件的需求量;按照 产品出厂的优先顺序,计算出全部加工 件和采购件的需求时间,并提出建议性 的计划订单。
闭环MRP系统
• MRP是建立在下面两个假设的基础上:
MRP计算举例
• MRP计算表:
总需求量G(t) 预计到达量S(t) 预计现存量H(t)
时段: 0 1 2 3 4 5 6 。。。n
净需求量N(t) 计划订货到达量P(t) 计划发出订货量R(t)
MRP系统基本运算的框图
开始 l=0 i=1 t=1
G(t) N(t) 计算P(t) H(t) R(t-L)=P(t)
• CRP保证了人力与设备的最佳利用和资源的有 效供给,实现了生产能力与资源的最佳配置。
MRPⅡ系统
• MRPⅡ的概念
–制造资源计划(Manufacturing Resource Planning, MRP)系统,为了区别物料需求计划系统(亦缩写为 MRP)而记为MRPⅡ。
–与MRP不同:集成了销售管理、成本管理和财务管 理的内容,不但解决了物流和信息流的统一,还集 成了资金流,对财务分析和决策提供支持。